PCB开路的原因及改善
PCB线路开、短路是各PCB生产厂家几乎每天都会遇到的问题,一直困扰着生产、品质管理人员,造成出货数量不足而补料,影响准时交货,导致客户抱怨,是业内人士比较难解决的问题。本人在PCB制造行业已经有20多年的工作经历,主要从事生产管理、品质管理、工艺管理和成本控制等方面的工作。对于PCB开、短路问题的改善积累了一些经验,现形成文字以作总结,提供同行们讨论,并期待对于管理生产、品质的同行们能够作为参考之用。
我们首先将造成PCB开路的主要原因总结归类为以下几个方面(鱼骨图分析):
现将造成以上现象的原因分析和改善方法分类列举如下:
一、露基材造成的开路:
1、覆铜板进库前就有划伤现象;
2、覆铜板在开料过程中的被划伤;
3、覆铜板在钻孔时被钻咀划伤;
4、覆铜板在转运过程中被划伤;
5、沉铜后堆放板时因操作不当导致表面铜箔被碰伤;
6、生产板在过水平机时表面铜箔被划伤; 改善方法:
1、覆铜板在进库前IQC一定要进行抽检,检查板面是否有划伤露基材现象,如有应及时与供应商联系,根据实际情况,作出恰当的处理。
2、覆铜板在开料过程中被划伤,主要原因是开料机台面有硬质利器物存在,开料时覆铜板与利器物磨擦而造成铜箔划伤形成露基材的现象,因此开料前必须认真清洁台面,确保台面光滑无硬质利器物存在。
3、覆铜板在钻孔时被钻咀划伤,主要原因是主轴夹咀被磨损,或夹咀内有杂物没有清洁干净,抓钻咀时抓不牢,钻咀没有上到顶部,比设置的钻咀长度稍长,钻孔时抬起的高度不够,机床移动时钻咀尖划伤铜箔而形成露基材的现象。
a、可以通过抓刀记录的次数或根据夹咀的磨损程度,进行更换夹咀;
b、按作业规程定期清洁夹咀,确保夹咀内无杂物。
4、板材在转运过程中被划伤:
a、搬运时搬运人员一次性提起的板量过多、重量太重,板在搬运时不是抬起,而是顺势拖起,造成板角和板面摩擦而划伤板面;
b、放下板时因没有放整齐,为了重新整理好而用力去推板,造成板与板之间摩擦而划伤板面;
5、沉铜后、全板电镀后堆放板时因操作不当被划伤:沉铜后、全板电镀后储存板时,由于板叠在一起再放下,板有一定数量时,重量也不轻,板角向下且加上有一个重力加速度,形成一股强大的冲击力撞击在板面上,造成板面划伤露基材。
6、生产板在过水平机时被划伤:
a、磨板机的挡板有时会接触到板面上,且挡板边缘又不平整有利器物凸起,过板时板面被划伤;
b、不锈钢传动轴,因损伤成尖状物体,过板时划伤铜面而露基材。
综上所述,对于在沉铜以后的划伤露基材现象,如果在线路上是以开路或线路缺口的形式表现出来,容易判断;如果是在沉铜前出现的划伤露基材,又是在线路上时,经沉铜后又沉上了一层铜,线条的铜箔厚度明显减小,后面开、短路测试时是难于检测出来的,这样客户使用时可能会因耐不住过大的电流而造成线路被烧断,潜在的质量问题和所导致的经济损失是相当大的。
二、无孔化开路:
1、沉铜无孔化;
2、孔内有油造成无孔化;
3、微蚀过度造成无孔化;
4、电镀不良造成无孔化;
5、钻咀烧孔或粉尘堵孔造成无孔化; 改善措施:
1、沉铜无孔化:
a、整孔剂造成的无孔化:是因整孔剂的化学浓度不平衡或失效,整孔剂的作用是调整孔壁上绝缘基材的电性,以利于后续吸附钯离子,确保化学铜覆盖完全,如果整孔剂的化学浓度不平衡或失效,会导致无孔化。
b、活化剂:主要成份是pd、有机酸、亚锡离子及氯化物。孔壁要有金属钯均匀沉积上,就必须要控制好各方面的参数符合要求,以我们现用的活化剂为例:
① 温度控制在35-44℃,温度低了造成钯沉积上去的密度不够,造成化学铜覆盖不完全;温度高了因反应过快,材料成本增加。
②、浓度比色控制在80%--100%,如果浓度低了造成钯沉积上去的密度不够, 化学铜覆盖不完全;浓度高了因反应过快,材料成本增加。
