加工手段主要有:注塑,挤出,吹塑,吸塑等。注塑可以加工生产比较复杂形状的产品,比如电视机外壳等。它是把塑料粒子预先在料管中加热,然后通过螺杆下压,把融化的原料注入到模具,冷却成型后就制成了产品。挤出就是原料经螺杆的连续推动,使之在料管中(俗称炮筒)加热塑化,然后在定型的模具中挤出,获得所需的形状,比如塑料扣板,水管等。吹塑和挤出有点相似,只不过它是把压缩空气置于其中来获得形状,比如塑料薄膜,塑料瓶等。吸塑比较简单,它先把预先制成的塑料片材,经过烘箱焙烤,然后放置在模具中,通过负压使片材与模具密贴而获得形状。
。。。。。。。。。。。。。。。。。。。。。。。。。。。。。。。。。。。。。。。。。。。。。。。。。。。。。。。。。。。。。。。。。。。。。。。。。。。。。。
注塑成型原理及注塑过程介绍 :注(射模)塑(或称注射成型)是塑料先在注塑机的加热料筒中受热熔融,而后由柱塞或往复式螺杆将熔体推挤到闭合模具的模腔中成型的一种方法。它不仅可在高生产率下制得高精度,高质量的制品,而且可加工的塑料品种多和用途广,因此注塑是塑料加工中重要成型方法之一。 A注塑机的基本功能:注塑是通过注塑机来实现的。注塑机的基本功能是:1。加热塑料,使其达到熔融状态;2。对熔体施加高压,使其射出而充满模腔。 B注塑过程/设备:热塑性塑料的注塑操作一般是由塑炼。充模。压实和冷却等所组成的。所用设备是由注塑机。注塑模具及辅助设备(如物料干燥等)组成的。
C注射装置:注射装置在注塑机过程中主要实现塑炼。计量。注射和保压补缩等功能。螺杆式注射装置用得最多,它是将螺杆塑炼和注射用柱塞统一成为一根螺杆而成的。实质上,应称为同轴往复复杆式注射装置。它在工作时,料斗内的塑料靠自身的重量落入加热料筒内,通过螺杆的转动,塑料沿螺槽向前移动,这时物料受到加热料筒外部加热器加热,同时内部还有剪切产生的热,温度上升在成为熔融状态。随着加热料筒前端材料的贮存,这些材料产生的反作用力(背压)将螺杆向后推,利用限位开关限制其后退量,当后退到一定位置时,使螺杆停止转动,由此决定(计量)一次的注射量。
模内的材料冷却后,制品一经取出,就再次合上模具,进入注射工序,这时注射装置的液压缸(注射油缸)向螺杆施力,在高压下螺杆成为射料杆,将其前端的熔体从喷嘴注入模具内。
螺杆式注射装置是由螺杆,料筒,喷嘴和驱动装置等部分构成的。注射用螺杆一般分加料,压缩,和计量三段,压缩比为2~3,长径比为16~18。当熔体从喷嘴射出去时,由于加压熔体上的注射力怕反作用力,一部分熔体会通过螺杆的螺槽逆流到后部。为防止这种现象,在螺杆的端部装上止逆阀。对于硬聚氯乙烯,则采用锥形螺杆头。
料筒是装纳螺杆的部分,它是由耐热。耐高压的钢材制的。在料筒的外围安装数组电热圈以加热筒内的物料,用热电偶控制温度,使塑料具有适宜的温度。
喷嘴是联接料筒和模具的过渡部分,其上装有独立的加热圈,因为它是直接影响塑料熔融状的重要部分。一般注塑多采用敞开喷嘴对于低粘度聚酉先胺。则采用针阀式喷嘴。
驱动螺杆的转动可用电动机或液压马达,螺杆的往复运动是借助液压力实现的。
通过注射装置表征注塑机的参数有:注射量是指注塑机每次注入模内的最大量,可用注射聚苯乙烯熔体的质量表示,或用注射熔体的容积表示;注射压力是
指在注射时施加于料筒截面上的压力;注射速度则指注射时螺杆的移动速度。 D合模装置:合模装置除了完成模具的开合动作之外,其主要任务是以足够的力抗冲注射到模具内的熔体的高压力,使模具锁紧。不让它张开。
