推荐第1篇:冲压车间工作总结
冲压车间工作总结
时光流逝,转眼间,我们即将迎来新的一年。在过去的一年中冲压车间在上级领导的大力支持和各部门的密切配合与车间全体员工的共同努力下顺利的完成了公司下达的各项任务,在此,我对冲压车间一年来的工作做以总结,同时也祈愿我们公司明年更美好。
一、工作回顾
1、产品产量方面
过去的一年里,车间在生产过程中批量小、技术不稳定和不完善的情况下,进行实验和摸索。为到达客户产量和质量的要求,我部门合理的调整生产加工工艺,和利用有限的资源,及时满足客户的交期,为今后产品打下了基础。
2、产品品质方面
在今年工作中,在确保生产任务的情况下。产品质量比往年有所提高。我坚信只要每个员工在提高产品意识情况下,全力的投入在生产每一个环节中,产品质量一定会稳步提高。
3、设备管理方面
在过去的一年里,各设备比较良好,并没有因为设备的问题影响到较大的工作,在定期的检修和保养下保证了设备的正常运转,进而确保了生产的稳定。
4、安全生产方面
在过去的一年里,我车间将安全生产纳入生产日常管理工作之中,随时做到车间员工的安全知识教育,监督和排除车间存在的安全隐患。确保了生产车间的有序运行。全年度未发生设备损坏事故。但是也出现了两次安全事故。
二、存在的不足和对策
生产车间在过去的一年里虽然做了很多的工作,也取得了一定的成绩,
但也还存在较多的问题,主要有以下方面的不足。
1、质量管理方面
1)员工质量意识淡泊:目前在一部分员工身上还存在事不关己,漠然置之的态度。这与培养员工质量意识,树立质量危机感,落实产品质量责任制做得不够好,不到位有很大的关系。
2)缺乏全员参与质量管理理念:我们现在缺乏的就是全员参与质量意思,在我们计件和工时制,没有质检的巡检下,有时候会出现一个真空地带,组员和组员之间谁都管谁都不管的局面。而且有的时候在生产现场执行力不到位的现象。
2、人员管理方面
员工的精神面貌和紧张感缺乏,在这方面我们必须策划一下整顿,制定完善的规章制度和培训计划。实施有效的激励措施,不断的提高员工的综合素质,以适应企业以后发展的需要。
三、从公司整体方面,我有几点
建议 。
1、建立健全的工作质量职责制度。对公司每个部门和员工都明确规定各部门和个人在工作中的具体任务、责任和权利,以便做到质量工作事事有人管,层层、人人有专责,办事有标准,工作有检查,这样才可以把质量有关的工作和广大员工的积极性结合起来形成一个严密的控制体系。
2、因公司员工的流动量大,个别的团队凝聚力和归属感不强,长期以来必将影响产品质量、工作效率,因此建议公司在企业文化和员工归属感和团队的凝聚力加强树立与培训。
3、经理、厂长、主任、班组长沟通比较少,让工作没有明确长远的方向,建议要定期召开工作会议,兼听下面员工的意见,敢于荐举贤才,总结工作成绩与问题,及时采取对策!
四、自身总结
2014年的工作已经告一段落,在这一年里,我经过自身努力,克服各种
困难,特别是在领导的大力支持下,这一年是有意义的、有价值的、有收获的。 基本上完成了本年度的 工作,经历 这两年来的生产管理工作为今后的工作打下了一定的经验基础。
虽然2014 年有所收获,但是也有自身的不足之处:
1.虽然年轻充满干劲,但是经验缺乏,在处理突发事件和一些新问题上存在着较大的欠缺。
2.跟不上来料加工单的加工进度,还缺乏主动与他们的沟通和交流的积极性 ,不善于有效的表达。这些个人因素直接影响到了工作的效果。
2014 年度工作规划
1.加强自身学习和实践,继续提高。 针对自己的岗位,重点是深入学习相关业务及研发相关知识,提高解决问题的能力。
2.竭尽全力完成 生产任务
在生产过程中充分沟通,过程受控, 在生产上更大的力度,完美的执行,
以健康愉快的心态积极主动地完成 生产任务。
3.完善自身素质。
工作保持长久的热情和积极性,所以这些年来我一直坚持做好自己能做好的事,一直做积累,一步一个脚印坚定的向着我的目标前行。
最后,我想说不管在哪里工作,做什么工作,态度和心态很重要,遇事把心放宽,才能更好的处理和解决面对的问题,从容的面对挑战,不断的去丰富充实自己,客观的面对自己的不足,更好的去改进,每个人都会有美好的明天!
我将加强自主管理的意识,勇于开拓创新,加强理论和业务学习,不断提高业务技术水平。也将会遇到很多困难,我相信,在领导关心培养下、同事的帮助下、自己的努力下,我将不断提升自己的工作技能水平和个人文化素质,为公司 建设作应有的贡献。
推荐第2篇:冲压
重庆工业职业技术学院
冲压模具及设备设计
题目: 端盖冲压模具设计
系 部: 机 械 系
专业名称: 模具设计与制造 班 级: 10 模 具 306 姓 名: 翟 露 学 号: 201010230632 指导教师: 洪 奕
2012-6-13
1
目录
一,端盖的工艺性 ........................................................................4 二
冲压工艺方案设计分析与确定 ........................................11 三.冲压工艺计算 ......................................................................14
四、冲压设备的选择..................................................................16
五、模具间隙 ..............................................................................17
六、冲裁模具凹、凸模刃口尺寸的确定。...........................19 七.闭合高度..................................................................................20
八、拉伸模具主要零部件的设计与选用 ...............................20
九、冲模工作零件的材料选用及热处理要求 .......................23 模具使用及维护说明书 .............................................................24 参考文献 ·····························································································27
2
前言
拉伸对于日常生活中的应用很广泛,是把一种材料变成我们可以利用的状态。拉伸是利用拉伸模在压力机的压力作用下,将平面柸料或空心件制成开口空心件的冲压工艺。
本说明书用到了很多我们已经学过的课程,还用到了一些课外的资料裁完成了这个课题设计,如:《冲压模具及设备》、《机械制图》、《机械制造基础》、《模具加工工艺》《公差与配合》等多门课程。查资料用得最多的是《中国模具大典》具体的标准件尺寸都是从上面参照取得
在这过程中刚开始不懂的时候,只有不断问同学,其中中途有次方案设计的时候真是云里雾里的做着做着就想放弃,感觉自己实在不想做了,但是由于有前面的冲压设计基础并不断询问同学才完成了。还有就是力的计算那部分和模具选择那部分,计算复杂繁琐模具更不知道在那能找到,后来也还是经过同学的帮住和相互讨论并一起查资料解决了该问题。
由于我还是一个设计的初学者,设计的水平有限,在该设计的过程中避免不了有的错误,请老师同学体谅,谢谢!
3
一,端盖的工艺性
4
对于冲裁来说工艺性如下: ㈠
经济性分析:
由于该产品为大批量生产,因此该零件适合冲压。 ㈡ 材料:
由图纸可知,该产品材料为08钢板,查资料书《冲压模具及设备》一书中29页2—3可知,它属于“冲压常用金属材料的力学性能”因此该产品适合冲压。 ㈢
结构尺寸:
1形状:冲压件的形状应尽量属于比较简单的类型,而且有一定的规则性,这样有利于材料的合理利用,以便节约材料,减少工序数目,生产周期短,效率高,提高模具寿命,降低冲件成本,此冲压件形状简单,故适合冲压,弯曲的形状也不是很复杂。
2尖角:因为冲呀件的内外转角处要尽量避免尖角,如果是尖角,那么他对模具的要求就很高的,模具在工作一段时间后很容易磨损的,因而模具的寿命就很短,生产效率不高,而且生产出来的零件有可能达不到要求。零件和模具的尖角处都很容易崩刃的,这样抄作工人的安全得不到保证,应以圆弧过渡。根据客户提供的图纸可知该零件没有直角,所以该冲压件满足要求。
3凸出悬臂和凹槽:冲裁件尽量避免有狭长的凸出悬臂和凹模,否则冲出来的零件精度达不到要求,很容易变形,对模具要求也很高,模具的寿命也不长。根据客户提供的图纸可知,该零件没有过长的窄长悬臂和凹槽,故适合冲压。
5
4冲孔:冲孔时孔的尺寸不应太小,否则会影响凸模的强度,从而影响零件的质量,查《冲压模具及设备》29页表2-3得08钢板的抗剪强度为255-353Mpa,查《冲压模具及设备》88页表4-3得圆形孔大于1.3t
因为该冲压件没有孔,所以不需要考虑。 ㈣、冲裁件精度与断面粗糙度。 1冲裁件精度等级:
冲裁件的经济公差等级不高于IT11级,一般落料件公差等级最好低于IT10级,冲孔件公差等级最好低于IT9级。根据用户提供的图纸,查资料《互换性与技术测量》表2.3,19页“标准公差值(GB/1800、3-1998)”,由于该冲压件没有标公差,所以都按未注IT14.
总结结论:综合以上冲裁的分析,该零件适合冲裁。 对于拉伸件的质量问题控制和工艺性:
6
㈠ 拉伸件的主要质量问题及控制: 1,起皱
起皱是一种受压失稳状态。
1),起皱产生的原因:凸缘部分是拉伸过程中的主要变形区,而该变形区受最大切向压应力,当切向压应力较大而坯料的相对厚度又较小时,凸缘部分的厚度切向压应力之间失去应有的比例关系,从而在凸缘的整个周围产生浪形的连续弯曲。 2),影响起皱的主要因素:
坯料的相对厚度t/D,它的值不能太小 拉伸系数
拉伸模工作部分的几何形状与参数 3),控制起皱的措施:可以采用压料装置 2,拉裂
1)
拉裂产生的原因:在拉伸过程中由于凸缘变形区应力应变很不均匀,靠近外边缘的坯料压应力大于拉应力,其压应变为最大主应变,柸料有所增厚:而靠近凹模孔口的柸料拉应力大于压应力,其拉应变为最大主应变,柸料有所变薄。
2) 控制拉裂的措施:可以适当加大凸凹模圆角半径,降低拉深力,增加拉伸次数,在压料圈底部和凹模上涂润滑剂等方法来控制。 ㈢,弯曲件的结构与尺寸
1,由图纸可以知道该拉伸件的形状比较简单,对称,所以适合拉伸。 2拉伸件壁厚公差或变薄量要求一般不应超出拉伸工艺壁厚变化规
7
律,不变薄拉伸工艺的的筒壁最大增厚量约为(0.2-0.3)T即为(0.2-0.3),最大变薄量为(0.1-0.18)T即为(0.1-0.18)
3如果当零件一次拉伸的变形程度过大时,为了避免拉裂,需采用多次拉伸,在保证必要的表面质量前提下,应允许内外表面存在拉伸过程中可能产生的痕迹。对于该零件来说,可以不用多次拉伸就能满足零件质量的要求。
4为了解觉冲压件在拉伸过程中有回弹,在保证装配要求的前提下,应允许拉伸件侧壁有一定的斜度。
5对于拉伸件的底部或凸缘上有孔时,孔边到侧壁的距离应该满足 a≥R+0.5t,对于该冲压件来说没有孔,所以不需要考虑。
6拉伸件的底与壁,凸缘与壁,矩形件的四角等处的圆角半径应满足:r≥t,R≥2t.rg≥3t,对于该冲压件来说,只需要考虑r就行,t为1mm,即2>1,所以满足要求,该冲压件适合拉伸。
7,拉伸件的径向尺寸应只标住外形尺寸和内形尺寸,而不能同时标注内外形尺寸,带台阶的拉伸件,其高度方向的尺寸标注一般应以拉伸件底部为基准。对于该冲压件来说,没有台阶,只标注了外形尺寸。
8
㈣,拉伸件的精度
尺寸公差等级在IT13级下,不易高于IT11级,圆筒形拉伸件的径向尺寸精度查表《冲压模具及设备》244页表6-2得±0.40
对于精度要求高的拉伸件需要增加整形工序,而对于该冲压件来说,公差为自由公差,公差等级为IT14所以不需要要考虑整形工序。
㈤拉伸件的材料
拉伸件的材料要求具有较好的塑性,屈强比小,板厚方向系数r大,板平面方向系数△r小
由《冲压模具及设备》29页表2-3得抗拉强度为400 MPa,屈服点为196 MPa.所以屈强比为196/400约为0,49,所以对于该冲压件所用材料屈强比要小于0.66,所以该冲压件的材料满足要求,适合拉伸。
9
㈥ 旋转体拉伸件坯料尺寸的确定 1,坯料形状和尺寸确定的原则。
拉伸件的坯料形状一般与拉伸件的截面轮廓形状近视相同,对于该冲压件来说,拉伸件的截面轮廓形状是圆形,所以坯料形状为圆形。 2,表面积相等原则
对于不变薄拉伸,在拉伸过程中板料的厚度有增厚也有变薄,但是实践证明,拉伸件的平均厚度与柸料厚度相差不大。由于拉伸后拉伸件与柸料厚度相等,体积不变,因此按柸料面积等于拉伸件表面积的原则确定柸料尺寸。
对于该冲压件来说查《冲压模具及设备》P246(6-2)公式可以得到:
首先算出切边余量查《冲压模具及设备》P246表6-4,,由于h/d=20/109=0.18 比值比较小,但是由于材料的各向异性的影响,所以需要留切边余量,保证冲压件质量的要求。切边余量⊿h取1.2mm 拉伸件
的
柸
料
直
径
:
D=
√104X104+4X109X19.2+6.28X2X104+8X2.5X2.5 ≈144mm P247表6-6序号3的公式: 拉伸件的拉伸次数:
t/D=1/144≈0.007。查《冲压模具及设备》P246表6-8,得出该冲压件需要压边圈,查出〔m1〕=0.53-0.55 〔m2〕=0.76-0.78 〔m3〕=0.79-0.80 〔m4〕=0.81-0.82 〔m5〕=0.84-0.85 由于m=d/D=109/144=0.76,于第一次极限拉伸系数〔m1〕
10
=0.53-0.55,即m>〔m1〕,所以该冲压件的拉伸次数为一次
总结结论:综合以上分析,该零件适合拉伸。 二
冲压工艺方案设计分析与确定
结合前面所设计的内容,得冲压件的工艺方案设计如下,
1、冲压类型
从直观的看出该零件的冲压类型为分冲裁和拉伸。该冲压件的要求的精度不高不需要很大的变形,所以容易满足,不需要增加附加的冲压工序。最后根据图纸分析冲压件的形状特点来得知冲压的类型为冲裁和拉伸。 2,冲压工序次数
冲压工序的次数分为两种类型:同种工序和不同工序。
对于冲裁件来说没有同种工序,对于拉伸件来说有可能有同种工序如 果他是单工序模,则冲压工序次数为 两次,如果它是级进模或复合 模,则冲压工序次数也为一次。
2、冲压工艺方案 冲压工艺方案有三种如下: 方案一:落料——拉伸——切边 方案二:拉伸与落料复合——切边 方案三:落料与拉伸级进冲压——切边
首先分析方案一:落料——拉伸——切边
优点:1)模具的结果简单,寿命长,制造的成本低。
11
2)冲出的制件精度高。 缺点:
1)工序分散,需要的模具多,设备多,工作人员也多,因 此提高了成本。
2)生产效率也低。适用于单件小批量生产。
3)在搬运过程中容易的变形。影响冲压件的精度。 4)安全系数不高。所以不适合采用
方案二:落料与拉伸复合——切边
通过此方案工艺路线可知,冲压件在该工艺方案中冲压的次数有一次,同时也可已知道该冲压件在工艺方案中冲压组合的方式为复合工序的冲压
优点:
1) 工序比较集中,结构紧凑,需要的模具数量少,所占用设备少,同时也减少工作人员,占地面积小 2) 生产效率高。适合于大批量生产。 3) 冲出的制件精度高,冲压件比较平整。 4) 模具的寿命比较高 缺点:
1) 模具结构复杂,制造难,维修不方便。
2) 冲压件的质量相对于“方案一”而言相对要低一些。 3) 模具的结构复杂,因此同时也对设备的要求也要高一些。
12
方案三:落料与拉伸级进冲压——切边
通过方案三的工艺路线可知,冲压件在该工艺方案中冲压的次数有一次,同时也可以知道该冲压在工艺方案中冲压组合的方式为级进冲压工序。 优点:
1)容易实现机械化,因此安全性相对于前面的几种方案要高一些
2) 工序集中,所需的模具数量少,设备数量少,也减少了工作人员。 3) 生产效率高 缺点:
1) 模具结构复杂,设计比较复杂,制造困难,维修也不方便,寿命也低,模具尺寸比较大。 2) 冲压件的质量都比前面几道方案都要低一些。 3) 级进冲压工序所需求的设备要求高,因此也提高了成本。
4) 拉伸件是要先落料在拉伸,由于先落料时,柸料不会自动掉入拉伸的孔内,需要增加其他装置,导致模具更加麻烦。 5) 浪费材料。
3.优化冲压工艺方案
根据用户所提供的图纸,并对图纸进行分析可知,冲压件的质
13
量要求并不高,最高的精度等级IT14,生产为大批量的生产,同时也对模具的寿命相对于较高,并且也要利于操作者的便利,生产效率也较高。因此通过对上诉工艺综合分析并对三种方案进行比较,选择最后确定的一种方案二,即拉伸与落料复合模。
三.冲压工艺计算
前面已经算出了坯料直径为144mm,拉伸次数为一次。, 排样分类:
a.有废料排样 b. 少废料排样 c. 无废料排样
由图纸分析可以得知尺寸的精度要求不高,形状较规则,结构简单,则选用少废料排样方法不浪费材料。 ㈠
料边与搭边和调料宽度的确定:
根据用户所提供的图纸可以知道该冲压件的厚度t=1mm最大宽度Dmax=144mm查《冲压模具及设备》P107可得工件的搭边值a1=0.8mm侧料边值a=1 mm 由图纸可以知道,可以知道该冲压件的精度要求不高,可以采用初定位(即导料板导向且无侧压装置),经过了解知该定位是人工送料,手工定位,操作者都是右手用力。因此导料销装到左侧。查表4-20可知Z=1mm,Δ=0.7mm。
查资料《冲压模具及设备》P106公式4-13,4-14得:
条料宽度B
0=(Dmax+2a+Z)
0
14
=(144+2x1+1)
=147
0.6mm
000.6
导料板间距离 :
B₀=B+Z
=Dmax+2a+2Z =144+2x1+2x1 =148mm 根据条料宽度查《冲压模具及设备》P30表2—5,选出了板料的规格为:2000x1500mm ㈡ 排样方式
经过上诉分析,本冲压件的排样方式的分为一种如下:
㈢ 材料的利用率。
每板条料数n3=(1500÷147)≈10条余30mm 每条零件数n4=(2000-1)/147≈13个 每板个数n=n3xn4=10X13=130个
材料利用率ŋ2=(130x16277.76)/(2000x1500)
15
x100%≈71%
四、冲压设备的选择 ㈠,拉伸力:
F=K1πd1tb
F=0.46X3.14X110X1X400=63553.6MPa 压料力:FY=π〔D2-(d1+2rd1)2〕p/4
FY=3.14〔1442-(110+2X2)2〕2/4
FY=12151.8 MPa 压料装置:
有图纸和精度要求,以及成本各方面的要求,选择弹性压料装置。弹性压料装置又分为三种:弹簧式,橡胶式,气垫式。气垫式的成本太高了,拉伸出来的零件质量高,所以不需要那么浪费。弹簧式和橡胶式通常用于浅拉伸件,所以适合该拉伸件,由于弹簧式比橡胶式拉伸力变化小一些,所以选折弹簧式压料装置。 冲裁时压力机应满足:
根据《冲压模具与设备》公式4—18可得F=KLT&,根据用户所提供的图纸t=1mm,查《冲压模具及设备》表2—3,29页得抗剪强度&=400Mpa因此可得:
F冲=K·L·t·Ʈ
=1.3x452.16x1x400
=235.1232KN
㈡ 卸料力,推件力,顶件力的计算:
由前面的分析可得选用弹性顶件的级进模,所以不需要算顶件
16
力,根据《冲压模具及设备》P110,公式4—20、4—
21、4—22得,查《冲压模具及设备》P110,表4-22得:kx=0.045 kt=0.055 kd=0.06则:
卸料力Fx=Kx·F冲=0.045x235.1232≈10.6KN 推件力:
Ft=n·Kt·F冲=1x0.055x235.1232≈13KN 顶件力FD=KD·F冲=0.06x235.1232≈14 KN 产品的卸料方式有:
1、弹性卸料+下出料
2、弹性卸料+上出料
3、刚性卸料+下出料
4、弹性卸料的倒装式复合模 我们选第1种则P=P冲+P推+P顶
=235.1232+13+14
=262KN 但是P≥(1.1-1.3)F∑
查资料《冲压模具及设备》P41表3-5压力机型号为“开式双柱可倾式压力机J23-35,其标称压力为350KN.
