推荐第1篇:品质部品质异常检讨报告
品质部品质异常检讨报告
事件问题描述如下:
在6-1至6-3号生产的T8椭圆1/2平钩26*29.5和T8 1/2斜钩V字型直径26的产品,现这两款产品在生产至出货过程中混料包装出货到客户那里,导致影响客户的出货交期,有损客户对我司的印象,并造成公司物力资源的重大损失。
产品工序责任人如下:
开机技术员:蔡灿军、赖虔洲
品质IPQC:廖仲坤、赖惠兰
点数贴标签:廖凤凤、罗贞凤、吕明
裁管:廖国林
出货检验:易浩
品质部经查证对此事做原因分析如下:
1、商务部的制令单上的图纸没更新只是文字描述。
2、针对产品规格和形状差不多的产品,且在同一台机器上生产,生产一款产品订单时更换模具生产下一款时,技术员未跟品质或点数工序沟通说下。
3、产品点数贴标签的时候标签贴错了,但当班的IPQC盖章时没检查到位发现问题。
4、裁管工序裁切时也没核对制令单来做,裁管员在裁管时没主动把首件拿给OQC检验确认。
5、生产出来的产品没有明确区分标识并分开放置,导致裁切、包装容易出错。
6、出货检查时OQC检验没及时发现问题杜绝流入客户那里。
7、新来员工及临时工未做相关岗前作业培训,容易放错误。
永久改善纠正措施如下:
1、通知此事件相关负责人,然后召开品质异常检讨会。
2、商务部发出的制令单产品资料要及时更新。
3、新来员工及临时工应做相关的产品品质与作业规模培训再上岗。
4、品质部加强对品质检验员的培训与督导,特别是出货检查要把关到位。
5、生产车间5S要做好,如产品要准确标识区分,对于类似的产品要做明显标识并分开放置。
6、各部门的岗位职责说明书的制定落实。让工作流程化,制度化。这样大家工作更顺心。
7、各部门的管理制度撰写制定出来,并落实执行到位。
8、成立ISO内部审核小姐,对各部门的工作流程、5S、管理制度、作业规范、检验规范等相关事项进行不定期地审核与督导。
对于这件事,作为品质主管的我,在对品质检验员的培训与监督工作没做到位,虽有做品质程序文件及相关表单记录,品质部也有按程序来做事,但没监督品质检验员落实执行到位。现出此品质异常造成了公司的重大损失及有损客户对我司的印象。我愿接受公司对我工作失职处罚及考核!
品质部:
推荐第2篇:品质异常奖惩制度
品质异常奖惩制度
品质奖惩制度
1.目的
加强员工的质量意识,减少生产品质异常,提高产品的质量和成品率。
2.范围
本办法覆盖公司内部铝轮生产全过程。
3.职责和定义
3.1品保部负责铝轮品质异常的发现和处置,以及奖惩的实施。
3.2相关部门负责监督本部门品质异常的日常管理。
3.3企管部负责对品质异常的复核。
3.4定义
3.4.1单班(个人)同一原因报废的数量在5件(含)以上的称为小批量报废,20件(含)以上的称为中批量报废,超过50件的称为大批量报废。
3.4.2单班(个人)同一原因不合格的数量在5件(含)以上的称为小批量不合格,20件(含)以上的称为中批量不合格,超过50件的称为大批量不合格。
3.4.3本制度所描述的品质异常指在日常生产活动中,依照公司的技术规范、工艺文件、作业标准或其他管理制度规范操作所可以避免的非预期质量不良,且该不良判定责任为操作者;或其他可经由目视或检验器具自检发现而未发觉的质量不良。
4.共有异常
4.1责任钢号
4.1.1未打订单、指令单、技术文件所要求的铸造钢号、热处理钢号、X光钢号、机加钢号等追溯钢号且流入下一工序按10元/件罚款。未按有效技术文件打或打错位置的按5元/件扣罚(含打印不整齐、不清晰的),试作时无法打的,书面联络技术部处理。
4.1.2未打订单、指令单、技术文件所要求的偏距、pCD代码、内部编号、客户特殊要求的钢号等钢号且流到下一工序按20元/件扣罚,未按有效技术文件打或打错位置,打印不清楚的且流入下一工序的同样按20元/件扣罚,试作时无法打的,书面联络技术部处理。
4.1.3未按4.1.1或4.1.2要求打号码,又无法分清责任人时,扣车间时50元/件处罚。
4.2当发现品质异常检验员要求停机改善而未停机改善,对检验员置之不理,拒签或未进行改善措施,继续生产造成不合格的,按该类不合格在本制度相关条款所表述的两倍扣罚责任者,按三倍扣罚班长。
4.3.1不按送检频率送检或首、中、末件检验轮子未做标识或不合格品未进行追溯的按每次处罚30元,责任领班连带处罚20元;导致批量不合格或批量报废的,另按本制度相关条款所表述的两倍扣罚责任者,领班连带50%。
4.3.2没按规定做好首,中,末件检查及检查记录的,按50元/次处罚,领班连带30元/次,主管连带20元/次。
4.4各站下转的轮子,未经品保签字接收的按每栈板10元扣罚。
4.5各站可直接判定不良未挑出而下送的,可依逐站方式归属不良及扣罚。
4.6工作过程人为碰伤、摔伤、去毛剌打伤,可以挽救的且自动挽救好的不扣款,导致报废的按10元/件处罚责任者,无法区分时按50元/件扣罚班组,转运过程导致报废的按20元/件处罚责任者。
4.7品质异常经过品保抽检或全检未被发现并流入下道工序的,责任分配按以下规定处理:
4.7.1未形成批量的,罚款由操作手自行承担;
4.7.2形成批量,且该异常在首中末件检查时已经存在但未被发现
4.7.2.1形成小批量的,品保检验员连带罚款总额的40%,操作手按规定扣款;
4.7.2.2形成中批量的,品保检验员连带罚款总额的50%,操作手按规定扣款;
4.7.2.3形成大批量的,品保检验员连带罚款总额的60%,操作手按规定扣款。
4.7.2.4形成批量,但该异常在首中末件检查时不存在的,免除检验员责任,由操作手全额承担罚款。
4.8.该工序如果系品保部全检的,检验员连带罚款总额的80%,操作手按规定扣款。
4.9品质异常被操作者自己在生产过程中发现并及时报告车间和品保部,免除30%责任。
4.10品保部误将合格品判为废品处理的,按20元/件进行处罚。
4.11不良品未放置规定区域或者与良品混放,或未作注明状态标识、原因标识,经发现每次扣责任者30元/次,班长连带扣10元/次。
4.12新进人员试用期内, 该站或该班干部应善尽教导督察责任 ,若因此作业上产生之异常或不良属人为疏失可避免的,该员该站或该班之直属相关干部,依情节轻重每次扣款10-30元。
4.13 日常生产时,各生产车间、各生产工序发生的本制度未有特殊表述的废品,每件扣款为该产品的计件工资的1.5倍。
5.特有异常:指各车间部门特有的异常,发生该异常进行处置时,按本款处理。
5.1铸造车间
铸造车间的特有品质异常指:铸件脱模变形(后距偏大或偏小)、裂纹、刻字字迹不清或残缺,顶杆印过高或过深、粘铝、拉伤、欠铸、偏距模块用错、备模员边模装错,装饰面粗糙,窗口缺肉、冒口切深等铸造缺陷。
5.1.1车轮任何部位有肉眼可见的明显的裂纹且流入下一工序,扣责任者30元/件。
5.1.2备模班装错模造成报废每次罚款50~100元;铸造领班罚款20元;形成批量的按5元/件处罚备模班,按2元/件处罚检验员,按2元/件处罚领班。
5.1.3备模班在备模时未确认或未核对好模具刻字及气门孔位置等造成产品与图纸不符的,按30元/次处罚备模员,导致返修的除承担返修费用外按1元/件处罚,导致报废的按5元/件处罚备模员。
5.1.4 切冒口工序造成品质异常时可返修按2元/件处罚,造成报废的按10元/件处罚。
5.1.5在铸造发现不按规定放置过滤网的,按10元/件扣罚操作手,领班连带扣罚5元
5.1.6 因未放过滤网或过滤网放置不当,导致铝轮因外观渣孔原因报废,尽管此现象在铸造毛坯上未能发现,在后续加工过程中发现的,按10元/件处罚。
5.1.7 铸造操作手未做好自主品管,在品保签收流转单时发现不合格异常时,本岗位可发现而未发现并未及时处理的,可以返修的除承担返修工资外按1元/件处罚,导致报废的按5元/件处罚。
5.1.8其他异常在本岗位发现并及时进行处理的,不予处罚;流入下道工序,可以返修的除承担返修工资外按1元/件处罚;导致报废的,按5元/件处罚。
5.1.9X光检验完成轮子,送检人员没有及时拉回车间的,按5元/件处罚送检人员。
5.1.10冒充品保检验人员在流转单上签名的,按100元/次处罚责任人,领班连带扣罚50元/次,主管连带扣罚30元/次。
5.2热处理车间
热处理车间的特有品质异常指:如机械性能未在标准范围之内,轮网椭圆度超差,A面平面度超差,轴向变形,抛丸抛变形,装卸过程碰伤,毛剌未打好,去毛剌碰伤装饰面,大力钻钻中心孔钻偏、钻大或用错钻头。毛坯运往毛坯存放区时混放。以上不良流入下一工序,且该不良属于热处理工序可以发现、可以校正的。
5.2.1预钻孔工序导致品质异常的,可以返修的按2元/件进行处罚,导致报废的按10元/件进行处罚;预钻孔未钻或没钻好的流到下工序按3元/件处罚。
5.2.2 毛剌未打好,椭圆度、平面度未整好,下一工序反馈后按2元/件处罚。
5.2.3 不同型号、不同规格、不同的材面混放,经机加发现后作业员每件按3元扣款,主管领班各按1元/件罚款。混放未挑出,造成撞车责任归机加。
5.2.4因操作未符合作业规范或要求整形不到位致使产品报废的,按5元/件处罚。
5.2.5擅自设定更改温度经品保人员发现,扣责任者100元/次,(无法查出责任者则扣当班所有员工),主管处罚50元/次,造成报废的按20元/件处罚。
5.2.6未实事求是或按规定频率记录温度情况的,每次处罚30元。。
5.2.7电镀半成品包装时轮子箱外标注与箱内轮子实物不符时,按20元/件扣罚责任人。
5.2.8对一些有明显缺陷的车轮不加控制,以致发往电镀厂或在抽检时发现报废每只扣责任者20元;工号钢号不清没挑出的连带20元/件处罚。
.5.2.9对于发往电镀厂的半成品,铆钉孔少钻的、气门孔未钻、磕碰伤等不良可发现而没发现的按10元/件扣罚责任人。
5.2.10其他异常在本岗位发现并及时进行处理的,不予处罚;流入下道工序,可以返修的除承担返修工资外按1元/件处罚;导致报废的,按10元/件处罚。
5.3机加车间
机加车间的特有品质异常指:(1)批量尺寸超差、CAp实配不良、pCD位置与图不符(含位置度超差)、pCD钻头用错、端径跳不良、批量动平衡不良(2)风嘴位置钻错、钻偏,铆钉孔钻偏或钻大或漏钻,拱丝孔偏倾斜或乱牙(3)夹偏,刀纹粗,磕碰划伤、批量振刀、批量接刀,车废不良。且上述品质异常责任者可以发现和判断。
5.3.1机加工风嘴工序和pCD沉孔加工/铆钉孔/CAp螺丝孔/装饰孔等工序未按作业规定造成品质异常的,按5元/件处罚,导致报废的按20元/件处罚。单独的风嘴加工工序、装饰孔工序和pCD沉孔加工工序不允许有调机废品。
5.3.2毛剌未刮好下转至下工序,按1元/件罚款,且要求立刻返修或另外承担返修费用。
5.3.3 除4.3.1所述之外的其他工序每班只允许有一只调机废品,超过该数量报废的按20元/件处罚。
5.3.4如果因为没有调机品需增用合格品调机的必须得到领班以上主管领导的许可。铸造按5件/规格提供给机加工,没提供时书面反馈扣铸造20元/件处罚。
5.3.5形成批量,且该异常在首中末件检查时已经存在但未被发现
5.3.5.1形成小批量的,品保检验员连带罚款总额的40%,机加站质检员连带罚款总额的50%,机加站调机员连带罚款总额的50%,操作手按规定扣款;
5.3.5.2形成中批量的,品保检验员连带罚款总额的50%,机加站质检员连带罚款总额的60%,机加站调机员连带罚款总额的60%,操作手按规定扣款;
