推荐第1篇:PCB心得体会
心得体会
经过一段时间的学习对PCB有一定的了解,这还少不了老师的指导。让我走了很少的弯路。中间遇到的问题有老师和同学的帮助。也是很有乐趣的
我没有用来做实际的产品设计,所以,对该软件的理解也很有限。介于自身的原因,感觉对PCB设计的领悟还不够深刻。首先,布局的合理程度直接影响布线的成功率,往往在布线过程中还需要对布局作适当的调整。由于做的是双层走线所以需要考虑横向纵向问题,还有美观等问题。接下来,PCB尺寸大小,尽可能即小又合理。布线,尽量避免绕线,直角等问题。
推荐第2篇:PCB心得体会
PCB心得体会
----学生:郭利伟
我是自动化专业的学生,由于PCB设计与我本专业联系比较紧密,所以选择了这门选修课。在老师的精心指导下,我对PCB设计这门课有了基本的认识。
PCB设计是指印制电路板设计。印制电路板的设计是以电路原理图为根据,实现电路设计者所需要的功能。印刷电路板的设计主要指版图设计,需要考虑外部连接的布局、内部电子元件的优化布局、金属连线和通孔的优化布局、电磁保护、热耗散等各种因素。简单的版图设计可以用手工实现,优秀的版图设计可以节约生产成本,达到良好的电路性能和散热性能。Altium Designer是一款在国内外享有盛名的PCB辅助设计软件。它集成PCB设计系统、电路仿真系统、PCB设计系统和FPGA设计系统于一体,可以实现从芯片级到PCB级的全套电路设计,大大方便了设计人员。而我们用的便是这款软件。下面我谈一下对这门课一点肤浅的认识。 一.电气连接的准确性
印制板设计时,应使用电原理图所规定的元器件,印制导线的连接关系应与电原理图导线连接关系相一致,印制板和电原理图上元件序号应一一对应。 二.可靠性和安全性
印制板电路设计应符合电磁兼容和电器安规及其余相关要求。 三.工艺性 印制板电路设计时,应考虑印制板制造工艺和电控装配工艺的要求,尽可能有利于制造、装配和维修,降低焊接不良率。 四.经济性
印制板电路设计在满足使用的安全性和可靠性要求的前提下,应充分考虑其设计方法、选择的基材、制造工艺等,力求经济实用,成本最低。
作为自动化专业的学生,PCB设计这门课是必要的技能。我也报名参加了飞思卡尔智能车比赛,这是检验学习成果的机会。同时在寒假,我应该继续学习这方面的知识,增长自己的能力,为将来奠定一个良好的基础。
最后感谢老师对我的讲授与指导,祝您工作顺利,生活美满。
推荐第3篇:PCB制版心得体会
PCB制板实训课程心得体会
在本学期PCB制板实训过程中,通过我们不断地努力和老师耐心的帮助,我们掌握了PCB制板的具体流程,同时,我们也在其中收获到了很多东西,比如动手能力和应变能力等。我们在已有的的理论基础上去展示我们的实践操作能力,我觉得这是一个提升动手能力的机会。
以前每次都是听老师在课堂上讲绘制PCB和制作PCB板的过程,是纯粹的理论,看了书上的理论知识,感觉只是对PCB有了一点了解,通过本学期的实际制板,我们深刻意识到理论与实践相结合的重要性。通过这学期对PCB制板课的进一步学习,真正的掌握了PCB制板的技能,并且顺利完成了对“51单片机最小系统”和“多谐振荡电路”的设计与制作。
虽然课程已经结束,但并不意味着我们要停止对它的学习,学好PCB制板对我以后的专业发展肯定受益匪浅。所以在以后的时间里,我将不断地对PCB制板进行深入的学习,并打算在下学期能够独立完成复杂双面板的制作。
以上为我对PCB制板这门课程的一些感想,和我对这门课以后学习的一个简单的计划。
2013年12月18日
冯旭彪
推荐第4篇:PCB制板心得体会
PCB制板心得体会
在本学期的电路制图与制板实训中,我结合上学期学到的理论知识,通过Altium Designer 画图软件(dxp.exe)自己动手:画原理图(电子彩灯、单片机最小系统)——导入PCB——制版,在学习制板的过
程中遇到了一系列问题,通过查找资料、问老师、百度,然后一一解决,以下是我在学习当中遇到的一些问题,解决办法及一些心得体会:
(1) 为使原理图美观,将相隔较远的两端连起来时,可用网络标号。
(2) 在原理图中给组件取名字时,A、B、C、D不能作为区分的标准。如:给四个焊盘取名JP1A、JP1B、JP1C、JP1D,结果在生成PCB时只有一个焊盘,如果把名字改为JP1A、JP2B、JP3C、JP4D、在PCB中就有四个焊盘。
(3) 在PCB中手动布线时,如果两个端点怎么
也连不上,则很可能是原理图中这两个端点没有连在一起。
(4) 自己画PCB封装时,一定要和原理图相一致,特别是有极性的组件。一定要与实际的组件相一致,特别是周边的黄线,是
3D
图的丝印层,即最终给组件留的空间。如:二极管、电解电容。 5) 手动布线更加灵活,通过 Design-----Rules,弹出对话框,可以设置电源线、地线的粗细。 (6) PCB自动布线时,先进行设置:线间距12mil 电源、地线宽度30mil 其他线宽 16mil。
(7) PCB图中如果组件变为警告色“绿色”,有(可能是组件之间靠得太近了,也有可能是封装不对,如:POWER的两个焊盘
10、11。如果内孔直径为110mil,则这两个焊盘变为绿色,只要把内孔直径改为100 mil,则正常了。
(8) 将几个焊盘交错的放置,则可以得到椭圆形的焊孔。
(9) 在原理图中,双击组件,不仅可以看到此组件的封装,还可以修改原件的封装,当然前提是封装已经存在。
(10) 在画封装图时,最好不要在封装图上写标注,否则,此标注将和封装连为一个整体,布线时,线不能通过此标注,给布线带来了麻烦,其实在中可以对组件标注。
(11) 在
PcbDoc
Schlib中画好图后,一定要修改名字,不能为默认的“*”,否则不能Update到PcbDoc中。
(12)可以通过把线加粗到一定程度,达到实心图的效果。如:按键的实心圆、发光二极管的实心三角形。 (13) 手动布线的时候,线只能有三种走法:水平的、垂直的、135度斜线的。
(14) 通过这次作业,终于弄清楚了后在给它画封装,还是很有意思的。
(15)开始应该先做好准备工作。第一步,把要用到的元器件的图形,不管是自己亲手画的,还是调用别人的,都统一放到自己建立的
DXP
的大致功能,发现画图很好玩,特别是自己画一个元器件,然
Sch.Lib中,这样用起来就不用到到处找了。第二步,给每一个元器件封装,同样不管是自己亲手画的,还是调用别人的,都统一放到自己建PCB.Lib中。在这个过程中有几个细节问题不能忽视,比如,在Sch.Lib中引脚的序号 Designator非常重要,它与PCB.Lib封装中的焊盘序号是一一对应的,在Sch.Lib中引脚的名称Display Name只是描绘这个引脚的功能而已,可有可无。在Sch.Lib对话框Library Component Properties中,Designator的内容显示在Sch.Doc中的标号,是可以单独移动的,Library Ref 的内容显示在Sch.Lib中的标号。当然,在Sch.Lib中图形必须要放在中心。在PCB.Lib中画封装时也必须要把封装画在中心,重立的点是尺寸问题,必须与实际的尺寸一致,通常,焊盘间距100mil,芯片两侧对称的焊盘间距为300mil。丝印层(黄线)图形代表的是元器件焊在板子上时所占用的空间大小。
(16) 原理图的绘制,最好是每个功能模块单独画,从库里调出元器件后,应该给它取个名字,在Designator中给它命名,如果是芯片就写上芯片的名字,不要用U1,U2等来标注,那样很容易弄混,出现重名的情况,重名的后果是只有一个导入到PCB中,用芯片的名字命名的另一个好处是,如果有错误可以直接找到芯片。网络标号必须写在引脚上,则无效。
(17) 由原理图导入到
wire线上,如果偷懒放在
PCB有时候很难一次成功,遇到的问题可能是由于原理图与封装没有很好的对应。比如:有时候引脚序号需要隐藏,就可能忽视了引脚序号,结果是引脚序号并不是所要求的,当然与焊盘上的序号无法对应起来;原理图中不同封装的元器件重名也会报错。只要保证每一个元器件的封装都是对的(元器件多了,就需要细心仔细了),最后都能导入到
PCB。
PCB(18)重头戏就在PCB中了。首先说一下在只要在原理图中修改好了,在中修改的问题,如果发现线连错了,就是原理图的问题,
PCB
中
Import changes from即可。如果发现要更换封装,可以在PCB.Lib中修改封装后Update with PCB即可,也可以在原理图中重新给元器件封装,然后在PCB中Import changes from即可(这种方法可能更好)。再说一下在PCB
中元器件的摆放问题,首先摆放有特定位置要求的元器件,需要手动操作的元器件都应该放在板子的边缘,比如:电源、串口、按键、排针等,能显示的元器件如数码管也要放在板子的最上面,便于观察;再摆放主要的芯片,然后把每个芯片电路的电容电阻都放在这个芯片的周围(要对照原理图来找电容电阻),对各个芯片电路进行合理摆放,要求尽量是直线式的走线,没有交错的走线;最后就是布线的问题,先自动布线看一下效果,如果元器件摆放的合理,自动布线的效果非常好,然后进行DRC检测,有时候是走线有问题,(走线变绿)撤销变绿的布线,手动给它布线,遵从顶层走横线,底层走纵线的原则。有时候是焊盘大小的问题,将焊孔改小一点就好了。 (19) PCB
布线完成后,接下来就是制板了,制
Altium Designer生成的PCB,在制板时要另存为PCB 4.0 Binary File(*.pcb),打开时要用protel99打开。 (20) 新建Gerber文件时要注意设置属性。 (21) PCB打孔完毕后,接着进行以下步骤:放入曝光机——抽真空——曝光(100s)——显影()——版过程中也有许多的学问,由于我们是使用蚀刻——冲洗——显影——冲洗——干燥;注意:如果布线密集时要适量增加曝光时间。
(22) 动手做之前以为很简单的,无非就是元器件多了,原理图复杂了,元器件摆放要讲究一些,虽然很多细节问题都知道了,但是还是犯了错,软件还是要多用,养成良好的习惯后,就不会再犯这样或那样的细节错误了。最欣慰的是在元器件的摆放问题上有了深刻的见解,这一次因为元器件摆放得合理,在布线这一环节走得很顺利,基本上是自动布线,只是稍微修改了一根线和一个焊盘的大小。好像越是复杂的电路,就越是能发挥出自动布线的优势,在自动布线的基础上进行手动布线,效果非常好!
PCB制板心得体会
学院:物信学院 班级:11级电信(2)班姓名:张 文 瑞
学号:20111060238 时间:2013.12.18
推荐第5篇:制作PCB的心得体会
天水师范学院
——PCB实验设计心得
学院:物理与信息科学学院
专业:电子信息科学与技术
班级:11电信(2)班
姓名:赵鹏举
学号:20111060241
制作PCB的心得体会
学习了一学期的PCB制版,我有很多的心得体会,在整个制版过程中,可以在Altium Designer6.9之下进行,也可以在DXP 2004下进行,但两者之间要关联的文件,可在打工软件后,在菜单栏DXP---属性preferences---system—file type将文件类型与该软件进行关联,以后就可双击文件而利用这个Altium Designer 6.9 打开那个文件。常用的要关联的文件有工程文件project, 原理图文件sch,当然还有PCB文件。
先新建原理图(sch图),再新建PCB图。还要建个SCH.lib和PCB.lib。 Sch.lib用来画库里找不到的元件,PCB.lib用来为该元件创建封装(先用游标卡尺量好尺寸),再将这个封装给了SCH.lib里新建的元件,这样就可以了。若要新建第二个元件,则TOOL-New Component,然后画矩形,放管脚。放管脚Pin时,Display name 要在矩形框内部,风络标识Designator 要在矩形框外部。还有在PCB.lib里画元件封装时一定要注意,将封装画在坐标的(0,0)点,否则将原理图导入PCB后,拖动元件时,会产生鼠标指针跑到别的地方去的现象。原理图上的连线,可以用线直接连,也可以用net网络标识。在建好原理图之后,要先导出所需元件的清单(reports---Bill of materials),里面的模板Template要空着,file format先.xls,然后点Export就可以保存了。建好原理图后,要进行编译,Project---compile schdoc.,若没弹出meage窗口,则需手动去右
下角system,,打开meages对话框,查看文件中的错误,对警告warnings 要进行检查,然后再导入PCB中。Design---updata PCB Document(第一个),就可将原理图导入到PCB中。
一次性修改多个元件的某项属性,可以按shift一个一个的选,也可以选中一个后右键,find similar objects ,然后在PCB Inspector中进行统一修改即可。如果要改变放置的过孔的大小,则步骤为:Tool—属性Preference—PCB Editor—Default—选择过孔Via,再点Edit Value更改后OK即可。
PCB图是实际要制作的电路板。Q键是PCB中mm和mil之间的转换。Ctrl+m是测量距离,P+V是放置过孔,Z+A是观看整图等常用操作。过孔是上下两层之间连接改线使用的,焊盘是用来焊接元件的。过孔大小Hole size==22mil , 直径Diameter==40mil较为好看且实用。
将所有器件布局好后。进行连线前,先要设置好线的粗细。比如12V电源线最好用30mil,信号线用12mil,需要线宽大约是1.5到2mm等。线宽与电流是有对应关系的。
布线前,要先设置好要布的各种线的宽度,如VCC和GND的线宽和信号NET的线宽。
(步骤:先选设计(D)—规则(R)—Design Rout,选电气规则(Electrical),将其线间距在右边窗口中设置为12mil,放入右边的窗口中,然后点应用;再Design---Rule Wizard---Routing中选择网络,在这个栏中将线宽的Name改一下,命名为VCC或GND,将其
线宽width constraint设置为30mil,后选width,将其线宽设置为12mil,然后点击应用,接着选择Routing Layers,在右边窗口中设置为Bottom Layer,然后选择Hole size,在右边窗口中将其最大值设置为2.54mm,最后点击确定(OK)。然后再设定优先级Priorities,然后要点Apply,最后OK即可。)
PCB中如果要改某个元件的封装,不用回到原理图,直接从PCB.lib中拖出所需封装即,(如果没有,则需要自己画),然后双击封装上的某个焊盘,将网络标识Designator改成需要连接的网络标识,就可完成对应,然后可进行连线。若是现有网络中不存在的网络标识,则需要在Design---Net list—Edit Nets中先All Nets后在第二栏中出现了现有网络中所有的Net,点Add,将Net Name就可添加上所想要的网络标识。然后再双击焊盘,就有了这个新的标识。
画好PCB图之后,要进行检查。首先要Project—Compile PCBDOC,从system中调出meage窗口进行错误检查。然后还要进行Tool—Design Rule Check(DRC)检查,查看是否有Rule上的错误。
线与焊盘之间的最小间距在Design—Rule----Clearance中进行设置。PCB制作的后期进行覆铜时,要想加大覆铜与焊盘之间的距,一般应大于20mil,应先将Design---Rule---Clearance中,最小安全间距改为20mil,然后PCB上很多元件变绿了,不用管,对要覆铜的区域进行覆铜,Place Polygon Plane(多边形面板),填覆铜区域的名字,可不填,覆铜所连接的网络,顶层还是底层,去除死铜(连不到GND的覆铜起不到降低电磁干扰的作用),覆盖所有相同名的网
络Pour over all same net,然后OK后会出现十字标,画出所需的覆铜区域就完成了覆铜的操作.覆好铜后,再将Design—Rule中的规则改回来即可。
PCB制作的最后,要将焊盘与连线之间加上泪滴,以避免连线与焊盘之间接触不良。步骤是Tool—Teardrop,选择all pad, all via即可,若有部分焊盘或过孔未加上泪滴,是因为连线未接到焊盘的正中间,重新连线,再重新添加即可解决。板子的最后,要加四个内径3.1mm,外径5.5mm的大过孔来固定板子,如果过孔变绿了,则需要改下design—rule—routing—routing via中过孔大小的规则,若还是绿色,则需要再改design—rule—manufacturing—Hole size,即可不为绿色。最后将四个孔对齐。还可右键鼠标,选option—选mechanical layer,去掉PCB上的keep out layer和multilayer,使PCB界面更清晰。在PCB上右键—option—Board option—visible grid中将line改为dots,有利于看清连线。
最后将其PCB进行制版,在制版的过程中,先将PCB转化在Protues 99SE下,进行钻孔和打印,之后再进行曝光、显影、蚀刻,这就是整个制版过程。在此过程中,我们更加熟悉的掌握了制版的每一个细节,能够从中学习到很多很多的东西,为以后的学习打下坚实的结果。
推荐第6篇:制作PCB的心得体会
制作PCB的心得体会
(王志亮_哈尔滨工业大学_超精密光电仪器工程研究所) (所用软件 Altium Designer 6.6绿色版,免安装) 要关联的文件,可在打工软件后,在菜单栏DXP---属性preferences---system—file type将文件类型与该软件进行关联,以后就可双击文件而利用这个Altium Designer 6.6 打开那个文件。常用的要关联的文件有工程文件project, 原理图文件sch,当然还有PCB文件。
先新建原理图(sch图),再新建PCB图。还要建个SCH.LIB和PCB.LIB. Sch.lib用来画库里找不到的元件,PCB.lib用来为该元件创建封装(先用游标卡尺量好尺寸),再将这个封装给了SCH.LIB里新建的元件,这样就可以了。若要新建第二个元件,则TOOL-New Component.然后画矩形,放管脚。放管脚Pin时,Display name 要在矩形框内部,风络标识Designator 要在矩形框外部。还有在PCB.LIB里画元件封装时一定要注意,将封装画在坐标的(0,0)点,否则将原理图导入PCB后,拖动元件时,会产生鼠标指针跑到别提地方去的现象。
原理图上的连线,可以用线直接连,也可以用NET网络标识。在建好原理图之后,要先导出所需元件的清单(reports---Bill of materials),里面的模板Template要空着,file format先.xls(excell的后缀的那个),然后点Export就可以保存了。
建好原理图后,要进行编译,Project---compile schdoc.,若没弹出meage窗口,则需手动去右下角system,,打开meages对话框,查看文件中的错误,对警告warnings 要进行检查,然后再导入PCB中。Design---updata PCB Document(第一个),就可将原理图导入到PCB中。 一次性修改多个元件的某项属性,可以按shift一个一个的选,也可以选中一个后右键,find similar objects ,然后在PCB Inspector中进行统一修改即可。如果要改变放置的过孔的大小,则步骤为:Tool—属性Preference—PCB Editor—Default—选择过孔Via,再点Edit Value更改后OK即可。
PCB图是实际要制作的电路板。Q键是PCB中mm和mil之间的转换。Ctrm+m是测量距离,P+V是放置过孔,Z+A是观看整图等常用操作。过孔是上下两层之间连接改线使用的,焊盘是用来焊接元件的。过孔大小Hole size==22mil , 直径Diameter==40mil较为好看且实用
。
将所有器件布局好后。进行连线前,先要设置好线的粗细。比如12V电源线最好用20mil,信号线用12mil,走2A电流,需要线宽大约是1.5到2mm等。线宽与电流是有对应关系的,如下:
布线前,要先设置好要布的各咱线的宽度,如12V的线宽和120V的线宽。
(步骤:先建类Design—claes—Net claes中右键—Add claes—右键Rename claes之后,在右边窗口中将要设置的线,如120V的线,放入右边的窗口中,然后close;-------再Design---Rule Wizard---Routing
中选线宽
width constraint----Next
后选Advanced---Next后选Belong to Net Claes, condition value中选刚建的那个,然后next,直到finish后自动打开Rule栏用来设置线宽,在这个栏中将线宽的
Name
改一下,然后Advanced---(InNetCla(\'com\'))(不好使时,改用NetClaes,在后面括号中填上’com’),然后在下面图示处设定好线宽后,再设定优先级Priorit,然后要点Apply,最后OK,即可,再画出的12V线就成了要求的线宽了。)
PCB中如果要改某个元件的封装,不用回到原理图,直接从PCB.LIB中拖出所需封装即,(如果没有,则需要自己画),然后双击封装上的某个焊盘,将网络标识Designator改成需要连接的网络标识,就可完成对应,然后可进行连线。若是现有网络中不存在的网络标识,则需要在Design---Netlist—Edit Nets中先AllNets后在第二栏中出现了现有网络中所有的Net,点Add,将NetName就可添加上所想要的网络标识。然后再双击焊盘,就有了这个新的标识。
画好PCB图之后,要进行检查。首先要Project—Compile PCBDOC,从system中调出meage窗口进行错误检查。然后还要进行Tool—Design Rule Check(DRC)检查,查看是否有Rule上的错误。
线与焊盘之间的最小间距在Design—Rule----Clearance中进行设置。PCB制作的后期进行覆铜时,要想加大覆铜与焊盘之间的距,一般应大于20mil,应先将Design---Rule---Clearance中,最小安全间距改为20mil,然后PCB上很多元件变绿了,不用管,对要覆铜的区域进行覆铜,Place Polygon Plane(多边形面板),填覆铜区域的名字,可不填,覆铜所连接的网络,顶层还是底层,去除死铜(连不到GND的覆铜起不到降低电磁干扰的作用),覆盖所有相同名的网络Pour over all same net,然后OK后会出现十字标,画出所需的覆铜区域就完成了覆铜的操作.覆好铜后,再将Design—Rule中的规则改回来即可。
PCB制作的最后,要将焊盘与连线之间加上泪滴,以避免连线与焊盘之间接触不良。步骤是Tool—Teardrop,选择all pad,all via即可,若有部分焊盘或过孔未加上泪滴,是因为连线未接到焊盘的正中间,重新连线,再重新添加即可解决。板子的最后,要加四个内径3.1mm,外径5.5mm的大过孔来固定板子,如果过孔变绿了,则需要改下design—rule—routing—routing via中过孔大小的规则,若还是绿色,则需要再改design—rule—manufacturing—Holesize,即可不为绿色。最后将四个孔对齐。还可右键鼠标,选option—选mechanical layer,去掉PCB上的keep out layer和multilayer,使PCB界面更清晰。在PCB上右键—option—Board option—visible grid中将line改为dots,有利于看清连线。将PCB图先打印出来,与实际元件大小对比好后,再送去制板,1:1打印是file—page setup—scale(比例)改为1.0即可。
画好的PCB检查没有错误后,就可以移交厂商来做了。
推荐第7篇:PCB实训心得体会(优秀)
jiu jiang university pcb制版实训报告
专 业: 电子信息工程技术
班 级: b1111 学 号: 21111060120 学生姓名: 指导教师: 实习时间: 2012-11-12至2012-11-16 实训地点: 电子信息实验楼 pcb制版实训
一、实习的意义、目的及作用与要求 1.目的: (1)了解pcb设计的流程,掌握pcb设计的一般设计方法。 (2)锻炼理论与实践相结合的能力。 (3)提高实际动手操作能力。 (4)学习团队合作,相互学习的方法。 2.要求:
(1)遵守实习纪律,注意实习安全。 (2)按时、按要求完成各项子任务。 (3)及时进行总结,书写实习报告。 (4)每人必须做一快pcb板。
3、意义:
(1)提高自身能力,完成学习任务。 (2)掌握一种cad软件的使用。 (3)了解前沿技术。
(4)就业的方向之一。
二、pcb制版的历程 1.绘制原理图 2.新建原理图库 3.新建元件库封装
4.导入元件封装库及网络列表 5.pcb元件布局 6.pcb布线 7.打印pcb图
8.制作电路板
三、元件库的设计
1.原理图元件库的制作;
1)打开新建原理图元件库文件*.lib 2)新建原理图元件
a、放置引脚,圆点是对外的端口。 b、画元件外形。 c、修改引脚属性。
[名称][引脚数(必须从1开始并且连续)] 隐藏引脚及其他信息 3)修改元件描叙
默认类型、标示、元件封装 4)、重命名并保存设计。
若还需要新建其他元件,可以\工具 \新建元件 a、独立元件
b、复合元件含子元件
5)设计中遇到的问题,怎么方法解决的
制作原理图元件库比较简单,因此在制作过程中没有出现什么问题。但是在制作过程中应特别注意,在放置引脚,圆点是对外的端口,并且注意修改引脚数应从1开始。 6)设计的原理图元件库截图
图1 lib.2/.4元件库 图2 lib.2/.4元件库 2.元件封装库的制作; 1)打开新建的元件封装库。 2)添加焊盘、调整焊盘的位置、修改焊盘的属性。
焊盘可置于任意层
利用标尺或坐标工具定位焊盘
焊盘命名必须与原理图元件number相同 3)画元件外形
必须在top overlayer 层操作 4)设置参考点
编辑/设置参考点
5)重命名、存盘。 6)设计中遇到的问题,怎么方法解决的 a、在元件封装库的制作过程中,对焊盘的左右距离没有按标准调好,后来问了同学,就把距离按标准调和。 b、在做完元件封装库的制作之后,对文件进行了重命名,可是忘记了进行保存,后老师检查之后才发现这个问题。 c、应注意焊盘的间距与实物引脚间距相同, 内部标号与原理图标号一致,保证实际引脚与原理图引脚对应。 7)设计的元件封装库截图
图1 rb.2/.4封装 图2 rb.2/.4封装
注:电解电容参数:
外径:160mil,焊盘间距:90mil 焊盘外径:52mil,孔:28mil 按键开关参数:
长:320mil,宽:250mil 线宽:10mi,中间圆直径、水平:250mil,垂直:175mil 焊盘大小,外径:78mil,孔:78mil
四、原理图的绘制 1)、添加原理图元件库。
\design explorer 99 se\library\sch miscellaneous devices.ddb protel dos schematic libraries.ddb 2)、摆放元件
从元件库选择元件
查找元件 3)元件调整 x,y,space 拖动
删除多余元件 4)连接电路 篇二:pcb实训报告 pcb实训报告
学生姓名 专 业 嵌入式系统工程 班 级 时 间 2012年6月23日 指导教师
计算机与软件学院 1 pcb实训
一、实训目的
本次实训是针对pcb制图课程结束后的一次综合实训,为检验和巩固学生对pcb制图学习成果以及提高其电子设计制作能力,以达到提高学生综合分析能力、实践技能的目的。
二、实训内容及要求
1、实训内容
以at89c51为主芯片,制作一个银行报号系统,其原理图电路如图1至图5所示。本次实训所用芯片为at89c51。它是我们最熟悉的一类单片机,很适合与初学者学习与实践。 2 图1 sch原理图主控模块 at89c51芯片简介: 4kb可编程flash存储器(可擦写1000次)三级程序存储器保密 静态工作频率:0hz-24mhz 128字节内部ram 2个16位定时/计数器 一个串行通讯口 6个中断源
32条i/o引线 片内时种振荡器 at89c51具体图片: 3 at89c51详细引脚功能: 外接晶体引脚 xtal1 19 xtal2 18 xtal1是片内振荡器的反相放大器输入端,xtal2则是输出端,使用外部振荡器时,外部振荡信号应直接加到xtal1,而xtal2悬空。内部方式时,时钟发生器对振荡脉冲二分频,如晶振为12mhz,时钟频率就为6mhz。晶振的频率可以在1mhz-24mhz内选择。电容取30pf左右。
*型号同样为at89c51的芯片,在其后面还有频率编号,有12,16,20,24mhz可选。大家在购买和选用时要注意了。如at89c51 24pc就是最高振荡频率为24mhz,40p6封装的普通商用芯片。 3.复位rst,在芯片中的引脚号为9. 在振荡器运行时,有两个机器周期(24个振荡周期)以上的高 4 电平出现在此引腿时,将使单片机复位,只要这个脚保持高电平,51芯片便循环复位。复位后p0-p3口均置1引脚表现为高电平,程序计数器和特殊功能寄存器sfr全部清零。当复位脚由高电平变为低电平时,芯片为rom的00h处开始运行程序。常用的复位电路如图2所示。
*复位操作不会对内部 ram 有所影响
。 p0端口[p0.0-p0.7] p0是一个8位漏极开路型双向i/o端口,端口置1(对端口写1)时作高阻抗输入端。作为输出口时能驱动8个ttl。
对内部flash程序存储器编程时,接收指令字节;校验程序时输出指令字节,要求外接上拉电阻。
在访问外部程序和外部数据存储器时,p0口是分时转换的地址(低8位)/数据总线,访问期间内部的上拉电阻起作用。 p1端口[p1.0-p1.7] p1是一个带有内部上拉电阻的8位双向i/0端口。输出时可驱动4个ttl。端口置1时,内部上拉电阻将端 5篇三:pcb实习报告
实训时间
pcb 工艺》实训
学院 :电子工程学院 专业 :电子信息工程 班级 :a1022班 姓名 :张丽 学号 :11011010203 指导老师 :林政剑 2012年05 月28日 至 06 01 《
:月日
一、pcb的相关介绍:
(1)pcb的分类:
根据电路层数分类:分为单面板、双面板和多层板。
单面板 :在最基本的pcb上,零件集中在其中的一面,导线集中在另一面上。
双面板 :电路板的两面都有布线,双面板的面积比单面板大了一倍,而且因为布线可以互相交错(可以绕到另一面),它更适合在比单面板更复杂的电路上。
多层板 :多层板用上了更多单或双面布线板。 (2)protel99se三个常用的快捷键: 鼠标左键+x—浮动图件左右翻转; 鼠标左键+y—浮动图件上下翻转;
鼠标左键+空格键—浮动图件转至90°。
二、原理图设计:
(1) 新建设计和编辑环境的设置: 1.打开protel 99se; 2.单击file菜单下的new,弹出一个对话框,新建sch文件,选择所需要的存储位置; 3 .选择e盘,在e盘新建一个文件夹,自己命名,并保存。 (2) 元件属性的编辑和操作: 1.从元件的库列表中选择所需要的库,如dos和devices库; 2.在库中找到所需元件,点击place,将其移入编辑界面; 4.返回之前制作的.sch编辑界面,点击add将制作的8res这个文件装入,再在该界面添所需标号;
5.连线。有直接连线法和网络标号法两种。 6.电气检查。原理图绘制好后,需要对原理图进行电气检;点击tool菜单下erc命令。默认状态下,除了抑制警告不选外,其他的都要选择,这为检查带来方便。 7.材料清单的生成。点击reports菜单下的“bill of material”,则会弹出生成清单向导。根据提示选择所生成的材料清单。 原理图如下: vcc p00p01p02p03p04p05p06p07r11235688res
三、原理图转为pcb图: 1.填写元件封装名:如下表: (注:key , keybm封装自带的封装库里没有,需要自己绘制。) 2.放置元器件焊盘。点击放置菜单中的键放置焊盘,在放置焊盘前可以按tab 键更改其属性 x-size(焊盘x轴大小):80mil y-size(焊盘y轴大小):80mil shape (焊盘形状 ):round designator(焊盘编号);1 hole size (焊盘孔径):30mil rotation (角度):0.000 x-locaton(焊盘x轴坐标):暂时默认即可,以后可以根据需要修改。 y-locaton(焊盘y轴坐标):暂时默认即可,以后可以根据需要修改。 其中,x/ysize用来设置焊盘大小,手工制板一般讲其设成80mil;designator是焊盘的编号,用数字和字母都可以,但必须与原理图中元件的管脚编号保持一致;hole size为内孔大小,一般设为30mil。
实验实训(设计)计划
系(部): 信息工程系
专 业: 电子信息工程技术
二〇一五年 七月 pcb实训(设计)报告
项目名称:电子产品分析与制作实训
专 业:电子信息工程技术班 级:电信142 企业指导老师:校内指导老师:陈思海
学 号:201400928姓 名:李聪 地 点:sy405时 间:2015.7.6-7.9 二〇一五年 七 月九日
绵阳职业技术学院实验实训(设计)
进度检查及成绩评定表
前 言
电子技术实训是高等职业院校电子、通信、电气、计算机及相关专业学生主要的实践性教学环节。当今的社会竞争日益激烈,选拔人才,评选优胜,知识竞赛之类的活动愈加频繁,那么也就必然离不开抢答器。而现在的抢答器有着数字化,智能化的方向发展,这就必然提高了抢答器的成本。鉴于现在小规模的知识竞赛越来越多,操作简单,经济实用的小型抢答器必将大有市场。本抢答器通过十分巧妙的设计仅用两块数字芯片便实现了数显抢答的功能,与其他抢答器电路相比较有分辨时间极短、结构清晰,成本低、制作方便等优点,并且还有防作弊功能。因此,我们制作了这款简易一路抢答器屏弃了成本高,体积大,而且操作复杂。我们采用了数字显示器直接指示,自动锁存显示结果,并自动复位的设计思想,因而本抢答器具有显示直观,不需要人干预的特点。而且在显示时抢答器会发出叮咚声使效果更为生动。工厂、学校和电视台等单位常举办各种智力竞赛, 抢答记分器是必要设备。
目录
第一章
实训任务„„„„„„„„„„„„„„„„„„„„„„„„..7 实训目的„„„„„„„„„„„„„„„„„„„„„„„„..7 实训要求„„„„„„„„„„„„„„„„„„„„„„„„..7 训练内容和方法„„„„„„„„„„„„„„„„„„„„„..8 第一节原理图 ...........................................9 一原理图设计 ..........................................9 二原理图元件库元件设计 ................................9 第二节 pcb图 .........................................10 一 pcb设计 ..........................................10 二 pcb元件库元件设计 ................................10 第三节遇到问题和解决办法 ..............................11 一原理图部分 .........................................11 二 pcb部分 ..........................................11 第二章抢答器制作实习....................................12 元件介绍 .............................................12 第一节印制技术 ........................................13篇五:各类电子实训心得体会
焊接收音机心得 一
今年的半学期电子工艺实训给我留下深刻的感受,从中学习到了画图、焊接以及其他零件的用途与方法,在焊接电路板时,也学到了很多东西,比如焊法、零件的形状和种类、元器件的基本常识等等。真是让人受益匪浅,终于能体会到不同零件的奇妙组合中展现的人类智慧的结晶。知识的重要性在我心中再次提升,电子产品知识产权的垄断,让我既看到了机遇又看到了挑战,学习是现在我们唯一的行动方针。
电子产品总是让人感觉得非常的神奇,比如收音机,一个小小的盒子竟能发出各种声音,使我们在孤独时给予陪伴,在痛苦时给予安慰,在无聊时给予一丝轻松和愉快。比如手机,使得和遥远的亲人说话,谈判业务等等。电子无处不在,所以我的好奇心使我产生了兴趣,如今我终于可以亲手试一试,焊接我自己的电路板。
电烙铁(焊枪)的介绍使我大吃一惊,原来我们用的是日本货,日本一个弹丸之地确实有我们值得学习的地方。我以前所见的焊枪时平头的,接220幅的,向我们这样的初手如果枪头碰到电线皮的话,那后果不堪设想。可是如今的焊枪非常的先进,有温度的控制,有降压的装置,又有耐高温的电线皮。使我们的危险降至到零,让我们没有后顾之忧,完全进入到焊接的快乐之中。尽情的发挥自己的想象力,在不知不觉中已经掌握了焊接的技术,并得到了老师的充分肯定。焊东西需要松香,但早已被上届的同学们使用完了,给我们带来非常大的麻烦,也许是环境的变化,在恶境中的成长的人经验更丰富,毅力更坚强。我们学习了更为方便更为快捷的焊接方法。我发现面对困难时我们更应该逆流而上,如果这次放弃了,那下回呢?所以在这次的实习中我学习到了重要的思想上的指导方法。 在练习焊接时,我时刻默念老师教的焊接五步,遵循正确的步骤才是最简洁的方法。虽然我多次失败,但我从不放弃,手多次被烫了,但我觉得这是接触电子的开始,以后还要接触更多的,为以后的学习大号良好的基础与健康心理,所以我要多练习,多总结,多观察,记笔记,从经验中分析出要点与方法。一开始老师让我们在电路板上卸零件然后再焊上,这对我来说是很有意思的事情,有冷静的思考了一下,其实这也是让我们在大战前充分的了解焊枪的特性,在考试中能非常连贯的焊上三个脚使之成为一个正方体。一想到这就感到棘手,还能怎办呢,只能练习练习再练习,再练习的同时我们还做各种作品,也就是用铜线焊各种东西。我觉得这是最有意义的事情,又非常快速的锻炼了焊接的技巧,有激发了大家的兴趣,使课堂得到双赢的效果。能想出这一点子的老师绝对有超强的观察力和与同学沟通的能力。终于在平时训练中,总结出非常有效的方法,功夫不负有心人,在最终的考试中,我以最快最坚固最光亮最润滑而赢得了老师的好评,也使我得了本班的第一个优,付出是有回报的,我认为这是没有成功的人的想法,其实你真的努力了,回报也就不重要了。
当发下来收音机的零件时,我如获瑰宝,如果这次成功的话,那我将上一大步,这精密的仪器只要错一点,那么没有声音,再找错误将士难上加难。所以我更加专心听老师讲课,我对怎么焊已经掌握了,我开始注意零件的美观,想把这收音机做的精致点,就像工厂作业的流水线,我找遍了各种资料,各种样板,观察他们的制作意图。得到了更加宝贵的经验。比如,怎样焊才能使那些卸零件的人用不了卸下的零件,怎样焊使零件上的型号在一侧,怎样焊使散热达到最大等等,
有时想是没有用处的,还必须去考察,去学习,去实践考察,只有这样才能有实质的进步,还有要和同学共同讨论,解决各种困难,在困难中你能了解更多的非课本的知识,还能再找错误的同时锻炼你的观察力,所以我知道了很多零件的作用,并了解到什么样的现象是哪块的电子区域出现了错误,小小的成功给我很大的动力,我知道我会继续努力的。 在整个的实习中我学习了很多的东西,使我眼界打开,感受颇深。简单的焊接使我了解到人生学习的真谛,课程虽然结束了,但学习还没结束,电子的世界将为我打开,只有继续以电子实习的感受而获得的指导思想走下去,在事业的途中打开另一扇门。 焊接收音机心得 二 这个星期我们班进行了为期一周的电子工艺实习,实习任务是制作一台收音机,其实是进行简单的组装而已!