五、模具间隙
间隙对冲裁过程有着很大的影响,对冲裁件起着决定性的作用,它确定的方法有两种:理论确定法和经验确定法。由于理论确定法误差很大所以选择经验确定法。
由图知道冲裁件的厚度t=1mm,冲裁件的材料是08,则查《冲压模
17
具及设备》93页表4—10“冲裁模初始双面间隙z”,可知Zmin=0.1mm,Zmax=0.14mm。
如果不考虑其它因素,间隙越小越好,冲出来的零件质量就越好,但必须要考虑其他的因素,间隙很小时,材料的挤压和摩擦作用增强,容易产生凹模胀列,使凸凹模相互啃刃等异常现象,对于该零件来说边缘质量要求不高,孔的质量高,又是级进模,如果间隙很小,模具在使用过程中越变越大,影响模具的使用寿命。凸凹模磨损后刃口处形成圆角,冲裁件会出现很多的毛刺,也会使冲裁件质量变差的。因此为了减少模具的磨损,延长模具的寿命,保证冲裁件质量的情况下,因选择较大的间隙,所以间隙为z=0.14mm 拉伸工艺的辅助工序: 1.润滑
拉伸过程中,板料与模具的接触面之间要产生相对滑动,有摩擦力存在。对于该拉伸件来说,该冲压件外表面不需要太大的摩擦力,所以要润滑来满足零件的质量要求,,和减小拉应力,减小拉伸系数,提高模具寿命, 2,热处理
在拉伸过程中,由于板料因塑性变形而产生较大的加工硬化,会容易变形不能进行加工,为了能达到质量要求,工作正常运行,减小内应力,所以要进行热处理。而对于一般金属材料是对其退火处理。对于该拉伸件来说,它是用的08软钢,只要工艺过程制定准确,模具设计合理,可以不需要中间退火。
18
3,酸洗
经过热处理的工序件,表面有氧化皮,需要清洗后才可以继续进行拉伸或者是其它冲压加工。
六、冲裁模具凹、凸模刃口尺寸的确定。
为了使制造方便,制造成本低,调整方便、检验方便、装配方便,则选择配合制作来制造模具。
㈠、落料,落料时以凹模为基准,配作凸模 见《冲压模具及设备》P97查表4-14得X1=0.5 分类:A1=1440 0.62
则凹模尺寸:
Ad=(Amax-X·∆) Ad1=(144-0.5x0.62)
0.62/40=143.69
0.1550
故落料凸模刃口尺寸按凹模实际刃口尺寸配制,保证双面间隙
值0.140mm 如下图;
19
七.闭合高度
在前面的设计中,已经选择了设备,因此必须使模具的闭合高度介于压力机的最大装模高度与最小装模高度之间,这样才能把模具能装到设备上去满足下公式:(Hmax-T)-5≥(Hmin-T)+10查《冲压模具及设备》p41表3—5可得:JB23-35压力机参数如下 最大闭合高度:Hmax=270mm 最小闭合高度:Hmin=215mm (Hmax-T)-5>Hm>(Hmin-T)+10 当垫板T=50mm时,则 215mm>Hm>285mm
八、拉伸模具主要零部件的设计与选用
最后得出模具装配图如下: 图又百度文库选取增加了弹簧卸料板.方便卸料。
20
14151613121718192021222311109872462554321
㈠工作零件
1.凸凹模的圆角半径确定
凹模圆角半径:凹模圆角半径rd越大,材料越易进入凹模,但是rd过大了,又容易起皱。rd,因此在材料不起皱的前提下rd尽量取大一些。rd =0.8√(D-d)t=0.8√(144-109)X1=4.74mm 凸模圆角半径:因为该拉伸件拉伸次数只有一次,所以凹模圆角半径就是图纸上所标注的R2.2.凸,凹模的间隙
查《冲压模具及设备》P296表6-2得间隙为(1—1.1)t=(
1 21
—1.1)X1=1-1.1取1.1mm 3,凸凹模工作尺寸及公差
凸凹模工作尺寸及公差按最后一次拉伸的计算。 当拉伸件标注外形尺寸时,则:
Dd=(Dmax--0.75△)6d0=(110-0.75X0.62)+0.080=109.535+0.080
Dp=(Dmax--0.75△-2Z)-6P0=(110-0.75X0.62-2X1.1)-0.050=107.335-0.050 ㈡、定位零件
在这里用定位销,用来给φ10mm中间孔定位,保证零件的质量要求,把定位销安装在顶板上, d=10mm L=8 JB/T7649.9 材料45热硬度为43-48HRC.㈢卸料装置和出料装置
在这里选用刚性卸料,弹性不能够满足它的要求,采用两根推杆进行卸料。
顶板的规格为28X11.5 材45热硬度为43-48HRC.
卸料推杆M10 ㈣模架及其零件 1 模架
由于该冲压件精度要求不高,而且是小型零件,结构简单,左右送料比较方便,模架尺寸查《冲压模具及设备》如下: 上模座尺寸:250mmx200mmx45mm(GB/T2855.5—90) 下模座尺寸:250mmx200mmx45mm(GB/T2855.6—90) 凸模固定板尺寸:250mmx200mmx30mm
22
2 导向零件
根据用户所提供的图纸可知该冲裁件为大批量生产,为了保证模具有较高的精度和寿命,一般都采用导向零件对上、下模进行导向,以保证上模对于下模的正确运动,则选用导柱、导套导向。 导柱尺寸:32mmx190mm(GB/T2861.1—90) 导套尺寸:32mmx105mmx43mm(GB/T2861.6—90)
导柱与模座的配合:H7/r6,套在与模座的配合:H7/m6,导柱与导套的配合:H7/h6 ㈤ 其它支成和固定零件
模柄已经标准化,查《冲压模具及设备》p160图4-87中的c型凸缘模柄,用三个螺钉固定在上模的座的窝孔内,它的规格为查《冲压模具及设备》40mmX75mm,其配合为H7/js6模柄选用通用模柄A3材料 固定螺钉为M12.冲模中用的紧固件螺钉和销钉,其中螺钉起连接固定作用,销钉起定位作用则:
查《冲压模及设备》查表“螺钉规格选用”得选用M6螺钉。 螺钉之间、螺钉与销之间的距离、销钉螺钉距凹模刃口及边缘的距离均不应过小,以防降低模板强度,其最小距离查《冲压模及设备》表4—27得A=14 B=17 C=5销钉直径取10mm
九、冲模工作零件的材料选用及热处理要求
根据《冲压模具及设备》表9—4 凸模:材料Cr4W2MoV 工作硬度56~58HRC
23
凹模:材料Cr4W2MoV工作硬度60~62HRC 上、下模座:材料HT250 模柄:A3 顶板:45 工作硬度43~48HRC 导柱、导套:T10A 20钢渗碳深度0.5~0.8淬火回火60~62HRC 卸料板:Q275 凸凹模固定板:Q275 导料板:45 淬火回火43~48HRC 挡料销:T7A 淬火回火52~56HRC 导正销,定位销:T8 淬火回火52~56HRC 螺钉:45 头部淬火回火43~48HRC 销钉:45 淬火回火43~48HRC 推杆:45 淬火回火43~48HRC
模具使用及维护说明书
一、模具安装
模具安装在型号为J23-35:250KN,最大闭合高度是205的开式双柱可倾式压力机上。
安装前,检查压力机上的上下模具安装表面的清洁干净,并检查在有无在修磨模具后遗留物防止阻碍准确安装和意外事故。
安装时,根据模具闭合高度调整压力机滑块的高度,使滑块在下
24
止点式其底面与工作台之间规定位置,,将滑块再停于下止点,然后调节滑块的高度,使其模柄进入模柄孔,并通过滑块上的压块与螺钉将模柄固定。‘
安装完后,将压力机滑块上调3~5mm,开动压力机,空行程1~2次将滑块停于下止点,固定下模座,在进行试冲,逐步调整滑块所需的高度。将压力机上的卸料板调到需要的位置。
二、模具的工作过程
该模具可以完成落料,拉伸两个工序。调料送进时,由导料销导向定位,模具合模冲裁凹模,推件块向下运动,通过压边圈压料,再由拉杆和推件块向下运动,把拉伸件从凹模中卸出来。
三、模具的维护
1、确定模具导料部分无杂物。
2、打开压力机,空合模数次,保证正确运动和定位。
3、按模具设计参数调试模具并生产。
4、模具使用生产过程中操作人员应在模具前端两侧。
5、模具使用时应该经常检查模具的工作台面和工作刃口,清理材料的积瘤,排除灾不正确使用过程中的废料,以免废料涨模,导致模具破裂。
6、按总装图正确装配模具,并保证模具结构(见装配图)
7、按设计说明书中所选的压力机(J10 :250KN最大闭合高度是150mm的开式双柱可倾式压力机)安装模具在 工作台面上,并正确安装模具,保证模具中心与压力机中心重合。
25
8、请客户严格按照上述程序使用模具,严禁人体或异物在模具工作区间内,否则会造成人身伤害和财产损伤。
9、模具每次使用后应保养压料面,型面应清除材料积瘤。
10、存放前清洁模具 ,并要涂油后方可合模存放。
11、模具应放在方木上,并保证摆放不倾斜,以保证导柱导套正确配合。
12、建议客户每生产3000~5000件后,按以上保养方法保养模具一次,以便延长模具寿命。
13、打开模具确认模具型面无杂物,确定导料销、挡料销的位置正确。
14、模具在使用过程中发出异常声音时应立即停止工作,由现场的模修工检查并排除故障。
15、模具应在存放状态装卸。
总结
这次的设计是对拉伸的一个基本知识的应用。虽然这次做的这个 零件机构和工艺都比较简单。但是却包含拉伸的很多难点以及重点, 在这次设计中重新拿起了很久没用过的资料。加深了各方面知识的应用和记忆。
为了做这个课题设计我具体用到我们所学过的《冲压模具及设备》、《机械制图》、《机械制造基础》、《模具加工工艺》《公差与配合》
26
等多门课程。查资料用得最多的是《中国模具大典》具体的标准件尺寸都是从上面参照取得。
从分析零件图到模具的设计与装配图的绘制,在指导老师的带领下,自己认真的设计制作。其中遇到了很多自己无法解决的问题,然后通过与老师,同学的询问讨论,解决了不少的问题,也让我学到了很多东西,使我在这短暂的时间里,对冲压模具的认识有了很大的提高。
总之,本次课题设计,检验了我学习的成果,让我学到了很多,为我以后的工作奠定了基础。虽然设计出来任然有很多错误,但依我现在这水平是避免不了的。模具设计的整个过程,利用对零件图形的工艺性分析,设计出适合加工零件的模具,以达到生产要求,提高生产效率,零件的冲裁工艺性分析、冲裁模具结构的确定是模具设计的重要内容,只要合理就可以保证其加工精度及其各项指标要求。
最后谢谢洪老师传授我们这么丰富的知识和经验,以及帮助过我的同学朋友老师,谢谢你们的帮助,在今后的学习中我会更加努力的去学习。
参考文献
1.徐政坤主编.《冲压模具及设备》.北京.机械工业出版社.2005 2.屈波主编.《互换性与技术测量》.西安.西安电子科技大学出版社.2007 3.夏巨堪和李志刚主编的《中国模具设计大典》 4.黄淑蓉和陈国发主编《机械工程设计基础》
27 5.王茂元主编的《机械制造技术》
6.杨玉苹和高士龙主编的《接卸制图与AoutoCAD》 7.张红英和朱怀忠主编的《工程材料及热处理》 8.刘奎敏主编的《机械制图与计算机绘图》 9.参考百度文库
28
推荐第3篇:冲压
复合冲压:压力机的一次行程内在模具的一个工位上完成两道以上冲压工序,是一种多工序冲压。 连续冲压:压力机的一次行程内在连续模具的不同工位上完成多道冲压工序,是一种多工序冲压,也称级进冲压。
模具闭合高度:模具进行到下死点时,上模板的上表面与下模板的下表面之间的高度。 压力机闭合高度:滑块在下死点时,滑块底平面到工作台(不包括压力机垫板厚度)的距离。 冲裁:利用模具使板料沿着一定的轮廓形状产生分离的一种冲压工序。冲裁模:冲裁所使用的模具叫冲裁模,它是冲裁过程必不可少的工艺装备。凸、凹模刃口锋利,间隙小。 冲裁间隙:凸、凹模刃口间缝隙的距离。
弯曲:将板料,型材,管材或棒材等按设计要求弯成一定的角度和一定的曲率,形成所需形状零件的冲压工序。
回弹:塑性弯曲时伴随有弹性变形,当外载荷去除后,塑性变形保留下来,而弹性变形会完全消失,使弯曲件的形状和尺寸发生变化而与模具尺寸不一致的现象。
拉深:又称拉延,利用拉深模在压力机的压力作用下,将平板坯料或空心工序件制成开口空心零件的加工方法。
起皱:由于切向压应力引起板料失去稳定而产生弯曲。
凸耳:板料经过冲压成形后,原本应该平齐的壁沿变成高低不平的波浪形,把波浪形中凸起的部分称为凸耳。 拉裂:薄板成形过程中板料变薄最剧烈处的径向拉应力大于板料的抗拉强度,此处就会拉裂。 胀形:利用模具强迫板料厚度减薄和表面积增大,以获得零件几何形状的冲压加工方法。 胀形工艺方法:起伏成型:板料作用下,通过局部胀形而产生凸起或凹下的冲压加工方法。主要用来增加零件刚度和强度。圆柱形空心毛胚胀形:将圆柱形空心毛胚向外扩张成曲面空心,零件的冲压加工方法。张拉成型:将毛坯贴靠在凸模表面,对毛坯附加张拉力使毛坯成弯曲件的冲压加工方法。 翻边:利用模具把板料上的孔缘或外缘翻成竖边的冲压加工方法。按工艺特点分:内孔翻边,外缘翻边,变薄翻边。按变形性质力分:伸长类,压缩类,体积变形的变薄翻边。伸长类翻边特点:变形区材料受拉应力,切向产生伸长变形,导致厚度减薄,容易发生破裂。压缩类翻边特点:变形区材料切向受压缩应力,产生压缩变形,厚度增大,容易发生起皱。内/外曲翻边:用模具把毛坯上内凹/外凸的外边缘翻成竖边的冲压加工方法。
影响圆孔翻边成型或极限的因素如下:1材料延伸率和应变硬化指数n大,k小,成型极限大。2孔缘无毛刺和硬化时,k小,成型极限大。3用球形,锥形,抛物形凸模翻边时,k小,成型极限大。4板料相对厚度越大,k越小,成型极限越大。 冲裁力:冲裁过程中凸模对板料施加的压力。 卸料力:从凸模上卸下箍着的料所需要得力。
推件力:将梗塞在凹模内的料顺冲裁方向推出所需要的力。 顶件力:逆冲裁方向将料从凹模内顶出所需要的力。
翘曲:冲裁件呈曲面不平现象。它是由于间隙过大、弯矩增大、变形拉伸和弯曲成分增多而造成的,另外材料的各向异性和卷料未矫正也会产生翘曲。
扭曲:冲裁件呈扭歪现象。它是由于材料的不平、间隙不均匀、凹模后角对材料摩擦不均匀等造成的。
变形:由于坯料的边缘冲孔或孔距太小等原因,因胀形而产生的。 排样:冲裁件在条料、带料或板料上的布置方法。
搭边:排样时冲裁件之间以及冲裁件与条料侧边之间留下的工艺废料。
负间隙冲裁:凸模尺寸大雨凹模尺寸,冲裁过程中出现的裂纹方向与普通冲裁相反,形成一 个锥形毛坯。
应变中性层:板料弯曲时,外层纤维受拉,内层纤维受压,在拉伸与压缩之间存在这一个既不伸长也不压缩的纤维层。 应力中性层:毛坯截面上的应力,在外层的拉应力过度到内层压应力时发生忽然变化的或应力不连续的纤维层。
校正弯曲:板料经自由弯曲阶段后,开始凸凹模表面全面接触,此时,如果凸模继续下行,零件受到模具挤压继续弯曲,弯曲力急剧增大。
应变分布图:冲压成形时零件上各点或局部各点的应变分布情况。
应力分布图:零件上各点过局部各点的应变在二维主应变平面上的分布状况。
起伏成形:板料在模具作用下,通过局部胀形而产生凸起或凹下的冲压加工的方法。 圆柱形空心毛坯胀形:将圆柱形空心毛坯向外扩张成曲面空心零件的冲压加工方法。 拉深系数m:以拉深后的直径d与拉深前的坯料D(工序件dn)直径之比表示。 压力机闭合高度:滑块在下死点时,滑块底平面到工作台的距离。 模具的闭合高度:模具在最后工作位置时上下模之间的距离。模具闭合高度必须与压力机的闭合高度相适应,应介于压力机最大和最小闭合高度之间。 板料的冲压成形性能:板料对冲压成形工艺的适应能力。
两种失稳现象:拉伸失稳:表现为板料在拉应力作用下局部出现颈缩或破裂;压缩失稳:表现为板料在压应力作用下出现皱纹。
成形极限:板料发生失稳之前可以到达的最大变形程度。
成形极限图:板料在不同应变路径下的局部极限应变构成的曲线或条带形区域。
间隙对冲裁切断面质量的影响:凸凹模间隙控制在一定合理的范围内时,由凸凹模刃口沿最大剪切力方向产生的裂纹将相互重合,此时冲出的制件断面虽有一定斜坡,但比较平直,光洁,毛刺很少,且所需冲裁力很小,间隙过小时上下裂纹中将产生二次剪切,制件断面的中部留下撕裂面,两头为光亮带,在端面出现挤长的毛刺。间隙过大时,材料的弯曲与拉伸增大,拉应力增大,材料易被撕裂,且裂纹在离开刃口稍远的侧面产生,致使制件光亮带减小蹋角与断裂斜度都增大,毛刺大而厚,难以去除。间隙对尺寸精度的影响:间隙较大时材料所受拉伸作用增大,冲裁完后因材料的弹性恢复使落料尺寸小于凹模尺寸,冲孔孔径大于凸模直径。间隙较小时,由于材料受凸凹模挤压力大,冲裁完后材料的弹性恢复使落料件尺寸增大,冲孔孔径变小。间隙对冲裁力的影响:随间隙的增大冲裁力有一定程度的降低,但影响不是很大。间隙对卸料力、推件力的影响比较显著。随间隙增大,卸料力和推件力都将减小。间隙对模具寿命的影响:小间隙将使磨损增加,甚至使模具与材料之间产生粘结现象,并引起崩刃、凹模胀裂、小凸模折断、凸凹模相互啃刃等异常损坏。所以,为了延长模具寿命,在保证冲裁件质量的前提下适当采用较大的间隙值是十分必要的。
