目
录
一.序言 ……………………………………………………3 二.夹具的概述………………………………………………3 2.1夹具的现状及生产对其提出新的要求 2.2现代夹具的发展方向 2.3机床夹具及其功用
2.4机床夹具在机械加工中的作用 2.5机床夹具组成和分类 2.6机床夹具的分类
三.零件的分析………………………………………………7 3.1零件的工艺分析
四.工艺规程设计 …………………………………………7 4.1确定毛坯的制造形式
4.2基面的选择 4.3制定工艺路线
4.4机械加工余量、工序尺寸及毛坯尺寸的确定 4.5确定切削用量及基本工时
五.夹具设计 ………………………………………………19 5.1定位基准的选择 5.2定位误差分析 5.3切削力及夹紧力计算
1 1 课设小结………………………………………………………22 参考文献………………………………………………………22
一、序 言
课程设计在我们学习了大学的大部分基础课、技术基础课之后进行的,这是我们在进行课程设计对所学各课程的深入综合性的总复习,也是一次理论联系实际的训练,因此,它在我们的大学生活中占有重要的地位。另外在做完这次课程设计之后,我在想我能在下面几方面得到锻炼:
(1)运用机械制造工艺学课程中的基本理论以及在生产实习中学到的实践知识,正确地解决一个零件在加工中的定位,夹紧以及工艺路线安排,工艺尺寸确定等问题,保证零件的加工质量。
(2)提高结构设计能力。通过设计夹具的训练,获得根据被加工零件的加工要求,设计出高效,省力,经济合理而能保证加工质量的夹具的能力。
(3)学会使用手册以及图表资料。掌握与本设计有关的各种资料的名称,出处,能够做到熟练的运用。
就我个人而言,我希望在这次课程设计中锻炼自己发现问题、分析问题和解决问题的能力。由于个人能力有限,设计尚有许多不足之处,恳请各位老师给予指教,本人将表示真诚的感谢!
二、机床夹具概述
2.1夹具的现状及生产对其提出新的要求
现代生产要求企业制造的产品品种经常更新换代,以适应市场激烈竞争,尽管国际生产研究协会的统计表明中不批,多品种生产的工件已占工件种类数的85%左右。然而目前,一般企业习惯与采用传统的专用夹具,在一个具有只能感等生产的能力工厂中约拥有13000~15000套专用夹具。另一方面,在多品种生产的企业中,约隔4年就要更新80%左右的专用夹具,而夹具的实际磨损量只有15%左右,特别
3 3 最近年来柔性制造系统(FMS)、数控机床(NC),加工中心(MC)和成组加工(GT)等新技术被应用和推广,使中小批生产的生产率逐步趋近于大批量生产的水平。
综上所述,现代生产对夹具提出了如下新的要求; (1)、能迅速方便地装备新产品的投产以缩短生产准备周期; (2)、能装夹一组相似性特征的工件; (3)、适用于精密加工的高精度的机床; (4)、适用于各种现代化制造技术的新型技术;
(5)、采用液压汞站等为动力源的高效夹紧装置,进一步提高劳动生产率。 2.2现代夹具的发展方向
现代夹具的发展方向表现为精密化、高效化、柔性化、标准化等四个方面: 2.3机床夹具及其功用 2.3.1机床夹具
夹具是一种装夹工件的一种工艺装备,它广泛地应用于机械制造过程的切削加工,热处理装配,焊接和检测等工艺过程中。机床夹具设计是一项重要的技术工件。
2.3.2机床夹具的功能
在机床上应用夹具装夹工件时,其主要功能是使工件定位和夹紧。 1.机床夹具的主要功能
机床夹具的主要功能是装夹工件,使工件装夹中的定位和夹紧。 (1)、定位
