φ10.8m直径钢筋砼圆筒施工技术
摘要:介绍钢筋砼圆筒预制工艺
关键词:圆筒 钢筋 模板 砼 施工
1.概述
青岛北海船厂三十万吨级修船码头工程位于青岛市海西湾倒观咀附近。该码头工程为北海船厂二期“双加”技改项目的主体工程,属青岛市重点项目。码头前沿总长660m,结构型式为重力式座床式圆筒型式。圆筒直径10.8m,高11.0m,壁厚28cm,无底板,设前趾和内趾。顶部临海侧局部加强。
圆筒预制场设在现场新近回填场地上。回填料为开山石,大块石护坡。考虑圆筒安装时为500t起重船直接吊安,只沿海侧单排布置。 2.施工工艺选择
2.1受施工工期及期间气候影响,根据已有的施工经验,整个圆筒分两层施工,即钢筋分两次施工,砼分两次浇筑。模板考虑大片结构,根据设备起重能力,模板分四节:第一层两节高分别为2.1m、3.0m,第二层两节高分别为3.1m、3.0m。模板每节分四片。
2.2施工设备
主要施工设备为行走式塔式起重机,起重能力100t m。一座25m3/h强制式搅拌站,带两台配料机、称量斗及水泥罐,一台HBT60拖式砼输送泵,一台厦工ZL50装载机。 3.钢筋工程
圆筒配筋种类不多,分为三类:前趾和内趾的弯起钢筋,竖向受力筋,环向受力筋。弯起筋下料与加工在钢筋加工厂进行,并分类放置。竖向钢筋根据施工分段长度在加工厂下料,环向钢筋在加工厂对焊接长至设计尺寸前趾及内趾钢筋,竖向钢筋绑扎均为常规施工,主要施工难点在环向筋成型与绑扎以及竖向筋位置固定。
3.1第一层钢筋绑扎
待底胎模施工完毕且达到一定强度后,即铺设隔离层。隔离层分三层:粉细砂5mm左右厚,塑料编织布一层,油毡原纸一层。在油毡原纸上画好前趾及内趾钢筋位置记号。由于趾的弯起筋为封闭的,且内套有环向钢筋,因此只能先放好1/3的内趾钢筋,再将环向筋套进内趾筋内。相对固定好环筋与内趾筋,然后再套其余趾部弯起筋。最后将趾部钢筋和趾内环向筋相互绑扎起来并加固形成底部骨架。
趾部钢筋架立完毕,将钢筋绑扎架立于内趾钢筋上。钢筋绑扎架的上下端各沿环向伸出16根钢管,通过圆心在钢管上标刻内环和外环筋的位置,并且固定内外环向筋各一道。环向筋Ф18以下可以直接在上面环绕成型后绑扎。上下环向筋定位后先将内侧所有环向筋围绕在钢筋绑扎架上,然后将内侧立筋全部就位于已固定的上下环向筋上。内侧立筋和水平环向筋绑扎完毕开始固定外侧立筋,再将外侧环向筋直接往已绑扎固定的立筋上环绕绑扎。
3.2第二层钢筋绑扎
第一层砼模板拆除后,便为第二层钢筋绑扎做好准备工作。将三角支撑牛腿用螺栓固定在预埋在砼里的圆台螺母上,将钢筋绑扎支架吊放在牛腿上。同时沿圆筒外侧搭设脚手架并铺设跳板。脚手架高度5.0m。
第二层环向筋预先在做好的胎模上成型后,由塔吊分别将内外环向筋分两次吊上去放在第一层已浇好砼面上。吊钢筋时必须使用吊架,且多点吊,否则会引起加工好的环向钢筋变形。在胎模上环绕环向筋时,内侧环向筋要比设计尺寸略小,外侧环向筋要比设计尺寸略大。环向筋吊上去后,同样在钢筋绑扎架上端伸出钢管用来固定环向筋位置。绑扎时仍按先内侧后外侧,先立筋再环向筋的顺序。 4.模板工程
4.1底胎模形成
由于在新近回填场地上施工,为减小底胎模因沉降而断裂,底胎模现浇厚度20cm砼。模板用拼制的木模。先决定圆心,该圆心位置要做牢固,因为钢筋绑扎及模板安装均需要使用该圆心。用经纬仪钢卷尺沿环向定若干点,再用水准仪找支模水准点。然后支模、浇砼。支模时根据底层模板竖肋位置预埋φ28PVC塑料管用作加固模板穿通长拉杆用。
4.2模板设计 4.2.1模板套数
圆筒总共有65个,考虑模板重复使用次数及钢材的疲劳破坏,根据经验,设计2套整模板,即从第一节到第二节各设计2套,也就是考虑每套模板周转35次而保持不变形和不被破坏。
4.2.2模板结构、构造