刚开始时我并不清楚电子工艺实习到底要做些什么的,以为像以前的金工实习那样这做做那做做。后来得知是自己做一台收音机,而且做好的作品可以带回去呢。听起来真的很有趣,做起来应该也挺好玩的吧!就这样,我抱着极大的兴趣和玩的心态开始这次的实习旅途。
第一天并不是学制作,而是做一些基本工的练习,练习如何用电烙铁去焊接元件。电烙铁对我来说并不陌生,我以前在电子协会时用过很多,算得上会用但谈不上是熟练那个,所以我也很认真地对待这练习的机会。焊接看起来很简单但个中有很多技巧要讲究的,在焊的过程中时间要把握准才行,多了少了都不行!练习时最好边做边想想老师教的动作技巧这样学得比较快一点。
第二天的主要任务是了解收音机的大致原理。说真的,虽然自己是学电子专业的但对很多常用的电子元件还不认识呢。老师也知道我们常识少,所以从元件识别入手。这个老师讲课很风趣,经常让我们引进不禁,这样学习气氛比起我们平时上专业课时好多了。老师讲完原理后,我们就开始把每个元件照着图纸插到pcb板上。
第三天,我们要把插好的每个元件焊接上去。我的pcb板已经搞好一半多了,所以这天早上不久我就把它焊接完毕啦。我很高兴,因为我是我们班第一个拿作品去给老师调试的。调试后发现我的制作有点小问题,但经我细心检查修改后最终成功了!听着自己的制作发出的声音心里甜甜的,因为这是我的劳动结晶! 第四天的任务是把收音机的外壳装上去,第五天老师教我们写实习报告的细则及注意事项。这样一个星期的实习就结束了,时间过得真快,真有点不舍得的感觉。 这次实习很有趣很轻松,通过老师的讲解我懂得了收音机的基本原理同时也学到了很多有关电子的专业知识。在实习过程中不断提高自己的动手能力之余也体会到了实践的乐趣。因为在实践时往往会遇到很多问题,遇到问题后要细心检查才能发现其中的错误,最后就要想办法去解决这些问题。这样的一个过程不知不觉地使我的实践能力提高,为以后学习、做实验打下基础!
电子电工实训心得 . . 具有良好的职业素质和较高的职业技能是构成二十一世纪,面向现代化企业生产、管理一线的高素质技术人员的两个基本要素。职业素质的提高与职业技能的掌握都具有养成教育的特征,应该贯穿到教育的整个过程。电子工艺实训是根据电子信息类高级人才所需的能力结构而规划的,是技术基础能力的训练,也就是为了培养学生基础能力而开设的。电工电子实训目标就是:“培养学生的职业素质和培训学生的职业技能。”职业技能培养的内容包括电工电子基本操作能力、电工电子基本操作能力、电子电工基本工程能力。使学生了解和掌握电子产品制造、工艺设计系统集成与运行维修所具备的基本操作能力、识图能力、简单电路的制作及电子产品辅助开发能力。 . 本次实训,我们一共做了六个项目,别是: .
一、三相异步电动机正反转控制 通过这个实训我们掌握了控制电路的接线及检查的方法。学习了低电压电器的有关知识,了解其规格,型号及使用方法。掌握了三相异步电动机的正反转控制电路的工作原理,了解控制电路的基本环节的作用。
二、三相异步电动机的星形-三角形减压起动控制 通过这个实训掌握了三相异步电动机的星形-三角形减压起动的工作原理,加深了对控制电路的基本环节的作用的了解。也了解了继电器的结构、使用方法、廷时时间的调整及在控制系统中的应用。
三、白炽灯的双开关控制及日光灯的安装 通过这个实训,我们学会了白炽灯的两地控制方法。学会了日光灯的安装。
四、整流滤波稳压电路 通过这个实训,我们熟悉了线性集成稳压电路的工作原理和特点。掌握三端固定及三端可调输出电压的集成稳压器的使用。学习了测量集成稳压电源的技术指标的方法。结合直流稳压电源的制作、调试,练习和掌握电路板的焊接。
五、正常工作。能够正确使用电烙铁。熟练焊接电路板。能够对电路板进行检测,对电路板进行故障徘除。通过这个实训,我们也了解了放大器的原理。
六、rc正弦振荡电路 通过这个实训,我们能够识别相关的电子元器件,检测其能否正常的工作。能够对电路板进行检测,对电路的故障进行排除。 . 通过了为期两周的电子电工实训,我确实是学到了很多知识,拓展了自己的的视野。通过这一次的电子电工实训,增强了我的动手打操作的能力。记得我在读高中的时候,我帮家里安装一个开关控制电路,由于自己的动手能力不够强,结果把电路接成短路,还好因为电路原先装有保险丝,才没有造大的安全事故。而通过这一次的电子电工实训,我就掌握了日光灯电路的安装,学会了白炽灯的两地的控制方法。也学习了一些低压电器的有关知识,了解了其规格、型号及使用的方法。更主要的是,我还学会了电路的接线及检查的方法。 在后面的几个实训的项目里有用到了一些常用的电子元器件,所以通过了实训,我能够识别相关的电子元器件,如电阻器、电位器、电容器、二极管、晶体管和 三端集成稳压器等常有的电子元器件。知道了它们的形状、它们的分类、它们的型号规格、它们的用法以及如何检测这些电子元器件的好坏。 通过了这两周的电子电工的实训,也培养了我们的胆大、心细、谨慎的工作作风。由于前面的三个实训是通过接上日常低压电路来完成的,所以就要讲求用电的安全,不许用手触及各电气元件的异电部分及电动机的转动部分。也要求操作的时候要心细、谨慎,避免触电及意外的受伤。在后面的几个实训中用到了电烙铁,也是要求学生掌握电烙钱的正确使用的方法,避免意外的受伤。
通过这一次的电子电工的实训,也培养了我们的规范化的工作作风,以及我们的团结协作的团队的精神。
电工实训体会
电工这一周的实训使我对实际生活和生产车间的电有了一点的认识,让我从中得到了锻炼,对以前的知识加以巩固,还提高了自己的动手能力,培养了团体间的携手和作能力。
一周的电工实训进行的紧张有序,使我们有在车间实习体验。这次实训是对实际条件下的依次模拟考核,使用的电压在220伏到380伏,所以对我们的要求很高,弄不好会有触电的危险,还有烧毁仪器,在实训开始前老师告诉我们,安全放在第一,能马虎,开电的时候要检查一遍,还要通知其他人,以免触电,老师又讲了试验时应注意的问题,然后我们按分好的组开始做试验。
刚开始作一周实训,以为要做很多试验,发下材料一看才四个,这次电工实训一共有四次试验,第一个试验是家用供电线路实训,主要目的是要学会日光灯电路,一灯两地控制,灯光可调电路,声光延时电路,铡刀控制电路的正确接法。以前我对家用供电线路的了解,只存在火线,零线。一些开关的连接,再实际生活中电是危险物,在家根本不叫碰,所以知道的不多。通过老师的讲解使我们有了一定的了解,我们接的很顺利,声光延时开关必须用东西包住才能使灯泡亮。通过这次实训让我对家用点有了一定的了解。 第二个试验是电动机反-正转实训,我们上学期有一定的理论知识,我想应该没问题,可以做起来,可一做不是那一回事,接完后电机不转,发现是接触点不能吻和。我们将电压改变后,电路恢复正常工作,电机开始反-正转。这让我懂的接线必须认真,不能马虎。在做任何事都必须认真做。是我感受颇多。
第三个试验电动机既可点动又可自锁控制线路实训,这个试验线路和上一个没有查别,在加上已经做过二个试验,我们对电器的应用有一定的熟悉。操作起来就比较顺利,我从中学到了很多,让我对电机有了新得认识,可以顺利的进行调控。 最后一个试验是工作台自动往返循环线路实训,要求我们通过实际安装接线掌握有电气原理图变换成安装接线图的方法,并掌握行程开关的作用,以及机床电路的应用。这个试验很复杂,我们接完线,打开开关,可机床不动,我们检查线路,发现一个地方没有连线,我们把线接上,机床动了。虽然和试验要求不一样,但我们很高兴,因为它动了,我们有把线检查了好几遍,没有发现问题,我们很着急,把高频调到低频,还是不行,最后我们把
1、
2、
3、4它们换个来,机床动了,我们成功了。
一周的实习期瞬间结束了,但一颗炽热的心依然还在那实习的场地依依不舍,特别是对咱们的指导老师很是敬佩。
通过几天的实习,使我懂了许多许多的道理,真可谓是“受益非浅”啦,这次我们的实习任务,虽然算不上很重,其任务就是按图安装一些简单的照明电路。原
理谈不上很复杂,但是真正要安装起来那得费一把劲,由于是四位同学共用一个工位,最重要的是双方协作精神,这一点我体会最深。
做工有条不紊的进行着,这项工作需要特别的细心,弄不好的话很容易让自己做的一切从头再来。首先,必须把安装的器材清好检查是否完好,再次就是要运用巧劲把每副夹子上好,牢固,一下午下来人累得是筋疲力尽,但看到自己安装的效果,还是感到很欣慰的,再过一年半我们就要步入社会,踏上自己的工作岗位,但我感觉到一周的学习期就是以后生活的写照,我会运用自己的书本知识和实践能力去撑稳,那在江中的风帆?? 第一次看着电动机通过自己动手接线转起来,那种感觉是自豪的。自己在心里会说:“呃,我也能让电动机转起来,哈,开心。加油,其实这蛮好玩的嘛”。 我们的老师总是先给我们讲一些理论的内容,再准备让我们接线。刚开始接线时我们就按着图接下来,一点秩序也没有,所以接好了的线看过去乱乱的像蜘蛛网一样。现在想到都觉得好笑。
也因为电工课我们了解到了很多我们平时都不会认真去注意的常识,比如安全用电常识、电工基本操作(怎么连接导线)、电气照明(主要是日光灯);还有一些常用的低压电器(意所布的线布的先后顺序,比如说布线时应把其他的线都布好了之后再布开关的线,交流接触器,继电器等);行程开关的用法;电动机的结构和铭牌意义;控制电路故障分析与排除等。恩,总之,感觉学到的东西还是蛮多的。四次的电工对手亲身体会到整体思考的重要性,布一块好板就必须要有整的逻辑思维,布板要注意各元器件的空间排布还要注意到布线时线与线不能相交且要注 通过了这一周的电子电工的实训,也培养了我们的胆大、心细、谨慎的工作作风。由于前面的三个实训是通过接上日常低压电路来完成的,所以就要讲求用电的安全,不许用手触及各电气元件的异电部分及电动机的转动部分。也要求操作的时候要心细、谨慎,避免触电及意外的受伤。在后面的几个实训中用到了电烙铁,也是要求学生掌握电烙钱的正确使用的方通过这为期一周的电工实训,我确实是学到了很多知识,拓展了自己的的视野。通过这一次的电工实训,增强了我的动手打操作的能力。记得我在读高中的时候,我帮家里安装一个开关控制电路,由于自己的动手法,避免意外的受伤。能力不够强,结果把电路接成短路,还好因为电路原先装有保险丝,才没有造大的安全事故。而通过这一次的电工实训,我就掌握了日光灯电路的安装,学会了白炽灯的两地的控制方法。也学习了一些低压电器的有关知识,了解了其规格、型号及使用的方法。更主要的是,我还学会了电路的接线及检查的方法。 通过这一次的电工的实训,也培养了我们的规范化的工作作风,以及我们的团结协作的团队精神。
推荐第8篇:PCB常识
PCB常识教程 第一章 PCB基板材料
覆铜箔层压板(Copper Clad Laminates,简写为CCL)简称覆铜箔板或覆铜板,在整个印制电路板上,主要担负着导电、绝缘和支撑三个方面的功能。
一、覆铜箔板的分类方法
1、按板材的刚柔程度分为刚性覆铜箔板和挠性覆铜箔板两大类。
2、按增强材料不同,分为:纸基、玻璃布基、复合基(CEM系列等)和特殊材料基(陶瓷、金属基等)四大类。
3、按板所采用的树脂粘合剂,分为:
(1)纸基板
酚醛树脂XPC、XXXPC、FR-
1、FR-2等板、环氧树脂FR-3板、聚脂树脂等类型。
(2)玻璃布基板
环氧树脂(FR-
4、FR-5板)、聚酰亚胺树脂PI、聚四氟乙烯树脂(PTFE)类型、双马酰亚胺改性三嗪树脂(BT)、聚苯醚树脂(PPO)、聚二苯醚树脂(PPE)、马来酸酐亚胺一苯乙烯树脂肪(MS)、聚氰酸酯树脂、聚烯烃树脂等类型。
4、按覆铜箔板的阻燃性能分类,可分为阻燃型(UL94-VO、V1级)非阻燃型(UL94-HB级)两类板。
5、按基板的厚度及覆铜板厚度可分为:H/0,1/0,2/0-------单面板材;H/H,1/1,2/2--------双面板材;1-1-0.5 OZ(安盎) 1-1 OZ (安盎) 2-2 OZ(安盎)
6、覆铜箔板产品型号的表示方法(GB/T 4721-92)
(1)第一个字母C,表示铜箔;
(2)第
二、三两个字母,表示基材所用的树脂;
① PF表示酚醛② EP表示环氧③ UP表示不饱和聚酯④ SI表示有机硅
⑤ TF表示聚四氟乙烯⑥ PI表示聚酰亚胺⑦ BT表示双马来酰亚胺三嗪
(3)第
四、五两个字母,表示基材所用的增强材料:
① CP表示纤维素纤维纸② GC表示无碱玻璃布③ GM表示无碱玻璃纤维毡
④ AC表示芳香族聚酰胺纤维布⑤ AM表示芳香族聚酰胺纤维毡
(4)覆铜箔板的基板内芯以纤维素纸为增强材料,两表面贴附无碱玻璃布者,在CP之后加“G”表示;
(5)在字母末尾,用一短横线连着两位数字,表示同类型而不同性能的产品编号;
(6)具有阻燃性的覆铜箔板,在产品编号后加有“F”字母表示。
7、纸基覆铜箔板在20℃~60℃之间进行的冲裁加工称为冷冲,在60℃以上进行的冲裁加工称为热冲。
8、UL标准与UL认证
UL是“保险商试验室”的英文字头。
(1)安全标准文件:UL746E(标准题目为:聚合材料工业用层压板、纤维缠绕管、硬化纸板及印制线路板用材料)。
与UL746E有关的标准有:UL746A(聚合材料—短期性能评定)、UL746B(聚合材料—长期性能的评定)、UL746C(聚合材料—电气设备的评定)、UL796(印制电路板)、UL94(各种电气装置和设备中零部件用塑料的可燃性试验)。
(2)覆铜箔板的UL认证,是以UL746E(96年10月开始实施的修订稿)、UL94为检测标准。
认证过程中要进行试验测定的项目:
①在判定UL申请的样品属于何种等级方面有:
a、红外吸收光谱(IR) b、灰分 c、热解重量分析(TG) d、耐燃性
②在样品的层压板基板(去铜箔)的试验有:
a、大电流起弧引燃(HAI) b、热丝引燃(HWI) c、高压起弧引燃(HV ARI)
d、高压电弧起痕速率(HV AIR) e、介电强度 f、弯曲强度
g、相比起痕指数(CTI) h、体积电阻率 i、吸水性
③覆有铜箔的样品试验有:
a、铜箔粘合强度 b、热冲击性
(3)其它覆铜箔板质量安全认证机构
①欧洲客户要求:BS(英国:BS-415)、VDE(德国:DIN VDE 0860)
②北美洲客户要求:CSA(加拿大)
二、覆铜箔板主要原材料介绍
(一)按铜箔的制法,可分为压延铜箔(W类)和电解铜箔(E类)。[IPC-CF-150E]
1、压延铜箔是将铜板经过多次重复辊轧而制成的,其耐折性和弹性系数大于电解铜箔,铜纯度(99.9%)高于电解铜箔(99.8%)。在毛面上比电解铜箔平滑,有利于电信号的快速传递。因此,在高频高速传递、细导线的PCB的基板上,采用压延铜箔;在音响设备上的PCB基材的使用,还可提高音质效果;还用于为了降低细导线,高层数的多层线路板的热膨胀系数(TCE)而制的“金属夹心板上”。
2、电解铜箔是通过专用电解机(又称电镀机),在圆形阴极辊铜上连续生产出的,初产品称为毛箔,再经表面处理,包括粗化层处理,耐热层处理(纸基覆铜箔板所用铜箔无此处理),钝化处理。
(1)热层处理有:镀黄铜处理(TC处理);处理面呈灰色的镀锌处理(TS处理,或称TW处理);处理面呈赤色的镀镍和锌处理(GT处理);压制后处理面呈黄色的镀镍和锌处理(GY处理)等种类。
常见电解铜箔的品种、特性
代号 对照IPC中等级 特 性
STD 1级型 一般通用型产品
HD 2级型 常温延伸性,耐折性好
THE 3级型 常温延伸率大,高温延伸性良好
MP 粗化面为低粗化度,具有好的高温延伸性
LP(VLP、SLP) 粗化面为低粗化度,适用于精细图形的PCB上
3、电解铜箔的各种技术性能与其对覆铜箔板性能的影响。
(1)厚度。
铜箔厚度用公称厚度和质量厚度(g/㎡)来表示。
铜箔厚度标准
铜箔
代号 公制 英制 允许公差
单位面积质量(8/㎡) 标称厚度
(㎜) 单位面积质量(OZ/ft2) 标称厚度
(mils) g/㎡ ㎜
T(3/8) 107.0 0.012 0.35 0.47 ±10 ±0.001
H(1/2) 153.0 0.0172 0.50 0.68 ±15 ±0.0015
M(3/4) 229.0 0.0257 0.75 1.01 ±22 ±0.0025
1 305.0 0.0343 1 1.35 ±30 ±0.0035
2 610.0 0.0686 2 2.70 ±61 ±0.007
(2)外观。表面要求无异物,无变色,无铜粉,不允许光泽面(S面)凹凸不平。
(3)抗张强度与延伸率。STD型在高温下的延伸率和抗张强度较低,同时,由于它与基板材料热态下延伸率相差较大,会引起板的尺寸稳定性和平整性能变差,PCB的金属化孔的质量下降以及使用PCB时产生铜箔断裂问题。THE型和LP型在热态下延伸性方面比STD型铜箔优越。LP型因它的结晶结构更提高了它的韧性,在热态抗张强度方面更优于THE型铜箔,并在延伸率方面,高温下一直保持着与常态大致相同的性能。
(4)剥离强度。铜箔与基材在高温高压压制后,它们之间的粘合强度(成垂直方向受力),称为铜箔剥离强度(又称抗剥强度)。决定此性能高低与铜箔的品种,粗化处理水平和质量,耐热层处理方式和水平有关;纸基覆铜箔板还与涂敷的铜箔胶粘剂有很大关系。低粗化度的LP、VLP、SLP型铜箔,在制作精细线条的PCB和多层板上,其抗剥强度性能比一般铜箔(STD型),THE型更优异些。对铜箔产品剥离强度的测定,除常态条件外,还有:浸焊锡后(260℃)高温中(在125℃),加热处理后(48小时/180℃),吸湿条件处理后(18℃ HCL 21℃ 20分钟浸渍),氢氧化钠浸泡处理后(10% NaOH,80℃,2小时浸渍)。其中酸性或碱液处理后的剥离强度性能用劣化率(%)来表示。
(5)耐折性
压延铜箔高于电解铜箔。电解铜箔横向略高于纵向;压延铜箔纵向比较稳定,横向在150℃的热处理温度下,低于电解铜箔,在150℃以上,才逐渐显示出较高的耐折性。
(6)表面粗糙度
铜箔的粗化面(M面)的粗化度,有两表示:一种表示是平均粗化度(Ra),它表示在一定面积铜箔粗化面上,粗化膜峰高低的中心线的以外一侧(峰尖侧)的平均高度。另一种表示是最大粗化度(Rmax)。
(7)蚀刻性
低粗化度的铜箔蚀刻性能优于普通铜箔,具有蚀刻时间短,并保证细导线幅宽的尺寸精度的优点。
(8)抗高温氧化性
在180℃热空气中处理30分钟后,观察光泽面是否变色,与铜箔钝化处理的质量水平有关。
4、铜箔的厚度在17.5㎜(0.5OZ)以下称超薄铜箔(UTF)。生产厚度低于12㎜者,
必须要有“载体”的帮助。目前生产的9㎜和5㎜厚的UTE,主要采用铝箔(0.05~0.08mm)或铜箔(0.05㎜左右)作为载体。
(二)玻璃纤维布有铝硼硅酸盐型的碱玻璃纤维(E),D型或Q型(低介电常数)、S型(高机械强度)、H型(高介电常数),在覆铜箔板中绝大多数采用E型。
1、玻璃布采用平纹组织布,具有断裂强度大,尺寸稳定性好,不易变形,重量厚度均匀的优点。
2、表征玻璃布的基本性能的项目有:经纱、纬纱的种类、织布的密度(经纬纱根数)、厚度、单位面积的重量,幅宽以及断裂强度(抗张强度)等。
3、纸基覆铜箔板的主要增强材料——浸渍纤维纸按纸浆的不同分为:棉纤维浆(以棉短绒为原料)和木纤维浆(又分为阔叶浆和针叶浆)。其主要性能指针有:纸的定量均匀性(一般选用125g/㎡或135g/㎡)密度、吸水性、抗张强度、灰分含量、水分等。
三、按NIMA标准,一般纸基覆铜箔板按其功能划分,常见的有:XPC、XXXPC、FR-1(XPC-FR)、FR-2(XXXPC-FR)、FR-3等品种。除FR-3板为环氧树脂外,其它各类板均以酚醛树脂为主。以“FR”为代号的板,表示其具有阻燃性。
1、一般纸基覆铜箔板采用单面覆铜箔为主,常用的厚度规格在0.8~2.0㎜范围内(0.8;1.0;1.2;1.6;2.0㎜),适用于电子元器件孔的间距为1.78㎜,连接器孔的间距为2.0㎜的PCB的冲孔加工。
2、XPC板(国内又称为“HB”板),主要用于收音机、收录机、电子钟、汉字处理器、个人计算机键盘、个人用小型计算器、电子琴、小型电动玩具等方面。FR-1板(国内又称为“VD”板),主要用于彩色电视机、显示器、工业监视器、录像机、VCD机、数码录音机、家用音响、洗衣机、电饭锅、电热毯等方面。
3、酚醛纸基覆铜箔板的基本性能主要包括介电性能、机械性能、物理性能、阻燃性等。应用性能主要是指板的冲孔加工性,加工板的尺寸变化和平整性方面的变化,板在不同条件下的吸水性,板的冲击强度,板在高温下的耐浸焊性和铜箔剥离强度的变化等。
(1)冲孔质量及预热温度的关系(X:不好;O:好)。
加热温度 破裂 凸胀(拉包) 孔断面 层间分离 尺寸变化 孔收缩平整度
低温 × O※ O※※ O※ O O O
高温 O × × × × × ×
注:※在过低的温度下,密集孔的冲孔也容易造成基板的凸胀和层间分离现象。※※在过低的温度下冲孔,孔的切断面反而会变坏。
(2)酚醛纸基覆铜箔板在PCB加工尺寸变化有如下规律:
①尺寸变化率横向比纵向大。
②在蚀刻、清洗后的烘干 三次UV固化、干燥的加工过程,板的尺寸一般呈收缩变化,且收缩率较水。在冲孔加工区域,板的尺寸变化较大;冲孔加热后板的膨胀率增大,冲孔冷却后板的收缩率增大。
③冲孔加热温度的增高,板的尺寸稳定性受到的影响也越来越大。
(3)“动态平整度”测定表明:板的横向翘曲(弓曲方向同板的横向)大于纵向翘曲。板在制造图形的加工过程中,一般为负翘曲(铜箔在上的板形成“凹形”为负翘曲);加热冲孔时为正翘曲,冲孔冷却后和波峰焊后均呈负翘曲。从总体上来看:当板在加工过程中尺寸膨胀时为正翘曲,收缩时为负翘曲。板的吸水性低其平整度为准,尺寸稳定性好。
(4)印制电路加工过程尺寸变化的测试点
① ② ③ ④ ⑤ ⑥ ⑦ ⑧ ⑨
原始状态 印刷阻蚀刻剂,干燥 蚀刻
洗净 干燥 阻焊油墨干燥 丝网印刷干燥 冲孔
(加热) 冲孔以后(冷却) 钎焊
烘烤
温度,
时间 蚀刻温度、时间;洗净温度、时间 温度
时间 烘烤
温度,
时间 烘烤
温度,
干燥 温度
时间 室温 260℃
5S
2次
4、板的加工性(冲孔加工性/机械加工、平整度、尺寸稳定性);板的可靠性(耐湿性、耐金属离子的迁移性);板的安全性(耐漏电痕迹性、阻燃性、环保问题)。
四、玻璃布基覆铜箔板是指NEMA标准牌号为G
10、G
11、FR-
4、FR-5四种环氧玻璃基覆铜箔板。G
10、G11为非阻燃型板,FR-
4、FR-5为阻燃型板。G
11、FR-5的耐热性高于G
10、FR-4板。目前FR-4板用量在一般型玻璃基覆铜箔板中占90%以上。
1、一般玻璃布基覆铜箔板的增强材料采用E型玻璃纤维布,常用牌号为:76
28、21
16、1080三种;采用的电解粗化铜箔为0.018㎜(1/2OZ)、0.035㎜(1OZ)、0.07㎜(2OZ)三种。PC标准中规定:D、E、G分别表示单根纤维标称直径为
5、
7、9μm。
2、一般FR-4板分为两种:
(1)FR-4刚型板,常见板厚范围在0.8~3.2㎜。
(2)多层线路板芯部用的薄型板,常见板厚范围在0.06~0.75㎜。
注:薄型芯板的厚度为实测板厚度减去所覆铜箔厚度。
3、PCB基板材料的耐热性主要表现在耐热软化性和耐热老化性。
(1)耐热软化性,是表征基板材料树脂——高分子物在高温下的物理变化的特征。
测定基板材料的Tg,目前常用三种方法:
1 TMA法(Thermal Mechanical Analysis)俗称为热膨胀法。它通过温度等速的上升,2 当材料发生急剧热膨胀的温度点,3 为Tg点。
4 DSC法(Differential Scanning Calorimetric)俗称为量热法。通过示差扫描量热计测定标5 准物和试样温度,6 作出差热曲线的方法。找出曲线突变时的温度(这是板材在玻璃化转变时发生的比热突变造成的),7 得到Tg。
8 DMA法(Dynamic Mechanical Analysis),9 俗称为形变法。经过对材料的在等速升温下的弯曲振动,10 测定衰减率的曲线的最大值时的温度,11 此温度是Tg。
(2)耐热老化性,是表征基板材料树脂——高分子物在长时间高温处理的条件的化学变化的特性。
4、高频电路用的覆铜箔板最主要的特性是低介电常数和低介质损耗因子(tanδ)。高频电路需要高信号传播速度V(cm/n sec)。V与光带速(c)、介电常数(ε)关系公式是:V=K (K为常数)。当ε越大,其V越低。信号的传送损失与信号在导体内损失、介质内损失有关。而导体内损失与基板的ε的平方根成正比。介质内损失与ε的平方根、tgδ成正比。同时,传送损失还与频率有关,频率越高,传送损失越大。
五、表面和芯部的增强材料,由不同材料构成的刚性覆铜箔板称为复合基覆铜箔板。以CEM(Composite Epoxy Material)系列覆铜箔板用量最大,其中CEM-1(环氧纸基芯料)和CEM-3(环氧玻璃无纺布芯料)是最主要的两个品种。
项目 CEM-1 CEM-3
组
成
结
构 铜箔
玻璃布
纤维纸
玻璃布
铜箔
玻璃布
玻璃无纺布
玻璃布
铜箔
主树脂 阻燃型环氧树脂 阻燃型环氧树脂
板厚㎜ 0.8 1.6 0.8 1.6
灰份% 32.6~39.8 16.4~23.2 42.7~68.3 29.7~44.9
弯曲强度PSI 50000 35000 50000 40000
阻燃性 UL94V-0 UL94V-0
红外吸收光谱 符合UL光谱图 符合UL光谱图
CEM-1板主要用于高频特性要求高的印制电路上,如:监视器和电视机的调谐器,电源开关,超声波设备,电子计算机电源和键盘。也可用于电视机、录音机、录像机、收音机、电子设备、仪表、汽车电子产品、办公自动化设备、电子玩具等具有阻燃性能要求的进行冲孔加工的PCB上。
玻璃纤维无纺布(玻璃毡)制造方法:将直径5~10μm的细玻璃纤维切断成短纤维(长度在5~15㎜),用此在湿式短网抄纸机上制成纤维无纺布。然后在布上涂上粘合剂(一般是水溶性环氧树脂或水溶性丙烯酸树脂)经加热干燥,制成玻璃纤维无纺布。CEM-3板所用的玻璃纤维无纺布定量在30~125g/㎡,密度:0.1~0.5g/m3,抗张强度:1.2~7kgf/㎜2。
在钻孔加工中,CEM-3的钻头刃尖的寿命,比FR-4板高2-5倍。在冲孔加工中,比FR-4板优异。
CEM-3的厚度精度偏差略大于FR-4板。
CEM-3板在扭曲方面比较偏大。
CEM-3做为双面PCB基材,可部分代替FR-4板,进行金属化孔的加工。
耐漏电痕迹性是PCB用于电源基板等高压条件下的一个安全性的性能指针。UL标准中将CEM-3板的此项性能——相比起痕指数(CTI),要求在3级以下。“175<CTI≦250(V)”
CEM-3的耐热性强于FR-4板。
六、金属基覆铜箔板的特性主要是靠占有绝大部分板厚成份的金属板性能所决定的。
1、金属基板的优异散热性可防止在PCB上装载的元器件及基板工作温度的上升,对熔断电流也有明显的提高。金属基板的散热性,主要取决于:绝缘层的厚度、绝缘层的热传导性、金属基的金属种类。
2、金属基板具有高机械强度和韧性,具有高的尺寸稳定性和平整度。
3、金属基板可充当屏蔽板,起到屏蔽电磁波作用。
4、双面铁铝基板的热膨胀系数接近铜的热膨胀系数,有利于金属化孔的质量和可靠性。
5、铁金属基既可起印制电路板的作用,又起着小型电动机的定子基板的功能。
七、挠性覆铜箔板(FPC)的主要特性和用途。
要求特性 主要用途举例
薄型化、高折曲性化 FDD、HDD、CD的传感器、DVD
多层化 个人计算机、计算机、照相机、通信设备
线路精细化 打印机、LCD
高耐热性 汽车电子产品
高密度安装、小型化 照相机
电气特性(阻抗控制) 个人计算机、通信装置
1、挠性覆铜箔板按绝缘薄膜层(又称介电基片)分类,可分为聚酯薄膜挠性覆铜箔板,聚酰亚胺薄膜挠性覆铜箔板及氟碳乙烯薄膜或芳香聚酰胺纸挠性覆铜箔板。按性能分类,有阻燃型和非阻燃型挠性覆铜箔板。按制造工艺法分类,有二层法和三层法。三层法板是由绝缘薄膜层、粘结层(胶粘剂层)、铜箔层组成。二层法板只有绝缘薄膜层、铜箔层,其生产工艺有三种:
由热固性的聚酰亚胺树脂层和热塑性的聚酰亚胺树脂层复合在一起组成绝缘薄膜层。
先在绝缘薄膜层上涂覆一层阻挡层金属(barrier metal),然后进行电镀铜,形成导电层。
采用真空溅射技术或蒸发沉积技术,即把铜置于真空中蒸发,然后把蒸发的铜沉积在绝缘薄膜层上。二层法与三层法相比具有更高的耐湿性和Z方向上的尺寸稳定性。
2、挠性覆铜箔板的金属箔稻田采用压延铜箔最为合适;绝缘薄膜主要有聚酯薄膜、聚酰亚胺薄膜、氟碳乙烯薄膜以及芳香聚酰胺纸;层间粘结剂主要有环氧树脂、丙烯酸酯树脂、酚醛改性聚乙烯醇缩丁醛树脂、聚酯树脂、聚酰亚胺树脂类等。
3、聚酯薄膜用于挠性板工作条件在105℃以下情况,常用厚度在25—125μm;聚酰亚胺薄膜厚度在7.5—75μm范围内(7.5、12.
5、
25、50、75μm)。薄膜的主要性能项目有:拉伸强度(断裂强度)、断裂延伸度、抗张弹性率、热膨胀系数、介电常数、体积电阻系数、表面电阻系数、耐击穿电压等。粘结剂的一般涂层厚度在12.5—40μm。
八、覆铜箔板在使用、储存时应注意的问题
1、覆铜箔板是由纵横向机械强度不
一、受湿膨胀、受热收缩的纤维(织物)和受热软化、导热性差的树脂构成的基板,同时和热膨胀系数与基板有着很大差异的铜箔粘接结合,这样就形成各向异性。
2、冲剪加工注意事项
纸基和CEM-1覆铜箔板在剪床剪切下料时,环境温度不应低于20℃,并根据板冲切特性,有的板材在冲切加工时要先进行预热。
纸基和CEM-1覆铜箔板的模具冲料和冲孔,冲模刃口之间的间隙在一般情况下为板厚的2—3%,模孔尺寸设计时,应考虑基板加热时产生收缩0.5—1.0%的余量,冲方形孔,其四角应带有圆弧。
覆铜箔板有纵向和横向之分。一般而言,在板的翘曲(包括动态翘曲)、尺寸变化、弯曲强度等特性上,板的纵向比横向好得多。绝大多数厂家的产品字符的竖方向为板的纵方向。因板材方向性方面的性能差异,在PCB排版设计时
应注意:
①长方形的PCB的长边应取沿板材的纵向; ②PCB的插头部端线以沿板的纵向为宜;
③端部突出部位,底线也应沿板的纵向为宜; ④不同孔形排列,图形孔沿板纵向为宜。
3、生产时应注意的问题
铜箔面的油污会降低抗蚀剂对铜箔的附着力。铜箔面经清洗、研磨、冲洗、干燥后,应立即涂覆抗蚀剂,以确保铜箔面的清洁度,防止浸润不匀。
蚀刻后清洗不充分会降低其介电性以及造成变色。板在苛性钠溶液或有机溶液中长时间地浸渍,会造成层间粘合力性能的下降及板面变色。
4、钎焊时应注意的问题
(1)基板的耐浸焊性的测定方法
覆铜箔板的耐浸焊性(又称热冲击后起泡)测定方法:从被测试的覆铜箔板上切取边长度为25+/-1mm的正方形,试样为2个。不蚀去铜箔,边缘应平整,试样的铜箔面涂一层薄的滑石粉(防止作耐浸焊性试验时铜箔粘上焊锡,不易判断是否起泡)。耐浸焊性测定在焊锡浴中进行,焊锡浴深度不小于40mm,浴口截面积不大于100×75mm ,并附有调控温装置,其温度范围为0—300℃。一般耐浸焊性的测定温度稳定在260℃下进行,试样达到规定的浸焊时间后取出,检查是否起泡或分层。
(2)波峰焊接的焊锡温度一般应控制在250℃以下,SMD的再流焊接的温度也不能太高;手工焊接时电烙铁的表面温度应保持在300℃以下,而且要尽量缩短接触基板、基板上线路、焊盘的时间。当PCB在刚沾覆上焊锡后,切勿向线路、焊盘施加外力。
(3)为了减少玻璃布基覆铜箔板的残余内应力,在加工前对板材进行预处理——通常在130—150℃下,在带有循环风的烘箱中烘烤一段时间(板材不能直接接触热源)。烘板的温度和时间需根据板材厚度、面积大小及数量等加以选定。
5、覆铜箔板储存注意事项
覆铜箔板应储存在低温、低湿的场所内:温度为25℃以下,相对温度为65%以下。
防止阳光对板直接照射。
板材储存时不应歪斜状态下存放,不要过早地将其包装材料撤除,将其裸露。
取用、搬运覆铜箔板时,应带上柔软、清洁的手套操作。
取用、搬运板材,要防止板的边角部位划碰其它板的铜箔面,造成碰伤、划痕。
注:基板铜箔朝上时的凹曲变形称为板的负翘曲(高温潮湿环境);基板铜箔朝上时的凸曲变形称为板的正翘曲(干燥高温环境)。
第二章 制前工程
一、PCB图的设计
1、物理组件即是电子器件的封装尺寸在PCB上的一个平面映像,又要考虑布线及生产工艺的可行性。
2、PCB布局分为交互式布局和自动布局,一般是在自动布局的基础上用交互式布局进行调整。
布局原则是把互连关系多的组件就近放置,即同一个功能块的组件布在一起。
考虑电路的特性,尽量按它们的特性放置在一起,避免交插。(数字电路、模拟电路)
布SMD组件时,组件放置尽可能做到在印制板两面贴装。
国际标准组件的两个腿间距是0.1英吋。
组件的布局要以产品结构为主,要服从产品结构的整体。工作温度高的组件放置在PCB板的边沿或通风好的地方。
在一个PCB板上,组件的布局要求要均衡、疏密有序,不能头重脚轻或一头沉。
布局的检查
①印制板尺寸是否与加工图纸尺寸相符?能否符合PCB制造工艺要求?有无定位标记?
