方
技 术
案
目录
(一)、气固混燃锅炉简介„„„„„„„„„„„„3
(二)、设计原则、标准和规范„„„„„„„„„„8
(三)、设计依据资料及技术要求„„„„„„„„„9
(四)、气固锅炉物料热量衡算„„„„„„„„„„10
(五)、主要设备选型„„„„„„„„„„„„„„11
(六)、主要运行参数„„„„„„„„„„„„„„12
(七)、气固锅炉流程及公用工程简述„„„„„„„12
(八)、自控仪表„„„„„„„„„„„„„„„„14
(九)、乙方投标报价范围„„„„„„„„„„„„18
(十)、气固锅炉设计性能验收标准„„„„„„„„19
(十一)、技术服务及优惠条件„„„„„„„„„„20
(十二)、其他(附件)
平面布置图、工艺流程图
(一)、气固混燃锅炉简介
1、气固混燃锅炉概述
造气气固混燃锅炉是化工循环经济的典型产品:循环经济是一种以资源的高效利用和循环利用为核心,以“减量化、再利用、资源化”为原则,以低消耗、低排放、高效率为基本特征的装置。
造气气固混燃锅炉,是将造气生产过程产生的吹风气、造气炉渣、除尘器细灰,掺入部分粉煤和煤矸石在气固混燃锅炉内进行流化燃烧,达到制取高位热能蒸汽的目的。产出的中温中压蒸汽部分经背压发电,背压后的低压蒸汽供造气、甲醇精馏使用,少量中温中压蒸汽经减温减压后供变换和其它工段使用,达到一炉多用。同时将用于造气的原料达到吃干榨净的目的。
造气气固混燃锅炉,其优越的性能远远大于第二代吹风气余热锅炉。如安全性,克服了第二代造气吹风气燃烧炉开车点火时送合成气的爆炸条件,避免了吹风气回收过程中的爆炸因素,使造气吹风气回收过程达到安全化。
对于煤造气生产甲醇的企业,采用气固混燃锅炉的最大收益是将甲醇产量提高17-20%。其原因是,甲醇生产的合成放空气经提氢后其热值只有1900kcal/m3(合成氨的合成放空气经提氢后为3850 kcal/m3),比合成氨低一半,无法点燃造气的吹风气,只有多烧氢气或水煤气,因而造成甲醇产量低、消耗高。甲醇生产合成放空气中的甲烷含量低,属半低热值气体(甲烷含量只有5-7%)。如湖北某甲醇厂,5万吨的甲醇(单醇)装置选用第二代吹风气余热锅炉,每天少产甲醇11.2吨;河南某甲醇厂8万吨的生产装置选用第二代吹风气余热锅炉回收造气吹风气,其合成放空气远远不够,不得不以水煤气与合成气混合作点火源,多烧的水煤气每天少产甲醇17.6吨。气
固混燃锅炉是以煤为点火源,造气吹风气直接进入即可燃烧,节约的氢气,使产量增加17-20%。
固定层造气炉生产合成氨,采用气固混燃锅炉,是以造气炉渣和粉煤为点火源,燃烧造气吹风气,可少用或不用合成点火气,节约氢气或水煤气,一般企业可使合成氨产量增加3-5%,如一套10万吨的合成氨企业,采用气固混燃锅炉,在不增加各项消耗的前提下,每天可多产合成氨10-15吨,每天可增加2-3万元的纯利。如我国的西南部,生产合成氨是以贵州煤为原料,其半水煤气中的CH4含量偏低,生成的合成放空气比用山西煤少一半,因而无法维持造气吹风气稳定燃烧,需要多烧水煤气或氢气,采用气固混燃锅炉可使合成氨产量增加8-10%。
第一代造气吹风气余热锅炉,其燃烧形式是上燃蓄热式,利用高热值合成气燃烧蓄热后,来燃烧低热值的造气吹风气,回收热量、副产蒸汽,保护环境。
第二代造气吹风气余热锅炉(现在普遍使用的一种),在第一代的基础上,增加了燃烧喷头,减少了炉内格子砖,使炉内的阻力大大减小,减小了造气炉吹风阶段的阻力,增大了造气炉的负荷,同时烟气燃烧更为完全,使造气蒸汽达到了自给,但其蓄热能力差,在助燃气量不足的情况下炉温下降不能正常送吹风气。