决定模具刃口尺寸及制造公差原则:落料制件尺寸由凹模尺寸决定,冲孔时孔的尺寸由凸模决定;考虑到冲裁中凸凹模的磨损,设计落料模时,凹模基本尺寸应取工件尺寸公差范围内的最小尺寸,设计冲孔模时,凸模基本尺寸则应取工件孔的尺寸公差范围内的较大尺寸;去顶冲模刃口制造公差时,应考虑制件的精度要求。 搭边的作用:补偿定位误差和剪板误差,确保冲出合格零件;增加条料刚度,方便条料送进,提高劳动生产率;搭边还可以避免冲裁时条料边缘的毛刺被拉人模具间隙,从而提高模具寿命。影响搭边值的因素:材料的力学性能,硬材料的搭边值可小一些;软材料、脆材料的搭边值要大一些。材料厚度,材料越厚,搭边值也越大。冲裁件的形状与尺寸,零件外形越复杂,圆角半径越小,搭边值取大些。送料及挡料方式,用手工送料,有侧压装置的搭边值可以小一些;用侧刃定距比用挡料销定距的搭边小一些。卸料方式,弹性卸料比刚性卸料的搭边小一些。 齿圈压板冲裁应满足条件:1模具有齿圆压块,有顶出器,形成刃口的三向压应力。2选择合理的合成压力,齿圆压板力。3模具间隙比冲裁间隙小很多。4刃口部分很小。
冲压工艺规程的主要内容:对冲压件进行工艺分析,通过分析比较确定最佳工艺方案,确定模具结构形式,合理选择冲压设备,编写工艺文件和设计计算说明书冲压件的工艺分析:技术方面:根据产品图纸,主要分析该冲压件的形状特点、尺寸大小、精度要求和材料性能等因素是否符合冲压工艺的要求。经济方面:主要根据冲压件的生产批量,分析产品成本,阐明采用冲压生产可以取得的经济效益。影响冲压工艺的因素:冲压件形状和尺寸;冲压件精度;尺寸标注;生产批量;冲压件厚度、板料性能等。冲压件各工序先后顺序安排原则:对带孔或有缺口的冲裁件,若用简单模,一般先落料,再冲孔或切口,使用连续模时则应先冲孔或切口,后落料;对带孔的弯曲件,孔边与弯曲区间距较大,可先冲孔,后弯曲,孔边在弯曲区附近,则先弯曲再冲孔;对带孔的拉深件,一般先拉深后冲孔,但若孔在零件底部,且孔的尺寸要求不高时,可先冲孔后拉深;多角弯曲件,一般先弯外角再弯内角;对于形状复杂的拉深件,先成形内部形状,在拉深外部形状;整形或校正工序应在冲压件基本成形后进行。工序的组合方式:生产批量大,进行复合模或连续模冲压;小批量生产常选用单工序简单模;尺寸过小的冲压件复合连续模生产;精度要求高用复合模。
单工序模:在压力机的一次行程内,只完成单一工序的模具。复合模:在压力机的一次行程内在模具的一个工位上完成两道以上冲压工序的模具。连续模:在压力机的一次行程内,在连续模具的不同工位上完成多道冲压工序的模具。模具压力中心:冲裁时的合力作用点或多工序模各工序冲压力的合力作用点。
材料弯曲现象:弯曲件的弹性回跳;中性层位置内移;弯曲区板料厚度的变薄;板料长度的增加;板料横截面的畸变、翘曲和拉裂。
最小相对弯曲半径:防止外层纤维拉裂的极限弯曲半径。影响因素:零件的弯曲角α;α越小,直边部分参与变形的分散效应越显著;板料纤维方向,弯曲件的折弯线与板料纤维方向垂直时最小,平行时最大;板料的表面和侧边质量,较差的话较大。
影响弯曲件回弹量的因素:材料的机械性能;切向应变;弯曲角α。减少回弹措施:改进弯曲件局部结构和选用合适材料;补偿法;校正法;拉弯法。
影响筒件拉深过程因素:板料性能;凸凹模圆角半径和摩擦:凹模圆角半径过大,将在毛坯自由表面区起皱,凸模圆角半径过大时,破裂将上移到已有加工硬化的区域,摩擦具有两重性,法兰部分润滑是有益的,可减少摩擦功,凸模与筒壁之间的摩擦可增大拉深能力; 圆筒件拉深过程中出现的问题及防止措施:起皱:原因:主要是由于法兰的切向压应力超过了板料的临界压应力所引起,最大切向压应力产生于毛胚法兰外缘处,起皱始于此处。措施:1采用压边圈,把法兰押金在凹模表面上2多道工序拉伸时,可采用反拉深防止起皱。3采用拉深筋或拉深槛。拉裂:原因:径向拉应力大于板料的抗拉强度,便会产生拉裂。防止措施:1采用适当的拉深比和压边力2增大凸模表面粗糙度3材料的比值小,n,R值大。凸耳:原因:毛胚的各向异性。防止措施:1提高材料的均匀性2合适的拉深比。残余应力:原因:拉深过程中,外表面为拉应力,内表面为压应力。防止措施:使板料变薄。要保证拉深顺利进行,每次拉深西数应大于拉深极限拉深系数,拉深系数小,拉深比大,变形程度大。 锥形件拉深方法:1当锥角α和比值h1/d2很小,且拉深比k不大于筒件第二次拉深允许值时,可先拉深成直径为d1的圆筒件,然后拉深成锥形件2先拉深称阶梯形,使其外轮廓切线与对称轴的交角等于锥角α,在最后一次将阶梯毛胚拉深成锥形零件。3逐次拉深称成锥面,逐次增加锥面长度。
弯曲模决定原则:工件标注外形尺寸时,应以凹模为基准件,间隙取在凸模上。工件标注内形尺寸时,应以凸模为基准件,间隙取在凹模上。
凸缘变形区的起皱主要决定于一方面是切向压应力σ3的大小,越大越容易失稳起皱;另一方面是凸缘区板料本身的抵抗失稳的能力。最易起皱的位置凸缘边缘区域。防止起皱:压边。 筒壁的拉裂主要取决于一方面是筒壁传力区中的拉应力;另一方面是筒壁传力区的抗拉强度。防止拉裂一方面要通过改善材料的力学性能,提高筒壁抗拉强度;另一方面通过正确制定拉深工艺和设计模具,降低筒壁所受拉应力。
冲压生产的三要素:合理的冲压工艺,先进的模具,高效的冲压设备。
根据材料的变形特点分:分离工序、成形工序。分离工序:冲压成形时,变形材料内部的应力超过强度极限σb,使材料发生断裂而产生分离,从而成形零件。分离工序主要有剪裁和冲裁等。成形工序:冲压成形时,变形材料内部应力超过屈服极限σs,但未达到强度极限σb,使材料产生塑性变形,从而成形零件。成形工序主要有弯曲、拉深、翻边等。 冲模根据工艺性质分类:冲裁模、弯曲模、拉深模、成形模等。根据工序组合程度分类:单工序模、复合模、级进模。
板料冲压成形性能包括:抗破裂性;贴膜性:板料在冲压过程中取得模具形状的能力;定形性:零件脱模后保持在模内即得形状的能力。冲压成形性能划分:主要用抗破裂性作为评定冲压成形性能的指标,α破裂:由于板料所受拉应力超过材料强度极限引起的破裂;β破裂:由于板料的伸长变形超过材料的局部延伸率引起的破裂;弯曲破裂:由于弯曲变形区的外层材料中拉应力过大引起的破裂;
模拟实验:模拟某一类实际成形方式来成形小尺寸试样的板料冲压试验。
板料的是个基本性能指标与冲压成形性能的关系:①屈服极限:材料受外力到一定限度时,即使不增加负荷它仍继续发生明显的塑性变形,发生屈服现象时的应力,用σs表示;σs小,材料容易屈服,成形后回弹小,贴模性和定位性好。②屈强比:钢材的屈服强度与抗拉强度的比值;屈强比小板料由屈服到破裂的塑形变形阶段长,有利于冲压成形,对抗破裂性有利。③延伸率:描述材料塑性性能的指标,材料在拉伸断裂后,总伸长与原始标距长度的百分;延伸率大板料允许的塑形变形程度大,抗破裂性较好。④应变硬化指数n:因塑性变形引起的硬度和强度增加的度量,表征材料的强度的;n值大,不仅增大失稳极限应变,而且使应变分布均匀,提高总体成形极限。⑤塑性应变比R:单向拉伸试样的宽度应变和厚度应变的比值;R值越大,板料平面方向比板厚方向易变形,不易起皱,且拉深力也小,传力区不易拉破,有利于拉深成形性能。⑥凸耳参数ΔR:凸耳影响零件的形状和尺寸精度,必要时需切除。⑦晶粒度N:N越大晶粒越细。⑧表面粗糙度:过大形成应力集中,对成形性能不利。⑨夹杂物和偏析:过大对成形性能不利。⑩应变速率敏感系数m:指材料在单项拉伸过程中变形抗力的增长率和应变速率的比值;m大有利于抑制成形时的颈缩或破裂。
推荐第4篇:冲压
1、分离工序:指冲压过程中使冲压件与板料的模具。
沿一定的轮廓相互分离的工序。基本工序:
13、复合模:在冲压的一次行程过程中,在同冲孔、落料、切断、切口、切边、剖切、一工位上同时完成两道或两道以上冲压工序的整修等。模具。
发生破坏的条件下,工件能够弯成的内表面最小圆角半径称最小弯曲半径。它是衡量弯曲变形程度的主要标志。
26、回弹:弯曲卸载后,塑性变形保留,弹
性变形消失,弯曲角形状和尺寸都发生与加载时变形方向相反的变化的现象称为回弹。
薄拉深。
工艺零件分为:工作零件(凸模、凹模、凸凹
9、拉深过程的毛坯分成五个部分:平面模)
凸缘区、凸缘圆角部分、筒壁部分、底定位零件(挡料销、定位板、导料板、侧刃) 部圆角部分、圆筒底部分。
卸料与推件零部件(卸料板、推件器、打杆)
2、冲孔:用冲孔模沿封闭轮廓冲裁工件或毛
14、冲裁间隙:指冲裁模的凸模与凹模刃口之坯,冲下部分为废料。间的间隙,也就是凸、凹模刃口间缝隙的距离。
10、拉深变形程度用 拉深系数m 表示。 结构零件分为:导向零件(导柱、导套、导板)
11、拉深模中压边圈的作用是防止工件安装与固定零件(模柄、模板、螺钉、销钉、在变形过程中发生 起皱
弹簧、垫板、固定板)
3、落料:用落料模沿封闭轮廓冲裁板料或条
15、冲裁是利用模具使板料沿一定的轮廓形状料,冲下部分为制件。分离的一种冲压工序。它包括切断、修边、落
27、拉深系数:是指拉深后圆筒形件的直径
与拉深前毛坯(或半成品)的直径之比 。
12、矩形件拉深时,直边部分变形程度
2、冲裁件断面质量及影响因素
相对较小,圆角部分变形程度相对 较断面特征:圆角带:出现在弹性变形阶段 大。
光亮带:出现在塑性变形阶段,光亮带占的比
4、塑性成形工序:指材料在不破裂的条件下料、冲孔等。主要指落料、冲孔
产生塑性变形,从而获得一定形状、尺寸
16、卸料力: 冲裁时,工件或废料从凸模上
28、极限拉深系数:在保证侧壁不破坏的情和精度要求的零件。基本工序:弯曲、拉深、成形等。
5、弯曲:把平面毛坯料制成具有一定角度和尺寸要求的一种塑性成形工艺。
6、拉深:将一定形状的平板毛坯通过拉深模
卸下来的力叫卸料力。
17、推件力: 从凹模内将工件或废料顺着冲
裁的方向推出的力。
18、顶件力: 逆着冲裁方向将工件或废料从
凹模腔顶出的力。
况下所能得到的最小拉深系数称为极限拉深系数(可查表)。
1、冲裁的变形过程分为弹性变形阶段、塑性变形阶段、断裂分离阶段三个阶段。
2、断面分为:圆角带、光亮带、断裂带、毛刺四部分
3、降低冲裁力的措施:阶梯凸模冲裁、斜刃口冲裁、加热红冲。
4、根据材料的利用情况冲裁排样的方式
13、拉深加工时,润滑剂涂在与凹模接例越大,断面质量越好 断裂带:出现在断裂触的 毛坯表面上。
分离阶段,断面粗糙带有斜度
14、拉深过程中的辅助工序有中间退火、冲裁件断面质量影响因素: 润滑、酸洗等。
1) 材料的性能对断面质量的影响
15、弯曲件展开长度的计算依据是弯曲2)模具刃口状态对断面质量的影响 前后应变中性层长度不变 。 判断:
3)模具冲裁间隙大小对断面质量的影响
3、模具冲裁间隙大小对断面质量的影响 冲压成各种形状的开口空心件;或以开口
19、排样:指冲裁件在板料或条料上的布置空心件为毛坯通过拉深,进一步使空心件改变形状和尺寸的冷冲压加工方法。
7、胀形:指从空心件内部施加径向压力,强
方式。
20、搭边:指冲裁时制件与制件之间、制件
与条料边缘之间的余料。
1、后次拉深的拉深系数可取得比首次拉深的拉1)当冲裁间隙合理时,凸模与凹模刃口沿最大
深系数小。(×)
剪应力方向所产生的裂纹在扩展时能够互相重迫局部材料厚度减薄和表面积增大,获得
21、材料利用率:是指冲裁件的实际面积与所需形状和尺寸的冷冲压工艺方法。
所用板料的面积之比。
分为:有废料排样、少废料排样、无废
2、拉深系数越小,说明拉深变形程度越大。(√) 合,这时冲裁件切断面虽有一定的斜度,但比料排样。
3、要分多次拉深的圆筒形件,每次拉深系数应较平直,光洁,毛刺很少平整、光洁,断面质
该大于或等于图表推荐值。(√)
量较好。
8、翻边:指利用模具将工件上的孔边缘或外
22、模具的闭合高度(H模):指模具在最低
5、废料分为结构废料和工艺废料两种
缘边缘翻成竖立的直边的冲压工序。
工作位置时,上、下模之间的距离。
6、模架分类:后侧导柱模架、对角导柱
4、一般情况下,拉深模的凹模的圆角表面粗糙2)间隙过大时,材料的弯曲与拉伸增大,拉应模架、中间导柱模架、四导柱模架等。
度应比凸模的圆角表面粗糙度小些。(√) 力增大,材料易被撕裂,材料在凸凹模刃口处
9、缩口:指将预先拉深好的圆筒或管状坯
23、模具压力中心:指模具冲压力合力的作料,通过模具将其口部缩小的冲压工序。
10、单工序模:在冲压的一次行程过程中,只能完成一个冲压工序的模具。
11、单工序模:在冲压的一次行程过程中,只能完成一个冲压工序的模具。
12、级进模:在冲压的一次行程过程中,在不
用点。冲压时,其压力中心应与压力机滑块中心相重合。
24、应变中性层:在弯曲变形时,由于材料
的连续性,因而在内层和外层中间存在一个既不伸长也不缩短的中间层,称应变中性层。
7、模具压力中心是指模具冲压力合力的
5、在拉深过程中,压边力过大或过小均可能造产生的裂纹会错开一定的距离而产生二次拉作用点。要求冲压时,其压力中心应与压力机滑块中心相重合。
8、拉深件分类按形状分为:旋转体零件
成拉裂。(√)
裂,第二次拉裂产生的断裂层斜度增大,断面
6、弯曲件的中性层一定位于工件1 / 2料厚位的垂直度差,毛刺大而厚,难以去除,使冲裁
置。(×)
件断面质量下降。
3)当冲裁间隙过小时,板料在凸、凹模刃口处
(直壁旋转体、曲面旋转体)、对称盒形
1、冲压模具的基本结构组成
件和不对称复杂零件。按变形过程中坯按模具零件的功能可分为工艺零件和结构零件的裂纹不能重合。凸模继续压下时,发生二次料厚度是否变化分为:不变薄拉深和变两部分。
剪切,在零件的中部产生断裂带,而两头为光同的工位上同时完成两道或两道以上冲压工序
25、最小弯曲半径:在保证毛坯外层纤维不
亮带,在断面出现挤长的毛刺,这时断面斜度力较小,结构复杂,可靠性与安全性较差。
表现为弯曲件的曲率变化及角度变化。
向产生压应力,在这两种压力的作用下,凸缘加高度
区的材料发生塑性变形并不断的被拉入凹模内,2)高度基本不变,仅减少圆角半径、逐渐减小
筒形直径的方法。
较小,毛刺虽有所增长,但易去除,只要中间适用范围:卸料力不是特别大的各种冲裁模。 影响回弹的因素: 撕裂不是很深,仍可应用。
4、冲裁间隙对冲裁过程的影响
6、弯曲的变形特点
1)材料的机械性能:回弹量与材料的σs/E成成为圆筒形零件。
11、起皱的原因、影响因素及防止措施 1)变形区主要发生在弯曲件的圆角部分,直线正比
1)、冲裁间隙对冲裁件尺寸精度的影响。当模部分没有变形只是刚性移动。 2)相对弯曲半径: r/t越小,弹性变形在总原因:起皱主要是由于凸缘处的切向压应力超
过了板料的临界压应力所引起的。 具制造精度确定后,间隙较大时,拉伸作用增大:2)变形区内,纵向金属纤维长度发生变化,内的变形所占的比例减小,回弹量就越小
落料件尺寸小于凹模尺寸,冲孔孔径大于凸模层纵向纤维受压缩短,外层纵向纤维受拉变长。 3)弯曲角:弯曲角越大,变形区的长度越大,影响因素:a:凸缘部分材料的相对厚度 直径;间隙较小时,挤压力大:落料件尺寸增大,3)弯曲变形区材料变薄:变形程度愈大,变薄角度回弹量就越大 冲孔孔径变小。
2)、冲裁间隙对冲裁工艺力的影响 现象愈严重
b:切向压应力的大小(拉深时,变形程度越大,
4)弯曲方式和模具结构:板料的弯曲方式有自就越容易起皱。)
4)板材弯曲时,分:窄板(b / t 3 )两种情况,窄板横断面形状为外窄回弹大,在有底的凹模内校正弯曲时回弹小。 极限小,变形区内的切向压应力也相对减小,料不易撕裂,冲裁力增大;间隙增大,材料所受内宽的扇形,宽板基本保持为矩形。
5)摩擦:可增大变形区的拉应力,使零件形状因此板料不容易起皱)
防止措施:主要采用压边圈防皱 拉应力增大,材料易产生裂纹,冲裁力减小。 5)弯曲变形程度可以用相对弯曲半径r/t来表更接近模具形状。 3)、间隙对模具寿命的影响 示。
6)弯曲件形状、模具间隙:形状越复杂,回弹a:用于双动冲床的刚性压边圈,主要靠调整压越小
9、弯曲工序的安排原则
边圈与凹模表面间隙保证防皱。
b:用于单动冲床的弹性压边圈,常用动源为橡间隙小,冲裁力增大,接触压力增大,摩擦力
7、弯曲时的主要质量问题有那些 增大,模具发生磨损,模具寿命降低;间隙过拉裂、截面畸变、翘曲及回弹
大时,板料的弯曲拉伸相应增加,使模具刃口1)、拉裂:外层纤维受拉变形而断裂。开裂原原则(1):对多角弯曲件,因变形会影响弯曲胶、弹簧、气垫。 端面上的增压力增大,容易产生崩刃或产生塑因: 性变形使磨损加剧,降低模具寿命。 为提高模具寿命,一般需要采用较大间隙。
5、卸料装置的分类及其特点和应用范围 1)刚性卸料板 a)弯曲线方向
件的形状精度,故一般应先弯外角,后弯内角。
12、影响极限拉深系数的因素
前次弯曲要给后次弯曲留出可靠的定位,并保1)材料的内部组织和力学性能:塑性好,组织
均匀,晶粒大小适当;屈强比小,塑性应变比b)板料表面和冲裁断面的质量剪切表面有缺证后次弯曲不破坏前次已弯曲的形状。 陷,不光洁,有毛刺
原则(2):结构不对称弯曲件,弯曲时毛坯容大,板料的拉深性能好,极限拉深系数就小。