确定工件在夹具中占有正确的位置的过程,定位是通过工件定位基准而与夹具定位元件的定位面接触成配合实现的正的定位可以保证加工面的尺寸和位置的精度要求。 (2).夹紧
工件定位后将其固定,使其在加工过程中保持定位位置不错的操作。由于工件
4 4 在加工时,受到各种力的作用若不将其固定,则工件会松动、脱离,因此夹紧为工件提高了安全和可靠的加工条件。 2.机床夹具的特殊功能
机床夹具的特殊功能主要是对刀与导向。 1)、对刀
调整刀具切削相对工件或夹具的正确位置如铣床夹具中饿对刀块,它能迅速地确定铣刀相对于夹具的正确位置。 2)、导向
如铣床夹具中的钻模板与钻套,能迅速的确定钻头的位置,并引导其进行钻削,导向元件制成模板形成故钻床夹具长称为钻模、镗床夹具(镗模)也是具有导向的功能的。
2.4机床夹具在机械加工中的作用
在机械加工中,使用机床夹具的目的主要有一些六个方面,然而在不同的生产条件下,应该有不同的侧重点。夹具设计时应该综合考虑加工的技术要求,生产成本个工人操作方面的要求以达到预期的效果。
(1)、保证加工精度 (2)、提高劳动生产率 (3)、改善工人的劳动条件 (4)、保证工艺纪律 (5)、降低生产成本 (6)、扩大机床工艺范围
这是生产条件有限的企业中常用的一种技术改造措施,如车床上的拉削,钻孔加工等,也可用夹具装夹的加工较复杂的成型面。 2.5机床夹具组成和分类
5 5 (1)、系统元件
(2)、夹紧元件
(3)、夹具体
(4)、连接元件
(5)、对刀与导向装置
(6)、其他元件或装置 一.机床夹具的基本组成部分
虽然各类机床夹具的结构有所不同但按主要功能加以分析。机床夹具的基本组成部分是定位元件,夹紧装置和夹具体三个部分,这也好似夹具体的主要内容。 1.定位元件
定位元件是夹具的主要功能元件之一 ,通常当工件定位基准面的形状确定后,定位元件的结构也就确定了。
2.夹紧装置也是夹具的主要元件之一,一般铰链压板、螺钉、夹紧装置等。 3.夹具体
通常夹具作为铸件的结构、锻件结构、焊接结构,形状有回转体形和底座等多种定位元件,夹紧装置等分布在夹具体不同的位置上。
二、夹具的其他组成部分
为满足夹具的饿其他功能要求,各种夹具好要设计其他的元件个装置。 1.连接元件
根据机床的工作特点,夹具在机床上的安装。
连接常有的两种方式:一种是安装在机床工作台上,另一种是安装在机床主轴上,连接元件用于确定夹具本身在机床上的位置。 2.对刀与导向装置
对刀装置常见在铣床夹具中,用以对刀块调铣刀对刀前的位置,对刀时,铣刀不能与对刀块直接相连,以免碰伤铣刀的切削刃和对刀块工作表面。
6 6 导向装置钻模板、钻套、镗模的镗模支架。镗套,它们能确定刀具的位置,并引导刀具进行切削。 3.其他元件和装置
根据加工的需要,有些夹具分别采用分度装夹,靠模装置上下料加工工艺机器人等。
2.6机床夹具的分类
1、按夹具的通用特性分类
这是一种基本的分类方法,主要反应夹具在不同生产类型中的通用特性,故也是选择夹具主要依据。目前,我国常用的夹具有通用夹具、专用夹具和自动化生产夹具等五大类。
2、按夹具使用的机床分类
这是专用夹具设计使用的分类方法,如车床、铣床、刨床、钻床、数控车床等夹具。设计专用夹具时机床的类别、组别、型别主要参数均以确定。它们不同点是机床切削成型运动不同、故夹具与机床的连接方式不同它们的加工精度要求也各不相同。
三、零件的分析
3.1零件的工艺分析
零件下方的Φ25mm的孔与操作机构相连,上方的Ф55mm的半孔则是用于与所控制齿轮所在的轴接触,通过上方的力拨动下方的齿轮变速,两零件铸造为一体,加工时分开。
