推荐第1篇:家用空调换热器设计
家用空调换热器设计
一、蒸发器的设计
对于家用空调器的开发,只有少数新产品是需要重新开发新模具,设计新的外形结构,而大多数产品开发只是在原有外形尺寸下进行换热器重新设计,这样我们在设计时换热器的结构尺寸基本上没有调节的可能了,当然,如果在给定的结构尺寸下,我们所选定的蒸器不能满足规格的要求,最常用的方法在原有的基础上增加小块翅片,以增加换热面积,若仍不能满足规格要求,我们只有尝试使用具有较大换热面积的室内机。
下面谈谈对于蒸发器几何尺寸一定情况下回路设计的方法。首先我们要确定蒸发器的流路数,然后再依据流路数来考虑每个流路制冷剂的流向。
1.流路数确定。制冷剂在蒸发器的变化是从饱和的液体(实际上也含有少量节流后闪发的气体)开始吸热后一部分液体气化后变成气体,随着制冷剂的流动,铜管内气体量不断增多,制冷剂的流速随着体积的增大而增大,此时的流动阻力也增大,当所有制冷剂全部变成气体后,若仍继续换热,制冷剂的所进行的就是显热交热,其换热系数很低,因此为了保证蒸发器的利用率较高,我们在系统调试时应尽量使制冷剂在蒸发器内刚刚完全蒸发,当然这个问题与流路数的确定并不相关,在这里就不再讨论。根据传热学的基本知识,我们知道较高的制冷剂流速可以获得换热系数,从而提高制冷系统的制冷量,但由流体力学的知识我们可以知道,制冷剂的流动阻力随着其流速增大而增加,因此会导致蒸发器内制冷剂的压降增加,从而降低了压缩机的吸入压力,而压缩机的吸气压力对于压缩机的出力有着很明显的影响,因此我们在确定流路数时应折衷考虑这两个方面的影响,从而使得蒸发器的利用率最大。根据一般的经验,蒸发器内气体流速在6~8m/s比较合适,这样我们根据制冷剂气态和液态时比容的比值推算出液体流速:
对于R22和R407C液体流速为0.1~0.15m/s,这样我们可以大致估算出每个流路的换热量约为: ф9.53mm铜管每个流路换热量为1600~2100W ф7.94mm铜管每个流路换热量为1000~1400W ф7.0mm铜管每个流路换热量为800~1000W 对于R410A其液体流速为0.15~0.2m/s,这样我们可以大致估算出每个流路的换热量约为: ф9.53mm铜管每个流路换热量为2000~2500W ф7.94mm铜管每个流路换热量为1300~1700W ф7.0mm铜管每个流路换热量为900~1300W 依据以上的数据我们可以先确定换热器流路数,然后再进行流路设计。 2.流路设计。当我们根据制冷量定下来流路数后,我们就得考虑如何分配这些铜管,以保证最充分的换热效果,在进行流路设计之前,我们要先确定一个大的方向,即蒸发器是采用顺流还是逆流设计,通常情况下,采用逆流会有利于提高传热温差,达到提高换热量的目的,但如果是热泵型空调,若蒸发器采用逆流设计时在制热时就变成顺流换热形式了,这样会导致制冷剂在后面的换热温差极少,严重影响换热器的利用率,综合考虑,对于热泵型空调我们在蒸发器中通常采用顺流设计。另一个注意点就是在换热器流路设计时尽量保证液体在下,气体在上。在确定了制冷剂的走向后,我们接下来就是要考虑如何分配每个流路的管程数了,管程的分配一个主要的原则就是换热好的部分分配少一点的管,换热差的多分配一些铜管。对于家用空调机来说,因为受结构的限制,但为了追求较高的能效比或达到较高的能力,我们对于换热器经常会采取多折叠的设计方式,但是通常我们换热器的弯曲形状却并不能很好的迎合风机流场的分布,也就是说在换热器的每个折叠块所经过的空气流速会相差较多,因此我们在一些风速较低的地方在铜管分配时就可以适当多分配一些,尽量保证每个流路的制冷剂都能够完全蒸发,当然我们还可能通过调节分配器上分液管的长度来调节每个流路制冷剂的流量,从而使得每路的制冷剂能够完全蒸发,但在流路设计时我们应尽量在假设每路流量是一样的情况下进行,这样当实际上每个流路出现一定程度的不平衡时我们才可能通过调节分液毛细管长度来解决,如果我们在设计流路未考虑蒸发器各个部分的差异,当实测时各流路平衡差别太大时,通过调节分液毛细管长度可能不能解决这个问题。还有一个问题在回路设计时也应注意,就是我们尽量不要将制冷剂的出口集中在一起,这样会导致经过蒸发器各个部分处理后的空气温差相差较大,这样在风道里混合后就会产生凝结水,严重时出风口会有吹水的现象,这样的问题通常在凝露试验会产生。
二、冷凝器的设计
冷凝器的设计在与蒸发器有着相同的注意点,特别是对于热泵型的空调,冷凝器既要考虑制冷时的换热效果,也要兼顾制热运行时的能力,这方面基本与蒸发器的设计相同,对于室外换热器作为冷凝器来说,换热器内大多数为液态制冷剂,而且在高压状态制冷剂气液两相的比容相差不像低压时那么大,所以制冷剂在冷凝器的液态流速可以比蒸发器高,一般设计时取0.4~0.5m/s,每路的换热量为: ф9.53mm铜管每个流路换热量为2200~3200W ф7.94mm铜管每个流路换热量为1500~2200W ф7.0mm铜管每个流路换热量为1100~1600W 当然冷凝器作为室外工作的换热器,它与蒸发器的设计上还是存在一些不同点的。 1.在制冷系统中,若换热器作为蒸发器工作,其内制冷剂的温度变化不大,因此采用顺流或是逆流对于换热的影响并不是很大,但对于冷凝器来说,其内制冷剂的温度变化很大,若采用顺流设计时制冷剂在换热器未端时传热温差很小,影响换热器换热效量,更不利于形成较大的过冷度,因此冷凝器应采用逆流设计。其实对于蒸发器来说,当制热时它的工作状态也应是逆流,因此对于热泵机型换热器的设计,不管是蒸发器或是冷凝器我们都应使它在作为冷凝器工作时为逆流。
2.翅片间距的选择。冷凝器在室外工作,考虑到空气质量以及化霜时凝结水的排除,翅片间距不应选得太小,以免脏堵或化霜排水不畅。对于开窗翅片,若冷凝器选用单排时间距不应小于1.2mm,两排时不应小于1.6mm,三排是不小于1.8mm(不推荐使用三排冷凝器)。
3.针对除霜时的特殊回路设计。考虑到除霜时盘管最底下受到盘管上面化霜时流下的水的影响,这部分的霜会较难融化,因此我们在进行回路设计时应考虑让温度最高的制冷剂流过这部分铜管,以确保除霜效果,这样我们在进行回路设计时应确保一路的进口在盘管的最下面。
4.对于仅为单冷机型的冷凝器设计因不用考虑制热方面的因素,可以适当减少流路数以增加制冷剂流速,提高换热效果,因为对于冷凝器来说适当的压力损失对于压缩机能力的影响并不是很大,而且冷凝器内的压力降相对于排气压力所占的比例很少,对系统能力影响不如蒸发器压降明显,当然,过大的冷凝压降会额外增加压缩机的功耗,影响能效比。
三、关于换热器设计的一些特殊流路
对于制冷系统来说,换热器中通常是气液两相共存的状态,由于气体的比容比液体要大很多,因此当制冷剂在气态时其流速比液态时大很多,相应的其流动阻力也会大很多,因此为了减少气态时的阻力又不降低液态时流速,我们可以采用二叉树型的流路形式来兼顾二者,示意图如下:
采用这样的流路设计可以更好的提高换热器的换热效果,但每个部分所占比例可能不一定相同,需要针对具体情况加以分析,在实际应用中我们并不常采用这种流路,因为这种回路设计比较难调试平衡,特别是室内机换热器,当其每个部分换热效果相差较多时,要在回路设计时保证各流路的平衡比较难,可能需要多次试验才能得到较为理想的回路设计。
推荐第2篇:列管式换热器设计
第一章 列管式换热器的设计
1.1概述
列管式换热器是一种较早发展起来的型式,设计资料和数据比较完善,目前在许多国家中已有系列化标准。列管式换热器在换热效率,紧凑性和金属消耗量等方面不及其他新型换热器,但是它具有结构牢固,适应性大 ,材料范围广泛等独特优点,因而在各种换热器的竞争发展中得以继续应用下去。目前仍是化工、石油和石油化工中换热器的主要类型,在高温高压和大型换热器中,仍占绝对优势。例如在炼油厂中作为加热或冷却用的换热器、蒸馏操作中蒸馏釜(或再沸器)和冷凝器、化工厂中蒸发设备的加热室等,大都采用列管式换热器[3]。
1.2列管换热器型式的选择
列管式换热器种类很多,目前广泛使用的按其温度差补偿结构来分,主要有以下几种: (1)固定管板式换热器:这类换热器的结构比较简单、紧凑,造价便宜,但管外不能机械清洗。此种换热器管束连接在管板上,管板分别焊在外壳两端,并在其上连接有顶盖,顶盖和壳体装有流体进出口接管。通常在管外装置一系列垂直于管束的挡板。同时管子和管板与外壳的连接都是刚性的,而管内管外是两种不同温度的流体。因此,当管壁与壳壁温度相差较大时,由于两者的热膨胀不同,产生了很大的温差应力,以致管子扭弯或使管子从管板上松脱,甚至毁坏整个换热器。
为了克服温差应力必须有温度补偿装置,一般在管壁与壳壁温度相差50℃以上时,为安全起见,换热器应有温差补偿装置。
(2)浮头换热器:换热器的一块管板用法兰与外壳相连接,另一块管板不与外壳连接,以便管子受热或冷却时可以自由伸缩,但在这块管板上来连接有一个顶盖,称之为“浮头”,所以这种换热器叫做浮头式换热器。这种型式的优点为:管束可以拉出,以便清洗;管束的膨胀不受壳体的约束,因而当两种换热介质的温差大时,不会因管束与壳体的热膨胀量的不同而产生温差应力。其缺点为结构复杂,造价高。
(3)填料函式换热器:这类换热器管束一端可以自由膨胀,结构与比浮头式简单,造价也比浮头式低。但壳程内介质有外漏的可能,壳程终不应处理易挥发、易爆、易燃和有毒的介质。
(4)U型管换热器:这类换热器只有一个管板,管程至少为两程管束可以抽出清洗,
1 管子可以自由膨胀。其缺点式管子内壁清洗困难,管子更换困难,管板上排列的管子少。
对于列管式换热器,一般要根据换热流体的腐蚀性及其它特性来选择结构与材料,根据材料的加工性能,流体的压力和温度,换热器管程与壳程的温度差,换热器的热负荷,检修清洗的要求等因素决定采用哪一类型的列管式换热器。
1.3换热器内流体通入空间的选择
哪一种流体流经换热器的壳程,哪一种流体流经管程,下列各点可供参考(以固定管板式为例)。
(1)不清洁和易结垢的流体易走管内,因为管内清洗比较方便。
(2)腐蚀性的流体易走管内,以免管子和壳体同时受腐蚀,而且管子也便于清洗和检修。
(3)压强高的流体易走管内,以免壳体受压,可节省金属消耗量。
(4)饱和蒸汽易走管间,以便于及时排除冷凝液,且蒸汽较洁净,它对清洗无要求。 (5)有毒流体易走管内,使泄露机会较少。
(6)被冷却的流体易走管间,可利用外壳向外的散热作用,以增强冷却效果。 (7)粘度大的液体或流量较小的流体,易走管间,因流体在有折流板的壳程流动时,由于流速和流量的不断改变。在低Re值(Re>100)下即可达到湍流,以提高对流传热系数。
对于刚性结构的换热器,若两流体的温差较大,对流传热系数较大者易走管间,因壁面温度与α大的流体温度相近,可以减少热应力。
1.4流体流速的选择
增加流体在换热器中的流速,将加大对流换热系数,减少污垢在管子表面上沉积的可能性,即降低了污垢热阻,使传热系数增大,动力消耗就增多。所以适宜的流速要通过经济衡算才能确定。
此外,在选择流速时,还要考虑结构上的要求。例如,选择高的流速,使管子数目减少,对一定的换热面积,不得不采用较长的管子或增加程数。管子太长不易清洗,且一般管长都有一定的标准;单程变成多程使平均温度降下来。这些也是选择流速时应考虑的问题。
表1-1至表1-3列出了常用的流速范围,可供设计参考。所选的流速,应尽可能避免在滞流下流动。
表1-1常用的流速范围
Table 1-1 The scope of common use in current velocity
流体种类 管程流速 m/s 壳程流速m/s
一般流体 0.5~3 0.2~1.5
易结垢液体
>>1 >>0.5
气体 5~30 3~15
表1-2安全允许速度
Table 1-2 The speed of the safe admiion of the liquid
液体名称
安全允许速度/m/s
乙醚、二硫化碳、苯 甲醇、乙醇、汽油
<1
<2~1.5
丙酮 <10
表1-3不同粘度液体的常用流速
Table 1-3 The different of the liquidin common use current velocity
液体粘度/mPa.s 最大流速/m/s >1500 0.6
1500~500 500~100 100~35 35~1 <1 0.75
1.1
1.5
1.8
2.4 1.5确定设计方案的原则
1.5.1满足工艺和操作的要求。
设计出的流程和设备首先要保证质量,操作稳定,这就必须配置必要的阀门和计量仪表等,并在确定方案时,考虑到各种流体的流量,温度和压强变化时采取什么措施来调节,而在设备发生故障时,检修应方便。
1.5.2满足经济上的要求。
在确定某些操作指标和选定设备型式以及仪表配置时,要有经济核算的观点,既能满足工艺和操作要求,又使施工建简便,材料来源容易,造价低廉。如过有废热可以利用,要尽量节省热能,充分利用,或者采取适当的措施达到降低成本的目的。
1.5.3保证安全。
在工艺流程和操作中若有爆炸,燃烧、中毒、烫伤等危险性,就要考虑必要的安全措施。又如设备的材料强度的验算,除按规定应有一定的安全系数外,还应考虑防止由于设备中压力突然升高或者造成真空而需要装置安全阀等。以上所提的都是为了保证安全生产所需要的。
第二章 列管式换热器热力计算
2.1稳态传热
稳态传热的基本方程式为:Q=KA△tm (1) Q K A △tm 热负荷,W;
总传热系数,W/m2•℃; 换热器总传热面积,m2;
进行换热的两流体之间的平均温度,℃。
2.1.1热负荷
当忽略换热器对周围环境的散热损失时,根据能量平衡,热流体所放出的热量应等于冷流体所吸收的热量,即
Q=Wh(Hh1-Hh2)=Wc(Hc2-Hc1) (2)
式中
Q W H 换热器的热负荷,kJ/h或W; 流体的质量流量,kg/h; 单位质量流体的焓,kJ/kg;
下标c,h分别表示冷流体和热流体,下标1和2表示换热器的进出口。
若换热器中两流体无相变化,且流体的比热容不随温度而变或可取平均温度下的比热容时,即
Q=WhCph(T1-T2)=WcCpc(t2-t1) (3)
式中
Cp t T 流体的平均比热容,kJ/( kg•℃); 冷流体的温度,℃; 热流体的温度,℃。
若换热器中有热流体的相变化,即
Q=Whγ=WcCpc(t2-t1) (4) 式中
Wh γ
饱和蒸气(即热流体)的冷凝速率,kg/h; 饱和蒸气的冷凝热,kJ/kg。
4 2.1.2总传热系数
(1) 总传热系数的计算式
两流体通过管壁的传热包括以下过程[4]。 a.热流体在流动过程中把热量传给管壁的对流热。 b.通过管壁的热传导。
c.管壁与流动中的冷流体之间的对流传热。
d.换热器在实际操作中,传热表面上常有污垢积存,对传热产生附加热阻,使总传热系数降低。在估算K值时一般不能忽略污垢热阻。由于污垢层的厚度及导热系数难以准确地估计,因此通常选用污垢热阻的经验值,作为计算K值的依据,若管壁内、外侧表面的污垢热阻分别用Rsi及Rso表示。
1/K=1/αo+do/αidi+Rso+Rsido/di+bdo/λdm (5) 其中
αo αi Rsi、Rso di、do、dm b λ
2.1.3平均温度
变温传热时,若两流体的相互流向不同,则对温度差的影响也不同,通常逆流传热效果好,以逆流为列,推导出计算平均温度的通式。
Δtmˊ=(Δt1+Δt2)/2 (6) Δt1=T1-t2 Δt2= T2-t1 式中
T1, T2 t1, t2 热流体的进出口温度, ℃; 冷流体的进出口温度, ℃;
Δtm=ΦΔtΔtmˊ (7) Δtmˊ
管外流体传热膜系数,w/m2·℃; 管内流体传热膜系数,w/m2·℃;
管壁内、外侧表面的污垢热阻,m2·℃/ w; 管内径、外径和内、外径的平均直径,m; 管子壁厚,mm;
管壁材料的导热系数,w/m2·℃;
按逆流计算时的平均温度差, ℃;
5 ΦΔt 温度差校正系数,无量纲;
温度差校正系数ΦΔt与冷热流体的温度变化与关,是P和R两因素的函数,即
ΦΔt=f(P,R) 式中P= (t2-t1)/ (T1- t1)=冷流体温升/两流体的最初温度差
R= (T2 -T1)/ (t2-t1)=热流体的温降/冷流体的温升
温度校正系数ΦΔt值可根据P和R两因素从相应的图中查得 温度差校正系数图是基于以下假设作出的。 壳程任一截面上流体温度均匀一致。 (1)管方各程传热面积相等。
(2)总传热系数K和流体比热容Cp为常数。 (3)流体无相变化。
(4)换热器的热损失可以忽略不计。
2.2对流传热膜系数
无相变对流传热的传热膜系数 2.2.1管内传热膜系数
对低黏度流体,Re>10000,0.7
αi=0.023λi/di Rei0.8 Prin (8) 加热n取0.4;冷却n取0.3 2.2.2管外传热膜系数
αo=0.36(λ/dm) Rei0.55 Pri1/3(µ/µw)0.14 (9) Re=2×103~1×106
有相变对流传热的传热膜系数[5]
1/3蒸汽在水平管外冷凝
ao=1.163×0.945(λf3ρf2g/μfGg/) (10)
2.3流体压强降的计算
2.3.1管程流动阻力
管程阻力可按一般摩擦阻力公式求得。对于多程换热器,其总阻力∑ΔPi等于直管阻力、ΔP2阻力及进、出口阻力之和。一般进、出口阻力可忽略不计,故管程阻力的计算式为
6 ∑ΔPi=(ΔP1+ΔP2)FtNp (11)
式中
ΔP
1、ΔP2 Ft 分别为直管及回弯管中因摩擦阻力引起的压强降,Pa;
结垢校正因数,无量纲,对Φ25×2.5 mm的管子,取1.4, 对Φ19×2mm的管子,取1.5;
Np 管程数;
ΔP1=λ(L/d)×(ρu2/2) (12) ΔP2=3ρu2/2 (13)
2.3.2壳程流动阻力
现已提出的壳程流动阻力的计算公式虽然较多,但是由于流体的流动状况比较复杂,因此使计算得到的结果相差很多。下面壳程压强降ΔP0的公式,即
∑ΔP0=(ΔP1ˊ+ΔP2ˊ)FsNs (14)
式中
ΔP1ˊ 流体横过管束的压强降 ΔP2ˊ 流体通过折流板缺口的压强降, Fs 壳程压强降的结垢校正因数,无量纲,液体可取1.15,气体可取1.0
ΔP1ˊ=Ff0nc(NB+1)(ρu2/2) (15) ΔP2ˊ= NB(3.5-2h/D)ρu2/2 (16)
式中F
管子排列方法对压强降的校正因数,对正三角形排列F=0.5,对转角正方形为0.4,正方形为0.3。
f0
壳程流体的摩擦系数,当Reo>500时, f0=5.0 Re0-0.228; nc
横过管束中心线的管子数,管子按正三角形排列nc=1.1×n1/
2管子按正方形排列nc=1.19×n1/2
NB
折流挡板数;
H
折流挡板间距,m;
u0
按壳程流通截面积A0计算的流速,m/s,而 A0=H(D-ncd0) 一般来说,液体流经换热器的压强降为10~100 kPa,气体的为1~10 kPa。
第三章 工艺流程
汽提塔(E101)底部的溶液经减压阀LC9202减压到1.76Mpa进入中压分解分离器(V102),溶液在此闪蒸并分解,分离后尿液进入中压分解塔(E102A/B),甲铵在此分解E102A壳体用0.5Mpa蒸汽供热,E102B用汽提塔蒸汽冷凝液分离器(V109)的2.5Mpa蒸汽冷凝供热。
从中压分解塔分离器顶部出来的含有氨和二氧化碳的气体先送到真空预浓缩器(E104)壳程中,被中压碳铵液泵(P103A/B)送来的碳铵液吸收,其吸收和冷凝热用来蒸发尿液中的部分水份,然后进入中压冷凝器(E106)用冷却水冷却,最终进入中压吸收塔(C101)。
中压吸收塔为泡罩塔,它用氨升泵(P105A/B)来的液氨和氨水泵(P107A/B)送来的氨水共同洗涤二氧化碳。中压吸收塔顶部含有微量惰性气氨进入氨冷器(E109)冷凝成液氨,收集于氨收集器(V105),不凝气通过氨回收塔(C105)进入中压惰性气体洗涤塔(C103)。惰性气体放空,其吸收热通过中压氨吸收塔(E111)用冷却水带走,氨水通过氨水泵(P107A/B)被送到中压吸收塔。
中压吸收塔底部溶液通过高压甲铵泵(P102A/B)加压到15.5Mpa送到甲铵冷凝器(E105),返回合成圈。
这里所做的换热器设计就是对中压吸收塔出来的气氨进行冷凝成液氨的设备进行设计计算,以下是氨冷凝器所在工艺流程中的位置(见附图3-1)。
第四章 换热器工艺过程计算
4.1设计任务和条件
物料:NH
3、循环水等。其中循环水走管程。 工艺条件:
壳程:操作压力:1.62 MPa 温度 43℃~38℃(入/出) 管程:操作压力:0.4 MPa 温度 32℃~36℃(入/出) 其中:NH3:流量:580 m3/h 密度13 Kg/m3
4.2设计过程
列管式换热器的选型和设计计算步骤 4.2.1试算并初选设备规格
(1)确定流体在换热器中的流动途径。 (2)根据传热任务计算热负荷Q。
(3)确定流体在换热器两端的温度,选择列管换热器的形式;计算定性温度,并确定在定性温度下的流体物性。
(4)计算平均温度差,并根据温度差校正系数不应小于0.8的原则,决定壳程数。 (5)依据总传热系数的经验值范围,或按生产实际情况,选定总传热系数K值。 (6)由总传热速率方程Q=KSΔtm,初步算出传热面积S,并确定换热器的基本尺寸(如d、L、n及管子在管板上的排列等),或按系列标准选择设备规格。
4.2.2计算管程、壳程压强降
根据初定的设备规格,计算壳程、管程流体的流速和压强降。检查计算结果是否合理或满足工艺要求。若压强降不符合要求,要调整流速,再确定管程数或折流板间距,或选择另一规格的换热器,重新计算压强降直至满足要求为止。
4.2.3核算总传热系数
计算管程、壳程对流传热系数,确定污垢热阻Rsi和Rso,再计算总传热系数K/,比较K的初设值和计算值,若Kˊ/K=1.15~1.25或(Kˊ-K)/K=15.5%~30%,则初选的换热器合适。否则需另设K值,重复以上计算步骤[6]。
9 4.3工艺计算过程
4.3.1定性温度下流体物性
NH3:ρ=13kg/m
3 μ=0.918×10-5 Pa·s λ=0.0215W/M·℃
γ=1373kJ/kg Cp=0.67kJ/kg· ℃
V=580 m3/h 循环水:ρ=995.7 kg/m3
μ=80.07×10-5 Pa·s
λ=0.6176 W/M·℃
Cp=4.174 kJ/kg· ℃
液氨:ρf=583 kg/m3
λf=0.432kcal/m·h·℃
μf=0.306kg/m·h
g=12.7×107
本设计中涉及到氨的相变化传热过程,根据两流体的情况,循环水走管程,氨走壳程进行计算。
4.3.2试算和初选换热器的型号
(1)计算热负荷和冷却水流量
Q=Q1(显热)+Q2(潜热)
Q1=WCp(T1-T2)=VρCp(T1-T2)=(580×13/3600)×0.67×103×(43-38)=7016.4w Q2=Wγ=Vργ=(580×13/3600)×1373×103=2875672.2w Q= Q1+ Q2=7016.4+2875672.2=2882688.6w WH20=Q/CpΔt=2882688.6/(4.174×103×(36-32))=172.657kg/s VH2O= WH20/ρ=172.657/995.7=0.173m3/s (2)计算两流体的平均温度差
暂按单壳程、多管程进行计算。逆流时平均温度差为 NH3 43℃→38℃
水 36℃←32℃
Δt 7℃ 6℃
Δtmˊ=(Δt1+Δt2)/2=6.5℃
而 R=(T1-T2)/(t2- t1)=1.25 P=(t2- t1)/(T1- t1)=0.364 由P、R值查图4—17查得ΦΔt=0.92 所以Δtm=ΦΔt×Δtmˊ=0.92×6.5=5.98℃
(3)初选换热器型号
根据两流体的情况,假设K=1100 W/M·℃
10 故S=Q/K×Δtm=2882688.6/1100/5.98=438.2m2
由于Tm-tm=5-4=1℃<50℃ 因此不需要考虑热补偿。据此,由换热器系列标准,有关参数如下表4-1:
表4-1换热器系列标准
Tab.4-1 Heat exchange is related to data
参数
壳径D/mm 公称面积S0/m2 公称压强/MPa 管子尺寸/mm 管子总数
管长/m 管子排列方法 管程数
1000 446.2 1.62 Φ19×2 1267 6 三角形 1 实际传热面积S0=ПndL=1267×3.14×0.019×(6-0.1) =446 m2。若采用此换热面积的换热器,则要求过程的总传热系数为1100 W/M·℃。
4.3.3核算压强降 (1)管程压强降
∑ΔPi=(ΔP1+ΔP2)FtNp
其中 Ft=1.5 Np=1 管程流通面积Ai=(п/4)di2n/Np=0.785×0.0152×1267/2=0.2239m2 ui=Vs/Ai=0.173/0.2239=0.8m/s Rei=diuiρ/μ=0.019×0.8×995.7/(80.07×10-5)=14922.4 设管壁粗糙度ε=0.1mm, ε/d=0.1/15=0.0067,由第一章中的λ-Re关系图中查得
λ=0.039 所以ΔP1=λ(L/d)×(ρu2/2)=0.039×(6/0.015)×(995.7×0.82/2)=4970.5Pa ΔP2=3ρu2/2=3×995.7×0.82/2=955.9 Pa 则 ∑ΔPi=(4970.5+955.9)×1.5×1=29839.35 Pa<100Kpa (2)壳程压强降
∑ΔP0=(ΔP1ˊ+ΔP2ˊ)FsNs
11 其中Fs=1.0 Ns=1
ΔP1ˊ=Ff0nc(NB+1)(ρu2/2) 管子为三角形排列,F=0.5 nc=1.1 n1/2=1.1×12671/2=39 取折流挡板间距h=0.3m NB=L/h-1=6/0.3-1=19 壳程流通面积A0=H(D-ncd0)=0.3×(1-39×0.019)=0.0777 m2 u0=V0/A0=580/3600/0.0777=2.07m/s Re0= d0u0ρ/μ=0.019×2.07×13/(0.918×10-5)=55696.1>500 f0=5.0 Re0-0.228=5.0×55696.1-0.228=0.414 所以 ΔP1ˊ=0.5×0.414×39×(19+1)×13×2.072/2=4497 Pa ΔP2ˊ= NB(3.5-2h/D)ρu2/2=19×(3.5-2×0.3/1)13×2.072/2=1534.6Pa ∑ΔP0=(4497+1534.6)×1×1=6031.6 Pa<10kPa 计算表明,管程和壳程压强降都能满足题设的要求。 4.3.4核算总传热系数 (1)管程对流传热系数αi Rei=14922.4 Pri=μCp/λ=80.07×10-5×4.174×103/0.6176=5.41
