前言
本次实习所去企业为田东炼油厂,公司现有原产原油3万吨的小油田、年加工原油100万吨的炼油厂、年加工蜡油100万吨的润滑油厂以及与生产相配套的原油、成品油铁路专用线和钦州港区原油储运库(目前钦州港内铁路向未建成,该厂原料均采用大吨位汽车运送)。此外,本公司还在钦州港区的广西田东沥青有限公司占有部分股份。炼油厂主要装置有:20万吨/年常减压原油蒸馏、80万吨/年常压原油蒸馏、7万吨/年重油催化、2万吨/年石脑油芳构化等生产装置和相应的辅助生产车间及配套公用工程。润滑油厂设有10万吨/年糠醛精制、5万吨/年酮苯脱蜡脱油、3万吨/年油品精制及调合、1万吨/年石蜡精制等生产装置。主要产品有90#。93#无铅汽油、0#柴油系列、200#溶剂油、民用液化石油气、重油等,产品多达50余种,所有产品均达国颁部颁标准,产品畅销广西各地及云、贵、粤、湘等省。
在陈小鹏教授和王琳琳教授的带领下,我们在炼油厂的常减压车间、催化裂化车间和酮苯车间进行实习,实习内容为了解工厂基建、生产和发展的全过程;产品品种、生产工艺、主要设备、产品质量和技术规格;原料产品的性质、贮藏、运输以及产品用途等方面的概况。
实习期间,仔细观察分析各工段工艺流程,做好实习笔记,结合自己现有的知识,收集资料,编写了这份实习报告。报告概括了本次实习的目的和任务,具体分析了各工段工艺流程以及主要设备情况等。由于知识水平有限,报告中难免有错误和不足之处。请老师给予批评指正。
报告编写人: 2011年3月20日
毕业实习的目的和任务
毕业实习是在学生学完教学计划中所规定的各门课程后,并在生产实习的基础上进行的。
(一) 实习目的
1、印证、巩固、提高和运用所学过的理论知识,特别是专业课程的理论知识。培养学生理论联系实际的能力。
2、进一步丰富实际生产知识。提高学生观察问题、分析问题和解决的问题的能力。
3、收集必要的数据、资料,为毕业设计、毕业论文做好准备。
4、向工程技术人员、工人学习,进一步培养劳动观念,群众观点和辩证唯物主义的观点。
(二) 实习要求
1、能从理论上阐明生产实际问题,对重点工段的工艺问题,应做较深入的理论分析和评比。
2、对重点工段的生产流程及主要设备有较深入细致的了解,绘制详细的生产流程图。并对设备和流程进行评比。
3、掌握正常操作的重点,能对典型事故处理及开停工步骤有所了解并进行理论分析。
4、对全厂性问题及非工艺部分,应结合工艺要求作一般性了解。
5、收集相关资料。
(三) 实习内容
1、全厂发展概况及组织,产品品种,生产方法,之间的相互关系,厂内交通运输及总体布置。
2、全厂原料,燃料、水、电、气、汽的供需情况。
3、原料和成品的质量、贮存与运输情况。
4、生产方法、生产过程的基本原理及优缺点。
5、生产流程、主要操作条件,各种管路、分析取样、控制装置、阀门等的安排与使用。
6、了解主要设备在生产中的作用,设备的数量、类型、规格、构造及生产能力;设备的主要尺寸。所用材料及结构特点;设备的保温、防腐、安装与维修等问题。
7、各岗位正常操作的方法,工艺指标及报表分析。
8、设备的开停工,整个车间的开停工步骤及注意事项。经常性事故及处理方法,重大事故的分析与预防措施。
9、原料、半成品及成品的分析方法、分析项目。及取样方法等。