造气气固混燃锅炉,它和第二代相比又有了突破性的发展,并申请了国家专利,专利号为ZL 201120050994.X。
造气气固混燃锅炉和第二代造气吹风气余热锅炉相比有如下优点:
(1)、安全性
克服了第二代造气吹风气燃烧炉开车点火时送合成气时的爆炸条件,避免了吹风气回收过程中的爆炸因素,使造气吹风气回收过程达到安全化。
(2)、气固混燃锅炉回收造气吹风气过程中,是以煤为点火源,可少用或不用合成点火气,即造气吹风气回收不受合成因素的影响,节约氢气和半水煤气,可使合成氨产量提高3-5%。
(3)、中小型尿素厂一台气固混燃锅炉就能达到全厂蒸汽自给,实现了尿素生产的两炉变一炉和两煤变一煤的目标。
(4)、解决了造气生产废气、废渣、废灰综合治理的难题,保护了环境。
(5)、一炉多用、一炉多能,停掉能耗高的锅炉,节约能源,提高效率,同时可减掉部分操作人员。
(6)、一台气固锅炉的投入,两台锅炉的收益,使新建和扩建的企业节约投资达50%。
2、燃烧机理与设备构成
气固混燃锅炉运用了沸腾床和流化床锅炉的燃烧特性,采用了吹风气余热锅炉的模式。对造气系统产生的废气、废渣、废灰能够达到同时混燃,在单烧吹风气时该炉将成为一台吹风气余热锅炉,单烧煤(或高硫煤)、矸石、煤渣等时将成为一台内循环流化床锅炉,渣、气、煤混烧将成为气、固流化混燃锅炉。因其热量回收形式上同燃煤锅炉和吹风气余热锅炉相似,所以可以称做“双热源气固混燃锅炉”。造气气固混燃锅炉是目前解决合成氨—尿素甲醇生产系统两煤变一煤、两炉变一炉的唯一方案,也必将成为吹风气余热锅炉的换代产品。
气固混燃锅炉可以根据不同的要求作成各种规格型号,在吨位上分有10-150吨/时,在压力上分有1.3 MPa、2.5 MPa、3.82 MPa、3.82 MPa、9.8 MPa等。
气固混燃锅炉的燃烧部分由二台设备组成,一台是气固混燃炉,另一台是燃尽除尘炉;其混燃炉采用钢制外壳制成,下部为沸腾床,渣、煤下部混燃,有风室、布封板风帽、采压点、观火孔、加煤口、返料口。中部有吹风气进口、合成驰放气喷头、废液碰头等。内衬采用
一、二级高铝砖砌筑,沸腾段采用磷酸盐砖或耐高温耐磨高强浇注料,顶部采用球顶砖砌成,主体耐火保温层厚度550mm,其中耐火层230mm、高铝隔热保温砖65mm、保温棉255mm;燃尽除尘炉采用钢制外壳制成,有顶进底排气式或低进顶排气两种方式,采用耐高温耐磨二级高铝砖砌成,主体耐火保温层厚度550mm,内部砌筑烟尘导流分离器,底部设为水封刮板捞渣机或干式下灰阀。
气固混燃锅炉的热量回收由两部分组成,一是混燃炉内的受热面;二是燃尽除尘炉后的水冷屏、蒸汽过热器、余热锅炉对流管束、省煤器、空气预热器。
3、优势特点 (1)、操作稳定
气固混燃锅炉燃煤、燃气同时进行,具有热量互补作用。 燃煤稳定的情况下,对于吹风气来讲是一个恒定的热源,无须考虑合成放空气量的多少影响炉温,避免了因合成放空气量的不稳定而导致吹风气运行不正常的现象,也可不用合成放空气,也可配烧低热值的其它气体,如变压吸附的逆放气等。
吹风气燃烧正常的情况下,即使燃煤稍有变化,吹风气的热量也能起补充作用。
沸腾段内无受热面、无热量的移走,在加煤变化的情况下,炉温的稳定性远远大于循环流化床锅炉,因而操作的难度比循环流化床锅炉小的多。 (2)、安全