αi=0.023λ/d Rei0.8 Pri0.4=0.023×(0.6176/0.02)×14922.40.85.410.4 =4061.6 W/m2 ·℃ (2)壳程对流传热系数α0 由于发生相变传热可有公式α
ˊ0
=0.945(λ
3fρf2g/μfGgˊ)1/3 Ggˊ=W/(L(Nt)2/3)=Vρ/(L(Nt)2/3)=580×13/(6×12672/3)=10.7kg/s αˊ0=0.945(λ3fρf2g/μfGgˊ)1/3
=0.945×(0.4323×5832×12.7×107/(0.306×10.7))1/3=9635.2kcal/m2·h·℃ α0=1.163αˊ0=1.163×9635.2=11205.7 W/m2·℃
(3)污垢热阻
查阅资料,管内、外侧污垢热阻分别取为 Rsi=0.00017 m2·℃/W Rs0=0.00017 m2·℃/W (4)总传热系数K0 管外侧热阻忽略时,总传热系数K0为 K0=1/(1/α0+ Rso+ Rsid0/di+d0/di/αi)
=1/(1/11205.7+0.00017+0.00017×0.019/0.015+0.019/(0.015×4061.6)) =1272.3 W/m2·℃
由前面的计算可知,选用该型号的换热器时要求过程的总传热系数为1100 W/m2·℃。在规定的流动条件下,计算出的K0为1272.3 W/m2·℃,故所选择的换热器是合适的,安全系数为 (K0-K)/K×100%=(1272.3-1100)/1100×100%=15.7%。
13 第五章 换热器主体设备工艺尺寸的确定
5.1管子的规格和排列方法
选择管径时,应尽可能使流速高些,但一般不超过前面介绍的流速范围。易结垢、粘度较大的液体宜采用较大的管径。我国目前试用的列管换热器系列标准中仅为Ф25mm×2.5mm及Ф19mm×2mm两种规格的管子[7]。
管长的选择是以清洗方便即合理使用管材为原则。长管不便于清洗,且容易弯曲。一般出厂的标准管长为6m,则合理的换热管长应为1.5m、2m、3m和6m。系列标准中也采用这四种管长。此外管长和壳径应相适应,一般去L/D为4~6(对直径小的换热器可取大些)。
如前所述,管子在管板上的排列方法有正三角形、正方形和转角正方形等。正三角形排列的优点有:相同壳程内可排列更多的管子;管板的强度高;流体走短路的机会少,且管外流体扰动较大,因而对流传热系数高。正方形排列的优点是便于清洗列管外壁,使用与壳程流体易产生污垢的场所;但其对流传热系数较正三角形排列时低。转角正方形排列则介于上述两者之间,与直列排列相比,对流传热系数可适当的提高。
管子在管板上排列的间距t(指相邻两管子的中心距),随管子和管板的连接方法的不同而异。通常,胀管法取t=(1.3~1.5)d0,且相邻两管外壁间距不应小于6mm,即t≥(d0+6)。焊接法取t=1.25d0。
5.2管程和壳程数的确定
当流体的流量较小或传热面积较大而需管数很多时,有时会使管内流速降低,因而对流传热系数较小。为了提高管内流速,可采用多管程。但是程数过多时,导致管内流动阻力增大,增加动力费用;同时多程会使平均温度差下降;此外多程隔板使管板上可利用面积减少。设计时应考虑这些问题。列管换热器的系列标准中管程数有
1、
2、4和6程等四种。采用多程时,通常应使每程的管子数大致相等[8]。 管程数m可按下式计算,即
m=u/uˊ
其中
u 管程内流体的适宜流速m/s;
uˊ 管程内流体的的实际流速m/s。
当温度差校正系数Ф△t低于0.8时,可采用壳方多程。如壳体内安装一块与管束平行
14 的隔板,流体在壳体内流经两次,称为两壳程。但由于壳程隔板在制造、安装和检修等方面都有困难,故一般不采用壳方多程的换热器,而是将几个换热器串联起来使用,以代替壳方多程。例如当需壳方两程时,即将总管数等分为两部分,分别装在两个内径相同而直径较小的外壳中,然后把两个换热器串联使用。
5.3折流挡板
安装折流挡板的目的,是为加大壳程流体的速度,是湍流程度加剧,以提高壳程对流传热系数[9]。
最常用的为圆缺型挡板,切去的弓形高度约为外壳内径的10%~40%,一般取20%~25%,过高或过低都不利于传热。
两相邻档板的距离(板间距)h为外壳内径D的(0.2~1)倍。系列标准中采用的h值为:固定管板的有150、300和600三种,单位均为mm;浮头的有150、200、300、480和600五种,单位均为mm。板间距过小,不便于制造和检修,阻力也较大。板间距过大,流体就难于垂直的流过管束,使对流传热系数下降。
5.4外壳直径的确定
换热器的壳体的内径应等于或稍大于(对浮头式换热器而言)管板的直径。根据计算出的实际管数、管径、管中心距及管子的排列方法等,可采用作图的方法确定壳体内径。但是,当管数较多又要反复计算时,用作图法就太麻烦了。一般在初步设计中,可先选定两流体的流速,然后计算所需的管程和壳程的流通截面积,与系列标准中查出外壳的直径。待全部设计完后,仍用作图法画出管子排列图。为了使管子均匀排列,防止流体走“短途”,可适当增减一些管子[10]。
另外,初步设计中也可用下式计算壳体的内径,即
D=t(nc-1)+2b 其中
D t nc b 壳体内径,m; 管中心距,m;
横过管束中心线的管数;
管束中心线上最外层的中心至壳体内壁的距离,一般取b=(1~1.5)d0;
m。nc值可用下面公式估算,即 管子按正三角形排列 nc=1.1n1/2
15 管子按正方形排列 nc=1.19n1/2 式中n为换热器的总管数。
表5-1壳体标准尺寸 Table 5-1 Hull stock size
壳体外径/mm 最小壁厚/mm 325 8
400 500 600 700
800 900 1000
1100 1200
14 5.5主要附件
封头:封头有方形和圆形两种,方形用于直径小(一般小于400mm)的壳体,圆形用于大直径的壳体[11]。
缓冲挡板:为防止壳程流体进入换热器时对管束的冲击,可以在进料口装设缓冲挡板。 导流筒:壳程流体的进、出口和管板间必存在有一段流体不能流动的空间(死角),为了提高传热效果,常在管束外增设导流筒,使流体进、出壳程时必然经过这个空间。
放气孔、排液孔:换热器的壳体上常安有放气孔和排液孔,以排除不凝气体和冷凝液等。换热器中流体进、出口的接管直径按下式计算,即
D=(4Vs/∏u)1/2
式中
Vs u 流体的体积流量,m3/s; 流体在接管中的流速,m/s;
流速u的经验值可取为 对液体 u=1.5~2m/s 对蒸汽 u=20~50m/s 对气体 u=(0.15~0.2)p/ρ (ρ为压强,KPa;ρ为气体密度,Kg/m3)。
5.6材料选用
列管换热器的材料应根据操作压力、温度及流体的腐蚀性等来选用。在高温下一般材料的机械性能及腐蚀性能下降 。同时具有耐热性、高强度及耐腐蚀性的材料是很少有的。目前常用的金属材料有碳钢、不锈钢、低合金钢、铜和铝等;非金属材料有石墨、聚四氟乙烯和玻璃等。不锈钢和有色金属虽然耐腐蚀性能好,但价格高且较稀缺,应尽量少用[12]。
表5-2列管换热器各部件的常用材料
Table 5-2 The common material for each parts of the tube heat exchanger
部件或零件名称
材料牌号
碳素钢 不锈钢
壳体、法兰 A3F、A3R、16MnR 16MN+ 0Cr18Ni9Ti 法兰、法兰盖 16Mn、A3 16MN+1CrNi9Ti 管板 A4 1CrNi9Ti 膨胀节 A3F、16MnR 1CrNi9Ti 挡板和支撑板 A3F 1CrNi9Ti 螺栓 16Mn、40Mn、40 MnB 换热管 10号
螺母 A
3、40Mn 1CrNi9Ti 垫片 石棉橡胶板 支座 A3F 5.7管板尺寸的确定
5.7.1管板受力情况分析
列管换热器的管板,一般采取平板管,在圆平板上开孔装设管束,管板又与壳体相连。管板所受载荷除管程和壳程压力外,还承载管壁和壳壁的温差引起的变形不协调作用等[13]。管板受力情况较为复杂,影响管板应力大小又如下因素:
(1)与圆平板类似,管板直径、厚度、压力大小,使用温度等对管板应力又显著影响。
(2)管束的承载作用。换板与许多换热管刚性的固定在一起,因此,管束起着支撑的作用,阻碍着管板的变形。在进行受力分析时,常把管板看成是放在弹性基础上的平板,列管就起着弹性基础的作用。其中固定式换热器管板的这种支撑作用最为明显。
(3)管孔对管板强度和刚度的影响。由于管孔的存在,削弱了管板的强度和刚度,同时在管孔边缘产生高峰应力。当管子连接在管束之后,管板孔内的管子又能增强管板的强度和刚度,而且也抵消一部分的高峰应力。通常采用管板的强度与刚度削弱系数来估计它的影响。
17 (4)管板边缘固定的形式。类似与圆平板、管板边界条件不同,管板应力状态是不同的。管板边缘有不同的固定形式,如夹持,兼支、半夹持等。通常以介于简支和夹持之间为多。这些不同的固定结构对管板应力产生不同程度的影响,在计算中,管板边缘中的固定形式是以固定系数来反映的。
(5)管壁和壳壁的温度所引起的热应力。由于管壁和壳壁温度不同产生变形量的差异,不仅使管子、壳体的应力有显著的增加,而且使管板的应力有很大的增加,在设备启动和停车过程中,特别容易发生这种情况。如采用非刚性(非固定管板式)结构换热器,这种情况影响会减少或消除。
(6)当管板又兼做法兰时,拧紧法兰螺栓,在管板上又会产生附加弯矩。 (7)其它,当管板厚度较大,管板上下两平面存在有温差,则产生附加热应力。当管子太长而无折流板支托时,管子会弯曲造成管板附加压力。当管板在制造、胀接或焊接管子时,也会产生一些附加压力。
目前设计管板厚度的方法很多,由于处理问题的出发点不同,考虑问题周密程度不同,而结果往往彼此相差很大。
5.7.2管板尺寸
当管子与管板采用胀接时,应考虑胀管时对管板的刚度要求,管板的最小厚度(不包括腐蚀余量),按表5-3规定,包括厚度附加量在内建议不小于20mm。
表5-3 管板最小厚度(mm) Table 5-3 The thickne of the thick wooden board that minimum deals take care of(mm)
换热器外径d0(mm) 管板厚度b(mm) ≤25 3/4dc 32 22 38 25 57 32
结 论
本次是对中压分解和回收工段中对氨冷凝器的设计通过对所需冷凝器进行物料衡算及热量衡算,首先估算换热面积而后选择适合的换热器型号,对选定的换热器进行面积的计算和压降核算以及总传热系数的核算,在满足这些计算中得到了设计的换热器是单壳程单管程换热器,壳径D= 1000 mm、公称面积S0=446.2 m
2、公称压强P=1.75 Mpa、管子尺寸d=Φ19×2 mm、管子总数n=126
7、管长L=6 m,理论计算值出来的换热器与实际生产中的换热器有不同。这次设计换热器没有温度的补偿,而实际生产中有温度的补偿,而且设计的换热器是单壳程单管程的,实际生产中的是单壳程双管程的。设计出的换热器都满足设计条件,但是从经济角度来考虑,可能不是很经济造价或设计出的设备所花代价会比较高,不过通过本次设计让我也学到了很多的东西,理论还是和实际有差距,在满足理论要求的同时还要考虑其经济性。
推荐第3篇:换热器设计现状
摘要:随着现代工业的快速发展,在保护生态环境下的能源紧缺问题逼迫着人们寻找新能源的开发,换热器是一种重要的在不同温度的 的不同介质之间实现热量交换的设备,在世界能源危机不断加剧的情形下,换热器的强化传热技术备受关注,大量的相关研究也是层出不 穷,都在努力解决能源短缺问题。而本文主要介绍了我国换热器的现状以及存在的问题,还涉及换热器的基本概念、工作原理、分类、发展趋势。
关键词:换热器;设计现状;管式换热器;板面式换热器
前言
换热器又称热交换器,是将热流体的部分热量传递 给冷流体的设备,实现热量的传递。热换器在工业领域应 用广泛,在食品、化工、石油、制药、机械等领域都有涉 及。换热器存在的形式既可以是一种单位设备,如加热 器、冷却器等,也可以不是独立存在的,比如是某一工艺 设备的组成部分。热换器的不断更新发展不仅是热换器行 业自身的发展,更是为使用热换器的各个工业行业的能源 问题的解决提供好的途径。
一、换热器的国内研究现状
对于各型换热器的强化换热技术的研究,主要集中在对 换热器内流体流态变化以及对各部件的参数优化研究两方 面,而对换热器部件参数的主要研究对象就是换热管( 板) 排 列方式 ( 顺排或叉排)、换热管( 板) 排数、换管( 板) 间距大 小、肋片布置问距、肋片形状等。国内对于换热器肋片换热 的研究起步比较晚、经验比较少,多借鉴于国外,无论是理论 研究还是实验研究都还需进一步深入,技术创新还不够,但 是对各因素对换热器性能影响的研究也比较全面。总的来 说,仍然存在以下问题: ( 1) 换热器换热的理论研究不够完 善,可供对肋片实际应用优化设计的理论依据太少,对于换 热公式推导出的解析解较少,目前大多是通过试验、数据分 析拟和而成的经验公式; ( 2) 换热的理论体系缺乏系统性, 不够完善; ( 3) 因为试验环境、材料、仪器的精度以及试验方 法不同,在同一个研究方向的某些问题的研究结论存在的分 歧较多,很难形成统一的意见,暂不能形成对实践的可靠指 导; ( 4) 目前对换热器的研究大多基于一维、二维的换热,国 内对于三维的换热模型的研究过少,同时,对于一维和二维 传热模型的前提假设条件很苛刻,得出的结论适用性不强; ( 5) 结合试验建立的部分换热理论还缺乏严谨性和局限性。
一、热换器的工作原理1.工作原理 换热器按照传热原理可以分为表面式换热器、蓄热式 换热器、流体连接间接式换热器、直接接触式换热器。但 总的来说,换热器就是遵循了热平衡的原理,简而言之就 是把高温物体的热量传送给低温物体。在传热工程中,其
内部有两个管道回路,一个是热源温度高,另一个温度低 是被加热源,通过热源将热量传输给被加热源来提高被加 热源的温度。而且在加热源之前有个调节阀用来控制被 加热源的温度,用调节阀来控制所需的热量的程度和时间 点等。
二、典型的热换器类型 1.管式换热器 管式换热器主要分为套管式换热器和管壳式换热器。 套管式换热器如字面意思,是将直径不同的管进行同心套 接,然后将多个元件用u型弯管连接而成的。而管壳式换热 器是由壳体、折流板等部分组成,管束安装在壳体内部, 再把一端或者两端固定在管板上面。而管板与管箱的连接 方式也多种多样了,可以焊接也可以用螺栓,但是连接处 的检测就需要格外严格了,要充分保障连接处无缝隙, 质量确保。套管式换热器运用范围主要是用于传热面积需 求不大的地方,只能小范围运用,主要是小空间的建筑室 内。因为他的占地面积较大,管与管连接所用的接头过 多,发生泄漏的可能性也随之增大,如果工程量过大就会 使得发生泄漏的可能性也随之增大,后期的危险性大,承 担过大风险造成不必要的费用。所用材料多,物质流动的 阻力也增大,加热的效率降低,而且能覆盖的面积也减少 了。但是它的优点是组合方式简单易懂,损坏后无需专人 也能大概看懂问题所在,所需的专业知识少。维修清洗便 捷,适合高温、高压的流体物质使用。管壳式换热器依靠 其结构简易、安全性能高、承受高温高压能力强等优良性 能,所以在目前的大多数工业工程中使用比例大。管壳式 换热器按照不同的分类标准可以分为不同的种类。根据其 结构不同可以分为固定管板式换热器、浮头式换热器、U 型管式换热器等等。
2.板面式换热器 板面式换热器顾名思义就是通过板面进行换热的换热 器。板面一般不是平滑的表面,是有凹凸不平的纹路,流 体通过板面时造成扰动提高热效率。板面式换热器的优点 是占地面积较小,能省下更大的空间,也会对室内的美观 减少影响。相比于管壳式换热器,板面式质量更轻,所用 的材料更少,而且凹凸不平的版面使得传热效率更高。由 于其结构特点,使得流体能在较低的速度下就到达端流状 态,加强了传热,节省了不少时间,提高效率。但是板式 换热器流道狭窄,处理量小,流动阻力大,承受高压高温 效果也较差的缺点。板面式换热器形式多种多样,可分为 板式换热器、板壳式换热器、螺旋板式换热器伞板式换热 器等等。螺旋式换热器由于其螺旋状的外形,能促使流体 随螺旋状自动流动,易于冲刷,不易结垢。
三、换热器未来发展趋势
未来工业生产上对换热器的要求是:传热效率高、流 体阻力小;强度、刚度、稳定性都要足够;结构合理,节 省材料,成本较低;制造、装拆、检修方便等。产品高效 化、节能化、大型化都将是换热器产业发展的方向。国家 要大力建设节约型环保社会,这一方面将促进换热器产业 的高速发展,国家提供足够的支持力度,刺激换热器行业 的积极性。另一方面也将引领产业向高效、环保、节能方 面发展。2013年,国务院颁布了《能源发展的“十二五” 规划》,规划中的条例表明了基于石油、化工等行业的需 求将稳定增长。市场的广阔需求和国家的大力支持都推动 着换热器产业在技术上的革新和在品种上的多样化趋势。 国家的资金和政策支持引领更多的人才投入和精力投入, 必然推动换热器行业的创新发展。
四、总结 随着经济发展,工业化进程加快,能源短缺问题成为 世界性难题,新能源的开发、节能环保都成为世界共同关 注的话题。近年来,国内换热器行业在节能增效、提高传 热效率、降低降压方面都取得了显著的成绩。但是在技术 上,与国外的换热器相比依然有很多难题需要去克服。我 国在换热、散热、冷却设备上都是强大的重要的市场,市 场需求量大。基于国家政策的支持和市场日益增长的需求 量,我国换热器产业具有一个很好的前景,是蓬勃发展的 朝阳企业。
参考文献 [1]祝银海,厉彦忠.板翅式换热器翅片通道中流体流动与传热的算流 体力学模拟[J].化工学报,2006,57(5):1102-1106.[2]陈永东,陈学东.LNG成套装置换热器关键技术分析[J].天然气工 业,2010,30(1):96-100.[3]陈永东,周兵,程沛.LNG工厂换热技术的研究进展[J].天然气工 业,2012,32(10):80-85.
推荐第4篇:管壳式换热器设计
管壳式换热器设计
管壳式换热器的换热设计由复杂的电脑软件完成,对换热器换热原理的掌握可以更有效的使用好软件。
本文阐述了换热器设计基础,包括如下几个方面:管壳式换热器构件;根据结构和用途划分的管壳式换热器类型;换热设计所需数据;管侧设计;壳侧设计包括管子排布,折流板和壳侧压降;平均温差。管侧和壳侧的换热和阻力降方程众所周知,本文着重他们之间的相互作用以使换热器设计最优化。
管壳式换热器构件
设计者需充分了解管壳式换热器的机械构件及其对换热设计的影响。管壳式换热器的主要构件包括:壳体,壳盖,管子,管箱,管箱盖,管板,折流板,管口。
其它构件包括拉杆,定位件,通道隔板,防冲板,纵向挡板,密封条,支撑和支座。TEMA有详细的部件描述。
一个管壳式换热器包括三部分:前封头,壳体和后封头。图1给出了不同结构的TEMA名称。换热器可以表示为有三部分的字母代号,例如BFL换热器表示罩盖,纵向隔板双壳程和固定管板后封头。
换热器类别 固定管板式
固定管板式换热器(图2)是垂直的管子两头固定在管板上,管板与壳体焊接在一起。这种结构包括可移动管箱盖(如AEL),罩盖型管箱盖(如BEM)和整体管板(如NEN)。
固定管板式结构简单,成本低,不需要膨胀节。固定管板式拆除管箱盖或帽后管子可以机械清洗,而且壳侧没有法兰连接壳侧流体不易泄漏。
固定管板式管束固定在壳体上,管外侧无法进行机械清洁,但可以使用化学清洁。如管侧壳侧温差太大,管板无法吸收不同的应力,则需要加膨胀节,此时不适合用固定管板式。 U型管式
U型管换热器管子是U型,只有一个管板,成本也较低。
U型管换热器一端自由,管束在不同的应力下可伸缩,U型管换热器管束可以抽出,管外侧可以清洁。
U型管换热器管内无法有效的清洁,U型端须要有柔性转轴才能清洁。所以对于U型管换热器易结垢流体不易走管内。
浮头式
浮头式换热器用途广泛,价格昂贵。浮头式换热器一端管板固定于壳侧,另一端浮动。管束可以伸缩,管子内外都可以清洁。管侧壳侧都可以走脏的流体,炼油多用浮头式换热器。
浮头式换热器有多种结构。两种最常用的是可抽钩圈式浮头(TEMA S)和可抽式浮头(TEMA T)。
TEMA S在化工应用普遍,浮头盖和浮动管板通过可活动且分开的钩环用螺栓连接在一起。浮头罩位于壳体末端,包含在一个更大直径的壳盖内。拆除换热器时,先拆开壳盖,然后是分开的钩环,再拿掉浮头盖,最后管束可以从固定端抽出。
TEMA T的结构是,管束和浮头可以一起从固定端抽出,壳体直径比浮头法兰大。浮头盖与浮动管板用螺栓直接连接不需要分开的钩环。
这种结构的优势在于管束可以直接从壳体中抽出,不须移走壳盖或浮头盖,这样可以缩短维修时间。这种结构特别适合于不适合使用U型管式使用较脏热介质的釜式再沸器(不适合使用U型管式)。由于增加了壳径,这种结构在所有换热器中成本最高。
另外两种浮头式结构是填料函式浮头(TEMA P)和带套换填料函式浮头(TEMA W)。这两种结构易泄漏应用局限于壳侧流体无毒无爆炸危险的情况且中压中温(4MPa,300℃)。 按用途分换热器类别
换热器,冷却器,加热器,冷凝器,再沸器等。 设计数据
换热设计前,工艺供应商须提供以下数据: 1.两侧流体的流量。
2.两侧流体的出入口温度。3.两侧流体的操作压力。
当气相密度未提供时须要操作压力,液体性质不随压力变化,操作压力不是必须数据。 4.两侧流体允许压降。
允许压降是换热器设计的重要参数。液体压降50-70 kPa,粘性流体压降更高,尤其是在管侧。气体压降5-20 kPa,一般取10 kPa。 5.两侧流体污垢系数。
如果未提供,设计者可以从TEMA标准中获得或者选取经验值。
6.两侧流体的物理性质。进出口温度下的粘度,导热系数,密度和比热容。进出口温度的粘度必须提供,尤其对于液体,不同温度下的粘度变化是没有规则的。 7.热负荷。壳侧和管侧的热负荷须一致。
8.换热器类型。设计者可以根据之前提供的各种换热器类型的特点选择。 9.管子尺寸。
推荐第5篇:换热器基本知识
一、换热器的结构型式有哪些?
换热器是很多工业部门广泛应用的一种常见设备,通过这种设备进行热量的传递,以满足生产工艺的需要。可按用途、换热方式、结构型式三种不同的方法进行分类。按结构型式分类如下:
换热器分为管式换热器、板式换热器、新型材料换热器和其他型式的换热器。
管式换热器又分为:套管式换热器、管壳式换热器、沉浸式换热器、喷淋式换热器和翅片管式换热器。
板式换热器又分为:夹套式换热器、平板式换热器、伞板式换热器、螺旋板式换热器、板翅式换热器和板壳式换热器。
新型材料换热器分为:石墨换热器、聚四氟乙烯换热器、玻璃换热器和钛材及其他稀有金属材料换热器。
其他形式的换热器包括回转式换热器和热管。
二、换热器管为什么会结垢?如何除垢?
因为换热器大多是以水为载热体的换热系统,由于某些盐类在温度升高时从水中结晶析出,附着于换热管表面,形成水垢。在冷却水中加入聚磷酸盐类缓冲剂,当水的PH值较高时,也可导致水垢析出。初期形成的水垢比较松软,但随着垢层的生成,传热条件恶化,水垢中的结晶水逐渐失去,垢层即变硬,并牢固地附着于换热管表面上。
此外,如同水垢一样,当换热器的工作条件适合溶液析出晶体时,换热管表面上即可积附由物料结晶形成的垢层;当流体所含的机械杂质有机物较多、而流体的流速又较小时,部分机械杂质或有机物也会在换热器内沉积,形成疏松、多孔或胶状污垢。
换热器管束除垢的方法主要有下列三种。
一、手工或机械方法
当管束有轻微堵塞和积垢时,借助于铲削、钢丝刷等手工或机械方法来进行清理,并用压缩空气,高压水和蒸汽等配合吹洗。当管子结垢比较严重或全部堵死时,可用管式冲水钻(又称为捅管机)进行清理。
二、冲洗法
冲洗法有两种。第一种是逆流冲洗,一般是在运动过程中,或短时间停车时采用,可以不拆开装置,但在设备上要预先设置逆流副线,当结垢情况并不严重时采用此法较为有效。
第二种方法是高压水枪冲洗法。对不同的换热器采用不同的旋转水枪头,可以是刚性的,也可以是绕性的,压力从10MPa至200MPa自由调节。利用高压水除污垢,无论对管间、管内及壳体均适用。高压水枪冲洗换热器效果较好。应用广泛。
三、化学除垢
换热器管程结垢,主要是因为水质不好形成水垢及油垢的结焦沉淀和粘附两种形式,用化学法除垢,首先应对结垢物质化验分析,搞清结垢物性质,就可以决定采用哪种溶剂清洗。一般对硫酸盐和硅酸盐水垢采用碱洗(纯碱、烧碱、磷酸三钠等),碳酸盐水垢则用酸洗(盐酸、硝酸、磷酸、氟氢酸等)。对油垢结焦可用氢氧化钠、碳酸钠、洗衣粉、液体洗涤剂、硅酸钠和水按一定的配比配成清洗液进行清洗。采用化学清洗的办法,现场需要重新配管,比较花费时间。
三、管壳式换热器管子与管板的连接方法有哪几种?如何选择?
根据换热器使用条件、加工条件的不同,基本可分为胀接、焊接、胀焊并用三大类。
其中胀接又可分为:机械胀管、液压胀管、液袋胀管、橡胶胀管、爆炸胀管、脉冲胀管、粘胀等。
焊接分为:普通焊接、内孔焊接、高频焊接、摩擦焊接、钎焊和爆炸焊接。
胀焊并用分为:强度焊+贴胀、强度焊+强度胀、强度胀+密封焊、强度胀+贴胀+密封焊、强度焊+强度胀+贴胀。
换热器进行水压试验和气密试验的基本原则如下:
(1)液压试验时,圆筒的薄膜应力不得超过试验温度下材料屈服点的90%;在气压试验时,此应力不得超过试验温度下材料屈服点的80%;
(2)制造完工的换热器应按GB150“钢制焊接压力容器技术标准”的规定进行压力试验;
(3)换热器需经水压试验合格后方可进行气密性试验;
(4)压力试验必须用两个量程相同的并经过校正的压力表。压力表的量程在试验的2倍左右为宜,但不应低于1.5倍和高于4倍的试验压力;
(5)换热器的开孔补强圈应在压力试验以前通入0.4~0.5Mpa的压缩空气检查焊缝质量;
(6)水压试验和气密性试验的试验介质、试验温度、试验方法要严格按照容器压力试验的有关规定进行;
(7)换热压力容器液压试验程序应按GB151规定进行;
(8)水压试验和空密性试验在确认无泄漏后,应保压30min。
四、换热器泄漏后如何进行试漏检查?怎样进行堵管?
一、试漏检查
为了查明管子的泄漏情况,首先要作水压试验,,一般均采用在管子外侧加压力的外压试验。其方法是:把水通入壳体,保持一定时间,用目测检查两端管板处管子的泄漏情况,对漏管做出记录。
二、堵管
管子本身的泄漏一般情况下是无法修复的,假如泄漏管子的数量不多时,可以用圆锥形的金属堵头将管口两端堵塞,如管程压力较高时,堵紧后再焊住更可靠。堵头的长度一般为管内径的2倍,小端直径应等于0.85倍的内径,锥度为1:10,堵头材料的硬度应低于或等于管子的硬度。用堵管来消除泄漏时堵管数不得超过10%。
五、换热器腐蚀的主要部位是哪些?为什么会发生腐蚀?