②组件在二维、三维空间上有无冲突?
③组件布局是否疏密有序,排列整齐?是否全部布完?
④需经常更换的组件能否方便的更换?插件板插入设备是否方便?
⑤热敏组件与发热组件之间是否有适当的距离?
⑥调整可调组件是否方便?
⑦在需要散热的地方,装了散热器没有?空气流是否通畅?
⑧信号流程是否顺畅且互连最短?
⑨插头、插座等与机械设计是否矛盾?
⑩线路的干扰问题是否有所考虑?
3、PCB布线有单面布线,双面布线及多层布线。布线方式有自动布线及交互式布线,在自动布线之前,可以用交互式预先对要求比较严格的线进行布线,输入端与输出端的联机应避免相邻平行,以免产生反射干扰。必要时应加地线隔离,两相邻层的布线要互相垂直,平行容易产生寄生耦合。
降低地线与电源线之间产生的噪音。
①在电源、地线之间加上去耦电容;
②尽量加宽电源、地线宽度,最好是地线比电源线宽,它们的关系是:地线>电源线>信号线。通常信号线宽为:0.2—0.3mm,最细宽度可达0.05—0.07mm,电源线为1.2—2.5mm;
③对数字电路的PCB可用宽的地导线组成一个回路,即构成一个地网来使用;
④用大面积铜层作地线用,在印制板上把没被用上的地方都与地相连作为地线用,或是电源、地线各占用一层。
数字电路的频率高,模拟电路的敏感度强。高频的信号线尽可能远离敏感的模拟电路器件。在板内部数字地和模拟地是分开的,它们之间互不相连,只是在PCB与外界连接的接口处(如插头等),数字地与模拟地(仅)有一点短接,或者是数字电路与模拟电路的临界处(仅)有一点短接。也有不共地的设计。
特殊信号线的处理
①内存布线
②时钟线(延长信号线来实现)
③防干扰线
④雨滴形布线,模拟电路在走线与焊盘连接处需要圆滑的过滤,同时也增强焊点的附着力。补线时,最好是走钝角或弧线。
信号线布在电(地)层上时,首先应考虑用电源层,其次才是地层。(最好是保留地层的完整性)
大面积导体中连接腿要做成十字花焊盘,称之为热隔离(heat shield)俗称热焊盘(Thermal)。
布线中使用的网格系统
标准元器件两腿之间的距离为0.1英吋(2.54mm),所以网格系统的基础一般就定为0.1英吋(2.54mm)或小于0.1英吋的整倍数,如:0.05英吋、0.025英吋、0.02英吋等。
(7)设计规则检查(DRC)
检查布线设计是否符合设计者所制定的规则,同时也需确认所制定的规则是否符合印制板生产工艺的需求,检查内容有以下几方面:
线与线,线与组件焊盘,线与贯通孔,组件焊盘与贯通孔,贯通孔与贯通孔之间的距离是否合理,是否满足生产要求。
电源线和地线的宽度是否合适,电源与地线之间是否是紧耦合(低的波阻抗)?在PCB中是否还有能让地线加宽的地方?
对于关键的信号线是否采取了最佳措施,如长度最短,加保护线,输入线及输出线被明显地分开。
④模拟电路和数字电路部分,是否有各自独立的地线。
⑤后加在PCB中的图形(如图标、注标)是否会造成信号短路。
⑥对一些不理想的线形进行修改。
⑦在PCB上是否加有工艺线?阻焊是否符合生工艺的要求,阻焊尺寸是否合适,字符标志是否压在器件焊盘上,以免影响电装质量。
⑧多层板中的电源地层的外框边缘是否缩小,如电源地层的铜箔露出板外容易造成短路。
4、CAM资料
拼板
把若干小板拼成一个面积符合生产要求的大板,或是把一个产品所用的PCB拼在一起而便于生产安装。
光绘资料
光绘图的资料格式有Gerber、Pentax、Dainippon—Screen、Muton等。我国最常用的是Gerber,其特点如下:
①资料码:ASCⅡ、EBCDIC、EIA、ISO码等。(常用:ASCⅡ码)②资料单位:英制、公制。(常用:英制)
③坐标形式:相对坐标、绝对坐标(常用:绝对坐标)。④资料形式:省前零、定长、省后零(常用:定长)
⑤资料格式:整数字元加小数字
常用:2,3(英制,整数2位,小数3位)
2,4(英制,整数2位,小数4位)
3,3(公制,整数3位,小数3位)
钻孔资料
钻孔资料格式有Excellon、Trudrill等各种格式,目前我国常用的是Excellon格式的钻孔资料。
①资料码:ASCⅡ、EBCDIC、EIA码等。(常用:ASCⅡ码) ②资料单位:英制、公制。(常用:英制)
③坐标形式:相对坐标、绝对坐标(常用:绝对坐标) ④资料形式:省前零、定长、省后零(常用:定长)
⑤资料格式:整数字元加小数字常用:2,3(英制,整数2位,小数3位)3,3(公制,整数3位,小数3位)
(3)裸板测试资料的基板构成
①每个测试点所属的信号名(或序号)。②组件腿的序号(或名称)及其在PCB上的坐标。
③组件在PCB板上的引用名(如U
1、R1……)。④被测试点所在的面,组件面(A)或焊接面(B)或二面都可以。
二、照相制版工艺
1、照相底版在印制板生产中的用途如下:
(1)图形转移中的感光眼掩膜图形,包括线路图形和光致阻焊图形。
(2)网印工序中的丝网模版的制作,包括阻焊图形和字符。
(3)机械加工(钻孔和外形铣)数控机床编程依据及钻孔参考。
2、印制板生产用照相底版需满足的条件:
照相底版的尺寸精度必须与印制板所要求的精度一致,并应考虑到生产工艺造成的偏差进行补偿。
(2)照相底版的图形应符合设计要求,图形符合完整。
(3)图形边缘平直整齐,不发虚;黑白反差大,满足感光工艺要求。
照相底版的材料应具有良好的尺寸稳定性,即由于环境温度和湿度变化而产生的尺寸变化小。
(5)双面板和多层板的照相底版,要求焊盘及公共图形的重合精度好。
(6)照相底版各层应有明确的标志和命名。
(7)照相底版片基能透过所要求的光波波长,一般感光需要的波长范围是3000—4000A。
激光光绘图机可绘制出线宽1mil(0.0254mm)或更细的线条;定位精度和重复精度达到+/-0.2mil(+/-0.005mm)。
3、光绘
使用光绘机直接将CAD设计的PCB图形资料送入光绘机的计算机系统,控制光绘机,利用光线直接在底片上绘制图形,再经显影、定影得到照相底版。
(1)向量式光绘机
①最具代表性的向量式光绘机为美国GERBER公司开发的系列光绘机,其使用的光绘资料格式GERBER RS-274格式已成为印制板设计生产行业的标准资料格式。向量式光绘机均为平台式光绘机,曝光焊盘时采用闪光曝光(Flash)方式,用高压氙灯作为光源;曝光线条时采用移动曝光方式,用钨灯作为光源。
②向量式光绘机不足之处
A、受到符号盘数量限制,一个码盘只有24个符号盘,最多的也仅有50多个符号盘,在设计印制板时,焊盘和线条的尺寸就受到了限制。
B、设计者在设计印制板时,必须和生产部门进行协调,使用光绘机现有符号盘,
否则设计出的印制板将无法绘出。
C、由于采用非激光光源,当聚焦不好时,常出现边缘发虚的问题;当符号盘的尺寸变化较大时,就如同照相机的光圈作了很大调整,容易造成尺寸大的图形曝光过度而尺寸小的图形却曝光不足。
D、采用光源和放置底片的平台在X、Y方向交叉移动方式进行光绘,其光绘速度
受到机械运动速度的限制。
(2)扫描式光绘图机(激光光绘机)
按照激光绘图机的结构,可以分为平板式、内圆桶式(Internal Drum)和外滚桶式(External Drum)激光绘图机。
①平板式光绘图机,代表产品美国GERBER公司的MODEL 20、加拿大ESCHER GRAD公司的EG-2200。
A、优点:a底片是平放在台面上,易吸平。 b振动小,驱动装置故障率低。 c有的激光绘图机有精度反馈检测装置,可使Y方向的精度很高。
B、缺点:在X方向不能做得太大,X方向尺寸越大,失真也就越大。
②内圆桶式激光绘图机,代表产品为美国GERBER公司的Crescent。
内圆桶式激光绘图机绘制的底版,可以达到很高的分辨率(1/4mil),绘制一张24*30英吋的底版只需5分钟。
③外滚桶式激光绘图机,代表产品为以色列ORBOTECH公司的LP5008。
A、缺点:a振动大,需要常调整;而且要功率较大的真空泵,才能把底片吸平。 b32束光素与另一个32束光素之间的连接有时可能要产生误差。
(3)光绘资料格式
光绘资料格式是以向量式光绘机的资料格式Gerber资料为基础发展起来。发展了激光绘图机后,兼容了HPGL惠普绘图机格式,Image2000,GASK,AOI Image,DXF,TIF等专用和通用图形资料格式。Gerber资料的正式名称为Gerber RS-274格式。向量式光绘图机通过D码来控制、选择码盘,绘制出所要求的图形。以典型的Protel的D码表为例,此类D码表为ASCⅡ文件,可用任何非文本编辑软件进行编辑,文件扩展名为.APT
D10 CIRCULAR 8 8 0 LINE
每行定义一个D码,包含有6种参数:
①第一列为D码,由字母“D”加一数字组成。
②第二列为该D码代表的符号的形状说明,如CIRCULAR表示该符号的形状为圆形。
③第三列和第四列分别定义了符号图形的X方向和Y方向的尺寸,单位为mil。
④第五列为符号图形中心孔的尺寸,单位也是mil。
⑤第六列说明了该符号盘的使用方式,LINE表示这个符号用于划线,FLASH表示用于焊盘曝光,MULTI表示既可用于划线又可用于曝光焊盘。
(4)Gerber RS-274格式中的命令说明:
D01 开快门 G36/G37 区域填充开/关 D02 关快门 G54 更换码盘,允许在光绘过程中更换整个码盘
D03 曝光焊盘 D09 同D03 G55 照相曝光模D10—D999选择符号盘 G56 描绘图形符号
G01 直线差补系数1× G57 显示符号 G02 顺时针绘圆弧 G58 显示并辉符号
G03 逆时针绘圆弧 G60 直线差补系数100× G04 放弃当前数据块,在下一数据块
G70 英制资料中如没有有效命令,则恢复至G01 G71 公制资料 G10 直线差补系数10×
G74 禁止360度圆弧差补 G11 直线差补系数0.1× G75 允许360度圆弧差补 G12 直线差补系数0.01×
G90 绝对坐标方式 G20 同G02 G91 相对坐标方式 G21 同G02
M00,M01 选项停止 G30 同G03 M02 程序结束 G31 同G03 M30 磁带结束/倒带Gerber资料是由一些X、Y坐标,句柄和分隔符组成:
① X------Y------ 表示光绘机移动的位置 ② * 为分隔符
4、CAD和CAM
印制板CAD(计算机辅助设计—Computer Aided Design)系统按照其软件运行的硬件平台区分可以分为工作站(Work station)CAD系统和微机(PC)CAD系统。
印制板CAD设计生产流程图:
提取网络表
修 改
工作站CAM(计算机辅助制造—Computer Aided Manufacturing)系统中著名的有以色列Orbotech公司和美国Gerber公司及Scitex公司的产品。CAM系统的主要功能如下:
1 编辑功能
a添加焊盘、线条、圆弧、字符等元素 b改变焊盘、线条尺寸 c移动焊盘、线条、字符等
d删除各种图形,自动删除没有电气联接的焊盘和过线孔 e生成水滴焊盘 f阻焊漏线自动处理 g网引字符盖焊盘自动处理
2 自动布线规则检查(DRC)在完成DRC后,3 可以自动修改有问题的设计。
4 拼板、旋转和镜向
5 添加电镀夹片、内层排胶条和测试图形
6 添加各种定位孔
7 生成数控钻床钻孔资料和铣外形资料
8 生成光板测试模板钻孔资料和网络表
9 计算导体铜箔的面积
照相制版的计算机辅助制造技术实用化是由CAM软件和激光绘图机共同完成的。
5、重氮片
重氮片是一种非银盐感光材料,是将一层非常薄的含有重氮盐的光敏物质及有色染料耦合剂和酸性稳定剂,涂复在聚酯基片上构成的。
氮片成为主要生产片的优点:
①分辨率高。重氮盐的分子颗粒只有1.5毫微米,其分辨率可以达到1000线/mm。 ②明室操作。重氮片的感光波长范围是紫外光(300—450毫微米),感光速度比干膜慢5—10倍,可以在普通灯光线下曝光和显影。
③显影方便。通常在60—66℃的氨水蒸汽中显影,不需定影,没有过显影问题。显影时底片最少要经过显影机两次,以保证完全显影;显影后不需要再经冲洗或干燥。
④容易对位。重氮底片一般透可见光,可以透过底片与钻过孔的印制板直接对准。
(2)重氮片使用注意事项:
①重氮片在未曝光前,不应长时间曝露在含氨的空气中。
②重氮片在未显影前,不要长时间曝露在灯光下。
③重氮片和重氮底版在保管和使用时,绝对不能接触乙醇等有机溶剂。
④重氮底版修版时,应用专用的修版料,否则会不遮光或易脱落。
⑤重氮片显影时,温度不能太高。
6、照相底版的检验
(1)照相底版的检测一般采用目检
照相底版的外观检验。应用肉眼(标准视力,正常色感)在最有利的观察距离和合适的照明下,不用放大进行检验。定性检查照相原版的标记、外观、工艺质量和图形等。
细节和细节的尺寸检验。细节检验一般使用线性放大约10倍或10倍以上的光学仪器,使用透射光检查是否有导线缺陷和导线间是否有脏点。细节尺寸检验应使用带有测量刻度并可进行读数的线性放大约10倍或线性放大约100倍的专用光学仪器,仪器的测量误差不能大于5%,在检验大于25毫米距离的尺寸时,可以使用带有精密刻度的网格玻璃板。
光密度的检验。光密度指透射光密度,检验时可以使用普通光密度计测量透明部分和不透明部分,测量面积为1mm直径。
(2)照相底版的尺寸稳定性
环境温度和相对湿度是影响照相底片尺寸变化的两个主要因素,底片的尺寸越大,总偏差就越大。
①底片尺寸变化与温、湿度的关系
保持偏差在1mil(0.0254mm)的底片尺寸 温度变化范围 相对湿度变化范围
10″ 254mm ±4℃ ±9%
20″ 508mm ±2℃ ±4.5%
30″ 762mm ±1℃ ±3%
40″ 1016mm ±1℃ ±2%
注:如果环境温度和相对湿度同时发生变化,则表中保持偏差在1mil内的底片尺寸应减小一半。厚胶片(0.175mm—0.25mm)对环境变化的敏感程度比薄胶片(0.1mm)小一些。
②未开封的原装底片,应保持在相对湿度50%,温度20℃的条件下储存和运输。
③底片使用之前,应对底片作尺寸稳定处理,即:将底片开封,去除内包装,使之与环境空气接触24小时以上。底片曝光、冲洗后,也应对底片作尺寸稳定处理,使其尺寸恢复到偏差允许范围内。
④使用照相原版复制生产底片时,应先检查照相原版的尺寸,复制完成后再对复制的每一张底片进行检查,在环境中放置一段时间,以保证底片的尺寸稳定。复制过程中如使用了“中介底片”则必须保证中介底片在恢复到所要求的尺寸范围内后,再翻制下一代底片。
⑤使用生产底片晒像生产时,由于灯光的热度,在多次曝光后。也可能使胶片变形,就应停止使用已经变形的底片,待其尺寸恢复后再用。晒像定位应尽量采用四槽定位,在底片发生变形时,可以使尺寸偏差向四面分散。
第三章 多层板压合
概述
1、多层板的优点:
(1)装配密度高、体积小、重量轻; (2)各组件(包括元器件)间的联机减少,提高了可靠性;
(3)可以增加布线层,从而加大了设计的灵活性; (4)能构成具有一定阻抗的电路;
(5)可形成高速传输电路; (6)安装简单、可靠性高。
(7)可设置电路、磁路屏蔽层,可设置金属芯散热层以满足屏蔽、散热等特种功能需要;
2、多层板的缺点:
造价高;(2)技术难度大;(3)周期长;(4)需高可靠性的检测手段。
3、多层板制造工艺的独特方面
专用材料;(2)定位系统;(3)层压;(4)钻孔和去环氧腻污。
二、多层板专用材料
1、薄覆铜板层压板
主要是指用于制作多层印制板的聚酰亚胺/玻璃、BT树脂/玻璃、氰酸酯/玻璃、环氧/玻璃等类型的薄覆铜箔层压板。它与一般双面板相比,具有以下特色:
厚度公差更严;
尺寸稳定性要求更严、更高,裁剪方向的一致性要注意;
薄覆铜箔层压板强度低,易损伤折断,在操作和储运中需格外小心;
多层板的薄线路板总表面积大,其吸潮能力比双面板大得多,要求材料在储存中应加强除湿、防潮措施,在其后的层压、焊接和存放中亦应如此。
2、多层板用预浸渍材料(俗称半固化片或粘结片)
预浸渍材料是由树脂和载体构成的一种片状材料,其中的树脂是处于B-阶段。
多层板用半固化片必须具有:
均匀的树脂含量; 非常低的挥发物含量; 能控制的树脂动态粘度;
均匀、适宜的树脂流动性; 符合规定的凝胶时间。
外观质量
应平整、无油污、无外来杂质或其它缺陷、无破裂和过多的树脂粉末,但允许有龟裂纹。
特性
1 层压前的特性
树脂含量(%)
流动性(%):≤20%无流动型、21~30%低流动型、31~45%中流动型、>50%高
流动型
挥发物含量(%)
凝胶时间(S):A(20~60秒)、B(61~100秒)、C(101~150秒)、D(151~
200秒)
2 层压后的特性是指3 按生产厂推荐的工艺参数压制成标4 称厚度为0.8mm的层压板的电气、热冲击和可燃性等项特性。
5 选择半固化片的原则:在层压时树脂能填满印制导线间的空隙;能在层压中排除叠片间空气和挥发物;能为多层板提供必须的树脂/玻璃布比率为基础,同6 时要考虑到层压板尺寸、布线密度、层数和厚度等实际情况。
A.预固化程度低的树脂,其原始粘度也小,受压后易外溢;
B.层压时挥发物将因受热而从树脂中逸出,并推动树脂一起外流;
C.层压时树脂的流失(B%)与半固化片的原始树脂净厚度(h。)和层压时某一瞬间的树脂净厚度(h)有如下关系:B=(1-h/h。)×100%
D.当树脂熔融粘度低时,粘结层的厚度主要是由玻璃布的厚度决定的;在树脂熔融粘度高时,粘结层的最终厚度主要是由半固化片中的可流树脂量来决定的。
半固化片的存放
7 温度在10~21℃范围内
8 湿度对半固化片的影响
A.在大气环境中存放将会使半固化的挥发物含量增加。
B.在相对湿度为20~40%下存放时,流动性稍有增加;在相对湿度为40~70%下存放时,流动性大幅度增加;在相对湿度为70~90%下存放时,流动性仅有轻微的增加趋势;在相对湿度为90%下只需放置15分钟,流动性就会显著增加,再继续延长存放时间,增值就不明显了。
C.粘性时间短(B阶程度高)的半固化片,其流动性对湿度的敏感性也大;粘性时间长(B阶程度低)的半固化片湿度对其的影响也小。
D.湿度对凝胶时间的影响不大,常为±5秒的测量误差所掩盖。
使用注意事项
①进行层压时,操作者必须戴上洁净的棉纱手套或尼龙手套,以防止手沾污粘合面。
②由折叠造成玻璃布断裂,层压中半固化片将会由于树脂的高压流动而从断裂处被整个撕裂,此种半固化片严禁使用。
③批号不同的半固化片不能混合使用,除非它们具有相同的预固化、流动性。
三、定位系统
电路图形的定位系统贯穿于多层照相底版制作、图形转移、层压和钻孔等工艺步骤,有销钉定位和无销钉定位两种方式。整个定位系统的定位精度应争取高于±0.05mm,其定位原理为:两点定线、三点可定面。
1、影响多层板间定位精度的主要因素有:
照相底版的尺寸稳定性;
基板的尺寸稳定性;
定位系统的精度;
加工设备精度,操作条件(温度、压力)和生产环境(温度和湿度);
电路设计结构,布局的合理性,如埋孔、盲孔、贯通孔、焊盘大小、导线布局均匀性、内层图形边框设置等;
层压模板与基材的热性能的匹配性;
参考资料:FR-4的热膨胀系数为13~15PPM/℃;不锈钢A1S1 300或A1S2 400热膨胀系数为11~16PPM/℃;
42CrM04不锈钢热膨胀系数在20~300℃时为12.9PPM/℃。
2、多层板的销钉定位法
两孔定位
由于在X方向上受到限制,往往在Y方向上产生尺寸“飘移”。
一孔一槽定位
在X方向上一端留有余隙,避免Y方向上尺寸的无序“飘移”。
三孔(呈三角形分布)或四孔(呈十字形分布)定位
防止生产过程中在X和Y方向上的尺寸变化,但由于销钉和孔的紧配合而使芯片基材在“锁定”状态下成型,由此产生的内应力会造成多层板的锅底和翘曲。
四槽孔定位
此种方法是由美国Multiline公司推出,是以槽孔的中心线为定位基准,因此由诸种因素造成的定位误差可以均匀在中心线的两边,而不是积累在一个方向上
第四章 数控钻孔
一、影响钻孔加工的六大要素
1、钻床
(a)数控钻床的刚性与振动。 (b)钻轴的刚性、振动与转速。 (c)位置精度与重复定位精度。 (d)Z轴进给速率。
(e)弹簧夹头精度。 (f)吸尘器。 (g)空压机气压和气量适宜,无水、无油。
2、钻头
(a)钻头的种类与几何形状。 (b)材质。 (c)拿刀与放刀。 (d)精度。 (e)表面粗糙度。 (f)重磨次数。
3、工艺参数
a.加工方法与切削条件。 B.切削速度即转速。 C.进给。 d.待加工板的层数与每叠板的块数。 E.分步加工法。
4、上、下垫板
a.材质与硬度。 B.均一性。 C.热容量。 D.变形、弯曲与翘曲。 E.厚度及公差。
5、加工板材
A.板材种类,材质厚度与铜箔厚度。 B.层结构,方向性。 C.树脂含量。 D.均匀性。 E.变形与翘曲。
6、加工环境
A.操作者的熟练程度与工作经验。 B.装、夹水平及固定程度。 C.温度、湿度。 D.照明。 E.外力与振动。
F.管理、检验、搬运。
二、数控钻床
1、PCB生产对数控钻床的要求:具有高稳定性、高可靠性、高速度和高精度。
2、数控钻床的钻轴分两种:一种是空气轴承的钻轴,最高转速11万转/分,甚至高达12万转/分。另一种是滚动轴承的钻轴,最高转速可达80000转/分。
3、数控钻床特性与参数项目。
A.钻轴数。 B.工作台面尺寸(最大加工面积)。 C.工作台速度。 D.定位精度。E.重复定位精度。 F.综合钻孔精度。 G.反馈系统。 H.钻轴间距。I.适用钻头直径。 J.自动换刀数。 K.控制系统。 L.驱动系统。M.钻轴类型。 N.钻孔速率。 O.压缩空气气压。 P.电源功率。
三、钻头
1、钻头的种类与结构
印制板钻孔用钻头有直柄麻花钻头、定柄麻花钻头和铲形钻头。
直柄麻花钻头大都用于单头钻床,钻较简单的印制板或单面板,钻孔深度可达钻头直径的10倍。在基板叠层不的情况下,使用钻套可避免钻偏。
定柄麻花钻头能实现自动更换钻头,定位精度高,不需要使用钻套。大螺旋角,排屑速度快,适于高速切削。在排屑槽全长范围内,钻头直径是一个倒锥,钻削时与孔壁的摩擦小,钻孔质量较高。钻柄直径有Ф2㎜,Ф3㎜和Ф3.175㎜三种。钻头直径小于Ф3.175㎜的是Ⅰ型,直径Ф3.2㎜~Ф6.35㎜是Ⅱ型。
铲形钻头的特点是棱刃(付切削刃)的长度只有0.6㎜~1㎜(取决于钻头直径),其余的棱刃被磨去。钻孔时,只有钻头顶尖一小部分承担钻削,与孔壁摩擦非常小,因而热量的累积也很少,较少产生腻污,适于多层板钻孔。
2、硬质合金麻花钻头结构尺寸与形位公差(IPC-DR-570)
名称 Ⅰ型钻头 Ⅱ型钻头
钻头直径公差 d +0/-0.0127㎜ d +0/-0.0127㎜
钻头切削刃长度公差 I +/-0.381㎜ I +0.762㎜/-1.148㎜
钻柄直径公差 D +0/-0.0762㎜ D +0/-0.0101㎜
总长度公差 L +0.127㎜/-0.381㎜
倒锥公差 切削刃长度内直径公差0.0051~0.0127㎜
钻心锥度 切削刃长度内锥度0.51㎜
刃背宽度角 64°±2° 70°±2°
肩部角 19° 无
螺旋角 35°±2° 28°±2°
顶角 130°±2° 165°±2°
第一主后角 15°±2° 12°±2°
第二主后角 30°±3°
排屑槽面粗糙度Ra 0.2μm或更小
第一主后面粗糙度Ra 0.1μm或更小
棱刃面(付后面)粗糙度Ra 0.15μm或更小
钻头(切削刃)对钻柄的不同心度 0.0127㎜
两条主切削刃的不对称度 0.0152㎜
表面缺陷 检查时规定的放大倍数
φ0.32~φ1.50㎜放大40倍
φ1.55~φ3.1㎜放大30倍
>φ3.1㎜放大20倍 主切削刃一
3、正确使用钻头之方法
钻头应装在特制的包装盒里,避免振动和相互碰撞。
使用时,从包装盒里取出钻头应随即装到主轴的弹簧夹头里或自动更换钻头的刀具库里,用完随即放回包装盒里。
测量钻头直径要用工具显微镜等非接触式测量仪器,避免切削刃与机械测量仪接触而被碰伤。
钻头装到主轴上的伸出长度要调整一致,多主轴钻床更要注意这一点。
用40倍立体显微镜检查钻头切削刃的磨损。
要经常检查主轴和弹簧夹头的同心度。
定柄钻头在弹簧夹头上的夹持长度为钻柄直径的4~5倍才能夹牢。
要经常检查主轴压脚。压脚接触面要水平且与主轴垂直。基板叠层包括上、下垫板要在钻床的工作台上的一孔一槽式定位系统中定位牢、放平。使用胶粘带将叠板四周粘牢在工作台面上,以减少钻头折断并防止切屑进入叠层或下面。要防止钻胶粘带使钻头粘附切屑,造成排屑困难。
新钻头入厂检验时要抽检其4%是否符合规定。并100%的用10~15倍的显微镜检查其缺口、擦伤和裂纹。
(10)钻头适时重磨,可增加钻头的重磨次数,延长钻头寿命。在两条主切削刃全长内,磨损深度应小于0.2㎜,重磨时要磨去0.25㎜,当磨损直径与原直径相比较减少2%时,则钻头报废。
三、上、下垫板
(一)上垫板
1、对上垫板的要求
有一定表面硬度,但又不能太硬。 不含树脂成份。 导热系数大。 有一定的刚性及弹性。
2、目前普通双面板钻孔常使用的上垫板主要是0.3~0.5㎜厚的酚醛纸胶板、环氧玻璃布板和铝箔。
3、高质量多层板的上垫板可采用0.35㎜厚的复合上垫板:上、下两层是0.06㎜的铝合金箔,中间层是纯纤维质的芯。
4、钻小孔和钻SMT或FPT板的孔,可采用0.16㎜的薄型复合上垫板,其特点如下:
防止钻孔上表面毛刺,不管孔径如何,允许毛刺高度的极限是0.008㎜(8μm)人手能感到的最小毛刺高度是0.015㎜。
护覆铜箔层压板。 (3)不折断钻头。 (4)提高孔位精度。 (5)冷却钻头,降低钻孔温度,不腻污孔。
(二)下垫板
1、对下垫板的要求。
硬度适宜。 树脂含量或其它杂质成份含量少。 固化程度好。平整度好,不变形,不吸水。
有利于钻头散热或能冷却钻头。
2、目前常使用的下垫板主要是高密度纤维板。
3、高质量多层板的下垫板可采用铝合金箔波纹板作下垫板,其结构是:两面是铝合金箔,中间是铝合金波纹板,胶接而成平整,光滑的复合板。
四、钻孔工艺参数
钻孔工艺参数主要包括切削速度,进给和每只钻头的钻孔数。
1、切削速度
切削速度是指钻头外径的线速度,其计算公式如下:
d:钻头直径(mm)n:主轴转速(rpm)
理想的切削速度是钻头横刃与主切削刃磨损程度相同。如果横刃磨损太快,表明切削速度太低;如果主切削刃靠近外径之处磨损太快,表示切削速度太高。
2、进给
进给表示钻头在单位时间内钻进材料的深度,其计算公式如下:F=nf(㎜/min)
f: 进给转速比(㎜/r) n: 钻头的转速(r/min)
进给转速比f表示每一转的进刀量。允许的最大进给转速比约为钻头直径的13%,一般取钻头直径的5~7%,高速钻孔时取10~12%;f的取值范围为0.02~0.2㎜,当f0.2㎜时,不仅钻孔质量低劣而且易断钻头。
3、钻头的钻孔数
一只钻头的钻孔数与被钻材料的种类,采用的切削速度和进给、钻孔质量有关。
多层板:每钻500孔刃磨一次,允许磨2~3次,每钻1000个孔可刃磨2次。
双面板:钻3000个孔刃磨一次,然后钻2500个孔,再刃磨一次钻2000个孔。
刃磨后的钻头应在四氯化碳中用超声波清洗,清除粘附在钻头上的环氧树脂和切屑。
五、钻孔中需注意的一些重要问题
1、钻床X、Y伺服系统通电和钻轴预热时间要长些,使钻床处于稳定状态。
2、每个钻轴的压脚垫要调整到比钻头长出1.3㎜左右;压脚压力为21~42N/㎝2,钻头直径小于0.5㎜时,应使用刚性压脚垫。
3、吸尘器的抽气量每轴约为0.8m3/min。
4、钻轴的径向跳动量应定期测量;对钻φ0.5㎜以下的小孔,跳动量为0.012㎜以下。
5、双面板叠层厚度约为钻头直径的5倍,多层板叠层厚度约为钻头直径2~3倍。每叠多增加一层覆箔板,钻孔偏差将增加0.01㎜以上。
6、定位采用一孔一槽式定位系统,钻孔板四周用胶粘带将其四周粘牢,防止粉尘进入叠层中,产生毛刺。
7、各钻孔参数(上、下垫板,叠层厚度及转速、进给、每只钻头的钻孔数)要经过试验证明是合理的,钻小孔时还要选择退刀速度。
8、多层板钻孔宜使用铲形钻头。钻头穿透叠层,排屑槽要超出叠层上表面0.8㎜以上。
六、钻孔参量对孔的影响
钻孔参量 对 钻 孔 的 影 响
孔眼
腻污 孔内
粉屑 钻头温度过高 钻头过度磨损 钻头折断 钉头
毛刺 孔壁撕裂 分层 钻头
晃动 孔位置精度
钻头切削速度 ○ ○ ○
进给 ○ ○ ○ ○ ○ ○ ○ ○
转速降低 ○ ○
叠层高度 ○ ○ ○ ○ ○
钻孔数(1只钻头) ○ ○ ○ ○
上垫板材料 ○ ○ ○ ○
下垫板材料 ○ ○ ○ ○ ○
印制板材料 ○ ○ ○ ○
钻头类型 ○ ○ ○ ○ ○ ○ ○
钻头几何形状 ○ ○ ○ ○ ○ ○ ○ ○
重磨钻头的清洗 ○ ○ ○ ○
压力脚压力 ○ ○
吸尘器真空度 ○ ○
钻轴径向跳动 ○ ○ ○ ○ ○ ○
孔内停留时间 ○ ○ ○ ○
机床速度变化 ○ ○ ○ ○ ○
机器(X和Y)不稳定 ○
机器定位精度 ○
叠层定位压紧 ○ ○
层压板固化 ○
七、印制板钻孔的质量缺陷
印制板钻孔的质量缺陷,分为钻孔缺陷和孔内缺陷。孔内缺陷又分为铜箔缺陷和基板缺陷。
1、钻孔缺陷
有偏孔、多孔、少孔和孔径错,以及断钻头、堵孔、未钻透。
2、孔内缺陷
(1)铜箔缺陷
①分层:与基板分离。 ②钉头:内层毛刺。 ③腻污:热和机械的粘附层。④毛刺:钻孔后留在表面的突出物。
⑤碎屑:机械性的粘附物。 ⑥粗糙:机械性的粘附物。
(2)基板缺陷
①分层:基板层间分离。 ②空洞:增强纤维被撕开而留下的空腔。 ③碎屑堆:堆积在空腔里碎屑。
④腻污:热和机械的粘附层。⑤松散纤维:未粘结牢的纤维。 ⑥沟槽:树脂上的条纹。⑦来复线:螺旋形凹槽线。
第三章 总流程介绍
多层板
⑪金手指板
开料→内层→压合→钻孔→一铜(PTH)→干膜→二铜 →防焊→金手指→喷锡→成型
⑫喷锡板
开料→内层→压合→钻孔→一铜(PTH)→干膜→二铜→防焊→喷锡→成型
⑬化金板
开料→内层→压合→钻孔→一铜(PTH)→干膜→二铜→防焊→化金→成型
⑭抗氧化板(OSP)
开料→内层→压合→一铜(PTH)→干膜→二铜→防焊→OSP→成型
双层板
⑪LED
开料→钻孔→一铜(PTH)→干/湿膜→镍金→防焊(文字)→成型
⑫网络板
开料→ 钻孔→一铜→干膜→二铜 (去墨,蚀刻,剥锡铅) →防焊(文字)→成型
第四章 多层板各流程详解
第一节 开料
㈠开料流程: 分条机→裁切机→磨边机
IPQC管理项目:开料尺寸
检验辅助工具:千分尺.卷尺
第二节 内层
㈡内层:
多层电路板内层通常是使用薄铜箔基板,在其表面形成内层线路后完成内层板制作程序.
总流程:磨刷机→印刷机→曝光→显影→蚀刻→剥膜→烘干
⑪内层前处理机(磨刷机):
内层前处理的作用:提高光阻(药膜)与基材的结合力.
流程: 进料→脱脂→加压水洗(2道)→磨边→中压水洗→微蚀→加压水洗(5道)→吹干→ 烘干→出料
脱脂原因:因为PCB表面大多数都会有一层防氧化物以防止铜面氧化.
磨边.微蚀作用:去除氧化层获得清洁的金属面,并且粗化铜面提高后序附着力.