四、工艺规程设计
4.1确定毛坯的制造形式
根据《机械制造工艺设计简明手册》(机械工业出版出版社、哈尔滨工业大学李益民主编) 零件材料为HT200,考虑零件在机床运行过程中所受冲击不大,零件结构又比较简单,故选择铸件毛坯。
4.2基面的选择
7 7
基面的选择是工艺规程设计中的重要工作之一。基面选择的正确与合理,可以使加工质量得到保证,生产率得以提高。否则,加工工艺过程中会问题百出,甚至还会造成零件大批报废,使生产无法正常进行。 (1)粗基准的选择。
以零件的小头上端面为主要的定位粗基准,以两个小头孔外圆表面为辅助粗基准。
(2)精基准的选择。
考虑要保证零件的加工精度和装夹准确方便,一句“基准重合”和“基准统一”原则,以粗加工后的地面为主要的定位精基准,以两个小头孔外圆柱表面为辅助的定位精基准。
4.3制定工艺路线
制定工艺路线的出发点,应当是使零件的几何形状、尺寸精度及位置精度等级等技术要求能得到合理的保证。在生产纲领已确定为大批生产的情况下,可以考虑采用万能性机床配以专用夹具,并尽量使工序集中来提高生产率。除此之外,还应当考虑经济效果,以便使生产成本尽量下降。
工艺路线方案一:
工序Ⅰ: 钻、扩、粗铰、精铰Φ25孔。以Φ40外圆和其端面为基准,选用Z5120A立式钻床加专用夹具。
工序Ⅱ:铣φ55的叉口及上、下端面。利用Φ25的孔定位,以两个面作为基准,选用X5020A立式铣床和专用夹具。
0.4工序Ⅲ:粗、精铣550的叉口的内圆面。利用Φ25的孔定位,以两个面作为基准,选用X5020A立式铣床和专用夹具。
工序Ⅳ:粗铣35×3的上表面。以Φ25的孔和Φ55的叉口定位,选用X5020A立式铣床加专用夹具。
工序Ⅴ:精铣35×3的上表面。以Φ25的孔和Φ55的叉口定位,选用X5020A
8 8 立式铣床加专用夹具。
工序Ⅵ:粗铣40×16的槽,以Φ25的孔定位,选用X5020A立式铣床加专用夹具。
工序Ⅶ:切断φ55的叉口,用宽为4的切断刀,选用X5020A立式铣床加专用夹具。
工序Ⅷ 检验。 工艺路线方案二:
工序Ⅰ:切断φ55叉口,用宽为4的切断刀,选用X5020A立式铣床加专用夹具。
工序Ⅱ:铣φ55的叉口及上、下端面。利用Φ25的孔定位,以两个面作为基准,选用X5020A立式铣床和专用夹具。
0.4工序Ⅲ:粗、精铣550的叉口的内圆面。利用Φ25的孔定位,以两个面作为基准,选用X5020A立式铣床和专用夹具。
工序Ⅳ:粗铣35×3的上表面。以Φ25的孔和Φ55的叉口定位,选用X5020A立式铣床加专用夹具。
工序Ⅴ:精铣35×3的上表面。以Φ25的孔和Φ55的叉口定位,选用X5020A立式铣床加专用夹具。
工序Ⅵ:粗铣40×16的槽,以Φ25的孔定位,选用X5020A立式铣床加专用夹具。
工序Ⅶ:钻、扩、粗铰、精铰Φ25孔。以Φ40外圆和其端面为基准,选用Z5120A立式钻床加专用夹具。
工序Ⅷ 检验。
以上工艺过程详见附表1“机械加工工艺卡片”。
以上加工方案大致看来是合理的,但通过仔细考虑零件的技术要求以及可能采取的加工手段之后,就会发现仍有问题,主要表现在φ25的孔及其16的槽和φ55的端面加工要求上,以上三者之间具有位置精度要求。为了避免造成一定的
9 9 加工误差;通过分析可以比较工艺路线方案一最为合理。 具体方案如下:
工序Ⅰ: 钻、扩、粗铰、精铰Φ25孔。以Φ40外圆和其端面为基准,选用Z5120A立式钻床加专用夹具。
