推荐第1篇:数控论文
院系:物理与机电工程学院 专业:电气自动化技术 姓名:陈楠祥 学号:2012049505
数控加工与编程技术对电气自动化技术的意义
“电气自动化技术”专业与“数控加工与编程技术”对社会的发展有着很重要的意义:一是属于信息产业,信息产业被人们誉为“朝阳产业”,发展快、需要人才多、待遇高,是当今科技发展的趋势所在,因此,作为信息产业中的重要一员,电气自动化技术专业与“数控加工与编程技术”同样有着光辉的前途;二是“电气自动化技术”与“数控加工与编程技术”的应用范围广,目前,几乎所有的工业部门都可以同自动控制与数控加工挂上钩,现代化的农业、国防也都与自动化和数控息息相关;三是电气自动化技术专业与“数控加工与编程技术”对于个人发展非常有利。电气自动化技术专业课程设置的覆盖面广,所学的东西与其他学科交叉甚多。这也与本专业的来历有关,电气自动化技术专业大部分源于计算机或者电子工程系的自动控制专业。
数控加工的最大特征有二点:一是可以极大地提高精度,包括加工质量精度及加工时间误差精度;二是加工质量的重复性,可以稳定加工质量,保持加工零件质量的一致。也就是说加工零件的质量及加工时间是由数控程序决定而不是由机床操作人员决定的。
数控加工具有如下优点:(1)提高生产效率;(2)不需要熟练的机床操作人员;(3)提高加工精度并且保持加工质量;(4)可以减少工装卡具;(5)容易进行加工过程管理;(6)可以减少检查工作量;(7)可以降低废、次品率;(8)便于设计加工变更,加工设定柔性强;(9)容易实现操作过程的自动化,一人可以操作多台机床;(10)操作容易,极大减轻体力劳动强度。
数控加工的缺点:(1)费用高,不利于加工大批量零件;(2)操作人员要求高,工资成本高; (3)系统复杂,维修费用高,需要好的工作环境。
随着制造设备的数控化率不断提高,数控加工技术在我国得到日益广泛的使用,在模具行业,掌握数控技术与否及加工过程中数控化率的高低已成为企业是否具有竞争力的象征。
对于“数控”专业人员,主要是学习数控编程等以及一些机床加工知识,从事机床操作。而对于 “电气自动化技术”专业人员,主要是学习电工知识、电气自动化控制,包括可编程序控制器PLC、变频技术、电机调速、变压器、数控加工与编程技术、单片机、自动检测与转换技术、工厂供配电等强电弱电等。虽然我们不是数控专业的,但是数控技术不仅与“电气自动化技术”专业有着密切的关系,而且在我们的实际生活当中占据了很大的比例。
数控技术是用数字信息对机械运动和工作过程进行控制的技术,数控装备是以数控技术为代表的新技术对传统制造产业和新兴制造业的渗透形成的机电一体化产品,即所谓的数字化装备,如数控机床等。其技术涉及多个领域:(1)机械制造技术;(2)信息处理、加工、传输技术;(3)自动控制技术;(4)伺服驱动技术;(5)传感器技术;(6)软件技术等。
数控技术及装备是发展新兴高新技术产业和尖端工业的使能技术和最基本的装备。世界各国信息产业、生物产业、航空、航天等国防工业广泛采用数控技术,以提高制造能力和水平,提高对市场的适应能力和竞争能力。工业发达国家还将数控技术及数控装备列为国家的战略物资,不仅大力发展自己的数控技术及其产业,而且在\"高精尖\"数控关键技术和装备方面对我国实行封锁和限制政策。因此大力发展以数控技术为核心的先进制造技术已成为世界各发达国家加速经济发展、提高综合国力和国家地位的重要途径。
传统的机械加工都是用手工操作普通机床作业的,加工时用手摇动机械刀具切削金属,靠眼睛用卡尺等工具测量产品的精度的。现代工业早已使用电脑数字化控制的机床进行作业了,数控机床可以按照技术人员事先编好的程序自动对任何产品和零部件直接进行加工了。这就是我们说的“数控加工”。数控加工广泛应用在所有机械加工的任何领域,更是模具加工的发展趋势和重要和必要的技术手段。
数控机床是按照事先编制好的加工程序,自动地对被加工零件进行加工。我们把零件的加工工艺路线、工艺参数、刀具的运动轨迹、位移量、切削参数(主轴转数、进给量、背吃刀量等)以及辅助功能(换刀、主轴正转、反转、切削液开、关等),按照数控机床规定的指令代码及程序格式编写成加工程序单,再把这程序单中的内容记录在控制介质上(如穿孔纸带、磁带、磁盘、磁泡存储器),然后输入到数控机床的数控装置中,从而指挥机床加工零件。
这种从零件图的分析到制成控制介质的全部过程叫数控程序的编制。数控机床与普通机床加工零件的区别在于数控机床是按照程序自动加工零件,而普通机床要由人来操作,我们只要改变控制机床动作的程序就
1
可以达到加工不同零件的目的。因此,数控机床特别适用于加工小批量且形状复杂要求精度高的零件 由于数控机床要按照程序来加工零件,编程人员编制好程序以后,输入到数控装置中来指挥机床工作。程序的输入是通过控制介质来的。
经过这一学期的《数控加工与编程技术》学习,让我明白了数控加工与编程的一些基本的方法:在普通机床上加工零件时,首先应由工艺人员对零件进行工艺分析,制定零件加工的工艺规程,包括机床、刀具、定位夹紧方法及切削用量等工艺参数。同样,在数控机床上加工零件时,也必需对零件进行工艺分析,制定工艺规程,同时要将工艺参数、几何图形数据等,按规定的信息格式记录在控制介质上,将此控制介质上的信息输入到数控机床的数控装置,由数控装置控制机床完成零件的全部加工。我们将从零件图样到制作数控机床的控制介质并校核的全部过程称为数控加工的程序编制,简称数控编程。数控编程是数控加工的重要步骤。理想的加工程序不仅应保证加工出符合图样要求的合格零件,同时应能使数控机床的功能得到合理的利用与充分的发挥,以使数控机床能安全可靠及高效地工作。
一般来讲,数控编程过程的主要内容包括:分析零件图样、工艺处理、数值计算、编写加工程序单、制作控制介质、程序校验和首件试加工。
例如我们学校实验室最近安装了一个新型的机器人实验室,实验室里的机器手能模仿人手和臂的某些动作功能,用以按固定程序抓取、搬运物件或操作工具的自动操作装置。机械手是最早出现的工业机器人,也是最早出现的现代机器人,它可代替人的繁重劳动以实现生产的机械化和自动化,能在有害环境下操作以保护人身安全。在现今的生活上,科技日新月益的进展之下,机械人手臂与有人类的手臂最大区别就在于灵活度与耐力度。也就是机械手的最大优势可以重复的做同一动作在机械正常情况下永远也不会觉得累!机械手臂的应用也将会越来越广泛,机械手是近几十年发展起来的一种高科技自动生产设备,作业的准确性和环境中完成作业的能力。工业机械手机器人的一个重要分支。机械手可以减省工人、提高效率、降低成本、提高产品品质、安全性好、提升工厂形象。多关节机械手的优点是:动作灵活、运动惯性小、通用性强、能抓取靠近机座的工件,并能绕过机体和工作机械之间的障碍物进行工作.随着生产的需要,对多关节手臂的灵活性,定位精度及作业空间等提出越来越高的要求。多关节手臂也突破了传统的概念,其关节数量可以从三个到十几个甚至更多,其外形也不局限于像人的手臂,而根据不同的场合有所变化,多关节手臂的优良性能是单关节机械手所不能比拟的。
这种机器人的应用就有包含“数控加工与编程技术”与“电气自动化技术”相结合的应用,通过数控加工生产出机器手,再加上电气自动化技术的可编程序控制器PLC的应用,使得机器人能够代替我们人类来工作,能更好的适应未来的需要与发展。
随着计算机技术的迅速发展,数控机床的应用日益广泛,井进一步推动了数控系统的发展,产生了自动编程系统、计算机数控系统、计算机群控系统和天性制造系统。计算机集成制造系统及计算机辅助设计、制造一体化是机械制造一体化的高级阶段,可实现产品从设计到制造的全部自动化。
综上所述,机械设备控制技术的产生,并不是孤立的,而是各种技术相互渗透的结果。它代表了正在形成中的新一代的生产技术,已显示出并将越来越显示出强大的威力。
数控机床控制技术的发展趋势:高速化、高精度化、高可靠性、复合化、智能化、柔性化、集成化和开放性是当今数控机床行业的主要发展方向。
数控技术的问世已有40多年的历史,它是由机械学、控制学、电子学、计算机科学四大基础学科发展起来的一门综合性新型学科。技术发展的需要对21世纪的数控技术提出了更高的要求。
当今的市场,国际合作的格局逐渐形成,产品竞争日趋激烈,高效率、高精度加工手段的需求在不断升级,用户的个性化要求日趋强烈,专业化、专用化、高科技的机床越来越得到用户的青睐。
新一代数控系统的开发核心是开放性。开放性有软件平台和硬件平台的开放式系统,采用模块化,层次化的结构,并通过形式向外提供统一的应用程序接口。
为解决传统的数控系统封闭性和数控应用软件的产业化生产存在的问题。目前许多国家对开放式数控系统进行研究,数控系统开放化已经成为数控系统的未来之路。目前开放式数控系统的体系结构规范、通信规范、配置规范、运行平台、数控系统功能库以及数控系统功能软件开发工具等是当前研究的核心。网络化数控装备是近两年的一个新的焦点。数控装备的网络化将极大地满足生产线、制造系统、制造企业对
2
信息集成的需求,也是实现新的制造模式如敏捷制造、虚拟企业、全球制造的基础单元。国内外一些著名数控机床和数控系统制造公司都在近两年推出了相关的新概念和样机。
学习“电气自动化技术”专业的人员将来可以去当“数控机床维修技术员”,因为数控机床就有用到伺服系统,与“电气自动化技术”专业有着密切的联系,数控机床维修技术员的职责是:负责各类数控系统、PLC、伺服系统的维修;负责解决各类数控机床的电气及机械故障;负责制定设备的日常维护保养计划及备件计划;对设备性能的改进提供解决方案。
所以要做好一名数控机床维修技术员,首先我们要学好自己的专业知识,多增加对数控加工与编程技术的理解与认识,多向有经验者学习,不断发挥自己的人生价值,为社会贡献出自己的一份力量。 数控加工中心是从数控铣床发展而来的。与数控铣床的最大区别在于加工中心具有自动交换加工刀具的能力,通过在刀库上安装不同用途的刀具,可在一次装夹中通过自动换刀装置改变主轴上的加工刀具,实现多种加工功能。
数控加工中心是由机械设备与数控系统组成的适用于加工复杂零件的高效率自动化机床。数控加工中心是目前世界上产量最高、应用最广泛的数控机床之一。它的综合加工能力较强,工件一次装夹后能完成较多的加工内容,加工精度较高,就中等加工难度的批量工件,其效率是普通设备的5~10倍,特别是它能完成许多普通设备不能完成的加工,对形状较复杂,精度要求高的单件加工或中小批量多品种生产更为适用。
数控加工中心是一种功能较全的数控加工机床。它把铣削、镗削、钻削、攻螺纹和切削螺纹等功能集中在一台设备上,使其具有多种工艺手段。加工中心设置有刀库,刀库中存放着不同数量的各种刀具或检具,在加工过程中由程序自动选用和更换。这是它与数控铣床、数控镗床的主要区别。特别是对于必需采用工装和专机设备来保证产品质量和效率的工件。这会为新产品的研制和改型换代节省大量的时间和费用,从而使企业具有较强的竞争能力。
数控加工中心工有下列优点:
①大量减少工装数量,加工形状复杂的零件不需要复杂的工装。如要改变零件的形状和尺寸,只需要修改零件加工程序,适用于新产品研制和改型。
②加工质量稳定,加工精度高,重复精度高,适应飞行器的加工要求。
③多品种、小批量生产情况下生产效率较高,能减少生产准备、机床调整和工序检验的时间,而且由于使用最佳切削量而减少了切削时间。
④可加工常规方法难于加工的复杂型面,甚至能加工一些无法观测的加工部位。 数控加工中心的缺点是机床设备费用昂贵,要求维修人员具有较高水平。 学习“电气自动化技术”专业的人员将来也可以从事数控加工中心工作,数控加工中心比普通的数控机床的要求与条件要高很多,当然企业主要是要招“电气自动化技术”专业的人员当“数控机床维修技术员”,所以说“电气自动化技术”专业与“数控”专业,有着很重要关系,而且将来这两种专业的工作比较好找也很有发展前途,为社会的发展,起到了一个很重要的作用。
电气自动化技术专业属于制造大类,装备制造业是为国民经济和国防建设提供技术装备的基础性、战略性产业。随着我国经济的快速发展,现代化电气设备的广泛应用,工业生产的自动化程度越来越高,工业电气自动化已成为现代工业发展的基础和主导,因此,企事业部门急需电气自动化技术专业的技术人才。同时,随着装备制造业新技术、新工艺、新设备的不断涌现,企业现有电气设备维修管理人员的知识老化,适应行业发展的高素质技能型人才严重短缺。
经济发展逐步全球化,外资企业和合资企业不断进入中国,这些企业起点高,技术新,有大量的设备需要用到“电气自动化技术”和“数控加工与编程技术”方面知识;与此同时,很多大中型企业为了提高产品质量和数量以加大竞争力,进行技术改造,也引进先进设备培养高新技术人才,随着机电一体化的设备越来越多,PLC控制技术、现场总线技术、变频技术、计算机集散控制技术(DCS)、微电子技术等新知识在各行各业中特别是在工业岗位中用得越来越多,原来这些岗位的人员只懂得传统的控制,故在未来的五至十年内急需大量高层次、具有较强实践能力的技能型专门人才去充实这些岗位,以满足和适应不断增
3
长新技术的需要,这样就需要大量的电气自动化技术专业与数控专业人才,另外商业、娱乐场所、住宅管理也需要这样的高级技术应用型人才。
所以我们要培养掌握好“电气自动化技术”专业与“数控加工与编程技术”的基本理论和知识、技能,以便将来从事工业电气控制设备及系统安装、设计、调试、维护及技术管理的高级技术应用性专门人才。
推荐第2篇:数控论文
系统参数发生变化或改动,机械故障,机床电气参数未优化电机运行异常,机床位置环异常或控制逻辑不妥,是生产中数控机床加工精度异常故障的常见原因。 关键词 :数控机床 加工精度异常 故障诊断 生产中经常会遇到数控机床加工精度异常的故障。此类故
摘要 : 系统参数发生变化或改动,机械故障,机床电气参数未优化电机运行异常,机床位置环异常或控制逻辑不妥,是生产中数控机床加工精度异常故障的常见原因。
关键词 :数控机床 加工精度异常 故障诊断
生产中经常会遇到数控机床加工精度异常的故障。此类故障隐蔽性强,诊断难度比较大。形成这类故障的原因主要有五个方面:{1}机床进给单位被改动或变化。{2}机床各个轴的零点偏置[NULL OFFSET]异常。{3}轴向的反向间隙[BACK LASH]异常。{4}电机运行状态异常,即电气及控制部分异常。{5}机械故障,如丝杠,轴承,轴联器等部件。另外加工程序的编制,刀具的选择及人为因素,也可能导致加工精度异常。
1. 系统参数发生变化或改动
系统参数主要包括机床进给单位,零点偏置,反向间隙等。例如SIMENS,FANUC数系统,其进给单位有公制和英制两种。机床修理过程中某些处理,常常影响到零点偏置和间隙的变化,故障处理完毕后应作适时的调整和修改;另一方面,由于机械磨损严重或连结松动也可能造成参数实测值的变化,需要对参数做相应的修改才能满足机床加工精度的要求。 2. 机械故障导致的加工精度异常
一台THM6350立式加工中心,采用SIMENS 840D系统。在加工联杆模具过程中,忽然发现Z轴进给异常,造成至少1毫米的切削误差量(Z向过切)。调查中了解到:故障是忽然发生的。机床在点动,MDI(手动数据输入方式)操作方式下各个轴运行正常,且回参考点正常;无任何报警提示,电气控制部分硬故障的可能性排除。分析认为,主要应对以下几个方面逐一进行检查。
[1]检查机床精度异常时正在运行的加工程序段,特别是刀具长度补偿,加工坐标系(G54—G59)的校对和计算。
[2]在点动方式下,反复运动Z轴,经过视,触,听对其运动状态诊断,发现Z向运动噪
音异常,特别是快速点动,噪音更加明显。由此判断,机械方面可能存在隐患。
[3]检查机床Z轴精度。用手摇脉冲发生器移动Z轴,(将其倍率定为1X100的挡位,即每变化一步,电机进给0.1毫米),配合百分表观察Z轴的运动情况。在单向运动精度保持正常后作为起始点的正向运动,脉冲器每变化一步,机床Z轴运动的实际距离d=dl=d2=d3….=0.1mm,说明电机运行良好,定位精度也良好。而返回机床实际运动位移的变化上,可以分为四个阶段:①机床运动距离d1>d=0.1mm(斜率大于1);②表现出为d1=0.1>d2>d3(斜率小于1);③机床机构实际没移动,表现出最标准的反向间隙;④机床运动距离与脉冲器给定数值相等(斜率等于1),恢复到机床的正常运动。
无论怎样对反向间隙(参数1851)进行补偿,其表现出的特征是:除了③阶段能够补偿外,其他各段变化依然存在,特别是①阶段严重影响到机床的加工精度。补偿中发现,间隙补偿越大,①阶段移动的距离也越大。
分析上述检查认为存在几点可能原因:一是电机有异常;二是机械方面有故障;三是丝杠存在间隙。为了进一步诊断故障,将电机和丝杠完全脱开,分别对电机和机械部分进行检查。检查结果是电机运行正常;在对机械部分诊断中发现,用手盘动丝杠时,返回运动初始有非常明显的空缺感。而正常情况下,应能感觉到轴承有序而平滑的移动。经过拆卸检查发现其轴承确实受损,且有滚珠脱落。更换后机床恢复正常。
3. 机床电气参数未优化电机运行异常
有一台北京产的立式数控铣床,配备SIMENS840D系统。在加工过程中,发现X轴精度异常。检查发现X轴存在一定间隙,且电机启动时存在不稳定的现象。有手触摸X轴电机时感觉电机抖动比较厉害,停止是抖动不明显,尤其是点动方式下比较明显。分析认为,故障原因有两点,一是丝杠反向间隙很大;二是X轴电机工作异常。利用SIMENS系统的参数功能,对电机进行调试。首先对存在的间隙进行补偿;调整伺服增益参数及脉冲抑制功能参数,X轴电机的抖动消除,机床加工精度恢复正常。
4. 机床位置环异常或控制逻辑不妥
一台TH61140加工中心,系统是FANUC18I,全闭环控制方式。加工过程中,发现该机床Y轴精度异常,精度误差最小为0.006mm,最大为1.4mm。检查中,机床已经按照要求设置了G54工件坐标系。在MDI(手动数据输入方式)方式下,以G54坐标系运行一段程序即“G00G90G54Y80F100;M30;”,待机床运行结束后显示器上显示的机械坐标值为“-1046.605”,记录下该数值。然后在手动方式下,将机床点动到其他任意位置,再次在MDI方式下运行上次的程序段,待机床停止后,发现此时机床机械坐标数值显示为“-1046.992”,同第一次执行后的数值相比差了0.387mm。按照同样的方法,将Y轴点动到不同的位置,反复执行该程序段显示器上显示的数值不定。用百分表对Y轴进行仔细检查,发现机械位置实际误差同数显显示出的误差基本一致,从而认为故障原因为Y轴重复定位误差过大。对Y轴的反向间隙及定位精度进行检查,重新做补偿,均无效果。因此怀疑光栅尺及系统参数等有问题。但为什么产生如此大的误差,却未出现相应的报警信息呢?进一步检查发现,次轴为垂直方向的轴,当Y轴松开时主轴箱向下掉,造成了误差。
对机床的PLC逻辑控制程序做了修改,即在Y轴松开时,先把Y轴使能加载,再把Y轴松开;而在夹紧时,先把轴夹紧后,再把Y轴使能去掉。调整后机床故障得以解决。
推荐第3篇:数控论文
数控电火花线切割加工
1 引言
数控电火花线切割加工是一项涉及多门学科的综合性技术,是模具制造中的主力装备。成型塑料制品的模具简称为塑料模具,塑料模具生产的塑料制品在机械、电子工业中有着广泛的应用。在金属加工中,数控电火花线切割始终是塑料模加工的利器。不论是动模、定模、零配件,还是特殊加工场合,只要编制出正确的数控程式,电火花线切割在塑料要模中发挥着越来越重要的作用。
线切割主要用于加工各种形状复杂和精密细小的工件,例如冲裁模的凸模、凹模、凸凹模、固定板、卸料板等,成形刀具、样板、电火花成型加工用的金属电极,各种微细孔槽、窄缝、任意曲线等,具有加工余量小、加工精度高、生产周期短、制造成本低等突出优点,已在生产中获得广泛的应用,目前国内外的电火花线切割机床已占电加工机床总数的60%以上。
根据电极丝的运行速度不同,电火花线切割机床通常分为两类:一类是高速走丝电火花线切割机床(WEDM-HS),其电极丝作高速往复运动,一般走丝速度为8~10m/s,电极丝可重复使用,加工速度较高,但快速走丝容易造成电极丝抖动和反向时停顿,使加工质量下降,是我国生产和使用的主要机种,也是我国独创的电火花线切割加工模式;另一类是低速走丝电火花线切割机床(WEDM-LS),其电极丝作低速单向运动,一般走丝速度低于0.2m/s,电极丝放电后不再使用,工作平稳、均匀、抖动小、加工质量较好,但加工速度较低,是国外生产和使用的主要机种。
根据对电极丝运动轨迹的控制形式不同,电火花线切割机床又可分为三种:一种是靠模仿形控制,其在进行线切割加工前,预先制造出与工件形状相同的靠模,加工时把工件毛坯和靠模同时装夹在机床工作台上,在切割过程中电极丝紧紧地贴着靠模边缘作轨迹移动,从而切割出与靠模形状和精度相同的工件来;另一种是光电跟踪控制,其在进行线切割加工前,先根据零件图样按一定放大比例描绘出一张光电跟踪图,加工时将图样置于机床的光电跟踪台上,跟踪台上的光电头始终追随墨线图形的轨迹运动,再借助于电气、机械的联动,控制机床工作台连同工件相对电极丝做相似形的运动,从而切割出与图样形状相同的工件来;再一种是数字程序控制,采用先进的数字化自动控制技术,驱动机床按照加工前根据工件几何形状参数预先编制好的数控加工程序自动完成加工,不需要制作靠模样板也无需绘制放大图,比前面两种控制形式具有更高的加工精度和广阔的应用范围,目前国内外95%以上的电火花线切割机床都已采用数控化。
切割属电加工范畴,是由前苏联人发明的,我国是第一个用于工业生产的国家,当时由复但大学和苏州长风机械厂合作生产的这是最早的机型叫复旦型,我们国内在此基础上发展了快走丝系统(HS).欧美和日本发展了慢走系统(LS),
主要区别:是
1、电极丝我国采用钨钼合金丝,国外采用黄铜丝。
2、我国采用皂化工作液,国外采用去离子水。
3、我国的走丝速度为11米/秒左右,国外为3~5米/分。
4、我们的电极丝是重复利用的直到断丝为至,国外是走过后不再重用。
5、我们的精度不如国外高。
1.1数控电火花切割加工原理与特点 1.1.1数控电火花切割加工原理
电火花数控线切割加工的过程中主要包含下列三部分内容(如图a所示): (1)电极丝与工件之间的脉冲放电。
(2)电极丝沿其轴向(垂直或Z方向)作走丝运动。 (3)工件相对于电极丝在X、Y平面内作数控运动。
(1)电火花线切割加工时电极丝和工件之间的脉冲放电
电火花线切割时电极丝接脉冲电源的负极,工件接脉冲电源的正极。在正负极之间加上脉冲电源,当来一个电脉冲时,在电极丝和工件之间产生一次火花放电,在放电通道的中心温度瞬时可高达10000°C以上,高温使工件金属熔化,甚至有少量气化,高温也使电极丝和工件之间的工作液部分产生气化,这些气化后的工作液和金属蒸气瞬间迅速热膨胀,并具有爆炸的特性。这种热膨胀和局部微爆炸,将熔化和气化了的金属材料抛出而实现对工件材料进行电蚀切割加工。通常认为电极丝与工件之间的放电间隙在0.O1mm左右,若电脉冲的电压高,放电间隙会大一些。
为了电火花加工的顺利进行,必须创造条件保证每来一个电脉冲时在电极丝和工件之间产生的是火花放电而不是电弧放电。首先必须使两个电脉冲之间有足够的间隔时间,使放电间隙中的介质消电离,即使放电通道中的带电粒子复合为中性粒子,恢复本次放电通道处间隙中介质的绝缘强度,以免总在同一处发生放电而导致电弧放电。一般脉冲间隔应为脉冲宽度的4倍以上。
为了保证火花放电时电极丝不被烧断,必须向放电间隙注人大量工作液,以便电极丝得到充分冷却。同时电极丝必须作高速轴向运动,以避免火花放电总在电极丝的局部位置而被烧断,电极丝速度约在7~10m/s左右。高速运动的电极丝,还有利于不断往放电间隙中带入新的工作液,同时也有利于把电蚀产物从间隙中带出去。
电火花线切割加工时,为了获得比较好的表面粗糙度和高的尺寸精度,并保证电极丝不被烧断,应选择好相应的脉冲参数,并使工件和钼丝之间的放电必须是火花放电,而不是电弧放电。 (2)电火花线切割加工的走丝运动
为了避免火花放电总在电极丝的局部位置而被烧断,影响加工质量和生产效率。在加工过程中电极丝沿轴向作走丝运动。走丝原理如图b所示。钼丝整齐地缠绕在储丝筒上,并形成一个闭合状态,走丝电机带动储丝筒转动时,通过导丝轮使钼丝作轴线运动。
(3)X、Y坐标工作台运动
工件安装在上下两层的X、Y坐标工作台上,分别由步进电动机驱动作数控运动。工件相对于电极丝的运动轨迹,是由线切割编程所决定的。
1.1.2数控电火花切割加工特点
数控电火花线切割是数字系统控制下直接利用电能加工工件的一种方法,因一些与其他加工方相比有自己独立的特点:
(1)直接利用线状的电极丝作电极,不需要制作专用电极,可节约电极的设计、制造费用。
(2)可以加工用传统切削加工方法难以加工或无法加工的形状复杂的工件。对不同的工件只需编制不同的控制程序,对不同形状工件都很容易实现自动加工,很适合小批量形状复杂零件、单件和试制品的加工,且加工周期短。
(3)利用电蚀加工原理,电极丝与工件不直接接触,两者之间的作用很小,故而电极丝、夹具不需要太高强度。
(4)传统的车、铣、钻加工中,刀具硬度必须比工件大,而数控电火花线切割机床电极丝材料不必比工件材料硬,可节省辅助时间和刀具费用。
(5)直接利用电、热能进行加工,可以方便地对影响加工精度的加工参数(脉冲宽度、间隔、伺服速度等)进行调整,有利于加工精度提高,便于实现加工过程的自动化控制。
(6)工作液一般采用水基乳化液或纯水,成本低,不会发生火灾。
(7)利用四轴或五轴联动,可加工锥度、上下面异形体或回转体等零件。
(8)由于电极丝比较细,可以方便地加工微细异形孔、窄缝和复杂截面的型柱、型孔。由于切缝很窄,实际金属去除量很少,材料的利用率很高。对加工、节约贵重金属有重要意义。
(9)采用移动的长电极丝进行加工,使单位长度电极丝的损耗较少,从而对加工精度的影响比较小,特别在慢走丝线切割加工中,电极丝一次性使用,电极丝损耗对加工精度的影响更小。
正是由于电火花线切割加工有许多突出确良特点,因面在国内外发展都很快,在塑料模具加工中已获得了广泛的应用。
电火花线切割要求有严格的工作环境
(1)满足线切割机床所要求的空间尺寸;
(2)选择能承受机床重量的场所;
(3)选择没有振动和冲击传入的场所。
线切割放电机床是高精度加工设备,如果所放置的地方有振动和冲击,将会对机台造成严重的损伤,从而严重影响其加工精度,缩短其使用寿命,甚至导致机器报废。
(4)选择没有粉尘的场所,避免流众多的通道旁边;
线切割放电机器之本身特性,其空气中有灰尘存在,将会使机器的丝杆受到严重磨损,从而影响使用寿命;
线切割放电机器属于计算机控制,计算机所使用的磁盘对空气中灰尘的要求相当严格的,当磁盘内有灰尘进入时,磁盘就会被损坏,同时也损坏硬盘;线切割放电机本身发出大量热,所以电器柜内需要经常换气,若空气中灰尘太多,则会在换气过程中附积到各个电器组件上,造成电器组件散热不良,从而导致电路板被烧坏掉。因此,机台防尘网要经常清洁。
(5)选择温度变化小的场所,避免阳光通过窗户和顶窗玻璃直射及靠近热流的地方
高精密零件加工之产品需要在恒定的温度下进行,一般为室温20C;
由于线切割放电机器本身工作时产生相当大的热量,如果温度变化太大则会对机器使用寿命造成严重影响。
(6)选择屏蔽屋:因线切割放电加工过程属于电弧放电过程,在电弧放电过程中会产生强烈的电磁波,从而对人体健康造成伤害,同时会影响到周围的环境.
