声威水泥公司生产实习
一、单位简介
陕西声威建材集团有限公司,创建于2003年4月,是一家以生产和销售水泥为主的大型民营股份制企业。是陕西省水泥行业龙头企业之一。200
7、2008年连续两年水泥销售总量排名全省第一。集团注册资金2.3亿元人民币。至2010年12月底集团总资产23亿元,员工1800多人,集团现拥有泾阳声威、铜川声威、凤县声威、安塞声威、榆林声威、浙江声威六家水泥生产企业。目前,集团已形成了集约化、规模化、集团化发展模式。铜川声威水泥是“全国水泥行业60家重点扶持企业”声威集团下属企业铜川声威建材有限责任公司建于2003年11月,总投资近10亿元,是一家集水泥、熟料生产、销售、矿山开采为一体的大型建材环保企业。公司占地700多亩,位于铜川市黄堡镇,陕西省优秀外来投资企业及铜川市重点企业。
铜川声威共规划建设三条5000吨生产线,一期5000t/d水泥熟料生产线项目,由声威集团投资4.3亿元,于2004年2月28日动工,2005年6月28日投产,生产高标号水泥100万吨,商品熟料70万吨,实现年销售收入29600万元,税金2740万元。铜川声威第二条5000t/d水泥熟料生产线于2009年投产。声威三期正在建设当中。预计铜川声威三条生产线全部建成投产后,产值将达到达12亿、利润2.4亿,税金9000万元。
铜川声威所投建的大型水泥熟料生产线均为工艺最为先进的干法生产线,采用当前行业先进的悬浮预热窑外分解干法燃烧生产工艺,导入全自动化的dcs集散型过程控制系统与qcx在线质量控制系统,充分利用模拟数字与计算机技术,实行中央控制室电视监测,摇控操作,可保证生产安全和产品的稳定优质。这些项目符合国家产业结构调整政策,属国家发改委鼓励和发展项目,其采用的新型干法工艺,处于国际领先水平,代表当今水泥行业的发展方向。
铜川声威注重企业的高速稳定发展,同时尤为关注发展循环经济、环境的保护以及资源的整合重组及再利用。2008年6月,作为发展循环经济的重要途径的铜川声威一期项目配套的纯低温余热发电项目正式开工建设,预计于2009年2并网发电。该低温余热发电项目工程装机容量9wm ,包括两炉一机,项目总投资5000万元,年发电量可达6000万千瓦,年供电量5500万千瓦,每年可节约标准煤2.26万吨,减少二氧化碳排放量2.7万吨。
铜川声威建材有限责任公司是声威集团实施西部大开发战略,实现集团跨跃式多布局发展的重点环节。铜川声威将凭借铜川市高品质自备石灰石矿产资源,先进的设备工艺,全新的公司治理结构,灵活的管理机制,多年的技术积累,打造成陕西省一流的花园式水泥工业企业。
二、安全教育
虽然我们只是厂里普通的实习生,但厂里对我们的安全教育毫不松懈。为了防止不安全事故发生,在进厂的第一天老师和厂里的领导就对我们进行了安全教育,具体要求如下:
(1)不动不懂不清楚的设备,对于不懂的设备,严禁随意操作,防止设备停转或导致安全事故发生。
(2)必须佩带安全帽,安全帽对人身安全起了关键的保护作用,要求入厂就必须佩带安全帽,在职员工少佩带一次安全帽罚款200元。
(3)注意自身的安全行为,不做有安全隐患的事情,保护好自身和设备. (4)“三不伤害”,即不伤害别人,不伤害自己,不被别人伤害。