合模机构无论是机械还是液压或液压机械式,应保证模具开合灵活,准时,迅速而安全。从工艺上要求,开合模具确要有缓冲作用,模板的运行速度应在合模时先快后慢,而在开模时应先慢再慢。借以防止损坏模具及制件。
在成型过程中为了保持模具闭合而施加到模具上的力称为合模力,其值应大于模腔压力与制件投影面积(包括分流道)之积。模腔内的平均压力一般在20~45Mpa之间。
由于合模力慎线反映出注塑机成型制品面积的大小,所以常用注塑机的最大合模力来表示注塑机的规格,但合模力与注射量之间也存在一个大致的比例关系。可是,合模力表示法并不能直接反映注射制品体积的大小,使用起来还不方便。要国际上许多厂家采用合模力/当量注射容积表示注塑机的规格,对于注射容积,为了对于不同机器都有一个共同的比较标准,特规定注射压力屡100Mpa时的理论注射容积,即当量注射容积=理论注射容积*额定注射压力/100Mpa。 E控制系统:注塑机液压控制系统主要分常规液压控制系统,伺服控制系统和比例控制系统。。由于液压系统复杂,这里以比例阀油路系统为例说明梗概。这一系统的特点是:在油路系统中有控制流量的和压力怕比例元(电磁比例流量阀或电磁比例流量换向阀,电磁比例压力阀)。
通过外边给定电的仿真信号和磁力的比例作用,来控制阀芯的开口量或阀芯的弹簧力对系统流量或压力进行控制,从而达到注射速度,螺杆速度,启闭速度与注射压力。保压压力。螺杆转矩。注射座推力。顶出力。模具保护压力实行单级,多级控制或无级控制。 答案补充
那叫塑料改性,是添加了一些添加剂,根据要改的性质不同,添加的添加剂也是不同的
。。。。。。。。。。。。。。。。。。。。。。。。。。。。。。。。。。。。。。。。。。。。。。。。。。。。。。。。。。。。。。。。。。。。。。。。。。。。。。。
1.所谓注塑成型(Injection Molding)是指,受热融化的材料由高压射入模腔,经冷却固化后,得到成形品的方法。该方法适用于形状复杂部件的批量生产,是重要的加工方法之注射成型过程大致可分为以下6个阶段合模 注射 保压冷却开模制品取出 上述工艺反复进行,就可连续生产出制品。
2.所谓模具(Mold)是指,树脂材料射入金属模型后得到具有一定形状的制品的装置。
塑料模具,是塑料加工工业中和塑料成型机配套,赋予塑料制品以完整构型和精确尺寸的工具。由于塑料品种和加工方法繁多,塑料成型机和塑料制品的结构又繁简不一,所以,塑料模具的种类和结构也是多种多样的。
一种用于压塑、挤塑、注射、吹塑和低发泡成型的组合式塑料模具,它主要包括 塑料模具 由凹模组合基板、凹模组件和凹模组合卡板组成的具有可变型腔的凹模,由凸模组合基板、凸模组件、凸模组合卡板、型腔截断组件和侧截组合
板组成的具有可变型芯的凸模。模具凸、凹模及辅助成型系统的协调变化。可加工不同形状、不同尺寸的系列塑件。塑料加工工业中和塑料成型机配套,赋予塑料制品以完整构型和精确尺寸的工具。由于塑料品种和加工方法繁多,塑料成型机和塑料制品的结构又繁简不一,所以,塑料模具的种类和结构也是多种多样的。
随着塑料工业的飞速发展和通用与工程塑料在强度和精度等方面的不断提高,塑料制品的应用范围也在不断扩大,塑料制品所占的比例正迅猛增加.一个设计合理的塑料件往往能代替多个传统金属件.塑料产品的用量也正在上升.