(7)选择通风条件好,宽敞的厂房,以便操作者和机床能在最好的环境下工作.
1.2数控电火花切割机床
1.2.1电火花线切割机床分类
1.按走丝的速度分为:可分为慢速走丝方式和高速走丝方式线切割机床
2.按加工特点分为:可分为大、中、小型以及普通直臂切割型与锥度切割型线切割机床。
3.按脉冲形式分为:可分为RC电源、晶体管电源、分组脉冲电源及自适应控制电源线切割机床。
1.3数控电火花线切割工艺基础
1.3.1模坯准备 1.3.2工件的装夹与调整 1.3.3电极丝的选用和调整 1.3.4工艺参数的选择
1.4数控电火花切割机床的基本编程方法
1.4.13B格式编制程序 1.4.2Pre编程
推荐第4篇:数控论文
学院
毕业论文
题 目 数控零件加工工艺设计 专 业 数控技术 年 级 2009级 学生姓名 指导教师
2011.06.29
摘 要
随着数控技术的不断发展和应用领域的扩大,数控加工技术对国计民生的一些重要行业(IT、汽车、轻工、医疗等)的发展起着越来越重要的作用,因为效率、质量是先进制造技术的主体。高速、高精加工技术可极大地提高效率,提高产品的质量和档次,缩短生产周期和提高市场竞争能力。而对于数控加工,无论是手工编程还是自动编程,在编程前都要对所加工的零件进行工艺分析,拟定加工方案,选择合适的刀具,确定切削用量,对一些工艺问题(如对刀点、加工路线等)也需做一些处理。并在加工过程掌握控制精度的方法,才能加工出合格的产品。
本文根据数控机床的特点,针对具体的零件,进行了工艺方案的分析,工装方案的确定,刀具和切削用量的选择,确定加工顺序和加工路线,数控加工程序编制。通过整个工艺的过程的制定,充分体现了数控设备在保证加工精度,加工效率,简化工序等方面的优势。
前 言
在机械加工工艺教学中,机械制造专业学生及数控技术专业学生都要学习数控车床操作技术。让学生了解相关工种的先进技术,同时培养工作岗位的前瞻性;在讲授数控知识的同时,必须要求学生掌握基本的机械加工工艺,增强系统意识,理解手动操作与自动操作之间的联系,真正把学生培养成为适应各种工作环境和岗位的多面手。数控车工基础工艺理论及技能有机融合,包括夹具的使用、量具的识读和使用、刃具的刃磨及使用、基准定位等,分类叙述了车床操作、数控车床自动编程仿真操作、数控车床编程与操作的初、中级内容。以机械加工中车工工艺学与数控车床技能训练密切结合为主线,常用量具识读及工件测量、刀具及安装、工件定位与安装、金属切削过程及精加工,较清晰地展示了数控车工必须掌握的知识和技能的训练途径。对涉及与数控专业相关的基础知识、专业计算,都进行了有针对性的论述,目的在于塑造理论充实、技能扎实的专业技能型人才。
本文以与切削用量的选择,工件的定位装夹,加工顺序和典型零件为例,结合数控加工的特点,分别进行工艺方案分析,机床的选择,刀具加工路线的确定,数控程序的编制,最终形成可以指导生产的工艺文件。在整个工艺过程的设计过程中,要通过分析,确定最佳的工艺方案,使得零件的加工成本最低,合理的选用定位夹紧方式,使得零件加工方便、定位精准、刚性好,合理选用刀具和切削参数,使得零件的加工在保证零件精度的情况下,加工效率最高、刀具消耗最低。最终形成的工艺文件要完整,并能指导实际生产。
第2章 工艺方案分析
2.1 零件图
技术要求
1 去除毛刺 尖角倒钝。 2 未注倒角均为45。 3 无热处理和硬度要求。
2.2 零件图分析 该零件表面由圆柱、顺圆弧、逆圆弧、圆锥、槽、螺纹等表面组成。尺寸标注完整,选用毛坯为45#钢,Φ55mm×150mm,无热处理和硬度要求。
2.3 确定加工方法
加工方法的选择原则是保证加工表面的加工精度和表面粗糙度的要求。由于获得同一级精度及表面粗糙度的加工方法一般有许多,因而在实际选择时,要结合零件的形状、尺寸大小和形位公差要求等全面考虑。
图上几个精度要求较高的尺寸,因其公差值较小,所以编程时没有取平均值,而取其基本尺寸。
在轮廓线上,有个锥度10度坐标P
1、和一处圆弧切点P2,在编程时要求出其坐标,P1(45.29 ,75) P2(35,56.46)。
通过以上数据分析,考虑加工的效率和加工的经济性,最理想的加工方式为车削,考虑该零件为大批量加工,故加工设备采用数控车床。
根据加工零件的外形和材料等条件,选用CJK6032数控机床。
2.4 确定加工方案
零件上比较精密表面的加工,常常是通过粗加工、半精加工和精加工逐步达到的。对这些表面仅仅根据质量要求选择相应的最终加工方法是不够的,还应正确地确定从毛坯到最终成形的加工方案。
毛坯先夹持左端,车右端轮廓113mm处,右端加工Φ39mm、SΦ42mm、R9mm、Φ35mm、锥度为10度的外圆,Φ52mm.调头装夹已加工Φ52mm外圆,左端加工Φ25mm×33mm、切退刀槽、加工螺纹M25mm×1.5mm. 该典型轴加工顺序为:
预备加工---车端面---粗车右端轮廓---精车右端轮廓---切槽---工件调头 ---车端面---粗车左端轮廓---精车左端轮廓---切退刀槽---粗车螺纹---精车螺纹
第3章 工件的装夹
3.1 定位基准的选择
在制定零件加工的工艺规程时,正确地选择工件的定位基准有着十分重要的意义。定位基准选择的好坏,不仅影响零件加工的位置精度,而且对零件各表面的加工顺序也有很大的影响。合理选择定位基准是保证零件加工精度的前提,还能简化加工工序,提高加工效率。
3.2 定位基准选择的原则
1)基准重合原则。为了避免基准不重合误差,方便编程,应选用工序基准作为定位基准,尽量使工序基准、定位基准、编程原点三者统一。
2)便于装夹的原则。所选择的定位基准应能保证定位准确、可靠,定位、夹紧机构简单、易操作,敞开性好,能够加工尽可能多的表面。
3)便于对刀的原则。批量加工时在工件坐标系已经确定的情况下,保证对刀的可能性和方便性。
3.3 确定零件的定位基准
以左右端大端面为定位基准。
3.4 装夹方式的选择 为了工件不致于在切削力的作用下发生位移,使其在加工过程始终保持正确的位置,需将工件压紧夹牢。合理的选择夹紧方式十分重要,工件的装夹不仅影响加工质量,而且对生产率,加工成本及操作安全都有直接影响。
3.5 数控车床常用的装夹方式
1)在三爪自定心卡盘上装夹。三爪自定心卡盘的三个卡爪是同步运动的,能自动定心,一般不需要找正。该卡盘装夹工件方便、省时,但夹紧力小,适用于装夹外形规则的中、小型工件。
2)在两顶尖之间装夹。对于尺寸较大或加工工序较多的轴类工件,为了保证每次装夹时的装夹精度,可用两顶尖装夹。该装夹方式适用于多序加工或精加工。
3)用卡盘和顶尖装夹。当车削质量较大的工件时要一段用卡盘夹住,另一段用后顶尖支撑。这种方式比较安全,能承受较大的切削力,安装刚性好,轴向定位准确,应用较广泛。
4)用心轴装夹。当装夹面为螺纹时再做个与之配合的螺纹进行装夹,叫心轴装夹。这种方式比较安全,能承受较大的切削力,安装刚性好,轴向定位准确。
3.6 确定合理的装夹方式
装夹方法:先用三爪自定心卡盘毛坯左端,加工右端达到工件精度要求;再工件调头,用三爪自定心卡盘毛坯右端Φ52,再加工左端达到工件精度要求。
第4章 刀具及切削用量
4.1 选择数控刀具的原则
刀具寿命与切削用量有密切关系。在制定切削用量时,应首先选择合理的刀具寿命,而合理的刀具寿命则应根据优化的目标而定。一般分最高生产率刀具寿命和最低成本刀具寿命两种,前者根据单件工时最少的目标确定,后者根据工序成本最低的目标确定。
选择刀具寿命时可考虑如下几点根据刀具复杂程度、制造和磨刀成本来选择。复杂和精度高的刀具寿命应选得比单刃刀具高些。对于机夹可转位刀具,由于换刀时间短,为了充分发挥其切削性能,提高生产效率,刀具寿命可选得低些,一般取15-30min。对于装刀、换刀和调刀比较复杂的多刀机床、组合机床与自动化加工刀具,刀具寿命应选得高些,尤应保证刀具可靠性。车间内某一工序的生产率限制了整个车间的生产率的提高时,该工序的刀具寿命要选得低些当某工序单位时间内所分担到的全厂开支M较大时,刀具寿命也应选得低些。大件精加工时,为保证至少完成一次走刀,避免切削时中途换刀,刀具寿命应按零件精度和表面粗糙度来确定。与普通机床加工方法相比,数控加工对刀具提出了更高的要求,不仅需要冈牲好、精度高,而且要求尺寸稳定,耐用度高,断和排性能坛同时要求安装调整方便,这样来满足数控机床高效率的要求。数控机床上所选用的刀具常采用适应高速切削的刀具材料(如高速钢、超细粒度硬质合金)并使用可转位刀片。
4.2 选择数控车削用刀具
数控车削车刀常用的一般分成型车刀、尖形车刀、圆弧形车刀以及三类。成型车刀也称样板车刀,其加工零件的轮廓形状完全由车刀刀刃的形伏和尺寸决定。数控车削加工中,常见的成型车刀有小半径圆弧车刀、非矩形车槽刀和螺纹刀等。在数控加工中,应尽量少用或不用成型车刀。尖形车刀是以直线形切削刃为特征的车刀。这类车刀的刀尖由直线形的主副切削刃构成,如90°内外圆车刀、左右端面车刀、切槽(切断)车刀及刀尖倒棱很小的各种外圆和内孔车刀。尖形车刀几何参数(主要是几何角度)的选择方法与普通车削时基本相同,但应结合数控加工的特点(如加工路线、加工干涉等)进行全面的考虑,并应兼顾刀尖本身的强度。
二是圆弧形车刀。圆弧形车刀是以一圆度或线轮廓度误差很小的圆弧形切削刃为特征的车刀。该车刀圆弧刃每一点都是圆弧形车刀的刀尖,应此,刀位点不在圆弧上,而在该圆弧的圆心上。圆弧形车刀可以用于车削内外表面,特别适合于车削各种光滑连接(凹形)的成型面。选择车刀圆弧半径时应考虑两点车刀切削刃的圆弧半径应小于或等于零件凹形轮廓上的最小曲率半径,以免发生加工干浅该半径不宜选择太小,否则不但制造困难,还会因刀尖强度太弱或刀体散热能力差而导致车刀损坏。 4.3 设置刀点和换刀点
刀具究竟从什么位置开始移动到指定的位置呢?所以在程序执行的一开始,必须确定刀具在工件坐标系下开始运动的位置,这一位置即为程序执行时刀具相对于工件运动的起点,所以称程序起始点或起刀点。此起始点一般通过对刀来确定,所以,该点又称对刀点。在编制程序时,要正确选择对刀点的位置。对刀点设置原则是:便于数值处理和简化程序编制。易于找正并在加工过程中便于检查,引起的加工误差小。对刀点可以设置在加工零件上,也可以设置在夹具上或机床上,为了提高零件的加工精度,对刀点应尽量设置在零件的设计基准或工艺基谁上。实际操作机床时,可通过手工对刀操作把刀具的刀位点放到对刀点上,即“刀位点”与“对刀点”的重合。所谓“刀位点”是指刀具的定位基准点,车刀的刀位点为刀尖或刀尖圆弧中心。平底立铣刀是刀具轴线与刀具底面的交点。球头铣刀是球头的球心,钻头是钻尖等。用手动对刀操作,对刀精度较低,且效率低。而有些工厂采用光学对刀镜、对刀仪、自动对刀装置等,以减少对刀时间,提高对刀精度。加工过程中需要换刀时,应规定换刀点。所谓“换刀点”是指刀架转动换刀时的位置,换刀点应设在工件或夹具的外部,以换刀时不碰工件及其它部件为准。
4.4 确定切削用量
数控编程时,编程人员必须确定每道工序的切削用量,并以指令的形式写人程序中。切削用量包括主轴转速、背吃刀量及进给速度等。对于不同的加工方法,需要选用不同的切削用量。切削用量的选择原则是:保证零件加工精度和表面粗糙度,充分发挥刀具切削性能,保证合理的刀具耐用度,并充分发挥机床的性能,最大限度提高生产率,降低成本。 第5章 典型轴类零件的加工
5.1 轴类零件加工工艺分析
(1) 技术要求
轴类零件的技术要求主要是支承轴颈和配合轴颈的径向尺寸精度和形位精度,轴向一般要求不高。轴颈的直径公差等级通常为IT6-IT8,几何形状精度主要是圆度和圆柱度,一般要求限制在直径公差范围之内。相互位置精度主要是同轴度和圆跳动;保证配合轴颈对于支承轴颈的同轴度,是轴类零件位置精度的普遍要求之一。图为特殊零件,径向和轴向公差和表面精度要求较高。
(2)毛坯选择
轴类零件除光滑轴和直径相差不大的阶梯轴采用热轧或冷拉圆棒料外,一般采用锻件;发动机曲轴等一类轴件采用球墨铸铁铸件比较多。如图典型轴类直径相差不大,采用直径为60mm,材料45#钢,在锯床上按150mm长度下料。
(3)定位基准选择 轴类零件外圆表面、内孔、螺纹等表面的同轴度,以及端面对轴中心线的垂直度是其相互位置精度的主要项目,而这些表面的设计基准一般都是轴中心线。用两中心孔定位符合基准重合原则,并且能够最大限度地在一次装夹中加工出多格外圆表面和端面,因此常用中心孔作为轴加工的定位基准。
当不能采用中心孔时或粗加工是为了提高工作装夹刚性,可采用轴的外圆表面作定位基准,或是以外圆表面和中心孔共同作为定位基准,能承受较大的切削力,但重复定位精度并不太高。
数控车削时,为了能用同一程序重复加工和工件调头加工轴向尺寸的准确性,或为了端面余量均匀,工件轴向需要定位。采用中心孔定位时,中心孔尺寸及两端中心孔间的距离要保持一致。以外圆定位时,则应采用三爪自定心卡盘反爪装夹或采用限未支承,以工件端面或台阶儿面作为轴向定位基准。
(4)轴类零件的预备加工 车削之前常需要根据情况安排预备加工,内容通常有:直--毛坯出厂时或在运输、保管过程中,或热处理时常会发生弯曲变形。过量弯曲变形会造成加工余量不足及装夹不可靠。因此在车削前需增加校直工序。
切断---用棒料切得所需长度的坯料。切断可在弓形锯床、圆盘锯床和带锯上进行,也可以在普通车床切断或在冲床上用冲模冲切。
车端面和钻中心孔—对数控车削而言,通常将他们作为预备加工工序安排。 (5) 热处理工序 铸、锻件毛坯在粗车前应根据材质和技术要求安排正火火退火处理,以消除应力,改善组织和切削性能。性能要求较高的毛坯在粗加工后、精加工前应安排调质处理,以提高零件的综合机械性能;对于硬度和耐磨性要求不高的零件,调质也常作为最终热处理。相对运动的表面需在精加工前或后进行表面淬火处理或进行化学热处理,以提高其耐磨性。
(6) 加工工序的划分一般可按下列方法进行:
①刀具集中分序法
就是按所用刀具划分工序,用同一把刀具加工完零件上所有可以完成的部位。再用第二把刀、第三把完成它们可以完成的其它部位。这样可减少换刀次数,压缩空程时间,减少不必要的定位误差。
②以加工部位分序法
对于加工内容很多的零件,可按其结构特点将加工部分分成几个部分,如内形、外形、曲面或平面等。一般先加工平面、定位面,后加工孔;先加工简单的几何形状,再加工复杂的几何形状;先加工精度较低的部位,再加工精度要求较高的部位。
③以粗、精加工分序法 对于易发生加工变形的零件,由于粗加工后可能发生的变形而需要进行校形,故一般来说凡要进行粗、精加工的都要将工序分开。
综上所述,在划分工序时,一定要视零件的结构与工艺性,机床的功能,零件数控加工内容的多少,安装次数及本单位生产组织状况灵活掌握。另建议采用工序集中的原则还是采用工序分散的原则,要根据实际情况来确定,但一定力求合理。
(7)工时在加,加工顺序的安排应根据零件的结构和毛坯状况,以及定位夹紧的需要来考虑,重点是工件的刚性不被破坏。顺序一般应按下列原则进行:
①上道工序的加工不能影响下道工序的定位与夹紧,中间穿插有通用机床加工工序的也要综合考虑。
②先进行内形内腔加工序,后进行外形加工工序。
③以相同定位、夹紧方式或同一把刀加工的工序最好连接进行,以减少重复定位次数,换刀次数与挪动压板次数。
④在同一次安装中进行的多道工序,应先安排对工件刚性破坏小的工序。
在数控车床上粗车、半精车分别用一个加工程序控制。工件调头装夹由程序中的M00或M01指令控制程序暂停,装夹后按“循环启动”继续加工。 (8)走刀路线和对刀点选择
走刀路线包括切削加工轨迹,刀具运动到切削起始点、刀具切入、切出并返回切削起始点或对刀点等非切削空行程轨迹。由于半精加工和精加工的走刀路线是沿其零件轮廓顺序进行的,所以确定走刀路线主要在于规划好粗加工及空行程的走刀路线。合理确定对刀点,对刀点可以设在被加工零件上,但注意对刀点必须是基准位或已精加工过的部位,有时在第一道工序后对刀点被加工毁坏,会导致第二道工序和之后的对刀点无从查找,因此在第一道工序对刀时注意要在与定位基准有相对固定尺寸关系的地方设立一个相对对刀位置,这样可以根据它们之间的相对位置关系找回原对刀点。这个相对对对刀位置通常设在机床工作台或夹具上。
5.2 典型轴类零件加工工艺
(1)确定加工顺序及进给路线
加工顺序按粗到精、由近到远(由右到左)的原则确定。工件右端加工:既先从右到左进行外轮廓粗车(留0.5mm余量精车),然后从右到左进行外轮廓精车,最后切槽;工件调头,工件左端加工:粗加工外轮廓、精加工外轮廓,切退刀槽,最后螺纹粗加工、螺纹精加工。
(2)选择刀具
1)车端面:选用硬质合金45度车刀,粗、精车用一把刀完成。
2) 粗、精车外圆:(因为程序选用 G71循环所以粗、精车选用同一把刀)硬质合金90度放型车刀,Kr=90度,Kr'=60度;E=30度,(因为有圆弧轮廓)以防与工件轮廓发生干涉,如果有必要就用图形来检验.3)车槽: 选用硬质合金车槽刀(刀长12mm,刀宽3mm) 4)车螺纹:选用60度硬质合金外螺纹车刀. (3)选择切削用量
推荐第5篇:数控论文
首页 浏览文档 共享文档 我要上传搜 索 高级搜索
数控系 2011 届数控设备应用与维护专业毕业生 毕 业 设 计 姓名:何立冬 班级:083521 毕业设计题目:FANUC 0i 系列进给伺服系统调试与诊断 指导老师: 目录第一章 数控机床的基本组成及维护 第一节 数控机床的基本组成 第二节 数控机床的维修应用及维护 第三节 数控机床的故障诊断第二章 数控机床伺服系统的了解及分类 第一节 数控系统组成及作用 第二节 伺服系统的概述 第三节 伺服系统的组成及分类 第四节 伺服系统的作用第三章 FANUC 0i 系列数控系统的基本介绍 第一节 FANUC 简介 第二节 FANUC 系统的介绍
第四章 FANUC 0i-mate 系列进给伺服系统调试与诊断 第一节 FANUC 0i-mate 系列进给伺服系统 第二节 FANUC 0i-mate 系列进给伺服系统的调试 第三节 FANUC 0i-mate 系列进给伺服系统的参数 第四节 FANUC 0i-mate 系列进给伺服系统故障诊断第一章 数控机床的基本组成及维护 第一节 数控机床的基本组成 数控机床一般由控制介质、数控装置、伺服系统和机床本体组成。图 1—2 的实线所示为开环控制的数控机床框图。 为了提高机床的加工精度,在上述系统中再加入一个测量装置(即图 1—2 中的虚线部分),这样就构成了闭环控制的数控机床框图。开环控制系统的工作过程是这样的:将控制机床工作台运动的位移量、位移速度、位移方向、位移轨迹等参量通过控制介质输入给机床数控装置,数控装置根据这些参量指令计算得出进给脉冲序列(包 ,然后经伺服系统转换放大,最后控制工作台按含有上述 4 个参量)所要求的速度、轨迹、方向和距离移动。若为闭环系统,则在输入指令值的同时,反馈检测机床工作台的实者间有误际位移值,反馈量与输入量在数控装置中进行比较,若有差值,说明二差,则数控装置控制机床向着消除误差的方向运动。 1控制介质:以指令的形式记载各种加工信息; 2数控装置:接受输入的加工信息,经数控装置运算处理,向伺服系统发出相应的脉冲; 3伺服系统:把数控装置的脉冲信号转换成机床运动部件的机械位移;用于实现数控机床的进给伺服控制和主轴伺服控制。 4机械系统:包括,主轴部分、进给系统、刀库和自动换刀装置ATC、自动托盘交换装置APC等。 图 1.4 进给伺服系统组成 第二节 数控机床的应用及维护 学技术的发展,对机械产品提出了高精度、高复杂性的要求,而且产品的更新换代也在加快,这对机床设备不仅提出了精度和效率的要求,而且也对其提出了通用性和灵活性的要求。数控机床就是针对这种要求而产生的一种新型自动化机床。数控机床集微电子技术、计算机技术、自动控制技术及伺服驱动技术、精密机械技术于一体,是高度机电一体化的典型产品。它本身又是机电一体化的重要组成部分,是现代机床技术水平的重要标志。数控机床体现了当前世界机床技术进步的主流,是衡量机械制造工艺水平的重要指标,在柔性生产和计算机集成制造等先进制造技术中起着重要的基础核心作用。因此,如何更好的使用数控机床是一个很重要的问题。由于数控机床是一种价格昂贵的精密设备,因此,其维护更是不容忽视。
一、数控机床1.数控加工的概念数控机床的工作原理就是将加工过程所需的各种操作(如主轴变速、工件的松开与夹紧、进刀与退刀、开车与停车、自动关停冷却液)和步骤以及工件的形状尺寸用数字化的代码表示,通过控制介质(如穿孔纸带或磁盘等)将数字信息送入数控装置,数控装置对输入的信息进行处理与运算,发出各种控制信号,控制机床的伺服系统或其他驱动元件,使机床自动加工出所需要的工件。所以,数控加工的关键是加工数据和工艺参数的获取,即数控编程。数控加工一般包括以下几个内容:1对图纸进行分析,确定需要数控加工的部分;2利用图形软件(如 CAXA 制造工程师)对需要数控加工的部分造型;3根据加工条件,选择合适的加工参数,生成加工轨迹(包括粗加工、半精加工、精加工轨迹);4轨迹的仿真检验;5生成 G 代码;6传给机床加工。2.数控机床的特点1具有高度柔性在数控机床上加工零件,主要取决于加工程序,它与普通机床不同,不必制造、更换许多工具、夹具,不需要经常调整机床。因此,数控机床适用于零件频繁更换的场合。也就是适合单件、小批生产及新产品的开发,缩短了生产准备周期,节省了大量工艺设备的费用。2加工精度高数控机床的加工精度,一般可达
到 0.005~0.1mm,数控机床是按数字信号形式控制的,数控装置每输出一个脉冲信号,则机床移动部件移动一个脉冲当量(一般为 0.001mm),而且机床进给传动链的反向间隙与丝杠螺距平均误差可由数控装置进行补偿,因此,数控机床定位精度比较高。3加工质量稳定、可靠加工同一批零件,在同一机床,在相同加工条件下,使用相同刀具和加工程序,刀具的走刀轨迹完全相同,零件的一致性好,质量稳定。4生产率高数控机床可有效地减少零件的加工时间和辅助时间,数控机床的主轴转速和进给量的范围大,允许机床进行大切削量的强力切削,数控机床目前正进入高速加工时代,数控机床移动部件的快速移动和定位及高速切削加工,减少了半成品的工序间周转时间,提高了生产效率。5改善劳动条件数控机床加工前经调整好后,输入程序并启动,机床就能自动连续的进行加工,直至加工结束。操作者主要是程序的输入、编辑、装卸零件、刀具准备、加工状态的观测,零件的检验等工作,劳动强度极大降低,机床操作者的劳动趋于智力型工作。另外,机床一般是封闭式加工,即清洁,又安全。6利于生产管理现代化数控机床的加工,可预先精确估计加工时间,所使用的刀具、夹具可进行规范化、现代化管理。数控机床使用数字信号与标准代码为控制信息,易于实现加工信息的标准化,目前已与计算机辅助设计与制造(CAD/CAM)有机地结合起来,是现代集成制造技术的基础。3.数控机床使用中应注意的事项使用数控机床之前,应仔细阅读机床使用说明书以及其他有关资料,以便正确操作使用机床,并注意以下几点:1机床操作、维修人员必须是掌握相应机床专业知识的专业人员或经过技术培训的人员,且必须按安全操作规程及安全操作规定操作机床;2非专业人员不得打开电柜门,打开电柜门前必须确认已经关掉了机床总电源开关。只有专业维修人员才允许打开电柜门,进行通电检修;3除一些供用户使用并可以改动的参数外,其它系统参数、主轴参数、伺服参数等,用户不能私自修改,否则将给操作者带来设备、工件、人身等伤害;4修改参数后,进行第一次加工时,机床在不装刀具和工件的情况下用机床锁住、单程序段等方式进行试运行,确认机床正常后再使用机床;5机床的 PLC 程序是机床制造商按机床需要设计的,不需要修改。不正确的修改,操作机床可能造成机床的损坏,甚至伤害操作者;6建议机床连续运行最多 24 小时,如果连续运行时间太长会影响电气系统和部分机械器件的寿命,从而会影响机床的精度;7机床全部连接器、接头等,不允许带电拔、插操作,否则将引起严重的后果。二 数控机床维修 数控机床维修工作所包含的内容有:日常维护、修理和排除故障。 日常维护: a.每日须检查的内容:如导轨表面、润滑油箱、气源压力、液压系统、CNC、I/O 单元各种防护网及清洗各种过滤网等; b.每半年或每年的检查与维护作业:如滚珠丝杠油脂更换涂覆,更换主轴油箱用油,伺服电机碳刷的清理,更换润滑油和清洗液压泵; c.不定期的维护作业:如导轨镶条的检查与压紧或放松,冷却水箱液面高度与过滤器的清洗,排屑器是否畅通、主轴传动带的松紧调整等。 故障判断: 对故障现场做充分调研,了解故障的表现,工作寄存器及缓冲工作寄存器中相关内容,了解正在执行程序段内容及自诊断报警内容。分析中要利用机床的技术档案与各种资料,找出造成故障的各种原因。