工序Ⅱ:铣φ55的叉口及上、下端面。利用Φ25的孔定位,以两个面作为基准,选用X5020A立式铣床和专用夹具。
0.4工序Ⅲ:粗、精铣550的叉口的内圆面。利用Φ25的孔定位,以两个面作为基准,选用X5020A立式铣床和专用夹具。
工序Ⅳ:粗铣35×3的上表面。以Φ25的孔和Φ55的叉口定位,选用X5020A立式铣床加专用夹具。
工序Ⅴ:精铣35×3的上表面。以Φ25的孔和Φ55的叉口定位,选用X5020A立式铣床加专用夹具。
工序Ⅵ:粗铣40×16的槽,以Φ25的孔定位,选用X5020A立式铣床加专用夹具。
工序Ⅶ:切断φ55的叉口,用宽为4的切断刀,选用X5020A立式铣床加专用夹具。
工序Ⅷ 检验。
4.4机械加工余量、工序尺寸及毛坯尺寸的确定
零件材料为HT200,硬度170~220HBS,毛坯重量约1.12kg。根据《机械加工工艺师手册》(以下简称《工艺手册》)知生产类型为大批生产,采用金属模铸造毛坯。
根据上述原始资料及加工工艺,分别确定各加工表面的机械加工余量、工序尺寸及毛坯尺寸如下:
1、毛坯余量及尺寸的确定
毛坯余量及尺寸的确定主要是为了设计毛坯图样,从而为工件毛坯的制造作准备,该工序在这里不做详细说明,主要说明一下毛坯尺寸及相应公差的确定,以
10 10 便毛坯制造者参考。根据《工艺手册》,结合加工表面的精度要求和工厂实际,要合理地处理好毛坯余量同机械加工工序余量之间的不足。
(1)粗铣φ55的叉口的上、下端面的加工余量及公差。
该端面的表面粗糙度为3.2,所以先粗铣再精铣。查《机械加工余量手册》(以下简称《余量手册》)中的表4-2成批和大量生产铸件的尺寸公差等级,查得铸件尺寸公等级CT分为7~9级,选用8级。MA为F。再查表4-2查得加工余量为2.0 mm。由《工艺手册》表2.2-1至表2.2-4和《机械制造工艺与机床夹具》中表1-15及工厂实际可得:Z=2.0mm,公差值为T=1.6mm。 (2)加工35×3的上表面的加工余量及公差。 同上方法得:2Z=4.0,公差值为1.3 mm。 (3)铣40×16的槽的上表面的加工余量及公差。 同上方法得:2Z=4.0,公差值为1.6 mm。
2、各加工表面的机械加工余量,工序尺寸及毛坏尺寸的确定 (1) 钻φ25的孔加工余量及公差。
毛坯为实心,不冲出孔。该孔的精度要求在IT7~IT9之间,参照《工艺手册》表2.3-9~表2.3-12确定工序尺寸及余量为:
查《工艺手册》表2.2-5,成批和大量生产铸件的尺寸公差等级,查得铸件尺寸公等级CT分为7~9级,选用8级。MA为F。公差值T=0.12 mm, 钻孔φ23mm 扩孔φ24.8 mm
2Z=1.8 mm 铰孔φ25 mm
2Z=0.2 mm
由于本设计规定的零件为大批量生产,应该采用调整法加工,因此在计算最大、最小加工余量时,应按调整法加工方式予以确定。
(2)铣φ55的叉口及上、下端面
11 11 因为叉口的粗糙度为3.2,所以粗铣再精铣。参照《工艺手册》表2.3-9~表2.3-12确定工序尺寸及余量为:
查《工艺手册》表2.2-5,成批和大量生产铸件的尺寸公差等级,查得铸件尺寸公等级CT分为7~9级,选用8级。MA为F。公差值T=1.4 mm 粗铣φ55的叉口及上、下端面余量1.0 mm。
2Z=2.0 精铣φ55的叉口及上、下端面。
2Z=2.0 (3)粗铣35×3的上端面
因为该面的粗糙度为6.3,所以粗铣一次即可。参照《工艺手册》表2.3-9~表2.3-12确定工序尺寸及余量为:
查《工艺手册》表2.2-5,成批和大量生产铸件的尺寸公差等级,查得铸件尺寸公等级CT分为7~9级,选用8级。MA为F。公差值T=1.3mm 粗铣35×3的上端面
2z=2.0 (4)粗铣40×16的上表面
此面的粗糙度要求为3.2,所以分粗精加工即可。参照《工艺手册》表2.3-9~表2.3-12确定工序尺寸及余量为:
查《工艺手册》表2.2-5,成批和大量生产铸件的尺寸公差等级,查得铸件尺寸公等级CT分为7~9级,选用8级。MA为F。公差值T=1.6mm,其偏差±0.7 粗铣40×16的上表面
2Z=2.0 (5)铣40×16的槽
此面的粗糙度要求为3.2,所以粗铣再精铣。参照《工艺手册》表2.3-9~表2.3-12确定工序尺寸及余量为:
查《工艺手册》表2.2-5,成批和大量生产铸件的尺寸公差等级,查得铸件尺寸公等级CT分为7~9级,选用8级。MA为F。公差值T= 1.6mm 。 粗铣40×16的槽
2Z=2.0 精铣40×16的槽
2Z=2.0
12 12 (6)切断φ55叉口
4.5确定切削用量及基本工时
工序Ⅰ: 钻、扩、粗铰、精铰Φ25孔。 1.加工条件
工件材料:灰铸铁HT200 加工要求:钻Φ25的孔,其表面粗糙度值为Rz=1.6 μm;先钻Φ23的孔在扩Φ24.8的孔,再粗铰Φ24.94孔,再精铰Φ25孔。 机床:Z5125A立式钻床。
刀具:Φ23麻花钻,Φ24.8的扩刀,铰刀。 2.计算切削用量 (1)钻Φ23的孔。 ①进给量
查《机械制造工艺与机床夹具课程设计指导》P47表2-23钻孔进给量f为0.39~0.47 mm/r,由于零件在加工23mm孔时属于低刚度零件,故进给量应乘系数0.75,则f=(0.39~0.47)×0.75=0.29~0.35mm/r,查表得出,现取f=0.25mm/r。此工序采用Φ23的麻花钻。
所以进给量f= 0.25mm/z ② 钻削速度
切削速度:根据手册表2.13及表2.14,查得切削速度V=18m/min。
1000v100018ns249.24(r/min)dw23 根据手册nw=300r/min,故切削速度为
dwnw23300V21.67(m/min)
10001000③ 切削工时 l=23mm,l1=13.2mm.查《工艺手册》P9-143表9.4-31,切削工时计算公式:
13 13 tm1ll1l2802313.21.55(min)nwf3000.25
① 扩孔的进给量
查《切削用量手册》表2.10规定,查得扩孔钻扩Φ24.8的孔时的进给量,并根据机床规格选取
F=0.3 mm/z ②切削速度 扩孔钻扩孔的切削速度,根据《工艺手册》表28-2确定为
V=0.4V 钻
其中V 钻为用钻头钻同样尺寸的实心孔时的切削速度.故
V=0.4×21.67=8.668m/min 1000v10008.668ns111.3(r/min)dw24.8 按机床选取nw=195r/min.③切削工时
切削工时时切入L1=1.8mm,切出L2=1.5mm tm1ll1l2801.81.51.4(min)nwf1950.3
① 粗铰孔时的进给量
根据有关资料介绍,铰孔时的进给量和切削速度约为钻孔时的1/2~1/3,故
F=1/3f钻=1/3×0.3=0.1mm/r V=1/3V钻=1/3×21.67=7.22m/min 1000v10007.22ns92.2(r/min)dw24.94
②切削速度
按机床选取nw=195r/min,所以实际切削速度
Vdwnw100024.94195100015.27(m/min)