(5)认真听从车间安排,由于生产现场工人少,实习人数多,所以进入每个车间都要听从安排,排队参观,不影响生产。
(6)有安全意识,到生产现场时,要注意上下左右前后看,避免踩空,撞头,跌落,被运行中的设备伤害,触电等危险。
(7)不拥挤,不单独行动,实习参观时,有序参观,遇到突发情况不慌张,不拥挤,不随意单独行动。
三、水泥生产工艺流程说明
新型干法水泥技术,是指以悬浮预热和预分解技术为核心,并采用计算机及其网络化信息技术进行水泥工业生产的综合技术。其内容主要有:原料矿山石灰石破碎、原料粉磨、原燃材料预均化、生料预均化、新型节能粉磨、高效预热器和分解炉、新型篦式冷却机、高耐热耐磨及隔热材料、计算机及网络化信息技术等。使用以上技术进行水泥生产的优点是高效、优质、节能、节约资源、符合环保和可持续发展的要求。其特点是:生产大型化,完全自动化、能实现废弃物的再利用,是发展循环经济的切入点。
整个工厂分为原料车间,烧成车间,水泥车间,中控室,检验室,余热发电六个车间。从矿山向厂内依次是预均化堆场,立磨,悬浮预热器系统,回转窑,篦冷机,熟料库,熟料库熟料经过均化后,通过皮带输送到水泥粉磨车间,依次经过配料站,打散机,磨机,水泥磨,水泥库,包装机,出厂。所有数据都反映到中控室,经中控室和一线人员协调后直接操做各步骤情况,如调整喷煤量来调整回转窑温度等。
(一)、水泥生产工艺过程
干法窑外分解工艺主要包括生料制备、熟料烧成和水泥粉磨三个部分。简述如下:
1、生料制备
生料粉磨的目的就是要使生料的细度适于将其烧成熟料。
破碎及预均化
(1)破碎 破碎过程要比粉磨过程经济而方便,合理选用破碎设备和和粉磨设备非常重要。在物料进入粉磨设备之前,尽可能将大块物料破碎至细小、均匀的粒度,以减轻粉磨设备的负荷,提高黂机的产量。物料破碎后,可减少在运输和贮存过程中不同粒度物料的分离现象,有得于制得成分均匀的生料,提高配料的准确性。
(2)原料预均化 预均化技术就是在原料的存、取过程中,运用科学的堆取料技术,实现原料的初步均化,使原料堆场同时具备贮存与均化的功能。 原料预均化的基本原理就是在物料堆放时,由堆料机把进来的原料连续地按一定的方式堆成尽可能多的相互平行、上下重叠和相同厚度的料层。取料时,在垂直于料层的方向,尽可能同时切取所有料层,依次切取,直到取完,即“平铺直取”。
注:生料原料的来源
矿山开采的灰岩矿石进厂后,经单段锤式破碎机破碎,破碎后的石灰岩原料用皮带运输机运至碎石预均化堆场中进行均化及储存。
粘土由在厂区内开采,汽车拉运进厂,储存于粘土堆棚。铁质校正原料用铜矿渣,由汽车运输进厂储存于铜渣堆棚。硅质校正原料采用砂岩,汽车运输进厂储存于砂岩堆场(露天)。
石灰石、粘土和铜矿渣、砂岩在配料站经电子皮带秤计量配料后由皮带运输机送至atox50生料磨立磨粉磨,烘干热源采用窑尾废气。
出磨生料由高浓度电除尘收集后送至连续式均化库均化并储存;出库生料经固定流量计计量后由喂料设备送至窑尾的预热器预热分解。
2、熟料烧成
燃料:
熟料煅烧所用燃料主是烟煤,由汽车运输进厂存储于原煤预均化堆棚中,经均化后由皮带运输机送至原煤仓缓存,然后经除铁器除铁,电子皮带称计量后进入立式辊磨系统进行煤粉制备,成品煤粉储存于窑头、分解炉煤粉仓中以备用;烘干介质采用窑头篦冷机的废气。成品煤粉分别经各自的菲斯特计量称计量后由气力输送设备送至回转窑和分解炉作燃料。
