青岛大学本科毕业论文(设计)
1.前言
纯棉机织物作为一种主要的织物类型,其前处理效果的好坏关系到后续的染色、印花及后处理工序[5]。所以纯棉前处理过程应受到高度重视。但是传统的前处理工艺碱用量太高,耗时太长,不符合当今的节能减排要求。为了既能使织物的处理效果达到要求又能省时节能,对其前处理过程在传统工艺基础上进行多方面优化。
1.1纯棉坯布上的杂质
[15]
未经处理的纯棉坯布上含有很多杂质,给之后的染色、印花、后处理等工序带来很大障碍。所以,要想得到优质的染色产品、印花产品或漂白产品,必须将织物上的杂质去除掉,并且处理效果越好对后续工艺越有利。为了更好的去除织物上的杂质,需要对这些杂质的性质进行了解,从而使处理过程有针对性。棉织物上存在的杂质可以分为以下三类: (1)棉纤维生长过程中伴生的杂质
棉纤维由表皮层、初生胞壁、次生胞壁和胞腔组成。表皮层是棉纤维的最外层,主要由果胶物质、油蜡和蛋白质等组成。初生胞壁紧贴着表皮层,位于表皮层和次生胞壁之间,主要是纤维素的网状组织,也含有一定数量的油蜡和果胶物质。纤维素是构成棉纤维的主体,主要存在于次生胞壁。胞腔位于棉纤维中心,含有蛋白质、矿物盐及一些色素等。由此可见,棉纤维中的天然杂质大部分都分布在初生胞壁和表皮层中。 (2)棉花收获过程中产生的杂质
棉花在采摘和收获加工过程中也会产生一些杂质如棉籽壳、塑料绳、铁丝等,但是经过纺纱加工后,残留在织物上的杂质主要是棉籽壳。棉籽壳主要由木质素、单宁、纤维素、半纤维素以及其它的多糖类物质组成,此外还含有少量的色素、油蜡、蛋白质和矿物质。其中木质素是最主要的成分。棉织物上棉籽壳的多少与配棉等级与棉纱质量关系很大。 (3)纺织过程中人工添加的杂质
为了提高织造效率和坯布质量。棉织物在织造过程中需要对经纱进行上浆。棉织物浆纱采用的浆料主要包括淀粉、聚乙烯醇(PVA)、蜡类润滑剂、防腐剂等。一般织物的上浆率在4-8%左右。
棉织物上的天然杂质和棉籽壳在高温(90℃以上)条件下会被烧碱溶胀、皂化和分解,从而从棉织物上脱落下来,达到去除的目的。在4-10g/L烧碱的作用下,棉织物上的淀粉浆在一定温度(50℃以上)下会被烧碱溶胀,然后经过水洗会从棉织物上脱落下来。这就是长期以来用烧碱对棉织物进行前处理的主要依据。
青岛大学本科毕业论文(设计)
1.2棉织物前处理方法
1.2.1传统工艺[3]
棉织物传统前处理工艺包括退浆、煮练和漂白等工序(烧毛和丝光等在此实验中不予考虑)。
(1)生产中常用的退浆方法主要有酸退浆、碱退浆、酶退浆和氧化剂退浆。在实际生产中,要根据织物类型、织物上浆料种类和含量等来确定使用何种退浆工艺。通常可以选择一种方法或两种方法相结合。每种退浆方法的退浆原理是不同的,现将常用退浆方法的退浆原理介绍如下:
①碱退浆 在热烧碱溶液中,淀粉和变性淀粉、羧甲基纤维素等天然浆料以及PVA和PA类等合成浆料,均能发生溶胀。它们从凝胶状变为溶胶状,所以对纤维的吸附能力下降,在机械搅拌的条件下容易从纤维上脱落下来。另外,某些含有羧基的变性淀粉和聚丙烯酸类浆料以及羧甲基纤维素,在热碱液中会生成水溶性较高的钠盐,溶解度增大,这些溶解的浆料在水洗过程中会被除去。
②酸退浆 在稀硫酸溶液中,淀粉等浆料能发生一定程度的水解,从而使其水溶性提高。在水洗过程中,这些水解产物能从织物上洗除达到退浆目的。但是该方法易对纤维造成损伤且退浆率不高。
③酶退浆 酶作为一种生物催化剂具有专一性、高效性和作用条件温和等特点。淀粉酶可以催化淀粉发生高效水解,而对其他类型的浆料没有作用。所以淀粉酶退浆只适用于淀粉和变性淀粉退浆的织物。该方法退浆率较高,且不会对纤维造成损伤。
④氧化剂退浆 在碱性条件下,应用过氧化氢、过硫酸盐和亚溴酸钠等氧化剂作用于织物进行退浆。在该条件下,氧化剂能与淀粉大分子中的α-1,4-苷键和α-1,6-苷键、伯羟基和C-C键反应,发生苷键断裂且伯羟基被转化为羧基,葡萄糖环开环分裂,最终产物为水和二氧化碳。合成浆料被氧化后发生大分子链的断裂。但是氧化剂也会对纤维造成损伤,所以应严格控制其工艺条件。
⑵生产中常用的精练方法是碱精练,近年来也发展了酶精练技术。棉纤维中的天然杂质包括果胶物质、含氮物质、蜡状物质、灰分、色素和棉籽壳等。在碱精练中,烧碱能使果胶的酯键水解生成水溶性的羧酸钠盐而被除去;含氮物质中的20%能溶于热水被除去,其他的部分需要在烧碱液中长时间煮沸除去;棉纤维中灰分可以在溶解过程或经酸洗和水洗除去;蜡状物质中的脂肪酸类物质能在热碱液中发生皂化,水洗可去除,其余的经乳化