5.3.5.3形成大批量的,品保检验员连带罚款总额的60%,机加站质检员连带罚款总额的70%,机加站调机员连带罚款总额的70%,操作手按规定扣款。
5.3.6试漏员漏检或由于工作不细心,错检,每件罚款200元,超过3件公司给予开除,必要时追究刑事责任,所有劳动报酬全部扣除。
5.3.7品保部机加检查站未对机加过程中发现的有铸造缺陷但可通过氩弧焊补救的轮子进行适当处置的,按误判为废品处理,按10元/件进行处罚。
5.3.8涂装回机加返修之轮圈 , 若返修量超过1.2 m/m 时, 有可能造成轮圈强度不足, 亦即J部(耳部)13 m/m返修后变成11.8m/m以下;J部(耳部)12m/m 返修后变成10.8m/m以下时,加工单位须主动提出测试要求,若未能提出致返修后强度不足属加工单位责任时,加工调试前五件不扣款,后调试品应扣3元/件。
5.3.9 发生其他机加品质异常时,可以返修的按5元/件进行处罚,导致报废的按10元/件进行处罚。
5.3.10动平衡不良责任由机加、热处理、铸造三个部门均摊;发现批量不良仍在生产的,按20元/件处罚。
5.3.11毛坯有异常无法修补应挑出报废,如流入下站扣责任者按5元/件扣罚。
5.3.12有修改方案加工的试验轮,没打修改方案号的,按20元/件处罚。
5.4涂装车间
涂装车间的特有品质异常指:批量桔皮,起皱,色差,颗粒,砂印,磨痕,磨变形,尘点,漆膜性能异常(厚度、附着力、硬度、盐雾试验)碰伤,摔变形。
5.4.1对新来的油漆应采取小批量试做,未采取小批量(此处特指20-30件)试做而产生的批量品质异常(此处特指≥30件)每次按50元处罚责任人。
5.4.2形成中批量的砂印、磨痕、磨变形,不影响最终品质时,按0.1元/件扣款;因砂印、磨痕、磨变形等操作原因构成报废的按10元/件处罚。
5.4.3漆膜附着力、厚度、硬度、每天车轮的首件、中件及末件应及时检验,否则产生品质异常每件按1元/件处罚(透明粉除外)。
5.4.4对一些有明显缺陷的车轮不加控制,以致发往客户或在终检检出报废每只扣责任者或涂装车间20元。
5.4.5对于一些该用补土修补的车轮,没有修补导致于终检检出每只扣款10元;虽然修补,但没有打磨,以致外观不良,终检检验后每只扣款20元。
5.5包装班(含电镀包装):
5.5.1混装≤5件,每只车轮罚款20元,;形成小批量的每只车轮罚款20元,并通报批评,且开除直接责任者;标签、配件用错的,作业时碰伤报废的按20元/只扣罚。
5.5.2 胶带未粘好,纸箱包装不整齐,每发现一箱扣款2元,标签粘贴不整齐,每发现一箱扣款5元。
5.5.3 配件短缺或装饰钉未打的每箱扣罚20元,装饰钉未打到位的,每颗扣罚5元。
5.5.4包装过程中因没采取保护措施造成轮子脏污等不良时按10元/件扣罚
5.5.5 电镀厂回厂轮子有可发现而没发现的明显不良,回厂后被发现的按10元/件扣罚外检责任者,
5.5.6包装检验员可发现而没发现的明显不良下送被发现10元/件扣罚责任者。
5.5.7包装人员未按规定盖责任印章或盖不清楚的,按20元/件扣罚。
5.5.8 电镀厂回厂轮子箱外标注与箱内轮子实物不符时,按20元/件扣罚电镀厂。
5.5.9未攻丝或未攻好丝,造成无法正常安装螺丝,经返攻丝后合格的按5元/件处罚电镀厂,若无法安装螺丝造成报废的,除轮子退回电镀厂外再按20元/件处罚电镀厂。
5.5.10电镀厂回厂轮子有明显不良,回厂后被发现的,除轮子退回电镀厂外,按10元/件扣罚电镀厂。
5.5.11电镀厂回厂的[入库许可证]的订单号或内部编号与订单不符时,按10元/次扣罚外检人员
5.5.12其他异常在本岗位发现并及时进行处理的,不予处罚;流入下道工序,可以返修的除承担返修工资外按1元/件处罚;导致报废的,按10元/件处罚。
5.6仓库
仓库特有品质异常指:仓管员发料、发货发错,或数量发错;仓库没有按入库出库规定程序去做,仓库物品标识不规范不清晰,不同规格不同客户产品混放;搬运工摔伤碰伤车轮。
5.6.1仓管员发料发错,导致影响品质、影响生产,根据情节轻重处罚款50~100元。
5.6.2成品仓库多发或少发,多发按实际成本金额赔偿;少发4件以下处罚30~60元;4件以上处罚50~120元。
5.6.4仓库物品标识不规范不清晰,每发现一次罚款10~30元。
5.6.5不同规格不同客户产品(样品除外)混放,不论是入库时还是发货时,对责任人按5元/件处罚。
5.6.6装卸工在搬运装卸成品时,没按规定作业造成纸箱损坏,或在库成品未加以防护造成纸箱脏等不良时,按10元/件扣罚,轮子报废时按20元/件扣罚。
5.6.7其他异常在本岗位发现并及时进行处理的,不予处罚;可以返修的除承担返修工资外按1元/件处罚;导致报废的,按20元/件处罚。
5.7销售部与顾客沟通不及时影响品质每次处罚50~100元。
6.过程控制奖励制度:
6.1在过程控制中下工序发现上工序不良品并主动挑出,对责任人或责任部门按本制度所列条款处罚,处罚金额的40%奖励给发现者;所挑选出的不良无法找到责任者的,由责任部门承担责任;所挑选出的不良不属于本制度所述之品质异常,按3元/件奖励发现者。
6.2对于磕碰划伤实行逐站管理,即下一工序发现不良品扣罚上一工序。
7.关于顾客品质抱怨及退货处罚:
7.1对于顾客退货对主要责任部门每次/批按200元处罚,相关部门每次/批按连带100元处罚。
7.2客户抱怨时,品保部与责任单位于二天内建立8D小组,,否则延误按20元/天处罚。
7.3对于顾客退货处罚金额最高不超过1500元。
8其他
8.1对员工的处罚当月最高限额以保留生活费为标准(操作工300元、检验员450元、领班以上600元),超出部分下月再扣。
8.2在未来公司对操作者实行成品率考核后,经本制度处理的废品可在操作者指标考核中予以剔除,但因此产生的成品率考核奖励不予计算。
9.本制度未能描述的异常情况,由企管部会同相关部门参考类似条款处理;涉及生产部、技术部等部门原因造成的批量品质异常按成本异常奖惩制度处理。
10.本制度解释权归品保部。
推荐第3篇:品质异常大会演讲稿
各位同事,各位工友: 大家早上好!
针对于广州宗麟客户理赔的重大品质异常,直接赔款70250元,间接的返工成本及人工工时,包括取消订单而造
成的库存成本及品质异常至今未交货的27300M库存仍需要返修的半成品及成品公司本次的 损失在二十多万元左右,经济上受损只是损失的一部分,声誉、信誉的损失后果是及其严重的,因为此事我们随时都会面临丢掉自己的客户,丢掉了客户就意味着丢掉了我们手里的饭碗,可想而知产品的品质关系着一家企业的生死存亡。
一,质量是企业的生命,是公司赖以生存和发展的前提与保证,是全体同仁稳定发展的前提,是关系公司存亡
的大事;众所周知,日本在二次世界大战后,从一个战败国到成为世界第二大经济强国,实质上来自于品质的振兴,从地摊货上升至高品质、高价位的精品;而丰田“汽车门”事件反映出全员精细化理念落实的细微化的差异会给公司带来致命的打击;公司小的时候,质量是与其它大公司竞争的一个重要筹码;公司发展到一定规模的时候,质量更是支撑公司稳步健康发展的前提,丰田“汽车门”事件就是最好的案例!市场占有率越大,质量问题的负面影响也越大,有时甚至是颠覆性的毁灭,三鹿奶粉事件是强有力的说明!公司以高标准严要求定位品质,将质量提升至公司所有发展战略的最前
端,是告诉公司所有同仁,必须将质量与科源的生存相连,我们的价值才能体现!才能有我们共同的明天!第二点:质量文化是企业文化的基础,全员质量意识和思想是指导开展各类质量工作的前提,是决定质量工作的
行为与习惯及成果;质量不仅仅指产品质量,它还包括工作质量、服务质量!除了直接生产人员外,其它辅助部门人员的工作质量会影响产品质量,而服务质量包含直接面对外部的客户和公司内部人员上下工序间的服务!所以,有的同事单纯的讲产品质量其实是不明白质量本身的含义:质量是在我们身边、我们身上,我们工作与生活中无所不在的一种特质!当我们认识质量,重视质量,认真对待质量的时候,在我们工作、生活的所有活动中就形成了一种质量文化,而质量文化是企业文化的基础:1.质量状况是衡量企业是否尽到社会责任的最重要的标准,是企业价值观问题;2.质量文化是企业诚信的根基,是企业人品格问题; 3.质量文化是人本文化的体现,是企业人精神问题;4.质量文化是全体员工素质的体现,是人员素质问题;质量文化与企业的宗旨、品格、精神、管理、素质提升密不可分,所以,我们必须在质量文化的基础上建设我们的企业文化,提升我们的企业文化!我们的公司才能基业长青,百年长存!
第三点:员工职业化程度决定质量文化上升至品牌文化的高度企业走上百年长存的发展之路,必定经由质量文化
提升到品牌文化之路,而员工职业化程度在某种程度上决定质量文化提升到品牌文化的高度!职业化就是专职化或专业化,职业化包含四个方面:
1.职业化的工作技能:就是像个做事的样子;职业化的技能,俗称“专业”,就是做什么首先要会什么;如果把职业化比作盖房子的话,专业就如同房子的地基,地基不扎实的房子就像空中楼阁,摇摇欲坠;
2.职业化的工作形象:就是看起来像那一行的人;是职业化的外在体现,是“房子”的外饰面,也就是俗话说什么就要像个做什么的样子”,它包含着装,谈吐,行为举止;
3.职业化的工作态度:就是用心把事情做好;是职业化的内在表现,是“房子”的内装潢,体现了主人在精神层面的品味;
4.职业化的工作道德:就是对一个品牌信誉的坚持;是职业化的核心内涵,是“房子”的支柱。
人们每天都在做两件事情,喜欢做的事和必须做的事;职业化的职业者必须快乐地去做自己不喜欢的事。
第四点:品质就是人品,品质的好与坏就是人的工作习惯和行为的好坏问题,是职业操守的问题。有的人认为,
我的工作不直接产出产品也不直接面对客户,那么细小的事情与细节的东西就无所谓了;有的员工认为,机器能动,能用,没有功能上的问题,外观和细节上的小问题就不必要斤斤计较;有以上两种思想的人没有真正理解“客户”和“质量”两种理念:“客户”的定义是与之相关连的工作链接和相关部门的链接的关系,直接与间接产生关系与服务的都是“客户”关系;最能反映“质量”的核心是细小和细微的事情。细微和细小环节才能彰显技术和能力的实力。这就是“细节决定成败”的核心所在。
广州本田雅阁汽车第一批汽车生产出来,开始试车,结果才跑190迈,汽车车身就开始颤动。日本总部接到电报
后派一名专家及5全部指标达到要求。后来经过深入调查了解发现,汽车组装过程所有的装配动作都有严格的要求,包括拧螺丝,拧多少
圈才合格都有规定;而中方的装配员工认为螺丝只要拧紧了就行了,拧多少圈的标准根本不重视,也正是这样的工作态度,产出的结果却是天壤之别。工作中的细节看上去不引人注意,却恰恰是一个人工作态度的最好证明。那些优秀的、成就非凡的人,总是于细微之处用心,在细微之处着力。正是因为他们认真对待工作的每一个细节,将工作做到尽善尽美,才使他们获得了成长和发展的机会。上面四个主题表面上互不相干,实质上却是层层剥开的。从所有出现过的质量问题分析原因,部分原因与工作技能相关连,部分原因是工作态度导致的结果,所有的质量问题都与每一个岗位,每一项工作相关联。最根本的原因是我们职业化素质高度不够。
各位同事各位工友,广州宗麟客户理赔的重大品质异常就如一面警钟,血的教训时时提醒我们耳边警钟长鸣,类似的问题不能再次发生,从我做起从身边的 小事做起,让我们携手同行,在科源这条战船上,用品质作浆,大家齐心协力,划向辉煌的明天!
