互利共赢的供应商质量控制
前言
近年来,随着对供应链的重视,供应商管理正逐渐成为企业和学术界的关注对象,IS09000族标准以及QS 9000标准都对供应商的管理提出了相应的要求,与供应商管理有关的研究成果正逐渐增多,一些软件巨头也推出了供应商关系管理的软件,但是在这些研究成果和应用软件中,涉及到的供应商质量控制的内容只是一些最基本的要求,而供应商质量控制恰恰是供应商管理的最基本、最重要的内容。另一方而,质量管理界对质量控制的研究取得了大量的成果,遗憾的是这些成果大多依然局限于企业的内部控制,仅仅研究从企业内部各环节如何改善产品的质量,而基于供应链的角度来研究质量控制的成果尚不多见。因此,系统地研究经济全球化形势下供应商质量控制的理论与方法,将有助于推动我国企业产品质量的快速提高和供应链竞争优势的形成与巩固。
1、质量与企业共存
质量一直是一个随着时代的变化而不断变化的概念,人们对质量的认识也往往因关注点不同而有所不同。如,早在1908年,通用汽车公司的工程师们在皇家汽车俱乐部会员们的面前拆解了3辆凯迪拉克轿车,并把这些零件混在一起,而后从中选择零件重新组装成车,然后驾车绝尘而去。这令在场的会员极为震惊,认为凯迪拉克车质量之高令人惊叹。显然在当时,汽车零件具有互换性是一种了不起的质量特性,这也是福特公司的N型车和T型车取得辉煌成功的重要原因。时至今日,即使农用三轮车的零部件也具有极高的互换性,零部件的标准化和互换性已经是理所当然的事情,不再是吸引顾客的重要质量特性。可见质量的内涵是不断变化的。那么究竟什么是质量呢? (1)市场竟争就是企业间对“顾客”的争夺,在日益激烈的“顾客”争夺战中,质量、价格、交付 (交付日期、方式和手段)和服务是企业常用的四个法宝,其中质量是根本,离开质量其他三项将变得毫无意义,因此可以说质量己成为市场竞争的焦点。它反映了产品是否能够反映顾客需求、能否满足顾客需求,从面决定了产品的市场前途。有鉴于此,质量己成为一项全球性运动,世界上所有优秀企业无一不把质量作为企业战略的关键内容,从战略的角度来规划质量。
(2)对于企业经营者来说,认识到质量对企业的重要意义只是经营企业的第一步,重要的是如何利用科学的方法来保证产品和服务的质量,使顾客满意,来保证过程和工作的质量来获互利共炭的供应商质量控制得良好的业绩。
众所周知,企业管理是社会生产力发展到一定程度的历史产物,质量管理作为企业管理的组成部分,同样也是社会发展的客观要求,特别是顾客处于主导地位的今天,要使顾客满意,就必须有过硬的产品质量和服务质量,这就要求企业积极推行先进的质量管理理论与方法,不断进行质量管理创新。
2、企业与供应商质量控制
随着生产社会化的不断发展,企业的生产活动分工越来越细,专业化程度越来越强,促使生产技术水平越来越高,产品质量得到大幅度改善。通常,某一产品不可能由一个企业从最初的原材料开始加工直至形成顾客最终使用的产品,往往是通过多个企业分工协作来完成。另外,先进生产方式的广泛应用,如准时生产、敏捷制造、零库存等,使企业与供应商的关系愈加紧密,企业与供应商的关系也由单纯的买卖关系向互利共底的合作关系演变。
ISO 9000族标准自1987年诞生以来受到了世界各国的一致追捧,全球约50多万家企业通过ISO 9001质量管理体系认证足以说明这套管理标准在引领国际管理潮流方面的巨大成功。在备受企业欢迎的新版标准ISO 9000:2000中,互利的供应商关系被作为八项质量管理原则之一,充分体现了供应商关系管理在企业经营实践中的作用和价值。企业要贯彻这一原则,就必须从思l 想上认识到供应商的重要性,重视与供应商良好关系的培育,并采取有力措施与之建立一种互利共赢的合作性关系。
3、供应商选择
选择合适的供应商是对供应商进行质量控制最有效手段,如果供应商选择不当,无论后续的控制方法多么先进、控制手段多么严格,都只能起到事倍功半的效果。因此要对供应商进行质量控制首先必须科学合理地选择供应商。
(1)企业在生产经营过程中,所需要的原材料和零部件不可能都由自己生产提供,决定其中哪些应由供应商提供不是一个简单的买不买的问题,因为这涉及企业的业务流程,甚至涉及到企业与供应商之间的业务流程再造,属于企业战略层次的问题。因而对零部件的自产和外购的选择必须综合考虑企业的经营环境、企业自身实际情况以及供应商的总体情况。
1)经营环境分析
企业对于零部件自产还是外购的决策需要建立在对其经营环境的准确分析和把握的基础之上。企业所在行业的整体状况与发展态势、国家宏观经济形势、企业产品的社会需求现状及未来预侧等因素都会影响到企业产品的产销量。而预期的企业产销量是企业进行各项决策如互利共赢的供应商质量控制投资规模、设备配置的主要依据,也是企业零部件自产与外购决策的重要依据。另外,竞争对手的零部件自产与外购情况也是企业进行决策的重要参考依据。
