推荐第1篇:金相检验工作总结
金相检验工作总结
在热处理过程中,金相检验具有很重要的地位。金相检验是一道非常严谨的工作,主要包括取样、镶嵌、磨制、抛光、侵蚀、观察、检测等几个步骤,每一道工序都必须仔细认真完成,只要一道工序出现工作失误都可能造成误检、数据偏差较大。在昆山溢阳潮热处理有限公司实习的过程当中,我有许多的心得体会,我把主要的技术步骤总结如下。
取样。根据检验零件的技术要求,在被检零件上选择有代表性的部位取试样。试样的截取应该便于以后的磨制和观察、检测为准。齿类零件做试样时一般切两个齿并留齿根(从动轴、空调机齿、中间轴、倒档齿轮30
33、主轴齿轮3049,巴西伊顿158
8、1182,金杯主动、猎豹前后桥主动等)。其他的零件必须与检测面垂直,切时注意别烧伤。尤其是切荣立减速轴是必须慢速、冲水到位,否则就切坏了。
镶嵌。我们公司用的镶嵌材料是HM3金相镶嵌粉。镶嵌时,被检测面朝下,镶嵌粉一般放7小勺就够了,保温10分钟左右即可取出。
磨制。磨制包括粗磨和细磨。粗磨:经取样和镶嵌的试样,首先应在砂轮片上磨平,磨制划痕均匀。在砂轮打磨试样时,用力均匀压力不要太大,并经常用水冷却,避免试样因受热而发生组织变形。细磨:由粗到细的各号水磨砂纸和金相砂纸上依次进行磨制。我们公司主要用240、600、1000号水磨砂纸和金相砂纸进行磨制。磨制时用力要均匀,在每张砂纸的磨制时间不要太长,一般每一张砂纸磨制试样的个数不超过5个。每换一张另一号砂纸磨制时,试样都要转动90度。粗磨和细磨时要将试样洗净,试样在冲水的状态下磨制。 磨制
的时间不能太长,否则试样会倒角。
抛光。这是最关键的一步也是最后一步,目的是除去最后一道砂纸留下的划痕,得到光滑如镜的检测面。我们主要是机械抛光,抛光织物是绒布。磨料是金刚石喷雾抛光剂。抛光时将磨料均匀的喷在织物上,试样的磨痕要和转盘的的方向垂直,抛光用力均匀,较小的施
加压力。
侵蚀。侵蚀是把金相样品浸在化学侵蚀液里或用带有化学侵蚀剂的脱脂棉球擦拭一定时间,借助化学侵蚀剂对金属的化学作用使金相组织呈现出来。我们使用化学侵蚀剂为硝酸酒精溶液,用1%的硝酸酒精溶液进行轻腐蚀,主要为了观察齿根部位非马组织的厚度,非马组织到现在我还没有搞懂,总是腐蚀不出来。其他的试样一般都是用4%的硝酸酒精溶液进
行腐蚀,腐蚀时间5s左右。
观察。我们金相组织分析时用100*、400*金相显微镜镜的镜头对试样表面进行观察分析试样内部金相组织:渗碳层的深度,齿顶碳化物的含量等级,节圆残余处马氏体的含量等级,心部铁素体的含量等级。用放大100*的显微镜头对整个被检面的晶粒度进行分析评定和整个被检面的组织观察,用400*镜头对金相组织中残余马氏体的等级进行判定。 这个步
骤我觉得挺简单的,也很容易掌握。
有效硬化层测定。在最终热处理后的零件横截面上进行,硬度压痕在指定的宽度为1.5mm的范围内,沿与表面垂直的一条或多条平行线上进行。两相邻压痕间的距离(S)应不小于压痕对角线的2.5倍。从表面到各逐次压痕衷心之间的距离,每次增加不超过0.1mm。同时,测量表面到各压痕的积累距离的精度为±0.5um。压痕一般应在9.807N(1kgf)试验力下测出,并用放大400*的小负荷维氏硬度计测量。表示代码:渗碳和碳氮共渗共渗有效硬化层(DC)、渗氮和氮碳共渗有效硬化层(DN)、高频感应淬火有效硬化层(DS),硬化层界限一般是550HV、513HV、510HV、450HV等。心请教是做好工作的前提,实习是走上社会的第一步,实习可以积累工作经验,而虚心请教是积累工作经验最直接的途径,因此,工作中遇到不明白的地方,我就虚心地请同事,在他们耐心的教导中我不断走向成熟,也积累
起一定的工作经验
半年的实习时间结束了,在这段时间里,我学到了许多书本上不能学到的知识,更加透彻的了解了热处理这门工艺,了解它的知识技能,而且也掌握了一部分专业技术,希望以后能有更多的时间去继续掌握和研究这门技术,在实习的过程中,我同时也学到了许多的处世道理,师傅和领导的教诲,让我受益匪浅。要大胆的去做事,不能拖拖拉拉的,自己不懂的就大胆的去问,社会是一个更大的练兵场,我相信,只要自己努力了,奋斗了,就一定会
有一片属于自己的天地
推荐第2篇:金相检验操作规程
金相检验操作规程
取样-粗磨-细磨-抛光-腐蚀-显微观察评级
1、取样 ,取样要具有代表性,试样尺寸尽量12-20mm范围内,截取过程中应防止组织发生变化(要求截取试样过程中试样受热、受外力作用都能尽量小)通常用于切割试样的有砂轮切割机、原材料检测试样:a)试样的金相检测面要平行于轧制方向;
2、细磨细磨一般在金相砂纸上对粗磨好的试样进一步磨制,为抛光作好准备。细磨一般要由粗到细依次经过240#400#800#金相砂纸。每更换一道砂纸,试样转动90°角,以观察上道砂纸划痕是否全部磨掉。细磨后,将试样和双手冲洗干净。
3抛光 抛光的目的是除去试样磨面上磨痕,使其呈光亮无痕的镜面。 抛光在涂有金刚石研磨膏的专用抛光机上进行,并在抛光机上沿半径方向往复移动或转动,以防产生抛光道痕或拖尾。抛光好的试样冲洗干净,并迅速用吹风机吹干。
3.2.5试样的腐蚀 为进行显微组织检验,须对抛光好的金属试样进行腐蚀,以显示其真实,清晰的组织结构。腐蚀试剂4%硝酸酒精溶液腐蚀金相显微组织:一般过程:冲洗抛光试样-酒精擦洗-吹干-腐蚀-冲洗-酒精擦洗-吹干。
根据所需放大倍数选择物镜及目镜。试样的显微组织检验包括腐蚀前的检验和腐蚀后的检验。腐蚀前主要检验试样中的夹杂物、裂纹、孔隙等及发现磨制过程中所引起的缺陷。腐蚀后主要检验试样的显微组织。
推荐第3篇:金相检验标准
**************** (1) 低倍检验
1 GB/T226-1991
钢的低倍组织及缺陷酸蚀检验法
2 GB/T1979-2001
结构钢低倍组织缺陷评级图
3 GB/T 4236-1984
钢的硫印检验方法
4 GB/T 1814-1979
钢材断口检验法
5 GB/T 2971-1982
碳素钢和低合金钢断口检验方法
6 YB/T 731-19870
塔型车削发纹检验法
7 YB/T 4002-1992
连铸钢方坯低倍组织缺陷评级图
8 YB/T 4003-1991
连铸钢板坯缺陷硫印评级图
9 YB/T 4061-1991
铁路机车、车轴用车轴(含硫印缺陷评级图) 10 YB/T 153-1999
优质碳素结构钢和合金结构钢连铸方坯低倍组织缺陷评级图
11 TB/T 3031-2002
铁路用辗钢整体车轮径向全截面低倍组织缺陷的评定
12 CB/T 3380-1991
船用钢材焊接接头宏观组织缺陷酸蚀试验法
13 HB/Z 210-1991
涡喷型发动机涡轮内、外轴锻件低倍组织标准
14 QJ 2541-1993
不锈钢棒低倍锭型偏析检验方法 **************** (2) 基础标准
1 GB/T13298-1991
金属显微组织检验方法
2 GB/T224-1987
钢的脱碳层深度测定法
3 GB/T10561-1988
钢中非金属夹杂物显微评定方法
4 GB/T 6394-2002
金属平均晶粒度测定方法
5 GB/T/T13299-1991 钢的显微组织(游离渗碳体、带状组织及魏氏组织)评定方法
6 GB/T/T13302-1991 钢中石黑碳显微评定方法
7 GB/T4335-1984
低碳钢冷轧薄板铁素体晶粒度测定法
8 JB/T/T5074-1991
低、中碳钢球化体评级
9 ZBJ36016-1990
中碳钢与中碳合金结构钢马氏体等级
10 DL/T 652-1998
金相复型技术工艺导则 **************** (3) 不锈钢
1 GB/T6401-1986
铁素体奥氏体型双相不锈钢α-相面积含量金相测定法
2 GB/T1223-1975
不锈耐酸钢晶间腐蚀倾向试验方法
3 GB/T1954-1980
铬镍奥氏体不锈钢焊缝铁素体含量测量方法
4 GB/T/T13305-1991
奥氏体不锈钢中α-相面积含量金相测定法 **************** (4) 铸钢
1 GB/T8493-1987
一般工程用铸造碳钢金相
2 TB/T/T2451-1993
铸钢中非金属夹杂物金相检验
3 TB/T/T2450-1993 ZG230-450铸钢金相检验
4 GB/T/T13925-1992 高锰钢铸件金相
5 GB/T5680-1985
高锰钢铸件技术条件(含金相组织检验) 6 YB/T/T036.4-1992 冶金设备制造通用技术条件高锰钢铸件(高锰钢金相组织检验) 7 JB/T/GQ0614-1988
熔模铸钢ZG310-570正火组织金相检验 **************** (5) 化学热处理及感应淬火
1 GB/T11354-2005
钢铁零件 渗氮层深度测定和金相组织检验
2 GB/T9450-1988
钢件渗碳淬火有效硬化层深度的测定和校核
3 QCn29018-1991
汽车碳氮共渗齿轮金相检验
4 JB/T4154-1985 25MnTiBXt钢碳氮共渗齿轮金相检验标准
5 NJ251-1981
20MnTiBRe钢渗碳齿轮金相组织检验
6 ZB/T04001-1988
汽车渗碳齿轮金相检验
7 TB/T/T2254-1991
机车牵引用渗碳淬硬齿轮金相检验
8 JB/T/T6141.1-1992
重载齿轮渗碳层球化处理后金相检验
9 JB/T/T6141.3-1992
重载齿轮渗碳金相检验
10 JB/T/T6141.4-1992
重载齿轮渗碳表面碳含量金相判别法
11 GB/T5617-1985
钢的感应淬火或火焰淬火有效硬化层深度的测定
12 GB/T9451-1988
钢件薄表面总硬化层深度或有效硬化层深度的测定
13 ZB/J36009-1988
钢件感应淬火金相检验
14 ZB/J36010-1988
珠光体球墨铸铁零件感应淬火金相检验
15 NJ304-1983
渗碳齿轮感应加热淬火金相检验
16 JB/T2641-1979
汽车感应淬火零件金相检验
17 CB/T3385-1991
钢铁零件渗氮层深度测定方法 **************** (6) 轴承钢
1. YJZ84 高碳铬轴承钢(含酸浸低倍组织、非金属夹杂物、显微孔隙、退火组织、碳化物不均匀性、碳化物带状、碳化物液析评级图) 2.GB/T9-68
铬轴承钢技术条件(含低倍缺陷、非金属夹杂物、退火组织、碳化物网状、碳化物液析评级图) 3 GB/T3086-82 高碳铬不锈轴承钢技术条件(含酸浸低倍组织、火组织、共晶碳化物不均匀度、非金属夹杂物、微孔隙评级图) 4 YB/T688-76
高温轴承钢Cr4Mo4V技术条件(含碳化物不均匀度评级图) 5 JB/T1255-91 高碳铬轴承钢滚动轴承零件热处理技术条件(含退火组织、淬回火组织、碳化物网状、断口评级图) 6 ZB/J36001-86 滚动轴承零件渗碳热处理质量标准(含粗大碳化物、渗碳表面层淬 回火组织、心部组织、网状碳化物评级图) 7 JB/T1460-92 高碳铬不锈钢滚动轴承零件热处理技术条件(含退火组织、淬回火组织、断口评级图) 8 JB/T2850-92 Cr4Mo4V高温轴承钢滚动轴承零件热处理技术条件(含淬火组织、淬回火组织评级图) 9 JB/T/T6366-92 55SiMoVA钢滚动轴承零件热处理技术条件(含退火组织、淬回火组织、渗碳淬回火组织评级图) **************** (7) 工具钢
1 GB/T1298-77
碳素工具钢技术条件(含珠光体组织、网状碳化物评级图) 2 GB/T1299-85
合金工具钢技术条件(含珠光体组织、网状碳化物、共晶碳化物不均匀) 3 YB/T12-77
高速工具钢技术条件(含低倍碳化物剥落、共晶碳化物不均匀度评级图) 4 ZB/J36003-87 工具热处理金相检验标准
5 GB/T4462-84
高速工具钢大块碳化物评级图 **************** (8) 零部件专用标准
1 GB/T/T13320-91 钢质模锻件金相组织评级图及评定方法
2 ZB/J18004-89 传动用精密滚子链和套筒链零件金相检验
3 ZB/J26001-88 60Si2Mn钢螺旋弹簧金相检验
4 ZB/J94007-88 柴油机喷嘴偶件、喷油泵柱塞偶件、喷油泵出油阀偶件金相检验
5 JB/T3782-84
汽车钢板弹簧金相检验标准
6 NJ309-83
内燃机连杆螺柱金相检验标准
7 NJ326-84
内燃机活塞销金相检验标准
8 JB/T/T6720-93 内燃机排气门金相检验标准
9 JB/T/NQ180-88 内燃机气门座金相检验
10 JB/T/GQ1050-84
45、40Cr钢淬火马氏体金相检验
11 JB/T/GQ1148-89 机床用40Cr钢调质组织金相检验
12 JB/T/GQ•T1150-89 机床用38CrMoAl钢验收技术条件及调质后金相检验
13 JB/T/GQ•T1151-89 机床用45钢调质组织金相检验
14 NJ396-86 低淬透性含钛优质碳素结构钢齿轮金相检验
15 JB/T/T5664-91 重载齿轮失效判据
16 CJ/T 31-1999 液化石油气钢瓶金相组织评定
───────────────────────────────── 二.铸铁
*************** (1) 基础标准
1 GB/T7216-87
灰铸铁金相
2 GB/T9441-88
球墨铸铁金相检验
3 JB/T3892-84
蠕墨铸铁金相标准
4 JB/T2212-77
铁素体可锻铸铁金相标准
5 JB/T3021-81
稀土镁球墨铸铁等温淬火金相标准
6 JB/T/Z303-87
灰铸铁与球墨铸铁断口扫描电镜分析图谱
7 CB/T1165-88
船用灰铸铁金相标准
8 CB/T1030-83
蠕虫状石墨铸铁金相检验
9 TB/T/T2255-91 高磷铸铁金相
10 TB/T/T2449-93 蠕墨铸铁金相检验 **************** (2) 零部件专用标准
1 GB/T2805-81
内燃机单体铸造活塞环金相检验(JB/T/T6016-92) 2 GB/T3509-83
内燃机筒体铸造活塞环金相检验(JB/T/T6290-92) 3 JB/T2330-93
内燃机高磷铸铁缸套金相标准
4 NJ325-84
内燃机硼铸铁单体铸造活塞环金相标准 5 JB/T/T5082-91 内燃机硼铸铁气缸套金相检验
6 JB/T/Z179-82
中锰抗磨球墨铸铁金相标准
7 JB/T/NQ100-86 内燃机钒钛铸铁气缸套金相检验
8 JB/T/NQ178-88 内燃机钒钛铸铁单体铸造活塞环金相检验
9 JB/T/T6724-93 内燃机球墨铸铁活塞环金相检验
10 JB/T3934-85
汽车、摩托车发动机单体铸造活塞环金相检验
11 ZB/T T12007-89 汽车、摩托车发动机球墨铸铁活塞环金相标准
12 ZB/T T06002-89 汽车发动机镶耐磨圈活塞金相标准
13 ZB/U05004-89 中、大功率柴油机离心铸造气缸套金相检验
14 TB/T/T2253-91 球墨铸铁活塞金相检验
15 TB/T/T2448-93 合金灰铸铁单体铸造活塞环金相检验
16 YB/T4052-91
高镍铬无限冷硬离心铸铁轧辊金相检验
17 JB/T/T6954-93 灰铸铁接触电阻加热淬火质量检验和评级
18 CB/T/T 3903-1999 中、大功率柴油机离心铸造气缸套金相检验
───────────────────────────────── 三.表面处理
1 GB/T4677.6-84 金属和氧化覆盖厚度测试方法-截面金相法
2 GB/T5929-86 轻工产品金属镀层和化学处理层的厚度测试方法-金相显微镜法
3 GB/T6462-86
金属和氧化物覆盖层-横断面厚度显微镜测量方法
4 GB/T6463-86
金属和其他无机覆盖层-厚度测量方法评述
5 GB/T9790-88 金属覆盖层及其他有关覆盖层维氏和努氏显微硬度试验
6 GB/T11250.1-89 复合金属覆盖层厚度测定-金相法
7 JB/T/T5069-91 钢铁零件渗金属层金相检验方法
8 JB/T/T6075-92 氧化钛涂层金相检验方法
9 ZBJ92004-87 内燃机精密电镀减摩层轴瓦检验标准
───────────────────────────────── 四.铝合金及铜合金
1 GB/T3246-82
铝及铝合金加工制品显微组织检验方法
2 GB/T3247-82
铝及铝合金加工制品低倍组织检验方法
3 GB/T10849-89
铸造铝硅合金变质
4 GB/T10850-89
铸造铝合金过烧
5 GB/T10851-89
铸造铝合金针孔
6 GB/T10852-89
铸造铝铜合金晶粒度
7 GB/T7998-87
铝合金晶间腐蚀测定法
8 GB/T8014-87 铝及铝合金阳极氧化阳极氧化膜厚度的定义和有关测量厚度的规定
9 GB/T3508-83
内燃机铸造铝活塞金相检验
10 QJ1675-89
变形铝合金过烧金相试验方法
11 JB/T3932-85
汽车、摩托车发动机铸造铝活塞金相标准
12 JB/T/NQ179-88 内燃机稀土共晶铝硅合金金相检验
13 JB/T/T5108-91 铸造黄铜金相
14 QJ2337-92
铍青铜的金相检验方法 15 YB/T797-71
单相铜合金晶粒度测定法
16 YB/T731-70
电真空器件用无氧铜含氧量金相检验法
17 ZB/T12003-87 汽车发动机轴瓦铜铅合金金相标准
18 NJ355-85 内燃机铸造铜铅合金轴瓦金相检验标准
19 CB/T1196-88 船舶螺旋浆用铜合金金相含量金相测定方法
───────────────────────────────── 五.粉未冶金及硬质合金
1 GB/T9095-88
烧结铁基材料-渗碳或碳氮共渗硬化层深度的测定
2 JB/T2798-81
铁基粉未冶金烧结制品金相标准
3 JB/T2869-81
烧结金属材料密度的测定
4 JB/T2867-81
烧结金属材料表观硬度的测定
5 ZBH72007-89 烧结金属摩擦材料金相检验法
6 ZBH72012-90 碳化钨钢结硬质合金金相试样制备方法
7 GB/T3488-83
硬质合金-显微组织的金相测定
8 GB/T3489-83
硬质合金-孔隙度和非化合碳的金相测定
───────────────────────────────── 六.有色合金及稀有金属
1 GB/T4296-84
镁合金加工制品显微组织检验方法
2 GB/T4297-84
镁合金加工制品低倍组织检验方法
3 GB/T1554-79
硅单晶(111)晶面位错蚀坑显示测量方法
4 GB/T3490-83
含铜贵金属材料氧化亚铜金相检验方法
5 GB/T4194-84
钨丝蠕变试验、高温处理及金相检验方法
6 GB/T4197-84
钨钼及其合金的烧结坯条、棒材晶粒度测试方法
7 GB/T5168-1985
两相钛合金高、低倍组织检验方法
8 GB/T5594.8-85 电子元器件结构陶瓷材料性能测试方法-显微结构的测定
9 GB/T6623-86
抛光硅片表面热氧化层错的测试方法
10 GB/T8755-88
钛及钛合金术语和金相图谱
11 GB/T8756-88
锗单晶缺陷图谱
12 GB/T8760-88
砷化镓单晶位错密度的测量方法
13 GB/T11809-89
核燃料棒焊缝金相检验
14 YB/T935-78
贵金属及其合金的金相试样制备方法
15 YB/T732-71
铜、镍及其合金管材和棒材断口检验方法
16 JB/T3657-84
汽车发动机轴瓦锡基和铅基合金金相标准
17 GB/T1156-87 ChSnSb11-6合金轴瓦金相评级 18 CB/T1156-92
锡基轴承合金金相检验
───────────────────────────────── 七.其他有关标准
