烧结自动化工艺介绍
高炉炼铁所使用的主要含铁原料是烧结矿。近几年,我国生铁产量不断上升,烧结矿用量大幅增加,提高烧结矿的质量、降低消耗、节约能源、保护环境在烧结生产中显得越来越重要,也是烧结生产工艺技术发展的永恒的课题和方向。
一、中国烧结技术发展情况
1、建设现代化混匀料场 ,优化用料结构
一大批钢铁企业建立了现代化的原料厂,进口粉矿的使用改善了烧结用料 ,使含铁原料得到了优化 ,所生产的烧结矿不但产量高、质量好 ,环保也有所改善 ,工序能耗也低。
2、小型烧结设备向大型化转变
烧结机大型化已普遍受到认同,新上烧结机普遍大型化 ,小型烧结机大都延长扩大面积或淘汰。
3、一般的混匀制粒到强化混匀制粒的转变
混合制粒时间的延长,由传统的一混和二混30 ~ 60 S 和50 ~80 S延长至120 S 和 180 S,有的甚至增加三段混合 ,混合制粒时间高达480 S 以上。并多方面采取强化制粒措施 ,增加石灰用量 ,烧结粉尘预先制粒 ,添加各种增效节能添加剂 ,在混合机进出口料端设导料板和挡圈并安装强化造球挡料板,采用含油尼龙衬板和雾化喷水等提高了混合料
的成球率和小球强度 ,混合料透气性大为提高,为厚料层烧结创造了条件 。
4、酸性及自熔性烧结矿向高碱度烧结转变
由于高碱度烧结矿还原性能及强度好 ,从1979年初,高碱度烧结矿的技术在全国得到推广。以高碱度烧结矿为主搭配部分酸性炉料 (球团矿、块矿) 已成为我国公认的高炉合理的炉料结构。
5、薄料层向厚料层的转变
1985年以前 ,重点钢铁企业烧结厂的料层厚度为220 ~ 250 m m ,生产采用薄铺块砖的方针。烧结矿强度及环保差 ,工序能耗高达105 kg/ t (标煤 ) ,1985年以后 ,随着烧结新技术 ,如球团烧结法、配加合理的生石灰用量及生石灰消化技术、预热混合料、各种增效节能添加剂等的实施 ,提高了料层的透气性 ,为厚料层烧结提供 了条件和保障 。
目前 ,我国厚料层烧结已达到国际最先进的水平。尤其是莱钢烧结机 ,烧结机布料厚度已高达到 750~800 m m ,居国际和国内领先水平。
6、生产热烧结矿向冷烧结矿的转变
1970 年以前 ,我国烧结机大部分生产热烧结矿 ,不能生产冷烧结矿 ,主要原因是烧结矿冷却设备不过关。1985年以后 ,解决了大型烧结机的冷却设施 , 实现了烧结矿的冷却。烧结矿冷却的实现 , 解决了烧结矿的整粒筛分 ,为烧结机采用铺底料创造了条件 ,也为高炉长寿、高产奠定了基础。
7、低品位烧结矿向高品位烧结矿的转变
1998年以前 ,我国重点钢铁企业烧结厂烧结矿的品位仅为52%左右。近几年,由于进口高品位矿增多和国内精粉品位的提高,烧结矿品位逐步提高,已达54%以上 ,不少烧结 厂达到 58% ~ 60% ,烧结矿FeO 和Si O下降。有的厂已实现高铁低硅的烧结法 。
8、烧结机低作业率向高作业率的转变
1985年以前 , 我国烧结机作业率较低 ,重点钢铁企业烧结厂和地方骨干企业烧结厂作业率仅为 79.26%和73.85%。1989年以后 由于普遍采用了新型结构和材质的没备 , 管理和操作水平的提高 ,烧结机的作业率普遍提高 ,烧结机的产能得到有效发挥 。
9、人工操作向高度自动化转变
1970年以前 ,我国烧结厂的操作如人工跑盘配料、烧结机速度和点火温度的控制、混合料水分的控制等全凭简单的仪表和人工操作 ,稳定性很差 。而目前新建和改扩建的大型和中型烧结机几乎都采用了较为完善的过程监控和控制项目,并采用计算机系统对全厂的生产过程自动进行操作、监视 控制及生产管理。有些厂还采用了模糊控制系统技术 ,人 工智能也在开发之中。
10、机械除尘向高效除尘的转变
烧结烟气除尘和环境除尘设备实现由多管或旋风除向高效布袋除尘和干式电除尘的转变 ,除尘效率大大提高 ,高达99%以上 ,环保大为改观。