第一代或第二代吹风气燃烧炉均需要点火气源,低于650℃时吹风气就不能燃烧,送入的吹风气就会发生爆炸,(如山东某化肥厂新建的一套30吨的吹风气燃烧炉,在点火烘炉时操作不当产生爆炸,整套系统除锅炉本体外全部损坏,重新投资近100万元,二个月的时间才修复,其它厂爆炸的可能性也经常发生);第二个方面,造气吹风气座板阀开关频繁,关闭不严煤气进入燃烧炉在配风阀来不及调节时,发生爆燃爆炸的现象也时有发生。
而气固混燃锅炉是以煤为点火源,始终是长明火,不会存在爆燃爆炸现象;另外气固混燃锅炉在煤的燃烧过程中,温度高且有氧气过剩,若有多余的煤气送入时只能继续燃烧,不会发生任何爆炸现象。因而气固混燃锅炉是极其安全可靠的。 (3)、连续运行周期长
气固混燃锅炉燃煤沸腾段内不设受热面,燃煤悬浮段烟气流速低于2m/s,悬浮段下部设受热面,吸收燃煤产生的辐射热,降低锅炉的造价,出悬浮段烟气温度在880℃左右,吹风气入口以上采用绝热燃烧,可使吹风气中的可燃气体及携带煤粉燃烧完全,因而沸腾段部分不存在锅炉排管的磨损和冷热不均产生应力而导致设备损坏的问题,悬浮段部分烟气流速低使受热面的磨损大大降低,因而气固混燃锅炉运行周期将连续超过360天。 (4)、节能效果显著
山东瀚海化工厂气固混燃锅炉未投运之前,开一至两台35t/h的链条炉,冬季开两台,该炉型节能效果比较好,其链条锅炉的炉渣残碳不足5%,但是当40t/h的气固混燃锅炉投运后,巨大的节煤效益才体现出来,全厂的燃料煤不用了。三废炉开启前后比较,在气固锅炉掺烧造气炉渣量比例不是高限的情况下,日节约燃料煤50余吨。 (二)、设计原则、标准和规范
一、设计原则
1、总体设计方案、工艺流程、控制方案的编制及设计以原化工部通用设计为基础,着重突出节能、减排、降低成本的原则;
2、采用目前国内先进成熟可靠的气固热能回收技术,即气固混燃锅炉专利技术,其专利号为:ZL 201120050994.X。能耗处于国内先进水平;
3、新建气固混燃锅炉回收8台煤气发生炉的吹风气、炉渣、提氢后的放空气、合成驰放气;
4、尽量充分利用厂内现有公用工程系统,以尽可能的降低工程造价和运行后的产品成本,同时缩短建设周期。
二、设计标准和规范
1、非标设备的设计、制造、安装、管理、运行遵守的规范、标准及规定:
(1)、《化学工业炉耐火、隔热材料选用规定》(HG/T20683-1999) (2)、《化学工业炉金属材料选用规定》(GBJ211-87) (3)、《石油化工钢制压力容度器材料选用标准》(SH3065-95) (4)、《钢制压力容器焊接规程》(JB/T4709-2000) (5)、《工业设备及管道绝热工程设计规范》(GB50264-97) (6)、《钢制压力容器》(GB150-98)
(7)、《石油化工企业设备和管道涂料防腐蚀设计与施工规范》 (SH/T3022-99)
(8)、《化学工业炉结构安装技术条件》(HG20544-92) (9)、《钢制常压容》(JB4735-97)
2、砌筑施工及材料标准:
(1)《化学工业炉砌筑技术条件》HG20543-92 (2)《工业炉砌筑工程施工及验收规范》GBJ211-87
3、锅炉部分设计制造标准:
(1)、《蒸汽锅炉安全技术监察规程》
(2)、《烟道式余热锅炉通用技术条件》JB/T6503 (3)、《水管锅炉受压元件强度计算》GB/T9222 (4)、《工业锅炉安装工程施工及验收规范》GB50273
(三)、设计依据资料及技术要求
1、造气炉φ2800mm8台,正常开8台造气炉,造气炉烧煤棒,合成氨能力10万吨/年