1 GB/T14999.1-1994 高温合金棒材纵向低倍组织酸浸试验法 高温合金棒材纵向低倍组织酸浸试验法
GB/T14999.2-1994 高温合金横向低倍组织酸浸试验法 高温合金横向低倍组织酸浸试验法
GB/T14999.5-1994 高温合金低倍、高倍组织标准评级图谱 YB/T 4093-1993 GH4133B合金盘形锻件纵向低倍组织标准 ───────────────────────────────── 八.其他有关标准
1 ZB/N33002.1-1988 金相显微镜系列
2 ZB/N33002.2-1988 金相显微镜技术条件
3 GB/T6846-1986
确定暗室照明安全时间的方法 4 GB/T/T4342-1991 金属显微维氏硬度试验方法
5 GB/T/T15749-1995 定量金相手工测定方法
6 GB/T/T17359-1998 电子探针和扫描电镜,X射线能谱定量分析通则 7 GB/T 18876.1-2002 应用自动图像分析测定钢和其它金属中金相组织、夹杂物含量和级别的标准试验方法第1部分:钢和其它金属中夹杂物或第二相组织含量的图像分析与体视学测定
我国现行常用热处理标准(zz)
序号
标准级别号
标准名称
01 JB/T 10174-2000
钢铁零件强化喷丸的质量检验方法 02 JB/T 10175-2000
热处理质量控制要求
03 JB/T 3999-1999
钢件的渗碳与碳氮共渗淬火回火 04 JB/T 4155-1999
气体氮碳共渗
05 JB/T 4202-1999
钢的锻造余热淬火回火处理 06 JB/T 4390-1999
高、中温热处理盐浴校正剂 07 JB/T 7951-1999
淬火介质冷却性能试验方法 08 JB/T 8929-1999
深层渗碳
09 JB/T 9197-1999
不锈钢和耐热钢热处理 10 JB/T 9198-1999
盐浴硫氮碳共渗 11 JB/T 9199-1999
防渗涂料技术要求
12 JB/T 9200-1999
钢铁件的火焰淬火回火处理 13 JB/T 9201-1999
钢铁件的感应淬火回火处理 14 JB/T 9202-1999
热处理用盐 15 JB/T 9203-1999
固体渗碳剂
16 JB/T 9204-1999
钢件感应淬火金相检验
17 JB/T 9205-1999
珠光体球墨铸铁零件感应淬火金相检验 18 JB/T 9206-1999
钢件热浸铝工艺及质量检验 19 JB/T 9207-1999
钢件在吸热式气氛中的热处理 20 JB/T 9208-1999
可控气氛分类及代号 21 JB/T 9209-1999
化学热处理渗剂技术条件 22 JB/T 9210-1999
真空热处理
23 JB/T 9211-1999
中碳钢与中碳合金结构马氏体等级 24 JB/T 8555-1997
热处理技术要求在零件图样上的表示方法
25 JB/T 4215-1996
渗硼(代替JB4215-86和JB4383-87) 26 JB/T 8418-1996
粉末渗金属
27 JB/T 8419-1996
热处理工艺材料分类及代号 28 JB/T 8420-1996
热作模具钢显微组织评级 29 JB/T 7709-1995
渗硼层显微组织、硬度及层深测定方法 30 JB/T 7710-1995
薄层碳氮共渗或薄层渗碳钢铁显微组织检验
31 JB/T 7711-1995
灰铸铁件热处理 32 JB/T 7712-1995
高温合金热处理
33 JB/T 7713-1995
高碳高合金钢制冷作模具用钢显微组织检验
34 JB/T 4218-1994
硼砂熔盐渗金属(代替JB/Z235-85和JB4218-86)
35 JB/T 7500-1994
36 JB/T 7519-1994
分析方法
37 JB/T 7529-1994
38 JB/T 7530-1994
39 JB/T 6954-1993
40 JB/T 6955-1993
41 JB/T 6956-1993
42 JB/T 6047-1992
法
43 JB/T 6048-1992
44 JB/T 6049-1992
45 JB/T 6050-1992
46 JB/T 6051-1992
47 JB/T 5069-1991
48 JB/T 5072-1991
49 JB/T 5074-1991
50 GB/T 18177-2000
51 GB/T 7232-1999
52 GB/T 17358-1998
定方法
53 GB/T 16923-1997
54 GB/T 16924-1997
55 GB15735 - 1995
56 GB/T 15749-1995
57 GB/T 13321-1991
58 GB/T 13324-1991
59 GB/T 12603-1990
60 GB/T 11354-1989
验
61 GB/T 9450-1988
校核
62 GB/T 9451-1988
深度的测定
63 GB/T 9452-1988
低温化学热处理工艺方法选择通则 热处理盐浴(钡盐、硝盐)有害固体废物 可锻铸铁热处理 热处理用氩气、氮气、氢气一般技术条件
灰铸铁件接触电阻淬火质量检验和评级
热处理常用淬火介质技术要求
离子渗氮(代替JB/Z214-84)
热处理盐浴有害固体废物无害化处理方 盐浴热处理
热处理炉有效加热区的测定
钢铁热处理零件硬度检验通则
球墨铸铁热处理工艺及质量检验
钢铁零件渗金属层金相检验方法
热处理保护涂料一般技术要求
低、中碳钢球化体评级 钢的气体渗氮
金属热处理工艺术语
热处理生产电能消耗定额及其计算和测钢的正火与退火处理 钢的淬火与回火处理
金属热处理生产过程安全卫生要求 定量金相手工测定方法 钢铁硬度锉刀检验方法 热处理设备术语
金属热处理工艺分类及代号
钢铁零件渗氮层深度测定和金相组织检 钢铁渗碳淬火有效硬化层深度的测定和 钢件薄表面总硬化层深度或有效硬化层 热处理炉有效加热区测定方法
64 GB/T 8121-1987
热处理工艺材料名词术语
65 GB/T 5617-1985
钢的感应淬火或火焰淬火后有效硬化层深度的测定
推荐第4篇:金相、力学检验个人工作总结
金相、力学检验个人工作总结自今年4月份开始进入单位,转眼一年过去了。对于本人来说,又积累了一年的经验。在这短暂的一年中,由于院、部门领导,各位同行同事以及亲友的帮助,较顺利地完成了自己的本职工作,让本人在检测技术能力上取得了较大的进步。在此谨感谢各位领导,同事。总结过去,展望未来,现将2010年工作简要总结如下:
一、学而时习之,不断提高在检验工作上,作为一名金相、力学检验的新人,我充分的意识到首先我需要虚心的学习理论、充分的参与实践操作工作,尽快的提高自身检验能力。在领导、同事的关怀和帮助下,使我很快的熟悉了工作环境,明确了工作任务及目标。并于7月份、9月份分别参加物理专业技能培训以及全省无损检测培训,均使自己受益匪浅。对待每项检测任务,我都积极的协助有经验的老员工去完成检测工作,并在检测的实践工作过程中边学习理论,边掌握实践。对于不懂的问题就虚心向专业人士请教并实践掌握之。截止目前,已基本掌握相关检测技术方法及检测手段。累计完成了力学、金相实验报告89份。
二、吃得苦中苦,爱岗敬业在工作中,除了学习理论检测知识及掌握检测技术来提高自己的检测能力外,我也意识到要提高自己的工作热情、端正自己的工作态度,才能保证对送检试样的检测质量。
推荐第5篇:弹簧钢的金相检验
弹簧钢的金相检验
1.低倍检验 弹簧表面若存在缺陷,则降低疲劳强度和使用寿命。所以钢材表面不应有裂缝、折叠、拉裂、结巴、发纹、气泡、夹杂和压入氧化皮等表面缺陷。钢材的横截面酸浸倍组织试片上,不得有肉眼可见的缩孔、气泡、裂纹\\、夹杂、翻皮及白点等缺陷、一般疏松、中心疏松\\、偏析均不得超过3级。经热处理后交货的硅锰弹簧钢断口上不得有肉眼可见的石墨碳。低倍组织缺陷按GB1979-80进行检验,断口按GB1841-79进行检验。
2.脱碳的检验 弹簧表面脱碳后的铁素体组织,强度和屈强比都较低,而且淬火时表面不发生相变,体积没有变化 ,而心部则发生马氏体转变体积增大,因而表面处于张应力状态,降低弹簧的疲劳性能。例如60Si2MnA汽车板簧,脱碳层深度增加一倍,疲劳寿命将降低一倍。由此可见,控制脱碳对提高弹簧寿命是有很大实际意义的。
按照GB1222-75规定,弹簧钢材单面脱碳层深度不得超过其直径或厚度的1.5~3%。弹簧成品脱碳更应该严格控制。目前已采用可控气氛防止脱碳,并用喷丸处理以改善表面应力状态。脱碳层的检验按GB224-78进行。
3.石墨碳检验 Si-Mn系合金弹簧钢,在热处理时,碳易于石墨化。使钢变脆,所以对钢中的石墨含量应严格控制。 石墨碳的检验是在抛光后的表面上,在放大250倍显微镜下选取石墨析出量最多的视场,对照冶标YB43-64中的图片进行评级。 石墨碳含量分为以下4个级别:0级
石墨碳含量≦0.03%;1级
石墨碳含量﹥0.03~0.08%;2级
石墨碳含量﹥0.08~0.15%;3级
石墨碳含量﹥0.15%。
4.晶粒度检验 弹簧钢晶粒度应该细小均匀,如果晶粒粗大,则脆性增大,降低使用寿命。在GB1222-75中规定,某些弹簧钢要进行本质晶粒度检验,晶粒度的级别应在5~8级范围内合格。晶粒度级别可按冶标YB25-77进行评定。
5.非金属夹杂物的检验 非金属夹杂物降低弹簧钢的疲劳强度,因而弹簧钢要求有较低的非金属夹杂物含量。一般氧化物硫化物的最高级别都应小于3,二者之和不大于5.5级。非金属夹杂物级别按冶标YB25-77评定。
6.铁素体条带的检验
由于原材料中有带状偏析,因而弹簧在淬火回火后,铁素体分布不均匀,可能出现白色带状痕迹;另一方面,淬火加热温度偏低时,也可能残留未溶铁素体,这些地区都是薄弱环节,最易破坏的地区,所以对铁素体条带要严格控制。
7.非马氏体组织检验
弹簧钢因淬火加热温度偏低而出现残留铁素体,或因淬火冷却不足而出现贝氏体、淬火屈氏体等组织缺陷,从而降低了弹簧的性能。机械工业部制定的钢板弹簧检验标准(试行),将淬火组织分成8级,1~5级合格,6~8级不合格。 1级 细致的回火屈氏体;
2级 中等细致的回火屈氏体; 3级 呈带状分布的回火屈氏体;
4级 较粗的回火屈氏体;
5级 回火屈氏体+少量贝氏体;
6级 回火屈氏体+贝氏体+铁素体; 7级 回火屈氏体+带状分布的铁素体;8级 回火屈氏体+铁素体+珠光体
推荐第6篇:热处理金相检验标准
调质热处理金相检验标准
1.取样位置
金相检验以实物解剖为主,允许用形状尺寸相似、同材料、同方法或同炉处理的试样(块)代替。样(块)解剖位置应在淬火区长度1/3处。
2.制取试样的方法
试样应在冷态下用机械方法制取,在制取试样过程中,不能出现因受热而导致组织改变的现象。
3.试样尺寸
试样尺寸以磨面面积小于400mm2,高度15~20为宜。
4.检测部位
碳素结构钢调质金相取样位置标准按1~3mm深度检验。
5.金相组织评定
调质处理的金相组织在金相显微镜下放大500倍观察,按1~8级评定。当评定的金相组织介于两个级别之间时,以下一个级为判定级别。合格为1—4级。
引用标准:
JBT 5944-1991 工程机械热处理件通用技术条件 GB13298-91金属显微组织检验方法
GBT 13320-1991 钢质模锻件 金相组织评级图及评定方法
推荐第7篇:金相检验安全操作规程
金相检验安全操作规程
第一节
金相显微镜安全操作规程
1 工作前检查电源,开关是否有裸露部位,电器元件损坏及时维修, 防止漏电。
2 亮度调整切忌忽大忽小,也不要过亮,影响灯泡的使用寿命,同时 也伤害视力,要调到合适亮度;
3 工作结束等光源冷却后套上防尘罩。
4 显微镜应放在水平固定的工作台上,未经允许不得任意移动。
第二节
金相研磨机安全操作规程
1 工作前检查电源,开关是否有裸露部位,电器元件损坏及时维修, 防止漏电。
2 更换砂轮片前检查砂轮片是否有裂纹,更换时严禁用锤敲打。接通 电源后待研磨机旋转正常方可操作。
3 在使用砂轮片研磨机的同时,启动除尘开关,进行除尘。
4 磨样时试样应顺着研磨盘旋转方向, 操作时操作人员应配带劳保护 具(防护眼镜,口罩手指套),精神集中,用力均匀适宜。非操作人员 禁止进入
5 研磨盘上放防护罩,防止火花飞溅,操作环境处不允许有易燃、易 爆物品。
6 研磨试样时要有水冷却。
7 定时清整研磨盘,使其平整,及时更换破碎砂纸。
8 砂纸抛光布要平整,破损要及时更换。
第三节
镶嵌机安全操作规程 1 工作前检查电源,开关是否有裸露部位,电器元件损坏及时维修, 防止漏电。
2 打开镶嵌机盖时,头部应避开镶嵌机上方,以免发生外伤害。
3 试样直径超过 6mm应用砂轮切割方法剪断,不宜用剪刀剪。
4 试样冷却后方可从模具中取出,取试样时用镊子夹取,不得直接用 手,以免烫伤。
5 镶嵌完后将内筒和压块表面清洗干净,以利于下一次镶嵌。
第四节
金相试样腐蚀安全操作规程
1 工作前检查电源,开关是否有裸露部位,吹风机电器元件损坏及时 维修,防止漏电。
2 配制腐蚀剂前应配戴好胶皮手套,并检查有无破损。
3 在配制酒精溶液腐蚀剂时,先倒入酒精,再缓慢加入酸液,操作间 严禁烟火。
4 试样应充分吹干,不得有酸等腐蚀液留在表面,以免腐蚀皮肤。
5 操作时精力集中,戴口罩眼镜,打开排风装置进行操作。
第五节
电解腐蚀仪安全操作规程
1 工作前检查电源,开关是否有裸露部位,电器元件损坏及时维修, 防止漏电。
2 配制溶液时注意先倒溶剂,后加入溶质,操作间严禁烟火,防止发 生喷溅、爆炸等事故。 3 腐蚀时间不超过 2 分钟,腐蚀电压不超过 12V。
4 试样吹干用的风机应常检查是否有漏电现象,以免发生触电。 5 操作时精力集中,戴口罩眼镜,打开排风进行操作。
6 浸蚀剂应存放在避光,稳定安全的地方,避免阳光直射及高温。
7 红色夹子接阳极,黑色夹子接阴极,将试样固定在电路阳极。
8 电解时,应选择腐蚀功能的运行按钮,不能使用抛光功能的运行按 钮。避免阴极和阳极直接接触引起短路。
9 电解完毕,关闭电解仪开关, 拔下电源插头, 电解液放入指定瓶内, 以免腐蚀电极。
10 系统设置有过载保护,当电解时不显示电流时,按设备后面的两 个过载保护按钮,可以使电路恢复正常。
第六节
预磨机安全规程
1 工作前检查电源,开关是否有裸露部位,电器元件损坏及时维修, 防止漏电。
2 操作前认真阅读说明书,不当操作会导致设备损坏或自身受伤。
3 设备应放置在干燥、远离磁场的室内。
4 设备操作环境中不允许有易燃、易爆的气体、液体、粉末。
5 开始磨削前要检查磨头锁紧装置处于锁紧状态。
6 当磨头下降快接触到试样时速度要慢,磨头不能撞击试样。
7 开启机器时,关闭安全门,机器运转期间安全门关闭。
8 装卸试样时要戴手套,以免划伤或烫伤。
9 定期检查润滑剂是否足够,不足时应及时补充。
第七节
金相试样切割机操作规程
1 手动操作时, 操作员在向下按压手柄时用力均匀, 避免切割片破碎。
2 自动切割试样时,速度不能过大,以免切割片破碎,飞出伤人。 3 切割试样完毕,试样温度过高取试样时应戴手套并确保冷却液的循 环。
4 更换砂轮切割片后手动运行切割片,确保无误再启动机器
5 夹牢试样切割过程中关闭安全门,非操作人员禁止进入。
6 切割片属易耗品,在更换时应避免被划伤,以及操作不当使切割片 折断。
推荐第8篇:金相检验标准汇总表
金相检验标准
GB/T 10561-89 钢中非金属夹杂物含量的测定标准评级图显微检验法 GB/T 10561-2005 钢中非金属夹杂物含量的测定标准评级图显微检验法 GB/T 1979-2001 结构钢低倍组织缺陷评级图
GB/T 6394-2002 金属平均晶粒度测定方法
GB/T 6394-2002 系列图 I(无孪晶晶粒++浅腐蚀100×)
GB/T 6394-2002 系列图Ⅱ(有孪晶晶粒++浅腐蚀+100×)
GB/T 6394-2002 系列图Ⅲ(有孪晶晶粒+深腐蚀75×)
GB/T 6394-2002 系列图Ⅳ(钢中奥氏体晶粒++渗碳法100×)
GB 224-1987 钢的脱碳层深度测定法
GB 226-1991 钢的低倍组织及缺陷酸蚀检验法
GB 2828-1987 逐批检查记数抽样程序及抽样表
GB 4236-1984 钢的硫印检验方法
GB 16840.4-1997 电气火灾原因技术鉴定方法 第4部分:金相法
GB/T 9450-2005 钢件渗碳淬火硬化层深度的测定和校核
GB/T 13298-1991 金属显微组织检验方法
GB/T 18876.1-2002 应用自动图像分析测定钢和其他金属中金相组织、夹杂物含量和级别的标准试验方法 第1部分
GB/T 4340.1-1999 金属维氏硬度 第一部分:试验方法
GB/T 14999.4-94 高温合金显微组织试验方法
GB/T 230.1-2004 金属洛氏硬度试验 第 1 部分: 试验方法 ( A, B, C, D, E, F, G, H, K, N, T标尺)
GB/T 231.1-2002 金属布氏硬度试验 第 1 部分: 试验方法
GB/T 3488-1983 硬质合金 显微组织的金相测定
GB/T 3489-1983 硬质合金 孔隙度和非化合碳的金相测定
GB/T 4194-1984 钨丝蠕变试验,高温处理及金相检查方法
GB/T 5617-1985 钢的感应淬火或火焰淬火后有效硬化层深度的测定
GB/T 6401-1986 铁素体奥氏体型双相不锈钢中α-相面积含量金相测定法
GB/T 7216-1987 灰铸铁金相
GB/T 8493-1987 一般工程用铸造碳钢金相
GB/T 8755-1988 钛及钛合金术语金相图谱
GB/T 9441-1988 球墨铸铁金相检验
GB/T 9450-1988 钢件渗碳淬火有效硬化层深度的测定和校核
GB/T 9451-1988 钢件薄表面总硬化层深度或有效硬化层深度的测定
GB/T 11809-1998 压水堆核燃料棒焊缝金相检验
GB/T 13305-1991 奥氏体不锈钢中α--相面积含量金相测定法
GB/T 13320-1991 钢质模锻件 金相组织评级图及评定方法
GB/T 13925-1992 铸造高锰钠金相
GB/T 17455-1998 无损检测 表面检查的金相复制件技术
GB 1814-1979 钢材断口检验方法
GB 2971-1982 碳素钢和低合金钢断口检验方法
GB/T 7998-2005 铝合金晶间腐蚀测定方法
GB/T 1298-2008 碳素工具钢
GB/T 1299-2000 合金工具钢 GB/T 1954-1980 铬镍奥氏体不锈钢焊缝铁素体含量测量方法
GB/T 3086-1982 高碳铬不锈轴承钢技术条件
GB/T 3246.1-2000 变形铝及铝合金制品显微组织检验方法
GB/T 3246.2-2000 变形铝及铝合金制品低倍组织检验方法
GB/T 7998-2005 铝合金晶间腐蚀测定方法
GB/T 3508-1983 内燃机铸造铝活塞金相检验标准
GB/T 4194-1984 钨丝蠕变试验、高温处理及金相检查方法
GB/T 4197-1984 钨钼及其合金的烧结坯条、棒材晶粒度测试方法
GB/T 4296-2004 变形镁合金显微组织检验方法
GB/T 4297-2004 变形镁合金低倍组织检验方法
GB/T 4335-1984 低碳钢冷轧薄板铁素体晶粒度测定法
GB/T 4342-1991 金属显微维氏硬度试验方法
GB/T 4462-1984 高速工具钢大块碳化物评级图
GB/T 4677.6-1984 金属和氧化覆盖层厚度测试方法 截面金相法
GB/T 5168-1985 两相钛合金高低倍组织检验方法
GB/T 5594.8-1985 电子元器件结构陶瓷材料性能测试方法 显微结构的测定