塑料模具是一种生产塑料制品的工具.它由几组零件部分构成,这个组合内有成型模腔.注塑时,模具装夹在注塑机上,熔融塑料被注入成型模腔内,并在腔内冷却定型,然后上下模分开,经由顶出系统将制品从模腔顶出离开模具,最后模具再闭合进行下一次注塑,整个注塑过程是循环进行的. 按照成型方法的不同,可以划分出对应不同工艺要求的塑料加工模
塑料模具具类型,主要有注射成型模具、挤出成型模具、吸塑成型模具、高发泡聚苯乙烯成型模具等。
1、塑料注射(塑)模具
它主要是热塑性塑料件产品生产中应用最为普遍的一种成型模具,塑料注射成型模具对应的加工设备是塑料注射模具对应的加工设备是塑料注射成型机,塑料首先在注射机底加热料筒内受热熔融,然后在注射机的螺杆或柱塞推动下,经注射机喷嘴和模具的浇注系统进入 模具型腔,塑料冷却硬化成型,脱模得到制品。其结构通常由成型部件、浇注系统、导向部件、推出机构、调温系统、排气系统、支撑部件等部分组成。制造材料通常采用塑料模具钢模块,常用的材质主要为碳素结构钢、碳素工具钢、合金工具钢,高速钢等。注射成型加工方式通常只适用于热塑料品的制品生产,用注射成型工艺生产的塑料制品十分广泛,从生活日用品到各类复杂的机械,电器、交通工具零件等都是用注射模具成型的,它是塑料制品生产中应用最广的一种加工方法。
2、塑料压塑模具
包括压缩成型和压注成型两种结构模具类型。它们是主要用来成型热固性塑料的一类模具,其所对应的设备是压力成型机。压缩成型方法根据塑料特性,将模具加热至成型温度(一般在103°—108°),然后将计量好的压塑粉放入模具型腔和加料室,闭合模具,塑料在高热,高压作用下呈软化粘流,经一定时间后固化定型,成为所需制品形状。压注成型与压缩成型不同的是没有单独的加料室,成型前模具先闭合,塑料在加料室内完成预热呈粘流态,在压力作用下调整挤入模具型腔,硬化成型。压缩模具也用来成型某些特殊的热塑性塑料如难以熔融的热塑性塑料(如聚加氟乙烯)毛坯(冷压成型),光学性能很高的树脂镜片,轻微发泡的硝酸纤维素汽车方向盘等。压塑模具主要由型腔、加料腔、导向机构、
推出部件、加热系统等组成。压注模具广泛用于封装电器元件方面。压塑模具制造所用材质与注射模具基本相同。
3、塑料挤出模具
用来成型生产连续形状的塑料产品的一类模具,又叫挤出成型机头,广泛用于管材、棒材、单丝、板材、薄膜、电线电缆包覆层、异型材等的加工。与其对应的生产设备是塑料挤出机,其原理是固态塑料在加热和挤出机的螺杆旋转加压条件下熔融,塑化,通过特定形状的口模而制成截面与口模形状相同的连续塑料制品。其制造材料主要有碳素结构钢、合金工具等,有些挤出模具在需要耐磨的部件上还会镶嵌金刚石等耐磨材料。挤出中工工艺通常只适用热塑性塑料品制品的生产,其在结构上与注塑模具和压塑模具有明显区别。
3、塑料吹塑模具