2、D600型造气鼓风机,每个单元有4台造气炉,造气炉制气循环时间120s,吹风时间为28-30s
3、吹风气: CO 5.5%,H2 2%,其余为N
2、CO2
4、燃烧炉进驰放气成份,CH4为27.9%,H2为43.5%,N2为28.6%,吨氨按消耗半水煤气3300标方计,半水煤气中CH4按2.5%计。合成驰放气中甲烷含量以18%计。氢回收率设定为85%
5、造气炉入炉煤质为5500大卡,吨氨煤耗实物量为1.55~1.60吨;煤中含灰渣量为25%,灰渣含碳量为15-18%
6、蒸汽条件: 发汽量 Q=50t/h
蒸汽压力 P=3.82MPa(表) 蒸汽温度 T=435℃ 给水温度 T=98~104℃
7、主要气体参数: 燃烧温度 900~1050℃
排烟温度 150~170℃ 用于煤棒烘干 混燃炉内烟气截面流速 ≤3m/s 系统阻力 ≤2800Pa 炉膛负压 -10~-50Pa
8、混合料:热值≥1000Kcal/kg;混合料粒度0~12mm
9、混燃炉粗渣残C≤2.0%、锅炉尾部细灰残C≤8%
10、烟气(CO+H2)%≤0.3%(V/V)
(四)、三废炉物料热量衡算
1、按常规计算,吹风气的低位发热值为243kcal/Nm3气量按45000 Nm3/h,提氢后的驰放气的低位发热值为3303kcal/Nm3气量按1260 Nm3/h。
2、查表知,3.82Mpa、435℃的过热蒸汽的热焓为790kcal/kg;锅炉给水的热焓按90 kcal/kg计算。
3、一台50t/h气固混燃炉,回收8台Φ2800的造气炉的吹风气和合成驰放可产3.82Mpa、435℃的蒸汽15t/h,燃煤渣部分按每小时产蒸汽35吨设计,煤渣混合料的热值按1000~3500 Kcal/kg 设计,炉渣可全部用完。燃煤渣产蒸汽正常按50~115%负荷调节,满足气固混燃炉产蒸汽50 t/h。在不影响产蒸汽符合的情况下可回收1~3吨难处理的有机废液,满足环保要求。
4、一次风配风量为46000m3/h;二次风配风量26600m3/h;燃烧产烟气量为12万Nm3/h。
(五)、主要设备选型( 50t/h气固混燃锅炉设备选型)。
1、气固燃烧炉规格尺寸:Φ8528×21000×14 mm(Q235B) 燃烧炉可根据燃烧固体物料的粒径大小调整直径和高度,直径可到11米,高度可到32米。其目的可保证≤100um的物料一次性燃烧完全
气固燃烧炉保温层厚度:550 mm 气固燃烧炉外壳温度:≤55℃
气固燃烧炉布风板、风帽规格:Φ3800×30 ;Φ5.5/4.2 吹风气预混器: Φ1420 无焰燃烧喷头:Φ500×900
2、燃尽除尘炉规格尺寸:Φ6520×20800×10 mm(Q235B) 除尘炉设计有返料功能,可将未燃尽的碳颗粒返回炉膛内继续燃烧 燃尽除尘炉保温层厚度:55 mm 燃尽除尘炉外壳温度:≤55℃
3、50t/h P=3.82Mpa T=435℃的隧道窑式锅炉一台套(包括:水冷屏、蒸汽过热器、锅炉对流管束、省煤器、空气预热器、炉内受热面、布风板、风帽等)。
4、静电除尘器:入口烟气量12万Nm3/h,烟气含尘量6~10g/Nm3,除尘效率>99%,出口含尘量≤50mg/Nm3(以当地环保要求为准)。
5、一次风机:风机型号9-19№16D,转速1450r/min,流量32531-58000m3/h,全压13035Pa;配用电机型号Y355-4,功率315kw,电压6kv,数量1台。