三、数控机床电气设备维修的方法与实践转载 。
一、数控设备的维护保养知识 数控设备是一种自动化程度较高,结构较复杂的先进加工设备,是企业的重点、关键设备。要发挥数控设备的高效益,就必须正确的操作和精心的维护,才能保证设备的利用率。正确的操作使用能够防止机床非正常磨损,避免突发故障;做好日常维护保养,可使设备保持良好的技术状态,延缓劣化进程,及时发现和消灭故障隐患,从而保证安全运行。
1、数控设备使用中应注意的问题 1.1 数控设备的使用环境 为提高数控设备的使用寿命,一般要求要避免阳光的直接照射和其他热辐射,要避免太潮湿、粉尘过多或有腐蚀气体的场所。腐蚀气体易使电子元件受到腐蚀变质,造成接触不良或元件间短路,影响设备的正常运行。精密数控设备要远离振动大的设备,如冲床、锻压设备等。 1.2 电源要求 为了避免电源波动幅度大(大于±10)和可能的瞬间干扰信号等影响,数控设备一般采用专线供电(如从低压配电室分一路单独供数控机床使用)或增设
稳压装置等,都可减少供电质量的影响和电气干扰。 1.3 操作规程 操作规程是保证数控机床安全运行的重要措施之一,操作者一定要按操作规程操作。机床发生故障时,操作者要注意保留现场,并向维修人员如实说明出现故障前后的情况,以利于分析、诊断出故障的原因,及时排除。 另外,数控机床不宜长期封存不用,购买数控机床以后要充分利用,尤其是投入使用的第一年,使其容易出故障的薄弱环节尽早暴露,得以在保修期内得以排除。在没有加工任务时,数控机床也要定期通电,最好是每周通电 1-2 次,每次空运行 1 小时左右,以利用机床本身的发热量来降低机内的湿度,使电子元件不致受潮,同时也能及时发现有无电池报警发生,以防止系统软件、参数的丢失。
2、数控机床的维护保养 数控机床种类多,各类数控机床因其功能,结构及系统的不同,各具不同的特性。其维护保养的内容和规则也各有其特色,具体应根据其机床种类、型号及实际使用情况,并参照机床使用说明书要求,制订和建立必要的定期、定级保养制度。下面是一些常见、通用的日常维护保养要点。 2.1 数控系统的维护 1)严格遵守操作规程和日常维护制度 2)应尽量少开数控柜和强电柜的门 在机加工车间的空气中一般都会有油雾、灰尘甚至金属粉末,一旦它们落在数控系统内的电路板或电子器件上,容易引起元器件间绝缘电阻下降,甚至导致元器件及电路板损坏。有的用户在夏天为了使数控系统能超负荷长期工作,采取打开数控柜的门来散热,这是一种极不可取的方法,其最终将导致数控系统的加速损坏。 3)定时清扫数控柜的散热通风系统 应该检查数控柜上的各个冷却风扇工作是否正常。每半年或每季度检查一次风道过滤器是否有堵塞现象,若过滤网上灰尘积聚过多,不及时清理,会引起数控柜内温度过高。 4)数控系统的输入/输出装置的定期维护 80 年代以前生产的数控机床,大多带有光电式纸带阅读机,如果读带部分被污染,将导致读入信息出错。为此,必须按规定对光电阅读机进行维护。 5)直流电动机电刷的定期检查和更换 直流电动机电刷的过渡磨损,会影响电动机的性能,甚至造成电动机损坏。为此,应对电动机电刷进行定期检查和更换。数控车床、数控铣床、加工中心等,应每年检查一次。 6)定期更换存储用电池 一般数控系统内对 CMOSRAM 存储器件设有可充电电池维护电路,以保证系统不通电期间能保持其存储器的内容。在一般情况下,即使尚未失效,也应每年更换一次,以确保系统正常工作。电池的更换应在数控系统供电状态下进行,以防更换时 RAM 内信息丢失。 7)备用电路板的维护 备用的印制电路板长期不用时,应定期装到数控系统中通电运行一段时间,以防损坏。 2.2 机械部件的维护 1)主传动链的维护 定期调整主轴驱动带的松紧程度,防止因带打滑造成的丢转现象;检查主轴润滑的恒温油箱、调节温度范围,及时补充油量,并清洗过滤器;主轴中刀具夹紧装置长时间使用后,会产生间隙,影响刀具的夹紧,需及时调整液压缸活塞的位移量。 2)滚珠丝杠螺纹副的维护 定期检查、调整丝杠螺纹副的轴向间隙,保证反向传动精度和轴向刚度;定期检查丝杠与床身的连接是否有松动;丝杠防护装置有损坏要及时更换,以防灰尘或切屑进入。 3)刀库及换刀机械手的维护 严禁把超重、超长的刀具装入刀库,以避免机械手换刀时掉刀或刀具与工件、夹具发生碰撞;经常检查刀库的回零位置是否正确,检查机床主轴回换刀点位置是否到位,并及时调整;开机时,应使刀库和机械手空运行,检查各部分工作是否正常,特别是各行程开关和电磁阀能否正常动作;检查刀具在机械手上锁紧是否可靠,发现不正常应及时处理。 2.3 液压、气压系统维护 定期对各润滑、液压、气压系统的过滤器或分滤网进行清洗或更换;定期对液压系统进行油质化验检查和更换液压油;定期对气压系统分滤气器放水; 2.4 机床精度的维护 定期进行机床水平和机械精度检查并校正。机械精度的校正方法有软硬两种。其软方法主要是通过系统参数补偿,如丝杠反向间隙补偿、各坐标定位精度定点补偿、机床回参考点位置校正等;硬方法一般要在机床大修时进行,如进行导轨修刮、滚珠丝杠螺母副预紧调整反向间隙等。
二、维修工作的基本条件 数控机床的身价从几十万元到上千万元,一般都是企业中关键产品关键工序的关键设备,一旦故障停机,其影响和损失往往很大。但是,人们对这样的设备往往更多地是看重其效能,而不仅对合理
地使用不够重视,更对其保养及维修工作关注太少,日常不注意对保养与维修工作条件的创造和投入,故障出现临时抱佛脚的现象很是普遍。因此,为了充分发挥数控机床的效益,我们一定要重视维修工作,创造出良好的维修条件。由于数控机床日常出现的多为电气故障,所以电气维修更为重要。 1.人员条件 数控机床电气维修工作的快速性、优质性关键取决于电气维修人员的素质条件。 1 首先是有高度的责任心和良好的职业道德。 2 知识面要广。要学习并基本掌握有关数控机床电气控制的各学科知识,如计算机技术、模拟与数字电路技术、自动控制与拖动理论、控制技术、加工工艺以及机械传动技术,当然还包括上节所讲的基本数控知识。 3 应经过良好的技术培训。数控技术基础理论的学习,尤其是针对具体数控机床的技术培训,首先是参加相关的培训班和机床安装现场的实际培训,然后向有经验的维修人员学习,而更重要且更长时间的是自学。 4 勇于实践。要积极投入数控机床的维修与操作的工作中去,在不断的实践中提高分析能力和动手能力。 5 掌握科学的方法。要做好维修工作光有热情是不够的,还必须在长期的学习和实践中总结提高,从中提炼出分析问题、解决问题的科学的方法。 6 学习并掌握各种电气维修中常用的仪器、仪表和工具。 7 掌握一门外语,特别是英语。起码应做到能看懂技术资料。 2.物质条件 1 准备好通用的和某台数控机床专用的电气备件。 2 非必要的常备电器元件应做到采购渠道快速畅通。 3 必要的维修工具、仪器仪表等,最好配有笔记本电脑并装有必要的维修软件。 4 每台数控机床所配有的完整的技术图样和资料。 5 数控机床使用、维修技术档案材料。 3.关于预防性维护 预防性维护的目的是为了降低故障率,其工作内容主要包括下列几方面的工作。 1 人员安排为每台数控机床分配专门的操作人员、工艺人员和维修人员,所有人员都要不断地努力提高自己的业务技术水平。 2 建规建档针对每台机床的具体性能和加工对象制定操作规章,建立工作与维修档案,管理者要经常检查、总结、改进。 3 日常保养对每台数控机床都应建立日常维护保养计划,包括保养内容如坐标轴传动系统的润滑、磨损情况,主轴润滑等,油、水气路,各项温度控制,平衡系统,冷却系统,传动带的松紧,继电器、接触器触头清洁,各插头、接线端是否松动,电气柜通风状况等等及各功能部件和元气件的保养周期每日、每月、半年或不定期。 4 提高利用率数控机床如果较长时间闲置不用,当需要使用时,首先机床的各运动环节会由于油脂凝固、灰尘甚至生锈而影响其静、动态传动性能,降低机床精度,油路系统的堵塞更是一大烦事;从电气方面来看,由于一台数控机床的整个电气控制系统硬件是由数以万计的电子元器件组成的,他们的性能和寿命具有很大离散性,从宏观来看分三个阶段:在一年之内基本上处于所谓quot磨合quot阶段。在该阶段故障率呈下降趋势,如果在这期间不断开动机床则会较快完成quot磨合quot任务,而且也可充分利用一年的维修期;第二阶段为有效寿命阶段,也就是充分发挥效能的阶段。在合理使用和良好的日常维护保养的条件下,机床正常运转至少可在五年以上;第三阶段为系统寿命衰老阶段,电器硬件故障会逐渐增多,数控系统的使用寿命平均在 8~10 年左右。 因此,在没有加工任务的一段时间内,最好较低速度下空运行机床,至少也要经常给数控系统通电,甚至每天都应通电。
三、维修与排故技术 1.常见电气故障分类 数控机床的电气故障可按故障的性质、表象、原因或后果等分类。 1 以故障发生的部位,分为硬件故障和软件故障。硬件故障是指电子、电器件、印制电路板、电线电缆、接插件等的不正常状态甚至损坏,这是需要修理甚至更换才可排除的故障。而软件故障一般是指 PLC 逻辑控制程序中产生的故障,需要输入或修改某些数据甚至修改 PLC 程序方可排除的故障。零件加工程序故障也属于软件故障。最严重的软件故障则是数控系统软件的缺损甚至丢失,这就只有与生产厂商或其服务机构联系解决了。 2 以故障出现时有无指示,分为有诊断指示故障和无诊断指示故障。当今的数控系统都设计有完美的自诊断程序,时实监控整个系统的软、硬件性能,一旦发现故障则会立即报警或者还有简要文字说明在屏幕上显示出来,结合系统配备的诊断手册不仅可以找到故障发生的原因、部位,而且还有排除的方法提示。机床制造者也会针对具体
机床设计有相关的故障指示及诊断说明书。上述这两部分有诊断指示的故障加上各电气装置上的各类指示灯使得绝大多数电气故障的排除较为容易。无诊断指示的故障一部分是上述两种诊断程序的不完整性所致如开关不闭合、接插松动等。这类故障则要依靠对产生故障前的工作过程和故障现象及后果,并依靠维修人员对机床的熟悉程度和技术水平加以分析、排除 3 以故障出现时有无破坏性,分为破坏性故障和非破坏性故障。对于破坏性故障,损坏工件甚至机床的故障,维修时不允许重演,这时只能根据产生故障时的现象进行相应的检查、分析来排除之,技术难度较高且有一定风险。如果可能会损坏工件,则可卸下工件,试着重现故障过程,但应十分小心。 4 以故障出现的或然性,分为系统性故障和随机性故障。系统性故障是指只要满足一定的条件则一定会产生的确定的故障;而随机性故障是指在相同的条件下偶尔发生的故障,这类故障的分析较为困难,通常多与机床机械结构的局部松动错位、部分电气工件特性漂移或可靠性降低、电气装置内部温度过高有关。此类故障的分析需经反复试验、综合判断才可能排除。 5以机床的运动品质特性来衡量,则是机床运动特性下降的故障。在这种情况下,机床虽能正常运转却加工不出合格的工件。例如机床定位精度超差、反向死区过大、坐标运行不平稳等。这类故障必须使用检测仪器确诊产生误差的机、电环节,然后通过对机械传动系统、数控系统和伺服系统的最佳化调整来排除。 2.故障的调查与分析 这是排故的第一阶段,是非常关键的阶段,主要应作好下列工作: ① 询问调查 在接到机床现场出现故障要求排除的信息时,首先应要求操作者尽量保持现场故障状态,不做任何处理,这样有利于迅速精确地分析故障原因。同时仔细询问故障指示情况、故障表象及故障产生的背景情况,依此做出初步判断,以便确定现场排故所应携带的工具、仪表、图纸资料、备件等,减少往返时间。 ② 现场检查 到达现场后,首先要验证操作者提供的各种情况的准确性、完整性,从而核实初步判断的准确度。由于操作者的水平,对故障状况描述不清甚至完全不准确的情况不乏其例,因此到现场后仍然不要急于动手处理,重新仔细调查各种情况,以免破坏了现场,使排故增加难度。 ③ 故障分析 根据已知的故障
推荐第6篇:数控论文
谈数控技术的现状及发展
作者:辽宁科技大学 06机械8班
丁洪帅
内容摘要:
随着科学技术的高速发展,制造业领域发生了根本的变化。数控技术的广泛应用大大提高了生产效率和产品质量,使得机械加工进入了柔性自动化时代。数控技术集传统的机械制造、计算机、现代控制、传感技术、信息处理、光机电技术于一体,是现代制造技术的基础。它的应用和发展不仅给机械制造界带来深刻的变化,而且给其他领域带来了变革。数控设备在现代工业中得到广泛的应用,其数量和数控化率高低已成为衡量一个国家工业现代化水平的重要标志。本文将对数控技术的含义、现状、未来发展以及我国数控技术的未来发展空间这四个方面进行探讨。
关键词:
数控技术,现实发展状况,未来发展及变革空间,我国数控技术的发展 正文:
一,数控的基本理解
数控技术是指用数字、文字和符号组成的数字指令来实现一台或多台机械设备动作控制的技术。它所控制的通常是位置、角度、速度等机械量和与机械能量流向有关的开关量。数控的产生依赖于数据载体和二进制形式数据运算的出现。1908年,穿孔的金属薄片互换式数据载体问世;19世纪末,以纸为数据载体并具有辅助功能的控制系统被发明;1938年,香农在美国麻省理工学院进行了数据快速运算和传输,奠定了现代计算机,包括计算机数字控制系统的基础。数控技术是与机床控制密切结合发展起来的。1952年,第一台数控机床问世,成为世界机械工业史上一件划时代的事件,推动了自动化的发展。
数控技术也叫计算机数控技术,目前它是采用计算机实现数字程序控制的技术。这种技术用计算机按事先存贮的控制程序来执行对设备的控制功能。由于采用计算机替代原先用硬件逻辑电路组成的数控装置,使输入数据的存贮、处理、运算、逻辑判断等各种控制机能的实现,均可通过计算机软件来完成。
二,数控技术的现状
近年来我国企业的数控机床占有率逐年上升,在大中企业已有较多的使用,在中小企业甚至个体企业中也普遍开始使用。在这些数控机床中,除少量机床以fms模式集成使用外,大都处于单机运行状态,并且相当部分处于使用效率不高,管理方式落后的状态。
2001年,我国机床工业产值已进入世界第5名,机床消费额在世界排名上升到第3位,达47.39亿美元,仅次于美国的53.67亿美元,消费额比上一年增长25%。但由于国产数控机床不能满足市场的需求,使我国机床的进口额呈逐年上升态势,2001年进口机床跃升至世界第2位,达24.06亿美元,比上年增长27.3%。
近年来我国出口额增幅较大的数控机床有数控车床、数控磨床、数控特种加工机床、数控剪板机、数控成形折弯机、数控压铸机等,普通机床有钻床、锯床、插床、拉床、组合机床、液压压力机、木工机床等。出口的数控机床品种以中低档为主。
同时,新产品开发有了很大突破,技术含量高的产品占据了主导地位。数控机床产量的大幅度增长也是我国数控领域的基本现状之一。数控机床发展的关键配套产品有了较大的突破,近年来通过政府的支持,数控机床\"\"套餐\"\"开始摆上“餐桌”。如北京航天机床数控系统集团公司建立了具有自主知识产权的新一代开放式数控系统平台;烟台第二机床附件厂开发了为数控机床配套的多种动力卡盘和过滤排屑装置;济南第二机床集团公司的数控龙门镗铣床、数控落地镗铣
床及数控锻压设备等30多个系列100多个品种的数控\"\"套餐\"\",吸引了人们广泛关注。
三,数控技术的发展空间
从目前世界上数控技术及其装备发展的趋势来看,其主要研究热点有以下几个方面:
第一,高速、高精加工技术及装备的新趋势:
效率、质量是先进制造技术的主体。高速、高精加工技术可极大地提高效率,提高产品的质量和档次,缩短生产周期和提高市场竞争能力。为此日本先端技术研究会将其列为5大现代制造技术之一,国际生产工程学会(CIRP)将其确定为21世纪的中心研究方向之一。
在加工精度方面,近10年来,普通级数控机床的加工精度已由10μm提高到5μm,精密级加工中心则从3~5μm,提高到1~1.5μm,并且超精密加工精度已开始进入纳米级(0.01μm)。
在可靠性方面,国外数控装置的MTBF值已达6 000h以上,伺服系统的MTBF值达到30000h以上,表现出非常高的可靠性。
第二.,5轴联动加工和复合加工机床快速发展:
采用5轴联动对三维曲面零件的加工,可用刀具最佳几何形状进行切削,不仅光洁度高,而且效率也大幅度提高。一般认为,1台5轴联动机床的效率可以等于2台3轴联动机床,特别是使用立方氮化硼等超硬材料铣刀进行高速铣削淬硬钢零件时,5轴联动加工可比3轴联动加工发挥更高的效益。但过去因5轴联动数控系统、主机结构复杂等原因,其价格要比3轴联动数控机床高出数倍,加之编程技术难度较大,制约了5轴联动机床的发展。
当前由于电主轴的出现,使得实现5轴联动加工的复合主轴头结构大为简化,其制造难度和成本大幅度降低,数控系统的价格差距缩小。因此促进了复合主轴头类型5轴联动机床和复合加工机床(含5面加工机床)的发展。
第三, 智能化、开放式、网络化成为当代数控系统发展的主要趋势:
21世纪的数控装备将是具有一定智能化的系统,智能化的内容包括在数控系统中的各个方面:为追求加工效率和加工质量方面的智能化,如加工过程的自适应控制,工艺参数自动生成;简化编程、简化操作方面的智能化,如智能化的自动编程、智能化的人机界面等;还有智能诊断、智能监控方面的内容、方便系统的诊断及维修等。
数控系统开放化已经成为数控系统的未来之路。所谓开放式数控系统就是数控系统的开发可以在统一的运行平台上,面向机床厂家和最终用户,通过改变、增加或剪裁结构对象(数控功能),形成系列化,并可方便地将用户的特殊应用和技术诀窍集成到控制系统中,快速实现不同品种、不同档次的开放式数控系统,形成具有鲜明个性的名牌产品。
网络化数控装备是近两年国际著名机床博览会的一个新亮点。数控装备的网络化将极大地满足生产线、制造系统、制造企业对信息集成的需求,也是实现新的制造模式如敏捷制造、虚拟企业、全球制造的基础单元。
第四, 重视新技术标准、规范的建立:
(1) 关于数控系统设计开发规范
如前所述,开放式数控系统有更好的通用性、柔性、适应性、扩展性,美国、欧共体和日本等国纷纷实施战略发展计划,并进行开放式体系结构数控系统规范(OMAC、OSACA、OSEC)的研究和制定,世界3个最大的经济体在短期内进行了几乎相同的科学计划和规范的制定,预示了数控技术的一个新的变革时期的来临。
(2) 关于数控标准
数控标准是制造业信息化发展的一种趋势。数控技术诞生后的50年间的信息交换都是基于ISO6983标准,即采用G,M代码描述如何(how)加工,其本质特征是面向加工过程,显然,他已越来越不能满足现代数控技术高速发展的需要。为此,国际上正在研究和制定一种新的CNC系统标准ISO14649(STEP-NC),其目的是提供一种不依赖于具体系统的中性机制,能够描述产品整个生命周期内的统一数据模型,从而实现整个制造过程,乃至各个工业领域产品信息的标准化。
第五,数字式交流伺服成为主流,数字式交流伺服系统体积小,性能好,调试方便,克服了过去模拟伺服系统用电位器调节的不便。通过数字设定可优化速度,电流环,可进行转矩限制,进行加减速控制,另外可以和外
部计算机通讯,备份伺服参数,并在上位机显示电流,扭矩波形,便于观察。
四,我国数控技术发展
我国数控技术发展应该结合我国的具体实际,在一下几个方面多家改进: 首先,中国厂多人众,极需正确的方针、政策对数控机床的发展进行有力的指引。应学习美、德、日经验,政府高度重视、正确决策、大力扶植。在方针政策上,应讲究科学精神、经济实效,以切实提高生产率、劳动生产率为原则。
其次,在方法上,深入用户,精通工艺,低中高档并举,学习日本,批量生产,占领市场,减少进口,扩大出口。
再次,在步骤措施上,必须使国产数控系统先进、可靠,狠抓产品质量与配套件过关,打好技术基础。近期重在打基础,建立信誉,扩大国产数控机床的国内市场份额,远期谋求赶超世界先进水平,大步走向世界市场。
最后,必须狠抓根本,坚持“以人为本”,加速提高人员素质、培养各种专家人才,从根本上改变目前低效、落後的状态。人是一切事业成败的根本,层层都要重视“培才、选才、用才”,建立学习型企业,树立企业文化,加速培育新人,培训在职人员,建立师徒相传制度,举办各种技术讲座、训练班和专题讨论会,甚至聘请外国专家、顾问等,尽力提高数控。
数控技术的应用不但给传统制造业带来了革命性的变化,使制造业成为工业化的象征,而且随着数控技术的不断发展和应用领域的扩大,他对国计民生的一些重要行业(汽车、轻工、医疗等)的发展起着越来越重要的作用,因为这些行业所需装备的数字化已是现代发展的大趋势。数控技术的未来发展空间是很广阔的,数控技术的发展离不开整个社会服务体系的完善,包括人材培训,维修服务等方面的配合,这也是我国社会需要加紧步伐的部分,中国今后要加速发展数控机床产业,既要深入总结过往的经验教训,切实改善存在的问题,又要认真学习国外的先进经验,沿正确的道路前进。
推荐第7篇:数控车论文
浅谈中职学校《数控车削编程与操作》的教学策略 内容摘要:本文根据中职学校学生的特点与本校具体情况从帮助学生树立学好专业技能的信心,补差补缺,逐步提高学生知识水平,运用灵活的教学手段,精心设计教学内容,改进教学方法等方面就如何搞好《数控车削编程与操作》课程的教学浅谈了一些具体做法。
关键词:数控车工、教学方法、教学效果
随着新型工业化的发展,数控加工技术在机械制造业中已广泛使用,数控专业人才是国家紧缺型人才,目前全国数控专业人才仍有60多万个空缺岗位,月薪都在6000多元以上,数控技能全面的人才年薪达20万元,由此,各地中职学校都在新办数控专业,数控车工技术作为一门独立的新的学科走进了中职学校的课堂。然而目前一些中职学校在数控专业的教学方面存在着数控设备数量偏少,生源素质良莠不齐,师资力量薄弱等问题。下面就如何根据中职学校学生的特点与本校具体情况,搞好该专业中的《数控车床编程与操作》课程的教学,激发学生的学习积极性与主动性,培养学生创造能力和创新与协作精神,以适应社会对数控技能型人才的迫切需求谈一谈本人在教学工作中的几点具体做法。
一、帮助学生树立学好专业技能的信心
目前中职学校的学生大多出生在上世纪90年代以后,多数同学个性较强,缺乏吃苦耐劳的品格。有的同学文化基础较差,怕向老师提问题。原因多是怕提出的问题太简单让人笑话,更怕老师不耐烦说自己笨。所以做为教师具有诲人不倦的耐心,关心和帮助学生树立信心十分重要。我在教学中常常注意活跃课堂气氛,搞好和同学的关系并经常鼓励他们,并且还时常注意对学生的敬业精神、创造能力及创新精神等综合职业素质的培养。我常告诫学生“做任何事情有信心不一定能成功,但没有信心一定要失败!”、“知识改变命运,学习成就未来!”,以此来激发他们的学习信心和勇气。
二、补差补缺,逐步提高学生知识水平
数控专业要求学生有一定的数学基础知识,如三角函数、平面几何等,以利于编程时的节点计算等。但是,中职学校招收的学生大多数文化基础差,有的初中和小学的知识都没弄清楚,数学基础也比较差,面对着这些学生,我经常深入学生中为他们补课,以达到补差补缺,逐步提高的目的。
三、精心设计教学内容,改进教学方法
数控加工技术中的一些理论十分抽象,多数学生由于受文化程度 的影响理解起来非常困难,因此教师在教学中要精心设计教学内容,改进教学方法,才能提高课堂教学效果;我在教学中结合课程特点,采用任务驱动法来组织教学做过如下设计: 任务项目课题:轴类零件的加工
问题分析:在学习了数控编程的基础理论后,需进一步提高学生的动手技能。为使学生能较快较好的掌握操作技能,按数控车床中级工的标准进行技能训练。由轴类零件图,按要求加工出零件。
任务分析:要完成本次课题,学生需要做完下面几项工作:
一、分析零件的图样
1、看懂零件图
2、精度分析:尺寸精度,形位公差,表面粗糙度
二、加工工艺分析
1、编程原点的确定;
2、制定加工方案及加工路线;
