机械制造工艺课程设计
一、机械制造工艺设计步骤
1.分析及审查零件图样和产品装配图样; 2.确定零件生产类型和毛坯种类; 3.确定工件的定位基准; 4.拟定机械加工工艺路线;
5.确定各工序的加工设备和工艺装备;
6.计算各工序的加工余量、工序尺寸及公差; 7.确定各工序的切削用量和工时定额; 8.编制工艺文件。
二、零件的结构分析
1.熟悉零件图样,分析零件的用途和各项技术条件;
2.分析零件表面的组成和特征,将零件大致分为轴类零件、套类零件、齿轮类零件、叉架类零件和箱体类零件五大类;
3.分析零件的结构工艺性; 4.确定主要表面的加工方法。
三、零件的技术要求分析
零件的技术要求分析包括下面几项内容: 1.加工表面的尺寸精度和形状精度; 2.主要加工表面之间的相互位置精度; 3.加工表面的粗糙度及表面质量要求; 4.热处理及其它要求。
四、计算生产纲领和确定生产类型
生产纲领的大小对生产组织和零件加工工艺过程起着重要作用,它决定了各工序所需专业化和自动化的程度,以及所应选用的工艺方法和工艺装备。
零件的生产纲领可按下式计算:
NQn(1a%b%) (8.1-1)
式中 N-零件的生产纲领,单位为 件/年;Q-产品的生产纲领,单位为 台/年;n-每台产品中零件的数量 单位为 件/台;a-备品的百分率;b-废品的百分率。
根据〔1〕表5-5确定生产类型和工艺特点。
五、设计说明书的编写
说明书是课程设计的总结性文件。通过编写机械加工工艺规程设计说明书,进一步培
134 养学生分析、总结和表达的能力,巩固、深化课堂教学和课程设计中所获得的知识,掌握机械工艺设计的内容、方法和步骤。
说明书应概括地介绍设计的整个过程,对设计中的方案进行论证及比较,针对主要数据的选取及计算应作重点陈述。说明书内容要求系统性好,条理清晰,图文并茂,充分表达自己对设计过程的感悟和独特见解。文内公式、图表、数据等出处,应以“〔 〕”注明参考文献的序号。
说明书主要包括下面几项内容: 1.封面; 2.目录;
3.零件的工艺性分析;
4.机械加工工艺路线的拟定; 5.机械加工工序的设计; 6.设计小结; 7.参考文献。
机械制造工艺规程设计流程
一、毛坯的选择 1.毛坯的选择原则
(1)零件的材料和力学性能 相同的材料采用不同的毛坯制造方法,其力学性能有所不同。铸铁件的强度从离心浇注、压力浇注、金属型浇注、砂型浇注的铸件依次递减;钢质零件的锻造毛坯,其力学性能高于钢质棒料和铸钢件。
(2)零件的结构形状和外廓尺寸 直径相差不大的阶梯轴宜采用棒料,相差较大时宜采用锻件;形状复杂、力学性能要求不高可采用铸钢件,形状复杂和薄壁的毛坯不宜采用金属型铸造;尺寸较大的毛坯,不宜采用模锻、压铸和精铸,多采用砂型铸造和自由锻造;外形复杂的小零件宜采用精密铸造方法,以避免过多的机械加工。
(3)型材的使用 一般零件宜采用热轧型材;冷拔型材精度较高、尺寸较小,毛坯精度要求较高的中小型零件宜采用冷拔型材。
(4)生产类型 大批量生产时宜采用高精度与高生产率的毛坯制造方法,单件小批量生产时宜采用投资小的毛坯制造方法。
2.毛坯的制造方法与工艺特点
(1) 铸造毛坯的工艺特点及参数见表8.3-1; (2) 锻造毛坯的工艺特点及参数见表8.3-2; (3)轧制毛坯的工艺特点及参数见表8.3-3。 3.毛坯的加工余量及公差
(1)铸造毛坯的加工余量见表8.3-
4、公差见表8.3-5;
135 (2)热轧圆钢的尺寸及偏差见表8.3-6~表8.3-9; (3)冷拔圆钢的尺寸及偏差见表8.3-10和表8.3-11; (4)钢质模锻件的加工余量及公差。
钢质模锻件的加工余量的大小主要取决于锻件质量和复杂程度,机械加工加工余量一般从1~5mm根据具体情况选取,钢质模锻件的公差查阅GB12362-90。
二、基准的选择
定位基准的选择对加工面的位置精度、零件的工序数量及加工顺序起着决定作用。因此,必须根据基准选择原则,综合各方面因素加以确定。粗、精基准确定后,还应考虑各工序加工时工件的定位方案和夹紧方法。
三、拟定机械加工工艺路线 1.加工阶段的划分
根据零件的加工精度、表面粗糙度、表面质量及力学性能的不同要求,把整个工艺过程分成不同的加工阶段,以便逐步达到加工要求。主要的加工阶段有:
① 粗加工阶段; ② 半精加工阶段; ③ 精加工阶段; ④ 光整加工阶段。
2.零件表面加工方法的选择