GB/T 5617-2005 钢的感应淬火或火焰淬火后有效硬化层深度的测定
GB/T 5680-1998 高锰钢铸件
GB/T 5929-1986 轻工产品金属镀层和化学处理层的厚度测试方法 金相显微镜法
GB/T 6462-2005 金属和氧化物覆盖层 厚度测量 显微镜法
GB/T 6463-2005 金属和其它无机覆盖层厚度测量方法评述
GB/T 6846-1986 确定暗室照明安全时间的方法
GB/T 8014.1-2005 铝及铝合金阳极氧化 氧化膜厚度的测量方法 第1部分测量原则
GB/T 8014.2-2005 铝及铝合金阳极氧化 氧化膜厚度的测量方法 第2部分质量损失法
GB/T 8014.3-2005 铝及铝合金阳极氧化 氧化膜厚度的测量方法 第3部分分光束显微镜法
GB/T 8493-1987 一般工程用铸造碳钢金相
GB/T 8756-1988 锗晶体缺陷图谱
GB/T 8760-2006 砷化镓单晶位错密度的测量方法
GB/T 9095-1988 烧结铁基材料 渗碳或碳氮共渗硬化层深度的测定
GB/T 9451-2005 钢件薄表面总硬化层深度或有效硬化层深度的测定
GB/T 9790-1988 金属覆盖层及其他有关覆盖层 维氏和努氏显微硬度试验
GB/T 10849-1989 铸造铝硅合金变质
GB/T 10850-1989 铸造铝硅合金过烧
GB/T 10851-1989 铸造铝合金针孔
GB/T 10852-1989 铸造铝铜合金晶粒度
GB/T 11250.1-1989 复合金属覆层厚度的测定 金相法
GB/T 11354-2005 钢铁零件 渗氮层深度测定和金相组织检验
GB/T 13320-2007 钢质模锻件 金相组织评级图及评定方法
GB/T 14999.1-1994 高温合金棒材纵向低倍组织酸浸试验法
GB/T 14999.2-1994 高温合金横向低倍组织酸浸试验法
GB/T 14999.3-1994 高温合金棒材纵向断口试验法
GB/T 14999.4-1994 高温合金显微组织试验法
GB/T 14999.5-1994 高温合金低倍、高倍组织标准评级图谱
GB/T 15749-1995 定量金相手工测定方法 GB/T 18876.1-2002 应用自动图像分析测定钢和其他金属中金相组织、夹杂物含量和级别的标准试验方法 第1部分钢和其他金属中夹杂物或第二相组织含量的图像分析与体视学测定
GB/T 18876.2-2006 应用自动图像分析测定钢和其它金属中金相组织、夹杂物含量和级别的标准试验方法 第2部分:钢中夹杂物级别的图像分析与体视学测定
GB/T 13299-1991 金相组织评级图及评定方法
GB/T 13788-2000 冷轧带肋钢筋
JB
JB/T 5074-2007 低、中碳钢球化体评级
JB/T 3829-1999 蠕墨铸铁金相
JB/T 9205-1999 珠光体球墨铸铁零件感应淬火 金相检验
JB/T 7946.1-1999 铸造铝合金金相 铸造铝硅合金变质
JB/T 7946.2-1999 铸造铝合金金相 铸造铝硅合金过烧
JB/T 9204-1999 钢件感应热处理 金相检验
JB/T 5664-1991 重载齿轮 失效判据
JB/T 6141.1-1992 重载齿轮渗碳层球化处理后金相检验
JB 3782-1984 汽车钢板弹簧金相检验标准
JB/T 1460-2002 高碳铬不锈钢滚动轴承零件热处理技术条件
JB/T 2122-1977 铁素体可锻铸铁 金相
JB/T 2330-1993 内燃机高磷铸铁气缸套 金相检验
JB/T 2798-1999 铁基粉末冶金烧结制品 金相标准
JB/T 2850-1993 Cr4MO4V高温轴承钢滚动轴承零件 热处理技术条件
JB/T 5069-1991 钢铁零件渗金属层 金相检验方法
JB/T 5082.1-2008 内燃机 气缸套 第1部分:硼铸铁金相检验
JB/T 5108-1991 铸造黄铜 金相
JB/T 6016-1992 内燃机单体铸造活塞环 金相检验
JB/T 6075-1992 氮化钛涂层 金相检验方法
JB/T 6141.3-1992 重载齿轮 渗碳金相检验
JB/T 6141.4-1992 重载齿轮 渗碳表面碳含量金相判别法
JB/T 6290-1992 内燃机筒体铸造活塞环 金相检验
JB/T 6366-1992 55SiMoVA钢滚动轴承 零件热处理技术条件
JB/T 6720-1993 内燃机进、排气门 金相检验
JB/T 6724-1993 内燃机球墨铸铁活塞环 金相检验
JB/T 6954-1993 灰铸铁接触电阻加热淬火质量检验和评级
其他
DL/T 674-1999 火电厂用20钢珠光体球化评级标准
DL/T 652-1998 金相复型技术工艺导则
YB/T 153-1999 优质碳素结构钢和合金结构钢连 铸方坯低倍组织缺陷评级图
YB 935-1978 贵金属及其合金的金相试样制备方法 YB 4061-1991 铁路机车 车辆用车轴
YB/T 036.4-1992 冶金设备制造通用技术条件 高锰钢铸件
YB/T 4002-1991 连铸钢方坯低倍组织缺陷评级图
YB/T 4003-1997 连铸钢板坯低倍组织缺陷评级图
CB 1030-1983 蠕状石墨铸铁金相检验
CB/T 3694-1995 现场金相复型检验方法
CB 1156-92 锡基轴承合金金相检验
CB 1196-1988 船舶螺旋桨用铜合金相含量金相测定方法
CB 3380-91 船用钢材焊接接头宏观组织缺陷酸蚀试验法
CB 3385-1991 钢铁零件渗氮层深度测定方法
TB/T 2254-1991 机车牵引用渗碳淬硬齿轮金相检验标准
TB/T 2255-1991 高磷铸铁金相
TB/T 2448-1993 合金灰铸铁单体铸造活塞环 金相检验
TB/T 2450-1993 ZG230-450铸钢金相检验
TB/T 2451-1993 铸钢中非金属夹杂物金相检验
TB/T 3031-2002 铁路用辗钢整体车轮径向全截面低倍组织缺陷的评定
QJ 1675-1989 变形铝合金过烧金相试验方法
QCN 29018-1991 汽车碳氮共渗齿轮金相检验
JJG 335-1991 标准显微维氏硬度块
CJ/T 31-1999 液化石油气钢瓶金相组织评定
推荐第9篇:金相检验培训心得
金相检验培训心得
首先,非常感谢公司给我提供了这次培训机会,我感到十分荣幸。这次培训使我在充实自己专业知识的同时也开阔了眼界、拓展了思路,下面,我具体总结一下这次培训的心得体会。
此次的培训内容是金相检验,培训时间为三天,共分为理论和实验两部分。
理论培训主要以金属学基础、钢的热处理基础、金相检验技术理论知识为主。
理论培训部分。主要包括金属学基础、钢的热处理基础、宏观金相检验技术、金相检验技术设备等几个方面。首先是系统学习了金属学基础,对金属材料的结构和组织进行了初步的了解,同时,也学习了金属材料的性能,并针对我厂实际着重的学习了金属材料的焊接性能;然后通过对铁碳相图的分析学习了金属不同组织的成因和物理特性;最后是热处理对金属成分的影响以及金相检验原理和设备介绍。
实验培训部分。首先,简要的介绍一下金相检验。金相检验分为宏观金相检验和微观金相检验,对壁厚大于6mm的焊接件进行酸蚀宏观检验;对壁厚小于或等于6mm的焊接件则进行微观检验;有时酸蚀宏观检验难于定性的缺陷也可进行显微分析。
常规的金相法往往是解剖材料来截取试样检验(破坏性试验)。这就破坏了材料的连续性,从而给继续使用带来困难,甚至造成产品的报废。 因此,无损金相检验应运而生。无损金相检验方法是在选定的检测部位,在现场磨制其表面金相,腐蚀后进行观察。观察方法有两种:一:用显微镜在现场直接进行观察照相。但这种方法不能观察曲面,对球形压力容器(千斤顶缸体)的检测存在着困难;二:用复型法进行观察检验,即在腐蚀好的部位,在现场用AC纸做其表面复型,然后在复制品上喷一层铝,这样制得的试样可以压平,并能用高级金相显微镜进行高低倍观察照相,由于AC纸各向同性,不产生畸变,因而保证反映实际的组织。这种检测方法对于球形容器,特别是焊接接头部位具有突出的优越性。另一方面,该检测方法需1—2小时便可以完成取样,具有方便快捷的特点。同时,它不影响生产运行,这对研究使用中的液压支架金相组织变化具有特殊意义。
接下来就是通过金相检验结果来分析焊缝质量问题,常见焊缝缺陷主要包括未焊透、裂纹、疏松、夹杂及气孔等几种。不允许组织为马氏体和屈氏体两种。通过对焊缝的金相检验分析,进而对焊接工艺进行有针对性的改进,以提高焊缝质量。
以上是对培训内容的简略介绍和总结,接下来结合我对金相检验的理解谈一谈金相检验技术在公司未来发展中的位置和重要性。
我厂主要产品为液压支架,液压支架主要由结构件、液压系统和控制系统组成。其中,结构件和千斤顶缸体作为主要承载元件都是焊接而成的,因此,焊缝的质量直接影响到液压支架的产品质量。目前我国液压支架结构件大都采用16Mn和Q460为主要板材,体积及自重偏大,给液压支架的运输及安装带来了很大的困难。随着液压支架向大工作阻力和高可靠性要求的方向发展,如何在保证强度的前提下,尽量减轻支架重量是一个需要急需解决的问题,采用更高强度的板材是最有效的途径。由于高强钢具有较高的强度和硬度,焊接稳定性较差,易出现裂纹和热影响区性能的变化,减低结构件的使用寿命。因此应根据焊缝力学分析和金相检验的相关结果制定合理的焊接工艺,从而保证支架焊接质量的可靠性。焊缝需要满足液压支架工作时各项性能要求,而这些性能受控于成分、内部显微组织、杂质和缺陷、表面组织及应力状态等,其中主要是成分和组织。成分和组织在很大程度上控制着所有组织敏感性能。焊缝工艺控制质量的第一个因素就是化学成分,化学成分通过相变等方式控制组织中的相、体积分数和形态,如马氏体形态、贝氏体形态。高碳马氏体和上贝氏体都是有害组织,而低碳马氏体和下贝氏体则相对机械性能较好。所以,金相检验是验证和解释所设计焊缝工艺是否合理的强有力的手段。
我厂现阶段检验方法主要以无损探伤为主,而对焊缝具体组织成分研究不足,这严重阻碍了我厂向高端液压支架进军的步伐。工欲善其事必先利其器,希望我厂从长远出发,建立起一套合理有效的检验和工艺改进机制,走出竞争激烈的低端支架市场,真正的以鲁尔支架为契机成为世界液压支架巨头。
推荐第10篇:国内金相检验标准目录
国内金相检验标准目录
一、钢材
**************** (1)低倍检验
1. CB 3380-1991 船用钢材焊接接头宏观组织缺陷酸蚀试验法 2.GB/T 226-1991 钢的低倍组织及缺陷酸蚀检验法 3.GB 2971-1982 碳素钢和低合金钢断口检验方法 4.GB/T 1814-1979 钢材断口检验法
5.GB/T 1979-2001 结构钢低倍组织缺陷评级图 6.GB/T 4236-1984 钢的硫印检验方法 7.GB/T 15711-1995 钢材塔形发纹酸浸检验方法
8.TB/T 3031-2002 铁路用辗钢整体车轮径向全截面低倍组织缺陷的评定 9.YB 4002-1991 连铸钢方坯低倍组织缺陷评级图
10.YB/T 153-1999 优质碳素结构钢和合金结构钢连铸方坯低倍组织缺陷评级图
11.YBT 4003-1997 连铸钢板坯低倍组织缺陷评级图
****************
(2) 基础标准(钢的显微组织评定)
1.2.3.DL/T 652-1998 金相复型技术工艺导则 GB/T 224-2008 钢的脱碳层深度测定法
GB/T 4334-2008 金属和合金的腐蚀 不锈钢晶间腐蚀试验方法 4.5.6.7.8.9.GB/T 4335-1984 低碳钢冷轧薄板 铁素体晶粒度测定法
GB/T 10561-2005 钢中非金属夹杂物含量的测定 标准评级图显微检验法 GB/T 13298-1991 金属显微组织检验方法 GB/T 13299-1991 钢的显微组织评定方法 GB/T 13302-1991 钢中石墨碳显微评定方法
GB/T 13320-2007 钢质模锻件 金相组织评级图及评定方法
10.GB/T 14979-1994 钢的共晶碳化物不均匀度评定法 11.GB/T 15749-2008 定量金相测定方法
12.GB/T 18876.1-2002 应用自动图像分析测定钢和其他金属中金相组织、夹杂物含量和级别的标准试验方法 第一部分
13.GB/T 18876.2-2006 应用自动图像分析测定钢和其他金属中金相组织、夹杂物含量和级别的标准试验方法 第二部分
14.GB/T 18876.3-XXXX 应用自动图像分析测定钢和其它金属中金相组织、夹杂物含量和级别的标准试验方法 第三部分
15.GB/T 6394-2002 金属平均晶粒度测定法 16.JB/T 5074-2007 低、中碳钢球化体评级
17.JB/T 9211-2008 中碳钢与中碳合金结构钢马氏体等级
****************
(3) 不锈钢
1.CB/T 1209-1992 0Cr17Ni4Cu4Nb(17-4PH)+马氏体沉淀硬化不锈钢金相检验
2.GB 4234-2003 外科植入物用不锈钢 3.GB/T 1220-2007 不锈钢棒
4.GB/T 1954-2008 铬镍奥氏体不锈钢焊缝铁素体含量测量方法 5.GB/T 4334.1-2000 不锈钢10%草酸浸蚀试验方法 6.GB/T 4334.2-2000 不锈钢硫酸-硫酸铁腐蚀试验方法 7.GB/T 4334.3-2000 不锈钢65%硝酸腐蚀试验方法 8.GB/T 4334.4-2000 不锈钢硝酸-氢氟酸腐蚀试验方法 9.GB/T 4334.5-2000 不锈钢硫酸_硫酸铜腐蚀试验方法 10.GB/T 4334.6-2000 不锈钢5%硫酸腐蚀试验方法
11.GB/T 6401-1986 铁素体奥氏体型双相不锈钢中α-相面积含量金相测定法
12.GB/T 13305-2008 不锈钢中α-相面积含量金相测定法
**************** (4) 铸钢
1.GB/T 5680-1998 高锰钢铸件
2.GB/T 8493-1987一般工程用铸造碳钢金相 3.GB/T 13925-1992铸造高锰钢金相 4.TB/T 2450-1993 ZG230-450铸钢金相检验 5.TB/T 2451-93铸钢中非金属夹杂物金相检验
6.YB/T 036.4-1992 冶金设备制造通用技术条件高锰钢铸件
**************** (5) 化学热处理及感应淬火 1.CB 3385-1991 钢铁零件渗氮层深度测定方法
2.GB/T 5617-2005 钢的感应淬火或火焰淬火后有效硬化层深度的测定 3.GB/T 9450-2005 钢件渗碳淬火有效硬化层深度的测定和校核 4.GB/T 9451-2005 钢件薄表而总硬化层深度或有效硬化层深度的测定 5.GB/T 11354-2005 钢铁零件 渗氮层深度测定和金相组织检验 6.GB/T 11354-2005 钢铁零件 渗氮层深度测定和金相组织检验 7.GB/T 18177-2000 钢件的气体渗氮
8.JB/T 3999-1999 钢的渗碳与碳氮共渗淬火回火处理 9.JB/T 6141.1-1992 重载齿轮渗碳层球化处理后金相检验 10.JB/T 6141.2-1992 重载齿轮 渗碳质量检验 11.JB/T 6141.3-1992 重载齿轮渗碳金相检验
12.JB/T 6141.4-1992 重载齿轮 渗碳表面碳含量金相判别法 13.JB/T 7709-2007 渗硼层显微组织、硬度及层深检测方法 14.JB/T 7710-2007 薄层碳氮共渗或薄层渗碳钢件 显微组织检测 15.JB/T 9198-1999 盐浴硫氮碳共渗
16.JB/T 9200-1999 钢铁件的火焰淬火回火处理 17.JB/T 9204-2008 钢件感应淬火金相检验
18.JB/T 9205-2008 珠光体球墨铸铁零件感应淬火金相检验 19.QCn 29018-1991 汽车碳氮共渗齿轮金相检验 20.QC/T 262-1999 汽车渗碳齿轮金相检验 21.QC/T 502-1999 汽车感应淬火零件金相检验
22.TB/T 2254-1991 机车牵引用渗碳硬齿轮金相检验标准
****************
(6) 轴承钢
1.GB/T 3086-2008 高碳铬不锈轴承钢 2.GB/T 18254-2002 高碳铬轴承钢
3.JB/T 1255-2001 高碳铬轴承钢滚动轴承零件热处理技术条件 4.JB/T 1460-2002 高碳铬不锈钢滚动轴承零件热处理技术条件 5.JB/T 2850-2007 Cr4Mo4V高温轴承钢零件 热处理技术条件 6.JB/T 6366-1992 55SiMoVA钢滚动轴承 零件热处理技术条件 7.JB/T 7362-1994 滚动轴承 零件脱碳层检查方法 8.JB/T 8881-2001 滚动轴承零件渗碳热处理技术条件 9.YB 9-68 铬轴承钢技术条件
****************
(7) 工具钢
1.GB 1298-1986 碳素工具钢技术条件 2.GB 4462-1984 高速工具钢大块碳化物评级图 3.GB/T 1299-2000 合金工具钢 4.GB/T 9943-2008 高速工具钢
5.JB/T 7713-2007 高碳合金钢制冷作模具显微组织检验 6.JB/T 8420-2008 热作模具钢显微组织评级 7.JB/T 9129-2000 60Si2Mn钢 螺旋弹簧 金相检验 8.YB/T 5058-2005 弹簧钢、工具钢冷轧钢带 9.ZBJ 36003-1987 工具热处理金相检验标准
****************
(8) 零部件专用标准
1.CJ/T 31-1999 液化石油气钢瓶金相组织评定 2.JB 3782-1984 汽车钢板弹簧 3.JB/T 5664-2007 重载齿轮 失效判据 4.JB/T 6720-1993 内燃机进、排气门金相检验 5.JB/T 8118.2-1999 内燃机 活塞销 金相检验 6.JB/T 8837-2000 内燃机连杆螺栓金相检验 7.JB/T 8893-1999 内燃机 气门座 金相检验 8.JB/T 9730-1999 柴油机喷油嘴偶件、喷油泵 9.QC/T 521-1999 汽车发动机气门挺杆技术条件
─────────────────────────────────
二、铸铁
***************
(1) 基础标准
1.GB/T 7216-2009 灰铸铁金相检验 2.GB/T 8491-2009 高硅耐蚀铸铁件 3.GB/T 9437-2009 耐热铸铁件 4.GB/T 9441-2009 球墨铸铁金相检验
5.JB 3021-1981 稀土镁球墨铸铁等温淬火金相标准 6.JB/T 2122-1977 铁素体可锻铸铁金相标准 7.JB/T 3829—1999 蠕墨铸铁金相 8.TB/T 2255-1991 高磷铸铁金相
****************
(2) 零部件专用标准
1.JB/T 9745-1999 内燃机 硼铸铁 单体铸造活塞环 金相检验 2.JB/T 2330-1993 内燃机 高磷铸铁 气缸套金相检验 3.JB/T 5082.1-2008 内燃机 气缸套 硼铸铁金相检验 4.JB/T 6016-1992 内燃机单体铸造活塞环金相检验 5.JB/T 6290-1992 内燃机筒体铸造活塞环金相检验 6.JB/T 6724-1993 球墨铸铁活塞环金相检验
7.JB/T 6954-1993 灰铸铁接触电阻加热淬火 质量检验和评级 8.QC/T 284-1999 汽车、摩托车发动机球墨铸铁活塞环金相标准 9.QC/T 555-2000 汽车、摩托车发动机单体铸造活塞环金相检验 10.11.