青岛大学本科毕业论文(设计)
作用除去;木质素(棉籽壳的主要成分)中的酚羟基与烧碱作用发生分解,使其在碱液中的溶解度变大,从而可以被除去。上述为碱精练的作用原理。酶精练是利用酶对特定杂质的专一作用,在适宜条件下发生催化作用而使杂质被除去。酶精练与碱精练相比,前者吸水性差,棉籽壳去除效果差。因此,酶精练工艺还需要优化。
⑶生产中常用的漂白方法主要有过氧化氢漂白、次氯酸钠漂白和亚氯酸钠漂白。这三种漂白方法中,应用最广泛的是过氧化氢漂白,因为其漂白产品的白度和白度稳定性较好,并且污水处理难度小。另外,该种方法适应范围较广,能适用于各种纤维的漂白。次氯酸钠漂白的工艺和设备比较简便并且成本较低,可用于棉织物和涤棉织物的漂白,对麻类的漂白效果好。但是次氯酸钠漂白废水中含有效氯,会带来环境污染等问题。亚氯酸钠的去杂能力很强,漂白白度非常好,可用于棉、麻和涤棉织物的漂白。但是由于漂白过程释放腐蚀性强、毒性大的二氧化氯,所以它对设备要求很高,这样就使漂白成本提高。而且二氧化氯的释放会带来环境问题,这都给其应用带来限制。
传统工艺处理后织物的退浆率、毛效和白度等测量指标均能达标,效果非常理想。但是其能耗大,历时久且对织物强力有较大损伤。
1.2.2短流程工艺
早在20世纪50年代,国外已出现了前处理短流程工艺,这在当时被称作单程法连续漂白。传统前处理练漂工序分为退浆、煮练和漂白三步,所以短流程工艺就是把三步合并为两步或者一步[5]。按工艺合并方式的不同,可以有以下两种分类。
⑴两步法工艺
①退浆-碱氧工艺 该工艺中织物先经退浆,再经碱氧一浴煮漂。其中,碱氧一浴中氢氧化钠的浓度很高而使过氧化氢易分解,所以应该选择性能良好的双氧水稳定剂。该工艺的关键是退浆及随后的洗涤必须彻底,使织物上的浆料和部分杂质尽可能多的除去,这样就减轻了碱氧一浴煮漂的工作压力。此工艺适用于上重浆的纯棉厚重织物[5]。
②退煮-氧漂工艺 该工艺中织物先经退煮一浴处理,再经过氧化氢漂白。此工艺中碱浓度较低,该条件下过氧化氢分解速率相对较小,对纤维损伤较小[5]。但是退浆与煮练结合后,浆料在强碱浴中不容易洗净,这样会影响退浆和煮练效果。所以退煮后必须对织物进行彻底水洗。
⑵一步法工艺
该工艺中将所有试剂加入一浴中,织物经一步处理即可。为了达到与传统工艺相近的
青岛大学本科毕业论文(设计)
处理效果,此工艺中碱浓度和加工温度等应提高。但碱浓度过高会使过氧化氢的分解速率加快加重织物损伤。为降低织物损伤,我们可以选择降低氢氧化钠或过氧化氢浓度,加入性能较好的染整助剂或降低加工温度。但是本实验采用汽蒸法不可能降低处理温度,所以只好通过降低化学试剂的用量和加入高效助剂来达到实验目的[7]。
短流程前处理工艺是前处理工序的发展方向,经过近几十年的努力,短流程前处理工艺已广泛应用于各种织物。但是短流程前处理工艺并不是万能的,它有其适用的织物类型。因此必须根据织物特点、加工要求、客户要求等因地制宜地制定合理的短流程前处理工艺[5]。
1.3研究内容、目的和意义
纯棉机织物的前处理工艺有多种,如传统工艺和两步法、一步法短流程工艺,每种方法都有各自的优势和缺点。在本实验中,对前处理的各种方法进行了研究并对其进行优化。选择符合企业生产要求的汽蒸法进行实验。在工艺优化过程中,采用正交法对每种处理方案进行探究。实验重点研究短流程的一步法工艺,通过一系列实验确定其最佳工艺处方,并且对工艺条件如加工时间和轧液率等因素进行了讨论找到符合节能环保要求的工艺因素。
20世纪70年代爆发了中东石油危机,导致能源紧张,由于前处理工序的能耗在总能耗中占有较大的比例,因而促使西方国家研究开发了高效低耗的短流程前处理新工艺。随着精细化工和精密自动测控仪器的开发,提供了合理地缩短或合并前处理工序的可能性,因而在20世纪70年代后期,促成染整行业短流程前处理新工艺得到了迅速发展。我国直到20世纪80年代中期才开始短流程前处理新工艺的研究,但发展不快,客观上由于可供选择的高效助剂跟不上发展需要,且大部分工厂因利用原有设备而受到了限制。自1988年以来中国纺织工程学会染整专业委员会已连续召开了四届前处理学术讨论会,重点狠抓了短流程前处理新工艺的推广应用。因而近年来该新工艺已广泛应用于各种织物,其覆盖面也逐步扩大,助剂的配套以及设备的合理组合都有了较大进展。这一转变使得织物前处理工艺有可能达到节能、节水、缩短工时和提高工效的目的[2]。