模板结构、构造包括分片、分节、配板、横、竖楞、止浆、操作平台等内容。因预制件为圆弧形,经比较大块钢板卷制和定型组合钢模板拼制对构件外观质量,模板本身造价等综合因素后选用定型组合钢模板竖向配板,槽钢水平围囹,桁架竖向楞结构。在选配板时,分别计算不同板宽所引起的矢高差,以及日后模板拆除的应用,选外板用20cm宽钢模板,内板用30cm宽钢模板。根据塔吊起重能力,内外模弧长34.9m、32.15m都均分为4片,且留置8—10cm调节缝。第一节2.1m,第二节3.0m,第三节3.1m,第四节3.0m。每片模板重量最重为3.2t,最轻为2.9t,小于塔吊最小起吊能力3.5t,调节缝的设置是为避免模板的制作、支立及使用后变形的误差,在支模时出现连接不上和达不到所需的圆度,同时也为方便拆模而设立。内模调节缝用4mm钢板上焊螺栓固定,外模调节缝在相邻片模板之间,设在模板端的角钢和插入相邻两角钢间的木闸板、楔子组成。
止浆措施:第一节模板与底胎模之间的止浆选用8—10mm泡沫板裁成宽5cm,用胶水粘贴在底胎模侧面上,内外模用对拉螺栓紧固后泡沫板被压缩为只有1mm左右。能达到止浆措施。上下两模板之间止浆措施由10mm厚海绵条来保证。第三节模板与原砼面即施工缝的止浆:由固定在模板上的槽型橡胶止浆带和泡沫板共同作用来达到良好的止浆效果,且不影响构件外观质量。
操作平台:在第二节和第四节模板上设立上平台,在第三节模板上设立下平台。同时设立专用内操作平台。
4.2.3 模板受力分析、计算
根据受力分析,当模板采用上下对拉结构时,环向力很小,所以圆形模板受力计算完全可以按平面模板假定进行计算。
砼侧压力按中国港口工程技术规范推荐的公式计算,其公式如下:
Pmax=0.8+2.4KV1/2
式中:Pmax—砼最大侧压力t/m2;
K—温度系数
V—砼浇筑速度 m/h 设计取K=1.33,V=1.5 故Pmax=4.7t/m2 选取水平围囹为[8,间距675mm。竖向桁架上下腹杆为2[6.3和2∠63×5。间距为81.4cm。见图4。
4.2.4模板加工
模板加工在预制场内进行。为保证圆弧的准确性,在靠近塔吊处,按一片模板大小用砖砌胎模,分内(凹)弧、外(凸)弧各一个。定型组合钢模板用螺栓连接,围囹与角钢焊接桁架再与围囹进行焊接。在组装模板时,要在底胎模上定出中心线然后往两侧分拼,同时做出桁架及围囹刻度。模板一片组装完毕,由塔吊吊开存放于场内,然后进行表面处理。表面处理包括电刷除锈、子堵缝、电砂轮磨平、刷机油保养。
每节模板的4片均加工完毕后,在现场底胎模上进行试拼、调整,以利于安装。
4.2.5模板支拆
4.2.5.1第一层的
1、2节模板
由于有成型准确的底胎模,在安装时只须找准每片的平面位置,在制作底胎模时便将模板每片位置、刻度线放在其上。先装第1节2片外模,调好垂直度及钢筋保护层后,安装与之相对应的内模。内外模通过对拉杆加固,同时调整壁厚、半径、垂直度。然后安装另外2块外模和内模。第1节内外各4片模板安装完毕,对直径椭圆度、垂直度、壁厚、保护层统一进行调整,检查合格后开始装第二节模板。安装之前,先将10mm厚海绵条用扎丝固定在下层模板时连接肋上,作为止浆用。第二节模板安装时先将4片外模全部装好且与下层模板固定后再安装4块内模。上下层模板连接方式:模板之间通过U形卡,间隔用M12×25螺栓加固,桁架之间用M16×40螺栓连接。外模加固从上到下只设3道拉杆:第一道通过底胎模预埋PVC管穿通长对拉螺杆,第二道用预制撑筒内穿对拉杆螺杆,在第一节模板顶下10cm位置,第三道在第2节模板顶下10cm圆台来加固。
4.2.5.2第二层
3、4节模板