换热器腐蚀的主要部位是换热管、管子与管板连接处、管子与折流板交界处、壳体等。腐蚀原因如下:
一、换热管腐蚀
由于介质中污垢、水垢以及入口介质的涡流磨损易使管子产生腐蚀,特别是在管子入口端的40~50mm处的管端腐蚀,这主要是由于流体在死角处产生涡流扰动有关。
二、管子与管板、折流板连接处的腐蚀
换热管与管板连接部位及管子与折流板交界处都有应力集中,容易在胀管部位出现裂纹,当管与管板存在间隙时,易产生Cl+的聚积及氧的浓差,从而容易在换热管表面形成点坑或间隙腐蚀使它成为SCC的裂源。管子与折流板交界处的破裂,往往是由于管子长,折流板多,管子稍有弯曲,容易造成管壁与折流板处产生局部应力集中,加之间隙的存在,故其交界处成为应力腐蚀的薄弱环节。
三、壳体腐蚀
由于壳体及附件的焊缝质量不好也易发生腐蚀,当壳体介质为电解质,壳体材料为碳钢,管束用折流板为铜合金时,易产生电化学腐蚀,把壳体腐蚀穿孔。
管壳式换热器的检修内容是:
一、小修内容
1)拆卸换热器两端封头或管箱;
2)清洗、清扫管子内表面和壳体异物。并检查换热器两端盖、管箱的腐蚀、锈蚀、裂纹、砂眼等缺陷;
3)对管束和壳体进行试压和试漏;
4)检查螺栓及保温、防腐;
5)进行局部测厚。
二、中修内容
1)包括小修内容;
2)抽出管束清理、清扫、清洗,并检查换热管的变形和弯曲情况;
3)检查隔板和折流板及拉杆螺栓的腐蚀情况;
4)检查换热器各密封面情况,表面不应有划痕、凹坑和点蚀。
三、大修内容
1)包括中、小修内容;
2)全面检查换热器的运行情况,并对管板与管子焊接处进行着色检验。 管壳式换热器日常维护的内容
管壳式换热器日常维护和监测应观察和调整好以下循环水的工艺指标。
一、温度
温度是换热器运行中的主要控制指标,从换热器进出口流体温度变化的情况可分析换热器的换热效果,判断换热器传热效率的高低,主要在传热系数上,传热系数低其效率也低,由进出口的温度可决定对换热器进行检查和清洗。
二、压力
换热器列管若干结垢严重,则阻力增大,所以日常要对换热器的进出口压差进行测定和检验,特别对高压流体的换热器更要特别重视,如果列管泄露,高压流体一定向低压侧泄漏,造成低压侧压力上升较快,甚至超压。所以必须解体检修或堵管。
三、振动
换热器内部的流体流速一般较高,由于流体的脉冲和流动都会造成换热管的振动,或者整个设备振动,但最危险的是工艺开车过程中,提压或加负荷较快,很容易引起换热管振动,特别是在隔板处,管子振动的频率较高,容易把管切断,造成断管泄漏,遇到这种情况必须停机解体检查,检修换热器。
固定管板式换热器有哪几部分组成?结构特点是什么?浮头式换热器的浮头有几种形式?
固定管板式换热器主要由外壳、封头、管板、管束折流板或支撑板等部件组成。
其结构特点是:在壳体中设置有平行管束,管束两端用焊接或胀接的方法固定在管板上,两端管板直接和壳体焊接在一起,壳体的进出管直接焊接在壳体上,装有进口或出口管的封头管箱用螺栓与外壳两管板紧固。管束内根据换热管的长度设置了若干块折流板。这种换热器,管程可以用隔板分成任何程数。
浮头换热器的浮头常用的有两种形式。第一种是靠夹钳形半环和若干个压紧螺钉使浮头盖和活动管板密封结合起来,保证管内和管间互不渗漏。第二种是使浮头盖法兰直接和勾圈法兰用螺栓紧固,使浮头盖法兰和活动管板密封贴合,虽然减少了管束的有效传热面积,但密封性可靠,整体也较紧凑。
板式换热器的工作原理是什么?有何特点?
板式换热器是由许多波纹形的传热板片,按一定的间隔,通过橡胶垫片压紧组成的可拆卸的换热设备。板片组装时,两组交替排列,板与板之间用粘结剂把橡胶密封板条固定好,其作用是防止流体泄漏并使两板之间形成狭窄的网形流道,换热板片压成各种波纹形,以增加换热板片面积和刚性,并能使流体在低流速成下形成湍流,以达到强化传热的效果。板上的四个角孔,形成了流体的分配管和泄集管,两种换热介质分别流入各自流道,形成逆流或并流通过每个板片进行热量的交换。
其特点:(1)体积小,占地面积少;(2)传热效率高;(3)组装灵活;(4)金属消耗量低;(5)热损失小;(6)拆卸、清洗、检修方便;(7)板式换热器缺点是密封周边较长,容易泄漏,使用温度只能低于150ºC,承受压差较小,处理量较小,一旦发现板片结垢必须拆开清洗。
六、板式换热器有哪几部分组成?有什么作用?
板式换热器主要由传热板片、密封垫片、两端压板、固定封头、活动封头(头盖)、夹紧螺栓、支架、进出管等组成。
各部件作用如下:
一、传热板片
传热板片是换热器主要起换热作用的元件,一般波纹做成人字形,按照流体介质的不同,传热板片的材质也不一样,大多采用不锈钢和钛材制作而成。
二、密封垫片
板式换热器的密封垫片主要是在换热板片之间起密封作用。板式换热器的泄漏多是因为密封垫片压错位或者老化引起的。
三、两端压板
两端压板主要是夹紧压住所有的传热板片,保证流体介质不泄漏。
四、夹紧螺栓
夹紧螺栓主要是起紧固封头和换热板片的作用。夹紧螺栓一般是通扣螺纹,预紧螺栓时,一定用力矩扳手,使固定板片的力矩均匀。
五、挂架
主要是支承换热板片,使其拆卸、清洗、组装等方便。
板式换热器中、大修的内容有哪些?
板式换热器中修的内容是:
(1)拆除进出管清洗杂物;
(2)检查进出管的橡胶内衬,不应有裂纹和破坏;
(3)检查测量螺栓预紧力和板片总体尺寸。
板式换热器大修的内容是:
(1)包括中修内容;
(2)如换热器结垢,应解体清洗,或者另行配管在线化学清洗;
(3)用放大镜检查密封垫片的弹性和压缩变形情况,必要时可以更换;
(4)检查传热板片变形情况;
(5)检查传热板片有无腐蚀、穿孔等缺陷;
(6)重新组装,压紧螺栓;
(7)试压;
(8)复位。
板式换热器的拆装程序如下:
(1)板式换热器拆卸前,首先测量板束的压紧长度尺寸,做好记录(重装时应按此尺寸);
(2)拆下夹紧螺栓和全部换热片;
(3)取下各板片上的密封垫片,为防止用螺丝刀刺破板片,可采取液氮急冷法,使橡胶板条急冷变形,然后撕下;
(4)清理密封槽内的残余粘结剂,清洗板片上的污垢;
(5)用灯光或渗透法检查传热板片有无裂纹或穿孔。检查板片上是否有凹坑或变形;
(6)修复或更换损坏的板片;
(7)重新组装。组装前首先用丙酮清洗密封槽,并用401号粘结剂,水平位置粘好密封条;
(8)粘好密封条的板片,每50片一组,用20~30mm的钢板压紧,在周围环境温度为30~35ºC的范围内固化24h,可以挂片;
(9)挂片完毕,轻挂两端压盖,并穿固定螺栓;
(10)用力矩扳手均匀地拧紧螺栓;
(11)测量组装压紧后板片的总长度;
(12)装进出口内衬套;
(13)整体试压。首先将板片一侧的流体通道的入口管盲死,装满水,然后在板片另一侧的工作介质通道出口管上加一带放气短管的盲板,在试压侧装上压力表。充满水后用手压泵加压,为操作压力的1.5倍,并保持30min,压力无下降即可连接外管。
板式换热器泄漏主要由以下原因造成:
(1)换热板片腐蚀穿透;
(2)换热板片有裂纹;
(3)夹紧螺栓紧固不均匀;
(4)换热板片变形太大;
(5)密封垫片断裂或老化;
(6)密封垫片厚度不均;
(7)密封垫片压偏。
板式换热器与列管式换热器比较有什么优点?
(1)体积小,占地面积少。板式换热器占地面积为同样换热能力的列管式换热器的30%左右。
(2)传热效率高。传热系数可达16700KJ/(m2*h*ºC)[4000kcal/(m2*h*ºC)],较之列管换热器高2~4倍。
(3)组装方便。当增加换热泪盈眶面积时,只需多装板片,进出口方位不需变动。
(4)金属消耗量低;
(5)拆卸、清洗、检修方便,不易结垢。
推荐第6篇:换热器心得
换热器心得.换热器机组控制是学校为地方经济服务开设的一门课程,也为学生提供了就业的另一途径,四平市被称为全国换热器之乡,在这里对于我们自动化专业的学生是比较好就业的地方。 实训的第三天,下午一点在张旭老师带领下,我们参观了四平巨元瀚洋板式换热器有限公司。首先公司员工为我们介绍公司的状况和主要生产器件。然后在师傅的带领下,我们参观了车间,我们看到制作板式换热器的全过程,师傅详细讲解了每一道制作的步骤,加深了我们对板式换热器的更深一步得了解。经介绍四平巨元瀚洋板式换热器有限公司与有着丰富资本运作经验的深圳比克公司重组,达成战略合作伙伴关系,于2009年6月30日在美国纳斯达克实现柜台交易,并于今年7月8日借壳在美国纳斯达克成功转为主板上市,成为吉林省第一家在纳斯达克资本市场成功上市的公司。四平巨元瀚洋板式换热器有限公司的上市,是四平市进行资本运作的成功典范。
通过参观板式换热器工厂,对这门课程有了感性的认识,对换热器的结构有了具体认识。在理解换热器工艺的基础上,掌握了换热器装配中常用 的技术设计要求,掌握了换热器冷热交换及设计工艺。
这次实训让我明白板式换热器主要由框架和板片两大部分组成。 板片由各种材料的制成的薄板用各种不同形式的磨具压成形状各异的波纹,并在板片的四个角上开有角孔,用于介质的流道。板片的周边及角孔处用橡胶垫片加以密封。? 框架由固定压紧板、活动压紧板、上下导杆和夹紧螺栓等构成。? 板式换热器是将板片以叠加的形式装在固定压紧板、活动压紧板中间,然后用夹紧螺栓夹 这次实训使我感受很深:
一、要学会吃苦恼劳不在困难面前低头,在工作时不应耍脾气要学会适应别人与别人沟通我们工作是一个团体不是个人的。要想做好任何事,除了自己平时要有功底外,我们还需要一定的实践动手能力,操作能力,每个同学都应该完善自己的文化知识。在这个竞争如此激烈的社会中,只有努力充实自己才能不被社会淘汰。
二、以前在学校对自己的未来十分迷茫,但通过这次实训我们体会到了我们这一行的艰辛和干这一行所需要必备怎样的能力,在校期间我们要明确自己未来的方向、定下目标给自己定位,并克服困难提升能力来适应自己的岗位。
增强了我们对本专业的热爱,培养了我们实事求是、一丝不苟的学风;培养了我们脚踏实地、团结协作的作风和敬业爱岗的精神,激励了学生的创意和创新精神;
培养了我们认真、刻苦,勇于实践的工作作风,养成规范、严谨的工作态度,使我们想着具有高层次社会道德、文化修养并掌握先进技术理念与技能的工艺技术人员、助理工程人员又迈进了一步!
这是一个短暂而又充实的实训,虽然结束了但是我们获益匪浅。虽然实训结束了但我们现在的学习并未结束,我们应该珍惜在学校的短短时光,多学习,把自身的弱势和不足变成优势与特长,扫清我们就业道路的阻碍,为自己的未来而努力加油!
在此要感谢我们亲爱的老师是你们无私的奉献给我们更多的希望。我会努力加油,用优异的成绩来回报你和社会。
推荐第7篇:换热器论文
09无机非(1)
材料工程基础论文
管壳式换热器论文
摘要; 本文主要介绍管壳式换热器。并分析其特点。 关键词:管壳式换热器、传热管束、管板、折流板
正文:管壳式换热器由壳体、传热管束、管板、折流板(挡板)和管箱等部件组成。壳体多为圆筒形,内部装有管束,管束两端固定在管板上。进行换热的冷热两种流体,一种在管内流动,称为管程流体;另一种在管外流动,称为壳程流体。为提高管外流体的传热分系数,通常在壳体内安装若干挡板。挡板可提高壳程流体速度,迫使流体按规定路程多次横向通过管束,增强流体湍流程度。换热管在管板上可按等边三角形或正方形排列。等边三角形排列较紧凑,管外流体湍动程度高,传热分系数大;正方形排列则管外清洗方便,适用于易结垢的流体。 管壳式换热器
流体每通过管束一次称为一个管程;每通过壳体一次称为一个壳程。图示为最简单的单壳程单管程换热器,简称为1-1型换热器。为提高管内流体速度,可在两端管箱内设置隔板,将全部管子均分成若干组。这样流体每次只通过部分管子,因而在管束中往返多次,这称为多管程。
类型:由于管内外流体的温度不同,因此换热器的壳体与管束的温度也不同。如果两温度相差很大,换热器内将产生很大热应力,导致管子弯曲、断裂,或从管板上拉脱。因此,当管束与壳体温度差超过50 ℃时,需采取适当补偿措施,以消除或减少热应力。根据所
09无机非(1)
材料工程基础论文
采用的补偿措施,管壳式换热器可分为以下几种主要类型:
① 固定管板式换热器 管束两端的管板与壳体联成一体,结构简单,但只适用于冷热流体温度差不大,且壳程不需机械清洗时的换热操作。当温度差稍大而壳程压力又不太高时,可在壳体上安装有弹性的补偿圈,以减小热应力。
② 浮头式换热器 管束一端的管板可自由浮动,完全消除了热应力;且整个管束可从壳体中抽出,便于机械清洗和检修。浮头式换热器的应用较广,但结构比较复杂,造价较高。
③ U型管换热器 每根换热管皆弯成U形,两端分别固定在同一管板上下两区,借助于管箱内的隔板分成进出口两室。此种换热器完全消除了热应力,结构比浮头式简单,但管程不易清洗。
非金属材料换热器 化工生产中强腐蚀性流体的换热,需采用
09无机非(1)
材料工程基础论文
陶瓷、玻璃、聚四氟乙烯、石墨等非金属材料制作管壳式换热器。这类换热器的换热性能较差,只用于压力低、振动小、温度较低的场合。
流道的选择
进行换热的冷热两流体,按以下原则选择流道:①不洁净和易结垢流体宜走管程,因管内清洗较方便;②腐蚀性流体宜走管程,以免管束与壳体同时受腐蚀;③压力高的流体宜走管程,以免壳体承受压力;④饱和蒸汽宜走壳程,因蒸汽冷凝传热分系数与流速无关,且冷凝液容易排出;⑤若两流体温度差较大,选用固定管板式换热器时,宜使传热分系数大的流体走壳程,以减小热应力。
操作强化
当管壁两侧传热分系数相差很大时(如粘度小的液体与气体间的换热),应设法减小传热分系数低的一侧的热阻。如果管外传热分系数小,可采用外螺纹管(低翅片管),以增大管外一侧的传热面积和流体湍动,减小热阻。如果管内传热分系数小,可在管内设置麻花铁,螺旋圈等添加物,以增强管内扰动,强化换热,当然这时流体的流动阻力也将增大。
管壳式换热器 - shell and tube heat exchanger 由一个壳体和包含许多管子的管束所构成,冷、热流体之间通过管壁进行换热的换热器。管壳式换热器作为一种传统的标准换热设备,在化工、炼油、石油化工、动力、核能和其他工业装置中得到普遍采用,特别是在高温高压和大型换热器中的应用占据绝对优势。通常的工作压力可达4兆帕,工作温度在200℃以下,在个别情况下还可达到更高的压力和温度。一般壳体直径在1800毫米以下,管子长度在9米以下,在个别情况下也有更大或更长的。
09无机非(1)
材料工程基础论文
为提高换热器的传热效能,也可采用螺纹管、翅片管等。管子的布置有等边三角形、正方形、正方形斜转45°和同心圆形等多种形式,前3 种最为常见。按三角形布置时,在相同直径的壳体内可排列较多的管子,以增加传热面积,但管间难以用机械方法清洗,流体阻力也较大。管板和管子的总体称为管束。管子端部与管板的连接有焊接和胀接两种。在管束中横向设置一些折流板,引导壳程流体多次改变流动方向,有效地冲刷管子,以提高传热效能,同时对管子起支承作用。折流板的形状有弓形、圆形和矩形等。为减小壳程和管程流体的流通截面、加快流速,以提高传热效能,可在管箱和壳体内纵向设置分程隔板,将壳程分为2程和将管程分为2程、4程、6程和8程等。管壳式换热器的传热系数,在水-水换热时为1400~2850瓦每平方米每摄氏度〔W/(m2〃℃)〕;用水冷却气体时,为10~280W/(m2〃℃);用水冷凝水蒸汽时,为570~4000W/(m2〃℃)。
分类
管壳式换热器按结构特点分为固定管板式换热器、浮头式换热器、U型管式换热器、双重管式换热器、填函式换热器和双管板换热器等。前 3种应用比较普遍。
固定管板式换热器
它是管壳式换热器的基本结构形式。管子的两端分别固定在与壳体焊接的两块管板上。在操作状态下由于管子与壳体的壁温不同,二者的热变形量也不同,从而在管子、壳体和管板中产生温差应力。这一点在分析管板强度和管子与管板连接的可靠性时必须予以考虑。为减小温差应力,可在壳体上设置膨胀节。固定管板式换热器一般只在适当的温差应力范围、壳程压力不高的场合下
09无机非(1)
材料工程基础论文
采用。固定管板式换热器的结构简单、制造成本低,但参与换热的两流体的温差受一定限制;管间用机械方法清洗有困难,须采用化学方法清洗,因此要求壳程流体不易结垢。
浮头式换热器
浮头式换热器的结构为管子一端固定在一块固定管板上,管板夹持在壳体法兰与管箱法兰之间,用螺栓连接;管子另一端固定在浮头管板上,浮头管板与浮头盖用螺栓连接,形成可在壳体内自由移动的浮头。由于壳体和管束间没有相互约束,即使两流体温差再大,也不会在管子、壳体和管板中产生温差应力。浮头式换热器适用于温度波动和温差大的场合;管束可从壳体内抽出用机械方法清洗管间或更换管束。但与固定管板式换热器相比,它的结构复杂、造价高。
U型管式换热器 一束管子被弯制成不同曲率半径的U型管,其两端固定在同一块管板上,组成管束。管板夹持在管箱法兰与壳体法兰之间,用螺栓连接。拆下管箱即可直接将管束抽出,便于清洗管间。管束的U形端不加固定,可自由伸缩,故它适用于两流体温差较大的场合;又因其构造较浮头式换热器简单,只有一块管板,单位传热面积的金属消耗量少,造价较低,也适用于高压流体的换热。但管子有U形部分,管内清洗较直管困难,因此要求管程流体清洁,不易结垢。管束中心的管子被外层管子遮盖,损坏时难以更换。相同直径的壳体内,U形管的排列数目较直管少,相应的传热面积也较小。
双重管式换热器
将一组管子插入另一组相应的管子中而构成的换热器。管程流体从管箱进口管流入,通过内插管到达外套管的底
09无机非(1)
材料工程基础论文
部,然后返向,通过内插管和外套管之间的环形空间,最后从管箱出口管流出。其特点是内插管与外套管之间没有约束,可自由伸缩。因此,它适用于温差很大的两流体换热。但管程流体的阻力较大,设备造价较高。
填函式换热器
填函式换热器的结构,管束一端与壳体之间用填料密封。管束的另一端管板与浮头式换热器同样夹持在管箱法兰与壳体法兰之间,用螺栓连接。拆下管箱、填料压盖等有关零件后,可将管束抽出壳体外,便于清洗管间。管束可自由伸缩,具有与浮头式换热器相同的优点。由于减少了壳体大盖,它的结构较浮头式换热器简单,造价也较低;但填料处容易渗漏,工作压力和温度受一定限制,直径也不宜过大。
双管板换热器管子两端分别连接在两块管板上,两块管板之间留有一定的空间,并装设开孔接管。当管子与一侧管板的连接处发生泄漏时,漏入的流体在此空间内收集起来,通过接管引出,因此可保证壳程流体和管程流体不致相互串漏和污染。双管板换热器主要用于严格要求参与换热的两流体不互相串漏的场合,但造价比固定管板式换热器高。
特点
这种换热器结构较简单,操作可靠,可用各种结构材料(主要是金属材料)制造,能在高温、高压下使用,是目前应用最广的类型。由壳体、传热管束、管板、折流板(挡板)和管箱等部件组成。壳体多为圆筒形,内部装有管束,管束两端固定在管板上。进行换热的冷热两种流体,一种在管内流动,称为管程流体;另一种在管外流
09无机非(1)
材料工程基础论文
动,称为壳程流体。为提高管外流体的传热分系数,通常在壳体内安装若干挡板。挡板可提高壳程流体速度,迫使流体按规定路程多次横向通过管束,增强流体湍流程度。换热管在管板上可按等边三角形或正方形排列。等边三角形排列较紧凑,管外流体湍动程度高,传热分系数大;流体每通过管束一次称为一个管程;每通过壳体一次称为一个壳程。图示为最简单的单壳程单管程换热器,简称为1-1型换热器。为提高管内流体速度,可在两端管箱内设置隔板,将全部管子均分成若干组。这样流体每次只通过部分管子,因而在管束中往返多次,这称为多管程。同样,为提高管外流速,也可在壳体内安装纵向挡板,迫使流体多次通过壳体空间,称为多壳程。多管程与多壳程可配合应用。
09无机非(1)
材料工程基础论文
参考文献:1.http://www.daodoc.com/100k/read.php?tid=3280 3.江南 易宏 甑亮 岑汉钊.管壳式换热器壳程强化传热 研究进展.化肥工业 1998 25 6 : 27 321
4.罗运禄 谭志明 崔乃英 张绣云.氮肥厂换热设备的强 化改造.化肥工业
23 2 : 21 251
推荐第8篇:换热器概论
换热器
机电工程技术学院 过程
091班 盖伟
随着科技高速发展的今天,换热器已广泛应用国内各个生产领域,换热器跟人们生活息息相关。换热器顾名思义就是用来热交换的机械设备。有气体-气体交换,气体-液体交换,液体-液体交换这几种。就是一种介质热能降低,另一种介质热能增多,达到热平衡,符合Q(吸) =Q(放)的热平衡公式。
在化工生产中换热器可作为加热器、冷却器、冷凝器、蒸发器和再沸器等,应用更加广泛。换热器种类很多,但根据冷、热流体热量交换的原理和方式基本上可分三大类即:间壁式、混合式和蓄热式。在三类换热器中,间壁式换热器应用最多 换热器简介及分类
换热器是一种非常重要的换热设备,能够把热量从一种介质传递给另一种介质,在各种工业领域中有很广泛的应用。尤其在化工、能源、交通、机械、制冷、空调等领域应用更广泛。换热器能够充分利用工业的二次能源,并且能够实现余热回收和节能。
换热器的种类很多,根据不同的工业领域可以选用不同的换热器,可以更大的发挥换热器的传递热量的作用。现在由于人们追求换热器重量轻、占地面积少、使用经济性高,从而推动了紧凑式换热表面的发展,所以紧凑式换热器在实际应用中种类很多。管壳式的换热器在过程工业中的应用很广泛。除了工业中用到的主要换热器种类,如紧凑式换热器、管壳式换热器、再生器和板式换热器外,还有其他特殊的换热器,如双套管、热管、螺旋式、板壳式、夹套式等。
换热器根据传递过程分为:间接接触式——直接传递式、蓄热式、流化床等。 直接接触式——冷却塔。 根据流动形式分为:并流、逆流、错流。
根据分成情况分类:单程换热器、多程换热器、
根据流体的相态分类:气-液换热器、液-液换热器、气-气换热器。 根据传热机理分类:冷凝器、蒸发器 1.2常见换热器原理及特点
各种换热器的作用、工作原理、结构以及其中工作的流体种类、数量等差别很大,因此几种常见换热器的构造和原理如下: ■ 板式换热器的构造原理、特点:
板式换热器由高效传热波纹板片及框架组成。板片由螺栓夹紧在固定压紧板及活动压紧板之间,在换热器内部就构成了许多流道,板与板之间用橡胶密封。压紧板上有本设备与外部连接的接管。板片用优质耐腐蚀金属薄板压制而成,四角冲有供介质进出的角孔,上下有挂孔。人字形波纹能增加对流体的扰动,使流体在低速下能达到湍流状态,获得高的传热效果。并采用特殊结构,保证两种流体介质不会串漏。 ■螺旋板式换热器的构造原理、特点:
螺旋板式换热器是一种高效换热器设备,适用汽-汽、汽-液、液-液,对液传热。它适用于化学、石油、溶剂、医药、食品、轻工、纺织、冶金、轧钢、焦化等行业。按 结构形式可分为 不可拆式(Ⅰ型)螺旋板式及可拆式(Ⅱ型、Ⅲ型)螺旋 板式换热器。 ■ 列管式换热器的构造原理、特点: 列管式换热器(又名列管式冷凝器),按材质分为碳钢列管式换热器,不锈钢列管式换热器和碳钢与不锈钢混合列管式换热器三种,按形式分为固定管板式、浮头式、U型管式换热器,按结构分为单管程、双管程和多管程,传热面积1~500m2,可根据用户需要定制。 ■ 管壳式换热器的构造原理、特点:
管壳式换热器是进行热交换操作的通用工艺设备。广泛应用于化工、石油、石油化工、电力、轻工、冶金、原子能、造船、航空、供热等工业部门中。特别是在石油炼制和化学加工装置中,占有极其重要的地位。 ■ 容积式换热器的构造原理、特点:
自动控温节能型容积式热交换器,它充分利用蒸汽能源、高效、节能,是一种新型热水器。普通热水器一般需要配置水水热交换器来降低蒸汽凝结水温度以便回用。而节能型热交换器凝结水出水温度在45℃左右,或直接回锅炉房重复使用。这样减少了设备投资,节约热交换器机房面积,从而降低基建造价,因此节能型容积式热交换器深受广大设计、用户单位欢迎。
钢衬铜热交换器比不锈钢热交换器经济,并且技术上有保证。它利用了钢的强度和铜的耐腐蚀性,即保证热交换器能承受一定工作压力,又使热交换器出水质量好。钢壳内衬铜的厚度一般为1.0mm。钢衬铜热交换器必须防止在罐内形成部分真空,因此产品出厂时均设有防真空阀。此阀除非定期检修是绝对不能取消的。部分真空的形成原因可能是排出不当,低水位时从热交换器,或者排水系统不良。水锤或突然的压力降也是造成压负的原因。 ■ 浮头式换热器的构造原理、特点:
浮头式换热器其一端管板与壳体固定,而另一端的管板可以在壳体内自由浮动。壳体和管束对热膨胀是自由的,故当两种介质的温差较大时,管束与壳体之间不会产生温差应力。浮头端设计成可拆结构,使管束可以容易地插入或抽出,这样为检修和清洗提供了方便。这种形式的换热器特别适用于壳体与换热管温差应力较大,而且要求壳程与管程都要进行清洗的工况。
■ 管式换热器的构造原理、特点:
DLG型列管式换热器利用热传导和热辐射的原理,烟道气通过管程与逆流通过壳程的空气进行能量交换,从而达到输出洁净热空气的目的。该换热器结构紧凑,运行可靠,列管采用耐高温的薄壁波纹管,增加发传热面积和换热效率。广泛应用于化工、制药、轻工等行业废气余热利用和空气加热。 ■热管换热器的构造原理、特点:
热管是一种高效传热元件,其导热能力比金属高几百倍至数千倍。热管还具有均温特性好、热流密度可调、传热方向可逆等特性。用它组成热管换热器不仅具有热管固有的传热量大、温差小、重量轻体积小、热响应迅速等特点,而且还具有安装方便、维修简单、使用寿命长、阻力损失小、进、排风流道便于分隔、互不渗漏等特点。
热管是由内壁加工有槽道的两端密封的铝(轧)翅片管经清洗并抽成高真空后注入最佳液态工质而成,随注入液态工质的成分和比例不同,分为KLS低温热管换热器、GRSC-A中温热管换热器、GRSC-B高温热管换热器。热管一端受热时管内工质汽化,从热源吸收汽化热,汽化后蒸汽向另一端流动并遇冷凝结向散热区放出潜热。冷凝液借毛细力和重力的作用回流,继续受热汽化,这样往复循环将大量热量从加热区传递到散热区。热管内热量传递是通过工质的相变过程进行的。将热管元件按一定行列间距布置,成束装在框架的壳体内,用中间隔板将热管的加热段和散热段隔开,构成热管换热器。
■ 汽水换热器的构造原理、特点:
该换热器是在板式换热器的基础上加装降温与降压器而组成的,利用调节器对高蒸汽或高温水进行一级换热使之降之150℃以下。进入板式换热器进行换热,适用于高温蒸汽及高温水(150℃以上)。这种装置集板式换热器同时具有降温与降压器的优点。使换热器更加充分地进行热量交换。
■ 空气换热器的构造原理、特点:
加热炉窑为了降低能耗,在烟道中设置空气换热器,以回收烟气中的大量余热,达到节约燃料、降低生产成本,提高燃烧温度、增加炉子的产量。空气换热器是余热利用的理想设备,在轧钢加热炉、热处理炉、煅造加热炉等各种工业炉窑上得到广泛应用。炉用空气换热器的种类很多, 目前国内外绝大多数采用的是金属换热器,空气换热器是利用炉窑排出的尾气热量将空气预热至一定的温度后返回炉内助燃或用于其它设备。金属换热器具有体积小、热交换效率高、严密性好、结构简单等特点。 ■ 波纹管换热器的构造原理、特点:
产品特点一种新型的强化传热节能型高效换热设备,在传统列管式换热器的基础上,采用强化传热技术,是对传统各类换热器的重大突破。公称通径DN325~2000mm;公称压力P0.6~.4Mpa;换热管规格Ф19,Ф25,Ф32,Ф42.壁厚0.5~1.0;工作介质水-水、汽-水、油-水、油-油等多种换热介质。总传热系数水-水K=2000~3500w/㎡;汽-水K=2500~4000w/㎡;其它介质视介质物理性能及工况而定。优性能传热效率高,防腐能力好,不污、不堵、不易结垢,无需维护,密封可靠,运行平稳,占地少,节省投资。 ■石墨换热器的构造原理、特点:
圆块孔式石墨换热器由柱形不渗透性石墨换热块、石墨上下盖和其间的氟氧橡胶(或柔性石墨)O型圈及金属外壳、压盖等组装而成。是目前较先进、性能较优越的一种石墨换热器。圆柱形石墨换热块有较高的结果强度,并易与解决密封问题;在密封中采用氟橡胶(或柔性石墨)O型圈密封介质,加装压力弹簧作为热胀冷缩的自动补偿,以起到密封保持作用;采用短通道提高紊流程度使设备结构度高、耐温耐压性能强、抗热冲击性能好、体积利用率高、传热效果好并便于装拆检修。设备纵向孔走腐蚀性介质,横向孔走非腐蚀性介质。
间壁式换热器的类型包括板式换热器,夹套式换热器,沉浸式蛇管换热器,喷淋式换热器,套管式换热器,管壳式换热器。
板式换热器是一种结构紧凑,组装方便,占地面积小,传热系数的热交换设备。当雷诺数为200时,就能达到湍流状态,热系数可达4000-7000W/M2℃,是同等流速的管壳式换热器的3至5倍。设计上是软硬结合的热混合的设计技术,不同的波纹面的孪生软硬板,根据不同的要求,可以组合不同的阻力的流道,从而使传热达到最优化,可实现其经济合理化。其最大的缺点由于组合件是有橡胶密封,承压有极限,不能应用相高压的环境中。由于板片之间交叉成网状结构,要求其运行的介质分子的颗粒要有一定的范围,不然很容易堵塞,由于独特的组合形式,泄露时维修极其方便,更换配件简单,所以大多行业用量较大,例如集中供热行业、轻工、石油、化工食品等多个行业。
管壳式换热器是一种设计复杂制造工艺繁琐的换热设备,在压力容器的制造过程中,必须遵守相应的章程和制度,管板的厚度,壳体的厚度都得符合GB6654-1996和GB713-1997的相应标准,不锈钢的标准符合GB/T4237-2007的水平,换热管的设计也要根据腐蚀程度,抗压能力上做严格的选择。其在运行的过程中流体的相对流向一般有顺流和逆流2种。顺流时,入口处两流体的温差最大,并沿传热表面逐渐减小,至出口处温差为最小。逆流时,沿传热表面两流体的温差分布较均匀。在冷、热流体的进出口温度一定的条件下,当两种流体都无相变时,以逆流的平均温差最大顺流最小管式换热器在完成同样传热量的条件下,采用逆流可使平均温差增大,换热器的传热面积减小;若传热面积不变,采用逆流时可使加热或冷却流体的消耗量降低。前者可节省设备费,后者可节省操作费,故在设计或生产使用中应尽量采用逆流换热。管式换热器当冷、热流体两者或其中一种有物相变化(沸腾或冷凝)时,由于相变时只放出或吸收汽化热,流体本身的温度并无变化,因此流体的进出口温度相等,这时两流体的温差就与流体的流向选择无关了。除顺流和逆流这两种流向外,还有错流和折流等流向。管式换热器在传热过程中,降低间壁式换热器中的热阻,以提高传热系数是一个重要的问题。热阻主要来源于间壁两侧黏滞于传热面上的流体薄层(称为边界层),和换热器使用中在壁两侧形成的。污垢层,金属壁的热阻相对较小.管式换热器增加流体的流速和扰动性,可减薄边界层,降低热阻提高给热系数。但增加流体流速会使能量消耗增加,故设计时应在减小热阻和降低能耗之间作合理的协调。为了降低污垢的热阻,可设法延缓污垢的形成,并定期清洗传热面。管式换热器都用金属材料制成,其中碳素钢和低合金钢大多用于制造中、低压换热器;不锈钢除主要用于不同的耐腐蚀条件外,奥氏体不锈钢还可作为耐高、低温的材料;铜、铝及其合金多用于制造低温换热器;镍合金则用于高温条件下;非金属材料除制作垫片零件外,有些已开始用于制作非金属材料的耐蚀 换热器,如石墨换热器、氟塑料换热器和玻璃换热器等。管式换热器按不同方式不同分类1.固定管板式。固定管板式换热器的两端管和壳体制成一体,当两流体的温度差较大时,在外壳的适当位置上焊上一个补偿圈,或膨胀节。当壳体和管束热膨胀不同时,补偿圈发生缓慢的弹性变形来补偿因温差应力引起的热膨胀。特点为结构简单、造价低廉、壳程清洗和检修困难,壳程必须是洁净且不易结垢的物料。2.U形管式 。U形管式换热器每根管子均弯成U形,流体进、出口分别安装在同一端的两侧,封头内用隔板分成两室,每根管子可自由伸缩,来解决热补偿问题。特点为结构简单,质量轻,适用于高温和高压的场合。管程清洗困难,管程流体必须是洁净和不易结垢的物料。 3.浮头式。换热器两端的管板,一端不与壳体相连,该端浮头。管子受热时,管束连同浮头可以沿轴向自由伸缩,完全消除了温差应力。特点为结构复杂、造价高,便于清洗和检修,完全消除温差应力,应用普遍。但就其安装要有一定的空间,占地面积大,使用于寿命较长冶金,焦化等要求热交换率低的场所。