水泥熟料是使合格的水泥生料在预分解系统、回转窑系统进行加热煅烧(温度需达到一定的要求:约1450度左右),经过一系列复杂的物理化学反应后,变成高熟料,再对高温熟料进行冷却后的形成的产品。
生料在带喷旋管道式分解炉的五级旋风预热系统,经预热、部份分解后进入分解炉,由煤粉制备系统来的煤粉喷入分解炉内燃烧提供热量,加热分解,一般分解率可达90%-95%,然后进入回转窑窑尾,通过窑头喷煤管喷入煤粉在窑内燃烧,随着回转窑的转动,生料向窑头移动,在烧结带经1450°c加热形成熟料,烧成熟料经篦冷机冷却后,送至熟料库存储。
3、水泥粉磨
水泥粉磨原料主要有几种:
熟料:从熟料库经由皮带输送机运送至水泥配料站熟料小库。
石膏:石膏由汽车运输进厂,存放在堆棚中。再由铲车从石膏堆棚铲入破碎机喂料坑,破碎后经皮带输送机、斗式提升机送入水泥配料站石膏小库。
煤矸石:煤矸石由汽车运输进厂露天分别堆放备用。再由铲车从煤矸堆场铲入破碎机喂料坑,破碎后经皮带输送机、斗式提升机送入水泥配料站煤矸石小库。
石粉:石粉由汽车运进厂存储于石粉堆棚中待用。由铲车将其从堆棚铲入石粉喂料坑,经皮带输送机、斗式提升机送入水泥配料站小库。砂岩:砂岩由汽车运输进厂,存放在堆棚中。再由铲车从砂岩堆棚铲入破碎机喂料坑,破碎后经皮带输送机,斗式提升机送入水泥配料站砂岩库。
水泥粉磨是水泥制造的最后一道主要工序。其主要功能为将水泥熟料、缓凝剂(即石膏)及性能调节材料(即各种混合材)等粉磨到一定的细度,形成一定的颗粒级配以满足水泥混凝凝土浆体的施工、凝结、硬化等指标要求。
从配料站库来的各种材料如:熟料、石膏、煤矸石、硫酸渣、砂岩等经电子皮带秤计量后进入辊压机中挤压、粉碎,再经斗式提升机输送,分选后符合一定粒度要求的物料进入磨机,在开流高细高产水泥磨中进行粉磨,出磨水泥经提升机、空气输送斜槽送入水泥库储存(依不种粉磨品种进入不同的成品库);由水泥库底卸出的水泥经斜槽、提升机、斜槽、中间小仓进入包装机,包装好的水泥经皮带运输机送至成品库或直接装车出厂。散装水泥依品种不同分别进入各自小仓,然后密封输送至水泥散装车,散装车辆经地磅计量后出厂。
(二)、水泥生产工艺特点
1、首先水泥厂是一个高耗行业,其主要能源消耗为石油类、天然气类、煤碳类、电力等;不管是传统窑型还是最新型研发或新建的工艺型式,消耗的能源大部份均为一次直接能源,为不可再生能源;我国除早期引进设设的生产线为烧重油类外,余大多数均以煤碳作为能源,当然电力消耗为二次能源,但其大多出于火力发电厂,火力发电主要还是消耗煤碳类能源。因此节能降耗、寻找使用代替能源是每一位水泥工作长期的追求。