10、车间总的物料及能量平衡,以确定原料与能量的利用率并与理论可能最佳情况比较,提出改善与提高利用率的方法与途径。
11、了解重大的技术改革情况,分析生产中存在的问题和薄弱环节,提出强化生产的途径。
12、
了解车间“三废”的危害及治理情况。
第一章、工厂及车间概况
企业简介
中油广西田东石油化工总厂有限公司是广西壮族自治区国资委监管的国有控股公司,前身为广西田东石油化工总厂,始建于1978年。2004年,广西田东石油化工总厂(出资60%)与中石油南方石油勘探开发有限责任公司(出资40%)进行增资改制,成立中油广西田东石油化工总厂有限公司。现公司注册资本为3.1亿元,公司总占地面积为323290平方米,其中生产区面积为233300平方米。现有员工860人,其中,高级职称12人,中级职称128人(其中技师16人),大专以上学历216人,中专学历155人。公司炼油厂位于广西田东县,距田东汽车站1.5km;田东火车站约1.0km。右江河及南昆高速公路毗邻县城,南—昆铁路、二级路324 国道从公司生产厂区旁边经过,交通极为便利。
公司现有原产原油3万吨的小油田、年加工原油100万吨的炼油厂、年加工蜡油100万吨的润滑油厂以及与生产相配套的原油、成品油铁路专用线和钦州港区原油储运库(目前钦州港内铁路向未建成,该厂原料均采用大吨位汽车运送)。此外,本公司还在钦州港区的广西田东沥青有限公司占有部分股份。炼油厂主要装置有:20万吨/年常减压原油蒸馏、80万吨/年常压原油蒸馏、7万吨/年重油催化、2万吨/年石脑油芳构化等生产装置和相应的辅助生产车间及配套公用工程。润滑油厂设有10万吨/年糠醛精制、5万吨/年酮苯脱蜡脱油、3万吨/年油品精制及调合、1万吨/年石蜡精制等生产装置。主要产品有90#。93#无铅汽油、0#柴油系列、200#溶剂油、民用液化石油气、重油等,产品多达50余种,所有产品均达国颁部颁标准,产品畅销广西各地及云、贵、粤、湘等省。
公司地处百色市右江河谷的田东县,距田东汽车站1.5km;田东火车站约1.0km。2009年销售收入13.21亿元,上缴税金2.42,实现利润755万元;2010年销售收入23.673亿元,上缴税金3.52亿元,实现利润8300万元。为落实2008年10月21日吴邦国委员长在田东县调研和指导深入学习实践科学发展观活动时重要讲话精神,中国石油天然气集团公司决定对田东石化总厂技改项目帮扶援建。援建项目将新建:50万吨/年催化裂化、8万吨/年气体分馏和3万吨/年聚丙烯装置。现已建成中间交接,2011年4月试车投产。项目投产后,公司每年原油一次加工能力将达到100万吨(最大可达120万吨)。每年可产汽油24.9万吨、柴油45.0万吨、液化气5.96万吨(含0.88万吨丙烷)、润滑油3.0万吨、聚丙烯2万吨、石蜡1万吨等主要产品。销售收入预计可达50亿元,利税10亿元以上。
公司“十二五”规划
按照“稳定采油、提升炼油、发展润滑油”的思路,进一步优化资源配置,调整产品结构。
1、加大勘探开发,立足油田稳产。随着油田开发的深入,采出程度的提高,稳产难度加大,油田开发即将进入产量递减期。为进一步提高油田开发效益,实现五年稳产年油量3.0×104t,整体提高采收率5.3个百分点,必须有增储上产的产能建设计划,加强基础研究和目标方案论证的科研技术计划,以及油田开发配套的地面工程等技改计划,以提高水驱动用程度和采收率为目的的综合治理效果。“十二五”期间,采油、钻探预计总投资9350万元。