6、二次风机:风机型号9-19№11.2D,转速1450r/min,流量24126-36189m3/h,全压7009Pa;配用电机型号Y315M-4,功率132kw,电压380v,数量1台。
7、引风机:风机型号Y4-73No22D,转速960r/min,流量233000m3/h,全压4256Pa;配用电机型号JSQ148-6,功率430kw,电压6kv,数量1台。
8、上煤除渣设备
(1)DJ大倾角皮带输送机一台;斗式提升机型号HL400,输送量47.2m3/h,功率11kw,数量1台。
(2)皮带给煤机型号TD65-5050型,输送带宽度500mm,功率1.1kw。数量2台。
(3)螺旋给煤机型号LS200,功率5.5kw。数量2台。
9、烟囱Φ2400×45000mm。数量1台。
10、湿法脱硫设备:出口烟气含硫量≤100mg/Nm3(以当地环保要求为准)
(六)、主要运行参数
1、燃烧温度900-1050℃、排烟温度150~170℃(烘干煤球)。
2、混燃炉内烟气流速≤3米/秒。
3、系统阻力<2800Pa。
4、炉膛负压-10~ -50Pa。
5、燃烧炉壁温≤55℃(常温状态下)
6、锅炉入口烟气含尘量8~12g/Nm3
7、烟气出口含尘量≤50mg/Nm3(上除尘设备后)
8、蒸汽产量为50t/h
9、蒸汽压力3.82Mpa
11、蒸汽温度450℃
12、固体物料:热值≥1000Kcal/kg;粒度0~12mm,超细灰物料20~100um可采用分级燃烧,使其在炉膛内一次燃烧完全
13、混燃炉粗渣残C≤2.0%、
14、锅炉尾部细灰残C≤8%
15、烟气(CO+H2)%≤0.3%(V/V)
16、可回收1~3吨废液
(七)、三废炉流程及公用工程简述
1、三废炉流程简述 (1)、固体物料
造气炉渣、造气细灰、煤沫、煤矸石等经过筛分、破碎(粒度0~12mm)、混合后热值在1000~3500kcal/kg左右的混合物料通过斗式提升机输送至煤仓,然后经过皮带给煤机输送至小给煤斗;由给煤斗经螺旋给煤机输送至气固混燃锅炉的沸腾段与经风室上来的一次风流化燃烧产生950~1050℃左右的高温烟气,此高温烟气中的可燃物质在上升过程中与配入的上下二次风进一步燃烧放热。未燃尽的物料经除尘器分离后返回炉膛内继续燃烧。 (2)、吹风气
由造气工段来的吹风气经过U型水封在吹风气燃烧喷头(预混器)与配入的二次风充分混合后进入气固混燃锅炉的中上部,被从燃烧炉下部上来的高温烟气点燃释放出其中的潜热。 (3)、提氢后放空气及合成驰放气
由合成工段来的提氢后放空气及合成驰放气经减压后进入驰放气水封,由水封进入驰放气燃烧喷头(无焰燃烧器),与配入的二次
风由炉膛中上部进入气固混燃锅炉,驰放气与配入的空气在炉内混合同时被从燃烧炉下部上来的高温烟气点燃并释放其中的潜热。 (4)烟气
燃煤燃气产生的高温烟气在炉膛内进一步上升,经过上烟道进入燃尽除尘炉后进一步燃烧除尘后进入余热回收锅炉,依次经过水冷屏、蒸汽过热器、余热锅炉对流管束、省煤器、空气预热器,而后进入静电除尘器,降温至150℃以下的烟气经过进一步除尘,尘含量均在50mg/Nm3以下的符合环保要求的烟气送入烟囱放空,或根据用户需求适当提高烟气排烟温度用于煤球烘干。 (5)、除氧水
来自除氧工段的除氧软水首先进入省煤器吸收烟气的低位热能,经过提温的除氧软水进入锅筒,然后经过锅筒进入余热锅炉的对流管束、水冷屏及气固混燃锅炉内的受热面,产生的汽水混合物再进入锅筒,经过汽水分离后的水继续循环使用。 (6)、蒸汽