2)市场供应情况
零部件的社会供应状况也是企业决定自产还是外购的重要依据。企业与其供应商的关系的实质就是相互依存的关系,正如一家势力雄厚、规模巨大的企业会吸引很多供应商在其周围投资设厂一样,具有完善配套供应商的区域也常常吸引大的企业甚至跨国公司前来投资办厂。某种零部件的社会供应能力、价格、质量和服务水平在很大程度上影响着企业的自产与外购决策。因此,企业应全面了解其产品中零部件的社会供应情况,注意从互联网上、展览会、供应商来信等渠道收集供应商的企业介绍、产品样本、获奖证书、代理商授权书、营业执照、产品实物质量水平以及市场行情等方面的信息。然后,按照供应商提供物资种类,可分别建立原材料、零部件、包装材料等不同类别的潜在供应商档案。
(2)供应商的检测设备是供应商赖以测量、分析和改进的基础条件。如果供应商不具备必要的检测手段,就无法提供真实准确的质量数据,供应商的质量控制就如空中楼阁。所以,在初选供应商时,了解供应商的检测设备的配备情况和先进程度同样是十分必要的。
(3)过程能力指数和过程性能指数是反映供应商生产过程质量保证能力的两个重要参数。过程能力指数反映供应商短期的过程能力满足公差要求的程度。过程性能指数反映供应商长期的过程能力满足公差要求的程度。供应商是否进行过程能力指数和过程性能指数的计算分析,可以在一定程度上反映其是否在生产过程中进行了预防控制。过程能力指数和过程性能指数的变化则可以反映供应商的质量保证能力和质量改进潜力的大小,在很大程度上反映供应商的实力和管理水平。因此,调查供应商的过程能力指数和过程性能指数是选择供应商的重要依据。
4、供应商的质量控制
质量管理的一项重要原则是“过程方法”,企业为了有效运作,必须识别并管理许多相互关联的过程,特别是这些过程之间的相互作用。供应商是过程管理的源头之一,是过程输入的重要因素,因而,供应商提供的产品质量如何,对于企业的过程质量、体系质量和产品质量具有举足轻重的作用。
(1)产品开发设计阶段,根据不同产品的不同要求,在产品开发设计建议书或产品设计开发任务书中提出先行试验项目和课题,有针对性地为采用新原理、新结构、新材料、新工艺,进行先行试验,为了确保试验的效果和以后批量生产的需要,这一阶段的一项重要工作就是对供应商进行初步控制,确保在新产品设计的各个阶段以及批量生产时,都能够有适合新产品或新服务需要的合格供应商。
l (2)企业在批量生产过程中,对供应商的质量控制主要包括监控供应商的过程能力指数和过程性能指数、监控供应商的测量系统、审核供应商的质量管理体系、进货质量检验、推动供应商的质量改进、以及来自供应商的不合格品的处置和质量问题的解决等活动。
1)批量生产阶段,供应商提供的产品或服务的质量直接决定了企业向顾客提供的产品或服务的质量特性,企业在供应商合作的过程中,应监控供应商的质量保证能力的变化,为了使监控有效,企业应就此与供应商达成一致,并遵循协商一致的标准和程序进行。监控的目的一般有两个,一是防止供应商的质量保证能力出现下降的情况,确保最终产品或服务的质量,实现顾客满意;二是与供应商共同发现改进的机会,寻找改进的切人点,在更高层次上创造价值。
由于在批量生产阶段供应商大批量连续供货,采购产品的质量、价格、供货的及时性等对企业产品的质量和企业实现其经营方针、目标都有十分重要的作用,为了更加科学地评价和选择供应商,这一阶段的供应商评价应尽量采用定量分析的方法。根据产品和服务的不同,定量分折的方法也不同,以下简单介绍常用的过程能力分析、测量系统分析、质量管理体系评价、水平对比法和优秀模式等方法。
①供应商过程能力分析
过程能力是指过程加工质量方面的能力,而不是加工数量方面的能力。在批量生产阶段,为了保证批量生产的产品满足顾客的需求和期望,供应商生产过程的稳定性就十分重要了,决定供应商是否有能力稳定地连续提供符合质量要求的产品的众多因素中,供应商的过程能力是一个决定性的因素。因为当供应商的过程能力不足时,供应商提供合格产品只是个良好的愿望,即便是加大检验力度,也只能是在短期内有效,难以持续。所以,对过程能力不足,短期改进无望的供应商,应该停止合作。
②供应商测量系统分析
企业对供应商的质量控制,包括对供应商的选择、评价和控制,都离不开数据和对数据的分析,缺少足够的数据,仅仅靠经验和直觉对供应商进行选择和评价,其风险是不言而喻的。对供应商的评价和控制所使用的数据大多是由测量提供的,如果测量数据失真或误差很大,都会导致采购行为的缺陷或失败。因此,在批量生产阶段,为了确保采购的质量,应该对供应商的测量系统进行监控。
2)与供应商的沟通
与供应商沟通的方式是多种多样的,但是这些方式的目的是一致的,企业和供应商共同关注顾客,建立企业和供应商共同满意的融洽的合作伙伴关系,共同对产品和服务进行持续的改进,以便及时、有效地适应市场的变化。满足顾客的需求和期望,实现企业和供应商共同的价值,共同追求并实现卓越。