③ 在生产过程中要维护好活化剂的溶液,如果污染程度较严重,会造成孔壁沉积的钯不致密,导致后续化学铜覆盖不完全。
c、加速剂:主要成份是有机酸,是用以去除孔壁吸附的亚锡和氯离子化合物,露出后续反应的催化金属钯。我们现在用的加速剂,化学浓度控制在0.35-0.50N,如果浓度高了把金属钯都去掉了,导致后续化学铜覆盖不完全。如果浓度低了,去除孔壁吸附的亚锡和氯离子化合物效果不良,导致后续化学铜覆盖不完全。
d、化学铜参数的控制是关系到化学铜覆盖好坏的关键,以我司目前所使用的药水参数为例:
① 温度控制在25--32℃,温度低了药液活性不好,造成无孔化;如果温度超过38℃时,因药液反应快,铜离子释出也快,造成板面铜粒而返工甚至报废,这样沉铜药液要立即进行过滤,否则药液有可能造成报废。
② Cu2+控制在1.5—3.0g/L,Cu2+含量低了药液活性不好,造成孔化不良;
如果浓度超过3.5g/L时,因药液反应快,铜离子释出也快,造成板面铜粒而返工甚至报废,这样沉铜药液要立即进行过滤,否则药液有可能造成报废。Cu2+控制主要通过添加沉铜A液进行控制。
③ NaOH控制在10.5—13.0g/L为宜,NaOH含量低了药液活性不好,造成孔化不良。NaOH控制主要通过添加沉铜B液进行控制,B液内含有药液的稳定剂,正常情况下A液和B液是1:1进行补充添加的。 ④ HCHO控制在4.0—8.0g/L,HCHO含量低了药液活性不好,造成孔化不良,如果浓度超过8.0g/L时,因药液反应快,铜离子释出也快,造成板面铜粒而返工甚至报废,这样沉铜药液要立即进行过滤,否则药液有可能造成报废。HCHO控制主要通过添加沉铜C液进行控制,A液内也含有HCHO的药液成分,所以添加HCHO时,先要计算好补充A液时的HCHO浓度升高量。
⑤ 沉铜的负载量控制在0.15—0.25ft2/L,负载量低了药液活性不好,造成孔化不良;如果负载量超过0.25ft2/L时,因药液反应快,铜离子释出也快,造成板面铜粒而返工甚至报废,这样沉铜药液要立即进行过滤,否则药液有可能造成报废。生产时第一缸板必须要用铜板进行拖缸,使沉铜药液的活性激活起来,便于后续沉铜产品的反应,确保孔内化学铜的致密度和提高覆盖率。
建议:为了达到以上各项参数的平衡和稳定,沉铜缸添加A、B液,应配置一台自动加料机,以更好地控制各项化学成份;同时温度也采用自动控制装置使沉铜线溶液的温度处于受控状态。
2、孔内残留有湿膜油造成无孔化:
a、丝印湿膜时印一块板刮一次网底,确保网底没有堆油现象存在,正常情况下就不会孔内有残留湿膜油的现象。
b、丝印湿膜时使用的是68—77T网版,如果用错了网版,如≤51T时,孔内有可能漏入湿膜油,显影时孔内的油有可能显影不干净,电镀时就会镀不上金属层而造成无孔化。如果网目高了,有可能因油墨厚度不够,在电镀时抗镀膜被电流击破,造成电路间很多金属点甚至导致短路。
3、粗化过度造成无孔化:
a、线路前如果是采用化学粗化板面的话,对粗化溶液的温度、浓度、粗化时间等参数要控制好,否则有可能因板镀孔铜厚度薄,无法承受粗化液的溶铜力而造成无孔化。
b、为了加强镀层和基铜的结合力,电镀前处理都要经过化学粗化后再电镀,所以对粗化溶液的温度、浓度、粗化时间等参数要控制好,否则也有可能造成无孔化问题。
4、电镀无孔化:
a、电镀时厚径比较大(≥5:1)时孔内有气泡,是因为振动力不足,无法使孔内的空气逸出,无法实现离子交换,使得孔内没有镀上铜/锡,蚀刻时把孔内的铜蚀掉而造成无孔化。
b、厚径比较大(≥5:1),电镀前处理时由于孔内有氧化现象没有清除干净,电镀时会出现抗镀现象,没有镀上铜/锡或镀上去的铜/锡很薄,蚀刻时起不到抗蚀效果导致把孔内的铜蚀掉而造成无孔化。