谢谢大家!
推荐第4篇:供应商品质异常管理协议
供应商品质异常管理协议
一、目的
对供应商提供的材料品质进行管控,确保采购产品持续满足客户需求。
二、适用范围
本办法适用于供应商提供我公司(工厂、安装现场)材料配件品质异常的控制。
三、职责
1、质量管理部负责来料品质抽检, 品质异常处理以及供应商整改验证,并负责配合采购部实施对供应商选择和评价。
2、采购部负责供应商选择、评价、考核管理,按季/年度组织供应商业绩评鉴,督促供应商品质整改。
3、工程项目部负责直送工地材料的验收抽检,并及时反馈材料不良信息。
4、仓库负责入库材料的验收、库存管理和不良品标识等
5、生产部负责制程在线材料不良信息的反馈、退库办理,配合不良品的处理。
四、管理要求
(一)材料品质异常之发现和处理
1、工厂来料检验,经质量管理部IQC依据图纸、材料国家(行业)标准以及《来料检验作业指导书》抽检判定为品质不良时,由IQC作出处理意见,经部门经理批准执行。处理方式:拒收、退货、筛选、返工、特采。
2、生产部在加工中发现来料品质不良时,反馈质量管理部查实并提出处理意见,经生产经理确认后执行。在线材料不良处理方式:退换货、筛选、返工、特采。
3、产品来料在验货或安装过程发现不良时,应及时报告品质T/C查实,由品质T/C反馈采购部、质量管理部、工程部,采购部通知供应商到现场处理,工程部跟踪处理结果,品质T/C记录不良信息,跟踪整改情况。产品来料不良处理方式:退换货、筛选、返工、特采。
(二)供应商品质不良的处置和索赔
1、当发生供应材料品质不良时,IQC应将不良材料标识隔离,在线不良时,还应通知仓库冻结、标识和隔离不良材料。
2、质量管理部应立即反馈采购部,重大批量不良时,采购部必须通知供应商两个工作日内到公司确认解决。
3、供应商对品质异常的处理时限:收到投诉两个工作日必须书面回复解决方案。
3、供应商材料不良的索赔和处罚
① 批量不良材料让步使用(特采)时,涉及功性能不良材料的特采批,扣除当批货款的10%;外观不良的特采批,扣除当批货款的5%。
② 生产、安装在线材料批量不良:需我公司生产或安装人员100%筛选或返工,所发生费用由供应商承担,人工费按20元/小时计。
③来料经多工序加工后发现批量品质不良,所造成的加工、材料等损失,由供应商承担。
④ 供应商来料品质不良造成工程投诉、索赔及客户端投诉、索赔等严重后果,相关损失由供应商承担。
⑤ 供应商不守诚信,不按我公司的质量整改要求进行改善,连续三批次重复提交同类品质不良产品,零产品处以1000-5000元罚款,批量性不良处以10000-50000元罚款。
4、质量索赔的执行:由质量管理部填写[品质不良索赔通知单],附上[投诉/退货通知单]、损失计核单据等,交采购部送达供应商确认签章。
5、供应商将签章后的索赔单扫描或快递至采购部,由采购部发放到质量管理部和财务部执行扣款。
(三)供应商的质量考评(占业绩考评的40%权重)
1、质量管理部IQC负责来料品质不良数据、工程反馈材料不良等统计和定期汇总(月/季/年) ,以作为供应商考评的依据。
2、采购部负责按《供应商管理办法》定期组织对供应商进行进行考评,质量管理部负责其中供货质量方面考评,扣分标准如下:
① 供应商当月品质批次合格率低于95%,按每低于1%扣2分;
② 生产部、项目部制程在线批量性轻微不良,每发生一次扣2分(批次合格率高于98%除外);制程重大批量不良(停工、返工等)每发生一次扣5分;
③ 客户抱怨、投诉每件/次10分;
④ 不按规定时间回复投诉扣2分,不按期完成质量整改、重复提交不合格材料每次扣5分;
⑤ 供应商不按要求及时提供材料质保资料,工程部投诉一次扣2分。
3、供应商业绩考评中,服务、交期、成本项按 《供应商管理办法》考评。
(四)考评分级及动态管理
1、根据质量考评得分,按以下标准划分供应商质量等级,确定相应的管理方式:
、采购部根据每季度供应商考评结果对供应商进行分级管理,成本部对采购的订单分配应进行监督。
3、连续两季度为C级的供应商,采购部应停止新下单,列入淘汰名单,重新选择新的 供应商。
4、评定为D级质量供货单位如为公司唯一的供应商时,采购部应报公司领导批准暂时 供货,同时采购部必须在一个月内寻找到替代供应商。
5、被淘汰的供应商通过质量整改达到要求,经采购、质量等部门重新调查评估后,才 可进入我公司合格供应商名录
五、附录: [品质不良索赔通知单]
六、本办法经批准后发布实施 附录
供应商总经理签字:
新星总经理签字:
推荐第5篇:品质异常处理流程(推荐)
炳燊精密模具实业有限公司
品质异常处理流程
(公开文件,共4页)
一、目的:
规范品质异常处理流程,提高品质异常处理的时效性,确保来料质量及生产的正常运转,同时满足顾客的质量要求。
二、范围:
适用于本公司来料、制程、出货品质异常的处理。
三、定义: 3.1 来料品质异常:
a、不符合相关检验标准要求,且不良率超过质量目标时; b、合格物料制程中发现重点物料不合格时;
c、有经过改善且有效果确认,但又重复发生品质异常时。 3.2 制程品质异常:
a、使用不合格的原料或材料; b、同一缺陷连续发生;
c、不遵守作业标准或不遵守工艺要求; d、机械发生故障或精度磨损; e、其他情形影响到产品质量时。 3.3 出货品质异常:
a、客户投诉或抱怨;
四、职责 4.1 来料品质异常:
品质:a.负责填写《品质异常联络单》“异常描述”部分;
b.负责将《来料检验报告》、《品质异常联络单》发送于采购,抄送工程、生产; c负责品质异常改善结果确认。 采购:负责将《来料检验报告》、《品质异常联络单》发送给供应商并及时与供应商联系跟踪供应商及时回复“原因分析”“纠正与预防措施”并将结果回复品质部.4.2 制程品质异常: 品质部: a,负责品质异常之最终判定; b,负责确认品质异常责任部门;
c,负责主导品质异常案例的处理过程;
d,负责对责任单位的改善结果进行追踪确认
1 / 4 炳燊精密模具实业有限公司
异常责任单位:
a负责品质异常的原因分析,提出临时措施及长期改善对策并执行。 生产部:
a负责品质异常的改善和预防措施的实施及验证改善措施的有效性; 其它相关单位:
a在需要时进行异常改善的配合 4.3 出货品质异常: 品质部:
a负责将品质异常通知各部门及确定责任部门; b负责异常改善后的跟踪确认; c负责处理客户抱怨 异常责任单位:
a负责品质异常的原因分析,提出临时措施及长期改善对策并执行。 生产部:
a负责品质异常的改善和预防措施的实施及验证改善措施的有效性; 营业部:
a负责将客户抱怨反馈给相关部门。 其它相关单位:
a在需要时进行异常改善的配合
五、工作程序: 5.1 进料品质异常: 5.1.1
依相关检验标准判定不合格,针对不合格物料标示“不合格”,并立即移至不良品区域。 5.1.2 异常成立4小时内开立《品质异常联络单》通知采购。 5.1.3 采购接《品质异常联络单》后4小时内转责任供应商。 5.1.4 供应商需于1个工作日内针对异常物料提出临时对策,如对异常内容有疑问,需在4小时与品质相关人员确认清楚。 5.1.5 供应商必须在《品质异常联络单》要求的期限前(如无明确要求,默认为《品质异常联络单》发出后2个工作日内)回复完整的改善方案。 5.1.6
品质部对供应商回复内容进行确认,针对改善措施不合格部分予以退件,要求供应商重新回复。改善措施合格,则报告予以归档,跟踪后续进料品质状况,依5.1.7执行。 5.1.7
针对供应商改善后产品加严检验,连续追踪3批无异常予以结案,转正常检验;连续追踪3批中途发现不良现象仍存在,则重复5.1.2-5.1.7。 5.1.8 如供应商改善措施回复后连续2个月无进料,则强制结案,后续进料依正常检验执行。 5.1.9
2 / 4 炳燊精密模具实业有限公司
如同一质量问题连续发起两次品质异常,验证结果无明显改善,则需采购部组织召开供应商评审,决定是否需要取消供应商资格。 5.2
制程品质异常: 5.2.1 发现制程产品不良,应立刻停止加工。 5.2.2 如异常属现场作业人发现,需立即找品质部确认不良现象可否接收。如异常可接受则继续生产,不可接收依5.2.3执行。 5.2.3
依相关检验标准进行判定,确认不良成立时,应开具《检测不良记录表》。 5.2.4 将不合格内容标识在工件上,立即移至不良品区域。 5.2.4.1 不良品如以进行返工、返修达到合格要求,则由品质部发出《不良返修报告书》,生产对不良品进行返工、返修,返工返修后需交付品质进行检验,合格品进行出货区,品质回收报告书,统计返修用时,交返修者签名。 5.2.4.2 判定重做时,生产1小时内填写补料单,交工程确认后,同《异常分析报告》一起交采购,采购1小时内下加急采购单,生产跟进材料,所有工序加急处理(如内部制程超出负荷,可申请外协)。如影响出货交期,营业客户客户交期。 5.2.5 当异常问题严重,品质部又不能明确判定时,则由品质、工程、生产、营业共同会签,品质部开立《品质异常联络单》,责任部门分析原因、改善措施后,发送至营业部,最终由营业转发给客户,营业部负责跟踪客户回复处理结果,并将客户处理结果发给各部门。 5.2.6
生产部按客户处理意见返工或重做(必须要有补料单),营业部1小时内回复客户最终送货时间。当处理意见为让步接收时,品质部将工件转入出货区,并附上《品质异常联络单》和客户回复的处理意见,出货时此工件不贴合格标签。 5.2.7 制程品质异常开立时机。 5.2.7.1 制程异常属材料所致,需第一时间通知责任单位、品质前往确认,双方判定标准一致,确认异常成立,则开立《品质异常联络单》要求责任单位改善。 5.2.7.2 产品制造过程中如发现产品不良时,品质应开出《检测不良记录表》待工程、品质、制造担当分析出原因找出责任单位后由责任单位进行对策,品质部监控对策实施有效性 5.2.7.3 当产品制造不良时,品质应立即召集工程、品质等单位对问题点进行分析,找出原因和对策,等问题点解决后,方可再生产。相关不合格品的控制见《不合格处理流程》。 5.2.7.4 品质再现(品质异常重复发生)时,开立《检测不良记录表》,通知生产单位整改。 5.2.8 所有制程中《检测不良记录表》需生产部、工程部进行会签,生产、工程接到品质异常 3 / 4 炳燊精密模具实业有限公司
信息后半小时内需针对异常现象提出临时对策。 5.2.9 责任单位需于《品质异常联络单》或《检测不良记录表》要求期限前,针对异常现象提出长期改善方案。 5.2.10
品质部对责任单位回复内容进行确认,针对改善措施不合格部分予以退件,要求责任单位重新回复。改善措施合格,则报告予以归档,由品质跟踪后续进料品质状况,依5.2.11执行。 5.2.11 返工OK产品需重新送品质检验,重新检验合格转入出货区,检验不合格依《不合格处理流程》要求执行。 5.2.12 针对异常改善后产品,品质加严检验,连续追踪3批无异常后予以结案,转正常检验。 5.2.13 如异常发生后连续2个月无生产,则强制结案,后续生产依正常检验执行。 5.3 出货品质异常: 5.3.1
客户投诉或抱怨,由营业将投诉或抱怨内容0.5小时内发给品质部,抄送到生产、工程。 5.3.2 如客户退货返修,依5.2.4.1执行。 5.3.2.1
如客户判定重做时,依5.2.4.2执行。 5.3.3 品质部24小时内分析外流原因及预防措施,并回复给营业部,抄送到生产、工程。 5.3.4 营业部1小时内将品质回复内容确认,并回复给客户。 5.3.5 异常单回复后,由文员统一归档整理/追踪。 5.3.6 改善对策执行后,品质部依对策内容进行追踪确认,连续1个月内无同样异常外流再发,则予以结案。 5.3.7 追踪期内再发则重新开立《检测不良记录表》,依5.3.4-5.3.6执行。
4 / 4
推荐第6篇:模切品质异常整改措施
机器一部10月份品质异常整改措施
制程异常9单
问题点1——纸毛(金王彩盒、标签类;)
原因分析:
a部门对待此问题不够严谨、
b上机次数频繁且每一次生产数量不多、
c异型处“飞机孔、水滴孔”更换时压力过大、d纸张尺寸过小(大度三开)导致机器压力不均匀。
整改措施:
a针对机台进行单独沟通,明确该异常给公司带来的损失,让其严格执行品质要求并积极配合部门整改(长期有效控制)。
b按啤板室管理规定,各机台每一次下机的啤板认真填写生产批次与数量,异常啤板在下机后第一时间只会到当班主管。
c在生产中更换孔位、啤刀需重新调整压力,避免新刀压力过大而受损。 d制作啤板时(类似led彩盒),务必在版尾加装平衡刀。
问题点2——啤走位(歌尔x
12、x32系列)、喇叭口(杜蕾斯、oakley) 原因分析:
a各车间温、湿不一致,尤其是丝印后的产品 b坑纸裱后不平整、起翘,直接导致模切走位 c修改后的啤板有误差
整改措施:
a有带窗口坑盒产品,在制作啤板时窗口需留活动位,方便每一批次生产进行调整。 b挑选式生产,针对起翘严重的产品调手动机分批分机台生产。
c旧单生产时,各机台同样需要成型检查(啤板在使用过程中有存在碰撞现象),主管在签署首件认真把关。
让步放行15单
主要问题点(啤走位、喇叭口、击凸走位、爆角、爆针刀)
原因分析:
a手啤机台帮机经验不足,在续纸过程中有放不位现象, b自动啤有个别机长出现机器未完全调试好就开始生产,
c每一年刚进入冬季天气干燥纸张易变形,各工序未能及时防服好,导致纸张上面的一部份与中间位有明显的误差,导致产品版尾位击凸走位严重,