─────────────────────────────────
三、表面处理 ****************** 1.GB/T 4677.6-1984 金属和氧化覆盖层厚度测试方法截面金相法 TB/T 2448-1993 合金灰铸铁单体铸造活塞环金相检验 YB/T 4052-1991 高镍铬无限冷硬离心铸铁轧辊金相检验 2.GB/T 5929-1986 轻工产品金属渡层和化学处理层的厚度测试方法 3.GB/T 6462-2005 金属和氧化覆盖层 厚度测量 显微镜法
4.GB/T 9790-1988 金属覆盖层及其他有关覆盖层 维氏和努氏显微硬度试验 5.GB/T 11250.1-1989 复合金属覆层厚度的测定 金相法 6.JB/T 5069-1991 钢铁零件渗金属层金相检验方法 7.JB/T 6075-1992 氮化钛涂层 金相检验方法
─────────────────────────────────
四、铝合金 ************** (1) 基础标准
1.GB 10852-1989 铸造铝铜合金晶粒度
2.GB/T 1173-1995 铸造铝合金
3.GB/T 3246.1-2-2000 变形铝及铝合金制品显微组织检验方法 4.GB/T 3246.2-2000 变形铝及铝合金制品低倍组织检验方法 5.GB/T 7998-2005 铝合金晶间腐蚀测定方法
6.GB/T 8014.1 -2005 铝及铝合金阳极氧化 氧化膜厚度的测量方法 第1部分 测量原则
7.GB/T 8014.2 -2005 铝及铝合金阳极氧化 氧化膜厚度的测量方法 第2部分 质量损失法
8.GB/T 8014.3 -2005 铝及铝合金阳极氧化 氧化膜厚度的测量方法 第3部分:分光束显微镜法 9.GB/T 8733-2000 铸造铝合金锭 10.GB/T 10849-1989 铸造铝硅合金变质 11.GB/T 10850-1989 铸造铝硅合金过烧 12.GB/T 10851-1989 铸造铝合金针孔 13.GB/T 15115-94 压铸铝合金
14.JB/T 7946.1-1999 铸造铝合金金相.铸造铝硅合金变质 15.JB/T 7946.2-1999 铸造铝合金金相.铸造铝硅合金过烧 16.JB/T 7946.3-1999 铸造铝合金金相.铸造铝合金针孔 17.JB/T 7946.4-1999 铸造铝合金金相.铸造铝铜合金晶粒度 18.QJ 1675-1989 变形铝合金过烧金相试验方法
****************
(2) 零部件专用标准
1.GB 3508-1983 内燃机铸造铝活塞金相检验标准 2.JB/T 6289-2005 内燃机铸造铝活塞金相检验
3.JB/T 8892-1999 内燃机 稀土共晶铝硅合金活塞 金相检验 4.QC/T 553-2008 汽车、摩托车发动机铸造铝活塞 金相检验
─────────────────────────────────
五、铜合金 *************** 1.GB/T 10119-2008 黄铜耐脱锌腐蚀性能的测定
2.GB/T 10567.2-2007 铜及铜合金加工材残余应力检验方法 氨薰试验法 3.JB/T 5108-91 铸造黄铜
4.JB/T 9749-1999 内燃机铸造铜铅合金轴瓦金相检验 5.QC/T 281-1999 汽车发动机轴瓦铜铅合金金相标准 6.QJ 2337-1992 铍青铜的金相试验方法
7.YS/T 335-1994 电真空器件用无氧铜含氧量金相 8.YS/T 336-1994 铜、镍及其合金管材和棒材断口检验法 9.YS/T 347-2004 铜及铜合金平均晶粒度测定方法
10.YS/T 449-2002 铜及铜合金 铸造和加工制品显微组织检验方法
─────────────────────────────────
六、粉未冶金及硬质合金 ******************************* 1.GB 3488-1983 硬质合金-显微组织的金相测定
2.GB/T 3489-1983 硬质合金 孔隙度和非化合碳的金相测定
3.GB/T 9095-2008 烧结铁基材料渗碳或碳氮共渗层深度的测定及其验证 4.GB/T 10425-2002 烧结金属摩擦材料表观硬度的测定 5.JB/T 2798-1999 铁基粉末冶金烧结制品金相标准 6.JB/T 9137-1999 烧结金属摩擦材料金相检验法
─────────────────────────────────
七、有色合金及稀有金属 ******************************* 1.CB 1156-1992 锡基轴承合金金相检验
2.GB/T-4197-1984 钨钼及其合金的烧结坯条、棒材晶粒度测定方法 3.GB/T 1554-1995 硅晶体完整性化学择优腐蚀检验方法 4.GB/T 4194-1984 钨丝蠕变试验,高温处理及金相检查方法 5.GB/T 4296-2004 变形镁合金显微组织检验方法 6.GB/T 4297-2004 变形镁合金低倍组织检验方法 7.GB/T 5168-2008 α-β钛合金金高低倍组织检验方法 8.GB/T 6611-2008 钛及钛合金术语和金相图谱 9.GB/T 8756-1988 锗单晶缺陷图谱
10.GB/T 8760-2006 砷化镓单晶位错密度的测量方法 11.GB/T 13810-2007 外科植入物用钛及钛及钛合金加工材 12.GB/T 13818-1992 压铸锌合金
13.GB/T 5594.8-1985 电子元器件结构陶瓷材料性能测试方法 显微结构的测定
14.QC/T 516-1999 汽车发动机轴瓦锡基和铅基合金金相标准 15.QJ 2917-1997 钛及钛合金金相检验方法
16.YS/T 370-2006 贵金属及其合金的金相试样制备方法
─────────────────────────────────
八、高温合金相关标准
******************** 1.GB/T 14999.1-1994 高温合金棒材纵向低倍组织酸浸试验法 2.GB/T 14999.2-1994 高温合金横向低倍组织酸浸试验法 3.GB/T 14999.3-1994 高温合金棒材纵向断口试验法 4.GB/T 14999.4-1994 高温合金显微组织试验法
5.GB/T 14999.5-1994 高温合金低倍高倍组织标准评级图谱 6.YB 4093-1993 GH4133B合金盘形锻件纵向低倍组织标准
─────────────────────────────────
九、其他有关标准 ***************** 1.DL/T 884-2004 火电厂金相检验与评定技术导则 2.GB/T 1979-2001 结构钢低倍组织缺陷评级图介绍 3.GB/T 3203-1982 渗碳轴承钢 技术条件
4.GB/T 4340.1-2009 金属材料 维氏硬度试验 第1部分:试验方法 5.GB/T 4340.2-1999 金属维氏硬度试验2:硬度计的检验 6.GB/T 4340.3-1999 金属维氏硬度试验3:标准硬度块的标定 7.GB/T 5612-2008 铸铁牌号表示方法
8.GB/T 8063-1994 铸造有色金属及其合金牌号表示方法 9.GB/T 15749-2008 定量金相测定方法 10.11.12.GB/T 17359-1998 电子探针和扫描电镜X射线能谱定量分析方法通则 GB/T 17360-1998 钢中低含量Si、Mn 的电子探针定量分析方法 GB/T 18876.1-2002 应用自动图像分析测定钢和其它金属中金相组织、夹杂物含量和级别的标准试验方法
第1部分:钢和其它金属中夹杂物或第二相组织含量的图像分析与体视学测定
心
部
2010杭州众享技术培训中中国机械专家网培训年12月15日
第11篇:铸钢的金相组织及检验
铸钢的金相组织及检验
一、铸造碳钢的金相组织及检验
(一)铸造碳钢的显微组织
1.铸态组织 为铁素体+珠光体+魏氏组织。如图8-
1、图8-2。
图8-1 ZG230-450铸钢铸态组织 (100×) 图8-2 ZG310-570铸钢铸态组织 (100×)
铸态组织的形貌和组成相的含量与钢的碳含量有关。碳含量越低的铸钢,铁素体含量越多,魏氏组织的针状越明显、越发达,数量也多。随铸钢碳含量的增加,珠光体量增多,魏氏组织中的针状和三角形的铁素体量减少,针齿变短,量也减少,而块状和晶界上的网状铁素体粗化,含量也增多。若存在严重的魏氏组织,或存在大量低熔点非金属夹杂物沿晶界呈断续网状分布,将使铸钢的脆性显著增加。
2.退火组织 为铁素体+珠光体。铁素体呈细等轴晶。珠光体分布形态随钢的碳含量增加而变化。随钢的碳含量增加,珠光体呈断续网状分布→网状分布→珠光体与铁素体均匀分布,其含量也不断增多。若退火组织中存在残留的铸态组织或组织粗化均属于不正常组织。
3.正火组织 为铁素体+珠光体,分布较均匀,如图8-3。与退火组织相比较,正火组织的组成相更细、更均匀,珠光体含量稍多。若存在残留铸态组织或组织粗化均属不正常组织。
4.调质组织 ZG270-500以上牌号的铸造碳钢可进行调质处理,组织为回火索氏体,见图8-4。若出现未溶铁素体或粗大的回火索氏体属不正常组织。
图8-3 ZG230-450 铸钢正火组织 (100 ×) 图8-4 ZG35CrMo铸钢调质组织 (650×) 5.几种常用铸造碳钢的组织 见表8-1, 表8-1 常用铸造碳钢的组织
铸 造 碳 钢 ZG200-400 ZG230-450 ZG270-500 ZG310-570 ZG340-640 显 微 组
织 铸态 魏氏组织+块状铁素体+珠光体 珠光体+魏氏组织+铁素体 珠光体+铁素体 部分铁素体呈网状分布 铁素体呈网状分布 退火 铁素体+珠光体 珠光体+铁素体 珠光体呈断续网状分布 珠光体呈网状分布 正火 铁素体+珠光体 珠光体+铁素体 调质 回火索氏体
(二)铸造碳钢的质量检验
铸造碳钢多数用于一般工程,金相检验按照GB/T 8493-1987《一般工程用铸造碳钢金相》标准进行。主要是在金相显微镜下进行显微组织鉴别及晶粒度和非金属夹杂物级别的测定。标准规定金相试样从力学性能试块或试样上切取,特殊情况由供需双方协商决定。
1.显微组织检验 试样用2~4%硝酸酒精溶液侵蚀后,在显微镜下按大多数视场确定其组织。对铸态、退火、正火态组织放大100倍观察,对调质态组织在500倍下鉴别。
GB/T 8493-1987标准对ZG200-400、ZG230-450、ZG270-500, ZG310-57
7、ZG340-640五种铸钢分别按铸态、退火、正火及调质状态下的正常和非正常组织的特征列表作了文字说明,并列出了标准组织照片,供对照评定。
2.晶粒度测定 奥氏体晶粒度和铁素体晶粒度的测定方法,按 GB/T 8493-1987标准的规定执行。被测试样在放大100倍下与标准晶粒度图对照进行评级。若放大倍数为非100倍时,按YB/T 5148标准规定的方法评定。
3.非金属夹杂物的评级 GB/T 8493-1987标准将铸造碳钢中的非金属夹杂物分为五级,并列出了5张标准级别的照片,供对照评级用。
二、铸造低合金结构钢的金相组织
各种能进行压力加工(锻、轧)的低合金结构钢,基本上都可以作为铸钢,但为满足铸造性能的要求需适当调整化学成分。常用的铸造低合金钢有ZG22Mn、ZG40Mn、ZG40Mn
2、ZG40Cr、ZG35CrMo、ZG35SiMn、ZG20MnMo、ZG50B和ZG25MnVCu等。
铸造低合金结构钢可以进行退火、正火处理。由于它们的淬透性较好,可以用淬火-回火方法进行强化处理。为消除铸造应力、细化晶粒和防止开裂,淬火前一般要预先经退火或正火处理。这类钢还可以进行表面淬火或化学热处理。
几种常用铸造低合金钢的热处理组织如下: 1.铬钢、铬钼钢
(1) 铬钢。如ZG40Cr,经常在调质状态下使用。组织为均匀的回火索氏体。
(2) 铬钼钢。如ZG35CrMo, 铸态组织为粗大的铁素体+珠光体,略呈魏氏组织,并可见明显的枝 晶状组织。退火组织为铁素体十珠光体。其中珠光体含量的体积分数约占50%。正火组织为珠光体+少量铁素体。细晶粒铁素体呈细网络状分布,其含量明显少于退火组织。珠光体分散度也更大,有时会出现贝氏体和铁素体组织(钼元素抑制珠光体析出的结果)。淬火组织为针状淬火马氏体。马氏体针中等粗细,分布较均匀(组织与35CrMo锻钢淬火相似)。调质组织为均匀的回火索氏体。 2.钼钢如ZG15Mo钢、ZG25Mo钢。
(1) ZG15Mo钢.退火组织为铁素体十少量珠光体。其中铁素体呈等轴晶,珠光体呈块状均匀分布。 正火组织为铁素体+少量珠光体。调质组织为回火索氏体,有针状分布痕迹。
(2) ZG25Mo钢。退火及正火组织类似于ZG15Mo钢,仅其中珠光体含量较多,分布更均匀一些。对于大型铸件常采用正火+高温回火处理,得到的组织与正火态相似。调质组织为回火索氏体。若铸件不先作预处理,铸件内存在枝晶偏析严重,直接淬火+高温回火(调质)后的索氏体分布不均匀。 3.锰钢、硅锰钢
(1) ZG40Mn2钢的正火组织为珠光体+铁素体。铁素体量少且呈较细网状分布。淬火组织为淬火马氏体。调质后得到均匀的回火索氏体。
(2)硅锰钢常使用调质态,组织与相应的锰钢相似。这两种钢都有过热敏感性和对回火脆性敏感的特点。 4.铬镍钢、铬镍钼钢及硼钢例ZG40CrNiMo或ZG50B钢,它们都使用调质态,组织均为均匀分布的回火索氏体。
三、铸造高锰钢的金相组织
(一)高锰钢的组织和性能特点
高锰钢是在过共析碳钢(ωc=1.0%~1.3%)中增加锰含量(ωMn = 11%一14%),使Mn/C之比接近10/1,再经过水淬后得到室温下单一奥氏体组织的钢。这类钢具有在承受冲击载荷和严重摩擦作用下使钢发生显著硬化的特性,而且载荷越大,其表面层的硬化程度越高,耐磨性就越好,是一种典型的耐磨钢。由于它的加工硬化能力很大,不利于压力加工和切削加工,宜采用铸造成型,一般仅在铸造状态下使用,故属铸钢范围。典型的高锰钢牌号为ZGMn13系列。
水韧处理: ZGMn13钢铸态组织中存在着碳化物,使铸件的性能既硬又脆。欲使高锰钢具有高的韧性和耐磨性,必须获得单一奥氏体组织。将ZGMn13铸件加热至高温(1000~1100℃)保温一段时间,使铸态组织中的碳化物全部溶人基体奥氏体中。然后迅速淬水快冷,使碳化物来不及从过饱和的奥氏体中析出,以获得均匀的单相奥氏体组织,这种热处理称为水韧处理。
高锰钢的高硬度获得: 经过水韧处理的ZGMn13钢的组织为单一的奥氏体,具有高的韧、塑性,硬度一般为180~220 HB范围。在受到剧烈的冲击载荷和严重摩擦力(压应力)作用下,使受力表层发生强烈的塑性变形,迅速造成加工硬化,使硬度高达50~55 HRC,有效地提高了耐磨性,而铸件内部仍保持着原有良好的韧塑性。
水韧处理的质量对铸造高锰钢的耐磨性起着十分关键的作用。若水韧处理后的ZGMn13钢的组织未达到单相奥氏体,表明水韧处理温度过低,使韧性较差。若出现单相奥氏体的晶粒粗大(晶粒度大于5级),则表明水韧处理温度过高,铸件的屈服强度显著下降。
水韧处理后的ZGMn13钢一般不作回火处理,也不适合在250℃以上工作温度下服役。
(二)铸造高锰钢的组织
1.铸态组织 铸造高锰钢平衡态凝固后的最终铸态组织应为:奥氏体基体+少量珠光体型共析组织十大量分布在晶内和晶界上的碳化物, 如图8-5。
图8-5 ZGMn13铸钢铸态组织 (500X) 图8-6 ZGMn13铸钢水韧处理组织 (100X) 2.水韧处理后的组织 正常组织为过饱和的单相奥氏休,晶粒大小不匀,如图8-6。也允许有少量均匀分布的粒状碳化物存在。
3.铸造高锰钢的常见缺陷 主要是分散分布的或串连成断续网状分布的显微疏松、气孔、非金属夹杂物及沿晶裂纹等。
(三)铸造高锰钢的金相检验
应按GB/T 13925-1992《铸造高锰钢金相》标准,进行显微组织、晶粒度和非金属夹杂物级别的评定。 1.显微组织 高锰钢经水韧处理后的组织,应为奥氏体或奥氏体加碳化物。 2.碳化物评级按未溶、析出、过热碳化物分别评定。 3.晶粒度评级按YB/T 5148-1993标准评定。
4.非金属夹杂物(氧化物十硫化物)评级在100倍的Φ80 mm视场中选取最严重的视场评定。
铸铁的分类及金相检验
铸铁是一种含碳量的质量分数大于2.11%的铁碳合金。铸铁中的碳可以固溶、化合和游离三种状态存在。在铸铁的凝固、结晶和随后的热处理过程中,碳的存在状态还会发生变化,从而影响到铸铁的组织和性能。在工业铸铁中,除碳、硅以外,还含有锰、硫、磷等其他元素。特殊性能的合金铸铁分别含有铬、钼、铜、镍、钨、钛、钒等合金元素。铸铁的显微组织主要由石墨和金属基体组织所构成。铸铁金相检验主要检验:石墨的形态、大小和分布状况,以及金属基体中各种组织组成物的形态、分布和数量及其相互配置的情况等,并按相应的金相标准进行各项评级。
由于铸铁组织中的石墨比较柔软,有些石墨的颗粒尺寸较大,甚至结构较松散,应特别注意防止在铸铁试样制备过程中产生石墨剥落、石墨曳尾,或抛光不足等制样缺陷,以免有碍对铸铁石墨和组织的正常检验。 铸铁的分类方法有多种,一般按铸铁中碳的存在状态、石墨的形态特征及铸铁的性能特点可将铸铁分为五类:白口铸铁、灰铸铁、球墨铸铁、可锻铸铁和蠕墨铸铁。
一、白口铸铁
(一)白口铸铁的分类及基本组织
按铸铁的化学成分,可将白口铸铁分为亚共晶白口铸铁、共晶白口铸铁和过共晶白口铸铁。
当共晶成分的铁水冷却时,先发生共晶转变,形成渗碳体和奥氏体的共晶体称莱氏体。当冷却至共析温度以下时,共晶体中的奥氏体转变成珠光体。因此,共晶白口铸铁的莱氏体组织在室温时由渗碳体(白色基体)与珠光体(黑色)组成,见图8-7。亚共晶白口铸铁的组织在室温时为莱氏体加珠光体,其中珠光体呈树枝状分布,见图8-8。而过共晶铸铁的组织为初生渗碳体加莱氏体,见图8-9。
图8-7 共晶白口铸铁组织 (100×) 图8-8 亚共晶白口铸铁组织 (100X) 图8-9 过共品自口铸铁组织 (100X) 由于渗碳体硬而脆.所以生产上使用的白口铸铁大多数采用共晶成分或亚共晶成分。
白口铸铁主要用于要求具有高硬度和高耐磨性的铸件,其应用较多的是激冷白口铸铁和高铬白口铸铁。
(二)激冷白口铸铁的金相检验
激冷白口铸铁(又称冷硬铸铁)是铁水在结晶时,通过对铁水的激冷作用而得到的白口铸铁。激冷白口铸铁一般选用高碳低硅铁水。高的含碳量有利于形成碳化物,低的含硅量可以避免白口区出现石墨。此外,为了获得必要的白口层深度,并细化晶粒.提高珠光体弥散度以提高白口层硬度,往往加人合金元素,如铬、钼、铜、镍等。
生产上,一般采用金属型浇注而获得。由于受金属型冷却能力所限,只能在距激冷面的一定深度内得到白口组织,其内层便出现麻口,并逐渐过渡至灰口。这样,便得到表面高硬度而心部具有一定韧性的激冷白口铸铁。
1.白口层深度 为了保证激冷铸铁的高硬度和高耐磨性,必须确保必要的白口层深度。检验时,应从激冷面开始沿着激冷方向制取金相磨面。
2.白口区的石墨 当铸铁的含硅量过高或浇注温度过低时,往往在白口区内析出石墨。这种石墨一般呈点状,故称点状石墨。点状石墨的存在,将降低白口层的硬度。为此,应对点状石墨的数量加以严格控制。点状石墨数量检验应在铸铁的激冷面上进行。
3.白口组织 共晶激冷铸铁的组织为莱氏体。莱氏体沿激冷方向呈树枝状分布。对于亚共晶激冷铸铁,尚存在呈枝晶分布的珠光体。
(三)高铬白口铸铁的金相检验
高铬白口铸铁的含铬量的质量分数一般为12~34%。高的含铬量不仅可以形成高硬度的合金碳化物,而且可以改变基体组织。当含铬量的质量分数达10时,铸铁中会出现呈菊花状分布的(Cr, Fe)7C3碳化物,其硬度为1200~1600 HV。随着含铬量的不同,可获得三种不同基体的高铬白口铸铁:①含质量分数12 ~28铬的马氏体铸铁;②含质量分数30%~34铬的铁素体铸铁;③含质量分数13%~30%铬和10%~15%镍的奥氏体铸铁。
为了获得马氏体基体组织,高铬白口铸铁必须进行淬火、回火处理。 高铬白口铸铁的金相检验主要是对碳化物和基体的检验。
1.碳化物 高铬白口铸铁中的碳化物,主要作用是提高铸铁的硬度和耐磨性。碳化物应是呈菊花状均匀分布的共晶碳化物。
2.基体组织 对于含铬量较高的铸态型高铬白口铸铁,其铸态基体组织为奥氏体。对于含铬量较低的高铬白口铸铁,其铸态基体为奥氏体和少量马氏体和珠光体。
(四)白口铸铁的热处理
白口铸铁热处理的目的是消除内应力,提高耐磨性或冲击韧性,以适应在冲击载荷下工作,扩大应用范围。常用的热处理有:消除内应力退头、淬火和回火及等温淬火等。
1.消除内应力退火 它大多应用于高合金白口铸铁,将铸铁加热到800~900℃保温一定时问后随炉冷却以消除铸件的内应力。
2.白口铸铁的淬火与回火 它主要应用于Mn-Mo、Mn-Si、Mn-Cr、Cr-Mo、Ni-Cr-Mo等合金白口铸铁,在吹风冷却,甚至在空气冷却时就可以获得马氏体加渗碳体加残留奥氏体,或获得贝氏体加渗碳体加残留奥氏体的基体组织,再通过低温回火得以提高综合力学性能。
3.白口铸铁的等温淬火 白口铸铁通过等温淬火则可获得下贝氏体加渗碳体加残留奥氏体的组织,这种组织具有较好的综合力学性能,特别是耐冲击性。
