推荐第1篇:现场改善
现场改善——低成本管理方法
序言
1986年,我在东京的大仓大饭店时,
再形成更新更好的标准。总之,改善是永无止境的。
近年来,我们见到了许多有关企业经营成功的策略,如过眼云烟般来来去去。但在我的经验里,“改善”跟这些不同。它不是一时流行的风潮,它协助我们如何以最基本的方法工作。从事工作的过程本身,就是要完成工作,也是能令我们深具成就感的方法。对我而言,那是带给我真正欢乐的所在。在今天高度竞争的企业环境中,欲想在自己的领域成为领先者,应当持续自问:“我们应如何将明天的工作,做得比今天更好?”在本书中,今井正明所给予我们的,正是如此做的工具。
爱德华·詹森三世(Edward C.Johnson, III)
富达投资公司
董事长兼首席执行官
现场改善——低成本管理方法
前言
我的前一本书(《改善:日本企业成功的奥秘》,McGraw-Hill,1986年)阐明了“改善”的主要手段,例如:全面质量管理、全员生产保全、准时制、质量小组和提案建议制度,也谈及各种不同的“改善”原则和观念。
“现场改善”,对欧美管理文化而言,算是新近引入的词。“现场”意指工作的场所,在本书即是阐明如何运用常识性、低成本的方法来管理工作场所—产生附加价值的地方;不论它是一条生产线、保险部门或者是会计办公室。这不是一本理论性的书,而是一本行动性的书。就最终的宗旨而言,不管读者吸收了多少知识,若不能付诸于每日实务工作上,也是没有什么用的。《现场改善》并不专注理论上的知识,仅仅提供了一个简单的参考构架,用以解决问题。为此目的,提供了许多检查表、范例及个案研究实例。
常识性、低成本的改善方法
今天的管理人员,时常喜欢尝试一些复杂的工具和科技方法,去处理一些可以用常识性、低成本的方法解决的问题。他们必须抛弃总是试图用非常复杂、尖端的科技去解决日常问题的习性。
将一般常识用到实务上,就是本书的主旨。它适用于每一个人:经理人员、工程师、督导人员和一般人员。随着将一般常识应用到实务上,《现场改善》也谈到经理人员的角色及发展成为一个学习型组织的必要性。我认为,最高阶层经营者的角色之一,就是要去激励所有管理人员去达到更高的目标;而
员工,就不可能提供质量良好的产品和服务给顾客。
在日文里,“Muda”的意思是浪费。任何不会产生附加价值的活动,就是Muda。在现场的人,不是正在产生附加价值,就是没有产生附加价值。这对其他诸如机器及材料资源而言,也是相同的。假设公司的员工们,每做了1份有价值的工作,就随附9份Muda;如果将Muda降为8份,而使附加价值增加为2份,他们的生产力也就加倍了。消除Muda,可以作为改进生产力和降低作业成本的最有效方法。“改善”着眼在现场消除Muda,而非通过加大投入来增加价值。
用一个简单的例子,来说明“改善”的成本效益。假设作业员正在组装家庭器具,站在工作台前,要将某些零件装上去,这些装配的零件,装在一个大箱中,并放在作业员的后方。转身去取一件零件,需耗费5秒钟的时间,而实际装配所需的时间仅为2秒。
现在,让我们假想,零件放在作业员的正前方,他仅需简单地向前伸出手臂,就可拿取零件—一个仅需耗费1秒钟的动作。作业员可以利用节省的时间,集中全力于有附加价值的装配工作上。简单地改变零件位置,消除取零件的时间浪费,就产生了4秒钟的收益,如此就可转换成为增加3倍的生产力!
像这样许多流程里的小改善,逐渐累积起来,就会形成显著的质量改进,而成本效益和生产力也会跟着改进。应用这样的方式,遍及所有管理活动,尤其是在最高管理层,可逐渐地达成准时生产、精益管理体系。相反地,一个具有创新思想的经理人员,或许会倾向于买一部设备,使作业员的装配工作更快些。但是,这并没有消除转身到后面取零件的Muda。此外,买进这个设备要花钱,而消除Muda则不需花费成本。
在现场实施“改善”的
现场改善——低成本管理方法
目
录
序言 .................................................................................1 前言 ...................................................................................3 致谢 ..................................................................................29 目录 ...................................................................................5
行动(Action)→PDCA的循环,以PDCA循环作为“改善”持续运作的工具,以达成“维持标准”和“改进标准”的目标。PDCA是整个“改善过程”中,最重要的观念之一。
“计划”是指建立改善的目标(既然“改善”是一种生活方式,所以在任何场所中,应当有一个目标可供改进)。“执行”是指依计划推行。“检查”是指确认是否按计划的进度在实行,以及是否达成预定的计划。“行动”是指新作业程序的实施及标准化,以防止原来的问题再次发生,或者是再设定新的改进目标。PDCA不断地在旋转循环,一旦达成改善的目标,改善后的现状,便随即成为下一个改善的目标。PDCA的意义就是永远不满足现状,因为员工通常较喜欢停留在现状,而不会主动去改善。所以管理人员必须持续不断地设定新的挑战目标,以带动PDCA循环。
任何一个新的工作流程,在初期都是呈不稳定的状态。开始进行PDCA改善时,必须先将任何现有的流程稳定下来。此一稳定的过程称之为:标准化(Standardize)→执行(Do)→检查(Check)→行动(Action)SDCA循环。
在当前的流程里,每当发生异常时,便必须反问自己下列问题:是否因为没有标准而发生的?是否因为没有遵守标准而发生的?或者因为标准不适当而发生的?惟有建立了标准,并且确实遵守,以将当前的流程稳定下来,才能再进行下一个PDCA循环。
所以SDCA的目的,就是在标准化和稳定现有的流程,而PDCA的目的则在于提高流程的水准。SDCA是表示“维持”,而PDCA就表示“改善”,此为管理层的两项主要职责。
后,便应当承诺绝不将不合格品或不正确信息,往下一流程传送。当组织内的每一个人都能依此信念实践时,则在外部的市场顾客,最终也能接收到高质量的产品或服务。一个真正良好的质量保证体系,就是指在组织内的每一个人,都能认同及实践这种信念:下一流程就是顾客。
全员生产保全
在日本及海外,实施全员生产保全(Total Productive Maintenance)的制造业公司正逐日增多。TQM强调总体管理绩效及质量的改进,TPM则着重于设备质量的改进。TPM是通过总体的预防保养制度,来延长设备的寿命,以追求设备效率的最大化。
就如TQM涵盖了公司内的每一个人,TPM也涵盖了工厂内的每一个人。厂房环境维持的5S活动,是现场里另一主要的活动,也可视为TPM的前奏活动。然而在许多实例中,5S是与TPM分开来推行的,而且也收到了不凡的效果。
方针展开
虽然“改善活动”的目的是在从事改善,但是若每一位从事改善的人员,缺乏目标的指引,则改善的成效也有限。管理部门应设定明确的改善目标,以指引每一位员工,同时能正确领导所有的改善活动,向既定目标迈进。真正具有改善成效的活动,是需要予以密切地督导推行的。
首先,最高管理部门必须设定长期的方针,再细分为中期方针及年度方针。最高管理部门必须有一个方针展开的计划,往下传达至下一管理层,直至到达现场为止。当方针逐层往下展开至下一阶层时,其方针计划及活动的明确化也随之增加。例如,某一方针叙述为:“为维持竞争力,我们必须降低10%的成本。”也许现场会进一步展开更明确的活动方针,如提高生产力、降低库存及不合格品、改进生产线的结构。
没有目标的改善活动,就如同没有终点站的旅途。改善是在每一个人都能为达成目标而工作时,才能产生最大的效果;而管理部门的职责,就是要设定这个改善的目标。
改善活动的终极目标
由于“改善”涉及所采用的改善活动方式,所以我们必须先知道,在企业的改善活动里,哪一方面是最急切需要改进的。此一问题的答案就是:质量、成本和交货期(QCD)的改善活动。这在我的前一本书:《改善:日本企业成功的奥秘》是称为质量、成本及进度(QCS)。从那之后,QCD已取代了QCS,成为被普遍使用的术语了。
品质,不仅是指完成品或服务的质量,而且也是指完成这些产品和服务所必需的“过程的质量”。成本是指:设计、生产、销售及服务产品或“服务”的总体成本。交货期是指:将所需产品的数量及时送达顾客手中。当这三项被定义为QCD的条件,都能达成时,顾客自然就能满足了。
QCD的改善活动,在各个部门间,担任起彼此的沟通桥梁作用,如研究开发、工程、生产、销售和售后服务。因此,跨部门的使用是必要的,同时也要与供应商和经销商合作。检讨自己公司目前在市场上QCD的地位和建立改善QCD方针的优先顺序,就是高层管理者的责任。
本书往后的章节里,搜集了一些改善活动实例,说明各个来自于制造业和服务业不同行业的公司,如何推行有关现场改善的观念和体系的实务做法。
是在现场工作。因此,现场涵盖了多种层面的办公及管理部门。这些服务业公司的大多数部门里,也具有一些部门间活动的内部顾客,这些活动也可视为现场。若打电话到日本的工厂总经理、生产经理或质量经理,很可能会从其助理那里得到如下的回答:“他到现场去了。”
一些知名公司的总经理,对现场的工作都具有丰富的背景。他们对现场事物的进展都能充分了解,并能提供必要的支持。
这两种不同的现场观点:一种管理层的角色在于提供支持给现场,现场位于管理结构的顶层(倒三角形),另一种管理层的角色在于提供政策和资源给现场,现场置于管理结构的底层(正三角形);就“现场-管理”的关系而言,具有同等效用。“现场”与“管理”共同分享同等的重要性。“现场”通过提供产品或服务来满足顾客,而“管理”则是通过策略的设定和方针展开,以达成在现场的目标。因此,改善的动力应是“由下而上”和“由上而下”,两者兼具。正三角的管理层位于组织的顶端,他们要带动设立方针、目标和优先顺序,以及人力和金钱等的资源分配。在此模式下,管理层必须做好领导统筹。并决定采用哪一种最迫切需要的“改善活动”。这种达成公司目标的过程,称为“方针展开”。由于正三角形所示的“现场-管理”的关系,位在顶层的许多管理人员倾向于认为,他们的工作总是在告诉“现场”人员做什么事。然而,从倒三角形可以看出,现场是位在顶端,管理人员可由此看出,为了提供合适的协助,他们应当倾听现场人员的声音并向其学习。因此,“现场”成了达成常识性和低成本改善的来源。
“管理”与“现场”这两种模式的各自角色,是不应该混为一谈的。
改善事例庆应大学的助理教授川濑武治,在“解决工业工程的问题”(1995年日刊《工业新闻》)文章中写道:公司内的人员可分成两种类别:一类是为公司赚钱的人,另一类为不赚钱的人。仅有那些开发、生产和销售产品的
可以获得具实质性的解答。
着重在以常识及低成本的解决方式,而不是以昂贵和既定方法为导向的解决方式。
员工开始乐于改善,而且容易受到鼓舞。
同时可以增强改善的认知和工作效率的能力。
作业人员在工作时,可以思索改善。
为了从事改善,不须经常向上级管理层取得核准。
的行程表,来接待这些有潜在市场的顾客。首先是一个长达1小时的附图简报,以及报告他们在改进质量方面所做的努力。接着,访客希望能参观现场。到达后,这些采购经理人员被带到会议室里。然而,采购团人员坚持立即跳过在会议室的议程,马上到现场去。一到现场,停留了仅仅几分钟,在准备离去之前,工厂的总经理贝维德(Bewildered)恳求着:“请告诉我们,你们的见解!”这个采购团回答:“我们看到了一个低水准的厂房环境,而且杂乱无章。更糟的是,我们看到有些工人在流水线上工作时抽烟。假如管理部门容许这种事在现场发生,便是在处理汽车安全零件上不够慎重,我们不愿跟不够慎重的管理层交易。”
厂房良好环境的维持,表示员工士气高昂及纪律严谨。任何公司都可以在短期内,达成一个高水准有纪律的公司。然而要长久维持下去,可就是一件极富挑战性的工作了。而且,5S一旦消失不见,就会显现出一个杂乱无章的现场。要提高现场里的士气和自律,需要获得员工的参与、介入和共享资源。某些活动是在加速改善的过程及维持其动力,但最终必然带来企业文化的改变。这些活动包含团队合作,诸如质量小组和其他的小集团活动,以及员工提案建议制度。在小集团活动中,工人可以继续找出潜在的改善目标。当现场的员工参与改善活动,而且看到所产生的戏剧化成果改变,便会变得更热心、更有纪律了。
在工厂和在公司办公室里的方针展开活动上,要有更积极、正面的沟通,使工人得以参与改善目标的设定,而各种可视管理工具的应用,也扮演了一个维持现场改善风气的极重要角色
现场管理的金科玉律
大多数的经理人员,较喜欢把办公室当做工作的场所,而且希望自己能远离发生事件的生产现场。大多数的经理人都仅是通过每天、每周甚至每月一次的报告和会议,来接触、了解现场的实情。
与现场保持密切的接触及了解,是效率化管理生产线的
及“对于那个流程你有何想法?”佐加无法回答大部分的问题,因而了解到自己的观察,漏失了许多重要的地方。
督导人员向佐加耐心地解释他无法回答的问题重点,用图表画在一张纸上,以便将整个流程描述得更清楚、正确。直到此刻,佐加才明白他的师傅对流程有更深入地认识,也了解自己的无知。
渐渐地,佐加明白了:现场是所有信息的来源。他的师傅接着告诉他,要成为一个够格的丰田人,就必须喜欢现场,这是每一个丰田员工所必需的信念—现场是公司内最重要的地方。
佐加说:“的确,这是我接受过的最好的训练,它帮助我成为一个真正的现场人。而且这种现场思想,终生影响我的工作生涯。即使是现在,每次我看到一个问题,我的心中,立即就大声清楚地吼出:先到现场去看看!”
这在日本,是一种现场常见的训练方式。大野耐一是以开发丰田生产方式出名的。当大野注意到有哪一位督导人员,没有真实地掌握现场的状况,便会带着他到工厂去,画上一个圈圈,要求这位督导站在里面,直到他明白了为止。大野也力促经理人员要去寻访现场。他会说:“每天到现场去,而且去的时候,不要磨破了你的鞋底却毫无所获。最少每次都能带回一个改善的构想。”
当大野刚开始在丰田导入准时制的观念时,遭到来自四面八方的阻力。其中一个最强烈地反对意见,是来自公司内的财务人员,他们只相信书面财务报告,而且经常不愿支持分配资源给与现场有关的改善活动,因为这样做,并不能立即从最底层的生产线获得成果。大野力促会计人员去工厂。他告诉他们,每年要穿破两双鞋子到现场走走,看看存货、效率、质量等如何被改善,而且这些改善对成本的降低是如何地做贡献,这些终将产生较高的利润。
在大野的晚年,他公开演讲以分享自己的经验。据报道,他有一次的演讲起头如此问道:“听众中有财务人员吗?”当有些人举起手时,大野告诉他们说:“你们并不是要来了解我将要演讲的内容。纵使你了解了,也将无力推行,因为你们是远离现场而生活的。我知道你们是多么的忙碌。我认为当你们回到办公室时,宁愿把时间耗在办公桌上的工作。”他以开玩笑的方式说完这些话。他明白能获得财务管理人员的支持,对现场改善是极为重要的。
富士全录公司的总裁—宫原明的职业生涯,是从富士胶卷公司的成本会计开始的。他知道现场才是所有真实资料的来源,宁愿到现场去探查所取得的信息。当他收到财务报表,看到所列的不合格品资料时,便感觉急切地要去现场,观察造成这些不合格品的原因。因为他认为一个会计人员的工作,不是单纯地与数字为伍,而应去了解这些数字产生的过程。由于经常在现场里见到宫原,最后,生产线的督导人员必须在靠近生产线的地方,准备一张桌子供其使用。
后来他终于调到富士全录公司,并且高升至其他的管理职位,他仍然对现场迷恋。举例来说,当他担任工农业部门的部长时,现场即是指他的业务人员和服务人员,与客户接触的场所。他伴随着服务人员去拜访客户,并非仅阅读报表,而使他对客户的需求有更好的了解。
有一次我旅行到中美洲,拜访了一家八百伴的分公司,这是总部设在中国香港的一家日本超级市场连锁店的公司,其连锁店遍布全球。我问了总经理,有谁在仓库的角落有办公室,多久去现场一次?(在超级市场,现场系指店面、仓库及结账台的地方。)这位经理用非常抱歉的态度回答说:“你知道,我有一位负责现场的助理,所以并没有经常去现场。”当我强求他告诉我正确的次数时,
他说:“好吧!我每天必须到那儿大约30次。”这位经理为每天“仅”到现场30次感到歉意!
“当我走过现场时,”他告诉我说:“我不仅观看有多少位顾客,商品有否正确地陈列,哪项商品较受好评等,而且也往上看看天花板,往下看看地面是否有任何异常现象。走过现场及看看正前方,是任何一位经理随便都办得到的做法,你知道吗?”有一个地方确定不是现场,那就是经理的办公桌。当一位经理人员依据资料,在他的办公桌上做决策,那么这位经理人员就不是在现场,而此时就必须对原始资料的来源详加质疑。
举个例子来说明。由于日本是位于活火山活动频繁的区域,有许多温泉渡假区。这些渡假区的主要卖点就是露天浴池,游客可以一边泡在浴池中,一边欣赏远方的河川山脉。最近我在一家大型的温泉大饭店休了几天假,这儿有室内浴池和室外浴池。多数游客都是先到室内的浴池浸泡后,才走下楼梯到室外的露天浴池浸泡。正常来说,我看到每个浴池约各有一半的旅客在浸泡。有一天晚上,发现室内的浴池几乎空无一人。当我进入之后才了解,原来是水温太高了。因而导致大家都往露天浴池挤,因为那里的水温刚好很适当。
明显地,室内浴池出了差错。一位清洁人员带着另外的浴巾进来,想要清洁这个浴池,却没有注意发觉有何不妥之处。当我告诉她这个问题,她马上打了电话,接着水温就恢复正常了。
稍后,我与饭店的总经理讨论这个突发事件。他是我的好朋友,他告诉我说,室内浴池的温度是设定在摄氏24.5℃,而室外的浴池是设定在摄氏43℃。这位总经理继续解释说“我们有一间监控室,我们的工作人员会随时密切注视着浴池、房间的温度,火警警报系统以及诸如此类的事。不论何时,当他看到仪表有异常时,便需采取处置行动。”说到此,我反驳他说:“不对,注视仪表的人,仅仅是依赖
另外一家我拜访过的工厂,我得知每当总公司的大人物来访时,厂长就必须耗费数个小时,在会议室内回答那些大人物愚蠢的问题。这些经理人员不去现场了解进行中的事务,而且经常留下了一些不适当、找麻烦的指示。“没有这些会议,我们还可以做得更好呢!”厂长这样告诉我。
这位厂长对会议的见解,表露出在最高管理层与工作现场之间有巨大的鸿沟存在,此情况削弱了公司挑战内部的浪费和外部的竞争能力。管理层的此种做法,通常会引来工人对其不尊重的态度。
公室内做一些书面工作。我认为自己拥有了所有的答案,而且能处理任何一件事。现在,我发现到通过改善活动,我们何以做得不一样了。例如质量小组会议以及倾听工人的提案,走到工作场所去,把更多的时间花在现场,观察每一个问题并且将它们矫正。我发掘出我的员工都有很多的能力—艺术的才华以及实务的技术,这些都是以往我所不了解的。他们自己都能从事所有的改善工作,使生产线变得不一样。”
“我花了90%的时间在现场里,使我能看得到工人的问题,”普利欧说着,“以前当他们进办公室告诉我他们的问题,我必须听他们说,但是无法为他们做许多事。我不了解我们是以这种方式年复一年来经营我们的工作,而且我设想每一件事都没问题。但是,事实并非如此。借着走入现场,我能真正地了解到工人所说的事物了。”
“现在,我注意到每一个人都能在他们的工作上付出更多努力。他们感到兴奋,以自己的部门为荣。他们将每一件工作保持得有条有理、更为清洁。工作场所看起来很好。而且新人进来时,都愿意在那儿工作。自己感觉很好,而他们看起来也很好。他们看到正在进行中的这些改变,这些改变也产生了不同的变化,使他们的工作更容易做。”
并马上办”的精髓)。所协议出的程序往后就必须经常地遵守。有问题及客人抱怨时,此程序就必须再检查修正,使旅馆的传真文件处理制度,随时持续地改进。
质量、成本及交货期,并不是个别不同的议题,反而是彼此间密切地关联着。不论价格多么吸引人,花钱购买缺乏质量的产品或服务是毫无意义的。反过来说,即使能够提供吸引人的价格,以及良好质量的产品和服务,若未能将产品及时、准确地送达顾客手中,也是没有意义的。
好。
有一次,我参观了一家工厂,管理人员以他SQC的成就深以为傲。我看到许多管制图张贴在他的房间墙上。但是,一当我步入现场,我发觉没有一个人了解变异的意义。作业员没有标准,而且装配每一件产品的方法都不一样。有时甚至没有在指定的场所装配。在参观时,机器重复地出故障,产生了许多不合格品。然而,这位管理人员仍以他的SQC为傲!
改善事例东京大学教授久米均说过:我认为欧美对质量控制,旨在“控制”质量以符合标准及规格之规定,日本式的特征则是集中在“改进”(改善)质量。换句话说,日本的方式是有系统地持续不断地去改善。
在横川惠普公司(YHP)装配线的浸锡流程,质量改善的卓越成就的实例,可以作为此论点的说明。该公司在1978~1982年之间,成功地将不合格率从4 000ppm(百万分之一)降低至3ppm。YHP的质量改善分为两个时期:1978~1979年及1980~1982年。在这两个不同时期的质量改善活动,有相当大的不同。
举例来说,在
质量是从组织内的每一个人,承诺绝不将不合格品或不完整的信息,送至下一流程开始。石川馨博士所说的“下一流程就是顾客”,指在同一公司内的内部顾客,绝不应把不合格品送至下一流程的顾客,以免造成他们的不便。在现场,这样的想法有时就写成为“不接受、不制造、不流出”,当每个人都能认同实现这个理念时,一个良好质量保证体系就能存在了。
改进生产力以降低成本
当以较少的(资源)“投入”,生产出相同的产品“产出”,或以相同的“投入”,生产出较多的“产出”时,生产力就改进了。在此所称的“投入”系指像这些项目如人力资源、设施和材料。“产出”意指像这些项目如产品、服务、收益及附加价值。降低生产线上的人数,尽力越少越好。这不仅降低成本,更重要的也减少了质量问题,因为更少的人手,表示更少的人为错误的机会。我们有许多方法可以运用流水线上的正式员工。管理层应当考虑借着改善活动,以抽出人力作为其他有附加价值活动的人力资源的来源。当生产力提高的时候,成本就跟着下降了。
降低库存
库存占用空间,延长了生产交期,产生了搬运和储存的需求,而且吞噬财务资产。产品或在制品,“坐”在厂房的地面或是仓库里,是不会产生任何的附加价值。相反地,它们恶化了质量,甚至当市场改变或竞争对手导入新产品时,会在一夜之间变成废品。
一般的制造业公司,使用了其所应需的:4倍空间、2倍的人力、10倍的交期时间。通常“现场改善”消除输送带生产线,缩短生产线,把分离的工作站并入主体生产线,降低库存,减少搬运。所有的这些改善,减少了空间的需求。从现场改善所释放出来的空间,可作为增加新生产线或保留为未来扩充之用。类似的改善也可导入非制造业的环境。
通过应用这些已经开发多年的各种管理体系,使得质量、成本及交货期能同时达成。也因此,公司能比以往赚取更多的利润。
现场改善——低成本管理方法
致谢
《现场改善:低成本管理方法》,是在我的著作《改善:日本企业成功的奥秘》一书于1986年出版后,10年来在我的改善顾问生涯中,所孕育出来的一本新书。
本书是与我的改善协会(Kaizen Institute)的顾问们和在我的顾客现场中,实地从事现场改善活动的许许多多作业员、工程师和经理们,以及支持我们工作的专家们,共同合著的一本书。为此,我内心对他们真是感激不已!