2)、截面畸变:窄板弯曲时,外层受拉伸长,易发生偏移,应尽可能采用成对弯曲后,再切2)毛坯相对厚度t/D: t/D越小,极限拉深系
数越大 特点:能承受较大的卸料力,卸料可靠、安全;板厚板宽收缩,内层受压缩短,板厚板宽增加,开的工艺方法。 但操作不方便,生产效率不高。 使板材截面变为梯形
原则(3):批量大、尺寸小的弯曲件,应采用3)拉深模具:凸模圆角半径、凹模圆角半径、
凹模表面质量 适用范围:料厚在0.5mm以上的材料,常用于3)、翘曲:弯曲过程中,内外层拉压相反的应级进模弯曲成形工艺以提高生产率。
单工序模,与凸模间的单边间隙一般:力在横向形成一平衡力矩,卸去载荷后,在宽原则(4):如果弯曲件上孔的位置受弯曲过程4)拉深条件:压边圈、次数、润滑 0.10.5mm。 2)弹性卸料板 度方向上引起与弯矩相反的弯曲,即翘曲
8、弯曲回弹及其影响因素
影响而且精度要求较高,则应在弯曲后再冲孔,
13、宽凸缘圆筒形件(dt/d>1.4)的拉深方法 否则孔的位置精度无法保证。
对于宽凸缘圆筒形件,在第一次拉深时,就拉成零件所要求的凸缘直径,在以后各次拉深中,特点:有敞开的工作空间,操作方便,生产效弯曲卸载后,塑性变形保留,弹性变形消失,
10、拉深变形过程
率高,冲压前对毛坯有压紧作用,冲压后又使弯曲角形状和尺寸都发生与加载时变形方向相在拉深力的作用下,毛坯内部的各个小单元体凸缘直径不变。
冲压件平稳卸料,从而制件较为平整;但卸料反的变化,这种现象称为回弹。弯曲回弹现象之间产生了内应力,在径向产生拉应力,在切1)圆角半径基本不变,缩小筒形直径来达到增
推荐第5篇:冲压4月份工作总结计划
00000000
2012年4月冲压厂技质科
工作总结
一、工艺管理
1.完成对车桥23种零件所有模具内部图片的拍摄,编制 ;
2.完成车桥23种零件的控制计划,过程FAMA及流程图等工艺文件的编制;
3.完善料FE-1仓库零件装箱标准,及装箱图片;
4.完成生产现场工艺文件的检查,填补工作,共补齐GC-2作业指导书2种零件的编制 ;
5.完成对生产过程中,所有出现问题的模具进行维修与跟踪;
二、质量管理
1.完成对5月改善活动的(样件、首件检具台的制作;);
2.完成对检具维护、整理、规划的改善;
3.完成对生产过程中不良品处理流程的更改与跟踪;
4.完成对返修不良品记录分析;
5.完成对发济南GC-1检具的跟踪,及其发放;(共计27付检具);
6.完成所有检具无定位销的统计,及其对FE-1检具的定位销补给;
7.完成对吉利反馈的问题零件进行跟踪;
8.完成对5月份自检、互检零件的奖金统计及其发放;
9.完成5月份质量会议记要的编制、及其更改;
三、其他
1、完成对新进员工安全,质量入职培训工作;
2、本月辞职人员0人,工作调动人员0人,新进人员1人,目前检验员7人,工艺员1人,质量员1人,返修组6人。
3、接收公司各部门文件,传阅并归档12份;
4、.上报、发放各类文件7份;
00000000
2012年05月冲压厂技质科
工作计划
1、对生产线员工进行质量培训工作。
2、跟踪所有零件在生产过程中出现过的质量问题。
3、及时跟踪产品所发生的问题点,并第一时间进行处理。
4、继续统计报废零件,返修零件,模具整改等工作。
5、FE-1作业指导书完善(图解、说明易发故障点,及时更新)。
6、完成样件、首件摆放台制作工作。
7、完成对检具的维护,整理,规划工作。
8、FE-1 检验基准(方法、周期、频次),指导书完善。
9、完成对冲压质量Audit评审工作。
10、对设备工艺参数检查。
推荐第6篇:冲压车间年度工作总结
时光流逝,转眼间,我们即将迎来新的一年。在过去的一年中冲压车间在上级领导的大力支持和各部门的密切配合与车间全体员工的共同努力下顺利的完成了公司下达的各项任务,在此,我对冲压车间一年来的工作做以总结,同时也祈愿我们公司明年更美好。
一、工作回顾
1、产品产量方面
过去的一年里,车间在生产过程中批量小、技术不稳定和不完善的情况下,进行实验和摸索。为到达客户产量和质量的要求,我部门合理的调整生产加工工艺,和利用有限的资源,及时满足客户的交期,为今后产品打下了基础。
2、产品品质方面
在今年工作中,在确保生产任务的情况下。产品质量比往年有所提高。我坚信只要每个员工在提高产品意识情况下,全力的投入在生产每一个环节中,产品质量一定会稳步提高。
3、设备管理方面
在过去的一年里,各设备比较良好,并没有因为设备的问题影响到较大的工作,在定期的检修和保养下保证了设备的正常运转,进而确保了生产的稳定。
4、安全生产方面
在过去的一年里,我车间将安全生产纳入生产日常管理工作之中,随时做到车间员工的安全知识教育,监督和排除车间存在的安全隐患。确保了生产车间的有序运行。全年度未发生设备损坏事故。但是也出现了两次安全事故。
二、存在的不足和对策
生产车间在过去的一年里虽然做了很多的工作,也取得了一定的成绩,但也还存在较多的问题,主要有以下方面的不足。
1、质量管理方面
1)员工质量意识淡泊:目前在一部分员工身上还存在事不关己,漠然置之的态度。这与培养员工质量意识,树立质量危机感,落实产品质量责任制做得不够好,不到位有很大的关系。
2)缺乏全员参与质量管理理念:我们现在缺乏的就是全员参与质量意思,在我们计件和工时制,没有质检的巡检下,有时候会出现一个真空地带,组员和组员之间谁都管谁都不管的局面。而且有的时候在生产现场执行力不到位的现象。
2、人员管理方面
员工的精神面貌和紧张感缺乏,在这方面我们必须策划一下整顿,制定完善的规章制度和培训计划。实施有效的激励措施,不断的提高员工的综合素质,以适应企业以后发展的需要。
三、从公司整体方面,我有几点建议 。
1、建立健全的工作质量职责制度。对公司每个部门和员工都明确规定各部门和个人在工作中的具体任务、责任和权利,以便做到质量工作事事有人管,层层、人人有专责,办事有标准,工作有检查,这样才可以把质量有关的工作和广大员工的积极性结合起来形成一个严密的控制体系。
2、因公司员工的流动量大,个别的团队凝聚力和归属感不强,长期以来必将影响产品质量、工作效率,因此建议公司在企业文化和员工归属感和团队的凝聚力加强树立与培训。
3、经理、厂长、主任、班组长沟通比较少,让工作没有明确长远的方向,建议要定期召开工作会议,兼听下面员工的意见,敢于荐举贤才,总结工作成绩与问题,及时采取对策!
四、自身总结
2012年的工作已经告一段落,在这一年里,我经过自身努力,克服各种困难,特别是在领导的大力支持下,这一年是有意义的、有价值的、有收获的。 基本上完成了本年度的 工作,经历 这两年来的生产管理工作为今后的工作打下了一定的经验基础。
虽然2012 年有所收获,但是也有自身的不足之处:
1.虽然年轻充满干劲,但是经验缺乏,在处理突发事件和一些新问题上存在着较大的欠缺。
2.跟不上来料加工单的加工进度,还缺乏主动与他们的沟通和交流的积极性 ,不善于有效的表达。这些个人因素直接影响到了工作的效果。
2013 年度工作规划
1.加强自身学习和实践,继续提高。 针对自己的岗位,重点是深入学习相关业务及研发相关知识,提高解决问题的能力。
2.竭尽全力完成 生产任务
在生产过程中充分沟通,过程受控, 在生产上更大的力度,完美的执行,以健康愉快的心态积极主动地完成 生产任务。
3.完善自身素质。
工作保持长久的热情和积极性,所以这些年来我一直坚持做好自己能做好的事,一直做积累,一步一个脚印坚定的向着我的目标前行。
最后,我想说不管在哪里工作,做什么工作,态度和心态很重要,遇事把心放宽,才能更好的处理和解决面对的问题,从容的面对挑战,不断的去丰富充实自己,客观的面对自己的不足,更好的去改进,每个人都会有美好的明天!
我将加强自主管理的意识,勇于开拓创新,加强理论和业务学习,不断提高业务技术水平。也将会遇到很多困难,我相信,在领导关心培养下、同事的帮助下、自己的努力下,我将不断提升自己的工作技能水平和个人文化素质,为公司 建设作应有的贡献。
推荐第7篇:冲压车间年终工作总结
2011年度冲压车间工作总结
在以吴董事长为首的公司领导坚强领导下,冲压车间2011年全体员工全面贯彻落实科学发展观,积极应对复杂多变的宏观经济环境,锐意改革进取,齐心协力狠抓安全生产,深入挖掘生产潜力,努力节能降耗,注重产品质量,开展岗位技能培训,不断提升生产技能,努力打造优秀团队,取得了显著成绩,全年共计生产1496种15197897件/套产品,产品合格率达到99%以上,产品报废率同比2010年下降30%,完成了公司下达的全年生产计划,为公司发展做出了积极努力。
一年来,我们冲压车间管理班子贯彻执行公司《生产车间相关管理标准》,认真履行自己的职责,按照公司领导的工作指示和生产部月、周生产计划,做好本部门工作管理,组织生产,现将冲压车间2011年工作总结向领导汇报,请审阅。
一、生产与现场管理
在严格按照生产部下达的每周和临时性增补计划,组织实施生产的同时,及时将各生产过程中发生的不符合产品技术要求的产品进行打磨、复压、校正等措施,增加边角料利用,优化生产程序,加强各机组员工轮岗技术培训,为生产需求做储备,针对生产过程中出现的问题,及时与相关部门沟通,解决,确保生产有序进行。
现场管理方面,在加强生产现场监督管理的同时,及时做好产品入库、转序、清理、整顿,保持生产现场清洁,产品、工位器具摆放有序,追求“5S”管理目标。
二、质量管理
严格督促员工执行公司质保部产品质量管理条例规定,从生产源头抓起,
注重细节,从原材料尺寸、材质、数量到产品模具安装调试,专人负责,重点防范,严肃认真核查员工生产图纸、工艺卡等相关技术文件的领取和产品“三检”过程,及时与相关部门沟通解决生产过程中出现的产品质量问题,整改合格后,再继续生产,设立产品质量奖惩制度,对员工每月承兑产品质量奖励和处罚,对提高产品质量,增强员工工作责任心起到了促进作用。
三、安全、设备管理
吸取2010年几起工伤事故教训,一年来狠抓员工安全教育,监督员工严格认真执行安全生产规章制度和操作规程,加强安全生产巡查力度,发现安全隐患及时排除、整改,认真做好安全巡查记录,每天交接班前管理人员做好安全生产情况对接工作,在全体员工的共同努力下,本年度冲压车间无重大工伤事故发生。
严格执行设备操作规程和设备维护保养制度,督促、抽查各机位员工上下班对设备例行维护保养,填写设备点检卡,发现问题及时向设备部报修,防止设备人为损坏,下半年,冲压车间对所属冲压设备全部进行了清洗、保养和重新补漆。
四、模具管理
2011年我车间在积极协助模具车间对新产品模具调试工作同时,针对D802发动机支撑梁加固板切口模架操作存在安全隐患和D4-sgo骑马螺栓、B1第六横梁加固板等产量大、模具状态老化的产品模具提前报请整改复制,确保了车间正常生产,重点对车间模具库加强管理,重新对模具库现有模具进行归类、编序,完善了模具领用、归库、送修登记工作,使损坏模具情况有追溯性,对责任人的核查有了依据,对模具管理有了很好的效果。
五、工艺技术管理
2011年我们着重加强了图纸和相关技术资料收发、更新、归类存档工作,专人负责收发登记,对新产品 及时与相关技术部门沟通,并对一产品的生产特性收集整理相关数据在技术文件中标注,方便员工生产操作,确保生产操作与工艺文件规定的一致性。
回顾2011年冲压车间的工作和生产过程,虽然经过全体员工的共同努力,取得了一些成绩,但距离公司领导的要求还有很大差距,车间的工作管理和生产组织实施还不尽如人意,存在不少问题,具体如下:
一、2011年生产过程中虽然没有发生重大人身伤害事故,但有几起手臂划破和
手指碰伤事故,给公司造成了经济损失。
二、产品质量虽有稳中提升,但仍报废了7083件,返工7055件。
三、生产现场管理还有漏洞,各班组之间生产现场时常发生脏、乱、差现象。
四、模具使用后回库前清洁保养较差,归库不到位,送修不及时现象时有发生。
五、设备维护保养不细,加注润滑油不及时,故障发现不了问题。
六、“IE”改善活动开展不够广泛,积极性不高。
在新的一年中,我们要认真总结2011年车间管理工作和生产实施的经验教训,贯彻执行公司领导的各项指示,认真参加培训学习,不断提高工作管理水平。
一、严格执行公司制度的各项规章制度,进一步完善车间安全生产,质量监控
工作,加强员工技能培训,提高员工生产技能和质量意识,加大产品质量奖罚力度,降低产品报废和返工概率。
二、广泛开展深入挖掘节能降耗和“IE”改善活动,采取有效奖励措施,鼓励
员工积极提出合理化建议,进一步优化生产程序,营造车间改革创新,学习提高生产技能,努力工作的氛围,增强员工的团队凝聚力,培养更多的
生产技术骨干,提升车间生产能力。
三、加强在库模具管理工作,做好模具编序、定位、存档和闲置模具区分,完
善模具领用、归库、送修、整改机制和在库模具维护保养,严格执行模具使用管理规定。
四、加强车间冲压设备的日常维护保养工作,做到外表整洁,润滑充分,报修
及时,努力提高员工设备维护保养能力。
五、加强车间员工思想教育,努力提高员工的素养和职业道德,培养和发掘车
间人才,增强员工的凝聚力,打造优秀团队。
展望催人奋进的2012年,吴董事长将我们常青公司壮美新蓝图已经绘就在象征着腾飞的龙年,我们信心倍增,豪情满怀,冲压车间全体员工必将顽强拼搏,开拓进取,努力工作,为我们常青公司发展做出新贡献。
冲压车间
2012年1月8日
推荐第8篇:汽车冲压工程师工作总结
冲压工艺技术员2015年终总结及明年工作计划
自开始做冲压工作至今,已有一年多的时间了。在这一年前,凭借自己的努力、领导的提携,以及同事们的帮助,从一名刚刚出校门的大学生成为了一名冲压工艺员。在这期间,我主要负责冲压工艺的制定、维护及更新,虽然工作量比以前要繁重的多,但给我提供了一个全面了解冲压工艺的机会,加强了我对冲压工艺的认知和掌握,并提高了我对发生各类质量问题时独立分析和处理问题的能力,为我进一步从事动平衡设定改善工作打下良好的基础。
下面我对2015年的工作进行总结。
1、我对冲压工艺员工作的认识及态度
自被任命为冲压工艺员之后,我开始逐渐进入这一角色。虽然以前在大学里对冲压的相关知识有一定的了解和掌握。但做改善工作的过程中,感到要做一名合格的技术人员,还是觉得压力很大。这主要是由以下一些原因造成的,一是各条冲压生产线的工艺不是太精通;二是各条冲压生产线的设备也不精通;三是与人沟通能力差;我必须把以前漏掉的知识重新学习一次。面对这种压力,我感到自己责任的重大。了解条冲压生产线的工艺和设备,就成了我的工作重点。在2015这一年里,我对A、B、C三条冲压生产线的设备和工艺进行熟悉和了解,学习了如何制定冲压操作作业指导书以及对机床参数的设定,并对有异议的问题与相关人员进行探讨,以确保工艺的准确性。
2、本年度工作内容
(1)、负责A、B、C线EOP零件以及量产件的冲压工艺的制定,并及时维护、更新现有工艺,保证生产过程的稳定。
(2)、积极参加新项目的开发工作,做好新项目零件的数模图纸的存档工作、新项目零件的材料送样工作、以及试模工作,及时制作新零件的临时冲压指导工艺,并且协助同事们完成其他相关工作。
(3)、了解汽车体系相关知识,负责编制CP、PFMEA等相关文件,并协助体系专员与同事发现生产中所遇到的问题,并积极提出整改措施,来提升公司体系管理水平
(4)、做好冲压有关信息的收集工作,做好材料、废料、冲压工时等项目的制定与更新工作,并与同事们探讨材料、废料以及冲次的提升空间。
3、工作成果与亮点
(1)、基本完成冲压A、B、C线量产以及EOP零件的冲压工艺编制工作,尤其移新厂区的A线零件的冲压工艺编制工作,确保生产有序进行。
(2)、参与新项目零件的开发工作。
4、感受
要说苦和累,每一位工友肯定都深有体会,而作为冲压工艺员的我对其中的味道别有体味。为了不影响正常生产很多新项目零件的试模工作都放在周末以及晚上。因此我不得不牺牲周末以及晚上的时间对模具进行跟踪,加班也是家常便饭。很多人问我,这么干?值不值?我也不知道这样做值不值?但我知道我是一名冲压工艺员,工作需要,我必须这样做。这样才能保证项目不断推进推进以及生产的平稳有序
5、工作中存在的不足和2016年工作目标
在今年的工作中,我经过自己的努力,虽然取得了一定的工作成果。但我感到离一个优秀的冲压工艺员标的准还有很大差距。
这主要表现在
①在质量事故中,由于对质量、模具、设备等信息缺乏足够的了解,处理起来比较吃力。
②专业知识还是有所欠缺,在这项工作中,自己有点力不从心的感觉。
③在工作中,缺乏总结能力和汇总能力,思维单一,导致走了很多误区。
针对这些不足,我计划在下一年里要继续加强自身的学习力度,尽快将冲压工艺吃通吃透,并协调与其他技术员的关系。努力多学习一些专业知识,并向有经验的前辈学习,吸取他们的经验,提高自己的工作能力!