3、工件的定位,装夹与刀具量具的选用;
4、切削用量的选择
(1) 主轴转速 (2) 进给速度
(3) 切削深度(背吃刀量)
5、轮廓基点(节点)的计算;
6、确定加工工艺,填写数控加工工艺卡;
三、编写加工程序及输入程序
四、工件的加工操作
1、装夹工件,装刀、对刀;
2、加工操作:程序检测,处理加工过程中出现的问题;
五、工件的检测及评分
按中级工标准进行自评 相关知识:普车基本理论与普车技能、数控基础理论知识、机械加工工艺学理论知识、制图知识、测量原理。 材料清单:45钢(毛坯料)
刀具:符合要求的数控车刀、外圆粗车刀、三角螺纹刀、切断刀、外圆精车刀。
量具:千分尺、游标卡尺、半径规等。 实施过程: 第一阶段:活动开始
讨论分析零件图,提出任务要求:
1、学生分成6人一组
2、判断工作表面,精度要求最高表面,看懂零件图
3、每一小组按要求加工出零件 第二阶段:项目活动开展
1、每一小组按要求编写工艺卡和编写零件程序
2、操作机床加工工件,生产出合格零件
3、自我检测评分
4、各小组介绍自己的加工过程,展示成果
5、回答其他小组提问 第三阶段:总结
学生根据加工的零件,总结由图纸到零件的整个顺序
通过这样精心设计教学内容,采用合理的教学方法,大大提升了学生的学习兴趣以及学生参与的主动性、积极性、收到了良好的教学效果。
四、贴近生活,引入形象生动的实例来提升学生学习兴趣
在项目引入的教学环节中教师应在课前进行认真思考选择合理的项目。项目的内容应尽可能选择日常生活中常见的,并且在教学过程中能够完成的零部件。如果无法找到,教师可自行设计比较合适的项目。项目设置中也可适当增加可以提升学生学习兴趣的项目。例如:我在教学中以酒杯的制作为例介绍圆弧的编程加工过程。
我在教学过程中利用问题的设置引出本次课完成的项目。以生活中一些有趣味的东西,可以使学生了解相关知识,又能提高上课积极性。
五、运用灵活的教学手段获得良好教学效果
为了提高教学效果,我根据学校具体情况在教学中打破传统教学模式,灵活运用多种教学手段将教学环境突破到课堂、仿真实验室和实训车间三个场所。首先,在课堂上进行必要的编程理论讲解,并多举些典型实例让学生反复去练习和体会。其次,在仿真实验室利用数控仿真软件对学生进行系统的编程与操作仿真训练。这一阶段一般为四至五周的时间,应使所有同学都能够利用仿真软件加工出中等复杂程度的零件。最后,深入实训车间,指导学生由易到难的去加工四至五个典型零件。教学中我还采用多媒体等现代教学手段让学生看加工视频录像,带领学生到车间实际参观,指导学生将所得的感性认识上升为理性认识,激发和增强了学生的学习兴趣,获得良好的教学效果。
总之,在教学过程中,我们教师要结合中职学生的需要,采用多种灵活的教学手段,有效地利用学校的教学条件和网络资源以及社会资源来开展教学,从而提高学生的学习兴趣,培养学生数控编程与操作能力,为学生今后发展打下基础。
推荐第8篇:数控编程论文
数 控 编 程 实习报 告
分院:机电分院 班级:机制4班 姓名:宣
科 学号:20130410220403 日期:2016.12.21
数控编程是数控加工准备阶段的主要内容之一,通常包括分析零件图样,确定加工工艺过程;计算走刀轨迹,得出刀位数据;编写数控加工程序;制作控制介质;校对程序及首件试切。有手工编程和自动编程两种方法。总之,它是从零件图纸到获得数控加工程序的全过程。
本学期我分院布置了数控编程的实习任务为期2个周期共计2个课时,虽然时间短但是这次实习收益颇多。
每期的课堂讲座先是在机房进行理论学习然后下基地进行实践操作。
手工编程是指编程的各个阶段均由人工完成。利用一般的计算工具,通过各种三角函数计算方式,人工进行刀具轨迹的运算,并进行指令编制。这种方式比较简单,很容易掌握,适应性较大。使用于非模具加工的零件。
编程步骤
人工完成零件加工的数控工艺 分析零件图纸 制定工艺决策 确定加工路线 选择工艺参数 计算刀位轨迹坐标数据 编写数控加工程序单 验证程序 手工编程 刀轨仿真
优点
主要用于点位加工(如钻、铰孔)或几何形状简单(如平面、方形槽)零件的加工,计算量小,程序段数有限,编程直观易于实现的情况等。
缺点
对于具有空间自由曲面、复杂型腔的零件,刀具轨迹数据计算相当繁琐,工作量大,极易出错,且很难校对,有些甚至根本无法完成。
第 2 页 自动编程
定义
对于几何形状复杂的零件需借助计算机使用规定的数控语言编写零件源程序,经过处理后生成加工程序,称为自动编程。
随着数控技术的发展,先进的数控系统不仅向用户编程提供了一般的准备功能和辅助功能,而且为编程提供了扩展数控功能的手段。FANUC6M数控系统的参数编程,应用灵活,形式自由,具备计算机高级语言的表达式、逻辑运算及类似的程序流程,使加工程序简练易懂,实现普通编程难以实现的功能。
数控编程同计算机编程一样也有自己的"语言",但有一点不同的是,现在电脑发展到了以微软的Windows为绝对优势占领全球市场.数控机床就不同了,它还没发展到那种相互通用的程度,也就是说,它们在硬件上的差距造就了它们的数控系统一时还不能达到相互兼容.所以,当我要对一个毛坯进行加工时,首先要以我们已经拥有的数控机床采用的是什么型号的系统.
①通过这次实习我们了解了现代数控机床的生产方式和工艺过程。熟悉了一些材料的成形方法和主要机械加工方法及其所用主要设备的工作原理和典型结构、工夹量具的使用以及安全操作技术。了解了数控机床方面的知识和新工艺、新技术、新设备在机床生产上的应用。
②在数控机床的生产装配以及调试上,具有初步的独立操作技能。
③在了解、熟悉和掌握一定的数控机床的基础知识和操作技能过程中,培养、提高和加强了我的动手能力、创新意识和创新能力。
④这次实习,让我们明白做事要认真小心细致,不得有半点马虎。同时也培养了我们坚强不屈的本质,不到最后一秒决不放弃的毅力! ⑤培养和锻炼了劳动观点、质量和经济观念,强化遵守劳动纪律、遵守安全技术规则和爱护国家财产的自觉性,提高了我们的整体综合素质数控编程实习心得体会
第 3 页
推荐第9篇:大专数控论文
数控编程与刀具选用
摘要:装备工业的技术水平和现代化程度决定着整个国民经济的水平和现代化程度,数控技术及装备是发展新兴高新技术产业和尖端工业的使能技术和最基本的装备。制造技术和装备则是人类生产活动的最基本的生产资料,而数控技术又是当今先进制造技术和装备最核心的技术。经过数十年的努力,伴随着电子技术及计算机技术的发展,数控机床不断的更新换代,在品种上所有的通用的机床除了数控化外,还有数控成型类机床,特种加工类机床及快速成型机床。在此,所谓数控机床是数字控制机床的简称,亦称NC机床,是为了满足单件、小批、多品种自动化生产的需要而研制的一种灵活的、通用的能够适应产品频繁变化的柔性自动化机床,具有适应性强、加工精度高、加工质量稳定和生产效率高的优点。它综合应用了电子计算机、自动控制、伺服驱动、精密测量和新型机械结构等多方面的技术成果。为此,数控编程是目前数控系统中最能明显发挥效益的环节之一,其在实现设计加工自动化、正确选用刀具原则,提高加工精度和加工质量、缩短产品研制周期等方面发挥着重要作用。在诸如航空工业、汽车工业等领域有着大量的应用。由于生产实际的强烈需求,国内企业外都对数控编程技术进行了广泛的研究,并取得了丰硕成果,
关键词:数控编程,刀具选用。
1.数控编程与其发展
数控编程是目前CAD/CAPP/CAM系统中最能够发挥重要作用,减少了不必要的步骤,提高生产效率。下面就对数控编程及其发展作一些介绍:
1.1数控编程的基本概念。
数控编程是从零件图纸到获得数控加工程序的全过程。它的主要任务是计算加工走刀中的刀位点t简称CL点)。刀位点一般选为刀具轴线与刀具表面的交点。
1.2数控编程技术的发展概况
随着计算机技术的高速发展,传统的制造业开始了根本性的变革,各工业发达国家投入巨资,对现在制造业进行研究和开发,提出了全新的制造模式。在现代制造系统中,数控技术是关键技术,它集微电子,计算机,信息处理,自动检测与控制等高新技术于一体,具有高精度,高效率,柔性自动化等特点,对制造业发生根本性的变革,由专用型封闭式开环控制模式向通用型开放式实时动态全闭环控制模式发展。在集成化基础上,实现了超薄性,超小型化;在智能化基础上,实现了高速、高精、高效控制,加工过程中可以制动修正、调节与补偿各项参数,实现了在线诊断和智能化故障处理。
大力发展以数控技术为核心的先进制造技术已成为我们国家加速经济发展、提高生产水平,在数控加工中的程序编制问题上, APT语言编制数控程序经过几十年代发展,先后形成了APTII、APTIII、APT(算法改进,增加多坐标曲面加工编程功能) APT-AC(增加切削数据库管理系统)和APT-/SS (增加雕塑曲面加工编程功能)等先进版。
采用APT语言编制数控程序具有程序简炼,走刀控制灵活等优点,使数控加工编程从面向机床指令上升到面向几何元素。APT仍有许多不足之处:采用语言定义零件几何形状,难以描述复杂的几何形状,缺乏几何直观性;缺少对零件形状、刀具运动轨迹的直观图形显示和刀具轨迹的验证手段;难以全部和CAD数据库和CAPP系统有效连接;不容易作到高度的自动化,集成化。
针对APT语言的缺点,利用三维设计、分析、NC加工一体化的功能,开发出CATIA系统,随后很快出现了象EUCLID,UGII,INTERGRAPH,Pro/Engineering,MasterCAM及NPU/GNCP等系统,这些系统都有自己的特色,并且能够有效的解决了几何造型、零件
几何形状的显示,交互设计、修改及刀具轨迹生成,走刀过程的仿真显示、验证等问题,推动了CAD和CAM向一体化方向发展,逐步形成了计算机集成制造系统(CIMS)及并行工程(CE)的概念。目前,为了适应CIMS及CE发展的需要,数控编程系统向集成化和智能化,网络化等数控系统的发展趋势。
在集成化方面,以开发符合STEP标准的参数化特征造型系统为主,进行了大量卓有成效的工作,是国内外开发的热点;在智能化方面上,为了追求加工效率和加工质量方面的智能化,为了提高驱动性能及使用连接方便的智能化,为了能够智能诊断和智能监控的智能化,是我们往后的数控技术的发展艰巨任务,现在待我们去努力开发的开式冲压滚针轴承 , 止推轴承座,液压杆端轴承,
止推轴承座 , 球面滚子轴承, 滚针和保持架组件。网络化是近些年来数控机床发展的新的亮点,它的作用将极大地满足生产线、制造系统、制造企业对信息集成的需求,也是实现新的制造模式如敏捷制造、虚拟企业、全球制造的基础单元。 我相信会有这一天到来。
2.刀具的选用:
1.2数控加工常用刀具的种类:
数控刀具选择和切削用量的确定是数控加工工艺的主要内容,他不仅影响数控加工效率,而且直接影响加工质量,cad、cam技术的发展,使得在数控加工中直接利用cad的设计数据进行加工。因此,数控的刀具选择与切削用量在人机交互状态下完成,同时要求编程人员必须掌握刀具选择和切削用量的确定的基本原则来正确选择刀刃具及切削用量。选用刀具时,要使刀具的尺寸与被加工工件表面尺寸相适应。生产中,加工凸台,凹槽时,选用高速钢立铣刀,加工毛坯表面或孔时,选用硬质合铣刀,加工平面零件周边轮廓是,选用立铣刀,对一些变斜角轮廓外形加工,常用球刀,环形刀,锥刀。 1.3数控刀具的选择
数控车床刀具的选择及切削用量的确定
一.机床车刀分为尖形刀,圆形刀,成型刀
二.主轴转速的确定:根据已选定的背吃刀量,进给量及刀具耐用度来选择切削速度。 三.进给量V的确定:V的大小直接影响粗糙度的值和车削效率,因此,在保证表面质量的前提下,选择较高的进给速度。
四.刀具材料性能:a。硬度和耐磨性,b。强度和韧性c。耐热性与化学稳定性
五.常用刀具材料:a高速钢b。硬质合金c。其他材料(涂层刀片,陶瓷,金刚石,立方氮化硼) 切削用量的选择
一.粗车时,首先选择最大的背吃刀量,其次,选用进给量。最后选定合理的切削速度,增大背吃刀量,减少走刀次数,增大进给量,有利于断屑。
二.精车时,由于精度和表面粗糙要求高,加工余量不大且均匀,因此应选用较小(不太小)的背吃刀量和进给量,并选用切削性能高的刀具材料和合理的参数,以尽可能提高切削速度。
数控铣加工中刀具选用及切削用量
一.刀具结构:a整体性b。镶嵌式,c。特殊型式 二.刀具材料:a高速钢。B硬质合金c。金刚石
三.刀具种类:平端立铣刀,圆角立铣刀,球头刀和锥度铣刀 四.刀具特点:
A.刚性好,精度高,抗振好 B,互换性好,便于快速换刀
C.系列化,标准化,利于编程刀具管理 D.寿命高,切削性能稳定,可靠, 切削用量的确定
一.影响因素:a,机床,b,刀具,c工件,c,冷却液 二.选择原则:先背吃刀量,次进给量,后切削速度
此外,如果在进行模具加工时,由于球刀的端部切削速度为零,因此,为保证加工精度,则球刀常用于曲面的精加工,而平头刀具在表面加工质量和切削效率方面都优于球刀,所以在不过切的前提下,无论曲面加工或平面加工一般选用平头刀。另外,在市场上,俗话说:便宜货不是好货,选择好的刀等于选择成本高,但在加工质量和效率上看,则可以降低整个加工成本,这何乐而不为之.。
CNC加工中心刀具选择及切削用量的确定
在加工中心上,各种刀具分别装在刀库上,按程序规定随便选刀和换刀,因此,采用标准刀柄,以便使钻镗铣等工序用标准的刀具迅速,准确的装到机床主轴或刀库上,编程人员了解机床所用刀柄的结构尺寸,调整方法及调整范围,以便在编程时确定刀具的径向和轴向尺寸。
a, 总原则:安装调整方便,刚性好,耐用和精度高。在满足加工要求时的前提下,尽量选择较短的刀柄,以提高刀具加工刚性
B,遵循基本原则:1粗精加工的刀具应分开使用,即使相同尺寸规格刀具。2先铣后钻3,先进行曲面精加工,后进二次轮廓精加工4尽量减少刀具数量5一把刀具装上去,应完成其能进行的加工
切削用量的确定 一.切削考虑因素
切削速度V,提高V也是提高生产率的措施,但V与刀耐用度关系比较密切,随V的增大,刀的耐用度下降,故V的选择取决于刀耐用度
进给速度Vf,Vf应根据零件的加工精度和表面粗糙度要求以及刀具和工件材料来选择,加工表面粗糙度要求低时,VF可调大些,在加工过程中,VF通过员工调整,但最大进给速度受到系统性能限制 主轴转速,一般取决于V 切削深度,为保证零件的加工精度和表面粗糙度,应留一定余量进行精加工。
随着数控机床在生产实际中广泛应用,量化生产线的形成,数控编程已成为数控加工中的关键问题之一,在数控程序的编制过程中要在人机交换状态下选择刀具和确定切削用量,因此,编程人员必须熟悉选择方法和切削用量的原则,从而保证零件的加工质量和加工效率,充分发挥数控优点,提高企业经济效益和生产水平。
推荐第10篇:数控技师技师论文
江西工贸高级技工学校
数控技师论文
题 目:
数控车床的基本应用
系 (院):
机电技术系
专 业:
数控技术应用
年 级:
08数控技师班
姓 名:
张 永 东
学 号:
2008020103041
指导教师:
周伟 董跃平
二零一一年五月
摘 要
世界制造业转移,中国正在逐步成为世界加工厂。美国、德国、韩国等国家已经进入工业化发展的高技术密集时代与微电子时代,钢铁、机械、化工等重工业正逐渐向发展中国家转移。我国目前经济发展已经过了发展初期,正处于重化工业发展中期。
未来10年将是中国机械行业发展最佳时期。美国、德国的重化工业发展期延续了18年以上,美国、德国、韩国四国重化工业发展期平均延续了12年,我们估计中国的重化工业发展期将至少延续10年,直到2015年。因此,在未来10年中,随着中国重化工业进程的推进,中国企业规模、产品技术、质量等都将得到大幅提升,国产机械产品国际竞争力增强,逐步替代进口,并加速出口。目前,机械行业中部分子行业如船舶、铁路、集装箱及集装箱起重机制造等已经受益于国际间的产业转移,并将持续受益;电站设备、工程机械、床等将受益于产业转移,加快出口进程
关键词 : 数控 工业化发展 刀具 机床
Abstract Transfer of world manufacturing, China is gradually becoming the world's factory.United States, Germany, Korea and other countries have already entered the era of industrialization and the development of microelectronics era of high-tech intensive, steel, machinery, chemicals and other heavy industry is gradually transferred to developing countries.China's current economic development has been the early stages of development, the development of heavy industry is in the middle.
The next 10 years will be the best period of China's machinery industry.United States, the development of heavy chemical industry in Germany more than 18 years of continuity, the United States, Germany, South Korea four countries on average continue the development of heavy chemical industry for 12 years, we estimate that the development of China's heavy chemical industry will continue through at least 10 years, until 2015 .Therefore, in the next 10 years, with China to promote the proce of heavy and chemical industries, the Chinese firm size, product technology, quality and so will be significantly improved international competitivene of domestic machinery products increased, and gradually replace imports and exports accelerate.Currently, the central molecular machinery industry sectors such as shipbuilding, railway, container and container crane manufacturer, have already benefited from the international industrial transfer, and will continue to benefit; power plant equipment, engineering machinery, beds, etc.will benefit from the transfer of industries, accelerate the export proceKeywords: CNC machine tool industrial development
目 录
第一章 数控机床的产生......................................................................................................5 第二章 数控机床的发展......................................................................................................6 2.1 数控系统的发展......................................................................................................6 2.2 机床的发展趋势......................................................................................................6 第三章 数控机床的分类......................................................................................................7 3.1 按加工工艺方法分类..............................................................................................7 3.2金属切削类数控机床........................................................................................7 3.3特种加工类数控机床........................................................................................7 3.4板材加工类数控机床.......................................................................................8 4.1.合理选择切削用量.................................................................................................8 4.2.合理选择刀具.........................................................................................................8 4.3.合理选择夹具.........................................................................................................9 4.4.确定加工路线.........................................................................................................9 4.5.加工路线与加工余量的联系.................................................................................9 4.6.夹具安装要点.........................................................................................................9 第五章 程序首句妙用与控制尺寸精度的技巧................................................................10 5.1、程序首句妙用G00的技巧.................................................................................10 5.