除了要向书中列名的人士致谢之外,我特别要感谢久留米大学的泽田善次郎教授,他的《工场管理的可视管理》一书(由日刊工业新闻于1991年以英文出版),引发我“现场管理之屋”的灵感;谢谢宫崎产业经营大学企业管理学院院长真岛一郎教授,提供了撰写本书极多颇具价值的资料;也要谢谢改善顾问高桥健司、柿内幸夫、武田仁以及广布在世界各地我们的顾客,在他们的现场改善研习会中,有许多与我们共同携手合作的朋友们。
同时,我也要感谢:史都·卡蒙、金·卡达兹、汤姆·连、彼得·杜福、施纪·贝雷、加普·波士马、尾本广美、庵下喜美江、汤泽结美和其他改善顾问公司的人士;卡罗司·杜拉蒙托拉、雷诺·特札诺、乔奇·吉诺·哥提略兹、乔奇·提塞拉和阿根廷史创特(STRAT)的马利欧·蒙利亚哥,Bunge&Born公司的前任总经理安琪儿·派博西;毕生贡献于促进改善运动,但不幸已辞世的乔普·博肯和希格福雷·赫勒博士;我同时要向改善协会于欧洲开创初期,贡献良多的彼得·威拉特致谢。
我同时要感谢在写本书案例研究中的一些人士,包括布宜诺斯艾利斯(La Buenos Aires)公司的奈达加·摩诺和弗兰多·科拉弟、银河制造集团公司(Molinos Rio de la Plata)的耐斯德·赫里拉、陆卡司汽车公司的亚塞尔·博斯、迪士尼大学的盖里·布加纳和贝拉利·欧巴利、质量公司(Quality Inc.)的达拉·赫斯汀、富达投资(Fidelity)公司的比尔·尼格林和山德拉·苏可、爱信精机(Aisin Seiki)公司的白鸟进治(Shiratori Shoji)、音福科技(Infotec)公司的拜托里欧·纳里和丰田自动织机工厂的森裕,以及丰田工机公司的佐野良和井上胜夫。
最后,我要感谢我的执行助理—永山路得,她为此书历经数月不眠不休地工作至深夜。也要向我的妻子则子致意,因为她必须接受我的生活方式,经常游走于世界各地,并为伴随我而饱受压力。同时,也要向协助出版此书的人士致谢,特别是巴伯·吉诺伟奇,他协助校对我的手稿。另外,强尼·巴尔米尼、巴美拉·彼尔顿和麦格劳-希尔(McGraw Hill)公司的菲利浦·卢培尔,他们对本书的付梓,也发挥了极其重要的作用。
今井正明
推荐第2篇:现场改善读后感
现场改善—低成本管理方法的常识 ——读后感
现场改善的目的:
实现高质量;实现低成本;实现快交期;实现利润最大化。 现场改善的优势:
最直接、最真实;持续不断的;低成本;低风险;高回报。 现场改善的对象:4M1E 现场改善的方法:
人员是现场改善的基础;5S创造了有效的工作环境;标准化是确保质量的最好方法,也是工作上最节省成本的方法;消除了浪费实现利润最大化; 人员改善:
创造学习的氛围,给予现场人员实践与演练的机会;通过实践及演练转变人员的思想。 现场人员改善的基本原则:1.抛弃传统的固定的生产思想;2.思考如何做下去,而不是为何不能做;3.不要寻找借口,从质疑现行的做法开始;4.不要等待十全十美,即使只有50分的成功也要马上动手;5.立即改正错误;6.不要花费金钱改善;7.遇到困难时才会蹦出智慧的火花;8.问5次为什么,找出原因;9.记住:改善机会是无止境的。 通过提案建议制度及质量圈,来证明员工是否在积极的参与改善及管理阶层是否已建立起改善机构;通过提案建议制度员工与上司、员工与员工之间的沟通。 提案建议的内容:
使工作更容易,能排除单调的工作,能排除不方便的工作,是工作更安全,使工作更有生产力,改进产品质量,节省时间及成本。
培养人员自律的习惯:1.可视化管理2.制定目标3.发挥现场督导人员及现场经理的作用。 现场改善的方法:5S 1.整理(Seiri)将现场里需要与不需要的东西,区别出来。并将后者处理掉。2.整顿(seiton)将整理后需要的东西,安排成为有秩序的状态。3.清扫(seiso)保持机器及工作环境的干净。4.清洁(Seiketsu)延伸干净的概念至自己本身,并且持续执行上述3个步骤。5教养(Shitsuke)以设立目标的方式,来建立自律以及养成从事5S的习惯。 现场改善的方法——标准化
将全员达成共识的程序固定下来形成“标准”;管理人员推行标准化—执行—查核—处置(SDCA)的循环工作程序来维持标准;通过计划—执行—查核—处置(PDCA)的循环工作程序来调整现状和提高标准至较高的水准。 现场改善的方法——消除浪费
制造过多的Muda、存货的Muda、不合格品重复的Muda、动作的Muda、加工的Muda、等待的Muda、搬运的Muda、时间的Muda。
1.可视管理消除浪费;2.及时生产方式(JIT)消除浪费;
语句摘抄:为什么大多数企业领导者理解这一点并真正实施精益是如此之难。不幸的是,这个问题并没有什么简单的答案,因为一个基本的事实是:大多数人不愿意改变,而实施精益意味着大规模的改变(几乎所有的工作都需要改变),如果你想获得真正的成功。 我们应如何将明天的工作做得比今天更好。 解决问题唯有依靠生产现场——大野耐一
MTP教会了数代日本管理者中的很多人三件要事: 人际关系及员工参与的重要性。
持续改善工艺和产品的方法论及其价值观。
科学合理地运用“计划-执行-观察”循环步骤,来对人员和生产进行管理。 丰田生产系是文化驱动的,需要相互尊重和相互信任。 现场必须管理的事项:生产力、成本降低、安全、人员训练、改善活动、5S、提高员工技能、质量、生产停线次数。
每次改善的改变,当你说出来的时候,这些改变听起来可能非常厉害,但是对你的员工来说,这些也很可怕。很多年来,他们一直都在用这种方式处理问题,所以他们坚信这就是处理问题的唯一方式。所以他们一定会反对这种改变。因此我们要做到以下几点:让精益成为企业的战略;亲自实践,做一个改善狂人;确保所有员工都清楚,他们必须接受改善文化;迅速果断的执行改善行动;亲自去现场,并向各种层级的员工展示该做的事情;基于积极推行精益的前提设定企业的绩效衡量指标体系,即使它们不能在短期内实现;做好企业大翻新的准备,无论阻力有多大,无论有多少理由可以被用来作为某种目标不可能“在我们企业实现”的借口;摒弃那种过度分析过去的评价体系,而应采用简单、客观的评价指标来提升企业绩效。有可能的话,采用当下最先进的精益生产技术,并且持续不断地向他人学习。
企业目前所处阶段的转变,就是从“只要生产就能销售的时代”转变为“只有顾客择的商品才能售出的时代”,也就是从“成长时代”进入了“成熟低成长时代”,品质的保持、提高和有竞争力的成本是企业发展的必要条件,考虑到市场竞争,销售价格必须要定到多少,必要的利润是多少,于是相应的成本必须要降低到多少。随着市场的变化,产量要发生变化,对品质的要求也很苛刻,顾客还要求缩短交货期,生产部门在应对这些问题上发挥着巨大作用。因此,以消减成本为目标的现场改善,势在必行.自本世纪六十年代以来,一些主要工业发达国家普遍对现场管理予于高度重视,取得了明显的效果,日本在这方面尤为突出。如日本丰田汽车公司长期致力于现场管理的研究与改进,形成了以丰田生产方式为代表的丰田现场管理模式,从而获得了高效率、低成本和强劲的竞争实力,这也是丰田汽车公司之所以能够成为世界第二大汽车公司的原因之一。在日本企业现场工作过的人会有深刻的体会,你的上司永远不会满足于你已经取得的进步和成就,你会被许多无形的鞭子不停的鞭策去努力,再努力,因为日本企业管理者认为:“现场改善是没有止境的,还存在许多可以改善的地方”。日本企业的现场改善一般按照5S改善、职责明确化、消减副产品、效率改善等几个步骤展开一轮又一轮的改善活动。同时管理者对于每次改善活动效果的要求并不太高,每天一点点进步也会令他们感到欣慰,只要他们一直在永无尽头的跑道上前行。
日本企业从上到下都非常关注现场管理,许多日本企业的高层决策人员,营销、采购、计划、研发等职能管理部门的负责人大多数从优秀的现场管理人员当中提拔。日本企业现场管理的精髓不在于其拥有先进的管理理论和管理制度,而在于他们的生产现场具有大批的实干家,不断去解决现场发生的问题,日式现场管理的严谨、刻板作风有时让人难以忍受,但不得不承认它确实非常有效。日本企业现场管理具有人性化、封闭式、定量式、高效性等特色。日本企业现场管理的许多做法和管理手段值得我们去学习、去借鉴,同时日本企业现场管理的成果也验证了其生命力。中国具有与日本不同的经济结构、不一样的社会环境和差异化的文化背景,许多日本企业很好的现场管理手段和管理观念在中国企业可能行不通,甚至根本不适用,但我们可以从中得到一些有益的启示。
改善之路,始于现场:原来管理的起点来自于现场改善;打开了工作思路;明白了领导不厌其烦的培训、检查的用意;从中学习的方法有种跃跃欲试的冲动。
推荐第3篇:《现场改善》读后感
读过很多精益管理类的书籍,还是被《现场改善》书中的精益思想所触动,感想颇深。作者金井正明是鼎鼎大名的质量管理专家,他在书中解释了如何运用常识性、低成本方法管理现场,也就是将常识付诸实践,正是此书的精髓。
有些管理者原本可以用常识性、低成本方法解决问题,却经常尝试应用各种复杂的工具和技术并花费太多的精力用于\"传授\"知识,而忽视了从由常识、自律、秩序和经济性等驱动的基本价值体系中进行团队学习。通过这本书,学习优秀的管理者在追求\"精益管理\"的过程中,如何努力带领整个公司去学习这些价值观,实现现场改善,从而实现成本降低、质量改进以及客户满意度提升。
现场改善的目标是什么?
作者认为,在质量、成本等主要的目标中,质量永远应该被放在第一位。无论提出的价格和交付条对客户说多么有吸引力,如果产品或者服务本身的质量不佳,公司就不可能赢得竞争。这也印证了在线总部全面推进\"品质领先\"战略的正确性和重要性。服务品质是我们公司的生命线,以客户为中心,推进服务质量责任制,狠抓人员解决问题能力的提升,夯实投诉运营基础,全面深化质量管理体系,持续做优10086热线服务,打造优势服务窗口形象和口碑,打造\"品质领先\"新局面。
现场改善的原则是什么?
作者强调,企业要维持一个稳定而有长远眼光的改善方面,公司里的每个人都必须一起努力,遵循现场改善三个最基本的法则:环境维持、浪费消除、标准化。
环境维持是好管理不可缺少的成分,借由环境维持,使员工从学习到实践到自律。没有自律的员工,就不可能提供质量良好的产品和服务给客户。标准化,维持标准是在每一个工序上保证质量和防止错误发生的方法,这也是我们为什么要制定严谨的服务规范、明晰的流程制度,并要求所有员工按规范执行的原因。浪费即是指不能创造附加价值的所有行为,我们所需要做的,就是去现场,观察话务员接线的情况,发现浪费,然后采取行动消除它。
我们要怎么做?
现场管理的金科玉律告诉我们,作为管理人员,(fsir)不能只把办公室当作工作的场所,只是通过每天、每周甚至每月一次的报告和会议,接触和了解现场的实情。管理者要与现场保持密切的接触及了解,当问题(异常)发生时,先去现场,是有效管理生产线的第一步。好好看看问题现场的现物,反复问\"为什么\"找出问题的根,这样能够当场并且及时地解决许多与现场相关的问题。最后在确定解决问题的方式有效之后,将新的工作程序予以标准化,以确保不会因为同样的原因再次发生问题或降低问题发生的影响程度。
总的说,本书的核心价值理念可概括为两点:
一是关注过程。改善要持续渐进的去做,不能急功近利的粗放经营,更不能一触即发高风险创新;现场是随地随处,用新的方式看待自己工作的技能以及改变自己工作方式的技能,逐渐地实现精益管理;
二是以人为本。\"现场改善\"的主体是\"员工\",只有\"员工\"认同了现场改善的重要性和好处,主动参与和开展一系列改进工作方法的改善活动,才能实现质量、成本最优的目标,实现效益最大化的目的。因此,员工的努力、士气、沟通、训练、团队、参与及自律等至关重要。
\"纸上得终觉浅,绝知此事要躬行\"在市场竞争日趋激烈今天,想要在自己的领域成为领先者,应当持续自问:我们应如何将明天的工作,做得比今天更好?
推荐第4篇:现场改善(考试)
太业《现场改善》培训试卷(2012年)
一、填空题(25空,每空1分,共25分)
1、企业的改善活动,目的在于改善 QCD及确保安全。前者指的是质量、成本和交期。
2、标准化、5S (厂房环境维持) 及 消除浪费 为常识性、低成本现场改善三大支柱。
3、“在与管理人员谈话中,假使在前5-10分钟之内能听到‘改善’和‘现场’的字眼,便可论定这是一家好公司”。
4、发掘现场原因的最有效方法之一,就是持续地问“为什么”,直到找到问题的原因为止。此过程有时亦称为“问5次为什么”。
5、“标准”的其中一种定义,是指“做事情的最佳方法”。
6、质量,狭义而言,是指产品或服务的质量;广义而言,是指产出这些产品与服务的工作和过程的质量。我们可称前者为“结果面”的质量,后者为“过程面”的质量。需要谨记的是,没有后者就没有前者。
7、开发一个新产品或设计一个新流程的工作,是先由书面作业开始的。在书面阶段,严格地进行设计评审,可以大大提升质量、降低成本和加快进度。
8、现场里,管理人员必须管理的5个M是指:人员( Manpower )、机器(Machines)、材料(Material )、方法( Methods) 及 测量( Measurement )。
9、现场之屋需建立在员工参与的基础上。现场之屋的根基包括:团队合作、提高士气、自律、质量圈、提案建议制度及可视管理。
二、名词解释(共6题,每题2分,共12分)
1.PDCA:计划、执行、检查、行动的循环。行动是指根据检查结果,进行方法和流程的完善并标准化。
2.SDCA:标准化、执行、检查、行动的循环。行动是指根据检查结果,进行方法和流程的完善并标准化。
3.QCD:指质量、成本和交期。
4.TQM:全面质量管理。强调全员参与,推进总体绩效及质量的改进。 5.JIT:及时生产方式
6.TPM:全员生产保全。通过总体的预防保养制度,来延长设备的寿命,以追求设备效率的最大化。
三、简答题(共36分)
问题1:现场管理的五项金科玉律是什么?(5分) 1)当问题(异常)发生时,要先去现场; 2)检查现物(有关的物件); 3)当场采取暂行处置措施; 4)发掘真正原因并将之排除;
5)标准化以防止再发生。
问题2:厂房环境维持的5S,内容是什么?(5分)
1)整理:将现场里需要与不需要的东西,区别出来。并将后者处理掉; 2)整顿:将整理后需要的东西,安排成为有秩序的状态; 3)清扫:保持机器及工作环境的干净;
4)清洁:延伸干净的概念至自己本身,并且持续执行上述3个步骤; 5)素养:以设立目标的方式,来建立自律以及养成从事5S的习惯。
问题3:JIT 生产方式有哪些基本观念?(6分)
1)节拍时间(生产一个产品的理论时间)与周期时间(生产一个产品实际耗费的时间 ) ; 2)单件流(在每个流程里,仅允许加工一个产品、流动一个产品 ); 3)后拉式生产(依据后流程的需要量生产); 4)自动化;
5)U型细胞式生产线; 6)缩短换模时间。
问题4:现场7大浪费是哪些?(7分) 1)制造过多的浪费; 2)存货的浪费;
3)不良重修的浪费; 4)动作的浪费; 5)加工的浪费; 6)等待的浪费; 7)搬运的浪费。
问题5:为成功地达成改善目标,主要推行的改善活动有哪些?(6分) 1)全面质量控制/ 全面质量管理(TQM); 2)及时生产方式(JIT); 3)全员生产保全(TPM); 4)方针展开;
5)提案建议制度; 6)小集团活动。
问题6:要实现现场成本降低,必须同时实施哪7项活动?最重要的是哪一项?(7分) 1)改进质量; 2)改进生产力; 3)降低库存;
4)缩短生产线;
5)减少机器停机时间; 6)减少空间;
7)降低生产交期;
其中以改进质量为最重要。
四、问答题(共27分)
问题1:学习《现场改善》课程后,从现场管理的角度,你认为提升太业产品质量的基本思路和做法是什么?(8分)
首先要检查现有程序,询问如下问题: • 我们有标准吗?
• 现场的环境维持(5S)做得怎样? • 现场里有多少浪费存在? 然后,开始采取行动,例如: • 推行现场的五项金科玉律。
• 训练员工,承诺不将不合格品送到下一流程。 • 鼓励团队活动及提案建议制度以解决问题。
• 搜集资料,以获取对问题的性质有更多的了解并解决之。
• 开始制作简单的夹具及工具,使工作更容易做,结果更可靠。
问题2:在你的理解中,太业推行5S活动的好处有哪些?(7分) • 创造清洁、卫生、舒适及安全的工作环境。 • 提高员工士气。
• 协助员工养成自律的习惯; • 消除现场的浪费。
• 显现出异常现象,诸如不合格品及过多的库存、材料短缺、生产线不平衡、机器故障及交期延误的问题,以便解决。 • 有助于安全,减少工业意外事故。 • 有助于全员生产保全(TPM)。
问题3:针对5S、SDCA/PDCA和消除浪费三个改善支柱,就公司或部门现存需要改善的地方,试各举两例。(12分)
推荐第5篇:现场改善术语
现场改善术语解说
u 允收品质水准(AQL) Acceptable Quality Level 允收品质水准是顾客与供货商之间的交易运作模式.容许供货商在协议的条件下, 交付某一限定比率的不良品.v 问五次为什么(Ask why five times) 一个发掘问题真正原因的常识原则.w 查核现场(Check gembutsu) 当欲探寻问题的根源时, 在现场实地有形的物体加以调查.x 符合性(Conformance) 用以表示产品或服务能达到相关规格、合约或规则, 所要求的一个确定指示或评定.y 管制图(Control Chart) 为一个具有上下管制界线的图.在其图上, 绘有一系列的样本或样本组统计量的测定值.此图通常绘有一条中心线, 用以协助侦测所绘之统计值, 有否趋向其中之一条管制界线.z 成本-----Cost 在QCD的范畴中, [成本]一词通常系指成本管理,而非削减成本.成本管理涉及到对各种资源的适度管理, 以及消除所有类别的无驮(浪费).在此种方式下, 会降低总成本.{ 跨功能(部门)管理----Cro-functional management 为达成QCD跨越部门之间的管理活动.| 周期时间----Cycle time 作业员完成加工一个产品的实际耗费时间(参阅产距时间Takt time).} 交期----Delivery 在QCD的范畴中, [交期]一词系指交货时间以及数量, 皆要符合顾客的要求.~ 不按受, 不制造, 不流出----Don’t get it, don’t make it, don’t send it.在现场里推行的一个常识性口号.在任何一个QCD计划中, 应将品质是最优先的信念予以实践出来.例如: 不要从上制程接受不良品, 不要在自己的制程上制造出不良品, 以及一旦有不良品制造出来, 不可明知故犯地流到下一制程.uu 失效树分析-----Failure Tree Analysis(F T A) 借着确定因果关系及利用树关图, 来认定问题的机率.失效树分析是用来分析及事先避免任何安全性及可靠度上的问题.uv 现场管的五项金科玉律----Five golden rules of gemba management 一套在现场推行[现场改善]时,最实用的提醒剂..(1) 当有问题发生时[要先去现场].(2) 检查现物.(3) 当场采取暂行处置措施.(4) 发掘真因并排除.(5) 标准化以防止再发.uw 5M----Five M’s
在现场用以管理资源的方法.这五项资源皆以英文[M]开头, 特地称之为[5M]----人员
(Manpower), 机器(Machine), 材料(Material), 方法(Method)和量测(Measurement).ux 5S----Five S’s
是一种为维持良好工厂环境的查核表, 为使工作场所更有秩序, 效率及纪律.它源自于五个有S音开头的日文----Seiri(整理).Seiton(整顿), Seiso(清扫), Seiketsu(清洁),Shituke(教养).套用英文相当之字则为Sort(分类=整理), Straighten(定位=整顿), Scrub(刷洗=清
扫), Systematize(制度=清洁)及Standardize(标准=教养).某些分司则采用为5C作战..Clear out(清除=整理),Configure(形迹=整顿), Clean & check(清洁及检查=清扫), Conform(遵守=清洁)及Custom & practice (习惯及实践=教养).uy 流线生产----Flow Production 及时生产方式的基本支柱之一.在流线生产里, 机器是依据加工的顺序排列.如此, 工作物在制程之间的流动, 就不会中断或停滞.uz 失效模式及有效性分析----FMEA 借着分析零组件对最终成品失效模式的影响结果; [失效模式及有效性分析]可以用来对一个新产品的作何潜在的设计缺点, 做事前预测及消除.FMEA也可用来针对新生产设备的役计审查活动(叫做制程FMAA) u{ 现场----Gemba 日文一词意指[实地], 现在则采用管理上的术语, 意义为[工作场所], 或者称之为[产生附加价值]的地点.在制造业来说, 通常系指[工场].u| 现物----Gembutsu 在现场里所发现的有形对象.例如: 工作物, 不良品, 夹具, 工具, 及机器.u} 去现场----Go to gemba 现场改善的第一项原则, 这是一个提醒剂.不管何时, 当异常发生或经理人员欲了解生产作业的现状, 他(或她)应立即去现场, 因为现场是所有信息的来源.vt 海因利奇法则----Heinrich’s Law 一项有关于意外事故与伤害的比率法则.海因利奇用下列的比率表示之: 重度伤害: 轻度伤害: 无伤害=1:29:300此公式表示: 当你看到一个因意外事故重伤的人, 同样的事故可能也造成二十九人的轻微伤害.同时, 或许有三百人经历同样的事故, 但幸运地没有受到伤害.vu 危险预知训练----Hiyari KYT(Kiken-yochi training) KYT系指对预见的危险做事前演练, 并且采取预防的措施.vv 惊吓报告----Hiyari report(Scare report) 惊吓报告, 是由工人写给上级主管的报告.用以报告会造成品质问题及/和意外事故的不安全状况.vw 石川(鱼骨)图----lsikawa(fishbone)diagram 由石川声教授首先发展出来的图表.用来表示原因(制程)及影响(结果)的关系.此图系用来确定真因, 同时也是解决问题的七种基本手法之一.vx 国际标准组织9000系列标准----( ISO 9000 Series standards) 一套关于品质管理及品质保证的国际标准规范.此套规范用以协助公司对品质体系应执行的要件, 做好文件的管理, 以确保符合产品的规格要求.vy 自动化----Jidhoka (Autonomation) 每当不良品制造出来时, 能使机器自动停止下来的一种装置.此装置是JIT导入的要点.vz 自主研现场改善----Jishuken gemba kaizen 在一九六零年代初期, 自主研(自主的JIT研究小组)首先在丰田集团的公司的现场, 开始推?蠮IT的活动.v{ 及时生产方式JIT----(Just-in-time) 藉由在公司内, 消除流程间所有各种的无驮(浪费), 并以及时送达货品以符合顾客的要求,来达成产品或服务的最佳品质, 成本及交期的一种生产体系.最早是由丰田汽车公司发展出来, 亦称为丰田生产体系(Toyota Production System), 精实生产方式(Lean production system)及看板生产方式(Kanban System) v| 自主管理----JK (jishu kanri) 自主管理的日文意思为自动自发管理之意.系指工人在其上级管理人员的指导之下, 将参与改善活动视为日常工作的一部分.此与品管圈活动有所不同, 后者系自原性并由工人依自已的意志进行.v} 改善观念----Kaizen concepts 在推行改善时, 所必须了解及关践的主要观念.(1) 改善与管理.(2) 改善与结果.(3) 导守P D C A 循环/SDCA循环.(4) 品质第一.(5) 用数据说话.(6) 下一制程就是顾客.wt 改善事例----(Kaizen Story) 用于组织各层级中的一种解决问题之标准程序.改善事例分为八大步骤: (1) 主题选定.(2) 现况调查及目标设定.(3) 资料分析以确定真因.(4) 对策拟定.(5) 对策实施.(6) 效果确认.(7) 标准化.(8) 检讨上述过程及未来计划.wu 改善活动体系----Kaizen systems 欲达成世界级所必须建立的主要活动系.(1) 全面品质管理(Total Quality Management) (2) 及时生产方式(Just-in-time production system) (3) 全员生产保全(Total Productive Maintenance) (4) 方针展开(Policy Deployment) (5) 提案建议制度(Suggestion System) (6) 小集团活动(Small-group activities) wv 看板----Kanban 在及时生产方式中, 用以管理批量生产的一种沟通工具.看板, 在日文里系指一种信号板, 挂附在生产线某一已知号码的零件或产品上, 并指示运送某一已知的数量.当这些数量的零件用完之后, 此看板即送回原处, 变成生产指示, 以再生产.ww 工数----Kosu 生产作业, 可区分为机器的时间和人员的时间, 工数系指在一已知的制程中, 完成一个产品的加工动作所耗费的人员时间.是将此一制程的工作人数, 乘上实际完成此制程的时间, 再除以所生产的产品数量, 用来衡量作业员的生产力.工数降低是在现场生产力改善的主要衡量方式之一.wx 晨集----Morning market 在现场中的[每日例行工作], 包含在工作之前依据现物原则, 检查前一天所做的不良品(现物), 如此才能尽早采取对策.此一包含现场人员的(而非职员)会议, 是在早上开工时的第一件事.wy 无驮----(浪费)Muda 日文一词意指[浪费].当使用在工作场所的管理时, 泛指没有附加价值的活动.在现场里,仅有两种型态的活动: 有附加价值和没有附架价值.在现场改善中, 首先致力于消除各种没有附加价值的活动.消除下列范围的[无驮], 期使对Q C D产生重大的改善: 生产过多, 库存, 不良品, 动作.加工.等待.搬运及时间.无驮的消除即是以低成本, 常识性的方法, 来求改善的缩影.wz 无稳----Mura 日文意指不规律或变化性.w{ 无理----Muri 日文意指过劳性或困难性.w| 一个流----One-Piece flow 在及时生产方式里, 仅允许每次将一个产品从此制程流到另一制程, 使无驮最小化.w} 柏拉图----Pareto chart 将原因从最大影响度, 依序排至最小影响度的一种图表工具.它是依扰[柏拉图原理]而来, 是由品管大师裘兰博士(J.M.Juran)订定出来的.此80:20原则, 指出[80%的结果, 是来自于20%的原因所造成].柏拉图为解决问题的基本七手法之一种.xt PDCA----Plan-Do-Check-Action 计划—执行—查核—外置, 是从事持续改进(改善)所应遵行的基本步骤.xu 后拉式生产----Pull Production 及时生产方式的基本要件之一, 前制程仅补充生产后制程所耗用掉数量的产品.xv 前推式生产----Push Production 后拉式生产的相反词.前制程尽其所能生产愈多的产品, 欲不顾及后工程实际上的需求数;并且不管是否有所需求, 全部将之送给后制程.xw 品质保证最佳生产线证书----QA Best-Line Certification 一种厂内的认证制度.用以证明某一特定生产线, 其品质保证的成效达到世界级水准.xx QCD----(Quality, Cost, Delivery) 品质, 成本及交期, 被视为管理的首要目标.当管理能成功达成QCD的目标时, 则顾客的满意及企业的成功, 也会随之而来.xy QCDMS 在现场里, 经常将M士气(Morale)及S安全(Safety)加入QCD, 做为欲达成的目标.xz 品质机能展开----QFD (Quality Function Deployment) 一种管理的方法.首先先确认顾客的需求, 然后经由各个阶段对产品展开下去: 设计, 工程, 生产, 销售, 及售后服务.x{ QS 9000 美国版的ISO 9000系列.由三大汽车公司要求施行于其供应厂商.与ISO 9000系列之一般要求来作说明比较, QS 9000明定一些额外的要求, 特别是对标准及矫正行动, 要求持续地改进 x| 品质----Quality 在QCD的范畴理, 品质系指送达至顾客的产品或服务的品质.在此状况下, 品质是指符合规格和顾客的要求.广义而言, 品质包含产品或服务的设计, 生产, 交货及售后服务工作的品质.x} 品管圈----QCC(Quality Control Circles) 由一小群员工(十人或以下)组成, 以从事品质改善或自行改善的研究团体.品管圈导源自日本, 被称为品质管制圈(品管圈).品管圈是在工作场所, 自原地执行改善活动, 持续从事一部
分全公司性的相互教育.品质管制, 自我发展及生产力改善的计划.yt SDCA----Standardize-Do-Check-Action 标准化—执行—查核—处置, 是在维持现关时, 应当遵行的基本步骤.yu 同时实现QCD----Simultaneous realization of QCD 最高管理阶层应清楚公司内, 所有的阶层都是致力于过成品质, 成本及交期之工作任务.最终的目标是QCD能同时实现.但是, 三者之间首先要实现的, 仍应以品质为第一优先.yv 小集团活动----Small-group activity 为解决他们自己作场所的问题, 而形成的现场集团活动.通常由现场的作业员五~十人组成集团.他们的活动大都与品质圈活动类似.然而小集团活动并不仅限于诸如品质改善.降低成本, 全员生产保全(TPM)和生产力改善, 同时也扩及到娱乐性或其它社交性活动.yw 标准化----Standardization 标准化为现场改善三项基本活动之一, 意指将工作的最佳方式予以文件化.yx 标准作业----Standardized work 人员, 机器和材料的最佳组合状况.标准作业的三要素是产距时间, 作业顺序和标准在制品数量.yy 标准----Standards 工作的最佳方式, 即是由管理当局针对分司所有主要的业务, 设定一套方针, 规则, 指示及程序书, 作为全员执行其工作的指导, 以求获致好的成果.yz 统计制程管制----Statistical proce control (SPC) 应用统计尝上的技巧, 以管理控制制程.有时亦经常与统计品质管制互用.y{ 储存室----Store room 在现场用以储存在制品或物品的场所.储存室与一般的仓库是不相同的, 因为在储存室里, 仅能保存标准的储存量.y| 提案建议制度----(Suggestion System) 在日本, 提案建议制度, 是高度被归属于个人导向改善活动的一种方式.日本式的提案建议制度, 着重于激发员工工作士气, 和建设性的参与感, 它远甚于欧美对形能的注重以经济上及金钱上的奖劢.y} 产距时间----Takt Time 完成生产一个顾客所订产品的所需时间.是以总生产时间, 除以生产需要数而订定出来的.zt 3K 日文用来表示在现场里惯见的印象----危险( Kiken ), 脏污( Kitanai )和劳累(Kitsui), 与此形成直接对比的, 是理想的现场, 为一个能附加真正价值, 以及达成QCD构想来源的场所 zu 3M 指无驮(Muda----浪费), 无稳(Mura)和无理(Muri).这三个字词常用来当做改善的查核点, 协助工作人员及管理当局, 以确认可供改善的地方.zv 在现场的3M----Three M’s (3M) in gemba 在现场三个主要需加以管理的资源----人员(Manpower), 材料(Material)和机器(Machine).有时再加上方法(Method)和量测(Measurement)而称为5M..zw 全员生产保全----TPM ( Total productive maintenance) 全员生产保全, 是意图在机器的整个寿命期内, 获取最大设备效率的发挥.TPM牵连到所有部门各个层级里的每一个人, 它透过小集团和自主活动, 激劢员工从事工厂的保全活动.它包含如下的基本要件: 保全体系之发展, 基本的厂房环境维持教育, 问题解决技巧, 和零故障及现场零意外的活动.由工作人员所做的自主保全, 是TPM的重要支柱之一.5S则为TPM的第一步骤
zx 全公司品质管制----(TQC) Total Quality Control 为品质而组成的改善活动, 包含了公司的每一个人----管理人员和工作人员, 以整合总体的力量, 致力于每一个层面的改善.它设想这些活动, 最终将获致顾客满意度的提升企业经营的成功.在日本, 使用全面品质管理TQM(Total Quality Management)为名词已相当普遍, 现在已取代了TQC名词.zy 两天期现场改善----Two-Day gemba kaizen) 在日产汽车公司及其供货商内, 实施的现场改善活动.它是选定某一特定制程, 及由内部改善指导老师, 工程师和生产线上管理人员组成的小集团, 在现场里花费二天时间, 利用及时生产方式和其它有关的查核表, 以达成改善目标.zz 价值分析----Value Analysis 一九四七年, 由美国奇异电气公司麦尔斯(L.D.Miles) 所导入降低成本的方法.它着眼于上游阶段的产品设计及设计审查, 如此能降低材料和零件的成本.它包含了产品设计, 生产工程, 品质保证和制造等跨功能(部门)的合作.VA也被当做提升竞争力标竿.z{ 价值工程----Value Engineering(VE) 一九五四年, 由美国国防部所发展出来, 是一种降低成本的方法与运用的方式.在日本VA?蚔E几乎都被视为相同的目的(参看价值分析).z| 目视管理----Visual Management 一种有效的管理方法, 它以清晰可见的方式, 提供信息及现物给工作者和管理者, 以让大家能实时确认异常状况.