⑫印刷(光阻的涂布)
光阻主要用于线路图案的制作,内层线路制程使用时先将要保留的线路覆盖,再以蚀刻将不要的金属除去.制作线路的光阻主要有三种形式,它们各为感旋旋旋旋光性干膜.液态光阻.电着光阻.我司采用的是:液态光阻(湿膜).
液态光阻的优点:可形成很薄的厚度,因此解像表现较好.
光阻有:光硬化式的负型膜.光分解型的正形膜.我司采用的是正型膜.
注:完成光阻涂布后进行曝光前,若有尘埃于板面就会造成线路线形的缺点,所反应出来的是短/断路问题.因此除了操作的环境必须保有洁净度,我司采用的是无尘室进行管制.
⑬内层曝光:
流程:预烤泠却OK板→对位→曝光→静置→待显影
负型膜反应区是不溶性(我们所说的没有被光照射到的地方,在后序显影时将被显影液冲洗掉)
⑭内层: 显影,蚀刻,剥膜
流程:入料→显影(3段)→加压水洗→吸干→吹干→中检→蚀刻→循环水洗→吸干→中检→剥膜→加压水洗→酸洗→循环水洗→吸干→烘干→出料
A.显影制程的目的是:将曝光形成的选别影像,经过显影液的处理而显像出影像.显影液对于负型光阻曝光区有较好的溶解度,对此型则相反,这些可溶的光阻被显影液去除的动作就是显影的目的.
注: (我司采用的是水平显影会产生水滞效应—指板子在水平输送湿制程调备中一如蚀刻,进行上下喷洒蚀刻时,朝上的板面会积存蚀刻液而形成一层水膜,妨碍了后来所喷下来新鲜蚀刻液作用,及阻绝了空气中氧气的助力,造成蚀刻效果不足,其蚀刻比起下板面之上喷要减慢些)由于电路板上方有水滞效应,因此一般上方的喷压要比下方略大以排除水滞的影响,以平衡上下板面的反应速度达成一致.又由于整板的显影均匀度未必完全一致,同时显影时会有残膜回沾的问题,因此显影完成点一般都会设定在显影槽的60-80%间.
B.蚀刻的目的:将光阻未覆盖的金属区域蚀除.
注:因为蚀铜液会不断侵蚀线路侧面而显影侧向反应较慢,所以蚀刻完成点要比显影点更后面点,一般都会超过80%蚀刻槽长度.
♀♂㊣ C.蚀刻常出现的问题及其对策:
问题 产生原因 改善对策
蚀刻上下面不均匀 喷口被堵住 检查
喷口磨擦变大,喷击力不足 换新喷嘴
喷嘴所在的喷管管位或管方向不对 检查各喷管位置及角度并按厂商维护手册调整
输送带上滚轮轨迹有前后重叠现象 调整每枝转轴上滚轮前后参差
各喷管中流量调整不正确 检查每支喷管所呈现喷压,并作必要调整
喷管有漏水现象 常发生在喷管与输液接头处
蚀刻液面太低,导致空转或有空气进入 补充蚀刻液
蚀刻同一板面上局部不均匀 干膜显像或除膜没有彻底而留有膜渣 检查影响及显像液喷压,及调整其浓度速度及温度
棕色底片不良导致干膜制程发生膜渣 检查及修补底片上微孔,或更换用旧的棕片
干膜压膜前板面不够清洁 检查及改善清洁过程
镀铜厚度不均匀造成有的过蚀有的蚀刻不足 改善镀铜或改用性能更好的蚀刻液
过度蚀铜 由于喷嘴或喷管的角度不对,喷液有问题 调整喷管或喷嘴角度
喷压太强 正确喷压应该在20-30 PSI 之间
阻剂破损或浮起 调整喷压,同时要检讨清洁及显像之操作
板子在蚀刻机中行径不直不正 装机没有在水平状态 检查其水平
喷管不在应有的板直线上,导致板面上喷压不均 检查
输送带齿轮破损导致输送杆停动或动作不正确 换掉损坏齿轮
输送杆弯扭 换掉变形输送杆
上下喷压不平衡 当下压太大时,较轻的板子会被举起
**********************碱性含氨蚀刻液常出现的问题************************
蚀刻机中盐类结晶太多 碱性蚀刻液太低常在以下 注意补充槽中药液是否用完
注意药液补充管路是否堵住
检查控制补充控制器是否失效
检查抽风是否太强,导致氨气流失而损失蚀刻能量
蚀刻液失效,有结晶沉淀于槽底 蓄液槽中加水太多,导致PH下降蚀液水解 检查不正常的水源,如冷凝管破裂或板子本身带入水份太多等.
蚀刻率减慢,有时停放一段时间后会恢复快速,但不久又慢了 蚀液槽中吹气管被堵 蚀液中的氧气是蚀铜的必须品要设法吹入少量的空气并减少氨气的流失
阻剂剥落进入槽液中 蚀液的PH太高 某些干膜或UV硬化的阻剂当PH太高时将会剥离
过蚀 输送带速度太慢 检讨进行速度,铜厚度及蚀液三者之间的关系
蚀液的PH太高 高PH影响蚀速不大,但会增加侧蚀,可加大抽风以赶氨气使以降低PH值至正常的范围内
蚀液比重降至正常范围下 比重下降对蚀速影响不大,但却会造成较大的侧蚀,可加入铜浓度高的蚀液以提高比重减少侧蚀
蚀铜不足 输送带速率太快 调整
PH太低,低于操作范围 碱性含氨蚀铜液PH低时侧蚀会减少,但也带来蚀铜不足,故要调整至最佳状况
比重太高 在正常比重范围内,对蚀速影响不大但比重太高时,侧蚀会降低,也应该调整至其平衡点,添加无铜补充子液时可降低比重.
蚀铜温度不够 检查加温器是否损坏
喷压不足 调整喷嘴压力
*************************氯化铜蚀液之问题*******************************
氯化反应太剧使蚀刻机周围充满了氯气 ORP测头太脏 检查测头,如发现尖端有氧化物时,用橡皮擦拭
测头不标准 测头在装机时应该先校正
氯气源到蚀刻槽间的管路漏气 用浸过稀氨水的湿布沿沿管路附近移动,漏氯气处立即出白雾状的氯化铵即为明证
控制氯气流量电磁阀漏气 更换
蚀刻速率突然减慢 回收反应减慢或失效 如用氯气时检查出气管路有否结冻死,可用电风扇吹之使解冻/如用其他方式时,检查化学品槽是否用完或管路或电磁阀的问题
管路漏水致使蚀液稀释 蚀液比重是否下降,应在1.261-1.283,太低时表示有水漏入,要检查冷凝管及其他可能的来源
蚀速减慢 ORP设定的毫伏数太低 不可低于500毫伏,否则再生能量会不够
蚀液被漏水处或板子带入的水所稀释 检查漏水处,或在输送线中加装气幕或挤水的橡皮轮
比重太高 应维持在1.261-1.283间(55℃)
过蚀 输送速度太慢 调整
蚀液中盐酸太多 分析盐酸含量,并检查管路
比重太低 在55℃下检查其比重是否仍在上述范围,可增加含铜量以提高比重
蚀液发生过度再生 检查设定之ORP数据,应在500-540毫伏间.
蚀刻不足 输送速度太快 确定铜厚与输送速度关系
蚀液温度太低 调整
比重太高 加水稀释至范围内
喷压不够 检查液面是否太低,导致马达抽空或管路漏水
蚀液再生不足 检查ORP设定
*************************氯化铁蚀液之问题*******************************
蚀剂速率太慢 蚀液中已蚀铜饱和 换新液当液中铜量到达60g/l时即需换新
泡沫太多 添加剂太多或蚀刻液受到污染 品质好的氯化铁通常是不会造成泡沫的,可加入少许八碳醇类做消泡剂
蚀液呈土黄色并郁积黄泥堵住管路 系统中累积之氯化亚铁及氯化亚铜太多 添加体积量0.5%的粗盐酸使氯化成可溶物而除去
蚀速突然减慢 漏水冲淡蚀液 蚀液比重应该在1.381-1.408之间
过蚀 输送带速率太慢 调整铜厚与输送速率间的关系
蚀液中盐酸含量太高 正常的游离盐量应在0.1N以下,检查调整
蚀液比重太低 氯化铁蚀刻比重范围在55℃下应1.381-1.408间
蚀刻不足 输送速度太快 调整
温度不够 冬天应该加温以适应生产
比重太高 换掉蚀液
喷压太低 检查压力计.液面.及管路漏水
******************硫酸双氧水蚀液(多做为微蚀用)***************************
双氧水或过气化物消耗过度 液温太高导致过气化物分解 按厂高建议操作
化药储存环境温度太高引起过氧化物安定剂分解 改善环境或更换药品
蚀液受污染某些有机化物引起氧化物分解 板子进蚀液前要洗干净
锡铅线路有变黑现象 锡铅比例不对 注意锡铅电镀及镀层比例
蚀液中抑止攻击锡铅抑止剂不够 按厂商建议分析添加
蚀速减慢 浓度太低温度太低 分析进行补充,注意温度
硫酸浓度过高限制蚀铜 调整
铜量太高,接近饱和 将蚀液降温,使铜盐结晶冻出来
蚀液泡沫太多 专密添加剂过量 按正常量添加,以减少泡沫
蚀速太快 过氧化物或温度太高 分析过氧化物及检查温度
速率促进剂加入太多 注意添加量
局部反应过剧使其温度上升而加速蚀刻 搅拌蚀液使温度均匀
I.内层检查项目:a.内层线路方面:短断路,线路缺口,线路剥离,曝偏,间距不足,线细,铜渣,污染.b.树脂基材方面:基材破损,异物污染,气泡.c.树脂基材方面:镀层不良,破孔,孔内粗糙.
II.我司内层(L)产生问题有:刮伤.开路.掉墨.沙孔.缺口.内短.内开.曝光不良.对反/偏.露铜.残膜.残铜.蚀刻过度.显影不洁.油墨入孔.
III.内层板常出现问题原因及改善对策:
问题及可能的因素 对策
1.内层薄基板在输送带上被拉入受损
内层板之强度不够 @输送前用胶带贴一片硬板做为前导
@内层板应该有良好的板边溢胶补强设计
2.内层板烤不当造成板弯,或板边溢胶中气泡太多或分层
&支架不当造成板弯 @可用工具孔作挂烤
&内层板迭在一起烤 @无法把夹在中心的板子烤完全,应该分开
&烘烤时间不够 @应该在90-100℃中烤8小时以上
&内层板烤后又再吸水 @已烤干的内层线路板应该存放在干箱内或低温烤箱内等待压板
内层板尺寸不稳定造成多层板的板挠板扭
基板太薄磨刷过度造成伸张 @减轻磨子的压力(按基板厚度而定)
@减少其变形,以方便影像转移
&内层板板边溢胶(设计不当,溢胶不顺,形成应力,造成变形) @选择适当板边设计,改进溢胶
黑氧化处理不良,不均匀(只能用在环氧树脂)
&槽内浓度或温度不够 @按厂商资料改进
&内层线路上阻剂残渣未清除净 @加强黑化前前处理清洁
&前清洁及微蚀不良 @分析或更换槽液
&槽液不均匀 @加强搅拌
&因加热器绝缘不良(钢槽壁上形成迷走电流造成铜面的电化学腐蚀) @加强加热器绝缘
&液中浮有氧化铜粒子 @过滤除去
&处理时上架不妥 @做好间隔以利槽液流通
&处理浸渍时间不对 @通常时间太长,反行松驰黑化膜
红氧化或棕氧化处理不均匀
&槽液浓度不对 @按原厂资料去做
&前处理微蚀不良 @改善微蚀加强表面粗化
&氧化膜发展不均形斑痕 @入槽前用缄液预浸
&搅拌太猛导致灰色的碳酸盐在槽液上出现 @搅拌使空气中的二氧化碳与液的氢氧化钠形成碳酸盐膜,除此之处也可不用空气搅拌.
第三节 压合
㈢压合
总流程: (压合基准孔制作) →(压板前处理)棕化→组合→迭合→压合
⑪压合基准孔制作:
内层压合的主要固定模式有两种:以预先做好的插梢孔插入插梢来固定压合,这样的方式被称为插梢压合法.事先加工的对位孔以铆钉的方式将所有内层板固定压合,作业上比插梢压合操作简单出利于量产,因此而被称为量产式压合.
不论多层板以何种压合生产,多于一张内层板的电路板结构都会作出对位孔.而压板后则必须读出内层的基准记号,加工出钻孔所使用的对位基准孔.钻孔对位基准孔在内层作业时就已制作在内层板上,藉由机械读取及公差平均的过程,钻出适当的工具孔.由于压板后电路板会收缩,因此一般在内层设计都会做补偿以防止位置偏移,故工作底片在制作电路板前会预先将内层线路予以等比例调节.
⑫水平棕化线(压合前处理):
流程:入料→酸洗→循环水洗→清洁段→加压水洗→纯水洗→中检→棕化(预浸)段→棕化→加压水洗→纯水洗→吸干→ 烘干→收料
注:
酸洗目的:清洗铜面残留的氧化物,手指纹.循环水洗目的:将铜面残留药水用水清洗(水洗目的)
清洁目的:清洗铜面残留的氧化物,手指纹,油脂,有机物.预浸目的:防止污染物带入棕化段.
棕化段目的:将内层板铜面作氧化处理.
增加内层板与树脂接触的表面,加强二者附着力.
增加铜面对流动树脂之润湿性,使树脂能流入各死角而在棕化后有更好的抓地力.
在裸铜表面产生一层致密的钝化层,以阻绝高温下液态树脂中胺类对铜面的影响.:
⑬迭合流程:
送水承载盘→放牛皮纸→盖铜箔→迭内层板→铺铜箔→无尘布擦铜板→盖铜板→放挡板→放牛皮纸→盖上盖板
注:作用
放牛皮纸目的:缓冲压力.盖铜板:用来作内层板隔层.铺铜箔:用来作内层板增层用.放挡板:防止铜板滑移.
⑭压合流程:
入料→热压→执行程序→冷压→下料
热压:将内层板与胶片粘合.
I.内层(P)检验缺点:刮伤.凹点.凹陷.板厚薄.尺寸不符.棕化不良.铹坏
II.压板制程常出现的问题原因及对策
(1).缺点名称:板内异物
造成原因:外层板所看到的板内异物多数都是从压板制程中压入的,如果是非金属又不影响信赖度,基本上不是问题,但是从品质外观角度来看仍是缺点.它的主要来源有两个:1.叠板中异物掉落进入板中.2.打铆钉时金属粉掉入.
解决方案:对于板内异物的改善,必须注意压板时的环境控制及操作动作,只要环境及操作有改善,板内异物是可以降低的.可能解决的方案如后:
1.对叠板的作业,要避开容易产生直接掉落灰尘的动作,避免在叠板区的上方作业.机械的设计,有摩擦的区域要尽量设计在操作台以下,如果必须设计在操作台上,必须有包覆的设计.作业人员必须穿戴标2.准的服3.装及手套,环境必须管制严谨,否则异物很难改善.
4.多数的量产型电路板厂,都使用金属铆钉作内层板固定作业,但是在打铆钉时金属粉削很容易产生回跳现象且不5.易察觉,要改善此问题可以考虑改用不同6.的操作方式或不同7.的铆钉材质.
(2).缺点名称:片状气泡
造成原因:所谓的片状气泡不同于织纹式的气泡,它的区域涵盖了多个织纹的交叉点,成整片的形状,因此称为片状气泡.主要问题是因为基材的结合力不佳造成材料分离,它的可能成国如:1.内层板粗化处理不良.2.基材胶片的树脂涂布不良 3.胶片的挥发物过高,造成遇热膨胀分离.
解决方案:针对以上主要问题提出以下解决方案:
1.粗化处理以往都是用黑化制程,但是控制并不2.容易,近来不3.少的棕化制程出现,可以改善内层铜墙铁壁的表面状态.
4.一般玻璃布都会在织布及烧灰后,在其表面涂布一层结合力促进剂,再进入树脂槽含树脂.如果接口处理不5.良,容易在受热冲击时产生材料崩裂,因此对供货商所采用的制作技术,电路板制造者也应关心.
6.一般胶片的挥发物含量都有一定的标7.准,如果过高就有可能在受热时产生膨胀分离的现象.小区域的状态就是片状气泡,这种缺点一样也要要求供货商改善.
(3).缺点名称:邹折
造成原因:压板邹折的问题,一般说来有两个主要的因素:1.铜皮叠合不平整造成邹折.2.树脂流动不均造成邹折.
解决方案: 针对以上主要问题提出以下解决方案:
针对铜皮叠合不平的问题,由于现在电路板的线路制作愈来愈细,多数已使用二分之一盎司以下的铜皮来制作,因为铜皮本身已相当薄,操作一不小心就会邹折,因此在操作上可以多下功夫.
树脂流动是压板必然的行为,但是如果内层的铜分布不均使树脂的流动性必须提高才能填充,这样的状态树脂会拉扯铜皮造成邹折,较有效的解决方法是在电路板的空地,在可能的状态下留下假铜垫,藉以降低树脂的流动量,同时在可填充完整的状态下,可以采用较低量树脂,如此邹折的问题应该可以降低.
(4).缺点名称:压板凹陷
造成原因:所谓的压板凹陷,就是在压板过程中有异物夹在铜皮与铜板间,在胶片热熔后异物的形状转移印在电路板表面所形成的凹陷.
解决方案:铜板与铜皮间的清洁度改善是主要的问题,有厂商使用载体铜皮,因载体接触电路板因此不会发生凹陷的问题.也有的厂商加强清洁动作,并将铜板先和铜皮结合,再送入叠板作业,以防止叠板操作中的落尘,降低压板凹陷.甚至有特殊的做法,将铜板当成载体先镀上一层铜,再作粗化处理成为压合用的铜皮,由于铜板与铜皮的压板前就完全结合,铜板又在电镀前完全清洗,因此只要铜板没有凸点,就不会有凹陷问题.
(5).缺点名称:板面白点/织纹显露
造成原因:玻纤布交织点处之经纬束出现上下分离情形时,相较于周围完整结构的区域,会呈现色泽较淡或白色点状者,称为”白点”(Measling).如果是表面纤维树脂不足或被化学品侵蚀则会在表面呈现白色十字点,这种现象则应该称为织纹显露,其成因不同于是板面白点缺陷.基要主成因如:1.玻纤表面处理不良造成板内部局部分离.2.电路板处层经过多次的化学制程,表面的环氧树脂被侵蚀造成玻纤外露.
解决方案:针对可能的原因解决对策如下:
基材内的玻纤是由许多根玻纤丝制成玻纤纱,再编织玻织布前会做”上浆”处理,以减少编织的摩擦损伤.织布后用高温焚化法将有机浆料烧掉,称为”烧洁”.清洁后的玻织布后,会做”硅烷偶合处理”,以增加树脂与玻织间的结着力.由于玻织布与树脂之物性相差很大,常会在高温处理中因膨胀系数不同而造成分离.硅烷处理即在其间增加化学键,以改善接着力减少分离的风险.但是玻璃布外表容易处理,其内部及交叉处则因硅烷处理剂不易进入,浸泡树脂时也不易浸润,较容易出现瑕疵.这些区域由于容易残存空隙,一旦板材吸入较多水气及受到较大的热应力时,即常出现分离而呈现白点.改善的方式是在烧洁时必须确实完整,硅烷处理时必须浸润确实,玻璃布浸泡时其参数必须调整,某些时候降低处理速度或作多次处理都会减少缺点的发生有所帮助.
压板过程中叠板所选用的胶片会随设计不同而调整,一般制作者未使操作简便且费用低,常使用单张胶片作叠合动作.问题是单片胶片不但有可能压合密合度不佳,也有可能胶量不足使电路板表面胶量极低,这样就容易产生”织纹显露Weave exposure”的问题.如果压板所用的参数较差,升温过快或压力过大也有可能造成树脂流动过大,表面过薄造成织纹显露,多数的电路板目前仍以环氧树脂为主要的树脂系统,双氧水、剥锡液等经过长时间浸泡,都会浸蚀树脂。这些都是织纹显露的主要原因,针对这些因素显而易见的改善方法是,选择恰当的胶片组合以提供足够的树脂,压板时避免过大的树脂流动,生产电路板时减少重工的机会以免树脂被浸蚀。
第四节 钻孔
⑪钻孔机作业流程:
双面板:
生管下料→裁板→上PIN→备针→贴铝板→程序输入及处理→上机→设定坐标→钻孔→检查→下机→退PIN→检查→PTH
多层板:
制前处理→选定模板→备板→程序输入及处理(内层)→ 设定坐标→钻PIN孔→上PIN孔→程序输入及处理(外层)→ 上机贴铝板钻→孔检查→下机→退PIN→检查→PTH
⑫操作条件
A.钻头转数:钻头外缘在线性速度可按下式计算:
周速(米/分)=钻头转数(rpm)×钻头直径×∏
1000
通常钻头的外缘周速在100-200M/MIN之间.而小孔钻孔机的转数也有其上限,通常在十万rpm左右,故操作时应该尽量不发生振动的良好转数下去进行钻孔,且应该时常加以检查及改善.
B.切削速度/转速
切削速度是指刀刃每分钟所移动(切削)的距离,即SFM=∏D×rpm/12切削速度直接影响钻孔温度,当切削速度增大时,钻孔温度也会增高,所产生沾污就越多,对钻头的磨损也越大.但切削速度越小时,则钻孔精度越差.切削速度是受主轴转速的限制(如表J)
钻头直径
主轴转速
80000rpm 110000rpm
0.10 25 5
0.15 37 69
0.20 50 86
0.25 63 103
0.30 75 120
0.35 88 138
0.40 100 155
0.45 113 172
0.50 125
C.进刀速度(mm/min):
凡钻头旋转一周而能刺入材料的深度,称不进刀速(Chip load),其计算如下:
进刀量Chip load(mm/Rev)=进刀速度(mm/min)
钻头转数(Rev/min)
小孔钻孔的进刀量以0.005-0.03mm/Rev(0.2-1.2 mil/Rev)左右较为适当,且孔径愈小,纵横比(Aspect Ratio)愈高时,其进刀量也应该愈低才对.
D.退刀速度(Retraction Rate)
90%的断钻头是发生在退刀过程中,因止为防止断钻头,钻小孔的退刀速度必须选好.若退刀速度慢,钻头与孔壁的摩擦大,产生的沾污就多.如果退刀速度过快,产生的阻力也很大,易导致断钻头毛刺和孔壁粗糙,对于钻小孔有必要采用小的退刀速度.钻小孔的钻孔参数对钻孔品质都有影响,一般钻小孔采用如下参数表:
孔径
(φMM) 主轴转数
(K RPM) 切削速度
(M/MIN) 进刀速度
(UM/REV) 退刀速度
(M/MIN)
0.15 80 38 10 2.5
0.20 80 50 14 2.5
0.25 80 63 17 2.5
0.30 80 75 21 3.2
0.35 80 88 25 4.0
0.40 80 100 28 5.0
0.45 80 113 30 6.0
E.迭板高度
F.盖板(铝片)及垫板
盖板作用:可以防止毛头的发生,并可提高孔位的精准度,且有散热及改进钻孔的品质.然而在钻小孔时,盖板却反变成了钻也的负担,成为钻头折损的主要原因.铝片的厚度为0.1-0.2mm左右.
垫板作用:当牺牲板避免钻针伤及钻孔平台,同时降低底部产生的毛边.但是为了减轻钻头的负担,其刺入的垫板的深度,以稍稍大于钻头半个真径为宜.
I.钻孔(D)检验缺点:刮伤.孔偏.漏钻.多孔.毛边.爆孔.塞孔.断针.孔不透.孔壁粗糙.孔大孔小.
II.钻孔工艺注意事项:
A.上PIN主要是起固定作用.
B.备针时钻头从小到大排,按照记录来挑(防止造成混乱).
C.贴铝片其作用可以防止毛头的发生,并可提高孔位的精准度,且有散热及改进钻孔的品质.
♀♂㊣ III.钻孔中常发生问题及处理
问题 产生原因 解决方案
孔位不正不准 钻头摇摆晃动 减少基板叠放的层次/增加转速减少进刀率/重磨及检查所磨之角度及同心度/注意钻头在夹头上的位置是否正确/退屑槽长度不足/校正及改正钻机对准度及稳定性.
盖板不正确 盖板应该均匀平滑并具有散热的功能
基板材料变形使孔位移位 注意材料在钻前钻后的烘烤稳定
定位工具系统不良 检查工具孔的大小及位置
程序带不正确或损伤 检查程序带及读带机
孔径有问题 用错钻头 钻头在上机前要仔细检查钻机的功能是否正确
钻头损毁 换掉并定出钻头使用的政策
钻头重磨次数太多造成退屑槽长度不足 明定钻头使用政策,并检查重磨之品质
主轴损耗 修理或换新
胶渣太多 进刀及转速不对 按材料性质做钻孔及切微片试验以找出最好情况
钻头面在孔中时间太长 改进转速及进刀率以减少孔中时间/降低叠板的层数/检查钻头重磨的情况/检查转速是否降低或不稳
底材尚没有澈底干固 钻孔前基板要烘烤
钻头之击数太多,以致退屑槽长度不足 限定重磨次数,超过了则废弃
盖板及垫板有问题 改换正确的材料
孔中有织维突出 钻头退刀速率太慢 增加退刀速率
钻头受损 重磨及限定钻头使用政策
钻头有问题 按钻头条件的改变及微切片检验之配合找出适合的条件
内层铜箔出现钉头
钻头退速太慢 增加钻头退刀速率
切屑量不正确 对不同材料做各种不同的切屑量试验以找出最正确的排屑
钻头受损 重磨钻头并定出每支钻头应有的击数/更换钻头设计
主轴速率不正确 做实验找出最好的切屑量/检查主轴速度之变异
孔缘口发生白圈 发生热机应力 换掉或重磨钻头/减少钻头留在孔中时间
玻璃纤维组织太粗 改换为玻璃较细的胶片
孔壁粗糙 进刀率变化较大 维持稳定的进刀率
进刀率太快 使用正确的转速及进刀率
盖板及垫板不正确 改换盖板及垫板
固定钻头之真空度不足 检查钻机之真空系统/检查主轴转速变化
毛头 钻头不利 换掉或重磨钻头/定出每支钻头击数
板与板之间有异物 改进板子上机的操作
切屑量不正确 使用正确的切屑量
盖板太薄,使上层之板发生毛头 改用较厚之盖板
压力不正确,使孔朝上之孔口发生毛头 修理钻机
垫板不正确,使孔朝下之孔口发生毛头 使用平滑坚硬的垫板/钻完一叠板后要换掉垫板
孔中有渣屑 盖板板或垫板不正确 更换
孔中有毛头挤住钻头 换掉盖板或垫板
固定钻头之真空度不够 检查钻机真空系统
钻头螺旋角度太小 更换钻头
板子叠放太多层 减少叠板之层数
钻孔条件不对 增加进刀率及转速
静电吸附 提高相对湿度至45%以减少静电的发生
孔形不圆 主轴有问题 更换主轴轴承
钻头上尖点偏心或钻刃高度不对 检查钻头或更换
板叠最上层处出现圈状钻屑附连 没有使用盖板 板叠最上层要加用盖板
钻孔条件不对 降低进刀速率或转速
钻头容易断裂 钻机操作不当 检查压力脚压紧时压力/调整压力脚与钻头间的各种关系/检查主轴转速变化/检查台面在操作时的稳定度
钻头有问题 上机检查钻头/注意退料槽长度是否够
进刀太快 降低进刀率
所钻之板叠层数太多 减少板叠层数
IV.钻头较小转速则要快,易于板面穿透,而进/退刀速不能过快,因为扭矩力加大;钻头较大则转速不能过快,防止有些边孔钻不干净,进刀速不能太快,因为孔径大易拉损铜皮,退刀速也不能过快.因为易使铜皮玻璃纤维过多溢出.
第五节 一铜
㈤一铜
总流程:前处理→DESMEAR→PTH→电镀一次铜→后处理
电镀铜作用:依靠电流把铜离子吸附在金属表面上.(化学沉铜是通过表面处理机化学反应而镀上铜)
一铜板标准要求
厚度(尤其是孔铜厚度)及均匀性.
板面不允许铜渣,凹陷.
孔内堵塞,孔内无铜不允许.
板面刮伤不允许.
⑪DESMEAR(除胶渣)
DESMEAR作用:用于处理多层板因钻孔所产生残留下来的胶糊(SMEAR),将内层与电镀孔铜能得以导通,并防止孔铜拉离,另一方面能使孔壁粗化,以利于后制程化学铜有更好的附着表面.
流程: 膨松槽→回收槽→双水洗→除渣槽→回收槽→预中和槽→双水洗→中和槽→双水洗
膨松槽:打断树脂胶渣本身的聚集结,将孔内的树脂及胶渣加以膨松及软化,以利于后制程高锰酸钾之咬蚀.
除胶渣剂:(碱性高锰酸钾溶剂).它能打断树脂系统中的链接,将已膨松软化的树脂胶渣予以去除.
中和剂: 去除残留于孔壁的二氧化锰及锰酸盐类物质,以利于后制程的进行.
⑫化学铜(PTH)
流程:整孔剂→市水洗→微蚀→市水洗→酸洗→市水洗→预浸→活化剂→市水洗→速化剂→市水洗→化学铜
PTH的主要作用:在孔壁上之非导体部份之树脂及玻璃进行金属化,以进行后来之电镀铜制程.
(A).各药水的作用:
清洁剂及整孔剂处理:主要是湿润孔壁并且脱泡(我司采用振动法脱泡)
微蚀:去除氧化活化钯用量.
预活化:为了防止水份带入活化槽.
活化处理:将钯吸附在孔壁树脂及玻璃上(采用震动法脱泡).
速化剂:把板子表面所吸附的活化胶将物的锡壳去除,使钯核能露出来而提高其活性.
化学铜:一般0.3-.-0.5U即可(主要完成孔壁导电作用).
(B).PTH注意事项:
a.按时按量添加药水(由专业人员添加)
b.不定期检检查各槽液水位是否正常,防止药水流入其它槽内.
c.上下料时要轻拿轻放,下料时要把酸浸,上下料都应该戴耐酸手套.
d.每班应该做一次背光试验.
(C).PTH常出现问题及处理:
问题点 原因 处理
背光不良 药水含量不足 分析药水含量并调正
板面起泡 微蚀不良 检查微蚀是否到更换期,化验其含量是否正常.
板面胶渍 加强PTH前检验动作
板面指纹 戴手套作业
板面颜色暗黄色 CU2+含量不足,反应高效率慢 加足够药水
孔破 孔径太小药水不易灌入 检查振动马达.摇摆是否正常
PTH后的板浸酸浓度过高或浸泡时间过久 化验药水浓度.及做到先进先出原则.
孔内有杂物 加强PTH前处理
⑬一次铜
电镀铜层的必要性,应该有良好的抗拉力.伸长率.均匀在厚度.细致的结晶等.
流程:上料→前处理(酸浸)→上槽→镀铜→下槽→下料
(A).电镀后做基本的外观检验,内容包括了镀层色泽.污染异物.凹陷或刮伤.短断路或缺口等等.
(B).一铜(J)检验缺点:刮伤.磨痕.水印.铜粒.镀层脱落.露基材.粗糙.黑孔.铜粒塞孔.烧焦.胶渍.孔内无铜.高孔.掉槽.镀层过厚
(C).镀一铜须注意事项:
a.根据化验结果添加足够药水致标准 b.上架必须夹紧,防止掉槽或导电不良
c.上下料必须戴耐酸手套,轻拿轻放 d.铜液面不得低于钛篮2/3,但也不能超过钛篮袋口.
(D).镀一铜发生问题及处理:
问题点 原因 处理
烧焦 电流过大 降低至合适电流
光泽剂缺少 做哈氏片添加光泽剂
靠近阳极 修理变形的挂具
搅拌不足 增加搅拌力度
硫酸浓度过高 稀释硫酸浓度
板面发红 光泽剂过量 电解活性碳过滤消耗光泽剂
液温过高 开冷却降温至正常
光泽剂不足 化验进行添加
板面颗粒 镀槽内有浮颗粒;加阳极铜有杂质进入槽液;液面高于阳极袋口;槽液遭污染 加强电解吸附掉在铜槽内铜渣,杂物;加强过滤遭污染的槽液应该换掉;排放多于的铜液.
氧化 板子在空气中太久遭氧化 酸浸放置
脱层 镀前板上有污染,杂物 加强前处理及检验
孔破 导电不良被槽内酸蚀咬掉 检查挂具镙丝是否松动,电流是否正常
PTH不良 改进PTH作业
凹点 铜槽液内空气搅拌不足 加强搅拌均匀
槽液遭油渍污染 加强活性碳处理及过滤
镀前板面不洁 加强前处理及检查
第六节 干膜
㈥干膜
总流程:前处理→压膜→对位→曝光→显影
⑪干膜刷磨机(前处理)
流程:入料→酸洗→市水洗→磨刷(两组)→高压水洗→市水洗→海棉吸水→风干→烘干→出料
流程说明:
磨刷的作用:除去板面的污染物,保证干膜与铜面有良好的附着力.
水破实验:承正常刷磨之板经各个流程完成后取出即放入水中共中5S左右,拿出水面以45度角静置,观察水膜破裂时间,要求20秒以上.
注意事项:
a.每班必须进行机身清洁,检查喷嘴是否堵塞.b.每班必须做磨痕试验(1-1.5CM) c.依化验进行添加药水
d.每小时做一次水破试验.e.每周对刷轮进行一次整平校正,刷幅测试.
⑫压膜机作业
流程:磨刷来板→粘尘→压膜→插架泠却→待对位
压膜作用:将干膜贴在板面上(压上一层药膜(感光阻剂)和保护膜(聚乙稀膜.聚酯膜)),便于后行的线路转移.
注意事项:
a.割膜时要整齐,防止板边有干膜碎,用除尘纸除干膜碎.b.割膜不能撕起保护膜.
c.压膜时没有拉直容易造成折邹.d.压膜起泡与压膜速度.温度有关.
⑬干膜曝光机作业
流程:静置OK压膜板→对位→曝光→静置→显影(负型光阻为见光聚合的光阻,而正型光阻则是见光分解的光阻.)
①.对位时注意事项:
对棕片菲林时不能偏位.错位.或贴反;每贴一块PCB板要做一次清洁动作除干膜碎.灰尘.
②.曝光流程:对位后→抽真空→赶气→曝光→出料
曝光原理:在紫外光线照射下,光引发剂吸收了光能分解成游离基,游离基再引发聚合胶反应,反应后形成不溶于稀碱液的体型大分子结构.
曝光注意事项:
a.每班都应该在开机后做曝光尺,保持曝光能量在7-9格 b.曝光一次必须有清洁动作
c.赶气时要将空气尽量压出来 d.曝光时线路密集的地方要面向mglar.
⑭干膜显影作业
流程:曝光后静置OK板→撕保护膜→显影→水洗→吹干→吸干→接板插架→检查
显影是去除光阻较弱的区域,因此负型光阻的见光区与正型光阻的非见光区都会在显影后留下来.
显影注意事项:
a.喷嘴正常喷液方向对齐板面且连续成一条直线 b.定期检查喷嘴有无堵塞
c.显影压力与水洗压力要达到标准 d.显影液在生产中会产生泡沫,应加入适当的消泡剂.
(A).我司干膜(A)检验缺点:刮伤.缺口.开路.掉膜.沙孔.露铜.对位偏.显影不洁.曝光不良.垃圾.干膜碎.穿菲林.短路.迭板.显影过度.胶渍.压膜不良.周期不良.撕胶不良.渗镀.
(B).干膜作业中外层线路常发生的问题与处理:
问题点 原因 处理
曝光不良 曝光能量过高,吸真空不足,赶气不到位 做曝光尺调整能量,检查真空马达,mylar有无破损,满意赶气动作.
撕胶不良 板边粗糙割膜不齐边角在撕的过程中分离脱落 注意撕胶动作
杂物 机台.菲林等垃圾造成及压膜后粘尘 清洁动作做到位,环境保持清洁
短路 板边干膜碎,曝光机玻璃.mylar上有脏点 割膜后要做好除干膜碎动作.曝光进清洁动作
显影过度 曝光能量过底.显影点太小(小于40%)显影时速度太慢.药水温度太高.浓度过高 调整曝光能量.调整显影点.对药水进行化验
开路 干膜碎,底片.机台有脏点,垃圾,菲林刮伤等 防止干膜碎产生,规范作业动作
露铜 干膜碎,底片.机台有脏点 对位前干膜碎清除必须做好,底片.机台要定时清洁检查
显影不洁 显影点太高(大于80%),显影速度太快,药水温度不足,浓度过底 调整显影点.速度,化验药水并添加至范围
周期不良 周期修改失误,作业过程中脱落 首件确认,作业过程中检验
压膜不良 机器故障造成,人为造成 机器维修,进行教学
菲林碎 割膜不完整,对位曝光时封边不全 割膜检查,对位前封过检查首件
第七节 二铜
.㈦二铜
总流程:二次铜→去膜→蚀刻→剥锡
⑪镀二次铜
流程:上料→酸性清洁→市水洗→微蚀→市水洗→酸浸→镀铜
(A).我司二铜(K)检验缺点:刮伤.电镀不良.针孔.凹点.烧焦.夹伤.残铜.蚀刻过度.铜厚不足.孔内无铜.线细.夹膜.板面粗糙.掉槽.