d爆角——纸张过于干燥、啤板角度制作不合理、撕卡时有撕烂、手工作业的手法需要培训, e“美真”花生小将彩盒爆针刀——针刀长度不够、针刀与压痕条重叠(导致压力过大),作业不够仔细,
整改措施:
a手啤机台增加培训、加强抽检。
b重点控制操作不规范机长,对首件前的200张产品重点跟进。
c未能连线生产的产品,各机台下机后务必包膜,给到手工部任一产品务必包膜(防止纸张水分流失)。
d收集爆角问题点,制定并更新制板文件。
e花生小将彩盒,啤板已经修改,部门对此事件进行通报。
欠数5单
主要问题点原因及整改措施: 啤走位(歌尔px4外彩盒)
原因分析:生产中因为纸张在裱纸后弯翘严重影响正常开机(纸弯翘导致电眼报警),当时机台关闭电眼生产,导致此单欠数720个。
整改措施:a要求生产各机台在生产除(胶片产品)外,务必打开所有电眼、b当纸张来料严重变形时需分批次分机台生产。
爆角(aqua star)
原因分析:生产周期过长导致水分流失、纸张过于干燥、啤板角度制作不合理
整改措施:给到手工部任一产品务必包膜(防止纸张水分流失)、收集爆角问题点,制定并更新制板文件。
爆针刀(美真花生小将)
原因分析:“美真”花生小将彩盒爆针刀——针刀长度不够、针刀与压痕条重叠(导致压力过大),作业不够仔细,
整改措施:开会进行宣导,主管签署首件时重点把关,通知到现场pqc人员一起监督。
客诉3单
恒联纸业——三边预折有点生硬,上机调试不流畅,客户现在用手工粘盒
原因分析:印刷时由三种品牌纸张生产,打钉位不够大导致上机后易断;
整改措施:粘盒时折三边生产,加大钉位至1.5mm啤板已修改。
歌尔包装外盒(03版)——产品表面脏污,破损
原因分析:具体原因不清楚
整改措施:
金王 8139542(配7.4*7.9cm斜杯——模切走位,爆角
原因分析:啤板与文件间存在有1.5mm的误差
整改措施:已反馈商务及设计,修改印刷文件,已经修改。
责任人: 杨坤 2014-11-16
推荐第7篇:品质异常管理办法DOC[推荐]
品质异常管理办法
一、目的:
规范品质异常处理流程,提高品质异常处理的时效性,确保产线正常生产,满足客户要求。
二、范围:
适用于产品品质异常解决的所有过程。
三、定义:
3.1品质异常之定义 3.1.1产品品质异常:
3.1.1.1不符合相关检验标准要求时。 3.1.1.2重复发生品质异常时。 3.1.1.3客户抱怨及退货时。
3.1.1.4其它情形,影响到产品品质时。
3.1.2作业品质异常:因非偶然因素(即可避免的原因),现况虽未发生产品不良,但存在品质隐患。包含: 3.1.2.1不遵守操作标准操作;
3.1.2.2虽然照操作标准操作,但因各种标准不完善,以致无法控制变异原因; 3.1.2.3使用不合格的原料或材料; 3.1.2.4机械发生故障或磨损; 3.1.2.5作业员疲劳(或情绪欠佳); 3.1.2.6其它情形,可能存在品质隐患时。
四、职责 4.1 质量部
4.1.1负责品质异常最终判定、标示。 4.1.2负责确认品质异常责任部门。 4.1.3负责主导品质异常案例的处理过程。
4.1.4负责对责任单位的改善结果进行追踪确认。 4.2发生异常责任部门:
负责提出临时措施及长期改善对策并执行,责任单位在无法分析出原因及对策时,由责任部门召集相关人员协助分析改善。
4.3生产部:负责对改善措施的实施及验证改善措施的有效性。4.4物流部:负责入库质量异常品的分类存放、退回及报废。 4.5 其它相关部门:在需要时进行异常改善的配合。
五、工作程序: 5.1进料品质异常:
5.1.1 IQC依相关检验标准判定不合格,针对不合格物料标示“不合格”,并通知仓库立即移至不良品区域。
5.1.2IQC异常判定后1小时内开立《品质异常联络单》通知采购/生产计划/SQE。 5.1.3 SQE接到《品质异常联络单》后1小时内向供应商反馈品质不良。 5.1.3采购接《品质异常联络单》后1小时内确认物料是否退回,必要进组织内部评审以确认物料是否可以让步放行。
5.1.4供应商需于8小时内针对异常物料提出临时对策,如对异常内容有疑问,需在12小时内与我司相关人员确认清楚,必要时到现场确认。
5.1.5供应商必须在《品质异常联络单》要求的期限前回复完整的改善方案。 5.1.6 SQE针对供应商回复内容进行确认,针对改善措施不合格部分予以退件,要求供应商重新回复。改善措施合格,则报告予以归档,由IQC跟踪后续进料品质状况,依5.1.7执行。
5.1.7 IQC针对供应商改善后产品加严检验,连续追踪3批无异常予以结案,转正常检验。
5.1.8如供应商改善措施回复后连续3个月无进料,则强制结案,后续进料依正常检验执行。 5.2 制程品质异常: 5.2.1 IPQC发现重大异常时立即停机/停线并通知主管处理. 5.2.2如异常属现场作业人发现,需立即找QC确认不良现象可否接收。如异常可接受则继续开机生产,不可接收依5.2.3执行。
5.2.3IPQC依相关检验标准进行判定,确认不良成立时,要求生产部调整并现场整改。
5.2.4针对已生产产品依生产批号往前追溯,直至良品。
5.2.5 IPQC针对已追溯到的不良品标示“不合格”,并要求生产部立即移至不良品区域。
5.2.6生产现场异常改善后,生产部提出首件检验需求,IPQC检查合格后方可重新开线生产,如检查不合格,则重新调整或系统改善。5.2.7制程《品质异常联络单》开立时机:
5.2.7.1制程异常属原材料所致,需第一时间通知SQE前往确认,双方判定标准一致确认异常成立,则开立《品质异常联络单》要求责任单位改善。 5.2.7.2产品制造过程中如发现产品不良率超过5%时,IPQC应开出品质异常处理单待生产、质量、工艺、技术等部门分析出原因找出责任单位后由责任单位进行对策,质量部监控对策实施有效性。
5.2.7.3当产品制造不良率超过10%时,IPQC应立即通知产线停线并召集生产、质量、工艺等单位对问题点进行分析,找出原因并对策,等问题点解决后,方可再开线生产。
5.2.7.4品质异常重复发生时,开立《品质异常联络单》,通知生产部停线整改。
5.2.8所有制程中《品质异常联络单》需会签组长/生产主管,组长/生产主管接到品质异常讯息2小时内,需针对异常现象提出临时对策。
5.2.9责任部门需于《品质异常联络单》要求期限前,针对异常现象提出长期改善方案。
5.2.10 QE针对责任单位回复内容进行确认,针对改善措施不合格部分予以退件,要求责任单位重新回复。改善措施合格,则报告予以归档,由IPQC跟踪后续进料品质状况,依5.2.11执行。
5.2.11 IPQC针对责任单位改善后产品加严检验,连续追踪3批无异常予以结案,转正常检验。
5.2.12如责任单位改善措施回复后连续3个月无生产,则强制结案,后续生产依正常检验执行。 5.3 入库品质异常:
5.3.1 OQC依相关检验标准进行判定,确定不良成立时,针对不合格物料标示“不合格”,并要求生产部立即移至不良品区域。
5.3.2 QOC于半小时内开立《品质异常联络单》、《复检通知单》并附不良样品,要求生产单位重工。
5.3.3生产单位接OQC《品质异常联络单》、《复检通知单》及不良样品后,当天安排重工作业,并将回复生产失效原因及改善措施。
5.3.4重工OK产品需重新送OQC检验,重新检验合格予以合格入库,检验不合格转5.3.2要求执行。
5.3.5针对异常改善后产品,OQC时行加严检验,连续追踪3批无异常后予以结案,转正常检验。
5.3.6如异常发生后连续3个月无生产,则强制结案,后续生产依正常检验执行。5.4出货品质异常:
5.4.1 OQC依相关检验标准进行判定,确定不良成立时,针对不合格物料标示“不合格”,并要求物流部立即移至不良品区域。
5.4.2异常确认半小时内开立《品质异常联络单》、《复检通知单》并附不良样品,通知生管安排重工。
5.4.3生产部依安排重工作业,并于《品质异常联络单》回复生产失效原因及改善措施。
5.4.4重工完成产品需重新送OQC检验,依5.3.4执行。5.4.5针对异常改善后再出货产品,OQC时行加严检验,连续追踪3批无异常后予以结案,转正常检验。
5.4.6如异常发生后连续3个月无出货,则强制结案,后续出货依正常检验执行。5.5作业品质异常
5.5.1符合3.1.2任一项,作业品质异常成立。
5.5.2相关部门发现作业品质异常后,立即通知责任单位改善。
5.5.3针对重复发生作业品质异常未达到有效改善时,可开立《品质异常联络单》,由品控统一编号后,交责任单位提出整改措施。
5.5.4责任单位需于《品质异常联络单》需求期限前提出整改措施,由部门最高主管签核后回复异常反馈单位。
5.5.5异常单回复后,由质量部统一归档整理/追踪。
5.5.6改善对策执行后,责任单位QC依对策内容进行追踪确认,连续1个月内无同样异常再发,则予以结案。
5.5.7追踪期内再发则重新开立《品质异常联络单》,依5.5.3-5.5.6执行。
推荐第8篇:供应商品质异常处理协议书
供应商品质异常处理协议书
为了明确供应商产品质量责任,确保产品原材料及供应商的产品质量满足本公司需求,保障本公司生产顺利进行,经供、需双方商定达成以下协议。 1.质量责任:
1.1 供方应承担的责任:
1.1.1供方应对自己原材料进行严格的进货检验,对供应商的材料质量进行跟踪考核,建立质量档案。
1.1.2 供方应建立完善生产工序的控制管理,必须制定生产过程控制文件和作业指导书等,对产品质量有影响的关键工序建立质控点,所有质控点供方要有专人负责,每一个质控点有专门的措施和标准,措施和标准能得到有效的实施。
1.1.3 供方应使生产完全受控,若有失控,应及时查明原因,并采取相应的纠正预防措施。
1.1.4 供方提供的原材料应完全符合需方采购订单及品质规格中明确规定的质量要求,及相应的国际、国家、部委颁发的有关质量标准(包括隐含的质量需求),超出国际、国家质量要求的,以需方要求为准。 1.1.5 供方需保障原材料从出厂至需方收料之前的的包装、运输质量。
1.1.6 供方原材料在需方生产过程中发生品质异常造成需方生产线停线或已生产好的产品返工、返修。 1.1.7 因供方原材料质量问题造成需方产品出厂后发生批次性质量事故(客户索赔、退货等)。 1.1.8 供方原材料问题造成需方产品在用户中出现危及人身、财产安全的。
2.供方交货需遵守以下规定:
2.1 所有供方每批交货时均须有出货检验报告及检验合格标示,其检验内容必须是能保障其材料在需方使用中的性能、功能、装配、使用性、外观等符合要求,交货后有任何因材料发生的品质问题均由供方负责。 2.2 新产品或供方改模、修模必须要送样合格才能批量生产。
2.3 供方产品必须要有标识,标识上要有产品名称、型号规格、生产日期、数量、需方的料号等。
2.4 供方经需方认定批量供货的产品,不得随意更改设计、工艺、技术参数、外形尺寸等;如确实需要更改,必须先通知需方,同时须提供样品给需方确认,经需方确认合格后,才能供货,否则造成的一切损失全部由供方承担。
3.赔偿的具体要求协商确认如下:
3.1 供方原材料入厂后发生品质异常,供方不能处理而委托需方全检、加工,所需的返工等全部费用由供方承担(包括工时费、场地费、管理费、误船费、水电费等),全检的不合格品全部退回供方,并由供方及时补足相应数量。
工时费=处理工时×20元/(人.小时)
如供方需要在需方内部全检水电费、场地费每次100元,管理费每次100元。
3.2 供方原材料同种产品入厂后连续三次以上(含三次)在需方发生问题,需方品管部有权对供方进行暂扣并暂停检验,直到问题改善为止。
3.3 供方原材料入厂后,在生产线发生品质异常造成需方停线返工、返修时,供方需对需方的返工、返修、停线所造成的损失(含所有材料损失费用)进行赔偿。
赔偿费用=停线时间(小时)×300/小时+返工工时×20元/(人.小时)+材料损失费
3.4 供方的原材料因质量问题造成需方产品在客户使用过程中发生品质异常或在客户中出现危及人身、财产安全、丧失使用价值造成被客户索赔,所有索赔费用由供方负责。
3.5 对退回供方的产品,若供方在下次送货时混入,经需方发现,每次处罚人民币1000元。
3.6 需方向供方发出的品质异常单,供方需在1个工作天内回复短期处理方案,7个工作日回复有效的改进预防措施,延期或未回复依品质考核协议处理。
3.7 如发现无法返工的产品需要有权要求供方以先补货再处理不良品,如双方商讨的确产品无法返工需要报废的情况下,由供方在需方QC共同确认的情况下,处理后再退回供方,如不良再次混入则依3.5执行。
4.本协议内所赔偿处罚的金额原则上在相应货款中扣除,特殊情况按月在供方货款中扣除。5.对本协议有内容变更或增加事项时,可在双方协议下进行。 6.生效时间为双方签认本协议后送货时开始生效。
7.争议处理:供方对需方的处理有异议时,应在3个工作日内以书面的形式向需方提出,逾期视为认可需方的处理意见。
本协议为一式两份,双方签字盖章后各存一份,传真件具同等法律效力。
需方地址:
供方地址:
需方公司名称(盖公章):
供方公司名称(盖公章):
代表签字:
代表签字:
品质部代表:
采购部代表:
品质部代表:
采购部代表:
日
期:
日
期:
推荐第9篇:品质异常处理控制程序B(精)
目 录
1.………3 2.…3 3.…3 4.…3 5.…3 6.3 7.