换热器技术的发展前景, 换热器在国民经济和化工生产领域中对产品质量、能量利用率以及系统经济性、可靠性起着举足轻重的作用因此开发新型高效和结构紧凑的换热器是目前换热器研究的一个重要方向。因此,几十年来,高效换热器的开发与研究始终是人们关注的课题,国内外先后推出了一系列新型高效换热器。新型高效换热器简介1 气动喷涂翅片管换热器2 焊接式板式换热器3 螺旋折流板换热器4 新型麻花管换热器Hitan绕丝花环换热器
而在我国换热器的制造技术远落后于外国,由于制造工艺和科学水平的限制,早期的换热器只能采用简单的结构,而且传热面积小、体积大和笨重,如蛇管式换热器等。随着制造工艺的发展,逐步形成一种管壳式换热器,它不仅单位体积具有较大的传热面积,而且传热效果也较好,长期以来在工业生产中成为一种典型的换热器。
在国外二十世纪20年代出现板式换热器,并应用于食品工业。以板代管制成的换热器,结构紧凑,传热效果好,因此陆续发展为多种形式。30年代初,瑞典首次制成螺旋板换热器。接着英国用钎焊法制造出一种由铜及其合金材料制成的板翅式换热器,用于飞机发动机的散热。30年代末,瑞典又制造出第一台板壳式换热器,用于纸浆工厂。在此期间,为了解决强腐蚀性介质的换热问题,人们对新型材料制成的换热器开始注意。60年代左右,由于空间技术和尖端科学的迅速发展,迫切需要各种高效能紧凑型的换热器,再加上冲压、钎焊和密封等技术的发展,换热器制造工艺得到进一步完善,从而推动了紧凑型板面式换热器的蓬勃发展和广泛应用。此外,自60年代开始,为了适应高温和高压条件下的换热和节能的需要,典型的管壳式换热器也得到了进一步的发展,这一类换热器不但是从材料上有了较大的突破,而且采用新颖的理念,增加强化传热。70年代中期,为了进一步减小换热器的体积,减轻重量和金属消耗,减少换热器消耗的功率,并使换热器能够在较低温差下工作,人们更是采用各种科学的办法来增强换热器内的传热。
70年代的世界能源危机,有力促进了换热强化技术的发展。为了节能将耗,提高工业生产经济效益,要求开发适用于不同工业过程要求的高效换热设备。所以这些年来,换热器的开发和研究成了人们关注的课题。当今换热器技术的发展以CFD(计算流体力学技术)、模型化技术、强化传热技术等形成一个高技术体系。所谓提高换热器性能,就是提高其传热性能。狭义的强化传热系数指提高流体和传热之间的传热系数。其主要方法归结为下述两个原理:温度边界层减勃和调换传热面附近的流体。
因此最近十几年来,强化传热技术受到了工业界的广泛重视,得到了十分迅速的发展,凝结是工业中普遍遇到的另一种相变换热过程,凝结换热系数很高,但经过强化措施还可以[3]进一步提升换热效率。
换热器的研究目的
任何一种石油、化工产品,都是人们利用一定的生产技术和按照特定的工艺要求,将原料经过一系列的物理或化学加工处理得到的。在生产实践中,要实现某种化工生产就需要有相应的机器和设备。
石油化学等过程工业的绝大数生产过程都是在化工设备这一特定空间内进行的。化工容器及设备是为生产工艺过程服务的,它必须在规定的工艺条件下,在单位时间内,尽可能利用最少的资源,最小的空间生产最多的产品,而且在经济上也是最为合理的。他们的性能,对整个装置的产品产量、生产能力、消耗定额以及“三废”治理和环境保护等方面都有重大影响。
随着石油化工装置的大型化和高参数化,开发和应用新型、高效、节能的化工设备,对石油化工生产具有非常重大的意义。
[4] [参考文献] [1] 曹伟.国外新型换热器技术[J].机电设备,2000,(2):46~47.[2] 方书起,祝春进,等.强化传热技术与新型高效换热器研究进展[J].化工机械,2004,(31)4.[3] 马晓驰.国内外新型高效换热器[J].化工进展,2001,(20)1.[4] 矫明,徐宏,等.新型高效换热器发展现状及研究方向[J].化工设计通讯,2007,(33)3.[ 5] 宋亚非,姜丽,沈占军各种换热器的原理及应用[ J] 2010.11
推荐第9篇:列管式换热器
江西科技师范大学
食品科学与工程专业《化工原理课程设计》说明书
题目名称
列管式换热器的设计
专业班级
11级食品科学与工程
学
号 20111912 20111878 20111911 学生姓名
胡利君 吕亚琼 钟翠 指导教师
常军 博士
2012 年 11 月 06日
目录
1.概述…………………………………………………………………………………
1 1.1设计方案………………………………………………………………………1
1.1.1设计条件…………………………………………………………………1
1.1.2选择换热器类型…………………………………………………………1
1.1.3传热器管程安排…………………………………………………………
2 1.2设计换热器的要求……………………………………………………………2 2.衡算…………………………………………………………………………………2
2.1传热面积的计算………………………………………………………………2
2.1.1定性温度的确定…………………………………………………………3
2.1.2计算平均传热温差………………………………………………………3
2.1.3初算传热面积……………………………………………………………3
2.2工艺结构尺寸…………………………………………………………………3
2.2.1管径和管内流速…………………………………………………………3 2.2.2管程数和传热数管数……………………………………………………3 2.2.3平均传热温差校正及壳程数……………………………………………
4 2.2.4传热管排列和分程方法…………………………………………………4
2.2.5壳体直径…………………………………………………………………4
2.2.6折流板……………………………………………………………………4 2.2.7接管………………………………………………………………………
5 2.3换热器核算……………………………………………………………………5 2.3.1传热面积校正……………………………………………………………5 2.3.2壳程传热膜系数…………………………………………………………6 2.3.3污垢热阻和壁管热阻……………………………………………………6 2.3.4换热器内压降得核算……………………………………………………7 3.总结………………………………………………………………………………8 4.附录………………………………………………………………………………9 4.1计算总表………………………………………………………………………9 4.2设备选型表…………………………………………………………………10 5.图纸………………………………………………………………………………11 6.参考文献及资料…………………………………………………………………12
1.概述 1.1设计方案
换热器是化工、石油、食品及其他许多部门的通用设备,在生产中常用的一种换热机械装置。按用途它可分为加热器、冷却器、冷凝器、蒸发皿和再沸器等。根据冷、热流体热量交换的原理和方式可分为三大类:混合式、蓄热式、间璧式。
本设计以列管式换热器为模型,以进口温度5℃、出口温度70℃、流量为30m3/h为 设计条件,针对列管式换热器生产过程中最主要的设备部件进行模拟设计和选型,本论文进行工艺设计、主要设备及附件尺寸的设计。
1.1.1设计条件
两流体的温度变化情况:热流体进口温度160℃,出口温度105℃;流体进口温度5℃,出口温度70℃。冷流体的流量为30m3/h。
1.1.2 选择换热器的类型
列管式换热器可分为固定管板式换热器、浮头式换热器和U型管式换热器。该换热器用饱和水蒸气加热,冬季操作时,其进口温度会降低,故而会加大管壁温度和壳体温度之差,所以温差较大。同时,在清洗和检修时,整个管束可以从壳体中抽出,因此应选用浮头式换热器。
1.1.3传热管管程安排
由于水较易结垢,如果流速太低,将会加快污垢增长速度,使换热器的热流量下降;因此,饱和水蒸汽应走壳程,水走管程。
1.2设计换热器的要求
(1)合理的实现所规定的工艺条件
传热量流体的物热力学参数与物理化学性质是工艺过程所规定的条件。设计者应根据这些条件进行热力学和流体力学的计算,经过反复比较,使所设计的换热器具有尽可能小的传热面积,在单位时间内传递尽可能多的热量,其具体做法如下。
增大传热系数?在综合考虑流体阻力及不发生流体诱发振动的前提下,尽量选择高的流速。
提高平均温差?对于无相变的流体,尽量采用接近逆流的传热方式。因为这样不仅可以提高平均温差,还有助于减少结构中的温差应力,在允许的条件下,可提高热流体的进口温度或降低冷流体的进口温度。
妥善布置传热面?例如在管壳式换热器中,采用合适的管间距和排列方式,不仅可以加大单位空间内的传热面积,还可以改善流体的流动性质,错列管束的传热方式比并列管束的好。如果换热器中的一侧有相变,另一侧流体为气相,可在气相一侧的传热面上加翅片,以增大传热面积,更有利于热量的传递
(2)安全可靠
换热器是压力容器,在进行强度,刚度,温差应力以及疲劳寿命计算时,应遵循我国《钢制石油化工压力容器设计规定》与《钢制管壳式换热器设计规定》
等有关规定与标准。这对保证设备的安全可靠起着重要作用
(3)有利于安装,操作与维修
直立设备的安全费往往低于水平或倾斜的设备。设备与部件应便于运输与装拆,在厂房移动时不会受到楼梯,梁柱的妨碍,根据需要可添置气,液排放口,检查孔与敷设保温层
(4)经济合理
评价换热器的最终指标是:在一定的时间内固定费用(设置的购置费和安装费等)与操作费(动力费,清洗费,维修费等)的总和为最小。在设计或选型时如果有几种换热器都能完成生产任务的需要,这一指标尤为重要。
传热面上垢层的产生和增厚,使传热系数不断降低,传热量随之减少,故有必要停止操作进行清洗。在清洗时不仅无法传递热量,还要支付清洗费,这部分费用必须从清洗后传热条件的改善得到补偿,因此存在一最适宜的运行周期
严格的讲,如果孤立的从换热器本身来进行经济核算已确定适宜的操作条件与适宜的尺寸是不够全面的,应以整个设备为对象进行经济核算或设备的优化。但要解决这样的问题难度很大,当影响换热器的各项因素改变后对整个系统的效益关系影响不大时,按照上述观点单独地对换热器进行经济核算仍然是可行的
选择换热器时,要遵循经济,传热效果优,方便清洗,符合实际需要等原则
2.衡算
2.1传热面积的计算
2.1.1定性温度的确定
57037.5C 2T1T2160105132.5C
热流体的定性温度:T22 冷流体的定性温度:Tt1t221附录三水在平均温度37.5C下的有关物性数据由可得
Cp,c4.174103J/kg.K,992.2kg/m3,653.3106pa.s
0.635W/(m.K)
1附录三饱和水蒸汽在平均温度132.5C的有关物性数据由可得
Cp,h4.266103J/(kg.K),1.650kg/m3,217.8106pa.s
0.686W/(m.K)
热负荷(忽略热损失):
30992.2QTqm,ccp,c(t2t1)4.174103(705)2.24106W
3600饱和水蒸汽用量(忽略热损失):
qm,hQT2.241069.55kg/s 3cp,ht4.2661055
2.1.2计算平均传热温差
t1T1t11055100C t2T2t21607090C
因为t11002,所以 t290tm逆=t1t21009095C 22
2.1.3初算传热面积
由于壳程气体的压力较大,故可选较大的K值。假设K610W/(m2.C),则可估算传热面积为:
QT2.24106S估=38.65m2
Ktm61095
2.2工艺结构和尺寸
2.2.1管径和管内流速
取管内流速u1.8m/s,传热数管数n10
d4qv430/36000.024m un1.8102由附录二十一查阅可选用33.53.25mm规格的钢管得d0.027m
根据
4q430/3600uv21.4m/s
d0.0272
2.2.2管程数和传热管数
4qv430/3600Ns11
d2u0.02721.4按单程管设计,所需的传热管长度为:
L S估d0NS38.6533.434
0.033511
按单程管设计,传热管过长,宜采用多管程结构。根据本设计实际情况采用非标准设计,先去传热管长度l8.5m,则该换热管的管程数为:
L34
Np4
l8.5传热管总数: n11444
2.2.3平均传热温差校正及壳程数
平均温差校正系数如下:
pt2t17050.42 T1t11605T1T21601050.85 t2t17051R按单壳程,双管程结构,查参考文献图4-25得t0.943平均传热温差:
tmttm逆=0.94395=89.585C
由于平均传热温差校正系数大于0.8,同时壳程流体流量较小,故取双壳程合适。
2.2.4传热管排列和分程方法
采用组合排列法,即每程内均按正三角形排列,隔板两侧采用正方形排列。
取管心距pt1.25d0,则pt1.2533.541.87542mm 隔板中心到离其最近一排管中心距离:
PZt627mm 各程相邻管的管心距为54mm。
2.2.5壳体直径
采用多管程结构,壳体直径可按参考文献式(4-15)估算。取管板利
2用率,则壳体直径为:
D1.05Ptn/1.054244/0.75337.78mm
按卷制壳体的进级档,可取D400mm。
2.2.6折流板
采用弓形折流板,取弓形折流板园缺高度为壳体内径的25%,则切去的圆缺高度为
h0.25400100mm
可取h100mm。
取折流板间距B0.3D(0.2DBD),则
B0.3400120mm
可取B为120mm。
折流板数目NB
传热管长8500-1=-1=69.870
折流板间距1202.2.7接管
壳程流体进出口接管:取接管内流体流速ui2.5m/s,则接管内径为:
D4qvui40.009550.0698m
2.5圆整后可取管内径为70mm。
管程流体进出口接管,取接管内流体流速u27m/s,则接管内径为:
D
430/36000.389m
72.3换热器核算
2.3.1传热面积校正
管程传热膜系数0.023diRe0.8pr0.4
管程流体流通截面积
nSid20.0272441/80.01258m2
42管程流体流速和雷诺数分别为:
uiqv30/36000.6624m/s Si0.01258Rediu/0.0270.6624992.227162 6653.310普朗特数:
4.174103653.3106Pr4.29
0.635Cpi0.023 diRe0.8Pr0.40.0230.635271620.84.290.43414W/(m2.C) 0.027
2.3.2壳程传热膜系数
00.36id'eRe00.55Pr(/w)0.14
13管子按正三角形排列,传热当量直径为:
4(d'e3223Ptd0)4(0.0422-0.03352)2424==0.025m2
d00.0335壳程流通截面积:
s0=BD(1-d033.5)=120400(1-)=9.71410-3m2
pt42壳程流体流速及其雷诺数分别为: 9.55/1.65u0==60m/s
0.0097140.027595.81.655 Re0==1.2210-6217.810普朗特数: 4.266103217.810-6Pr0==1.362
68.210-2粘度校正:
(/w)0.14=1.05
10.68250=0.36(1.2210)1.36231.05=7171W/m2.C
0.025
2.3.3污垢热阻和管壁热阻
查参考文献表4-6, 管外侧污垢热阻R00,管内侧污垢热阻
1Ri=0.0002(m2.C)/W,根据我们的清洗方式估计管内污垢热阻变化大概是在
10%-20%已知管壁厚度b=0.0335m,碳钢在该条件下的热导率为50W/(m.C)。
总传热系数k:
dm=0.0225m2
K111223W/(m2.C)d0Rdbd0.03350.00020.80.03350.03350.033511i00R00.0270.6350.02257171ididdm059270.027
传热面积校核:
QT2.24106S'==19m2
Ktm逆122395换热器的实际传热面积为S: Sd0lNT0.03358.54439m2
换热器面积裕度为:
s/s'39/192.05
传热面积裕度合适,该换热器能够完成生产任务。
2.3.4换热器内压降得核算
管程阻力:
pi(p1p2)NsNpFt
lui2
Ns1,Np2 ,P1d21由Re27162,传热管相对粗糙度0.01,查参考文献中Re双对数坐标图得0.038,流速ui1.40m/s,992.2kg/m3,所以:
8.5992.21.42p10.03811632.3pa
0.0272992.21.42p2332917pa
22pi(111632.32917)1141.489623pa ui2管程流体阻力在允许范围内。
壳程阻力:
p0(p1'p2')FtNs
其中Ns1,Ft1
流体流经管束的阻力:
p1'Ff0nc(Nb1)u022
0.2288512200F0.5
f05Re00.220.35
nc1.1n1.1447.3
NB70
u0595.m8s/
1.65595.82p1'0.50.357.3(701)265628
2流体流过折流板缺口的阻力:
2hu02 p2'NB(3.5)D2其中h0.1m,D0.4m
1.65595.82p2'70(3.50.5)149987
2总阻力:p265628149987415615
3.总结
经过三个星期的努力,我们的设计终于完成了。也许可能存在很多不足之处,但是看到我们的成果也感到很欣慰。通过这次设计,让我们在各个方面都有很大提高,在设计中经常查找资料提高了我们检索和查阅资料的能力,我们还学会了一些关于设计的基本操作和基本规范,在计算过程中更加仔细和严谨,同时进一步扎实了所学的理论知识,对所学基础知识和专业知识进行了一次综合运用和系统复习,思维方式和设计思想有了进一步提高。因为此次设计由三个人一起完成,所以我们充分运用了团队协作,通过分工合作,培养了我们的团队意识和协作精神,也增进了朋友间的友谊。当然,在这次设计中,我们有很多方面有待加强,比如说没有完全理解设计中的一些问题,还有不会灵活地运用公式。具体有在找饱和水蒸汽热阻时,查了很多资料,没有找到相关数据,所以我们将它假定为零。
4.参考文献及资料
(1)王志魁,刘丽英,刘伟.化工原理第四版M.北京:化学工业出版社,2010 (2)申迎华,郝晓刚.化工原理课程设计M.北京:化学工业出版社,2009 (3)方书起,魏新利.化工设备课程设计指导M.北京:化学工业出版社,2010
附录一
换热器主要结构尺寸和计算结果
参数 流量
进(出)口温度/C 定性温度/C
管程
30m3/h
壳程
3438kg/h 160(105)
5(70)
37.5 992.2 5(70) 37.5 992.2 4.147
653.3106
0.635 4.29 浮头式 1400
132.5 1.650 160(105) 132.5 1.650 4.266
217.8106
0.686 1.3652 / / / / /
/
/
壳程
6.0
7171
0.117 密度/kg/m3 进(出)口温度/C
定性温度/C
密度/kg/m3
定压比热容/KJ/kg.C
黏度/pa.s 热导率/W/m.C
普朗特数 型号
壳体内径/mm 管径/mm 管长/mm 管数目/根
33.52.5
8500 44 38.65 4 管程 1.32 5927 0.04036 传热面积/m2
管程数 主要计算结果 流速m/s 表面传热系数/W(m2.C)
阻力/Mpa
污垢热阻/(m2.C)/W
热流量/kw
0.0002
0
2.24106
95 1001 2.05 1 1 32 正三角形 70 120 碳钢 传热温差/C 传热系数/W/m2.C
裕度/% 壳程数 台数
管心距/mm
管子排列 折流板数/个
折流板间距/mm
材质
附录2 设备选型表
序号 名称 1 折流板 2 3 4 5 6 7 8 9 10 11 12 13 14 15 16 17 18 19
规格
长280mm 33.53.25mm型号
PSJJ7A132-0-4 定距管 壳体 封头 接管 接管 螺母 法兰 支座 垫片 传热管 拉杆1 拉杆2 顶丝 螺柱 管板 管板
厚2.5mm DN1100mm 702.5mm 401.5mm M20 RF 550-2.5
数量 生产厂家 8 石家庄蓝宝机械制造有限
公司
GB/14976-1994 265 上海斯普热能技术有限公
司
Q235-A 1 淄博泰勒换热设备有限公
司
Q235-A 2 阿里巴巴-佛山市顺德区佛
茂钢材贸易有限公司
BR01-A 2 上海化工装备有限公司 BR006 GB6170-92 HG20615
2 156 2 1 2
上海化工装备有限公司 沙河市四方紧固件制造有
限公司
武汉威孚热工技术有限公司
河北同力自控阀门制造有限公司
西安捷安达换热设备厂 山东省聊城市首发金属制品有限公司
河北沧州上浦电器设备有限公司
河北沧州上浦电器设备有限公司
山东宏达科技集团有限公司
沙河市四方紧固件制造有限公司
澳昭美金属材料有限公司 澳昭美金属材料有限公司 广州市柯凌自控阀门有限公司
安徽德仪仪器仪表有限公司公司 耳式支座B2 JB1165-732 25mm 252.5mm 25mm 25mm
JB-T4704-2000
GB/T8162-1999 265 PSJJ7A1.32-0-5 4 PSJJ7A1.32-0-7 3 GB85-88 JB-T4707-2000
12 72 M20
PSJJ7A1.32-0-2 1 PSJJ7A1.32-0-6 1
PN-YFQ-025S
2 1 折流挡双弓型 板
压力泵
推荐第10篇:换热器综述
换热器的综述
前言
随着换热器在工业生产中的地位和作用不同,换热器的类型也多种多样,不同类型的换热器各有优缺点,性能各异。在换热器设计中,首先应根据工艺要求选择适用的类型,然后计算换热所需传热面积,并确定换热器的结构尺寸。 换热器按用途不同可分为加热器、冷却器、冷凝器、蒸发器、再沸器、深冷器、过热器等。
换热器组内的传热过程目的一般可以分为两类: 一类是为了热功转换, 另一类是为了加热或者冷却物体.相应地, 传热过程也包含熵产最小以及火积耗散极大这两种不同的优化原理.通过分析换热器组内的传热过程, 并在一定约束条件下利用不同的原理对换热器组的面积分配进行优化, 得出熵产最小原理适用于包含在热力循环中的换热器优化问题, 而火积耗散极大原理则更适合分析仅涉及传热过程的换热器优化问题.并且, 在使用熵产最小原理优化热力循环中的换热器时, 除了需要考虑冷、热端换热器产生的熵产外, 也应考虑乏汽排放到外部环境引起的熵产.在换热器的设计中,很多因素都将影响到换热器的设计是否优化合理、安全可靠,是否能正常运转、高效耐用。 本文通过对管壳式换热器设计的综述,增强对换热器设计环节的重视与考虑,使设计更加准确、完善。
一、
换热器 1.1换热器的介绍
换热器是将热流体的部分热量传递给冷流体的设备,又称热交换器。换热器是实现化工生产过程中热量交换和传递不可缺少的设备。换热器被应用于超过 80%的能源利用系统, 它是热能和化工等工程领域中最重要的设备之一.因此, 提高换热器的换热性能通常被认为是提高能源利用效率的关键因素之一.经过长期的不懈努力,科研人员已经提出了多种不同的主动/被动式强化换热技术来提高换热性能。在石油、化工、轻工、制药、能源等工业生产中,常常需要把低温流体加热或者把高温流体冷却,把液体汽化成蒸汽或者把蒸汽冷凝成液体。这些过程均和热量传递有着密切联系,因而均可以通过换热器来完成。随着经济的发展,各种不同型式和种类的换热器发展很快,新结构、新材料的换热器不断涌现。为了适应发展的需要,我国对某些种类的换热器已经建立了标准,形成了系列。换热器的应用广泛,日常生活中取暖用的暖气散热片、汽轮机装置中的凝汽器和航天火箭上的油冷却器等,都是换热器。它还广泛应用于化工、石油、动力和原子能等工业部门。它的主要功能是保证工艺过程对介质所要求的特定温度,同时也是提高能源利用率的主要设备之一。换热器既可是一种单元设备,如加热器、冷却器和凝汽器等;也可是某一工艺设备的组成部分,如氨合成塔内的换热器。换热器是化工生产中重要的单元设备,根据统计,热交换器的吨位约占整个工艺设备的20%有的甚至高达30%,其重要性可想而知。
换热器的发展已经有近百年的历史,被广泛应用在石油、化、冶金、电力、船舶、集中供热、制冷空调、机械、食品、制药等领域。 进入80 年代以来,由于制造技术、材料科学技术的不断进步和传热理论研究的不断完善,有关换热器的节能设计和应用越来越引起关注。 按照用途来分:预热器(或加热器)、冷却器、冷凝器、蒸发器等。按照制造热交换器的材料来分:金属的、陶瓷的、塑料的、石墨的、玻璃的等。按照温度状况来分:温度工况稳定的热交换器,热流大小以及在指定热交换区域内的温度不随时间而变;温度工况不稳定的热交换器,传热面上的热流和温度都随时间改变。按照热流体与冷流体的流动方向来分:顺流式、逆流式、错流式、混流式。按照传送热量的方法来分:间壁式、混合式、蓄热式等三大类。其中间壁式换热器的冷、热流体被固体间壁隔开,并通过间壁进行热量交换的换热器,因此又称表面式换热器,这类换热器应用最广。
目前在发达的工业国家热回收率已达96 % ,换热设备在石油炼厂中约占全部工艺设备投资的35 %~40 %。其中管壳式换热器仍然占绝对的优势, 约70 %。其余30 %为各类高效紧凑式换热器、新型热管和蓄热器等设备, 其中板式、板翅式、热管及各类高效传热元件的发展十分迅速。随着工业装置的大型化和高效率化, 换热器也趋于大型化, 并向低温差设计和低压力损失设计的方向发展。当今换热器的发展以CFD、模型化技术、强化传热技术及新型换热器开发等形成了一个高技术体系。
管壳式换热器是以封闭在壳体中管束的壁面作为传热面的间壁式换热器,结构一般由壳体、传热管束、管板、折流板(挡板)和管箱等部件组成。目前,国内外工业生产中所用的换热设备中,管壳式换热器仍占主导地位,虽然它在换热效率、结构紧凑性和金属材料消耗等方面不如其它新型换热设备,但它具有结构坚固,操作弹性大,适应性强,可靠程度高,选材范围广,处理能力大,能承受高温高压等特点,所以在工程中仍得到广泛应用。以下是几种常见的管壳式强化换热器。
螺旋槽管换热器,横纹管换热器,螺旋扁管换热器,螺旋扭曲管换热器,波纹管换热器,内翅片管换热器,缩放管换热器,波节管管壳式换热器,三维内肋管换热器,管内插入物换热器
1.2换热器发展前景:
换热器的所有种类中,管壳式换热器是一个量大而品种繁多的产品,由于国防工业技术的不断发展,换热器操作条件日趋苛刻迫切需要新的耐磨损、耐腐蚀、高强度材料。近年来,我国在发展不锈钢铜合金复合材料铝镁合金及碳化硅等非金属材料等方面都有不同程度的进展,其中尤以钛材发展较快。钛对海水氯碱醋酸等有较好的抗腐蚀能力,如再强化传热,效果将更好,目前一些制造单位已较好的掌握了钛材的加工制造技术。对材料的喷涂,我国已从国外引进生产线。铝镁合金具有较高的抗腐蚀性和导热性,价格比钛材便宜,应予注意。近年来国内在节能增效等方面改进换热器性能,提高传热效率,减少传热面积降低压降,提高装置热强度等方面的研究取得了显著成绩。换热器的大量使用有效的提高了能源的利用率,使企业成本降低,效益提高。
1.3换热器的工作原理
换热器是将热流体的部分热量传递给冷流体的设备,即在一个大的密闭容器内装上水或其他介质,而在容器内有管道穿过。让热水从管道内流过。由于管道内热水和容器内冷热水的温度差,会形成热交换,也就是初中物理的热平衡,高温物体的热量总是向低温物体传递,这样就把管道里水的热量交换给了容器内的冷水,换热器又称热交换器
1.4换热器的维护
二、管壳式换热器简述 2.1管壳式换热器结构
管壳式换热器主要有壳体、管束、管板和封头等部分组成,壳体多呈圆形,内部装有平行管束,管束两端固定于管板上。进行换热的冷热两种流体,一种在管内流动,称为管程流体;另一种在管外流动,称为壳程流体。为提高管外流体的传热分系数,通常在壳体内安装若干挡板。挡板可提高壳程流体速度,迫使流体按规定路程多次横向通过管束,增强流体湍流程度。换热管在管板上可按等边三角形或正方形排列。等边三角形排列较紧凑,管外流体湍动程度高,传热分系数大;正方形排列则管外清洗方便,适用于易结垢的流体。
流体每通过管束一次称为一个管程;每通过壳体一次称为一个壳程。图示为最简单的单壳程单管程换热器,简称为1-1型换热器。为提高管内流体速度,可在两端管箱内设置隔板,将全部管子均分成若干组。这样流体每次只通过部分管子,因而在管束中往返多次,这称为多管程。同样,为提高管外流速,也可在壳体内安装纵向挡板,迫使流体多次通过壳体空间,称为多壳程。多管程与多壳程可配合应用。
2.2管壳式换热器类型
由于管内外流体的温度不同,因之换热器的壳体与管束的温度也不同。如果两温度相差很大,换热器内将产生很大热应力,导致管子弯曲、断裂,或从管板上拉脱。因此,当管束与壳体温度差超过50℃时,需采取适当补偿措施,以消除或减少热应力。根据所采用的补偿措施,管壳式换热器可分为以下几种主要类型:
2.2.1固定管板式换热器 1)、结构特点:两块管板均与壳体相焊接,并加入了热补偿原件——膨胀节。 2 )、优点:结构简单、紧凑、能承受较高的压力,造价低,管程清洗方便,管子损坏时易于堵管或更换。 3)、缺点:不易清洗壳程,壳体和管束中可能产生较大的热应力。 4)、适用场合:适用于壳程介质清洁,不易结垢,管程需清洗以及温差不大或温差虽大但是壳程压力不大的场合。
5)膨胀节的作用:由于两块管板都与壳体固定,当壳体、换热管受热、受压都会发生变形,加入膨胀节减少热应力来吸收热膨胀差。
2.2.2 浮头式换热器 1)、结构特点:一块管板固定,另一块是浮动的与浮头盖用浮头钩圈法兰相连。 2)、优点:管内和管间清洗方便,不会产生热应力。 3)、缺点:结构复杂,设备笨重,造价高,浮头端小盖在操作中无法检查。 4)、适用场合:壳体和管束之间壁温相差较大,或介质易结垢的场合。
2.2.3 U形管式换热器 1)、结构特点:只有一块管板,换热管呈U形。 2)、优点:结构简单,价格便宜,承受能力强,不会产生热应力。 3)、缺点:布板少,管板利用率低,管子坏时不易更换。 4)、适用场合:特别适用于管内走清洁而不易结垢的高温、高压、腐蚀性大的 物料。
2.3影响换热器管板腐蚀的主要因素有:
(1)介质成分和浓度:浓度的影响不一,例如在盐酸中,一般浓度越大腐蚀越严重。碳钢和不锈钢在浓度为50%左右的硫酸中腐蚀最严重,而当浓度增加到60%以上时,腐蚀反而急剧下降;
(2)杂质:有害杂质包括氯离子、硫离子、氰离子、氨离子等,这些杂质在某些情况下会引起严重腐蚀
(3)温度:腐蚀是一种化学反应,温度每提升 10℃,腐蚀速度约增加1~3倍,但也有例外; (4)ph值:一般ph值越小,金属的腐蚀越大; (5)流速:多数情况下流速越大,腐蚀也越大。 总结
随着我国工业的不断发展,对能源利用、开发和节约的要求不断提高,因而对换热器的要求也日益加强。换热器的设计、制造、结构改进及传热机理的研究十分活跃,一些新型高效换热器相继问世。随着换热器在工业生产中的地位和作用不同,换热器的类型也多种多样,不同类型的换热器各有优缺点,性能各异。在换热器设计中,首先应根据工艺要求选择适用的类型,然后计算换热所需传热面积,并确定换热器的结构尺寸。
若要保持总传热系数,温度越大、换热管数越多,折流板数越多、壳径越大,这主要是因为煤油的出口温度增高,总的传热温差下降,所以换热面积要增大,才能保证Q和K.因此,换热器尺寸增大,金属材料消耗量相应增大.通过这个设计,我们可以知道,为提高传热效率,降低经济投入,设计参数的选择十分重要
在管壳式换热器设计过程中,设计者应当充分了解且熟悉各相关技术规范及计算公式,在对客户要求充分理解的基础上,参考其它成功的设计案例中的设计方式及相关资料,使设计出的产品达到安全、经济、可靠,做到设备长周期安全运行
三、参考文献
《换热器》秦叔经、叶文邦等 ,化学工业出版社(2003) 《化工过程及设备设计》华南工学院化工原理教研室
《化工原理》天津大学化工原理教研室编 天津:天津大学出版社.(1999) 《过程设备设计》(第二版)化学工业出版社
GB151-1999,管壳式换热器
黄伟昌,王玉.管壳式换热器设计要点综述[J].管道技术与设备,2009,(06).董宝春.管壳式换热器的工艺设计[J].甘肃石油和化工,2009,(03).陈群.换热器组传热性能的优化原理比较
第11篇:南昌大学食品列管式换热器设计书
食品工程原理课程设计
设计题目:列管式换热器的设计
班级:
设计者:
学号:
设计时间:2013 年 5 月 12 日~19 日
指导老师: 食品工程原理课程设计
目录
1.1 概述 .............................................................................................................................................3
1.2 换热器的结构与类型 ..................................................................................................................3
1.2.1 列管式换热器的基本构型与流体行程 .....................................................................................4
1.2.2 列管式换热器的类型 .................................................................................................................5
1.3 列管式换热器的主要部件 ...........................................................................................................7
1.3.1 换热管.........................................................................................................................................7
1.3.2 管板.............................................................................................................................................9
1.3.3 封头、管箱、分程隔板 .............................................................................................................9
1.3.4 折流挡板的选用 .......................................................................................................................10
1.3.5 其他主要部件 ...........................................................................................................................10
1.4 固定管板式换热器的优点 .........................................................................................................11
1.5 确定设计方案 ............................................................................................................................12
1.5.1 选择换热器的类型 ...................................................................................................................12
1.5.2 流体流动途径的选择 ...............................................................................................................12
1.6 传热过程工艺计算 ....................................................................................................................13
1.6.1 冷热流体的物理性质 ...............................................................................................................13
...............................................................................................................14 1.6.2 传热面积的初步计算
1.7 核算 ...........................................................................................................................................16
.......................................................................................................................16 1.7.1 传热系数的计算 1.7.2 核算传热面积 A0 ......................................................................................................................19 1.7.3 核算压力降 ...............................................................................................................................20 1.6.3 结构设计及计算 ........................................................14
1.8 主要附属件的选定 ....................................................................................................................23
1.8.1 接管直径 ...................................................................................................................................23
1.8.2 封头的选用 ...............................................................................................................................24
1.8.3 管板的选择 ...............................................................................................................................24
1.8.4 管板与管子连接 .......................................................................................................................25
1.8.5 管箱的选择 ...............................................................................................................................25
1.8.6 定距管.......................................................................................................................................26
1.8.7 拉杆的选择及数量 ...................................................................................................................26
1.8.8 各零件的选用 ...........................................................................................................................27
1.9 主题装置图的绘制(见 A1 图纸) ...........................................................................................27
2.0 附表 ...........................................................................................................................................27
2.1 收获及感想 .........................................................................................................错误!未定义书签。
2.2 主要参考文献 ............................................................................................................................30
1 / 32
食品工程原理课程设计
《食品工程原理及单元操作》课程设计任务
班级:
姓名:
设计一台用饱和水蒸气(表压 400~500kPa)加热水的列管式固 定管板换热器,水流量为 80(t/h),水温由20℃ 加热到 60℃。
1、设计项目:
①热负荷
②传热面积 ④外壳直径及长度 ⑤接管直径
2.设备图主视图、左视图(部分剖)。 0 号、1 号或 A4 纸(4 号)画图 3.设备管口表零部件明细表,标题栏表。
管子排列 外壳及管板厚度 ③⑥2 / 32
食品工程原理课程设计
1.1 概述
在不同温度的流体间传递热能的装置称为热交换器,简称为换热器。在换热器中至少要有两种温度不同的流体,一种流体温度较高,放出热量;另一种流体则温度较低,吸收热量。35%~40%。随着我国工业的不断发展,对能源利用、开发和节约的要求不断提高,因而对换热器的要求也日益加强。换热器的设计、制造、结构改进及传热机理的研究十分活跃,一些新型高效换热器相继问世。
随着换热器在工业生产中的地位和作用不同,换热器的类型也多种多样,不同类型的换热器各有优缺点,性能各异。在换热器设计中,首先应根据工艺要求选择适用的类型,然后计算换热所需传热面积,并确定换热器的结构尺寸。按用途不同可分为:加热器、冷却器、冷凝器、蒸发器、再沸器、深冷器、过热器等。按传热方式的不同可分为:混合式、蓄热式和间壁式,列管式换热器是间壁式换热器的主要类型,也是应用最普遍的一种换热设备。按其结构类型分,有列管式、板面式、版壳式、螺旋板式、板翅式、管翅式等。
列管式换热器发展 较早,设计资料和技术数据较完整,目前在许多国家都已有系列化标准产品。虽然在换热效率、紧凑性材料消耗等方面还不及一些新型换热器,但它具有结构简单、牢固、耐用,适应性强,操作弹性大,成本较低等优点,因此仍是化工、石化、石油炼制等工业中应用最广泛的换热设备。
1.2 换热器的结构与类型
3 / 32
食品工程原理课程设计
1.2.1 列管式换热器的基本构型与流体行程
列管式换热器主要由壳体、换热管束、管板、封头等部件组成,
图 2-1 为它的基本构型,此式为卧式换热器,此外还有立式的。在圆
筒形的壳体内装有换热管束,管束安装固定在壳体内两端的管板上。
封头用螺丝钉与壳体两端的法兰连接,如需检修或清洗,课将封头盖
拆除。
图 2-1 列管式换热器的基本构型
冷热流体在列管式换热器内进行热交换时,一种流体在管束与壳
体间的环隙内流动,其行程称为壳程;另一种流体在换热管内流动,
其行程成为管程。如需换热器较大传热面积时,则应排列较多的换热
管束。为提高管程流体流速,强化传热,可将换热管分为若干组,称
为多管程。同样,为提高壳程流体的涡流程度,以提高对流传热系数,
强化传热,可在壳体内安装横向式或纵向式的折流挡板。这样,壳程
流体的流速和流向可不断发生改变,使雷诺数在较低时
就 能达到湍流。
4 / 32
第12篇:运用aspen及其套件设计换热器
运用aspen及其套件EDR设计换热器
青海大学化工学院 张鹏宇
目录 1.生产要求设定
2.启动aspen设置前奏
2.1确定合适的modle library 模块
2.2建立流程图
2.3输入工程标题
2.4输入组分
2.5选择物性方法
2.6输入物流参数
3.进行换热器选型
3.1采用shortcut简捷计算
3.2填写估计的总传热系数
3.3模拟计算,列出简捷计算结果
3.4按国家标准选型 4.选择Detailed详细核算
4.1设置冷热流体走程
4.2使用Design Specification调整冷却水流率
4.3设置壳程管程压降计算方式
4.4设置总传热系数计算方式
4.5填写冷热流体侧污垢系数
4.6填写壳程管程数据
4.7填写折流板及管嘴数据
4.8运行计算,列出换热器详细计算结果
4.8.1 exchanger details换热器详细数据
4.8.2 pres drop 各程压力降及压力降分析
4.8.3 流速探讨及分析 5.用EDR 软件核算,出图
5.1 数据传递
5.2 EDR数据检查,核对补充
5.3运行计算,列出换热器详细计算结果
5.3.1 EDR换热器详细数据
5.3.2 pres drop 各程压力降及压力降分析
5.3.3 流速探讨及分析
5.4列出换热器装配图
5.5列出换热器布管图和设备数据
5.6打印出图
6.对比Aspen换热器详细计算,说明EDR其优缺点。
1.生产要求设定
某生产过程中,需处理每年114000吨/年苯,现将苯从80度冷却至40度,冷却介质采用循环水。循环水入口温度32.5度,出口温度取37.5度。要求换热器裕度为10%~25%,换热器内流体流动阻力小于50Kpa.
2.启动ASPEN设置前奏
2.1选择合适的modle library 模块
启动ASPEN,新打开一个空白的blank文件,该换热器用循环水冷却,冬季操作时进口温度会降低,考虑到这一因素,估计该换热器的管壁温和壳体壁温之差较大,因此初步确定选用带膨胀节的固定管板式换热器。在heat Exchangers 下选择heatX下的GEN-HS模块。
2.2建立流程图
连接物流线,建立如图所示的流程图,至此flowsheet已经完整。
2.3输入工程标题
单击下一步N
,填写标题,这个可以随意。
2.4输入组分
继续单击下一步,在component ID 中填写H20按回车,再填C6H6回车,物质直接出现,不用查找。
2.5选择物性方法
继续单击下一步,选择物性方法。根据一些其他文献的选择方法,我们在property method一栏下拉选择CHAO-SEA.物性方法。
2.6输入物流参数
由于循环冷却水较易结垢,为便于水垢清洗,应使水走管程,苯走壳程。所以1与2走的水,3与4走的苯。那么在接下来的stream 1中填写温度32.5度,设置压力为1.2个大气压。在composition下拉选择MASS-FLOW,单位选择KG/h。 暂时设置循环水的初始流量为5000KG/h.过后将运用Design Specification 调整水的流量。将stream 2填写37.5度,压力1.2atm.其他不设置。 将stream 3填写温度80度,压力也为1.2atm,填写苯的流量16000kg/h(根据处理114000吨苯每年而约得)。 stream 4不作设置。
3.进行换热器选型
3.1采用shortcut简捷计算
下一步,在blocks- B1-specification-calculation下面选择shortcut表示采用简捷计算以便进行换热器的选型。在preure drop下面设置冷热流体的outlet preure压力降为0.
3.2填写估计的总传热系数
在UMethods 下面填写估计的换热器总传热系数为300 W/(M2*K).至此简捷计算数据已经输入完成。
3.3模拟计算,列出简捷计算结果
单击下一步,按确定,在数据浏览器里的blocks-b1下的exchanger details 可以看到该换热器的热负荷为319KW.需要的换热面积为52.8M2 .与纸质版换热器设计中的325KW,51.3M2.相差不大。可以继续采用详细核算。
3.4按国家标准选型
按照换热器面积及规定6M的管长,查《化工工艺手册》从JB/T4715-1992中选标准系列换热器BEM450-1.6-62.5-6/25--1,单管程,单壳程,壳径450mm,换热面积62.5m2,换热管Φ25mm×2.5mm,管长6M,管数135根。三角形排列,管心距32 mm。
4.选择Detailed详细核算 4.1设置冷热流体走程
现在选择Detailed 表示type 选择rating 表示详细核算。Hot fluid 选择shell。在exchanger specification 下面选择Hot stream outlet temperature.Value 填写40度。表示要规定苯的出口温度为40度。
4.2使用Design Specification调整冷却水流率
在此栏新建一个DS-1.在DS-1下的define新建一个S。点击edit,开始编辑。在type下选择stream-var ,选择2,表示要设计调整水出口(2)的输出流量。然后选择variable为temp表示温度是可以操作的变量。
在spec下面按如图填写,target 填写37.5度表示要使水的出口温度为37.5度。
在vary栏下填type为 stream-var, stream选择1,variable填 ma-flow.这些表示要调整1的水流量数据使2出口温度达到我所想要的37.5度。然后在lower上填写40000,uper上填写60000.表示水的调整区间。
运行后可以得到水的流量为55164Kg/h。
4.3设置壳程管程压降计算方式
壳程和管程都选择calculated from geometry,表示根据换热器几何结构计算壳程和管程的压降。LMTD不用选择,是它默认值constant就好了。
4.4设置总传热系数计算方式
在U METHOD选择film coefficients,表示根据传热面两侧的膜系数计算总传热系数。
4.5填写冷热流体侧污垢系数
在film coefficients 页面壳程和管程都选择 calculated from geometry,表示根据换热器传热面两侧的几何结构计算膜系数。查《化工工艺设计手册》热流体侧的污垢系数取0.000176M2*K/W,冷流体侧的污垢系数取0.00026M2*K/W.
4.6填写壳程管程数据
在blocks-B1-geometry 栏下的shell下的TEMA shell type选择E-One pa shell 表示单壳程。填写包括管程数1,换热器水平安置,壳径450mm.
在tubes一栏下选择管子类型光滑管,填写管程数据,包括管子根数135根,管长6000mm,管心距32mm,管外径0.025meter. 管内径0.00225meter。
4.7填写折流板管嘴数据
包括19块折流板,切率25%。
管嘴设置如下。
4.8运行计算,列出换热器详细计算结果
4.8.1 exchanger details换热器详细数据
如上图,热负荷319KW,需要换热面积为56.9平米,实际换热面积为63.6平米,富余6.7平米。面积裕度11%,完美满足要求。
4.8.2 pres drop 各程压力降及压力降分析
如图,壳程管程压力降都小于1KPA。远远小于50KPA,满足 要求。即壳程和管程的流动阻力都非常满足要求。
4.8.3 流速探讨及分析
由上图可以看出,管程壳程流速非常平缓,这既能满足水和苯的流量要求,还能避免因流速过快而对换热器产生更多损耗。壳程最大流速0.08m/s,管程最大流速0.28m/s,均偏小, 因为软件计算结果未报警,所选换热器可用。
5.用EDR 软件核算,出图 5.1 数据传递
在blocks--B1--specification中选择shell and tube 表示用EDR软件详细核算。用EDR软件新建一个”shell and tube”空白的冷凝器设计文件后关闭。 在B1下的EDR option中把EDR空白文件导入。然后单击“transfer geometry to shell and tube”按钮,把ASPEN plus对冷凝器详细核算结果传入EDR软件。
5.2 EDR数据检查,核对补充
在下面的几个图中,按照图中的数据,填写完整。
热流组成页面
热流物性方法选择
冷流组成页面
冷流物性方法选择
5.3运行计算,列出换热器详细计算结果
5.3.1 EDR换热器详细数据
在rezult -overall summary 可看到全方位的换热器详细数据
5.3.2 pres drop 各程压力降及压力降分析
由以上详细核算图可知,各程压力降总和50KPA,符合设计要求,比课本求压力降方法要迅速,便捷得多。
5.3.3 流速探讨及分析
壳程速率为0.19m/s,管程速率为0.34m/s。均比较小。这是由于换热器形态以及送料大小和进出口规定温度的缘故。
5.5列出换热器装配图
5.6列出换热器布管图和设备数据
5.7打印出图 6.对比Aspen换热器详细计算,说明EDR其优缺点。 在进行换热器详细核算的时候,EDR确实比Aspen的计算要精确,而且EDR能计算Aspen 不能计算的数据。EDR软件是换热器的专业精细设计核算软件,能够完整地从设计直到出图。用Aspen进行换热器的设计只够参看一些换热器基本数据,无法进行出图。但EDR由于其功能更全,包络面更广,其也产生一些问题,用Aspen 传递数据时需要补充数据,有些不需要处理的部分也加进来了,所以会显得不够简洁明了。
第13篇:换热器浮头换热器
浮头式换热器
一、浮头式换热器的概述
浮头式换热器的一端管板是固定的。与壳体刚性连接,另一端管板是活动的,与壳体之间并不相连。活动管板一侧总称为浮头,浮头式换热器的管束可从壳体中抽出,故管外壁清洗方便,管束可在壳体中自由伸缩,所以无温差应力;但结构复杂、造价高,且浮头处若密封不严会造成两种流体混合。浮头式换热器适用于冷热流体温差较大(一般冷流进口与热流进口温差可达110℃),介质易结垢需要清洗的场合。
二、浮头式换热器的总体结构
三、浮头式换热器的特点
1、浮头式换热器的优点
(1)管束可以抽出,以方便清洗管、壳程。 (2)介质间温差不受限制。
(3)可在高温、高压下工作,一般温度小于等于450°,压力小于等于6.4Mpa。 (4)可用于结垢比较严重的场合。 (5)可用于管程易腐蚀场合。
2、浮头式换热器的缺点 (1)小浮头易发生内漏。
(2)金属材料耗量大,成本高20%。 (3)结构复杂。
三、浮头式换热器的应用
浮头式换热器适用于壳体和管束之间壁温差较大或壳程介质易结垢的场合。
四、浮头式换热器的导流结构
为使壳程进口段管束充分传热,浮头式换热器可采用内导流或外导流结构。
1、内导流浮头式换热器
内导流筒换热器是在换热器的壳程筒体内设置了内导流筒使换热器的前或后端未加导流筒前难以利用换热的换热管得以充分利用,从而增大换热器的有效换热面积。
2、外导流浮头式换热器
外导流式换热器是在原换热器的壳程筒体上增加一个放大筒节用以扩散壳程流体,并使流体从换热器壳程的两端进入壳程,从而避免了在换热器布管时考虑布管弓形的高,而使增加了同规格上换热器的布管数目并有效利用了换热器前后端的换热管从而增大了有效换热面积。
第14篇:换热器工作原理
管壳式换热器的三种分类
管壳式换热器按照应力补偿的方式不同,可以分为以下三个种类:
1、固定管板式换热器
固定管板式换热器是结构最为简单的管壳式换热器,它的传热管束两端管板是直接与壳体连成一体的,壳体上安装有应力补偿圈,能够在固定管板式换热器内部温差较大时减小热应力。固定管板式换热器的热应力补偿较小,不能适应温差较大的工作。
2、浮头式换热器
浮头式换热器是管壳式换热器中使用最广泛的一种,它的应力消除原理是将传热管束一段的管板放开,任由其在一定的空间内自由浮动而消除热应力。浮头式换热器的传热管束可以从壳体中抽出,清洗和维修都较为方便,但是由于结构复杂,因此浮头式换热器的价格较高。
3、U型管换热器
U型管换热器的换热器传热管束是呈U形弯曲换热器,管束的两端固定在同一块管板的上下部位,再由管箱内的隔板将其分为进口和出口两个部分,而完全消除了热应力对管束的影响。U型管换热器的结构简单、应用方便,但很难拆卸和清洗。
管壳式换热器,管壳式换热器结构原理
管壳式换热器由一个壳体和包含许多管子的管束所构成,冷、热流体之间通过管壁进行换热的换热器。管壳式换热器作为一种传统的标准换热设备,在化工、炼油、石油化工、动力、核能和其他工业装置中得到普遍采用,特别是在高温高压和大型换热器中的应用占据绝对优势。通常的工作压力可达4兆帕,工作温度在200℃以下,在个别情况下还可达到更高的压力和温度。一般壳体直径在1800毫米以下,管子长度在9米以下,在个别情况下也有更大或更长的。