根据零件的加工表面特征、加工经济精度和表面粗糙度来选择加工方法。 (1)外圆加工查阅〔1〕表5-7和图5-15; (2)孔加工查阅〔1〕表5-8和图5-16; (3)平面加工查阅〔1〕表5-9和图5-17; (4)米制螺纹加工见表8.3-12;
(5)齿形加工见表8.3-13和表8.3-14。 3.加工顺序的安排 应遵循“先粗后精”、“先面后孔”、“先主后次”、“基面先行”的原则,合理安排各工序的位置。
4.热处理工序的安排
(1)提高切削性能的预热处理安排在粗加工之前; (2)整体热处理安排在半精加工之前; (3)表面热处理安排在精加工之前。 5.检验工序的安排
检验工序一般安排在粗加工后、精加工前,送往外车间前,重要工序和工时长的工序前、后,零件加工结束后、入库前。
6.辅助工序的安排
(1)表面强化工序 如滚压、喷丸处理等,一般安排在工艺过程的最后。 (2)表面处理工序 如发蓝、电镀等,一般安排在工艺过程的最后。
(3)探伤工序 如X射线检查、超声波探伤等多用于零件内部质量的检查,一般安排
136 在工艺过程的开始。磁力探伤、荧光检验等主要用于零件表面质量的检验,通常安排在工艺过程的最后。
(4)平衡工序 包括动、静平衡,一般安排在精加工前后。
(5)去毛刺、去磁、清洗、涂油、防锈等辅助工序可根据整个工艺过程妥善安排。
四、选择机床设备及工艺装备 1.机床的选择
(1)机床规格应与零件外形尺寸相适应;
(2)机床精度应与工序要求的加工精度相适应; (3)机床的生产率应与零件生产类型相适应; (4)与本企业现有设备条件相适应。
各种机床的形状、位置加工经济精度见表8.3-15~表8.3-20,各种机床的主要技术参数见表8.3-21~表8.3-34。
2.刀具的选择
(1)一般采用标准刀具;
(2)中批以上生产,可采用高效率的复合刀具及专用刀具; (3)刀具的类型、规格及精度应符合加工要求。 3.量具的选择
(1)单件、小批量生产时,应尽可能选用通用量具; (2)大批量生产时,应采用各种专用量具和检具; (3)量具的精度等级应与被测工件的精度相适应。 4.夹具的选择
(1)单件小批量生产时,应尽可能采用通用夹具,也可采用组合夹具; (2)中批以上生产时,应采用专用夹具; (3)夹具的精度应与工序的加工精度相适应。
五、确定工序余量、工序尺寸及公差 1.确定工序余量
(1)分析计算法 此法须有可靠的实际数据资料,目前应用较少;
(2)经验估计法 根据工艺人员的实际经验确定加工余量,通常所取的加工余量偏大,一般用于单件小批生产;
(3)查表修正法 查阅有关手册,再结合实际加工情况进行修正,此法应用较为普遍。各加工方法的工序余量见表8.3-35~表8.3-53。
2.工序尺寸的确定
(1)当加工过程中基面没有转换时,可以由最后一道工序开始往前推算。
(2)当加工过程中基面需要转换时,可借助工艺尺寸链的分析来计算工序尺寸及其上下偏差。
(3)对于孔系坐标尺寸,通常在零件图样上已标注清楚。如果未标注清楚,就要利用平面工艺尺寸链来计算孔系坐标尺寸。
3.工序公差的确定
137 工序公差按各工序的加工经济精度来确定,并按“入体原则”换算出上下偏差。 4.钻螺纹底孔的直径可按下面的经验公式计算
脆性材料(铸铁、青铜等):钻孔直径d0=d螺纹大径-1.1P 韧性材料(钢、紫铜):钻孔直径d0=d螺纹大径-P 钻孔深度=螺纹长度+0.7d螺纹大径
式中 P为螺纹的螺距,单位为mm。
六、切削用量的选择
根据切削用量三要素对刀具寿命、生产率和加工质量的影响,选择切削用量的顺序应为:首先选尽可能大的背吃刀量ap,其次选尽可能大的进给量f,最后选尽可能大的切削速度vc。粗加工时,背吃刀量的选择以提高生产率和保证刀具耐用度为主;精加工时,背吃刀量的选择以保证零件的加工精度和表面质量为主。
1.车削时切削用量的选择可查阅表8.3-54~表8.3-64; 2.孔加工时的切削用量选择可查阅表8.3-65~表8.3-70; 3.铣削时切削用量的选择
铣削用量包括背吃刀量ap、侧吃刀量ae、每齿进给量fz(单位为mm/z)或每转进给量f(单位为mm/r)和切削速度vc。端铣时,ap为切削层深度,ae为被加工表面宽度;圆柱铣削时,ae为切削层深度,ap为被加工表面宽度。