11、中温废气由不可回收利用向回收利用的转变
1980年以前,我国烧结生产中产生的中温废气主要是环冷机、带冷机冷却烧结矿产生的中、低温废气 ,一般直接排放不回收利用。1985 年后相继建成了一批余热回收装置 , 有用于点火保温炉做助燃风的,有用于热风烧结的,有用于生产热水或蒸汽的,虽然起步较晚但有起色 ,经济效益显著。
二、烧结的概念
烧结是钢铁生产工艺中的一个重要环节,它是将各种粉状含铁原料,配入适量的燃料和熔剂,加入适量的水,经混合和造球后在烧结设备上使物料发生一系列物理化学变化,将矿粉颗粒黏结成块的过程。经烧结而成的有足够强度和粒度的烧结矿可作为炼铁的熟料。利用烧结熟料炼铁对于提高高炉利用系数、降低焦比、提高高炉透气性保证高炉运行均有一定意义。
三、烧结工艺流程介绍
1、铁矿粉造块的目的:
◆综合利用资源,扩大炼铁用的原料种类。
◆去除有害杂质,回收有益元素,保护环境。
◆改善矿石的冶金性能,适应高炉冶炼对铁矿石的质量要求。
2、铁矿粉造块的方法:烧结法和球团法。
3、铁矿粉造块后的产品:分别为烧结矿和球团矿。(供高炉炼铁生产的主要原料)
4、 目前生产上广泛采用带式抽风烧结机生产烧结矿。烧结生产的工艺流程如下图所示。主要包括烧结料的准备,配料与混合,烧结和产品处理等工序。
5、烧结的原材料准备:
含铁原料:含铁量较高、粒度
熔剂:要求熔剂中有效CaO含量高,杂质少,成分稳定,含水3%左右,粒度小于3mm的占90%以上。在烧结料中加入一定量的白云石,使烧结矿含有适当的MgO,对烧结过程有良好的作用,可以提高烧结矿的质量。
燃料: 主要为焦粉和无烟煤。对燃料的要求是固定碳含量高,灰分低,挥发分低,含硫低,成分稳定,含水小于10%,粒度小于3mm的占95%以上。
6、烧结的配料与混合: 配料目的:获得化学成分和物理性质稳定的烧结矿,满足高炉冶炼的要求。
配料方法:质量配料法,即按原料的质量配料;通过电子计量设备,按一定比例配兑原材料。
混合目的:使烧结料的成分均匀,水分合适,易于造球,从而获得粒度组成良好的烧结混合料,以保证烧结矿的质量和提高产量。
混合的方法:加水润湿、混匀和造球。根据原料性质不同,可采用一次混合或二次混合两种流程。一次混合的目的:润湿与混匀,当加热返矿时还可使物料预热。二次混合的目的:继续混匀,造球,以改善烧结料层透气性。用粒度10~Omm的富矿粉烧结时,因其粒度已经达到造球需要,采用一次混合,混合时间约50s。使用细磨精矿粉烧结时,因粒度过细,料层透气性差,为改善高炉透气性,必须在混合过程中造球,所以采用二次混合,混合时间一般不少于2.5~3min。我国烧结厂大多采用二次混合。
7、配料与混合的主要设备: 电子计量称:对放置在皮带上并随皮带连续通过的松散物料进行自动称量的衡器。主要有机械式(常见的为滚轮皮带秤)和电子式两大类。电子皮带秤是使用最广泛的皮带秤。由承重装置、称重传感器、速度传感器和称重显示器组成。
主要用到的自动化产品:称重传感器、速度传感器、数显表、变频器、电动机。
混合机:混合机械是利用机械力和重力等,将两种或两种以上物料均匀混合起来的机械。混合机械广泛用于各类工业和日常生活中。常用的混合机械分为气体和低粘度液体混合器、中高粘度液体和膏状物混合机械、热塑性物料混合机、粉状与粒状固体物料混合机械四大类。
8、烧结生产:
烧结作业是烧结生产的中心环节,它包括布料、点火、烧结等主要工序。
布料:将铺底料、混合料铺在烧结机台车上的作业
当采用铺底料工艺时,在布混合料之前,先铺一层粒度为10~25mm,厚度为20~25mm的小块烧结矿作为铺底料,其目的是保护炉箅,降低除尘负荷,延长风机转子寿命,减少或消除炉箅粘料。铺完底料后,随之进行布料。布料时要求混合料的粒度和化学成分等沿台车纵横方向均匀分布,并且有一定的松散性,表面平整。目前采用较多的是圆辊布料机布料。