2、作为2005年新建的现代化大型水泥企业,其工艺应用系统大部份遵循节能降耗原则,采用新型成熟窑外预分解生产工艺,与传统立窑、湿法窑、干法中窑窑、立波尔窑、旋风预热器窑相比,节能方面具有非常明显的优点,其与传窑型最大的区别在于把生料的预热、分解任务大部份放在预热器系统,使其在系统内得以快速悬浮分散、换热,且换热效率大幅度提高,并且约有60%燃料在这个系统中燃烧放热、换热,极大地减轻了窑内热负荷,延长了耐火衬料的使用寿命;回转窑只承担少量的碳酸盐分解,主要承担物料的烧结任务,使窑速得以大幅度提升,单位容积产能大幅度升高。另外,生料制备中烘干热采用窑尾废气,生料的预热、脱水,部份分解在c1-c4旋风筒及其相关管路中,除有效降低废气出口温度外,还把相当大一部份余热得以回收利用。煤粉的制备采用窑实篦冷机多余废气作烘干源,同样大幅度回收热量。篦冷机高温段的废气作为二三次风分别进入窑内及分解炉为煤粉的燃烧提供o2,回收热量可观。因此该系统在国内水泥企业当中属先进水平,在国际上也具有较明显的优势,达到发达国家中上游水平。
3、采用abb公司集散控制系统,所有设备运行、参数控制、参数调节、质理控制均在中央控室中进行;现场分若干个中继站,设置系列的传感器、变送器、并通过高速光纤实现数据与中央控制室实时传输交换。具有自动化程度高,劳生产率高,单位熟料投资少等特点。
4、采用较多新型节能设备、采取了较多的节能管理措施,使能耗指标达到全国优良水平。
5、在传统工艺中,水泥行业给人的感觉是高污染行业,与脏乱差挂钩,声威水泥厂属新建新型窑外分解大型企业,环保设施、环保管理均得以质的飞跃,厂区内空气清新、绿树成荫、鸟语花香,根本看不到丝毫“脏”的表现,是环保清洁型企业。
(三)、水泥生产工艺先进性
干法窑外分解生产工艺是当今国内普遍采用的水泥生产新技术,具有工艺先进、可靠、机械化和自动化程度高、节能、减污效果好,产品质量好,产量高等优点。
该工艺把水泥生产中的熟料燃烧分为预热、分解和烧成三个过程,根据反应过程分别在预热器、分解炉和回转窑中进行。
(四)、节能先进措施有以下几方面:
1、厂址选位于李家沟柒家山的一个荒谷里,只占用了极少的一部分耕地。
2、自初步设计开始,厂方与设计院方就进行反复磋商、论证,工艺布置充分利厂内山坡地势特点,从高至低布置生产线,有效降低了构筑物高度,缩短了物料的转运输送距离,降低了物料提升高度,从而大大有效地降低了物料转运输送及提升功率,降低了单位产品电耗。
3、响应行业“上大关小”的潮流,毅然决定在铜川建立5000t/d熟料生产线,现今产量已达5600t/d,是目前为止陕西省内水泥行业单线生产能力最大的企业;在设备选型上大胆采用新工艺新技术,为降低单位产品能耗起着关键的作用:
? 采用丹麦fls公司生产的生料立磨系统,设计能力430t/h,目前台产已达
480t/h,该生料系统集原料烘干与粉磨一体,充分利用窑尾废气余热,不必专设烘干机,大大增加废气的利用率,提高热回收率,有效的降低了熟料的单位热耗;在粉磨原理上,利用拉杆给物料施加压力,通过物料间的剪切、挤压、研磨作用,使物料得以细磨,达到了“以破代磨”的作用,与传统球磨机相比可以降低30%的电耗。
? 采用德国菲凡公司技术国内制造的煤立磨,集烘干粉磨一体,同样大幅度
降低了单位产品的热耗及电耗。
? 采用南京水泥设计院的低压损防堵高效预分解系统,在5600t/d时,c1出
口压力只有5400—5600pa左右,c1出口温度只有315℃左右,有效地降低了废气热损,降低了系统热耗及电耗。
? 采用第三代控制流空气梁篦冷机,二次风温达1150℃,三次风温达900℃,
热回收率>70%,有效降低系统热耗,降低标煤耗量.