14 14 ③切削工时
切削工时,切入l2=0.14mm,切出l1=1.5mm.tm1ll1l2800.141.54.18(min)nwf1950.1
① 精铰孔时的进给量
根据有关资料介绍,铰孔时的进给量和切削速度约为钻孔时的1/2~1/3,故
F=1/3f钻=1/3×0.3=0.1mm/r V=1/3V钻=1/3×21.67=7.22m/min
1000v10007.22ns91.975(r/min)dw25
②切削速度
按机床选取nw=195r/min,所以实际切削速度 dwnw25195V15.3(m/min)
10001000③切削工时
切削工时,切入l2=0.06mm,切出l1=0mm.tm1ll1l2800.0604.1(min)nwf1950.1
工序Ⅱ:铣φ55的叉口的上、下端面。 ① 进给量
采用端铣刀,齿数4,每齿进给量af=0.15mm/z(《机械制造工艺与机床夹具课程设计指导》。 故进给量f=0.6mm ②铣削速度:
cvdoqvvmxvyvuvpvkv(m/min)
(表9.4-8) Tapafawz由《数控加工工艺》中第五章表5-6得切削速度为9~18m/min 根据实际情况查表得V=15 m/min
15 15 ③切削工时
引入l=2mm,引出l1=2mm,l3=75mm。
查《工艺手册》P9-143表9.4-31,切削工时计算公式:
tm1ll1l31nwf22758.7(min)150.6
工序Ⅲ铣φ55的叉口 ①进给量
由《工艺手册》表3.1-29查得采用硬质合金立铣刀,齿数为5个,由《数控加工工艺》中第五章表5-5得硬质合金立铣刀每齿进给量f为0.15~0.30,由手册得f取0.15mm/z
故进给量f=0.75 mm/z.
②铣削速度:
由《数控加工工艺》中第五章表5-6得硬质合金立铣刀切削速度为45~90mm/min, 由手册得V取70mm/min.③切削工时
引入l=2mm,引出l1=2mm,l3=75mm。
查《工艺手册》P9-143表9.4-31,切削工时计算公式:
tm1
lll13nwf22757.5(min)700.15
工序Ⅳ:铣35×3的上端面。 ① 进给量
采用端铣刀,齿数4,每齿进给量af=0.15mm/z(《机械制造工艺与机床夹具课程设计指导》。 故进给量f=0.6mm ②铣削速度:
16 16
cvdoqvvmxvyvuvpvkv(m/min)
(表9.4-8) Tapafawz由《数控加工工艺》中第五章表5-6得切削速度为9~18m/min 根据实际情况查表得V=15 m/min ③切削工时
切入l=3mm,行程l1=35。
查《工艺手册》P9-143表9.4-31,切削工时计算公式:
tm1llnwf13354.2(min)150.6
工序Ⅴ:铣40×16槽的表面。 ① 进给量
该槽面可用变速钢三面刃铣刀加工,由前定余量为2mm故可一次铣出,铣刀规格为φ32,齿数为8。由《工艺手册》表2.4-73,取每齿进给量为0.15mm/z,ap=2mm故总的进给量为f=0.15×8=1.2 mm/z。
②切削速度
由《工艺手册》表3.1-74,取主轴转速为190r/min。则相应的切削速度为:
Dn 32190v19.1(m/min)10001000
③切削工时
切入l=2mm切出l1=2mm,行程量l3=40mm。
查《工艺手册》P9-143表9.4-31,切削工时计算公式:
tm1lll23nwf22401.92(min)19.11.2
工序Ⅵ铣40×16的槽。 进给量