印染是高能耗、高污染行业,印染用水量占全部纺织工业用水的80%。该实验在传统工艺基础上探究清洁生产工艺,从而减轻废水污染。印染产业必须向环境友好型方向发展,以生态环保理念开发并推广各类减少污染、节约能源、利于健康的新技术和新产品。就减轻环境污染和降低能源消耗等角度来讲,对短流程前处理工艺进行研究有其现实意义。
青岛大学本科毕业论文(设计)
2.实验
2.1实验材料、化学品和仪器
2.1.1实验材料
烧毛后的纯棉机织物坯布
2.1.2实验所需化学品
表2.1实验药品
试剂名称
氢氧化钠 过氧化氢(30%) 氧漂稳定剂GEO 精练剂 渗透剂JFC
生产厂家
齐鲁石化公司研究院试剂厂 莱阳经济技术开发区精细化工厂 青岛大学研制 青岛大学研制 青岛大学研制
2.1.3实验所需仪器
表2.2实验仪器
仪器名称
HH-2恒温水浴锅 M215织物毛效仪 SC-80C全自动色差计
101-1-S型电热恒温鼓风干燥箱 电子万用炉 34cmA型双篦蒸锅 AO-01气动小轧车 T300电子天平
生产厂家
江苏金坛新一佳保 青岛山纺仪器有限公司 北京康光仪器有限公司 上海跃进医疗器械厂
北京市永光明医疗仪器有限公司 潮安县彩塘群兴五金厂 天津华普有限公司
常熟市天量仪器有限责任公司
其他仪器:烧杯(500ml、50ml),量筒,温度计,玻璃棒,表面皿,药匙,pH试纸。
青岛大学本科毕业论文(设计)
2.2实验内容
2.2.1实验材料准备
将烧毛后的纯棉机织物坯布剪成40cm×20cm的布样,对每块织物进行称重。
2.2.2退浆、煮练、漂白三步法工艺
三步法是纯棉坯布前处理的传统工艺。该方法处理效果好,对织物上杂质去除较彻底。但是其碱用量较大且处理时间较长,所以带来了能源浪费和污水处理困难等问题。为确定该种方法的最佳工艺,采用正交法来进行一系列实验。进行这种工艺实验的目的是为了与后面的短流程工艺作比较,从而有利于实验结论的得出。
三步法工艺处方如下[1]:
退浆工艺
氢氧化钠 8-12g/L 渗透剂JFC 1g/L 轧液体积 200ml 80-85℃轧碱,汽蒸45min 轧液率=110% 煮练工艺
氢氧化钠 40g/L 精练剂 6g/L 轧液体积 200ml 55℃轧煮练液,汽蒸90min 轧液率=110% 氧漂工艺
过氧化氢(100%) 4.5-6g/L 氧漂稳定剂GEO 2-3g/L 精练剂 4g/L 氢氧化钠调pH至10.5-11 轧液体积 200ml
青岛大学本科毕业论文(设计)
常温轧氧漂液,汽蒸45min 轧液率=110% 实验步骤:
退浆工艺:在烧杯中加入规定量的蒸馏水,然后称取规定量的氢氧化钠,边搅拌边加入烧杯中,搅拌至完全溶解后加入规定量的渗透剂,并搅拌均匀成退浆液。将织物润湿,在80-85℃条件下浸轧退浆液(两浸两轧,轧液率为110%),然后100℃下汽蒸45min。处理完之后,将织物取出,用热水(85-90℃)洗一次,温水(50-60℃)洗两次,然后冷水洗,最后烘干称重。
煮练工艺:在烧杯中加入规定量的蒸馏水,然后称取规定量的氢氧化钠,边搅拌边加入烧杯中,搅拌至完全溶解后加入规定量的精炼剂,并搅拌均匀成煮练液。将退浆后织物润湿,在55℃条件下浸轧煮练液(两浸两轧,轧液率为110%),然后100℃下汽蒸90min。处理完之后,将织物取出,用热水(85-90℃)洗一次,温水(50-60℃)洗两次,然后冷水洗净留作漂白。
漂白工艺:在烧杯中加入规定量的蒸馏水,然后量取规定量的过氧化氢(30%),边搅拌边加入烧杯中,搅拌均匀后加入规定量的氧漂稳定剂和精练剂,并用氢氧化钠调节pH至10.5-11,搅拌均匀成漂白液。将煮练后织物在常温条件下浸轧漂白液(两浸两轧,轧液率为110%),然后100℃下汽蒸45min。处理完之后,将织物取出,用热水(85-90℃)洗一次,温水(50-60℃)洗两次,然后冷水洗,最后烘干。
结果比较:测定不同处理试样的退浆率、毛效和白度,通过比较来确定三步法最佳工艺。
2.2.3退煮-氧漂两步法工艺