推荐第6篇:现场改善读后感
读《现场改善》有感
最近领导给我推荐了一本书——《现场改善》,在这里首先感谢领导对我的信任,让我有机会充实自己。在工作之余,我细细品读了这本书,读完以后受益匪浅。
首先谈谈现场改善这几个字的简单意思:
“改善”在中文里有两个意思:一是改正过失或错误;二是改变原有情况使其比较好一些。当我们把改善与企业联系在一起的时候,它就变成了一种企业经营管理的手段和思想。牛津英文词典将“改善”(Kaizen)定义为:一种企业经营理念,用以持续不断地改进工作方法和人员的效率等。而这个词汇是来自于日语,其含义是指持续不断地改进。虽然改善的步伐是一小步一小步、阶梯式的,但随着时间的推进,它会带来戏剧性的重大成果。同时,改善也是一种低风险的方式,因为在改善的过程中,如果发觉有不妥当之处,管理人员随时都可回复到原来的工作方法,而不需耗费大成本。
“现场”(Gemba) 指的是实际发生行动的场所,但是通常我们所指的现场,是狭义的现场,是指制造产品或提供服务的地方现场,可以简单地说为工作场所。现场不仅是所有改善活动的场所,也是所有信息的来源地。现场(Gemba)、现物(Genbutsu)、现实(Genjitsu),称之为三现主义,具体是指当发生问题的时候,要亲临现场,亲眼确认现物,认真探究了解现实,并据此提出和落实符合实际的解决办法和措施。
“现场改善”:综上所述,现场改善就是对工作场所的所有要素进行改良和优化,以提高效率、质量及降低成本的活动。
读完这本书,我发现作者的思想境界和管理思想超前而又实际,他通过点滴的小事解答了一个个复杂的问题,言简意赅,把不断改善的思想融入到了日常管理中。讲解了很多难以理解的概念,强调了人在现场管理中的作用,而我认为本书最大的精华就是阐明了降低成本惟有依靠生产现场的理念。
作者认为,提升质量的改善焦点是在企业运营中产生的,最具关键性的地方是现场,也就是实际发生行动的场所。所有企业都得从事三项赚取利润的主要活动:开发、生产和销售。若缺少这些活动,公司便无法生存并获长远发展,而现场正是这三项活动发生的场所。“现场改善”与欧美管理方式的最大不同处,在于不需要复杂的技术、烦琐的程度和昂贵的设备,只要透过全面质量管理、及时生产方式、可视管理等,便能轻易解决组织积弊,获得高水平的质量和巨额利润。
但在公司内进行现场管理应该说是非常困难的一件事,究其原因主要是大家对现场管理的作用不理解。每当有客户考评或公司检查时,各部门、车间、科室就开始进行现场整改,每个人似乎都知道了5S中“整理、整顿、清扫、清洁、素养”的含义,当客户离开或公司检查结束,大家似乎有了一种搞运动的感觉,一切又回归于原样。
而作者提出现场管理的目的是为了降低成本,认真理解作者的理念,发现他是多么的有见地。成本管理是公司提的最多,做的最差的工作,究其原因是我们没有理解作者所提的改善的思想。降低成本的精髓在于坚持改善,日复一日,年复一年的坚持改善,把功夫下在平时,不能在提出降成本的时候,搞一份“成本降低计划表”,通过数学公式计算出降低成本的金额,如果没有认真的不停改善,即使算得再准确也没有任何实际意义。
真正降成本就如作者所言“遵守既定的事”,做好本职工作,对本职工作不断提出疑问,不断改进,成本自然就会降低。最怕的是搞形象,搞运动,华而不实。正如张瑞敏先生所言“什么叫不简单,把一件小事千百万次做好就是不简单。”当你把本职工作做到极至,可能任何问题都得到解决了。
朴实的语言,简单的案例,包含的确是现场管理的精华。《现场管理》一书,这次读完有很深的感触,想不断提高,唯有多读,多想,多做。
推荐第7篇:现场改善读后感
现场改善读后感
从2007年工作以来,就开始接触现场改善,但都是针对一些具体的案例,从来没有像《现场改善》这本书这么系统,详细的来介绍现场该如何改善。2016年是东风新汽艰难的一年,也是值得纪念的一年,我们提出了以“三个中心”作为核心的管理理念,其中就将现场改善作为重要的一环。下面我就谈谈我对现场改善的看法吧:
现场改善顾名思义就是针对现场的改善,包含了两次含义一层是现场,另一层就是改善。两者相辅相成,互相照应。现场就好比我们工作的场地,不管是一线工人,还是高管总工,都有自己的一个现场,只不过是场地不一样罢了。而改善则是我们对工作的认识和理解,改善进行的越深,则对我们的工作认识和理解的越深。
现场改善具有一定的环境性。改善良好的生产和生活环境是提高生产效率的重要保证,是良好管理不可缺少的部分。现场改善必须要从最基础做起,最基础的就是5S,虽然从表面上看5S和我们的工作不怎么相干,但是5S却是一个企业成功的奠基,通过5S管理可以使得我们的现场整洁,养成员工良好的工作习惯,与此同时可以使得我们的安全管理很好的落实,5S是现场管理的重要一环。
现场改善具有一定的成本性。在企业生产中,如何低成本运营是一个企业能否产生更多利润的关键,要想把一个企业做好,实现其利润最大化,寻找更大的发展空间和发展前景,必须要消除浪费。结合七大浪费和企业家的十二把财务砍刀,使得我们杜绝和减少不必要的
浪费,把每一份资金都用到企业需要的地方去。
现场改善必须要坚持标准化作业。标准化是一个企业能否做到同质的重要保证。当然标准化并不仅仅指生产标准化,还包括我们管理的标准化,生产的标准化可以使得我们的产品更具有竞争力,而管理的标准化可以使得我们更规范,效率更高。
现场改善要有一颗改善的心。改善的目的并不是为了单纯的改善,那只是改善的起点。改善的延续是为了更好的支持生产,而改善的最高境界就是人人都有一颗改善的心,人人都在改善。当然改善不分大小,只要是改善都有其独特的魅力,只不过是释放的时间和延续性不一样罢了。做为一个企业人, 从企业的每一个细节做起,让企业上上下下都充满改善的理念,只有这样的企业才是充满活力的企业,因为改善可以改变现场,改变现场可以提升企业管理,提升企业管理可以增强企业活力,增强企业活力可以使得企业更好的创新,而成为一个创新的企业则是每一个企业不懈的追求。
拜读今井正明的《现场改善》一书,使得我对现场改善又有了更近一步的认识,书中提供的方法将帮助我们改进质量和安全,减少等待次数,防止浪费,进而改进企业的盈利能力;该书还让我们更好的认识到了如何兼顾质量、成本、交货期这个“铁三角”难题。
总之,现场改善作为一个企业的核心之一,它有着自己独特的魅力,它让人更好的认识到了一切皆有可能,改善是没有止境的,没有最好,只有更好,并且改善要根据自己企业的实际情况来制定总体的改善方略,不能照葫芦画瓢,照搬别人的东西。我们要根据自己的情
况来制作自己的衣服,衣服合不合适只有自己知道,不合适的衣服那怕是名牌,也只是费布一块。
用自己的心,走自己的路,带着自己的梦想,开始吧!
推荐第8篇:现场改善学习心得
现场改善学习心得
现场改善讲的内容是生产现场的改善,但是其中涉及到领导力也可以说是人际关系的问题,并且其重要程度不亚于专业技能,能否做好现场改善工作的一个关键问题是能否和相关的工人和领导协调沟通好,让他们支持你的方案并配合执行。这是目前中小型企业存在的一个严重的问题,即改善行动浮于表面。大多数工厂的现场5s仅仅只是为了应付检查就像学生寝室应付学校检查一样,人一走就恢复了脏乱差的原样。改善要求全员参与,改善的意识必须深入每个人的骨髓里,企业的改善才能有效地持续地进行。要树立全员改善意识是IE工作者重要且艰难的课题,因此要从事现场改善工作还要学习提高领导力的技能,对于我来说,我想想都觉得难,上了课才知道理想和现实的差距。
另外,老师一直强调创新,对现有教学模式的探讨,让我意识到目前传统的教学模式是多么低效率且高成本的,不管是对学校、教师还是学生都是如此。近几年,越来越多的网上教育出现,我自己也有买过便宜的课程,觉得非常的好,不限人数,不限时间、地点,学生还可以多次重复观看,我想随着网络课程的普及,传统的教学势必受到打击,如果再不实行改革就是在浪费资源。虽然这是一项艰巨且长远的任务,但是好像现状一直维持了好多年,学生学习的积极性不高的问题一直没有解决,也没有人去解决。
浪费无处不在,改善永无止境。总之在工业工程专业学了不少知识,虽然专业知识掌握的不怎么好,但意识算是有点了,本身对自己要求也不高。最后,非常感谢孙老师的敦敦教诲,让我们明白社会的现实,也非常喜欢老师轻松随性的教学方式!
推荐第9篇:现场改善读后感
现场改善读后感
(一):低成本高回报
冯文亭
首先谈谈现场改善这几个字的简单意思。\"现场\"指的是实际发生行动的场所,但是通常我们所指的现场,是狭义的现场,是指制造产品或提供服务的地方现场,可以简单地说为工作场所。现场不仅是所有改善活动的场所,也是所有信息的来源地。\"改善\"在中文中的解释是一是改正过失或错误;二是改变原有情况使其比较好一些。\"现场改善\"综上所述,现场改善就是对工作场所的所有要素进行改良和优化,以提高效率、质量及降低成本的活动。
现场的作业流程,环境状况直接关系最终产品的产能和质量,所以虽然改善的步伐是一小步一小步、阶梯式的,但随着时间的推进,它会带来戏剧性的重大成果。同时,改善也是一种低风险的方式,因为在改善的过程中如果发觉有不妥当之处,管理人员随时都可回复到原来的工作方法,而不需耗费很大的成本。所以说现场改善是一种低成本高回报的管理方法。
《现场改善》以图解的方式简单易懂地介绍了生产现场应如何正确应用5S推进法、降低成本、改善生产流程、员工培训等等在现场方方面面的技术管理改善。那么这些方法如何和我们的项目开发相结合,达到低成本高回报的现场改善效果呢。下面先5S推进法为例,讨论一下项目开发中的信息管理改善。
所谓5S,说的就是整理、整顿、清扫、清洁、和素养五个元素。整理即对信息进行分类丢弃;整顿即分类后的摆放整齐;清扫即仔细清洗;清洁即维持,对前三个S所达到的成果进行维持保护。素养即对前面4S中所产生的一些规定的严格遵守。书中针对5S推进法的改善方法,举了一个关于车间物品摆放问题的改善问题。生产车间是生产活动发生的场所,自然而然会摆放很多生产零部件,产生工具。但是如果这些东西杂乱无章,随处乱放,不仅会会直接导致车间空间浪费,工人行动不便,更重要的生产是需要的零件无法快速及时找到,拖慢生产进度,影响生产质量。
其实我们的项目开发也会发生如同生产车间一样的状况。项目开发过程中,会产生很多相关的文书资料,联络邮件、电话等,这些载体包含的项目信息如果没有及时分类整理,会导致很多不良的后果。比如说来自用户的式样变更信息没有及时归档整理,对应状态追踪等,会导致项目后期系统发生问题时无法进行回溯调查,项目报价时候作业量统计遗漏等。
参考书中5S推进法改善车间物品摆放问题的例子,我们可以对项目开发中的信息管理做一些努力。首先是整理,对手头现有的信息或者在接受到信息的时点,对其进行分类整理。对分类后的信息建立专门的记录文档或者用工具管理起来。例如进度管理表,检收问题表等。接下来是整顿。分类后的信息记录要规整,比如用表格,或者工具自带的格式按照一定的顺序记录下来,以便后期查找。之后是清扫。清扫是保持整洁的机制。项目开发过程就是一个信息不断累积的过程。新信息出现的时候,比如说收到用户的反馈邮件,或者与客户的TV会议,就会产生与项目相关的信息,这个时候必须及时将这些信息按照前面两个流程进行处理,否则将会导致信息遗漏和丢失。清洁和素养是对前面三个环节的巩固和维持。要及时对项目成员强调5S的概念,推进和贯彻前面三个流程,让项目成员能够在收到信息的时候有分类整理记录的意识和习惯,并会切实去做,培养5S的素养。如果一个项目开发中能够做好这5个方面,那么会对项目过程中的问题调查,进度把握,问题对应时效起到有好的现场改善效果。
现场改善读后感
(二)
最近领导给我推荐了一本书——《现场改善》,在这里首先感谢领导对我的信任,让我有机会充实自己。在工作之余,我细细品读了这本书,读完以后受益匪浅。
首先谈谈现场改善这几个字的简单意思:
\"改善\"在中文里有两个意思:一是改正过失或错误;二是改变原有情况使
其比较好一些。当我们把改善与企业联系在一起的时候,它就变成了一种企业经营管理的手段和思想。牛津英文词典将\"改善\"(Kaizen)定义为:一种企业经营理念,用以持续不断地改进工作方法和人员的效率等。而这个词汇是来自于日语,其含义是指持续不断地改进。虽然改善的步伐是一小步一小步、阶梯式的,但随着时间的推进,它会带来戏剧性的重大成果。同时,改善也是一种低风险的方式,因为在改善的过程中,如果发觉有不妥当之处,管理人员随时都可回复到原来的工作方法,而不需耗费大成本。
\"现场\"(Gemba)指的是实际发生行动的场所,但是通常我们所指的现场,是狭义的现场,是指制造产品或提供服务的地方现场,可以简单地说为工作场所。现场不仅是所有改善活动的场所,也是所有信息的来源地。现场(Gemba)、现物(Genbutsu)、现实(Genjitsu),称之为三现主义,具体是指当发生问题的时候,要亲临现场,亲眼确认现物,认真探究了解现实,并据此提出和落实符合实际的解决办法和措施。
\"现场改善\":综上所述,现场改善就是对工作场所的所有要素进行改良和优化,以提高效率、质量及降低成本的活动。
读完这本书,我发现作者的思想境界和管理思想超前而又实际,他通过点滴的小事解答了一个个复杂的问题,言简意赅,把不断改善的思想融入到了日常管理中。讲解了很多难以理解的概念,强调了人在现场管理中的作用,而我认为本书最大的精华就是阐明了降低成本惟有依靠生产现场的理念。
作者认为,提升质量的改善焦点是在企业运营中产生的,最具关键性的地
方是现场,也就是实际发生行动的场所。所有企业都得从事三项赚取利润的主要活动:开发、生产和销售。若缺少这些活动,公司便无法生存并获长远发展,而现场正是这三项活动发生的场所。\"现场改善\"与欧美管理方式的最大不同处,在于不需要复杂的技术、烦琐的程度和昂贵的设备,只要透过全面质量管理、及时生产方式、可视管理等,便能轻易解决组织积弊,获得高水平的质量和巨额利润。
但在公司内进行现场管理应该说是非常困难的一件事,究其原因主要是大家对现场管理的作用不理解。每当有客户考评或公司检查时,各部门、车间、科室就开始进行现场整改,每个人似乎都知道了5S中\"整理、整顿、清扫、清洁、素养\"的含义,当客户离开或公司检查结束,大家似乎有了一种搞运动的感觉,一切又回归于原样。
而作者提出现场管理的目的是为了降低成本,认真理解作者的理念,发现他是多么的有见地。成本管理是公司提的最多,做的最差的工作,究其原因是我们没有理解作者所提的改善的思想。降低成本的精髓在于坚持改善,日复一日,年复一年的坚持改善,把功夫下在平时,不能在提出降成本的时候,搞一份\"成本降低计划表\",通过数学公式计算出降低成本的金额,如果没有认真的不停改善,即使算得再准确也没有任何实际意义。
真正降成本就如作者所言\"遵守既定的事\",做好本职工作,对本职工作不断提出疑问,不断改进,成本自然就会降低。最怕的是搞形象,搞运动,华而不实。正如张瑞敏先生所言\"什么叫不简单,把一件小事千百万次做好就是不简单。\"当你把本职工作做到极至,可能任何问题都得到解决了。
朴实的语言,简单的案例,包含的确是现场管理的精华。《现场管理》一书,这次读完有很深的感触,想不断提高,唯有多读,多想,多做。
推荐第10篇:工厂现场改善
在改善的范畴里,管理具有两项主要的功能:“维持”( M a i n t e n a n c e )与“改进”( I m p r o v e m e n t )。“维持”是指从事于保持现有技术、管理及作业上标准的活动,以及支持这些标准所需的训练和纪律。在“维持”的功能下,管理部门要执行工作的指派,使每一个人都能依照标准的作业程序来工作;而“改进”则是以改进现有标准为目标的活动。日本的管理观点,因此可以浓缩为一句箴言来表示:维持标准和改进标准。
改进可再区分为“改善” ( K a i z e n )和“创新”( I n n o v a t i o n )。所谓“改善”,是由于持续不断的努力,所产生的诸多的小步伐改进,而逐次累积而成。“创新”则是借助大笔资源投资于新技术或设备,而产生戏剧性的变化的改进(不论任何场合,以金钱作为主要的评估因素时,创新便是昂贵的)。由于欧美的管理人员执迷于“创新”,他们既没有耐心,也忽视了“改善”能长期带给公司的利益。相反,“改善”则是强调要以员工的努力、士气、沟通、训练、团队、参与及自律来达成目标。这些都是一种常识性和低成本的改进方式。
“改善”是着重在“过程为导向”的思考模式上,这是因为要改进“结果”,必须先改进“过程”。预期的计划成果未能达成,表示其“过程”是失败的。管理部门必须确认及改正这种“过程面”的错误。“改善”是着重在“人际面”上的努力,此种东方的改善形态,恰与西方的着重在“结果面”的思想,形成尖锐的对比。以“过程为导向”的思想方式,应当运用在各种不同的改善活动上,诸如:计划→执行→核查→处置( P D C A )的循环、标准化→执行→核查→处置( S D C A )的循环、质量→成本→交期( Q C D )的活动、全面质量管理( T Q M )及时生产方式(JIT)和全员生产保全(TPM)。许多公司改善活动失败的原因,就在于轻忽“过程”。在“改善”的过程中,最关键性的就是最高管理部门的承诺和参与。管理部门的承诺和参与,必须适时地、持续地表现出来,以确保在“改善”的过程中获得成功。
一,现场改善考虑下手的几个方面:
1、工艺流程查一查
即向工艺流程要效益。分析现有生产、工作的全过程,哪些工艺流程不合理,哪些地方出现了倒流,哪些地方出现了停放,包括储藏保管、停放状态、保管手段(如储存容器配备、货架配备、设施条件)、有无积压状态?哪些工艺路线和环节可以取消、合并、简化?寻找最佳停放条件,确定经济合理的工艺路线。
2、平面图上找一找
即向平面布置要效益。仔细检查和分析工厂平面布置图、车间平面布置图和设备平面布置图,分析作业方式和设备、设施的配置,按生产流程的流动方向,有无重复路线和倒流情况,找出不合理的部分,调整和设计一种新的布局,使生产流程在新的布置图上路线最短,配置最合理。
3、流水线上算一算
即向流水线要效益。研究流水线的节拍、每个工序的作业时间是否平衡,如果发现不平衡,就要通过裁并、简化、分解等等手法,平衡流水线。消除因个别工序缓慢而导致的窝工和堆积。
4、动作分析测一测
即向动作分析要效益。研究工作者的动作,分析人与物的结合状态,消除多余的动作、无效动作或缓慢动作,如弯腰作业、站在凳子上作业、蹲着作业、作业场所不畅、没有适合的工位器具、人与物处于寻找状态等,通过对人的动作和环境状态的分析和测定,确定合理的操作或工作方法;探讨减少人的无效劳动,消除浪费,解决现场杂乱,实现人和物紧密结合,提高作业效率。
5、搬运时空压一压
即向搬运时间和空间要效益。据统计,在产品生产中搬运和停顿时间约占70-80%,搬运的费用约占加工费的25-40%,要通过对搬运次数、搬运方法、搬运手段、
搬运条件、搬运时间和搬运距离等综合分析,尽量减少搬运时间和空间,寻找最佳方法、手段和条件。
6、人机工程挤一挤
即向人机联合作业要效益。人和设备构成了人机工程,在分析时要分析作业者和机器在同一时间内的工作情况,有无窝工、等待、无效时间,通过调整工作顺序改进人机配合,寻求合理的方法,使人的操作和机器的运转协调配合,将等待时间减少到最大限度,充分发挥人和机器的效率。
7、关键路线缩一缩
即向网络技术要效益。将现有的工序和作业流程绘制成网络图。从中找出关键路线,然后从非关键路线上抽调人财物,加强关键路线,或采用平行作业。交差作业等等形式,实现时间和费用的优化。
8、场所环境变一变
分析生产、工作环境是否满足生产、工作需要和人的生理需要,分析现场还缺少什么物品和媒介物,针对不同类别场所的问题,分别提出改进建议,开展“整理、整顿、清扫、清洁、素养、安全”六项活动,做到永远保持A状态,不断改善B状态,随时清除C状态,使员工保持旺盛的斗志和良好的技能,所需物品随手可取,不需要之物随时得到清除,现场环境通畅、整洁、美化、安全、文明,使场所和环境在时间和空间上实现整体优化。
二,现场开展改善活动的过程中,要注意的问题:
1, 工作量降低了但质量却恶化了。
2, 虽然降低了0.7个人的工作量,但人却没减少。而周围的操作人有富余时间,在不断地摧促上一道工序的操作者加快速度。
3, 作业虽然已小批量化,但步骤时间及库存量都却增加了。
4,达到了谋求少人化的目的,但设备投资却花了很多钱。
5,虽然已有所改善,但如果换了人又恢复了原状。
三, 改善活动中的心态
1.好就是不好,不好就是好,要永无止境的改善下去.
好就是不好指的是失去了改善的机会,不好就是好指的是找到了改善的机会.
2.永无止境就是要追求:
(1)提高生产劳动率.
(2)减少不良率.
(3)缩短交期时间.
(4)降低库存,最好无库存.
(5)节省生产空间.
(6)提高设备可利用率.
3.就是有问题才去改善,不是没有问题就不去改善.
4.要打破传统一个人固定操作一个工位的思想,朝一个人多工序操作,弹性化方向发展.
5.掌握现场,现物,现实,现做,现查五现原则,不要只看书面的记录.
6.有50%的把握就要尝试去做,不要等到有100%的把握才去做改善.
7.改善要经历多次尝试才能成功,不是一次就能够全部成功.
8.要贯彻DIY的思想,马上动手做,不要在会议室里思考讨论.
9.用头脑智慧去克服问题,不是用金钱去摆平问题,不过可以通过用小钱去做大的事情.
10.要朝\"理想状态\"迈进,不要寻找不能做的原因,比如五没抵抗:没人,没钱,没时间,没空间,没条件.
11.\"理想状态\"就是:
(1)依据产距时间生产.