第三节模板安装前先找好水平点,并利用预埋圆台来固定可上下调整的用钢板加工的托架安装顺序仍是先装外模立于设立的两块水平托架上,将桁架对穿拉杆处对准圆台螺母预埋位置,上拉杆。同时将项丝与砼面顶紧,利用顶丝对模板垂直进行调整,调整完毕安装第二片外模,按同样顺序将4片外模安装完毕且进行调整后安装4块内模,内模与外模调整一致,内外模板加固见图7。第三节内外模各4片均安装完毕后,且将所有项目调整合格后再安装第四节模板。第四节模板安装同样是先装外模再装内模。壁厚由圆台螺母及预制撑筒来控制。
模板标高控制由技术人员从地面上往上用钢卷尺量测。
模板的拆除:第一层先将内模拆除,再拆除外模。第二层先将外模拆除3片,再拆除全部内模,最后拆除所剩的一块外模。 5.砼工程
根据已选定的砼泵送工艺,设计砼配合比。 5.1砼技术指标及原材料
圆筒砼强度有两种:水位变动区以下为C30,以上为C30,F250。因而配合比须设计两种,主要从外加剂上做文章。普通C30砼掺粉煤灰和高效泵送减水剂,有抗冻要求的C30,F250掺粉煤灰和减水剂、引气剂。减水剂选用MFN系列,引气剂选用PC—Ⅱ型。
砼坍落度设计为12—16cm,即进行分层减水; 砂率考虑泵送选为42%; 粗骨料选1—3cm碎石; 细骨料选淡水粗砂;
水泥为山铝普硅425#R型; 粉煤灰为Ⅱ级。 5.2砼施工 5.2.1砼搅拌
砼配料除粉煤灰、外加剂没采用电子计量外,其余原材料均电子计量。粉煤灰由磅秤称量后投放于料斗内,外加剂根据其比重由量杯来计量后直接投放于搅拌机内。即除水、外加剂外所有原材料均混和在一起一次性投入搅拌机内,同时往搅拌机注入需水量的2/3,搅拌2分钟后再加入剩余1/3的水,搅拌到3分钟,出料。
每次浇砼前均需测定砂石的含水率,同时对计量系统进行校核。对于第一罐料要进行坍落度测验,以便对水量作适量调整。
5.2.2 砼输送入仓、振捣
砼搅拌均匀后通过溜槽从搅拌机出料口进入拖泵料斗,由拖泵泵送,人工控制布料杆将砼均匀入仓。
5.2.2.1第一层砼浇筑顺序
由于第一层砼中有内趾及前趾,且内趾宽为1.0m,前趾宽也为1.0m,在砼入仓时先用串筒将砼从前趾开窗处浇满前趾,然后再通过串筒将砼从内趾开窗处浇内趾。封窗后从壁上下砼直接浇筒壁砼。
砼水平分层浇筑,分层厚度为35cm,落点距50cm。振捣也是分层进行。振点间距30cm,每一振点时间30—50s,不能漏振也不能过振,特别是有抗冻要求的砼更不能过振。
5.2.2第二层砼浇筑顺序
由于泵送砼富含浆,浇筑高大构件时,容易生出浮浆。为克服浮浆,采取措施一是逐层减水,措施二是浇至顶部时派专人清除部分浮浆,同时用砼补充。
针对砼顶部易干缩产生裂缝,采取措施是二次振捣、二次收面,第二次收面的时间以砼面接近失去塑性为准。并随即进行潮湿覆盖养护。 6.结束语
6.1由于钢筋绑扎采用了固定操作架的施工工艺,使钢筋绑扎间距、外形尺寸、定位等精确度得到满足,监理对钢筋施工很放心、满意。
6.2通过第一轮15个圆筒施工情况来看,由于模板设计时充分考虑其刚性,所以在施工时保证了圆筒尺寸和外观质量,满足了设计要求,在模板安装过程中,采用了固定支架及规范化的施工工艺,提高了工效。
6.3经检测评定,砼质量优良,外形尺寸及垂直度、圆的控制就像在图纸上画的一样精确。整个直径误差在10m内,比规范规定的27mm小许多,而且整个外观模板拼缝在一条线上,看起来非常美观。
6.4尚待改进的方面
6.4.1 由于第一次加工这样的圆弧模板,且受起重设备起重能力的影响,每层模板分2节。但由于加工时胎模长仅3.0m,且加工时不细心,使得上下模板桁架有一些错位而导致对接时较困难,同其余时连接板尺寸偏小,使得在连接板处对桁架有所破坏。因此建议胎模做通长6m,两节模板同时拼装,桁架同时连接,然后拼装完再分开吊走。这样能保证上下模板对位及桁架连接准确。
6.4.2第一层砼预埋圆台距砼顶太近,以致于第二层模板的找平托架拆卸较困难,应在设计时充分考虑这一点。
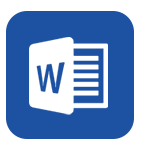