两步法工艺在传统工艺的基础上做了改进,将退浆和煮练放在一浴中进行,从而节省了氢氧化钠等化学品的用量并且使处理时间缩短。采用正交的方法进行一系列实验,由此来确定两步法最佳工艺,并与其他方法的处理结果进行比较。
两步法工艺处方如下[5]: 退煮工艺
氢氧化钠 20-25g/L 精练剂 6g/L 轧液体积 200ml
青岛大学本科毕业论文(设计)
55℃轧退煮液,汽蒸90min 轧液率=110% 氧漂工艺
过氧化氢(100%) 4.5-6g/L 氧漂稳定剂GEO 2-3g/L 精练剂 4g/L 氢氧化钠调pH至10.5-11 轧液体积 200ml 常温轧氧漂液,汽蒸45min 轧液率=110% 实验步骤:
退煮工艺:在烧杯中加入规定量的蒸馏水,然后称取规定量的氢氧化钠,边搅拌边加入烧杯中,搅拌至完全溶解后加入规定量的精练剂,并搅拌均匀成退煮液。将织物润湿,在55℃条件下浸轧退煮液(两浸两轧,轧液率为110%),然后100℃下汽蒸90min。处理完之后,将织物取出,用热水(85-90℃)洗一次,温水(50-60℃)洗两次,然后冷水洗,最后烘干称重。
漂白工艺:在烧杯中加入规定量的蒸馏水,然后量取规定量的过氧化氢(30%),边搅拌边加入烧杯中,搅拌均匀后加入规定量的氧漂稳定剂和精练剂,并用氢氧化钠调节pH至10.5-11,搅拌均匀成漂白液。将退煮后织物润湿,在常温条件下浸轧漂白液(两浸两轧,轧液率为110%),然后100℃下汽蒸45min。处理完之后,将织物取出,用热水(85-90℃)洗一次,温水(50-60℃)洗两次,然后冷水洗,最后烘干。
结果比较:测定不同处理试样的退浆率、毛效和白度,通过比较来确定两步法最佳工艺。
2.2.4退煮漂一步法工艺
一步法工艺较传统工艺和两步法工艺有更进一步的改善。它把传统退浆、煮练、漂白三步工艺各自的作用原理和去除对象合并在一步中完成。如碱在一步法中具有三方面的作用,又如过氧化氢也不仅是漂白剂,还可作为氧化退浆剂并且兼具对浆料、木质素及其他杂质的氧化作用[8]。由此可见,一步法工艺能有效利用化学品各方面的性能,从而减少了试剂用量使污水处理难度大大降低并可以缩短处理时间。因此一步法工艺有很高的研究价
青岛大学本科毕业论文(设计)
值,使染整行业高污染、高能耗的局面有所改善,达到节能环保目的。在本实验中,采用正交实验的方法来确定各种试剂的合理用量及影响处理效果的各种因素,从而确定其最佳工艺方案。
一步法工艺处方如下[5]:
氢氧化钠 15-25g/L 过氧化氢(100%) 10-15g/L 氧漂稳定剂GEO 6-8g/L 精练剂 8g/L 渗透剂 2g/L 轧液体积 200ml 常温轧工作液,汽蒸90min 轧液率=110% 实验步骤:
在烧杯中加入规定量的蒸馏水,然后称取规定量的氢氧化钠,边搅拌边加入烧杯中,搅拌至完全溶解后加入规定量的精练剂和氧漂稳定剂,最后加入过氧化氢并搅拌均匀成工作液。将织物润湿,在常温条件下浸轧工作液(两浸两轧,轧液率为110%),然后100℃下汽蒸90min。处理完之后,将织物取出,用热水(85-90℃)洗一次,温水(50-60℃)洗两次,然后冷水洗,最后烘干称重。
结果比较:比较第一组正交实验试样的退浆率、毛效和白度等测量指标,选出较理想的工艺处方,缩小各种试剂的浓度范围进行进一步的正交实验。由此类推,直至确定出最佳工艺配方及处理条件。
青岛大学本科毕业论文(设计)
3.结果与讨论
3.1退浆、煮练、漂白三步法工艺
正交实验方案为三因素三水平,其他条件为:退浆中渗透剂1g/L;煮练中氢氧化钠40g/L,精练剂6g/L;漂白中精练剂4g/L。
表3.1三步法工艺正交实验的因素及水平
因素
水平氢氧化钠(退浆)g/L 过氧化氢(100%)g/L 氧漂稳定剂g/L
8 10 12
4.5 5.0 6.0
2.0 2.5 3.0
表3.2三步法工艺正交实验表
试样编号 1 2 3 4 5 6 7 8 9 氢氧化钠(退浆)g/L 过氧化氢(100%)g/L 氧漂稳定剂g/L 8 8 8 10 10 10 12 12 12
4.5 5.0 6.0 4.5 5.0 6.0 4.5 5.0 6.0
2.0 2.5 3.0 2.5 3.0 2.0 3.0 2.0 2.5
青岛大学本科毕业论文(设计)
表3.3三步法工艺正交实验试剂用量表