锅筒内的饱和蒸汽由锅筒出来进入蒸汽过热器。在过热器内经过过热后温度在435℃左右、压力3.82MPa的过热蒸汽去汽轮机发电或经减温减压后并入低压蒸汽管网。 (7)、一次风
由一次风机出来的一次空气首先进入一次风空气预热器,经提温后的一次风进入风室经布风板上的风帽进入气固混燃锅炉的沸腾段流化煤渣混合物,使热值在1000-3500kcal/kg左右粒度0~12mm的煤渣混合物流化燃烧产生900~1050℃的高温烟气。 (8)、二次风
由二次风机出来的二次空气大部分进入二次风空气预热器,经提温后的二次风主要用来给煤渣混合物、吹风气及提氢后放空气和合成驰放气配风燃烧;使烟气中的可燃组分进一步彻底燃烧。
2、公用工程消耗 (1)、电耗
整个50吨三废炉系统装置用电大约在1000 kwh/h左右。 (2)、除氧软水
104℃的除氧软水每小时消耗53t/h左右。
(八)、自控仪表
1、控制系统的选择
本工程采用DCS集中控制方案。所有集中监控参数均引至控制室的DCS系统中,DCS由操作员站、工程师站、控制站、冗余的通讯总线及电源系统、打印机等配置而成。DCS系统要求留有上位机接口,以便实现全厂管控一体化。DCS的功能及各项技术指标应能满足本工程的要求,实现对机-炉的启动,停机,运行监视控制和管理等功能以及热电站安全联锁、紧急停车的控制。 (1)DCS系统的功能
1)数据采集和处理系统(DAS); 2)闭环控制系统(CCS); 3)顺序控制系统(SCS); 4)燃烧器管理系统(BMS);
5)GPS同步时钟由DCS厂家协调解决; 6)烟气连续监测装置。 (2)主要控制回路
1)为确保锅炉安全运行,克服假液位现象,设汽包液位三冲量调节。
2)为确保机组安全运行,设过热蒸汽温度调节。 (3)复杂控制系统 1)给水调节系统
锅炉中主要的复杂控制系统就是给水调节系统,一般由汽包液位、给水流量和蒸汽流量组成的三冲量串级调节系统来调节给水阀。汽包水位信号经汽包压力补偿后作为主调输入,蒸汽流量信号经温度、压力修正后,与给水流量信号一起作为副调的反馈输入。给水流量为加入喷水流量信号后的总给水流量。
2)主蒸汽温度调节系统
主蒸汽温度主要靠喷水进行调节,主蒸汽温度测量值作为主调的反馈输入值,与主汽温度设定值进行PID运算后送入副调。在副调中与减温器出口汽温进行调节运算,其结果经限幅后输出至执行机构,调节喷水减温的调节阀。由于主汽流量变化时,喷水量应相应地发生变化,故在主汽温度调节系统中,把主汽流量信号以前馈形式引入调节系统中。同时因主蒸汽温度与烟气温度及烟气流速有关,所以在调节主蒸汽温度时,也应考虑燃烧工况。
2、仪表选型
仪表选型以先进、安全、可靠、适用为原则。一般为智能型,采用HART通讯协议。变送器、特殊控制阀、分析仪采用近几年国内使用成熟的合资引进系列产品。
精度等级:一般为1.0、1.5级;用于计量为0.2、0.5级;变送器不低于0.075级;热电阻为A级;热电偶为Ⅰ级。
防护等级:所有现场仪表为全天候型,防护等级一般为IP65;特殊为IP68。
防爆要求:根据防爆区域的划分部分区域为防爆界区,故这些场所的现场仪表选型均为隔爆型,防爆等级不低于dⅡCT4。非防爆区和公用工程现场仪表按非防爆型考虑选型。
防冻要求:考虑当地气候条件,对易冻介质的现场仪表采取了保温、防冻措施,并应符合《仪表及管线伴热和绝热保温设计规定》HG/T20514-2000中有关规定。伴热保温采用低压蒸汽,可就近由工艺低压蒸汽管网上接取。
仪表选型具体如下: 1)温度测量