(3)不合格品的判定、分析和处置
虽然有了以上各种控制措施,但是不合格品的出现仍然是正常现象,除单件或少数几件产品、安全性要求较高的产品等少数产品以外,在许多情况下不合格品的出现是难以完全避免的。这时候就要根据不合格的性质、对最终产品的影响程度、供应商的信誉等因素对不合格品进行必要的评审,然后采取适当的措施处置不合格品,以防止不合格品的非预期使用或交付当出现不合格品以后,要分析产生不合格的囚素,采取纠正和预防措施。防止不合格的再次发生。对由于异常因素发生的不合格品,供应商要采取相应的措施,消除这些异常因素。
1)一致的技术标准和抽样方案
使用、提出和制定规格的部门必须合理地描述出拟采购的产品是什么,以便使供应商得到准确的理解,使采购人员能够准确地采购所需的产品。根据ISO 9001:2000标准的要求和企业的实际情况,这些技术标准一般是由设计、采购、管理、生产等部门制定,但在采购的实施时,采购部门要使用这些标准,因此.采购部门从一开始就应该介入这些标准的策划、起草和修订,否则,一旦这此标准止式发布实施,可能会使采购部门处于被动的地位,给采购工作带来麻烦。
l
2)不合格品的质量责任
当采购产品出现超出技术规范规定界限的不合格时,企业和供应商应在协商的原则下确定不合格产品的原因、商定解决产品质量的办法,并据此进行改进。当企业与供应商对不合格的认定分歧很大,双方无法协商解决,需要诉诸法律时,不合格产品质量责任的性质就发生了变化,必要时不排除需要追究某一方的法律责任。所以对产品技术要求和其他采购信息,企业一定要表述清除、完整、准确,并经过授权人员评审后再与供应商沟通,在与供应商达成一致的前提下再签订合同,并妥善保存采购、检验文件和记录。
3)不合格品的控制
当出现不合格品,如果是抽样检验,且不合格品的数量小于或等于合格判定数时,这种不合格属于正常现象,只要将不合格品更换成合格品,就应该判定交验批合格,企业应根据文件要求接受该批产品。这些个别的不合格产品可能属于正常波动引起的不合格,可以不必专门查找原因供应商可以作为止常的质量改进,逐步提高过程能力,减少这些不合格。
5、供应商的契约化控制
为了保证顾客对产品与服务的满意,企业必须对产品形成的全过程进行严格的管理与控制。为了使整个供应链中每一个环节,即合作伙伴,明确他们对质量的责任与义务,并保证实现,伙伴之间必须以契约的形式形成承诺,并按照承诺的内容测量质量与服务。这里所说的契约仅指得到相关方签署的,规定供应链各环节之间质量责任的文件化条款,包括合同和协议。严肃合理的契约对双方不仅起到可靠的约束作用,而且可以有效保护双方的利益。
(1)保证契约内容与标准、法规和企业制度的统一性
契约可引用或借鉴既定的法律、法规或规章制度、标准等。如可规定进厂检验抽样标准执行GB2828 抽样标准;电器产品安全性能必须符合GB4706等。如发现有与相关法律、法规、标准、制度不一致之处,发现方应及时提出修改。如在执行过程中发现不一致,发现方应及时通知不知情方,并按符合法律、法规、标准、制度的方式执行。
(2) 契约内容应实际有效
起草与签署契约时,必须考虑产品形成过程中的实际情况,考虑契约执行的可操作性。有些协议在制定时可能需要考虑的因素较多,规定需较为详细,但如果过于繁琐,缺乏可操作性,反而起不到应有的作用。例如,某公司需从供应商采购大量的加工轴承用的钢材。由于轴承对材料要求较严,加工精度较高,公司为保证质量,在协议中要求对方对每一批材料进行化学成分分析和物理性能试验。供应商如果引进整套试验设备,势必耗费大量的成本,同时要配备相应的技术人员。如果不增加资源配置,那么每次都要送社会检验机构检验,支付昂贵的试验费用。象这种契约,如果供应商仔细审验的话,他就会考虑进行利润-成本-风险分析,在价格上提高要求。这种协议履行起来就有较大难度,同时也容易引起一些不必要的纠纷,不利于供应链的稳固和质量价值链的形成。
(3) 契约应明确双方的权利和责任,鼓励供应商的持续改进与创新
契约中应明确供需双方的权利和责任,同时也应规定必要的奖惩性条款,一方面约束供应商的质量行为,另一方面鼓励供应商不断提高产品质量。对供应商的奖惩包括两种类型。其一是因质量责任的划分而产生的奖惩;其二是根据业绩考核而产生的奖惩。在实际的操作中,适当的奖励可能会产生意想不到的管理效果。某供应商的产品在顾客手中出现了较为严重的质量问题,企业立即通知供应商分析原因,采取整改措施。供应商接通知后,积极地派人到现场进行协助调查和分析,使问题很快得到了解决。本来根据双方的协议规定,该供应商除应承担全部质量责任外,还应承担数额不菲的罚款。但企业考虑到该供应商是自己的重要供应商,一直合作很顺利,质量稳定,决定奖励供应商对质量问题的快速反应和积极的态度,免除了所有的罚款。结果年终评定发现该供应商的产品合格率比上年有较大幅度的提高。