(B).镀二铜注意事宜:
a.根据化验结果添加药水至标准.b.上夹时要扭紧防止掉槽及导电不良,上架时不能锁到孔上及成型线内.
c.铜球要保持在钛篮的2/3以上,袋口要低于液面 d.当微蚀CU2+≥20g/l则换槽.e.每班都应该做切片测铜厚
(C).镀二铜常发生问题及处理:
问题点 原因 处理
烧焦 与一铜一样
镀层脱层 前处理不净 化验药水如有污染要换槽,并检查操作是否规范
前序显影不洁 微蚀后检查是否有微蚀不足,要求前工序改善
板面发红 光泽剂过量 电解活性碳过滤消耗光泽剂
液温过高 开冷却降温至正常
光泽剂不足 化验进行添加
针孔 湿润剂不足 补充至适量
电流过高 降低电流
过滤机漏气 出水口用阳极袋罩住,调正机台
板面颗粒 镀槽内有浮颗粒;加阳极铜有杂质进入槽液;液面高于阳极袋口;槽液遭污染 加强电解吸附掉在铜槽内铜渣,杂物;加强过滤遭污染的槽液应该换掉;排放多于的铜液.
局部漏镀 显影不洁 检查前工序显像作业,显影喷嘴是否堵塞
板面上有指纹或油渍污染 提高电镀前清洁及温度,带手套作业
镀液中添加剂不良 对添加剂进行分析化验
湿膜修补线路时待镀区被污染 修补时应该仔细防止污染待镀板面
孔破 电镀前酸浸时间长
镀液中有颗粒污染
前工序不良
⑫蚀刻线
流程: 去膜→蚀刻→剥锡
①.去墨段
作用:去除干膜使没有用的铜裸露出来,以便后序蚀刻掉
②.蚀刻段
蚀刻作用:蚀刻掉裸露的无用铜,留下线路.
蚀刻原理:尽量快地让金属表面不断与新鲜蚀刻液接触,以去除无用铜
③.剥锡段
剥锡作用:剥去保护线路不被蚀刻的锡保护层,使PCB板上的线路呈现出来.
(A).去墨.蚀刻.剥锡常见问题及处理方法:
问题点 原因 处理
去墨不净 药水浓度不足 根据化验添加至适量
喷嘴堵塞 每班检查喷嘴是否堵塞
后段水洗压力不足无法冲干净残屑 调整压力至规定范围内
剥锡不净 药液成份不足 根据化验添加至适量
喷嘴堵塞 每班检查喷嘴是否堵塞
蚀刻不将残铜 剥膜不净 检查剥膜段是否正常
蚀刻机传输速度过快 调整速度至适量
板在镀前遭刮伤 预防刮伤
PH值太低 根据化验添加至适量
比重增大,超出范围 根据化验添加至适量
喷压不足 调整喷压至合适范围
液温过低 加温
过蚀 输送速度太慢 调整速度到合适范围
PH值过高加重侧蚀 调整PH值到规定范围
第八节 防焊
防焊漆:印在线路板的规定范围上,以便在喷锡或波焊期间.阻止熔锡流到无关区域而造成短路,它可防止熔锡桥连接相邻线路,减少所需焊锡的数量.为线路图形提供物理化学保护.总之可绝缘线路,改善外观且有绿油上可印上文字供电路标识.(防焊塞孔的作用:a.防止散失温度.b.防止锡珠塞孔.)
㈧防焊
总流程:前处理→印刷→曝光机→显影→烘烤→文字
⑪防焊刷磨机(前处理)
①流程:放板→化学水洗→循环水洗→上刷1→下刷1→上刷2→下刷2→水洗→自来水洗→吸干→吹干→烘干→收板
②注意事项:
a.每班都要做幅测试.
b.根据每班化验添加药水 c.放板时一律要零件面朝上
d.每班必须做水破试验(水膜时间在5秒以上) e.要定时检查各时节嘴有无堵塞
f.金手指板的手指方向要与磨刷方向一致 g.每天测一次刷毛长度,刷毛长度小于或等于10MM须更换
磨刷好的板如存放超出1.5H没有刷(塞孔板1HA),须重新刷磨方可进行印刷.
⑫印刷防焊油墨
①流程:磨刷OK板→印刷→插架→静置
②印刷注意事项
a.印刷时随时保持网版上油墨充足 b.添加油墨时不可添加于白网内
c.以白纸洗网吸油前应该先抖动白纸以除纸屑 f.印好的板必须静止15分钟后方可进行预烤
d.擦拭网脏点时必须以无尘纵然粘稀释剂,洗完后必须以白纸洗网2-3次
e.使用油墨必须检查油墨型号是否有用错或搅拌错
⑬预烤
①流程:印刷→印刷后静置板→烘烤→静置冷却
②预烤注意事项:
a.每架板间距离为1.5-2CM b.放入烤箱的板其方向与烤箱内吹风方向一致,板架与烤箱壁间距应该大于1.5CM
⑭防焊曝光
①流程:预烤冷却OK板→对位→曝光→静置→显影
②防焊曝光注意事项
a.曝光房必须在黄色光下作业,温度要求20±4℃,相对温度要求55±10% b.曝光能量要到8-12格
c.曝光时赶气动作必须两个来回 d.统一IC或线路密集面向muylar e.预烤后的板必须冷却至室温后方可对位曝光
⑮防焊显影作业
①流程:曝光后静置OK板→显影→水洗→烘干→接板插架→检查
②防焊显影注意事项
a.喷嘴正常喷液方向对齐板面且连成一直线 b.显影压力与水洗压力应该达到规格要求
c.显影液在生产时有泡沫产生,要加入消泡剂 d.镍金板返洗后显影后须10分钟内印刷洗氧化
e.每班定期检查喷嘴是否堵塞 f.塞孔重工板过显影速度不超700rpm
(A).防焊(S)检验缺点:刮伤.起泡.色差.污染.杂物.氧化.G/F露铜.曝光不良.假性露铜.文字不清.文字偏位.油墨入孔.显影不洁.沾油墨.掉白漆.印刷不良.菲林刮花.塞孔不良.掉绿油桥.显影过度.棕片压痕.PAD露铜.冒油.防焊偏位.积墨.厚油.垃圾.对反.板面沾漆.露印
(B).术语解说:残膜的影响:残膜是指感光光阻剂在曝光显影后,板面上应该被冲显掉待镀二铜或化镍浸金的区域仍留有极薄但会阻挡电镀的透明残膜.
产生的原因:a.原光阻配方所加入的附着边促进剂过量.b.显像液老化或管理不当.c.曝光后板子放置太久,使光阻剂在铜面上过度老化而不易显干净.
(C).防焊作业中常遇到的问题及处理:
问题点 原因 处理
跳印漏印 线路铜太厚,绿添不易漏到底材上
攻角角度不合适 一般为25-35度斜进式
刮印速度过快也会漏印 印慢减少漏印
开口太小容易漏印 调整网布口度
板面粘网 距空距离不足 调整好距空
网布的张力不对 调整
印刷速度太快 调整
板翘 加来料检查
显像过度 显像前曝光不足造成受光区绿漆硬化不够 找好曝光能量
显像液温过高 控制温度
输送速度太慢 调整
曝光后显像前停置时间不足 停置30分钟使感光后续聚合反应还能进行到理想状态
显影不足 显像液成份过度消耗 更新显像液
显像液温度不足 调整
输送速度过快 调整
显像机喷嘴压力不正常 检查喷嘴及压力
显像后有残膜 机组后段喷洗不足 检查显像机组供水系统
出料段输送轮遭污染 检查并清洗干净
附着力不良绿漆浮离起泡 板面受污染 清洁板面
绿漆后烤不足,硬化不足 增加烘烤时间与温度
主剂与硬化剂配比不正确 调配好
板面带有湿气 做好预烤作业
文字脱落 硬化不足 增加烤板时间与温度
主剂与硬化剂配比不正确 调配好
绿漆中硬化剂太多 调整
烤箱抽风不良.挥发残迹累积太多 修理好烤箱抽风设备
绿漆印刷后没有及时硬化,文字附着力不良 印好绿漆的板子在烤箱停置不超过4H后烤也不行
♀♂㊣ 绿漆制程之问题原因与对策
问题 可能原因 改善对策
************液态感光绿漆Liquid Photoimageable Solder Mask(LPSM)************
皮膜不均匀 油墨在刮印时混入空气 刮印动作过猛或刮行方向不正确,应该改正
自动印刷机刮刀在行进中发生跳动 检查刮刀装置是否有异常并改善
烘烤后干燥情形不良 自动时出隧道式烤箱其中热源发生故障 检测出不良配件更换
如为传统式烤箱时可能是温度不足 检查监控的热偶是否仍功能正常并测绘其温度曲线
曝光时绿漆仍会沾着底片 曝光台面温度已升高(所形成的热膨胀甚至还会在对准度上造成偏差) 改善曝光台面吹冷气功能,加强冷却效果
所满印绿漆干燥不足 检查并更换
去墨区出现显像不足 显像液过度使用成份耗尽 检查更换
显像液温度不足,控温器可能失灵 另以温度计检测并改善加热装置
输送速度太快 检查院并另行试走,找出正确参数
前站曝光过度,使得遮光区绿漆发生部分硬化 “以阶段曝光表”试行找出正确的曝光能量
显像机喷嘴不正确 检查循环过滤机管路或喷嘴堵塞情形
留墨区发生显像过度 显像前曝光不足造成受光区绿漆硬化不够 “以阶段曝光表”试行找出正确的曝光能量
显像液温度过高,控制可能失灵 另用温度计检测及改善
输送速度太慢 调整
曝光后显像前停置时间不够 至少应维持30分钟,使感光后续聚合反应仍能进行到理想的状态
显像后应裸露铜面上出现残膜或残迹 机组后段喷洗作业不足 检查显像机组供水系统
出料段输送轮污染 检查及清洁各转轮,避免显像不足的板子入料,确保各轮缘不致沾到没有硬化的绿漆
显像后热烘硬化不够 配合感温热偶订定出正确温度曲线
硬化时间太短 调整
绿漆油墨的储存过期 更换油墨
*****************传统两液烘烤型绿漆Liquid Thermal Cure S/M ****************
对准性发生偏移 印刷工具调整不当 重新调整直到试印满意为止
网布”架空距离”太高 调整
刮刀压力太大 减轻刮刀压力
网版版膜书面太大,与网框搭配不当 网框每边应大过书面5-6寸,或框边长度为版膜边长的两倍,使书面居中以减少印偏
刮刀质地太软 增加刮刀的硬度值
网布开口度太大致使漏墨时过多 调整
网布张力不正确 调整张力
烘烤硬化不足 烘烤时间太短 增加烘烤时间
烘烤温度太低 调整
油墨主剂与硬化剂调和不正确 调整
烤箱通风不良 改善
附着力不良经常出现绿漆浮离 板面受到污染 如为金属导体表面(如铜面或熔锡面)应在印前做好机械刷磨或进行微蚀
绿漆硬化不足 调整时间及温度
绿漆与板面金属间的共容性不良 绿漆必须要与金属表面共容才行
板面带有湿气 做好印前预烤以及赶水气
绿漆沾垫或进孔 网印物料或工具不正确 调整
刮刀推力或架网张力太大 调整并试印
网目开口太大或”刮力面”覆网油墨过多 调整
油墨溢印过多 检查沾滞度,检讨原始绿漆底片开口程度,刮印后应尽快烘烤,减少湿膜蔓延溢出
网布上之版膜,图案出现破裂 重制版膜及小心贴网
网布”印墨面”受到油墨沾污 擦净网版增加吸墨纸干印之频度(指不加覆油墨,且另以白报纸代替实板进行吸墨式干印,使网布印墨面得以清洁)
网版距待印板之架空太高 降低架空高度,减少刮刀压力,延长网版耐用寿命
喷锡后绿漆出现浮离附着力故障 绿漆制程选择错误 选择可耐喷锡的绿漆并按供应商指示操作
环氧树脂主剂与硬化剂调配不当 按供应商要求配制
喷锡前绿漆烘烤不足 加强烘烤硬化
浸入熔锡时间过久 减少接触时间
熔锡温度过高 降低喷锡温度至适当范围
绿漆过度硬化 按供应商指示进行正确烘烤
绿漆烘烤过度甚至变色 温度太高,烘烤时间太长 降低烘烤温度与时间
耐湿气绝缘电阻值不足 绿漆会接触有害物质造成其中树脂受损 减少绿漆与强力清洁物料或溶剂(如二氯甲烷)的接触机会
绿漆调配网印或硬化不正确 按供应商要求进行调配
*********************紫外线(UV)硬化绿漆(常用于单面板)**************** ****
偏印 网印工具或物料不正确 重新制版及架网
网版架空距离太高 降低架空高度
刮刀压力太大 降低刮刀压力,若为自动印刷机进可将其刮刀压下深度稍加减轻
与网框搭配时其版膜书面显然面积过大 网框每边都应比网版书面要大5-6寸或保持网框面积为书面面积的两倍
刮刀质地太硬 降低刮刀硬度
硬化不足 输送速度太快或印墨太厚 降低输送速度或印墨厚度
绿漆颜色太深阻碍紫外光能量射入墨层中进行硬化 减少印墨厚度,并向供应商反映颜色问题要求改善
紫外光源强度不足 降低输送速度增加硬化时间/增加光源灯管数/更换强度不足的灯管/清洁.调整反射罩
附着力不足 待印板面受到污染 金属导体表面印前要加刷磨或采用微蚀
紫外光硬化不足 降低输送速度增加硬化时间/增加光源灯管数/更换强度不足的灯管/清洁.调整反射罩
绿漆与板面的匹配不良 所选用的绿漆必须与板面性质能够共容
板面湿气太重 加强印前烘烤
绿漆沾垫或进孔 网印物料或工具不正确 调整
刮刀推力或架网张力太大 调整并试印
网目开口太大或”刮力面”覆网油墨过多 调整
油墨溢印过多 检查沾滞度,检讨原始绿漆底片开口程度,刮印后应尽快烘烤,减少湿膜蔓延溢出
网布上之版膜,图案出现破裂 重制版膜及小心贴网
网布”印墨面”受到油墨沾污 擦净网版增加吸墨纸干印之频度(指不加覆油墨,且另以白报纸代替实板进行吸墨式干印,使网布印墨面得以清洁)
网版距待印板之架空太高 降低架空高度,减少刮刀压力,延长网版耐用寿命
喷锡后绿漆脱皮 所选用绿漆无法适应高温喷锡制程 选用耐得住喷锡的UV绿漆并按供应商的建议进行操作
喷锡前烘烤不足 加强烘烤硬化
浸入高温熔锡时间过久 减少接触时间
熔锡温度过高 降低喷锡温度
绿漆过度硬化 按供应商指示进行正确烘烤
紫外光硬化过度(波焊操作中板面绿漆出现破裂或崩落情形 照光时间太久或光源太强 增加输送速度或降低光源强度
耐湿气绝缘电阻不良 绿漆会遭强力溶剂或清洁剂攻击,以致树脂受损 减少绿漆与强力溶剂或清洁剂接触机会
绿漆硬化不足 按供应商建议做正确的硬化
绿漆配方达不到绝缘电阻的要求 更换品质好的
♀♂㊣♀♂㊣♀♂㊣♀♂㊣绿漆常见问题其可能原因及对策:
现象 原因 对策
气泡 油墨粘度过大 以稀释剂调整油墨粘度
刮刀速度太快 减低刮刀速度
Mesh数太小 提高mesh数
印完的板子没有静置 静置15-20分钟以上
针孔常发生线路密集处外观类似显像液渗透 线路密集处脏点没有消除 磨刷改成500 mesh尼龙刷或喷砂式磨刷机.并加强后段水洗压力至中压
剥锡铅液内的重氟化铵攻击板面形成凹洞残留液体形成 剥锡铅后以80-100℃热水冲洗,并配合两支500-1000 mesh 软毛尼龙刷刷洗
在印制场所高温受湿 避免板子在此种场所滞留或刷磨前烘烤去湿
邹折 网目(mesh)数太小 选择适当网目数
油墨不均 油墨印完采平放式
透明残膜 预烤时间过长 缩短预烤时间
预烤温度过高 降低温度
曝光没有吸真空 确认完全抽真空才曝光
作业过程从印刷完至显像照射过多U.V光所致 做批量管制,尽量调整先进先出观念.滞留过程尽量不要照到光线
棕色底片老化 检查棕片的光密度值及更换棕片
SMD板上方型焊垫上有水纹状 印刷溢膜较薄处油墨于作业过程中照射到U.V光所致 修改底片使用方垫处覆墨.并缩短从印刷到显像的作业时间
金手指上有条状scum 印刷溢膜较薄处油墨于作业过程中照射到U.V光所致 修改底片使覆墨处往下移/镀金处加磨刷消除/缩短从印刷到显像的时间
压痕 油墨预烤时间不够或温度太低 调整曝光时间与温度
油墨厚度不均使预烤不易干 调整印刷刮刀速度
曝光台上透明软盖压迫板面所致 更改曝光台使其具有跟软盖,下玻璃框类似的硬质材质
曝光台面温度过高 加冷却系统使台面温度降至25-30℃
侧蚀过大 曝光能量不足 提高
显像时间太长/温度太高/压力太大 调整
绿漆残留 吸气不良 确认完全真空才进行曝光
曝光过度 调整曝光量
U.V光透过电路板底材使对面不应该感光处造成感光 于底材配方加入适当阻光物质
VIA hole堵孔未满或中空 欲堵孔之孔径过过/mesh数太小 降低堵孔孔径/增加mesh数
绿漆表面容易沾锡 墨太薄/热烘烤不够 提高墨厚度至20-25υm./以MEK或二氯甲烷检查热烘烤是否适当
油墨流动(厚度不均) 油墨没有干/油墨太稀/直立插框 调整网目数或减少印刷次数/调整粘度/改成平放式
油墨表面粘底片 油墨没有干/台面温度过高 调整预烤时间跟温度/冷却台面温度
偏移(绿漆粘pad或线路沾锡) 底片膨胀伸长/底片设计错误/曝光时刮刀推赶真空挤压底片移动/对位不准 降低台面温度/设计时应该考虑到人工对位有±2mil误差/减少使用刮刀次数/加强人员训练
脆化 热烘烤过度 确认热烘烤的温度或时间
二次铜.锡铅电镀表面有点状凹陷 一般阻剂干膜与液态感光绿漆之显像混合槽共用使用 显像应该隔离生产(用不同显像机)
融锡板锡面变黑 印绿漆前刷磨时有微蚀进氯离子的污染 切掉微蚀开关
绿漆表面无光泽 曝光能量不够/显像温度太高 提高曝光能量/降低像影温度
第九节 镀金手指(电镀镍金)
作用:电镀镍金在PCB上一面只用于板边金手指处当成接触用途,希望在低电压下(2.5V)能完成瞬间导通(讯号传输),而且还希望成为可换式插拔接点的另一种互连任务.由于黄金永远不会生锈氧化,且接触电阻很低,因而被选为板边金手指的表面镀层,至于镀镍则是当成一种屏障层的作用,阻止金原子与铜原子之间的相互转移,避免黄金层贵金属性质降低.
㈨镀金手指
⑪镀金手指线作业流程:
进料检查→压胶→开天窗→上料检查→上料→刷磨→市水洗→微蚀→循环水洗→市水洗→酸洗→纯水洗→镍槽→循环水洗→市水洗→纯水洗→金槽→回收水洗→纯水洗→吹干→撕胶→烘干→检查→印可剥胶→烤板→喷锡
(A).金手指(G)检验缺点:金厚.镍厚.烧焦.发白.漏镀.渗镀.开窗不良.
(B).镀金手指注意事项:
a.每周要清洁一次刮水片,坏的要进行更换,铜电刷每周应该清洁一次.b.定期过滤
c.进料严格检查,是否有金手指沾绿油.白添.杂物.刮伤.凹点等.
d.开天窗时金手指开天窗的间距为1-1.5MM,上料时应该检查是否有漏开天窗,撕胶时必须戴手套作业.
e.镀金手指后检查是否有手指氧化.刮伤.露铜.白点.发雾.磨痕.烧焦.发白等不良
h.每班必须分析各槽药水.J.印好可剥胶后应该检查是否有漏印待问题.
k.烤可剥胶温度为140℃.5-10分钟.烤后必须再检验一次.
(C).金手指常发生问题及处理方法:
问题点 原因 处理
高电流区烧焦 金含量过低 添加金盐
搅拌不足 增加槽液过滤循环
电流太高 调整电流
镀金层有发白发雾 搅拌不足 增加槽液过滤循环
PH值太高 调整PH值降低
钴含量或光泽剂浓度太低 化验并调整到适量
无机物污染 换槽
刮伤 人为刮伤.撕胶刮伤.机器刮伤 调整
前工序造成的刮伤 加强检验
镀金面粗糙 低层NI层CU层已粗糙 加强本站进料检验
槽液中出现固体粒子 加强过滤.并用活性碳处理
镀金效率不足 增硬剂不足 调整至规定范围
有机污染 加强过滤
第十节 化金
㈩化金
化学镍金又叫沈镍金,业界常称无电镍金,又称沈镍金,是在清洁的铜面上利用钯离子与作为媒介进行化学镀镍,然后化学浸金的一种可焊性表面涂覆工程,它既有良好的接触导通性而且又有良好的装配焊接性能。
流程:上料→除油→循环水洗→微蚀→循环水洗→稀硫酸→循环水洗→预浸→活化→纯水洗→化学镍→纯水洗→浸金→回收水洗→纯水洗→浸厚金→回收水洗→纯水洗→盐水洗→下料
I.化金(E)检验缺点:金厚.镍厚.刮伤.化金不良.金面粗糙.露镍.
第十一节 OSP
(十一)OSP
有机保焊剂OSP,在绿漆后裸露的清洁铜面上,经涂布处理所形成的一层有机化合物的棕色皮膜.
作用:⑪保护铜面不在受外界影响而氧化.
⑫皮膜在焊接前可被稀酸或助焊剂所迅速除去而裸露铜面仍能展现良好的焊接性.
流程:入料→脱脂→加压水洗→微蚀→加压水洗→吸干→吹干→预浸→中检水洗→OSP→浸泡水洗→加压水洗→吸干→吹干→烘干→冷却→收料
第十二节 喷锡
(十二)喷锡
我司采用的垂直喷锡:也就是把板子先浸入熔锡中再取出以高温高压将多余的锡吹掉.
总流程:前处理→喷锡
⑪前处理:
流程:入料→微蚀→刷洗→水洗→吸水海绵→助焊剂→出料
⑫喷锡
流程:过完助焊剂→浸锡→拉上经风刀吹→清洗
(A).喷锡(H)检验缺点:刮伤.锡面粗糙.锡面氧化.锡塞孔.手指上锡.锡短.锡高.锡面发白.上锡不良.
(B).喷锡注意事项
a.喷金手指板及SMD喷锡板10-20PNL就清理风刀口上的锡渣 b.有SMD面朝前风刀方向一致
c.喷锡后的板不能沾有酸性药水 e.每周做两次喷锡炉处理(碳化物处理.除锡渣)
d.喷锡出现故障超过10分钟,泡过助焊剂的PCB板应该清洗干净.烘烤120℃.10分钟后再喷,以防掉油墨或金手指上锡
第十三节 成型
成型即根据客户需求将PCB板冲.锣成客户规定形状规格的单片或联片.
(十三)成型
CNC→V-CUT→斜边
⑪冲床
①作业过程:
依生产指示及成型板材质厚度领取指定模具→装好模具再清洁冲床工作台面→双手持平PCB板按PCB板上冲向将其卡进模具上的管位针→冲板→做首件件确认(对照生产指示和工程提供的样品进行检验) →量产
②注意事项
a.装模前检查模具管位针和套位会是否晃动.有则立即维修
b.对没有识别冲向及模糊的待冲板,作业应该停止查明后再冲 c.首件确认做到位
d.每次冲完后好清洁模具一次(用毛刷) e.注意漏冲孔.破孔.大孔.小孔.压伤.变形.冲偏.冲报废.冲伤线路.反料断裂.毛刺
⑫锣房(CNC)
①注意事项
a.检查压脚毛刷之磨损,以免撞钉或刮伤板面 b.清洁筒夹头后安装时必须锁到底为止
c.若主轴停止8小时以上,使用前必须暖主轴 d.保持台面清洁每趟成型后必须吸尘
②CNC常见问题及处理
问题点 原因 处理
外形尺寸超公差 操作中板子出现移位 加大压力脚压力.加设板内定位梢
板翘严重 重新检板.改善压板系统
数控指令不正确 检查软件及控制器
切后板边粗糙 铣刀磨耗 更换
铣刀附着胶渣过多 清洁
机台发生震动 减少机台震动
切后板出现白班 铣刀磨损 更换
进刀速与转速关系配合不良 调整
⑬V-CUT
①注意事项
a.刀片雪割运转方向上四依顺时针方向运转,下轴依逆时针方向
b.切割刀在操作前后,装板时不可以互碰或落地
c.新刀要先V-CUT纸板,生产到线边志毛屑时才能V-CUT纤维板
d.板成型后切割其长宽必须成直线.平等且长边要大于80mm以上
②出现问题及处理
问题点 原因 处理
不足 板材厚度不当
机台与投定值不对 调整
刻槽角度不正确 刻刀磨抽或损伤 更换
刻刀轮在板面上造成刮痕 导引轮施力过大 调整
滚轮不洁 检查清洁
⑭斜边
①常见问题及处理
问题点 原因 处理
斜边粗糙 裁刀不够利 磨或换
裁刀松脱或刀座没有夹紧 固定
斜边表面不平刀座松驰 固定
皮带磨损或损坏 更换
板厚不均匀 检查
进刀压力过大 压轮压力设定值过高 调整
轴承损坏 更换
第十四节 电测
(十四)电测
在PCB的制造过程中,有内层蚀刻后.外层线路蚀刻后.成品三个阶段要进行电测.
电测目的:减少不良板流出.(流程: 测试→找点→中检)
注(第十五节):镍金线
镍金线药水成份:
名称 主要成份 温度 时间 作用
酸性清洁剂 PC-455 22-55℃ 5-15分 清洁
微蚀 APS H2SO4 22-35℃ 30-120S 粗化
酸洗 H2SO4 室温 5-20分 去氧化
镍槽 胺基酸镍,氯化镍,硼酸 40-60℃ 15-20分(光宝系列20分) 胺基酸镍和氯化镍是Ni+主要来源,硼酸保持PH稳定
镍槽PCB板电流计算公式:
长*宽*2/100*1.8ASD*受镀面积*张数
注意事项:
⑪根据化验结果添加足够药水.⑫每班要做拉力试验,测NI厚.
⑬上下班要轻拿轻放.⑭上槽时,挂具之间1-2CM,不能重迭.
4.电镀镍金板不上锡原因分析:
⑪电镀前处理:酸性除油,因最近气温较低,可能有部分板件或表面阻焊残膜/处理不净,可以调整除油剂浓度/温度,另外微蚀也要注意微蚀深度和板面颜色均匀性;
⑫镀镍问题:镍缸污染油剂或金属污染较重,建议低电流电解或碳芯过滤;PH值异常,用稀硫酸或碳酸镍调整ok;镀镍厚度不够,孔隙率太高,检查镀镍电流密度,用电流卡表检查导电杆电流与仪表显示电流一致性,电镍时间,必要时可做金相切片观察镍层厚和层间表面状况;镀镍槽添加剂偏低/过高都有可能出现此类状况,但是添加剂低的可能较大些;此外氯化镍的含量对镍层可焊性也有点影响,注意调整至最佳值,过高应力大,过低度层孔隙率高;
⑬金层假镀,镍层水洗时间过长或氧化钝化,注意加强水洗时间控制,此处多用热纯水;
⑭后处理不良;水洗后应及时烘干,放入通风状况良好的地方,最好不要放在电镀车间内!
⑮其它的还要注意所有化学处理,清洗水水质要求比一般电镀要求要高些!一般用市水 / 自来水,循环再生水 / 井水湖水建议最好不要用,因为水中硬度高 / 含有其它络合有机物!最好配合化学分析检查
5.镍金线常出现问题及处理:
缺陷名称 原因 处理
针孔 1.湿润剂不足;2.电流过高;3.过滤机漏气 1.补充足够湿润剂;2.降低电流;3.出水口用阳极袋罩住,减少冲激力.
发白发雾 1.镀层下铜污染;2光剂不足;3.金属污染 1.上架前检查仔细OK;2。补充足够光泽剂;3。金属电解处理。
烧焦 1.电流过高;2.太靠近阳极 1.降低电流;2。修理变形挂具及检查操作动作。
镀层粗糙 1.槽液中有尚未溶解硼酸粉末;2.阳极袋破开或没有阳极袋过滤不当 1.添加固体物品时,应在袋内挂于槽中或由过滤器放入槽中。2。换上好的阳极袋,一定要阳极袋;3。检查过滤程度不当。
推荐第9篇:PCB工作总结
制作PCB注意事项
1.根据实物图选封装,焊盘的大小定格在直径2mm,方便钻孔。
2.充分调用库文件,实在不行,PCB库文件可根据实物图的引脚间距自己动手画。原理图应设置相关引脚。网上查找数据手册也是可以的。 3.注意单位的换算,毫米和英寸的换算,1.0mil=0.025mm.4.黄纸需要充分烘干,避免油墨散开。 5.注意缩放比例,保留过孔。
原理图
PCB封装
热转印
未腐蚀的铜板
推荐第10篇:PCB电路板
线路板加工,单面电路板,双面电路板,PCB电路板,PCB电路板厂,PCB电路板厂家-梅州市创福达电子有限公司,是一家专业生产各种高精密单,双面及多层印刷PCB电路板,致力于快速高密度多层板、特种PCB电路板的研发生产制造,为用户提供PCB线路板技术支持与服务。创福达电路板厂位于梅州市丰顺县工业区,占地面积4000平米,员工100人左右,月生产PCB线路板能力20000平米。创福达线路板厂家由多名PCB电路板业内人士创建,培养了一批制造经验丰富的员工,高素质的管理团队,先进的设备仪器和完善的质保体系,使我们不断提升在PCB电路板行业中的地位及在客户心中的良好形象。
工厂自 2006 年创建以来,规模迅速发展,拥有 4000 余平方米的厂房, 100多名员工。产品于2006年取得ISO900
1、SGS认证,2009年一次取得欧盟ROHS无铅产品认证和美国UL认证。引进整套先进的生产设备,培养了一支从事印刷电路板加工的专业队伍,健全了从市场开发,工程设计,到加工生产的一条龙服务。公司以生产优质产品,回报社会的经营管理宗旨。将广纳人才作为企业立足之本,视产品质量为企业之生命,为客户提供最优质的产品,最满意的服务。
我们的产品包括:高精密的双面 / 多层板(2-12层)、高 Tg厚铜箔板、热风整平、全板镀金、插头电金、涂覆铁弗龙等印制板,除此之外还可生产高难度的背板、PCMCIA及半孔板,特殊材料板如陶瓷板、聚四氟乙烯高频板、金属基板、混合介质板、HDI板,及各种定制的特种电路板。公司产品广泛应用于通信、计算机、电源、数码、工业控制、科教研发、汽车、航天航空等高科技领域。
日交货能力达 100 余个品种,月品种达,4000余种,面积达 20000平方米。制造经验丰富员工为 顾客度身定做样板。 双面板快速加工可在24小时完成, 4至8层板加工周期可达 48—72 小时,稳定支持顾客项目研发进程,占领市场先机。
我们倡导技术创新在企业经营中的主导地位,建立了从市场开发、工程订单、过程控制、品质保证、物料控制、售后服务等稳定的管理体系。“科技是第一生产力”公司上下充分尊重研发和创新,在激烈的市场竞争中我们不断的成长和提高,成为中国最好的快速PCB线路板工厂是我们不懈的目标.
第11篇:pcb设计
!1.DOS版Protel软件设计的PCB文件为何在我的电脑里调出来不是全图?有许多老电子工程师在刚开始用电脑绘制PCB线路图时都遇到过这样的问题,难道是我的电脑内存不够吗? 我的电脑可有64M内存呀!可屏幕上的图形为何还是缺胳膊少腿的呢?不错,就是内存配置有问题,您只需在您的CONFIG.SYS文件(此文件在C:\\根目录下,若没有,则创建一个)中加上如下几行,存盘退出后 重新启动电脑即可。DEVICE=C:\\WINDOWS\\SETVER.EXEDEVICE=C:\\WINDOWS\\HIMEM.SYSDEVICE=C:\\WINDOWS\\EMM386.EXE 160002.如何确定大电流导线线宽?请见1989年国防工业出版社出版的《电子工业生产技术手册》Vol12中的图形说明。3.为何要将PCB文件转换为GERBER文件和钻孔数据后交PCB厂制板?大多数工程师都习惯于将PCB文件设计好后直接送PCB厂加工,而国际上比较流行的做法是将PCB文件转换为GERBER文件和钻孔数据后交PCB厂,为何要“多此一举”呢?因为电子工程师和PCB工程师对PCB的理解不一样,由PCB工厂转换出来的GERBER文件可能不是您所要的,如您在设计时将元件的参数都定义在PCB文件中,您又不想让这些参数显示在PCB成品上,您未作说明,PCB厂依葫芦画瓢将这些参数都留在了PCB成品上。这只是一个例子。若您自己将PCB文件转换成GERBER文件就可避免此类事件发生。GERBER文件是一种国际标准的光绘格式文件,它包含RS-274-D和RS-274-X两种格式,其中RS-274-D称为基本GERBER格式,并要同时附带D码文件才能完整描述一张图形;RS-274-X称为扩展GERBER格式,它本身包含有D码信息。常用的CAD软件都能生成此二种格式文件。如何检查生成的GERBER正确性?您只需在免费软件ViewmateV6.3中导入这些GERBER文件和D码文件即可在屏幕上看到或通过打印机打出。钻孔数据也能由各种CAD软件产生,一般格式为Excellon,在Viewmate中也能显示出来。没有钻孔数据当然做不出PCB了。4.如何提高布通率?完成一个印制板图的设计一般都要经过原理图输入--网络表生成--定义Keepout Layer -- 网络表(元件)加载--元件布局--自动(手动)布线等过程。现今市面上流行的几种软件在元件自动步局功能上都不是很强大,往往通过手工步局更能提高布通率,但请别忘了充分运用Move to Gird 功能,她能将元件自动移到网格交叉点上,对提高布通率大有益处。5.PCB文件中如何加上汉字?在PCB文件中加汉字的方法有很多种,本人比较喜欢的方法还是下面将要介绍的:A.前提条件:您的PC中应安装有Protel99软件并能正常运行.B.步骤:将windows目录中的client99.rcs英文菜单文件copy 到另一目录下保存起来; 下载Protel99cn.zip 解包后将其中的client99.rcs复制到windows目录下; 再将其他文件复制到Design Explorer 99目录中;重新启动计算机后运行Protel99即会出现中文菜单,在放置|汉字菜单中可实现加汉字功能。6.怎样在PCB文件中描述长槽孔?如上图所示为一继电器封装,继电器管脚截面为长方形,那么印制电路板上的相应孔就应为长槽形,要描述这一长槽形孔,只需在相应焊盘中放置一排与孔等大的Pad即可,如上图中十字光标所指
第12篇:pcb各层解释
Mechnical: 一般多指板型机械加工尺寸标注层
Keepoutlayer: 定义不能走线、打穿孔(via)或摆零件的区域。这几个限制可以独
立分开定义。
Topoverlay: 无法从字面得知其意义。多提供些讯息来进一步讨论。
Bottomoverlay: 无法从字面得知其意义。可多提供些讯息来进一步讨论。 Toppaste: 顶层需要露出铜皮上锡膏的部分。
Bottompaste: 底层需要露出铜皮上锡膏的部分。
Topsolder: 应指顶层阻焊层,避免在制造过程中或将来维修时可能不小心的短路
Bottomsolder: 应指底层阻焊层。
Drillguide: 可能是不同孔径大小,对应的符号,个数的一个表。
Drilldrawing: 指孔位图,各个不同的孔径会有一个对应的符号。
Multilayer: 应该没有单独这一层,能指多层板,针对单面板和双面板而言。拓展能力!