2、控制尺寸精度的技巧...........................................................................................11 5.2.1.修改刀补值保证尺寸精度.......................................................................11 5.2.2.半精加工消除丝杆间隙影响保证尺寸精度...........................................11 5.2.3.程序编制保证尺寸精度...........................................................................11 5.2.4.修改程序和刀补控制尺寸......................................................................12 第六章
数控技术..............................................................................................................13 6.1数控机床运动坐标的电气控制.............................................................................13 参考文献.......................................................................................................................15
第一章 数控机床的产生
在机械制造工业中并不是所有的产品零件都具有很大的批量,单件与小批量生产的零件(批量在10~100件)约占机械加工总量的80%以上。尤其是在造船、航天、航空、机床、重型机械以及国防工业更是如此。
为了满足多品种,小批量的自动化生产,迫切需要一种灵活的,通用的,能够适用产品频繁变化的柔性自动化机床。数控机床就是在这样的背景下诞生与发展起来的。它为单件、小批量生产的精密复杂零件提供了自动化的加工手段。
根据国家标准GB/T8129-1997,对机床数字控制的定义:用数字控制的装置(简称数控装置),在运行过程中,不断地引入数字数据,从而对某一生产过程实现自动控制,叫数字控制,简称数控。用计算机控制加工功能,称计算机数控(computerized numerical ,缩写CNC)。
数控机床即使采用了数控技术的机床,或者说装备了数控系统的机床。从应用来说,数控机床就是将加工过程所需的各种操作(如主轴变速、松加工件、进刀与退刀、开车与停车、选择刀具、供给切削液等)和步骤,以及刀具与工件之间的相对位移量都用数字化的代码来表示,通过控制介质将数字信息送入专用的或通用的计算机,计算机对输入的信息进行处理与运算,发出各种指令来控制机床的伺服系统或其他执行元件,是机床自动加工出所需要的零件。
第二章 数控机床的发展
2.1 数控系统的发展
从1952年第一台数控机床问世后,数控系统已经先后经历了两个阶段和六代的发展,其六代是指电子管、晶体管、集成电路、小型计算机、微处理器和基于工控PC机的通用CNC系统。其中前三代为第一阶段,称作为硬件连接数控,简称NC系统;后三代为第二阶段,乘坐计算机软件数控,简称CNC系统。
2.2 机床的发展趋势
数控机床总的发展趋势是工序集中、高速、高效、高精度以及方便使用、提高可靠性等。
(1)工序集中 20世纪50年代末期,在一般数控机床的基础上开发了数控加工中心,即自备刀具库的自动换刀数控机床。在加工中心机床上,工件一次装夹后,机床的机械手可以自动更换刀具,连续的对工件进行多种工序加工。
目前,加工中心机床的刀具库容量可达到100多把刀具,自动换刀装置的换刀时间仅需0.5~2秒。加工中心机床使工序集中在一台机床上完成,减少了由于工序分散,工件多次安装引起的定位误差,提高了加工精度,同时也减少了机床的台数与占地面积,压缩了半成品的库存量,减少了工序间的辅助时间,有效的提高了数控机床的生产效率和数控加工的经济效益。
(2)高速、高效、高精度
高速、高效、高精度是机械加工的目标,数控机床因其价格昂贵,在上述三方面的发展也就更为突出。
(3)方便使用
数控机床制造厂把建立友好的人机界面、提高数控机床的可靠性作为提高竞争能力的主要方面。
1)加工编程方便
手工编程和自动编程已经使用了几十年,有了长足的发展,在手工编程方面,开发了多种加工循环、参数编程和除直线、圆弧以外的各种插补功能,CAD/CAM的研究发展,从技术上来讲可以替代手工编程。但是一套适用的CAD/CAM软件加上计算机硬件,投资较大,学习、掌握时间较长,对大多数的简单工件很不经济。
2)使用方法
数控机床普遍采用彩色CRT进行人机对话、图形显示和图形模拟的。有的数控机床将采用说明书、编程指南、润滑指南等存入系统共使用者调阅。
第三章 数控机床的分类
3.1 按加工工艺方法分类
3.2金属切削类数控机床
与传统的车、铣、钻、磨、齿轮加工相对应的数控机床有数控车床、数控铣床、数控钻床、数控磨床、数控齿轮加工机床等。尽管这些数控机床在加工工艺方法上存在很大差别,具体的控制方式也各不相同,但机床的动作和运动都是数字化控制的,具有较高的生产率和自动化程度。
3.3特种加工类数控机床
除了切削加工数控机床以外,数控技术也大量用于数控电火花线切割机床、数控电火花成型机床、数控等离子弧切割机床、数控火焰切割机床以及数控激光加工机床等。
3.4板材加工类数控机床
常见的应用于金属板材加工的数控机床有数控压力机、数控剪板机和数控折弯机等。近年来,其它机械设备中也大量采用了数控技术,如数控多坐标测量机、自动绘图机及工业机器人等。
第四章 数控车的工艺与工装削
数控车床加工工艺与普通车床的加工工艺类似,但由于数控车床是一次装夹,连续自动加工完成所有车削工序,因而应注意以下几个方面。
4.1.合理选择切削用量
对于高效率的金属切削加工来说,被加工材料、切削工具、切削条件是三大要素。这些决定着加工时间、刀具寿命和加工质量。经济有效的加工方式必然是合理的选择了切削条件。
切削条件的三要素:切削速度、进给量和切深直接引起刀具的损伤。伴随着切削速度的提高,刀尖温度会上升,会产生机械的、化学的、热的磨损。切削速度提高20%,刀具寿命会减少1/2。
4.2.合理选择刀具
1) 粗车时,要选强度高、耐用度好的刀具,以便满足粗车时大背吃刀量、大进给量的要求。
2) 精车时,要选精度高、耐用度好的刀具,以保证加工精度的要求。 3) 为减少换刀时间和方便对刀,应尽量采用机夹刀和机夹刀片。
4.3.合理选择夹具
1) 尽量选用通用夹具装夹工件,避免采用专用夹具; 2) 零件定位基准重合,以减少定位误差。
4.4.确定加工路线
加工路线是指数控机床加工过程中,刀具相对零件的运动轨迹和方向。 1) 应能保证加工精度和表面粗糙要求;
2) 应尽量缩短加工路线,减少刀具空行程时间。
4.5.加工路线与加工余量的联系
目前,在数控车床还未达到普及使用的条件下,一般应把毛坯上过多的余量,特别是含有锻、铸硬皮层的余量安排在普通车床上加工。如必须用数控车床加工时,则需注意程序的灵活安排。
4.6.夹具安装要点
目前液压卡盘和液压夹紧油缸的连接是靠拉杆实现的,液压卡盘夹紧要点如下:首先用搬手卸下液压油缸上的螺帽,卸下拉管,并从主轴后端抽出,再用搬手卸下卡盘固定螺钉,即可卸下卡盘。
第五章 程序首句妙用与控制尺寸精度的技巧
5.1、程序首句妙用G00的技巧
目前我们所接触到的教科书及数控车削方面的技术书籍,程序首句均为建立工件坐标系,即以G50 Xα Zβ作为程序首句。根据该指令,可设定一个坐标系,使刀具的某一点在此坐标系中的坐标值为(Xα Zβ)(本文工件坐标系原点均设定在工件右端面)。采用这种方法编写程序,对刀后,必须将刀移动到G50设定的既定位置方能进行加工,找准该位置的过程如下。
1.对刀后,装夹好工件毛坯;
2.主轴正转,手轮基准刀平工件右端面A;
3.Z轴不动,沿X轴释放刀具至C点,输入G50 Z0,电脑记忆该点; 4.程序录入方式,输入G01 W-8 F50,将工件车削出一台阶;
5.X轴不动,沿Z轴释放刀具至C点,停车测量车削出的工件台阶直径γ,输入G50 Xγ,电脑记忆该点;
6.程序录入方式下,输入G00 Xα Zβ,刀具运行至编程指定的程序原点,再输入G50 Xα Zβ,电脑记忆该程序原点。
。上述步骤中,步骤6即刀具定位在XαZβ处至关重要,否则,工件坐标系就会被修改,无法正常加工工件。有过加工经验的人都知道,上述将刀具定位到XαZβ处的过程繁琐,一旦出现意外,X或Z轴无伺服,跟踪出错,断电等情况发生,系统只能重启,重启后系统失去对G50设定的工件坐标值的记忆,“复位、回零运行”不再起作用,需重新将刀具运行至XαZβ位置并重设G50。如果是批量生产,加工完一件后,回G50起点继续加工下一件,在操作过程中稍有失误,就可能修改工件坐标系。鉴于上述程序首句使用G50建立工件坐标系的种种弊端,笔者想办法将工件坐标系固定在机床上,将程序首句G50 XαZβ改为G00 Xα Zβ后,问题迎刃而解。其操作过程只需采用上述找G50过程的前五步,即完成步骤
1、
2、
3、
4、5后,将刀具运行至安全位置,调出程序,按自动运行即可。即使发生断电等意外情况,重启系统后,在编辑方式下将光标移至能安全加工又不影响工件加工进程的程序段,按自动运行方式继续加工即可。上述程序首句用 G00代替G50的实质是将工件坐标系固定在机床上,不再囿于G50 Xα Zβ程序原点的限制,不改变工件坐标系,操作简单,可靠性强,收到了意想不到的效果。中国金属加工在线
5.2、控制尺寸精度的技巧 5.2.1.修改刀补值保证尺寸精度
由于第一次对刀误差或者其他原因造成工件误差超出工件公差,不能满足加工要求时,可通过修改刀补使工件达到要求尺寸,保证径向尺寸方法如下: a.绝对坐标输入法
根据“大减小,小加大”的原则,在刀补001~004处修改。如用2号切断刀切槽时工件尺寸大了0.1mm,而002处刀补显示是X3.8,则可输入X3.7,减少2号刀补。 b.相对坐标法
如上例,002刀补处输入U-0.1,亦可收到同样的效果。
同理,对于轴向尺寸的控制亦如此类推。如用1号外圆刀加工某处轴段,尺寸长了0.1mm,可在001刀补处输入W0.1。
5.2.2.半精加工消除丝杆间隙影响保证尺寸精度
对于大部分数控车床来说,使用较长时间后,由于丝杆间隙的影响,加工出的工件尺寸经常出现不稳定的现象。这时,我们可在粗加工之后,进行一次半精加工消除丝杆间隙的影响。如用1号刀G71粗加工外圆之后,可在001刀补处输入U0.3,调用G70精车一次,停车测量后,再在001刀补处输入U-0.3,再次调用G70精车一次。经过此番半精车,消除了丝杆间隙的影响,保证了尺寸精度的稳定。
5.2.3.程序编制保证尺寸精度
a.绝对编程保证尺寸精度
编程有绝对编程和相对编程。相对编程是指在加工轮廓曲线上,各线段的终点位置以该线段起点为坐标原点而确定的坐标系。也就是说,相对编程的坐标原点经常在变换,连续位移时必然产生累积误差,绝对编程是在加工的全过程中,均有相对统一的基准点,即坐标原点,故累积误差较相对编程小。数控车削工件时,工件径向尺寸的精度一般比轴向尺寸精度高,故在编写程序时,径向尺寸最好采用绝对编程,考虑到加工及编写程序的方便,轴向尺寸常采用相对编程,但对于重要的轴向尺寸,最好采用绝对编程。
b.数值换算保证尺寸精度
很多情况下,图样上的尺寸基准与编程所需的尺寸基准不一致,故应先将图样上的基准尺寸换算为编程坐标系中的尺寸。如图2b中,除尺寸13.06mm外,其余均属直接按图2a标注尺寸经换算后而得到的编程尺寸。其中, φ29.95mm、φ16mm及60.07mm三个尺寸为分别取两极限尺寸平均值后得到的编程尺寸。
5.2.4.修改程序和刀补控制尺寸
数控加工中,我们经常碰到这样一种现象:程序自动运行后,停车测量,发现工件尺寸达不到要求,尺寸变化无规律。如用1号外圆刀加工图3所示工件,经粗加工和半精加工后停车测量,各轴段径向尺寸如下:φ30.06mm、φ23.03mm及φ16.02mm。对此,笔者采用修改程序和刀补的方法进行补救,方法如下:
a.修改程序
原程序中的X30不变,X23改为X23.03,X16改为X16.04,这样一来,各轴段均有超出名义尺寸的统一公差0.06mm;
b.改刀补
在1号刀刀补001处输入U-0.06。
经过上述程序和刀补双管齐下的修改后,再调用精车程序,工件尺寸一般都能得到有效的保证。
数控车削加工是基于数控程序的自动化加工方式,实际加工中,操作者只有具备较强的程序指令运用能力和丰富的实践技能,方能编制出高质量的加工程序,加工出高质量的工件。
第六章
数控技术
6.1数控机床运动坐标的电气控制
数控机床一个运动坐标的电气控制由电流(转矩)控制环、速度控制环和位置控制环串联组成 。
(1)电流环是为伺服电机提供转矩的电路。一般情况下它与电动机的匹配调节已由制造者作好了或者指定了相应的匹配参数,其反馈信号也在伺服系统内联接完成,因此不需接线与调整。
(2)速度环是控制电动机转速亦即坐标轴运行速度的电路。速度调节器是比例积分(PI)调节器,其P、I调整值完全取决于所驱动坐标轴的负载大小和机械传动系统(导轨、传动机构)的传动刚度与传动间隙等机械特性,一旦这些特性发生明显变化时,首先需要对机械传动系统进行修复工作,然后重新调整速度环PI调节器。
速度环的最佳调节是在位置环开环的条件下才能完成的,这对于水平运动的坐标轴和转动坐标轴较容易进行,而对于垂向运动坐标轴则位置开环时会自动下落而发生危险,可以采取先摘下电动机空载调整,然后再装好电动机与位置环一起调整或者直接带位置环一起调整,这时需要有一定的经验和细心。 速度环的反馈环节见前面“速度测量”一节。
(3)位置环是控制各坐标轴按指令位置精确定位的控制环节。位置环将最终影响坐标轴的位置精度及工作精度。这其中有两方面的工作:
一是位置测量元件的精度与CNC系统脉冲当量的匹配问题。测量元件单位移动距离发出的脉
冲数目经过外部倍频电路和/或CNC内部倍频系数的倍频后要与数控系统规定的分辨率相符。例如位置测量元件10脉冲/mm,数控系统分辨率即脉冲当量为0.001mm,则测量元件送出的脉冲必须经过100倍频方可匹配。
二是位置环增益系数Kv值的正确设定与调节。通常Kv值是作为机床数据设置的,数控系统中对各个坐标轴分别指定了Kv值的设置地址和数值单位。在速度环最佳化调节后Kv值的设定则成为反映机床性能好坏、影响最终精度的重要因素。Kv值是机床运动坐标自身性能优劣的直接表现而并非可以任意放大。关于Kv值的设置要注意两个问题,首先要满足下列公式: Kv=v/Δ
式中v——坐标运行速度,m/min Δ——跟踪误差,mm
注意,不同的数控系统采用的单位可能不同,设置时要注意数控系统规定的单位。例如,坐标运行速度的单位是m/min,则Kv值单位为m/(mm·min),若v的单位为mm/s,则Kv的单位应为mm/(mm·s)。
其次要满足各联动坐标轴的Kv值必须相同,以保证合成运动时的精度。通常是以Kv值最低的坐标轴为准。
位置反馈(参见上节“位置测量”)有三种情况:一种是没有位置测量元件,为位置开环控制即无位置反馈,步进电机驱动一般即为开环;一种是半闭环控制,即位置测量元件不在坐标轴最终运动部件上,也就是说还有部分传动环节在位置闭环控制之外,这种情况要求环外传动部分应有相当的传动刚度和传动精度,加入反向间隙补偿和螺距误差补偿之后,可以得到很高的位置控制精度;第三种是全闭环控制,即位置测量元件安装在坐标轴的最终运动部件上,理论上这种控制的位置精度情况最好,但是它对整个机械传动系统的要求更高而不是低,如若不然,则会严重影响两坐标的动态精度,而使得机床只能在降低速度环和位置精度的情况下工作。影响全闭环控制精度的另一个重要问题是测量元件的精确安装问题,千万不可轻视。
(4)前馈控制与反馈相反,它是将指令值取出部分预加到后面的调节电路,其主要作用是减小跟踪误差以提高动态响应特性从而提高位置控制精度。因为多数机床没有设此功能,故本文不详述,只是要注意,前馈的加入必须是在上述三个控制环均最佳调试完毕后方可进行。
参考文献
1.《数控加工工艺学》
2.黄勇 陈子辰 浙江学 《机床数控系统的发展趋势 》 3.作者:李佳 《数控机床及应用》
4.2001年第30卷第1期 《机械设计与制造工程》 5.2005年第12期 《机电新产品导报》 6.2007年第34卷第8期 《机械》
7.2007年第4期 《世界制造技术与装备市场》 3.作者:李佳应用》
8.2001年第30卷第1期 《机械设计与制造工程》 9.2005年第12期 《机电新产品导报》 10.2007年第34卷第8期 《机械》
11.2007年第4期 《世界制造技术与装备市场》3.作者:李佳 应用》
12.2001年第30卷第1期 《机械设计与制造工程》 13.2005年第12期 《机电新产品导报》 14.2007年第34卷第8期 《机械》 15.2007年第4期 《世界制造技术与装备市场》
《数控机床及《数控机床及致
谢
时光匆匆如流水,转眼便是大学毕业时节,春梦秋云,聚散真容易。在这个美好的季节里,我在电脑上敲出了最后一个字,心中涌现的不是想象已久的欢欣,却是难以言喻的失落。是的,随着论文的终结,意味着我生命中最纯美的学生时代即将结束,尽管百般不舍,这一天终究会在熙熙攘攘的喧嚣中决绝的来临。
三年寒窗,所收获的不仅仅是愈加丰厚的知识,更重要的是在阅读、实践中所培养的思维方式、表达能力和广阔视野。很庆幸这些年来我遇到了许多恩师益友,无论在学习上、生活上还是工作上都给予了我无私的帮助和热心的照顾,让我在诸多方面都有所成长。感恩之情难以用语言量度,谨以最朴实的话语致以最崇高的敬意。
还要感谢我的父母,给予我生命并竭尽全力给予了我接受教育的机会,养育之恩没齿难忘; 他们不仅培养了我对中国传统文化的浓厚的兴趣,让我在漫长的人生旅途中使心灵有了虔敬的归依,而且也为我能够顺利的完成毕业论文提供了巨大的支持与帮助。在未来的日子里,我会更加努力的学习和工作,不辜负父母对我的殷殷期望!我一定会好好孝敬和报答他们!,
还有许多人,也许他们只是我生命中匆匆的过客,但他们对我的支持和帮助依然在我记忆中留底了深刻的印象。在此无法一一罗列,但对他们,我始终心怀感激。最后,我要向在百忙之中抽时间对本文进行审阅、评议和参加本人论文答辩的各位师长表示感谢!
第11篇:数控实习论文
在数控机床上加工零件时,要把零件的全部工艺过程、工艺参数及其他辅导动作,按动作顺序,根据数控机床规定的指令格式编写加工程序,记录于控制介质,然后输入数控装置,从而指挥机床。将这种从零件图样到获得数控机床所需的控制介质的全过程,称为程序编制即数控编程。
为了满足设计、制造,维修和普及的需要,在输入代码、坐标系统,加工指令,辅助功能及程序格式等方面,图标上已经形成了两种通用标准,即国际标准化组织(ISO)标准和美国电子工业学会(EIA)标准。我国机械工业部根据ISO标准制定了JB3050-82,JB3208-83,JB30512-82等国家标准。但是由于各数控机床生产厂家所使用的标准尚未完全统一。其所用的代码、指令及其含义不完全相同,甚至其程序的格式也不一样。 编程的一般步骤
1、分析零件图样和制定工艺过程及工艺路线。
该步骤主要包括:对零件图样要求的形状、尺寸、精度、材料及毛坯形状和热处理方法进行明确加工内容和要求;确定加工方案;选择适合的机床;确定合理的走刀路线及选择合理的切削用量等。在安排工序时,要根据加工特点按照换刀次数减少、空行程路线短及工序集中的原则,尽可能在一次装夹中就能完成所有工序。
2、数值处理
该步骤是根据零件的几何尺寸、加工路线,计算出零件轮廓线上的几何元素的起点终点及圆弧的圆心坐标。如果数控系统无刀具补偿功能,还应该计算刀具运行的中心轨迹。当用直线、圆弧来逼近非圆曲线(如渐开线、空间曲面的程序等)时,应计算曲线上各节点的坐标值。对于列表曲线、空间曲面的程序编制,其数字处理更为复杂,一般需要使用计算机辅助计算,否则难以完成。
3、编写加工程序
该步骤是在完成上述工艺处理及数值计算工作后,按照数控系统规定使用的功能指令代码及程序段格式,逐渐段编写加工程序单。依据编制人员应对数控机床的性能、程序指令及代码非常熟悉,才能编写出正确的加工程序。
4、程序输入
程序的输入可以通过键盘直接将程序输入数控系统,称为MDI方式输入。也可以先制作控制介质上的程序通过计算机通讯接口R232输入数控系统。
5、程序检验
对有图形显示功能的数控机床,可进行图形模拟加工,检查刀具运动轨迹是否正确。对无此功能的数控机床可以进行空运转检验以上方法只能证明运动轨迹的正确性,但不能查出被加工零件的精度。因此,需要对工件进行首件试切,当发现误差时,应分析误差产生的原因,加以修正。
第12篇:数控毕业设计论文
苏州市职业大学
毕 业 设 计 说 明 书
毕业设计题目轴类零件的加工工艺与编程
系 机电工程系
专业班级 数控4班
姓 名 朱 冰
学 号 1013020432
指导教师 李振兴
摘 要
年 月
日
随着科学技术的飞速发展和经济竞争的日趋激烈 产品更新速度越来越快 复杂形状的零件越来越多 精度要求越来越高
多品种、小批量生产的比重明显增加
激烈的市场竞争使产品研制生产周期越来越短
传统的加工设备和制造方法已难以适应这种多样化、柔性化与复杂形状零件的高速高质量加工要求
本课题来源于生产 是对所学知识的应用
它包括了三年所学的全部知识 在数控专业上具有代表性
而且提高了综合运用各方面知识的能力 程序的编制到程序的调试
零件的加工运用到了所学的AutoCAD、CAXA制造工程师软件、数控机床操作、子程序、刀具的选择、零件的工艺分析、数学处理、工艺路线等一系列的内容 这将所学到的理论知识充分运用到了实际加工中 切实做到了理论与实践的有机结合
关键词:数控;加工;工艺;编程
目 录
1引 言 1 1.1数控技术的发展及趋势 1 1.2数控车削加工工艺分析的主要内容 2 2轴类零件的加工工艺设计 3 2.1轴类加工的内容及工艺分析 3 2.1.1轴类零件加工的内容 3 2.1.2轴类零件加工的工艺分析 4 2.2轴类零件工艺路线的拟定 4 2.2.1工艺路线的确定 4 2.2.2辅助工序的安排 6 2.3数控机床及其工艺设备的选择 6 2.3.1数控机床的选择 6 2.3.2检测量具的选择 7 2.4轴类零件切削用量参数的确定 7 2.4.1确定主轴转速 7 2.4.2确定进给速度 8 2.4.3确定背吃刀量 8 2.5拟定数控加工工艺卡 8 2.5.1 数控加工工序 8 2.5.2 数控加工工序表 9 2.6刀具的选择 9 2.6.1刀具 9 2.6.2确定对刀点与换刀点 10 3轴类零件夹具的选用 11 3.1对轴类零件夹具的基本要求 12 3.2.1 夹具的类型 12 3.2.2零件的安装 12 4车削零件数控加工的编程 13 4.1数控坐标系的确定 13 4.2走刀路线的确定 13 4.3程序编制 14 5结 论 21 6致 谢 22 7参 考 文 献 23
1引 言
1.1数控技术的发展及趋势
机床数控系统
即计算机数字控制(CNC)系统是在传统的硬件数控(NC)的基础上发展起来的 它主要由硬件和软件两大部分组成 通过系统控制软件与硬件的配合
完成对进给坐标控制、主轴控制、刀具控制、辅助功能控制等
CNC系统利用计算机来实现零件程序编辑、坐标系偏移、刀具补偿、插补运算、公英制变换、图形显示和固定循环等
使数控机床按照操作设计要求 加工出需要的零件 1908年
穿孔的金属薄片互换式数据载体问世;19世纪末
以纸为数据载体并具有辅助功能的控制系统被发明;1938年 香农在美国麻省理工学院进行了数据快速运算和传输 奠定了现代计算机
包括计算机数字控制系统的基础
数控技术是与机床控制密切结合发展起来的 1952年第一台数控机床问世后
数控系统已经先后经历了两个阶段和六代的发展
其六代是指电子管、晶体管、集成电路、小型计算机、微处理器和基于工控PC机的通用CNC系统
其中前三代为第一阶段 称作为硬件连接数控
简称NC系统;后三代为第二阶段 乘坐计算机软件数控 简称CNC系统
数控加工技术是什么呢?简单的说就是利用数字化控制系统在加工机床上完成整个零件的加工
而且和传统的机械加工手段相比数控加工技术具有以下优点:
①加工效率高
利用数字化的控制手段可以加工复杂的曲面 而加工过程是由计算机控制 所以零件的互换性强 加工的速度快
②加工精度高
同传统的加工设备相比 数控系统优化了传动装置 提高分辨率 减少了人为误差
因此加工的效率可以得到很大的提高
③劳动强度低
由于采用了自动控制方式
也就是说加工的全部过程是由数控系统完成 不象传统加工手段那样烦琐 操作者在数控机床工作时 只需要监视设备的运行状态 所以劳动强度很低
④适应能力强
数控加工系统就象计算机一样 可以通过调整部分参数达到修改或改变其运作方式 因此加工的范围可以得到很大的扩展
从目前世界上数控技术及其装备发展的趋势来看
数控系统正在向电气化、电子化、高速化、精密化等方面高速发展 其主要研究热点有以下几个方面:
①高精高速高效化速度
②柔性化
③多轴化
④软硬件开放化
⑤实时智能化
21世纪的数控装备将是具有一定智能化的系统
智能化的内容包括在数控系统中的各个方面:为追求加工效率和加工质量方面的智能化 如加工过程的自适应控制
工艺参数自动生成;为提高驱动性能及使用连接方便的智能化
如前馈控制、电机参数的自适应运算、自动识别负载自动选定模型、自整定等;简化编程、简化操作方面的智能化
如智能化的自动编程、智能化的人机界面等;还有智能诊断、智能监控方面的内容、方便系统的诊断及维修等
1.2数控车削加工工艺分析的主要内容
①选择适合在数控机床上加工的零件 确定工序内容
②分析被加工零件图样 明确加工内容及技术要求
在此基础上确定零件的加工方案 制定数控加工工艺路线
如工序的划分、加工顺序的安排、与传统加工工序的衔接等
③设计数控加工工序
如工步的划分、零件的定位与夹具的选择、刀具的选择、切削用量的确定等
④调整数控加工工序的程序
如对刀点、换刀点的选择、加工路线的确定、刀具的补偿
⑤分配数控加工中的容差
⑥处理数控机床上部分工艺指令
总之
数控加工工艺内容较多 有些与普通机床加工相似
2轴类零件的加工工艺设计 2.1轴类加工的内容及工艺分析
2.1 球头轴零件图 2.1.1轴类零件加工的内容
数控车床与普通车床相比
具有加工精度高、加工零件的形状复杂、加工范围广等特点 但是数控车床价格较高 加工技术较复杂
球头轴零件可分为粗车、半精车和精车等阶段 一般分为:
①车削外圆 车削外圆是最常见、最基本的车削方法使用各种不同的车刀车削中小型零件外圆(包括车外回转槽)的方法 其中
左偏刀主要用于需要从左向右进给
车削右边有直角轴肩的外圆以及右偏刀无法车削的外圆
②车削内圆
车削内圆(孔)是指用车削方法扩大工件的孔或加工空心工件的内表面 这也是常用的车削加工方法之一
常见的车孔方法在车削盲孔和台阶孔时 车刀要先纵向进给
当车到孔的根部时再横向进给 从外向中心进给车端面或台阶端面
③车削平面
车削平面主要指的是车端平面(包括台阶端面) 常见的方法是用左偏刀车削平面 可采用较大背吃刀量 切削顺利 表面光洁
大、小平面均可车削使用90·左偏刀从外向中心进给车削平面
适用于加工尺寸较小的平面或一般的台阶端面用90·左偏刀从中心向外进给车削平面 适用于加工中心带孔的端面或一般的台阶端面使用右偏刀车削平面 刀头强度较高 适宜车削较大平面 尤其是铸锻件的大平面
④车削锥面
锥面可分为内锥面和外锥面
可以分别视为内圆、外圆的一种特殊形式
内外锥面具有配合紧密、拆卸方便、多次拆卸后仍能保持准确对中的特点 广泛用于要求中准确和需要经常拆卸的配合件上
在普通车床上加工锥面的方法有小滑板转位法、尾座偏移法、靠模法和宽刀法等 小滑板转位法主要用于单件小批量生产 内外锥面的精度较低 长度较短(≤100mm);尾座偏移法用于单件或成批生产轴类零件上较长的外锥面;靠模法用于成批和大量生产较长的内外锥面;宽刀法用于成批和大量生产较短(≤20mm)的内外锥面
⑤车削螺纹
在普通车床上一般使用成形车刀来加工螺纹
加工普通螺纹、方牙螺纹梯形螺纹和模数螺纹时使用的成形车刀
⑥车削台阶、槽
选择数控加工内容时 可按下列顺序考虑:
①普通机床无法加工的内容应优先选择;
②普通机床难加工
质量难保证的内容应重点选择
③普通机床加工效率低 手工操作劳动强度大的内容
虽然数控车床加工范围广泛 但是因受其自身特点的制约
某些零件仍不适合在数控车床上加工
2.1.2轴类零件加工的工艺分析
①粗加工:主要是下料 下料的要求是棒料的直径55㎜ 长度是150㎜
并且要求下料长度的误差不能超过正负1㎜并在棒料两端钻中心孔 中心孔:A4/8.5 并且
要求中心应均匀一致 为下一步工序做准备
②半精加工:半精车外圆 先粗车外圆然后 再半精车外圆
而其他的各尺寸以及跳动的要求都要符合图纸的要求
③精加工:精车外圆 先半精车外圆 最后精车外圆
而其他的各尺寸以及跳动的要求都符合图纸的要求
2.2轴类零件工艺路线的拟定 2.2.1工艺路线的确定