(4)契约的内容应公正、公平
l 契约应是经过双方充分协商达成的共识,不应只是一方对另一方的宣言或要求,内容要经过双方认可和确认。另外,契约内容应涵盖从产品开发、试制、检验、包装运送到不合格品处理、售后服务的全过程,所以契约可包含多个层次,如供货合同、质量保证协议、技术协议、售后服务协议等。
6、供应商的业绩评定与动态管理
供应商作为产品实现的重要资源之一必然要讲求其有效性。2000版ISO9000标准就把管理体系的有效性作为一个重点来考虑,因此对供应商进行业绩评定十分重要,它是进行动态管理、择选劣汰的依据。
(1)评定方法
按照采购要求,对关键材料、主要材料和次要材料定期进行质量缺陷分级评定。规定关键参数的缺陷分记为3分,主要缺陷为2分,次要缺陷为1分。一批材料中根据规定的抽样方法最大分数为6分。质量工程师据此对供应商进行等级评定,并向供应商发出通知。这种方法操作简单,节省人力,但评价指标偏少。
(2) 动态管理
根据业绩记录,定期对所有供应商进行动态分级评定。将所有供应商划分为A、B、C、D四级,根据材料价值、质量要求、加工难易程度、社会供应状况等因素确定供应商定点个数。定点个数为1的A类供应商,订单分配为100%;定点个数为1的B类供应商,订单分配为100%,但需开发该材料的新供应商;定点个数为2的A、B类供应商分别分配订单60%和40%;定点个数为3的A、B、C类供应商分别分配订单55%、30%和15%;D类供应商应被淘汰。这种分级评定与管理将供货订单与供应商绩效、材料分级结合起来,使订单的分配比较科学合理。当然,这种方法对企业管理的整体水平也提出了很高的要求。
l Mutually beneficial supplier quality control Preface In recent years, with the emphasis on the supply chain, vendor management is becoming a busine and academia about the object, IS09000 standards QS 9000 family of standards and vendor management are all put forward the corresponding requirements, and supplier management-related Research is gradually increased, the software giant also introduced a number of supplier relationship management software, but in these research results and application software, related to the quality control of the content provider is only the most basic requirements, and supplier quality control Supplier management is precisely the most fundamental and important content.The other party, quality management, quality control sector made a lot of research results, unfortunately, most of these results is still limited to the company\'s internal controls, only the link from the internal study how to improve product quality, and based on supply chain Point of view of the results of quality control is still rare.Therefore, the systematic study of the economic globalization supplier quality control theories and methods, will help promote China\'s rapid increase in product quality and supply chain formation and consolidation of competitive advantage.