(2)一个流方式生产.
(3)后拉式看板生产.
12.要发挥部门团队精神,共同努力达成目标.
13.要问五次为什么,找出问题的真正根源所在.
14.要顾全大局,例外情况特殊处理.
15.要观察有无三无现象并进行改善.
16.改善固然可喜,但是维持更是重要.
17.维持就是遵守标准作业,管理者要去督促检查是否有按标准作业.
18.要具备改善循环(PDCA)的四大意识,即品质意识、维持意识、问题意识、改善意识。
19.医生开处方,病人要吃药,老师教学生,学生要维持,指的是要把改善真正去实施起来。
20.问题就是机会,改善就是赚钱。
四,产生创意的思考法则:
1)相反法则-现行的方式逆向倒过来做,将会变得如何呢?
2)拼图法则-将每一基本部分分解出来,再尝试其它组合的方式,是否会有意想不到的效果呢?
3)大小法则-改变尺寸﹑形状等的大小,看看其影响会变得如何呢?
4)例外法则-将经常发生的事物与偶然发生的事物做区别,将偶然发生的状况加以例外管理原则来控制即可,而不要将经常发生的事物也用相同的管理方式来管理。
5)集合法则-尝试将不同的单元事物结合在一起,是否要以增加使用者的功用及效果?
6)更换法则-将顺序加以更换,效果是否会较好呢?
7)替代法则-考虑用别的方式来替代现有的方式,会有什么样的结果呢?
8)模仿法则-模仿是创造的最佳触媒,藉著参考现有的东西加以思考很容易引发新的创意出来。
9)水平法则-发挥自己的联想力,考虑由水平的方向去思考,突破传统及习惯上的束缚。
10)定数法则-将经常发生的事物予以制度化,可以产生许多简化的效果及提高效率。
五,现场改善的心得:
抛开所有固定的观念;
说干就干,多说无用
不让金钱溜走,以智慧取胜;
化解问题。多问五次“为什么”
改革无限。总想着现在还很差
大家一起学习现场改善顺口溜:
现场改善很重要,环境整洁心情好。
偏有员工不自觉,东西乱放占通道。
5 S工作一推行,画线之后皆看到,从此通道就通了。
现场改善很重要,成本一算降不少。
人人都在讲节约,原先浪费不见了。
纸张皆作双面用,纸箱回收讲环保。
浪费的钱谁也没得到,节约的钱奖励进腰包。
现场改善很重要,安全事故不见了。
危出了事故找原因,人人为安全勤思考,积善行德功劳高! 现场改善很重要,品质月月在提高。
生产工人有干劲,品管干部喜眉梢。
以前品质常出错,不是特采就退货。
QCC活动开展后,一个个问题被攻破!
QC检查特严格,还是批批PASS过!
现场改善很重要,从此大家效率高。
办事不再是推托,个个文明又礼貌。
以前常为交期愁,出不了货又睡不好觉。
如今工作标准化,避免了推诿和争吵。
大家团结一条心,达成目的没烦恼!
第11篇:《现场改善》读书笔记
《现场改善》读书笔记
1.成长时代:成本+利润=销售价格
成熟低成长时代:销售价格—成本=利润
2.速度化的一年,所有业务都要加速办理。包括:
LT:缩短准备时间;
CO:削减成本;
AC:快速的行动;
CS:迅速的客户应对;
QT:提升品质。
3.改善的时候,最重要的两点:根据企业的目的,对改善工作进行定位;要在企业中集思广益。
4.改善是企业达成目标和支持企业永久发展的手段,是集合企业全体成员智慧的企业经营的一种思维方式。
5.改善的目的:企业盈利能力的提高;产品竞争力的维持与提高。
6.提案制度的规律:如果注重数量的话,质量就会下降;如果注重质量的话,那么大家就会对提案敬而远之。
7.改善三部曲:改善是从定量地对现象进行观察开始的;找到差距(本来应该有的、理想状态、世界第
一、业界最高水平、标准、优秀者);将其变成视觉性表达(文字、数字、图画、图标等形式,通俗易懂)。
8.整理(1S):将生产现场的物品,清晰地分为马上会使用到的物品和不会马上使用的物品,并且将不会马上使用到的、不需要的物
品进行处理。
9.要重视时间而非价值,清理并非把不需要的东西扔掉,而是远离现场,可利用粘贴红标签来进行整理活动。
10.整顿(2S):将需要的物品,放在对自己或后续工序来说易于使用的位置,于是管理就变得一目了然了。
11.放置场所的标示:品目标示、位置/编号标示、后续工序标示、数量标示、管理负责人标示。
12.物品摆放遵循的动作经济四原则:缩短距离:要把物品摆放得近一些;同时使用双手:两只手同时进行产生附加价值的工作方法;减少动作次数;轻松愉快地工作。
13.丰田公司前总经理大野耐一提出的七种浪费:生产过剩的浪费;等待的浪费;搬运的浪费;加工本身的浪费;库存的浪费;动作的浪费;次品的浪费。
14.生产过剩的浪费:定位成七种浪费中最恶劣的浪费。原因是,如果允许了这种浪费,那么剩下的六种浪费就会同时发生。相反,如果发生了这种浪费,并开始改善的话,以前隐匿的看不见的其他六种浪费都会显示出来。
15.生产过剩的浪费分为两种:过多的生产过剩:很多人认为,手上空着,继续生产更能产生利润,但是,生产是好的,如果卖不出去,就那么剩着,这部分就会完成变成损失了,另外,就算是迟早都能卖出去的产品,到卖出去那天之前,还要搬到仓库里,进行保管和管理,这样一来,就会产生更多本来完全不必要的工作;
过快的生产过剩:可能有人会想,反正也是要生产的,早点做完没什么关系,但是因为是在发货之前的时间里,生产出来的产品不可能就放在原地,需要暂时搬运到其他地方去,所以就会产生诸如此类的各种多余的工作,生产应该按照规定的时间进行。
16.等待的浪费:就是手上空闲,没有事情做的状态,我认为这是其中浪费中性质最好的一种,但是让等待的浪费显示出来是很苦难的。
17.等待浪费也分为两种:第一是周期发生的等待,这种等待经常会出现在传送带作业中,比如循环时间是60秒,而工作时间只有50秒,那么就有10秒钟的等待。第二种是监视浪费:在机械进行组装生产时,需要用到手的工作非常少,实际上,只有当设备出现问题的时候才需要动手,而其他时间就是对设备进行监视。这里就需要为设备增添主动报警功能,当出现故障时会通过声音、灯光来提醒人员进行修理,其他时候人员一直在做一些能够产生附加价值的工作。
18.搬运的浪费,无论搬运多少次,既不会提升品质,也不会降低成本,更不会产生任何附加价值,只不过改变了物品的位置而已。工厂中的距离是自己造成的,是可以把浪费消除的。
19.搬运浪费分为两种:大的搬运浪费:说的是诸如把大量的零件放在托盘上,用叉车搬运这类的搬运。小的搬运浪费:说的是诸如组装作业中每次伸手取零件这类的搬运。
20.加工本身的浪费可以分为两类:第一类,就是作业本身很必要也
很苦难,但是客户却完全没有给予很好的评价。比如,去毛边。另一种存在于工作方法和工序组合中,作业的编排或者机器设备的布局,全部都是这种浪费的对象。
21.库存浪费大致分为两个内涵:一是因为库存是一种金钱转化为货物的状态,所以为了在短时间内产生利润,有必要提高周转的速度;二是,一旦有库存的话,在生产上必定就会出现松懈,于是浪费变得比较隐蔽,改善的速度会减慢。
22.动作浪费,指动作中不产生附加价值的部分,无论是人的动作还是机器设备的动作,没有意义的动作都应该全部去除。动作经济四原则就是改善很好的切入口。
23.关于品质,我们分为两部分来考虑:诞生的品质,产品在设计阶段是否良好;成长的品质,比如通过避免失误、作业训练等,能够产出何种程度的优良产品。
24.许多公司在改善过程发现需要设备,就匆忙地购入设备,从来没有想过自己也可以制造设备,没有考虑设备的内制化。在内制化过程中要考虑设备是通用的还是专用的。
25.供应链管理之一:必须从消费者一侧进行拉动。从供应链的左侧向右侧推是不会动的,必须从右侧拉动。
26.供应链管理之二:库存过多,就难以拉动。链条的每一环之间,重叠的部分很大,所以无论怎么拉,也不过是抻平了重叠的部分,难以做到让所有的环节都动起来,这部分重叠的就是库存。
27.供应链管理之三:批量过大,就难以拉动。链条上的环很大,导
致自身锅中,所以拉不动,二链条上环的大小,就是批量。
28.供应链管理之四:一旦有瓶颈,就会断裂。实际上众多的环节中只要有一环是薄弱的,就是瓶颈。
29.依据转换时间上的差异,可将转换分为内部工序转换和外部工序转换。内部工序转换是停止生产进行的工序转换;外部工序转换是不停止生产而进行的工序转换。
30.工序改善,第一步就是将尽可能多的工序转换作业按外部转换来进行;举例子,火车站买票,大多数人都会在排队时确认一下到自己去的地方的票价,并且准备好需要的零钱,等着轮到自己购买;也有一些人不提前准备好,等轮到自己的时候在慌慌张张查自己所乘的车次,然后问价,再掏钱,一致常招来周围人的侧目。
31.工序改善,第二步是内部工序转换的改善,可以运用一下三个关键词来进行改善:手动脚不动,要提前把所有需要的东西准备好,一旦开始之后,就绝不再去取物品;看到螺丝钉立刻改善,无论是安装螺钉还是拆卸螺钉,请按照一定的形式进行改善,比如,使用夹钳来代替螺钉,或者确认强度的基础上,减少使用不必要的螺钉,以减少螺钉的使用数量,如果做不到上述内容的话,可以统一螺钉的种类,一消除拾取工具时所需的调整,也可以用颜色加以区分,是工人能马上拿到所需的螺钉,总之,一定要进行改善;不要两方去合,要一方贴住一方对齐,是的他们的位置能够轻易地固定下来。
32.管理者是被委以经营辅助者作用的人,这个作用大概分为三种:
业务目标的达成,人才的培养,为此而进行的环境建设。
33.管理者的工作重点:为实现目标而制定计划,研究不利因素,事先排除、解决;将上一级的目标与实现方法分解为自己组织的目标和现实方法,让下属真正理解并能想象出该如何行动;决定对分解后的目标应如何分工,让部下制定实现目标的计划;分析现有的经营资源,补足有所欠缺的资源,另一方面也需要拥有清理不必要资源的勇气;定期监督目标计划的进展,进行相应的指导、建议和激励。
34.五合一的管理循环:观察,持续观察队员寻找研究课题的情况;赞同,一旦队员决定了研究课题,就告诉他们,试试看吧;援助,遇到什么困难就告诉我,是不是有什么烦恼啊;欣赏,对于研究课题的报告,就一句话,做得很好;认可,让全体成员认可。
第12篇:培训心得体会现场管理与改善
培训心得体会 现场管理与改善
打印 引用 发布时间:2011-05-20 培训心得体会 现场管理与改善 心得体会
管理不分行业,外行人管内行人才能称真正的管理。管理需要内功,才能进行能量的传递,赢得众人的支持。
从本职工作角度出发,让我深有感触主要有两点:人员管理和品质管理。
人员管理
对于现场的管理,从人、机、料、法、环、信、流来看,人员的管理是个难题。因为人是有感情、有思维的,一个人所做的不一定是他认为的最理想、最顺心的工作,如果他感到不称心,心理就可能别扭而意气用事。这有意识或无意识地会反映到他的工作上,都是会直接或间接地影响产品和生产效率。所以人员管理是现场的管理第一要素,经过学习和体验总结如下:
一、树立威信
首先树立领导的威信,指挥下属做事。人都是有惰性的,慢慢地下属就习惯了。你叫他做什么,他就做什么,下属会慢慢地养成听话的习惯。你是领导,他是下属,一定要记得彼此的身份。必要时可以打成一片,凝聚团队力量,但要把握尺度。
二、沟通 有空的时候多和下属聊天,毕竟领导比下属见识要广,很多职业发展方向之类的大问题领导完全可以给下属意见。这是培养信任的好办法,也是帮助领导了解下属的好途径,不论下属对事业有没有追求,领导就能通过沟通了解到下属的需求,知道需求就知道如何激励下属。
三、培训下属
一个能力强的领导根本不害怕下属更强悍,强将手下无弱兵,更无散兵。适当的培训只会使得领导多一条臂膀。“木桶理论”再次告诉我们,只有全员素质整体技能
提高了,才能提高团队的竞争力。给人一杯,自己要有一桶。在培训下属前,领导自己得先学习,先进步,有备而来,否则,领导拿什么教人呢?共同进步,和乐而不为。
http://news.youboy.com/
[原创]现场管理的一些总结
人气数:1112 评论数:1 收藏数:0
转发到:
更多>>
2011-03-25 21:11:45 星期五
一直想总结自己一些心得,可是总是以忙为借口,没有成文,事实上现场管理改善工作,很多现场管理人员也是以忙为借口,因而现场一塌糊涂。在有些工厂巡查时,垃圾到处乱丢,包括零食(比如瓜子壳,花生壳,鸡蛋壳,速溶咖啡包装袋,话梅袋子等),这是其一,其二,区域划分不清楚,产品没任何标识,积了一层灰尘的东西还在说刚生产没几天的东西。其三,部分机器没生产,但电源是开着的,第四,消防通道没有,消防器材下面堆放物体。。。。这是一些现状,企业管理人员可能是漠视这些,问他们为啥会这样,一个字忙,两个字没人。这是真实的原因吗?答案是肯定的,肯定不是。在于管理人员的心态,在工作管理过程中有没有重视这些问题。
人肯定喜欢工作在一个干净整洁的环境,舒适的场所,可这环境的造就是需要在管理层的带领下,全员的参与下,持续进行下,才会有的。 那如何做呢?
第一, 合理区域划分布局,全员现场管理改善的培训(培训是持续的)。说到培训,对基层员工的培训可以在早会简单宣导几句,或周会等,一定要多讲,多说,不是想起来就说一下,没想起不说。这容易形成一个误区,那就是员工会认为这是一个不太重要的工作。慢慢培养他们将这些工作当成是日常工作分不开的一部分,也就是说形成习惯。
第二, 不外乎是成立6S小组,建立相关6S规章制度,可以给予一定的激励措施。 第三, 执行6S检查工作,外加管理人员的日常巡查。检查和巡查时,一定要关注一些卫生死角,管理不善的地带特别是所谓的临时物料堆放区,车间的一个常人少去的黑角落(在平常巡查工厂的过程中,我常发现有些物料是堆放了很久,但却又是工厂大部分人在寻找的产品)。此外检查一定客观公正,不要让检查工作形式化。
班组的现场管理水平是企业的形象、管理水平和精神面貌的综合反映。
班组的现场管理水平是企业的形象、管理水平和精神面貌的综合反映,是衡量企业素质及管理水平高低的重要标志。搞好班组生产现场管理,有利于企业增强竞争力,改善生产现场,消除“跑、冒、漏、滴”和“脏、乱、差”状况,提高产品质量,保证安全生产,提高职工素质,对提高企业管理水平,提高经济效益增强企业竞争力具有十分重要的意义。
搞好班组建设、提高班组现场管理水平,应主要做好以下几项工作:
提高对加强班组生产现场管理重要性的认识。生产现场管理是企业管理的重要组成部分,是企业管理素质的集中表现。通过现场管理的好坏,即可判断出企业的广大职员的素质和管理水平,产品质量的可信赖程度,企业可协作程度。而班组又是企业生产现场管理的前沿阵地,所以,提高企业的班组生产现场管理水平,是企业自身发展的需要。
营造良好工作氛围,为班组建设奠定基础。良好的工作氛围包括整洁的作业现场、安全的工作环境、融洽的人际氛围,团队的合作精神。一个良好的工作环境能有效保证员工的思想稳定,提高员工的工作热情,更加有利于班组凝聚力、战斗力的生成。为此,应做好以下工作:
关心职工。领导和职工之间应融洽相处,关心职工生活和工作,为职工办实事,改善职工生活水平,增强企业凝聚力。
加强民主管理。生产期间,应定期召开民主生活会,要求全班职工都要积极提出一些合理化建议,充分发挥民主监督作用。
加强6S管理。在班组生产现场管理中,通过导入“6S”管理活动(整理、整顿、清扫、清洁、素养、安全),形成以班组管理为活动平台,以人的素养为核心因素,以整理、整顿、清扫和清洁为环境因素,以安全、环保为目标因素的生产现场动态管理系统,从而为职工创造一个安全卫生舒适的工作环境。
发挥班组长的作用。作为班组长,在企业中充当的是一个兵头将尾的角色,通过合理运用手中的权力,调动每个员工的工作积极性,使班组充满活力,为此必须:做好班组长的选拔、培训、考核、激励等工作。班组长要做好表率。在班组建设中表率是指班组长的“自治”行为,在班组做表率不仅是让组员效仿,还是衡量班组长是否合格的基本标准。
强化教育培训,提高员工的素质。加强教育培训,主要是指对班组进行技能、安全生产、岗位职责和工作标准等方面的教育培训,同时将培训成绩记入个人档案,与个人的工资、奖金、晋级、提拔挂钩。
开展班组达标管理工作。企业应制订可操作性的达标标准,标准内容力求系统考虑,整体推进,分步实施,同时应把班组达标工作的总目标分解到每个职工,通过强化考核,细化管理,确保企业总体工作目标的完成。为配合企业推进达标工作,企业还应建立有效的激励机制,鼓励先进班组和个人。
健全组织、权责分明、加强领导。为切实加强组织领导,保证班组建设工作健康有序地进行,应成立班组建设工作领导小组,行使指导和监督的职能。领导小组由企业主要负责人任组长,分管领导任副组长,各职能部门的负责人为组员。在班组建设工作领导小组下成立班组建设工作考核工作小组,具体负责班组达标管理等班组建设工作的检查督促和考核奖惩工作。
健全班组生产现场管理体制。班组不管大小, 要建立以班组长、党团小组长、政治宣传员等为核心的班委会。班委会的任务是确定班组建设目标, 为开好班组会做准备。另外还要建立“工管员”制, “工管员”一般包括质量管理员、考勤员、工具材料员、文明生产员、劳保生活员, 管理落实到人头, 形成人人有事干、事事有人管。
建立一套现场管理制度(标准)和检查考评制度。要对班组生产现场进行规范化管理,使班组工作进入有序管理的状态,就要制订相应的管理标准,包括:
生产现场管理标准化。生产现场管理必须从基础抓起,即从制订工作标准、完善工作标准和真正贯彻执行及考核工作标准着手。生产现场的工作标准可以分解成三个有明显区别的部分:一是管理工作标准,二是工作程序标准,三是工作人员工作标准。
加强班组内部基础管理。建立各类基础管理台帐、报表制度及工序奖惩考核办法;注重半成品库的基础管理工作,起到前道控制、后道监督的作用;充分利用电脑等现代化设备,使各类统计报表及生产任务单的下达均取代手工操作,提高工作效率,等等。通过这些基础管理,促进班组管理工作日趋规范。
建立健全班组生产现场管理规章制度。包括围绕生产、安全、技术和思想政治工作所制订的各种规章制度、条例、程序、办法等,如巡回检查制度、交接班制度、工作票制、岗位责任制度、安全责任制度、技术培训制度等,并且要规范统一,落到实处。
第13篇:生产成本控制与现场改善心得体会(材料)
生产成本控制与现场改善心得体会
通过这次培训使我对成本控制有了更深刻的理解。成本是与产品密切相关的,而产品包括质和量,质也就是合格率,量直接关系到固定成本,量的提升使均摊到每个产品上的固定成本降低。只有降低成本才能产生出更多的价值,价值也就是有效的生产劳动,所以应尽量剔除或降低生产中无效劳动,彻底清除生产的十大损失:动作的损失、搬运的损失、寻找的损失、等待的损失、平衡的损失、换产的损失、速度的损失、品质的损失、库存的损失、跑冒滴漏的损失。只要这样才能提高生产效率,在有限的时间里,做出更多的有效劳动,而清除这些损失的根本在于做好5S:整理、整顿、清扫、清洁、素养。我们现在做的5S只是表面上的,而且有的只是三分钟热度,没有真正体会到5S带来的帮助,5S最重要的就是清洁,也就是保持,将整理、整顿、清扫工作彻底做好。
通过培训还有深刻的一点就是生产标准化的提高。生产车间是不需要技术的,只需要技能。标准化的提高可以使生产的有效劳动提高,降低废品率。
韩暄
2011年6月1日
第14篇:现场改善术语解说
现场改善术语解说
允收品质水准(AQL) Acceptable Quality Level
允收品质水准是顾客与供货商之间的交易运作模式. 容许供货商在协议的条件下, 交 付某一限定比率的不良品.
问五次为什么(Ask why five times) 一个发掘问题真正原因的常识原则.
查核现场(Check gembutsu)
当欲探寻问题的根源时, 在现场实地有形的物体加以调查.
符合性(Conformance) 用以表示产品或服务能达到相关规格、合约或规则, 所要求的一个确定指示或评定.
管制图(Control Chart)
为一个具有上下管制界线的图. 在其图上, 绘有一系列的样本或样本组统计量的测定值.此图通常绘有一条中心线, 用以协助侦测所绘之统计值, 有否趋向其中之一条管制界线.
成本-----Cost
在QCD的范畴中, [成本]一词通常系指成本管理,而非削减成本. 成本管理涉及到对各种资源 的适度管理, 以及消除所有类别的无驮(浪费). 在此种方式下, 会降低总成本.
跨功能(部门)管理----Cro-functional management 为达成QCD跨越部门之间的管理活动.周期时间----Cycle time 作业员完成加工一个产品的实际耗费时间(参阅产距时间Takt time).交期----Delivery 在QCD的范畴中, [交期]一词系指交货时间以及数量, 皆要符合顾客的要求.不按受, 不制造, 不流出----Don’t get it, don’t make it, don’t send it.
在现场里推行的一个常识性口号. 在任何一个QCD计划中,应将品质是最优先的信念予以实践出来.例如: 不要从上制程接受不良品, 不要在自己的制程上制造出不良品以及一旦有不良品制造出来, 不可明知故犯地流到下一制程.
失效树分析-----Failure Tree Analysis(F T A)
借着确定因果关系及利用树关图, 来认定问题的机率. 失效树分析是用来分析及事先避免任 何安全性及可靠度上的问题.现场管理的五项金科玉律----Five golden rules of gemba management 一套在现场推行[现场改善]时,最实用的提醒剂..(1) 当有问题发生时[要先去现场]. (2) 检查现物.
(3) 当场采取暂行处置措施. (4) 发掘真因并排除. (5) 标准化以防止再发. 5M----Five M’s
在现场用以管理资源的方法. 这五项资源皆以英文[M]开头, 特地称之为[5M]----人员 (Manpower), 机器(Machine), 材料(Material), 方法(Method)和量测(Measurement).5S----Five S’s
是一种为维持良好工厂环境的查核表, 为使工作场所更有秩序, 效率及纪律. 它源自于五个有S音开头的日文----Seiri(整理). Seiton(整顿), Seiso(清扫), Seiketsu(清洁),Shituke(教养). 套用英文相当之字则为Sort(分类=整理), Straighten(定位=整顿), Scrub(刷洗=清扫), Systematize(制度=清洁)及Standardize(标准=教养). 某些分司则采用为5C作战..Clear out(清除=整理),Configure(形迹=整顿), Clean & check(清洁及检查=清扫), Conform(遵守=清洁)及Custom & practice (习惯及实践=教养).流线生产----Flow Production
及时生产方式的基本支柱之一. 在流线生产里, 机器是依据加工的顺序排列. 如此, 工作物在制程之间的流动, 就不会中断或停滞.失效模式及有效性分析----FMEA
借着分析零组件对最终成品失效模式的影响结果; [失效模式及有效性分析]可以用来对一个新产品的作何潜在的设计缺点, 做事前预测及消除. FMEA也可用来针对新生产设备的役计审查活动(叫做制程FMAA) 现场----Gemba
日文一词意指[实地], 现在则采用管理上的术语, 意义为[工作场所], 或者称之为[产生附加价值]的地点.在制造业来说, 通常系指[工场]. 现物----Gembutsu
在现场里所发现的有形对象. 例如: 工作物,不良品,夹具,工具及机器. 去现场----Go to gemba
现场改善的第一项原则, 这是一个提醒剂. 不管何时, 当异常发生或经理人员欲了解生产作业的现状, 他(或她)应立即去现场, 因为现场是所有信息的来源. 海因利奇法则----Heinrich’s Law
一项有关于意外事故与伤害的比率法则. 海因利奇用下列的比率表示之: 重度伤害: 轻度伤害: 无伤害=1:29:300此公式表示: 当你看到一个因意外事故重伤的人, 同样的事故可能也造成二十九人的轻微伤害. 同时, 或许有三百人经历同样的事故, 但幸运地没有受到伤害. 危险预知训练----Hiyari KYT(Kiken-yochi training)
KYT系指对预见的危险做事前演练, 并且采取预防的措施.惊吓报告----Hiyari report(Scare report)
惊吓报告, 是由工人写给上级主管的报告. 用以报告会造成品质问题及/和意外事故的不安全 状况.石川(鱼骨)图----lsikawa(fishbone)diagram
由石川声教授首先发展出来的图表. 用来表示原因(制程)及影响(结果)的关系. 此图系用来确定真因, 同时也是解决问题的七种基本手法之一. 国际标准组织9000系列标准----( ISO 9000 Series standards)
一套关于品质管理及品质保证的国际标准规范. 此套规范用以协助公司对品质体系应执行的要件, 做好文件的管理, 以确保符合产品的规格要求. 自动化----Jidhoka (Autonomation)
每当不良品制造出来时, 能使机器自动停止下来的一种装置. 此装置是JIT导入的要点.自主研现场改善----Jishuken gemba kaizen
在一九六零年代初期, 自主研(自主的JIT研究小组)首先在丰田集团的公司的现场, 开始推行的JIT的活动.及时生产方式JIT----(Just-in-time) 藉由在公司内, 消除流程间所有各种的无驮(浪费), 并以及时送达货品以符合顾客的要求,来达成产品或服务的最佳品质, 成本及交期的一种生产体系. 最早是由丰田汽车公司发展出来, 亦称为丰田生产体系(Toyota Production System), 精实生产方式(Lean production system)及看板生产方式(Kanban System) 自主管理----JK (jishu kanri)
自主管理的日文意思为自动自发管理之意. 系指工人在其上级管理人员的指导之下, 将参与改善活动视为日常工作的一部分. 此与品管圈活动有所不同, 后者系自原性并由工人依自已的意志进行. 改善观念----Kaizen concepts
在推行改善时, 所必须了解及关践的主要观念.(1) 改善与管理.(2) 改善与结果.