5、钻咀烧孔或粉尘堵孔无孔化:
a、钻孔时钻咀使用寿命没有设置好,或者使用的钻咀磨损较严重,如缺口、不锋利,钻孔时磨擦力太大而发热,造成孔壁烧焦无法覆盖化学铜而造成无孔化。
b、吸尘机的吸力不够大,或者工程优化时没有做好,钻孔时孔内有粉尘堵塞,在化学铜时没有沉上铜而造成无孔化。
三、线路有“胶”开路(各类胶纸上的“胶”容易脱落或粘网胶溶解后形成“胶”):
1、水平机传动辘上有“胶”粘到板面线路上造成开路;
2、放板台面上有“胶”粘到板面线路上造成开路;
3、粘网胶溶解在湿膜中涂覆在板面线路上造成开路;
4、用胶纸封网时,胶纸上的“胶”溶解在湿膜中,然后涂覆在板面线路上时造成开路; 改善方法:
1、水平机传动辘上有“胶”粘到板面线路上造成开路:
a、生产单面板时板面上有“胶”未清理干净,过水平磨板机时粘在传动辘上,后续过板时板面线路位置正好粘上胶,电镀时抗镀,蚀刻时蚀掉线路而造成开路。
b、生产金手指板时板面上贴着抗电镀的蓝胶,由于未贴紧使其在过水平磨板机时脱落,粘在传动辘上,蓝胶长时间高温下变成胶状,在后续过板时板面线路位置正好粘上胶迹,电镀时抗镀,蚀刻时蚀掉线路而造成开路。
2、放板台面上有“胶”粘到板面线路上造成开路: 磨板机后面接板台、丝印台、对位台、显影机后面的接板台、线路质检台、非金属化孔塞孔台等,这些要放置生产板的台面上有“胶”时,生产板放置台面上时线路上就有可能粘上“胶”,电镀时抗镀,蚀刻时蚀掉线路而造成开路。
3、粘网胶溶解在湿膜中涂覆在板面线路上造成开路:
a、粘网胶粘网版时不要把粘网胶粘在网版内,虽然在丝印区外,但因印制每一次板时必须刮一次网底油墨,这样在网版内的粘网胶多次被刮的情况下,粘网胶被溶在油墨中,然后被印在板面的线路上,在电镀时抗镀,蚀刻时线路被蚀掉而造成开路。
b、因在印制每一次板时都必须刮一次网底油墨,在靠近操作人员一边的网框封胶处用一块覆铜板的绝缘板封住,这样在靠近操作员一边的网框上的粘网胶就不会被刮到,避免粘网胶被溶在油墨中,从而避免电镀时抗镀,蚀刻时蚀掉线路形成开路。
4、用胶纸封网时,胶纸上的胶溶解在湿膜中,然后被涂覆在板面线路上时造成开路:
网印时规定不得使用胶纸封网印制,只能根据板的大小进行晒网生产,从而避免了胶纸封网时,胶纸上的胶溶解在湿膜中,然后涂覆在板面线路上时造成开路。
四、固定位开路:
1、对位菲林线路上划伤造成开路;
2、对位菲林线路上有沙眼造成开路;。 改善方法:
1、对位菲林线路上划伤造成开路,菲林药膜面与板面或垃圾磨擦而划伤膜面线路,造成透光,在显影后菲林划伤处的线路还被油墨盖住,造成电镀时抗镀,蚀刻时线路被蚀掉而开路。
2、对位时菲林药膜面线路上有沙眼,显影后菲林沙眼处的线路还被油墨盖住,造成电镀时抗镀,蚀刻时线路被蚀掉而开路。
五、显影不净开路:
1、曝光强度过大造成显影不净而开路;
2、板面上有垃圾曝光前赶气不良造成显影不净而开路;
3、显影药水失效导致显影不净而形成开路;
4、板面划痕过深导致显影不净而形成开路;
5、干膜起泡导致显影不净而形成开路; 改善方法:
1、曝光强度过大造成显影不净而开路,曝光时由于点光源是散射曝光的,油墨有一定的厚度,光通过折射的感光区域大于或等于线宽时,线路被油墨封盖住,显影不出来,电镀时抗镀,在退膜蚀刻后形成断线。
2、板面上有垃圾如干膜碎、碎胶带、铜屑等造成赶气不好导致显影不净而出现开路现象,这些垃圾都有一定高度,吸气时赶气不好,垃圾周围形成虚光区,显影时虚光区显影不净,电镀时抗镀退膜蚀刻后形成断线。
3、显影药水失效导致显影不净而形成开路。显影药水浓度过低或显影药水过板量过多,显影速度大快等,达不到理想的显影效果,线路表面还有一层有机物附着,在电镀时抗镀,退膜蚀刻后而断路。