是用来成型塑料容器类中空制品(如饮料瓶、日化用品等各种包装容器)的一种模具,吹塑成型的形式按工艺原理主要有挤出吹塑中空成型、注塑成型的形式按工艺原理主要有挤出吹塑中空成型、注射吹塑中空成型、注射延伸吹塑中空成型(俗称“注拉吹”),多层吹塑中空成型,片材吹塑中空成型等。中空制品吹塑成型所对应的设备通常称为塑料吹塑成型机,吹塑成型只适用于热塑料品种制品的生产。吹塑模具结构较为简单,所用材料多以碳素多则制造。
4、塑料吸塑模具
是以塑料板、片材为原料成型某些较简单塑料制品的一种模具,其原理是利用抽真空盛开方法或压缩空气成型方法使固定在凹模或凸模上的塑料板、片,在加热软化的情况下变形而贴在模具的型腔上得到所需成型产品,主要用于一些日用品、食品、玩具类包装制品生产方面。吸塑模具因成型时压力较低,所以模具材料多选用铸铝或非金属材料制造,结构较为简单。
5、高发泡聚苯乙烯成型模具
是应用可发性聚苯乙烯(由聚苯乙烯和发泡剂组成的珠状料)原料来成型各种所需形状的泡沫塑料包装材料的一种模具。其原理是可发聚苯乙烯在模具内能入蒸汽成型,包括简易手工操作模具和液压机直通式泡沫塑料模具两种类型,主要用来生产工业品方面的包装产品。制造此种模具的材料有铸铝、不锈钢、青铜等. 结构及基本零件
1、组成
吹塑模、铸塑模和热成型模的结构较为简单。
压塑模、注塑模和传塑模结构较为复杂,构成这类模具的零件也较多。
基本零件有:
①成型零件,包括凹模、凸模、各种成型芯,都是成型制品内、外表面或上、下端面、侧孔、侧凹和螺纹的零件。
②支承固定零件,包括模座板、固定板、支承板、垫块等,用以固定模具或支承压力。
③导向零件,包括导柱和导套,用以确定模具或推出机构运动的相对位置。
④抽芯零件,包括斜销、滑块等,在模具开启时用以抽出活动型芯,使制品脱模。
⑤推出零件,包括推杆、推管、推块、推件板、推件环、推杆固定板、推板等,用以使制品脱模。注塑模多推广采用标准模架,这种模架是由结构、形式和尺寸都已标准化和系列化的基本零件成套组合而成,其模腔可根据制品形状自行加工。采用标准模架有利于缩短制模周期。
2、作用
定模座板(面板):它的作用是将前模固定在上面。
流道板(水口板):它的作用就是在开模时把流道中的料去除。
定模固定板:它的主要作用是和b板一起成型产品。
推板:它的主要作用是在开模时将产品从模具中脱出。
动模固定板:它的主要作用是和a板一起成型产品。
垫板:它的作用是加强a板的强度和固定a板上的一些零件。
垫块:模脚,方铁等。它的作用是让顶板有足够的活动空间。
顶板:它的主要作用是固定顶针并在开模时通过注射机的顶杆推动顶针。
动模座板:下夹板,底板等。它的主要作用是将后模固定在上面。
导柱和导套:它们的主要作用是起导向作用,使前后模可以顺利完成所有的动作。
顶针:它的主要作用是在开模时将产品从推出。
。。。。。。。。。。。。。。。。。。。。。。。。。。。。。。。。。。。。。。。。。。。。。。。。。。。。。。。。。。。。。。。。。。。。。。。。。。。。。。
A.锁模力计算:
撑模力量=成品在开关模方向的投影面积(cm2)×模穴数×模内压力(kg/cm2); 模内压力随材料的不同而不同,一般原料取350-400kg/c㎡ 锁模力通常是要大于撑模力量的1.17倍!