第13篇:PCB焊接技术
用电烙铁焊接元件是基本的装配工艺,它对保证电子产品的质量起着关键的作用。下面介绍一些元器件的焊接要点。
1.焊接最好是松香、松香油或无酸性焊剂。不能用酸性焊剂,否则会把焊接的地方腐蚀掉。
2.焊接前,把需要焊接的地方先用小刀刮净,使它显出金属光泽,涂上焊剂,再涂上一层焊锡。
3.焊接时电烙铁应有足够的热量,才能保证焊接质量,防止虚焊和日久脱焊。
4.在焊接晶体管等怕高温器件时,最好用小平嘴钳或镊子夹住晶体管的引出脚,焊接时还要掌握时间。
5.烙铁在焊接处停留的时间不宜过长。
6.烙铁离开焊接处后,被焊接的零件不能立即移动,否则因焊锡尚未凝固而使零件容易脱焊。
7.半导体元件的焊接最好采用较细的低温焊丝,焊接时间要短
8.对接的元件接线最好先绞和后再上锡。
焊接技术
这里讲的焊接技术是指电子电路制作中常用的金属导体与焊锡之间的熔合。焊锡是用熔点约为183度的铅锡合金。市售焊锡常制成条状或丝状,有的焊锡还含有松香,使用起来更为方便。
1、握持电烙铁的方法
通常握持电烙铁的方法有握笔法和握拳法两种。
(1)、握笔法。适用于轻巧型的烙铁如30W的内热式。它的烙铁头是直的,头端锉成一个斜面或圆锥状的,适宜焊接面积较小的焊盘。
(2)、握拳法。适用于功率较大的烙铁,我们做电子制作的一般不使用大功率的烙铁(这里不介绍)。
2、在印刷电路板上焊接引线的几种方法。
印刷电路板分单面和双面2种。在它上面的通孔,一般是非金属化的,但为了使元器件焊接在电路板上更牢固可靠,现在电子产品的印刷电路板的通孔大都采取金属化。将引线焊接在普通单面板上的方法:
(1)、直通剪头。引线直接穿过通孔,焊接时使适量的熔化焊锡在焊盘上方均匀地包围沾锡的引线,形成一个圆锥体模样,待其冷却凝固后,把多余部分的引线剪去。(具体的方法见板书)
(2)、直接埋头。穿过通孔的引线只露出适当长度,熔化的焊锡把引线头埋在焊点里面。这种焊点近似半球形,虽然美观,但要特别注意防止虚焊。
烙铁使用的注意事项
(1) 新买的烙铁在使用之前必须先给它蘸上一层锡(给烙铁通电,然后在烙铁加热到一定的时候就用锡条靠近烙铁头),使用久了的烙铁将烙铁头部锉亮,然后通电加热升温,并将烙铁头蘸上一点松香,待松香冒烟时在上锡,使在烙铁头表面先镀上一层锡。
(2) 电烙铁使用一段时间后,可能在烙铁头部留有锡垢,在烙铁加热的条件下,我们可以用湿布轻檫。如有出现凹坑或氧化块,应用细纹锉刀修复或者直接更换烙铁头。
(3) 电烙铁通电后温度高达250摄氏度以上,不用时应放在烙铁架上,但较长时间不用时应切断电源,防止高温“烧死”烙铁头(被氧化)。要防止电烙铁烫坏其他元器件,尤其是电源线,若其绝缘层被烙铁烧坏而不注意便容易引发安全事故。
一般来说电烙铁的功率越大,热量越大,烙铁头的温度越高。焊接集成电路、印制线路板、CMOS 电路一般选用 20W 内热式电烙铁。使用的烙铁功率过大,容易烫坏元器件(一般
二、三极管结点温度超过 200℃ 时就会烧坏)和使印制导线从基板上脱落;使用的烙铁功率太小,焊锡不能充分熔化,焊剂不能挥发出来,焊点不光滑、不牢固,易产生虚焊。焊接时间过长,也会烧坏器件,一般每个焊点在 1.5 ~ 4S 内完成。
第14篇:PCB课程设计报告
课程设计报告
利用Altium Designer设计单片机最小系统
一、设计目的:
1.掌握、使用实用电子线路、计算机系统设计、仿真软件的能力。2.提高读图、分析线路和正确绘制设计线路、系统的能力。
二、基本要求:
1.了解原理图设计基础、了解设计环境设置、学习Altium Designer 软件的功能及其使用方法。
2.掌握绘制原理图的各种工具、利用软件绘制原理图。3.掌握编辑元器件的方法并构造原理图元件库。 4.熟练掌握手动布局以及手动布线的方法。
5.掌握绘制编辑元器件封装图的方法,构造印制板元件库。
6.了解电路板设计的一般规则、利用软件绘制原理图并自动生成印制板图。
三、设计内容和要求:
1.根据题目要求的指标,通过查阅有关资料,确定系统设计方案,并设计其硬件电路图。
2.绘制电路原理图,并绘制PCB板。
四、设计成果形式及要求:
1.电路原理图及PCB板图 2.编写课程设计报告。
五:设计的详细过程及心得体会
Altium Designer软件是由Altium公司推出的一款功能强大的电路CAD软件,广泛应用于电子电路设计。除了全面继承包括Protel 99se和Protel2004在内的先前一系列版本的功能和优点外,Altium Designer还增加了许多改进和高
课程设计报告
端功能。该软件全面集成了FPGA设计和SOPC设计功能,从而允许工程师能够将系统设计中的FPGA与PCB设计集成在一起。 利用Altium Designer软件设计系统的详细步骤如下:
1.绘制流程图
新建工程绘制原理图编译原理图导入PCB文件得到最终的原理图和PCB图PCB自动查错PCB的手动排版自动布线编辑网络表
2.绘制过程
(1) 电路原理图设计和绘制。
电路原理设计是整个系统设计的基础,一般有以下五个步骤: ① 设置原理图设计环境。
根据电路图的规模设定图纸的大小,另外通过原理图设置选项选择合适的格点、线形以及线宽等。
课程设计报告
② 元器件布局。
根据系统的需要从元器件库中选择相应的元件并放置在图纸上合适的地方,另外需对放置元件的标号和封装进行设定。虽然Altium Designer软件一直以来都自带丰富的元件,但是电子技术及相关器件的迅速发展,这就需要对元器件库中没有的元件创建新的集成库。添加原理图库需要根据元件信息进行器件外形绘制和引脚定义等步骤。这一过程可以通过对空的元件进行编辑,也可对现有的元件库中的元件进行必要的修改。(下图所示为原理图元件库添加元件)。
③ 原理图布线。
利用Altium Designer软件的布线工具将图纸上元件用具有电气意义的线(包括导线和总线)和符号(包括网络标号和端口号等)连接起来,另外根据需要放置电缘端子,这样就构成了完整的原理图。原理图布线讲求线路清晰并且美观匀称。
课程设计报告
④ 原理图调整和检查。
在保证原理图正确性的前提下对原理图进行调整以达到美观和整洁。同时对元件的编号、封装进行设定。这其中对元器件的封装设置尤为重要,我们需要根据最终选定的封装形式在封装编辑器中对其进行编辑。在完成前述的步骤后,利用Altium Designer 的电气规则对画好的电路原理图进行电气规则检查。若有错误,需要对其进行改正。
4 课程设计报告
⑤ 生成网络表。
网络表是电路原理图设计和印刷电路板设计之间的桥梁,执行生成网络表命令可以生成具有元件名、元件封装、参数及元件之间连接关系的网络表。
(2) 印刷电路板的设计。
通过印刷电路板得到电子产品的实际结构,是电路原理图变成一个具体产品的必经之路,印刷电路板的设计主要有以下六个步骤:
① 线路板规划。
根据要设计的电路确定电路板的尺寸板层数(可以通过PCB向导工具完成),接着在Keep-Out 层绘制电路板的边框,这样就设计出电路板的基本框架。
② 导入文件和网络。
导入文件和网络就是从原理图更新PCB操作,即将原理图中的元件符号和导线转换成PCB中的元件封装和网络。因此这步操作至关重要,需要 5
课程设计报告
认真对待出现的任何问题。在确保没有错误完成执行操作后,由飞线连接的所有PCB就会出现在编辑区中。
③ 设置设计规则。
设置规则包括电气规则、布线规则、布局规则、层规则等,每项还可进行细分。这些规则将直接影响到电路板的布线、性能和尺寸等一系列问题。通常我们需要对布线线宽、安全间隔规则和层设计规则进行调整。
④ 元件布局。
元件布局是否合理将直接影响到布线的速度和质量,对后续操作至关重要。在布局时一般先放置与机械尺寸有关的固定位置的元器件,再放置特殊的和较大的元器件,最后放置小的元器件。同时要兼顾布线方面的要求,例如高频元器件的放置要尽量紧凑,信号线的布线才可能尽可能的短,从而降低信号线的交叉干扰。
课程设计报告
⑤ 自动布线。
布线操作是PCB设计的重点,Altium Designer特有的智能交互式布线能力,只需拖拉即可完成布线。在自动布线的方式下,可以选择对全部对象布线,或者是对指定网络布线。 ⑥ 设计规则检查。
显示没有错误。
课程设计报告
⑦ 手工调整。
对自动布线不完善或不尽如人意的部分进行手工布线操作,另外手工调整阶段还要完成铺地、调整元件编号、添加字符(如需要)等操作。这样就完成了印制电路板的设计。
3.心得体会
首先,Altium Designer是一款功能十分强大的软件,我们所接触到和使用的它的功能仅仅是皮毛,所以课程设计结束之后,如果想进一步更深地理解PCB设计,还有很多的经验和技巧要学。为期两周的PCB课程设计让我对利用Altium Designer软件设计原理图和电路板的基本步骤有了初步的了解。
这次的课程设计与以往的有很大的区别,主要是自学教学视频和参考书,老师则给我们提供了学习的平台并随时进行答疑。这是一种新的学习方法,通过自学、同学之间相互交流以及老师的指导,提高了自身的自学能力。
在学习的过程中,我熟悉了利用软件设计系统的详细步骤,对原理图设计中的网络标号、端口号、电气规则检查和网络表等概念有了一定的了解,懂得了绘制印刷电路板的具体流程。除此以外,这次课程设计还加深了元器件封装的相关知识,并让我对于芯片的引脚、常用连接方式和功能有了深入的认识,受益匪浅。以下是我在绘制过程中的具体心得:
(1)画原理图的时候就要注意元器件的封装,这将比最后生成pcb图时再去检查要节省很多时间,原理图要严格按照所设计的电气关系连接。画图时要注意原理图的元器件编号和网络标号。原理图中NetLable摆放位置要注意,一定要把它放在有电气连接点的位置,如果把NetLable放在了管脚的中间,并没有构成电气连接,这样生成网表时根本就连不上。
(2)在原理图画好后要注意compile时meage框中显示的错误和警告,要耐心的一个一个读懂他们并且改正,这是一个整个原理图绘制过程中最能发现自己错误、总结经验的时刻,也是pcb设计中自我技能提升的时候,所以别怕错误多,错的越多,学的越多。
(3)一块好的PCB取决于好的布局。有经验的设计者在布局时一般都按电路
课程设计报告
功能分块布局。布局时尽量考虑布线方向和各种电源的相对集中性.如CPU跟其他元件的连接时IO口最好选择一定方向顺序选取,如顺时针,而不要将几个排在一起的如输入输出等在CPU上不按顺序选取而中间隔着其他信号,会增加布线的复杂程度。
除了学习上的收获,我还得到了许多经验与教训。初期,由于对器件知识的欠缺,我曾按照原理图所示将所有的去耦电容连接在一起,而不知道将它们并联到芯片周围。另外,在前期准备阶段不够仔细,导致许多元件的封装出现了问题,这也给后来印制电路板的设计带来了极大的不便。但“实践出真知”,这些教训也是本次课程设计极宝贵的经验。
六、主要参考文献:
[1] 史久贵.基于Altium Designer的原理图与PCB设计.机械工业出版社, 2009 [2].李珩.Altium Designer 6 电路设计实例与技巧.国防工业出版社, 2008 [3] 邹丽新 翁桂荣.单片微型计算机原理(第二版).苏州大学出版社, 2009
七、附录
第15篇:PCB实训
实训一:绘制电路原理图
1、电路原理图设计的一般步骤?
1创建工程文档 2创建原理图文件 3设置图纸大小 4放置元件图符号 5检查错误 6产生网络表 7保存并打印输出原理图
2、加载常用的原理图元件库;Miscel laneous Dovice.ddb的步骤?
点击左边浏览选择库 点击添加/移除 选择sch文件夹下的Miscel laneous Dovice.ddb点击添加
思考题:
1、**.sch,**.lib,**.pcb,分别是什么类型的文件?
Sch原理图文档 pcb pcb文档 lib原理图库文档
2、用键盘上的空格,x,y键分别怎样调整对象
X x轴翻转 ,y y轴翻转
实训二:建立元件库及创建原理图元件
在自己的数据库中创建元件库Newlibi.lib 制作名为LED-7的七段数码管的步骤?
思考题:
1、应该在哪个象限制作元件?
4 象限
2、元件符号由哪几部分组成?
两部分 由元器件图形和引脚组成
实训三:数字钟电路原理图的绘制
简述绘制数字钟电路原理图步骤?
1创建工程文档 2创建原理图文件 3设置图纸大小 4放置元件图符号 5检查错误 6产生网络表 7保存并打印输出原理图
要求说明:
1、图纸设置:自定义1300*900.横向,栅格设置均为10;
2、标题栏设置:标题、学号、姓名
思考题:
1、总线本身有没有实质上的电气意义? 如何让其接口具有电气属性?
本身没有实质上的电气意义 ,使用总线来代替一组导线,需要与总线分支和网络标号相配合完成电气意义上的链接
2、“网络标号”和“注释T”都可以放置文字,两者有什么区别?分别用在什么情况? 网络标号有实际的电气特性可做导线一样连接
而注释t只是单纯的放置文字没有电气意义
第16篇:有关PCB(总结)
PCB :Printed circuit board 印刷电路板
介电层(基材):Dielectric 用来保持线路与各层之间的绝缘性,俗称为基材。 基材的分类:
由底到高的档次划分: 94HB-94V0-22F-(CEM-1)-(CEM-3)-(FR-4) 94HB:普通纸板,不防火。(最底档的材料,不能做电源板。模冲孔。)
94V0:阻燃纸板。(模冲孔) 22F : 单面半玻纤板。(模冲孔)
CEM-1:单面玻纤板。(电脑钻孔,不能模冲孔。) CEM-3:双面半玻纤板。 FR-4:双面玻纤板。
由阻燃等级划分:(94V-0)-(94V-1)-(94V-2)-94HB TG:玻璃转化温度即熔点。PCB板必须耐燃,在一定温度下不能燃烧,只能软化。这时的温度点即是玻璃转化温度。
板材的国家标准:GB/T4721-4722 1992 、GB/T4723-4725 1992
板材的TG等级:TG大于等于130度、TG大于等于150度、TG大于等于170度。TG大于等于170度,叫做高TG印刷板。
防焊油墨:Solder Mask / Solder Resistant 并非所有的铜面都要吃锡上元件,因此非吃锡的区域,会印上一层隔绝铜面吃锡的物质(通常为环氧树脂),被免非吃锡间的线路短路。按不同的工艺:有绿油、红油、蓝油。
表面处理:Surface Finish 由于铜面在一般环境中,很容易氧化导致无法上锡,因此会在吃锡的铜面上进行保护。保护的方式有喷锡(HASL)、化金(EING)、化银(Immersion Silver)、化锡(Immersion Tin)、有机保焊剂(OSP)。
PCB板材的分类
1 按板材的刚柔程度分类可分为刚性覆铜箔板和挠性覆铜箔板两大类
2 按增强材料的不同分类可分为纸基、玻璃布基、复合基(CEM系列)和特别材料基(陶瓷、金属基)。
纸基板
酚醛纸基板俗称纸板、胶板、VO板、阻燃板、红字覆铜板、94V0、电视板、彩电板等。其中有多个牌子:建滔(KB字符)、长春(L字符)、斗山(DS字符)、长兴(EC字符)、日立(H字符)。
酚醛纸基板是以酚醛树脂为粘合剂,以木桨纤维纸为增强材料的绝缘层压材料。酚醛纸基板一般可进行模冲加工,成本低价格便宜,相对密度小的优点。酚醛纸基板的工作温度较低,耐湿性和耐热性与环氧玻纤布基板相比略低。纸基板是以单面覆铜板为主,但也出现了用银桨贯通孔的双面覆铜板产品。牌子有斗山(DS字符)。它在耐银离子迁移方面,比一般的酚醛纸基覆铜板有所提高,酚醛纸基覆铜纸板最常用的产品型号为FR-1(阻燃型)和XPC(非阻燃型)两种。单面覆铜纸板从板材后面的字符颜色可以轻易判断,一般红字为FR-1(阻燃型),蓝字为XPC(非阻燃型)。
环氧玻纤布基板
环氧玻纤布基板俗称环氧板、环纤板、纤维板、FR4。
环氧玻纤布基板是以环氧树脂作为粘合剂,以电子级玻璃纤维布作为增强材料的一类基板。它的粘合结片和内芯薄型覆铜板,是制作多层印刷电路板的重要基材。工作温度较高,本身性能受环境影响小。在加工工艺上,要比其它树脂的玻璃布基板具有很大的优越性。其中的牌子如生益科技。
复合基板(CEM)
复合基板俗称粉板、22F。主要是指CEM-1和CEM-3复合基覆铜板。
复合基板CEM-1是以木桨纤维纸或棉桨纤维纸作为芯材增强材料,以玻璃纤维布作为表层增强材料,两层都浸以阻燃环氧树脂制成的覆铜板,称为CEM-1。
复合基板CEM-3是以玻璃纤维纸作为芯材增强材料,以玻璃纤维布作表层增强材料,都浸以阻燃环氧树脂制成的覆铜板,称为CEM-3。
阻燃等级:
HB:UL94和CSAC22.No0.17标准中最低的阻燃等级,要求对3到13毫米厚的样品,燃烧速度小于40毫米每分钟;小于3毫米的样品,燃烧速度小于70毫米每分钟或者在100毫米的标志前熄灭。
V-0:对样品进行两次的10秒燃烧测试后,火焰在30秒内熄灭。不能有燃烧物掉下。 V-1:对样品进行两次的10秒燃烧测试后,火焰在60秒内熄灭。不能有燃烧物掉下。 V-2:对样品进行两次的10秒燃烧测试后,火焰在60秒内熄灭。可以有燃烧物掉下。
PCB板板材厚度,按国家标准来分有: 0.5mm/0.7mm/0.8mm/1.0mm/1.2mm/1.6mm/2.0mm/2.4mm/3.2mm/6.4mm PCB上的铜箔厚度,按国家标准来分有: 18um/25um/35um/70um/105um 对铜箔的要求金属纯度不低于99.8%,厚度误差不大于5um.
第17篇:PCB生产作业指导书
篇一:pcb生产能力作业指导书
德信诚培训网
pcb生产能力作业指导书 1.0目的:
提供本厂单双面生产技术能力的检查方法和标准,从而保证生产工具和不品之品质.2.0应用范围:
适用于目前的生产技术能力范围.3.0责任: 通过各种数据反映本厂生产能力范围.4.0定义:
cnc——电脑钻孔 pth——化学沉铜 slot——槽孔 5.0参考文件: 无
6.0生产能力范围内容: 6.1板料
6.1.1本公司常备物料 a、玻璃纤维板(fr4) 备注说明: 1)、以上板料厚度含基铜厚度。 2)、以上板料厚度及公差为ipc-4101clab/l等级,如因设计需要其他规格及等级 的板料首先查询仓库最新库存有无材料,如没有则通知业务部相关人员。 3)、以上几种板料供应商为kb(建滔)和国际,本厂常用板料尺寸规格为:41″*49″、
43″*49″。篇二:pcb生产能力作业指导书篇三:pcb设计作业指导书d
1、目的 规范产品的 pcb 工艺设计,规定 pcb 工艺设计的相关参数,使得 pcb 的设计满足电气性能、可生产性、可测试性等要求,在产品设计过程中构建产品的工艺、技术、质量、成本优势。
2、范围
本规范适用于所有公司产品的 pcb 设计和修改。
3、定义 (无)
4、职责
4.1 r&d 硬件工程师负责所设计原理图能导入pcb网络表,原理上符合产品设计要求。 4.2 r&d 结构工程师负责所设计pcb结构图符合产品设计要求。 4.3 r&d pcb layout工程师负责所设计pcb符合产品设计要求。
5、作业办法/流程图(附后) 5.1 pcb 板材要求
5.1.1 确定 pcb 所选用的板材、板厚等,例如pcb板材:fr-
1、fr-
4、cem-
1、cem-
3、纸 板等,pcb板厚:单面板常用1.6mm ,双面板、多层板常用1.2mm或1.6mm,pcb的板材和厚度由结构和电子工程师共同确定。
5.1.2 确定 pcb 铜箔的表面处理方式,例如镀金、osp、喷锡、有无环保要求等。
注:目前应环保要求,单面、双面、多层pcb板均需采用osp表面处理工艺,即无铅工艺。(特殊工艺要求除外,如:轻触按键弹片板表面需镀金处理) 5.1.3 确定pcb有关于防燃材料和等级要求,例如普通单面板要求:非阻燃板材xpc或fr-1 94hb和94v-0; tv产品单面板要求:fr-1 94v-0;tv电源板要求:cem1 94v-0;双面板及多层板要求:fr-4 94v-0。(特殊情况除外,如工作频率超过1g的,pcb不能用fr-4的板材)5.2 散热要求
5.2.1 pcb 在布局中考虑将高热器件放于出风口或利于空气对流的位置。
5.2.2 大面积铜箔要求用隔热带与焊盘相连,为了保证透锡良好,在大面积铜箔上的元件 的焊盘要求用隔热带与焊盘相连(对于需过1a以上大电流的焊盘不能采用隔热焊盘),如下图所示:
焊盘两端走线均匀 或热容量相当 焊盘与铜箔间以”米”字或”十”字形连接
5.2.3 大功率电源板上,变压器及带散热器的发热器件下面需开圆形直径为3.0mm-3.5mm 的散热孔。
5.2.4 解码板上,在主芯片的bottem层的大面积的地铜箔上需开斜条形绿油开窗,增加主 芯片的散热效果。
5.3 基本布局及pcb元件库选取要求
5.3.1 pcb布局选用的pcba组装流程应使生产效率最高:
设计者应考虑板形设计是否最大限度地减少组装流程的问题,如多层板或双面板的设计 能否用单面板代替?pcb每一面是否能用一种组装流程完成?能否最大限度的不用手工焊?使用的插件元件能否用贴片元件代替?
5.3.2 pcb上元器件尽可能整齐排列(x,y坐标),减少机器上下左右的行程变化频率, 提高生产效率。
5.3.3 为了保证制成板过波峰焊或回流焊时,传送轨道的卡抓不碰到元器件,元器件的外 侧距板边距离应大于或等于 5mm,若达不到要求,则pcb应加工艺边。工艺边要求如下: 机插定位孔及不能机插的区域:
55.3.4 上图中左边直径4 mm的圆形机插定位孔的位置必须固定,距离相邻两条板边的距 离各5 mm;右边4x5mm的椭圆孔只要与下板边(轨道边)的距离保持5 mm,与右板边的距离可以适当移动,但不能小于5 mm,且不大于拼板尺寸的四分之一;没有机插元件的pcb,可以不用增加机插定位孔。
5.3.5 安装孔的禁布区内无机插元器件和走线。(不包括安装孔自身的走线和铜箔) 5.3.6 考虑大功率器件的散热设计:元器件均匀分布,特别要把大功率的器件分散开,避免电路工作时pcb上局部过热产生应力,影响焊点的可靠性;大功率元件周围不应布置热敏感元器件,它们之间要留有足够的距离;电解电容不可触及发热元件,如大功率电阻、热敏电阻、变压器、散热器等;电解电容与热源(散热器、大功率电阻、变压器)的间隔最小为3.0mm,其它立插元器件到变压器的距离最小为2.5mm。 5.3.7 器件和机箱的距离要求:
器件布局时要考虑尽量不要太靠近机箱壁,以避免将 pcb 安装到机箱时损坏器件。
特别注意安装在pcb边缘的,在冲击和振动时会产生轻微移动或没有坚固的外形的器件,如:立装电阻、变压器等。
5.3.8 布局时应考虑所有器件在焊接后易于检查和维护,小、低元件不要埋在大、高元 件群中,影响检修。
5.3.9 可调器件周围留有足够的空间供调试和维修:
应根据系统或模块的pcba安装布局以及可调器件的调测方式来综合考虑可调器件的排布方向、调测空间。
5.3.10 引脚在同一直线上的插件器件,象连接器、dip 封装器件,布局时应使其轴线和 波峰焊方向平行。
5.3.11 轻的插件器件如二级管和1/4w电阻等,布局时应使其轴线和波峰焊方向垂直, 这样能防止过波峰焊时因一端先焊接凝固而使器件产生浮高现象。
5.3.12 为了保证可维修性,bga器件周围需留有4mm禁布区,最佳为5mm禁布区。一般情 况下bga不允许放置在背面,当背面有bga器件时,不能在正面bga 5mm禁布区的投影范围内布器件。
5.3.13 0603以下、soj、plcc、bga、0.6mm pitch以下的sop、本体托起高度 (standoff)>0.15mm的器件不能放在波峰面;qfp器件在波峰面要成45度布局。 5.3.14 两面回流再过波峰焊工艺的pcb板,焊接面的插件元件的焊盘边缘与贴片元件本 体的边缘距离应≥3.0mm。 5.3.15 易受干扰的元器件不能相互挨得太近,输入和输出元件尽量远离。
5.3.16 晶振放置位置尽量靠近主芯片相关引脚,晶振匹配电容等其它辅助件放置在晶 振和主芯片的间的连线上。
5.3.17 合理布置电磁滤波/退耦电容,此电容尽量靠近ic电源脚,rc回路靠近主ic。 5.3.18 pcb元件库的选取,规定从研发部pcb组标准元件库mtc-lib中统一调用,此元
件库存档路径:ftp://研发部/4_pcb元件库/mtc-lib,此元件库会随着新元件库的增加随时刷新;如果在此元件库当中没有的元件,需提供元件规格书制作新的标准元件库。篇四:pcb制造 化学实验作业指导书 1 目的
制订符合标准的实验方法,有预期控制产品质量,减少变差。 2 范围
仅适用于江苏苏杭电子有限公司各线药水分析控制。 3 职责
3.1 品质部主管负责本文件的编写和修订; 3.2 品质部理化实验室负责本文件的执行; 3.3 相关部门负责药水的添加。 4 定义 无
5 参考文件 无 6 程序
6.1 作业流程
6.2 除胶剂的分析方法 6.2.1 总mn含量的分析
6.2.1.1试剂:20%h2so4溶液 20%ki溶液 0.1n 硫代硫酸钠标准溶液 淀粉指示剂
6.2.2.2 步骤:用移液管移取1ml工作液至250ml锥形瓶中,加入20ml纯水,再加入20ml 20%h2so4 溶液和25ml 20%ki溶液摇匀,放于暗处反应5分钟,加入2-3ml淀粉指示剂,用0.1n 硫代硫酸钠 标
准溶液滴定至蓝色消失为终点。
6.2.2.3 计算:总mn(g/l)= 3.16× (标准液耗量)ml na2s2o3 6.2.3 kmno4含量的分析 6.2.3.1 试剂:10%bacl2溶液 6%na2so4溶液 20%h2so4溶液20%ki溶液 0.1n 硫代硫酸钠标准溶液
6.2.3.2 步骤:用移液管移取10ml工作液至100ml容量瓶中,加入5ml 10%bacl2溶液和5ml 6%na2so4 溶液,用纯水定容,摇匀后静置15分钟,精确移取上述清液10ml至250ml锥形瓶中,加入20ml 20%h2so4 溶液和25ml 20%ki溶液摇匀,放于暗处反应5分钟,加入2-3ml淀粉指示剂,用0.1n 硫代硫酸钠 标
准溶液滴定至蓝色消失为终点。
6.2.3.3 计算:kmno4(g/l)= 3.16×ml (标准液耗量) na2s2o3 6.2.4 k2mno4含量的分析 计算:k2mno4(g/l)= 总mn含量-kmno4含量 6.2.5氢氧化钠含量的分析
6.2.5.2步骤:用移液管移取1ml工作液至100ml烧杯中,加入50ml纯水,用0.1n hcl标准溶液滴 定
到ph=8.5为终点。
6.2.5.3计算:氢氧化钠(g/l)= 40×(m.v) mlhcl 6.3 预中和剂的分析方法 6.3.1硫酸的分析
6.3.1.1试剂:0.5n naoh标准溶液 甲基橙指示剂
6.3.1.2步骤:用移液管移取2ml工作液至250ml锥形瓶中,加入20ml去离子水,用0.2n naoh标 准
溶液滴定,由红色变成橙黄色为终点。
6.3.1.3 计算:硫酸(ml/l)= 13.3×(m×v) naoh 6.3.2 双氧水的分析 6.3.2.1 0.1n kmno4 标准液
6.3.2.2步骤:用移液管移取1ml工作液至250ml 的锥形瓶中,加入20ml去离子水,再加入20ml 20% 的硫酸溶液,用0.1n kmno4 的标准液滴定至微红色为终点; 6.3.2.3 计算:h2o2(%)=0.1515×v(标准溶液)ml kmno4 6.4 中和剂的分析方法 6.4.1硫酸的分析 6.4.1.1 试剂:0.5n naoh标准溶液 甲基橙指示剂
6.4.1.2步骤: 用移液管移取2ml工作液至250ml锥形瓶中,加入20ml去离子水,用0.2n naoh标准溶液滴定,由红色变成橙黄色为终点。 6.4.1.3 计算:硫酸(ml/l)= 13.3×(m×v) naoh 6.4.2 中和剂p-609分析
6.4.2.1 试剂:0.1n i2标准溶液碳酸氢钠 1%淀粉
6.4.2.2 步骤:用移液管移取4ml工作液至250ml锥形瓶中,加入20ml去离子水,加入2g碳酸氢 钠搅拌至完全溶解,加1ml 1%淀粉,用0.1n i2标准溶液滴至蓝色为终点。 6.4.2.3 计算:sy-609(%)= 0.667×v mli2 6.5 溶胀剂的分析方法 6.5.1 碱度的分析 6.5.1.1试剂:0.5n 盐酸标准溶液 酚酞指示剂
6.5.1.2 步骤:用移液管移取5ml工作液至250ml锥形瓶中,加入50ml纯水及2-3滴酚酞指示剂, 用0.5n hcl标准溶液滴定至红色消失为终点。 6.5.1.3 计算: 碱度(n)= 0.1×v(标准液耗量) mlhcl 6.6 整孔剂的分析方法 6.6.1 sy-601的分析
6.6.1.1 试剂:0.1n hcl标准溶液 甲基红指示剂
6.6.1.2 步骤:用移液管移取10ml工作液至250ml锥形瓶中,加入20ml去离子水, 再加入2-3滴 甲基红指示剂,用0.1n hcl标准溶液滴定,由橙黄色变成粉红色为终点。 6.6.1.3 计算:p-601(%) =v mlhcl×2.1 2+ 6.6.2 cu含量的分析
6.6.2.2步骤:用移液管移取20ml工作液至250ml锥形瓶中,加入20ml去离子水,再加 入25ml ph=10氨性缓冲液,再加入3-5滴pan指示剂,用0.1n edta标准溶液滴定至溶 液由紫色变为淡黄色为终。 2+ 6.6.2.3计算:cu (g/l) = 0.318×v(标准液耗量) mledta 6.7 微蚀剂的分析方法 6.7.1 硫酸含量的分析
6.7.1.1 试剂:1.0n naoh标准溶液 甲基橙指示剂
6.7.1.2 步骤:用移液管移取2ml工作液至250ml锥形瓶中,加入20ml去离子水,再加入2-3滴甲 基橙指示剂,用1.0n naoh标准溶液滴定,由红色变成橙黄色为终点。 6.7.1.3 计算:h2so4(%)= 1.33×v(标准液耗量)mlnaoh 6.7.2 aps的分析 6.7.2.1 试剂: 20%的硫酸溶液ki溶液0.1n的na2s2o3 6.7.2.2 取2ml工作液加入250ml的容量瓶中,滴入10~20ml 20%的硫酸溶液,再加入10~15ml的ki 溶液,滴3~8滴淀粉溶液,暗处静置5min后用0.1n的na2s2o3滴定至蓝色消失(即无色)为终点; 6.7.2.3 计算 aps(g/l)=n×v×59.5 6.8 预浸剂的分析方法 6.8.1酸度的分析 6.8.1.1 试剂:0.1n naoh标准溶液甲基橙指示剂 用比重计直接读数。
6.8.3 铜离子含量同整孔剂分析方法 6.9 活化剂的分析方法 6.9.1酸度的分析 6.9.1.1 试剂:0.1n naoh标准溶液甲基橙指示剂
6.9.1.2 步骤:用移液管移取1ml工作液至250ml锥形瓶中,加入20ml去离子水,再加入2-3滴甲 基橙指示剂,用0.1n naoh标准溶液滴定,由红色变成橙黄色为终点。 6.9.1.3 计算:酸度(n)= 0.1×v(标准液耗量) mlnaoh 6.9.2 sy-605活化剂浓度的分析
6.9.1.1分别取sy-605活化剂原液2.0ml,2.5ml,3.0ml,3.5ml,4.0ml于100ml的容 量瓶中,用5%的盐酸稀释至刻度,分别得到2.0%,2.5%,3.0%, 3.5%,4.0%的标准溶液。 6.9.1.2取工作液,与标准溶液进行比色,即得到浓度范围。 6.9.3 比重用比重计直接读数。 6.10 加速剂的分析方法 6.10.1酸度的分析
6.10.1.1 试剂:0.5n 碘标准液 1%淀粉指示剂
6.10.1.2 步骤:用移液管移取5ml工作液至250ml锥形瓶中,加入适量di h2o,再加入适量
6.10.1.3 计算:酸度(n)= 0.1× v(标准液耗量) mlnaoh 2+ 6.10.2 cu含量的分析
与预浸缸铜离子含量分析方法相同。 6.11 沉铜液的分析方法 6.11.2 cu2+含量的分析 6.11.2.1 试剂:20%h2so4溶液 20%ki溶液 10%kscn溶液 0.1n 硫代硫酸钠标准溶液 淀粉指示剂 6.11.2.2 步骤: 用移液管移取10ml工作液至250ml锥形瓶中,加入20ml 20%h2so4溶液和25ml 20%ki 溶液,用0.1n 硫代硫酸钠标准溶液滴定,由棕色变成淡黄色,用0.1n硫代硫酸钠标准溶液滴定至 溶液变为乳白色为终点。 2+ 6.11.2.3 计算:cu(g/l)= 0.635×v(标准液耗量) mlna2s2o3 6.12 图电除油剂的分析方法 6.12.1 硫酸的分析方法
6.12.1.1 试剂: 甲基橙 1.0 n naoh标准溶液
6.12.1.2 步骤: 取2ml待测液至250ml锥形瓶中,加入50ml纯水摇匀,再加入2-3d甲基橙指示剂,用1.0 n naoh标准溶液滴定至溶液变为橙黄色为终点。 6.12.1.3 计算:硫酸(ml/l) = 13.3×v(标准液耗量)ml naoh 6.12.2 图电微蚀剂的分析方法
6.12.2.1 试剂: 20%硫酸溶液 20%ki溶液 1%淀粉指示剂 0.1n na2s2o3 6.12.2.2 步骤: 取2ml待测液于250ml锥形瓶中,加入10-20ml 20%硫酸溶液,加10-15ml ki溶 液,加 3-8滴淀粉溶液,放暗处静置5分钟,用0.1n 硫代硫酸钠滴定至无色。 6.12.2.3 计算:nps(g/l)=59.5×n×v(标准液耗量) 6.12.3 硫酸含量的分析 6.12.3.1 试剂: 1.0 n naoh标准溶液 甲基橙指示剂
6.12.3.2 步骤: 用移液管取2ml工作液至250ml锥形瓶中,加入20ml去离子水,再加入2-3滴甲 基橙指 示剂,用1.0n naoh标准溶液滴定,由红色变成橙黄色为终点。 6.12.3.3 计算: h2so4 (%)=1.33×(标准液耗量)ml naoh 2+ 6.12.4 cu 含量分析
6.12.4.1 试剂:浓氨水 0.1n edta 紫脲酸铵 6.12.4.2 步骤:取1ml样本放入250ml锥形中,加50ml水,加浓氨水3-5滴,用edta 滴至紫罗兰 色。 2+ 6.12.4.3 计算: cu (g/l)=250×n×v(标准液耗量) 6.13.图电预浸剂的分析方法 6.13.1 硫酸的分析方法
6.13.1.1试剂:甲基橙指示剂 1n naoh 标准液
6.13.1.2步骤:取1ml样本置于250ml锥形瓶中,加50ml纯水,加3-5滴甲基橙指示剂,用naoh 滴 至黄色。
6.13.1.3计算:h2so4(%)=2.66×n×v(标准液耗量) 6.14.1硫酸铜含量的分析
6.14.1.1试剂: 20%氨水溶液,0.1n edta溶液,紫脲酸胺指示剂 6.14.1.2步骤: 用移液管移取2ml工作液至250ml锥形瓶中,加入50ml去离子水,加20ml 20%nh4h2o 溶液,加0.2-0.4g紫脲酸胺指示剂,用0.1n edta滴定至紫罗兰色为终点.6.14.1.3计算:cuso4·5h2o(g/l) = 125×( ) mledta×( ) n edta 6.14.2硫酸含量的分析 6.14.2.1试剂:1.0n 氢氧化钠标准液, 0.1%甲基橙指示剂
6.14.2.2 步骤:用移液管移取2ml试液到 250ml的锥形瓶中,加入50ml去离子水和2-3滴甲基橙指 示剂,然后用1.0n 氢氧化钠标准溶液滴定颜色由红色变橙黄色为终点。.6.14.2.3 计算:h2so4 (g/l) = 24.5×( )mlnaoh×( )n naoh 6.14.3 cl的分析 6.14.3.1 试剂:0.01n hg(no3)2标准液,0.1n agno3指示剂
6.14.3.2 步骤:取50ml工作液,加入50ml纯水及20ml20%hno3溶液,摇匀后再加入3-5dagno3 指示剂,充分震荡溶液后用0.01nhg(no3)2标准液滴定至溶液变清为终点。 6.14.3.3 计算:cl (ppm/l) = 710×( )ml hg(no3)2×( )n hg(no3)2 注意事项
1、温度低于20℃时,应控制cl在上限。
2、高区有铜粒或针孔时,应升高cl,补加sy-125 0.5ml/l。
3、所有原料应使用试剂级(cp级或ar级)。-- 6.14.4 赫尔槽实验光剂的分析方法
6.14.4.1 仪器/器具:电镀整流器 磷铜阳极 抛光黄铜片 267ml容量赫尔槽 除油剂 10% 硫酸 6.14.4.2 步骤
6.14.4.2.1 除掉黄铜片表面的防护膜,并用细砂纸擦光亮; 6.14.4.2.2 浸在除油剂中约3-5分钟; 6.14.4.2.3 取出黄铜片,用去离子水清洗干净; 6.14.4.2.4 浸在稀硫酸中约2-3分钟; 6.14.4.3.5 将黄铜片放入赫尔槽内,加入镀铜液至有效刻度,即276ml,打气搅拌,将电镀整流器正、负电极的夹子分别夹在磷铜片阳极及黄铜片上,电流调整至20a,时间设定为10分钟; 6.14.4.3.6 待镀10分钟后取出黄铜片,用去离子水清洗干净并吹干; 6.14.4.3.7 吹干后的黄铜片与赫尔槽标准卡对比,观察相应电流下阴影部分的光亮程度及镀层质量, 根据对比结果调整镀液。 6.15 镀锡剂的分析方法 6.15.1 h2so4分析
6.15.1.1取2ml待测液至250ml锥形瓶中,加入50ml纯水摇匀,再加入2-3d甲基橙指示剂,用1.0mol/l naoh标准溶液滴定至溶液变为橙黄色为终点。 6.15.1.2 计算:h2so4 (ml/l) = 13.3×(标准液耗量)mlnaoh 6.15.2 snso4分析
6.15.2.1 取20ml 20%盐酸溶液至250ml锥形瓶中,加入30 ml纯水后再加入5ml待测液摇匀,加入2-3滴淀粉指示剂,用0.1mol/l i2标准溶液滴定至溶液变为蓝色为终点。 6.15.2.2 计算:snso4(g/l) = 2.145×(标准液耗量)mli2
第18篇:PCB工艺总结
PCB工艺总结:
第一章、原材料
1、基板:一般印制电路板用基板材料可分为两大类:刚性基板材料和柔性基板材料。一般刚性基板材料的重要品种是覆铜板。它是用增强材料(包括玻纤布基覆铜板;纸基覆铜板;复合基覆铜板,另外还有特殊增强材料构成的覆铜板还有:芳酰胺纤维无纺布基覆铜板、合成纤维基覆铜板等),浸以树脂胶黏剂(即绝缘材料,酚醛树脂、环氧树脂(EP)、聚酰亚胺树脂(PI)、聚酯树脂(PET)、聚苯醚树脂(PPO或)、氰酸酯树脂(CE)、聚四氟乙烯树脂(PTFE)、双马来酰亚胺三嗪树脂(BT)),通过烘干、裁剪、叠合成坯料,然后覆上铜箔,用钢板作为模具,在热压机中经高温高压成形加工而制成的。一般的多层板用的半固化片,则是覆铜板在制作过程中的半成品(多为玻璃布浸以树脂,经干燥加工而成)。
2、铜箔:覆铜板的铜箔在出厂前需要进行表面处理。(有电镀铜箔和碾压铜箔,后者主要用在挠性产品中。) A 传统处理
a、瘤化处理:在粗面迅速镀一层铜 b、是否镀锌、镀镍处理 c、是否进行钝化处理
3、防焊漆:主要作用是留出板上等焊的通孔及PAD(锡垫),将其它的线路及铜面盖住,防止波焊时造成短路;防止湿气及各种电解质侵害线路、防止外来的机械伤害;绝缘功能。
防焊油漆颜色有绿、黄、白、黑。种类主要有环氧树脂IR烘烤型、UV硬化型、液态感光型,干膜防焊漆。
环氧树脂IR烘烤型:
UV硬化型:
液态感光型:液态感光双组份防焊油墨吧,其主要成份是:树脂,色粉,铜面促进剂,消泡剂,稳定剂等
干膜防焊漆:
4、油墨:
第二章 生产工工艺
一、内层制作工艺
1、裁板、磨边:将一张大料根据不同拼板要求用机器切成小料的过程。开料后的板边尖锐,容易划伤手,同时使板与板之间擦花,所以开料后再用磨边机磨边。
2、铜面处理:在印刷电路板制程中不管那一个步骤,铜面的清洁与粗化的效果关系着下一工序的成败。以下工序需要进行铜面处理: a.干膜压膜;b.内层氧化处理前; c.钻孔后;d.化学铜前;e.镀铜前;
f.绿漆前;g.喷锡(或其它焊垫处理流程)前;h.金手指镀镍前
除a.c.f.g.外,其余工序的铜面处理皆属制程自动化中的一部分。 (1)铜面处理工艺(a.刷磨法、b.喷砂法、c.化学法) 1刷磨法:需要做刷良试验,确定刷深及均匀性。 ○
a、优点: 成本低、制程简单弹性;
b、缺点: 薄板细线路板不易进行、基材拉长不适内层薄板、刷痕深时易造成D/F附着不易而渗镀、有残胶之潜在可能
c、工艺流程:利用刷磨均匀抛刷铜面其平整且刷痕一致,获得均匀的粗糙度,对油墨有良好的附著力。刷磨轮分三种: 尼龙刷磨;白毛清洗刷磨(无研磨剂)、不织布刷磨轮;
2.喷砂法:喷砂材料由70%矿物化火山岩组成,去除氧化物,粗糙铜面。○3 化学微蚀法(发展趋势,因为产品向着超薄方向发展):只针对内层薄片○(厚度小于8mil)使用。有时与刷磨工序联合使用。主要微蚀液为sps(过硫酸钠)+硫酸,过硫酸铵+硫酸体系;双氧水+硫酸体系.微蚀速度40~60u/s.