1、Quality and corporate co-existence Quality has been a change with the times changing the concept of people\'s understanding of quality is often due to concerns vary.For example, as early as 1908, GM engineers at the Royal Automobile Club members in front of dismantling the three Cadillac cars, and these components mixed together, and then choose the parts re-aembled into a car, then driving Pull away.This makes the presence of members of a very shocked that the high quality Cadillac amazing.Obviously at the time, with interchangeable parts is a great quality features, this is Ford\'s Model N Model T achieved brilliant succe and an important reason.Today, even if the farm also has a very high tricycle parts interchangeability, standardization and interchangeability of parts is already a matter of course, is no longer an important quality characteristics to attract customers.Visible quality content is constantly changing.So what is the quality? (1)Market competition among enterprises is the \"customer \" of the competition, in the increasingly fierce \"customers\" in the battle, quality, price, delivery (delivery dates, means and methods) and the service is commonly used in the four magic, where quality is Simply leave the quality of the other three will become meaningle, it can be said the quality has become the focus of market competition.It reflects whether a product can reflect the customer needs, can meet customer needs, from the surface determines the future of products in the market.In view of this, quality has become a global movement, all the world\'s best companies are all the quality as a key element of corporate strategy, from a strategic perspective to planning quality.
(2)For busine operators, it recognizes the importance of quality on busine enterprises is the first step, it is important how to use scientific methods to ensure l product and service quality, customer satisfaction, to ensure the quality of the proce and work to Be mutually beneficial and win-win supplier quality control with good results.As we all know, corporate management is the development of social productive forces to a certain degree of historical product, quality management as an integral part of busine management, is also the objective requirement of social development, especially in today\'s dominant customer, make customer satisfaction, there must be strong Product quality and service quality, which requires enterprises to actively implement the advanced quality management theories and methods of continuous quality management innovation.
2、Quality control of enterprises and suppliers With the continuous development of socialization of production, the production activities of the division of labor is getting smaller, growing degree of specialization, prompting increasing the level of production technology, product quality has been greatly improved.Typically, a product can not be from a busine started from the initial proceing of raw materials until the formation of the product end-use customers, often through multiple corporate division of labor to complete.In addition, the extensive application of advanced production methods, such as JIT, agile manufacturing, zero inventory, so that the relationship between enterprises and suppliers increasingly close relationship between companies and suppliers are from a simple buyer-seller relationship to the mutual cooperation between the end of a total evolution of .ISO 9000 family of standards since its inception in 1987 has been the consistent pursuit of the world, more than 50 million businees around the world through the ISO 9001 quality management system certification standards sufficient to explain this management trend in the leading international management\'s great succe.Welcome to the new busine in much the standard ISO 9000:2000, the mutually beneficial supplier relationships is one of eight quality management principles as a fully embodied the supplier relationship management practice in the busine role and value.Enterprises to implement this principle, we must recognize the ideological importance of supplier and attach importance to good relations with suppliers cultivation, and to take effective measures with the establishment of a mutually beneficial and win-win cooperative relations.