(3) 导守P D C A 循环/SDCA循环. (4) 品质第一. (5) 用数据说话. (6) 下一制程就是顾客. 改善事例----(Kaizen Story)
用于组织各层级中的一种解决问题之标准程序. 改善事例分为八大步骤: (1) 主题选定.(2) 现况调查及目标设定.(3) 资料分析以确定真因. (4) 对策拟定. (5) 对策实施. (6) 效果确认. (7) 标准化.
(8) 检讨上述过程及未来计划.改善活动体系----Kaizen systems 欲达成世界级所必须建立的主要活动系.(1) 全面品质管理(Total Quality Management) (2) 及时生产方式(Just-in-time production system) (3) 全员生产保全(Total Productive Maintenance) (4) 方针展开(Policy Deployment) (5) 提案建议制度(Suggestion System) (6) 小集团活动(Small-group activities) 看板----Kanban
在及时生产方式中, 用以管理批量生产的一种沟通工具. 看板, 在日文里系指一种信号板, 挂附在生产线某一已知号码的零件或产品上, 并指示运送某一已知的数量. 当这些数量的零件 用完之后, 此看板即送回原处, 变成生产指示, 以再生产. 工数----Kosu
生产作业, 可区分为机器的时间和人员的时间, 工数系指在一已知的制程中, 完成一个产品的加工动作所耗费的人员时间. 是将此一制程的工作人数, 乘上实际完成此制程的时间, 再除以所生产的产品数量, 用来衡量作业员的生产力. 工数降低是在现场生产力改善的主要衡量方式之一. 晨集----Morning market 在现场中的[每日例行工作], 包含在工作之前依据现物原则, 检查前一天所做的不良品(现物), 如此才能尽早采取对策.此一包含现场人员的(而非职员)会议, 是在早上开工时的第一件事. 无驮----(浪费)Muda 日文一词意指[浪费]. 当使用在工作场所的管理时,泛指没有附加价值的活动.在现场里仅有两种型态的活动: 有附加价值和没有附架价值. 在现场改善中, 首先致力于消除各种没有附加价值的活动. 消除下列范围的[无驮], 期使对Q C D产生重大的改善: 生产过多, 库存, 不良品, 动作. 加工. 等待. 搬运及时间. 无驮的消除即是以低成本, 常识性的方法, 来求改善的缩影. 无稳----Mura
日文意指不规律或变化性. 无理----Muri
日文意指过劳性或困难性. 一个流----One-Piece flow
在及时生产方式里, 仅允许每次将一个产品从此制程流到另一制程, 使无驮最小化.柏拉图----Pareto chart
将原因从最大影响度, 依序排至最小影响度的一种图表工具. 它是依扰[柏拉图原理]而来, 是由品管大师裘兰博士(J. M. Juran)订定出来的. 此80:20原则, 指出[80%的结果, 是来自于20%的原因所造成]. 柏拉图为解决问题的基本七手法之一种. PDCA----Plan-Do-Check-Action
计划—执行—查核—外置, 是从事持续改进(改善)所应遵行的基本步骤. 后拉式生产----Pull Production
及时生产方式的基本要件之一, 前制程仅补充生产后制程所耗用掉数量的产品.前推式生产----Push Production 后拉式生产的相反词. 前制程尽其所能生产愈多的产品, 欲不顾及后工程实际上的需求数; 并且不管是否有所需求, 全部将之送给后制程.品质保证最佳生产线证书----QA Best-Line Certification
一种厂内的认证制度. 用以证明某一特定生产线, 其品质保证的成效达到世界级水准.QCD----(Quality, Cost, Delivery) 品质, 成本及交期, 被视为管理的首要目标. 当管理能成功达成QCD的目标时, 则顾客的满意及企业的成功, 也会随之而来. QCDMS 在现场里, 经常将M士气(Morale)及S安全(Safety)加入QCD, 做为欲达成的目标.品质机能展开----QFD (Quality Function Deployment) 一种管理的方法. 首先先确认顾客的需求, 然后经由各个阶段对产品展开下去: 设计,工程,生产,销售及售后服务.QS 9000
美国版的ISO 9000系列. 由三大汽车公司要求施行于其供应厂商. 与ISO 9000系列之一般要求来作说明比较, QS 9000明定一些额外的要求, 特别是对标准及矫正行动, 要求持续地改进. 品质----Quality
在QCD的范畴理, 品质系指送达至顾客的产品或服务的品质. 在此状况下, 品质是指符合规格和顾客的要求. 广义而言, 品质包含产品或服务的设计,生产, 交货及售后服务工作的品质.品管圈----QCC(Quality Control Circles) 由一小群员工(十人或以下)组成,以从事品质改善或自行改善的研究团体.品管圈导源自日本, 被称为品质管制圈(品管圈).品管圈是在工作场所,自原地执行改善活动,持续从事一部分全公司性的相互教育.品质管制,自我发展及生产力改善的计划.
SDCA----Standardize-Do-Check-Action 标准化—执行—查核—处置, 是在维持现关时,应当遵行的基本步骤. 同时实现QCD----Simultaneous realization of QCD 最高管理阶层应清楚公司内,所有的阶层都是致力于过成品质,成本及交期之工作任务.最终的目标是QCD能同时实现.但是三者之间首先要实现的,仍应以品质为第一优先.小集团活动----Small-group activity
为解决他们自己作场所的问题,而形成的现场集团活动.通常由现场的作业员五~十人组成集团. 他们的活动大都与品质圈活动类似.然而小集团活动并不仅限于诸如品质改善.降低成本,全员生产保全(TPM)和生产力改善,同时也扩及到娱乐性或其它社交性活动. 标准化----Standardization 标准化为现场改善三项基本活动之一, 意指将工作的最佳方式予以文件化.标准作业----Standardized work
人员,机器和材料的最佳组合状况.标准作业的三要素是产距时间,作业顺序和标准在制品数量.标准----Standards
工作的最佳方式, 即是由管理当局针对分司所有主要的业务,设定一套方针,规则,指示及程序书,作为全员执行其工作的指导,以求获致好的成果. 统计制程管制----Statistical proce control (SPC) 应用统计尝上的技巧, 以管理控制制程. 有时亦经常与统计品质管制互用.储存室----Store room
在现场用以储存在制品或物品的场所.储存室与一般的仓库是不相同的,因为在储存室里仅能保存标准的储存量.
提案建议制度----(Suggestion System)
在日本, 提案建议制度, 是高度被归属于个人导向改善活动的一种方式.日本式的提案建议制度着重于激发员工工作士气和建设性的参与感, 它远甚于欧美对形能的注重以经济上及金钱上的奖劢. 产距时间----Takt Time
完成生产一个顾客所订产品的所需时间. 是以总生产时间, 除以生产需要数而订定出来的.3K
日文用来表示在现场里惯见的印象----危险(Kiken), 脏污(Kitanai)和劳累(Kitsui),与此形成直接对比的,是理想的现场,为一个能附加真正价值, 以及达成QCD构想来源的场所. 3M
指无驮(Muda----浪费), 无稳(Mura)和无理(Muri).这三个字词常用来当做改善的查核点,协助工作人员及管理当局,以确认可供改善的地方.
在现场的3M----Three M’s (3M) in gemba 在现场三个主要需加以管理的资源----人员(Manpower), 材料(Material)和机器(Machine).有时再加上方法(Method)和量测(Measurement)而称为5M..全员生产保全----TPM ( Total productive maintenance)
全员生产保全, 是意图在机器的整个寿命期内, 获取最大设备效率的发挥.TPM牵连到所有部门各个层级里的每一个人,它透过小集团和自主活动, 激劢员工从事工厂的保全活动. 它包含如下的基本要件: 保全体系之发展, 基本的厂房环境维持教育, 问题解决技巧, 和零故障及现场零意外的活动. 由工作人员所做的自主保全, 是TPM的重要支柱之一.5S则为TPM的第一步骤. 全公司品质管制----(TQC) Total Quality Control 为品质而组成的改善活动,包含了公司的每一个人----管理人员和工作人员,以整合总体的力量,致力于每一个层面的改善.它设想这些活动, 最终将获致顾客满意度的提升企业经营的成功. 在日本, 使用全面品质管理TQM(Total Quality Management)为名词已相当普遍, 现在已取代了TQC名词.两天期现场改善----Two-Day gemba kaizen) 在日产汽车公司及其供货商内, 实施的现场改善活动.它是选定某一特定制程及由内部改善指导老师,工程师和生产线上管理人员组成的小集团,在现场里花费二天时间,利用及时生产方式和其它有关的查核表,以达成改善目标.
价值分析----Value Analysis 一九四七年, 由美国奇异电气公司麦尔斯(L. D. Miles) 所导入降低成本的方法.它着眼于上游阶段的产品设计及设计审查,如此能降低材料和零件的成本.它包含了产品设计,生产工程,品质保证和制造等跨功能(部门)的合作. VA也被当做提升竞争力标竿. 价值工程----Value Engineering(VE)
一九五四年, 由美国国防部所发展出来, 是一种降低成本的方法与运用的方式. 目视管理----Visual Management
一种有效的管理方法,它以清晰可见的方式,提供信息及现物给工作者和管理者,以让大家能实时确认异常状况.
定置管理
定置管理是对生产现场中的人、物、场所三者之间的关系进行科学地分析研究,使之达到最佳结合状态的一门科学管理方法,它以物在场所的科学定置为前提,以完整的信息系统为媒介,以实现人和物的有效结合为目的,通过对生产现场的整理、整顿,把生产中不需要的物品清除掉,把需要的物品放在规定位置上,使其随手可得,促进生产现场管理文明化、科学化,达到高效生产、优质生产、安全生产。定置管理是“5S\"活动的一项基本内容,是\"5S\"活动的深入和发展。
开展定置管理应按照以下六个步骤进行:
(一)进行工艺研究
1.对现场进行调查,详细记录现行方法(工艺流程图等) 2.分析记录的事实,寻找存在的问题(方法研究和时间研究) 3.拟定改进方案
(二)对人、物结合的状态分析
在生产现场,人与物的结合有两种形式,即直接结合和间接结合。直接结合是指需要的东西能文即拿到手,不存在由于寻找物品而发生时间的耗费。间接结合是指人与物呈分离状态,为使其结合则需要信息媒介的指引。信息媒介的准确可靠程度影响着人和物结合的效果。
按照人与物有效结合的程度,可将人与物的结合归纳为ABC三种基本状态:A状态,表现为人与物处于能够立即结合并发挥效能的状态。B状态,表现为人与物处于寻找状态或尚不能很好发挥效能的状态。C状态,是指人与物没有联系的状态。这种物品与生产无关,不需要人去同该物结合。因此,定置管理就是要通过相应的设计、改进和控制,消除C状态,改进B状态,使之都成为A状态,并长期保持下去。
(三)开展对信息流的分析
人与物的结合,需要有四个信息媒介物:第一个信息媒介物是位置台帐,它表明“该物在何处”,通过查看位置台帐,可以了解所需物品的存放场所,第二个信息媒介物是平面布置图,它表明“该处在哪里”。在平面布置图上可以看到物品存放场所的具体位置。第三个信息媒介物是场所标志,它表明“”这儿就是该处”。它是指物品存放场所的标志,通常用名称、图示、编号等表示。第四个信息媒介物是现货标示,它表明“此物即该物”。它是物品的自我标示,一般用各种标牌表示,标牌上有货物本身的名称及有关事项。在寻找物品的过程中,人们通过第一个、第二个媒介物,被引导到目的场所。因此,称第一个、第二个媒介物为引导媒介物。再通过第三个、第四个媒介物来确认需要结合的物品。因此,称第三个、第四个媒介物为确认媒介物。人与物结合的这四个信息媒介物缺一不可。
(四)定置管理设计
定置管理设计,就是对各种场地(厂区、车间、仓库)及物品(机台、货架、箱柜、工位器具等)如何科学、合理定置的统筹安排。定置管理设计主要包括定置图设计和信息媒介物设计。 l.定置图设计 2.信息媒介物设计
(五)定置实施 1.清除与生产无关之物 2.按定置图实施定置 3.放置标准信息名牌
(六)定置检查与考核
定置管理的一条重要原则就是持之以恒。
全面质量管理
全面质量管理是在企业中以质量为中心,建立全员参与基础上的管理,全面质量管理的基本内容是\"三全\",即: (1)对全面质量的管理
全面质量指所有质量,即不仅是产品质量,还包括工作质量,服务质量。在全面质量中产品质量是核心。企业应以质量为中心。
(2)对全过程的管理
对产品的质量管理不限于制造过程,而是扩展到市场研究、产品开发、生产准备、采购、制造、检验、销售、售后服务全过程。 (3)由全体人员参与的管理
企业把\"质量第一,人人有责\"作为基本指导思想,将质量责任落实到全体职工,人人为保证和提高质量而努力。 全面质量管理的特点:
1采用科学的系统的方法满足用户需求
在全面质量管理中\"用户至上\"是十分重要的指导思想。
质量功能配置(QFD)方法:体现了开发产品应以市场为导向,以顾客的需求为唯一依据的指导思想,把产品的性能(功能)放在产品开发的中心地位,对产品性能进行定量描述,实现对功能的量化评价。 2以预防为主的事先控制的新时期 3计算机支持的质量信息管理 4突出人的因素
现代集成制造系统
计算机集成制造(CIM):CIM是一种组织、管理和运行企业的理念。它将传统的制造技术与现代信息技术、管理技术、自动化技术、系统工程技术等有机地结合,借助计算机,使企业产品全生命周期,即市场需求分析、产品定义、研究开发、设计、生产、支持(包括质量、销售、采购、发送、服务)及产品最后报废、环境处理等各阶段活动中有关的人/组织、经营管理和技术三要素及其信息流、物流和价值流(以产品T、Q、C、S、E等价值指标所体现的企业业务过程流,如成本流等)有机集成,并优化运行,以达到产品上市快、高质、低耗、服务好、环境清洁,进而提高企业的柔性、健壮性、敏捷性,使企业赢得市场竞争。
CIMS是一种基于CIM理念构成的计算机化、信息化、智能化、绿色化、集成优化的制造系统。 对于离散型制造,它主要分为五类技术:
(1)总体技术——系统总体模式,系统集成方法论,系统集成技术,标准化技术,企业建模和仿真技术,CIMS系统开发与实施技术。 (2)支撑技术 (3)设计自动化技术 (4)加工生产自动化技术 (5)经营管理与决策系统技术 (6)生产过程控制技术
质量管理小组(QC小组) QC小组,是企业员工围绕生产活动中的问题自由结合、自愿参加组织起来,主动进行质量管理活动的小组。 QC小组活动的指导思想是:(1)当家做主的思想,(2)质量第一的思想,(3)循序渐进的思想,(4)统计学的思想。QC小组还必须坚持“四个一切”:一切为用户服务;一切以预防为主,一切用数据说话,一切按PDCA循环办事。
QC小组的主要职能有:
(l)学习质量管理方法,制定措施,实施计划。
(2)组织好基础技术的学习,练好基本功,提高专业技术水平。 (3)要以用户的评价作为衡量QC小组活动好坏的标准。
(4)及时总结QC小组的活动成果,这是重要的一环,务必进行。一是课题解决的情况,二是QC小组活动的基本经验教训。
建立QC小组:①选课题:在确定QC小组课题时,一般首先选择一个月到二个月能见成效并尽量是一些共同性的问题为好。②确定QC小组成员:启发、动员与课题有关的人员参加QC小组时,尽量是同班工作的人组织起来,这样便于开展活动。③确定QC小组长。④QC小组登记。
目视管理技术
目视管理是利用形象直观、色彩适宜的各种视觉感知信息来组织现场生产活动,达到提高劳动生产率目的的一种管理方式。它是以视觉信号为基本手段,以公开化为基本原则。 目视管理的优点
1目视管理形象直观,有利于提高工作效率
2目视管理透明度高,便于现场人员互相监督,发挥激励作用
大机器生产既要求有严格的管理,又需要培养人们自主管理、自我控制的习惯与能力。目视管理为此提供了有效的具体方式。
3目视管理有利于产生良好的生理和心理效应 目视管理的内容
1规章制度与工作标准的公开化 2生产任务与完成情况的图表化
3与定置管理相结合,实现视觉显示信息的标准化 4生产作业控制手段的形象直观与使用方便化 5物品的码放和运送的数量标准化 6现场人员着装的统一化与实行挂牌制度 7色彩的标准化管理 推行目视管理的基本要求
统一,即目视管理要实行标准化,消除五花八门的杂乱现象。 简约,即各种视觉显示信号应易懂,一目了然。
鲜明,即各种视觉显示信号要清晰,位置适宜,现场人员都能看得见、看得清。 实用,即不摆花架子,少花钱、多办事,讲究实效。
严格,即现场所有人员都必须严格遵守和执行有关规定,有错必纠,赏罚分明。
5S活动
“5S”是整理(Seiri)、整顿(Seiton)、清扫(Seiso)、清洁(Seikeetsu)和素养(Shitsuke) 。“5S”活动的对象是现场的“环境”,它对生产现场环境全局进行综合考虑,并制订切实可行的计划与措施,从而达到规范化管理。“5S”活动的核心和精髓是素养,如果没有职工队伍素养的相应提高,“5S”活动就难以开展和坚持下去。 “5S”活动的内容
(一)整理
目的是:①改善和增加作业面积;②现场无杂物,行道通畅,提高工作效率;③减少磕碰的机会,保障安全,提高质量;④消除管理上的混放、混料等差错事故;⑤有利于减少库存量,节约资金;③改变作风,提高工作情绪。
(二)整顿
要点是:①物品摆放要有固定的地点和区域,以便于寻找②物品摆放地点要科学合理。③物品摆放目视化,使定量装载的物品做到过目知数,摆放不同物品的区域采用不同的色彩和标记加以区别。
(三)清扫
要点是:①自己使用的物品,如设备、工具等②对设备的清扫,着眼于对设备的维护保养。③清扫也是为了改善。
(四)清洁
要点是:(1)车间环境不仅要整齐,而且要做到清洁卫生,保证工人身体健康,提高工人劳动热情;(2)不仅物品要清洁,而且工人本身也要做到清洁,(3)工人不仅要做到形体上的清洁,而且要做到精神上的“清洁”,待人要讲礼貌、要尊重别人;(4)要使环境不受污染,进一步消除混浊的空气、粉尘、噪音和污染源,消灭职业病。
(五)素养
素养即教养,努力提高人员的素养,养成严格遵守规章制度的习惯和作风,这是“5S”活动的核心。 开展\"5S\"活动的原则
(一)自我管理的原则
(二)勤俭办厂的原则
(三)持之以恒原则
虚拟制造
TQCS难题,即以最快的上市速度(T--Time to Market),最好的质量(Q--Quality),最低的成本(C--Cost),最优的服务(S--Service)
虚拟制造是实际制造过程在计算机上的本质实现,即采用计算机仿真与虚拟现实技术,在计算机上群组协同工作,实现产品的设计、工艺规划、加工制造、性能分析、质量检验,以及企业各级过程的管理与控制等产品制造的本质过程,以增强制造过程各级的决策与控制能力。 虚拟制造的主要特点是: (1)产品与制造环境是虚拟模型
(2)可使分布在不同地点、不同部门的不同专业人员在同一个产品模型上同时工作,相互交流,信息共享,减少大量的文档生成及其传递的时间和误差,从而使产品开发以快捷、优质、低耗响应市场变化。
按照与生产各个阶段的关系,将虚拟制造分成三类,即以设计为核心的虚拟制造(DesignCentered VM)、以生产为核心的虚拟制造(ProductionCentered VM)和以控制为中心的虚拟制造(ControlCentered VM)。 “虚拟制造”应包括产品的“可制造性”、“可生产性”和“可合作性”的支持。 虚拟制造技术体系结构: (1)虚拟制造平台 (2)虚拟生产平台
※虚拟生产环境布局※虚拟设备集成※虚拟计划与调度 (3)虚拟企业平台
※虚拟企业协同工作环境 ※虚拟企业动态组合及运行支持环境 (4)基于PDM的虚拟制造平台集成
※支持虚拟制造的产品数据模型※基于产品数据管理(PDM)的虚拟制造集成技术※基于PDM的产品开发过程集成 虚拟现实技术在生产制造上的应用 1. 基于VR技术的产品开发
2. 虚拟现实技术在制造车间设计中的作用 3. VR技术在生产计划安排上的应用 采用虚拟制造技术可以给企业带来下列效益
1. 提供关键的设计和管理决策对生产成本、周期和能力的影响信息,以便正确处理产品性能与制造成本、生产进度和风险之间的平衡,作出正确的决策;
2. 提高生产过程开发的效率,可以按照产品的特点优化生产系统的设计;
3. 通过生产计划的仿真,优化资源的利用,缩短生产周期,实现柔性制造和敏捷制造;4. 可以根据用户的要求修改产品设计,及时作出报价和保证交货期。 成组技术(GT)
成组技术GT(GroupTechnology)是一门生产技术科学,它研究如何识别和发掘生产活动中有关事务的相似性,并对其进行充分利用。即把相似的问题归类成组,寻求解决这一组问题相对统一的最优方案,以取得所期望的经济效益。
将零件分类成组常用的方法有: 视检法;
视检法是由有生产经验的人员通过对零件图纸仔细阅读和判断,把具有某些特征属性的一些零件归结为一类。 生产流程分析法;
生产流程分析法PFA(ProductionFlowAnalysis)是以零件生产流程及生产设备明细表等技术文件,通过对零件生产流程的分析,可以把工艺过程相近的,即使用同一组机床进行加工的零件归结为一类。 编码分类法:
按编码分类,首先需将待分类的诸零件进行编码,即将零件的有关设计、制造等方面的信息转译为代码。为此,需选用或制定零件分类编码系统。 成组技术的应用
产品设计方面,制造工艺方面,生产组织管理方面 方法研究
方法研究的定义是:对现有的或拟议的工作(加工、制造、装配、操作)方法进行系统的记录和严格的考查,作为开发和应用更容易、更有效的工作方法以及降低成本的一种手段。 方法研究的目的: 1、改进工艺和程序
2、改进工厂、车间和工作场所的平面布置 3、改进整个工厂和设备的设计 4、经济的利用人力,减少不必的疲劳 5、改进物料、机器和人力的利用,提高生产率 6、改善实际工作环境,实现文明生产 7、降低劳动强度 方法研究的特点 1、求新意识
2、方法研究的指导思想——挖掘企业内部潜力 3、方法研究的着眼点——系统整体优化
工效学的定义为:研究人和机器、环境的相互作用及其合理结合,使设计的机器和环境系统适合人的生理、心理等特点,达到在生产中提高效率、安全、健康和舒适的目的。 人因工程
人因就是要去改善那些人们所常使用的器物与其所处的周遭环境,其使人与人本身的能力(Capabilities)、本能极限(Limitations)和需求之间(Need)能有更好的配合。
人因工程的主要目的有:
一、提高效率,如提高产质、减少失误,增加信赖度等等。
二、增进人性价值(Human values),如降低工作压力和疲劳度,增进安全,提升舒适感和满足感,以及改善生活品质等。
发展人因的主要目的就是要「以物就人」,而人因的本质简单地说就是要「如何使物就人」。 德尔菲法
德尔菲法的基本特征:匿名性、多次反馈、小组的统计回答。 德尔菲法本质上是一种反馈匿名函询法。其作法是,在对所要预测的问题征得专家的意见之后,进行整理、归纳、统计,再匿名反馈给各专家,再次征求意见,再集中,再反馈,直至得到稳定的意见。其过程可简单图示如下: 匿名征求专家意见——归纳、统计——匿名反馈——归纳、统计„„,若干轮后,停止。总之,它是一种利用函询形式的集体匿名思想交流过程。 价值工程
价值的定义为V——价值(Value Idex);F——功能评价值(Function Worthy);C——总成本(Total Cost)。价值工程包括三个基本要素,即价值、功能和成本。 价值工程的技术方法:
1.对象选择的方法
(1)ABC分析法,亦称成本比重分析法或巴雷特(Pareto)分析法,此种方法亦可用于对库存零件的分类控制。 在利用ABC分析法进行对象选择时,将零件按其成本大小进行排队,优先选择成本大的少数零件作为价值分析的对象。
(2)百分比法 这是一种按某项费用或某种资源,在不同产品和作业中或某一产品或作业的不同组成部分中,所占的比重大小来选择对象的方法。其次,与各产品的产值比重进行比较。
(3)产品寿命周期法 产品从试制到被淘汰的整个过程称为产品的寿命周期。一般经过四个阶段:投产期,发展期,成熟期和衰退期。
2.功能评价的方法
1)确定一个产品(或部件)的全部零件的现实成本。 2)把零件成本核算成功能成本。
3)确定功能的必要成本(最低成本,也称目标成本)。
4)计算各功能的价值。计算公式仍采用 V—F/C,但这里的 V 以价值系数表示之, F是以实现这一功能的必要成本来计量,C表示实现这一功能的现实成本,即 “价值系数=实现功能的必要成本/实现功能的现实成本”
计算出的功能价值(即价值系数)一般都小于1,即现实成本高于必要成本。现实成本和必要成本之差(C-F)就是改善的幅度,也称期望值。
5)按价值系数从小到大的顺序排队,确定价值工程对象、重点、顺序和目标。 3.方案创造的方法
(1)畅谈会法 头脑风暴法。 4.方案评价的选择的方法 (l)优缺点列举法
(2)定量评价法该方法:直接打分法,加权打分法。 价值工程的工作程序
1.选择价值工程对象2.收集情报3.功能分析4.创造新方案 5.分析与评价方案 6.验证和定案7.检查实施情况,评价活动成果
丰田生产系统
丰田生产系统实际上由准时制生产和自动故障检报两大支柱组成,再辅之以全面质量管理发展而成。 丰田生产方式在组织管理上具有两个明显的特点:
1)它是最大限度地将任务和责任分摊到生产线上产生附加价值的工人身上。
2)它具有及时发现每道工序或每件产品任何故障的机制,并能迅速发现问题的根源,使其不再重复。 核心竞争力
核心竞争力是企业竞争力中那些最基本的能使整个企业保持长期稳定的竞争优势、获得稳定超额利润的竞争力,是将技能资产和运作机制有机融合的企业自组织能力,是企业推行内部管理性战略和外部交易性战略的结果。 核心竞争力的特征
(1)核心竞争力为企业提供了一个进入多种产品市场的潜在途径(延展性)。 (2)核心竞争力能为顾客带来较大的最终用户价值(有用性)。 (3)核心竞争力应不易被竞争对手模仿(独特性)。