推荐第9篇:冲压班班长工作总结
2010 年 冲压班班长工作总结 各位领导,各位同事下午好: 2009 年即将结束,我们将迎来新的一年,在过去的一年中冲压班在上级领导和各部门的协调配合下,顺利的完成了公司及生产科下达的各项生产任务和其它相关的指标。 2009 年全年工作中,本班组坚持 “ 安全第一,预防为主 ” 的方针,除认真落实公司实行的安全生产责任制外,还将提高安全生产意识融入到工作中,切实提高岗位安全操作技能。每天早上利用晨会的时间给大家讲一些安全常识,让大家时时刻刻牢记安全的重要性。同时我们定期对车间设备进行维护保养,每天打扫车间的环境卫生,为生产的正常运行提供了一个良好的空间。 当工作需要加班加点时,大家能积极工作,没有任何怨言,这充分显示了冲压班工员的拼搏精神,更充分展示了我班员工 “ 爱岗敬业 ” 精神。在工作中我们除了执行公司下达的生产任务外,还吸取工作经验,诚然,我们目前的工作中也存在一些不足和问题,主要表现在: 1 、产品质量没有明显的提高,自检力度不够,员工的质量意识差,主要还是我的工作不到位, 2 、现在 5S 没有做好 虽然与前况相比,有了很大的进步。但在 5S 管理方面我存大着很多不足,最主要是缺少持之以恒的管理方针,有时为了准时交产量而忽略 5S 的持之以恒的管理。 4 、各种表格没有及时填写。 5 、个别员工还看不懂图纸,业务技能还需进一步提高。
推荐第10篇:冲压车间年度工作总结
2013年度冲压车间工作总结 2013年以想干事、会干事、干成事为目标。认真履行职责,圆满完成各项任务。为了今后更好的做好生产任务,总结经验,提高工作方法和效率,克服不足。
一、班组的建设与管理得到加强。
1、充分利用车间班前班后会,将公司做大做强的精神认真传达,使车间员工真正领会到公司的发展要求、前景和目标,筑建员工以厂为家的思想。
2、加强了自身专业知识学习。车间班组长的责任直接影响车间的工作质量,因此,了解产品的工艺要求,认真学习api标准,使我能真正发挥技术骨干和模范带头作用。
二、狠抓安全管理不放松。
1、加强了对班组安全检查力度,完善了岗位责任制,发现问题及时通报并限期整改,使安全隐患大大降低,确保了xx年的安全生产。
2、充分利用周六生产例会时间,认真分析一周来的安全生产情况,将车间发生的安全事故认真分析总结,吸取经验,杜绝类似事故的再次发生。
三、生产、技术管理得到加强。
质量技术科为班组配备了专职质检员,加强了对产品的检查力度,对产品的工艺各项参数进行控制,避免不合格的产品流出车间,减少了客户的质量异议 。
四、现场管理得到改善。
制定了现场管理制度,并在生产过程中认真执行,并认真组织实施,使现场管理得到大的改善。 虽然取得了一定的成绩,但仍存在着很多问题和不足,主要表现如下方面:
一、安全方面:
安全管理有好多没有到位,这主要表现在以下几点:
1、安全管理力度不够。安全培训不到位,检查不到位,有好多时候,由于我们的工作当中劳动量比较大,工人的体力消耗比较大,为此在生产安全检查过程中,发现的安全隐患没有严肃的指出或者没有按照安全管理制度进行处罚,现在想来是完全不对的,在安全事故没有发生以前,就应该不讲情面,只有这样,才能彻底消灭安全隐患。为此,我想在今后的工作中,不存在人情面子的安全隐患没有指出或处理的。
2、违章操作的几乎没有处理过。在工作过程中,有好多操作没有严格按照操作规程操作,但是当时又没有发生安全事故,所以大多只是口头批评,而没有严肃处理。现在想来,这是安全隐患的重中之重。因此在今后的工作中,凡是出现的任何违章操作的,一律停工休息。
二、生产、成本方面:
因简单追求产量,使有时个别班组为了当班的自身的利益,出现了:
1、交接班不协调。私自修改加工程序 ,对设备进行超负荷运行,磨损刀杆,对下一班的正常生产造成难度。
2、设备带病工作。在生产过程中,为了尽可能的提高产量,在设备出现故障隐患时,没有及时进行修理,结果既缩短了设备使用寿命,又加大了设备维修资金的投入,把设备的维修时间转移到了下一个班次,并延长了维修时间。凡是已经发现设备有简单的小故障并通知维修工维修,应该停车检修而没有停车的,加大处罚维修工的力度,同时我们在今后的工作中要进一步建立完善的管理制度,我在想能不能把技术工(维修工)分出几个档次,这可以通过考核或者评审的办法进行分档,这样如果发现维修工人不处理当班设备故障的,进行降低技术工档次的处罚。
3、管理不到位,有跑冒漏现象,成本考核制度不健全,落实责任不到位。应加大管理力度,建立成本考核制度,量化考核。
三、质量方面:
1、下料长度不一:原因:管理不到位。方案:(1)找最佳标准,定量管料长度(2)随时抽查。
2、产品成才率不高及不合格产品混入成品里:原因:员工没有责任心。方案:(1)加强教育及考核力度(2)加大巡检力度,防止漏检.
四、现场管理方面:
定置管理仍没有完全到位。到目前为止,我们还没有真正的对所有的物品进行定置管理,只是临时决定一些物品的摆放,同时由于工人的懒散性和素质的高低不等,有时在作业场地完成作业后,不能做到人走场地清,乱放的现象仍然存在。这一点我们应该建立定置管理图,以便在今后的工作中能够依图加强巡查,对未按照标准进行摆放的,进行严格处罚。
五、设备现场管理没有完全到位。
由于人人都有惰性,操作人员总是能省事就省事。这样设备上面的铁屑及切削液等经常不能及时清理。为此,我们准备加强设备铁屑及切削液清扫的检查,对能够及时清理并及时检查出设备隐患的,给予一定的奖励,对没有及时清扫的班组,则给予适当的处罚。
六、培训方面:
1、在岗位培训方面,不要说其他人了,就是我本人,实事求是的说,学习的也少了,我现在感觉靠经验进行管理是不行的,而现在我的技术知识又太有限了,因此在工作过程中大多靠的就是经验了。这一点在今后的工作中,准备加强学习,首先自己能够解决的办法就是多召开一些岗位工人的专题会议,让大家多谈一谈工作中的好的经验和办法,这样既提高了其他人的岗位工作能力,对我也是一个学习。
2、一般岗位的培训太少。我们现在只是在一些主要的岗位实行岗前培训,但是对一般岗位的培训几乎没有。这样大多数工人的各方面的素质差距太大,一般岗位人员认为自己不被重视,挫伤了一般人员的工作积极性。
七、个人存在问题:
1.自身管理水平欠缺,应继续加强学习,提升自身素养,提高管理能力。 2.工作力度不够大,工作细节没有妥善处理好。今后要把工作做细、做到位。 3.安全工作没有做到位。在以后我要严格落实各项规章制度,做好安全工作。
为切实抓好xx年班组的工作,我将按以下几个方面进行开展工作:
1、继续坚持“安全第一,预防为主”的方针,严格按照安全操作规程进行管理。全面落实安全生产责任制,重点抓好班组管理。发现问题立即处理当事人。对查出的安全隐患,当作事故对待,按照事故三不放过的原则进行处理。小事当作大事抓,把事故消灭在萌芽之中。
2、做好节能降耗,降低生产成本。(1)会同车间制定班组交接班制度,加大检查力度,提高产量,确保产品质量。 (2)加大低值易耗、辅材的考核,低值易耗品、切削液、机械油、刀片进行计量,降低产品消耗。
3、强化质量管理 (1)进一步完善生产工艺,对影响产品质量,如碰伤端面、内镗表面光洁度加大管理力度,防止次品与废品的出现。 (2)加大生产工艺的检查力度,对不认真执行工艺的员工进行通报批评,并上报处理。
4、认真落实公司下达的生产任务。(1)根据各车间用工人员情况,制定最佳用工人员方案,由班组和车间共同配合积极招收新工人,确保正常生产人员的配备。 (2)合理调度、均衡生产,根据生产需要,协调好各工序生产进度,合理调配各工序生产任务。
5、积极做好现场管理 (1)对成品或半成品以及废品区别存放,加强巡查,对未按要求进行处罚 (2)强化设备管理,责任到人,每月对设备管理、使用进行总结。 加强产成品的防护措施,将所有产成品全部盖好,做到防碰防撞
6、加强自身学习,并认真注重岗位培训。篇二:冲压车间年度工作总结
冲压车间年度工作总结 -总结 作应有的贡献。 〔冲压车间年度工作总结〕随文赠言:【受惠的人,必须把那恩惠常藏心底,但是施恩的人则不可记住它。——西塞罗】篇三:2011年冲压车间年终工作总结 2011年度冲压车间工作总结
在以吴董事长为首的公司领导坚强领导下,冲压车间2011年全体员工全面贯彻落实科学发展观,积极应对复杂多变的宏观经济环境,锐意改革进取,齐心协力狠抓安全生产,深入挖掘生产潜力,努力节能降耗,注重产品质量,开展岗位技能培训,不断提升生产技能,努力打造优秀团队,取得了显著成绩,全年共计生产1496种15197897件/套产品,产品合格率达到99%以上,产品报废率同比2010年下降30%,完成了公司下达的全年生产计划,为公司发展做出了积极努力。
一年来,我们冲压车间管理班子贯彻执行公司《生产车间相关管理标准》,认真履行自己的职责,按照公司领导的工作指示和生产部月、周生产计划,做好本部门工作管理,组织生产,现将冲压车间2011年工作总结向领导汇报,请审阅。
一、生产与现场管理
在严格按照生产部下达的每周和临时性增补计划,组织实施生产的同时,及时将各生产过程中发生的不符合产品技术要求的产品进行打磨、复压、校正等措施,增加边角料利用,优化生产程序,加强各机组员工轮岗技术培训,为生产需求做储备,针对生产过程中出现的问题,及时与相关部门沟通,解决,确保生产有序进行。
现场管理方面,在加强生产现场监督管理的同时,及时做好产品入库、转序、清理、整顿,保持生产现场清洁,产品、工位器具摆放有序,追求“5s”管理目标。
二、质量管理
严格督促员工执行公司质保部产品质量管理条例规定,从生产源头抓起,
注重细节,从原材料尺寸、材质、数量到产品模具安装调试,专人负责,重点防范,严肃认真核查员工生产图纸、工艺卡等相关技术文件的领取和产品“三检”过程,及时与相关部门沟通解决生产过程中出现的产品质量问题,整改合格后,再继续生产,设立产品质量奖惩制度,对员工每月承兑产品质量奖励和处罚,对提高产品质量,增强员工工作责任心起到了促进作用。
三、安全、设备管理
吸取2010年几起工伤事故教训,一年来狠抓员工安全教育,监督员工严格认真执行安全生产规章制度和操作规程,加强安全生产巡查力度,发现安全隐患及时排除、整改,认真做好安全巡查记录,每天交接班前管理人员做好安全生产情况对接工作,在全体员工的共同努力下,本年度冲压车间无重大工伤事故发生。
严格执行设备操作规程和设备维护保养制度,督促、抽查各机位员工上下班对设备例行维护保养,填写设备点检卡,发现问题及时向设备部报修,防止设备人为损坏,下半年,冲压车间对所属冲压设备全部进行了清洗、保养和重新补漆。
四、模具管理 2011年我车间在积极协助模具车间对新产品模具调试工作同时,针对d802发动机支撑梁加固板切口模架操作存在安全隐患和d4-sgo骑马螺栓、b1第六横梁加固板等产量大、模具状态老化的产品模具提前报请整改复制,确保了车间正常生产,重点对车间模具库加强管理,重新对模具库现有模具进行归类、编序,完善了模具领用、归库、送修登记工作,使损坏模具情况有追溯性,对责任人的核查有了依据,对模具管理有了很好的效果。
五、工艺技术管理 2011年我们着重加强了图纸和相关技术资料收发、更新、归类存档工作,专人负责收发登记,对新产品 及时与相关技术部门沟通,并对一产品的生产特性收集整理相关数据在技术文件中标注,方便员工生产操作,确保生产操作与工艺文件规定的一致性。
回顾2011年冲压车间的工作和生产过程,虽然经过全体员工的共同努力,取得了一些成绩,但距离公司领导的要求还有很大差距,车间的工作管理和生产组织实施还不尽如人意,存在不少问题,具体如下:
一、2011年生产过程中虽然没有发生重大人身伤害事故,但有几起手臂划破和
手指碰伤事故,给公司造成了经济损失。
二、产品质量虽有稳中提升,但仍报废了7083件,返工7055件。
三、生产现场管理还有漏洞,各班组之间生产现场时常发生脏、乱、差现象。
四、模具使用后回库前清洁保养较差,归库不到位,送修不及时现象时有发生。
五、设备维护保养不细,加注润滑油不及时,故障发现不了问题。
六、“ie”改善活动开展不够广泛,积极性不高。 在新的一年中,我们要认真总结2011年车间管理工作和生产实施的经验教训,贯彻执行公司领导的各项指示,认真参加培训学习,不断提高工作管理水平。
一、严格执行公司制度的各项规章制度,进一步完善车间安全生产,质量监控
工作,加强员工技能培训,提高员工生产技能和质量意识,加大产品质量奖罚力度,降低产品报废和返工概率。
二、广泛开展深入挖掘节能降耗和“ie”改善活动,采取有效奖励措施,鼓励
员工积极提出合理化建议,进一步优化生产程序,营造车间改革创新,学习提高生产技能,努力工作的氛围,增强员工的团队凝聚力,培养更多的
生产技术骨干,提升车间生产能力。
三、加强在库模具管理工作,做好模具编序、定位、存档和闲置模具区分,完
善模具领用、归库、送修、整改机制和在库模具维护保养,严格执行模具使用管理规定。
四、加强车间冲压设备的日常维护保养工作,做到外表整洁,润滑充分,报修
及时,努力提高员工设备维护保养能力。
五、加强车间员工思想教育,努力提高员工的素养和职业道德,培养和发掘车
间人才,增强员工的凝聚力,打造优秀团队。
展望催人奋进的2012年,吴董事长将我们常青公司壮美新蓝图已经绘就在象征着腾飞的龙年,我们信心倍增,豪情满怀,冲压车间全体员工必将顽强拼搏,开拓进取,努力工作,为我们常青公司发展做出新贡献。
冲压车间
2012年1月8日篇四:冲压车间年度工作总1 冲压车间年度工作总结
虽然2012 年有所收获,但是也有自身的不足之处: 1.虽然年轻充满干劲,但是经验缺乏,在处理突发事件和一些新问题上存在着较大的欠缺。
2.跟不上来料加工单的加工进度,还缺乏主动与他们的沟通和交流的积极性 ,不善于有效的表达。这些个人因素直接影响到了工作的效果。 2013 年度工作规划 1.加强自身学习和实践,继续提高。 针对自己的岗位,重点是深入学习相关业务及研发相关知识,提高解决问题的能力。 2.竭尽全力完成 生产任务
在生产过程中充分沟通,过程受控, 在生产上更大的力度,完美的执行,以健康愉快的心态积极主动地完成 生产任务。 3.完善自身素质。 工作保持长久的热情和积极性,所以这些年来我一直坚持做好自己能做好的事,一直做积累,一步一个脚印坚定的向着我的目标前行。
最后,我想说不管在哪里工作,做什么工作,态度和心态很重要,遇事把心放宽,才能更好的处理和解决面对的问题,从容的面对挑战,不断的去丰富充实自己,客观的面对自己的不足,更好的去改进,每个人都会有美好的明天!