3、Vendor Selection Choose the right supplier is a supplier of the most effective means of quality control, supplier selection if improper, no matter how advanced the follow-up control, controls how strict, can only play a le effective results.So to the quality control of suppliers must first be scientific and rational choice of suppliers.(1)Enterprises in the production proce, raw materials and parts needed for production can not be provided by their own to decide which of them should be suppliers of buying a not a simple iue because it involves busine procees, even involving Between enterprises and suppliers to the busine proce reengineering, strategic-level iues in enterprises.Thus parts of the self-produced and purchased options to be taken into account the busine environment, the l actual situation of their own and suppliers in general.1)Analysis of busine environment Enterprises are outsourcing parts production for the decision or need to create in the accurate analysis of their operating environment and grasp basis.The overall position of companies and the industry development trend, the national macroeconomic situation, the social needs of enterprise products for predicting the future status and other factors will affect production and sales of enterprise products.Anticipated production and sales of enterprise decision-making enterprise for the mutual benefit of suppliers, such as quality control of the scale of investment, mainly based on device configuration, but also busine and outsourcing parts production for an important basis for decision making.In addition, competitors and the outsourcing of parts production for corporate decision-making situation is an important reference.2)Market supply Supply situation in parts of the social enterprise decision is an important basis for self-produced or purchased.Busine relationships with its suppliers is the eence of interdependence, as a strong power, large-scale enterprises will attract many suppliers set up plants in their surroundings, like, a complete set of regional suppliers often attract large enterprises and even Multinational companies to invest and set up factories.Some parts of the social supply capacity, price, quality and service levels of the enterprise is largely self-produced and outsourcing decisions.Therefore, enterprises should fully understand the social components of their products, availability, attention from the Internet, exhibitions, suppliers and other channels to collect letters from suppliers of busine introduction, product samples, award certificates, power of attorney agents, busine license, Products quality level and market conditions and other information.Then, in accordance with the types of suppliers to provide materials, were established to raw materials, components, packaging materials, such as different types of potential suppliers file.
(2)Testing equipment supplier which the supplier measurement, analysis and improvement of basic conditions.If the supplier does not have the neceary means of detection, we can not provide true and accurate quality data, quality control of suppliers like castles in the air.Therefore, in the primary suppliers to understand the supplier\'s testing equipment and advanced levels with the situation is also very neceary.(3)Proce capability index and proce performance index of the production proce is reflected in supplier quality aurance capabilities of the two important parameters.Proce capability index reflects the ability of suppliers to meet short-term course of the degree of tolerance requirements.Proce performance index reflects the ability of suppliers to meet long-term proce requirements of the degree of tolerance.Does the supplier to proce capability index and proce performance index calculation and analysis, to a certain extent, reflect the production proce is conducted in the prevention and control.Proce capability index and the change proce performance index can reflect the ability of the supplier quality aurance and quality improvement of the size of the potential, l largely reflecting the strength and supplier management.Therefore, the investigation supplier proce capability index and proce performance index is an important basis for selection of suppliers.
4、Supplier Quality Control Quality management is an important principle is the \"proce approach\", enterprises in order to function effectively, must identify and manage the many interrelated procees, especially the interaction between these procees.Supplier is one of the sources of proce management is an important factor in the proce input, and thus, the quality of suppliers to provide products for busine proce quality, system quality and product quality has a pivotal role.(1)Product development and design stage, according to the different requirements of different products, product development, design or product design and development of proposals put forward in the book first pilot project tasks and iues, targeted for the introduction of new principles, new structures, new materials, new procees, The first test, in order to ensure test results and future production needs, an important task at this stage is that of the suppliers under control, to ensure that all stages of new product design and ma production, are to have fit the new Product or service needs of qualified suppliers.(2)Enterprises in the production proce, quality control of suppliers include monitoring supplier proce capability and proce performance index, monitor supplier measurement system, the audit supplier quality management system, purchase quality inspection, and promote supplier Quality improvement, and defective products from suppliers, disposal and quality of problem solving and other activities.1)Production stage, suppliers of products or services directly determine the quality of the busine to provide customers with the quality of the product or service features, enterprises in the proce of suppliers, vendors should monitor changes in the quality aurance capabilities, in order to Monitoring effective, enterprises should reach agreement on this with the supplier, and follow the agreed standards and procedures.The purpose of monitoring generally have two, one supplier\'s quality aurance to prevent the decline in capacity, to ensure that the quality of the final product or service to achieve customer satisfaction; the second is working with vendors to find opportunities for improvement, looking for people to improve the cutting Point, at a higher level to create value.Production stage due to high volume supplier of continuous availability, purchase products, quality, price, availability, timeline and other quality products for enterprises and businees realize their operating principles, and target has a very important role, in order to more scientific Evaluation and selection of suppliers, supplier evaluation at this stage should be a quantitative analysis.According to the different products and services, quantitative differences in methods of folding points, the following brief analysis of commonly used proce capability, measurement system analysis, quality management system aement, comparing the level of law and good models and other methods.