二、灰铸铁
灰铸铁是指金相组织中石墨呈片状的铸铁。由于这种铸铁具有生产简便、成本低和足够高的使用性能等特点,所以它是工业上应用最广泛的一种铸铁材料。按照灰铸铁的化学成分和性能特点,将其分为普通灰铸铁、合金灰铸铁和特殊性能灰铸铁。生产上,通过孕育处理而获得的高强度铸铁又称孕育铸铁。
(一)灰铸铁的牌号及基本组织
国家标准GB/T 9439-1988《灰铸铁件》,根据Φ30 mm的单铸试棒的抗拉强度分级,规定了HT100、HT150、HT200、HT250、HT300、HT350六级灰铸铁的牌号。各牌号中的数字为其单铸试棒具有的抗拉强度Rm (MPa)。 不论灰铸铁的成分如何,其平衡冷却的室温组织均为石墨和铁素体。受到某些因素的影响(如化学成分和冷却速度等),则可能出现碳化物和磷共晶。因此,铸铁结晶后的组织可能是珠光体和铁素体,或全部珠光体。也有可能存在共晶碳化物或二次碳化物,甚至初生碳化物。可能还存在磷共晶。为了确保灰铸铁强度,一般需要获得珠光体基体。
灰铸铁中的片状石墨在空间的分布实际上并非是孤立的片状,而是以一个个石墨核心出发,形成一簇簇不同位向的石墨分枝,以构成一个个空间立体结构。同一簇石墨与其间的共晶奥氏体构成一个共晶团。铸铁凝固之后,便由这种相互毗邻的共晶团所组成。
(二)灰铸铁的金相检验
灰铸铁金相检验必须按照国家标准GB/T 7216-1987《灰铸铁金相》的规定方法和内容进行。
灰铸铁的金相试块应取自抗拉试棒距断口10 mm处,或从试棒的底部切除10 mm后再取金相检验试块。试块尺寸应包括试棒半径的一半。由于特殊需要,从铸件上取样时,应在报告中注明取样部位和壁厚等情况,但不允许直接从浇口和冒口上切取金相试块。 1.灰铸铁石墨的检验
(1) 石墨分布。标准规定灰铸铁石墨检验应在未侵蚀的试样上进行,观察放大倍数为100倍。将 石墨分布分为A型、B型、C型、D型、E型和F型。如图8-10所示。 1) 片状(A型)石墨:特征是片状石墨均匀分布。
2) 菊花状(B型)石墨:特征是片状与点状石墨聚集成菊花状。其心部为少量点状石墨,外围为卷曲片状石墨。这种石墨一般铁水经孕育处理后在较大的过冷度下形成。
3) 块片状(C型)石墨:特征是部分带尖角块状、粗大片状初生石墨及小片状石墨。 4) 枝晶点状(D型)石墨:特征是点状和片状枝晶间石墨呈无向分布。 5) 枝晶片状(E型)石墨:特征是短小片状枝晶间石墨呈有方向分布。
6) 星状(F型)石墨:特征是星状(或蜘蛛状)与短片状石墨混合均匀分布。
生产中,在同一铸件的同一部位上往往存在几种形状的石墨。从石墨分布形状对灰铸铁性能的影响看,一般以A型石墨和B型石墨为好。
片状(A型)石墨 菊花状(B型)石墨 块片状(C型)石墨
枝晶点状(D型)石墨 枝晶片状(E型)石墨 星状(F型)石墨 图8-10 灰铸铁石墨分布形态 100×
(2)石墨长度。在灰铸铁中,石墨长度也是影响铸铁力学性能的重要因素。抗拉强度随石墨长度的增加而降低。国家标准将石墨长度分为八级。
2.灰铸铁基体组织的检验 灰铸铁的基体组织一般为珠光体或珠光体加铁素体。在某些情况下,也可以得到贝氏体或马氏体组织。此外,由于受化学成分和冷却速度的影响,在铸铁结晶后,可能出现碳化物和磷共晶。
(1)珠光体粗细和珠光体数量。灰铸铁的珠光体一般呈片状,片状珠光体的粗细可以用渗碳体与铁素体的片间距来表示。珠光体的片间距愈小,铸铁的强度和硬度愈高。 珠光体数量是指珠光体和铁素体的相对量。在灰铸铁中,珠光体数量愈多,铸铁的强度、硬度和耐磨性愈高。
(2)碳化物的分布形态和数量。生产中的大多数普通灰铸铁件碳化物含量均较少,但在合金铸铁和耐磨铸铁中,会出现较多碳化物。根据碳化物的分布形态,可分为条状碳化物、块状碳化物、网状碳化物和莱氏体状碳化物。虽然碳化物具有很高的硬度,却降低铸铁的韧性,并恶化加工性能。国家标准将碳化物分为1--6级,级别的名称依次为:碳
1、碳
3、碳
5、碳
10、碳15,碳20。各级名称中的数字表示该级碳化物数量体积分数(%)。
(3)磷共晶类型分布形态和数量。根据磷共晶的形态特征,将磷共晶分为二元磷共晶、三元磷共晶、二元磷共晶-碳化物复合物和三元磷共晶-碳化物复合物四种类型。 在金相检验中,为了鉴别碳化物和磷共晶,也可以采用染色法。
一般来说,灰铸铁的磷共晶数量随铸铁含磷量的增加而增多。磷共晶硬而脆,显著降低铸铁的韧性。国家标准将磷共晶数量分为1~6级,级别名称依次为磷
1、磷
2、磷4、磷
6、磷8和磷10。各级名称中的数字表示该级磷共晶的近似含量。
(4)灰铸铁共晶团的检验。灰铸铁在共晶转变时,共晶成分的铁水形成由石墨和奥氏体所组成的共晶团。由于共晶团边界上常富集一些夹杂物和偏析物以及某些低熔点共晶体,所以可以利用适当的侵蚀剂将共晶团边界显示出来。
灰铸铁共晶团的大小反映铸铁机械性能的高低。在其他条件相同的情况下,共晶团愈细小,铸铁的强度愈高。
三、球墨铸铁
球墨铸铁的石墨呈球状,或接近球状,因此铸铁中因石墨引起的应力集中现象远比片状石墨的灰铸铁小。此外,球状石墨不像片状石墨那样对金属基体存在严重的割裂作用,这就为通过热处理以提高球墨铸铁基体组织性能,从而发掘其性能潜力提供了条件。为此,对球墨铸铁的石墨和基体组织的检验,是球墨铸铁生产的一个重要环节。
根据球墨铸铁的成分、力学性能和使用性能,一般将其分为普通球墨铸铁、高强度合金球墨铸铁和特殊性能球墨铸铁。
(一)球墨铸铁的牌号及基本组织
球墨铸铁的牌号是根据其所具有的力学性能指标而划分的。共分为8种牌号,即QT400-
18、QT400-
15、QT450-
10、QT500-
7、QT600-
3、QT700-
2、QT800-
2、QT900-2。牌号中短划线前面的数字为该牌号所具有的抗拉强度Rm (MPa),后面的数字为延伸率A(%)。各种牌号的球墨铸铁有其相应的金属基体组织:QT400-18 , QT400-
15、QT450-10主要为铁素体;QT500-7为铁素体+珠光体;QT600-3为珠光体十铁素体;QT700-2为珠光体;QT800-2为珠光体或回火组织;QT900-2为贝氏体或回火组织。此外,还可能存在碳化物及磷共晶等组织。
(二)球墨铸铁的石墨及其检验
1.石墨形态 所谓石墨形态,是指单颗石墨的形状。实际上,球墨铸铁中的石墨并不全是理想的球状。由于不同形态的石墨对金属基体连续性的割裂程度不同,因此石墨形态是影响球墨铸铁力学性能和使用性能的重要因素。
GB/T 9441-1988《球墨铸铁金相检验》根据石墨面积率(单颗石墨的实际面积与其最小外接圆面积的比率)值将球墨铸铁的石墨形态分为球状、团状、团絮状、蠕虫状和片状。
2.石墨球化率及其确定 在金相检验中,通常所见到的是几种形态的石墨共存。在这种情况下,评定石墨的球化质量须用球化率来解决。所谓球化率,是指在规定的视场内,所有石墨球化程度的综合指标。它反映该视场内所有石墨接近球状的程度。
国家标准根据石墨形态及其分布和球化率,将球墨铸铁石墨球化分为1-6级。标准还列出了各球化级别的标准等级图片,在使用时,可对照标准等级图片进行评级。
球墨铸铁的力学性能在很大程度上决定于球化率。一般来说,在其他条件相同的情况下,球化率愈高,力学性能也高。
3.石墨大小 石墨大小也会影响球墨铸铁的力学性能。石墨球细小可减小由石墨引起的应力集中现象。而且,细小的石墨球往往具有高的球化率。因此,均匀、圆整、细小的石墨可以使球墨铸铁具有高的强度、塑性、韧性和疲劳强度。国家标准参照国际标准中关于石墨大小的分级方法,将石墨大小分为六级。
(三)球墨铸铁的基体组织及其检验
球墨铸铁铸态下的基体组织为铁素休和珠光体。大多数球墨铸铁有必要进行热处理改善其基体组织,从而达到所需要的性能。球墨铸铁的正火处理,可以消除铸造应力,细化晶粒,而且可以获得全部珠光体或以珠光体为主的基体组织。铁素体基体组织往往是通过退火来达到的。此外,由于受到化学成分和冷却速度的影响,在基体组织中,可能出现碳化物和磷共晶。在某些高合金含量的特殊性能球墨铸铁的基体中,还会出现马氏体和奥氏体。在有些情况下,一些合金球墨铸铁(如铜钼合金球墨铸铁)经正火处理后,会在晶界处出现马氏体或贝氏体组织,这将增加球墨铸铁的脆性。
在基体组织中,各种相(或组织)的形态、分布和相对量对铸铁性能的影响起着决定性的作用。这正是金相检验所要解决的问题。
GB/T 9441-1988《球墨铸铁金相检验》对于球墨铸铁铸态和正火、退火态的基体组织的检验作了明确规定。 1. 珠光体粗细和珠光体数量 在一般情况下,球墨铸铁的珠光体呈片状。按照珠光体的片间距, 将其分为粗片状珠光体、片状珠光体和细片状珠光体。珠光体的粗细虽对球铁性能有影响,但其影响的程度远较珠光体数量和球化率对性能的影响来得小。珠光体数量是指珠光体与铁素体的相对量。对于高
(a)铁素体基体 (b)铁素体+珠光体基体 (c)珠光体基体 图8-11 不同基体的球墨铸铁
强度球铁,应确保高的珠光体数量;而对于高韧性球铁,则应确保高的铁素体数量。
在铸态或完全奥氏体化正火后,球墨铸铁的铁素体呈牛眼状(图8-11)。它在球墨铸铁中很常见。 国家标准将珠光体数量分为珠95~珠5共十二级。
2. 分散分布的铁素体数量 如果采用直接加热至三相区进行部分奥氏体化正火工艺,则铁素体呈 分散分布的块状,如图8-12所示。当采用完全奥氏体化后炉冷至三相区保温,进行二阶段正火工艺时,
图8-12 块状铁素体 (100×) 图8-13 网状铁素体 (100×)
铁素体呈分散分布的网状,如图8-13 所示。国家标准按块状和网状两个系列,各分为六级,依次为铁
5、铁
10、铁
15、铁20、铁25和铁30。各级别名称中的数字表示该级分散分布铁素体数量的体积分数(%)的近似值。
3.磷共晶数量 在铸铁中,磷共晶作为一种低熔点组织,总是分布在晶界处和铸件最后凝固的热节部位。球墨铸铁中的磷共晶,多为由奥氏体、磷化铁和渗碳体所组成的三元磷共晶。由于磷共晶显著降低冲击韧性,一般情况下,球墨铸铁的磷共晶含量的体积分数应控制在2%以下。
在球墨铸铁中,磷共晶数量对性能的影响比磷共晶形态对性能的影响要显著。国家标准中的磷共晶数量分为五级,依次为磷0.5、磷
1、磷1.5、磷
2、磷3。各级别名称中的数字表示该级磷共晶数量的体积分数(%)的近似值。
4.渗碳体数量 在球墨铸铁结晶后,往往在组织中出现一定数量的渗碳体。严重时,出现莱氏体。渗碳体显著降低球墨铸铁的塑性和韧性,并恶化加工性能。在球墨铸铁的生产中,若渗碳体作为硬化相单独存在时,其含量的体积分数一般应小于5%作为控制界限。对于某些高韧性球墨铸铁,应作更严格的控制。 国家标准将渗碳体数量分为五级,依次为渗
1、渗
2、渗
3、渗5和渗10。各级别名称中的数字表示该级渗碳体数量的体积分数(%)的近似值。
(四)球墨铸铁等温淬火的组织及检验
1.等温淬火的组织 当等温温度比较低时,获得针状贝氏体,也称下贝氏体。针状贝氏体经侵蚀后在显微镜下呈针状。针状贝氏体具有高的强度和硬度,但塑性和韧性较低。当等温温度比较高时,获得羽毛状贝氏体也称上贝氏体。这种组织总伴有较多的高碳残留奥氏体,羽毛状贝氏体具有较高的综合力学性能。当等温温度在Ms附近时,获得针状贝氏体与马氏体的混合组织,在部分奥氏体化等温淬火的条件下,获得贝氏体与铁素体的混合组织,前者强度、硬度高,脆性大,而后者虽然强度稍低,但塑性和韧性较高。 检验球墨铸铁等温淬火组织,可按JB/T 3021-1981《稀土镁球墨铸铁等温淬火金相标准》进行。 2.贝氏体长度 奥氏体化温度愈高,则转变成贝氏体的尺寸愈长。在贝氏体形态及其他条件相同的情况下,贝氏体尺寸愈长,力学性能愈低。JB/T 3021-1981标准将贝氏体的长度分为五级。
3.白区数量 所谓白区,是指球墨铸铁经等温淬火后,集中分布在共晶团边界上尚未转变的残留奥氏体和淬火马氏体。试样经侵蚀后呈白色断续网络状。试验表明,奥氏体化温度愈高,等温转变愈不充分,铸铁中稳定奥氏体的合金元素含量愈高,则白区数量愈多。
白区增加球墨铸铁的脆性,为此,应控制白区的数量。标准将白区数量分为四级。
4.铁素体数量 球墨铸铁等温淬火后的铁素体一般出现于部分奥氏体化的淬火状态下,其数量决定于三相区内未溶铁素体的多寡。一般来说,少量铁素体的存在,虽使强度和硬度有所降低,但使塑性、韧性和疲劳强度有所提高。标准中将铁素体数量分为四级。
(五)球墨铸铁几种常见的铸造缺陷
1.球化不良和球化衰退 球化不良和球化衰退的显微组织特征是除球状石墨外,出现较多蠕虫状石墨。球化不良和球化衰退的球墨铸铁铸件只能报废。
2.石墨飘浮 石墨飘浮的金相组织特征是石墨大量聚集,往往出现开花状。在壁厚较大的铸件上容易出现。石墨飘浮降低铸件的力学性能。
3.夹渣 球墨铸铁的夹渣一般是指呈聚集分布的硫化物和氧化物。在显微镜下,为黑色不规则形状的块状物或条带状物,常见于铸件的上表面或泥芯的下表面。具有夹渣的铸件,力学性能低。严重时,使铸件渗漏。
4.缩松 缩松是指在显微镜下所见到的微观缩孔。缩松分布在共晶团的边界上,呈向内凹陷的黑洞。缩松破坏了金属的连续性,降低力学性能,严重时引起铸件渗漏。
5.反白口 反白口的组织特征是在共晶团的边界上出现许多呈一定方向排列的针状渗碳体。一般位于铸件的热节部位。在反白口区域内,往往都存在较多的显微缩松。
四、可锻铸铁
可锻铸铁是将铸态白口铸铁毛坯经过石墨化或脱碳处理而获得的铸铁。可锻铸铁具有较高的强度及良好的塑性和韧性,故也称延展性铸铁。
按照可锻铸铁的化学成分、热处理工艺及由此而导致的组织和性能之别,将其分为黑心可锻铸铁和白心可锻铸铁。黑心可锻铸铁是由白口铸铁毛坯经石墨化退火后获得团絮状石墨。白心可锻铸铁是由白口铸铁毛坯经高温氧化脱碳后获得全部铁素体或铁素体加珠光体组织(心部可能尚有渗碳体或石墨)。在黑心可锻铸铁中,又分为黑心铁素体可锻铸铁和黑心珠光体可锻铸铁。我国应用最多的是黑心铁素体可锻铸铁。其组织是团絮状石墨和铁素体。由于团絮状石墨对金属基体的割裂作用远比片状石墨小,因此可锻铸铁的性能比灰铸铁高。然而,不如球墨铸铁。
黑心可锻铸铁主要用于承受冲击、震动及扭转载荷下的零件,如汽车后桥、轮壳,低压阀门、水暖零件和机床附件等。
(一)黑心可锻铸铁的牌号及基木性能
我国的黑心可锻铸铁的牌号是按其力学性能指标划分的,共分为八级,即KTH300-0
6、KTH300-0
8、KTH350-
10、KTH370-
12、KTH450-0
6、KTH550-0
4、KTH650-0
2、KTH700-02。牌号中前面的数字表示其具有的抗拉强度Rm (MPa),后面的数字为其伸长率A(%)值。
(二)黑心可锻铸铁的退火
(a) 铁素体基体可锻铸铁 (b)珠光体基体可锻铸铁 图8-14 不同基体的可锻铸铁
黑心可锻铸铁的石墨化退火需要很长的时间。铸铁化学成分、退火设备和退火工艺都是影响退火效率的重要因素。一般情况下,可选用较高的退火温度,但退火温度过高,会使石墨形状恶化。
1.对铸态白口铸铁的要求 在化学成分的选择上,一般选用低碳和低硅的成分,以利于铸态下能获得无铸造缺陷的白口铸铁毛坯,又利于在热处理时,在保证充分石墨化的前提下尽量缩短退火时间以及达到预定的力学性能。
2.退火工艺 生产中常见的黑心可锻铸铁的退火工艺分为五个阶段。
(1)升温阶段。从室温加热至950℃左右。在这一阶段中,白口铸铁组织中的珠光体转变成奥氏体。 (2)第一阶段石墨化。在950℃左右保温,使渗碳体分解,析出石墨。第一阶段石墨化完成之后,铸铁在高温时的组织是石墨和奥氏体。
(3)中间降温阶段。从高温(约950℃左右)冷却至稍低于共析温度的过程中,碳从奥氏体中析出,并依附在原有的团絮状石墨上,最后,奥氏体转变成珠光体。在这一阶段内,冷速太快,会出现二次渗碳体。冷速太慢,会延长退火时间。
(4)第二阶段石墨化。在710~730℃保温,主要是共析渗碳体的分解。所析出的碳扩散至原有石墨表面上。在随后的冷却过程中,奥氏体转变成铁素体。
这一阶段也可以从高温炉冷至780℃左右,以缓慢的冷却速度通过共析区,使奥氏体直接转变成铁素体和石墨。
(5)冷却阶段。第二阶段石墨化后,炉冷至650℃左右后,出炉空冷。空冷的目的是防止回火脆性。如果铸件在450~550℃不快速冷却,将在铁素体晶界上析出三次渗碳体,使铸件产生白脆性。
3.加速石墨化退火的工艺措施 可锻铸铁的退火时间长,能耗大。缩短退火周期,提高退火质量对可锻铸铁的生产具有重要意义。对铁水进行孕育处理,通过孕育剂的作用,既能保证铁水在凝固时得到全部白口组织,又能使白口毛坯在退火时容易石墨化。
(三)黑心可锻铸铁的石墨及检验
白口铸铁在退火过程中,退火石墨也要经过石墨形核和石墨长大两个阶段。在正常的退火温度下,使退火石墨呈团絮状。如果退火温度过高,或含硅量过高,使退火石墨的紧密度降低,而出现絮状或聚虫状石墨。 1.石墨形状 在黑心可锻铸铁中,常见的石墨有:团球状、团絮状、絮状、聚虫状、枝晶状。 JB/T2122-1977《铁素体可锻铸铁金相标准》根据视场中各种形状石墨的数量,将石墨形状分为五级。 2.石墨分布及石墨颗数 标准将石墨分布和石墨颗数分别分为三级和五级。
(四)黑心可锻铸铁的基体组织及检验
为了保证可锻铸铁高的塑性和韧性,其基体组织应为铁素体。在生产过程中由于某些工艺因素的影响,可能会出现其他组织。
对黑心可锻铸铁基体组织的检验,主要是对珠光体和渗碳体的残余量及表皮层厚度的检验。
1.珠光体残余量 珠光体残余是由于第二阶段石墨化退火不充分所致。标准将珠光体残余量分为五级。 2.渗碳体残余量 渗碳体残余是由于第一阶段石墨化退火不充分所致。此外,在中间降温阶段冷却太快,会出现二次渗碳体。将渗碳体残余量体积分数分为小于或等于2%和大于2%两个级别。
3.表皮层厚度 黑心可锻铸铁的表皮层是指出现在铸件外缘的珠光体层或铸件外缘的无石墨铁素体层。表皮层的形成是铸件在第一阶段石墨化退火温度过高,使铸件表皮奥氏体强烈脱碳所引起的。将表皮层厚度分为四级。
在对黑心可锻铸铁的石墨及基体组织进行金相检验时,可按照JB/T 2122-1977标准中对各检验项目所规定的检验方法及组织特征的文字说明及其相应的标准图片对照比较进行级别评定。
第12篇:国内金相检验标准(精)[定稿]
一.钢材
(1) 低倍检验
1 GB/T 226-1991 钢的低倍组织及缺陷酸蚀检验法 2 GB/T 1979-2001 结构钢低倍组织缺陷评级图 3 GB/T 4236-1984 钢的硫印检验方法 4 GB/T 1814-1979 钢材断口检验法
5 GB/T 2971-1982 碳素钢和低合金钢断口检验方法 6 YB/T 731-19870 塔型车削发纹检验法
7 YB/T 4002-1992 连铸钢方坯低倍组织缺陷评级图 8 YB/T 4003-1991 连铸钢板坯缺陷硫印评级图
9 YB/T 4061-1991 铁路机车、车轴用车轴(含硫印缺陷评级图) 10 CB/T 3380-1991 船用钢材焊接接头宏观组织缺陷酸蚀试验法 (2) 基础标准
1 GB/T/T13298-91 金属显微组织检验方法 2 GB/T224-1987 钢的脱碳层深度测定法
3 GB/T10561-1988 钢中非金属夹杂物显微评定方法 4 GB/T 6394-2002 金属平均晶粒度测定方法 5 GB/T/T13299-1991 钢的显微组织(游离渗碳体、带状组织及魏氏组织)评定方法 6 GB/T/T13302-1991 钢中石黑碳显微评定方法
7 GB/T4335-1984 低碳钢冷轧薄板铁素体晶粒度测定法 8 JB/T/T5074-1991 低、中碳钢球化体评级
9 ZBJ36016-1990 中碳钢与中碳合金结构钢马氏体等级 10 DL/T 652-1998 金相复型技术工艺导则 (3) 不锈钢
1 GB/T6401-86 铁素体奥氏体型双相不锈钢α-相面积含量金相测定法 2 GB/T1223-75 不锈耐酸钢晶间腐蚀倾向试验方法
3 GB/T1954-80 铬镍奥氏体不锈钢焊缝铁素体含量测量方法 4 GB/T/T13305-91 奥氏体不锈钢中α-相面积含量金相测定法 (4) 铸钢
1 GB/T8493-87 一般工程用铸造碳钢金相 2 TB/T/T2451-93 铸钢中非金属夹杂物金相检验 3 TB/T/T2450-93 ZG230-450铸钢金相检验 4 GB/T/T13925-92 高锰钢铸件金相
5 GB/T5680-85 高锰钢铸件技术条件(含金相组织检验) 6 YB/T/T036.4-92 冶金设备制造通用技术条件高锰钢铸件(高锰钢金相组织检验) 7 JB/T/GQ0614-88 熔模铸钢ZG310-570正火组织金相检验 (5) 化学热处理及感应淬火
1 GB/T11354-89 钢铁零件 渗氮层深度测定和金相组织检验 2 GB/T9450-88 钢件渗碳淬火有效硬化层深度的测定和校核 3 QCn29018-91 汽车碳氮共渗齿轮金相检验
4 JB/T4154-85 25MnTiBXt钢碳氮共渗齿轮金相检验标准 5 NJ251-81 20MnTiBRe钢渗碳齿轮金相组织检验 6 ZB/T04001-88 汽车渗碳齿轮金相检验
7 TB/T/T2254-91 机车牵引用渗碳淬硬齿轮金相检验 8 JB/T/T6141.1-92 重载齿轮渗碳层球化处理后金相检验 9 JB/T/T6141.3-92 重载齿轮渗碳金相检验