我将加强自主管理的意识,勇于开拓创新,加强理论和业务学习,不断提高业务技术水平。也将会遇到很多困难,我相信,在领导关心培养下、同事的帮助下、自己的努力下,我将不断提升自己的工作技能水平和个人文化素质,为公司 建设作应有的贡献。
第11篇:冲压操作规程
冲压车间操作规程
1.上岗必须穿好工作服、劳保鞋,长发必须扎起并戴好工作帽。
2..检查电源开关及设备各处开关是否全部正常。光电保护装置等安全防护措施应完整好用,无松动现象。
3.开动电机空转试车,确认压力机各部分运行正常,作业指示灯显示正确。4..待装模具的各部分应无损坏、无松动、无变形。
5.调模员安装或拆卸模具时须轻搬轻放。必须在吊运前,将吊运元件安装牢固。
6.必须选择与工艺要求及模具结构相符的压力机。模具置入压力机,并得到正确的定位才能紧固。带模柄的模具,以模柄为定位,先紧固上模,后紧固下模。模柄小于压力机滑块的模柄孔时,必须采用专用开口衬套,衬套开口应正贴于滑块部分。
7.上、下模座与压力机滑块和工作台面完全贴合后,才能将紧固点逐个对称拧紧。紧固夹紧螺栓时,必须采用适当扳手,禁止在扳手上插入导管拧动螺帽。调模时必须采用压力机的寸动或微动装置,高度的调整必须仔细进行。
8.固定模具的紧固元件必须有防松装置(例如垫圈等),确认紧固可靠后方可进行试冲。试冲前工作台上扳手等杂物必须清理干净,模具上所有的润滑部位都必须润滑。 9.试冲前必须开启光电保护装置,冲制过程中严禁关闭光电保护装置。
10.成批生产开始前,调模员或班组长,应对操作员说明模具的功能,操作要点和安全防护等有关事项。
11.冲制一批工件后,必须将所有紧固元件再次紧固。冲制工作过程中,应随时注意模具的紧固情况,严防模具脱落。
12.冲压作业时,操作必须使用工具,严禁用手直接伸进模腔取物,手用工具不得放在模具上。冲制工件不得堆放在压力机工作台面上。
13.多人操作同一台压力机应有统一指挥,信号清晰,待对方作出明确应答,并确认离开危险区再动作。
14.操作员应时刻注意光电保护装置是否正常,如发现异常,应立即停机,机床启动开关处挂牌通告警示,班组长上报专业人员修理。
15.压力机发生溜车和电器失灵等现象,或模具发生损坏时,应立即停机,机床启动开关处挂牌通告警示,班组长上报专业人员修理。
16.对压力机进行检修、调整以及在安装、调整、拆卸模具时,应在机床断开能源(如电、气、液)、机床停止运转的情况下进行,并在滑块下加放垫块可靠支护,机床启动开关处挂牌通告警示。
17.实行脚踏开关领用制:作业需要使用脚踏开关的,须经班组长或主任确认,并认真填写【脚踏开关领用登记表】后才能使用,使用完毕后应及时归还。
18.使用脚踏开关前应检查是否处于正常工作状态,如有异常应立即停止使用,班组长上报专业人员修理。
19.在模腔内调整工件位置或揭取卡在模内的工件时,脚必须离开踏板。
20.操作完毕要切断压力机电源、关闭空气节门,应将滑块停在上止点,使设备处在停歇状态。 21.剪板人员在操作过程中,必须戴手套,防止板材划破手掌,严禁将手伸入保护隔栏,严禁拆卸保护隔栏。
编制人: 审核人:
第12篇:冲压操作规程
冲压安全操作规程
安全生产、人人有责,所有职工必须认真贯彻执行
一、工作前应按规定穿戴好劳保用品注意力要集中,禁止边操作边闲谈、或抽烟,违者罚款50元。
二、开车前进行检查各部位润滑系统是否良好,然后空运转二分钟是否正常,安全装置是否可靠,不按规定罚款50元。
三、头、手切勿伸入冲头行程冲模区内,严禁手入虎口,根据模具情况,要使用各种工具工作,在脚踏操作时,手脚配合要协调、思想要高度集中,加料和取料脚应离开踏板以免发生事故,在离模100毫米内不准戴手套操作,违规操作罚款500元。
四、落料:
(1)在落料生产过程中,所有落的板材不允许放在架子或者小车上面,要做到少放多拿,如发现有不按规定罚款50元。
(2)在落料生产过程中,所落在模具内的废品,要用吸盘或镊子拿出,决不允许用手取拿,如有违反者,罚款200元。
(3)冲孔、折弯、成型、在生产过程中,绝不允许用手取拿件,必须用专用工具比如(镊子、吸盘、钩子)等,如有违反罚款500元。
五、禁止在操作时与他人说笑、打闹、酒后严禁上机,严禁模具里面有双件以上的同时工作、如有发现罚款100元。
六、机动冲床踏板周围不许存放其他杂物,在运转过程中,严禁伸手取物或清除残料,违规操作罚款100元。
七、工作完毕后要切断电源,提前十分钟要清除脚料或废料使用的工具放置整齐,通道畅通,必须做到安全文明生产,如有不按规定罚款50元。
临沂星海工贸有限公司 编制:
审批:
第13篇:冲压模具设计
1、主要冲压工序
【1】分离工序(切断、冲裁(落料、冲孔)、切口、切边)【抗剪强度】 【2】变形工序(弯曲、拉伸、成形(起伏(压筋)、翻边)、缩口、胀形、
整形)【屈服期限】
(金属变形三个阶段:①弹性变形 ②均匀塑性变形 ③集中塑形变形)
2、冲压材料
【机器】考虑其强度和硬度
【电机电器】导电性和导磁性
【化工容器】耐腐蚀性
【1】材料塑形好,允许变形程度大,可减少冲压工序次数和中间退火次数
【2】延伸率(δ)、杯突试验深度大或屈服极限/强度极限((屈强比)σs/σb)、冷弯试验中的弯曲直径(d)小,其塑形就好。
【3】模具间隙是按材料厚度来确定的(材料厚度公差必须符合国家标准)
【公差过大会影响工件质量】
3、冲压机种类
【1】曲柄压力机(开式压力机、闭式压力机)
【2】双动拉深压力机
【3】摩擦压力机
【4】液压机
(*闭合高度、最大装模)
4、模具设计参数(标准件、压力中心) 4.1【冲裁间隙】Z=D凹—D凸(凹模直径D凹
、凸模直径D凸)(单边D/2) 4.2【凸凹模刃口尺寸计算原则——落料和冲孔】
4.21【落料件】尺寸取决于凹模尺寸,落料模应先定凹模尺寸,用减小凸模
尺寸来保证合理间隙。
【冲孔件】尺寸取决于凸模尺寸,冲孔模应先定凸模尺寸,用增大凹模
尺寸来保证合理间隙。
4.3【计算凸、凹模刃口尺寸需要用到的参数】Zmin 和Zmax、落料公差(δ凸、
δ凹)和冲孔公差(δ凸、δ凹)、系
数(χ) 4.4【冲裁力P0(N)】
【平刃口凸、凹模】 P0=Lδτ
【L(冲裁件周长mm)、δ(材料厚度mm)、τ(材料的抗剪强度MPa)】
【考虑其他因素,实际冲裁力:P =1.3P0≈Lδσb】【σb(材料的抗拉强度MPa)】 4.5【阶梯分布】一个模具里多个凸模,分为大凸模、小凸模,为防止折断,小
凸模一般比较短,与大凸模呈阶梯状分布,大、小凸模的高度差
为H(取决于材料厚度)。
(δ≤3mm时,H=δ;δ>3mm时,H=0.5δ) 4.6【卸料力、推件力、顶出力计算】
❶卸料力:P卸=K卸P(N)
❷推件力:P推=nK推P(N)
❸顶出力:P顶=K顶P(N)
【P(卸料力)、n(卡在凹模洞口内的工件(或废料)数目)、K(系数)】 4.7【排样、搭边和条料宽度】
4.7.1【排料】
4.7.1.1【排料方式】❶直排 ❷斜排 ❸直对排❹斜对排❺混合排❻多行排
nF 4.7.1.2【材料利用率(一个进距内的材料利用率η)】η=×100%
bh
F(冲裁件面积(包括冲出的小孔面积))
n(一个进距内冲裁件数目)
b(条料数目)
h(进距) 4.7.2【搭边】
搭边值大小,能太大,浪费材料;太小容易挤进凹模,影响模具
寿命。(搭边值大小可查表)
5、模具类型
【冲裁模具类型】❶单工序模❷级进模❸复合模 【凹模】
❶凹模孔口形式
❷凹模外形尺寸(凹模厚度H、壁厚C)
【凹模厚度H】H=Kb(mm) (K—系数 b—冲件最大外形尺寸)
【凹模壁厚C】 【小凹模】 C=(1.5—2)H (mm)
【大凹模】 C=(2—3)H (mm) 【凸凹模】(复合模)
(不集聚废料的凸凹模最小壁厚)
【黑色金属和硬材料】 1.5δ(须大于0.7mm)
【有色金属和软材料】 ≈δ(须大于0.5mm) 【凹模上螺钉孔、圆柱销孔的最小距离】(跟是否淬火有关,淬火距离比较大) 【凹模强度校核】(检验凹模厚度,因为凹模厚度不够,会使凹模产生弯曲,损
坏模具。
H最小=3P 10
【H最小—凹模最小厚度(mm) P—冲裁力(N)】
【凸模】
【结构型式】 ❶标准圆形凸模
❷带护套的小孔凸模(适用于冲孔直径与料厚相近的小孔) ❸快换凸模(用于大型冲模中冲小孔易损坏 ❹大圆凸模 ❺非圆形凸模
【凸模长度】 L=H1+H2+H3+Y 【H1—凸模固定板的厚度】
【H2—卸料板的厚度】
【H3—导尺的厚度】
【Y—自由尺寸(凸模的修磨量4—6mm;凸模进入凹模的深度0.5—1mm;凸模固定板与卸料板之间的安全距离A,可取15—20mm。】 【凸模强度校核】❶压应力校核❷弯曲应力校核
【凹模、凸模的镶拼结构】
【镶块紧固】
❶框套热压法❷框套螺钉紧固法❸销钉、螺钉紧固法
【镶块尺寸mm】
H:B:L=(0.6-0.8):1:(3-5)
尺寸范围:H(30-75);B(60-170);L(最大至300) 【凸模、凹模固定】
❶机械固定(采用螺钉紧固、压配合等方法) ❷粘结固定(①低熔点合金浇注固定法②环氧树脂粘结固定法③无机粘结剂固定
法④) 【定位零件】
3 【定位板、定位销】(定位板(定位销)高度与材料厚度有关) 材料厚度δ(mm):
3-5 定位板(销)高h(mm): δ+2 δ+1 δ
【导尺(或导料销)】
【侧压】❶簧片压块式 ❷弹簧压块式(侧压力大,适合冲裁厚料)❸ 压板
式(适用于单侧刃级进模)
【挡料销】挡料销高度与材料厚度有关,可以查表得到
【挡料销型式】❶圆柱头式挡料销❷钩形挡料销❸活动挡料销❹初始挡料销
【侧刃】切去条料旁侧的少量材料来限定送料进距(提高生产率,保证较高定位精度,有利于自动化)
【侧刃固定方法】❶压配合固定❷铆接固定❸螺钉固定❹销钉固定 【导正销】(主要用于级进模)
【型式】❶压入式❷螺钉固定式
【卸料和推件零件】 【型式】❶固定卸料板❷弹性卸料板❸废料切刀❹弹性卸料和刚性推件装置❺弹
性卸料和弹性推件装置 【弹簧、橡皮的选用】
❶【圆柱螺旋压缩弹簧】(弹簧压缩量、弹簧根数、弹簧装配长度)
❷【橡皮】
【卸料板和凸模之间的间隙】(可查表)
【卸料弹簧窝座深度】
【卸料板螺钉沉孔深度】
【打杆长度】
【顶杆长度】
【导向、联接固定零件及其他】
【导柱、导套 】(用于要求精度高的冲模)
【布置型式】❶后侧导柱❷中间导柱❸对角导柱❹四个(或六个)导柱
【结构型式】❶滑动导柱导套 ❷滚珠导柱导套
【导板】
【厚度】H1=(0.8-1)H凹
(H凹
—凹模厚度 )
【上、下 模】(模座分带导柱和不带导柱)
【垫板】
【凸模固定板】(❶ 圆形 ❷矩形)
【模柄】
【平衡侧压力结构】
【模具压力中心计算】
【模具总体设计】 ⑴【掌握资料】❶冲压件图纸及技术条件❷生产批量❸冲压设备❹模具制造条件
⑵【总体设计任务】❶模具类型的确定
❷操作方式、进出料方式的确定
❸定位、卸料、推件、导向、联接固定等型式的确定
❹模具压力中心的确定
❺模具外形尺寸确定 【模具类型确定】(以冲裁工件要求、生产批量、模具加工条件等为主要依据)
❶【冲裁工件要求、生产批量】单工序模、级进模、复合模
无导向模、导柱模、导板模
❷【模具外形尺寸确定】(包括模柄尺寸、闭合高度、模座俯视尺寸)(与
所选冲床规格有关)
❸【模座尺寸】一般冲床工作台每边尺寸大于下模座尺寸50—70mm
【模具设计中须考虑的安全措施】
【模具材料及使用寿命】
【冲压对材料的基本要求】
❶有足够的硬度和耐磨性(冲压模正常失效方式是磨损)
6 ❷有一定的强度和韧性 ❸有良好的加工工艺性 【模具常用材料】
【提高模具使用寿命的途径】
❶合理设计模具❷正确选用模具材料❸保证热处理质量和采用热处理新工艺❹保证加工质量和采用新的加工方法(加工模具新方法:①电火花加工和线切割加工(优点:不管材料硬度多高,均能加工,加工安排在热处理之后,从而解决热
7 处理变形问题)②低熔点合金和锌基合金浇铸(制造周期短,加工容易,成本低,废旧模具可以重熔再造))❺合理使用与维护
【冲裁件质量分析】(毛刺、剪裂带、光亮带、塌角)
【精冲】 ❶精冲过程 ❷精冲材料
❸精冲模设计的参数(⑴精冲力P总=P冲+P压+P推(①冲裁力②齿圈压板力③推板反压力④⑤);⑵凸凹模间隙) ❹精冲模具结构(设计注意事项:①刚度精度要求高②一般采用滚珠导柱模架③控制凸模进入凹模深度④添加排气孔或者排气槽⑤合理分布顶杆)
⑴模具结构:①活动凸模式②固定凸模式③简易精冲模
【弯曲】 【弯曲原理】
【弯曲变形过程】
【弯曲过程中的应力应变状态】
【应变中性层的位置及最小弯曲半径的确定】
【应变中性层的位置】
【最小弯曲半径的确定】
【弯曲件的回弹】
【回弹量的确定】
、
【影响回弹因素】❶材料的机械性能❷相对弯曲半径
r
❸弯曲角❹弯曲件的形状❺弯曲方式❻模具间隙 【减少回弹量的措施】
❶从改进产品设计和工艺来减少回弹量❷在模具结构上采取措施❸利用橡胶和
8 聚氨酯凹模进行弯曲❹采用拉弯工艺
【弯曲力计算】
【自由弯曲的弯曲力】
【弯曲件毛坯尺寸计算】
【弯曲件工序安排和模具结构】
9 【弯曲工序应考虑的原则】
❶两次弯曲成形❷三次弯曲成形❸对称弯曲❹连续工艺成型
【弯曲模的结构设计和典型结构】
⑴【弯曲模结构设计要点】
❶坯料放在模具应有可靠定位
❷不应使毛坯产生严重的局部变薄
❸弯曲过程中,应防止毛坯移动
❹弯曲区能得到校正
❺有消除回弹的可能性
❻毛坯放入到模具上和压弯后从模具中取出工件要方便
⑵【弯曲模具的典型结构】
❶V型件弯曲模❷ U型件弯曲模❸ 圆环件弯曲模❹ 铰链弯曲模❺连续弯曲模
【弯曲模工作部分的设计】
⑴【凸模、凹模圆角半径与凹模深度】
❶ 凸模圆角半径r凸
❷ 凹模圆角半径R凸
❸ 凹模深度h ⑵【凸、凹模间隙】
⑶凸、凹模工作部分尺寸与制造公差
⑷【斜楔的设计和计算】
【楔块受力分析】
【水平斜楔】
【向下倾斜运动的斜楔】
【向上倾斜运动的斜楔】
【楔块尺寸、角度的确定】
【拉深】
⒈【拉深的基本原理】
【拉深变形过程】
【拉深过程中毛坯的应力和应变状态】
【拉深过程中的起皱和断裂】
【旋转体拉深件的毛坯尺寸计算】
【修边余量】
【带料连续拉深】
第14篇:冲压岗位职责
质量工程师
1.每日开班前对质检科所属区域进行5S状态检查,不符合要求的地方,应通知该区域负责人立即整改,并在事后复查并将不符合项拍照留存作为考评依据。
2.每日收集前一天生产所发生的报废单,并与生产线日报表上填写的报废数量进行核对,确认无误后录入电脑存档,计算日报废率写入白板。3.每日检查返工单并检查返修组是否依据返工委托单内容进行正确返修,并将返修数量录入电脑存档,计算返修率,写入白板。
4.每周四前统计出前一周生产质量状态,包括报废率、返修率和PPM,并于周四下午一点钟通知相关人员召开质量会议。5.每月组织一次质量提高项目,并积极推动,跟踪落实。 6.每月组织一次内部培训,培训内容包括基本技能和体系流程。 7.每两周对大众所有生产零件按三坐标测量要求进行测量。 8.负责对量检具进行统一管理和发放,严禁使用失效量具和检具。 9.建立检具台帐和量具台帐。
附录: 1.报废单 2.返修委托单 3.每周质量分析统计表 4.每周质量会议记录 5.每月培训记录 6.每月项目进度表 7.三坐标委托书 8.量具发放记录表 9.量具检测统计表 10.检具检测记录表 11.检具登记一览表
生产线质检员
0.按照安全和环境负责区域负责所属区域安全和环境工作并在开班前检查,如有问题立即整改。
1.质检员按照生产计划,在生产前将检具放置于灯光室并将封样件悬挂于网架上,打开灯光室灯光。
2.在生产前依照工艺卡核对每台压机的工艺参数包括平衡缸压力,气垫压力、装模高度、和顶杆举升高度,如有与工艺卡不符合的停止生产立即通知机台长进行调整,所有工艺参数确认后在检查记录表备注一栏记录:工艺参数确认OK。
3.每班生产的第一件合格零件为首件,按照检验标准对零件进行检查,具体步骤按照检验作业指导书,首件检查完毕后将首件放置于检具上进行尺寸测量,检具使用按照检具作业指导书将测量尺寸记录于尺寸检查表上,如有任何问题应立即停止生产,解决问题后恢复生产。
4.在生产过程中,按照检验作业指导书要求的频次货时间间断的对零件进行抽检,抽检的标准依照检验标准,同时做好记录。抽检完成后将零件放置于检验区料架内,往复循环直至本轮生产全部完毕后,将所有抽检零件放入最后一个料架内,如有任何问题应立即停止生产,并同时进行追溯,解决问题后,才能恢复生产。
5.在每轮生产结束时按照检验标准对最后一个零件进行末检,并做好记录,将首检零件从检具上取下放入生产用料架内,将末检零件放置于检具上,进行尺寸测量,并做好记录。
6.每轮生产结束后将末检零件、检具和封样件归还至检具房。
7.每班生产结束后将质量检查表、尺寸测量表交与质量工程师存档,当班班长做好交接班记录对在过程中的不良现象及时传达至下一个班组,准确填写当班生产的报废单、返工单,将报废单交与质量工程师,返工单交返修组。
8.每班生产结束前10分钟,安全和环境负责人对自己所属区域进行清洁工作,班长负责检查。
9.每周周六班长根据检具清洁计划组织人员对检具房的封样件和检具进行清洁工作,质量工程师负责检查。
附录:
1.零件质量检查表 2.尺寸测量表 3.安全和环境责任图 4.检具清洁计划 5.可疑品处理流程 6.检具作业指导书 7.零件检验标准 8.零件检验作业指导书
包装终检员
1.按照安全和环境负责区域负责区域内安全工作并在开班前检查5S状态,如有问题立即整改。
2.依照零件检验标准和出库零件特殊要求对倒箱和终检库内零件进行终检,终检完成后在零件标签上(三联单)盖章确认。
3.对于批量(≥10)问题,应立即通知质量主管,进行确认,不得盲目判断。4.经终检确认后的零件应及时通知叉车放入成品库中并同时做好终检记录表。
附录:
1.零件检验标准 2.出库零件特殊要求 3.终检记录表 4.安全/环境区域图
包 装 工
1.每日对所负责区域进行清洁,并对本区域内安全负责。