(4)叠加性。即两项或多项核心能力一经叠加,可能会派生出一种新的核心能力。核心竞争力的不断演化 1 单件生产方式(workshop) 2 大量生产方式(ma Production) 3 精益生产方式(lean production) 4 全球智能化生产方式 先进制造技术中的物流支撑 物流是制品从生产线的终点到达消费者的有效移动以及从原材料的供应者到生产线起点的移动这样一种广泛范围的活动,是在制造业和商业中使用的语言,这一活动包括货物输送,保管,装卸搬运,包装,库存管理,工厂或仓库布局,订货处理,市场预测以及对顾客的服务,信息活动。 物流活动的基本功能有输送,保管,装卸包装及情报等5项活动。 适应于先进制造技术的物流模式:
1 信息传递(库存物资,在制品数量,品种在线实时统计,ERP软件,供应链间联网,电子数据交换) 2 物资运输(自动化仓库,AGV自动化运输小车,计量包装容器标准化,运输路径优化,运输基础设施建设,工业物资配送中心,专业运输公司)
3 从业人员制度(严格可行的计划管理制度,精确的统计数据) 制造生产模式的演变与敏捷制造
敏捷制造的6个领域(集成产品与过程开发/并行过程、人的问题、虚拟企业、信息与控制、过程与设备、法律障碍) 分形企业的理论与实践
分形企业(fractalenterprise)是借用分形几何中的自相似性概念描述的一种新的生产方式。
分形企业的自相似性包括:①企业组织结构的自相似,即以过程为中心建立企业的组织;②目标自相似,即单元的目标与企业的目标一致。分形企业的优化目标是:时间、柔性、质量、成本、生态和社会性。组织结构的自相似性强调自主,目标的自相似性强调自律。分形企业通过自律和自主的统一,提高企业的效率和柔性的统一。 分形企业在自相似的基础上具有自组织性的特点,表现为:①自监控:产品质量、总数、效率和性能等方面的自监控;②自调控:企业能力利用、资源配置分配和评价的自调控;③自确定:工作时间、生产方式等的自确定;④自治性:生产安排和控制的自主自治;⑤不是各人行为的协调和控制,而是分形的面向结果的评价。在分形企业中,各个子系统在企业的总体目标下,自主寻求局部最优解,相互通过消息进行磋商和协调,得到企业的满意解。
分形企业的实践
文化层-在文化层,从企业的价值和思考模式考察企业。企业文化的变化是一个长期的渐进的过程。在分形企业中,将采取一种新的模式,如自组织模式。
战略层-在战略层,从企业的市场、产品、知识、组织、用户和业务流程多方面考察企业。
社会信息层-在社会信息层,从企业中的人的相互关系和作用考察企业。其方法来自社会学和心理学。在分形企业中,企业职工将是如图4所示的复杂人。在分形企业中,把职工看作是共同决策者、共同管理者、共同设计者等。最终目标是发挥人的创造性。高的创造性意味着职工自己对工作系统进行优化,对各种变化作出适应性反应。 在经济-资金层,从创造价值的角度考察企业。
分形企业的组织形式有利于资金、成本等的管理。 信息层-在信息层,从企业的信息流考察企业。在分形企业中,采用分布式结构和高度自治的单元,对企业信息系统的要求也就大大提高。如:任意信息点间的信息交流;大范围的进行问题讨论;各种不同应用软件的集成以迅速解决问题。
分形企业利用分形几何理论,对复杂的制造系统采用自相似原理进行分析和重组。从而使制造系统得到简化和优化,使制造系统具有自组织的结构和功能,使制造系统具有很大的灵活性和很高的效率。 现代工业工程与新产品开发
工业工程(Industrial Engineering) 动态联盟的新产品开发组织模式
敏捷制造是通过虚拟公司,又称为动态联盟实现的。虚拟公司是一种两家以上的独立机构为了抓住迅速变化的市场机遇,各个成员在充分信任和合作的基础上联结起来的虚拟结构的公司,联盟成员发挥各自的核心专长,以求获得共同的收益。一旦完成既定的任务,该公司可自行解散。通过虚拟公司的运作,可以迅速有效地集成必要的资源,对市场变化灵活快速地进行反应。通过向外寻求合作伙伴,企业可以把精力集中于自身关键技术的研究,关注自身优势的核心技术。
精益生产的基本原理就是:不断改进﹑消除对资源的浪费﹑协同工作和沟通。精益生产方式的设计技术也体现这一思想。
并行工程是集成﹑并行地设计产品及其相关的各种过程(包括制造过程和支持过程)的系统方法。 现代信息技术的支持 “改善”是一种经营理念
改善(KAIZEN)的定义:一种企业经营理念。用以持续不断地改进工作方法与人员的效率等。
相对于一触即发式的创新思想而言,改善思想所带来的效果许多看来是微不足道的小效果。但改善的步伐虽然是一小步一小步、阶梯式的,随着时间的推移,它会带来戏剧性的重大成果。改善思想要求每一位管理人员及作业人员,要以相对较少的费用来改进工作方法。而这种运用常识的方法及低成本的改善手法,即能确保阶梯式的持续进步。长期而言,所积累的大成果足以获得回报。“改善”也是一种低风险的方式,因为在改善的过程中,如果发觉有不妥当之处,管理人员随时都可回复到原来的工作方法,而不需耗费大成本。
改善是一种开放式的管理,追求比现状更好:成本更低、效率更高、质量更好、交货期更短,至于如何达到的方法没有规定,需要每个人贡献出自己的智慧 TPM(全面生产管理) 推行TPM可期待的效果
1、有形效果●
提高设备综合效率●
提高劳动生产性●
减少市场投诉●
降低各种损耗●
缩短生产周期●
提高间接部门效率
2、无形效果●
企业体质的革新●
全员意识的革新●
充满活力的企业●
有成就感、满足感、能实现自我的企业●
有信心、能让客户信赖的企业
TPM的定义(TPM = Total Productive Management) ★追求生产系统效率(综合的效率)的极限为目标
★从意识改变到使用各种有效的手段,构筑能未然防止所有灾害、不良、浪费的体系(最终达成:「0」灾害、「0」不良、「0」浪费的体系)
★从生产部门开始、到开发、营业、管理等所有部门 ★从最高领导到第一线作业者全员参与
将装备出现故障以后采取应急措施的事后处置方法称为“事后保全( Breakdown Maintenance ,BM)”,将装备在出现故障以前就采取对策的事先处置方法称为“预防保全( Preventive Maintenance,PM)”,将为延长装备寿命的改善活动称为“改良保全( Corrective Maintenance ,CM)”,把为了制造不出故障不出不良的装备的活动叫做“保全预防( Maintenance Prevention ,MP)”,最后将以上BM、PM、CM、MP四种活动结合起来称之为“生产保全( Productive Maintenance ,PM) TPM的9大活动 第一,TPM基石-5S活动
5S是整理、整顿、清扫、清洁、素养的简称。5S活动是一项基本活动,是现场一切活动的基础,是推行TPM 阶段活动前的必须的准备工作和前提,是TPM其它各支柱活动的基石。 第二,培训支柱-“始于教育、终于教育”的教育训练
教育活动放在TPM活动各支柱的首位,主要想突出教育在TPM活动中的地位,什么都知道的人不会留在企业里。对于企业来讲,推进TPM或任何新生事物都没有经验,必须通过教育和摸索获得,而且TPM没有教育和训练作为基础,TPM肯定推进不下去。可以这么认为,教育训练和5S活动是并列的基础支柱。 第三,生产支柱-制造部门的自主管理活动
TPM活动的最大成功在于能发动全员参与,如果占据企业总人数约80%的制造部门员工能在现场进行彻底的自主管理和改善的话,必然可以提高自主积极性创造性,减少管理层级和管理人员,特别是普通员工通过这样的活动可以参与企业管理,而且能够提高自身的实力。所以自主管理活动是TPM的中流砥柱。 第四, 效率支柱-全部门主题改善活动和项目活动
全员参与的自主管理活动主要是要消灭影响企业的微缺陷,以及不合理现象,起到防微杜渐的作用,但对于个别突出的问题,就不得不采用传统的手段,开展课题活动。在TPM小组活动里按主题活动的方式进行,需要跨部门的可以组成项目小组进行活动。
第五, 设备支柱-设备部门的专业保全活动 所有的产品几乎都是从设备上流出来的,现代企业生产更加离不开设备。做好设备的管理是提高生产效率的根本途径,提高人员的技能和素质也是为了更好的操作和控制设备,因此设备管理是非常重要的,是企业必须面对的核心课题之一。将设备管理的职能进行细分是必要的,设备的传统日常管理内容移交给生产部门推进设备的自主管理,而专门的设备维修部门则投入精力进行预防保全和计划保全,并通过诊断技术来提高对设备状态的预知力,这就是专业保全活动。
第六, 事务支柱-管理间接部门的事务革新活动
TPM是全员参与的持久的集体活动,没有管理间接部门的支持,活动是不能持续下去的。其他部门的强力支援和支持是提高制造部门TPM活动成果的可靠保障,而且事务部门通过革新活动,不但提高业务的效率,提升服务意识,而且可以培养管理和领导的艺术,培养经营头脑和全局思想的经营管理人才。 第七, 技术支柱-开发技术部门的情报管理活动
没有缺点的产品和设备的设计是研究开发、技术部门的天职,能实现的唯一可能就是掌握产品设计和设备设计必要的情报,要获取必要的情报就离不开生产现场和保全及品质部门的支持,因此这种活动就是MP情报管理活动,设备安装到交付正常运行前的初期流动管理活动也属于此活动的范畴。 第八, 安全支柱-安全部门的安全管理活动
安全是万事之本,任何活动的前提都是首先要确保安全。安全活动定在第7大支柱,并不是安全第七重要,事实上安全活动从5S活动开始就始终贯穿其中,任何活动如果安全出现问题,一切等于0。 第九, 品质支柱-品质部门的品质保全活动
传统品质活动的重点总是放在结果上,不能保证优良的品质,更生产不出没有缺陷的产品.这种事后管理活动与抓住源头的事前管理的品质活动是不同的。品质保全活动放在最后一个支柱来叙述,是因为提高品质是生产根本目的,相对来说也是最难的一项工程。
柔性制造
多种方式进行柔性制造
细胞生产方式:与传统的大批量生产方式比较,细胞生产方式有两个特点:一个是规模小(生产线短,操作人员少),另一个是标准化之后的小生产细胞可以简单复制。由于这两个特点,细胞生产方式能够实现:(1)简单应对产量的变化,通过复制一个或一个以上的细胞就能够满足细胞生产能力整数倍的生产需求;(2)减少场地占用,细胞是可以进行简单复制的(细胞生产线可以在一天内搭建完成),因此不需要的时候,可以简单拆除,节省场地;(3)每一个细胞的作业人数少,降低了平衡工位间作业时间的难度,工位间作业时间差异小,生产效率高;(4)通过合理组合员工,即由能力相当的员工组合成细胞,可以充分发挥员工最高的作业能力水平。如果能够根据每一个细胞的产能给予员工相应的奖励,还有利于促成细胞间的良性竞争。
一人生产方式:我们看到过这样的情形,某种产品的装配时间总共不足10分钟,但是它还是被安排在一条数十米长的流水线上,而装配工作则由线上的数个人来完成,每个人的作业时间不过10到20秒。针对这样的一些作业时间相对较短的产品,如果我们能够打破常规(流水线生产),改由每一个员工单独完成整个产品装配任务的话,我们将可以获得意想不到的效果。
一个流生产方式:一个流生产方式是这样实现的:取消机器间的台车,并通过合理的工序安排和机器间滑机板的设置让产品在机器间单个流动起来。它的好处是:(1)极大地减少了中间产品库存,减少资金和场地的占用;(2)消除机器间的无谓搬运,减少对搬运工具的依赖;(3)当产品发生品质问题时,可以及时将信息反馈到前部,避免造成大量中间产品的报废。一个流生产方式不仅适用于机械加工,也适用于产品装配的过程。 企业的八大综合经营品质 1)经营方针和企业领导的作用 2)顾客和市场的理解和对应
3)经营战略、经营计划的制定和展开 4)人才培养和员工满意 5)程序管理和持续改善 6)信息的共享和有效利用 7)企业活动的成果 8)顾客满意
现场管理的金科玉律 第一步:先去现场
现场是所有信息的来源。当你看到资料时,要怀疑它!当你看到测量数据时,要怀疑它! 第二步:检查现物
改善是从问题认定开始。一旦认识清楚了,那就已经成功了一半。督导人员的工作之一,应当是要经常保持注视行动的现场,而且依据现场和现物的原则来认定问题。 第三步:采取暂行处置措施 第四步:发掘真正原因并将之排除。 第五步:标准化以防止再发
可视管理 可视管理一:找出问题 可视管理二:接触事实
可视管理三:管理人员必须管理5个M:人员(MANPOWER) 机器(MACHINES) 材料(MATERIALS) 方法(METHODS) 测量(MEASUREMENTS)。
可视管理四:5S 整理,整顿,清扫,清洁,教养.可视管理五:公布标准 可视管理六:设定目标
M u d a 任何没有附加价值的作业,在日本称为Muda。 现场所发现的 M u d a,分为下列7类: 1.制造过多的Muda。
此种形式的 M u d a,是由于提早生产造成的,尤其是对昂贵的机器,为了有效地运用而生产超过需要的数量。 2.存货的Muda。
成品、半成品、零件及物料的存货,是不会产生任何附加价值的,反而增加了营运的成本;因为占用了空间,需要额外的机器及设施。
3.不良重修的Muda。
不合格品干扰了生产活动,也耗费昂贵的重修费用。
4.动作的Muda。
任何人体的动作,若是没有直接产生附加价值,就是没有生产力。 5.加工的Muda。
机器加工作行程过长或过份加工、冲床没有生产力的冲击时,以及去毛边的动作,都是加工 M u d a。 在许多实例中,加工 M u d a也是由于流程无法同步所造成的。作业员经常把工作分得太精细,超越了需要的程度,这也是加工Muda的另一个例子。 6.等待的Muda。 7.搬运的Muda 为消除这样的搬运 M u d a,任何与主生产线分离的所谓离岛作业,应尽其可能并入主生产线内。
M u d a、无稳、无理,有时经常一起使用,在日本并称之为“三无”。
无稳(不规律化)不论何时,作业员工作的顺利性被中断了,或是零件、机器或生产流程的流畅性被中断了,就表示出现了无稳。无理(劳累的工作)无理意指作业员、机器以及工作的流程,处在一种费力气的状态下。
工业工程的基本职能 1.规划2.设计3.评价4.创新 丰田生产方式
用自己的手来写标准作业 协同作业就是一切 “创造流水线”是基础条件
丰田生产方式的两根支柱(1)非常准时(JUST 个人技术和集体行动相结合 目的是降低成本 均匀化生产 彻底分析浪费问题 现场主义 运用权限监督 传票卡
企业也有自律神经 重视长年使用的设备 以一当十 丰田式的指令系统
TIME)(2)自働化
IN 六大管理方法
“抽屉式”管理,现代管理也称之为“职务分析”。 “危机式”管理,“末日管理”
“一分钟”管理,具体内容为:一分钟目标、一分钟赞美及一分钟惩罚。 “破格式”管理,通过对人事的管理达到变革创新的目的。
“合拢式”管理,管理强调个人和整体的配合,创造整体和个体的高度和谐。 “走动式”管理,它主要是指企业主管体察民意、了解实情与下属打成一片,共创业绩
80/20原理
重要启示便是:避免将时间花在琐碎的多数问题上,因为就算你花了80%的时间,你也只能取得20%的成效:你应该将时间花于重要的少数问题上,因为掌握了这些重要的少数问题,你只花20%的时间,即可取得80%的成效。
一位工业工程师的养成训练,大致可分为四部分说明:
(1)科技与数理基础:包括物理、化学、数学、统计、电子计算器程序设计等。
(2)一般工程训练:包括工程力学、图学、制造工程、工程材料、电工原理、化工概论等。
(3)工业工程专业训练:包括动作与时间研究、工厂布置、工程经济、作业研究、生产管制、品质管制等。 (4)管理科学训练:包括工业组织与管理、会计与成本分析、工业心理学、行为科学等。
管理工作中的“七种浪费”
等待的浪费;协调不利的浪费;闲置的浪费;无序的浪费;失职的浪费;低效的浪费;管理成本的浪费 现场管理工具 1,5S管理
整理(SEIRI)、整顿(SEITON)、清扫(SEISO)、清洁(SETKETSU)、素养(SHITSUKE) 2,标准化
创新改善与标准化是企业提升管理水平的2大轮子。标准化有以下四大目的:技术储备、提高效率、防止再发、教育训练。 3,目视管理三要点: ①
无论是谁都能判明是好是坏(异常) ②
能迅速判断,精度高 ③
断结果不会因人而异 目视管理可以分为3个水准:
①
初级水准:有表示,能明白现在的状态 ②
中级水准:谁都能判断良否
③
高级水准:管理方法(异常处置等)都列明 4,管理看板
目标分解展示板,设备计划保全日历,区域分担图,安全无灾害板,班组管理现况板,定期更换板,QC工具,TPM诊断现况板.5,全面生产管理TPM
工业工程与服务业流程改善
一、动作分析
1、
停滞
2、
无效动作
3、
次序不合理
4、
不均衡(如:太忙碌、太清闲等)
5、
浪费
二、工程分析
制品分析、作业者工程分析、联合工程分析、事务工程分析
三、事务工程分析
1、信息传递的快速化、准确化。
2、
去除多余的表单文件,减少无效的事务工作。
三、时间分析
针对时间及产出做定量的分析,找出时间利用不合理的地方,从而进行改善的方法。
生产线平衡的定义
节拍(Cycle
time)是指连续完成相同的两个产品(或两次服务,或两批产品)之间的间隔时间。换句话说,即指完成一个产品所需的平均时间。 瓶颈:一个流程中生产节拍最慢的环节。 空闲时间:指工作时间内没有执行有效工作任务的那段时间,可以指设备或人的时间。
“生产线工艺平衡”即是对生产的全部工序进行平均化,调整各作业负荷,以使各作业时间尽可能相近。 生产线工艺平衡的改善原则方法
1、首先应考虑对瓶颈工序进行作业改善,作业改善的方法,可参照程序分析的改善方法及动作分析、工装自动化等IE方法与手段;
2、将瓶颈工序的作业内容分担给其它工序;
3、增加各作业员,只要平衡率提高了,人均产量就等于提高了,单位产品成本也随之下降;
4、合并相关工序,重新排布生产工序,相对来讲在作业内容较多的情况下容易拉平衡;
6、分解作业时间较短的工序,把该工序安排到其它工序当中去。
ABC理论与实施
ABC是Activity-Based Costing的英文缩写,即我们通常所说的作业成本法。 成本动因:是指导致成本发生的任何因素,亦即成本的诱致因素。 成本动因可分为资源动因和作业动因.至少有六个决策要在ABC系统实施前做出,即:
1.系统是和现存系统集成还是成为一个独立系统?
2.在实施前是否应有正式设计?
3.最终系统的所有权应归谁?
4.系统应该有多精确?
5.系统应该报出历史的还是未来的成本?
6.初步设计应该复杂还是简单?
标杆管理的五阶段流程模型: 1、决定向标杆学习什么 2、组成标杆学习团队 3、选定标杆学习伙伴 4、搜集及分析资讯 5、采取改革行动
“牛鞭效应”产生的主要原因是由于需求被人为的放大了。
MRPII/ERP没有有效办法解决这个问题,但JIT的实施能够有效地降低“牛鞭效应”的影响。当然长期计划还是必要的,而JIT计划功能不强。从几方面来说:
1.
需求是波动的,JIT只能在现有产能中有限度的自我调节。
2.
每项生产资源的获得都有一个前置时间,而且这个时间会随时变化的。
3.
生产计划如年计划,月计划,周计划等对企业的指导作用也是企业资源安排所必须的。
项目管理九大知识体系: 范围管理:项目为何总是做不完?范围管理要界定 风险管理:项目风险引发的问题、成因及防范法宝 沟通管理:做好项目沟通计划“灵犀”才能“点通” 质量管理:如何做好软件工程质量管理? 时间管理:磨刀不误砍柴功如何避免工期拖延? 成本管理:开源?节流?项目成本管理如何进行 人力资源管理:项目管理中“人”占什么位置 采购管理:增加利润的另一种方法:向采购要利润 整合管理:项目管理中的协调该怎么做?
风险管理
“隐形杀手”来自何方:
1、技术、性能、质量风险
2、项目管理风险
3、组织风险
4、项目外部风险 防范“杀手”四大法宝:
1、风险识别
2、风险分析(1)风险影响:它是指一旦风险发生可能对项目造成的影响大小。如果损失的大小不容易直接估计,可以将损失分解为更小部分再评估它们。风险影响可用相对数值表示,建议将损失大小折算成对计划影响的时间表示。(2)风险概率:它是风险发生可能性的百分比表示,是一种主观判断。(3)风险值:它是评估风险的重要参数。“风险值”=“风险概率”ד风险影响”。如:某一风险概率是25%,一旦发生会导致项目计划延长4周,因而,风险值=25%×4周=1周。
3、风险应对
4、风险监控。最有效的风险监控工具之一就是“前10个风险列表”,它是一种简便易行的风险监控活动,是按“风险值”大小将项目的前10个风险作为控制对象,密切监控项目的前10个风险。每次风险检查后,形成新的“前10个风险列表”
沟通管理
在一个比较完整的沟通管理体系中,应该包含以下几方面的内容:沟通计划编制、信息分发、绩效报告和管理收尾。
语言、文字还是“形象”等沟通方式的选择。提倡积极沟通。保持畅通的沟通渠道。
质量管理
质量管理总是围绕着质量保证(QualityAurance)过程和质量控制(QualityControl)过程两方面。 软件质量保证(SoftwareQualityAurance,以下简称SQA)
时间管理
1、项目活动定义,将项目工作分解为更小、更易管理的工作包也叫活动或任务,这些小的活动应该是能够保障完成交付产品的可实施的详细任务。
2、活动排序,在产品描述、活动清单的基础上,要找出项目活动之间的依赖关系和特殊领域的依赖关系、工作顺序。
3、活动工期估算,项目工期估算是根据项目范围、资源状况计划列出项目活动所需要的工期。
4、安排进度表,项目的进度计划意味着明确定义项目活动的开始和结束日期,这是一个反复确认的过程。关键路径法(CPM)。
5、进度控制,进度控制主要是监督进度的执行状况,及时发现和纠正偏差、错误。
人力资源管理
1、角色和职责分配。
2、人员配备管理计划。
3、组织机构图。团队建设活动 绩效考核与激励
集中安排
培训
采购管理 制定采购计划:
1、制造、采购分析
2、合同类型的选择
3、采购计划编制
采购过程管理:
1、询价(Solicitation)
2、供方选择(SourceSelection)
3、合同管理 采购成本分析:
1、招标成本
2、建设成本
3、所有权损耗成本
成本管理
项目成本或投资估算,项目的现金流分析,项目的不确定性分析,项目挣值管理:挣值管理(EarnedValueManagement,EMV)是综合了项目范围、进度计划和资源,测量项目绩效的一种方法。它比较计划工作量、实际挣得多少与实际花费成本,以决定成本和进度绩效是否符合原定计划。
如何把握信息化项目管理
信息化项目的关键要素只有三个,即时间、成本、质量。
其中资源的最终体现是成本,目标的最终体现是绩效。因此,一个信息化项目最核心的制约因素就是这三要素:时间要素、成本要素、绩效要素。而绩效的评价和控制往往量化到质量上,即质量要素。 项目管理中有五个方面的角色在发挥影响和作用。
一是用户方的业务人员。二是用户方的决策人员。三是开发方的技术人员。四是开发方的项目管理人员。五是项目的监管者。
SWOT分析法
SWOT分析是一种对企业的优势、劣势、机会和威胁的分析,在分析时,应把所有的内部因素(包括公司的优势和劣势)都集中在一起,然后用外部的力量来对这些因素进行评估。
把识别出的所有优势分成两组,分的时候应以下面的原则为基础:看看它们是与行业中潜在的机会有关,还是与潜在的威胁有关。
机会与威胁分析,环境发展趋势分为两大类:一类表示环境威胁,另一类表示环境机会。
现场管理包括:现场的物料管理、计划管理、设备管理、工具管理、人员管理、排产管理、5S管理等等。 问: 什么是现场管理的 “ 三即三现 ” 法 ? 现场作业时一旦发现有问题,应 “ 即刻 ” 前往 “ 现场 ” , “ 即席 ” (当场)观察 “ 现实 ” 并 “ 即刻 ” 处理 “ 现场 ” ,从而切中问题要点并产生解决问题的决策 问: 现场管理指示应明确哪些内容 ? ( 5w1 法) · 何人( WHO ) · 何时( WHEN ) · 何事( WHAT ) · 何地( WHERE ) · 何故( WHY ) · 如何( HOW ) 问: 什么是作业现场的目视管理 ? 对作业现场的进度状况、物料或半成品的库存量、品质不良状况、设备故障、停机原因等,以视觉化的工具,进行预防管理。使任何人都有了解好与坏的状态,即使新进人员也能很快缩小作业上的品质差异。 问: 现场管理的 “A、B、C” 法? · 把现场所看到的东西或感想用笔记下来。
· 把与自己的看法或要求不合的部分分为 A、B、C 三级,并决定 A 是明天要改善的, B 是一周后要改善的, C 是一个月后要改善的。 · 与相关负责人进行沟通。
· 每次回到现场时,检查进行状况,直到满意为止。 问 : NODEEM 现场管理循环? ·Neatne- 整洁 ·Order- 秩序 ·Decoration- 美观 ·Efficiency- 效率 ·Expenses- 成果 ·Morale- 士气 问: 什么是现场管理 7P 作业完善循环?
7P 作业完善循环是指通过审视作业标准对作业目标点的偏差,来发现和补缀现场管理盲点和管理真空的一套完善的作业方法。
问: 什么是现场管理的雷区控制法?
雷区控制法是指现场管理者在充分认识管理现场的管理理念和作业方法中不可逾越的区域;进行合理回避或排除的一种作业方法。
问: 你的现场管理实行了 TPM 全面生产管理了吗? · 以追求生产系统效率(综合的效率)的极限为目标。
· 从意识改变到使用各种有效的手段,构筑能防止所有灾害、不良、浪费的体系。 · 从生产部门开始,到开发、营业、管理等所有部门。 · 从最高领导到第一线作业者全员参与。 问: 现场管理的 One-Best 运动? · 一处保管。
· 一日处理(今日事,今日毕)。 · 一个资料夹(资料夹一册化)。 · 一小时会议。
· 一张纸(报告书一张篇幅表达完全)。 · 一分钟电话。
· 一张原稿(不必复印,只保管原稿)。 一件工具(不用工具,或简化成一件)。 问: 什么是现场管理中的 “ 重点训示 ”?
培训内容的重点,做成图表形式,以条文形式或图解方式,使培训人员一目了然,易于学习和接受。 问: 什么是现场咨询的寻踪管理 ? 现场咨询的寻踪管理主要指资讯的共有化、业务的标准化、原则化、简单化等,借此提供迅速而正确的资讯给生产现场,并有效解决问题。
问: 现场管理中何时使用 “ 红牌 ”? · 整理不合格; · 需继续改善的对象; · 需继续清理的对象; · 物品用途不明;
· 物品劣化、变质、不良; · 脏污、不清洁的物品; · 未处理好的事件或问题。 问. 现场生产管理微缺陷的预知与判定 ? · 用眼睛看:有没有摇晃、偏摆的情况; · 用鼻子闻:有没有怪味道; · 用耳朵听:有没有怪声音;
· 用手摸:设备本体各部分有无异常的发热状况或异常振动等现象。 问. 车间现场管理几种常用方法?