3、图像转移
(1)印刷法(将逐步被干膜法替代):下列是目前尚可以印刷法cover的制程: a.单面板之线路,防焊 ( 大量产多使用自动印刷,以下同) b.单面板之碳墨或银胶 c.双面板之线路,防焊 d.湿膜印刷 e.内层大铜面 f.文字
g.可剥胶(Peelable ink) (2)丝网印刷:
丝网印刷中几个重要基本原素:网材,网版,乳剂,曝光机,印刷机,刮刀,油墨,烤箱等,.a.网布材料
(1) 依材质不同可分丝绢(silk),尼龙(nylon),聚酯(Polyester,或称特多龙),不锈钢,等.电路板常用者为后三者.(2) 编织法:最常用也最好用的是单丝平织法 Plain Weave.b.网版(Stencil)的种类
(1).直接网版(Direct Stencil) 将感光乳胶调配均匀直接涂布在网布上烘干后连框共同放置在曝光设备台 面上并覆以原稿底片再抽真空使其密接感光经显像后即成为可印刷的网 版通常乳胶涂布多少次,视印刷厚度而定.此法网版耐用,安定性高,用于大 量生产.但制作慢,且太厚时可能因厚薄不均而产生解像不良.(2).间接网版(Indirect Stencil) 把感光版膜以曝光及显像方式自原始底片上把图形转移过来然后把已有图 形的版膜贴在网面上待冷风干燥后撕去透明之载体护膜即成间接性网版 其厚度均匀,分辨率好,制作快,多用于样品及小量产.c.油墨
油墨的分类有几种方式 (1).以组成份可分单液及双液型.(2).以烘烤方式可分蒸发干燥型化学反应型及紫外线硬化型(UV) (3).以用途可分抗蚀,抗镀,防焊,文字,导电,及塞孔油墨.不同制程选用何种油墨,须视各厂相关制程种类来评估,如碱性蚀刻和酸性蚀刻 选择之抗蚀油墨考虑方向就不一样.d、烘烤
不同制程会选择不同油墨, 烘烤条件也完全不一样,须根据厂商提供的 data sheet,再依厂内制程条件的差异而加以修改.一般因油墨组成不一 烘烤方式有风干,UV,IR等烤箱须注意换气循环温控时控等.
3、干膜法:
4、蚀刻:用于蚀刻的化学药液种类常见者有两种:一是酸性氯化铜(CuCl2) 蚀刻液,一种是碱性氨水蚀刻液,主要配方见下图:
酸性蚀刻液中CU2+浓度控制:
a.CuCl2酸性蚀刻反应过程之分析
铜可以三种氧化状态存在原子形成Cu°, 蓝色离子的Cu++以及较不常见 的亚铜离子Cu+金属铜可在铜溶液中被氧化而溶解见下面反应式1 Cu°+Cu++2 Cu+ ------------- (1) 在酸性蚀刻的再生系统就是将Cu+氧化成Cu++,因此使蚀刻液能将更多的 金属铜咬蚀掉
以下是更详细的反应机构的说明 b.反应机理及过程
直觉的联想在氯化铜酸性蚀刻液中Cu++ 及Cu+应是以CuCl2 及CuCl存 在才对但事实非完全正确两者事实上是以和HCl形成的一庞大错化物存 在的
Cu° + H2CuCl4 + 2HCl 2H2CuCl3 ------------- (2) 金属铜 铜离子 亚铜离子
其中H2CuCl4 实际是 CuCl2 + 2HCl 2H2CuCl3 实际是 CuCl + 2HCl 在反应式(2)中可知HCl是消耗品即使(2)式已有些复杂但它仍是以下两 个反应式的简式而已
Cu°+ H2CuCl4 2H2CuCl3 + CuCl (不溶) ---------- (3) CuCl + 2HCl 2H2CuCl3 (可溶) ---------- (4) 式中因产生CuCl沈淀会阻止蚀刻反应继续发生但因HCl的存在溶解 CuCl维持了蚀刻的进行由此可看出HCl是氯化铜蚀刻中的消耗品而且 是蚀刻速度控制的重要化学品。
1) 蚀刻机理:
Cu+CuCl2→Cu2Cl2 Cu2Cl2+4Cl-→2(CuCl3)2-
2) 影响蚀刻速率的因素:影响蚀刻速率的主要因素是溶液中Cl-、Cu+、Cu2+的含量及蚀刻液的温度等。 a、Cl-含量的影响:溶液中氯离子浓度与蚀刻速率有着密切的关系,当盐酸浓度升高时,蚀刻时间减少。在含有6N的HCl溶液中蚀刻时间至少是在水溶液里的1/3,并且能够提高溶铜量。但是,盐酸浓度不可超过6N,高于6N盐酸的挥发量大且对设备腐蚀,并且随着酸浓度的增加,氯化铜的溶解度迅速降低。 添加Cl-可以提高蚀刻速率的原因是:在氯化铜溶液中发生铜的蚀刻反应时,生成的Cu2Cl2不易溶于水,则在铜的表面形成一层氯化亚铜膜,这种膜能够阻止反应的进一步进行。过量的Cl-能与Cu2Cl2络合形成可溶性的络离子(CuCl3)2-,从铜表面上溶解下来,从而提高了蚀刻速率。 b、Cu+含量的影响:根据蚀刻反应机理,随着铜的蚀刻就会形成一价铜离子。较微量的Cu+就会显著的降低蚀刻速率。所以在蚀刻操作中要保持Cu+的含量在一个低的范围内。 c、Cu2+含量的影响:溶液中的Cu2+含量对蚀刻速率有一定的影响。一般情况下,溶液中Cu2+浓度低于2mol/L时,蚀刻速率较低;在2mol/L时速率较高。随着蚀刻反应的不断进行,蚀刻液中铜的含量会逐渐增加。当铜含量增加到一定浓度时,蚀刻速率就会下降。为了保持蚀刻液具有恒定的蚀刻速率,必须把溶液中的含铜量控制在一定的范围内。 d、温度对蚀刻速率的影响:随着温度的升高,蚀刻速率加快,但是温度也不宜过高,一般控制在45~55℃范围内。温度太高会引起HCl过多地挥发,造成溶液组分比例失调。另外,如果蚀刻液温度过高,某些抗蚀层会被损坏。
5、剥膜:剥膜在pcb制程中有两个工序会使用:一是内层线路蚀刻后之D/F剥除,二 是外层线路蚀刻前(剥除(若外层制作为负片制程))。化学药液多为NaOH或KOH浓 度在1~3%重量比。内层之剥膜后有加 酸洗中和也有防铜面氧化而做氧化处理者。
6、AOX检测:内层板线路成完后,必须保证通路及绝缘的完整性(integrity),即如同单面板一样先要仔细检查因一旦完成压合后,不幸仍有缺陷时,则已为时太晚,对于高层次板子而言更是必须先逐一保证其各层品质之良好,始能进行压合, 由于高层板渐多,内层板的负担加重,且线路愈来愈细,万一有漏失将会造成压合后的昂贵损失.传统目视外,自动光学检查(AOI)之使用在大厂中已非常普遍, 利用计算机将原图案牢记,再配合特殊波长光线的扫瞄,而快速完美对各层板详作检查但AOI有其极限,例如细断路及漏电(Leakage)很难找出,故各厂渐增加短断路电性测试。
7、压合:
(1)表面氧化处理:
A.增加与树脂接触的表面积,加强二者之间的附着力(Adhesion).B.增加铜面对流动树脂之润湿性,使树脂能流入各死角而在硬化后有更强的抓地力
C.在裸铜表面产生一层致密的钝化层(Paivation)以阻绝高温下液态树脂中胺类(Amine)对铜面的影响
主要有黑化与棕化工艺:
黑化:黑化工艺:它是一种氧化处理在碱性介质中的一种化学反应, 使得树脂与铜面的接触面积增大,结合力加强。在化学反应中通常使用强氧化剂亚氯酸钠(NaclO2)、高锰酸钾(K2MnO4)等,以NaclO2化学反应为例: 4Cu+NaCLO2 ------ 2Cu2O+NaCL 2Cu2O+NaCLO2 ------ 4CuO+NaCL 黑氧化处理的产物主要是氧化铜(CuO), 黑化层因液中存有高碱度而杂有Cu2O,此物容易形成长针状或羽毛状结晶。此种亚铜在高温下容易折断而大大影响铜与树脂间的附着力, 并随流胶而使黑点流散在板中形成电性问题,而且也容易出现水份而形成高热后局部的分层爆板。黑化因结晶较长,厚度较厚,一般铜面的瑕疵较容易盖过去而能得到色泽均匀的外表。但光面的黑化层却容易受酸液之侧攻而现出铜之原色,有些人认为黑化的产物是氧化铜和氧化亚铜,这是业内的一些错误论调,经过分析,可以测定铜原子和氧原子之间的结合能,氧化物表面铜原子和氧原子之间的比例;
黑化同时也带来了一种缺陷,黑化层较厚,经PTH后常会发生粉红圈, 这是因 PTH中的微蚀或活化或速化液攻入黑化层而将之还原露出原铜色之故。对于粉红圈的处理又分为还原法和溶解法,其解决方法是提高黑化膜的抗酸能力,但是整个生产成本明显增高。
棕化:棕化过程是铜在一种酸性的介质中的一种化学反应,棕化处 理的产物主要是氧化亚铜(CU20),棕化层则呈碎石状瘤状结晶贴铜面,其结构紧密无疏孔,与胶片间附着力远超过黑化层,不受高温高压的影响,成为聚亚醯胺,另外氧化亚铜膜具有致密、完整、均匀提供一致性的粗糙度,为下一步有机金属转化膜提供了良好的物理结构。
棕化液的组成[3~6]:
① 硅烷类化合物,特别是易水解成膜的硅烷偶联剂,使用一种或多种,有些不易溶于水,需要使用醇类有机溶剂,辅助溶解,最佳使用浓度质量百分比1%-5%(未水解时的浓度)。加入棕化液前,令硅烷部分或完全水解。水解处理就是把硅烷与酸性水混合搅拌,或者与含醇类化合物的水混合。
② 唑、吡咯等化合物。咪唑、苯并咪唑、三唑、苯并三唑等衍生物。如1,2,3-三唑,1,2,4-三唑,3-甲基-1,2,4-三唑,羟基苯并三唑等。使用浓度:重量百分比0.1%-10%。最佳1%-3%。
③ 氧载体。如过氧化氢。有助于唑类化合物吸附于铜表面,若缺少,则唑类化合物无法吸附于铜面上。原因:很薄的一层铜被氧氧化后,铜表面很可能首先形成了铜-唑类化合物。用量:重量百分比0.1%-5%,最好1%-2%。太少则处理时间过长,太多则微蚀过度。过氧化氢在这里的作用不是微蚀形成粗糙铜,而是去除一薄层铜,有利于有机铜层的沉积,该层能有效地提高结合力。
④ 有机或无机酸。如硫酸、磷酸、硝酸,醋酸、甲基磺酸、乙醇酸、柠檬酸等。其中硫酸最好,成本低,不会增加废液处理难度。硫酸作用:一方面有利于硅烷水解,另一方面有利用去除一薄层铜。使用浓度:重量百分比1%-40%,最好5%-15%。
⑤ 锌化合物。可溶性的有机或无机锌盐。如硝酸锌、硫酸锌、磷酸锌、醋酸锌、甲烷磺酸锌。使用浓度:重量百分比0.01%-20%。最佳0.2%-2%。作用:在铜面吸附的第一层唑类化合物与后续吸附的唑类化合物之间,锌化合物参与形成配位络合物,这样可以形成足够厚的沉积层,该沉积层表现为暗棕色,适合应用于线路板制造。如果不使用锌化合物,则沉积层厚度很薄、颜色很淡,并且沉积层非常不均匀。
⑥ 过氧化氢稳定剂:苯磺酸、乙二胺四乙酸、巯基乙酸、硅酸钠。重量百分比浓度0.001%-1%,依稳定剂种类不同,选择相应浓度。
棕化工序:碱清洗→DI水洗→预浸液→棕化液→DI水洗→烘干。碱洗目的是除去铜表面的有机残渣和轻微的氧化层。预浸目的是保证铜表面的化学活泼性,使棕化变得快速和均匀,其中棕化是整个生产线的关键。
工艺条件:
① 使用PVC或聚四氟乙烯槽,采用摇摆或轻微搅拌。 ② 浸渍或水平喷淋。 ③ 处理温度为 30℃~38℃。温度低则耗时长,温度高则铜易微蚀过度,且过氧化氢会分解。 ④ 处理时间为30秒~75秒 (水平喷淋)。
各组分的作用 ① 硫酸:帮助双氧水微蚀铜,水解含OH的有机聚合物,使其中的R基团变为H,以增强有机聚合物与铜的结合力。 ② 双氧水作用是蚀刻一层很薄的铜,促使有机金属层沉积在金属铜面上。过硫酸铵(钠)等也可以使用,但文献认为双氧水更好[7]。
③ 含OH的有机A:其与相同分子之间反应的同时与半固化环氧树脂聚合;同时与含N 的杂环化合物B、金属铜(含OH)形成化学键。
④ 含N的杂环化合物B:与基体铜结合外,通过A的桥键与环氧树脂结合,含N的杂环化合物分子间通过铜离子以配位键的形式连接起来,增加了棕化层的厚度和平整性。 ⑤ 氯离子:对板子的颜色、微蚀厚度、抗撕强度有很大影响。需要监测其浓度。 ⑥ 3,5-二硝基水杨酸等含硝基的有机化合物[7],可以与金属表面反应,特别是铜和铜合金,以提供均匀的金属转化层,该层有利于和聚合物材料成键。
棕化液再生:棕化处理是一个化学蚀铜反应过程,随着棕化生产的进行,棕化液中的铜离子浓度不断上升,当铜离子超过一定限量后,棕化液便会因铜离子过多而产生棕化铜面发白、棕化铜面色泽不均等品质问题,因此,此时棕化槽液必须进行处理,使铜离子控制在一定范围内,从而保证棕化产品的品质。通常棕化过程中铜离子浓度达到一定限量后,需要不断排放棕化液,同时补充添加液以降低铜离子浓度,且保持棕化槽各有效组分含量的稳定。 为了提高棕化液的利用率,可以收集排放的棕化液A,经过除铜和调整处理后作为棕化添加液B使用,即将棕化液A经过浓缩,成为铜离子含量较高的浓缩液,然后经过冷却结晶析出硫酸铜晶体,使溶液铜离子含量降低,最后通过对棕化液有效成分分析调整,得到添加液B,再添加到棕化生产过程中,达到棕化液循环使用的目的。
主要工艺流程:A.碱性清洗- 也有使用酸洗.市售有多种专业的化药,能清除手指纹油脂,scum或有机物
B.酸浸-调整板面PH,若之前为酸洗,则可跳过此步骤.C.微蚀- 微蚀主要目的是蚀出铜箔之柱状结晶组织(grain structure)来增加表面积,增加氧化 后对胶片的抓地力通常此一微蚀深度以50-70微英吋为宜微蚀对棕化层的颜色均匀上非 常重要, D.预浸中和- 板子经彻底水洗后,在进入高温强碱之氧化处理前宜先做板面调整 ,使新鲜的铜 面生成- 暗红色的预处理,并能检查到是否仍有残膜未除尽的亮点存在
E.氧化处理-市售的商品多分为两液,其一为氧化剂常含以亚氯酸钠为主,另一为氢氧化钠及添 加物,使用时按比例调配加水加温即可通常氢氧化钠在高温及搅动下容易与空气中的二氧化 碳形成碳酸钠而显现出消耗很多的情况,因碱度的降低常使棕化的颜色变浅或不均匀,宜分析 及补充其不足温度的均匀性也是影响颜色原因之一,加热器不能用石英,因高温强碱会使硅 化物溶解操作时最好让槽液能合理的流动及交换
F.还原此步骤的应用影响后面压合成败甚巨.G.抗氧化此步骤能让板子的信赖度更好,但视产品层次,不一定都有此步骤.H.后清洗及干燥-要将完成处理的板子立即浸入热水清洗,以防止残留药液在空气中干涸在板面 上而不易洗掉,经热水彻底洗净后,才真正完工 (2)、叠板
胶片相态变化:胶片中的树脂为半硬化的 B-Stage 材料,在受到高温后即会软化及流动,经过一段软化而流动 的时间后,又逐渐吸收能量而发生聚合反应使得黏度增大再真正的硬化成为 C-Stage 材料。 压合机种类:
a、舱压式压合机:压合机构造为密闭舱体,外舱加压、内袋抽真空受热,压合成型。各层板材所承受之热力与压力来自四面八方加压加温之惰性气体
优点: 因压力热力来自于四面八方故其成品板厚均匀流胶小可使用于高楼层
缺点: 设备构造复杂成本高且产量小
b、液压式压合机:液压式压合机构造有真空式与常压式。其各层开口之板材夹于上下两热压盘间,压力由下往上压,热力藉由上下热压盘加热传至板材。 优点:a.设备构造简单成本低且产量大 b.可加装真空设备有利排气及流胶 缺点: 板边流胶量较大板厚较不均匀 C.ADARA SYSTEM Cedal 压合机 Cedal为一革命性压合机,其作动原理为在一密闭真空舱体中利用连续卷状铜箔迭板。在两端通电流,因其电阻使铜箔产生高温,加热。Prepreg用热传系数低之材质做压盘,藉由上方加压达到压合效果。因其利用夹层中之铜箔加热,所以受热均匀,内外层温差小,受压均匀 。比传统式压合机省能源故其操作成本低廉。 优点: a.利用上下夹层之铜板箔通电加热省能源操作成本低 b.内外层温差小受热均匀产品品质佳 c.可加装真空设备有利排气及流胶 d.Cycle time短约4Omin.e.作业空间减小很多.f.可使用于高楼层
缺点: 设备构造复杂成本高且单机产量小迭板耗时 压合机热源:
a、电加热式:于压合机各开口中之压盘内安置电加热器直接加热 优点: 设备构造简单成本低保养简易
缺点: a.电力消耗大;b.加热器易产生局部高温使温度分布不均 b、加热软水使其产生高温高压之蒸汽直接通入热压盘: 优点: 因水蒸汽之热传系数大热媒为水较便宜
缺点: a.蒸气锅炉必需专人操作设备构造复杂且易锈蚀,保养麻烦;b.高温高压操作危险性高
C.藉由耐热性油类当热媒以强制对流方式输送将热量以间接方式传至热压盘 优点: 升温速率及温度分布皆不错操作危险性较蒸汽式操作低 缺点: 设备构造复杂价格不便宜保养也不易 D.通电流式: 利用连续卷状铜箔迭板在两端通电流因其电阻使铜箔产生高温加热Prepreg用热传系数低之材质做压盘减少热流失
优点: a.升温速率快(35/min.)内外层温差小及温度分布均匀;b.省能源操作成本低廉
缺点: a.构造复杂设备成本高 叠板结构:
若压合机有十二个开口,每一开口有上下热压盘,共十三个热压盘。迭板方式以钢质载盘为底盘,放入十二张牛皮纸及一张铜箔。基板中间以一层镜面钢板一层板材的方式迭入十二层板材,上面再加一层镜面钢板及一张铜箔基板和十二张牛皮纸再盖上钢质盖板.A-1 迭板结构各夹层之目的
a.钢质载盘,盖板(Pre plate): 早期为节省成本多用铝板,近年来因板子精密度的提升已渐改成硬化之钢板,供均匀传热用.b.镜面钢板(Separator plate): 因钢材钢性高, 可防止表层铜箔皱折凹陷,拆板容易。钢板使用后如因刮伤表面或流胶残留无法去除,就应加以研磨。
c.牛皮纸: 因纸质柔软透气的特性可达到缓冲受压均匀施压的效果,且可防止滑动。因热传系数低可延迟热传均匀传热之目的,在高温下操作牛皮纸逐渐失去透气的特性,使用三次后就应更换 。
d.铜箔基板:其位于夹层中牛皮纸与镜面钢板之间,可防止牛皮纸碳化后污染镜面钢板或黏在上面,缓冲受压均匀施压
e.其它有脱模纸 (Release sheet)及压垫 (Pre pad) Conformal pre的运用,大半都用在 软板coverlayer压合上.压板过程中压力变化:
a.初压(吻压 Ki preure):每册(Book)紧密接合传热,驱赶挥发物及残余气体
b.第二段压:使胶液顺利填充并驱赶胶内气泡,同时防止一次压力过高导致的皱折及应力
c.第三段压:产生聚合反应使材料硬化而达到C-stage d.第四段压:降温段仍保持适当的压力,减少因冷却伴随而来之内应力 压板后处理: a、后烤:通常后烤条件是150,4小时以上.如果先前压合步 骤curing很完整,可不做后烤,否则反而有害( 降低Tg ).目的:a.让聚合更完全.b.若外表有弯翘,则可平整之.c.消除内部应力并可改善对位.B.铣靶,打靶-完成压合后板上的三个箭靶会明显的出现浮雕(Relief), 手动作业:将之置于普通的单轴钻床下用既定深度的平头铣刀铣出箭靶及去掉原贴的耐热胶 带,再置于有投影灯的单轴钻床或由下向上冲的冲床上冲出靶心的定位孔,再用此定位孔定 在钻床上即行钻孔作业注意要定时校正及重磨各使用工具, b.X-Ray透视打靶: 有单轴及双轴,双轴可自动补偿取均值,减少公差.C.剪边(CNC裁板):-完成压合的板子其边缘都会有溢胶,必须用剪床裁掉。以便在后续制程中作业方便及避免造成人员的伤害,剪边最好沿着边缘直线内1公分处切下,切太多会造成电镀夹点的困扰,最好再用磨边机将四个角落磨圆及边缘毛头磨掉,以减少板子互相间的刮伤及对槽液的污染。或者现在很普遍直接以CNC成型机做裁边的作业。
8、钻孔
钻孔房环境设计
A.温湿度控制: 一般钻房的温度应控制在18-22℃、相对湿度≦50€‚当温湿度不符合要求,会影响钻机的性能表现。
B.干净的环境:钻房环境力求清洁。钻机清理时不可使用高压风枪吹尘,此举一方面会影响操作员健康,另一方面会影响钻机的寿命及精度。
C.地板承受之重量 D.绝缘接地的考量 E.外界振动干扰
钻孔过程使用的物料:
钻针(a.硬度高耐磨性强的碳化钨(94%b.耐冲击及硬度不错的钴(4%)、c.有机黏合剂)、盖板、垫板。
9、镀通孔:
其目的使孔壁上之非导体部份之树脂及玻纤束进行金属化( metalization ), 以进行后来之电镀铜制程,完成足够导电及焊接之金属孔壁。主要包括以下几个步骤:
(1)去巴里:钻完孔后,若是钻孔条件不适当,孔边缘有1.未切断铜丝2.未切断玻纤的残留,称为burr.因其要断不断,而且粗糙,若不将之去除,可能造成通孔不良及孔小,因此钻孔后会有de-burr制程.也有de-burr是放在Desmear之后才作业.一般de-burr是用机器刷磨,且会加入超音波及高压冲洗的应用.(2)除胶渣 (Desmear) A.目的: a.去胶渣
b.创造表面粗糙的微孔,增加结合力。 B.Smear产生的原因: 由于钻孔时造成的高温Resin超过Tg值而形成融熔状终致产生胶渣 此胶渣生于内层铜边缘及孔壁区会造成P.I.(Poor lnterconnection) C.除胶渣的四种方法: 硫酸法(Sulferic Acid) 、电浆法(Plasma)、铬酸法(Cromic Acid) 、高锰酸钾法(Permanganate).a.硫酸法:必须保持高浓度但硫酸本身为脱水剂很难保持高浓度且咬蚀出的孔面光滑无微孔,并不适用。
b.电浆法:效率慢且多为批次生产,而处理后大多仍必须配合其它湿制程处理。因此除非生产特殊板大多不予采用。
c.铬酸法:咬蚀速度快,但微孔的产生并不理想,且废水不易处理又有致癌的潜在风险故渐, 被淘汰
d.高锰酸钾法:因配合溶剂制程可以产生微孔同时由于还原电极的推出使槽液安定性获得较佳控制因此目前较被普遍使用。
高锰酸钾法(KMnO4 Proce)简介: A.膨松剂(70度,主要成分氢氧化钠、已二醇乙醚、已二醇,5min): a.功能:软化膨松Epoxy降低 Polymer 间的键结能使KMnO4 更易咬蚀形成 Micro-rough 速 率 作 用 Concentration b.不可和KMnO4 直接混合以免产生强烈氧化还原发生火灾 c.原理解释: (1)初期溶出可降低较弱的键结,使其键结间有了明显的差异。若浸泡过长,强的链接也渐次降低,终致整块成为低链接能的表面。如果达到如此状态将无法形成不同强度结面。若浸泡过短则无法形成低键结及键结差异如此 将使KMnO4咬蚀难以形成蜂窝面,终致影响到PTH的效果。
(2) 表面张力的问题: 无论大小孔,皆有可能有气泡残留。而表面力对孔内湿度也影响颇大。故 采用较高温操作有助于降低表面张力及去除气泡。至于浓度的问题,为使Drag out降低减少消耗而使用略低浓度,事实上较高浓度也可操作且速 度较快
在制程中必须先湿润孔内壁以后才能使药液进入作用。否则有空气残留后续制程更不易进入孔内其Smear将不可能去除
B.除胶剂 (80度 ): a.使用KMnO4的原因:选KMnO4而未选NaMnO4是因为KMnO4溶解度较佳,单 价也较低
b.反应原理: 4MnO4- + C + 4OH- =MnO4 + CO2 + 2H2O (此为主反应式) 2MnO4- + 2OH- 2MnO4= + 1/2 O2 + H2O (此为高PH值时自发性分解反应) MnO4- + H2O MnO2 + 2OH- + 1/2 O2 (此为自然反应会造成Mn+4沉淀) c.作业方式:早期采氧化添加剂的方式。目前多用电极还原的方式。操作不稳 定的问题已获解决
d.过程中其化学成份状况皆以分析得知但Mn+7为紫色, Mn+6为绿色,Mn+4 为黑色可由直观的色度来直接判断大略状态若有不正常发生则可能 是电极效率出了问题须注意
除胶剂再生:KMnO4的再生:要提高KMnO4工作液的使用效率,必须考虑将溶液中的MnO4 2-再生转变为MnO4 -,目前
普遍采用的是电解再生法,再生器利用的是阴极为大面积的不锈钢柱形圆筒,阳极为钛材料,其与阴极的面积比很小,MnO4-2-在阳极表面发生的反应为MnO4-2--e→MnO4- 。使用450~~550A的整流器,由于MnO4 2-不断地氧化成MnO4 -,因此工作液中不需大量添加KMnO4原料,它的少量添加是为了平衡工作液的带出损耗,因而大大降低了生产成本,使用较长时间的工作液在槽底会形成沉淀,需定期清除,以保证处理效果。
MLB214D为树脂蚀刻促进剂,可提高KMnO4的树脂蚀刻能力,提高工作液的润湿性,减少孔内气泡,其为白色粉末状固体。
C.中和剂(40度):由于锰是重金属,它的存在会使钯中毒,使钯离子或原子失去活化性能。必须把Mn7+/ Mn6+/MnO2用酸中和成为Mn2+,反应机理如下:
a.NaHSO3是可用的中和之一。其原理皆类似Mn or Mn+6 or Mn+4(Neutralizer)->Mn+2 (Soluable) b.为免于粉红圈,在选择Acid base必须考虑。HCl及 H2SO4系列都有。但Cl易攻击氧化层。所以用H2SO4/双氧水为Base 的酸较佳(还含有草酸钠)。
c .药液使用消耗分别以H2SO4及Neutralizer用自动控制设备来补充维护。 (3)整孔:
除胶渣后孔内呈现双极现象,其中Cu呈现高电位正电,Gla fiberEpoxy呈负电,整孔使表面清洁,孔壁呈正电性,以利Pd/Sn Colloid负电离子团吸附。
采用阴离子表面活性剂和硫酸。 (4)微蚀:
清除清孔后表面之所形成的薄膜和氧化物。微蚀液种类:sps(过硫酸钠)+硫酸,过硫酸铵+硫酸体系;双氧水+硫酸体系.微蚀速度40~60u/s.(5) 预活化 Catalpretreatment 1.为避免微蚀形成的铜离子带入Pd/Sn槽,污染槽液。 2.降低孔壁的表面张力
预浸槽与活化槽的成分基本相同,区别在于预浸槽中不含活化剂钯。 酸性胶体钯预浸液成分:SnCl2 :30g/L、HCl:30ml/L、NaCl:200g/L、脲素:50g/L (6) 活化
①活化反应机理:溶液中的Sn2+ 和Pd2+ 的浓度为2:1时所得到的活化液活化性能最好,因此时Sn2+ 和Pd2+ 在溶液中反应形成不稳定的络合物, Pd 2+ + 2Sn2+ →〔PdSn2〕6+ →Pd+Sn4+ +Sn 2+在30℃时〔PdSn2〕6+ 络离子歧化反应12min,大约有90%以上的络合离子被还原成金属钯,它 们呈现出极其细小的金属颗粒分散在溶液中,当加入大量Sn2+ 的和Cl -- 时,这些细小的钯核表面上很快吸附大量的Sn2+ 的和Cl-,形成带负电的胶体化合物 〔Pd(SnCl3)〕-,这些胶体化合物悬浮在溶液中(负 负相斥),不会沉聚,胶体钯在酸性环境中较稳定,当表面带正电荷的印制板浸入处理液后,胶体钯会很快被基材吸附,而完成活化处理。活化处理过的印制板,在水洗时,表面的SnCl2水解形成碱式锡酸盐沉淀。
②目前市售的胶体钯活化剂大多为盐基胶体钯。PdCl2:1g/l、NaCl:250g/l、SnCl2:12。8g/l、HCl:40ml/l、Na2SnO3:2g/l脲素:50g/l。
③CAT44浓缩液是一种不易燃,酸性,深褐色的液体,每公升大约含钯4。7g,比重约1。2。
(7) 速化 Accelerator
+71.Pd胶体吸附后必须去除Sn使Pd2+曝露如此才能在未来无电解铜中产生催化作用形成化学铜,实质是使碱式锡酸盐溶解,可用酸也可用碱处理,效果最好的是 1%的HBF4处理1~~2min。
2.基本化学反应为
Pd+2/Sn+2 (HF)Pd+2(ad) + Sn+2 (aq) Pd+2(ad) (HCHO)Pd(s) (8)化学镀铜
镀液成分及作用:
铜盐(253A CuSO4²5H2O)、
络合剂(253E EDTA 络合铜离子,减缓沉积速率),
还原剂(甲醛,次磷酸盐(新的还原剂,反应机理:Cu2+ + H2PO2- +H2O ====Cu↓+ H2PO3+2H+(酸性);Cu2+ + H2PO2- +2OH- ====Cu↓+ H2PO3+H2O(碱性)),
PH值调节剂 (NaOH,甲醛在强碱条件下才具有还原性,因此必须加入适量的碱。
添加剂:溶液中存在微量的Cu+ ,其歧化反应形成的铜粉具有催化作用,易加速化学铜溶液的分解。添加剂能络合Cu+ ,减小Cu+ 的干扰。
反应机理:
正常反应为 2HCHO+4OH++Cu2+→Cu+2HCOO-+H2O+H2 从反应式可看出,溶液必须为强碱性,HCHO的还原能力取决于碱性强弱,即PH值。在碱性中,必须有足够的络合剂,以稳定Cu2+不致生成 沉 淀。溶液中的相应成分必须保持相应的一定比例。同时反应必须有催化剂的催化作用。
副反应: 不管镀铜液使用与否,总是存在以下两个反应: Cu2O的生成:2Cu2+ +HCHO+5OH-→Cu2O+HCOO-+3H2O Cu2O +H2O→2Cu+ +2OH- 2Cu+ →Cu2+ +Cu 形成的铜 粉是分子量级的,分散于溶液中,这些小颗粒具有催化能力,当铜粉数量较多时,就会引起沸腾式的反应,导致溶液迅速分解。 HCHO与NaOH的反应:2HCHO+OH-→HCOO-+CH3OH 对于放置不用的化学铜液,几天后,因歧化反应,HCHO变成CH3OH和HCOOH,且消耗大量的NaOH,溶液PH值变低,因此放置不用的溶液重新起用时,必须重新调整HCHO和PH值,特别是HCHO含量小于3g/L时,会加速Cu2O的生成,加速铜液的分解。
目前新工艺:超声波辐射化学镀铜、激光增强化学镀、无钯化学镀 (9)剥挂架
10、一次铜
非导体的孔壁经PTH金属化后立即进行电镀铜制程, 其目的是镀上200~500微英吋以保护仅有20~40微英吋厚的化学铜被后制程破坏而造成孔破(Void)。
三、外层制作
1、铜面前处理(同内层制作工序)
2、压干膜:(溶剂显像型、半水溶液显像型、碱水溶液显像型),目前流行的为碱水溶液显像型,以碳酸钠显像、用稀氢氧化钠剥膜。
一、干膜的结构和种类
(1)干膜制造印制电路的优点 分辨率高,能制造线宽0.1mm的图形,在干膜厚度范围以内都能获得边缘垂直的线条,保证线条精度;干膜的厚度和组成基本稳定,避免成像时的不连续性,可靠性高;便于掌握。应用干膜可大大简化印制板制造工序,有利于实现机械化和自动化。
(2)干膜结构 干膜由保护膜聚乙烯、光致抗蚀剂膜和载体聚酯薄膜三部分组成,三者厚度分别是25弘m,几十至100μm和25μm。
(3)干膜种类 依照干膜显影和去膜方法的不同,将干膜分成三类:溶剂型干膜、水溶性干膜和剥离型干膜。
根据干膜的用途,也将干膜分成三类:抗蚀干膜、掩孔干膜和阻焊干膜。 (4)干膜的主要成分及作用
①胶黏剂 主要是使胶膜具有一定的化学、物理及机械性能,通常是酯化或酰胺化的聚苯丁树脂。胶黏剂不含感光基团,属于光惰性物质,它与组分的混溶性、成膜性、显影性和去膜性良好。
②光聚合单体 是胶膜的主要成分,在光引发剂的存在下,经紫外光照射发生聚合反应,而不溶于显影液,未感光部分被显影掉,形成抗蚀干膜图像。光聚合单体还是增塑剂,直接影响干膜的韧性、抗蚀性及贴膜性。它主要采用高沸点、易混溶的多官能团不饱和酯类,如三乙二醇双丙烯酸酯,季四醇三烯酸酯等。 ③光引发剂 在紫外光的照射下分解成游离基,引发聚合和交联反应的物质常用安息醚,叔丁基蒽、醌等。 ④增塑剂 用于增加干膜的韧性,降低贴膜温度,常用的是三缩乙二醇二乙酸酯。
⑤增黏剂 可增强干膜与铜表面之间的结合力,克服干膜固化后与铜表面之间产生应力而黏附不牢引起胶膜起皮翘起、渗镀。常用增黏剂有苯并三氮,苯并咪唑等,是氮杂环化合物,与铜表面形成配价键结构而提高黏附力。
⑥热阻聚剂 在于膜的制造、运输、贮存和使用过程中,可能发生热聚合,影响干膜的解像力和显影性能。为阻止热能引发的干膜聚合,可在于膜抗蚀剂中加入了对苯二酚,对甲氧基酚等物质。
⑦色料为使干膜抗蚀剂感光显影后形成良好的视觉反差,在干膜中加入了孔雀石绿、甲基紫、亚甲基蓝等颜料。
⑧溶剂 干膜中常用溶剂是丙酮和乙醇。
操作环境:无尘室中进行万级以上,环境温度应控制在23°±3,相对湿度应保持50RH±5左右。操作人员也要带手套及抗静电之无尘衣帽。
压膜机可分手动及自动两种,有收集聚烯类隔层的卷轮、干膜主轮、加热轮、抽风设备等四主要部份。 一般压膜条件为:
压膜热轮温度 120°±10 板面温度 50±10 压膜速度 1.5~2.5米/分 压力 15-40 psi
3、曝光: 曝光机种类 手动与自动
平行光与非平行光 LDI雷射直接暴光
A.手动曝光机是将将欲曝光板子上下底片以手动定PIN(引线末端的一段,通过软钎焊使这一段与印制板上的焊盘共同形成焊点)对位后送入机台面 吸真空后曝光
B.自动曝机一般含Loading/unloading,须于板子外框先做好工具孔,做初步定位。再由机台上之CCDCheck底片与孔的对位状况并做微调后入曝光区。
C、非平行光与平行光的差异:平行光可降低Under-Cut 其差异点可见图8.5显影后的比较做细线路(4mil以下)非得用平行光之曝光机
D、LDI(Laser Direct Imaging)激光直接感光之设备与感光方式是利用特殊之感光膜coating在板面。不须底片直接利用激光扫描曝光其细线可做 到2mil以内利用多beam方式18in³24in的板子已有号称曝光时间仅30秒。
4、显影
显像是把尚未发生聚合反应的区域用显像液(碳酸钠)将之冲洗掉已感光部份则因已发生聚合反应而洗不掉仍留在铜面上成为蚀刻或电镀之阻剂膜注意在 显像前不可忘记把表面玻璃纸撕掉。
5、二次铜(负片制作): (1)脱脂 (2)水洗 (3)微蚀 (4)水洗 (5)酸浸 (6)镀铜 (7)水洗
(8)镀锡
镀液成分及作用:
硫酸铜:是供给槽液铜离子的主源。配槽时要用化学级之含水硫酸铜结晶溶解使用。平时作业中,则由阳极磷铜块解离补充。配液后要做活性炭处理(Carbon treatment)及假镀(是指对于重金属污染物,可用较大面积的电解镍板,经活化洗净后,进入镀液中进行电解,以此去除重金属离子。这种方法叫做“假镀”(dummy))
硫酸:要使用试药级的纯酸硫酸有导电及溶解阳极的功用。日常操作中铜量因 吹气的氧化作用使阳极膜的溶解增加故液中的铜量会渐增而酸量会渐减。要逐日作分析,以维持其酸与铜之重量比在10:1以上,以维持良好的分布力。镀液在不镀时要关掉吹气以防铜量上升酸量下降及光泽之过度消耗 。
氯离子:有助阳极的溶解及光泽剂的发挥功能。使阳极溶解均匀,镀层平滑光泽。氯离子正常时阳极膜呈黑色,过量时则变成灰白色,配液及添加用的水一 定要纯,不可用自来水。因其加有氯气或漂白粉含次氯酸盐会带入大量的氯离子
阳极:须使用含磷0.02-0.06的铜块其面积最好为阴极的两倍
添加剂:主要有活性剂(聚乙二醇)、光泽(乙撑硫脲,二硫苯骈咪唑,四氢噻唑硫酮)、整平()、载体、润湿(消除氢气泡吸附在镀层表面所产生的针孔,主要种类包含乙基巳基硫酸钠、乙基巳基硫酸钠)等功能。
镀液的过滤循环::一则使镀液流动,再则使浮游物被滤掉。其过滤速度应每小时至少使镀槽全部镀液能循环3次。当然速度愈大愈能降低扩散层的厚度,有利电镀。滤心要在5微吋以下之密度以达清洁之目的。
6、镀锡:
二次铜后镀锡铅合金的目的:
a.蚀刻阻剂, 保护其所覆盖的铜导体不会在碱性蚀铜时受到攻击 b.装配焊接, 须再经IR重熔,目前多已不使用.