工作原理和结构 图1 [固定管板式换热器]为固定管板式换热器的构造。A流体从接管1流入壳体内,通过管间从接管2流出。B流体从接管3流入,通过管内从接管4流出。如果A流体的温度高于B流体,热量便通过管壁由A流体传递给B流体;反之,则通过管壁由B流体传递给A流体。壳体以内、管子和管箱以外的区域称为壳程,通过壳程的流体称为壳程流体 (A流体)。管子和管箱以内的区域称为管程,通过管程的流体称为管程流体(B流体)。管壳式换热器主要由管箱、管板、管子、壳体和折流板等构成。通常壳体为圆筒形;管子为直管或U形管。为提高换热器的传热效能,也可采用螺纹管、翅片管等。管子的布置有等边三角形、正方形、正方形斜转45°和同心圆形等多种形式,前3 种最为常见。按三角形布置时,在相同直径的壳体内可排列较多的管子,以增加传热面积,但管间难以用机械方法清洗,流体阻力也较大。管板和管子的总体称为管束。管子端部与管板的连接有焊接和胀接两种。在管束中横向设置一些折流板,引导壳程流体多次改变流动方向,有效地冲刷管子,以提高传热效能,同时对管子起支承作用。折流板的形状有弓形、圆形和矩形等。为减小壳程和管程流体的流通截面、加快流速,以提高传热效能,可在管箱和壳体内纵向设置分程隔板,将壳程分为2程和将管程分为2程、4程、6程和8程等。管壳式换热器的传热系数,在水-水换热时为1400~2850瓦每平方米每摄氏度〔W/(m(℃)〕;用水冷却气体时,为10~280W/(m(℃);用水冷凝水蒸汽时,为570~4000W/(m(℃)。
特点 管壳式换热器是换热器的基本类型之一,19世纪80年代开始就已应用在工业上。这种换热器结构坚固,处理能力大、选材范围广,适应性强,易于制造,生产成本较低,清洗较方便,在高温高压下也能适用。但在传热效能、紧凑性和金属消耗量方面不及板式换热器、板翅式换热器和板壳式换热器等高效能换热器先进。
分类 管壳式换热器按结构特点分为固定管板式换热器、浮头式换热器、U型管式换热器、双重管式换热器、填函式换热器和双管板换热器等。前 3种应用比较普遍。
固定管板式换热器 它是管壳式换热器的基本结构形式(图1 [固定管板式换热器])。管子的两端分别固定在与壳体焊接的两块管板上。在操作状态下由于管子与壳体的壁温不同,二者的热变形量也不同,从而在管子、壳体和管板中产生温差应力。这一点在分析管板强度和管子与管板连接的可靠性时必须予以考虑。为减小温差应力,可在壳体上设置膨胀节。固定管板式换热器一般只在适当的温差应力范围、壳程压力不高的场合下采用。固定管板式换热器的结构简单、制造成本低,但参与换热的两流体的温差受一定限制;管间用机械方法清洗有困难,须采用化学方法清洗,因此要求壳程流体不易结垢。
浮头式换热器 图2 [浮头式换热器]为浮头式换热器的结构。管子一端固定在一块固定管板上,管板夹持在壳体法兰与管箱法兰之间,用螺栓连接;管子另一端固定在浮头管板上,浮头管板与浮头盖用螺栓连接,形成可在壳体内自由移动的浮头。由于壳体和管束间没有相互约束,即使两流体温差再大,也不会在管子、壳体和管板中产生温差应力。对于图2a[浮头式换热器]中的结构,拆下管箱可将整个管束直接从壳体内抽出。为减小壳体与管束之间的间隙,以便在相同直径的壳体内排列较多的管子,常采用图2b[浮头式换热器]的结构,即把浮头管板夹持在用螺栓连接的浮头盖与钩圈之间。但这种结构装拆较麻烦。浮头式换热器适用于温度波动和温差大的场合;管束可从壳体内抽出用机械方法清洗管间或更换管束。但与固定管板式换热器相比,它的结构复杂、造价高。 U型管式换热器 一束管子被弯制成不同曲率半径的U型管,其两端固定在同一块管板上,组成管束(图3[U型管式换热器])。管板夹持在管箱法兰与壳体法兰之间,用螺栓连接。拆下管箱即可直接将管束抽出,便于清洗管间。管束的U形端不加固定,可自由伸缩,故它适用于两流体温差较大的场合;又因其构造较浮头式换热器简单,只有一块管板,单位传热面积的金属消耗量少,造价较低,也适用于高压流体的换热。但管子有U形部分,管内清洗较直管困难,因此要求管程流体清洁,不易结垢。管束中心的管子被外层管子遮盖,损坏时难以更换。相同直径的壳体内,U形管的排列数目较直管少,相应的传热面积也较小。
双重管式换热器 将一组管子插入另一组相应的管子中而构成的换热器(图4 [双重管式换热器])。管程流体(B流体)从管箱进口管流入,通过内插管到达外套管的底部,然后返向,通过内插管和外套管之间的环形空间,最后从管箱出口管流出。其特点是内插管与外套管之间没有约束,可自由伸缩。因此,它适用于温差很大的两流体换热。但管程流体的阻力较大,设备造价较高。
填函式换热器 图5 [填函式换热器]为填函式换热器的结构。管束一端与壳体之间用填料密封。管束的另一端管板与浮头式换热器同样夹持在管箱法兰与壳体法兰之间,用螺栓连接。拆下管箱、填料压盖等有关零件后,可将管束抽出壳体外,便于清洗管间。管束可自由伸缩,具有与浮头式换热器相同的优点。由于减少了壳体大盖,它的结构较浮头式换热器简单,造价也较低;但填料处容易渗漏,工作压力和温度受一定限制,直径也不宜过大。
双管板换热器 管子两端分别连接在两块管板上(图6[双管板换热器的结构特点]),两块管板之间留有一定的空间,并装设开孔接管。当管子与一侧管板的连接处发生泄漏时,漏入的流体在此空间内收集起来,通过接管引出,因此可保证壳程流体和管程流体不致相互串漏和污染。双管板换热器主要用于严格要求参与换热的两流体不互相串漏的场合,但造价比固定管板式换热器高。
第15篇:燃料油换热器计算
燃料油换热器计算
燃料油换热器计算
一、物性参数 M100燃料油物性参数 根据《油品储运设计手册》
油品容重修正系数
44204 8.971013.210(op0.7)5.0110油品密度
203 op1.00t/m15203 opop51.0025t/m
3 60op20op(tqu20)0.98t/m油品导热系数:
600.101(10.0005460)/1.0025 0.09748op油品粘度
82.7410 op11810e 油品的质量热容:
600.5COP4.1868(0.4030.0008160)/(1.0025)1.888
4 6060.0355(6050)6
T-55导热油性质:
140℃下密度为845kg/m3 140℃下比热为2.05kJ/kg·K 149℃下粘度为1.311mPa·s 149℃下导热系数:λ= 0.1134 W/m·K
第1页共 18 页
燃料油换热器计算
二、计算
天津大学版《化工原理》
(一)1500m3/h
1、试算和初选冷却器的规格 (1)计算热负荷
燃料油入口温度50℃,经换热器加热至70℃装船。 装船泵额定流量:1500m3/h 热负荷
Q = WhCpt
=1500×980×1.89×20/3600 = 15435 kW (2)导热油的量
导热油入口160℃,出口:140℃,则需要导热油的量
m=QCpt =
154352.0520 =376.46kg/s 需要的导热油量:376.46×3600/845 = 1603.85m3/h
(2)平均温度差
燃料油: 50℃ ——
70 ℃ 导热油: 160℃ ——
140 ℃
110℃
70℃
Δtm = 88.50℃ R = T1T2t2t1t2t1T1t1 = 16014070507050 = 1 P = = 11050 = 0.3333
=0.96 由R和P值,查图 6-15a,φΔtm = φΔt
ΔtΔtm’ = 0.96×88.50 =84.96 ℃
(3)初选换热器规格
根据两流体情况,取K选 = 400 W/ m·℃
第2页共 18 页
燃料油换热器计算
故
SQKtm =454m2 选择浮头式换热器(JB/T4717-92): DN1200
2管程,计算传热面积
504.3m2 管长L = 6 m 管径
Φ19×2 换热管数:1452 折流挡板间距
B = 300 mm 若采用这台换热器,要求过程的总传系数为:
KQStm = 360W/ m·℃
2、核算压降 (1) 管程压强降
管程平均通道面积
Ai = 0.1290 m2 ui = VSAi =
150036000.1290 = 3.23m/s Rei = du = 0.0153.2398082.74106 = 573857.87
0.2515以管壁粗糙度ε为0.25mm,则 ε/d = λ = 0.046 所以
ΔP1 = u22 = 0.0167 Lud22=0.046260.0159803.2322 =94063Pa ΔP2 = 3 = 39803.232 = 13928Pa Ft = 1.5
Ns = 1
Np =2 所以
ΣΔPi = (94063+13928)×1.5×1×2 = 326973 Pa (2) 壳程阻力降
第3页共 18 页
燃料油换热器计算
ΔP1′= Ffonc(NB1)uo22
管子为正三角排列,取F=0.5
nc = 1.1 (n) 1/
2= 1.1 (1452) 1/2 =41.92 取折流挡板间距
h=0.3 m NB = Lh1
=
60.3
1=19 AOh(Dncdo)=0
1.2-41.92×0.019)=0.1210 m2 uoVsAo = 3.68 m/s
0.0193.688451.311103Reo = douo =
= 45067 >500 fo = 5Reo-0.228 = 0.43 所以
ΔP1′= 0.5×0.43×41.92×19×
2hu
ΔP2′ = NB(3.5)D228453.6822 = 979796 Pa
220.38453.68
= 19(3.5)1.22
= 326135 Pa
po(p1\'p2\')FsNs
= (979796+326135)×1.15×1
=1501820.65Pa
3、核算总传热系数 (1)管程对流传热系数 αi Rei = 573857.87 Pr82.741060.981.888410/0.097481570.797
6第4页共 18 页
燃料油换热器计算
故 αi = 0.023(
= 0.023(di0.097480.015)Re0.8Pr0.33
0.8)(573857.87)1570.7970.33
= 68598.59 (2)壳程对流传热系数αo Ao= hD(1uo = dot1604)0.31.2(10.0190.025) = 0.0864m2
Reo = Pr36000.08640.0195.16845 = 5.16 m/s
=63191.30
31.311103cp2.05101.311100.1134323.7
故 αo = 0.36 *(λ/do)*Re^0.55 * Pr^(1/3) *0.95
= 0.360.11340.01963191.300.5523.71/30.95
=2561.24 (3)确定污垢热阻 Rso = 0.00018 Rsi =0.0009 (4)计算总传热系数 经计算 1Ko1Rso12561.24bdoOmdmRsidoddoid
0.000919151968598.591
5 =
0.000180.0019194517
= 0.00039040.000180.0000047190.001140.00001846
Ko= 576.84 K计/K选 = 576.84/360= 1.60 满足要求,但导热油壳程压降太大。
第5页共 18 页
燃料油换热器计算
(二)800m3/h
1、试算和初选冷却器的规格 (1)计算热负荷
燃料油入口温度50℃,经换热器加热至70℃装船。 装船泵额定流量:800m3/h 热负荷
Q = WhCpt
=800×980×1.89×20/3600 = 8232 kW (2)导热油的量
导热油入口160℃,出口:140℃,则需要导热油的量
m=QCpt =
82322.0520 =200.78kg/s 需要的导热油量:200.78×3600/845 = 855m3/h
(2)平均温度差
燃料油: 50℃ ——
70 ℃ 导热油: 160℃ ——
140 ℃
110℃
70℃
Δtm = 88.50℃ R = T1T2t2t1t2t1T1t1 = 16014070507050 = 1 P = = 11050 = 0.3333
=0.96 由R和P值,查图 6-15a,φΔtm = φΔt
ΔtΔtm’ = 0.96×88.50 =84.96 ℃
(3)初选换热器规格
根据两流体情况,取K选 = 400 W/ m·℃ 故
SQKtm =242m2 选择浮头式换热器(JB/T4717-92): DN900
第6页共 18 页
燃料油换热器计算
2管程,计算传热面积
279.2m2 管长L = 6 m 管径
Φ19×2 换热管数:800 折流挡板间距
B = 300 mm 若采用这台换热器,要求过程的总传系数为:
KQStm = 385.57W/ m·℃
4、核算压降 (3) 管程压强降
管程平均通道面积
Ai = 0.0707 m2 ui = VSAi =
80036000.0707 = 3.14m/s Rei = du = 0.0153.1498082.74106 = 557868
0.2515以管壁粗糙度ε为0.25mm,则 ε/d = λ = 0.046 所以
ΔP1 = u22 = 0.0167 Lud22=0.046260.0159803.1422 =88894Pa ΔP2 = 3 = 39803.142 = 14494Pa Ft = 1.5
Ns = 1
Np =2 所以
ΣΔPi = (88894+14494)×1.5×1×2 = 310164 Pa (4) 壳程阻力降 ΔP1′= Ffonc(NB1)uo22
管子为正三角排列,取F=0.5
nc = 1.1 (n) 1/
2= 1.1 (800) 1/2 =31.11 取折流挡板间距
h=0.3 m
第7页共 18 页
燃料油换热器计算
NB = Lh
1=
60.31
=19 AOh(Dncdo)=0
0.9-31.11×0.019)=0.0927 m2 uoVsAo = 2.56 m/s
0.0192.568451.311103Reo = douo =
= 31351 >500 fo = 5Reo-0.228 = 0.47 所以
ΔP1′= 0.5×0.47×31.11×19×
2hu
ΔP2′ = NB(3.5)D228452.5622 = 384617 Pa
220.38452.56
= 19(3.5)1.22
= 157827 Pa
po(p1\'p2\')FsNs
= (384617+157827)×1.15×1
=623810.6Pa
5、核算总传热系数 (4)管程对流传热系数 αi Rei = 557868 Pr82.741060.981.888410/0.097481570.797
6故 αi = 0.023(
= 0.023(di0.097480.015)Re0.8Pr0.33
0.8)(557868)1570.7970.33
= 67065.15 (5)壳程对流传热系数αo
第8页共 18 页
燃料油换热器计算
Ao= hD(1uo = dot855)0.30.9(10.0190.025)
= 0.0648m2
Reo = Pr36000.06480.0193.6658451.311103 = 3.665 m/s
=44882.97
3cp2.05101.311100.1134323.7
故 αo = 0.36 *(λ/do)*Re^0.55 * Pr^(1/3) *0.95
= 0.36
=2122 (6)确定污垢热阻 Rso = 0.00018 Rsi =0.0009 (4)计算总传热系数 经计算 1Ko1RsobdoRsidoddo0.11340.01944882.970.5523.71/30.95
O1mdmid
19151967065.151
5 =21220.000180.00191945170.0009
= 0.00047130.000180.0000047190.001140.000018886
Ko= 551 K计/K选 = 551/385.57= 1.43 满足要求。
第9页共 18 页
燃料油换热器计算
(三)800m3/h,因壳程导热油压降大,放大一级
1、试算和初选冷却器的规格 (1)计算热负荷
燃料油入口温度50℃,经换热器加热至70℃装船。 装船泵额定流量:800m3/h 热负荷
Q = WhCpt
=800×980×1.89×20/3600 = 8232 kW (2)导热油的量
导热油入口160℃,出口:140℃,则需要导热油的量
m=QCpt =
82322.0520 =200.78kg/s 需要的导热油量:200.78×3600/845 = 855m3/h
(2)平均温度差
燃料油: 50℃ ——
70 ℃ 导热油: 160℃ ——
140 ℃
110℃
70℃
Δtm = 88.50℃ R = T1T2t2t1t2t1T1t1 = 16014070507050 = 1 P = = 11050 = 0.3333
=0.96 由R和P值,查图 6-15a,φΔtm = φΔt
ΔtΔtm’ = 0.96×88.50 =84.96 ℃
(3)初选换热器规格
根据两流体情况,取K选 = 400 W/ m·℃ 故
SQKtm =242m2 选择浮头式换热器(JB/T4717-92): DN900
第10页共 18 页
燃料油换热器计算
2管程,计算传热面积
260.6m2 管长L = 4.5 m 管径
Φ19×2 换热管数:1006 折流挡板间距
B = 300 mm 若采用这台换热器,要求过程的总传系数为:
KQStm = 371.81W/ m·℃
6、核算压降 (5) 管程压强降
管程平均通道面积
Ai = 0.089m2 ui = VSAi =
80036000.089 = 2.50m/s Rei = du = 0.0152.5098082.74106 = 444162
0.2515以管壁粗糙度ε为0.25mm,则 ε/d = λ = 0.046 所以
ΔP1 = u22 = 0.0167 Lud22=0.046260.0159802.522 =56350Pa ΔP2 = 3 = 39802.52 = 9187.5Pa Ft = 1.5
Ns = 1
Np =2 所以
ΣΔPi = (56350+9187.5)×1.5×1×2 = 196612.5Pa (6) 壳程阻力降 ΔP1′= Ffonc(NB1)uo22
管子为正三角排列,取F=0.5
nc = 1.1 (n) 1/
2= 1.1 (1006) 1/2 =34.89 取折流挡板间距
h=0.3 m
第11页共 18 页
燃料油换热器计算
NB = Lh
1=
4.50.31
=14 AOh(Dncdo)=0
1.0-34.89×0.019)=0.1011 m2 uoVsAo = 2.35 m/s
0.0192.358451.311103Reo = douo =
= 28779 >500 fo = 5Reo-0.228 = 0.48 所以
ΔP1′= 0.5×0.48×34.89×19×
2hu
ΔP2′ = NB(3.5)D228452.3522 = 37122Pa
220.38452.3
5 = 14(3.5)1.22
= 97997 Pa
po(p1\'p2\')FsNs
= (37122+97997)×1.15×1
=155387Pa
7、核算总传热系数 (7)管程对流传热系数 αi Rei =
444162 Pr82.741060.981.888410/0.097481570.797
6故 αi = 0.023(
= 0.023(=55886
di0.097480.015)Re0.8Pr0.33
0.8)(444162)1570.7970.33
(8)壳程对流传热系数αo
第12页共 18 页
燃料油换热器计算
Ao= hD(1uo = dot)0.31(10.0190.025) = 0.072m2
855Reo = Pr36000.0720.0193.308451.311103 = 3.30 m/s
=40413
3cp2.05101.311100.1134323.7
故 αo = 0.36 *(λ/do)*Re^0.55 * Pr^(1/3) *0.95
= 0.36
=2003 (9)确定污垢热阻 Rso = 0.00018 Rsi =0.0009 (4)计算总传热系数 经计算 1Ko1RsobdoRsidoddo0.11340.019404130.5523.71/30.95
O1mdmid
1915195588615
=20030.000180.00191945170.0009
= 0.00049930.000180.0000047190.001140.000022665
Ko= 542 K计/K选 = 542/372= 1.46 满足要求。
第13页共 18 页
第16篇:换热器毕业设计论文
河南机电高等专科学校毕业设计说明书
第1章
浮头式换热器是管壳式换热器系列中的一种,它的特点是两端管板只有一端与外壳固定死,另一端可相对壳体滑移,称为浮头。浮头式换热器由于管束的膨胀不受壳体的约束,因此不会因管束之间的差胀而产生温差热应力,另外浮头式换热器的优点还在于拆卸方便,易清洗,在化工工业中应用非常广泛。本文对浮头式换热器进行了整体的设计,按照设计要求,在结构的选取上,即壳侧两程,管侧四程。首先,通过换热计算确定换热面积与管子的根数初步选定结构,然后按照设计的要求以及一系列国际标准进行结构设计,设计的前半部分是工艺计算部分,主要设根据设计传热系数、压强校核、壳程压降、管程压降的计算;设计的后半部分则是关于结构和强度的设计。主要是根据已经选定的换热器型式进行设备内各零部件(如壳体、折流板、管箱固定管板、分程隔板、拉杆、进出口管、浮头箱、浮头、支座、法兰、补强圈)的设计。
换热器是国民经济和工业生产领域中应用十分广泛的热量交换设备。随着现代新工艺、新技术、新材料的不断开发和能源问题的日趋严重,世界各国已普遍把石油化工深度加工和能源综合利用摆到十分重要的位置。换热器因而面临着新的挑战。换热器的性能对产品质量、能量利用率以及系统运行的经济性和可靠性起着重要的作用,有时甚至是决定性的作用。目前在发达的工业国家热回收率已达96%。换热设备在现代装置中约占设备总重30%左右,其中管壳式换热器仍然占绝对的优势,约70%。其余30%为各类高效紧凑式换热器、新型热管热泵和蓄热器等设备。其中板式、螺旋板式、板翅式以及各类高效传热元件的发展十分迅速。在继续提高设备热效率的同时,促进换热设备的结构紧凑性,产品系列化、标准化和专业化,并朝大型化的方向发展。浮头式换热器是管壳式换热器系列中的一种。换热管束包括换热管、管板、折流板、支持板、拉杆、定距管等。换热管可为普通光管,也可为带翅片的翅片管,翅片管有单金属整体轧制翅片管、双金属轧制翅片管、绕片式翅片管、叠片式翅片管等,材料有碳钢、低合金钢、不锈钢、铜材、铝材、钛材等。壳体一般为圆筒形,也可为方形。管箱有椭圆封头管箱、球形封头管箱和平盖管箱等。随着我国工业化和城镇化进程的加快,以及全球发展中国家经济的增长,国内市场和出口市场对换热器的需求量将会保持增长,客观上为我国换热器产业的快速发展提供了广阔的市场空间。从市场需求来看,在国家大力投资的刺激下,我国国民经济仍将保持较快发展。石油化工、能源电力、环境保护等行业仍然保持稳定增长,大型乙烯项目、大规模的核电站建设、大
河南机电高等专科学校毕业设计说明书
型风力发电场的建设、太阳能光伏发电产业中多晶硅产量的迅速增长、大型环境保护工程的开工建设、海水淡化工程的日益成熟,都将对换热器产业产生巨大的拉动。
未来散热器将会朝着更加节能环保和美观实用的角度不断创新与发展,短时期钢制柱式散热器和铜铝复合散热器任将会是市场主流产品与选择。
换热器在工业生产和生活的各个领域都得到了广泛的应用,而且其功作性能的优劣直接影响着整个装置和系统综合性能的好坏,因此换热器的合理设计极其重要,所以一个合理的换热器应满足一下的几点要求:
(1)在给定的工作条件(流体流量、进口温度等)下,达到要求的传热量和流体出口温度;
(2)流体压降要小,以减小运行的能量消耗; (3)满足外形尺寸和重量要求;
(4)安全可靠,满足最高工作压力,工作温度以及防腐、防漏、工作寿命等方面要求;
(5)制造工艺切实可行,选材合理且来源有保证,以减少初投资;
(6)安装、运输以及维修方便等。按照设计要求,在结构的选取上,为了增大压差校正系数,采用了壳侧两程管侧四程。
通过换热计算确定换热面积与管子的根数初步选定结构,然后按照设计的要求以及一系列国际标准进行结构设计。在结构设计时,要考虑许多因素,例如传热条件、材料、介质压力、温度、流体性质以及拆卸等等。之后对有些部件进行强度校核并进行对其优化设计。
换热设备是化工、炼油、动力、食品、轻工、原子能、制药、机械及其他许多工业部门广泛使用的一种通用设备。在化工厂中,换热设备的投资约占总投资的10%-20%,在炼油厂中,约占总投资的35%-40%。
1.1换热设备的应用
浮头式换热器由于管束的膨胀不受壳体的约束,因此不会因管束之间的差胀而产生温差热应力,另外浮头式换热器的优点还在于拆卸方便,易清洗,在化工工业中应用非常广泛。在工业生产中,换热设备的主要作用是使热量又温度较高的流体传递给温度较低的流体,使流体温度达到工艺过程规定的指标,以满足工艺过程上的需要。此外,换热设备也是回收余热和废热,特别是低位热能的有效装置。
河南机电高等专科学校毕业设计说明书
图1-1浮头式换热器实物图
1.2换热器设备的分类
1.2.1按作用原理分类 (1)直接接触式换热器
直接接触式换热器又称混合式换热器,是利用冷,热流体直接接触,彼此混合进行换热的换热器。为增加两流体的接触面积,以达到充分换热,在设备中常放置填料和栅板,通常采用塔状结构。如冷却塔,冷却冷凝器等。 (2)蓄热式换热器
蓄热式换热器又称回热式换热器,是借助于固体构成的蓄热体与热流体和冷流体交替接触,把热量从热流体传递给冷流体的换热器。在换热器内首先由热流体通过,把热量积蓄在蓄热体中,然后由流体通过,由蓄热体把热量释放给冷流体。由于两种流体交替与蓄热体接触,因此不可避免地会使两种流体少量混合。若两种流体不允许有混合,则不采用蓄热式换热器。 (3)间壁式换热器
它又称表面式换热器,是利用间壁将进行热交换的冷热两种流体隔开,互不接触,热量由热流体通过间壁传递给冷流体的换热器。间壁式换热器是工业生产中应用最为广泛的换热器,其形式多样,如管壳式换热器和板式换热器都属于间壁式换热器。 (4)中间载流体式换热器
它是把两个间壁式换热器由在其中循环的载流体连接起来的换热器。载流体在高温流体换热器和低温流体换热器之间循环,在高温流体换热器中吸收热量,在低温流
河南机电高等专科学校毕业设计说明书
体换热器中把热量释放给低温流体,如热管式换热器等。 1.2.2按作用方式分类 (1)管式换热器
管式换热器都是通过管子壁面传热的换热器。按传热管的结构形式不同大致可分为蛇管式换热器、套管式换热器、缠绕管式换热器和管壳式换热器等。蛇管式换热器一般由金属或非金属管子,按需要弯曲成所需的形状,如圆盘形、螺旋形和长的蛇行等。它是最早出现的一种换热设备,具有结构简单和操作方便等优点。按使用状态不同,蛇管式换热器又可分为沉浸式蛇管和喷淋式蛇管两种。套管式换热器是由两种不同大小直径的管子组装成同心管,两端用U形弯管将他们连接成排,并根据实际需要,排列组合成传热单元,换热时,一种流体走内管,另一种流体走内外管间的环隙,内管的壁面为传热面,一般按逆流方式进行换热。两种流体都可以在较高的温度、压力、流速下进行换热。套管式换热器的优点是结构简单,工作适应范围大,传热面积增减方便,两侧流体均可提高流速,使传热面的两侧都可有较高的传热系数;缺点是单位传热面的金属消耗量大,检修、清洗和拆卸都较麻烦,在可拆连接处容易造成泄漏。管壳式换热器是目前应用最为广泛的换热设备。在圆筒形壳体中放置了许多管子组成的管束,管子的两端固定在管板上,管子的轴线与壳体的轴线平行。为了增加流体在管外空间的流速并支撑管子,改善传热性能,在筒体内间隔安装多块折流板,用拉杆和顶距管将其与管子组装在一起。换热器的壳体上和两侧的端盖上装有流体的进出口,有时还在其上装设检查孔,为了安置测试仪表用的接口管,排液孔和排气孔等。缠绕管式换热器是芯筒与外筒之间的空间内将传热管按螺旋闲形状交替缠绕而成,相邻两成螺旋状传热管的螺旋方向相反,采用一定形状的定距管使之保持一定的距离。缠绕状传热管可以采用单根绕制,也可采用两根或多跟组焊后一起绕制。管内可以通过一种介质,称通道型缠绕管式换热器;也可分别通过几种不同的介质,而每种介质所通过的传热管均汇集在各自的管板上,构成多通道型缠绕管式换热器。缠绕管式换热器适用于同时处理多种介质等场合。 (2)板面式换热器
板面式换热器是通过板面进行传热的换热器。板面式换热器按传热板面的结构形式可分为以下五种:螺旋板式换热器、板式换热器、板翅式换热器、板壳是换热器和伞式换热器。板面式换热器的传热性能要比管式换热器优越,由于结构上的特点,使流体能在较低的速度下就达到湍流状态,从而强化了传热。板面是换热器采用板材制
河南机电高等专科学校毕业设计说明书
作,在大规模组织生产时,可降低设备成本,但其耐压性能比管式换热器差。
河南机电高等专科学校毕业设计说明书
第2章 浮头式换热器热力计算
浮头式换热器热力计算一般包括:定性温度和物性参数,初选结构,管程热力计算及流量计算,壳程换热计算,传热系数,管程压降,壳程压降压强校核。
2.1原始数据
油进口温度: t1=175℃ 油出口温度: t1=155℃ 油工作压力: P1=1.6MPa 水进口温度: t2\'=144℃
\"水出口温度: t2=163℃ \'\"水工作压力: P2=2MPa 壳体内径: DS=700mm 管箱内径: DN=750mm 换热管规格:Φ19×3 L=8m 2.2定性温度和物性参数计算
水的定性温度: t2t2144163t2153.5C 22水的密度: ρ2=913kg/m3 水的比热: Cp2=4.32kJ/kg℃ 水的导热系数:k2=0.686W/m℃ 水的粘度: μ2=168.8×10-6 水的柏朗特数:Pr2=1.08 油(柴油)的定性温度: t1t1175155t1165C 22油的密度: ρ1=715 kg/m3 油的比热: Cp1=2.48 kJ/kg℃ 油的导热系数:k1=0.133 W/m℃ 油的粘度: μ1=6.4×10-4
河南机电高等专科学校毕业设计说明书
油的普朗特数:
1000Cp1110002.486.4104Pr111.93k10.133
2.3 初选结构
管排列方式 :分程隔板两侧正方形,其余三角形 管子外径: d0=0.019m 管子内径:
di=d0-(2×3/1000)=0.013m 管长: L=8m 管间距:
s=1.5d0=1.5×0.19=0.0285m 壳体内径: Ds=0.7m 管束中心排管数:由公式