10 JB/T/T6141.4-92 重载齿轮渗碳表面碳含量金相判别法
11 GB/T5617-85 钢的感应淬火或火焰淬火有效硬化层深度的测定 12 GB/T9451-88 钢件薄表面总硬化层深度或有效硬化层深度的测定 13 ZB/J36009-88 钢件感应淬火金相检验
14 ZB/J36010-88 珠光体球墨铸铁零件感应淬火金相检验 15 NJ304-83 渗碳齿轮感应加热淬火金相检验 16 JB/T2641-79 汽车感应淬火零件金相检验 17 CB/T3385-91 钢铁零件渗氮层深度测定方法 (6) 轴承钢
1.YJZ84高碳铬轴承钢(含酸浸低倍组织、非金属夹杂物、显微孔隙、退火组织、碳化物不均匀性、碳化物带状、碳化物液析评级图) 2.GB/T9-68铬轴承钢技术条件(含低倍缺陷、非金属夹杂物、退火组织、碳化物网状、碳化物液析评级图) 3.GB/T3086-82高碳铬不锈轴承钢技术条件(含酸浸低倍组织、火组织、共晶碳化物不均匀度、非金属夹杂物、微孔隙评级图) 4.YB/T688-76高温轴承钢Cr4Mo4V技术条件(含碳化物不均匀度评级图) 5.JB/T1255-91高碳铬轴承钢滚动轴承零件热处理技术条件(含退火组织、淬回火组织、碳化物网状、断口评级图) 6.ZB/J36001-86滚动轴承零件渗碳热处理质量标准(含粗大碳化物、渗碳表面层淬 回火组织、心部组织、网状碳化物评级图) 7.JB/T1460-92高碳铬不锈钢滚动轴承零件热处理技术条件(含退火组织、淬回火组织、断口评级图) 8.JB/T2850-92Cr4Mo4V高温轴承钢滚动轴承零件热处理技术条件(含淬火组织、淬回火组织评级图) 9.JB/T/T6366-9255SiMoVA钢滚动轴承零件热处理技术条件(含退火组织、淬回火组织、渗碳淬回火组织评级图) (7) 工具钢
1 GB/T1298-77 碳素工具钢技术条件(含珠光体组织、网状碳化物评级图) 2 GB/T1299-85 合金工具钢技术条件(含珠光体组织、网状碳化物、共晶碳化物不均匀) 3 YB/T12-77 高速工具钢技术条件(含低倍碳化物剥落、共晶碳化物不均匀度评级图) 4 ZB/J36003-87 工具热处理金相检验标准
5 GB/T4462-84 高速工具钢大块碳化物评级图 (8) 零部件专用标准
1 GB/T/T13320-91 钢质模锻件金相组织评级图及评定方法 2 ZB/J18004-89 传动用精密滚子链和套筒链零件金相检验 3 ZB/J26001-88 60Si2Mn钢螺旋弹簧金相检验 4 ZB/J94007-88 柴油机喷嘴偶件、喷油泵柱塞偶件、喷油泵出油阀偶件金相检验 5 JB/T3782-84 汽车钢板弹簧金相检验标准 6 NJ309-83 内燃机连杆螺柱金相检验标准 7 NJ326-84 内燃机活塞销金相检验标准 8 JB/T/T6720-93 内燃机排气门金相检验标准 9 JB/T/NQ180-88 内燃机气门座金相检验
10 JB/T/GQ1050-84
45、40Cr钢淬火马氏体金相检验 11 JB/T/GQ1148-89 机床用40Cr钢调质组织金相检验
12 JB/T/GQ·T1150-89 机床用38CrMoAl钢验收技术条件及调质后金相检验
13 JB/T/GQ·T1151-89 机床用45钢调质组织金相检验
14 NJ396-86 低淬透性含钛优质碳素结构钢齿轮金相检验 15 JB/T/T5664-91 重载齿轮失效判据
16 CJ/T 31-1999 液化石油气钢瓶金相组织评定
二.铸铁
(1) 基础标准
1 GB/T7216-87 灰铸铁金相
2 GB/T9441-88 球墨铸铁金相检验 3 JB/T3892-84 蠕墨铸铁金相标准
4 JB/T2212-77 铁素体可锻铸铁金相标准
5 JB/T3021-81 稀土镁球墨铸铁等温淬火金相标准
6 JB/T/Z303-87 灰铸铁与球墨铸铁断口扫描电镜分析图谱 7 CB/T1165-88 船用灰铸铁金相标准 8 CB/T1030-83 蠕虫状石墨铸铁金相检验 9 TB/T/T2255-91 高磷铸铁金相 10 TB/T/T2449-93 蠕墨铸铁金相检验 (2) 零部件专用标准
1 GB/T2805-81 内燃机单体铸造活塞环金相检验(JB/T/T6016-92) 2 GB/T3509-83 内燃机筒体铸造活塞环金相检验(JB/T/T6290-92) 3 JB/T2330-93 内燃机高磷铸铁缸套金相标准
4 NJ325-84 内燃机硼铸铁单体铸造活塞环金相标准 5 JB/T/T5082-91 内燃机硼铸铁气缸套金相检验 6 JB/T/Z179-82 中锰抗磨球墨铸铁金相标准 7 JB/T/NQ100-86 内燃机钒钛铸铁气缸套金相检验
8 JB/T/NQ178-88 内燃机钒钛铸铁单体铸造活塞环金相检验 9 JB/T/T6724-93 内燃机球墨铸铁活塞环金相检验
10 JB/T3934-85 汽车、摩托车发动机单体铸造活塞环金相检验 11 ZB/T T12007-89 汽车、摩托车发动机球墨铸铁活塞环金相标准 12 ZB/T T06002-89 汽车发动机镶耐磨圈活塞金相标准
13 ZB/U05004-89 中、大功率柴油机离心铸造气缸套金相检验 14 TB/T/T2253-91 球墨铸铁活塞金相检验
15 TB/T/T2448-93 合金灰铸铁单体铸造活塞环金相检验 16 YB/T4052-91 高镍铬无限冷硬离心铸铁轧辊金相检验 17 JB/T/T6954-93 灰铸铁接触电阻加热淬火质量检验和评级
18 CB/T/T 3903-1999 中、大功率柴油机离心铸造气缸套金相检验 三.表面处理
1 GB/T4677.6-84 金属和氧化覆盖厚度测试方法-截面金相法
2 GB/T5929-86 轻工产品金属镀层和化学处理层的厚度测试方法-金相显微镜法 3 GB/T6462-86 金属和氧化物覆盖层-横断面厚度显微镜测量方法 4 GB/T6463-86 金属和其他无机覆盖层-厚度测量方法评述
5 GB/T9790-88 金属覆盖层及其他有关覆盖层维氏和努氏显微硬度试验 6 GB/T11250.1-89 复合金属覆盖层厚度测定-金相法 7 JB/T/T5069-91 钢铁零件渗金属层金相检验方法 8 JB/T/T6075-92 氧化钛涂层金相检验方法
9 ZBJ92004-87 内燃机精密电镀减摩层轴瓦检验标准 四.铝合金及铜合金
1 GB/T3246-82 铝及铝合金加工制品显微组织检验方法 2 GB/T3247-82 铝及铝合金加工制品低倍组织检验方法 3 GB/T10849-89 铸造铝硅合金变质 4 GB/T10850-89 铸造铝合金过烧 5 GB/T10851-89 铸造铝合金针孔 6 GB/T10852-89 铸造铝铜合金晶粒度 7 GB/T7998-87 铝合金晶间腐蚀测定法
8 GB/T8014-87 铝及铝合金阳极氧化阳极氧化膜厚度的定义和有关测量厚度的规定
9 GB/T3508-83 内燃机铸造铝活塞金相检验 10 QJ1675-89 变形铝合金过烧金相试验方法
11 JB/T3932-85 汽车、摩托车发动机铸造铝活塞金相标准 12 JB/T/NQ179-88 内燃机稀土共晶铝硅合金金相检验 13 JB/T/T5108-91 铸造黄铜金相
14 QJ2337-92 铍青铜的金相检验方法 15 YB/T797-71 单相铜合金晶粒度测定法
16 YB/T731-70 电真空器件用无氧铜含氧量金相检验法 17 ZB/T12003-87 汽车发动机轴瓦铜铅合金金相标准 18 NJ355-85 内燃机铸造铜铅合金轴瓦金相检验标准 19 CB/T1196-88 船舶螺旋浆用铜合金金相含量金相测定方 五.粉未冶金及硬质合金
1 GB/T9095-88 烧结铁基材料-渗碳或碳氮共渗硬化层深度的测定 2 JB/T2798-81 铁基粉未冶金烧结制品金相标准 3 JB/T2869-81 烧结金属材料密度的测定 4 JB/T2867-81 烧结金属材料表观硬度的测定 5 ZBH72007-89 烧结金属摩擦材料金相检验法
6 ZBH72012-90 碳化钨钢结硬质合金金相试样制备方法 7 GB/T3488-83 硬质合金-显微组织的金相测定
8 GB/T3489-83 硬质合金-孔隙度和非化合碳的金相测定 六.有色合金及稀有金属
1 GB/T4296-84 镁合金加工制品显微组织检验方法 2 GB/T4297-84 镁合金加工制品低倍组织检验方法
3 GB/T1554-79 硅单晶(111)晶面位错蚀坑显示测量方法 4 GB/T3490-83 含铜贵金属材料氧化亚铜金相检验方法 5 GB/T4194-84 钨丝蠕变试验、高温处理及金相检验方法 6 GB/T4197-84 钨钼及其合金的烧结坯条、棒材晶粒度测试方法 7 GB/T5168-85 两相钛合金高、低倍组织检验方法
8 GB/T5594.8-85 电子元器件结构陶瓷材料性能测试方法-显微结构的测定 9 GB/T6623-86 抛光硅片表面热氧化层错的测试方法 10 GB/T8755-88 钛及钛合金术语和金相图谱 11 GB/T8756-88 锗单晶缺陷图谱
12 GB/T8760-88 砷化镓单晶位错密度的测量方法 13 GB/T11809-89 核燃料棒焊缝金相检验
14 YB/T935-78 贵金属及其合金的金相试样制备方法 15 YB/T732-71 铜、镍及其合金管材和棒材断口检验方法 16 JB/T3657-84 汽车发动机轴瓦锡基和铅基合金金相标准 17 GB/T1156-87 ChSnSb11-6合金轴瓦金相评级 18 CB/T1156-92 锡基轴承合金金相检验 七.其他有关标准
1 ZB/N33002.1-1988 金相显微镜系列
2 ZB/N33002.2-1988 金相显微镜技术条件
3 GB/T6846-1986 确定暗室照明安全时间的方法 4 GB/T/T4342-1991 金属显微维氏硬度试验方法 5 GB/T/T15749-1995 定量金相手工测定方法
6 GB/T/T17359-1998 电子探针和扫描电镜,X射线能谱定量分析通则
7 GB/T 18876.1-2002 应用自动图像分析测定钢和其它金属中金相组织、夹杂物含量和级别的标准试验方法
第13篇:JX_金相检验软件系统_使用说明
一、系统简介
㈠ 基本功能:
《金相检验软件系统》是为从事金相检验的单位或个人专门开发的一套计算机软件系统,它的基本原理是:用视频采集卡或数码相机等硬件设备,采集到金相显微镜中的金相图片,再对该图片进行处理和分析,得到相关检验结果。该软件的主要功能如下: ⒈ 自动评级:
本软件以检验标准为依据,开发出了百余个类别两百余种软件功能模块,用户可根据需要,选择检验项目,在本软件的帮助下,完成检验工作。目前本系统的软件模块清单见附件。本软件模块的评级方式有以下三种:
自动评级:软件可自动得出最终分析结果;
辅助评级:软件可得出和分析结果有一定联系的参数;
比较评级:将采集下来的试样图像和标准图库进行比较,人工作出结果判断。 ⒉ 新建报告:
可按用户需求制作报告文档的录入界面、软件可自动生成电子报告文档,并提供报告的保存和打印功能。 ⒊ 打开报告:
打开并浏览已经保存的报告文件。 ⒋ 几何测量:
本软件提供了“直线”、“矩形”、“圆”、“多边形”、“角度”等多种测量工具及测量方法,可完成长度、面积、角度等测量工作。 ⒌ 查看图库:
用户可选择查看本软件收录的所有金相图谱,本软件金相图谱由用户提供原始资料,由我方录入。 ⒍ 定倍打印:
可一次装入多副图片,并可对其进行图像处理,设置说明文字和打印版面,进而生成一份适合各种行业特殊要求的报告文件。 ⒎ 脱机拼图
将多张图片拼接在一起(要求具体见图像拼接),图像拼接有“自动”和“手动”两种方式,如采用“自动”方式,则被拼接图像需要有重合部分;
⒏ 动态测量
在DirectX支持的采集卡和摄像头的视频影像上进行测量!无需将图片采集过后,可以直接在画面上进行实时、动态的测量,与静态测量相比较,增加了方便性和实用性!
㈡系统组成:
1 整个软件系统由如下部分组成: ⒈软件程序(光盘);
⒉加密狗:客户需事先选择加密狗类型(并口型或者USB型); ⒊文字资料:《使用说明书》(光盘上有WORD文档);
㈢硬件运行环境: ⒈电脑推荐配置:
⑴CPU:奔腾4型,主频2.8G以上; ⑵内存:1G及以上( 否则安装时会出错);
⑶硬盘:C盘可用空间2G以上,软件(推荐)安装在C盘; ⑷显示卡:可提供3D加速的AGP显示卡、可达到真彩色;
⒉视频采集卡:
本软件支持多种视频采集卡,用户可在“功能选择”菜单中选择相应的采集卡。
⒊CCD摄像头或者数码相机:
分辨率达到450线及以上的CCD摄像头以及数码相机均可。
㈣软件运行环境:
WINDOWS XP SP2(32bit)。
㈤售后服务:
我公司将为用户提供以下售后服务项目: ⒈技术咨询;
⒉软件的修改和升级; ⒊报告文件按客户要求制作;
二、安装说明
㈠加密狗安装:
⒈软件配备的是“USB”加密狗,插入USB口即可。
⒉打开电脑,将软件光盘放入光驱,在光盘上找到“HASP HL 80530A 加密锁驱动程序”文件夹(其中80530A 是表示加密狗的编号),运行其中的“HASPUserSetup.exe”文件,按其安装向导,逐步完成软件狗驱动程序的安装。
⒊如加密狗或者其驱动程序未能安装正确,软件运行后将自动退出。正确安装后加密狗上的指示灯会亮起。
㈡视频采集卡的安装:
根据硬件厂商的说明进行安装。
㈢软件安装:
运行光盘上的Windows Installer 软件包如:(80528金相检验软件系统(发行版 2008).msi),安装向导将逐步完成软件的安装,建议您将该软件安装在C盘上。
三、硬件参数
㈠基本原理:
计算机图像处理系统所采集的图像都有一个固定的X-Y比例,它是由显微镜、摄像头、图像采集卡、计算机、处理软件、采集图像分辨率、显示器分辨率等软、硬件环境共同决定的,其数据的含义是:在当前的软、硬件条件下,显示器的一个像素,代表的实际长度值。
应用图像软件进行图像分析时,必须先设定当前环境下的硬件参数,才能保证系统测量数据的真实性和准确性,否则,得出的结果将不准确。当软、硬件环境发生变化后,该参数必须作相应的变更。
参数测得后,应使用本软件的“几何测量”功能,对已知尺寸的测微尺图像进行测量,以验证数据的准确性。
㈡初始设置:
软件启动后,用户将根据提示,确定当前硬件参数值,可以立即进行测试,也可人工输入。具体界面如下:(图1)
㈢设置硬件参数:
该主要功能包含“选择或输入硬件参数”和 “采集测微尺图像标定”界面如下:
⒈选择或输入硬件参数:
该功能可让用户选择已经保存的参数值,也可以输入具体的硬件参数值。界面如下图所示:
⒉采集测微尺图像标定:
用户从新进行硬件参数设置,步骤如下: ·选择采样方式:
5 在(图1)界面选择“视频采集卡采集图像”或者“装入图像文件”的方法,按“确定”按钮装入测微尺图像。
·进行硬件参数标定:
该方法的基本原理是:在已知实际长度的测微尺图像上,移动电子标尺,软件在该标尺移动的过程中,自动得出覆盖部分的像素个数,由此求出在该硬件环境下,计算机显示器上每个像素所代表的实际长度。
该过程包含X方向硬件参数标定、Y方向硬件参数标定、填写硬件参数环境等步骤,具体情况如下:
·X方向硬件参数标定:
在“标定方向选择”栏目中,选择“水平标定”;
在“标尺移动对齐”栏目中,使用“移动标尺”和“缩放标尺”工具,将电子标尺精确对齐测微尺图像,要求电子标尺从左到右的每一个小格,均精确对齐测微尺的每一个小格;同时可调节标尺移动的速度,以及标尺颜色;
在“标定长度”栏目中,输入标尺所精确覆盖的被测物体的长度,例如本例中,电子标尺精确覆盖了测微尺53格的长度,已知该测微尺每小格长度为0.01毫米,53小格共计0.53毫米,因此在该栏目中输入“0.53毫米”; 在“硬件参数”栏目中,输入当前硬件环境,主要包括:显微镜型号和镜头配置、电子摄像装置情况、计算机软、硬件情况、视频采集时计算机和采集设备设置的分辨率等,这样可方便用户在使用过程中,调用已经设置过的硬件参数。
6 标定完成的硬件参数,将显示在“分辨率”栏目中。 ·Y方向硬件参数标定:
在“标定方向选择”栏目中,选择“垂直标定”;
在“标尺移动对齐”栏目中,使用“移动标尺”和“缩放标尺”工具,将电子标尺精确对齐测微尺图像,要求电子标尺从下到上的每一个小格,均精确对齐测微尺的每一个小格;同时可调节标尺移动的速度,以及标尺颜色;
在“标定长度”栏目中,输入标尺所精确覆盖的被测物体的长度,例如本例中,电子标尺精确覆盖了测微尺39格的长度,已知该测微尺每小格长度为0.01毫米,39小格共计0.39毫米,因此在该栏目中输入“0.39毫米” ;
标定完成的硬件参数,将显示在“分辨率”栏目中。 3查看硬件参数:
查看当前硬件参数值。界面如下:
四、核心功能
为了方便使用,本软件设立了“使用向导”(下拉菜单—工具选择中的第一项,也是工具条的第一项),它将引导用户完成所需工作,软件的主要核心功能均集于其中,“使用向导”界面如下。
·选择采样方案:
软件提供两种视频采集方案,用户必须选择一种,系统将采用此方案采集金相图片,具体情况如下:
1.图像文件装入:
装入保存在计算机磁盘上的BMP或者JPE格式的图像文件。 2.视频采集卡方式:
使用视频采集卡,捕捉CCD摄像头中的数码图像。
㈠自动评级
依照有关标准,进行金相图像分析,具体步骤如下: ⒈选择金相检验项目:
在列表中选择检验所需的金相标准,按“确定”间确认。
如果需要对一张试样图像用多种标准进行检验,可选择“多模块评级”,这样用户可一次多个检验标准,并在软件的引导下逐步进行评级工作。
⒉视频采集:
用户可在本界面中,按“图像采集”菜单进行金相图片的采集:
⒊图像处理:
金相图片采集后,系统将提供多种的图像处理功能,该部分内容说明如下: ⑴图像处理:
本界面左上角第二项的“图像处理”菜单中提供了十余种方法进行图像处理,具体内容如下:
·历史记录:
用户可以在这里查看已经进行过的“图像处理”操作过程,也可以读回已完成的操作过程进行行重新处理。 ·图像还原:
还原为采样时获得的原始图像。 ·使用画笔:
可用画笔在装入软件的图像上进行各种修改。客户可以采用颜色捕获(捕获装入图像的颜色)或者颜色选择的方法选择画笔的颜色,同时可调整画笔的粗细。当画笔的属性调整完成后,客户用鼠标拖动画笔在图像上进行修改。
画笔中可以看到金相图象显示在界面的左边,用户可选择右面的工具栏中的工具在该图片上进行绘制。工具栏从上到下依次是:
线条样本框:画笔线条样式;线条粗细:改变线条粗细;画笔类型:画笔类型有三种颜色,功能是一样,只是为避免同底色而设定的;调色板:用于改变画笔线条的颜色;图象还原:还原为原图;历史记录:可查看或读回已经完成的操作;放大缩小:缩小或放大,复原样图;画笔复位:选中时画笔完成一次选定后始终会回到线条样本框处。
(画笔版快在其它地方也存在,功能和界面是一样的,后面就不再作说明了) ·亮度调整:加亮或变暗整个图像。
·对比度调整:调整图像中明暗之间的差别。
·颜色调整:单独调整图像中红、绿、蓝三种颜色的深浅。 ·转换为灰度图像:把彩色图像变换为有256种深度的灰色图像。
·灰度自动色阶:自动将灰度图像的色阶变换到0-255区间。使灰度图像更加清晰,层次感更分明。
·二值化处理:根据临界值把图像转换为只有黑色和白色两种颜色的图像。 ·去除杂点(*):把图像中独立的黑色点变成白色。 ·膨胀(*):增大图像中黑色部分的面积。 ·细化(*):把图像中的黑色块变成细线。 ·连接断线(*):把断开的线条连接起来。 ·延长断线(*):把断头连接到线条上。
12 ·删除断头(*):把多余的断头删掉。 ·反相:反转图像的颜色。 ·通道:选择和组合红绿蓝色调。
·锐化:放大图像中色彩之间的差别, 使图像中原来模糊部分变得更清晰。 ·柔化:缩小图像中色彩之间的差别, 使图像中原来清晰部分变得更模糊。 ·边缘增强:加亮图像中色彩变化较大的分界线, 同时把其他颜色变暗。 ·边缘检测:加亮图像中色彩变化较大的分界线。
·中值滤波去噪:图像色彩变化较大时,增大其中色彩较暗的像素, 缩小图像中色彩较亮的像素, 使其保持中间值。
注:(*)表示该功能仅对二值化处理后的图像有效。
⑵充满窗口:可将大幅图像全部显示在当前窗口内。
⑶区域选择:
本软件提供了“矩形”、“圆形”等工具进行,进行区域选择,系统只处理选择后的区域部分。用户可用“位置移动”、“大小放缩”、“角度旋转”等工具完成区域选择,同时可以使用“选择变换速度”功能,控制选取范围的变换快慢。
⑷定尺评级:
本功能可设定图像选择区域的实际大小,分为“矩形定尺”和“圆形定尺”。
“矩形定尺”:在“区域选择”中选定“矩形”,在“定尺”框中输入定尺矩形的宽度和高度(不能超过图像的实际大小的限制),选中“定尺评级”即可。
13
“圆形定尺”:在“区域选择”中选定“圆形”,在“定尺”框中输入定尺圆形的直径(不能超过图像的实际大小的限制),选中“定尺评级”即可。
保存定尺:保存定尺后图像,在保存时,可调整图像的打印分辨率,分辨率调整界面如下:
按下“保存”按钮,可保存该图像,保存时可设定标尺位置及大小,按下确定键可将该图像保存到指定的磁盘位置。
该图像必须保存到磁盘上(使用“[定尺]保存选区图像”功能),然后才能进行以后的操作。 ⑸打印放大倍数:
15 本参数的含义是:图像打印后的实际尺寸,与被观测物实际大小之比。例如:在假设“打印放大倍数”设为100时,被观测物实际长度为100μ,用打印机将该图像打印出来后,其在打印纸上的实际长度为10毫米(100μ×100)。 ⑹设定打印图像:
确认当前的图像作为需要打印的图像。当图像被处理到满意的时候,按下该功能键,当前图像将作为被打印的图像记录下来。 ⑺保存选区:
将图像被选中的区域部分,以“BMP”或者“JPG”的格式保存在计算机磁盘上,保存时可设定标尺。 ⑻保存图像:
将图像以“BMP”或者“JPG”的格式保存在计算机磁盘上。保存在计算机磁盘上,保存时可设定标尺。 ⑼调分辨率:
该功能可调整图像X、Y方向的分辨率,具体界面如下:
上述工作完成后,返回“图像处理界面”可按“评定级别”按钮进入“自动评级”界面,也可按“结束”按钮返回“使用向导”界面。
⒋自动评级:
16 下面以一个典型的金相分析模块:“金属平均晶粒度的测定 GB6394-86”来说明自动评级的全过程。
⑴评级界面:
该部分的软件界面和内容说明如下:
·图库:
界面左边的滚动栏中,显示了和本标准相关的金相图谱,用户可以通过人工观察的方法,将右边采样得到的金相图片和它进行比较,进而得出评级结论。操作方法是:用鼠标点击图库中被选择的图片(选中的图片以红框表示),其评定的结果就在右边的“评定级别”栏目中显示出来。
·金相图片:
采集及处理后的金相图片显示在界面的右边,下方有一系列按钮和显示框,控制图像的显示情况,其中:
“显示倍数”框中显示的倍数是:该金相图片以图谱为基准的放大倍数。例如图谱放大倍数为100倍,该栏目显示为“227” ,就表示该金相图片比图谱大2.27倍。 “按原图尺寸显示”:图片按采集后的实际尺寸显示。 “按图谱倍数显示”:图片的显示倍数和图谱倍数一致。
“按设定倍数显示”:图片按设定倍数显示,软件可设定100、200、300、400、500等5个显示倍数。
“按调整倍数显示”:用户可按“+”、“-”按钮调整图片显示倍数。
17 “评定级别”:该栏目显示金相图片的最终评级结果。 ·打印:
按下“打印”按钮后,用户将选择打印的格式和内容,本软件预制了“单独打印图像”和“按《通用格式》生成报告文件”两中方式,供用户选择。如果选择“单独打印图像” ,系统将按用户事先确定的“打印放大倍数”打印该图像,界面如下。
·打印标尺:用户可以在这里选择是否需要显示标尺
·标尺长度:用户可以设置标尺表示的方式。“微米“和”毫米“是两种打印后在纸上的尺寸的单位。就是说打印出的标尺是实物尺寸的“毫米“乘上“打印放大倍数”得到的打印尺寸“毫米“。这两种表示方式用户可以按自己的需要选其中一个。
·标尺分格:用户可以设置分格表示的格数
·打印放大倍数:用户可以设置打印在纸上的图象是实物的放大倍数的植。
如果选择“按《通用格式》生成报告文件” ,系统要提示用户先完成报告有关信息的录入,并确定打印放大倍数,以下是信息录入界面和报告打印预览界面。
“保存Word文档”:将生成的报告格式保存为Word文档,用户可打开该文件进行浏览和修改(要求系统中必须装有“Word2000”)。
“装入报告附图”:用视频采集卡或者直接装入磁盘上的图形文件。 “图像处理”:提供了十余种图像处理方法,用户根据需要进行图像处理。 “绘制箭头”:在图像上绘制箭头,以便标识需要特别指示的图像部分。 “倍数和标尺”:设定图像的“打印放大倍数”和“标尺大小”。 “删除报告附图”:删除报告中的插图。
“评级历史信息”:该功能类似“记事本”,可自动记录所有评级信息,该信息可粘贴、编辑和删除。
·打印设置和报告保存
设置打印机有关参数;右上角是红色表示报告未存盘,绿色表示已存盘。 ⑵自动评级界面:
该部分的软件界面和内容说明如下:
·金相图片
采集及处理后的金相图片,显示在界面的左上方。 ·图像数据
图像中各部分的定量分析数据,显示在界面的左下方。 ·统计直方图
软件对分析得到的各种定量分析数据进行统计后,生成统计直方图,显示在界面右上方。 ·晶粒搜索参数:
用户可根据自己对图像的要求,设置以下三个可调参数: [最小面积] 在采集的视频图像中,有时难免出现一些杂点。这些非组织的杂点会减慢计算速度、干扰组织分析和评级结果,严重时甚至使评级无法完成。此时可调整[最小面积]的数值。软件系统约定,凡是小于最小面积的粒子一概忽略,不于处理。有效地解决了这一问题。
[最大面积] 在所分析的组织图像中,有时可以根据组织面积的大小进行分类。此时可调整[最大面积]的数值,从而获得正确的粒子分类,准确评定级别。但是,如果进入模块后,发现[最大面积]的预设值是一个很大的数,则表示本模块最大面积预设置一般不需要调整。此时,凡是大于最大面积的粒子也一概忽略不计。
[边界调整] 20 采集的视频图像对比度不一定适合软件系统处理(例如图像过于“淡”或“浓”), 此时可调整[边界调整]的数值。一般情况下,调整[边界调整]的数值会影响到粒子搜索边界的位置:临界值增大,边界扩大;临界值减小,边界缩小;[边界调整]的预设值由软件系统自动计算,客户可根据视频图像的实际情况加以调整。 ·级别评定:
显示评级结果和相关数据。 ·最大晶粒:
显示金相图片中最大晶粒的相关数据。
按下“确定”键以后,系统将返回“评定级别”界面,该评级结果将作被系统记录并保存下来。
㈡新建报告:
该功能专门用于制作比较特殊的检验报告,具体步骤如下: ⒈视频采集:按照用户选择的方式,进行金相图片的采集。 ⒉图像处理:金相图片采集后,系统将提供多种的图像处理功能。
⒊报告生成:本软件预制了“单独打印图像”和“按《通用格式》生成报告文件”两种方式,供用户选择。
上述内容和“自动评级”中的相应内容一致,这里不再详细叙述。
㈢打开报告:
用户可打开已经保存在磁盘上的、由本软件生成的金相检验报告进行浏览和打印。
㈣几何测量:
用户可应用多种测量工具,完成图像的测量工作,具体步骤如下: ⒈视频采集:
按照用户选择的方式,进行金相图片的采集。
⒉图像处理:
⑴(图像)充满窗口 ⑵区域选择 ⑶定尺
⑷打印放大倍数 ⑸保存选区 ⑹保存全图
21 上述内容和“自动评级”中的相应部分一致,这里不再叙述。 ⑺几何测量:按下该按钮,将进入“几何测量”界面。 ⑻结束测量:结束测量工作。
⒊几何测量:该功能的界面和说明如下:
22 ⑴金相图片:显示在界面的左边,用户可选择测量工具,在该图片上进行测量。 ⑵字体和线宽调整:字号是用户可选择多种尺寸的字体来显示测量信息。线宽是 调整测量工具的线的粗细
⑶颜色选择:用户可自由选择颜色来显示测量信息。
·绘制对象颜色:是对用户将要用于测量的工具的线条设定颜色。
·活动对象颜色:是对用户完成测量工作后的显示测量信息移字时的颜色设定。
(上面两项是在测量前先设定, 是测量完成后无法改变的) ·选项:这是几何测量时的设置。
这里提供了单位选择;单位,序号控制;测量距离控制;抗锯齿控制;折线测量控制;标尺,光标控制;测量两直线夹角控制功能的设定。
⑷测量工具:用户可选择“测量距离”、“测量矩形”、“测量圆形”、“测量多边形”、“测量角度”、“测量两直线夹角”、“测量折线长度”、“测量弧度”等工具,以及“两点法”、“拖动法”等测量方法进行几何测量。具体方法是:先选中测量工具,再用鼠标在图片上拖动。
⑸信息显示框:显示当前测量信息。
(双击折线测量的信息可以显示分段测量的数据信息,分段数据信息可以保存)
23
⑹平均值:计算当前所有测量数据结果的平均值。
⑺重画窗口:清除已经完成的测量信息,回到刚装入图像时的状态。
⑻生成Excel接口文件:将滚动条中的数据生成可在Excel中打开的文本文件。 ⑼保存当前图像:以BMP或者JPG的格式保存测量后的图像。 ⑽打印:可打印图像或者按“通用测量报告格式”打印测量报告。 ⑾打印设置:设置打印机有关参数。 ⑿返回图像处理:返回图像处理界面。
⒀放缩选择:
“放缩显示”:不改变图像物理尺寸,进行图像放缩;
“放缩图像充满窗口”:使图像物理尺寸缩小至充满窗口,在每次测量过程中,该操作只能使用一次,由于图像物理尺寸缩小,图像质量(影响存图和打印)将随之下降。
推荐选择:如果希望图像质量不变,推荐,此时仅改变图像显示大小,图像物理尺寸并不改变。
㈤查看图库:
用户可查看本软件系统中的金相图库,具体步骤如下: ⒈ 选择图谱:根据需要选择图谱。
⒉ 查看图谱:选中图谱后,按下“确定”键,系统将显示该图谱内容,用户可使用 下拉菜单中“查看信息”选项,调整图谱显示状况。
24
㈥定倍打印:
可装入多副图片,可对图片进行图像处理,并设置不同的说明文字和打印版面,具体界面及说明如下:
⒈ 打印预览框:位于界面左边,预览打印效果。
⒉ 图像选择框:位于界面中间,可选择需要处理的图像。 ⒊ 图像文字说明:
在图像文件的页眉、页脚、文字说明处点击鼠标右键,将出现文字输入框,用户可在此输入需要的文字说明。
⒋ 文字选项:设置文字相关信息。 ⒌ 打印选项:设置打印页面相关信息。
⒍ 每页打印的图像数:该数据可根据需要进行调节。
⒎ 标尺设置:设置标尺的位置、大小、是否绘制到被选择的图像等信息。 ⒏ 绘制箭头:绘制箭头到被选中的图像上,同时可设置箭头的相关信息。 ⒐ 图像处理:提供几十种方法处理被选中的图像,具体内容前面已有说明。
⒑ 功能键:提供了“装入图像”、“保存图像”、“删除图像”、“删除全部图像”、“打印”等功能键。
25
㈦ 图像拼接:
1、在“功能选择”菜单中的“脱机拼接”中选择该功能。
2、图像拼接界面:
26 .以下是图像拼接后的情况:
拼接原理:
图像拼接有“自动”和“手动”两种方式,如采用“自动”方式,则被拼接图像需要有重合部分;如采用“手动”方式,可先用鼠标选中某张图,再用键盘的方向键移动它。
以“多行多列”的图像拼接为例。软件以1行1列的图为基准,先完成各行图像
27 的拼接(以第一行为例,先完成1行2列和1行1列的2张图的拼接,再完成按此顺 序完成该行余下图像的拼接)。各行内部的图像拼接完成后,完成整个图像的拼接 (先将第2行的图像和第1行的图像拼接起来,再按此规律完成整个图像的拼接)。 图像周边剪裁:
“剪裁像素”可以按0-10个像素之间的设定,软件将按此设定对图像边缘进行裁 剪。“复原”可使被剪裁但未保存的图像,恢复到剪裁之前的图像。 工作界面:
全部图像:在窗口范围内显示所有的图像。 原图尺寸:在拼接图像为原始尺寸条件下工作。 显示选择:
匹配:是否显示每张图参与搜索的区域(紫红色)和被搜索的区域(浅蓝色)。 拼图:是否显示拼图后的区域边界。 拼接参数:
重合估计:标明该图像中,被搜索图像的区域的大小。软件将在此区域内,搜索是否有和相临图的“匹配区域”相同的部分,并以此为依据完成图像拼接。
匹配尺寸:标明该图像中,参与图像搜索区域的大小。软件将以此区域为准,在
相临图的“重合区域”内进行搜索,查看是否有和该“匹配区域”相重合的部分,并以此为依据完成图像拼接。
拼接速度:图像拼接的速度。速度的快慢决定拼接的精确度。 机时(秒):完成拼接图像文件所用掉的时间。 载入文件:
选择需要拼接图像文件的目录位置,图像将自动装入。可被拼接的图像格式为BMP 或JPG文件。被拼接的图像文件的名称必须按“@行数_列数.bmp”格式设定(例如: @1_1.bmp,指的是该文件位于1行1列)。 拼接演示:
将软件预装的图像进行拼接,以演示图像拼接过程。 自动拼接:
按设定完成的拼接参数,进行自动拼接工作。 图像原位:
将所有图像恢复到拼接前的位置。 拼接检查:
用户可以用人工的方法检查拼图后的图像重合部分是否正确。
28
在此图中,大红色的部分和紫红色的部分因为完全一致,属重合部分,软件以此为依据,完成了本次图像拼接。 保存拼图:
将拼接后的图保存为BMP或JPG格式。 结束:
退出图像拼接工作界面。
29 ⒏动态测量: ● 选择动态测量,进入
● 设定动态测量视频窗口尺寸:
30 ● 进入测量窗口后,需要进行标定,标定方法同软件标定.
● 使用操作方法同二维测量.
31 ● 打印报告及保存报告等,和二维测量相同.
32
五、专业功能
㈠ 图像共聚焦:
该功能模块的作用是:将拍摄对象相同、但焦距不同的几张照片,重合成一张完全清晰的照片。界面及重合效果如下图:
共聚焦原理:
首先要完成几幅图像的“配准”工作(因为在拍摄多幅图像时,拍摄视场的位置 可能发生变化),具体做法是:取出 “被配准图像”的“配准块”,在“基准图像” 的“配准区”中进行搜索,确定“被配准图像”和“基准图像”的位置偏差。
再按设定的“聚焦块”对装入的每张图像进行分割,依次比较每个区域的清晰 度,选择出最清晰的图像部分,再将筛选出的各部分组成为一个图像。 选择“基准图像”:
软件自动分析的装入图像的清晰度,并自动选择最清晰的图像作为基准图像(文 件名为大红色),用户也可自己指定基准图像(用鼠标选取)。 图像周边剪裁:
“剪裁像素”可以按0-10个像素之间的设定,软件将按此设定对图像边缘进行裁 剪。“复原”可使被剪裁但未保存的图像,恢复到剪裁之前的图像。 工作界面:
全部图像:在窗口范围内显示所有的图像。 原图尺寸:在拼接图像为原始尺寸条件下工作。
33 显示选择:选择软件需显示的文字信息。 共聚焦参数:
匹配块:图像配准时,其他图像和基准图像作比较时的区域。
匹配区:图像配准时,其他图像的“匹配块”在“基准图像”中搜索的区域。
聚焦块:图像合成时,分割每张图像的分割区域。
㈡ OpenGL三维光图:
本模块通过对图像组织亮度的分析,构建二维图像的三维模型。该软件模块可检查被观测试样是否平整。 机时(秒):完成本次共聚焦所需的时间。
34
六、系统功能
㈠视频采集卡型号选择:
本软件支持多种视频采集卡进行图像的采集,可在“功能选择”菜单中选择型号:
我方还可根据客户具体需求,将其他采集卡的图像采集软件集成到本软件中。具体使用时可在软件的“功能选择”主菜单中选择相应的视频采集卡型号。客户需提供给我方视频采集卡、驱动程序、二次开发包SDK.
㈡演示全部模块:
自动运行所有的软件功能模块。在软件的“功能选择”主菜单中可选择本项功能。
㈢设置系统参数:
在“使用向导”界面上点击“设置系统参数”,界面如下:
35
其中各项:采样方案提示、打印放大倍数的单位、模块列表显示方式等可以按照客户使用习惯设定。
㈣保存-恢复系统参数:
可保存、恢复系统标定值,该数据将以*.hsp格式保存在磁盘上。
36 标定完成,确认正确后,按保存备份,升级或者重新安装时,按恢复,然后指定路径,导回硬件参数。免去您多次标定的麻烦。
37
七、实际操作示例
㈠晶粒度评级(模块 【74】黑白相面积及晶粒度评级 ):
以下是分析一副金相图片的过程。使用者需要求得该金相图片的黑色和白色晶粒的晶粒度。本次分析使用软件的74号分析模块进行。
采集的原始图片:
1.第1步,亮度调整到-100:
调整后效果如下:
38
2.第2步,对比度调整到100:
调整后效果如下:
39
3.第3步,Sobel 边缘检测:
调整后效果如下:
40
4.第4步,手工描绘晶界(绿色部分):
5.第5步,自动评级-搜索白晶粒(将边界B设为0):
41
6.第6步,自动评级-同时搜索黑白晶粒(将边界B设为80):
㈡非金属夹杂评级(模块【 2】非金属夹杂物显微评定): ⒈水平测微尺图像(横向标定图像):
42
⒉垂直测微尺图像(纵向标定图像):
⒊水平标定:
43
⒋垂直标定:
⒌非金属夹杂物初始采样图像:
44
⒍进入{区域选择和图像处理界面}:
⒎点击[图像处理]-[转换为灰度图像]:
45
⒏点击[图像处理]-[灰度自动色阶]:
⒐[灰度自动色阶]处理效果:
46
⒑调整亮度(程度数值增加到70):
⒒调整对比度(程度数值增加到40):
47
⒓进入自动评级模块:
⒔自动评级:点击自动评级按钮完成
48
㈢球墨铸铁_球化分级_石墨大小分级(模块【20】【21】) 球墨铸铁_采样原图:
49
⒈ 转换为灰度图像-操作:
⒉ 转换为灰度图像-结果:
50
第14篇:个人工作总结 (检验人员)
个人工作总结
2017年,我在中心领导、科长及同事们的关心与帮助下,圆满的完成了各项工作,并取得了相应成绩。现将本年度的工作总结如下:
一、解放思想,更新观念
在过去的一年里,作为一名入党积极分子,我认真学习习总书记系列讲话,学党规党章,坚决拥护党的领导,坚持以“三个代表”的重要思想为准则,努力践行科学发展观,以高于党员的标准严格要求自己。十九大顺利召开后,我又认真学习了习总书记在大会上作出的报告,将报告的精神融汇贯通到现实生活和工作中来,以为人民服务作为主要目标,踏踏实实做人,认认真真做事。
二、业务工作和学习方面
业务工作中,我认真履行单位和科室的各项规章制度,遵守检验检测相关规定。实验验操作严格遵循作业指导书,保证数据客观公正。现将一年来业务总结如下:
1、认真值班,服从单位值班安排,遵守值班制度,准时到岗,不迟到早退,不无故缺席,认真做好值班记录。值班期间没有发生一件有损单位和同事的事件。
2、明确责任,工作中,我主要负责协调理化组日常工作,生活饮用水、食品中色谱部分项目的检测。
3、在过去的一年里,和同事共同完成864份水碘、1867份盐碘、4500份尿碘检测,为地方病科碘缺乏病工作提供有力的数据支持;完成95份生活饮用水中氨氮、耗氧量、亚氯酸盐、三氯甲烷、四氯化碳、电导率项目的检测;完成一份自治区CDC派发的阴离子合成洗涤剂考核样。
4、参与主持科室举办的针对八县一市实验室人员的尿碘和生活饮用水技术培训班,提高了基层实验室检测能力。
5、参与中心组织的内审,经过6个月的精心准备,我们顺利通过了实验室计量认证审核,并取得相关资质。
6、根据质量手册和程序文件规定,完成实验室新进人员培训和质量监督,并填写质量监督记录。
7、对实验仪器进行归档管理,完成仪器和标准的期间核查,并填写相关记录。
8、认真填写实验室试剂入库和领用台账,定期更新试剂库数据和检查试剂库安全,防止易燃易爆、易制毒试剂丢失,防止安全隐患的存在。
9、完成自治区青年基金《兽药残留中硝基呋喃的检测》课题的相关工作。
三、工作中存在的问题和不足
在总结成绩的同时,本人认为在以下方面还存在问题和不足:在思想上还存在一定的惰性和依赖思想;工作上,思维开放度还不够广,创新意识跟不上,工作形式比较呆板,安于现状。
我决定在来年的工作和学习中,首先,努力提高思想,向党组织靠拢;其次,积极主动的申报课题,弥补实验室在科研方面的空白;最后,完善实验室相关规定,优化实验室人员配置,减少资源浪费。
第15篇:调质钢的金相组织及检验
调质钢的金相组织及检验
调质钢通常是指采用调质处理(淬火加高温回火)的中碳优质碳素结构钢和合金结构钢,如
35、
45、50、40Cr、40MnB、40CrMn、30CrMnSi、38CrMoAlA、40CrNiMoA和40CrMnMo等。
调质钢主要用于制造在动态载荷或各种复合应力下工作的零件(如机器中传动轴、连杆、齿轮等)。这类零件要求钢材具有较高的综合力学性能。
一、调质钢的热处理
(一)预先热处理
为了消除和改善前道工序(铸、锻、轧、拔)遗存的组织缺陷和内应力,并为后道工序(淬火、切削、拉拔)作好组织和性能上准备而进行退火或正火工序就是预先热处理。
关于调质钢在切削加工前进行的预先热处理,珠光体钢可在Ac3 以上进行一次正火或退火;合金元素含量高的马氏体钢则先在Ac3 以上进行一次空冷淬火,然后再在Ac1以下进行高温回火,使其形成回火索氏体。
(二)最终热处理
调质钢一般加热温度在Ac3以上30~50℃,保温淬火得到马氏体组织。淬火后应进行高温回火获得回火索氏体。回火温度根据调质件的性能要求,一般取500~600℃之间,具体范围视钢的化学成分和零件的技术条件而定。因为合金元素的加人会减缓马氏体的分解、碳化物的析出和聚集以及残余奥氏体的转变等过程,回火温度将移向更高。
二、调质钢的金相检验
(一)原材料组织检验 调质工件在淬火前的理想组织应为细小均匀的铁素体加珠光体,这样才能保证在正常淬火工艺下获得良好的淬火组织---细小的马氏体。
(二)脱碳层检验 钢材在热加工或热处理时,表面因与炉气作用而形成脱碳层。脱碳层的特征是,表面铁素体量相对心部要多(半脱碳)或表面全部为铁素体(全脱碳),从而使工件淬火后出现铁素体或托氏体组织,回火后硬度不足,耐磨性和疲劳强度下降。因此调质工件淬火后不允许有超过加工余量的脱碳层。金相试样的磨面必须垂直脱碳面,边缘保持完整,不应有倒角。脱碳层的具体测量方法可按GB/T 224-1987标准进行。
(三)锻造的过热和过烧检验
锻造加热时,由于加热温度高,不仅奥氏体晶粒粗大,而且有些夹杂物发生溶解而在锻后冷却时沿奥氏体晶界重新析出。一般过热时,仅出现粗大的奥氏体晶粒并产生魏氏组织。在一些低合金钢中还会出现粗大的贝氏体或马氏体组织。 过热时沿奥氏体晶界析出的常为MnS或FeS。用一般试剂无法侵蚀显示奥氏体晶界,最好方法用饱和的硝酸铵溶液进行电解侵蚀。侵蚀后试样的奥氏体晶界呈白色网状。由于过热锻件晶粒粗大,使得塑性和韧性下降,容易造成脆断。