2、力争在防城港建设一座300万/年吨沥青厂。与和广西北部湾港务集团合作,投资1.5亿元在防城港企沙工业园区建设一座300万吨/年沥青厂。并利用好现有的5万吨级码头及原油储运库,以满足公司今后的进一步发展需要。
3、完善炼油工艺。力争原油加工能力达250万吨/年,新增20万吨/年催化重整装置;新增30万吨/年汽油、柴油加氢精制装置,50万吨/年延时焦化装置。
4、延伸石化产业链,建设30万吨/年润滑油厂。充分利用中石油钦州1000万吨/年炼油厂的加氢尾油进行深度加工,生产润滑油产品。新增150万吨/年原料油预处理装置;20万吨/年酮苯脱蜡脱油装置;15万吨/年润滑油白土精制;8万吨/年石蜡精制;8万吨/年石蜡成型,改扩建铁路专线设施。(该项目总投资为5.22亿元,在现有年加工5万吨/年润滑油厂的基础上进行扩建,是润滑油厂生产能力达到年加工蜡油30万吨。
第一章,
常减压车间
常减压车间主要是通过物理蒸馏的方法,将原油蒸馏,得到不同的产品,如,汽油、液化气、柴油、重油等产品。
生产流程简述
由原油贮罐来的40°C的原油经原油泵加压后经换热器1(原油与初顶油汽换热器),换热器2(原油与常顶油汽换热器),换热器3(原油与减一线油换热器),换热器4(原油与常四线油换热器),换热器5(原油与常一线油换热器),换热器6(原油与常二线油换热器)换热至120度后经电脱盐脱水。
原油经电脱盐脱水后与油渣、减二线油换热,分二路;一路与减一线油、油渣换热;第二路与减三线油、常三线油、常二中油换热至200°C与第一路油混合进初馏塔。 初馏塔顶部的油汽经过换热、冷却后去油水分离器,切水后由泵抽出分二路,第一路返回初馏塔顶,第二路出装置。初馏塔塔底油由泵抽出后分二路;第一路经常压炉对流室加热至210°C返回初馏塔中部,第二路与减四线油、减二线油换热后分三路,第一路与油渣换热;第二路与常二中油、常四线油换热;第三路与减三线油、减四线油换热,与第
一、第二路加热至280°C混合进常压炉,经常压炉加热至365°C进常压塔。
常压塔顶部的油汽经换热,冷却后去油水分离器,切水后,由泵抽出分二路,一路返回常压塔,另一路出装置。
常一线油由常压塔抽出进常一线汽提塔,油汽经塔顶返回常压塔,常一线油由泵从塔底抽出经换热,冷凝后出装置。
常二线油由常压塔抽出进常二线汽提塔,油汽从塔顶返回常压塔,常二线油由泵从塔底抽出经换热,分二路,一路返回常压塔,另一路经冷却后出装置。
常三线油由常压塔抽出进常三线汽提塔,油汽从塔顶返回常压塔,常三线油由泵从塔底抽出经换热、冷却后出装置。
常四线油由常压塔抽出进常四线汽提塔,油汽从塔顶返回常压塔,常四线油由泵从塔底抽出经换热、冷却后分二路,一路出装置,令一路去减顶回流装置。
常二中油由泵抽出经换热后返回常压塔。
常低油由泵抽出去减压路加热至400°C进减压塔,或直接经减渣换热,冷却出装置(不开减压装置时)。
减顶油汽被抽真空系统抽出,经冷却后冷凝油经泵经常二或常三或汚油管线出装置。
减一线油由减压塔抽出进减一线汽提塔,油汽从塔顶返回减压塔,减一线油由泵从汽提塔塔底抽出经换热,冷却后,一路返回减压塔顶,一路出装置。