试样编号 氢氧化钠(退浆)g 1 2 3 4 5 6 7 8 9 1.6 1.6 1.6 2.0 2.0 2.0 2.4 2.4 2.4 0.2 0.2 0.2 0.2 0.2 0.2 0.2 0.2 0.2 渗透剂g
氢氧化精练剂钠(煮(练)g 8 8 8 8 8 8 8 8 8
煮
过氧化
氧漂稳
精练剂(
氧
pH(氢氧化钠调) 10.5-11 10.5-11 10.5-11 10.5-11 10.5-11 10.5-11 10.5-11 10.5-11 10.5-11
氢(30%)定剂g g 2.97 3.30 3.96 2.97 3.30 3.96 2.97 3.30 3.96
0.4 0.5 0.6 0.5 0.6 0.4 0.6 0.4 0.5
练)g 1.2 1.2 1.2 1.2 1.2 1.2 1.2 1.2 1.2
漂)g 0.8 0.8 0.8 0.8 0.8 0.8 0.8 0.8 0.8 3.1.1退浆率的测定
本实验用失重法来测定织物的退浆率。该方法首先应明确织物上浆料总的含量,所以先剪取40cm×20cm的纯棉坯布称重,对其进行全退浆。织物退浆前后质量差就可认为是浆料含量。全退浆工艺为[1]:
氢氧化钠 10g/L 过氧化氢(100%) 6g/L 渗透剂 1g/L 氧漂稳定剂GEO 2g/L 浴比 1:30 温度 95-100℃ 时间 2h
青岛大学本科毕业论文(设计)
表3.4三步法工艺正交实验退浆率的测定
试样编号 0(全退浆) 1 2 3 4 5 6 7 8 9 处理前质量g 11.14 11.24 11.20 11.36 11.07 11.41 10.97 11.01 11.47 11.36
处理后质量g 8.68 9.22 9.30 8.66 8.98 9.15 8.90 8.90 9.18 9.07
质量差g 2.46 2.02 1.90 2.05 2.09 2.26 2.07 2.11 2.29 2.29
退浆率%91.42 94.24 91.28 89.95 95.83 92.92 91.35 85.63 88.25 由表中数据得,两步法处理后织物退浆率均能达到要求。
3.2.2毛效的测定
用毛细效应测试仪测定各个织物的毛效,测定方法同3.1.2所述。
表3.11两步法工艺正交实验毛效的测定
试样编号 毛cm 效7.0 8.6 5.9
7.7
10.5
10.0
8.0
9.0
10.5 1 2 3
9 由表中数据得,碱浓度相对较低时织物的毛效较低,碱浓度提高后织物的毛效有所提高能达到甚至超过最低要求。
3.2.3白度的测定
用SC-80C全自动色差计测量处理后织物白度。测量步骤同3.1.3。
青岛大学本科毕业论文(设计)
表3.12两步法工艺正交实验白度的测定
试样编号 白度 70.23 68.36 71.47平均值 70.02 74.98 76.32 77.65 76.32 75.01 76.68 74.48 75.39
70.65 70.07 69.88 70.20
72.04 69.67 71.12 70.94
73.63 70.43 74.59 72.88
69.71 68.74 72.93 70.46
76.61 75.80 76.35 76.25
73.08 73.08 72.03 72.73 1 2 3
9 由表中数据得,两步法处理后织物白度都在70以上,均能达标。
3.2.4两步法正交实验讨论和最佳工艺的确定
由表3.10得,本实验中的退煮-漂两步法工艺处理后的织物退浆率都能达标。由表3.11得,各个试样的毛效参差不齐。其中碱浓度越高的处方处理后试样的毛效普遍较高,说明碱浓度越高越有利于杂质的去除。但是在碱浓度相同的试样中,毛效也不尽相同,有的甚至相差较大,如试样
1、2和3。因为过氧化氢也具有去除织物上杂质的功效并且漂白处方中还添加了精练剂,这在一定程度上能弥补上一步煮练效果不好的缺点。虽然它们碱浓度相同但是漂白工艺中过氧化氢的用量是不同的,这导致了处理后除杂效果的不同。所以三者毛效不太接近,其中2的毛效最好,这可能是由于过氧化氢用量增加的缘故。但3的过氧化氢用量比2高而毛效却不如2好,可能是因为其稳定剂用量过高抑制了过氧化氢的有效分解,从而使其除杂效果不理想。试样4-6的毛效规律同试样1-3是相同的,可以用相同的理论来解释。而试样7-9碱浓度相同,毛效值是递增的。它们的碱浓度高,退煮后织物上杂质残留较少,在漂白中需少量的过氧化氢即可。所以这时过氧化氢是过量的,稳定剂浓度越高过氧化氢的利用率越高。这导致了试样7-9毛效递增的趋势。由表3.10和3.11,综合退浆率、毛效值和试剂用量尽量少等因素,可以选择试样2的处方为较合理工艺。