①Supplier proce capability analysis l Proce capability refers to the ability of the proce of proceing quality, rather than the number of proceing capacity.In the production stage, in order to ensure ma production of products to meet customer needs and expectations, supplier stability of the production proce is very important to determine whether the supplier has ability to consistently meet the quality requirements to provide continuous product of many factors, Supplier proce capability is a decisive factor.Because when the supplier\'s proce capability is insufficient, to provide qualified products supplier is only a good will, even if efforts to increase testing, can only be effective in the short term, unsustainable.Therefore, lack of proce capability, supplier of short-term improvement of hopelene, should stop cooperation.②Measurement System Analysis provider Company quality control of suppliers, including supplier selection, evaluation and control, are inseparable from the data and analysis of the data, the lack of sufficient data, experience and intuition alone the supplier selection and evaluation of the risk Is self-evident.Supplier evaluation and control of the data used are mostly provided by the measure, if the measurement error of the data distortion or large, will lead to purchases defect or failure.Therefore, in the ma production stage, in order to ensure the quality of procurement, suppliers should monitor the measurement system.2)Communication with suppliers Way of communicating with suppliers are diverse, but the purpose of these approaches is consistent, enterprise customers and suppliers of common concern, the establishment of enterprises and suppliers satisfaction of harmonious cooperation partnership for sustainable products and services Improvements in order to timely and effectively adapt to market changes.Meet customer needs and expectations of enterprises and suppliers of common values and common aspirations and achieve excellence.(3)Determination of nonconforming product, analysis and disposal of Even with these various control measures, but there is still substandard products is a normal phenomenon, in addition to single or a few pieces of products, products with higher security requirements and a few other products, in many cases, the emergence of non-conforming product Is hardly avoidable.This time will be based on the nature of failure, the degree of influence on the final product, the supplier\'s reputation and other factors neceary for the aement of nonconforming product, and then take appropriate measures to deal with nonconforming product to prevent unintended non-conforming product When a nonconforming use or delivery of goods after the prisoners failed to analyze the factors have to take corrective and preventive measures.To prevent the failure from happening again.Anomalies occur due to defective products, suppliers to take appropriate measures to eliminate these abnormal factors.1)Consistent technical standards and sampling plan Use, and develop specifications proposed department must reasonably describe what the products to be purchased, to enable vendors to get an accurate understanding of the procurement staff to purchase the required products l accurately.According to ISO 9001:2000 standards and the actual situation, the technical standard is normally provided by the design, procurement, management, production and other departments to develop, but in the implementation of the procurement, the procurement departments should use these standards, so.Procurement from Beginning, these standards should be involved in the planning, drafting and revision, otherwise, if only for publish this implementation of this standard, may make the purchasing department in a paive position, to the procurement of trouble.2)Responsibility for substandard quality of goods When purchasing products in exce of unqualified technical specification limits, companies and suppliers should be identified in consultation with substandard products under the principle of reason, the agreed approach to solve product quality and make improvements accordingly.When the enterprise failed and suppliers found great differences on the two sides can not be resolved through consultation, need to resort to the law, the substandard nature of the responsibility of product quality changes, if neceary, do not rule out the need to pursue a party\'s legal responsibility.Therefore, the product requirements and other procurement information, enterprises must expre clear, complete, accurate, and after review by authorized personnel to communicate with suppliers, in agreement with the supplier under the premise of re-signing of the contract, and retain procurement, Inspection documents and records.3)Control of nonconforming product When nonconforming product, if it is sampling, and the number of unqualified or le qualified to determine the number, this failure is a normal phenomenon, as long as the replacement of defective products into the qualified product, you should determine the approved inspection Qualified enterprises should be based on documents required to accept the batch.The failure of these individual products may be part of the normal fluctuations of the failure, you can not find the cause of the specialized supplier of quality can be improved as the only constant, and gradually improve the proce capability and reduce the failure.