减二线油由减压塔抽出进减二线汽提塔,油汽从塔顶返回减压塔,减二线油由泵从汽提塔塔底抽出经换热后,一路返回减压塔,一路经冷却后出装置。 减三线油由减压塔抽出进减三线汽提塔,油汽从塔顶返回减压塔,减三线油由泵从汽提塔塔底抽出经换热后,一路返回减压塔,一路经冷却后出装置。
减四线油由减压塔抽出进减四线汽提塔,油汽从塔顶返回减压塔,减四线油由泵从汽提塔塔底抽出经换热后、经冷却后出装置。
减压渣油经泵从减压塔低抽出经换热、冷却水箱冷却至95°C后出装置。 初定、常顶、减顶部凝汽经容器回收部分液化气后去常、减压炉作为燃料汽。
注氨注水:氨气(液氨)和软化水在氨水罐混合后经泵直接注入初馏塔顶馏出口管线,氨水在油水分离器回收至氨水罐。
注破乳剂:直接注入进装置前的原油管线。
第二章、催化裂化车间
催化裂化车间主要加工从常减压车间过来的蜡油、油渣,在催化剂作用下,经高温高压将重油催化裂化为液化气、汽油、柴油等轻质油。
减压蜡油和减压渣油分别从催化原料油中间罐区和燃料油罐区用泵抽出装置。在管线中混合后,先后与轻柴油、分馏中段循环油、油浆换热至250°C后,与渣油混合后进加热炉加热后与回炼油油浆混合后进入提升管反应汽下端的喷嘴。
提升管反应器的进料与来自再生器的再生催化剂接触,并迅速汽化、反应。反应生成的反应油汽进入沉降器,先经旋风分离器除去大量的催化剂后,催化剂进入塔下部,反应会的待生催化剂经汽提段汽提后进入再生器进行烧焦再生。空气在床层中与催化剂良好接触,使催化剂上的焦燃烧很快。并放出大量的热,使一段床层达到650—660°C二段床层达到670—690°C左右。燃烧生成的烟汽经旋风分离器除去大量催化剂后,先经双动滑阀,后经降压孔板降压、消声器、经管道利用余热加热蒸汽后排至大气。
反应汽油进入分馏塔底,先经人字挡板与油浆逆流循环接触,一方面洗去油汽中的催化剂,另一方面使油汽由480°C降至375°C进入第一层塔盘进行分馏。分馏塔顶油汽115°C经冷却至40°C,后进入容器(使油水汽分层),从容器分离出粗的汽油,用泵送至吸收塔塔顶作为吸收剂。富汽进入空气压缩机加压。
轻柴油自分馏塔的第14层或16层。自流入轻柴油汽提塔,经蒸汽汽提后的轻质柴油215°C用泵加压,先与新鲜原料油后,再与除盐水换热至40°C,一部分经冲洗后作为产品送出装置。另一部分作为吸收剂送至吸收塔,富吸收油返回分馏塔的第18层,还有部分用于燃料油封油和冲洗油用。
顶循环油用泵从22层抽出,抽出温度160°C与除盐水换热至80°C返回第26层。中段循环油用泵从第11层抽出,温度为250°C先经吸收稳定部分的再沸器换热后,再与新鲜原料油换热至170°C后,返回分馏塔的14层。分馏塔设置了重柴油抽出阀,当需要时,重柴油从第9层抽出,经换热从300°C冷却至60°C作为产品送出装置。回炼油从第二层塔板抽出进入回炼油罐,后经泵加压,部分返塔,部分与原料油混合。油浆循环油经泵从塔底抽出,温度为375°C,一部分与原料油换热,后经过蒸汽发生器,使油浆循环油冷却至297°C返回塔底部第一层塔板下。另一部分经泵送至提升管反应器回炼。