由表3.12得,9组试样的白度值均能达到要求。为节省试剂用量,在试样1-3中进行选择。再结合表3.10和3.11的分析可得,试样2的工艺配方为两步法工艺中较合理工艺。
3.3退煮漂一步法工艺
3.3.1一步法工艺处方的确定
(1)第一次正交实验
青岛大学本科毕业论文(设计)
正交实验方案为三因素三水平,其他条件为:精练剂8g/L,渗透剂2g/L。
表3.13一步法工艺第一次正交实验的因素及水平
因素 水平氢氧化钠g/L
过氧化氢(100%)g/L 氧漂稳定剂g/L
15 20 25
10 13 15
6 7 8 表3.14一步法工艺第一次正交实验表
试样编号 1 2 3 4 5 6 7 8 9 氢氧化钠g/L 15 15 15 20 20 20 25 25 25
过氧化氢(100%)g/L 氧漂稳定剂g/L 10 13 15 10 13 15 10 13 15
6 7 8 7 8 6 8 6 7
青岛大学本科毕业论文(设计)
表3.15一步法工艺第一次正交实验试剂用量表 试样编号 氢氧化钠g
过氧化氢(30%)g
氧漂稳定剂g
精练剂g
渗透剂g 1 2 3 4 5 6 7 8 9 3 3 3 4 4 4 5 5 5
6.60 8.58 9.90 6.60 8.58 9.90 6.60 8.58 9.90
1.2 1.4 1.6 1.4 1.6 1.2 1.6 1.2 1.4
1.6 1.6 1.6 1.6 1.6 1.6 1.6 1.6 1.6
0.4 0.4 0.4 0.4 0.4 0.4 0.4 0.4 0.4 ①退浆率的测定
与3.1.1相同,本次正交实验中用失重法来测定织物退浆率。全退浆工艺同上。
表3.16一步法工艺第一次正交实验退浆率的测定
试样编号 0(全退浆) 1 2 3 4 5 6 7 8 9 处理前质量g 11.14 11.25 11.26 11.42 11.30 11.29 11.44 11.32 11.34 11.53
处理后质量g 8.68 9.55 9.64 9.65 9.31 9.50 9.39 9.30 9.36 9.47
质量差g 2.46 1.70 1.62 1.77 1.99 1.79 2.05 2.02 1.98 2.06
退浆率%83.05 84.83 84.05 85.20 86.72 83.28 84.81 83.12 84.86 由表中数据得,织物退浆率均在80%以上,达到要求。所以氢氧化钠浓度应小于25g/L。 ②毛效的测定
用毛细效应测试仪测定各个织物的毛效,测定方法同3.1.2所述。
表3.23一步法工艺第二次正交实验毛效的测定
试样编号 毛cm 效8.0 7.5 9.6
8.2
5.5
8.5
7.0
7.0
8.5 1 2 3
9 由表中数据得,织物毛效普遍在8.0以上。 ③白度的测定
用SC-80C全自动色差计测量处理后织物白度。测量步骤同3.1.3。
22
青岛大学本科毕业论文(设计)
表3.24一步法工艺第二次正交实验白度的测定
试样编号 白度 71.09 69.36 72.52平均值 70.99 74.48 70.18 70.92 71.86 74.13 74.15 70.67 72.98
72.79 71.41 72.83 72.34
70.33 70.37 70.67 70.46
71.44 70.33 72.84 71.54
69.42 68.25 67.90 68.52
73.43 73.06 71.65 72.71
71.16 71.31 70.57 71.01 1 2 3
9 由表中数据得,织物白度均接近70。 ④第二次正交实验结果讨论
由表3.22得,本次正交实验的9组试样的退浆率均大于83%,退浆效果较好。由表3.24得,除试样7外,其他试样的白度值均能达到要求。由表3.23得,本次正交实验9组试样的毛效值较第一次正交实验有明显提高,但是其变化没有明显规律。如试样1-3,它们的毛效分别为8.0、7.5和9.6。虽然三者的碱浓度相同,但是其过氧化氢浓度是递增的。由于过氧化氢在一步法中对织物上的杂质也具有氧化作用,所以引起毛效的不同。又因为稳定剂用量的不同,使反应过程中过氧化氢的有效分解量有差异,从而导致过氧化氢对杂质的不同作用程度,就表现为毛效的高低起伏不呈现明显规律。但是总体来讲,该次正交实验中被处理织物的退浆率、毛效和白度等测量指标是比较接近处理要求的。所以,可以在本次实验基础上并结合节能减排的宗旨进一步缩小主要试剂如氢氧化钠和过氧化氢的用量范围。