s(Nc1)4d0Ds
得Nc=22 总管子数:由:
1.1NtNc得 Nt=400
选型:采用双壳程四管程。
2.4 管程换热计算及流量计算
试选传热系数: k0=240 W/m2℃ 传热面积:由
得A0=190.91m2 逆流平均温差:
A0Nt d0ltNt大t小201919.5C t大20lnln19t小
河南机电高等专科学校毕业设计说明书
无量纲量参数:
Pt216314419t20.612t217514433t1 t117515520t11.05t2t216314419 R温差校正系数:按2壳程4管程查得0.88 有效平均温差:
tmtN0.8819.517.16C
设计传热量:
Q0A0k0tm190.9124017.16786244W
换热效率:取η=0.98 油流量:
G1水流量:
G2Q0360078624458231kg/h
t1)2.48200.981000Cp1(t1Q0360078624434484kg/h Cp2(t2t2)4.32191000管程流通截面(4管程): A2(Nt2400)di()0.01320.0133m2 4444管程流速:
w2G2344840.789m/s
2a236009130.01333600管程雷诺数:
Re2管程换热系数:
2w2di9130.7890.013554782168106
h23605(10.015t2)20.8/(100di)0.23605(10.015153.5)0.7890.8/(1000.013)0.2 2385.4W/mC
河南机电高等专科学校毕业设计说明书
2.5 壳程换热计算
折流板的设计:纵向折流板中间分程,横向安置弓形折流板。 弓形折流板弓高:
H0.20Ds0.200.700.14m
折流板间距:
BDS0.70.233m 33壳程流通截面:
a1d110.019BDs(10)0.230.70(1)0.027m22s20.0285
壳程流速:
G1582313600w136000.0838m/s
1a17150.027壳程量流速
W11w17150.838599kg/m2s
壳程当量直径:
DsNtd00.7024000.0192de0.046m
Ntd04000.019壳程雷诺数:
RefW1de2215990.04643053
6.4104切去弓形面积所占比例:查得
afaT0.0145
壳程传热因子:查得js96
管外壁温度:tW1假定后再复核,设tW1=160℃
壁温下的粘度:
W11.6104Pas1
河南机电高等专科学校毕业设计说明书
粘度修正系数:
1(10.146.40.14)()0.92W11.61
2.6传热系数
水侧污垢热阻: r117.2105m2℃/W 油侧污垢热阻: r252.0105m2℃/W 管壁热阻:r忽略 总传热热阻:
rd11dr1r200h1dih2di10.01910.0190.0001720.00052583.50.0132385.40.013 0.00326m2C/W传热系数:
kj11306.7 r0.00326传热系数的比值:
kjk0306.71.28 240管外壁热流密度:
q1管外壁温度:
Q0786244=4118W/m2℃ Ntd0l4000.0198q1(tW1t1110.000172)=167.2℃ r1)1754118(583.5h1误差校核:
tWtW1tW1=167.2-160=7.2℃
误差不大,不必再重算。
河南机电高等专科学校毕业设计说明书
2.7管程压降
壁温:
tW2t1q1(11(0.00172)=161.3℃ r1)153.54188583.5h1壁温下水的粘度:w280.3105PaS 管程摩擦系数:查得i0.02 管子沿程压降:
LniiW22(0.789913)2840.02Pi()()()141313Pa 22di229130.0130.99回弯压降:
2(0.789913)W22444546.9Pa Pr()4nt222913进出口管处质量流速:
222WN2w进9131.21314.7kg/ms 出口进出管口处压降:
1314.72PN2()1.51.51419.9Pa
222913管程结垢校正系数:根据r2及Φ193得 d21.2 管程压降:
P2(PiPr)d2PN2(1413.34546.9)1.21419.923834PaWN2
2.8 壳程压降
当量直径:
Ds2Ntd020.7024000.0192de0.0427m DsNtd00.7024000.019雷诺数:
Re1
W1de15990.42739965
6.410411
河南机电高等专科学校毕业设计说明书
壳程摩擦系数:查得00.27 管束压降:
W12Ds(nB1)059920.70(331)0.27P0()[]()[]()41043.3Pa 1de12715de0.92管嘴处质量流量:
2WN1w进出口7151.521608.8kg/m2s
进出口管压降:
1608.82PN1[]1.51.52714.9Pa
2127152WN2导流板阻力系数:取ip5 导流板压降:
1608.82Pip[]ip59049.8Pa
2127152WN2壳程结垢修正系数:查表取d01.38 壳程压降:
P1P0d0PipPN141043.31.389049.82714.968404Pa
2.9 压强校核
管程工作压力P22.0MPa,查表得[P2]2.5MPa 壳程工作压力P11.6MPa,查表得[P1]1.8MPa 压强校核:
P2[P2] 符合要求
P1[P1] 符合要求
河南机电高等专科学校毕业设计说明书
第3章 结构设计
结合热力计算确定换热流程、面积、排列方式、壳体、管箱、固定管板、分程隔板、以及其他零部件。
3.1换热流程设计
采用2壳程4管程的2-4型换热器。由于换热器尺寸不大,可以用一台,未考虑采用多台组合使用。管程分程隔板采用丁字型结构,其主要优点是布管紧密。壳体分程采用纵向隔板。
管程的分程隔板采用丁字型结构如图3-1所示,其主要优点是布管紧密。
图3-1丁字形隔板
3.2管子和传热面积
换热管除要求具有足够的强度外,当采用胀管法固定时,还要求管子有良好的塑性,避免因胀接而产生裂缝。焊接固定时,要求管子可焊性好,一般采用优质碳钢,以保证管子质量,一般对于无腐蚀性或腐蚀性不大的流体可采用10号钢和20号钢管,在强腐蚀性流体的情况下,可采用不锈钢、钢、铝等无缝管,在强腐蚀性流体的情况下,可采用石墨管、聚四氟乙烯管等。由于水、油腐蚀性不大,故可采用碳钢,现选择20号钢的无缝钢管。
根据设计要求采用193的无缝钢管。 管子总数为400根。其传热面积为:
Ad0LNt0.0198400190.91m2
3.3管子排列方式
管子在管板上的排列方式,应力求均布、紧凑并考虑清扫和整体结构的要求。基本的排列方式有五种:
等边三角形:一边与流向垂直是常用的形式,与正方形排列相比传热系数高,可节省15%的管板面积。适用于不生污垢、可用化学清洗污垢和允许压降较高的工况;
河南机电高等专科学校毕业设计说明书
转角三角形。三角形的一边与流向平行,其特点介于等边三角行和正方形两种排列之间,不宜用于卧式冷凝器,因下方管子形成的厚度越来越厚的凝膜会使传热削弱;
正方形排列最不紧凑,但便于机械清扫,常用于壳程介质易生污的浮头式换热器; 同心圆排列,用于小壳径换热器时比正三角形排列还紧凑,靠近壳体的地方布管均匀。
对于多管程换热器常采用组合排列法,每程均属正三角形排列,而各层面间呈正方形排列,以便于安排分程隔板。
综合比较以上几种布管方式,可采用组合排列形式,中间正方形,其余三角形。布管位置如图3-2示。十字形的走廊是为了装设分程隔板,故有壳程流体的泄漏和旁流的问题,共有406个管孔,其中6个孔为安装拉杆用。
图3-2 管子排列
3.4壳体
壳体材料除要满足一定的强度外,由于制造过程中经过卷板、冲压和焊接,故要求材料有一定的塑性和可焊性,一般采用含碳量较低的3R钢、16nR钢等,现选用16nR钢。
壳体内径Ds=700mm 壳体壁厚:
pDSc t2[]p
河南机电高等专科学校毕业设计说明书
[]t为壳体工作温度下的许用应力,已知壳程设计温度为220℃,则tw
1.21.670026.8mm21670.851.21.6 实取10mm,之后要用有限元分析软件ANSYS进行强度校核。
3.5 管箱
3.5.1 封头
根据压力容器设计规范采用材质为16MnR的标准椭圆封头,在满足强度要求的情况下,其壁厚可用以下公式计算:
pDSc t2[]0.5p已知管程设计温度为200℃,则tw
1.21.675027mm
21700.850.51.21.6实取12mm,之后用ANSYS进行强度校核。 曲面高度:
hDD75012190.5mm 444D-封头的平均直径 直边高度h025mm 3.5.2壁厚
pDS1.21.6750c27.02mm 2[]tp21700.851.21.6实取12mm,之后要用ANSYS进行强度校核。 内径:D\"750mm 长度:L0300mm
河南机电高等专科学校毕业设计说明书
3.6 固定管板
外径:D1797mm 板厚:b50mm
管板上开孔数与孔间距与管的排列一致。管板材料选用Q235钢。
管子与管板的连接必须牢固、不泄漏、不产生大的应力变形,最常见的连接方法为胀接,胀接只能用于工作压力低与4MPa和温度低于300℃的场合;对于高温、高压、易燃、易爆的运行条件多采用焊接,但采用焊接容易产生热应力且间隙中流体不流动很容易造成间隙腐蚀,采用胀焊并用的方法可以避免。
由于工作压力和温度都不是特别高,而且管子的间距比较大,管板和管子的连接采用胀接。换热管在管板内的胀接长度L=38mm。
3.7 分程隔板
3.7.1 管程分程隔板
管箱的分程在固定端管箱与浮头端管箱内都要安装分程隔板,隔板的布置见图3-1,由于两端管箱不是很长,卸下清洗时不用拆下来,因此可以将隔板直接焊接在箱体上。管程隔板要考虑密封问题,它们的密封是通过在固定管板和浮动管板插隔板的槽内安放密封填料。为了保证填料能起到密封作用,隔板的长度要按安装的尺寸进行计算。
3.7.2壳程分程隔板
安装壳体的分程隔板一方面要考虑到密封问题,另一方面要便于拆卸,因此采用图3-3所示的装置来安装隔板,当转动偏心杆手柄,偏心杆的凸轮推动与其相接的端头包有密封填料的板可使两端夹紧也可使其松开,便于拆卸。对于浮头式管束要能够拆卸必须要隔板可以拆卸。因此,此装置是必须要用的。
河南机电高等专科学校毕业设计说明书
隔板偏心杆密封填料
图3-3壳体分程隔板
3.8折流板
采用弓形折流板,材料钢板,由于壳内分程,每程均采用半弓形如图3-4所示,布置方式采用垂直切口流动方向。
图3-4折流板
按一个壳程计算(计算过程见热力学计算)得: 拱高:h140mm 板间距:B230mm 板数:nB33 板厚:B6mm
由于考虑到实际安装时由于第一块折流板的位置壳体接管位置的影响,在一个壳程内折流板的实际个数应为32个,总的折流板数为64。
3.9 拉杆
材质为钢。直径φ12,共6根。拉杆是用来安装折流板的。每个折流板最好由三个拉杆来定位。其布置位置见图3-4。
河南机电高等专科学校毕业设计说明书
3.10 进出口管
3.10.1 管程进口管
2按2wN.9 3000取wN21.2m/s 则2w29131.211862进出口流通截面积为:
aN2G2344840.00807m2
36002wN236001186.9进出口管内径为:
DN24aN240.008070.101m
取用1004mm的热扎钢管。 3.10.2 管程进出口管
2按1wN2000取wN11.5m/s 1则1wN17151.51072.5 进出口流通截面积为:
aN1G1582310.01508m2
36001wN136001072.5进出口管内径为:
DN24aN140.015080.139m
取用1504.5mm的热轧钢管。
3.11 浮头箱
外头盖内直径:
D1DN100mm800mm
外头盖同样采用材质为16MnR的标准椭圆形封头: 厚度12mm 曲面高度:
h2DD180012203mm 444
河南机电高等专科学校毕业设计说明书
直边高度h25mm
3.12 浮头
如图3-5所示为浮头端的装配图,包括碟形盖,钩圈法兰和浮动管板,由于浮动管板要与管子胀接后从壳体一端伸到另一端,因此管板的外直径应小于壳体内径,其主要尺寸如下:
图3-5 浮头结构图
浮动管板外直径:D0690mm 浮动管板厚:b500mm 浮头法兰外径:
DfoDN80mm780mm
浮头法兰内直径:
Df1Df2(5013)654mm 碟形盖内半径:
L0.75Df10.75654409.5mm
厚度:0取15mm 3.13 补强圈
在实际设计和名义厚度大于12mm时,接管Dg>80mm就必须加开孔补强,当壳体名义厚度小于或等于12mm时,接管Dg>50mm就必须加开孔补强。因此对于Dg=100的管箱接管和Dg=150的壳体接管都必须进行开孔补强。
在补强圈标准中规定了补强圈的尺寸,按标准尺寸Dg =100的接管补强圈外直径D0=210mm,Dg =150的接管补强圈外直径D0=300mm。补强圈的厚度可通过等面积补强法进行计算。这里设定补强圈的厚度均为15mm。
河南机电高等专科学校毕业设计说明书
3.14 法兰
3.14.1法兰密封面的形式
压力容器和管道法兰联接中,常用的密封面型式有以下三种。
(1)平面型密封面
密封表面是一个突出的光滑平面(又称突平面)。这种密封面结构简单,加工方便,便于进行防腐衬里。但螺栓上紧后,垫圈材料容易往两侧伸展,不易压紧,用于所需压紧力不高且介质无毒的场合。
(2)凹凸型密封面
它是由一个凸面和一个凹面所组成,在凹面上放置垫圈,压紧时,由于凹面的外侧有挡台,垫圈不会挤出来。
(3)榫槽型密封面
密封面是由一个榫和一个槽所组成,在垫圈放在槽内。这种密封面规定不用非金属软垫圈,可采用缠绕式金属包垫圈,易获得良好的密封效果。它适用于密封易燃、易爆、有毒介质。密封面的凸面部分容易破坏,运输与装拆时都应注意。
在选取密封面时综合考虑介质因素和装拆的因素,壳体法兰均采用凹凸面型密封面,管箱接管法兰采用平面型密封面,壳体接管法兰采用凹凸型密封面。 3.14.2 壳体法兰
壳体接管采用平颈对焊法兰,由于管箱、壳体、浮头箱直径都不一样,因此在选用法兰时,不能只按标准选取。如图3-6为壳体与浮头箱的对接法兰,DN=800mm的是按标准选取的,而DN=700的法兰是按DN800法兰螺栓孔的位置来设计其尺寸的,
图3-6凹凸面密封法兰
河南机电高等专科学校毕业设计说明书
大致尺寸如下: DN=800mm的法兰,D=960mm, D1=915mm,D2=876mm,D3=866mm,H=115mm, h=35mm,δ=48mm,δ1=16倒圆角R=12mm,螺柱孔径r=26,配M24的双头螺柱。
DN=700mm的法兰,D=960mm,D1=915mm,D4=863mm, H=115mm, h=35mm, δ=46mm,δ1=16,倒圆角R=12mm,螺柱孔径r=26,配M24的双头螺柱。
其它的法兰装配尺寸见三维实体图。 3.14.3 接管法兰
管箱接管采用平颈对焊法兰,如图示:
图3-7接管法兰
设计尺寸按化工机械标准设计,其尺寸大致如下: 管箱接管:DN=100 PN=2.5MPa时:
N=132mm,K=190mm,D=235mm,H=66mm,H1=12mm,S=6mm,法兰厚度C=24mm螺栓孔直径L=22mm,配M20的螺栓8个
壳体接管:DN=150 PN=1.6MPa时:
N=132mm,K=190mm,D=285mm,H=61mm,H1=12mm,S=6.5mm,法兰厚度C=22mm,螺栓孔直径L=22mm,配M20的螺栓8个
另外,对焊时法兰要在颈部开坡口。
3.15 支座
卧式设备一般采用两个鞍座。这是因为基础水平高度有可能不一致,如果使用多个支座,将会造成支座反力分布不均匀,从而引起设备的局部应力增大,因此采用两个支座。
采用双支座时,一个鞍座为固定支座,地脚螺栓为圆孔;另一个鞍座为活动支座,地脚螺栓为长圆孔,配合两个螺母,第一个螺母拧紧后,倒退一圈,然后再用第二个
21
河南机电高等专科学校毕业设计说明书
螺母锁紧。这样,可以使设备在温度变化是自由伸缩。如图示:
δ4Ⅰ型Ⅱ型
图3-8 鞍式支座
其主要尺寸为:h=200mm;l1=640mm;b1=150mm;1 =10mm;2 =8mm;l3=350mm;b3=120mm; 3=8mm;弧长830mm;b4=200mm; 4=6mm;e=36mm;l2=460mm。
支座的安放位置也有一定的标准,一般支座与壳体端面的距离A
22
河南机电高等专科学校毕业设计说明书
第4章 安装与拆卸
设计中要考虑到安装问题,各零部件的结构不能影响整个装配体的安装,对于浮头式换热器,设计的初衷是可以拆下管束进行清洗。因此也要考虑到拆卸的问题,其安装步骤可概述如下:
(1)焊接部件:将所有的焊接部件进行焊接,包括管箱,壳体,浮头箱,碟形盖,支座等;
(2)安放折流板:将拉杆的一个螺纹端拧入固定管板的螺纹孔,6根拉杆都装好,然后每套入一组定距杆再装一组折流板,依次把折流板装在拉杆上,直到最后两块折流板装上后用螺母套在拉杆的另一个螺纹端拧紧固定;
(3)安装管子:将管子沿折流板的孔一根根穿入,并在固定管板上进行胀接。另一端装上浮动管板并进行胀接;
(4)安装壳程隔板:先将壳程隔板两侧的偏心杆机构装好,将壳程隔板从管束侧面装入并将一头插入固定管板上安装隔板的槽中;
图4-1安装示意图
(5)安装壳体:将焊接好的壳体从浮动管板的那一端套入,使之前装好的组件(如图4-1示)完全装入壳体内,在壳程隔板的伸出端扭动偏心杆的摇柄使隔板两侧的密封填料挤紧,从而达到壳程的分程密封;
(6)安装管箱:在固定管板端接已焊接好的管箱,将管箱法兰与壳体法兰对接用双头螺柱连接。在浮头端装上钩圈法兰和碟形盖,(钩圈法兰由两个半圆形构成,使其安装方便)用双头螺柱连接;
(7)安装浮头箱:将浮头箱法兰与壳体法兰对接用双头螺柱连接; (8)安装支座:将支座焊接到壳体上。
23
河南机电高等专科学校毕业设计说明书
总结
通过三个月的努力,我的毕业设计终于圆满完成。虽然做的过程很辛苦,但是看到自己的成果,我感到很欣慰。作为大学三年的最后一道大作业—毕业设计,使我在各个方面都有了很大的提高,收获很大。具体表现在以下几个方面:通过在设计中经常查资料提高了我们检索和查阅资料的能力;进一步扎实了所学的理论知识,对所学基础知识和专业知识进行了一次综合应用和系统复习;思维方式和设计思想更加全面化和系统化。养成了勤学好问的习惯,敢于面对困难,能够独立的查找和解决问题,也提高了自己的创新能力。将理论知识和生产实际相结合,为以后的工作和学习打下了很好的基础,但是,设计过程中仍然存在不足之处,有的问题还需要进一步展开研究。具体如下:
(1)管子的胀接没有进行分析计算;
(2)由于管程与壳程的分程使管子的排列不均匀,故存在旁流与侧流的问题,此问题尚未进行分析;
(3)通常在进液管口有挡板控制流速和引流,此结构尚未设计。
24
河南机电高等专科学校毕业设计说明书
致谢
首先,向尊敬的导师李老师致以衷心的谢意,在大三毕业设计期间,李老师以其渊博的知识、开阔的思维使我在知识和能力上获得了极大的提高;更重要的是,李老师在工作方面严谨的作风、积极进取的态度对我产生了巨大的积极影响。这次毕业论文设计李老师给予我许多帮助,在设计的选题以及设计的方法上,提供了许多宝贵的建议。李师在毕业设计期间,对我们要求严格,使我们能够基本独立完成设计任务,培养我们独立解决问题的能力,还从自己的宝贵时间中抽时间为我们审阅设计内容,并给予纠错,帮助改正。这些帮助和教导将使我在今后的学习和工作中奋发向上、积极进取,在学业和事业上取得更好的成绩。
而后更重要的,我要感谢我的母校--河南机电高等专科学校给了我三年深造的机会,让我学到了为人的优良品质和工作所需的知识技能,让我在学识和内涵上得到提高。感谢河南机电高等专科学校的老师和同学们这几年来的对我的关心和鼓励。老师们课堂上激情洋溢,课堂下细心辅导;同学们在学习中的认真热情,生活上的热心主动,所有这些都让我的三年大学生活收获不少,也充满了感动。感谢我的家人,他们的支持与鼓励是得我能顺利的完成学业。
最后,衷心感谢在百忙之中抽出宝贵时间对我论文进行评阅的专家、学者及亲爱的老师们!
25
河南机电高等专科学校毕业设计说明书
参考文献
[1]朱聘冠.换热器原理及计算[M].北京 :清华大学出版社,1987 [2]史美中,王中铮.热交换器原理与设计[M].北京:东南大学出版社,1996 [3]钱颂文.换热器设计手册[M].北京:化学工业出版社,2003 [4]庄俊,徐通明,石寿椿.热管与热管换热器[M].上海:上海交通大学出版社,1987 [5]董大勤.化工设备机械基础[M].北京:化学工业出版社,1990 [6]化工设备机械基础编写组.化工设备机械基础[M].北京:石油化学工业出版社,1978 [7]赵克勤,王秀珍,王正.石油化工容器及设备[M].武汉:华中理工大学出版社,1990 [8][美]贾瓦特M.H.化工设备结构分析与设计[M].北京:中国石化出版社,2003 [9]顾芳珍,陈国桓.化工设备设计基础[M].天津:天津大学出版社,1997 [10]黄振仁,魏新利.过程装备成套技术[M].北京:化学工业出版社,2003
26
第17篇:换热器的种类
管壳式换热器由一个壳体和包含许多管子的管束所构成,冷、热流体之间通过管壁进行换热的换热器。管壳式换热器作为一种传统的标准换热设备,在化工、炼油、石油化工、动力、核能和其他工业装置中得到普遍采用,特别是在高温高压和大型换热器中的应用占据绝对优势。通常的工作压力可达4兆帕,工作温度在200℃以下,在个别情况下还可达到更高的压力和温度。一般壳体直径在1800毫米以下,管子长度在9米以下,在个别情况下也有更大或更长的。
工作原理和结构 图1 [固定管板式换热器]为固定管板式换热器的构造。A流体从接管1流入壳体内,通过管间从接管2流出。B流体从接管3流入,通过管内从接管4流出。如果A流体的温度高于B流体,热量便通过管壁由A流体传递给B流体;反之,则通过管壁由B流体传递给A流体。壳体以内、管子和管箱以外的区域称为壳程,通过壳程的流体称为壳程流体 (A流体)。管子和管箱以内的区域称为管程,通过管程的流体称为管程流体(B流体)。管壳式换热器主要由管箱、管板、管子、壳体和折流板等构成。通常壳体为圆筒形;管子为直管或U形管。为提高换热器的传热效能,也可采用螺纹管、翅片管等。管子的布置有等边三角形、正方形、正方形斜转45°和同心圆形等多种形式,前3 种最为常见。按三角形布置时,在相同直径的壳体内可排列较多的管子,以增加传热面积,但管间难以用机械方法清洗,流体阻力也较大。管板和管子的总体称为管束。管子端部与管板的连接有焊接和胀接两种。在管束中横向设置一些折流板,引导壳程流体多次改变流动方向,有效地冲刷管子,以提高传热效能,同时对管子起支承作用。折流板的形状有弓形、圆形和矩形等。为减小壳程和管程流体的流通截面、加快流速,以提高传热效能,可在管箱和壳体内纵向设置分程隔板,将壳程分为2程和将管程分为2程、4程、6程和8程等。管壳式换热器的传热系数,在水-水换热时为1400~2850瓦每平方米每摄氏度〔W/(m(℃)〕;用水冷却气体时,为10~280W/(m(℃);用水冷凝水蒸汽时,为570~4000W/(m(℃)。
特点 管壳式换热器是换热器的基本类型之一,19世纪80年代开始就已应用在工业上。这种换热器结构坚固,处理能力大、选材范围广,适应性强,易于制造,生产成本较低,清洗较方便,在高温高压下也能适用。但在传热效能、紧凑性和金属消耗量方面不及板式换热器、板翅式换热器和板壳式换热器等高效能换热器先进。 分类 管壳式换热器按结构特点分为固定管板式换热器、浮头式换热器、U型管式换热器、双重管式换热器、填函式换热器和双管板换热器等。前 3种应用比较普遍。 固定管板式换热器 它是管壳式换热器的基本结构形式(图1 [固定管板式换热器])。管子的两端分别固定在与壳体焊接的两块管板上。在操作状态下由于管子与壳体的壁温不同,二者的热变形量也不同,从而在管子、壳体和管板中产生温差应力。这一点在分析管板强度和管子与管板连接的可靠性时必须予以考虑。为减小温差应力,可在壳体上设置膨胀节。固定管板式换热器一般只在适当的温差应力范围、壳程压力不高的场合下采用。固定管板式换热器的结构简单、制造成本低,但参与换热的两流体的温差受一定限制;管间用机械方法清洗有困难,须采用化学方法清洗,因此要求壳程流体不易结垢。
浮头式换热器 图2 [浮头式换热器]为浮头式换热器的结构。管子一端固定在一块固定管板上,管板夹持在壳体法兰与管箱法兰之间,用螺栓连接;管子另一端固定在浮头管板上,浮头管板与浮头盖用螺栓连接,形成可在壳体内自由移动的浮头。由于壳体和管束间没有相互约束,即使两流体温差再大,也不会在管子、壳体和管板中产生温差应力。对于图2a[浮头式换热器]中的结构,拆下管箱可将整个管束直接从壳体内抽出。为减小壳体与管束之间的间隙,以便在相同直径的壳体内排列较多的管子,常采用图2b[浮头式换热器]的结构,即把浮头管板夹持在用螺栓连接的浮头盖与钩圈之间。但这种结构装拆较麻烦。浮头式换热器适用于温度波动和温差大的场合;管束可从壳体内抽出用机械方法清洗管间或更换管束。但与固定管板式换热器相比,它的结构复杂、造价高。
U型管式换热器 一束管子被弯制成不同曲率半径的U型管,其两端固定在同一块管板上,组成管束(图3[U型管式换热器])。管板夹持在管箱法兰与壳体法兰之间,用螺栓连接。拆下管箱即可直接将管束抽出,便于清洗管间。管束的U形端不加固定,可自由伸缩,故它适用于两流体温差较大的场合;又因其构造较浮头式换热器简单,只有一块管板,单位传热面积的金属消耗量少,造价较低,也适用于高压流体的换热。但管子有U形部分,管内清洗较直管困难,因此要求管程流体清洁,不易结垢。管束中心的管子被外层管子遮盖,损坏时难以更换。相同直径的壳体内,U形管的排列数目较直管少,相应的传热面积也较小。
双重管式换热器 将一组管子插入另一组相应的管子中而构成的换热器(图4 [双重管式换热器])。管程流体(B流体)从管箱进口管流入,通过内插管到达外套管的底部,然后返向,通过内插管和外套管之间的环形空间,最后从管箱出口管流出。其特点是内插管与外套管之间没有约束,可自由伸缩。因此,它适用于温差很大的两流体换热。但管程流体的阻力较大,设备造价较高。
填函式换热器 图5 [填函式换热器]为填函式换热器的结构。管束一端与壳体之间用填料密封。管束的另一端管板与浮头式换热器同样夹持在管箱法兰与壳体法兰之间,用螺栓连接。拆下管箱、填料压盖等有关零件后,可将管束抽出壳体外,便于清洗管间。管束可自由伸缩,具有与浮头式换热器相同的优点。由于减少了壳体大盖,它的结构较浮头式换热器简单,造价也较低;但填料处容易渗漏,工作压力和温度受一定限制,直径也不宜过大。
双管板换热器 管子两端分别连接在两块管板上(图6[双管板换热器的结构特点]),两块管板之间留有一定的空间,并装设开孔接管。当管子与一侧管板的连接处发生泄漏时,漏入的流体在此空间内收集起来,通过接管引出,因此可保证壳程流体和管程流体不致相互串漏和污染。双管板换热器主要用于严格要求参与换热的两流体不互相串漏的场合,但造价比固定管板式换热器高。
第18篇:波纹管换热器总结
波纹管换热器
1.波纹管的类型
波纹管是在普通换热管的基础上经特殊工艺加工而成的一种管内外都有凹凸波形,既能强化管内又能强化管外的双面强化传热管。从波形上分为螺旋形波纹和环形波纹二大类。由于螺旋型波纹管接头部位难处理从而使其使用受限,故现在广泛使用的是环形波纹管。其中环形波纹管分为波谷型波纹管、梯形波纹管、缩放管、波节管等几大类。
2.波纹管强化传热的原理
波纹管管内流体沿流动方向的流动是在反复改变速度及压力梯度下进行的,呈波峰处流体速度低、静压增大,波谷处流体速度增加、静压减小的状态,在波纹管的波峰进口处发生喷射效应,出口发生节流效应,两效应的结果使壁面内侧发生无数小旋涡,加强了流体的湍流程度,使管子的全部内表面都受流体的冲刷,既破坏了边界层,还冲刷了污垢层,从而不易结垢。由于其截面的周期性变化,管内外流体总是处于规律性的扰动状态,即使流体在很低的流速下,管内外便会形成比较强烈的扰动,即波纹管在强化管程传热的同时也能强化壳程传热。在低雷诺数下,波节管的换热与阻力性能比明显好于光管;在高雷诺数下,波节管与光管的换热与阻力性能比非常接近。 3.波纹管换热器与普通换热管的区别 3.1传热效率
波纹管由于存在波峰与波谷设计, 使流体流动时由于管内外截面连续不断地突变形成强烈湍流,即使在流速很小的情况下,流体在管内外均可形成强烈扰动,大大提高了换热管的传热系数。 3.2换热面积
与光管比较,波纹管的凹凸结构增加了冷热流体的接触面积,相同换热能力下,能够缩短换热管长度。 3.3结垢性能
流体流经波纹管的变截面后,产生小漩涡,不断冲刷边界层,在较低流速下形成湍流状态,污垢不易聚集,阻碍了污垢层的形成。 4.波纹管换热器的热力计算方法 详见波纹管换热器计算书 5.波纹管换热器结构 详见图纸
第19篇:管壳式换热器
目录
一、管壳式换热器概述 ........................2
二、换热管与管板的连接方式及特点 ............2
2.1、焊接 .........................................2 2.
2、胀接 .........................................3 2.3、胀接加焊接 ...................................3 2.3.
1、先胀后焊..............................................3
2.3.2、先焊后胀..............................................4
2.4、胶接加胀接 ...................................4
三、管壳式换热器的主要形式与结构 ............4
3.1、固定管板式换热器 .............................4 3.
2、浮头式换热器 .................................5
四、换热器的主要强度计算(管板) ............6 五.换热器的主要强度计算(圆平板) ...........8
5.1、基于圆平板的强度计算 .........................8 5.