.121600的槽可用高速钢三面刃铣刀加工,铣刀规格为φ16,齿数为10。由《机械加工工艺师手册》表21-5,取每齿进给量为0.15mm/z,ap=2mm,故总的进给量为
17 17 f=0.15×10=1.5 mm/z。 ②切削速度
由《工艺手册》表3.1-74,取主轴转速为190r/min。则相应的切削速度为:
Dn16 190v9.55(m/min)10001000
③切削工时
切入l=2mm,切出l1=2mm行程量l2=40mm。
查《工艺手册》P9-143表9.4-31,切削工时计算公式:
tm1+lll12nwf22403.0(min)9.551.5
工序Ⅶ:切断φ55叉口。 ① 进给量
采用切断刀,齿数4,每齿进给量af=0.15mm/z(《机械制造工艺与机床夹具课程设计指导》。 故进给量f=0.6mm ②铣削速度:
cvdoqvvmxvyvuvpvkv(m/min)
(表9.4-8) Tapafawz由《数控加工工艺》中第五章表5-6得切削速度为9~18m/min 根据实际情况查表得V=15 m/min ③切削工时
切出l=2mm,切出l1=2mm,行程量=75mm。
查《工艺手册》P9-143表9.4-31,切削工时计算公式:
tm1lll12nwf22758.7(min)150.6
18 18 工序Ⅷ:检验。
五、夹具设计
夹具是一种能够使工件按一定的技术要求准确定位和牢固夹紧的工艺装备,它广泛地运用于机械加工,检测和装配等整个工艺过程中。在现代化的机械和仪器的制造业中,提高加工精度和生产率,降低制造成本,一直都是生产厂家所追求的目标。正确地设计并合理的使用夹具,是保证加工质量和提高生产率,从而降低生产成本的重要技术环节之一。同时也扩大各种机床使用范围必不可少重要手段。
(一)设计思想
设计必须保证零件的加工精度,保证夹具的操作方便,夹紧可靠,使用安全,有合理的装卸空间,还要注意机构密封和防尘作用,使设计的夹具完全符合要求。
本夹具主要用来对φ55H7端面进行加工,这个孔尺寸精度要求为H7,表面粗糙度Ra3.2,扩、半精镗、精镗可满足其精度。所以设计时要在满足精度的前提下提高劳动生产效率,降低劳动强度。
(二)夹具设计
1、定位分析
(1)定位基准的选择
据《夹具手册》知定位基准应尽可能与工序基准重合,在同一工件的各道工序中,
0.023应尽量采用同一定位基准进行加工。故加工φ55H7端面时,采用φ250的外圆面和其的下端面作为定位基准。 (2)定位误差的分析
定位元件尺寸及公差的确定。夹具的主要定位元件为V形块与定位块,因为该定位元件的定位基准为孔的轴线,所以基准重合△B=0,由于存在间隙,定位基准会发生相对位置的变化即存在基准位移误差。
△Y=0.707δd=0.707×0.025mm=0.0177mm
2、切削力及夹紧力的计算
19 19
刀具:高速钢细齿圆锯片铣刀 直径do160mm 齿数 Z=50 又由《切削手册》表3.28中的公式:
F
CFapxFfzyFaeuFZdoqFnwF
其中: CF30
xF1.0
yF0.6
5uF0.8
3wF0
qF0.8 3
do160mm
Z=50 ap4mm
ae12mm
fz0.02m5m z/所以 F=63.5N 水平分力:FH1.1F63.51.169.9N
垂直分力;FV0.3F0.363.519.1N
又在计算切削力时,必须把安全系数考虑在内。安全系数KK1K2K3K4 其中 K1为基本安全系数1.5
K2为加工性质系数1.