业
务
流
程
业
务
流
职
责
参
考
用
语
适
用
目的……………………………………………………………………
范围……………………………………………………………………
定义……………………………………………………………………
文件……………………………………………………………………
分工……………………………………………………………………
程图 ……………………………………………………………………
说明 …………………………………………………………………3
7.1 ………3 7.
2停
产
(
恢
复
)
报警 ……………………………………………………………………
标准 ………………………………………………………………3 7.
3让
步
申
请
及
签
字
权限 ……………………………………………………………6 7.4……6 8……9 9………10
1.目的
完善质量反馈信息流程,使每个问题的反馈都能得到有效改善,便于异常质量信息的分析、整改,做好纠正预防措施,杜绝批量质量事故的发生,减少质量事故造成的损失, 同时满足顾客的质量要求。 2.适用范围 3.用语定义 无
质量存档 ……………………………………………………………………
. 流程KPI……………………………………………………………………
. 附录 ……………………………………………………………………
4.参考文件:
《质量异常报警流程》、《停产\\恢复流程》、《让步申请流程》 5.职责分工
5.1 质量部:负责质量信息的跟进和相关责任部门回复的整改措施进行跟进; 5.2 生产部:
负责开立影响生产现场正常进行的《品质异常信息报警单》,并负责追踪相关责任部门进行措施回复;
负责其他部门开立的有关生产《品质异常信息报警单》进行措施回复,并要跟进行措施的验证;
还要负责保存本部门开立的且相关责任部门回复合格的《品质异常信息报警单》及相关质量记录; 5.3 品质处:
IPQC负责对产品的过程进行监控; QA 负责对产品的出货进行质量检验控制;
5.4 质量督办负责统计现场、出货及工序前5位问题,由现场PE牵头组织处理,并制定改善行动措施;
5.5开发、质管、工艺:等职能部门负责确认不良问题点,分析不良的根本原因,出具纠正/预防的控制措施,如出现意见冲突,上诉一级申辩,或由事业部长定裁;
6.业务流程图: 后附
7.业务流程说明: 7.1报警:
7.1.1 质量体系中出现不符合问题时由TCE&Q或发现部门下达《体系纠偏单》并由质量革新部负责跟踪验证,并保存《体系纠偏单》及相关质量记录; 7.1.2 IQC检验经理对来料进行检验过程中发现物料不良后,应及时在检测平台中下达《纠偏单》并负责对下单的《纠偏单》进行追踪要求厂家及时在系统中进行回复,由IQE对物料厂家回复《纠偏单》中的整改措施进行跟踪、验收、关闭;
7.1.3 电脑板类似功能及外观不良问题连续出现3台,累计不良出现5台或发现严重异常问题点(如批量、重复问题)等,订单执行经理应立即停线并及时下达《品质异常信息报警单》, 转相应的IPQC审核后反馈现场的PE,由现场PE分析原因\\判定责任部门,并由责任部门制定改善、处理措施,下单部门及IPQC对回复的信息进行监控关闭,最终由相应的订单执行经理保存回复合格的《品质异常信息报警单》;
7.1.4 IPQC在每日巡检时,将在巡检过程中发现的异常问题点记录在《**工段稽核检查记录表》的日报表中,及时录入到《海尔智能电子质量管理查询平台》中;相应的责任订单执行经理对IPQC录入系统中的问题点进行措施回复;IPQC对于责任订单执行经理回复的整改措施进行验收,对于验收不合格的IPQC将在系统中直接给予判不合格打回;责任订单执行经理将重新在系统中回复有效的整改措施。IPQC在制程中发现重大质量隐患、重复发生的问题,IPQC将对责任生产线下达《质量预警停产通知单》,要求责任部门进行停线整改,整改完毕后IPQC去验收,合格后由相应的IPQC下达《质量恢复生产通知单》并通知生产线可以正常生产;
7.1.5 QA检验经理发现技术条件不符等问题时下达《信息反馈单》,由客户经理牵头反馈解决,品质处根据处理结果确定产品是否出货并保存《信息反馈单》及相关质量记录,并在出货前将《信息反馈单》随同产品一起给到事业部的质量部;
7.1.6 出货检验中出现的异常现象,由QA检验经理下达《质量整改单》给分公司,由分公司进行原因分析及措施回复,品质处对分公司回复的措施进行跟踪确认,无问题后将《质量整改单》与相应质量记录存档备案;
7.1.7在《品质异常信息报警单》回复后判定产品存在质量隐患需要返修或返工的产品,PE/IE下发作业指导书经IPQC会签、工艺处长签字批准后,应从生产线返修品投入口重新下线,同时有IPQC现场跟踪确认,对于批量改制或批量返修的产品需要客户经理召集工艺处、质管处、质改室、品质处及分公司等相关部门会议讨论评估,最终返修工艺根据会议讨论结果制订,IPQC在会签此类返修工艺时无相应会议记录禁止开线;
7.1.8 下单部门及IPQC根据《品质异常信息报警单》中措施的到位时间进行跟踪验证,并将措施的验证情况写在相应的报警单中,对于验证无问题的交由品质处负责人进行审核,质量部长批准后由下单部门将报警单予以存档备案; 注解:
1.《品质异常信息报警单》下达给上工序责任人,由接单人负责签收、追踪;2.《品质异常信息报警单》中紧急措施应在两小时内回复,不能及时出具时,应由第一责任人
召开会议,研究紧急措施;对于报警单的回复情况,IPQC会进行不定期的跟踪排查,下单部门将对不能及时回复的《品质异常信息报警单》汇总并对接单人进行通报处理;
3.《品质异常信息报警单》中根治措施应在48小时内回复,回复不及时将对责任人进行通报处理;
4.《品质异常信息报警单》以下单月份统一编号,如:2006年5月第一份即:06050001,依次类推,公司编号为:青岛(QD)做编号前缀,如QD06050001;5.对已关闭的《品质异常信息报警单》由相应的下单部门督办按照编号顺序进行存档,以月为单位累计交文控存档; 7.2 停产(恢复)标准及流程: 7.2.1停产标准:
出现异常质量信息(含报警流程中内容)报警后,两小时内未有任何反馈,对责任生产线进行停线、整顿,客户经理或分公司经理召集相关部门处理;
现场出现不按规定操作、重大质量事故或重复问题(一周内重复发生三次)没有根治措施,品质处IPQC下达《质量预警停产通知单》转分公司经理处理; 内/外审核出现严重不符合项,经体系审核员、公司经理人、品质处共同研究需停线整顿时,由品质处IPQC下达《质量预警停产通知单》转分公司经理处理; 产品事业部出现不良比率≥1%(10000PPM),由质改经理下达《质量预警停产通知单》,转分公司经理处理; 7.2.2 恢复标准:
整改措施有效,经第三方(TCE&Q、质量部)验收合格,下达《质量恢复生产通知单》方可试产,试生产时间控制在一小时内,无质量问题后方可进行批量生产;
经验收不合格的生产线继续停线整顿,直至质量部验收合格后方可正常生产;
注解:
1.停产通知单IPQC下发即可生效,分公司有异议可反馈品质处长、质量部长、事业部长,逐级上诉,反馈期间不可继续生产;
2.停产期间分公司经理与订单执行经理根据出现的问题组织全员对标准进行学习,并写出整改报告及质量承诺;
3.恢复生产前需将恢复生产请示单及整改措施提交品质处备案;7.3 让步申请及签字权限:
7.3.1 原则上不做让步,当定单紧急时由PE工程师或质量部长评估不会引起客户质量投诉的前提下方可让步;
7.3.2 让步申请人召集相关部门进行讨论,判断可行性并在《让步申请单》中会签意见;
7.3.3 权限部门意见栏必须由相应负责人评估后方可执行;
7.3.4 质量部长出具最终意见,品质处按意见控制闸口;
(注:1.当签字权限人不在公司内的情况下,需事业部长的签字方可执行;) 7.4 质量存档:
7.4.1 本平台中质量记录保存期限一年; 注解:
本文件一经批准立即实施,如违反规定对责任人处理时,有不符意见可申诉或由事业部长仲裁。
8.流程KPI 无
9.附录(见附表
附表A 表号:CX-ZLB-17-F01 《品质异常信息报警单》
附表B 表号: CX-ZLB-17-F02 《异常质量信息报警单台帐》
附表C 表号:CX-ZLB-17-F03 《让步申请单》
附表D 表号:CX-ZLB-17-F04 《让步单汇总表》
附表E 表号:CX-ZLB-17-F05 《质量预警停产通知单》 附表F 表号:CX-ZLB-17-F06 《质量恢复生产通知单》
附表G 表号:CX-ZLB-17-F07 《停产恢复台账》 (附表H 事业部信息反馈单格式)
推荐第10篇:SQE品质异常处理作业规定
核准: 九 牧 集 团 有 限 公 司 五 金 龙 头 事 业 部作业规定文件名称: SQE品质异常处理作业规定文件编号:WI11PB080000版次:A/0发行日期:受控状态:分发号:审查:编制:
第11篇:品质异常处理流程及方法
品质异常处理流程及方法
摘要:品质人员的工作职责之一就是要及时发现反馈生产中的品质异常状况,并督促现场执行改善措施、追踪其改善效果,保证只有合格的产品才能转入下一道工序,生产出高质量的产品.品质人员的工作职责
1、熟悉所控制范围的工艺流程
2、来料确认
3、按照作业指导书规定进行检验(首检、巡检)
4、作相关的质量记录
5、及时发现反馈生产中的品质异常状况,并督促现场执行改善措施、追踪其改善效果
6、特殊产品的跟踪及质量记录
7、及时提醒现场对各物料及成品明显标识,以免混淆
8、及时纠正作业员的违规操作,督促其按作业指导书作业
9、对转下工序的产品进行质量及标识进行确认
品质异常可能发生的原因
生产现场的品质异常主要指的是在生产过程中发现来料、自制件批量不合格或有批量不合格的趋势。品质异常的原因通常有:
A.来料不合格包括上工序、车间的来料不合格
B.员工操作不规范,不按作业指导书进行、新员工未经培训或未达到要求就上岗 C.工装夹具定位不准 D.设备故障
E.由于标识不清造成混料 F.图纸、工艺技术文件错误。
品质异常一般处理流程
1、判断异常的严重程度(要用数据说话)
2、及时反馈品质组长及生产拉长并一起分析异常原因(不良率高时应立即开出停线通知单)
3、查出异常原因后将异常反馈给相关的部门 (1)来料原因反馈上工序改善 (2)人为操作因素反馈生产部改善 (3)机器原因反馈设备部 (4)工艺原因反馈工程部 (5)测量误差反馈计量工程师 (6)原因不明的反馈工程部
4、各相关部门提出改善措施,IPQC督促执行
5、跟踪其改善效果,改善OK,此异常则结案,改善没有效果则继续反馈
怎样做才能尽可能的预防品质异常
SPC是一款专门分析品质异常的工具,它主要是应用统计分析技术对项目过程进行实时监控,区分出过程中
的随机波动与异常波动,了解每个工序有可能出现的品质异常、了解哪些工位容易出品质异常,从而对过程的异常趋势提出预警,以便及时采取措施, 消除异常,恢复稳定,从而达到稳定过程,提高和控制质量的目的.