2.每日依据产品标识卡(三联单)色标顺序进行倒架工作,在倒架工程中,注意轻拿轻放,避免碰伤,对于少量明显的磕碰伤零件,通知返修人员及时返修,对于料架内批量缺陷零件(≥10),通知终检人员进行判断。3.在倒架完成后及时通知终检人员进行检验。 4.每日填写倒架工作记录表
5.每日对客户料架进行清洁,擦拭油污,清除多余标签并检查料架是否完好,对于不合格料架及时通知料架维修人员进行维修。
附录:
1.倒架工作记录表 2.安全和环境责任图
料架维修员
1.负责本区域内安全和清洁工作。
2.积极配合包装工进行料架维修工作,并做好料架维修记录。
3.对维修完成后的料架进行料架清洁工作并通知包装工将合格料架投入使用。
附录:
1.料架维修记录 2.安全/环境区域图 3.电焊证
第15篇:冲压承包合同
承 包 合 同 书
发包方: (简称甲方).地址: 法人代表: 承包方: (简称乙方).承包代表: 身份证号: 为健全公司制度,提高产量、质量,降低生产成本,节约费用,提高经济效益,充分利用机器设备及保管,挖掘员工的潜能,体现多劳多得的精神,经公司领导研究,对甲方公司属下的冲压一车间实行承包责任制,经甲乙双方协商,签定本合同。
一、承包内容:甲方提供场所、主要设备、原材料,下达生产任务和管理,乙方负责加工生产。承包形式为来料加工生产,按产量计提包干。
二、承包期限自 年 月 日起至 年 月 日止,共 年。
三、承包产量、质量标准、各项管理指标及提成方法 1-自承包日起,乙方在排产和原材料充足的情况下按平均每月完成 万冲次为基数,以甲方仓库每月实际合格片进仓结算表为依据计算。一线员工按计件形式结算工资(详细见《冲压车间零件工序单价》附表1),目前公开的一线员工单价在承包期间不能在未经甲方许可下更改.二线后勤人员(包含维修工及管理人员等)则按实际进仓产量分表面及内芯件分别按冲次计提。表面件(包括面板、大小壳等)按每一个合格冲次 元计价,其他内芯件及附属配件按每合格冲次 元计价。承包车间员工属计件承包,不存在加班工资,包括节假日在内.2-乙方费用结算:设备维修属于300元以下由乙方自付,单件设备维修超300元以上及电器维修由甲方负责。新产品投产甲方负责第一次模具制造的费用,第一次模具由乙方负责加工,出现技术问题,一切经济损失由乙方负担,新模具价格由双方协商。乙方一次性预缴 元给甲方作抵押金,合同期满后将原交接生产资料设备等结算后发还.但如发现需要维修的甲方有权将抵押金作为维修费用处理,余额退回乙方.3-承包期间,乙方保证完成甲方的指令性计划。
4-承包期间,乙方按年度一次上缴固定资产折旧费 元,每月上缴行政管理费 1000 元,电费按每月抄表额按冲次结算(以现定电费价格 元/度电),如车间未达到限额生产量时,所有超出费用由承包车间支付;如车间能在限额生产量内节省耗电量的,则按节省的50%奖励给承包车间.(具体结算规定待电网电表安装好投产一个月后以附件形式发放通知。
四、主要审核技术指标
1-乙方保证承包期间平均每月完成甲方下达的生产任务,包括生产现场管理、计划生产达成率,详细见《承包车间产量、质量目标考核方案》
2-承包期间,乙方工资财务计算,详细见《承包车间产量、质量目标考核方案》 3-承包期间产品质量达到98%标准。
4-主要物资能源消耗指标:详细见《承包车间产量、质量目标考核方案》 5-安全生产和双保指标:详细见《安全生产岗位责任考核方案》
五、承包期间,甲方有权对乙方的经营管理活动进行监督和检查;
六、甲方的权利义务
1-合同生效之日,甲方应将下列生产资料交给乙方管理:
生产厂房 间,机器设备 等共 台,以及工具一批(详细列表见附表2)
1 2-在合同期内,甲方每月向乙方供应生产用火水 公斤,机油 公斤、乳化油 公斤、石蜡油 公斤由甲方按购买成本付款(按生产 万冲次为基础,如乙方未达到计划产量,则按每冲次计算支付其差额费用),其余低值易耗品等生产资料由乙方支付。
3-甲方有权对乙方的财务分配,工资核算,外购或外加工物资进行监督检查,有权督促乙方履行合同。
七、乙方的权利义务
1-乙方必须健全配备承包车间每个岗位的员工,严格执行甲方在生产、经营、财务管理、行政管理、工资、劳保、福利、环境保护、安全管理等所有相关制度,并应经常向甲方汇报生产,经营情况。如因管理不善而造成甲方生产混乱,或在厂区内违反厂规,国家法规的,甲方有权管理或处罚,情节严重的(如出现员工集体罢工或唆摆员工犯事)甲方有权单方面解除合同不予补偿。
2-乙方有责任对员工加强政治思想教育,处进精神文明建设,加强安全生产教育和措施,防止和减少工伤事故。如出现工伤事故费用在300/次元以下由乙方支付,300/次元以上由甲方和保险公司负责,如一个月内连续出现两次或以上工伤事故发生时,不论事故是否属入级事故均处以1000元罚款。如有入级工伤事故,给予乙方每次500元的罚款,如一年内无入级事故发生由甲方奖励2000元。入级工伤事故达1万元的取消当年所有奖励。
3-乙方有权根据职工的生产技能、工作效率、身体条件、劳动态度、执行纪律好坏等情况,决定后勤职工的工资多少,调整工作等,但必须遵守国家相关劳工法律,并提前向甲方经营管理者和行政部报告同意备案。
4-乙方能在保证质量和产量的前提下,能缩减原工艺或工序,经甲方相关部门确认可节约成本的,每项奖励300元,累计6个月甲方给予一次性奖励。乙方在承包期间,能在保证质量的前提下,能改进原有产品工序或工艺,经甲方相关部门确认投产能节约成本的,则按该产品一年度营业额可节约成本的5%金额给予乙方一次性奖励。承包期间,乙方对甲方提供的物料在保证使用质量的前提下,能提供单价更优惠的采购供应商的,已经甲方相关部门采纳则每项奖励50元.
八、甲方的违约责任
1-甲方如不按时、按量向乙方提供生产,机器设备和工具等,延迟2天,应按所欠交物料的 10 %,向乙方偿付违约金,乙方并可不交纳因该段期间物料延误而未能完成任务的款项,如果由于甲方延误提供的物料造成乙方不能生产的,经乙方要求,生产计划各项指标可以顺延。
2-甲方如不按时、按量向乙方供应电、柴油、汽油、劳保工具等,应按所欠物资价款的 5 %,向乙方偿付违约金,如果造成乙方损失的,甲方还应赔偿乙方的损失。
九、乙方的违约责任
1-乙方如不按时按量完成甲方下达任务,应按银行关于迟延付款的规定,向甲方偿付该项任务成本预算的7%违约金。
2-乙方在合同期满时,应将甲方提供乙方的厂房、机器设备和工具等,按原清单如数点交甲方,除自然损耗外,如有损坏或丢失,乙方应负责修复或赔偿。
3-乙方在生产活动中如有违反党的政策和国家法律的情况,甲方有权对乙方有关责任
2 人员作行政,经济处分,直至解除合同。
4-甲乙双方的相关往来业务资料,包括签定的所有合同,甲方在管理上的所有文件、规定、通知、生产任务内容、仓库单据、外包装、
一、二线工序单价和分配方案等只能保存一份原件,并由承包负责人和统计共同管理,一律不准以任何理由外借,复印等给员工带走。一旦违反视泄露商业机密处理,按甲方《文件保密管理条例》相关内容处理。
5-甲方的外包装、相关产品和牌子均已申请注册商标,也是市级名牌企业,乙方对甲方的相关技术资料,图纸工艺图、样板、模具、夹具等妥善管理和保存并不得外泄。如必须发外加工维修的应经甲方采购部及仓库签名确认,一旦违反经相关部门确认的则视泄露商业机密和侵犯商标注册处理,甲方保留所有追究权利。
十、违约责任
1-甲方不按合同条约 第六 条规定为乙方解决问题时,按 上缴行政管理费的 20% %交付违约金。
2-乙方未按合同完成产量总额的,按上缴行政管理费的20%交付违约金。 3-乙方未实现第 四 条规定的质量技术指标的,按上缴行政管理费的30%交纳违约金; 4-乙方承包期间,给甲方财产造成损害的,按实际财产损失的20%支付赔偿金(自然损害除外) 十
一、乙方承包者完不成承包指标时,分别按下列情况对乙方承包者进行处罚:
乙方完成或超额完成承包指标时,分别下列情况,对乙方承包折进行奖励:
1- 乙方完成上述承包指标以外的超额部分, 10 %作为集体提留基金,用于员工的奖励和福利经费,工伤事故处理等。
2- 乙方承包者完不成承包指标时,由于是乙方的原因造成无法完成生产任务时,按差额产品数量扣罚二线后勤人员的平均单价的50%。即:( 万冲次-实际完成冲次)*(平均单价)*50% 十
二、合同的变更或解除:双方如需要变更或解除合同时必须提前3个月通知对方.十
三、不可抗力。
在合同执行期间,如遇不可抗力的自然灾害,造成生产中断或其他经济损失,或遇偷窃,抢劫等行为时,经调查属实后,甲方应按损失的实际情况,酌情调整乙方的相关任务指标。
十四、争议的解决方式
因本合同发生争议时,双方应协商解决,协商不成时,以下列第 1 种方式解决: 1-交小榄工商局经济合同仲裁委员会仲裁; 2-交小榄法院审判。
十五、本合同自 时起生效。承包期满自然失效,甲乙双方在合同内形成的债权债务关系,不因合同期满而消失,在合同执行中,甲乙双方代表人如发生变更,不得变更本合同,甲乙双方也不得随意变更或解除合同,本合同如有未尽事宜,应由双方共同协商,作出补充规定,补充规定与本合同具有同等效力。
合同正本一式2份,甲、乙双方各执1份,副本一式 5 份,分送财务部、生产部、品质部、行政部、采购部各一份。
甲方签名(公章):
乙方签名:
3
2011年 月 日
第16篇:冲压课程设计
目录
第一章 概述…………………………………………………………………………………2 1.1冲压工艺的基本现状及发展趋势 ………………………………………………………2 1.2课程设计的目的及意义 …………………………………………………………………2 第二章 冲压工艺性分析与生产方案的确定………………………………………………3 2.1设计任务 …………………………………………………………………………………3 2.2冲压件工艺性分析 ………………………………………………………………………3 2.3冲压生产方案的确定 ……………………………………………………………………4 2.4确定模具类型 ……………………………………………………………………………4 第三章 冲压工艺设计与计算………………………………………………………………6 3.1排样设计 …………………………………………………………………………………6 3.2压力中心的确定 …………………………………………………………………………8 3.3刃口尺寸的计算 …………………………………………………………………………8 3.4冲压力的计算 ……………………………………………………………………………9 3.5冲压设备的选择 …………………………………………………………………………10 总
结………………………………………………………………………………………11 参考文献………………………………………………………………………………………11 致
谢………………………………………………………………………………………11
常用简单冲压零件的工艺设计
摘
要
本设计为常用简单冲压零件的工艺设计,根据设计题目零件的尺寸、材料、大批量生产等要求,首先分析冲压零件成形的结构工艺性,分析冲压件的形状、特点、尺寸大小、精度要求及所用材料是否符合冲压工艺要求,确定冲裁工艺方案及模具结构方案,然后通过设计计算毛坯尺寸,材料利用率等工艺计算,确定排样,计算冲压力和确定压力中心,确定模具间隙,计算模具刃口尺寸和公差,并绘出模具刃口尺寸图,计算冲压工艺力,选择冲压设备,确定压力机的各种类型、型号、规格。其中在结构设计中,主要对凸模、凹模、凸凹模、定位零件、卸料与出件装置、模架、冲压设备等进行了分析和选择。通过设计,学会运用标准、手册、图册和查阅有关技术资料,培养了工艺设计的基本技能,综合运用和巩固了冲压工艺等课程及有关课程的基础理论和专业知识,最终才完成这篇课程设计。
关键词:冲压件
工艺
冲压力
刃口尺寸
冲压设备
- 1
第二章 冲压工艺性分析与生产方案的确定
2.1设计任务
如图2-1为冲压工艺设计的零件图,此次课程设计的题目为常用简单冲压零件的工 艺设计,工件材料为:H62-M(黄铜),料厚:t=1.5mm,生产批量:大批量
图1-1 零件图
设计具体内容及步骤如下: (1)零件的工艺性分析
根据设计题目的要求,分析冲压零件成形的结构工艺性,分析冲压件的形状特点、尺寸大小、精度要求及所用材料是否符合冲压工艺要求。如发现冲压零件工艺性差,则需对冲压零件产品提出修改意见,但要经产品设计者同意。 (2)生产方案的制定
在分析了冲压件的工艺性之后,通常可以列出几种不同的冲压工艺方案,从产品质量、生产效率、设备占用情况、模具制造难易程度和模具寿命高低、工艺成本、操作方便和安全程度等方面,进行综合分析、比较,然后确定适合于具体生产条件的最经济合理的工艺方案。根据所确定的工艺方案和冲压零件的形状特点、精度要求、生产批量、模具制造条件等选定冲压模具类型。 2.2冲压件工艺性分析
一 结构与尺寸
该零件的结构较简单,形状对称,尺寸较小,最小宽度6≧1.5t,冲模所能冲制的最小孔径尺寸6.5≧3.5t,孔至边缘的最小距离3.75>1.5t,均适宜于冲裁加工。且零件与曲线的连接处允许有R﹥0.25t的圆弧过渡。
二 精度
零件图中未标注尺寸精度和位置精度,粗糙度也无要求,设计时一般按IT14级选取公差值。普通冲裁的冲孔精度一般在IT13级以下,所以精度满足要求。 三 材料
黄铜H62-M,软态,带料,抗剪强度b260MPa,退火状态下断面伸长率3.500,此材料具有较高的弹性和良好的塑性,其冲裁加工性较好。
四 表面质量
当冲裁厚度为2mm以下的金属板料时,其断面粗糙度可达12.5~3.2m满足该零件的工艺要求。
根据以上分析,该零件的工艺性较好,可以冲裁加工。
- 3
根据零件的冲裁工艺方案,采用级进冲裁模。虽然零件的生产批量较大,但合理安排生产可用手工送料方式,能够达到批量要求且能降低成本,因此采用手工送料方式。考虑零件尺寸较小,材料厚度较薄,为了便于操作和保证零件的精度,宜采用导料板导向,侧刃定距的定位方式。为了减少料头和料尾的消耗和提高定距的可靠性,采用双侧刃前后对角布置。考虑到零件厚度较薄为1.5mm采用固定卸料装置,为了便于操作 提高生产率 采用刚性推件装置。由于零件厚度较薄 冲裁件隙较小,又是级进模因此采用导向平稳的对角导柱模架。
综上所述,该级进模的主要零部件为落料模,冲孔模,导料板,侧刃,对角模柱,刚性卸料装置,刚性推件装置。
- 5
二、方案二
查查参考书《冲压工艺与模具设计》表2-18得相关数据: a\'=mm
a=1.44mm a1=1.8mm n=2 b1=1.3mm y=0.1mm z=0.5mm
条料宽度为
0BDmax2a\'2anb1
=14+1+2.88+2.6 =20.5mm
冲裁后废料宽度为
B1Dmax2a\'2a
=14+5+1
=17.9mm 导料板之间的距离为
B\'BZ
=17.93mm
B1\'B1Z
=20.53mm 一个冲裁零件的面积为
A=206.35mm2
进距为
s=24.1mm 根据条料规格查表得板坯尺寸为
b2050mm L=2410mm t=1.5mm 一根条料所能冲裁的零件的个数为
n=2410÷24.1=100 一根条料内总的利用率为
nA
BL206.35100= 20.52410=41.8% 其排样图如下:
图3-2 零件排样
3.2压力中心的确定
冲裁模的中心就是冲裁力合力的作用点。冲压时,模具的压力中心一定要与冲床滑块的中心线重合,否则滑块就会承受偏心载荷;使模具歪斜,间隙不均,导致冲床滑块与导轨和模具的不正常磨损,降低冲床和模具的寿命。所以在设计模具时,必须要确定模具的压力中心,并使其通过模柄的轴线,从而保证模具压力中心与冲床滑块中心重合。因冲裁件尺寸较小,冲裁力不大,且选用了对角导柱模架,受力平稳,则冲裁的压力中心位于冲件轮廓图形的几何中心上。 3.3 刃口尺寸的计算
图3-3 零件图
00.360零件外形尺寸140属于冲孔 0.45 60.30 22.30.52 属于落料,内形6.501.落料凹模刃口尺寸 。
零件图的尺寸均是凹模磨损后变大的尺寸,凹模各尺寸所以按公式
Ad(Amaxx)00.45404 (3-6)
计算,凸模尺寸根据凹模尺寸按间隙配制,计算结果如下:
1400.45 Ad1(140.50.45)0.112513.7750 mm 6 00.30 Ad2(60.750.30)0.30400.0755.7750mm
- 8
3-8)
(3-9)
(
114.44×260×1.5
=1.3×
=58021.08N 查参考书《冲压模具简明设计手册》表2.40得凹模刃口直壁高度 h=6mm 故nht=4 取KT=0.06
则推件力为:
FTnKTF
(3-10)
=4×0.06×58021.08
=13925.06N 由于压力机采用刚性卸料装置和下出料方式,故其冲裁时的总压力为:
FZFTF
(3-11)
=71946.14N 压力机的公称压力为:
F标(1.1~1.3)FZ
(3-12)
72
=(1.1~1.3) ×
= 79.2 kN~93.6 kN 3.5冲压设备的选择
通过校核,选择开式双柱可倾压力机J23—10能满足使用要求。其主要技术参数如下:
公称压力:100 kN
滑块行程:45 mm 滑块行程次数:145 次/min
最大封闭高度:180 mm 封闭高度调节量:130 mm
滑块中心线至床身距离:180 mm 立柱距离:180 mm
工作台尺寸(前后左右):130mm×200mm 垫板尺寸(厚度):35 mm
模柄尺寸(直径深度):38mm×55mm 滑块底面尺寸(前后左右):90mm×100mm
- 1011 -
第17篇:冲压知识
拉深模:把毛坯拉压成空心体,或者把空心体拉压成外形更小而板厚没有明显变化的空心体的冲模。
落料:排样,计算凸凹模间隙,卸料力计算,根据冲裁件结构设计模具结构、选取模具材料等。
冲孔:和落料差不多啦,冲孔以凸模为基准,落料以凹模为基准。