图2.2是加工工序及每个步骤的注释和注意事项
在程序编制中
编程人员必须充分掌握构成零件轮廓的几何要素参数及各几何要素间的关系 因为在自动编程时要对零件轮廓的所有几何元素进行定义 手工编程时要计算出每个节点的坐标 无论哪一点不明确或不确定 编程都无法进行
但由于零件设计人员在设计过程中考虑不周或被忽略 常常出现参数不全或不清楚
如圆弧与直线、圆弧与圆弧是相切还是相交或相离 所以在审查与分析图纸时 一定要仔细核算
发现问题及时与设计人员联系
零件的外形最好采用统一的几何类型及尺寸 这样可以减少换刀次数
还可能应用控制程序或专用程序以缩短程序长度 零件的形状尽可能对称
便于利用数控机床的镜向加工功能来编程 以节省编程时间
2.2.2辅助工序的安排
辅助工序一般包括去毛刺、清洗、上油、检验等 检验工序是主要的辅助工序 是合格证产品质量的重要措施 零件的每道工序加工完成之后
和零件全部加工完成之后都要进行检验工序 2.3数控机床及其工艺设备的选择 2.3.1数控机床的选择
根据零件产量、加工要求选择生产设备(根据专业要求需要选择数控车床) 我们选择SIEMENS的SINUMERIK802S/C数控车床
数控车床常用的功能指令有准备功能G、辅助功能M、刀具功能T、主轴转速功能S和进给功能F 由于车床种类不同 系统配置也各不相同
表2.1 SIEMENS的SINUMERIK802S/C数控车系统的常用功能指令 功能 代码 功能 代码 路径数据 暂停时间 G4 绝对/增量尺寸 G90 91 程序结束 M02 公制/英制尺寸 G71 G70 主轴运动
半径/直径尺寸 G22 G23 主轴速度 S 可编程零点偏置 G158 旋转方向 M03/M04 可设定零点偏置 G54~G57 G500 G53 主轴速度限制 G25 G26 轴运动 主轴定位 SPOS 快速直线运动 G0 特殊车床功能
进给直线插补 G1 恒速切削 G96/G97 进给圆弧插补 G2/G3 圆弧倒角/直线倒角 CHF/RND 中间点的圆弧插补 G5 刀具及刀具偏置
定螺距螺纹加工 G33 刀具 T 接近固定点 G75 刀具偏置 D 回参考点 G74 刀具半径补偿选择 G41 G42 进给率 F 转角处加工 G450 G451 准确停/连续路径加工 G9 G60 G64 取消刀具半径补偿 G40 在准确停时的段转换 G601/G602 辅助功能 M 2.3.2检测量具的选择
①游标卡尺
②数显测位尺
③外径千分尺
④螺纹塞规
2.4轴类零件切削用量参数的确定
数控编程时
编程人员必须确定每道工序的切削用量 并以指令的形式写人程序中
切削用量包括主轴转速、背吃刀量及进给速度等 对于不同的加工方法 需要选用不同的切削用量
切削用量的选择原则是:保证零件加工精度和表面粗糙度 充分发挥刀具切削性能 保证合理的刀具耐用度 并充分发挥机床的性能 最大限度提高生产率 降低成本
2.4.1确定主轴转速
主轴转速应根据允许的切削速度和工件(或刀具)直径来选择 其计算公式为:n=1000v/3.14×D
式中:v-切削速度 单位为m/m动
由刀具的耐用度决定;n-主轴转速 单位为r/min D-工件直径或刀具直径 单位为mm
计算的主轴转速n 最后要选取机床有的或较接近的转速为:
车外圆
粗车主轴转速为1300r/min 精车主轴转速为1600r/min
表2.2刀具的切削参数
加工步骤
刀具切削参数主轴转速 序号
加工内容
刀具规格 n/r.min 进给速度 v/mm.min
类型 材料
1 粗加工外轮廓
93°外圆偏刀 硬质合金 700
200 2 精加工外轮廓
93°外圆偏刀
630
160 3 切螺纹退刀槽
切槽刀
500
80 4 车M24螺纹 60°普通螺纹车
500
800 2.4.2确定进给速度
进给速度是数控机床切削用量中的重要参数
主要根据零件的加工精度和表面粗糙度要求以及刀具、工件的材料性质选取 最大进给速度受机床刚度和进给系统的性能限制
确定进给速度的原则:当工件的质量要求能够得到保证时 为提高生产效率
可选择较高的进给速度
一般在200--800mm/min范围内选取;车外圆 进给速度为400㎜/r 精车时
进给速度为200㎜/r 刀具空行程时
特别是远距离"回零"时
可以设定该机床数控系统设定的最高进给速度
2.4.3确定背吃刀量
车削用量的选择原则是:
(1)粗车时
首先考虑选择一个尽可能大的背吃刀量ap 其次选择一个较大的进给量f 最后确定一个合适的切削进度v 增大背吃刀量ap 可使走刀次数减少 增大进给量f有利于断屑
因此根据以上原则选择粗车切削用量对于提高生产效率 减少刀具消耗
降低加工成本是有利的
(2)精车时
加工精度和表面粗糙度要求较高 加工余量不大且均匀
因此选择较小(但不太小)的背吃刀量ap和进给量f 并选用切削性能高的刀具材料和合理的几何参数 以尽可能提高切削速度v
(3)零件的加工高度H≤(1/4-1/6)RD 以保证刀具有足够的刚度
切削用量的具体数值应根据机床性能 相关的手册并结合实际经验用模拟方法确定 同时
使主轴转速、背吃刀量及进给速度三者能相互适应 以形成最佳切削用量
2.5拟定数控加工工艺卡 2.5.1 数控加工工序
数控加工车削分十三次切削进行加工:
1.然后车削端面作为基准
2.首先进行车削最大外圆?80
3.车?70轴台阶轴
4.车削台阶平面
5.调头装夹
6.车削?65轴
7.车削椎面
8.车削?24圆柱
9.车削?20圆柱
10.车削球面
11.切螺纹退刀槽
12.车削工艺槽
13.加工螺纹M24
2.5.2 数控加工工序表 表2.3数控加工工序表
机械厂
产品名称或代号 零件名称 零件图号
轴类零件 轴类零件 001 工艺序号 程序编号 夹具名称 使用设备 001 WK11111 无
数控车床 工步号 工步内容 刀具号 备注 1 车削端面 T01 自动 2 车削最大外圆 T02 自动 3 车削?70圆柱 T01 自动 4 车削台阶平面 T02 自动 5 调头装夹
手动 6 车削?65圆柱 T01 自动 7 车削椎面 T01 自动 8 车削?24圆柱 T01 自动 9 车削?20圆柱 T01 自动
10 车削球面 T01 自动
11 切螺纹退刀槽 T03 自动
12 车削工艺槽 T03 自动
13 加工螺纹M24 T04 自动
2.6刀具的选择 2.6.1刀具
刀具的选择的原则:刀具的使用的寿命和装夹是否很方便 在加工轴时一般都是批量生产的 那就要求加工的时候必须有效率 装夹要很方便的 根据上面的分析 我采用机夹式刀片
机夹式刀片的材料是超硬质合金钢 对于机夹可转位刀具 由于换刀时间短
可以充分发挥其切削性能 提高生产效率
刀具寿命可选得低些 一般取15-30min .数控机床所选用的刀具常采用适应高速切削的刀具材料(如高速钢、硬质合金)并使用可转位刀片
根据以上的分析
在加工轴所采用的刀具是机夹式 超硬质合金钢的刀片 选择数控车削刀具
数控加工刀具必须适应数控机床高速、高效和自动化程度高的特点 一般应包括通用刀具、通用连接刀柄及少量专用刀柄 刀柄要联接刀具并装在机床刀架上 因此已逐渐标准化和系统化
为了适应数控机床对刀具耐用、稳定、易调、可换等要求近几年机夹式可转位刀具得到广泛的应用 在数量上达到整个数控刀具的30%-40% 金属切除量占总数的80%-90%
而加工轴所用的刀片超硬质合金钢
超硬质合金钢是以碳化钨(WC) 碳化钛(TiC)等 高熔点
高硬度的碳化物的粉末一起粘连的作用的金属钴粉末混合 加压成型
再烧结而制成一种粉末冶金制品 硬质合金具有高硬度(69-81HRC) 高热硬性(可达900-1000度) 高耐磨性和较高抗压强度.用它制造刀具 起切削速度
耐磨性与寿命都比高速钢高
超硬质合金钢制的刀片 装夹在刀体上使用.使用方便 大大的提高加工的效率
此外
对所选择的刀具
在使用前都需对刀具尺寸进行严格的测量以获得精确数据 并由操作者将这些数据输入数据系统 经程序调用而完成加工过程 从而加工出合格的工件 根据以上的分析
采用超硬质合金钢制的刀片 根据加工要求 主要选用的刀具
表2.4刀具表: 序号
加工内容
刀具规格
类型 材料 1 粗加工外轮廓
93°外圆偏刀 硬质合金 2 精加工外轮廓
93°外圆偏刀
3 切螺纹退刀槽
切槽刀
4 车M24螺纹 60°普通螺纹车
2.6.2确定对刀点与换刀点
对于数控机床来说 在加工开始时
确定刀具与工件的相对位置是很重要的 它是通过对刀点来实现的
"对刀点"是指通过对刀确定刀具与工件相对位置的基准点 在程序编制时
不管实际上是刀具相对工件移动 还是工件相对刀具移动 都把工件看作静止 而刀具在运动
对刀点往往也是零件的加工原点 选择对刀点的原则是:
①方便数学处理和简化程序编制;
②在机床上容易找正
便于确定零件的加工原点的位置;
③加工过程中便于检查;
④引起的加工误差小
对刀点可以设在零件上、夹具上或机床上 但必须与零件的定位基准有已知的准确关系 当对刀精度要求较高时
对刀点应尽量选在零件的设计基准或工艺基准上 对于以孔定位的零件
可以取孔的中心作为对刀点
对刀时应使对刀点与刀位点重合 所谓刀位点
是指确定刀具位置的基准点
3轴类零件夹具的选用
3.1对轴类零件夹具的基本要求
数控加工对夹具主要有两大要求:一是夹具应具有足够的精度和刚度;二是夹具应有可靠的定位基准 选用夹具时
通常考虑以下几点:
①尽量选用可调整夹具、组合夹具及其它通用夹具 避免采用专用夹具 以缩短生产准备时间
②在成批生产时才考虑采用专用夹具 并力求结构简单
③装卸工件要迅速方便 以减少机床的停机时间
④夹具在机床上安装要准确可靠 以保证工件在正确的位置上加工
本次设计采用普通的三爪自动定心卡盘 其工作效率高
使用方便、准确度高3.2工件装夹的类型及安装 3.2.1 夹具的类型
数控车床上的夹具主要有两类:一类用于盘类或短轴类零件 工件毛坯装夹在带可调卡爪的卡盘(三爪、四爪)中 由卡盘传动旋转;另一类用于轴类零件 毛坯装在主轴顶尖和尾架顶尖间 工件由主轴上的拨动卡盘传动旋转 3.2.2零件的安装
数控机床上零件的安装方法与普通机床一样 要合理选择定位基准和夹紧方案 注意以下两点:
①力求设计、工艺与编程计算的基准统一 这样有利于编程时数值计算的简便性和精确性
②尽量减少装夹次数 尽可能在一次定位装夹后 加工出全部待加工表面
由于本次设计的零件属于短轴类零件 故采用三爪自定心卡盘装夹 其安装方便、安装精度较高
4车削零件数控加工的编程 4.1数控坐标系的确定
数控车床坐标系统分为机床坐标系和工件坐标系
① 机床坐标系
以机床原点为坐标系原点建立起来的X、Z轴直接坐标系 称为机床坐标系
车床的机床原点为主轴旋转中心与卡盘后端面之交点 机床坐标系是制造和调整机床的基础 也是设置工件坐标系的基础
一般不允许随意变动参考点参考点是机床上的一个固定点 该点是刀具退离到一个固定不变的极限点 其位置由机械挡块和行程开关来确定 以参考点为原点
坐标方向与机床坐标方向相同所建立的坐标系叫做参考坐标系 在实际使用中通常是以参考坐标系计算坐标值
②工件坐标系
数控编程时应该首先确定工件坐标系和工件原点 零件在设计中有设计基准 在加工过程中有工艺基准
同时应尽量将工艺基准与设计基准统一 该基准点通常称为工件原点
以工件原点为坐标原点建立起来的X、Z轴直角坐标系为工件坐标系 在车床上工件原点可以选择在工件的左或右端面上 即工件坐标系是将参考坐标系通过对到平移得到的 4.2走刀路线的确定
①车端面
②钻孔
将棒料运进另一个车间
工序是给棒料进行钻中心孔和车端面 这也是非常重要的一步工序 因为
钻中心孔的好坏将会直接影响下一道工序的进行 要求也是很高的 重要的一步去毛刺 由于上一道工序是锯料 在锯掉的地方会有毛刺 在把毛刺去掉后
要对每一个棒了进行测量 以防止上一道工序出现的废料 再进行认真的测量
将要加工的工件放在专门的钻床上 对工件进行钻孔 是两头同时进行
并且要求钻孔在棒料的中心位置 中心孔:A4/8.8 并且
要求中心孔应均匀一致 在进行好钻孔后
将料放到普通的车床进行车两端面 对于车的要求是很高的 要求棒料的长度是150㎜ 正负0.5㎜
要求每一个工件都要进行检验
②粗车外圆
③精车外圆 上一道工序
将工件运进到另一个车间 主要数控车床车间
这道工序是最重要的一步 是进行精车外圆 先精车外圆 然后
是进行精车外圆
在数控车床上进行加工
用到的工装夹具是三爪液压卡盘 还需要顶针
顶针的作用就是使加工的棒料 保持同轴度
使加工的零件的精度可以达到更高 也使加工时更加的安全
所用到的测量工具是游标卡尺 外径千分尺 同理
再加工时加工的要求和加工的要求是一样的
而其他的各尺寸以及跳动的要求都要符合图纸的要求
④割槽
端面进行定位割槽并去毛刺;还要求对每批次量生产槽的轴向位置需结合内外球笼装配后之轴向窜动间隙以及总成压缩总长来定 同上一样
是在CNC车床上进行割槽 所用到的工装夹具是三爪卡盘 顶针
用到的测量的检具是游标卡尺
⑤车螺纹
4.3程序编制
数控车床主要是加工回转体零件
典型的加工表面不外乎外圆柱、外圆锥、螺纹、圆弧面、切槽等 我所做的工序是精车外圆 加工的程序如下:
加工程序及其备注
N10 G50 S10000 ;程序开始
N12 G00 G97 S700 T01
N14 M03
N16 M08
N18 G00 X46.777 Z27.753
N20 G00 X49.807 Z0.807
N22 G00 X44.807 Z0.807
N24 G00 X44.100 Z0.100
N26 G01 X44.100 Z-24.100 F200
N28 G00 X44.807 Z-23.393
N30 G00 X49.807 Z-23.393
N32 G00 X49.807 Z0.807
N34 G00 X42.807 Z0.807
N36 G00 X42.100 Z0.100
N38 G01 X42.100 Z-24.100 F200
N40 G00 X42.807 Z-23.393
N42 G00 X47.807 Z-23.393
N44 G00 X47.807 Z0.807
N46 G00 X40.807 Z0.807
N48 G00 X40.100 Z0.100
N50 G01 X40.100 Z-24.100 F200
N52 G00 X40.807 Z-23.393
N54 G00 X45.807 Z-23.393
N56 G00 X45.807 Z-0.293
N58 G00 X40.807 Z-0.293
N60 G00 X40.100 Z-1.000
N62 G01 X40.100 Z-11.000 F200
N64 G01 X40.100 Z-23.000
N66 G00 X41.100 Z-23.000
N68 G00 X49.807 Z-23.000
N70 G00 X46.777 Z27.753
N72 M09
N74 M30
N75 G50 S0
N76 G00 G97 700 T02
N77 M03
N78 M08
N79 G00 X42.450 Z24.023
N80 G00 X46.966 Z24.023
N81 G00 X46.966 Z3.600
N82 G00 X46.966 Z-1.400
N83 G00 X46.100 Z-1.900
N84 G41 N85 G01 X-0.100 Z-1.900 F200 N86 G00 X0.766 Z-1.400 N87 G00 X0.766 Z3.600 N88 G00 X0.766 Z24.023 N89 G00 X42.450 Z24.023 N90 G40 N91 M09 N92 M30
掉头装夹
N10 G50 S10000 N12 G00 G97 S700 T01 N14 M03 N16 M08 N18 G00 X27.033 Z41.455 N20 G00 X44.744 Z0.807 N22 G00 X39.744 Z0.807 N24 G00 X39.037 Z0.100 N26 G41 N28 G01 X39.037 Z-99.900 F200 N30 G01 X40.937 Z-99.900 N32 G00 X40.230 Z-99.193 N34 G00 X45.230 Z-99.193 N36 G00 X45.230 Z0.807 N38 G00 X37.744 Z0.807 N40 G00 X37.037 Z0.100 N42 G01 X37.037 Z-99.900 F200 N44 G01 X39.037 Z-99.900 N46 G00 X38.330 Z-99.193 N48 G00 X43.330 Z-99.193 N50 G00 X43.330 Z0.807 N52 G00 X35.744 Z0.807 N54 G00 X35.037 Z0.100 N56 G01 X35.037 Z-99.900 F200 N58 G01 X37.037 Z-99.900 N60 G00 X36.330 Z-99.193 N62 G00 X41.330 Z-99.193 N64 G00 X41.330 Z0.807 N66 G00 X33.744 Z0.807
N68 G00 X33.037 Z0.100
N70 G01 X33.037 Z-99.900 F200
N72 G01 X35.037 Z-99.900
N74 G00 X34.330 Z-99.193
N76 G00 X39.330 Z-99.193
N78 G00 X39.330 Z0.807
N80 G00 X31.744 Z0.807
N82 G00 X31.037 Z0.100
N84 G01 X31.037 Z-84.603 F200
N86 G03 X32.600 Z-90.000I-8.537 K-5.397
N88 G01 X32.600 Z-99.900
N90 G01 X33.037 Z-99.900
N92 G00 X32.330 Z-99.193
N94 G00 X37.330 Z-99.193
N96 G00 X37.330 Z0.807
N98 G00 X29.744 Z0.807
N100 G00 X29.037 Z0.100
N102 G01 X29.037 Z-82.301 F200
N104 G03 X31.037 Z-84.603 I-6.537 K-7.699
N106 G00 X31.257 Z-83.627
N108 G00 X36.257 Z-83.627
N110 G00 X36.257 Z0.807
N112 G00 X27.744 Z0.807
N114 G00 X27.037 Z0.100
N116 G01 X27.037 Z-80.976 F200
N118 G03 X29.037 Z-82.301I-4.537 K-9.024
N120 G00 X28.956 Z-81.304
N122 G00 X33.956 Z-81.304
N124 G00 X33.956 Z0.807
N126 G00 X25.744 Z0.807
N128 G00 X25.037 Z0.100
N130 G01 X25.037 Z-80.224 F200
N132 G03 X27.037 Z-80.976 I-2.537 K-9.776
N134 G00 X26.723 Z-80.027
N136 G00 X31.723 Z-80.027
N138 G00 X31.723 Z0.807
N140 G00 X23.744 Z0.807
N142 G00 X23.037 Z0.100
N144 G01 X23.037 Z-79.914 F200 N146 G03 X25.037 Z-80.224I-0.537 K-10.086
N148 G00 X24.530 Z-79.362
N150 G00 X29.530 Z-79.362
N152 G00 X29.530 Z0.807
N154 G00 X21.744 Z0.807
N156 G00 X21.037 Z0.100
N158 G01 X21.037 Z-72.399 F200
N160 G01 X22.600 Z-76.983
N162 G01 X22.600 Z-79.900 N164 G03 X23.037 Z-79.914 I-0.100 K-10.100
N166 G00 X22.369 Z-79.171
N168 G00 X27.369 Z-79.171
N170 G00 X27.369 Z0.807
N172 G00 X19.744 Z0.807
N174 G00 X19.037 Z0.100
N176 G01 X19.037 Z-66.532 F200
N178 G01 X21.037 Z-72.399
N180 G00 X21.478 Z-71.501
N182 G00 X26.478 Z-71.501
N184 G00 X26.478 Z0.807
N186 G00 X17.744 Z0.807
N188 G00 X17.037 Z0.100
N190 G01 X17.037 Z-60.665 F200
N192 G01 X19.037 Z-66.532
N194 G00 X19.478 Z-65.635
N196 G00 X24.478 Z-65.635
N198 G00 X24.478 Z0.807
N200 G00 X15.744 Z0.807
N202 G00 X15.037 Z0.100
N204 G01 X15.037 Z-54.900 F200
N206 G01 X15.072 Z-54.900
N208 G01 X17.037 Z-60.665
N210 G00 X17.478 Z-59.768
N212 G00 X22.478 Z-59.768
N214 G00 X22.478 Z0.807
N216 G00 X13.744 Z0.807
N218 G00 X13.037 Z0.100
N220 G01 X13.037 Z-54.900 F200
N222 G01 X15.037 Z-54.900
N224 G00 X14.330 Z-54.193
N226 G00 X19.330 Z-54.193
N228 G00 X19.330 Z0.807
N230 G00 X11.744 Z0.807
N232 G00 X11.037 Z0.100
N234 G01 X11.037 Z-19.900 F200
N236 G01 X12.100 Z-19.900
N238 G01 X12.100 Z-50.000
N240 G01 X12.100 Z-54.900
N242 G01 X13.037 Z-54.900
N244 G00 X12.330 Z-54.193 N246 G00 X17.330 Z-54.193 N248 G00 X17.330 Z0.807 N250 G00 X9.744 Z0.807 N252 G00 X9.037 Z0.100 N254 G01 X9.037 Z-7.490 F200 N256 G03 X10.100 Z-12.000 I-9.037 K-4.510 N258 G01 X10.100 Z-19.900 N260 G01 X11.037 Z-19.900 N262 G00 X10.330 Z-19.193 N264 G00 X15.330 Z-19.193 N266 G00 X15.330 Z0.807 N268 G00 X7.744 Z0.807 N270 G00 X7.037 Z0.100 N272 G01 X7.037 Z-4.755 F200 N274 G03 X9.037 Z-7.490 I-7.037 K-7.245 N276 G00 X9.354 Z-6.541 N278 G00 X14.354 Z-6.541 N280 G00 X14.354 Z0.807 N282 G00 X5.744 Z0.807 N284 G00 X5.037 Z0.100 N286 G01 X5.037 Z-3.246 F200 N288 G03 X7.037 Z-4.755 I-5.037 K-8.754 N290 G00 X7.023 Z-3.755 N292 G00 X12.023 Z-3.755 N294 G00 X12.023 Z0.807 N296 G00 X3.744 Z0.807 N298 G00 X3.037 Z0.100 N300 G01 X3.037 Z-2.367 F200 N302 G03 X5.037 Z-3.246 I-3.037 K-9.633 N304 G00 X4.777 Z-2.280 N306 G00 X9.777 Z-2.280 N308 G00 X9.777 Z0.807 N310 G00 X1.744 Z0.807 N312 G00 X1.037 Z0.100 N314 G01 X1.037 Z-1.953 F200 N316 G03 X3.037 Z-2.367 I-1.037 K-10.047 N318 G00 X2.575 Z-1.480 N320 G00 X7.575 Z-1.480 N322 G00 X7.575 Z-1.193 N324 G00 X-0.707 Z-1.193 N326 G00 X-0.000 Z-1.900 N328 G03 X1.037 Z-1.953 I0.000 K-10.100 F200 N330 G00 X0.406 Z-1.177
N332 G00 X44.744 Z-1.177
N334 G00 X27.033 Z41.455
N336 M01
N338 G50 S800
N340 G00 G97 S630 T01
N342 M03
N344 M08
N346 G00 X36.929 Z41.006
N348 G00 X45.937 Z-1.293
N350 G00 X-0.707 Z-1.293
N352 G00 X-0.000 Z-2.000
N354 G41
N356 G03 X10.000 Z-12.000 I0.000 K-10.000 F200
N358 G01 X10.000 Z-20.000
N360 G01 X12.000 Z-20.000
N362 G01 X12.000 Z-50.000
N364 G01 X12.000 Z-55.000
N366 G01 X15.000 Z-55.000
N368 G01 X22.500 Z-77.000
N370 G01 X22.500 Z-80.000
N372 G03 X32.500 Z-90.000 I0.000 K-10.000
N374 G01 X32.500 Z-100.000
N376 G01 X40.937 Z-100.000
N378 G00 X40.230 Z-99.293
N380 G00 X45.937 Z-99.293
N382 G00 X36.929 Z41.006
N384 M01
N386 G50 S800
N388 G00 G97 S630 T02
N390 M03
N392 M08
N394 G00 X45.251 Z37.632
N396 G00 X45.251 Z-50.600
N398 G00 X23.000 Z-50.600
N400 G00 X18.000 Z-50.600
N402 G41
N404 G01 X10.100 Z-50.600 F200
N406 G04X0.500
N408 G00 X23.000 Z-50.600
N410 G00 X23.000 Z-52.600
N412 M09
N414 M30 程序结束 5结 论
毕业设计是我们学了三年全部的课程 其中包括基础课程、技术基础课、以及专业课之后 在完成工作实习、校内课程设计的基础上 对所有学过的课程的深入地综合性的总结 也是一次对理论联系实际的实际训练 因此
它是我们大学所学、所用、所看的一次总结 它将在我们大学生活的精彩画卷画上一个句号
通过这次设计 我们综合了专业了知识 更是因为在设计中 遇到了许多的问题 得到了老师的解答 完成了工艺的设计
我希望能通过这次的毕业设计
对自己未来将从事的工作进行一次适应性的训练 从中锻炼自己分析问题、解决问题的能力 为以后所从事的工作进行基石地铺垫
6致 谢
三年的学习生活转瞬即逝 让人有些措手不及的感觉 好象还没开始已经结束
时间的流逝其过程中经历的坎坷使一个人慢慢成熟
因而我对过去的日子和给过我鼓励、帮助的人们总是心怀感激 并让我倍加珍惜未来的生活
本次毕业设计是在指导教师的悉心指导下展开的 从设计题目的提出到论文的完成 指导老师都在关注我们的进度
贺老师一丝不苟的治学态度和高度的责任感 在做毕业设计的过程中时刻影响和教育着我 使我难忘和感动 在此论文完成之际
谨向贺老师以最衷心的感谢
在毕业设计论文完成过程中 我也得到了同班同学的大力协助 让我感受到同学的友谊和真诚的关心 在此向他们表示诚挚的谢意
另外感谢我的班主任 他对我的关心和培养
在我读大学的这三年中给予我的帮助 特别是在做毕业设计的最后阶段
同时也是最需要帮助的时候给了我支持 才使得我能顺利完成毕业设计
最后向在百忙之中评阅本次毕业设计并提出宝贵意见的各位老师们表示最诚挚的谢意 同时向所有关心、帮助和支持我的老师和同学表示衷心的感谢 谢谢你们!