经空气压缩机加压后的富汽和来自解吸塔塔顶的解吸汽混合后,经冷却至40°C进人油汽分离器进行气液分离,分离出的油汽进入吸收塔的底部,经吸收剂吸收后,从塔顶出来进入再吸收塔底部。富吸收油从塔底自流入油汽分离器。从吸收塔顶来的富汽进入再吸收塔,用轻柴油再吸收后,塔顶为干气,作为燃烧气。塔底富汽吸收油返回分馏塔。油汽分离器出来的凝缩油用泵压至解吸塔进行解吸,解吸汽经冷却进入油汽分离器,塔底脱乙烷汽油经泵抽出,与稳定汽油换热至147°C进入稳定塔,C4以下的轻组分从塔顶馏出,经冷却后进入容302平衡汽化。冷却后的液态烃用泵从罐底抽出,一部分送回塔稳定塔顶作为回流,另一部分送至冲洗部分,经冲洗后作为产品抽出装置。稳定汽油自塔底出来,先与脱乙烷油换热,再经循环水冷却至40°C,然后一部分经泵送至吸收塔作为吸收剂,另一部分经冲洗、防胶处理后作为产品抽出装置。
固体钝化剂经换热后用泵送入原料管线与原料油混合后进入提升管反应器。
第三章、酮苯车间
酮苯车间分别以常压变压器油料、减压各测线油料作原料,以丁酮、甲苯为溶剂,采用冷冻结晶法生产润滑油和石蜡,既加工轻质原料,又加工重质原料,既要脱蜡又要脱油,因此,原料、产品品种多,工艺流程复杂,切换原料频繁,和其他车间相比,有明显不同。酮苯脱蜡装置是以常三线油和减压各侧线油为原料,以丁酮、甲苯二元溶剂混合后作为溶剂。利用酮苯混合溶剂对原料中的油、蜡有不同的溶解度和粘度较小的特性。在油冷冻结晶过程中按一定比例加入适当组成的溶剂,并经过滤将油蜡分离,滤液和蜡液经加热蒸发回收溶剂后送油、蜡出装置,回收后的溶剂循环使用。
一、结晶系统
1、
原料流程:
原料由罐区来—→原料泵(泵—1/1.2)抽出—→原料水冷器(冷—1)—→滤液换热套管(结—1/2)—原料一段氨冷器(结—2)原料二段氨冷器(结—3)—滤机进料罐(容—1.2)—去滤机(原料循环时,可经冷循环线回至原料循环入口)
2、
湿溶剂流程(或一次溶剂流程)
湿溶剂自湿溶剂罐(容—12)来—一次溶剂泵(泵—2/1.2)抽出后分两路一路去冷—1入口作预稀释;另一路去一次溶剂与滤液换冷(换—2)换冷后分三路;一路去结—1/1的第四根,一路去结—1/1)的出口。一路去结—1/2出口做冷点稀释溶剂。
3、
干溶剂流程
(1)、二次溶剂
干溶剂自(容—14)二次溶剂泵(泵—3/1,2)抽出—二次溶剂换热器(换—3)—溶剂一段氨冷器(冷—2/1,2)溶剂二段氨冷器(冷—2/3)—分两路;一路去结三出口做三次稀释;一路去滤机做冷洗。(循环时可经二次溶剂循环线至容—14)。
(2)、热溶剂流程
干溶剂自(容—14)来—二次溶剂泵(泵—3/1,2)抽出—溶剂加热器(换—4)—分两路;一路去设备冲洗管线;一路去滤机做温洗液。
4、
滤液流程
滤液自(容—6,7)来—滤液泵(泵—5/1,2)抽了出分三路;一路去滤液换冷套管(结—1/2);一路去一次溶剂换热器(换—2);一路去二次溶剂换热器(换—3);(换—2)、(换—3)出口→(结—1/1)→出口与(结—1/2)出口滤液会合→去油回收。
二、冷冻系统
1、
正压流程
经氨压机压缩后的高压气氨经油氨分离后→气氨干、湿空冷器(空冷—1,2)→氨立式水冷器(冷—13,14)→液氨贮罐(容—21,22,23)→经济器过冷(经—
1、
2、
3、
4、)→液氨分配站→去各氨冷器。
2、-20C系统的负压流程