当钢加热到更高温度,接近液相线时,会出现过烧现象。过烧特征是钢的粗大晶界被氧化和熔化,锻造时将产生沿晶裂纹,在锻件表面出现龟裂状裂纹。
(四)调质钢的淬火回火组织
调质钢正常淬火组织为板条状马氏体和针片状马氏体,当含碳量较低时,如30CrMo等,形态特征趋向于低碳马氏体。当含碳量较高,如60Si
2、50CrV等,形态特征趋向于高碳马氏体。
如果淬火加热温度过低,或保温不足,奥氏体未均匀化,或淬火前预先热处理不当,未使原始组织变得细匀一致,导致工件淬火后的组织为马氏体和未溶的铁素体,后者即使回火也不能消除(图5-1)。
图5-1 低碳马氏休+网状铁素体 (500 X) 图5-2 45钢调质处理之回火索氏体 (500×) 如果淬火加热温度正常,且保温时间足够,但冷却速度不够,以致不能淬透,结果沿工件截面各部位将得到不同的组织,即从表层至中心依次出现马氏体、马氏体+托氏体、托氏体+铁素体等组织。甚至表层也不能得到全马氏体组织。
当工件淬火温度正常,保温时间足够,且冷却速度也较大,过冷奥氏体在淬火过程中未发生分解,那么淬火后得到的组织应是板条状马氏体和针片状马氏体。在随后的高温回火过程中,马氏体中析出碳化物,最终得到的是均匀且弥散分布的回火索氏体(图5-2)。
第三节 弹簧钢的金相组织及检验
弹簧钢是用于制造各种弹性元件的专用结构钢,它具有弹性极限高、足够的韧性、塑性和较高的疲劳强度。弹簧钢含碳量比调质钢高,其中碳素弹簧钢的含碳量的质量分数约为0.6~1.05%;合金弹簧钢的含碳量的质量分数为0.4~0.74%。弹簧钢中加入的合金元素主要为硅和锰,目的是提高淬透性。要求较高的弹簧钢,还需要加入铬、钒或钨等元素。
弹簧钢的热处理方法主要有两种: (1)淬火加中温回火处理。 用这种处理方法的多数为热轧材料以热成形方法制作的弹簧,或者用冷拉退火钢丝以冷卷成型的弹簧。中温回火后的组织为回火托氏体,此弹簧有很高的弹性极限与屈服强度,同时又有足够的韧性和塑性。 (2) 低温去应力回火。应用这一处理方法的主要是一些用冷拉弹簧钢丝或油淬回火钢丝冷盘成形的弹簧。
钢丝成材过程的强化处理也有两种方法。一种是冷拉后的淬火回火处理,其组织为回火托氏体。另一种为“铅淬”冷拔,即将热轧盘条加热到奥氏体状态,然后淬到450~550℃的熔化铅液中作等温处理,得到冷拉性能很好的回火索氏体,最后通过一系列的冷拔,得到一定规格尺寸与强度的钢丝。这种钢丝组织为纤维状的形变回火索氏体。
弹簧钢的金相检验内容有非金属夹杂物、石墨、表面脱碳、显微组织等。
(一)石墨碳与非金属夹杂物检验 检查石墨碳及非金属夹杂物时,试样取样部位一般都在材料端部,也可按照双方协议的规定。其检查方法及评级可分别按 GB/T 10561-1989和GB/T 13302-1991标准进行评定。石墨碳及非金属夹杂物是弹簧钢的内部缺陷。
(二)表面脱碳层检验 在弹簧钢各种材料标准中对表面脱碳均有明确的规定,一般脱碳深度根据材料的厚度或直径的百分数而定,而且冷拉材料要比热轧材料严格,如公称直径≤8 mm的热轧圆钢,
其规定总脱碳层不大于直径的2.5%,而同规格的冷拉钢则为不大于2%。 检查材料表面脱碳时,试样的切取部位均在材料两端或其中任意一端,如为弹簧成品或半成品,一般可在任意部位取。脱碳层检验标准为GB/T224-1987。
(三)显微组织检验 经过退火处理热轧弹簧钢,其组织是珠光体或珠光体和网状铁素体。规格较大的冷拉弹簧钢一般经过球化退火处理,组织为球状珠光体。冷拉碳素弹簧钢丝(包括冷拉的65 Mn弹簧钢丝),因冷拉前经过索氏体转变(俗称铅淬)处理,所以冷拉后组织呈纤维状的索氏体。油淬火回火钢丝的组织为回火托氏体。图5-
3、图5-4分别为油淬火回火钢丝组织和冷拉铅浴处理钢丝组织。
图5-3 65Mn弹簧钢之回火托氏体 图5-4 50CrV弹簧钢冷拉铅浴处理 组织 (500×) 之形变索氏体组织 (500×)
用热轧弹簧钢制作弹簧时,由于采用热成形方法,然后需进行淬火、回火处理,故原材料的组织检验可以省略。冷拉退火钢丝用冷盘法加工弹簧,则要检验原材料组织的球化程度。若球化不良,则材料要重新球化退火。检查“铅淬”冷拉钢丝组织时,磨面应取纵向,其他试样磨面可以取任意方向。
对于用碳素弹簧钢和合金弹簧钢制作的内燃机气门弹簧,在检验组织及缺陷时,应按GB/T 2785-1988《内燃机气门弹簧技术条件》进行。对于汽车钢板弹簧的金相检验,则按照JB 3782一1984《汽车钢板弹簧金相检验标准》进行。金相试样应在钢板全长的l/4处截取,且截面距钢板一端距离不得小于50 mm。在检查带状组织时,金相磨面应取钢板的纵向截面。
第16篇:调质钢的金相组织及检验
调质钢的金相组织及检验
调质钢通常是指采用调质处理(淬火加高温回火)的中碳优质碳素结构钢和合金结构钢,如
35、
45、50、40Cr、40MnB、40CrMn、30CrMnSi、38CrMoAlA、40CrNiMoA和40CrMnMo等。
调质钢主要用于制造在动态载荷或各种复合应力下工作的零件(如机器中传动轴、连杆、齿轮等)。这类零件要求钢材具有较高的综合力学性能。
一、调质钢的热处理
(一)预先热处理
为了消除和改善前道工序(铸、锻、轧、拔)遗存的组织缺陷和内应力,并为后道工序(淬火、切削、拉拔)作好组织和性能上准备而进行退火或正火工序就是预先热处理。
关于调质钢在切削加工前进行的预先热处理,珠光体钢可在Ac3 以上进行一次正火或退火;合金元素含量高的马氏体钢则先在Ac3 以上进行一次空冷淬火,然后再在Ac1以下进行高温回火,使其形成回火索氏体。
(二)最终热处理
调质钢一般加热温度在Ac3以上30~50℃,保温淬火得到马氏体组织。淬火后应进行高温回火获得回火索氏体。回火温度根据调质件的性能要求,一般取500~600℃之间,具体范围视钢的化学成分和零件的技术条件而定。因为合金元素的加人会减缓马氏体的分解、碳化物的析出和聚集以及残余奥氏体的转变等过程,回火温度将移向更高。
二、调质钢的金相检验
(一)原材料组织检验 调质工件在淬火前的理想组织应为细小均匀的铁素体加珠光体,这样才能保证在正常淬火工艺下获得良好的淬火组织---细小的马氏体。
(二)脱碳层检验 钢材在热加工或热处理时,表面因与炉气作用而形成脱碳层。脱碳层的特征是,表面铁素体量相对心部要多(半脱碳)或表面全部为铁素体(全脱碳),从而使工件淬火后出现铁素体或托氏体组织,回火后硬度不足,耐磨性和疲劳强度下降。因此调质工件淬火后不允许有超过加工余量的脱碳层。金相试样的磨面必须垂直脱碳面,边缘保持完整,不应有倒角。脱碳层的具体测量方法可按GB/T 224-1987标准进行。
(三)锻造的过热和过烧检验
锻造加热时,由于加热温度高,不仅奥氏体晶粒粗大,而且有些夹杂物发生溶解而在锻后冷却时沿奥氏体晶界重新析出。一般过热时,仅出现粗大的奥氏体晶粒并产生魏氏组织。在一些低合金钢中还会出现粗大的贝氏体或马氏体组织。 过热时沿奥氏体晶界析出的常为MnS或FeS。用一般试剂无法侵蚀显示奥氏体晶界,最好方法用饱和的硝酸铵溶液进行电解侵蚀。侵蚀后试样的奥氏体晶界呈白色网状。由于过热锻件晶粒粗大,使得塑性和韧性下降,容易造成脆断。
当钢加热到更高温度,接近液相线时,会出现过烧现象。过烧特征是钢的粗大晶界被氧化和熔化,锻造时将产生沿晶裂纹,在锻件表面出现龟裂状裂纹。
(四)调质钢的淬火回火组织
调质钢正常淬火组织为板条状马氏体和针片状马氏体,当含碳量较低时,如30CrMo等,形态特征趋向于低碳马氏体。当含碳量较高,如60Si
2、50CrV等,形态特征趋向于高碳马氏体。
如果淬火加热温度过低,或保温不足,奥氏体未均匀化,或淬火前预先热处理不当,未使原始组织变得细匀一致,导致工件淬火后的组织为马氏体和未溶的铁素体,后者即使回火也不能消除(图5-1)。
图5-1 低碳马氏休+网状铁素体 (500 X) 图5-2 45钢调质处理之回火索氏体 (500×) 如果淬火加热温度正常,且保温时间足够,但冷却速度不够,以致不能淬透,结果沿工件截面各部位将得到不同的组织,即从表层至中心依次出现马氏体、马氏体+托氏体、托氏体+铁素体等组织。甚至表层也不能得到全马氏体组织。
当工件淬火温度正常,保温时间足够,且冷却速度也较大,过冷奥氏体在淬火过程中未发生分解,那么淬火后得到的组织应是板条状马氏体和针片状马氏体。在随后的高温回火过程中,马氏体中析出碳化物,最终得到的是均匀且弥散分布的回火索氏体(图5-2)。
第三节 弹簧钢的金相组织及检验
弹簧钢是用于制造各种弹性元件的专用结构钢,它具有弹性极限高、足够的韧性、塑性和较高的疲劳强度。弹簧钢含碳量比调质钢高,其中碳素弹簧钢的含碳量的质量分数约为0.6~1.05%;合金弹簧钢的含碳量的质量分数为0.4~0.74%。弹簧钢中加入的合金元素主要为硅和锰,目的是提高淬透性。要求较高的弹簧钢,还需要加入铬、钒或钨等元素。
弹簧钢的热处理方法主要有两种: (1)淬火加中温回火处理。 用这种处理方法的多数为热轧材料以热成形方法制作的弹簧,或者用冷拉退火钢丝以冷卷成型的弹簧。中温回火后的组织为回火托氏体,此弹簧有很高的弹性极限与屈服强度,同时又有足够的韧性和塑性。 (2) 低温去应力回火。应用这一处理方法的主要是一些用冷拉弹簧钢丝或油淬回火钢丝冷盘成形的弹簧。
钢丝成材过程的强化处理也有两种方法。一种是冷拉后的淬火回火处理,其组织为回火托氏体。另一种为“铅淬”冷拔,即将热轧盘条加热到奥氏体状态,然后淬到450~550℃的熔化铅液中作等温处理,得到冷拉性能很好的回火索氏体,最后通过一系列的冷拔,得到一定规格尺寸与强度的钢丝。这种钢丝组织为纤维状的形变回火索氏体。
弹簧钢的金相检验内容有非金属夹杂物、石墨、表面脱碳、显微组织等。
(一)石墨碳与非金属夹杂物检验 检查石墨碳及非金属夹杂物时,试样取样部位一般都在材料端部,也可按照双方协议的规定。其检查方法及评级可分别按 GB/T 10561-1989和GB/T 13302-1991标准进行评定。石墨碳及非金属夹杂物是弹簧钢的内部缺陷。
(二)表面脱碳层检验 在弹簧钢各种材料标准中对表面脱碳均有明确的规定,一般脱碳深度根据材料的厚度或直径的百分数而定,而且冷拉材料要比热轧材料严格,如公称直径≤8 mm的热轧圆钢,
其规定总脱碳层不大于直径的2.5%,而同规格的冷拉钢则为不大于2%。 检查材料表面脱碳时,试样的切取部位均在材料两端或其中任意一端,如为弹簧成品或半成品,一般可在任意部位取。脱碳层检验标准为GB/T224-1987。
(三)显微组织检验 经过退火处理热轧弹簧钢,其组织是珠光体或珠光体和网状铁素体。规格较大的冷拉弹簧钢一般经过球化退火处理,组织为球状珠光体。冷拉碳素弹簧钢丝(包括冷拉的65 Mn弹簧钢丝),因冷拉前经过索氏体转变(俗称铅淬)处理,所以冷拉后组织呈纤维状的索氏体。油淬火回火钢丝的组织为回火托氏体。图5-
3、图5-4分别为油淬火回火钢丝组织和冷拉铅浴处理钢丝组织。
图5-3 65Mn弹簧钢之回火托氏体 图5-4 50CrV弹簧钢冷拉铅浴处理 组织 (500×) 之形变索氏体组织 (500×)
用热轧弹簧钢制作弹簧时,由于采用热成形方法,然后需进行淬火、回火处理,故原材料的组织检验可以省略。冷拉退火钢丝用冷盘法加工弹簧,则要检验原材料组织的球化程度。若球化不良,则材料要重新球化退火。检查“铅淬”冷拉钢丝组织时,磨面应取纵向,其他试样磨面可以取任意方向。
对于用碳素弹簧钢和合金弹簧钢制作的内燃机气门弹簧,在检验组织及缺陷时,应按GB/T 2785-1988《内燃机气门弹簧技术条件》进行。对于汽车钢板弹簧的金相检验,则按照JB 3782一1984《汽车钢板弹簧金相检验标准》进行。金相试样应在钢板全长的l/4处截取,且截面距钢板一端距离不得小于50 mm。在检查带状组织时,金相磨面应取钢板的纵向截面。
第17篇:检验人员授权书
检验人员授权书
经公司考核和资格确认,现授予同志为本公司检验员,检验员职责与权限按公司《岗位说明书》执行。
2013年3月5日
第18篇:特种设备检验人员
特种设备检验人员、无损检测人员资格考核
报 名 须 知
1.中国特种设备检验协会承担的考试项目:
2.各项考试时间:
中国特种设备检验协会制定年度考试工作计划,于每年年初公布在中国特种设备检验协会网站上。中国特种设备检验协会培训部为配合相关考试项目举办相应考前辅导(培训),考前辅导自愿参加,辅导活动结束后即参加考试。
3.报名办法:
(1)按照总局要求(点击访问总局网站),检验检测人员资格考核,包括初试(取证)(包含补考)、复试(换证)、复试补考(补考),全部需要同时实行网上报名和纸制资料报名。请参加考试人员先到“检验检测人员管理系统”网上报名,网址http://jz.cnse.gov.cn/login.php。网上报名如有问题,请咨询该系统管理部门,电话:010-5906898
8、59068997。
(2)网上报名注册成功后打印《特种设备检验检测人员申请表(考试、证书申请)》,连同其他纸制申报资料(见本《须知》第4项、第5项、第6项)邮寄到中国特种设备检验协会(邮寄地址请见本《须知》第10项),中国特种设备检验协会不接受电话、传真、电子邮件等方式的报名。
(3)请在报名截止日期之前完成网上报名和纸制资料的邮寄,“报名截止日期”是指报考人员完成网上报名且将纸制申报资料寄达中国特种设备检验协会的日期,逾期不再受理。
(4)报名后可在“检验检测人员管理系统”中查询报名情况。报考人员网上报名及纸制报名资料全部合格后,才算报名有效,我协会依纸制报名资料进行资格审查,资料不全者应在报名截止日期之前补齐所缺资料,补交资料时,请在补交的资料上注明参加的班次及项目。
4.初试(取证)需要提交的纸制资料:
5.复试(换证)需要提交的纸制资料:
(1)复试(换证)申请表(在“检验检测人员管理系统”报名后生成的表格,表格需经申请人签字后方为有效,无需贴照片)(原件)1份;
(2)复试(换证)项目的证书复印件1份。
注:上一年度延期到下一年度复试的,需提供由总局颁发的延期证书。
6.关于补考:
(1)补考人员应具备补考项目的报考条件(如:补考报名时,所持低级别证应在有效期内); (2)需提交的资料:相应项目的申请表(在“检验检测人员管理系统”报名后生成的表格,表格需经申请人签字后方为有效,无需贴照片,请打印后于右上角注明“补考”)(原件)1份,此申请表应于相关项目报名截止日期之前邮寄至中国特种设备检验协会。
7.考试报到的通知:
中国特种设备检验协会将根据报名情况及相关考试安排,提前在网上公布各个考试项目的报到事宜(举办时间、地点等等)和人员名单。所有的考试活动均不再寄发书面报到文件。遇有特殊情况,需要对个别考试项目进行调整时,将提前在中国特种设备检验协会网站上予以公布,敬请随时浏览、关注该网站的各项更新,确保积极提前做好准备,按时参加考试。
8.考试结果查询:
请到中国特种设备检验协会网站之“全国考委会\\考核结果发布”中查询(点击访问)。
9.发证查询及执业注册:
(1)考试合格的人员请到中国特种设备检验协会网站之“全国考委会\\寄证查询”中查询(点击访问)资格证寄出的相关信息。
(2)收到资格证书后,应由所在单位按照《特种设备检验检测人员执业注册管理办法》的规定及相关办事程序(点击查看),到中国特种设备检验协会办理执业注册。
10.中国特种设备检验协会考试部门联系方式:
中国特种设备检验协会秘书处
全国特种设备检验人员资格考核委员会秘书处
全国锅炉压力容器无损检测人员资格鉴定考核委员会秘书处
2012年01月01日
第19篇:检验人员辞职报告
检验人员辞职报告
在一个职场工作几年后,我们可能会作出离职的决定,这时就要静下心来好好写写辞职报告了。是不是苦于写不出正规的辞职报告呢?以下是小编帮大家整理的检验人员辞职报告,欢迎大家分享。
检验人员辞职报告1
尊敬的领导:
您好!首先感谢您在百忙之中抽出时间阅读我的辞职信申请报告。
我是怀着十分复杂的心情写这封辞职信的。自我进入医院之后,由于您对我的关心、指导和信任,使我在检验行业获得了很多机遇和挑战。经过这段时间在医院的工作,我在检验领域学到了很多知识,积累了一定的经验,对此我深表感激。
由于我自身能力的不足,近期的工作让我觉得力不从心。为此,我进行了长时间的思考,觉得医院目前的工作安排和我自己之前做的职业规划并不完全一致,而自己对一个新的领域也缺乏学习的兴趣。
为了不因为我个人能力的原因而影响医院的运作,经过深思熟虑之后我决定辞去目前在医院的检验工作。我知道这个过程会给您带来一定程度上的不便,对此我深表抱歉。非常感谢您在这段时间里对我的教导和照顾。在医院的这段经历于我而言非常珍贵。将来无论什么时候,我都会为自己曾经是医院的一员而感到荣幸。我确信在医院的这段工作经历将是我整个职业生涯发展中相当重要的一部分。
祝医院领导和所有同事身体健康、工作顺利!
再次对我的离职给医院带来的不便表示抱歉,同时我也希望医院能够体恤我的个人实际,对我的.申请予以考虑并批准。最后,祝我们县医院一切顺利,万事如意。
此致
敬礼!
辞职人:xxx
20xx年xx月xx日
检验人员辞职报告2
尊敬的医院领导:
您好! 我很遗憾自己在这个时候向医院提出辞职申请。 十分感谢医院多年来对我的培养与帮助,使我在这个温暖的大家庭里成熟、成长。十六年来在我们医院的工作中,我学到了许多的医学技术知识,学会了很多做人的道理,积累了丰富的人生经验。在这里,我有过欢笑,也有过泪水,更有过许许多多的收获。在这里,有我不可磨灭的成长记忆,是我此生刻骨铭心的成长摇篮!同时,也非常感谢医院领导和同事们对我的信任与厚爱,使我30来岁就担任了党支部书记与科室负责人,给了我很多的荣誉,使我的人生历练如此精彩,让我倍感荣耀。我会十分重视并永远怀念在医院的这段经历,也会无比珍惜与大家的深厚感情,我确信这依然会是我的人生今后继续努力奋进的动力。 很遗憾的是检验科在我的领导下沦落到今天这般境地,实在是有负领导之所托及同事们的信任,在这里我仅向大家表示无比的愧疚!现提交辞职申请报告,对于由此给医院造成的不便,我深感抱歉。我将到其他单位去寻找适合我发展的平台,望领导批准我的辞职申请,并安排好工作交接人选。祝大家身体健康!
此致
敬礼!
申请人:
日 期:
第20篇:检验人员年终总结
年 终 总 结
今年的工作总体上来说比较忙碌,由于我是检验技术员,要全面保证检验工作的正常运转,满足生产和用户的须求。今年中在领导的帮助和支持下,在同事们的相互协助中,我学到了很多知识与技能。
今年中工作主要内容包含有:原材料的进货检验、外协加工件的检验、产成品检验、产成品的提交验收和日常的事务处理工作。
外协加工件检验:外协件一般尺寸要求高,检验的尺寸比较多,就给检查带来一定的难度。所有产品的加工件都要先送检到我们部门,为保证产品的质量和工作进度,对于数量少的外协件或者加工要求高的件实施全数检,对于要求不高大批量的外协件,我们会进行抽检验收。检查时我会认真地对每个产品比照图纸要求进行逐项进行核对,检查并填写检验记录单,对不符合项开具不合格处理单并通知送检者。由于机加工件的尺寸多,对专业知识要求强,那就更好地体现了我对专业知识过硬和对工作的认真。
原材料进货检验:原材料的进货检查是从源头上保障产品的质量,对产品质量的控制起到至关重要的地位。公司所有产品的原材料入库前我们都要全数检查,合格后方可入库。我要负责对原材料的符合性的判断,对每一种原材料都要全数和图纸进行比对检查,对符合要求的进行登记并做下检查记录,对不符合项要开具不合格处理单并通知送检者,保证入库的材料都是符合要求的原料。
产成品检验:成品的检查是保证我公司产品质量及性能的重要性。加工出来的产品都要通过我们成品检验进行全数验收,合格才能入库,由于成品的种类多数量大,还要进行三温检查,就给成品检查带来了很大的工作量,我就主动承担一些检查任务,对AMT、左右尾灯和调压器产品进行成品验收。AMT产品是我公司的重点产品,我对过程和成品进行全程检查并全部负责,全套产品其性能要求很高,相应对检查来说要求也就更高,那就更体现了我检查的专业技术。在成品检验忙不过来时还亲自到成检进行检查产品,在她们遇到困难时就主动帮她们进行协调处理,并指导她们在以后的检查工作中怎么应对处理。
成品的提交验收:产成品的提交验收是关系到用户代表对我公司产品的一个认同。满足用户和出库的需求时就会交验提交产品,当提交产品时我会整理提交产品目录,统计产品的品种及数量,并做出相应的产品提交单,当代表来验收产品时伙同检验进行产品的检查,直到顺利提交完产品。
日常的事务处理工作:对故障品的接收登记,协助部长处理一些日常工作,调节检验人员的工作量,协同技术部对其故障品的分析和处理,会同他们对一些产品进行例外检查和试验,协同生产部对产品和检验工作的调整,协同综合部对公司电脑的进行一些日常管理。
总之,在今后的工作中一定还要一丝不苟,仔细认真。工作之余还要经常总结工作教训,不断提高自己工作效率,并从中总结工作经验。检验岗位的日常工作比较繁琐,这就需要我们一定要勤于思考,改进工作方法,提高工作效率,减少工作时间, 不断学习的丰富自己的专业知识和专业技能,这会使我的工作更加得心应手。 以后我会以严谨的工作态度仔细完成自己的本职工作。
总结人:XXXX
2013/1/14
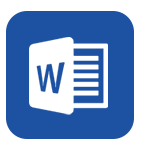