就地指示采用万向型双金属温度计,刻度盘直径一般为Φ100;需要集中检测的工艺参数的温度传感器采用国际统一标准的铠装热电偶(分度号为S或K)和铠装热电阻(分度号为Pt100)。
温度传感器保护管材质根据工艺介质的特性选取,一般采用304不锈钢的保护管。在工艺管道上安装的温度传感器,连接形式为螺纹式或法兰式。在设备上安装的温度传感器,连接形式一般为法兰式。测温传感器根据工况带温度计套管。
2)压力(差压)测量
集中测量时,一般采用智能型压力(差压)变送器,粘堵、结晶、腐蚀性介质的测量采用智能型隔膜压力(差压)变送器,可用手持编程器对其进行现场参数调整;就地测量时,根据不同的工艺介质工况,分别采用普通压力表、真空压力表、隔膜压力表、防腐压力表等;机泵出口采用耐振压力表。压力表刻度盘直径一般为100mm。
3)流量测量
对于一般介质和低压、低温蒸汽采用智能型涡街流量计;对腐蚀性或易堵的导电介质采用智能型电磁流量计,衬里一般为PTFE,电极根据不同介质选用不同材质;管道内径小于50mm的流量测量,一般采用金属转子流量计;高压介质采用透镜垫式高压孔板;高温蒸汽采用标准喷嘴;需经济核算或计量精度要求高的介质采用智能型质量流量计。
4)液位测量
对一般性工艺介质,选用智能型差压变送器、静压式液位计或磁翻板式液位计。对腐蚀性介质和特殊工况选用超声波或雷达式液位计或隔膜密封式智能型差压变送器。对料位采用电容式料位计。
5)分析仪表
根据各装置不同工艺要求,分别采用磁压式氧分析仪、热导式氢分析仪、红外线分析仪;锅炉燃烧系统氧量分析采用氧化锆分析仪;水质分析采用PH计和工业电导仪;对于含有可燃气体和有毒气体场所采用可燃气体和有毒气体检测报警仪。
6)执行机构
本工程一般采用气动执行机构,并附智能型电-气阀门定位器。根据不同介质和工况,分别选用单座阀、双座阀、球阀、套筒阀、蝶阀、开关阀等控制阀,并对阀门内件材质作了相应考虑。控制阀阀体材质不低于工艺管道的材料等级。控制阀一般为法兰连接,法兰等级和连接面与工艺管道规格相匹配。阀芯的流量特性根据控制对象不同分别为线性、等百分比或快开。开关阀的执行机构一般为气动弹簧复位型,并带阀位开关(可在DCS中显示阀的开或关状态)和电磁阀。锅炉房采用电动执行机构。
3、仪表的供电和供气
1.仪表的供电
控制室仪表电源负荷等级按特殊供电要求负荷考虑,为 220VAC±5%,50±0.5 Hz的交流电源。其电源由电气专业提供两路自动切换的独立供电回路,分别取自不同的电气低压母线段。
DCS采用不间断电源(UPS)供电,UPS电源输出质量要求应符合《仪表供电设计规定》HG/T20509-2000中有关规定。备用时间不少于30分钟。
2.仪表的供气
仪表用压缩空气由空压站引来。仪表供气应为连续的,当供气气源发生故障时,贮气罐应能持续供气15分钟以上。压力及质量要求应符合《仪表供气设计规定》HG/T20510-2000中有关规定。
(九)、乙方投标报价范围
1、硬件部分:提供三废锅炉装置所指定设备(从原料料仓入口到锅炉空预器出口所有设备、管道;成套DCS控制)。
1.1三废锅炉装置系统所供主体设备:包括燃烧炉、组合式除尘器、蒸汽过热器、余热锅炉、省煤器、空气预热器、风机、给煤除渣设备等;
1.2上煤系统的设备:皮带机、料仓、螺旋给煤机、除铁器。 1.3出渣系统的设备:冷渣机、刮板机。
1.4点火装置:锅炉燃煤采用床上点火,燃吹风气及其他尾气自动点火装置(再不燃煤的情况下启用);
1.5乙方负责界区内设备所有砌筑保温防腐(含内外保温并带保温材料)。