7参 考 文 献
[1]吴明友.数控机床加工技术.东南大学出版社.2000.6 [2]孙竹.数控机床编程与操作.机械工业出版社.1996.4 [3]艾兴、肖诗.削用量简明手册.北京机械工业出版社.1983.3 [4]徐宏主.数控加工工艺.化工工业出版社.2003.3 [5]孙江宏.陈秀梅.PRO/E2001数控加工教程.北京清华大学出版社.2001.4 [6]余英良.数控加工编程及操作.高等教育出版社.2004.4 [7]刘雄伟.数控机床与编程培训教程.机械工业出版社.2001.5 [8]杨学桐、李东茹、何文立
等距世纪数控机床技术发展战略研究.北京国家机械工业局.2000.3 ?? ?? ?? ??
苏州市职业大学机电工程系毕业设计说明书(论文)
用人要看他的忠诚度和可靠程度、归依企业的程度,希望能够跟企业结合一起的意向有多少,如果这三样东西都是对的,我们企业会给他非常大的机会去发展。
第13篇:数控 车工 技师 论文
数车实训的项目教学运用
李辉
【摘
要】:随着科学技术的迅速发展,传统的制造业已发生了显著的变化,职业技术学校作为生产一线操作和技术人才的培养基地,应及时合理地调整教学计划,快速高效地为现代社会培养出高质量的技术人才。而数控加工技术正越来越广泛的应用,提高教学水平是必须解决的问题,本文从项目式教学的特点出发,谈谈在数控车实训加工中的应用。 【关键词】:项目式教学;数控车技术;实训项目
项目教学法是现如今比较流行的一种教学方法,那什么才是项目教学法呢?实际上所谓项目教学法是师生通过完成一个完整的项目工作而进行的一种教学活动。
这种教学方法打破传统的教育手段,贯穿新的教育理念,以职业能力作为进行教育的基础、培养目标和评价标准;以通过职业分析确定的综合能力作为学习的科目;以市场对专项能力的需求方向作为安排教学计划的依据。项目式教学也是目前我国职业教育普遍认可的教育模式,也是我国职业教育的成功经验。随着计算机科学、信息技术的迅速发展,传统的制造业已发生了十分显著的变化,发达国家正进行由传统的制造技术向现代制造技术的转变,并提出了全新的制造模式。数控加工技术将逐步引航现代机械制造业的发展。职业院校作为生产一线技术人才的培养基地,应针对数控技术的发展方向,面对新技术、新工艺的不断出现、及时合理地调整教学计划,快速高效地为现代社会培养出合格的技术人才。项目式教学的目的在于用最短的时间和最有效的方法,使学生掌握某项技能。项目式教学的课程设置、教学大纲和教材是基于对
每个工种的任务和技能的深刻分析,严格按照工作规范,开发出不同的教学实训项目,每个实训项目都有明确的学习目标和要求,还有详细的工作步骤,强调学以致用。
一、对项目式教学的理解 1·含义
项目教学是将某门专业课程按类别分为若干技术或技能单元,每个技术或技能单元作为一个教学项目,实行理论、实践一体化的单元式教学,每个单元教学都以应用该项技术或技能完成一个作业来结束,并进行下一个项目的教学。项目教学就是师生为完成某一具体的工作任务而展开的教学行动。
2·特点
(1)该项目具有一个轮廓清晰的工作任务说明。 (2)它是某一教学课题的理论知识和实践技能的结合体。 (3)学生在一定的时间范围内能够组织自己的学习行为。 (4)学生自己克服、处理在项目工作中出现的困难和问题。 (5)能有明确而具体的成果展示。
(6)学习结束时,师生能对“项目”的完成情况作出评价。 3·说明
(1)相对于学科教学而言:与企业实际生产过程的结合更加紧密。 (2)体现在教学内容上:以实际生产过程为中心,具有典型性和案例型。 (3)体现在教学组织形式上:以合作式学习为主,是进行知识技能学习的学习小组,也是进行产品设计生产的工作小组;小组人数以3~6人为宜,推选组长。教师必须对学生做深入细致的调查研究,一般采用互补方式,不同知识结
构的学生相搭配,可以取长补短,相互借鉴;不同认知方式的学生相搭配,在各自发挥其优势的情况下,相互学习,使认知风格“相互强化”。
(4)体现在教学方法上:以实践性教学为主,强调学习的自主性和探究性。 (5)体现在教学场地上:以实验室和实习基地为主,是课堂与车间的整合。 4·注意
(1)项目活动是否符合学生已有的知识和正在学习的知识。 (2)此项目能否让学生感兴趣?能否激发学生学习积极性。 (3)怎样让学生更加了解自己并相互学习。
(4)如何让学生把自己所学知识与现实生活联系起来。
(5)项目内容是否有助于树立学生自信心。(6)项目活动是否考虑到了学生实际,进行分层教学。
5·程序
(1)任务阶段:教师布置任务,帮助学生理解任务;知道自己要做什么,要学哪方面的知识,练习哪方面的技能,达到什么样的目标。
(2)计划阶段:学生一般以小组方式工作,制定工作计划。
(3)实施阶段:教师做演示,学生根据计划完成自已的任务,教师及时指导。 (4)检查阶段:学生自行检查实训过程、结果。
(5)评价总结阶段:自我评价,交流心得。教师对学生在整个过程中出现的问题予以评价,对于学生在制作过程中出现的问题要给予及时纠正。目的是使学生通过一次技能训练对自己所掌握的理论知识及技能有所认识、有所提高。
二、对数控车实训项目的分解
1·数控车实训项目的设置
根据以上对项目式教学法的理解和要求,我们对数控车工技术做以下两个分类,一部分是机床的操作,一部分是机床控制指令和工艺的学习。
2·数控车每个实训项目的目标及要求 项目一:
(1)了解所教系统操作面板上个按扭的名称及其功能、用途; (2)熟练掌握手动、手轮操作的方式和方法。
项目二:
(1)了解所教系统编制程序的基本结构和格式; (2)掌握所教系统程序的编辑方法和应用。
项目三:
(1)了解数控车床简单轴类零件的加工方法; (2)掌握G00,G01,G90,G94指令的使用。
项目四:
(1)了解数控车床圆弧零件的加工特点; (2)掌握G0
2、G03指令的使用。项目五:
(1)了解槽类零件的加工方法和加工特点; (2)熟练掌握多把刀对刀方法。 项目六: (1)了解阶台轴的基本加工工艺及工艺准备; (2)掌握G71粗车循环、G70精车循环的应用。
项目七:
(1)了解数控车床车削螺纹的原理与特点; (2)掌握G
32、G92螺纹切削指
令的特点及应用。项目教学法和所有其他的教学法相同,不是单一的、孤立的,而是教学过程的一部分。不是所有的课程和课程的各个阶段都适用这种方法。对于数控实习教学来说,项目教学法更适合在学生实习的后期进行。在学生已经掌握了一些基本的加工工艺知识和编程、面板操作以后实施会更合理,会取得最好的教学效果。项目教学法对我来讲仍是一项新的尝试,在实习教学中如何更好的运用这种教学方法,如何合理的选择教材,如何在设计项目时把职业技能鉴定标准更好的融合进来,都是在以后的教学中需要进一步探讨和研究的内容。但是,不容质疑,项目教学法符合教学规律,是以培养学生综合能力为教育目标,以提高学生专业技能水平为主线,以适应市场需求为导向的教学方法、教学手段,随着教学理念的不断更新,项目教学法会不断发展、完善为贯穿整个教学的一种教学体系。
我们认为数控实训的功能应该是多方面的除满足教学需要外,还可以进行科研项目研究,提高教师自身的业务水平,同时为生产科研服务,并积极开展对外技术培训和技术服务,以及承接加工任务等,从中获得一定的经济效益,用以改善生产实习的条件、促进正常的教学科研活动,推动教学改革与课程的建设。
[参考文献] [1]吴言.项目教学法[J].中国职业技术教育, 2003(7).[1]刘云生.项目学习-信息时代重要的学习方式[J].中国教育学刊, 2002(2).
第14篇:数控专业毕业设计论文
提示:以下所有论文,将鼠标移至想要查看的标题上,按住Ctrl键并单击鼠标左键即可打开查看详细内容。也可咨询QQ:893628136
1.(字数:4522.页数:12 价格:¥50.00)
2.(字数:5881.页数:14 价格:¥60.00)
3.鼠标外壳凸模的数控加工(字数:2927.页数:17 价格:¥50.00)
4.(字数:6828,页数:18 价格:¥45.00)
5.起重机械部件线切割机加工程序设计(字数:5957,页数:10 价格:¥108.00)
6.(字数:7509,页数:20 价格:¥98.00)
7.组合件数控车工艺与编程(字数:12167.页数:24 价格:¥108.00)
8.(字数:10255,页数:34 价格:¥60.00)
9.型腔零件的数控编程加工(字数:5741,页数:50 价格:¥98.00)
10.(字数:17804,页数:33 价格:¥88.00)
11.(字数:14571,页数:37 价格:¥98.00)
12.(字数:8549,页数:21 价格:¥80.00)
13.(字数:7520,页数:29 价格:¥98.00)
14.花型类零件电火花线切割加工(字数:10162,页数:23 价格:¥80.00)
15.(字数:10925,页数:29 价格:¥80.00)
16.数控机床电气设计(字数:8717,页数:22 价格:¥60.00)
17.(字数:20105.页数:49 价格:¥118.00)
18.(字数:36510.页数:71 价格:¥118.00)
19.(字数:16017.页数:49 价格:¥128.00)
20.数控机床位置精度检测及标准研究(字数:17088.页数:55 价格:¥128.00)
21.(字数:19071.页数:49 价格:¥128.00)
22.(字数:13800.页数:50 价格:¥118.00)
23.(字数:9607,页数:20 价格:¥90.00)
24.零件的铣削加工造型与程序编制(字数:14467,页数:25 价格:¥98.00)
25.(字数:22848,页数:40 价格:¥98.00)
26.(字数:17070.页数:40 价格:¥108.00)
27.CA6140普通车床的经济型数控改造设计(字数:33356.页数:81 价格:¥118.00)
28.(字数:14793.页数:29 价格:¥118.00)
29.PLC编程在数控系统中的应用(字数:22348.页数:35 价格:¥98.00)
30.(字数:15159.页数:36 价格:¥98.00)
31.数控机床的应用与发展(字数:18265.页数:29 价格:¥98.00)
32.(字数:25176.页数:42 价格:¥98.00)
33.(字数:17295.页数:25 价格:¥98.00)
第15篇:数控仿真探索论文
探索斯沃数控仿真软件课堂教学
王建 裘敏浩 赵传彬
贵州电子信息职业技术学院 贵州 凯里 邮编 556600 摘 要:初学者在数控实习教学过程中易发生安全事故,造成机床和人身伤害。数控加工仿真系统是基于虚拟现实的仿真软件,是利用计算机来模拟实际的加工过程。采用数控仿真软件教学,不仅降低了运行成本,而且给学生更多的练习机会,在各种仿真过程中熟练掌握数控机床的加工生产技术,训练学生实习操作的技能技巧,提高数控教学水平。但数控加工仿真系统是一种模拟软件,它不可能完全代替实训。
关键词:数控技术 仿真软件 数控教学
研究目的:数控技术自问世以来,给世界各国制造业带来了革命性的变化。现在数控技术已成为制造业,特别是先进制造业的核心,也是体现一个国家综合国力水平的重要标志。企业的制造能力、适应市场能力和竞争能力都是建立在数控技术之上。随着我国制造业的蓬勃发展,需要大量掌握现代化制造技术的人才,特别对一线数控技术工人的需求量非常大,这就要求职业学校培养具有高技能的技术人才。但只在课堂上传授理论知识,比较枯燥乏味,学生很少有学习兴趣。因此,探索出一种投入小、见效快、学生容易理解且可以在课堂上操作给学生看的教学模式势在必行。
一、数控教学中应用数控仿真软件在的优点
要学好一门技术就要经过大量的实习实践,而数控技术更是一门实践性强的课程,良好实习环境是数控教学必不可少的条件。而数控实习设备属于的高科技产品,价格高,一台数控车或数控铣至少在10万左右,而一台数控加工中心要30万左右,多则达数百万。而且每个班级基本上都有五六十人左右,实习设备是远远不够的。从数量上和成本安全性上考虑,都不大适合学生的普及性教学和实训。如果数控机床的实训完全按照实操进行,需购置大量设备来满足学生实习,这样投入大、消耗多、成本高,一般学校难以承受,而使用数控加工仿真软件是解决此不足的主要途径,它既能解决实训设备不足、学生实习时间少的问题,又能解决初学者由于对数控系统及操作面板不熟悉而造成的安全问题,提高学生对数控系统操作及控制面板的熟悉度,让学生大胆地通过仿真对所编程序进行验证,使实习的安排达到多样化,提高学生的学习兴趣和编程能力,使数控技术的教学投入少、见效快,是一种经济实用、安全可靠、功能多样的教学辅助工具。
二、在数控教学中的应用数控加工仿真软件方法
在学习数控加工仿真软件前,一般是学生完成了专业基础理论教学(如机械基础,机械制图等)、专业基础实训教学(如钳工,普通车工等)的基础上进行的,仿真教学的目的是充分利用现有的资源,训练学生实习操作的技能技巧。怎样运用好数控加工仿真系统,使其发挥最好效果,具体应做如下几点:
1.在数控教学初期
在教学初期,主要以理论教学为主,学习数控编程的理论知识(如指令格式、编程方法等问题)。但同时在教学中应穿插数控仿真软件的学习,仿真软件主要解决软件的安装及基本的使用问题(如下1-1图)。可先用多媒体将数控仿真软件对学生进行集中训练,使学生对仿真软件的使用有全面的了解,然后让学生上机练习仿真软件的使用。
图1
2.教学中期
经过初期的软件学习后,学生基本掌握了数控机床面板及数控仿真软件的操作方法,数控教学应将理论与仿真有机结合起来,理论教学以编程方法和工艺为主,而仿真训练主要进行程序的输入、校验等练习,同时让学生了解不同数控系统(如下几图:1法拉克、2西门子、3广数、4华中等操作系统)的操作方式,将理论与实践结合起来。
图2法拉克
图3西门子
图4广州数控
图5华中数控
3.教学后期
数控加工仿真软件只是一种模拟教学软件,是对加工过程的模拟,并非真实的加工过程,它不可能完全代替教学,尤其是数控加工实训。在数控教学中,往往由于过分依赖仿真系统,
而忽视了机床加工练习。因为仿真软件与实际机床有着本质的区别,仿真软件无法替代学生在机床上加工时的真实感受,特别在切削用量的选择方面。因此,教学后期要合理安排时间,将仿真训练与实际数控机床操作训练有机结合,尽量让学生在机床上进行零件的加工训练,而仿真软件此时只是对程序验证的工具,学生可先在仿真系统上将零件模拟加工出来,然后再上机床实际加工,这样可以保证程序的正确性,减少在加工的过程中因程序问题而造成的安全事故。
华中数控仿真模拟“数控铣”加工零件示意图
华中数控仿真模拟“数控车”加工零件示意图
总结:把数控仿真软件用于数控教学中,将有利于改进教学方法,提高教学水平。但同时要正确处理仿真与实际操作的关系,不能用仿真软件完全代替数控实习,应合理安排仿真与实际操作的时间。
教育是高投入、高产出的行业,如何利用现有的资源和设备,以最少的成本,培养具有现代化数控技术应用和开发能力的新型数控车(铣)加工中心人才,将是职业教育探索的方向。
作者简介:王建 男 贵州电子信息职业技术学院助教 研究方向:机械类专业基础课程教学、研究
第16篇:关于数控论文数控刀具论文
关于数控论文数控刀具论文
刀具补偿在数控加工中的应用
摘要:在上世纪早期的数控加工中,编程人员根据刀具的理论路线和实际路线的相对关系来进行编程,容易产生错误。刀具补偿的概念出现以后,在数控加工中发挥了巨大的作用,有效提高了编程的工作效率。数控加工中常用的两种补偿是刀具半径补偿和刀具长度补偿,这两种补偿为我们解决了加工中因刀具形状而产生的问题。
关键词:数控加工;半径补偿;长度补偿
一、刀具半径补偿
刀具半径补偿的概念。因为有了刀具半径补偿,我们在编程时可以不要考虑太多刀具的直径大小。以铣刀铣削外轮廓为例,在没有使用半径补偿时,编程人员必须依次算出刀具中心各点的坐标,然后才能进行编程。当刀具直径发生变化时,各点的坐标必然也会发生变化,程序中的坐标点需重新进行计算,这样使得每一次刀具变化都要重新计算重新编程,大大增加了编程工作量。同样的情况如果使用了刀具半径补偿,编程人员不必计算刀具的实际中心轨迹,只需根据工件的轮廓计算出图纸上各点的坐标值然后编出程序,再把刀具半径作为补偿量放在半径补偿寄存器里。数控装置能自动计算出刀具中心轨迹,不管刀具半径如何变化,我们只需更改刀具半径补偿值,就可以控制工件外形尺寸的大小,对上述程序基本不用作修改。
刀具半径补偿的指令。刀具半径补偿是通过指令G
41、G42来执行的,基本格式为G41/G42 G00/G01 X_ Y_ H_;其中H为补偿量代码。补偿有两个方向:当沿着刀具切削方向看,刀具在工件轮廓的左侧是刀具半径左补偿用G41,反之则是刀具半径右补偿用G42。取消补偿用G40;刀具半径补偿的应用。在应用
、G42进行半径补偿时,应特别注意使补偿有效的刀具移动方向与坐标。刀具半径补偿的起刀位置很重要,如果使用不当刀具所加工的路径容易出错,将会影响加工的零件形状。正确的走刀应该是在刀具没有切削工件之前让半径补偿有效,然后再进行正常的切削。同样的道理在取消刀具半径补偿时,也应该是在切削完毕离开工件之后。
二、刀具长度补偿
刀具长度补偿的概念。数控铣床上刀具长度补偿只是和Z坐标有关,对于X、Y平面内的编程零点,由于刀具是由主轴锥孔定位决定,因此X、Y平面内的编程零点位置是固定不变的。对于Z坐标的编程零点就不一样了。在铣床上应用的每一把刀具长度都是不同的,例如,我们要钻一个深度为40mm的孔,然后将其进行攻丝,攻丝深度设为30mm,加工刀具假设为一把长为250mm的钻头和一把长为350mm的丝锥。首先用钻头钻削出40mm深的孔,机床以其为基准设定了相应的工件零点,当采用丝锥攻丝时,如果按照设定的工件零点开始加工,则由于两把刀具长度不同,从而使得攻丝过长,损坏了刀具和工件。此时如果采用刀具长度补偿,那么当工件零点设定之后,即使丝锥和钻头长度不同,在调用丝锥工作时,零点Z坐标已经自动向Z+(或Z-)补偿了丝锥与钻头的长度差,保证了加工零点的正确,这样就不会损坏刀具和工件了。
刀具长度补偿的指令。刀具长度补偿一般通过含有G43(G44)和H指令来实现的,格式为指令格式为G43 G01 Z_H_;或G44 G01 Z_H_。其中G43表示刀具长度正补偿,即把编程的Z值加上H代码指定的偏值寄存器中预设的数值后作为CNC实际执行的Z坐标移动值,也就是说实际执行的Z坐标值为Z\'=Z_+(H_);而G44则正好相反,实际执行的Z坐标值为Z\'=Z_-(H_)。其中H
可设正值或负值,我们可以将这两个指令通过H的正负值设定进行统一,即只用G43和G44其中之一。加工结束后要取消刀具长度补偿,用指令G49实现;刀具长度补偿的应用:(1)用刀具的实际长度作为刀具长度的补偿(推荐使用这种方式)。使用刀具的实际长度作为补偿就是使用对刀仪测量刀具的长度,然后把测量出来的数值输入到刀具长度补偿寄存器中,作为刀具长度补偿。以避免加工不同的工件时不断地修改刀具长度偏置值,减少由此产生的操作失误。(2)以其中一把较长的刀作为标准刀具,,这个标准刀具的长度补偿值为0,其余刀具实际长度与标准刀具长度的差值作为这些刀具的长度补偿数值,输入到其所采用的H代码地址内。(3)利用每把刀具到工件坐标系原点的距离作为各把刀的刀长补偿,该值一般为负;此时用于设定工件坐标系偏置的G54的Z值为0。以上是在数控加工中常用的两种补偿方式,它给我们的编程和加工带来很大的方便。
参考文献:
[1]王志平.机床数控技术应用[M].高等教育出版社,2003.
[2]叶伯生,戴永清.数控加工编程与操作[M].华中科技大学出版社,2005.
[3]宇龙数控仿真系统说明书[M].