? 企业内部大力挖掘系统潜力,提高台时产量、提高设备运转率,有效降低
各种消耗;在配料方面优化各种方案,改良生料易烧性,充分利用谷电,避开峰电,一方面降低电网负荷,另一方面又给企业增加了效益。
? 大型高压设备采用功率补偿技术,大幅度提高了功率因素,有效降低无用
功,降低单位产品电耗。
? 水泥粉磨系统采用辊压机+打散机预粉磨系统,单位产品电耗与传统方法相
比可降低30%。另一方面采用煤矸石,粉煤灰、工业副石膏等废弃物作混合材,掺入量依产品种类计划最高可达30%,年利用废弃物可达26万吨以上;另外,依据市场及国家相关法规,最终目标争取发散率达70%以上。
? 通过种种措施,目前生产线的综合熟料电耗已降至67kw.h/t以下,热耗可
以达到780大卡以下,达到了行业内的优良水平。
4、环保、减排及利废方面:目前企业建设项目竣工环评早已通过验收。
在废气治理方面,共选用各类收尘器46台,其中高压静电收尘器2台,高效袋式收尘器44台,经监测均达到《水泥厂大气污染物排放标准》规定要求;废水循环使用,重复利用率达到了95%以上,所排废水中主要污染物均达到《污水综合排放标准》的规定要求;采用封闭、负压操作、提高除尘设备完好率、投入率等方法有效控粉尘控的排放;采用增加隔离、消音装置使噪声尽量降至最低。随着国家对减排的要求越来越严格,在这方面的管理、技改的投入力度将进一步加大。 ? 2006年5月成立了安全环保科,设立专门机构专人负责。 ? 2006年水泥系统投产后,采用煤矸石、粉煤灰、工业副石膏等废弃物作混合
材,掺入量依产品种类计划达10—35%,年利用废弃物可达20万吨以上;另外,依据市场及国家相关法规,我们争取发散率达到50%以上。
? 集团为了发展循环经济,准备投资0.5亿元,配套建设生产线的纯低温余热
发电项目。07年8月5日院方来人将进行具体参数标定。现在正施工建设当中,该项目完成后吨熟料产生的余热可发电30千瓦时,每年可减少外购电4853万千瓦时,可节约标煤2.26万吨,减少二氧化碳排放量2.25万吨,减少二氧化硫排放量0.15万吨。 ? 针对厂内夏季部份设备轴承温度偏听高需增补部份清水冷却并外排的情
况,07年4月份决定把这部份水回收利用, 7月底主体完工,同年8月份投入使用,生产上真正实现水资源零排放。
? 新型回转窑还是理想的焚烧炉,不但温度高,且停留时间长,是分解有毒废
弃物最理想的焚烧设备,同时有毒的重金属还可以固化在熟料中,在限量下不影响水泥质量和安全。如果条件具备成熟,我们将乐意进行这方面的试验及应用。
(五)、水泥生产工艺能源消耗情况
下面按照新型干法水泥生产的工艺过程,介绍一下工艺过程的能源消耗情况。
1、生料制备:生料制备工序中主要消耗的能源是电能。其主要用于破碎石灰石的破碎机、粉磨生料的立式烘干磨、制备煤粉的煤磨以及用于提运各种物料的提升机、运输机、生料均化过程中用来提供搅拌和卸运需用的压力空气的罗茨风机等用电设备。
2、熟料烧成:熟料烧成工序中主要消耗的能源是煤和电力。煤主要消耗在用于熟料煅烧的回转窑和窑尾带喷旋管道分解炉的五级旋风预热器系统,煤粉约60%在分解炉中燃烧,约40%在回转窑内燃烧。电力主要消耗在用于熟料冷却和破碎的篦冷机以及预热器系统和收尘系统的风机等。
3、水泥粉磨:水泥粉磨工序中主要消耗的是电力,而且是消耗电力较多的工序。电力主要用于粉磨熟料、石膏、矿渣等的辊压机、打散机、球磨机等以及提运物料的皮带机和提升机、空气气斜槽、各类风机等。
4.所有设备均存在能耗效率,其无用功损耗也是其中之一,另外输电线路、变压器等的损耗也是一部份。
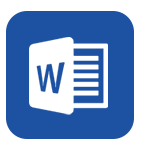