第12篇:产品异常报告
关于13925-1-1T产品发霉报告
雷课:
见文好!
针对13925-1-1T产品齿缝里面发霉事件,我司收到贵公司发来邮件,我们召集了主管,生产中各个环节的负责人,对问题作了深刻检讨,以及探讨,分析问题根本原因所在。并对问题制定改善措施,以免类似问题再次发生。
1.我们将对封孔槽温度进行管控,以免造成齿缝里面起雾等现象。
2.后工序,品检的产品,我们将增加人员,对产品进行100﹪全检。
3.对于封孔起雾,产品齿缝里面存粉沫状的东西,我们将进行返工处理。
连盛可五金制品有限公司
2014年8月19日
第13篇:异常分析报告
异常分析报告
公司领导签发:王振根 部门领导:王海峰 编写: 谢云峰 1.异常名称:#
1、2机组脱硫效率低于90%。
2.异常时间:#1机组脱硫效率低于90%时间为7月27日8:45-10:24,#2机组脱硫效率低于90%时间为7月27日9:10-11:13。3.异常前运行方式:二台循环泵运行,正常补浆。
4.处理过程:开三台循环泵运行,增加补浆量,同时倒运部分浆液至事故浆液罐,加大出石膏量,脱硫效率恢复至90%以上。5.异常分析:出石膏不及时,吸收塔内浆液品质变坏,导致脱硫效率下降。直接原因为石膏脱水机出力小,石膏厚度小(仅为30cm左右,而根据厂家提供的技术文件,可以保证石膏脱水机石膏厚度达到45mm左右。间接原因为二台脱水区地坑泵有缺陷,不能正常投运,同时安装的临时水泵出力不足,不能及时排出石膏脱水机排水,导致石膏脱水机不能连续投入运行。
6.防范措施:运行人员要加强对浆液密度、PH值等参数的关注,发现有变坏的趋势时提前进行调整;设备部要加强设备的管理工作,确保脱硫设备能正常投入运行;维护部要加强设备检修工作,发生设备缺陷时及时处理,避免发生纠皮现象
7.必须采取的应急措施: 遇到紧急情况(影响脱硫效率)时,可向公司环保负责人请示,得到同意后,可临时向雨水井溢流。 8.对责任单位及责任人的考核意见:
根据《河北大唐国际张家口热电有限责任公司脱硫系统考核制度》第二十四条,发电部辅控主管周永宏指导运行人员调整不到位,没有要求运行人员及时调整石膏厚度,考核200元;根据《河北大唐国际张家口热电有限责任公司脱硫系统考核制度》第十九条,设备部综合点检员张彦军未及时组织人员消除设备缺陷,考核200元;根据《河北大唐国际张家口热电有限责任公司脱硫系统考核制度》第二十七条,维护部消缺不及时,且在消缺过程中存在扯皮现象,考核维护部300元;根据《河北大唐国际张家口热电有限责任公司脱硫系统考核制度》第二十条,物资部未及时购买脱硫滤液水泵备件(7月8日物资需用计划已经得到王总审批,而所需备件至28日才到现场),考核物资部100元;
第14篇:异常分析报告
异常分析报告
由于近期老员工的陆续离职,新员工刚刚接触这个工作,对产品加工认知度及工作经验没有那么丰富。两次加工这类异常已经开会宣导教育了很多次,针对ET-780这次异常将对新老员工进行深刻教育,让员工明白两次加工的危害。强化螺纹孔全检要求,对规定详细化,并且告知每个操作人员。在工作中随时抽查员工是否遵守规定,若有不遵守规定的,对其教育再进行适当的处罚。
通止规通规不过,这个问题不是经常性出现,根据这次JY-037异常分析可能造成导致这次异常的原因,第一个原因由于产品加工位置的模具销为尖顶深度大概5MM-10MM之间,而且加工位置为盲孔,刀具在加工过程中按照先前编好的程式加工,模具销尖顶位置和加工螺纹孔的位置不一定是一致的,刀具的头部也是尖的,尖顶位置在加工的时候给刀具起到了一定的导向作用,这样的话就有可能导致刀具在加工过程中出现与产品部分不垂直,很有可能导致通规通不过。第二原因可能由于设备的精度比较高,对刀具有要求,现在加工底孔的刀具直径为Φ9.38,已经和上海后藤技术部联系过了,加大底孔刀具直径到Φ9.4,如果验证可以,今后就选用Φ9.4的刀具来加工,从源头上杜绝这类不该发生的异常!
以上是本人对这两次异常的分析总结。
时磊2014.6.4
第15篇:品质异常处理及不合格品管理办法
品质异常处理和不合格品管理办法
1.目的:
1.1 为有效的控制不合格和品质异常的重复发生消除产生不合格品的隐患。 2.范围:
2.1 本规定适用于生产制造过程出现品质异常和不合格品的评审及处理
3.定义:
3.1 不合格:不符合合同、标样、图纸、状态、公差、技术条件或其它规定的技术文件的要求。
3.2 不合格品:任何有一个或一个以上指标不符合合同、标样、图纸、状态、公差、技术条件或其它规定要求的产品。
3.3 轻度不合格品:指不构成对产品功能和使用造成影响的产品。(按正常工艺经后道加工后,仍能符合标准要求)
3.4 严重不合格品:指构成对产品功能和使用造成影响的产品。(必须改制或已无加工价值) 3.5 重大质量事故:指某产品在生产过程出现:经济损失达30000元以上批量不合格。 4.指导文件:
4.1 《不合格品控制程序》 5.职责:
5.1品检部负责提报异常与不合格;制造部负责组织相关部门进行评审;品工部负责制订对策措施。 5.2制造部负责按评审意见处理不合格品(包括处置过程中做好不合格品的隔离、标识,记录、信息传递)。 5.3品工部负责提供返工(修)作业指导书 5.4品检部负责对返工、返修产品进行确认;
5.5 各责任单位依不合格品评审得出的结论进行原因分析和纠正、预防措施,品检部进行措施验证。 6.工作程序:
6.3.检验员应在《不合格品(异常)处理单》注明(如属成品则记录其责任工序): 6.3.1 该产品的生产班组、日期、带班师傅、操作工等; 6.3.2 产品代号、工序名、状态、流程卡号、本批产量等; 6.3.3在不合格品特征描述栏目中注明5w2h。 6.4 对不合格品评审处理:
6.5.1.1品检部品质主管在收到《不合格品(异常)处理单》后应在4小时内签署处理意见后研发中心、品检部等部门进行评审,各相关评审部门应对影响产品质量的诸要素进行分析和判断后,提出对不合格品的处理意见,并填写在《不合格品(异常)处理单》相关栏位,具体要求如下:
(A)品检部门接到质量信息后,应对所发生的质量问题4小时内作追溯性分析,分析产品的原始记录,分析产生的原因。隔离由此原因而引起的半成品、成品。并对一些相对简单由员工主观原因引起的质量问题直接进行判定,提出纠正预防措施和处罚意见;反之,对一些相对复杂、由工艺设计原因引起的、重复发生的、品质部门无法采取有效措施进行提高的质量问题由制造部、品工部、项目部等相关部门分析;对一些会影响客户交货的质量问题,品检部门应即刻反应,召集相关人员进行原因分析,提出纠正预防措施。 (B)研发中心开发部接到质量信息处理单后,根据品检部门提供的原始记录与分析意见,仔细核对控制计划,找出问题产生的原因,提出纠正预防措施,持续改正产品工艺、控制计划及PPAP。在8小时内完成。对于一些技术部门还是难以判定或采取的纠正预防措施被验证是无效的质量问题,提请开发总监/常务副总处理。
(C)开发总监/常务副总根据品检部门、品工部、开发部、制造部门意见,在4小时内提出处理意见,对于一些涉及公司重大经济损失和严重影响公司声誉的质量问题,在发生后的1小时向总经理进行汇报。
6.5不合格品的处理:
6.5.1对不合格品评审处理后,品检部将处理单分发相关部门,对不合格品按处理单意见进行挑选、返工、报废处理。
6.5.2各个生产工序中的少数报废品,由检验员清点、核实并记录后,统一放至各车间的红色废品盒内,每天由专人予以清理。6.6纠正措施:
6.6.1品检部负责对责任单位的纠正和改进措施落实的每一步骤予以监控,在责任单位的纠正措施均已落实后,品质主管应对纠正后的产品质量和纠正前的产品质量进行分析,若恢复到正常的质量水平或达到标准要求,则可给予结案,若认为还有尚待纠正或改进时,可依《纠正和预防措施控制程序》规定进行处理。6.6.2 若在对不合格品评审处理中,需从技术更改方面进行彻底纠正,则应依《过程更改控制程序》规定执行。
6.6.3让步放行:让步放行,应由质保中心总监批准后方可执行,具体按《过程更改控制程序》规定执行 。
前言
本制度为规范公司“不合格品控制”而制定 本制度于2007年第一次修订
本制度由公司质保中心品检部提出
本制度由公司质保中心品检部负责起草 本制度由公司质保中心品检部负责归口
本制度由打印、
本制度主要起草人:
本制度审核人:
本制度批准人: 校对、共印份
第16篇:品质异常处理程序1_图文(精)
Y1.0 目的
为了明确和规范在品质异常处理过程中各相关部门及人员的作业职责和作业方法。 2.0 适用范围
适用于来料、制程、出货以及客户投诉等异常处理范围。
3.0 职责 3.1品质部:
A、负责过程《品质异常处理单》的提出和改善过程、改善结果的跟进与验证;
B、负责品质异常状况的统计记录、每周品质例会的主持召开及《品质异常处理单》的提出和改善过程、改善结果的跟进与验证;
3.2 生产部、采购部:负责每周品质例会的参加及品质部《品质异常处理单》、提出的回复(需对异常内容进行原因分析、纠正预防对策的制定及执行与反馈)。
3.3工程部:负责协助品质异常的处理和改善工作。3.4 副总经理/总经理:负责品质异常争议结果的裁决。
3.5 业务部:负责客户投诉的反馈及有效地处理顾客意见和与客户进行异常沟通。
4.0 作业程序
4.1客户投诉的品质异常反馈
4.1.1客户投诉反馈:业务部在接到客户投诉后,需对客户投诉内容进行整理并将投诉信息以书面形式反馈给品质部。
4.1.2 来料、制程不合格反馈:IQC、IPQC、FQC在做来料检验、成品检验时,如发现产品不合格,需向品质主管进行反馈。
4.1.3 其它品质异常反馈:如生产部自检、互检时发现产品不合格,也需要向品质部进行不良信息反馈。 4.2 品质异常的记录、统计
4.2.1品质部每日需对其它部门或人员所反馈的品质异常进行记录并进行品质异常的判定、《品质异常处理单》的提出工作。
4.2.2 品质部需每周对所发生的品质异常状况进行一次统计汇总同时将统计的〈品质周报表〉分发给相关部门各一份,并利用品质统计报表每周定期的组织相关部门或人员召开《品质周例会会议》(针对突发或重大品质异常事故,需另外约定时间召开品质专题会议),并在会议中对报表中所统计的异常结果进行“原因分析、改善对策”的讨论、制定。 4.3 品质例会召开及《质量整改通知单》的提出
4.3.1 品质例会的召开:品质会议主题主要为“本周内前两到三项最主要品质问题点的原因分析及改善对策的讨论”具体见《品质会议管理制度》。 4.3.2 《质量整改通知单》的提出:品质需把每周的品质周报表与品质例会所讨论做出的决议事项相结合,向相关责任部门以《质量整改通知》的形式提出改善要求。
4.4责任部门问题点原因分析
4.4.1相关部门在接到品质部所提出的《品质异常处理单》或《质量整改通知单》后,需对报告中所提出的问题点进行细部的发生原因分析,举例如生产部接到品质部《品质异常处理单》或《质量整改通知单》中所提出的如:“产品色不对板”不良时,生产部需对产生此不良现象的各责任组、人员的作业手法、设备的操作方法、流程执行情况等进行细部的原因分析,找到发生“色不对板”的主要责任组、责任人员以及主要原因,并将所分析的原因填写在报告中(责任部门在作原因分析时可利用“QC七大手法,如鱼骨图、柏拉图”等工具)。4.5责任部门问题点纠正改善对策的制定
4.5.1责任部门在问题点原因分析完成后,马上对所分析出的问题点发现原因制定纠正对策,所制定的纠正对策必须与分析出来的问题发生原因能一一相对应,并针对所制定的纠正对策来制定一个实施纠正措施的实施推进计划,确定过程控制的方法并纳入文件进行管理,以确保根本原因的消除,在生产中应用该措施时应监督其长期效果,所作出的对策必须是有效的、可执行实施的,同时需注明对策的实施执行时间、责任单位、责任人、计划完成时间、完成情况等。4.6责任部门问题点预防改善对策的制定