由于铅对人体有颇大的为害,废液处理不便宜因此纯锡电镀已渐取代传统锡铅 镀锡液组成:硫酸亚锡,硫酸和添加剂(蛋白质(Peptone)白明胶(Gelatin)-Naphthol 邻苯二酚(Hydroquinone))组成,硫酸亚锡含量控制在35克/升左右,硫酸控制在10%左右。
镀锡前需要进行水洗和酸洗,以消除Cu2+等离子污染影响。
7、蚀刻:
A.剥膜:将抗电镀用途的干膜以药水剥除 B.线路蚀刻:把非导体部分的铜溶蚀掉
碱性环境下,蚀刻液成分见内层铜蚀刻工序。
在碱性环境溶液中铜离子非常容易形成氢氧化铜之沉淀,需加入足够的氨水,使产生氨铜缝合离子团。则可抑制其沉淀的发生。同时使原有多量的铜及继续溶解的铜在液中形成非常安定的氨铜络合离子。此种二价的 氨铜络合离子又可当成氧化剂使零价的金属铜被氧化而溶解。不过氧化还 原反应过程中会有一价亚铜离子)出现即:一反应之中间态亚铜离子之溶解度很差必须辅助以,氨水氨离子及空气中大量的氧使其继续氧化成为可溶的二价铜离子而又再成为蚀铜的氧化剂周而复始的继续蚀铜直到铜量太多而减慢为止故一般蚀刻机之抽风除了排除氨臭外更可供给新鲜的空气以加速蚀铜
8、剥锡(铅):最后将抗蚀刻的锡(铅)镀层除去 上述步骤是由水平联机设备一次完工
剥锡液成分:溶液组成有氟系/H2O2,HNO3/H2O2等配方。
1、首先将需要处理的工件放入退锡水中,工件要错开放置,不要重叠,25℃—40℃条件下退除锡镀层,以退尽为止。
2、当锡镀层退除后,在铜基体上会有一层灰黑色的膜,视客户要求而定,如需要去除此膜则必须用我司配送的除膜剂再清洗一次。
3、将退尽锡层的工件从退锡水中取出后,用自来水冲洗干净,然后投入到除膜剂中把铜基体表面上的膜去掉,大约浸泡20秒钟至1分钟。最后取出工件用洁净自来水冲洗干净即可。
4、在退锡过程中要轻缓对工件进行搅拌,但要注意:不要使工件与工件之间因碰撞而损害了精密零件.最好是将工件装在固定的塑料框中,工件与工件之间有一定距离,退镀过程只要晃动框,而不需要碰到工件.同时也避免了工件之间的重叠.
9、防焊:
主要工艺流程如下:
印墨包含印刷型和帘涂型、静电喷涂型。
预烤:赶走油墨内的溶剂,使油墨部分硬化,不致在进行曝光时黏底片 后烤: A.通常在显像后墨硬度不足,会先进行UV硬化,增加其硬度以免做检修时刮伤.B.后烤的目的主要让油墨之环氧树脂彻底硬化,文字印刷条件一般为150°C,30min
10、文字印刷
11、表面焊垫的各种处理 (1)金手指及喷锡 A金手指:
a.贴胶,割胶:目的是让板子仅露出欲镀金手指之部份线路,其它则以胶带贴住防镀.b、镀镍(垂直):在此是作为金层与铜层之间的屏障防止铜扩散。镍液则是镍含量甚高而镀层应力极低的氨基磺酸镍(Ni(NH2SO3)2 )或者硫酸镍,还有辅助剂(硼酸(缓冲作用,维持pH平衡,浓度35~55g/l)、氯化镍(保证阳极正常溶解,防止阳极钝化)、光亮剂(ACR-3010,浓度25~35ml/l)、防针孔剂(赶走氢气泡,阴离子表面活性剂:十二烷基硫酸钠、二乙基已基硫酸钠))
c、镀金:以弱酸性柠檬酸系列的微氰镀液为宜。 B、喷锡(又称热风平整) 喷锡又称热风整平,是将印制板浸入熔融的焊料中,再通过热风将印制板的表面及金属化孔内的多余焊料吹掉,从而得一个平滑,均匀光亮的焊料涂覆层。
分为垂直式和水平式。 流程:
烤板——前处理——助焊剂涂覆—— 浸入熔融焊料——热风整平—— 后处理。
前处理包含:脱脂——清洗——微蚀——水洗酸洗(中和)——水洗热风干
(2)OSP(有机保焊膜,又称护铜剂,)
洁净的裸铜表面上,以化学的方法长出一层有机皮膜。这层膜具有防氧化,耐热冲击,耐湿性,用以保护铜表面于常态环境中不再继续生锈(氧化或硫化等);但在后续的焊接高温中,此种保护膜又必须很容易被助焊剂所迅速清除,如此方可使露出的干净铜表面得以在极短的时间内与熔融焊锡立即结合成为牢固的焊点。
除油所使用药液成分:(1) 柠檬酸(2) 润湿剂(非离子界面活性剂) 微蚀所用药液同内层微蚀工序((1) 过硫酸钠、(2) 硫酸),使铜表面微粗化, 与OSP膜之间有更好的附着性。
预浸:主成份为异丙醇及添加剂,作用:使銅面外層上一層保護膜,以避免銅離子帶入OSP槽內.OSP:主成份 (1)主成分:苯基三連唑和 (2)甲酸;作用使铜面外层覆盖一层有机保焊膜,防止铜面氧化.(3)化学镍金
A、化学镀镍 镀液: B.一般常用的镍盐为氯化镍(Nickel Chloride) C.一般常用的还原剂有次磷酸盐类(Hypophosphite)/甲醛(Formaldehyde)/联氨 (Hydrazine)/硼氩化合物(Borohydride)/硼氢化合物(Amine Borane) D.螯合剂以柠檬酸盐(Citrate)最常见
E.槽液酸碱度需调整控制传统使用氨水(Amonia)也有配方使用三乙醇氨(Triethanol Amine)除可调整PH及比氨水在高温下稳定同时具有与柠檬酸钠结合共为镍金属螯合剂使镍可顺利有效地沉积于镀件上.B、镀金
分为"置换式镀金"与"无电金(化学镀)"。
"浸镀金": 镀层薄且底面镀满即停止,Ni+2Au+→Ni2++2Au由于金和镍的标准电位相差较大,在合适的溶液中会发生金在镍表面置换沉积出来从反应式我们可以看出,浸金反应要进行必须要有镍层的存在,但随着置换出的金层厚度的增加,镍被完全覆盖后,浸金后反应就停止了。
常用化学浸金的配方与工艺条件:
氯化铵(150克/升);柠檬酸氢二铵(100克/升); 氰化亚金钾(2克/升);稳定剂(适量) 温度大于90℃; PH 4.0 化学镀金:原理是利用还原剂,将金还原后均匀沉积在被镀物上,达到所需要的厚度,金厚度可达15μ″以上。其反应式:Au++Red→Au0+ox 金(以氰化亚金钾形式加入) 0.5-2克/升 柠檬酸铵 40-60克/升 氯化铵 70-80克/升 偏亚流酸钾(钠) 10-15克/升 次亚磷酸钠 10-15克/升 PH 4.5-5.8 温度 90℃
化学镀镍层是极为均匀的,只要镀液能浸泡得到,溶质交换充分,镀层就会非常均匀,几乎可以达到仿形的效果。 电镀无法对一些形状复杂的工件进行全表面施镀,但化学镀过以对任何形状工件施镀。
4、化学沉锡(垂直生产线)
酸性除油剂:甲烷磺酸<10~25% ;丁氧基乙醇<2.5~10%;水:剩余部份 微蚀液:硫酸氢钠<10~25%,过硫酸钠<50~100%
浸锡基本剂:LP
浸锡基本剂:2000 外观:无色
外观:无色 状态:液体
状态:液体 比重:1.33g/l
比重:1.12g/l 溶解性:完全溶于水
溶解性:完全溶于水 气味:有较强的刺激性
气味:有刺激性气味 主要成份:
主要成份: 甲基磺酸<10~25% 硫脲<10~25% 水:剩余部份
水:剩余部份 锡溶液:SF-C
浸锡添加剂 • 外观:浅黄色
外观:无色 • 状态:液体
状态:液体 • 比重:1.50g/l
比重:1.02g/l • 溶解性:完全溶于水
溶解性:完全溶于水 • 气味:有较强的刺激性
气味:有刺激性气味 • 主要成份:
主要成份: • 甲基磺酸锡<25~50%
甲基磺酸<2.5~5% • 水:剩余部份
水:剩余部份
5、沉银
2Ag+ + Cu0 2Ag0 + Cu++
主要工艺流程及药液
酸性清洁 (175084, 100ml/L, 43oC, 45s ) 水洗
微蚀 (175085, 120g/l,175086,10g/l,2%的硫酸,2g/l的硫酸铜,37oC, 1min ) 水洗
预浸 (0.1-0.2N的硝酸, 175098,0.01-0.02M,38oC, 30s ) 银槽(0.12-0.22N的硝酸, 175098,0.02-0.04M,175097,0.6-0.9g/l, 52oC,60s ) 热纯水洗
抗氧化(XD-7437-T, 175503,30%,49-54oC, 1min ) 水洗
吹烘干
四、后序工序
成型、清洗、检验。
清洗:上板、高压冲洗——轻刷——水洗——吹干——烘干——冷却
第19篇:PCB设计总结
设计总结
通过本次设计,我体会到整个设计的流程是从规则设置-----元件布局------过孔扇出与布线-----铺铜的处理-----走线优化------验证设计----处理丝印与出GERBER。
在该设计过程中,我出现了很多问题,现归纳如下:
1, 对布局的思考太死板,没考虑到对后面走线的影响。 2, 走线不够通顺,不能很好的结合原理图来走线。 3, 哪些地方该铺铜,哪些地方不应铺铜比较模糊。 4, 软件设置不够熟悉。
由此总结几点要点。
一,关于过孔与铺铜的总结:
1,过孔尽量打到栅格点上,且保持对齐。
2,大电源部分要多打过孔,对于电感的处理,变压器的处理要注意。
铺铜不要超过焊盘下边缘。
3, 铜箔宽度不要太大,5.5~6.5mil,不能小于4.5,不要用整数、4,铜箔宽度尽量保持一致。
5,电源层大电源铜箔挖出一块区域作为小电源铜箔,可以通过设置其优先级,来达到铺铜效果。不同电源铜箔间距一致,一般25mil适宜。倒角一般采用45°。 二,关于走线的总结:
1,走线不能出现任意角度,一般保持45°角。
2,两个串联电容中间走线要加粗。走线间距保持3倍线宽较宜。
3, 电源引脚对应的耦合电容要直连,保持电源电路通顺。
4, 对于FPGA以及数据收发IC的IO口可以通过交换引脚是走线通顺。交换时保持数据口对应关系。 5,
模拟电路与数字电路走线要区分开,防止干扰产生。对应运放电路走线要加粗。 6, 大电源走线采用星形走线。可通过电源层走线。 7, 测试点要连入相应的网络。走线保持同组同层。
8, 接插件中间尽量不走线。出线保持间距一致,走完的线可以通过锁定防止误操作,做到美观统一。
第20篇:PCB专业术语总结
A
Acceleration 速化反应 (台) 加速反应
Accelerator 加速剂,速化剂 (台)促进剂,催化剂
Acceptable Quality Level (AQL)允收品质水准 (台)合格质量水平Acce hole 露出孔,穿露孔 (台)余隙孔 Accuracy 准确度 (台)精确度 Acid Dip 浸酸 (台) 弱酸蚀
Acrylic(resin) 压克力 (台)丙烯酸 (树脂) Active Parts 主动零件 (台)有源器件
Anisotropic Conductive Film(Adhesive) 单向导接着膜 (台) 单向导电膜 Anneal 韧化 (台) 退火
Any Layer Interstitial Via Hole(ALIVH) 阿力 制程 (台) 全层内部导通孔(工艺),任意层内部通孔(工艺)
Area Array Package 面积格列封装 (台) 面阵列封装
B
Ball Grid Array 球脚阵列 (台) 球栅阵列 Bandability 可弯曲性 (台) 可挠性
Bandwidth 频带宽度,频宽 (台) 带宽 Banking Agent 护岸剂 (台) 护堤剂 Bare Board 空板,未装板 (台) 裸板
Bare Chip Aembly 裸体芯片组装 (台) 裸芯片安装 Basic Grid 基本方格 (台) 基本网络 Blanking 行空断开 (台) 落料 Bleeding 渗流 (台) 渗出
Block Diagram 电路系统整合图 (台) 方块框图 Blotting 干印 (台) 吸墨 Blow Hole 吹孔 (台) 气孔
Bond Strength 结合强度 ,固着强度 (台) 粘合强度 Bondability 结合性,固着性 (台) 粘合性
Bonding Sheet (Ply ,Layer) 接合片,接着层 (台) 粘结片 Bonding Wire 结合线 (台) 键合线 Brazing 硬焊 (台) 钎焊
Breakaway Panel 可断开板 (台) 可断拼板
Breakdown Voltage 崩溃电压 (台) 击穿电压 Bright Dip 光泽浸渍处理 (台) 浸亮 Buildup Multiayer (BUM) 增层法多层板 (台) 积层法多层板 Burr 毛头 (台) 毛剌
Bus Bar 汇电杆 (台) 汇流排
C
Cap Laminaton 帽式压合法 (台) 覆盖层压法
Cavity Down / Cavity Up 方凹区朝下/方凹区朝上 (台) 空腔区朝下/空腔区朝上 Cell Phone 行动电话 (台) 移动电话 Chase 网框 (台) 网框
Chemical Resistance 抗化性,耐化性 (台) 耐化学性 Chip 芯片,晶粒,片状 (台) 芯片
Chip on Board (COB) 晶板接装法 (台) 载芯片板 Chip Scale Package 芯片级封装 (台) 芯片级安装 Circumferential Separation 环状断孔 (台) 环开断裂 Clad / Cladding 披覆 (台) 覆箔
Clinched Lead Terminal 紧箱式引脚 (台) 折弯引脚 Clok Frequency 时脉速率 (台) 时钟频率 Coaxial Cable 同轴缆线 (台) 同轴电缆 Cold Solder Joint 冷焊点 (台)虚焊点
Comparative Tracking Index 比较性漏电指数 (台) 相比起痕指数 Complex Ion 错离子 (台) 络离子 Component Hole 零件孔 (台) 组件孔 Component Side 组件面 (台) 组件面
Condensation Soldering 凝热焊接,液化放热焊接 (台) 冷凝焊接 Conductive Anodic Filament 玻纤纱式漏电 (台) 阳极性玻纤丝的漏电 Conductor Spacing 导体间距 (台) 导线间距 Core (Board) 核心板,核板 (台) 芯板 Core Material 内层板材,核材 (台) 内层芯材 Corner Crack 通孔断角 (台) 拐角裂缝 Corner Mark 板角标记
(台)
拐角标记
Counterboring 垂直向下扩孔,埋头孔 (台) 沉头孔
Countersinking 锥型扩孔,喇叭孔 (台) 锥形孔 Coupling Agent 耦合剂 (台) 偶联剂
Coupon , Test Coupon 板边试样 (台) 附连测试板 Coverlayer ,Coverlay 表护层 (台) 覆盖层 Crease 皱折 (台) 折痕 Creep 潜变 (台) 蠕变
Crohatching 十字交叉区 (台) 开窗口 Croover 越交,搭交 (台) 跨交 Crotalk 杂讯,串讯 (台) 串扰 Cure 硬化,熟化 (台) 固化,硫化
Current、Carrying Capability 载流能力 (台) 载流量 Curtain Coating 濂涂法 (台) 帘幕法
D
Daisy Chaining 菊花瓣连垫 (台) 串推 Deburring 去毛头 (台) 去毛剌 Definition 边缘逼真度 (台) 清晰度 Denier 丹尼尔 (台) 坦尼尔 Dent 凹陷 (台) 凹坑
Deposition 沉积, 附积 (台) 沉积 Desmearing 除胶渣 (台) 去钻污 Dewetting 缩锡 (台) 半润湿 Diazo Film 偶氮棕片 (台) 重氮底片 Dicing 芯片分割 (台)切片
Die Attach 晶粒安装 (台) 管芯安装 Die Bonding 晶料接着 (台) 管芯键合 Dielectric Breakdown 介质崩溃 (台)介质击穿
Dielectrie Breakdown Voltage 介质崩溃电压 (台) 介质击穿电压 Dielectric Constant ,Dk or εr 介质常数 (台) 介电常数
Differential Scanning Calorimetry (DSC) 微差扫瞄热卡分析法 (台) 示扫描量热法 Dimensional Stability 尺度安定性 (台) 尺寸稳定性 Direct / Indirect Stencil 直间版膜 (台) 直接/间接法网版 Discrete Component 散装零件 (台) 离散组件 Dipation Factor (Df) 散失因素 (台) 损耗因素 Drill Facet 钻尖切削面 (台) 钻尖切削面 Dual Wave Soldering 双波焊接 (台) 双波峰焊 Dynamic Flex (FPC) 动态软板
(台)
动态挠性板
Dynamic Mechanical Analysis (DMA) 动态热机分析法 (台) 动态力学分析法,热机械分析法
E
Eddy Current 涡电流 (台) 涡流
Edge -Board Connector 板边 (金手指)承接器 (台) 板边连接器 Edge -Board Contact 板边金手指 (台) 板边插头 Edge Spacing 板边空地,边宽 (台) 边距 EDTA 乙 = 胺四醋酸 (台) 乙 = 胺四乙酸 Electric Strength (耐)电性强度 (台) 电气强度
Electrophoresis 电泳动,电渗,电子构装 (台) 电泳 Etchback 回蚀 (台) 凹蚀阴影
Etch Factor 蚀刻因子,蚀刻函数 (台) 蚀刻系数 Etching Indicator 蚀刻指标 (台) 蚀刻指示图 Etching Resist 抗蚀阻剂 (台) 抗蚀刻 Eutetic Composition 共融组成 (台) 共晶组成 Excimer Lesar 准分子雷射 (台) 准分子激光
F
Face Bonding 晶面朝下之结合 (台) 倒芯片键合 Fatingue Strength 抗疲劳强度 (台) 疲劳强度 Fibet Exposure 玻织显露 (台) 露纤维
Fiducial Mark 基准记号,光学靶标 (台) 基准标记 Film Adhesive 接着膜,粘合膜 (台) 粘结膜
Fine pitch 密脚距,密线距,密垫距
(台)
精细节距
G
Gate Array 闸机阵列,闸列 (台) 门阵列 Gel Time 胶性时间 (台) 胶化时间,凝胶时间 Gelation Particle 胶凝点 (台) 凝胶点 Ghost Image 阴影 (台) 重影
Gla Transition Temperature , Tg 玻璃态转化温度 (台) 玻璃化温度 ,玻璃态转变温度 Grid 标准格 (台) 网格
Grid Wing Lead (台) 契形引线(脚)
H
Halation 环晕 (台) 晕环 Hay Wire 跳线 (台) 附加线
Holding Time 停置时间 (台) 停留时间 Hole Breakout 孔位破出 (台) 破坏 Hole Density 孔数密度 (台) 孔密度
Hole Pull Strength 孔壁抗拉强度 (台) 孔拉脱强度 Hole Void 破洞 (台) 孔壁空洞
Hole Air Soldrt Levelling (HASL) 喷锡 (台) 热风整平Hull Cell 哈尔槽 (台) 霍尔槽
I
Icicle 锡尖 (台) 焊料毛剌 Imaging 成像处理 (台) 成像 Imperegnate 含浸 (台) 浸渍
Information Appliance (IA) 资讯家电 (台) 信息家电 Integrated Circuit (IC) 积体电路器 (台) 集成电路 Interface 接口 (台) 界面
J
J调解器 Module 模组 (台) 模件、组件、模块
Moisture and Insulation Resistance Test 湿气与绝缘电阻试验 (MIR) (台) 潮热绝缘电阻试验 Monting Hole 组装孔, 机装孔 (台) 安装孔
N
Numerically Controlled ( N.C.)数值控制 (台) 数控 Negative 复片, 钻尖第一面外缘变窄 (台) 负像
NegativeMethyl Pyrrolidone (NMP) N甲基吡咯烷酮 Nodule 瘤 (台) 结瘤 Noise Budget 杂讯上限 (台) 最大杂音,最大噪声 Nominal Cured Thickne 标示厚度 (台) 标称厚度 NonContact 架空 (台) 非接触 (印刷) Offset 第一面大小不均 (台) 钻面不匀
Outer Lead Bond (OLB) 外引脚结合 (台) 外部引线粘接 Oligomer 寡聚物 (台) 低聚物 Outgaing 出气,吹气 (台) 逸气
Outgrowth 悬出,横出,侧出 (台) 镀层情况 Overhang 总浮空 (台) 镀层突出
Overpotential 过电位,过电压 (台) 趋电势
P
Panel Plating 全板镀铜 (台) 整板电镀
Paive Device (Component) 被动组件 (零件) (台) 无源组件 Pattern Plating 线路电镀 (台) 图形电镀 Patten Proce 线路电镀法 (台) 图形电镀法 Peel Strength 抗撕强度 (台) 剥离强度 Permittivity 容电率 (台) 电容率 ,介电常数 Phototinitator 感光启始剂 (台) 光敏剂 Pin 接脚,插梢,插针 (台) 管脚
Pin Grid Array (PGA) 针脚格列封装体 (台) 针栅阵列 Pitch 跨距,脚距,垫距,线距,中距 (台) 节距 Pits 凹点 (台) 麻点 Plasma 电浆 (台) 等离子
PlasticLem) 多层板压合 (台) 多层板压制 Relative Permitivity (εr)相对容电率 (台) 相比介电常数
Resin Coated Copper Foil 背胶铜箔 (台) 涂树脂铜箔 ,附树脂铜箔 Resin Flow 胶流量 , 树脂流量 (台) 树脂流动度 Resin Receion 树脂缩陷 (台) 树脂凹缩
Resin Rich Area 树脂丰富区 , 多胶区 (台) 树脂钻污 Resin Starved Area 树脂缺乏区 ,缺胶区 (台) 缺胶区 Resist 阻剂 ,阻膜 (台) 抗蚀剂
Resolution 解像 ,解像变,解析度 (台) 分辨率 Reverse Image 负片影像 (阻剂) (台) 负图像 Rigid - Flex Printed Board 硬软合板 (台) 刚挠印制板 Ring 套环 (台) 钻套
Ripple 纹波 (台) 波动 ,脉动
Roller Coating 滚筒涂布法 、辊轮涂布法 (台) 辊涂式
S
Scratch 刮痕 (台) 划痕
Secondary Side 第二面 (台) 辅面 Self-Alignment 自我回正 (台) 自定位 Shadowing 阴影 ,回蚀死角 (台) 凹蚀阴影 Shear Strength 抗剪 (力) 强度
(台) 剪切强度
Silver Fhrough Hole (STH)银胶通孔 ,银胶贯孔 (台) 银浆通孔 ,银浆贯孔 Single-Inline Package (SIP) 单边插脚封装体 (台) 单列直插式封装 Solder Connection 焊接点 (台) 焊点 Solder Paste 锡膏 (台) 焊膏
Solder Plug 锡塞 ,锡柱 (台) 焊料堵塞
Solder Spread Teat 散锡试验 (台) 焊料扩展试验 Solder Webbing 锡网 (台) 网状残锡 Soldering 软焊 ,焊接 (台) 软钎焊 ,焊接 Solid Content 固体含量 ,固形份 ,固形物
Solubility Product 溶解度乘积 ,溶解度积 (台) 容度积 Splay 斜钻孔 (台) 斜孔
Spray Coating 喷着涂装 ,喷射涂装 (台) 喷涂 Stencil 片膜 (台) 漏板 ,模版 Stringing 拖尾 ,牵丝 (台) 带状线 Stripper 剥除液 ,剥除器 (台) 剥离液
Supported Hole (金属) 支助通孔 (台) 支撑孔
Surface Mounting Technology 表面贴装技术 (台) 表面安装技术 Surge 突流 、突压 (台) 波动
Swaged Lead 压扁式引脚 (台) 挤压引线 Syringe 挤浆法 ,挤膏法,注浆法 (台) 注射法
T
Tab 接点 ,金手指 (台) 印制插头 Telegraphing 浮印 ,隐印 (台) 露印 Template 模板 (台) 靠模板
Tensile Strength 抗拉强度 (台) 拉伸强度 ,抗拉强度
Terminal 端子 (台) 端接 (点)
Thermal Conductivity 导热率 (台) 热导率 Thermal Shock Test 热震荡试验 (台) 热冲击试验
Thermogravimetric Analysis (TGA) 热重分析法 (台) 热解重量分析法 Thermosonic Bonding 热超音波结合 (台) 热声连 (焊)接 Thermount 聚醯胺短织席材 (台) 聚酰胺纤维无纺布
Thin Small Outline Packange (TSOP) 薄小型积体电路器 (台) 薄小外形封装 Thixotropy 抗垂流性 ,摇变性 ,摇溶性 ,静凝性 (台) 触变性 Tin Indicated 浸镀锡 (台) 浸锡
Total Indicated Runout (TIR) 总体标示偏转值 (台) 指针总读数 Touch Up 触修 ,简修 ,小修, (台) 修版
Transfer Bump 移用式突块 ,转移式突块 (台) 变换凸块 Treament ,Trearing 含浸处理 (台) 浸渍 Twist 板翘 、板扭 (台) 扭曲
U
Utimate Tensile Strength (UTS)极限抗拉强度 (台) 极限拉伸强度 Ultra Violet Curing (UV Curing) 紫外线硬化 (台)紫外线固化 Ultrasonic Bonding 超音波结合 (台) 超声连接
Unbalaned Transmiion Line 非平衡式传输线 (台) 非均衡传输线 Unsupported Hole 非镀通孔 (台) 非支撑孔 Urethane 胺基甲酸乙脂 (台) 氨基甲酸乙酯
V
V-Cut V型切槽 (台) V槽切割
Vacuum Evaporation (or Deposition )真空蒸镀法 (台) 真空镀膜法 Vacuum Lamination 真空压合 (台) 真空压制 Varnish 清漆 ,凡力水 (台) 树脂漆
Visual Examination (Inspection) 目视检查 (台) 目检 Voltage Breakdown (崩)溃电压 (台) 击穿电压 Voltage Plane Clearance 电压层的空环 (台) 电源层隔离
W
Wavine 波纹 、波度 (台) 云织
Weave Exposure 织纹显露 ;Weave Texture 织纹隐现 (台) 露布纹 Wedge Void 楔形缺口 (破洞) (台) 楔形空洞 Wet Lamination 湿压膜法 (台)湿法贴膜 Wetting 沾湿 、沾锡 (台) 焊料润湿 Wicking 灯芯效应 (台) 芯吸
Wire Bonding 打线结合 (台) 金属丝连接 Working Master 工作母片 (台) 工作原版 Wrinkle 皱褶 ,皱纹 (台) 皱褶
Z
Zigzag Inline Package (ZIP) 链齿状双排脚封装件 (台) 弯曲式直插封装
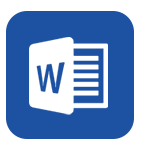