1.7鼓引风设备:一次风机、二次风机、引风机。
1.9吹风气、驰放气以水封入口做为界区分界线;水封入口以外部分管线由甲方设计制作安装。
1.11汽水系统:自锅炉给水自动调节阀前截止阀(含截止阀及配对法兰和连接件)至蒸汽过热器出口自动调节阀后截止阀(含截止阀及配对法兰和连接件)止之间的所有管道和各种阀门。
1.12造气吹风气配风系统的油压座板阀的油压控制系统的设计及安装由甲方负责。
1.13 DCS系统控制的设计安装由乙方负责。
1.14乙方只提供混燃炉、组合式除尘器、余热锅炉、静电除尘器、脱硫器、风机烟囱等界区内设备的基础条件图。土建的设计施工由甲方负责。
2、软件部分:提供成套三废混燃锅炉装置的工艺软件包 2.1管道及仪表流程图 2.2设备平立面布置图
2.3定型设备的样本、非标设备的装配图并明确其各项设计参数 2.4设备的管口方位图 2.5工艺设备一览表 2.6工艺管道安装材料一览表 2.7 成套DCS设计
2.8一次仪表清单及配套电气负荷表 2.9设备基础条件图
2.10烟风管道布置配管图
2.11工艺操作规程、开停车方案、烘炉方案 2.12设备和管道的外保温一览表 2.13输灰系统的工艺参数条件
2.14三废锅炉原料加工及输送系统的工艺参数条件
(十)、三废混燃炉设计性能验收标准
装置性能设计验收的具体内容:
1、性能验收的目的:是为了检验设备的所有性能是否符合设计的要求。
2、性能验收的地点:甲方生产现场。
3、性能验收时间:(冷热态)三废炉系统在通过冷态实验和72小时试运行合格后的1个月内由甲乙双方共同确认。
4、性能验收方式:甲乙双方共同进行各项性能验收,性能验收所需测点由乙方提供,甲方配合。
5、性能验收的项目和合格的标准及检测方法:
(1)、锅炉出力及参数:连续出力50t/h、主汽压力3.82MPa、主汽温度435℃ ——在线仪表检测,年运行时间不少于8000小时。 (2)、锅炉的热效率:83%。
(3)、锅炉汽水品质:GB12145-99《火力发电机组及蒸气动力设备水汽质量标准》——在线仪表检测、取样仪器分析及计算。 (4)、炉墙散热及炉本体密封性能:炉正常运行条件下,环境温度为25℃时,炉体外表面设计温度不超过55℃,散热量不超过290W/m2——在线仪表检测。外观无水、气、汽、灰、粉等泄漏。 (5)、排烟温度≤150℃。
(6)、炉渣含碳量:≤2%——取样仪器分析及计算。
(7)、锅炉连续排污率:≤2%——在线仪表检测。
(8)、点火排汽门和汽包、过热器安全门排汽能力:《蒸汽锅炉安全技术监察规定》——在线仪表检测与人工调试。
6、性能验收试验结果的确认。
性能验收试验报告由甲方组织编写,乙方参加,供需双方共同签章确认结论。
(十一)、技术服务及优惠条件
1、乙方接到甲方通知后3天之内,乙方派技术人员到甲方现场对系统全套设备制作、安装、调试进行现场技术指导。
2、乙方对甲方负责采购的设备、材料的订货提供技术指导。
3、乙方为甲方操作人员培训提供技术指导并协助联系培训单位,费用甲方自理。
4、乙方提供工艺指标和操作规程;制定开停车方案,负责烘炉开车指导工作(锅炉本体部分的煮炉开车除外)。
5、乙方对锅炉等附属设备招标提供参数负责技术把关。
6、甲方三废炉系统性能验收合格后,乙方免费向甲方提供技术服务2年。在该服务期限内乙方接到甲方通知(可电话通知)后3天内派技术人员到达甲方现场进行服务。
21
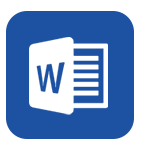