2、基于安置在弹性基础上的圆平板的强度计算 .......9 六.心得体会 ...............................10
一、管壳式换热器概述
管壳式换热器由壳体、传热管束、管板、折流板(挡板)和管箱等部件组成。壳体多为圆筒形,内部装有管束,管束两端固定在管板上。进行换热的冷热两种流体,一种在管内流动,称为管程流体;另一种在管外流动,称为壳程流体。为提高管外流体的传热分系数,通常在壳体内安装若干挡板。挡板可提高壳程流体速度,迫使流体按规定路程多次横向通过管束,增强流体湍流程度。换热管在管板上可按等边三角形或正方形排列。等边三角形排列较紧凑,管外流体湍动程度高,传热分系数大;正方形排列则管外清洗方便,适用于易结垢的流体。又称列管式换热器。是以封闭在壳体中管束的壁面作为传热面的间壁式换热器。这种换热器结构较简单,操作可靠,可用各种结构材料(主要是金属材料)制造,能在高温、高压下使用,是目前应用最广的类型。管壳式换热器具有可靠性高、适应性广等优点,在各工业领域中得到最为广泛的应用。近年来,尽管受到了其他新型换热器的挑战,但反过来也促进了其自身的发展。在换热器向高参数、大型化发展的今天,管壳式换热器仍占主导地位。
二、换热管与管板的连接方式及特点
2.1、焊接
换热管与管板采用焊接连接时,由于对管板加工要求较低,制造工艺简单,有较好的密封性,并且焊接、外观检查、维修都很方便,是目前管壳式换热器中换热管与管板连接应用最为广泛的一种连接方法。在采用焊接连接时,有保证焊接接头密封性及抗拉脱强度的强度焊和仅保证换热管和管板连接密封性的密封焊。对于强度焊其使用性能有所限制,仅适用于振动较小和无间隙腐蚀的场合。 采用焊接连接时,换热管间距离不能太近,否则受热影响,焊缝质量不易得到保证,同时管端应留有一定的距离,以利于减少相互之间的焊接应力。换热管伸出管板的长度要满足规定的要求,以保证其有效的承载能力。在焊接方法上,根据换热管和管板的材质可以采用焊条电弧焊、#$%焊、&’(焊等方法进行焊接。对于换热管与管板间连接要求高的换热器,如设计压力大、设计温度高、温度变化大,以及承受交变载荷的换热器、薄管板换热器等宜采用#$%焊。 常规的焊接连接方法,由于管子与管板孔之间存在间隙,易产生间隙腐蚀和过热,并且焊接接头处产生的热应力也可能造成应力腐蚀和破坏,这些都会使换热器失效。目前在国内核工业、电力工业等行业使用的换热器中,换热管与管板的连接已开始使
用内孔焊接技术,这种连接方法将换热管与管板的端部焊接改为管束内孔焊接,采用全熔透形式,消除了端部焊的缝隙,提高了抗间隙腐蚀和抗应力腐蚀的能力,其抗振动疲劳强度高,能承受高温、高压,焊接接头的力学性能较好;对接头可进行内部无损探伤,焊缝内部质量可得到控制,提高了焊缝的可靠性。但内孔焊接技术装配较难,对焊接技术要求高,制造和检验复杂,并且制造成本相对较高。随着换热器向高温、高压和大型化发展,对其制造质量要求越来越高,内孔焊接技术将会得到更加广泛的应用。
2.2、胀接
胀接是一种传统的换热管与管板的连接方法,利用胀管器械使管板与管子产生弹塑性变形而紧密贴合,形成牢固连接,达到即密封又能抗拉脱的目的。在换热器的制造过程中,胀接适用于无剧烈的振动,无过大的温度变化,无严重的应力腐蚀的场合。目前采用的胀接工艺主要有机械滚胀和液压胀接。机械滚胀胀接不匀,一旦管子与管板连接失效再用胀管来修复十分困难;采用液袋式液压胀接由电脑控制操作,精度较高,并能保证胀接紧密程度均匀一致,连接的可靠性比机械胀接要好。但对加工精度要求严格,对密布的接头要保证\"##$胀接成功也有一定困难,如果失效再胀接修复也较为困难。
2.3、胀接加焊接
当温度和压力较高,且在热变形、热冲击、热腐蚀和流体压力的作用下,换热管与管板连接处极易被破坏,采用胀接或焊接均难以保证连接强度和密封性的要求。目前广泛采用的是胀焊并用的方法。胀接加焊接结构能够有效地阻尼管束振动对焊缝的损伤,可以有效地消除应力腐蚀和间隙腐蚀,提高了接头的抗疲劳性能,从而提高了换热器的使用寿命,比单纯胀接或强度焊具有更高的强度和密封性。对普通的换热器通常采用“贴胀%强度焊”的形式;而使用条件苛刻的换热器则要求采用“强度胀%密封焊”的形式。胀接加焊接按胀接与焊接在工序中的先后次序可分为先胀后焊和先焊后胀两种。
2.3.1、先胀后焊
胀接时使用的润滑油会渗透进入接头间隙,而它们对焊接裂纹、气孔等有很强的敏感性,从而使焊接时产生缺陷的现象更加严重。这些渗透进入间隙的油污很难清除干净,所以采用先胀后焊工艺,不宜采用机械胀接的方式。采用贴胀虽
不耐压,但可以消除管子与管板管孔的间隙,所以能有效的阻尼管束振动到管口的焊接部位。但是采用常规手工或机械控制的胀接方法无法达到均匀的贴胀要求,而采用由电脑控制胀接压力的液袋式胀接方法可方便、均匀地实现贴胀要求。在焊接时,由于高温熔化金属的影响,间隙内气体被加热而急剧膨胀,这些具有高温高压的气体在外泄时对强度胀的密封性能会造成一定的损伤。
2.3.2、先焊后胀
对于先焊后胀工艺,首要的问题是控制管子与管板孔的精度及其配合。当管子与管板管孔的间隙小到一定值后,胀接过程将不至于损伤焊接接头的质量。但是焊口承受剪切力的能力相对较差,所以强度焊时,若控制达不到要求,可能造成过胀失效或胀接对焊接接头的损伤。在制造过程中,换热管的外径与管板管孔之间存在着较大的间隙,且每根换热管的外径与管板管孔间隙沿轴向是不均匀的。当焊接完成后胀接时,管子中心线必须与管板管孔中心线相重合,才能保证接头质量,若间隙较大,由于管子的刚性较大,过大的胀接变形将对焊接接头产生损伤,甚至造成焊口脱焊。
2.4、胶接加胀接
采用胶接和胀接的工艺有助于解决换热器中换热管与管板连接处经常出现的泄漏和渗漏的问题,重要的是根据被胶接件的工作条件正确选择胶接剂。在工艺实施过程中要结合换热器的结构、尺寸选择好工艺参数,主要包括固化压力、固化温度、胀紧力等,并在生产过程中严格进行控制。此工艺简单、易行、可靠,在企业的实际使用中已得到了认可,具有推广价值。
三、管壳式换热器的主要形式与结构
3.1、固定管板式换热器
固定管板式换热器的典型结构如图1.1所示。管束连接在管板上,管板与壳体焊接。其优点是结构简单、紧凑,能承受较高的压力,价格低,管程清洗方便,管子损坏时易于堵管或更换;缺点是当管束与壳体的壁温或材料的线膨胀系数相差较大时,壳体和管束中将产生较大的热应力。这种换热器适用于壳侧介质清洁且不易结垢并能进行清洗,管、壳程两侧温差不大或温差较大但壳侧压力不高的
场合。
为减少热应力,通常在固定管板式换热器中设置柔性元件(如膨胀节、挠性管板等),来吸收热膨胀差。
图1.1固定管板式换热器
1-折流挡板; 2-管束; 3-壳体; 4-封头; 5-接管; 6-管板;
3.2、浮头式换热器
浮头式换热器的典型结构如图1.2所示。两端管板中只有一端与壳体固定,另一端可相对壳体自由移动,称为浮头。浮头由浮动管板、钩圈和浮头端盖组成,是可拆连接,管束可从壳体内抽出。管束与壳体的热变形互不约束,因而不会产生热应力。
浮头式换热器的优点是管间和管内清洗方便,不会产生热应力;但其结构复杂,造价比固定管板式换热器高,设备笨重,材料消耗量大,且浮头端小盖在操作中无法检查,制造时对密封要求较高。适用于壳体和管束之间壁温差较大或壳程介质易结垢的场合。
图1.2浮头式换热器
1-壳盖; 2-固定管板; 3-隔板; 4-浮头钩圈法兰; 5-浮动管板; 6-浮头盖;
四、换热器的主要强度计算(管板)
管板的结构与一般的圆平板有相似之处,但差别亦不小。主要是管板上的开孔和同管板连接在一起的管束对管板强度的影响等。目前一些管板厚度设计公式因对各影响因素考虑不同而有较大差异。根据不同的设计依据,管板厚度的设计公式可概括为下列几类:
①将管板当作受均布载荷的实心圆板,以按弹性理论得到的圆平板最大弯曲应力为主要依据,并加入适当的修正系数以考虑管板开孔削弱和管束的实际支承作用。这种设计方法对管板作了很大简化,因而是一种半经验公式。但由于公式简单,便于运算,同时又有长期使用经验,结果比较安全,因而有些管板厚度设计公式仍以此作为基础。
②将管束当作弹性支承,而管板则作为放置于这弹性基础上的圆平板,然后根据载荷大小、管束的刚度和周边支承情况来确定管板的弯曲应力。由于它比较全面地考虑了管束的支承和温差等影响,因而比较精确,但计算公式较多,计算过程也较繁杂。在大力发展电子计算技术的今天,是一种有效的设计方法。
③取管板上相邻四根管子之间的棱形面积,按弹性理论求此棱形面积在均布压力作用下的最大弯曲应力。由于此法与管板实际受载情况相差甚大,仅用于粗略计算。
4.1
对管板还需进行剪切强度校核。当管板上布管区为圆形时,设最外圈管子中心圆直径为D。,根据外载和剪应力之间的平衡关系:
t1ttd000.309D0P
故
t0.25D0Ptt
式中:[t]t—管板材料在设计温度下的许用剪应力,取[t]t=0.8 [s]t;
t—不包括附加量的管板厚度,t=tc-C。
考虑管板开孔削弱系数为(1-do/to),则管板按剪切强度的计算公式为:
2tD0PD0t 4
式中:to ——管孔中心距,mm;
d。——管子外径,mm;
D。——布管区最外圈管子中心圆直径,mm 当布管区不是圆形时,则D。为布管区外缘管子中心连线所限定的周边当量直径,即:
D0
4A0 L0其中 L。——最外圈管子的中心距分段测量叠加后所形成的布管周长,如图4.2和4.3给出了按典型的三角形和正方形规则布管时的周长L。(图中粗线表示),mm;
A。——周长L。所包围的总面积,mm2。
图4.2三角形布管
图4.3正方形布管
此外,为满足制造工艺要求,管板还须有足够的厚度。胀接时,为保证胀接的可靠性,管板的最小厚度(不包括厚度附加量)按GB151选取。
管子和管板采用焊按连接时,由于焊接可以达到甚至超过管子本身的强度,所以只要管子强度足够,管板最小厚度可不受此限制,而由焊接工艺及管板焊接变形等要求来确定。
管板厚度应同时考虑上述弯曲强度、剪切强度及管板最小厚度三项因素,从中取最大厚度,然后加上厚度附加量
五.换热器的主要强度计算(圆平板)
5.1、基于圆平板的强度计算
管束对管板支承作用的大小随换热器结构形式而异。固定管板式换热器管束对管板的支承作用最为显著,而U形管式换热器的管子对管板不存在支承作用,浮头式和填函式换热器的管束和壳体可以自由变形,仅由于两管板的变形通过管束相互制约而存在支承作用。管板的计算可按受均布载荷的平板考虑,并针对实际存在的管束对管板的不同支承作用,对不同类型的换热器,用不同的结构系数K予以修正。
圆平板在各种不同支承条件下,按板的弯曲强度为依据的管厚tc设计公式的一般形式为:
tcDc
kPtC
将管板简化为圆平板按弯曲强度为依据的管板厚度tc的设计公式与上式非常相似,即:
KDctc2ptC
比较上述两式可以发现:式(2)中的K/2相当于式(1)中的,所以式(2)中的K基本上仍是取决于支承情况的系数。两式中其他各项形式上相同,整体管板=1,但由于管板设计中需考虑开孔及温差影响,因此含义略有差异。
式(2)中:
C ——附加厚度,mm;
Dc——管板计算直径(当用螺栓与法兰连接时,取垫片平均直径;对焊接于壳体上的管板,取壳体内径,如下图1所示),mm;
K ——结构系数,与换热器型式、管板的结构有关,对管子为直管,固定管板与浮动管板K=1.0,对U形管,找相关资料查取;
P ——设计压力(取管程压力pt与壳程压力ps中的较大者),MPa; []t——管板材料在设计温度下的许用应力,MPa。
5.2、基于安置在弹性基础上的圆平板的强度计算
由于管板结构的复杂,影响管板强度的因素很多,所以正确地进行管板强度分析是比较困准、复杂的。现行各国规范的管板厚度计算公式,都是对实际管板作一定的假定简化而得到的近似公式。由于所采用的假定简化各不相同,与真实管板受力状况必然有程度不同的差别,造成在同样条件下用现行的各国规范计算公式算得的厚度差别很大。这些公式尽管形式各异,但其大体上是分别在以下三种基本假设的前提下得出的。
⑴将管板看成为周边支承条件下受均布我荷的圆平板,应用平板理论得出计算公式。考虑到管孔的削弱,再引入经验性的修正系数。如美国TEMA标准,日本工业标准所采用的 简单而实用的公式,但其局限性较大。
⑵将管子当作管板的固定支撑而管板是受管子支撑着的平板。管板的厚度取决于管板上不布管区的范围。如西德AD规范采用的计算公式。实践证明,这种公式适用于各种薄管板的强度校核。
⑶认为管板是弹性基础上受均布载荷的多孔圆板,既考虑到管子的加强作用,又考虑到管孔的削弱作用。因此分析问题比较全面。如英国BS标准推荐的计算公式。
。
六.心得体会
通过这次作业,我知道了换热器结构的复杂与重要性,而且,我知道,在我今后的工作中我会时常和它接触,我工作的内容与它息息相关,所以我要更加努力的学习,学习和我专业有关的更多的内容,丰富自己的知识,更好的学习和理解专业知识。
第20篇:换热器外文翻译
换热器
关键术语
折流板-在管壳式换热器内等间距排布,支撑管束,防止震动,控制流速和流向,增大湍流程度,减少热点。
管箱-安装在管壳式换热器入口侧用于引导多管程换热器管侧流体流动的装置。 冷凝器-用于冷却和冷凝热蒸汽的一种管壳式换热器。
传导-由分子震动引起的通过固体即无空介质的热传递的方式。 对流-在流体中由流体流动引起的热传递方式。 逆流-指两股流束沿着相反方向流动,也称为反流。 错流-指两股流束沿着彼此垂直的方向流动。 压差-进出口之间的压力差;表示为ΔP,或德尔塔p。 温差-进出口之间的温度差;表示为ΔT,或德尔塔t。
固定管板式换热器-用于指管板与壳体刚性固定的管壳式换热器的术语。 浮头-指换热器上介质返回侧管板不与壳体固定,并且设计成当温度升高时可在壳体内伸长(浮动)。
污垢-在如冷却塔和换热器等设备内表面形成的,导致热传递效率降低和堵塞。 釜式再沸器-带有蒸汽分离腔的管壳式换热器,用于蒸馏系统中,为分离轻重组分提供高温,并维持热平衡。
层流-近乎完整的流线型流动,液流层在平行的轨道上流动。
多管程换热器-一种管程流体流过管束(热源)超过一次的管壳式换热器平行流-指两股流束沿着相同的方向流动,例如,管壳式换热器中的管侧流和壳侧流;也称为并流
辐射热传递-热量在热源和接收者之间通过电磁波传输。 再沸器-用于加热曾经沸腾的液体直到液体再次沸腾的换热器。 显热-通过温度的改变能够测量或感觉到的热量。 管壳式换热器-一种有一个圆筒壳环绕着管束的换热器。 壳侧-指管壳式换热器绕管外侧的流道。参见管侧。
热虹吸再沸器-当静态的液体被加热到沸点时会产生自然循环的换热器型式。 管板-管壳式换热器管端通过滚胀、焊接、或者两者并用的方法连接固定在其上的平板。
管侧-指通过管壳式换热器管内的流道,参见壳侧。 湍流-流体在漩涡中随机运动或混合。
换热器的类型 热量传递在工业过程中有非常重要作用。换热器广泛用于过程之间的热量传递,它能够使热流体的热通过热传导或对流的方式传递给冷流体。换热器为此过程提供加热或冷却。各种各样的的换热器被用于化工过程工业中。
在盘管式换热器中,蛇管浸没在水里或向其喷水来进行传热,这种操作方式传热系数较低且需要较大空间,因此它最适用于用较低的热负荷来冷凝蒸汽。 套管式换热器是采用一个管子包含在另一个管子里面的设计,管子可以是光管或外部翅片管。套管换热器通常采用串联使用,壳侧操作压力高至500磅/平方英寸(表压),而管侧5,000磅/平方英寸(表压)。
管壳式换热器有一个圆筒形壳体包在管束外面。流过换热器的流体被称为管侧流体或壳侧流体。换热器内有一系列折流板支撑着管束,用于引导流体流动,增大流速,减少管子震动,保护管子,并产生压力降。管壳式换热器可以分类为单程固定管板式、多程固定管板式、多程浮头式和U型管式。固定管板式换热器(图7.1)的管板与壳体固定。固定管板式换热器适用于最大温差为200°F (93.33°C)的操作。由于热膨胀的存在固定管板式换热器不能超过这个温差值。 它最适合用于冷凝或加热操作。浮头式换热器是为200°F (93.33°C)以上的高温差设计的。操作过程中,一块管板固定而另一块管板在壳体内“浮动”,浮动端未与壳体固定且可以自由膨胀。
再沸器是用于加热曾经沸腾的液体直到液体再次沸腾的换热器。工业上常用的类型有釜式和热虹吸式。
板式换热器主要由若干个金属板片构成,交替排列的金属板片是为冷热交换设计的。两相邻板片的边缘处有垫片,压紧后可达到密封的目的。板式换热器有冷热流体的进口和出口。板片和垫片的四个角孔形成了流体的分配管和汇集管,使冷热流体逆向经过相邻板间的波纹流道空间,该装置最适用于粘性和腐蚀性介质,其传热效率很高。板式换热器结构紧凑且便于清洗,操作温度限制在350到500°F (176.66°C到260°C),其目的是为了保护内部垫片,由于设计要求板式换热器不适合于沸腾和冷凝。工业过程中的大多数液液两相流体的交换都使用该设计。
风冷换热器在操作过程中不需要壳体,工艺管连接在一个进水口和一个可回程的汇流箱中,管子上可能存在翅片管或光管,翅片的作用是推动或拉动外界的空气越过暴露的管子,风冷换热器主要应用于高传热的冷凝操作。 螺旋板式换热器的特点是结构紧凑,该设计使流体在媒介中形成高湍流。同其他换热器一样,螺旋板式换热器有冷热流体的进口和出口,在内表面实现热的交换,螺旋板式换热器还有两个内部腔。
管式换热器的制造商协会通过多种设计的规范标准将换热器进行分类,其中包括美国机械工程师协会(ASME)的结构代码,公差和机械设计: B类,专为通用操作(经济和紧凑设计)
C类,专为适度的服务和通用操作(经济和紧凑设计) R类,专为恶劣的条件下(安全耐久性)
传热和流体流动
传热的方式有热传导,热对流,热辐射(图7.2),在石油化学产品中,炼油厂和实验室的环境中,这些方法需要被充分的理解,在所有的换热器中都能发现热传导和热对流过程的结合。传热的最佳条件是产品受热或冷却有较大的温差(温差越大,传热效果越好),高能量或高的冷却剂流率,较大的换热面积。
图7.2 传热
传导
热传导的热量是通过固体传递的,例如管子,封头,挡板,管板,翅片和壳体。这个过程发生在当分子固体矩阵从热源吸收热量,由于分子在一个固体矩阵并且不能移动,它们开始振动,这时能量就从热的一侧转移到冷的一侧。 热对流
对流是液体中较热部分和较冷部分之间通过循环流动使温度趋于均匀的过程,在液体中分子的运动形成电流,然后再重新分配能量,这个过程将持续进行直到能量分布均匀为止,在一个换热器中,这个过程发生在流体介质彼此接触进行能量交换时。挡板的排列方式和流体的流向将要决定这个对流会发生在换热器的各个部分。 热辐射
热辐射最好的例子是太阳使地球变得温暖,太阳的热量是通过电磁波传递的。热辐射是一个视线的过程,因此发射源和接收源的位置是非常重要的,在热交换器中没有辐射传热过程。 层流和湍流
流体流动的两个主要分类是层流和湍流(图7.3)。层式或流线型流动流体在管内流动时,其质点沿着与管轴平行的方向作平滑直线运动。此类流动的流量很小,有很小的扰动(旋转和涡流)。湍流通常有很大的流速。当流速增加时,层流模式将要改变成扰动模式,湍流是随机的运动或流体的混合。一旦湍流流动开始,分子的运动速度就要加快直到流体统一扰动为止。湍流流动允许液体分子混合使其比层流流动更容易吸收热量。层流流动促进了静电膜的发展,静电膜是一个绝缘体。湍流流动减少了静电膜的厚度,提高了传热率。平行流和串流
换热器可以通过不同的方式连接,最常见的串联和并联(图7.4),串流中(图7.4),在一个多通道的换热器中通过管侧流动排入到第二个换热器中,根据换热器是如何运行的这种排放路线可以被转向到壳程或管程中。导向原则是经过一个换热器的流动在它到第二个换热器之前。在并联流动中工艺工程是在同一时间经过多个换热器。
图7.3 层流和湍流
图7.4 并联和串联流
图7.5换热器的串行流
换热器的有效性
换热器的设计通常要考虑它是如何有效的传递能量,污垢是一个难题,它可能使一个换热器停止传递热量,在持续的运作期间,换热器不能保持清洁。污垢,水锈,和过程中的沉积物的结合使换热器内部的传热受到限制。这些沉积物在壳体壁面存在,抵抗了流体流动,减慢或停止热量的传导。一个换热器的污垢阻力取决于被处理液体的类型,在系统中的数量和悬浮物的类型,对换热器的热分解,和液流的流速和温度。增加流速或降低温度可以使污垢减少,通过检查管程内外的压力,壳程内外压力可以识别污垢。这些数据常被用来计算压差或计算管段阻力损失,进口,出口的压差是不同的,作为管段阻力损失或腐蚀和侵蚀是在热交换中存在的另一个问题,化学制品,热量,流体流动和时间会磨损换热器的内部结构。化学抑制剂被添加来防止腐蚀和结垢。这些抑制剂用来减轻腐蚀,藻类生长和矿物质的沉积。 套管换热器
套管换热器是一个简单的传热装置设计,套管换热器的管内部还有一根管子(图7.6)。外部管道作为壳程,内管作为管程,冷热流体能在同一个方向流动(并联流动),或相反方向流动(逆流或对流)。
流动方向通常是相反的,因为这样传热效率高,此效率是由于扰动,相碰撞的颗粒,相反的气流引起的。即使两个液体流从未彼此直接接触,这两个热能量流(冷和热)没有相互遇到。在每个管道内气流的对流混合散发热量。
图7.6 套管换热器
在一个平行流式换热器中,单相流的出口温度接近另一单相流的出口温度,在一个两相逆流换热器中,一种单相流的出口温度接近于另一单相流的进口温度,因为降低的温差小在平行流式换热器中只能进行少量的能量传递,静电膜对管道内热量交换产生限制,就如隔热屏障。
接近管子的液体是热的,远离管子的液体是冷的,任何类型的湍流效应将会打破静态膜和传递能量涡流室周围的一切,平行流不能产生湍流的漩涡。
套管换热器的系统局限性是其可以处理流率,最有代表性的是套管换热器的流率是很小的,低流率有利于层流流动。 夹套式换热器
夹套式换热器通常被使用于化工行业(图7.7),夹套式换热器有两种基本模式:套管和多管设计,夹套式换热器的规定壳程压力是500磅/平方英寸(表压),管程压力是5000磅/平方英寸(表压)。此类换热器得名于其不同寻常的发夹式形状,套管设计是管内部还有一根管子,翅片添加在管子外部可以增加热传递。
这个发夹类似于管壳式换热器,拉伸和弯曲成一个发夹。这个发夹设计有几个优点和缺点:它最大的优点是由于U型管的形状使其热膨胀系数很高, 它的翅片设计同时有要求流体有一个较低的传热系数,管侧有很高的压力。此外它很容易安装和清洗,其模块化的设计很容易增加节段;或更换部件物美价廉,供应充足。其缺点是并不像管壳式换热器成本效益低并且它需要特殊的垫圈。
图7.7 夹套式换热器
管壳式换热器
管壳式换热器是在工业中最常见的一种换热器。管壳式换热器适用于高流量,连续操作的场合,根据流程和需要的传热量管子的排列方式可以发生改变, 当管侧流或封头内流体进入到换热器中时两流体彼此平行流动。管程内有一种流体,壳程内有另一种流体流动。热量通过管壁传递给冷流体,热传递的发生首先是热传导,其次是热对流。图7.8显示的是一个单程固定封头式换热器。 流体流进和流出的交换器是针对特定于的液体蒸汽。在系统中液体从底部装置流动到顶部以减少或消除受到限制的蒸汽。气体从顶部流动到底部消除被堵塞或积累的液体,此标准既适用于管程流动又适合于壳程流动。 板框式换热器
板框式换热器是高传热、高压降装置。它由一系列用压缩螺栓固定的两端板间的垫圈(图 7.20 和 7.21)。平板之间的通道是为压降和湍流流动设计的,以为了完成高的传热效率。板式换热器的 开口通常位于杆端盖处。当热流体进入热通道时将会通过排出口被送进交替的板之间。然后到上面的板子处。当冷流体进入杆端盖处逆流的冷空气通道时。冷流体往上流动到平板上,热流体通过平板向下流动到 。这个薄板将冷热流体进行分离,防止泄露。流体流过板子后进入集管。平板被设计成有一系列交错的格子。热量通过热传导在平板表面进行传热,通过对流进入液体。整个管板流淌冷热流体和像个分隔管
冷热流体在板子的两个相对方向上平行流动。热流体在顶部流经换热器的垫圈。这个安排要考虑压降和湍流流动 当流体流经板子进入汇集箱时。冷流体的冷流体进入板式换热器的底部垫圈,与热流体形成对流。采集头位于换热器的上部。
板框式换热器有以下几个优点和缺点。他们很容易拆卸、清理、分散热量以至于没有热点。板子很容易增加和移动。其他的优点是流体阻力小、污垢小、热效率高。此外,如果垫圈泄露,当泄漏到外面时,很容易更换垫圈。
图7.20 板框式换热器
图7.21 板框式装配
板子也可以防止产品的交叉污染。板框式换热器可以产生与管壳式是换热器相比比较小的大的湍动,大的压降。板框式换热器的缺点是它对高温和高压的限制。垫圈很容易损坏和处理的液体不能兼容。
螺旋式换热器的设计以紧凑同心为特点,能形成高湍流流体(图 7.22)。这种换热器有两个基本类型: (1)两侧螺旋流、(2)横向螺旋流。
第一种类型的螺旋板换热器适用于液液流体进行换热 ,冷凝器,气体冷却器装置。流进换热器的流体是专为逆流操作设计的。水平轴安装使悬浮固体能够进行自动清理。
图7.22 螺旋式换热器
第二种类型的螺旋板换热器适用于冷凝器,气体冷却器、加热器和再沸器装置。垂直安装为高速液体和蒸汽结合和在蒸汽混合侧产生低压降创造了极好的条件。 第二种类型的螺旋板换热器适用于高流量率能抵消低流量率的液液系统 风冷换热器
翅片热风机和风冷换热器传热的的方式不同。风冷换热器提供了一个矩阵结构的平板或翅片管与进口或回流管连接。当空气作为外部的传热介质时要远离管子。翅片的这样多种形式安排是为了形成强制对流,增大传热系数。在强迫气流和诱发气流中翅片被安装管子的上方或下方。管子可以水平和垂直放置。 风冷换热器可的封头可以分类为管型箱,焊接箱,盖板,多歧管。管型箱和焊接箱在每个管子的端板上都有防水塞。这种设计方便逐根管进行清洗,如果泄露可以堵住,再轧制紧固管接头。盖板设计为所有管子提供简易的通道。在盖板和封头连接处要放置垫片。这样多样化的类型是为高压环境设计的。 机械翅片运用多样的驱动程序,在风冷换热器中可以发现普通驱动设置,包括电动机,压缩齿轮,蒸汽涡轮,内燃机,和液压马达。
图7.23 风冷换热器
翅片叶片是由铝和塑料组成的。铝翅片适用于操作温度高于300°华氏温度(148.88°C),而塑料翅片的操作温度被限制在160°F和180°F之间(71.11°C, 82.22°C)。
风冷换热器经常被应用于空气压缩装置中,在再循环系统中用于冷凝操作。这种类型的换热设备为周围空气与排除的工艺流体之间提供了一个40°F (4.44°C)温度差。比水冷换热器构造更简单,维修更便宜。风冷换热器没有与水相关的污染和腐蚀问题。他们有低廉的经营成本和优越的高温移除(200°F or 93.33°C以上)。
他们的缺点是对于液体或冷凝设备有高的流体出口温度,高的设备成本费的限制。此外,他们在额定情况下容易失火或爆炸。
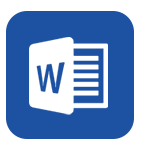