4、板面划痕过深导致显影不净形成开路,指贴膜前处理没有去除铜面划痕(或是机械磨刷板过重),划痕有一定的深度,划痕四周铜皮外翻并有一定高度。贴膜时在一定压力下划痕处干膜会裂开,且划痕处高于板面的铜皮会在划痕周围形成虚光区,以致曝光后形成余胶,显影时线路显影不出来,线路表面还有一层余胶附着,在电镀时抗镀,退膜蚀刻后而断路。
5、干膜起泡形成开路:
a、贴干膜过程中,由于温度过高,贴膜压力过低或滚辘表面有损伤,容易出现干膜起泡的现象。
b、对位过程中,由于对位偏操作员重新提起菲林再对位,导致薄膜有鼓起现象。
以上的起泡部位以及周围区域在曝光过程中形成虚光区,使线路曝光不良,造成线路幼线甚至开路。
六、抗镀开路:
1、显影时干膜碎附着线路上造成开路;
2、线路表面附着有油墨造成开路; 改善方法:
1、干膜碎附着线路上造成开路:
a、菲林边或者菲林上的“钻孔尾孔”、“丝印孔”没有用挡光胶纸完全封好,曝光时板边缘该处的干膜被光固化死,显影时变成为干膜碎块,掉在显影液或水洗缸里,后续过板时干膜碎块附着板面线路上,在电镀时抗镀,在退膜蚀刻后形成开路。
b、用干膜掩孔的非金属化孔,在显影时由于压力过大或附着力不够,把孔内的掩孔干膜冲破成碎片,掉在显影液或水洗缸里,后续过板时干膜碎块附着线路上,在电镀时抗镀,在退膜蚀刻后形成开路。
2、线路表面附着有油墨造成开路,主要原因是油墨没有预烤干或显影液的油墨量过多时,油墨附在板面上,然后又粘在后面的传动轴上或海棉吸水辘上,后续过板时附着在线路上,在电镀时抗镀,退膜蚀刻后形成开路。
七、锡薄开路:
1、电镀锡镀层亮边开路;
2、酸水溶锡后造成开路; 改善方法:
1、电镀锡镀层亮边开路:
a、抗镀膜的有机溶剂过高、锡光剂和油墨有机溶剂不兼容,造成电镀锡时亮边,即锡薄,退膜蚀刻后形成开路。
b、电镀锡缸的阳极棒不足,各化学成分不平衡,如硫酸亚锡过低,硫酸含量过低,光剂含量大低等等,造成电镀锡时亮边,即锡薄,退膜蚀刻后形成开路。
2、酸水溶锡后造成开路:
a、锡缸后水洗缸的酸浓度过高,在水洗时摇摆力度不够,孔内溶液的酸浓度较高,到退膜蚀刻前停留时间又过长,酸溶液会溶锡,造成锡薄甚至露铜,退膜蚀刻后形成开路。
b、板在电镀锡后,由于放置的地方地面上有含酸溶液,员工在经过时踩踏到酸溶液而溅到板面线路上,酸溶液溶锡,造成锡薄甚至露铜,退膜蚀刻后形成开路。
八、划伤开路:
主要原因是电镀锡后,员工操作不认真,板与板之间碰撞,造成线路上的锡面被划伤,如果深度较深到接近露铜或露铜时,在退膜蚀刻后形成开路。出现的地方主要是:
1、下板时多块板层叠在一起,插架逐块分开时,板与板之间的磨擦。
2、退膜后插板时,不留意造成板角碰伤线路锡面。
3、退膜后放入蚀刻机时,不留意造成板角碰伤线路锡面。
4、退膜后先烘干然后再蚀刻时,板转运或搬动过程中稍为不留意,就造成板角碰伤线路锡面。
九、撞断线开路:
主要原因是蚀刻后,员工操作不认真,烘干接板时接不过来,板角撞到前面板的线路上,有时甚至前面的板堆起来,后面出来的板以推移的力,使前面堆起来的板相互摩擦而造成开路。出现的地方主要是蚀刻机、退锡机、阻焊磨板机等机器后面的接板员接板接不过来,或预先没有准备好插板架,转换插板架时转换的时间长,后面的板紧跟着又出来了撞到前面板的线路上。
结论:我们通过上面的各种改善方法后,PCB开路问题得到了有效的改善,特别是露基材开路、无孔化开路、线路有胶开路、抗镀开路、锡薄开路等问题已得到有效的控制,当然,其它开路的问题还有待于提高整体管理水平、员工的操作技能、环境清洁度、工艺能力等才能得到更进一步的改善。
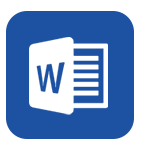