一般切削层深度根据加工质量要求、加工余量、工艺系统刚性和机床功率来选择。铣削平面时,当工件表面粗糙度Ra=25~12.5m时,若用圆柱形铣刀,其预留的切削层深度小于5mm,或用端铣刀,其预留的切削层深度小于6mm,则一次进给粗铣就可达到要求;当预留的切削层深度较大或工艺系统刚性较差或机床功率不足时,一般分两次进行铣削。当Ra=12.5~3.2m时,可分粗铣和半精铣两次铣削,半精铣时的切削深度为0.5~1mm。当Ra=3.2~0.8m时,可分三次铣削,半精铣时的切削深度为1.5~2mm,精铣时为0.5~1mm。铣刀的每齿进给量fz可按表8.3-71选取,铣削速度vc可按表8.3-72选取,铣槽的切削用量可按表8.3-73或表8.3-74选取。
4.磨削时切削用量的选择
磨削用量包括砂轮切入工件的径向进给量fr(相当于车削时的背吃刀量)、工件相对于砂轮的轴向进给量fa、工件旋转的线速度或工作台直线移动的速度vw和砂轮旋转的线速度vc。常用的磨削用量可按表8.3-75选取。
5.齿轮加工切削用量的选择
齿轮的制造方法以滚齿、插齿最为普遍,其切削用量的选择应根据工艺系统刚性、工件材料、齿轮模数、工件精度要求及表面粗糙度等因素综合考虑。齿轮加工切削用量的选 择步骤如下:
(1)确定切齿深度和走刀次数 滚齿时,一般模数不大的齿轮多采用一次走刀切至全齿深。但模数大于4mm的齿轮,或者机床功率不足,或者工艺系统刚性较差时,可以分两次
(2)确定进给量 滚齿的进给量可按表8.3-76选取,插齿的进给量可按表8.3-77选取。
(3)确定切削速度 齿轮刀具的切削速度可按表8.3-78的公式计算。
138
七、劳动定额的制订
劳动定额有时间定额(即工时定额)和产量定额两种表述方式。前者指完成一定工作量所用时间,后者指单位时间内完成规定的合格产品数;两者互为倒数。目前企业常用时间定额作为劳动定额指标。
1.工时定额按下面的公式计算
单件生产:tp=tj+ta+ts+tr =tB+ ts+tr (8.3-1)
成批生产: tpc=tp+te/n=tj+ta+ts+tr+te/n (8.3-2) 大量生产: tpc=tp=tj+ta+ts+tr (8.3-3) 式中 tj-基本时间;
ta-辅助时间,参照表8.3-79选取,tj + ta为作业时间; ta-辅助时间,参照表8.3-79选取,tj + ta为作业时间; ts-布置工作地时间,一般按作业时间的2%~7%计算; tr-休息与生理需要时间,一般按作业时间的2%~4%计算; te-准备与终结时间; n-每批件数。
2.基本时间tj的计算
Ll+l1+l2tjii (8.3-4)fnfn 式中 L-刀具行程长度(mm);
l-切削加工长度(mm);
l
1、l2-刀具切入、切出长度(mm),车削可参照表8.3-80、钻削可参照表8.3-81选取l
1、l2之和;
n-机床主轴转速(r/min); f-进给量(mm/r)。
139
八、绘制工序图及标注工序尺寸偏差 1.绘制工序图的要求
① 用粗实线表示本工序的各加工表面,其它部位用细实线表示; ② 加工表面上应标注表面粗糙度符号;
③ 工序图应标出本工序结束时应达到的尺寸、偏差及形位误差,与本工序加工无关的技术要求一律不写;
④ 工序图上应注明定位、夹紧符号;
⑤ 工序图以适当的比例、最少的视图表示出工件在加工时所处的位置状态,与本工序加工无关的部位不应表示。
2.标注工序尺寸偏差的要求
① 中间工序的工序尺寸,对于内孔、外圆、平面或沟槽,应按“入体原则”注成单向偏;。
② 中间工序尺寸,若属于孔轴中心距或孔到平面的距离,应标注成双向对称偏差; ③ 中间工序尺寸的公差可从相应的加工经济精度表中查得 ④ 最后工序的工序尺寸,应按图样要求标注。
九、编制工艺文件
1.填写机械加工工艺过程卡片; 2.填写机械加工工序卡片; 3.整理设计说明书。
十、注意事项
上述机械加工工艺数据表格为学生课程设计提供所需的参考资料,数据资料不是非常完
140 备,如需要可查阅下列手册。
1.王先逵主编.机械加工工艺手册.北京:机械工业出版社,2007. 2.孟少农主编.机械加工工艺手册.北京:机械工业出版社,1999.
3.美国可切削数据中心编.机械加工切削数据手册.北京:机械工业出版社,1989. 4.李益民机械制造工艺设计简明手册.北京:机械工业出版社,1991. 5.艾兴等编.切削用量简明手册.北京:机械工业出版社,1994.
141
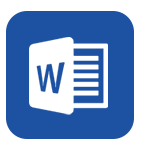