氢氧化钠浓度为25g/L时,处理效果达标,所以可以将其浓度范围缩小至23-25g/L。9组试样的白度值均能达到要求,为节省试剂可将其用量缩小至18-20 g/L。因此根据这两个浓度范围可以制定另一个正交实验组,进行深度探究。 (3)第三次正交实验
正交实验方案为三因素三水平,其他条件为:精练剂8g/L,渗透剂2g/L。
表3.25一步法工艺第三次正交实验的因素及水平
因素 水平氢氧化钠g/L
过氧化氢(100%)g/L 氧漂稳定剂g/L
23 24 25
18 19 20
6 7 8
23
青岛大学本科毕业论文(设计)
表3.26一步法工艺第三次正交实验表
试样编号 1 2 3 4 5 6 7 8 9 氢氧化钠g/L 23 23 23 24 24 24 25 25 25
过氧化氢(100%)g/L 氧漂稳定剂g/L 18 19 20 18 19 20 18 19 20
6 7 8 7 8 6 8 6 7
表3.27一步法工艺第三次正交实验试剂用量表 试样编号 氢氧化钠g
过氧化氢(30%)g
氧漂稳定剂g
精练剂g
渗透剂g 1 2 3 4 5 6 7 8 9 4.6 4.6 4.6 4.8 4.8 4.8 5.0 5.0 5.0
11.88 12.54 13.20 11.88 12.54 13.20 11.88 12.54 13.20
1.2 1.4 1.6 1.4 1.6 1.2 1.6 1.2 1.4
1.6 1.6 1.6 1.6 1.6 1.6 1.6 1.6 1.6
0.4 0.4 0.4 0.4 0.4 0.4 0.4 0.4 0.4 ①退浆率的测定
与3.1.1相同,本次正交实验中用失重法来测定织物退浆率。全退浆工艺同上。
24
青岛大学本科毕业论文(设计)
表3.28一步法工艺第三次正交实验退浆率的测定
试样编号 0(全退浆) 1 2 3 4 5 6 7 8 9 处理前质量g 11.14 11.56 11.54 11.49 11.59 11.43 11.41 11.43 11.32 11.36
处理后质量g 8.68 9.59 9.63 9.48 9.36 9.17 9.23 9.42 9.26 9.30
质量差g 2.46 1.97 1.91 2.01 2.23 2.26 2.18 2.01 2.06 2.06
退浆率%78.45 77.65 77.06 82.26 81.60 86.04 由表中数据得,试样1-3退浆率不达标,试样4-6退浆率均达到要求。 ②毛效的测定
用毛细效应测试仪测定各个织物的毛效,测定方法同3.1.2所述。
表3.34一步法工艺第四次实验毛效的测定
试样编号 1 2 6.3
3 7.0
4 6.5
5 4.5
6 5.5 毛效(cm) 7.9 由表中数据得,6个试样的毛效均不好。 ③白度的测定
用SC-80C全自动色差计测量处理后织物白度。测量步骤同3.1.3。
表3.35一步法工艺第四次实验白度的测定 试样编号 白度 1 70.02 71.56 70.14平均值 70.57 2 66.97 66.89 63.46 65.77
3 65.31 65.16 64.84 65.10
4 75.32 74.82 73.54 74.56
5 70.20 71.97 68.66 70.28
6 71.52 71.62 73.06 72.07 由表中数据得,试样4-6白度均达标。 ④第四次实验结果讨论
由表3.33和3.35得,试样4-6(过氧化氢浓度为19g/L)退浆率和白度达标而试样1-3(过氧化氢浓度为18g/L)退浆率和白度较低,这表明碱浓度为24 g/L条件下过氧化
28
青岛大学本科毕业论文(设计)
氢为19g/L时退浆和漂白效果好。
由表3.34得,6个试样的毛效均不达标。试样1-3的毛效较其他的好但是相差不大。这可能是因为稳定剂的用量而引起的。在过氧化氢浓度为19g/L时增加稳定剂用量就有可能达到目的。