· 蟑螂搜寻法:在一些不起眼的地方,可能会出现一些东西隐蔽地堆放着。 · 向上巡视法:或许这时你会看到天花板上用胶带贴的电线! · 向下巡视法:设备上、管道上可能搁着无人过问的抹布。 · 寻找舍不得的废弃物品法。 · 下班后巡视法。
问. 怎样进行人员识别的现场管理?
· 不同的佩戴: A.袖章、臂章、肩章,有资格认定的人员必须佩戴《认定章》; B.工卡颜色 人事编号,姓名后应加注职务和资格。
· 用不同的着装: A.熟练工与非熟练工着装不同; B.什么职务穿什么样的服装。 · 组织成员的相片化:将组织结构图画出,在相对应位置上,粘贴本人相片,公布于看板上。 问. 什么是现场控制点管理?
生产中有些作业点,可推动或制约整个作业流程的效率或质量,这就是关键作业点。控制它,就可能控制全线。管理行为也存在着这样的关键点,抓住它,对之实施全方位有效的控制就是控制点作业现场管理法。 问. 现场的安全管理?
现场安全管理主要是利用颜色刺激人的视觉,来达到警示及作为行为的判断标准,以起到危险预知的目的。 问.何时需要改善布局
· 现状布局已阻滞生产效率的进一步提高时 , 需要改善布局。
· 生产技术变更时,亦要进行相应的布局设置,以发挥更大的效益 , 需要改善布局。 · 设计(工艺)变更时, 需要相应改善布局 ,以发挥效益。 · 产量增加时 需要改善布局 。 · 增加新机种时 需要改善布局 。 · 场地搬迁时 需要改善布局 。 · 人事安全受到危害时 需要改善布局 。 问. 现场管理如何处理污染与泄漏 ? · 明确污染源的对象; · 大扫除; · 调查污染发生源; · 决定污染最严重的重点部位; · 详细调查,为什么会有污染; · 对策案之检讨; · 制作实施计划和实施对策; · 实施处理。 问. 如何进行饭堂、宿舍的现场管理?
· 饭堂工作人员必须着装整齐、必须穿白工衣、戴卫生帽、带毛巾。 · 地面干净、无饭菜、杂物、异物、空间无异味。 · 炊具光洁明亮,水池、锅台、打饭窗口台干净,无油污。 · 死角无脏物、饭菜渣、垃圾、虫蝇等。 · 炊具、碗筷摆放整齐,饭菜要有覆盖物。 · 窗台上不允许挂有碗勺等饮用物品。 · 桌凳干净、无油污。
· 宿舍走道内无垃圾、垃圾放于指定的垃圾桶且不得积满。 · 宿舍墙壁、天花板无灰尘、蜘蛛网。 · 宿舍走道、楼梯间无积水。
· 注意团队精神,企业形象,讲礼貌,讲文明。 问. 会议室与会议制度的现场管理 ? · 每一次会议的主题应表现鲜明;
· 会议室宽敞、明亮、整洁、美观、桌椅摆放整齐;
· 桌椅摆放的方向或形式应能体现与会者的等级高低,分清主要入口与出口; · 尽可能隔音,音响设备保持随时使用都不出异常情况; · 要有会议记录,会议时间限定; · 上次会议决议执行情况检查;
· 新的议程或新的决议,执行措施与方法,检查措施与方法,下次会议召开时间拟定; · 会后应清理及时。
问. 图书室、资料室、档案室的现场管理 ? · 通风、采光符不符合规定,照明度符不符合需要;
· 码放架是否排放整齐,高矮度适不适合取放方便,有无陈旧危险之处;
· 码放的物品是否标识清晰,分门另类是否规范,是否定期清扫和作过适当的防腐防潮防霉防盗处理。 · 借取及归还手续是否严格规范清晰; · 存放物品本身的档案是否建立完善;
· 防火措施是否符合要求,破损或陈旧程度如何。 问. 财务室、控制室、机要室的现场管理 · 保密程度做得如何,有否违反规定;
· 室内设施保养程度如何,防水、防电、防盗、防霉、防火的工作和设备都准备得如何; · 室内是否卫生清洁,码放整齐,标准清晰明显,出入登记和领取发还登记都严格把关没有; · 有否违规堆放私人或违规的物品; · 警示标识是否醒目。
问. 实验室、检验室、化验室的现场管理 ? · 防止易燃易爆、化学腐蚀、有害气体泄出等危险事故发生的设施和措施有否完善; · 易燃易爆、腐蚀性、剧毒性等物品的存放和保管是否规范、合理、正确,有无事故的 · 隐患,有无这些物品危害性的的醒目的警告标识和隔离手段; · 对非专职工作人员进出的条件规定是否标识清楚和严格执行; · 室内是否符合专业作业要求,专职人员是否按要求进入和进行作业;
· 室内的作业工具,物品,设施是否摆放合理,符合安全要求,标识清晰,清洁卫生; · 是否符合企业的保密等级条例规定。 问. 搬运方式的现场管理 ? · 机动性原则。即保持随时可搬动的状态。 · 自动化原则。
· 避免等待和空搬的原则。 · 缩短移动路途的原则。 · 安全原则。
· 确定固定搬运人员和搬运频度。 问. 特殊材料的现场管理 ? 对材料特殊性认识不清楚的话就有可能出现差错,这也正是现场管理盲点之一,若不特别留意,就无法生产出合格的产品;就会使设计人员的辛苦努力化成泡影;公司的商战大计也无法实现。 问. 材料申领的管理 ? 将材料分类管理。如分开生产主料和生产副料两大部分。生产主料可按生产计划发给。紧急情况下,使用《紧急出库表》,由相应级别的管理人员确认后领取。副料则根据单价、用途、数量的不同,设置相应的审批管理人员。 · 正确填写《材料申请表》,报上司承认。正常情况下的口头申领一概应以拒绝。
· 管理人员率先示范。 “ 宽以待己,严以待人 ” 的做法。应严格得以控制。办理手续不仅仅是为了留下一个凭证,也是为了精确控制数量和避免浪费,使管理人员心中有数。 问. 产品造成的企业环境恶劣怎样现场管理 ? · 严格按国家规定的粉尘、污水、有害的生产排泄物的排放标准进行选址,建厂规划与设计; · 尽可能大地扩大绿化面积;
· 严格按国家允许使用标准范围采购和建设安装生产设备; · 严格进行排污除尘设备的配套建设;
· 加强生产排泄物的再生处理工作,并配套好必要的再生处理设备和设施; · 及时清理、清扫,提高企业全体员工的绿色环保意识。
第15篇:现场改善术语要点
第1楼 [推荐]现场改善术语解说 (绝对超值)
现场改善术语解说
u 允收品质水准(AQL) Acceptable Quality Level
允收品质水准是顾客与供货商之间的交易运作模式.容许供货商在协议的条件下, 交 付某一限定比率的不良品.
v 问五次为什么(Ask why five times)
一个发掘问题真正原因的常识原则.
w 查核现场(Check gembutsu)
当欲探寻问题的根源时, 在现场实地有形的物体加以调查.x 符合性(Conformance)
用以表示产品或服务能达到相关规格、合约或规则, 所要求的一个确定指示或评定.
y 管制图(Control Chart)
为一个具有上下管制界线的图.在其图上, 绘有一系列的样本或样本组统计量的测定
值.此图通常绘有一条中心线, 用以协助侦测所绘之统计值, 有否趋向其中之一条管制界线.
z 成本-----Cost
在QCD的范畴中, [成本]一词通常系指成本管理,而非削减
成本.成本管理涉及到对各种资源
的适度管理, 以及消除所有类别的无驮(浪费).在此种方式下, 会降低总成本.
{ 跨功能(部门)管理----Cro-functional management
为达成QCD跨越部门之间的管理活动.
| 周期时间----Cycle time
作业员完成加工一个产品的实际耗费时间(参阅产距时间Takt time).
} 交期----Delivery
在QCD的范畴中, [交期]一词系指交货时间以及数量, 皆要符合顾客的要求.
~ 不按受, 不制造, 不流出----Don’t get it, don’t make it, don’t send it.
在现场里推行的一个常识性口号.在任何一个QCD计划中, 应将品质是最优先的信念予以实践
出来.例如: 不要从上制程接受不良品, 不要在自己的制程上制造出不良品, 以及一旦有不良 品制造出来, 不可明知故犯地流到下一制程.
uu 失效树分析-----Failure Tree Analysis(F T A)
借着确定因果关系及利用树关图, 来认定问题的机率.失效树分析是用来分析及事先避免任 何安全性及可靠度上的问题.
uv 现场管理的五项金科玉律----Five golden rules of gemba management
一套在现场推行[现场改善]时,最实用的提醒剂.. (1) 当有问题发生时[要先去现场].
(2) 检查现物.
(3) 当场采取暂行处置措施.
(4) 发掘真因并排除.
(5) 标准化以防止再发.
uw 5M----Five M’s
在现场用以管理资源的方法.这五项资源皆以英文[M]开头, 特地称之为[5M]----人员
(Manpower), 机器(Machine), 材料(Material), 方法(Method)和量测(Measurement).
ux 5S----Five S’s
是一种为维持良好工厂环境的查核表, 为使工作场所更有秩序, 效率及纪律.它源自于五个
有S音开头的日文----Seiri(整理).Seiton(整顿), Seiso(清扫), Seiketsu(清洁),
Shituke(教养).套用英文相当之字则为Sort(分类=整理), Straighten(定位=整顿), Scrub(刷洗=清
扫), Systematize(制度=清洁)及Standardize(标准=教养).某些分司则采用为5C作战..Clear out(清除=整理),Configure(形迹=整顿), Clean & check(清洁及检查=清扫), Conform(遵
守=清洁)及Custom & practice (习惯及实践=教养).
uy 流线生产----Flow Production
及时生产方式的基本支柱之一.在流线生产里, 机器是依据加工的顺序排列.如此, 工作物 在制程之间的流动, 就不会中断或停滞.
uz 失效模式及有效性分析----FMEA
借着分析零组件对最终成品失效模式的影响结果; [失效模式及有效性分析]可以用来对一个
新产品的作何潜在的设计缺点, 做事前预测及消除.FMEA也可用来针对新生产设备的役计审查 活动(叫做制程FMAA)
u{ 现场----Gemba
日文一词意指[实地], 现在则采用管理上的术语, 意义为[工作场所], 或者称之为[产生附加
价值]的地点.在制造业来说, 通常系指[工场].
u| 现物----Gembutsu
在现场里所发现的有形对象.例如: 工作物, 不良品, 夹具, 工具, 及机器.
u} 去现场----Go to gemba
现场改善的第一项原则, 这是一个提醒剂.不管何时, 当异常发生或经理人员欲了解生产作
业的现状, 他(或她)应立即去现场, 因为现场是所有信息的来源.
vt 海因利奇法则----Heinrich’s Law
一项有关于意外事故与伤害的比率法则.海因利奇用下列的比率表示之: 重度伤害: 轻度伤
害: 无伤害=1:29:300此公式表示: 当你看到一个因意外事故重伤的人, 同样的事故可能也造
成二十九人的轻微伤害.同时, 或许有三百人经历同样的事故, 但幸运地没有受到伤害.
vu 危险预知训练----Hiyari KYT(Kiken-yochi training)
KYT系指对预见的危险做事前演练, 并且采取预防的措施.
vv 惊吓报告----Hiyari report(Scare report)
惊吓报告, 是由工人写给上级主管的报告.用以报告会造成品质问题及/和意外事故的不安全 状况.
vw 石川(鱼骨)图----lsikawa(fishbone)diagram
由石川声教授首先发展出来的图表.用来表示原因(制程)及影响(结果)的关系.此图系用来
确定真因, 同时也是解决问题的七种基本手法之一.
vx 国际标准组织9000系列标准----( ISO 9000 Series standards)
一套关于品质管理及品质保证的国际标准规范.此套规范用以协助公司对品质体系应执行的
要件, 做好文件的管理, 以确保符合产品的规格要求.
vy 自动化----Jidhoka (Autonomation)
每当不良品制造出来时, 能使机器自动停止下来的一种装置.此装置是JIT导入的要点.
vz 自主研现场改善----Jishuken gemba kaizen
在一九六零年代初期, 自主研(自主的JIT研究小组)首先在丰田集团的公司的现场, 开始推? 蠮IT的活动.
v{ 及时生产方式JIT----(Just-in-time)
藉由在公司内, 消除流程间所有各种的无驮(浪费), 并以及时送达货品以符合顾客的要求, 来达成产品或服务的最佳品质, 成本及交期的一种生产体系.最早是由丰田汽车公司发展出 来, 亦称为丰田生产体系(Toyota Production System), 精实生产方式(Lean production
system)及看板生产方式(Kanban System)
v| 自主管理----JK (jishu kanri)
自主管理的日文意思为自动自发管理之意.系指工人在其上级管理人员的指导之下, 将参与
改善活动视为日常工作的一部分.此与品管圈活动有所不同, 后者系自原性并由工人依自已的 意志进行.
v} 改善观念----Kaizen concepts
在推行改善时, 所必须了解及关践的主要观念.
(1) 改善与管理.
(2) 改善与结果.
(3) 导守P D C A 循环/SDCA循环.
(4) 品质第一.
(5) 用数据说话.
(6) 下一制程就是顾客.
wt 改善事例----(Kaizen Story)
用于组织各层级中的一种解决问题之标准程序.改善事例分为八大步骤:
(1) 主题选定.
(2) 现况调查及目标设定.
(3) 资料分析以确定真因.
(4) 对策拟定.
(5) 对策实施.
(6) 效果确认.
(7) 标准化.
(8) 检讨上述过程及未来计划.__________________ 九思:
视思明,听思聪,色思温, 貌思恭,言思忠,事思敬, 疑思问,忿思难,见得思义
最后由 陈雷 在 06-22-2004 08:09 PM 编辑
向版主报告此贴 | IP地址: 61.53.76.61 06-22-2004 02:00 PM
陈雷 孤独牛粪
第2楼 是不是值啊,不值下面的不要买了,呵呵
wu 改善活动体系----Kaizen systems
性
别:
欲达成世界级所必须建立的主要活动系.
(1) 全面品质管理(Total Quality Management)
(2) 及时生产方式(Just-in-time production system) 注册日期: Apr 2004 来
自: 河南理工 发贴数量: 611 金
币: 7714
(3) 全员生产保全(Total Productive Maintenance)
(4) 方针展开(Policy Deployment)
(5) 提案建议制度(Suggestion System)
(6) 小集团活动(Small-group activities)
wv 看板----Kanban
在及时生产方式中, 用以管理批量生产的一种沟通工具.看板, 在日文里系指一种信号板,
挂附在生产线某一已知号码的零件或产品上, 并指示运送某一已知的数量.当这些数量的零件
用完之后, 此看板即送回原处, 变成生产指示, 以再生产.
ww 工数----Kosu
生产作业, 可区分为机器的时间和人员的时间, 工数系指在一已知的制程中, 完成一个产品
的加工动作所耗费的人员时间.是将此一制程的工作人数, 乘上实际完成此制程的时间, 再除
以所生产的产品数量, 用来衡量作业员的生产力.工数降低是在现场生产力改善的主要衡量方 式之一.
wx 晨集----Morning market
在现场中的[每日例行工作], 包含在工作之前依据现物原则, 检查前一天所做的不良品(现物
), 如此才能尽早采取对策.此一包含现场人员的(而非职员)会议, 是在早上开工时的第一件 事.
wy 无驮----(浪费)Muda
日文一词意指[浪费].当使用在工作场所的管理时, 泛指
没有附加价值的活动.在现场里,
仅有两种型态的活动: 有附加价值和没有附架价值.在现场改善中, 首先致力于消除各种没
有附加价值的活动.消除下列范围的[无驮], 期使对Q C D产生重大的改善: 生产过多, 库存
, 不良品, 动作.加工.等待.搬运及时间.无驮的消除即是以低成本, 常识性的方法, 来求 改善的缩影.
wz 无稳----Mura
日文意指不规律或变化性.
w{ 无理----Muri
日文意指过劳性或困难性.
w| 一个流----One-Piece flow
在及时生产方式里, 仅允许每次将一个产品从此制程流到另一制程, 使无驮最小化.
w} 柏拉图----Pareto chart
将原因从最大影响度, 依序排至最小影响度的一种图表工具.它是依扰[柏拉图原理]而来,
是由品管大师裘兰博士(J.M.Juran)订定出来的.此80:20原则, 指出[80%的结果, 是来自于
20%的原因所造成].柏拉图为解决问题的基本七手法之一种.
xt PDCA----Plan-Do-Check-Action
计划—执行—查核—外置, 是从事持续改进(改善)所应遵行的基本步骤.
xu 后拉式生产----Pull Production
及时生产方式的基本要件之一, 前制程仅补充生产后制程所耗用掉数量的产品.
xv 前推式生产----Push Production
后拉式生产的相反词.前制程尽其所能生产愈多的产品, 欲不顾及后工程实际上的需求数;
并且不管是否有所需求, 全部将之送给后制程.
xw 品质保证最佳生产线证书----QA Best-Line Certification
一种厂内的认证制度.用以证明某一特定生产线, 其品质保证的成效达到世界级水准.
xx QCD----(Quality, Cost, Delivery)
品质, 成本及交期, 被视为管理的首要目标.当管理能成功达成QCD的目标时, 则顾客的满意 及企业的成功, 也会随之而来.
xy QCDMS
在现场里, 经常将M士气(Morale)及S安全(Safety)加入QCD, 做为欲达成的目标.
xz 品质机能展开----QFD (Quality Function Deployment)
一种管理的方法.首先先确认顾客的需求, 然后经由各个阶段对产品展开下去: 设计, 工程 , 生产, 销售, 及售后服务.
x{ QS 9000
美国版的ISO 9000系列.由三大汽车公司要求施行于其供应厂商.与ISO 9000系列之一般要
求来作说明比较, QS 9000明定一些额外的要求, 特别
是对标准及矫正行动, 要求持续地改进 .
x| 品质----Quality
在QCD的范畴理, 品质系指送达至顾客的产品或服务的品质.在此状况下, 品质是指符合规格
和顾客的要求.广义而言, 品质包含产品或服务的设计, 生产, 交货及售后服务工作的品质.
x} 品管圈----QCC(Quality Control Circles)
由一小群员工(十人或以下)组成, 以从事品质改善或自行改善的研究团体.品管圈导源自日
本, 被称为品质管制圈(品管圈).品管圈是在工作场所, 自原地执行改善活动, 持续从事一部
分全公司性的相互教育.品质管制, 自我发展及生产力改善的计划.
yt SDCA----Standardize-Do-Check-Action
标准化—执行—查核—处置, 是在维持现关时, 应当遵行的基本步骤.
yu 同时实现QCD----Simultaneous realization of QCD
最高管理阶层应清楚公司内, 所有的阶层都是致力于过成品质, 成本及交期之工作任务.最
终的目标是QCD能同时实现.但是, 三者之间首先要实现的, 仍应以品质为第一优先.
yv 小集团活动----Small-group activity
为解决他们自己作场所的问题, 而形成的现场集团活动.通常由现场的作业员五~十人组成集
团.他们的活动大都与品质圈活动类似.然而小集团活
动并不仅限于诸如品质改善.降低成本
, 全员生产保全(TPM)和生产力改善, 同时也扩及到娱乐性或其它社交性活动.
yw 标准化----Standardization
标准化为现场改善三项基本活动之一, 意指将工作的最佳方式予以文件化.
yx 标准作业----Standardized work
人员, 机器和材料的最佳组合状况.标准作业的三要素是产距时间, 作业顺序和标准在制品 数量.
yy 标准----Standards
工作的最佳方式, 即是由管理当局针对分司所有主要的业务, 设定一套方针, 规则, 指示及
程序书, 作为全员执行其工作的指导, 以求获致好的成果.
yz 统计制程管制----Statistical proce control (SPC)
应用统计尝上的技巧, 以管理控制制程.有时亦经常与统计品质管制互用.
y{ 储存室----Store room
在现场用以储存在制品或物品的场所.储存室与一般的仓库是不相同的, 因为在储存室里, 仅能保存标准的储存量.
y| 提案建议制度----(Suggestion System)
在日本, 提案建议制度, 是高度被归属于个人导向改善活动的一种方式.日本式的提案建
议制度, 着重于激发员工工作士气, 和建设性的参与感,
它远甚于欧美对形能的注重以经济上 及金钱上的奖劢.
y} 产距时间----Takt Time
完成生产一个顾客所订产品的所需时间.是以总生产时间, 除以生产需要数而订定出来的.
zt 3K
日文用来表示在现场里惯见的印象----危险( Kiken ), 脏污( Kitanai )和劳累(Kitsui),
与此形成直接对比的, 是理想的现场, 为一个能附加真正价值, 以及达成QCD构想来源的场所 .
zu 3M
指无驮(Muda----浪费), 无稳(Mura)和无理(Muri).这三个字词常用来当做改善的查核点,
协助工作人员及管理当局, 以确认可供改善的地方.
zv 在现场的3M----Three M’s (3M) in gemba
在现场三个主要需加以管理的资源----人员(Manpower), 材料(Material)和机器(Machine).
有时再加上方法(Method)和量测(Measurement)而称为5M..
zw 全员生产保全----TPM ( Total productive maintenance)
全员生产保全, 是意图在机器的整个寿命期内, 获取最大设备效率的发挥.TPM牵连到所有部
门各个层级里的每一个人, 它透过小集团和自主活动, 激劢员工从事工厂的保全活动.它包含
如下的基本要件: 保全体系之发展, 基本的厂房环境维
持教育, 问题解决技巧, 和零故障及现
场零意外的活动.由工作人员所做的自主保全, 是TPM的重要支柱之一.5S则为TPM的第一步骤 .
zx 全公司品质管制----(TQC) Total Quality Control
为品质而组成的改善活动, 包含了公司的每一个人----管理人员和工作人员, 以整合总体的
力量, 致力于每一个层面的改善.它设想这些活动, 最终将获致顾客满意度的提升企业经营的
成功.在日本, 使用全面品质管理TQM(Total Quality Management)为名词已相当普遍, 现在 已取代了TQC名词.
zy 两天期现场改善----Two-Day gemba kaizen)
在日产汽车公司及其供货商内, 实施的现场改善活动.它是选定某一特定制程, 及由内部改
善指导老师, 工程师和生产线上管理人员组成的小集团, 在现场里花费二天时间, 利用及时生
产方式和其它有关的查核表, 以达成改善目标.
zz 价值分析----Value Analysis
一九四七年, 由美国奇异电气公司麦尔斯(L.D.Miles) 所导入降低成本的方法.它着眼于
上游阶段的产品设计及设计审查, 如此能降低材料和零件的成本.它包含了产品设计, 生产工
程, 品质保证和制造等跨功能(部门)的合作.VA也被当做提升竞争力标竿.
z{ 价值工程----Value Engineering(VE)
一九五四年, 由美国国防部所发展出来, 是一种降低成本的方法与运用的方式.在日本VA?
蚔E几乎都被视为相同的目的(参看价值分析).
z| 目视管理----Visual Management
一种有效的管理方法, 它以清晰可见的方式, 提供信息及现物给工作者和管理者, 以让大家 能实时确认异常状况.