4.6.1待纠正措施实施且有效后,责任部门需针对所发生的问题点制定“预防措施”,以保证类型问题的再次发生,主要作业方法为“修改现有的管理系统、操作系统、工作惯例,重新梳理现有的管理方法、操作流程等以防止这一问题与所有类似问题重复发生”,所作出的对策必须是有效的、可执行实施的,同时需注明对策的实施执行时间、责任单位、责任人、计划完成时间、完成情况等。4.7改善结果的跟进与验证
4.7.1品质部需对责任部门所作出的“原因分析、纠正措施、预防措施”进行验证,验证其是否合理、有效、可实施执行,如不能满足以上条件,视为对策不可行,必须由责任部门重新进行制定,如所制定的方案满足以上条件的,则由品质部安排人对方案的实施情况、完成时间、完成效果进行定期的检查与跟进,以确保方案实施的有效性与及时性,如所对策实施的结果验证为无法满足要求时,品质部有权要求责任部门重新制定对策实施,直至结果验证通过为止。5.0奖罚规定
5.1针对产品上线,车间组长所在车间上线任何产品,必须确认自己手上领有三大项资料(实物样板、工程资料、生产排期),指导员工任何工序的操作时,必须每道工艺核对过此三种资料,做到所做产品与此三种资料三项统一,确保因工艺错误或用料错误等因无核对导致的批量返工。所有款品质部《首件检验表》上组长必须签字确认所有资料已核对过。首件确认OK。如被查出因未按照要求核对资料及没签到首件所导致批量质量问题的组长给予一次罚款30元处罚。
5.2针对过程质量监控,车间组长在指导每一个员工操作时,必须先试做三至五个标准合格品,并在做的过程中清晰讲解每一个动作要领和工艺要求和所做工序与上下工序之间的关系。并提供给QC组长签首件。要让员工明白自己所做的该道工序要做到什么程度才是符合品质标准的,如果做不好会对下道工序有什么不良影响和对整个成品有什么不良影响。组长指导过后先查看确认该员工所做的前三件产品合格后方可离开进行下一个人的指导。否则发现一次罚款20元。
5.3品质部每周五主持品质例会,并出具《质量问题整改通知单》,汇总上一周各车间的不良率和数量最多的三项瑕疵问题点。由所在各车间主管,组长查出这些瑕疵点的主要责任人员的名单并填写在《质量问题整改通知单》上,对这些责任员工的处理方案是什么?同时分析导致这些员工出现这些问题是什么原因?针对所分
析的每一个原因的解决措施或方案?通过这些方案的实施预计达到的预期效果 逐项全部完整填写在《质量问题整改通知单》上,并签字确认会议后2天内交回品质部主管,最终由品质部监督在实际操作中有没有落实并在下一周的数据中验证是否达到预期目标?如果没有执行和落实的组长一次罚款30元、主管一次罚款50元处理;对于有执行但没有达到要求,而组长不提出改善要求的的一次给予组长10元罚款处理。
5.4针对重大质量事故导致批量返工或报废等,由品质部不定期随时召开品质专案会议,并出具《品质异常处理单》。由生产部组长负责查找责任员工并提出对责任员工的处理方案、分析原因并提供解决方案和时间、提供预防措施和落实时间,并详细填写在《品质异常处理单》上,车间组长填写签字完毕后在会后半小时内交回品质部组长及主管,由品质部监督是否落实实施,并对结果判定是否合格。对于没有执行落实的车间组长一次给予50元罚款处理;对于有执行落实但没有达到合格效果的车间组长一次给予20元罚款处理,并再次有组长分析没有做到的原因和应对的方案和计划落实的时间,并由品质部监督落实的结果。
5.5针对《品质异常处理单》、《质量整改通知单》中的方案实施要求,责任部门没有按要求执行的,主管第一次未执行的罚款20元,第二次未执行的罚款40元,以此类推。
5.6针对《品质异常处理单》、《质量整改通知单》中的方案实施要求,责任部门主管未按期完成的,延期一次罚款10元。
5.7对于不良率连续三周没有得到下降反而上升的,给予责任班组长罚款50元,给予责任主管罚款100元处理,连续5周没有下降反面上升的给予责任人罚款100元,给予责任主管罚款150元处理。
5.8对于当周问题点所制定实施的品质方案实施结果有效的,且不良率连续两周同比下降2%的,责任班组长奖励50元,责任主管奖励100元,连续三周同比下降5%的,责任班组长奖励100元,责任主管奖励150元。
5.9对于班组整体不良率在方案实施后连续三周控制在规定目标范围以内的,给予责任班组长、主管奖励100元,连续两个月都控制在目标要求范围以内的,给予责班组长、主管奖励200元。
5.10针对以上本文的所有规定,如品质部发现未按要求如期执行的,一次罚款50元,如发现品质部不按要求执行的发现一次罚款100元。
5.11针对以上罚款事项,如责任人拒绝罚款的,将由公司直接从其工次中拿出该罚款的金额。
5.12针对以上奖罚规定,品质部有权直接开出〈罚款单〉或《奖励单》给予副总经理、总经理签字确认进行罚款执行。
5.13针对以上罚款事项,一律以现场现金乐捐到“乐捐箱”中执行,对于拒绝接受罚款的,将直接到财务从其工资中拿出该罚款金额乐捐到“乐捐箱”中。6.0 相关文件
6.1 《品质例会管理制度》 6.2 《品质异常处理流程》 7.0 相关表单
7.1 《品质异常处理单》 7.2 《质量整改通知单》
7.3 《会议记录表》 7.4各部门品质目标要求: 部门
注塑部
移印部
喷油部
组装部
包装部
-63-
半成品目标要求 10% 10% 10% 10% 10%
成品目标要求 5%
5% 5% 5% 2%
报检合格率 98%
98%
98% 98% 98%
第17篇:品质异常处理通知单管理规定(推荐)
文件编号 版本版次 文件名称 品质异常处理通知单管理规定 页码页次 1 / 3 制定部门 1.0.目的: 规范制程品质异常处理流程,提高品质异常处理通知单的时效性,确保产线的正常运转,同时满足顾客的质量要求。 2.0.适用范围: 适用于本公司制程、出货品质异常的处理。
3.0.职责与权限:
NO.部门 职责与权限 品管部负责品质异常分析及改善有效性确认。 1 负责品质异常的改善和预防措施的实施。 2 生产部 负责协助参与原因分析及相应的预防改善措施。 3 技术部 4 其它相关部门 协助进行安排异常改善通知的配合 。 4.0.术语与定义:
4.1 制程品质异常:
a、严重缺陷超过3%; b、使用不合格的原料或材料; c、同一缺陷连续发生; d、不遵守作业标准或不遵守工艺卫生要求; e、机械发生故障或磨损; f、其他情形影响到产品质量时; 4.2 出货品质异常: 出货发现严重缺陷超过1%; 5.0.运作流程: 无 6.0 作业程序: 6.1 制程品质异常:
6.1.1异常属现场作业人员发现,需立即找QC或工程师确认不良现象可否接收。如异常可接受则继续生产,不可接收依6.1.2执行。 6.1.2 IPQC依相关检验标准进行判定,确认不良成立时,应开具《品质异常处理通知单》并评估异常的严重性要求生产部门暂停生产。
6.1.3针对已生产产品依产品标识卡信息往前追溯,直至良品。6.1.4 IPQC针对已追溯到的不良品标示“不合格”,并要求生产单位立即移至不良品区域,不良品如可以进行 文件编号
版本版次
文件名称 品质异常处理通知单管理规定 页码页次 2 / 3 制定部门 返工、返修达到合格要求,生产依需求的返工、返修方案对不良品进行返工、返修,返工返修后需交付IPQC进行检验,合格品进行流向下一站,不合格按照《不合格品控制程序》处理。
6.1.5生产后IPQC负责跟踪相关工序,确认临时应对措施是否有效。6.1.6制程品质异常开立时机: 6.1.6.1制程异常属材料所致,需第一时间通知责任单位、IQC前往确认,双方判定标准一致,确认异常成立,则开立《品质异常处理通知单》要求责任单位改善。
6.1.6.2产品制造过程中如发现产品同种异常现象不良率超过3%时,IPQC应开出《品质异常处理通知单》待技术与品质协助分析出原因找出责任单位后由责任单位进行对策,品质部监控对策实施有效性.。6.1.6.3品质再现(品质异常重复发生)时,开立《品质异常处理通知单》,评估重复发生事宜的情况通知生产单位停线整改。 6.1.7所有制程中《品质异常处理通知单》需生产部进行会签,技术部接到品质异常处理通知单后1小时内需针对异常现象提出临时对策。
6.1.8责任单位需于收到《品质异常处理通知单》48小时内,针对异常现象提出长期改善方案。6.1.9 品质工程师针对责任单位回复内容进行确认,针对改善措施不合格部分予以退件,要求责任单位重新回复。改善措施合格,则报告予以归档,由IPQC跟踪后续品质状况,依6.1.10~6.1.11执行。
6.1.10 IPQC 针对责任单位改善后产品加严检验,连续追踪2 天(或3 批)无异常予以结案,转正常检验。 6.1.11 如责任单位改善措施回复后连续2 个月无生产,则强制结案,后续生产依正常检验执行。 6.2 入库品质异常: 6.2.1 FQC 依相关检验标准进行判定,确定不良成立时,针对不合格物料标示“不合格”,并要求生产单位立即移至不良品区域。 6.2.2 FQC 于半小时内开立《品质异常处理通知单》并附不良样品(功能不良请技术协助分析处理),通知生产安排返工。 6.2.3 生产部接FQC《品质异常处理通知单》或《验货通报》及不良样品后,当天安排返工作业,FQC 负责跟踪返工及验证工作。 6.2.4 生产返工后的产品需重新送FQC 检验,重新检验合格予以合格入库,检验不合格依《不合格品控制程序》要求执行。 6.2.5 针对异常改善后产品,FQC 时行加严检验,连续追踪3 批无异常后予以结案,转正常检验。 6.2.6 如异常发生后连续2 个月无生产,则强制结案,后续生产依正常检验执行。 6.3 出货品质异常: 6.3.1 OQC 依相关检验标准进行判定,确定不良成立时,针对不合格品标示“不合格”,并要求仓库立即移至不良品区域。
文件编号
版本版次
文件名称 品质异常处理通知单管理规定 页码页次 3 / 3 制定部门 6.3.2 异常成立半小时内开立《品质异常处理通知单》并附不良样品(功能不良请技术协助分析处理),通知生产部安排返工。 6.3.3 生产部收到《品质异常处理通知单》或《验货通报》后安排返工作业,OQC 负责跟踪返工及验证工作。 6.3.4 生产返工后的产品需重新送OQC 检验,重新检验合格予以合格出货,检验不合格依《不合格品控制程序》要求执行。 6.3.5 针对异常改善后再出货产品,OQC 应加严检验,连续追踪3 批无异常后予以结案,转正常检验。 6.3.6 如异常发生后连续2 个月无出货,则强制结案,后续出货依正常检验执行。
6.4 作业品质异常 6.4.1 符合4.1 中d、e、f 任一项,作业品质异常成立。 6.4.2 相关单位发现作业品质异常后,立即通知责任单位改善。 6.4.3 针对重复发生作业品质异常未达到有效改善时,可开立《品质异常处理通知单》,由品质统一编号后,交责任单位提出整改措施。 6.4.4 责任单位需于收到《品质异常处理通知单》48小时内给出整改措施,回复反馈到单位。 6.4.5 异常单回复后,由品质统一归档整理/追踪。 6.4.6 针对不良产品可分析出根本原因,在品质异常处理通知单上直接回复原因分析并转交给责任单位回复改善及预防措施;如不能分析出根本原因,将不良实物与品质异常处理通知单转交技术部人员协助分析原因。 6.5 客户投诉或抱怨 客诉品质异常依《客户投诉处理程序》。 7.0.相关文件:
NO.文件名称 文件编号 1 2 3 8.0.相关记录
NO.记录名称 表单编号 保存期 记录保存部门 1 2 3
第18篇:六楼存在的品质异常问题明细
六楼5月份存在的品质异常问题点
1、自制白色天线每批次都存在一定比例的色差(杆套与固定座);
2、天线馈线编织网未裁断导致焊接连锡,(目前有所改善)!