冲孔为产品是有孔的,冲下的是废料.而落料是冲下的为产品,在模板上的是费料.冲压模具设计时,要考虑以下的内容:1.冲裁间隙.2.冲裁力(决定选用机台的吨位)3.闭模高度和开模高度(一般产品不须考虑开摸高度,但有的产品考虑到取料及成型要考虑)4.定位(工站模,连续模那就多了)5.落料6.内外导柱7.弹簧力8.取料 这只是一部分,你看一下
《装备制造技术》支承板零件(见图1)是一种连接件,起支承其他零部件的 作用,零件表面要求无划伤、油污等外观不良现象。它采用料 厚1.52 mm 的AMS5536(GH30)镍基板材。这种镍基板材合金 的强度保持性好,具有优良的抗氧化性、良好的冲压性和焊接 性能。该零件产量约20 万件/ 年,设计模具时要求尽量结构 简单、维修方便、装配可靠,以降低模具的制造费用。 1 冲压工艺分析
该零件结构较简单,孔边距最小为4.26 mm,尺寸精度最
高IT11 级,精度不高,冲裁工艺性良好。但弯曲形状为Z 形, 要保证弯曲后上下两平面的平行度较难,而且要防止弯曲过 程中产生偏移。因此,在设计弯曲模时,要注意解决上述问题。 2 冲压工艺方案制定
(1)工序性质的确定。根据零件的结构形状,可以知道成 形该零件的工序为:冲孔、落料和弯曲。
(2)工艺方案的确定。考虑到提高生产效率,根据零件结 构尺寸,可以采用复合冲压工艺,冲压工序为:冲孔、落料复 合→弯曲、整形复合,采用两套模具完成。
在冲孔、落料复合工序中,为了提高材料利用率,考虑支 承板展开后的形状,可以采用直对排(如图2 所示)。 在弯曲、整形复合工序中,利用第1 道工序中冲出的2 个 并排的Φ5.69 mm 圆孔定位,同时采用压料板压料可以防止 偏移。弯曲结束时再利用凸、凹模的挤压作用进行整形,可以 有效保证零件上下面的平行度。 3 模具结构设计
(1)冲孔落料复合模。如图3 所示,选用标准后侧导柱模
架,采用倒装式复合模,结构简单,便于操作。凸凹模17 装在 下模,冲孔凸模22 和落料凹模8 装在上模。条料定位方式采 用两个导料销和一个挡料销定位,其中挡料销和右边的导料 销需要在凹模上开设躲避孔,而靠左边的导料销为不削弱凹 模的强度,设计成活动导料销,如剖视图A- A 所示。上模中设 置刚性推件装置,将制件从凹模8 中推出。下模采用弹性卸 料,将条料从凸凹模17 上卸下。冲压时,先冲条料上的一排制
件,再翻转条料,冲出另一排制件,这样可以有效提高材料利用率。 4 结束语
冲压生产中,采用复合模结构,不仅可以提高生产效率,更重要的是保证零件的精度。本文中Z 形支承板采用两套复合模成形,其中冲孔、落料复合模,可有效保证制件上内孔与外形之间的位置精度,同时采用直对排可以提高材料利用率。弯曲、整形复合模,解决了制件弯曲时的偏移和上下面的平行度问题,模具结构简单,装配方便可靠,模具尺寸小,虽然取消了模具导向装置,但调整得好时,并没有影响模具精度,冲出的制件完全符合图纸要求,因而降低了模具制造费用。
一) 冲压工序术语1:落料:是将材料沿封闭轮廓分离的一种冲压工序,被分离的材料成为工件或工序件,大多数是平面性的。2:拉深:是把平直毛料或工序件变为空心件,或者把空心件进一步改变形装和尺寸的一种冲压工序。拉深时空心件主要依靠位于凸模底部以外的材料流入凹模而形成。4:冲孔:时将废料沿封闭轮廓从材料或工序件上分离的一种冲压工序,在材料或工件上获得需要的孔。
1.无凸缘筒形件
材料:08钢
料厚:2mm
一、拉深的概念及应用
拉深(又称拉延)是利用拉深模在压力机的压力作用下,将平板坯料或空心工序件制成空心零件的加工方法,它是冲压生产中应用最广泛的工序之一。拉深可加工旋转体零件、盒形零件及其他形状复杂的薄壁零件如图1所示。它广泛用于汽车、拖拉机、仪表、电子、航空和航天等各种工业部门和日常生活用品的生产中。
三、落料拉深复合模
图24为落料和首次拉深复合模的典型结构,适于圆形、矩形或正方形冲件的拉深。冲压时,上模下行,凸凹模3与落料凹模7冲出坯料外形,上模继续下行,拉深凸模8将坯料拉人凸凹模3成形。上模回程后,由顶件块(压边圈)2或推件块5将拉深件顶出或推出。该模具结构比较合理,也容易制造和调整,生产上用的很广。 该零件需拉深3次成形,所以其最总确定的加工工艺路线应为:落料与首次拉深复合——第2次拉深——第三次拉深——切边冲孔复合模——机加底孔——检验。
一、落料拉深复合模其它工艺计算 1.落料凸、凹模刃口尺寸计算
根据零件形状特点,刃口尺寸计算采用分开制造法。落料尺寸为φ10500.87,落料凹模刃口尺寸计算如下。
查得该零件冲裁凸、凹模最小间隙Zmin0.246mm,最大间隙Zmax0.360mm,凸模制造公差T0.025mm,凹模制造公差A0.035mm。将以上各值代入TA≤ZmaxZmin校验是否成立。经校验,不等式成立,所以可按下式计算工作零件刃口尺寸。
ADA(DmaxXΔ)00.035(1050.50.87)mm 00.035104.5650mmDT(DAZmin)0T(104.5650.246)00.025mm 104.31900.025mm2.排样计算
零件采用单直排排样方式,查得零件间的搭边值为1.5mm,零件与条料侧边之间的搭边值为1.8mm,若模具采用无侧压装置的导料板结构,则条料上零件的步距为106.5mm,条料的宽度应为
B(Dmax2ac)0(10521.81)00.7mm 109.600.7mm选用规格为2mm×1000mm×1500mm的板料,计算裁料方式如下。 裁成宽109.6mm,长1000mm的条料,则每张板料所出零件数为
15001000139117 109.6106.5裁成宽109.6mm,长1500mm的条料,则每张板料所出零件数为
10001500914126 109.6106.5经比较,应采用第二种裁法,零件的排样图如图40所示。
二、第二次拉深工艺计算
1.拉深凸、凹模尺寸计算
第二次拉深件后零件直径为43.41 mm,拉深凸、凹模间隙值仍为3mm,则拉深凸、凹模尺寸分别为
A0.080.08DA(d2t)0(43.412)0mm45.410mm
00DT(DA2Z)0T(45.416)0.05mm39.410.05mm
2.拉深力计算
图40 排样图
F拉d2tbK243.4124000.6N 65427.55N65.4kN根据以上力的计算,初选设备位J23—10。
三、模具零部件结构的确定 1.落料拉深复合模零部件设计 (1)标准模架的选用
标准模架的选用依据为凹模的外形尺寸,所以应首先计算凹模周界的大小。根据凹模高度和壁厚的计算公式得
凹模高度HKb0.2105mm21mm。 凹模壁厚C(1.5~2)H1.821mm38mm。 所以,凹模的外径为D105238181mm。
以上计算仅为参考值,由于本套模具为落料拉深复合模,所以凹模高度受拉深件高度的影响必然会有所增加,其具体高度将在绘制装配图时确定。另外,为了保证凹模有足够的强度,将其外径增大到200mm。
模具采用后置导柱模架,根据以上计算结果,查得模架规格为:上模座200mm×200mm×45mm,下模座200mm×200mm×50mm,导柱32mm×190mm,导套32mm×105mm×43mm。
(2)其它零部件结构
拉深凸模将直接由连接件固定在下模座上,凸凹模由凸凹模固定板固定,两者采用过渡配合关系。模柄采用凸缘式模柄,根据设备上模柄孔尺寸,选用规格为A50×100的模柄。
步骤拉深:
1冲压件的工艺分析 2只要工艺参数计算
1)毛胚的计算 2)确定拉深次数 3)排样及材料的利用率 4)计算工序压力
落料力 卸料力 拉深力 压边力 5)冲压设备的选择
3模具零件主要工作部分尺寸计算 1)落料刃口的主要尺寸计算 2)拉深刃口尺寸计算 3)模架的选择:模具设计与制造实训附表 4)弹性材料的选择与计算
第18篇:冲压工程师
工艺技术部——冲压工程师
1、汽车新产品开发车身零件同步冲压工艺分析;
2、制定车身冲压零件工艺方案;
3、车身零件工艺建模及CAE分析;
4、负责汽车覆盖件冲压模具开发;
5、供应商车身中小件模具开发工艺方案及模具结构审签;
6、产品试生产与供应商零件质量问题整改技术方案制定。
车体工程师
1、负责车体主断面设计和前期可行性分析工作;
2、负责车体各项性能指标及法规满足情况的把控工作;
3、负责 车体3D结构设计、2D图的绘制以及相关技术文件的编制;
4、负责新产品设计、试制、试验和试生产过程中车体问题的整改工作;
5、负责车体零部件各种技术状态的管理工作;
6、负责车体供应商管理和相关技术支持工作。
(一) 岗位描述
1、负责大型汽车覆盖件模具三维结构设计。
2、负责按要求进行大型汽车覆盖件模具二维图的拆分。
3、负责大型覆盖件模具加工装配的跟踪和现场技术问题的解决。
(二)任职条件
1、熟悉大型汽车覆盖件模具三维结构设计。
2、熟悉各种大型模具加工方法和相应设备的加工参数。
3、具有大型覆盖件模具加工装配现场技术问题的解决能力,能熟练操作CATIA、AUTOCAD等软件。
4、5年以上大型汽车覆盖件模具结构设计经验。
1、有一定的工装工艺及结构设计经验及能力。
2、有较强的金属材料基础知识和塑性成型理论知识。
3、熟悉大型汽车覆盖件模具三维结构设计
4、熟悉各种大型模具加工方法和相应设备的加工参数。
5、具有大型覆盖件模具加工装配现场技术问题的解决能力
6、能熟练操作CATIA、AUTOCAD等软件
7、3年以上大型汽车覆盖件模具结构设计经验。
8、全日制本科以上学历,3年以上工作经验
第19篇:车间冲压班个人工作总结
一、个人工作情况
2006年我毕业于昆明冶金高等专科学校,所学专业是物业管理。毕业后既回厂上班,在冲压班的五联机3#套管引长工序上工作。还记得才参加工作时,我跟着师傅在七联机的覆铜管引长工序上实习,是非常的不适应,一边忙着捡管,一边还要修床子。师傅告诫我从事这个工种,要学会用眼睛看、用耳朵听,机器坏了,不要手忙脚乱,要找准问题所在再对症下药,从根本上解决问题,不然会浪费许多时间和精力,这些话我至今还铭记在心。出师后,我自认为掌握了冲床的基本操作技能,很容易,但是经过实践后我发现,机器坏了,我总是修不好,既是修好了,干不了多长时间有出现新问题。于是就进入了一个恶性循环:哪里坏了修哪里,修好这里坏那里,到最后是越修越不行,不知如何是好。问题出在哪儿呢?
1、原因没找准。
2、不会及时快速地处理。
3、对床子零部件的外观不熟悉以及运行时的规律没有把握好。
4、不会对料头和床子问题部位进行细致地观察和分析。
5、基本功不扎实,冲子、模子、夹子的磨功太粗糙,直接影响到机器的正常运转。
6、不会进行简单地维修。
刚开始工作时苦工时还很吃力,月工时也勉强干够,奖金偏低。但是时间一长我发现,工厂的设备也是有规律可循的,只要有扎实的基本功和学会处理问题的方法技巧,就能够对机器熟能生巧、游刃有余,而且还出产品、出工时。随着经验的不断增长,对自己的设备也逐渐了解,基本工时也就日趋增长,成了非常容易的事。一段时间过后,我的超产工时有所稳定和提高,这让我很欣喜。
不仅如此,在三年的工作时间里,我在冲压班下料、引长等工序上实践,学习了冷冲压加工的基本原理、特点和应用。它可分为分离工序、成形工序及复合工序。会根据所提供的产品图样、分析冲压件的形状、尺寸、精度、断面质量、装配关系,确定基本的工序性质和数目,根据冲件生产批量和要求确定工序组合、根据各工序的变形特点、尺寸要求确定工序排列顺序,会计算毛坯尺寸、冲压力、模具闭合高度、压力中心。知道冷冲压的安全知识和安全防护装置,冷冲压模具的使用性能以及冷冲模的基本结构,冲裁的变形过程、断裂特征和工艺要求,冲裁件的质量及其影响因素,掌握了冲裁模的设计方法。会进行弯曲变形的分析、弯曲件的工艺计算,了解弯曲模的基本结构和设计方法。懂得了拉深工艺及其变形过程,会进行模具拉深力的计算,掌握了拉深工艺的设计方法。
另外,我还掌握了制图的基本知识和基本技能,知道点、直线、平面的投影特性,会作相关的投影图。掌握了立体三视图的投影规律,会在其表面上取点和线,求取相贯线。了解了轴测图的基本知识,会标注组合体的尺寸,会画机件剖视图。掌握了标准件和常用件的画法,零件图和装配图的画法及尺寸标注。对冲压班各道工序上的工具工装,能根据技术要求作设计图纸。
在工作的三年时间里,我从不迟到早退,也没有请假矿工,严格遵守工厂的各项规章制度和劳动纪律。工作中时刻严格要求自己,保质保量地完成了车间的生产任务,团结、帮助同事共同进步,营造了和谐的人际关系氛围。班长也肯定了我的工作成绩,希望继续保持现有的工作状态。
二、安全生产方面
从参加工作的第一天起,我就认识到对于我们这样一个民爆企业,安全生产的责任重于泰山,离开了安全谈生产,就无从谈起。只有保证人的生命财产安全,才能确保生产的顺利进行。因此,我严格遵守安全操作规程,并劝阻制止他人违章作业,认真履行安全职责,对本岗位的安全生产负责任;对危害生命安全和身体健康的行为提出批评、检举。在生产过程中我精心作业,交接班交接安全生产情况,为接班创造安全生产的良好条件,发现异常情况,及时处理和报告班长。平时还加强设备的维护和保养,保持作业现场的整洁、推行清洁生产。上岗按照规定穿戴好劳动保护用品,积极参加各种安全活动培训,强化了安全生产责任意识。在安全生产过程中,其最核心的是工艺安全、操作安全,为了实现安全生产,最根本的措施是提高技术装备本质的安全水平,也就是说从物质条件上根本消除、控制危险和有害因素。总之,只有不断地增强自我防护能力,才能带来企业的经济效益。工作三年以来,我安全生产过了每一天,然而每天对我来说都是安全生产的开始。
三、产品质量方面
“以质量求生存、以效益求发展”是对产品质量工作重视的结晶。三年的工作经验,使我对产品质量的认识更深了一个层次。第一,质量不是靠检验员检验出来的,他们只是起到一个督促的作用,关键是要提高自身的思想认识水平,重视自检工作的重要性,才能防止问题产品流出本道工序。第二,只要提高操作技能和操作水平,才能从根本上解决产品质量问题。第
三、产品质量牵扯到各道工序的各个环节,需要全体职工的共同关注和精心操作才能得到保证。第
四、产品质量是安全生产的重要保障,尤其是401车间的半成品质量直接影响到装配车间的生产安全以及雷管的销售业绩。因此,每一位职工都应该对产品质量给予高度重视,就本工序或其它工序的产品质量问题要能够及时发现、处理和汇报,把产品质量问题和废品控制在最小的范围内。总之,只有提高全体职工的质量意识,使他们牢固树立起“质量就是生命、质量就是效益”的重要思想,才能从源头上扼制产品出现质量问题。
四、经验和教训
1、冲压班的工作虽然很辛苦、很脏,而且技术性较强,但是我相信只要加强专业知识的学习和工作能力的培养,按照规律办事,发挥自己的主观能动性,稳步扎实地展开各项工作,是完全能够胜任这份工作的。
2、高效的工作是需要时间来保证的,是靠制度来执行的,我会一如既往地学习和发扬优良的工作传统和作风,做好每一份工作。
3、“安全第
一、预防为主”是工厂的安全指导方针,我会时刻牢记,把它当作工作时的座右铭。
4、质量是企业的生命线,质量工作的好坏最终影响到工厂的对外形象以及每位职工的切身利益,我会长抓不懈的。
在今后的工作中我会刻苦钻研、奋发图强、努力奋进,为工厂的建设积极献言献策,为工厂的发展做出更多更大的贡献。
第20篇:八月在冲压
八月在冲压
“接下来一个月你们将要在冲压实习,很累很热的,有没有什么想说的?”“没有”这是我们刚来冲压厂时与人事主管林华的一段对话。初出牛犊不怕虎呀,看不见困难的人是最无惧于困难,也最容易被困难打到的。
孰不知麻木的自信会使困难来的更束手无策。当培训员张静带我们下厂参观时,被太阳暴晒一天的厂房好像一个大锅炉,衣服贴在皮肤上都似在灼烧,阵阵热浪从房顶压下来。带着安全帽、穿着长袖的工装转了一圈,我发现衣服已经紧紧地贴在我的后背。这就是困难吧,不就是热吗?哥不怕。带着这样的心态逛完一圈我们就被准许提前下班了。在回去的路上我们谈笑风生,丝毫没有感觉到受苦的日子一步步逼近。
第二天早早起来,我们小微微野狼队整装待发,向冲压进军了。我被分到D线翘料,D线由于是气压机速度很快,我翘的料跟不上节拍。为了不因为我影响生产,我拼命的翘着,急的满头大汗,师傅看我这样一直鼓励我说不要紧,慢点别伤到手了。这一句句朴素的话着实让我感动。不知翘了多少料了,突然有人过来发水,师傅每人一瓶,我发了两瓶。我很疑惑地问了发水的师傅,师傅说人事部另外给你们加了一瓶。线上师傅一个个挥汗如雨都只能分到一瓶水,我干着最轻巧的活还受额外的待遇,真的受之有愧呀。右手翘左手拉,重复的动作我也不记得干了多少遍,当听见师傅说下班了,放下吸铁的右手宛然一个鸡爪子,麻木的伸不直了;长时间站立的小腿阵阵发麻,走起路来像唐老鸭。回到宿舍就直接到床上躺着了,连说话的力气都没了。想到接下来一个月都要这样,不免有点后怕。
在冲压实习的这一个月里,处处都能感受冲压厂的关怀,时时都被冲压工感动着。在小冲组摆料时,师傅把他的风扇转到我这边说他不热;在B线打油时,师傅总说累了你就去休息下吧;在下料组下料时,师傅把他的两个面包给我叫我多吃点长胖点;来到办公室,大家都很客气地让我们坐坐。这些在他们眼里都是很小的事,却深深的打动了我。虽然每天衣服都被汗水洗了一遍又一遍,但和他们在一起工作一起吃饭,也不免让疲惫的身躯找到了些许心灵的安慰。
当问起他们这么辛苦怎么干的下去时他们总会很轻巧的说声习惯了。40度的蒸炉里高强度的工作再习惯也会疲劳,支撑他们的信念也许是父母安逸的微笑、也许是孩子抱回的奖状、也许是妻子做好的晚饭。每个冲压工都是一个传奇,每个冲压工都有自己的幸福与不愉快。我们要真心的倾听他们的心声,和他们做知心朋友。让冲压厂成为一个彼此不分的大家庭。在冲压的这个月里我流过很多汗,多少次想逃避,但是他们的鼓舞让我不能轻言放弃,从他们身上我学到了朴素、真诚、坚持、责任、认真的态度。感谢他们对我的帮助,八月在冲压将是我职业生涯最难忘的一段回忆。
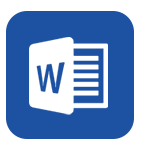