原料一段氨冷器(结—2)、溶剂一段氨冷器(冷—2/1,2/2),惰性气氨冷器(冷—4)所蒸发出的气氨→-20OC低压分享离器(分—2)→氨压机(机—
3、4)经压缩后走正压流程。
3、-40OC 系统的负压流程
原料二段氨冷器(结—3),溶剂二段氨冷器(冷—2/3)所蒸发出的气氨→-40C低压分离器(分—1)→氨压机(机—1,2)压缩后走正压流程。
三、真空系统
1、
发生机送气流程 OO灯油与工业风在发生炉(炉—3,4)内燃烧,所生成的安全气→6#分液罐(分—6)→安全气贮罐(容—16)→7#分液罐(分—7)→经补气阀至真空泵入口分液罐(分—8)。
2、
真空系统正压流程
循环气经真空泵(机—
5、6)压缩→惰性气水冷器(冷—3)→9#分液罐(分—9)→惰性气氨冷器(冷—4)→10#分液罐(分——10)→惰性气体中间罐(容——4)→分三路;一路经酮吸收器(容——19)排空(含氧量高及滤机密闭压力高时使用);一路滤机做反吹;一路去滤机做密闭(滤机密闭出来的气体去各罐做密闭气体,最后经循环线回到滤液罐(容——6)。
3、
真空系统负压流程
滤机三部真空抽出来的气体与循环气在滤液罐(容——6)汇合→泡沫分离罐(容——3)→8#分液罐(分——8)→真空泵(机——5,6)入口。
四、油回收系统
1、
油主物料流程
滤液自结晶系统来→经油低压塔顶换热器(换——6,7,8)与低压塔顶气换热→经油高压塔顶二次换热器(换——9,10)与油高压塔顶气换热→油低压塔(塔——1)→由油低压塔底泵(泵——7/1,2)抽出→经油汽提塔底换热(换——12)、高压塔顶换热器换热(换——11)→经滤液加热炉(炉——1)→油高压塔(塔——2)自压至油末次塔(塔——3)然后溢流到油汽提塔(塔——4)→由油汽提塔底泵(泵——8/1,2,)抽出→经由汽提塔底换热器(换——12)与油高压塔进料换热→经油出装置水冷器冷却后送至罐区。
2、
油回收各塔顶物料流程
(1)、油低压塔物料→油低压塔顶换热器(换——8,7,6)与油低压塔进料换热→油低压塔顶水冷器(冷——5,6)冷却→干溶剂罐(容——14)。
(2)、油高压塔顶物料→油高压塔顶一次换热器(换——11)与油高压塔进料换热→油高压塔顶二次换热器(换——10,9)与油低压塔进料换热→油高压塔顶水冷器(冷——7,8)冷却→至干溶剂罐(容——14)。
(3)、油末次塔、汽提塔顶汽,经(换——13)、(冷——9)、(冷——10),→(容——9)。
3、油回收冷大循环流程
油低压塔(塔——1)底物料→油低压塔底泵(泵——7/1,2)抽出→经汽提塔底换热器(换——12)→经高压塔顶一次换热器(换——11)→滤液炉(炉——1)→油高压塔(塔——2)→油低压塔底备用泵(泵——7/3)抽出→油末次塔(塔——3)→自流至油汽提塔(塔——4)→油汽提塔底泵(泵——8/1,2)抽出→油出装置换热器(换——12)→油出装置水冷器→经循环线至油低压塔顶换热器(换——6,7,8)→经油高压塔二次换热器(换——9,10)→油低压塔(塔——1)。
4、
油回收小循环流程
油低压塔底物料→油低压塔底泵(泵——7)抽出→经油汽提塔底换热器(换——12)→经油高压塔顶一次换热器(换——11)→经滤液加热炉(炉——1)→油高压塔(塔——2)→经小循环线至油低压塔(塔——1)。
五、蜡回收系统
1、