2K3刀具钝化系数 1.2
K4为切削特点系数(断续切削)1.2 所以 F ′=KFH=69.9x1.5x1.2x1.2x1.2=181.2N 为了克服水平方向的力,实际的夹紧力为
N(f1+f2)= KFH
其中 f1为螺母与螺杆间的摩擦系数
f2为工件与螺杆头(或压板)间的摩擦系数
又查得 f1 和f2为1.6 则
NKFH
f1f2181.2566N
0.160.16又选择的螺旋夹紧机构的基本尺寸如下(根据《机床夹具设计》 第三版表1-2-20、所以 N1-2-
21、1-2-
22、1-2-23查得:
950
6
30
2r′=0
M12mm
p1mm
rz5.67m
a135mtg20.1
5L=120mm Q=30N
20 20 则 可以提供的夹紧力为:
wQL
rtg1rz(a2) 所以w
=12030=3140N
5.675tg(136950)又由《机床夹具设计》 第三版表1-2-24查得 当螺纹的公称直径为12mm时 ,螺栓许用的夹紧力为5690N
由以上的数据可知:所选的螺旋机构提供的夹紧力大于所需的,且满足螺栓的许用夹紧力,故本夹具可以安全工作。 4.2.3 定位误差分析
1)定位元件尺寸及公差的确定 本夹具的定位元件为一圆柱销和一菱形销,其参数由(《机床夹具设计手册》图5-3及其表选 两定位销的尺寸及公差0.023为:φ250(定位销的公差取h8)。
2)零件图样规定
φ25mm的孔的中心线与φ55mm孔的中心线的长度误差为0.2mm,φ25mm孔中的定位销与夹具体的垂直度误差为0.05mm,,此项技术要求应由定位销宽配合中
0.0230.056的侧向间隙保证。已知φ25的宽为φ250mm,定位销为φ250mm(定位销的公差取h8),则 一个定位销与一个孔的定位误差为:
bmax0.021(0.033)/20.027mm
此处引起零件的定位误差为 x0.02720.054mm
故最大侧向间隙能满足零件的精度要求。
(2)计算φ25mm定位销的中心线与夹具体垂直度误差
0.023 定位销的宽度为φ250mm,
夹具体表面的粗糙度Ra1.6um
故 max0.0016(0.033)0.03360.05mm
所以最大垂直度误差能满足零件精度要求
3、夹具操作说明
如前所述,在设计夹具时,首先要考虑到能保证零件的加工精度,其次是要提高劳动生产率。为此,应先考虑所设计的夹具体与零件在夹具上的定位,在本道工序中,由于零件的底面的定位是用的夹具体,所以其表面粗糙度要求应比较高,视为关键面。又本道工序是铣断,其切削力不大,故在设计夹具时应考虑夹具的
21 21 简单及利用常用的一些零件。
夹具上装有对刀块,可以使夹具在一批零件加工之前很好的对刀;同时,夹具体底面上的一对定位键可使整个夹具在机床工作台上有一正确的安装位置,以利于铣削加工。
课程设计小结
通过这次课程,我有了很大的收获学到了很多的东西。本次课程设计是我们在学习了大学的大部分基础课,专业基础课后进行的。这是我们对所学各课进行的一次全面的、深入的、综合性的总复习,也是一次理论联系实际的训练,因此它在我们的四年大学生活中占有积极重要的地位。
就我个人而言,我通过本次课程设计对自己在大学中所学的知识进行一次良好的回顾,并在此基础上有所提高,从而锻炼自己发现问题、思考问题解决问题的能力,并培养认真、严谨的专业精神,为以后能够更好地去适应社会打下了良好的基础。
由于个人的能力有限,设计尚有诸多不足之处恳请老师大力支持,在次不胜感谢。
参考文献
1、杨叔子主编.机械加工工艺师手册.北京:机械工业出版社,2001
2、李益民主编.机械制造工艺设计简明手册.北京:机械工业出版社,1994
3、孙本绪、熊万武编.机械加工余量手册.北京:国防工业出版社,1999
4、机床夹具设计手册.北京:中国科学技术出版社
5、赵家齐主编.机械制造工艺学课程设计指导书.北京.机械工业出版社,2000
6、刘守勇主编.机械制造工业与机床夹具.北京:机械工业出版社,2000
7、田春霞主编.数控加工工艺.北京:机械工业出版社,2006
8、吴拓、方琼珊主编.机械制造工艺与机床夹具课程设计指导书.北京:机械工业出版社,2005
9、黄云清主编.公差配合与测量技术.北京:机械工业出版社,2001
22 22
23
附表1 机械加工工艺过程综合卡片
24
机械制造工艺学课程设计CA6140车床拨叉(831007)工艺规程及钻φ22的钻床夹具(全套图纸)
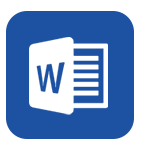