点火:点火操作是对台车上的料层表面进行点燃,并使之燃烧。
点火要求有足够的点火温度,适宜的高温保持时间,沿台车宽度点火均匀。点火温度取决于烧结生成物的熔化温度。常控制在1250±50℃
点火时间通常40~60s。
点火真空度4~6kPa。
点火深度为10~20mm。
烧结:准确控制烧结的风量、真空度、料层厚度、机速和烧结终点。
烧结风量:平均每吨烧结矿需风量为3200m3,按烧结面积计算为(70~90)m3/(cm2.min)。
真空度:决定于风机能力、抽风系统阻力、料层透气性和漏风损失情况。
料层厚度:合适的料层厚度应将高产和优质结合起来考虑。国内一般采用料层厚度为250~500mm。
机速:合适的机速应保证烧结料在预定的烧结终点烧透烧好。实际生产中,机速一般控制在1.5~4m/min为宜。
烧结终点的判断与控制:控制烧结终点,即控制烧结过程全部完成时台车所处的位置。中小型烧结机终点一般控制在倒数第二个风箱处,大型烧结机控制在倒数第三个风箱处。
例:带式烧结机抽风烧结过程是自上而下进行的,沿其料层高度温度变化的情况一般可分为5层,各层中的反应变化情况如图2—5所示。点火开始以后,依次出现烧结矿层,燃烧层,预热层,干燥层和过湿层。然后后四层又相继消失,最终只剩烧结矿层。
①烧结矿层
经高温点火后,烧结料中燃料燃烧放出大量热量,使料层中矿物产生熔融,随着燃烧层下移和冷空气的通过,生成的熔融液相被冷却而再结晶(1000—1100℃)凝固成网孔结构的烧结矿。这层的主要变化是熔融物的凝固,伴随着结晶和析出新矿物,还有吸入的冷空气被预热,同时烧结矿被冷却,和空气接触时低价氧化物可能被再氧化。 ②燃烧层
燃料在该层燃烧,温度高达1350~1600℃,使矿物软化熔融黏结成块。该层除燃烧反应外,还发生固体物料的熔化、还原、氧化以及石灰石和硫化物的分解等反应。
③预热层
由燃烧层下来的高温废气,把下部混合料很快预热到着火温度,一般为400~800℃。此层内开始进行固相反应,结晶水及部分碳酸盐、硫酸盐分解,磁铁矿局部被氧化。 ④干燥层
干燥层受预热层下来的废气加热,温度很快上升到100℃以上,混合料中的游离水大量蒸发,此层厚度一般为l0~30mm。实际上干燥层与预热层难以截然分开,可以统称为干燥预热层。该层中料球被急剧加热,迅速干燥,易被破坏,恶化料层透气性。 ⑤过湿层
从干燥层下来的热废气含有大量水分,料温低于水蒸气的露点温度时,废气中的水蒸气会重新凝结,使混合料中水分大量增加而形成过湿层。此层水分过多,使料层透气性变坏,降低烧结速度。
四、烧结工艺参数对烧结过程产品的影响
精矿粉是烧结的主要原料,它是选矿厂的最终产品。物理化学性能对烧结矿 质量影响最大。具体要求如下: 1.含铁量(矿石品位)
铁精矿的含铁量是衡量铁精矿粉质量的指标。精矿含铁量越高,生产出的烧结 矿含铁量也高,经济价值越高,铁精矿粉含铁量一般在55%-65%,当然越高越好。 2.脉石成分及含量
要求精矿粉的脉石矿物含量要少,而和含量高一些,经济价值也会高一些。 3.有害杂质
硫、磷、砷、铜、铅、锌、钾、钠。铁矿石中有害杂质含量越少越好。 4.铁精矿粉的粒度
精矿粒度很细,用网目表示,小于200目的占60%以上,精矿粒度粗细与矿石 的晶粒大小有关,与磨矿生产工艺有关。
烧结用的精矿粒度不宜太细,一般小于0.074mm(-200目)的量小于80%。 5.成分稳定
6.铁精矿粉的烧结性能
铁精矿粉的烧结性能对烧结过程和烧结矿的产量、质量都有十分重要的影响。 了解各种精矿烧结性能,选择和搭配使用烧结性能不同的铁精矿粉,合理掌握烧结因素,是充分利用资源,达到优质高产的有效措施。
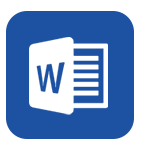