蜡回收系统主物料流程
冷蜡罐(容——8)物料→冷蜡泵(泵——6/1,2)抽出→经六塔换热器(换——13)与六塔顶汽换热→经蜡低压塔顶换热器(换——14)与蜡高压塔顶汽换热→蜡高压塔顶换热器(换——15,16)与蜡高压塔顶汽换热→蜡低压塔(塔——5),塔底物料由低压塔底泵(泵——9/1,2)抽出→经蜡汽提塔底换热器(换——17)与蜡汽提塔底物料换热→蜡液加热炉(炉——2)→蜡液高压塔(塔——6),(塔——6)底物料自压至蜡液末次塔(塔——7)→自流至蜡汽提塔(塔——8),塔底物料由蜡汽提塔底泵(泵——10)抽出→经汽提塔底换热器(换——17)与高压塔进料换热→经蜡出装置水冷器冷却→罐区。
2、
蜡回收各塔顶物料
(1)、蜡低压塔顶汽→蜡低压塔顶换热器(换——14)与蜡低压塔进料换热→干燥塔(或进塔——6顶水冷器)。
(2)、蜡高压塔顶汽→蜡高压塔顶换热器(换——16)→(换——15)与蜡低压塔进料换热→蜡高压塔顶水冷器(冷——11)冷却后→沉降罐(容——10)。
(3)、油、蜡回收汽末次塔顶汽与脱酮塔顶汽,干燥塔顶汽汇合在一起→经六塔顶换热器(换——13)与蜡低压塔进料换热→经六塔顶水冷器(冷——9,冷——10)冷却后→去水溶液罐(容——9)。
3、蜡回收冷大循环流程
蜡低压塔(塔——5)底物料→蜡低压塔底泵(泵——9/1,2)抽出→蜡汽提塔式底换热器(换——17)→蜡液加热炉(炉——2)→蜡高压塔(塔——6),塔底物料自流至→蜡低压塔底泵(泵——9/3)抽出→蜡末次塔(塔——7),塔底物料自流→蜡汽提塔(塔——8),塔底物料→蜡汽提塔底泵(泵——10)抽出→经蜡汽提塔底换热器(换——17)→经蜡出装置水冷器→蜡大循环线→六塔顶换热器(换——15,换——16)→蜡低压塔(塔——5)。
4、蜡回收小循环流程
蜡低压塔(塔——5)底物料→蜡低压塔底泵(泵——9/1,2,)抽出→蜡汽提塔换热器(换——17)→蜡液炉(炉——2)→蜡高压塔(塔——6),塔底物料→小循环线→自流至低压塔(塔——5)。
5、
水回收系统流程
滤液汽、末两塔,蜡液汽、末两塔,脱酮塔、干燥塔的顶部溶剂汽、水蒸汽的混合物汇合后进入(换——13)→水冷器(冷——9,冷——10)冷凝冷却后进入水溶剂罐(容——9)。溶剂在(容——9)中,因比重的不同分为上下两层,上层的物料为丁酮和甲苯的混合物,它们溢流到沉降罐(容——10)。下层的物料是水和丁酮的混合物,由通用泵抽出,打至脱酮塔(塔——10)进行汽提,使大部分酮汽化酮和水蒸汽由塔顶馏出,经六塔换热器(换——13)、六塔水冷器(冷——9,冷——10)冷却后,回到水溶剂罐(容——9)。脱酮塔(塔——10)底含微量的热水直接排入污水沟。
6、
溶剂干燥系统流程
沉降罐(容——10)内含少部分水,由干燥塔进料泵(泵——12)抽出,打入溶剂干燥塔的上部(塔——9),干燥塔内物料经来自(塔——5)顶的热溶剂气汽提后,塔底已干燥的溶剂由干燥塔底泵(泵——11/1,2)抽出,经干燥塔底水冷器(冷——12)冷却后,进入湿溶剂罐(容——12)。干燥塔顶含水混合气经六塔顶换热器(换——13)、六塔顶水冷器(冷——9,10)冷却后,进入水溶剂罐(容——9)。
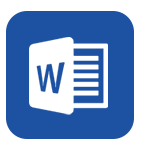