B.怎样选择合适的注塑机 :
1、选对型: 由产品及塑料决定机种及系列。
由于注塑机有非常多的种类,因此一开始要先正确判断此产品应由哪一种注塑机,或是哪一个系列来生产,例如是一般热塑性塑胶或电木原料或PET原料等,是单色、双色、多色、夹层或混色等。此外,某些产品需要高稳定(闭回路)、高精密、超高射速、高射压或快速生产(多回路)等条件,也必须选择合适的系列来生产。
2、放得下 :由模具尺寸判定机台的“大柱内距”、“模厚”、“模具最小尺寸”及“模盘尺寸”是否适当,以确认模具是否放得下。
模具的宽度及高度需小于或至少有一边小于大柱内距;
模具的宽度及高度最好在模盘尺寸范围内;
模具的厚度需介于注塑机的模厚之间;
模具的宽度及高度需符合该注塑机建议的最小模具尺寸,太小也不行。
3、拿得出 :由模具及成品判定“开模行程”及“托模行程”是否足以让成品取出。
开模行程至少需大于成品在开关模方向的高度的两倍以上,且需含竖浇道(sprue)的长度;
托模行程需足够将成品顶出。
4、锁得住 :由产品及塑料决定“锁模力”吨数。
当原料以高压注入模穴内时会产生一个撑模的力量,因此注塑机的锁模单元必须提供足够的“锁模力”使模具不至于被撑开。锁模力需求的计算如下:
由成品外观尺寸求出成品在开关模方向的投影面积;
撑模力量=成品在开关模方向的投影面积(cm2)×模穴数×模内压力(kg/cm2);
模内压力随原料而不同, 一般原料取350~400kg/cm2;
机器锁模力需大于撑模力量,且为了保险起见,机器锁模力通常需大于撑模力量的1.17倍以上。
至此已初步决定夹模单元的规格,并大致确定机种吨数,接着必须再进行下列步骤,以确认哪一个射出单元的螺杆直径比较符合所需。
5、射得饱: 由成品重量及模穴数判定所需“射出量”并选择合适的“螺杆直径”。
计算成品重量需考虑模穴数(一模几穴);
为了稳定性起见,射出量需为成品重量的1.35倍以上,亦即成品重量需为射出量的75%以内。
6、射得好 :由塑料判定“螺杆压缩比”及“射出压力”等条件。
有些工程塑料需要较高的射出压力及合适的螺杆压缩比设计,才有较好的成型效果,因此为了使成品射得更好,在选择螺杆时亦需考虑射压的需求及压缩比的问题。
一般而言,直径较小的螺杆可提供较高的射出压力。
7、射得快 :及“射出速度”的确认。
有些成品需要高射出率速射出才能稳定成型,如超薄类成品,在此情况下,可能需要确认机器的射出率及射速是否足够,是否需搭配蓄压器、闭回路控制等装置。一般而言,在相同条件下,可提供较高射压的螺杆通常射速较低,相反的,可提供较低射压的螺杆通常射速较高。因此,选择螺杆直径时,射出量、射出压力及射出率(射出速度),需交叉考量及取舍。
此外,也可以采用多回路设计,以同步复合动作缩短成型时间。
有一些特殊问题可能也必须再加以考虑:
大小配的问题:
在某些特殊状况下,客户的模具或产品可能模具体积小但所需射量大,或模具体积大但所需射量小,在这种况下,厂家所预先设定的标准规格可能无法符合客户需求,而必须进行所谓“大小配”,亦即“大壁小射”或“小壁大射”。所谓“大壁小射”指以原先标准的夹模单元搭配较小的射出螺杆,反之,“小壁大射”即是以原先标准的夹模单元搭配较大的射出螺杆。当然,在搭配上也可能夹模与射出相差好几级。
快速机或高速机的观念:
在实际运用中,越来越多的客户会要求购买所谓“高速机”或“快速机”。一般而言,其目的除了产品本身的需求外,其他大多是要缩短成型周期、提高单位时间的产量,进而降低生产成本,提高竞争力。通常,要达到上述目的,有几种做法:
射出速度加快:将电机马达及泵浦加大,或加蓄压器(最好加闭回路控制);
加料速度加快:将电机马达及泵浦加大,或加料油压马达改小,使螺杆转速加快;
多回路系统:采用双回路或三回路设计,以同步进行复合动作,缩短成型时间;
增加模具水路,提升模具的冷却效率。
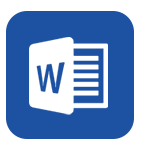