3、巴西MTLQ240910050PCS天线吸塑与彩卡飞机孔错位1-2.5CM,开出停 线整改通知单未回复 ;
4、自制天线二次出现压卯后馈线还有松动能拉动的现象(1次在后段H线物料上线前发现;2次在天线制程中IPQC抽检发现),已反馈给天线部并要求IPQC加管控。
5、前加工机器常出现故障、来料边带错位及元件排例错位导致一些元器件加工后变形和偏差大;
6、物料混、错料:
(1)同模机壳(上下盖)混料,(仓库、来料、产线清尾)
(2)仓库发错料:RJ45 10P8C黄色错为黑色10P8C 2K、W311R+LPA110308-A5KL线待生产仓库发错料原滤波器H7201DG 1210110209错发成TF-208DG 12101102009滤波器全部发错,料单未打错,实物发错 发料(已多次发生)
(3)K、L线晶振混料W311R晶振混料50PCS、W301A混32PCS、W316R186PCS晶振:18001300009 25MHZ-20PPM-10PF混入18000400009 25MHZ-30PPM-20PF;
(4)、产线清尾产品容易混、错料:
组装同模机壳常有混料或用错机壳现象 ;
包装光碟、保修(TENDA与IP-COM)常用错料;
7、生产首件错:与相比4月份有所改善(但还没有得到完全改善);
8、IPQC对无线测试的不懂导致在无线产品各个测试段的品质管控非常薄弱;
9、品质CAR开出后各单位很少有能及时回复(严重影响异常处理的跟进及改善效果的验证,甚至有些单位对开出的品质CAR不了了之);
第19篇:品质异常反馈单管理规定._图文(精)
1.0.目的:
规范制程品质异常处理流程,提高品质异常反馈单的时效性,确保产线的正常运转,同时满足顾客的质量要求。
2.0.适用范围:
适用于本公司制程、出货品质异常的处理。
3.0.职责与权限:
NO.部门 职责与权限
1 品管部 负责品质异常分析及改善有效性确认。
2 生产部 负责品质异常的改善和预防措施的实施。
3 工程部 负责协助参与原因分析及相应的预防改善措施。
其它相关部4 协助进行安排异常改善通知的配合 。
门
4.0.术语与定义: 4.1 制程品质异常: a、严重缺陷超过3%; b、使用不合格的原料或材料; c、同一缺陷连续发生;
d、不遵守作业标准或不遵守工艺环境要求; e、机械发生故障或磨损;
f、其他情形影响到产品质量时; 4.2 出货品质异常:
出货发现严重缺陷超过1%;
5.0.运作流程:
无
6.0 作业程序:
6.1 制程品质异常:
6.1.1异常属现场作业人员发现,需立即找QC或工程师确认不良现象可否接收。如异常可接受则继续生产,不可接收依6.1.2执行。
6.1.2 IPQC依相关检验标准进行判定,确认不良成立时,应开具《品质异常反馈单》并评估异常的严重性要求生产部门暂停生产。
6.1.3针对已生产产品依产品标识卡信息往前追溯,直至良品。
6.1.4 IPQC针对已追溯到的不良品标示“不合格”,并要求生产单位立即移至不良品区域,不良品如可以进行返工、返修达到合格要求,生产依需求的返工、返修方案对不良品进行返工、返修,返工返修后需交付IPQC进行检验,合格品进行流向下一站,不合格按照《不合格品控制程序》处理。
6.1.5生产后IPQC负责跟踪相关工序,确认临时应对措施是否有效。6.1.6制程品质异常开立时机:
6.1.6.1制程异常属材料所致,需第一时间通知责任单位、IQC前往确认,双方判定标准一致,确认异常成立,则开立《品质异常反馈单》要求责任单位改善。
6.1.6.2产品制造过程中如发现产品同种异常现象不良率超过3%时,IPQC应开出《品质异常反馈单》待工程与品质协助分析出原因找出责任单位后由责任单位进行对策,品质部监控对策实施有效性.。
6.1.6.3品质再现(品质异常重复发生)时,开立《品质异常反馈单》,评估重复发
生事宜的情况通知生产单位进行整改。
6.1.7所有制程中《品质异常反馈单》需生产部进行会签,工程部接到品质异常反馈单后1小时内需针对异常现象提出临时对策。
6.1.8责任单位需于收到《品质异常反馈单》48小时内,针对异常现象提出长期改善方案。
6.1.9 品质工程师针对责任单位回复内容进行确认,针对改善措施不合格部分予以退件,要求责任单位重新回复。改善措施合格,则报告予以归档,由IPQC跟踪后续品质状况,依6.1.10~6.1.11执行。
6.1.10 IPQC 针对责任单位改善后产品加严检验,连续追踪2 天(或3 批)无异常予以结案,转正常检验。 6.1.11 如责任单位改善措施回复后连续2 个月无生产,则强制结案,后续生产依正常检验执行。 6.2 入库品质异常:
6.2.1 OQC 依相关检验标准进行判定,确定不良成立时,针对不合格物料标示“不合格”,并要求生产单位立即移至不良品区域。
6.2.2 OQC 于半小时内开立《品质异常反馈单》并附不良样品(功能不良请工程协助分析处理),通知生产安排返工。
6.2.3 生产部接OQC《品质异常反馈单》或《验货通报》及不良样品后,当天安排返工作业,FQC 负责跟踪返工及验证工作。
6.2.4 生产返工后的产品需重新送OQC 检验,重新检验合格予以合格入库,检验不合格依《不合格品控制程序》要求执行。
6.2.5 针对异常改善后产品,OQC 时行加严检验,连续追踪3 批无异常后予以结案,转正常检验。
6.2.6 如异常发生后连续2 个月无生产,则强制结案,后续生产依正常检验执行。 6.3 出货品质异常:
6.3.1 OQC 依相关检验标准进行判定,确定不良成立时,针对不合格品标示“不合格”,并要求仓库立即移至不良品区域。
6.3.2 异常成立半小时内开立《品质异常反馈单》并附不良样品(功能不良请工程协助分析处理),通知生产部安排返工。
6.3.3 生产部收到《品质异常反馈单》或《验货通报》后安排返工作业,QC 负责跟踪返工及验证工作。
6.3.4 生产返工后的产品需重新送OQC 检验,重新检验合格予以合格出货,检验不合格依《不合格品控制程序》要求执行。
6.3.5 针对异常改善后再出货产品,OQC 应加严检验,连续追踪3 批无异常后予以结案,转正常检验。
6.3.6 如异常发生后连续2 个月无出货,则强制结案,后续出货依正常检验执行。 6.4 作业品质异常
6.4.1 符合4.1 中d、e、f 任一项,作业品质异常成立。 6.4.2 相关单位发现作业品质异常后,立即通知责任单位改善。
6.4.3 针对重复发生作业品质异常未达到有效改善时,可开立《品质异常反馈单》,由品质统一编号后,交责任单位提出整改措施。
6.4.4 责任单位需于收到《品质异常反馈单》48小时内给出整改措施,回复反馈到单位。
6.4.5 异常单回复后,由品质统一归档整理/追踪。
6.4.6 针对不良产品可分析出根本原因,在品质异常反馈单上直接回复原因分析并转交给责任单位回复改善及预防措施;如不能分析出根本原因,将不良实物与品质异常反馈单转交工程部人员协助分析原因。
第20篇:变压器异常声响报告
20MW光伏电站
SVG变压器异常声响检查报告
一、SVG变压器异常声响前的运行方式
20mw光伏电站
(1)35Kv#1进线3
511、35Kv#2进线3
512、35Kv#3进线3513的高压断路器和高压隔离开关在合位,接地倒闸在分位;
(2)35Kv无功补偿351T1的高压断路器和高压隔离开关在合位,接地倒闸在分位;
(3)35Kv接地变351SB的高压断路器和高压隔离开关在合位,接地倒闸在分位;
(4)35KvPT351Y在合位
(5)35Kv WCD一线3515的高压断路器和高压隔离开关在合位,接地倒闸在分位;
二、SVG变压器异常声响发现的经过
2016年5月15号早上在巡视检查光伏电站设备时,发现SVG变压器异常声响,并且有3-4秒的挡挡声音,一个小时内发生了4回,巡检人员立即通知值班人员,对其分析后不能确定具体声源位置,需要停电检查并报告上层领导,及时与厂家联系缝隙故障原因。
三、SVG变压器异常声响原因分析 变压器正常运行时,应发出均匀的“嗡嗡”声,这是由于交流电通过变压器线圈时产生的电磁力吸引硅钢片及变压器自身的振动而发出的响声。如果产生不均匀或其它异音,都属不正常的。
1、变压器声音比平时增大,声音均匀,可能有以下原因: (1)电网发生过电压。电网发生单相接地或产生谐振过电压时,都会使变压器的声音增大,出现这种情况时,可结合电压表计的指示进行综合判断。
(2)变压器过负荷时,将会使变压器发出沉重的“嗡嗡”声,若发现变压器的负荷超过允许的正常过负荷值时,应根据现场规程的规定降低变压器负荷。
2、变压器有杂音
有可能是由于变压器上的某些零部件松动而引起的振动。如果伴有变压器声音明显增大,且电流电压无明显异常时,则可能是内部夹件或压紧铁芯的螺钉松动,使硅钢片振动增大所造成的。
3、变压器有放电声
变压器有“劈啪”的放电声,若在夜间或阴雨天气下,看到变压器套管附近有蓝色的电晕或火花,则说明瓷件污秽严重或设备线卡接触不良。若是变压器内部放电则是不接地的部件静电放电或线圈匝间放电,或由于分接开关接触不良放电,这时应对变压器作进一步检测或停用。
4、变压器有爆裂声
说明变压器内部或表面绝缘击穿,应立即将变压器停用检查。
5、变压器有水沸腾声
变压器有水沸腾声,且温度急剧变化,油位升高,则应判断为变压器绕组发生短路或分接开关接触不良引起的严重过热,应立即将变压器停用检查。
对上述几种可能进行逐一排查,无过流过压,过负荷,无放电声,无短路故障,所以电站人员认为是外部或者内部部件的松动,导致震动或者碰撞。
四、SVG变压器异常声响的处理
加强巡视,观察有无扩大,监控参数,并做出检修计划上报领导。
2016.5.16
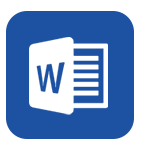