第16篇:低成本管理办法——现场改善
低成本管理办法——现场改善
所谓低成本管理方法,不是仅限于探讨如何降低成本的,而是一种费用较低的管理方法,现场改善即是一种。现场改善管理起源于日本,已被公认是一种主要的管理观念。
“改善”,意指持续不断地改进,它的步线是一小步一小步,阶梯式的,但随着时间的演进,它会带来戏剧性的重大成果。“改善”与创新不同,创新是一触即发式,令人瞩目,感受到实质的成果,但它的成果经常有争议,“改善”是运用常识的方法及低成本的“改善”手法,即能确保阶梯式的持续进步。它还是一种低风险方式。因为在改善的过程中,如果发觉有不妥当之处,管理人员随时都可回复到原来的工作方法,而无需耗费大成本。
一〃现场改善要遵循PDCA循环/SDCA循环;在“改善过程”中,首先要建立计划──执行──核查──处置,即PDCA循环,以此作为改善持续运作的工具,以达成“维持标准”和“改进标准”的目标。“计划”是指建立改善的目标。“执行”是指依计划推行。“核查”是指确认是否按计划的进度在实行,以及是否达成预定的计划。“处置”是指新作业程序的实施及标准化。以防止原来的问题再次发生,或者是再设定新的改进目标。PDCA不断地在循环。一旦达到改善的目标,改善后的现状便随即成为下一个改善的目标。PDCA的意义就是永远不满足现状,因为员工通常较喜欢停留在现状,而不会主动去改善。所以管理人员必须持续不断地设定新的挑战目标,以带动PDCA循环。任何一个新的工作流程,在初期都是呈不稳定状态。开始进行PDCA改善时,必须先将任何现有的流程稳定下来,此一稳定的过程称之为:标准化──执行──查核处置,即SDCA循环。
在当前的流程里,每当发生异常时,便必须反问自己下列问题:是否因为没有标准而发生的?是否因为没有遵守标准而发生的?或者因为标准不适当而发生的?唯有建立了标准,并且确实遵守,以将当前的流程稳定下来,才能再进行下一个PDCA循环。 二.主要的改善活动
1〃及时生产方式:及时生产方式的目的是要消除各种没有附加价值的动作和程序,同时达成一个去芜存菁的生产体系,以便更具弹性地去适应顾客的需求变化。要实现理想的及时生产方式,必须持续不断地实施一系列的改善活动,以消除现场中没有附加价值的工作。及时生产方式能够急速地大幅度降低成本,缩短交货周期,增强公司的获利能力。
2〃全员生产保全:全员生产保全着重于设备质量的改进。它通过总体的预防保养制度来延长设备的寿命,以追求设备效率的最大化。
3〃设定目标:管理部门应设定明确的改善目标,以指引每一位员工,同时能正确领导所有的改善活动,向既定目标迈进,最高管理部门要有一个达到目标的计划,往下传达至下一管理层,直至达到现场为止。而现场围绕目标展开一系列的工作。
4〃提案建议制度:它的功能着重在激励员工的参与来提高士气,激发员工对现场改善的兴趣,提出自己的建议。无论他们的建议有多小,管理者都应给予鼓励并有选择的付诸实施。管理阶层不期望能从每一个建议中获得很大的经济利益。着重培养,开发具有改善意识及自律化的员工,日积月累到很大的经济效益。 5〃小集团活动:所谓小集团活动是指,在工作现场的环境里,在公司内以非正式、自愿性质组成团体,去执行特定的工作任务。小集团活动不仅局限于质量方面的课题,而且也包含了成本、安全及生产力等方面的课题。 三〃现场改善
1〃现场与管理:在现场里,生产顾客满意的产品才能使公司生存和兴隆。常规组织的各个阶层──高级管理阶层、中级管理阶层、工程师职员及现场督导人员,都是为了提供现场必要的支援而存在。进一步而言,现场不仅是所有改善的活动场所,也是所有信息的来源。因此,为了解决现场发生的大小问题,管理阶层必须密切接触现场的实情。换句话说,不论管理阶层提供什么样的协助,都应是源自现场的特定需求。一旦管理阶层不尊重,不珍视现场时,便会经常下达一些不适当的指示,要求和其它支援服务给现场造成错误。
2.现场管理的金科玉律
大多数的管理人员,较喜欢把办公室当做工作的场所,而且希望自己能远离发生事件的生产现场。仅通过每天、每周、甚至每月一次的报告和会议,来接触、了解现场的实情。与现场保持密切的接触及了解,是效率化管理的第一步骤。因此有5项现场管理的金科玉律: (1)当问题(异常)发生时,要先去现场。 (2)检查现物(有关的物件)。 (3)当场采取暂行处置措施。 (4)发掘真正原因并将之排除。
(5)标准化──以防止同样错误再发生。 3.维护厂房良好环境的5S:
5S是代表5个日文字词,它是厂房现场维持的构成要项。
(1)整理(seini)将现场里需要与不需要的东西,区别出来。并将后者处理掉。 (2)整顿(seiton)将整理后需要的东西,安排成为有秩序的状态。 (3)清扫(seiso)保持机器及工作环境的干净。
(4)清洁(seikesu)延伸干净的概念至更彻底,并且持续执行上述3个步骤。 (5)教养(shitsuke)以设立目标的方式,来建立自律以及养成从事5S的习惯。 厂房良好环境的维持,表示员工士气高昂及纪律严谨。任何公司都可以在短期内达成一个高水准有纪律的公司。然而要长久维护下去,可就是一件极富挑战性的工作了。而且,5S一旦消失不见,就会显现出一个杂乱无章的现场。 4.检查现物 一有问题或异常的状况时,管理人员应该到现场去检查现物。借着在现场详细检视现物,重复地问着“为什么”而确认出问题的原因,而用不着使用那些高深复杂的科技。改善是从问题认定开始,一旦认识清楚了,那就已经成功了一半。管理人员的工作之一,应当是经常保持注视行动的现场。而且依据现场和现场的原则来认定问题。而不是在会议室里聚集在一起讨论问题。
5〃找出真正的原因: 应用现场现物原则及一般的常识,可以迅速地解决许多问题。好好地呆在问题的场所,观察现物,而且下定决心找问题的真正原因。许多与现场有关的问题,都可以即时地当场解决。其余的问题诸如:技术上的困难或新科技系统的导入,才需要长久的准备计划。
发掘现场原因的最有效方法之一,就是持续地问“为什么?”直到找到问题的原因为止。举例来说,假设你看到一位工人,正将铁屑洒在机器之间的通道地面上。 你问:“为何你将铁屑洒在地面上?” 他答:“因为地面有点滑,不安全。” 你问:“为什么会滑,不安全?” 他答:“因为那儿有油渍。” 你问:“为什么会有油渍?” 他答:“因为机器在滴油。”
你问:“为什么会滴油?”
他答:“因为油是从联结器泄漏出来的。” 你问:“为什么会泄漏?”
他答:“因为联结器内的橡胶油封已经磨损了。”
经常地利用问为什么,就可以确认出问题的原因以及采取对策克服之。
〖作者〗生产基地工程师
第17篇:《现场改善》读后感800字
《现场改善》读后感800字
王洪涛
今天拜读了今井正明先生《现场改善》一书,这本书分十四章,向我们阐述了改善焦点,也给我们指出了改善的重点,在质量、成本和交付等主要的项目中,质量永远应该放在第一位,如果产品或服务本身质量不佳,公司就不可能赢得市场竞争。下面就对本书的内容谈下我的感受。
一、《现场改善》中讲到5S是实施现场改善的第一步。近年来,我们公司也在大张旗鼓推行5S,管理人员在解放思想,工人的工作习惯在改变,生产现场通过改善环境焕然一新,员工的进取心得到加强,产品质量问题明显减少,现场脏乱差问是得到改善,最终得到客户认可。但书中讲到5S每步实施要一步一个脚印,不能急于求成就跳过了一些很重要的步骤,否则固化难以持续,最后就是形似神不似,要培养员工独立改善的思想。
二、改善目标是实现质量最优、消除浪费,交货期最短。现场改善主体是员工,我们在实际的生产当中,往往在交货期与质量上发生冲突,生产主管总是做一些“救火”,为完成数量牺牲质量,车间有些工人做计件追工时追数量,过程质量得不控制,发生质量问题并没有深入分析去刨根问底,最后大家都可以找一堆借口,把持续改善当成了下次做好的挡箭牌,产品带着潜在问题欠债交客户,发生问题再派人去现场整改,增加了大量的人工成本浪费。书中讲到质量、成本、交付他们之间有着十分紧密的联系,应该是先有质才有量,如果质量不过关,不管摆在客户面前价格有多么低,都无法打动他们,因此降低不合格率,眼光要瞄准最常见的5种不合格品上解决。
三、标准化是现场作业准则。如果工作场所已具备标准,工人也按标准行事,那么此过程就在掌控之下,下一步就是调整现状,并提升标准,这就需要PDCA工作持续改进的生产模式,结合生产现实,我们生产的产品很多的不健全和缺陷,或者是执行和监管不到位,下面工人干活流程不清,培训并没有深入工人心里,也导致我们产品质量波动大,隐形质量问题也多。
四、生产中的浪费,消除不增加附加值的工作。我们平时的七大浪费每个人都会讲出几点,但书中讲的浪费增加了“不均”和“无理”,不均是有变动的意思,无理则是指滥用或过载,任何事只要费力和不规律就有问题,书中讲到一但平稳工作中断,或是缺件,产品变更,机器没跟上,当然我们日常工作中经常碰到,这点在我们实际生产常见。
最后我想说,看一本书都会从中找到一些受用的启示和方法,我们要把所学到的东西运用到实际工作中去,我们要做的是如何把这些理解成自已的,要学会渔而不只是得到鱼。
第18篇:生产现场改善方案
东莞市摩卡科技有限公司
制造中心生产现场改善报告
尊敬的胡董事长、涂总:
你们好!
本人很高兴加入东莞市摩卡科技有限公司,也同时感谢胡董及涂总的信认 ,本人将尽心尽职把公司的品质、效率搞上去,降低成本、节约资源,以最少的投入创造最高的利润,同时也希望领导的支持和帮助,以下是我对公司现状分析及改善方案。
现状分析
1、生产方面:
1》没有生产流程图,标准工时,作业指导书,产能评估报告,按此人员的排布是否最合适?
2》生产线没有辅助治具的投入(工具、夹具)。 3》现场无7S 管控。
4》现场产能进度跟进无法提现,无生产看板,反应不出该线在做什么、并且现场管理拿什么现场数据去把握现状。
5》人员纪律松散,工衣着装颜色统一,不利于目视管理,在流水线分不清那个是管理那个是员工、那个是QC、那个是助拉,找也难
6》现场规划不合理,无法提现一个顺畅的生产制程。
7》产品制程划分不合理,在组装部份还有在焊接PCB板,焊线或焊零部件。
8》生产线没有物料员,物料管控失控。
9》没有异常问题的检导,如生产品质例会、新产品导入会议 10》现场管理的专业技能须进一步提升,执行力差。
2、品质方面
1》来料检验控制没有标准及依据。(电子料、五金、线材、塑胶、包材)
2》没有品质过程控制相关规定。 3》出货检验没有标准性。
4》工程没有成品检验基准书、外观检验标准、部件检验基准书及制程生产的流程图、SOP、BOM(完整性)工夹具。 5》来料检验项目没有记录档案,无法追逆及控件控制。
3、生管(PMC)方面
1》新产品导入(PP\\MP\\试产)没有产前会议的召开。 2》产品没有标准工时对计划的安排有一定的难度,不确定性 3》欠料特别严重。
4》公司没有体系运作的模式。
针对以上相关问题本人提出以下相关改善方案 一:培训教育方面
1、组织各部们管理人员对其管理的专业知识、理论知识及技能进行培训与考核,以提升自我管理能力并作成培训计划大纲及试卷来对管理能力的评估。
2、组织作业员基本知识与专业技能及企业文化的培训。以提高其技能达到我司之要求并作成培训计划大纲、及试卷来对其技能的评估。 二:组织架构方面
1、生产部组织架构图的制定与完善。
2、生产部管理担当岗位职责范围制定与执行。
3、部门程系文件的制定、评审与执行。三:现场管控方面
1、目标管理
1.1目标就是在一定时期内必须达成的成果。依据PMC下达的生产计划进行生产,为达目标,总是以目标为目的开展工作,对工作结果是否符合目标要求,一边开展工作。对工作结果是否符合目标要求进行评价或反省,以利于达成下一个目标借鉴目标管理的目的。
1.2交货期是管理者的主要工作之一,现场实际作业应把握:生产作业计划的合理性、生产计划与实际空难、计划调整的影响、人员状况、员工技能、缺料设备故障引起的停产、不良品对策及处理零部件\\工装夹具\\生产铺料是否齐全、生产是否正常、工作方法是否改善。
1.2.1现场的基本方法:深入一线、信息是否畅通、了解生产能力、注意员工状态、时间与动作研究。
1.2.2现场的注意事项:异常处理的制度化、现场教育、解释、工作职责明确、公正评价员工。
2、
问题的把握与改善
2.1当目标没有完成时先要了解真因,人员问题还是工作问题、组织问题还是目标问题、当前问题还是将来问题、内部问题还是对外问题、表象问题还是本质问题,利用现场分析改善手法5M1E(人、机、料、法、测、环),将问题逐一分解、深入分析,解决问题步骤:问题的明确化-----问题现状的把握-----目标设定-----界定问题发生原因-----原因分析、证据调查-----针对原因的对策-----对策的可行性分析-----对策的实施-----效果的掌握-----标准化。针对车间存在的各类质量问题,运用帕拉图+头脑风暴法+鱼骨图,对车间存在的各类质量问题进行分析,找出主要原因并拟定改善计划。
2.2配合工程标准资料(SOP、技术资料、流程图、工位分布图)依据标准作业,在相关关资料没有完善的情况下,组织部门管理统筹相关资料并作成文档形成文件以便后续可查及参考。
2.3组织管理对员工进行多能化作业培训,一人会多个岗位的作业内容,落实自检互检、降低作业不良、确保产品零缺点。优秀员工评比活动落实,做到评比的公正性,制定优秀员工评选管理制度,提高员工对工作的积极性。
2.4生产管理看板(生产线)制定,看板管理也是生产当中最有效的一个管理,看板相关内容:生产机型、订单批次、数量、计划每小时产能、每小时实标产能、差异、完成数、不良数、不良率、异常状况、拉长、PE、IE、IPQC、物料员等内容,当你走到生产线看一下看板时你就一目了然。
2.5晨会制度有效性,会议不宜过长,要简短精要,晨会是人员点到、活动发表、作业指导、生产总结、唤起注意、培训教育、信息交流的场所,有利于团队精神建设,能产生良好的精神面貌,提高干部自身水平,提高工作布置效率,养成遵守规定的习惯。
3、现场管理的实施方法
3.1重视所有的管理项目,决定重点的管理项目,原则是不给下个工程或客户添异常,设定目标值,计划达成率、直通率、不良率、QC提检合格率、客户投诉率。
3.2运用P-D-C-A管理循法,把未达标之项目有计划性的改善。P计划:达成生产,D实施:实行计划—作业设定,C检查:检查目标与实绩差,A行动:采取对策或者改善。
3.3管理方针:
3.3.1生产部工作口号:不接收不良品、不制造不良品、不传递不良品。
3.3.2品质管理方针:质量第
一、高效准时、客户满意、不断提高。
3.3.3生产管理方针:创新技术,改进生产工艺:科学管理,强化运作和谐:挖掘潜力,充分调动积极性:追求卓越,全面提升生产效率。3.3.4管理的要求:
3.3.4.1:已落实岗位置责任制为基础,实行全员责任包干制。
3.3.4.2:任务是死的,有条件要执行,没有条件创造条件也要执行。
3.3.4.3:决定了的事情就是对的,如有凝问,事后再说。
3.3.4.4:必须奖罚分明,且要及时,到位。3.3.4.5:必须建立全方位信任和信誉。
3.3.5:自主管理:以给自已做事的心态工作。自负其责,在符合标准的情况下自已拿主意。不推卸责任,以自我为跟本,完成工作任务。
3.3.6:三检法:自检,互检和专检,其作用是针对三个不。(不接收不良、不制造不良、不送出不良)要实行双检靠的是自主管理,灌输双检的重要性,不定时的现场抽查,有问题出现时强调双检关联双方的责任。
3.3.7:修理作业:修理作业是针对不良品的纠正措施,要通过修理进行举一反三,题出返馈意见,防止再发生,埋头苦干并不是一件好事,修理员是生产管理者、优其是拉长的摇蓝,也是拉长的培养对象。
3.3.8:现场作业必须按标准作业指导书作业,配合IE优化生产制程,消除制程中的七大浪费(等待的浪费、作业不良的浪费、加工所存在的浪费、搬运的浪费、加工过多的浪费、在库的浪费、工序不当浪费),改善治工具的有效性、提升生产效率,标准化作业。
4、七S现场管理法: 为什么要推行7S,7S可以塑造企业的形象、降低成本、准时交货、安全生产、高度的标准化、创造令人心旷神怡的工作场所 ,现场改善等方面发挥了巨大作用。
4.1:制定7S培训计划表。
4.2:制定7S检查日程表。
以上只是计划执行对策的一部份,后续针对现状继续拟定计划完善。
报告人:胡钱明
2011.11.30
第19篇:某改善民生工作心得体会
XX改善民生工作心得体会
XX改善民生工作心得体会怎么写,以下是小编精心整理的相关内容,希望对大家有所帮助! XX改善民生工作心得体会
科学发展观同民生直接相关。只有科学发展观落实好了,民生问题才能解决好;只有着力解决好民生问题,才能把科学发展观落到实处。我们民政部门要把思想和行动统一到上级和县委、县政府的决策部署上来,紧紧抓住学习实践活动这一难得的机遇,以保障和改善民生为重点,切实把科学发展观内化为思想观念,转化为工作思路,凝聚为工作动力,落实为政策措施,转变为体制机制,实现党员干部受教育、科学发展上水平、人民群众得实惠的目标要求。
一、改善民生是民政部门落实科学发展观的根本要求
以人为本,是科学发展观的核心,明确要求把实现好、维护好、发展好最广大人民根本利益作为党和国家一切工作的出发点和落脚点,做到发展为了人民、发展依靠人民、发展成果由人民共享。以人为本,最根本的要求就是以人民群众最关心、最直接、最现实的利益问题为重点,保障和改善民生、促进人的全面发展。民生问题,不仅关系广大人民群众的根本利益,而且影响到整个国家发展的大局。以人为本的崭新理念,彰显了党和政府对民生问题的倾心关注和改善民生的坚定意志,更让人民群众看到了中国实现共同富裕、全面小康、和-谐社会的美好希望。在这一理念的指导下,“让我国经济发展成果更多地体现在改善民生上”,成为了过去几年党中央执政理念中的一个鲜明特征;“改善民生是最大的政治”,逐渐深入人心,民生问题被量化纳入政府考核监督机制,各级官员的政绩观正从GDP坐标向“民生本位”转变;财政支出结构、调控方式的深刻变化,逐步从生产建设型财政转向公共财政,一系列有利于人的全面发展、有利于改善百姓生活、有利于维护老百姓根本利益的措施民生举措的密集推出,看病、上学、社会保障等一系列民生问题逐步破题。
民政是为民之政,是改善民生的重要职能部门,最能体现发展成果让人民群众共享。民政工作的业务多元,包括救灾救济、社会救助、社会福利、优抚安置、基层民-主政治建设、专项社会事务管理等等,但集中到一点就是“为民”,都属于民生的基础,抓住了“为民”,就是抓住了民政工作的灵魂和精髓。民政工作的对象主要包括“三个群体”,即困难群体、特殊群体、优抚群众,当他们有了困难,要找的第一个部门就是民政部门,要找的第一个干部就是民政干部,党和政府的爱民之情、利民之意、为民之举,很多方面是通过民政干部传递到这“三个群体”手中。民政工作在落实科学发展观的过程中,抓住了保障和改善民生这个关键环节,就抓住了民政工作发展的牛鼻子。民政部门贯彻落实好科学发展观,着力保障和改善民生问题,不仅仅是关系到民政部门自身形象,更关系到人民群众切身利益,关系到党和政府在人民群众中的形象。因此,我们在这次学习实践活动中和今后的工作中,必须紧紧抓住科学发展观的核心内容,把“以民为本、为民解困、为民服务”民政工作核心理念落到实处,把“解决民生、落实民权、维护民利”的职责落到实处,把党和政府对人民群众的关心落到实处,让人民群众共享改革发展成果,使民政工作的职能作用在紧紧保障和改善民生的工作实践中得到全面提升。
二、改善民生工作取得的成绩
(一)社会救助体系基本建立,民生保障水平逐年提高。以农村低保制度的建立为标志,覆盖城乡的最低生活保障制度初步建立。在城市,基本实现应保尽保。在农村,保障面逐步扩大。救助对象的认定从依据社会身份到依据贫困程度转变,救助资源的运用从零散到综合转变,救助程序从随意、粗放型到规范、精细型转变,困难群众的基本生活得到了明显改善。
(二)积极扶持社会福利事业发展,社会福利社会化进程明显加快。在老年人社会福利方面,初步形成了以居家养老为基础、社区为依托、福利机构为补充的养老新格局。在儿童社会福利方面,全面落实了养育、教育、医疗、康复、住房、就业等各项政策。借助彩票公益金和社会慈善力量,对孤残儿童和困难家庭残疾儿童,积极组织实施了“明天计划”、“蓝天计划”等一批手术康复项目和儿童福利机构建设项目。 XX改善民生工作心得体会
中央经济工作会议提出,把改善民生作为保增长的出发点和落脚点。这体现了科学发展观的要求,反映了广大人民群众的愿望。把改善民生作为出发点和落脚点,既能使人民群众在保增长中得到实惠,又有利于实现保增长的目标。
以人为本是科学发展观的核心。发展依靠人民,发展为了人民。经过30年改革开放,我国综合国力大大提高,人民生活明显改善,但是,仍有不少民生问题需要解决。今年南方部分地区的冰冻雨雪灾害和四川汶川特大地震,给人民生命财产造成重大损失,灾后重建十分紧迫。这次国际金融危机又给我国经济带来严重冲击,经济出现下滑,部分企业困难,财政增收减缓,就业压力增大。这些都会给群众生活造成不利影响,增加改善民生的压力。越是困难时候,越要高度关注民生。把改善民生作为保增长的出发点和落脚点,是贯彻落实科学发展观的迫切要求,是社会主义生产目的的具体体现,也是扩内需保增长的有效途径。把改善民生作为出发点和落脚点,就是把改善人民生活作为保增长的根本目的,就是让人民群众在保增长中得到更多实惠。应对国际金融危机冲击,当务之急是扩大内需。扩大内需不仅要扩大投资,也要扩大消费。进一步改善民生,将明显促进消费的扩大,带动经济增长。
中央高度重视改善民生,近年来出台了多项政策措施造福百姓。这次扩大内需促进增长,把改善民生放在了突出位置。4万亿元投资中,有一半多的投资涉及民生方面;具体安排提高城乡居民收入,特别是提高农民和城乡低收入群体的收入。中央经济工作会议对改善民生又作出一系列部署。各地区、各部门要坚决贯彻中央的决策部署,实实在在做好各项改善民生的工作,让人民群众共享保增长的成果,促进经济平稳较快发展。
要下大气力解决涉及群众利益的难点热点问题。明年的就业形势将非常严峻,必须实施更加积极的就业政策,全方位促进就业增长。支持劳动密集型产业和中小企业发展,吸纳更多就业。加强大学毕业生就业指导和服务。鼓励具备条件的返乡农民工进行创业,积极创造条件安排好其他农民工就地就近就业。加快完善城乡社会保障体系,解决群众后顾之忧。保障城乡困难家庭基本生活。加快灾后重建,安排好灾区群众过冬生活。提高教育和医疗服务水平,完善公共文化服务体系。切实加强食品药品质量安全和生产安全工作。
今年即将过去,元旦、春节将至。灾区群众怎么样?困难群众怎么样?人民群众有哪些困难急需解决?各级领导干部一定要带着对人民群众的深厚感情,到群众中去,调查研究,解决问题,把中央改善民生的政策落到实处,把党的温暖送进千家万户。
第20篇:生产成本控制与现场改善培训后心得体会
生产成本控制与现场改善培训后心得体会
中山市顶固金属制品有限公司品质体系办公室周健清
邮箱:isozs@126.com
2010-7-12
2010年7月10日至11日,本人参加了中山聚成公司举办的、汪锦晖老师主讲的《生产成本控制与现场改善》培训。通过两天培训,本人有如下心得体会。
1.
2.
3.
4.
5.
6.
7.
8.
9.
10.
11.
12.
13.
14.
15.
16.
17.18.设备、的临界寿命到了,不能方便检测的,或者检测成本太高了,就要更换。
19.临界寿命靠实验室找出来,并标准化。预知性保养。
20.西医不懂得治病,中医才会治病。西医只知道杀菌,好细胞与坏细胞一起都杀了。而中医知道疏导。这个教育我们,不要过分迷恋西方的管理方式,我们中国的管理也有可取之处。要辨证的看待这个
企业发展靠企业利润增长的积累,利润的积累靠成本的控制,生产过程成本控制是成本控制的关键点,合理的生产现场改善及成本控制可以为企业带来更大的综合效益,通过培训,受益匪浅,在今后工作中依据培训中的生产成本关键点控制调整思路,杜绝人浮于事的工作方式,今后生产控制具体在以下几方面着手改进控制;
一.生产现场问题分析
生产现场的问题主要为公司体制和人本身两个方面的问题:固定成本不会变。只能靠大量生产摊分。量越大,摊分的固定成本就越低。 只有管不好而倒闭的工厂,没有因技术不好而倒闭的工厂。 管理者只懂核心的二三分就可以了。 管理者懂得比较宽,而技术者懂得要深,但管就不好。 没有夕阳的产业,只有夕阳的管理。 有效劳动定义,原材料改变性质才能赚钱。人、设备、原材料加工中,发生物理、化学变化,生产出的合格产品的过程才是有效劳动。 无效劳动能剔就剔除,不能剔除就尽量缩小或缩短。 凡是计件的工厂,都是不会管理的工厂,计件是危险的管理模式。计件旧不负管理责任的表现。计件造成工人专挑好活便活来干,难干不好干的活没有人喜欢干。 品质最怕的是: 一是微量不良,二是耐用寿命的缩短。 系统需要管理力和执行力。 推行5S最重要的是要进行红牌作战。 以时间作为一种标准。 5S是正宗的,6S或者7S,NS都只是一种强调。日本的5S中包含了习惯、节约、安全。 中药房是最早用定置和看板管理的,但日本人却懂得变成一种系统并向全世界推广。 中国人是有条件的服从。一定要让员工参与,并且要他们认可,才能将事情做好。 必须的无效不能剔除,如果剔除了这个无效会导致更多的无效。例如定置工具用完以后必须放回原处,否则产生更多的无效。
1.公司体制a.完善公司内部管理体系,明确各单位职责.
b.各单位对自己单位工作职责进行细分,制定各项职责的实施方案.
c.以顾客满意为导向,通过精心策划和认真执行满足客户的需求.2.人(管理干部/技术人员)
提升现场管理能力,主要要提高课长/组长/技术员/班长等各级干部思想意识,只有统一思想认识,对各问题点通过PDCA循环的持续改善与及强有力度的实施,自然能取得事半功倍的改善效果.“生产现场改善”要从“人的改造”开始!二.现场七大浪费1.制造过多的浪费
2.存货的浪费3.不合格品重修的浪费
4.动作的浪费5.加工的浪费6.等待的浪费7.搬运的浪费据产品特性及客户纳期,制定合理的物料纳入及生产出荷计划,减少原料及消耗品仕挂,及时安排出荷,降低半成品及完成品库存。仕挂为万恶之首,许多生产品质的问题因为仕挂高而隐藏于我们的企业中.
提升加强现场管理干部异常发现及处理能力,能及时发现排除生产过程的动作浪费、加工浪费、等待浪费、搬运浪费等.三.JIT精益生产\"现场管理的精髓就是责任到人,人人都管事,事事有人管,哪怕是工作現場一扇窗戶的玻璃,其衛生清潔也有指定的員工負責.\"
JIT精益生产是指在需要的时候、按需要的量、生产所需的产品,又被称为准时制生产、适时生产方式、看板生产方式.
JIT的核心是零库存和快速应对市场变化.
通过各种改善手法的应用挑战七零极限目标(零切换浪费、零库存、零浪费、零不良、零故障、零停滞、零事故等),生产时达到可控及可预期效果.做推行JIT精益生产前,先将最基本的5S做好.現場管理的原点是從5S開始!!四.现场改善IE七手法
1.防错法:如何避免做错事情,使工作第一次就做好.
2.动改法:改善人体动作的方式,减少疲劳,使工作更为舒适,更有效率.
3.流程法:研究探讨牵涉到几个不同工作站或地点之流动关系,发掘可改善之处.4.五五法:用质问的技巧来发掘出改善的构想.
5.人机法:研究操作人员与机器工作的过程,发拨出可改善之处.6.双手法:研究人体双手在工作时的过程,发掘出可改善之处.
7.抽查法:用抽样观察的方法有效的了解问题的真象.
五.一个流生产一个流生产方式是按产品类别布置的多制程生产方式,产品在生产过程中实现单位流动,它是准时化生产核心,是解决在制品的秘方,是清除浪费的最好方法.优点:1.生产时间短2.在制品存量少
3.占用生产面积少4.易暴露问题点
5.容易适应市场与计划的变更
6.有利于保证产品品质
7.有利于安全生产
8.不需要高性能的,大型化的设备要点:1.考虑产品的先进先出、快速流动、前后关连生产线尽量靠拢
2.一致的生产步调、在制品数量明确化、产线保持顺畅
3.信息来源一元化、目视管理充分应用、信息及时、物流方向一致
4.员工要多功能训练,能同时担当多个工程,同时减少工程瓶颈5.保障良好的工作环境,完善必要的检查作业标准
6.保证工作环境的安全性,同时能有效控制品质
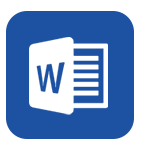