第17篇:数控车工技师论文
数控车工技师论文
时间:1970-01-01来源:网络发布者:webmaster
数控机床的应用与维护
科学技术的发展,对机械产品提出了高精度、高复杂性的要求,而且产品的更新换代也在加快,这对机床设备不仅提出了精度和效率的要求,而且也对其提出了通用性和灵活性的要求。数控机床就是针对这种要求而产生的一种新型自动化机床。数控机床集微电子技术、计算机技术、自动控制技术及伺服驱动技术、精密机械技术于一体,是高度机电一体化的典型产品。它本身又是机电一体化的重要组成部分,是现代机床技术水平的重要标志。数控机床体现了当前世界机床技术进步的主流,是衡量机械制造工艺水平的重要指标,在柔性生产和计算机集成制造等先进制造技术中起着重要的基础核心作用。因此,如何更好的使用数控机床是一个很重要的问题。由于数控机床是一种价格昂贵的精密设备,因此,其维护更是不容忽视。
一、数控机床
1.数控加工的概念
数控机床的工作原理就是将加工过程所需的各种操作(如主轴变速、工件的松开与夹紧、进刀与退刀、开车与停车、自动关停冷却液)和步骤以及工件的形状尺寸用数字化的代码表示,通过控制介质(如穿孔纸带或磁盘等)将数字信息送入数控装置,数控装置对输入的信息进行处理与运算,发出各种控制信号,控制机床的伺服系统或其他驱动元件,使机床自动加工出所需要的工件。所以,数控加工的关键是加工数据和工艺参数的获取,即数控编程。数控加工一般包括以下几个内容:
(1) 对图纸进行分析,确定需要数控加工的部分六剑客职教园(最大的免费职教教学资源网站);
(2) 利用图形软件(如CAXA制造工程师)对需要数控加工的部分造型;
(3) 根据加工条件,选择合适的加工参数,生成加工轨迹(包括粗加工、半精加工、精加工轨迹);
(4) 轨迹的仿真检验;
(5) 生成G代码;
(6) 传给机床加工。
2.数控机床的特点
(1) 具有高度柔性
在数控机床上加工零件,主要取决于加工程序,它与普通机床不同,不必制造、更换许多工具、夹具,不需要经常调整机床。因此,数控机床适用于零件频繁更换的场合。也就是适合单件、小批生产及新产品的开发,缩短了生产准备周期,节省了大量工艺设备的费用。
(2) 加工精度高
数控机床的加工精度,一般可达到0.005~0.1mm,数控机床是按数字信号形式控制的,数控装置每输出一个脉冲信号,则机床移动部件移动一个脉冲当量(一般为0.001mm),而且机床进给传动链的反向间隙与丝杠螺距平均误差可由数控装置进行补偿,因此,数控机床定位精度比较高。
(3) 加工质量稳定、可靠
加工同一批零件,在同一机床,在相同加工条件下,使用相同刀具和加工程序,刀具
的走刀轨迹完全相同,零件的一致性好,质量稳定。
(4) 生产率高
数控机床可有效地减少零件的加工时间和辅助时间,数控机床的主轴转速和进给量的范围大,允许机床进行大切削量的强力切削,数控机床目前正进入高速加工时代,数控机床移动部件的快速移动和定位及高速切削加工,减少了半成品的工序间周转时间,提高了生产效率。
(5) 改善劳动条件
数控机床加工前经调整好后,输入程序并启动,机床就能自动连续的进行加工,直至加工结束。操作者主要是程序的输入、编辑、装卸零件、刀具准备、加工状态的观测,零件的检验等工作,劳动强度极大降低,机床操作者的劳动趋于智力型工作。另外,机床一般是封闭式加工,即清洁,又安全。
(6) 利于生产管理现代化
数控机床的加工,可预先精确估计加工时间,所使用的刀具、夹具可进行规范化、现代化管理。数控机床使用数字信号与标准代码为控制信息,易于实现加工信息的标准化,目前已与计算机辅助设计与制造(CAD/CAM)有机地结合起来,是现代集成制造技术的基础。
3.数控机床使用中应注意的事项
使用数控机床之前,应仔细阅读机床使用说明书以及其他有关资料,以便正确操作使用机床,并注意以下几点:
(1) 机床操作、维修人员必须是掌握相应机床专业知识的专业人员或经过技术培训的人员,且必须按安全操作规程及安全操作规定操作机床;
(2) 非专业人员不得打开电柜门,打开电柜门前必须确认已经关掉了机床总电源开关。只有专业维修人员才允许打开电柜门,进行通电检修;
(3) 除一些供用户使用并可以改动的参数外,其它系统参数、主轴参数、伺服参数等,用户不能私自修改,否则将给操作者带来设备、工件、人身等伤害;
(4) 修改参数后,进行第一次加工时,机床在不装刀具和工件的情况下用机床锁住、单程序段等方式进行试运行,确认机床正常后再使用机床;
(5) 机床的PLC程序是机床制造商按机床需要设计的,不需要修改。不正确的修改,操作机床可能造成机床的损坏,甚至伤害操作者;
(6) 建议机床连续运行最多24小时,如果连续运行时间太长会影响电气系统和部分机械器件的寿命,从而会影响机床的精度;
(7) 机床全部连接器、接头等,不允许带电拔、插操作,否则将引起严重的后果。
二、数控机床的维护
数控系统是数控机床的核心部件,因此,数控机床的维护主要是数控系统的维护。数控系统经过一段较长时间的使用,电子元器件性能要老化甚至损坏,有些机械部件更是如此,为了尽量地延长元器件的寿命和零部件的磨损周期,防止各种故障,特别是恶性事故的发生,就必须对数控系统进行日常的维护。概括起来,要注意以下几个方面。
1.制订数控系统日常维护的规章制度
根据各种部件特点,确定各自保养条例。如明文规定哪些地方需要天天清理(如CNC系统的输入/输出单元——光电阅读机的清洁,检查机械结构部分是否润滑良好等),哪些
部件要定期检查或更换(如直流伺服电动机电刷和换向器应每月检查一次)。
2.应尽量少开数控柜和强电柜的门
因为在机加工车间的空气中一般都含有油雾、灰尘甚至金属粉末。一旦它们落在数控系统内的印制线路或电器件上,容易引起元器件间绝缘电阻下降,甚至导致元器件及印制线路的损坏。有的用户在夏天为了使数控系统超负荷长期工作,打开数控柜的门来散热,这是种绝不可取的方法,最终会导致数控系统的加速损坏。正确的方法是降低数控系统的外部环境温度。因此,应该有一种严格的规定,除非进行必要的调整和维修,不允许随便开启柜门,更不允许在使用时敞开柜门。
3.定时清扫数控柜的散热通风系统
应每天检查数控系统柜上各个冷却风扇工作是否正常,应视工作环境状况,每半年或每季度检查一次风道过滤器是否有堵塞现象。如果过滤网上灰尘积聚过多,需及时清理,否则将会引起数控系统柜内温度高(一般不允许超过55℃),造成过热报警或数控系统工作不可靠。
4.经常监视数控系统用的电网电压
FANUC公司生产的数控系统,允许电网电压在额定值的85%~110%的范围内波动。如果超出此范围,就会造成系统不能正常工作,甚至会引起数控系统内部电子部件损坏。
5.定期更换存储器用电池
FANUC公司所生产的数控系统内的存储器有两种:
(1) 不需电池保持的磁泡存储器。
(2) 需要用电池保持的CMOS RAM器件,为了在数控系统不通电期间能保持存储的内容,内部设有可充电电池维持电路,在数控系统通电时,由 5V电源经一个二极管向CMOS RAM供电,并对可充电电池进行充电;当数控系统切断电源时,则改为由电池供电来维持CMOS RAM内的信息,在一般情况下,即使电池尚未失效,也应每年更换一次电池,以便确保系统能正常工作。另外,一定要注意,电池的更换应在数控系统供电状态下进行。
6.数控系统长期不用时的维护
为提高数控系统的利用率和减少数控系统的故障,数控机床应满负荷使用,而不要长期闲置不用,由于某种原因,造成数控系统长期闲置不用时,为了避免数控系统损坏,需注意以下两点:
(1) 要经常给数控系统通电,特别是在环境湿度较大的梅雨季节更应如此,在机床锁住不动的情况下(即伺服电动机不转时),让数控系统空运行。利用电器元件本身的发热来驱散数控系统内的潮气,保证电子器件性能稳定可靠,实践证明,在空气湿度较大的地区,经常通电是降低故障率的一个有效措施。
(2) 数控机床采用直流进给伺服驱动和直流主轴伺服驱动的,应将电刷从直流电动机中取出,以免由于化学腐蚀作用,使换向器表面腐蚀,造成换向性能变坏,甚至使整台电动机损坏。
第18篇:车工 数控车工高级技师论文
车床钻攻六方螺母专用夹具的革新
摘要:设计制造该专用夹具适合在普通车床上加工中小批量TS300拖拉机专用左旋螺母内螺纹,解决了因机床的卡盘与尾座不会自动动作而反复停车装夹工件和拖动尾座的问题。
关键词: 普通车床 左旋螺母 钻攻夹具 不停车更换工件
丝攻卡具 传动误差 提高工效 降低劳动强度 普通车床,一般价格低廉,深受广大用户的欢迎,但其卡盘不会自动夹紧、尾座也不会自动进给,当使用该机床批量加工TS300拖拉机专用左旋螺母内螺纹时,必须反复装夹工件和拖动尾座,不但工作效率低下,而且增加了工人的劳动强度,本人为克服以上弊端,设计制作了六方螺母连续钻孔、攻丝夹具一套。
1、左旋六方螺母结构特点及工艺分析
左旋六方螺母是TS300型拖拉机前拉杆固定专用螺母,如下图1所示:
图1 左旋螺母
该螺母材料为冷锻毛坯,内孔有两毫米的加工余量,并带有内锥,加工时需先用钻头钻去两毫米的余量,然后用机攻丝锥攻丝完成。传统加工方法是把螺母夹持在卡盘上,钻头或丝锥安装在尾座套筒上,加工完工件后,退出尾座,从卡盘上卸下螺母,再安装下一件毛坯,这样反复操作,耗时耗力。
2、六方螺母专用夹具设计与分析
六方螺母专用夹具是结合六方螺母的自身特点和加工工艺需要量身制定的,该夹具结构形状如下图所示:
图2 六方螺母钻攻夹具
整个夹具是由导向槽部分和废刀杆焊接而成。
2 (1)T形型导向槽
该T型导向槽作用为工件毛坯的输送通道,整体由45号钢加工制作,为了便于输送工件,在导向槽的尾部上方开有一个上料缺口。前方槽口部位和后方Φ18的圆孔便于夹具的找正和工作中钻头与丝锥的进入和越位,槽宽和槽高与六方螺母自身形状尺寸相同,只是稍有间隙便于螺母在槽内滑动,并且槽对工件有定位的作用。根据工件的工艺特点与夹具的结构特点,该夹具可限制工件五个自由度,只有径向的移动没有限制,因为需要连续输送更换工件,所以工件应能在槽内灵活的径向移动。在加工过程中,夹具的中心线与机床主轴轴线等高,工件在夹具槽中由钻头或者丝攻前端的导向锥利用螺母本身的底孔自动定心,因此工件在连续加工过程中不用考虑工件的找正问题。
(2)Φ18圆形孔
该孔既是夹具的找正孔,同时也是钻头和攻丝的对正孔和越程孔,当钻头或丝锥切削部分越过该孔后方可退刀。
3、丝攻卡头结构分析与作用
在攻制内螺纹时,为了防止由机床丝杠与丝锥之间产生的传动误差,造成螺纹乱扣现象的发生,设计制作了专用丝攻卡头,如下图3所示,
图3 丝攻卡具装配图
1、套筒
2、卡头
3、圆柱销
4、紧固螺钉
5、丝锥
(1)零件1套筒,为了使丝攻卡具装夹牢固,不使套筒在攻制螺纹时与卡盘发生打滑现象,所以采用45号钢32×32六方材料车制而成,它即是卡具的安装套,又是卡头的导向套,它和卡头的配合应有合适的间隙。在套筒上铣有长10毫米宽6毫米的豆形槽,用以与件3圆柱销配合使用。
(2)零件2卡头,主要用于夹持丝锥,用45号钢车制,该零件最好热处理淬火。
(3)零件3圆柱销,采用标准件,该圆柱销与卡头为过盈配合,起到带动卡头旋转的作用并与套筒上的长10毫米,宽6毫米的豆形槽相配合,能使卡头在套筒内有4毫米的轴向窜动,用以消除传动误差,防止乱扣。
(4)零件4紧固螺钉,主要起到紧固丝锥的作用。
4、钻孔时夹具工作过程
工作前专用钻攻夹具在刀架上安装找正,然后用三爪自定心卡盘夹紧直柄钻头后对正夹具,启动机床后,在夹具的导向槽内放入工件,
4 使其基本对正导向孔,使钻头切削穿过工件后,大滑板横向移动退刀,然后在夹具导向槽内送入第二个工件,并顶出第一个工件,开始第二个工件的加工,如此循环操作。在更换工件期间机床主轴不需要停车,直至钻削加工完一定数量的六方螺母。
5、攻丝时夹具工作过程
首先用三爪自定心卡盘卡紧丝攻卡头后对正工件夹具,对刀完毕后,在专用夹具导向槽中送入已钻好孔的六方螺母,粗略对正后,即可攻丝,由于工件为左旋螺纹,所以机床主轴应反转时切削,当丝锥的切削部分穿过越程孔后,主轴正转退刀。滑板返程后,在T型导向槽内送入第二个工件同时顶出第二个工件,在主轴反转的同时,开始加工第二个工件,如此循环即可。
6、加工时须注意的问题
(1)由于该夹具工作效率较高,所以应充分冷却刀具,在攻制内螺纹时,由于主轴反复换向造成主电机发热,应采取冷却措施。
(2)找正时除用对刀孔对中心高外,注意保持夹具基准面与主轴轴线垂直。
(3)该夹具只能批量钻孔或者批量攻丝分离操作,若想实现钻攻结合连续动作可制作钻攻复合刀具。
(4)左旋螺母攻丝时卡盘应先反转,攻完螺纹后,停转,再正转退出。
(5)攻丝时和退出丝锥时,主轴旋转速度要必须保持恒定,以防螺纹导程不正确造成螺纹乱扣。
7、结论
(1)、使用了革新制作的夹具后,由工件转动改为刀具转动,而工件在夹具中不再转动,形成刀具与工件的位置置换,可实现不停车更换工件,省去了工件装夹的时间,降低了劳动强度,提高工作效率4倍。
(2)、该夹具结构简单,且易于制作,如加工其他小型零件钻攻工序可在原形状的基础上略加改造即可,造价低廉,易于推广。
8、参考文献:
(1)郑焕文,王宛山,《机械制造工艺学》.沈阳:东北工学院出版社,1988 (2)王先透,《机械制造工艺学》.北京:清华大学出版社,1989 (3)孙健,曾庆福,《机械制造工艺学》.北京:机械工业出版社,1989 (4)陈日耀,《金属切削原理》.北京:机械工业出版社,1991 (5)潘逊.《提高细长轴加工精度的措施》.《有色冶金节能》,2001 (6)庞学慧,辛志杰.《细长轴的轴向夹拉车削工艺》.《机械制造》,1997 (7)黄天铭,《机械制造工艺学》.重庆:重庆大学出版社,1998 (8)顾崇衔,《机械制造工艺学》.西安:陕西科学技术出版社,1989 (9)韩荣第,郭建亮,《细长杆车削浅析》,《机械研究与应用》,2004 (10)王公安,车工工艺学,中国劳动社会保障出版社,2005年6月第4版,2006年1月第3次印刷
第19篇:数控加工论文[1]
浅析数控加工中的过切现象及应对策略
赵玉刚$张$健$于光伟$胡$柳
(山东理工大学机械工程学院,山东淄博 %\"\"&’()
摘!要:数控系统在使用刀具半径补偿功能时,由于数控编程或工艺处理不当等,易产生工件过切现象。针
对以上过切现象,分析其原因并提出应对策略。
关键词:过切!刀具半径补偿!数控编程
中图分类号:\"#$%&! !文献标识码:’
!\"# $%&’()*) &%+ $+,-).*%/ 0#.\"1+ 213 45#3)*6# 7-..*%/ *% 787
)*+, -./01/,)*+23 4501,-6 3.01/785,*6 95.(:; =? @8; A1/5188B51/,:=/G,)5I= %\"\"&’(,J*2)
’()*+,-*:K58C,2J MB=/B0LL51/ =B F8; MB=;8EE 5E 510MMB=MB50F8,
780C F= =D8BE5N8 ;.FF51/O +10>GN51/ F
D8BE5N8 ;.FF51/O
./012+3):,D8BE5N8 J.FF51/;J.FF8B R0C5.E J=LM81E0F5=1;2J SB=/B0LL51/
近些年,由于数控加工的需要,大部分数控系统都废。本文针对经常出现的几种过切情况进行分析,给
已经具备了刀具半径补偿功能。在编程时,技术人员出应对策略并加以实现。 只需给出刀具半径值,并按照工件轮廓轨迹编制程序 $!数控加工中的过切现象及应对策略
代码,而不必经过繁琐的计算得到刀具中心轨迹路径。 这种只需改变刀具半径而无需改变程序就可以实现不$O $!加工小于刀具半径的内圆弧面
同刀具的数控加工,为数控加工带来方便。然而,数控当加工内轮廓圆弧,圆弧的半径小于刀具半径值
机床在加工中,由于编程轨迹处理不当、工艺过程处理时,此段圆弧刀具半径补偿将会导致过切,数控系统出
不当等原因导致切削过量现象,称为“过切”[!]。过切现报警提醒并停止于将要过切语句的起始位置[%]。 现象直接影响工件的表面质量,甚至导致加工产品报图!在加工圆弧!!&拐角处,半径为!!\" 的刀具
))))))))))))))))))))))))))))))))))))))))))))))))
备倍受推崇。因此笔者认为,柔性化生产和敏捷性生 %!缸体生产线工艺发展趋势
产是缸体生产线的工艺发展趋势。
汽车行业是一个技术密集型、资金密集性、劳动密参考文献
集型的产业,基于节省投资的需要,要求发动机生产线[!]叶伟昌O改进珩磨头结构提高珩孔质量[4]O机械工艺师,!((T(#)O 尽可能满足多品种生产的需要。同时由于国际环保和[%]葛延翔,郑云龙O缸孔平台网纹珩磨的评定方法和工艺实践[ 4]O汽
节能呼声的高涨,各国对汽车的排放、油耗提出了更高车制造业,%&&’(#)O 的限制,因此要求产品开发人员对发动机的持续性升[U]陶前昭,李胜柱O缸孔平台网纹珩磨工艺[
4]O现代制造工程,%&&%
级和改进已成为现实。所以发动机生产模式由传统的(U)O 少品种、大批量的生产模式向多品种、中小批量的生产 作者:董克安,男,!(T%年生,工程师,技术部长,
模式过渡,从而柔性化生产和敏捷性生产的重要性也主要从事发动机的生产制造工作,致力于新技术、新工
日益在发动机领域突显出来。美国福特公司、日本本艺的研发应用。
田公司等国际汽车龙头企业越来越关注发动机的柔性(编辑$谭弘颖)$$ 化生产和敏捷性生产,从而在发动机机加工生产线中,(收稿日期:%&!& V&W V!W)$$
文章编号:!!&!’\"象立式加工中心、卧式加工中心等具有相当柔性的设 如果您想发表对本文的看法,请将文章编号填入读者意见调查表中的相应位置。
·$ $$!\"# ·
出现过切现象,若机床不停止加工,在两个端点处出现
阴影部分的过切区域。因
此针对此种情况,若对过渡
圆弧有尺寸要求,应使得刀
具半径值小于加工的圆弧
半径;若要求不是很严格,
在做刀补处理时,可以省略
过渡圆弧,用刀具外形轮廓
代替需要加工的圆角。
!% \"#加工长度小于刀具直
径的沟槽
!% &% !$刀具过切现象
如图
&所示,被加工凹
槽底部宽度小于刀具直径
时,启动刀具半径补偿功
能,刀具中心轨迹为 ’! (!
)!*! ,在 (!、)! 点处出现过
切削区域如图 &阴影部分。
在这种情况下,机床数控系
统会报警并停留在该程序
段的起点位置。
!% &% &$刀具过切现象的应
对策略
若想加工出底部凹槽,需更改刀具,缩小刀具半
径,使得刀具直径值小于底部凹槽 ()的长度;若受到
加工条件的限制,不能改变刀具,此种情况只能改变刀
具半径补偿功能,附加一个过切判断。在刀具半径补
偿中,可以通过编程矢量与其相对应的修正矢量的标
量积的正负进行判别。在上图中,!\"为编程矢量,!!
\" ! 为
!\"对应的修正矢量,!为它们之间的夹角。则
标量积为
!\"·!! \" ! !\" !! \" ! \"\" !! \" ! + ,-.!(!)
显然,当 !\"·!! \" ! /0(即 102 / ! / )时,刀
具就要背向编程轨迹移动,造成过切削。图 &中 ! 3
!402,所以必定产生过切削。
假设
#! 坐标为($0,%0),&! 坐标为( $! ,%! ),刀具
中心轨迹的交点 ’($,%),且 #! !! 的单位方向向量为 (($0,(%0),\" ! $! 的单位方向向量为(($! ,(%! ),则存在
如下的关系式:
{($0)$)(%0)(%0)%)($0!0($)$! )(%!)(%!)%)($!!0 (&)
可得到刀具中心轨迹的交点’,从而将没有过切 判断的刀具中心轨迹*!#!&!+! ,
经过切判断并简化刀
具轨迹为 * ! ’+! ,这样可以解决过切问题,但不能加工
出底部的凹槽。图
5为凹槽过切时,刀具半径补偿经
过切判断,改变了走刀路线,避免了过切。
!, $#尖角加工的过切现象及处理 !, 5, !$刀具半径过大的情况 在数控加工中经常会
出现尖角情况,若刀具半径 足够小,加工的刀具轨迹可 以无限接近凹角顶点;但若
刀具半径很大,超过了夹角 端口的宽度,不仅此处凹角
不能加工,而且对其他轮廓轨迹带来过切。图 6为尖
角加工的过切现象,阴影部分为刀具在交点处的过切 区域。
尖角加工的刀具半径补偿功能的过切判断与上面 凹槽的判断相似,将编程轨迹 #&与刀具中心轨迹 !! \" ! 做矢量乘积,判断正负,从而得到是否过切。若对 此种过渡类型的加工无严格要求,可以简化刀具轨迹, 即得到 #! !! 与 \" ! $! 的交点,最终刀具中心轨迹为 * ! ’+! 。图
\"是加工尖角,出现过切现象时,经过切判断 而简化的刀具中心轨迹。
图
\"中,内圈图形为无刀补的刀具中心轨迹(即 轮廓轨迹),外圈为半径为 !0 77的刀具中心轨迹,在
右侧尖角处出现过切现象,刀具半径补偿功能经过切 判断,对原始的刀具路径轨迹进行修改,形成新的刀具 路径。
·$ $$!\"# ·
!% &% ’$内角交接处的过切
加工零件内角时,刀具半径小于内角端口的宽度 也可能产生过切,原因如下:(!)当刀具运动至内角交 点处,刀具与工件的接触面积增大,致使工件作用于刀 具的切削力增大,转过拐角时,刀具变为单面作用,切 削力减小,工艺系统弹性变形恢复,导致刀具向工件加 工侧延伸,产生过切;大惯性系统,
(’)对于大增益、进
给速度过高,其运动惯性导致工件过切[&]。
应对策略:(!)选择刚性好,抗振及受热应力变形 小的短柄刀具;(’)采用进给速度的分级,使得在拐角 处降低进给速度,从而减小刀具惯性,达到减小过切区 域的目的。
!\" #$刀具半径补偿的建立与
!轴的切入操作
开始加工工件前,在即将接触工件的位置建立刀 具半径补偿,再进行
!轴方向的切入,为保证程序运
行后得到正确的工件轮廓而不产生过切,编程时须注 意加工程序的结构[(]。
))))! *! +,) +\"( -!))) .)& *’ +)) /!)) *& 0) 1) *( +)! +(! 0’) 1!) 23 4!)) *\" /’ *3 /5!) *6 1\") *# 0\") *, 1’) *!) 0!) *!! +)) /!)) *!’ +() 0) 1) *!& .)\" *!( .)’
根据刀具半径补偿功 能编程规则,在
\"#$平面
内建立刀具半径补偿后,不 能连续出现两段 !轴的移
动指令,否则会出现补偿位 置不正确,系统无法获得下 一步补偿矢量,系统并不报 警,补偿照样进行,从而出 现过切现象,如图 3所示。
为避免过切现象的发生,对刀具半径补偿功能的 源程序进行修订,在获得刀具建立行后,继续读取程序 行,直到获得下一段程序的补偿矢量(即 *6行),而此
种判断是通过加工指令与 \"#$平面坐标关系判定的。 图
6所示,是对刀补程序进行修订后得到的模拟仿真
·$ $$!\"# ·
图。
!% %$各轴速度滞后性引起的过切
加工转角为直角的工件轮廓,其刀具中心正好沿
着两正交轴移动,在某一坐标伺服系统的位置为加工 终点,而另一个正交轴伺服系统紧接着接受位置指令, 速度瞬间从零加速至指定值。但在两正交轴改变的瞬 间,第一正交轴对指令位置有滞后性,使得第二正交轴 加速时,第一正交轴未到达拐点,出现过切。
应对策略:(!)在编程时,对第一正交轴采用分级 加度,或编程轨迹改变时有自动减速和加速功能;(’) 改变编程中正交轴的位置;(&)编程时在拐角处停留 一段时间[\"]。
&$结语
以上分析了数控加工过程中的几种过切现象及应 对策略。当然,引起过切的因素是多方面的,在编制数 控加工程序时,需综合考虑零件结构、刀具选择和编制 的数控程序代码等,才能得到规定的工件形状。
参考文献
[!]黄登红,王建平%刀具半径补偿中的过切现象及对策探讨[ 7]%现代 制造工程,’))\"(!)):’! 5’’% [’]唐和业,梅江平%由“刀具半径补偿”引起的过切现象[ 7]%数控技 术,’))\"(!’):63 566% [&]丁跃浇%数控铣床加工中的过切现象浅析[ 7]%机械设计与制造, ’))&(():#’ 5#&% [(]王粟%数控加工中心的过切现象分析[ 7]%计算机应用,’))\"(\"):\"\" 5 \"3% [\"]张伟%数控铣削中过切现象分析研究[7]%机械制造与研究,’))\",&( (():&\" 5&3,&,% 第一作者:赵玉刚,男,教授,主要研究方向为数控 技术及特种加工,已发表论文 36篇。
(编辑$余$捷)$$ (收稿日期:’)!) 5)\" 5!,)$$
文章编号:!!)!(3 如果您想发表对本文的看法,请将文章编号填入读者意见调查表中的相应位置。
第20篇:数控车技师论文
数控机床加工工艺路线的研究
理想的加工程序不仅应保证加工出符合图样的合格工件,同时应能使数控机床的功能得到合理的应用和充分的发挥。数控机床是一种高效率的自动化设备,它的效率高于普通机床的2——3倍,所以,要充分发挥数控机床的这一特点,必须熟练掌握其性能、特点、使用操作方法,同时还必须在编程之前正确地确定加工方案。
在数控机床加工过程中,由于加工对象复杂多样,特别是轮廓曲线的形状及位置千变万化,加上材料不同、批量不同等多方面因素的影响,在对具体零件制定加工方案时,应该进行具体分析和区别对待,灵活处理。只有这样,才能使制定的加工方案合理,从而达到质量优、效率高和成本低的目的。
在对加工工艺进行认真和仔细的分析后,制定加工方案的一般原则为先粗后精,先近后远,先内后外,程序段最少,走刀路线最短,由于生产规模的差异,对于同一零件的加工方案是有所不同的,应根据具体条件,选择经济、合理的工艺方案。
1、加工工序划分
在数控机床上加工零件,工序可以比较集中,一次装夹应尽可能完成全部工序。与普通机床加工相比,加工工序划分有其自己的特点,常用的工序划分原则有以下两种。
1.1 保证精度的原则
数控加工要求工序尽可能集中。常常粗、精加工在一次装夹下完成,为减少热变形和切削力变形对工件的形状、位置精度、尺寸精度和表面粗糙度的影响,应将粗、精加工分开进行。对轴类或盘类零件,将各处先粗加工,留少量余量精加工,来保证表面质量要求。同时,对一些箱体工件,为保证孔的加工精度,应先加工表面而后加工孔。
1.2 提高生产效率的原则
数控加工中,为减少换刀次数,节省换刀时间,应将需用同一把刀加工的加工部位全部完成后,再换另一把刀来加工其它部位。同时应尽量减少空行程,用同一把刀加工工件的多个部位时,应以最短的路线到达各加工部位。
实际中,数控加工工序要根据具体零件的结构特点、技术要求等情况综合考虑。
2、加工路线的确定六剑客职教园(最大的免费职教教学资源站)
在数控加工中,刀具(严格说是刀位点)相对于工件的运动轨迹和方向称为加工路线。即刀具从对刀点开始运动起,直至结束加工程序所经过的路径,包括切削加工的路径及刀具引入、返回等非切削空行程。影响走刀路线的因素很多,有工艺方法、工件材料及其状态、加工精度及表面粗糙度要求、工件刚度、加工余量,刀具的刚度、耐用度及状态,机床类型与性能等,加工路线的确定首先必须保证被加工零件的尺寸精度和表面质量,其次考虑数值计算简单,走刀路线尽量短,效率较高等。
下面举例分析研究数控机床加工零件时常用的加工路线。
2.1车圆锥的加工路线分析
数控车床上车外圆锥,假设圆锥大径为D,小径为d,锥长为L,车圆锥的加工路线如图1所示。
图1 车圆锥的加工路线
按图1(a)的阶梯切削路线,二刀粗车,最后一刀精车;二刀粗车的终刀距S要作精确的计算,可有相似三角形得:
此种加工路线,粗车时,刀具背吃刀量相同,但精车时,背吃刀量不同;同时刀具切削运动的路线最短。
按图1(b)的相似斜线切削路线,也需计算粗车时终刀距S,同样由相似三角形可计算得:
按此种加工路线,刀具切削运动的距离较短。
按图1(c)的斜线加工路线,只需确定了每次背吃刀量ap,而不需计算终刀距,编程方便。但在每次切削中背吃刀量是变化的,且刀具切削运动的路线较长。
2.2 车圆弧的加工路线分析
应用G02(或G03)指令车圆弧,若用一刀就把圆弧加工出来,这样吃刀量太大,容易打刀。所以,实际车圆弧时,需要多刀加工,先将大多余量切除,最后才车得所需圆弧。
下面研究分析车圆弧常用加工路线。
图2 圆弧切削路线的形式
在图2中,a图表示为同心圆形式,b图表示为等径圆弧(不同圆心)形式,c图表示为三角形形式,d图表示为梯形形式。不同形式的切削路线有不同的特点,了解它们各自的特点,有利于合理地安排其走刀路线。现分析上述几种切削路线:程序段数最少的为同心圆形式及等径圆形式;走刀路线最短的为同心圆形式,其余依次为三角形梯形及等径圆形式;计算和编程最简单的为等径圆形式(可利用程序循环功能),其余依次为同心圆、三角形式和梯形形式:金属切除率最高、切削力分布最合理的为梯形形式;精车余量均匀的为同心圆形式。
图3 阶梯切削路线的车圆弧
图3为车圆弧的阶梯切削路线。即先粗车成阶梯,最后一刀精车出圆弧。此方法在确定了每刀吃刀量ap后,须精确计算出粗车的终刀距S,即求圆弧与直线的交点。此方法刀具切削运动距离较短,但数值计算较繁。
图4 同心圆弧切削路线车圆弧
图4为车圆弧的同心圆弧切削路线。即用不同的半径圆来车削,最后将所需圆弧加工出来。此方法在确定了每次吃刀量ap后,对90°圆弧的起点、终点坐标较易确定,数值计算简单,编程方便,常采用。但按图4b加工时,空行程时间较长。
图5 车锥法切削路线车圆弧
图5为车圆弧的车锥法切削路线。即先车一个圆锥,再车圆弧。
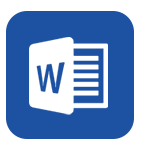