5、Control of contract suppliers In order to ensure customer satisfaction with products and services, companies must form the whole proce of product management and strict control.In order to make the whole supply chain, every link, that is, partners, specifically the quality of their responsibilities and obligations, and to ensure implementation of the contract between the partners must be in the form of the formation of commitment, and commitment to the contents of the measure in accordance with quality and service.Mentioned here refers only to the contract signed by the relevant parties to provide the quality of the supply chain responsibilities between the terms of documentation, including contracts and agreements.Serious and reasonable contract for both sides not only play the role of reliable constraints, and can effectively protect the interests of both.(1)Content and standards to ensure that contracts, regulations, and the unity of enterprise system l Contract may be quoted or learn from the established laws, regulations or rules and regulations, standards.Such as to require incoming inspection standards GB2828 random sample of standard; electrical products must comply with GB4706 and other security features.If found with the relevant laws, regulations, standards, system inconsistencies found shall timely changes.If found inconsistencies in the implementation proce, that party shall promptly notify the innocent party, according to compliance with laws, regulations, standards, institutional manner.(2)Content of the contract should be practical and effective Drafting and signing of contract, we must consider the actual proce of product formation, considering the operability of contract enforcement.Some protocols may need to consider in the development of many factors that need more detailed provisions, but if too cumbersome, the lack of maneuverability, but would not achieve its proper role.For example, a company should purchase from a supplier of proceing a large number of bearing steel.As bearing on the material requirements more stringent, higher precision, quality aurance company, ask for in the agreement for each batch of material chemical composition analysis and physical properties.If the introduction of full set of suppliers of test equipment, is bound to spend a lot of cost, while equipped with the appropriate technical staff.If you do not increase the allocation of resources, so each must be sent to community inspection institutions, to pay for expensive testing costs.Like this contract, if the supplier careful testing, he will consider the profitsrisk analysis, the price increase request.Such an agreement more difficult to perform up there, but also easily lead to unneceary disputes, is not conducive to the stability and quality of supply chain value chain formation.(3)Contract should be clear rights and responsibilities of both parties, to encourage suppliers to continuous improvement and innovation Contract should be clear rights and responsibilities of both supply and demand, but also should provide the neceary incentive provisions, on the one hand the quality of binding behavior of suppliers, on the other hand encourage suppliers to continuously improve product quality.Incentive of suppliers, including two types.One is the division of responsibility for the quality of the resulting rewards and punishments; the other is based on performance appraisal and reward and punishment generated.In the actual operation, the appropriate reward management may produce unexpected results.A supplier of the product in the hands of customers appeared more serious quality problems, companies immediately notify the supplier of the cause and take corrective measures.Suppliers take notice, sent to the site to actively aist in the investigation and analysis of the problem was quickly resolved.According to the agreement originally provided that the supplier should bear all the responsibility for quality in addition, we must also bear the amount of money in fines.However, taking into account the supplier companies is their key suppliers, have been working very smoothly, stable quality, decided to reward quality supplier of rapid response and a positive attitude, eliminating all of the fine.Year-end evaluation results found that the rate of qualified products suppliers are more substantial than the increase over the previous year.l (4)The contents of the contract should be fair and equitable Contract should be negotiated through the full consensus of both parties, not just one party against another or request a declaration, content to go through both the recognition and confirmation.In addition, the contract terms should cover product development, trial production, testing, packaging, delivery to non-conforming product proceing, service the whole proce, so the contract can contain multiple levels, such as supply contracts, quality aurance agreements, technology agreements, service Agreement.
6、Supplier performance evaluation and dynamic management Suppliers as an important resource for product realization is bound to emphasize its effectivene.2000 put the ISO9000 standard management system effectivene to consider as a priority, so the aement of supplier performance is important, it is the dynamic management, eliminating the basis by choosing inferior.(1)Evaluation Method Accordance with the procurement requirements of key materials, the main material and secondary materials on a regular basis for quality aement of defect claification.Provisions of sub-critical parameters of the defects recorded as 3 points, 2 points for major defects, minor defects was 1.Some materials, in accordance with the provisions of the sampling method the maximum score is 6 points.Quality Engineer accordingly suppliers rating, give notice to the supplier.This method is simple, save manpower, but the index below normal.(2)Dynamic Management Based on performance records, all suppliers on a regular basis for dynamic claification aement.All suppliers will be divided into A, B, C, D four, according to the material value, quality, ease of proceing, social availability and other factors point to determine the number of the supply agreement.A fixed number of claes is 1 supplier order allocation was 100%; fixed number of Cla B-1 supplier order allocation is 100%, but the need to develop new supplier of the material; fixed number of 2 A, B type distribution of order suppliers respectively 60% and 40%; fixed number 3 of the A, B, C category vendors were aigned the order 55%, 30% and 15%; D cla of suppliers should be eliminated.The aement and management of hierarchical order with the supplier to supplier performance, material grade combine to make more scientific and rational allocation of orders.Of course, this method the overall level of enterprise management also made very high demands.
l
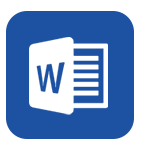