所以接下来的实验中要考虑稳定剂对处理效果的影响。其中过氧化氢浓度确定为19g/L。
(5)第五次实验
第四次实验中已经确定氢氧化钠浓度为24g/L,过氧化氢浓度为19g/L。本实验中确定稳定剂的用量。
实验处方为:氢氧化钠 24g/L 过氧化氢 19g/L 氧漂稳定剂GEO 5-9g/L 精练剂 8g/L 渗透剂 2g/L
表3.36一步法工艺第五次实验试剂用量表
试样编号 氢氧化钠g
过氧化氢(30%)g 1 2 3 4 5 4.8 4.8 4.8 4.8 4.8
12.54 12.54 12.54 12.54 12.54
1.0 1.2 1.4 1.6 1.8
1.6 1.6 1.6 1.6 1.6
0.4 0.4 0.4 0.4 0.4
氧漂稳定剂g
精练剂g
渗透剂g ①退浆率的测定
与3.1.1相同,本次正交实验中用失重法来测定织物退浆率。全退浆工艺同上。
29
青岛大学本科毕业论文(设计)
表3.37一步法工艺第五次实验退浆率的测定
试样编号 0(全退浆) 1 2 3 4 5 处理前质量g 11.14 11.52 11.57 11.65 11.69 11.81
处理后质量g 8.68 9.48 9.59 9.63 9.57 9.70
质量差g 2.46 2.04 1.98 2.02 2.12 2.11
退浆率%80.38 78.26 80.42 由表中数据得,试样1和3的退浆率达标。 ②毛效的测定
用毛细效应测试仪测定各个织物的毛效,测定方法同3.1.2所述。
表3.42一步法工艺第六次实验毛效的测定 试样编号 毛效(cm) 1 7.0
2 4.0
3 8.5 由表中数据得,试样3的毛效达标。 ③白度的测定
用SC-80C全自动色差计测量处理后织物白度。测量步骤同3.1.3。
31
青岛大学本科毕业论文(设计)
表3.43一步法工艺第六次实验白度的测定
试样编号 白度 1 68.82 68.73 72.20平均值 69.92
2 70.42 70.31 68.58 69.77
3 71.11 70.23 74.78 72.04 由表中数据得,试样3的白度达标。 ④第六次实验结果讨论
由表3.41得,试样1和3的退浆率达标。由表3.42得,试样3的毛效达标。由表3.43得,试样3的白度达标。综合三个表的结果可以得出,试样3的退浆率、毛效和白度值均能达到要求。由此可以确定,精练剂浓度为8g/L。 (7)第七次实验
本实验要确定渗透剂的用量。
实验处方为:氢氧化钠 24g/L 过氧化氢 19g/L 氧漂稳定剂GEO 9g/L 精练剂 8g/L 渗透剂 1-3g/L 表3.44一步法工艺第七次实验试剂用量表
试样编号 1 2 3 氢氧化钠g 4.8 4.8 4.8
过氧化氢(30%)g 氧漂稳定剂g 12.54 12.54 12.54
1.8 1.8 1.8
精练剂g 1.6 1.6 1.6
渗透剂g 0.2 0.4 0.6 ①退浆率的测定
与3.1.1相同,本次正交实验中用失重法来测定织物退浆率。全退浆工艺同上。
32
青岛大学本科毕业论文(设计)
表3.45一步法工艺第七次实验退浆率的测定
试样编号 0(全退浆) 1 2 3 处理前质量g 11.14 11.49 11.30 11.36
处理后质量g 8.68 9.48 9.30 9.30
质量差g 2.46 2.01 2.00 2.06
退浆率%81.36 76.31 73.43 ②毛效的测定
用毛细效应测试仪测定各个织物的毛效,测定方法同3.1.2所述。
34
青岛大学本科毕业论文(设计)
表3.50轧液率110%时试样毛效的测定
试样编号 毛效(cm) 1 8.5
2 4.5
3 2.0 ③白度的测定
用SC-80C全自动色差计测量处理后织物白度。测量步骤同3.1.3。
表3.51轧液率110%时试样白度的测定
试样编号 白度 1 72.27 72.09 71.24平均值 71.87
2 65.13 64.10 66.34 65.19
3 61.88 60.36 60.14 60.79 ④第一组实验结果讨论
由表3.45-3.47得,试样1(汽蒸120min)的退浆率在80%以上,毛效为8.5,白度值为71.87。其各项检测指标都能达到要求。而试样2和3都不达标。汽蒸120min时(退浆率为81.36,毛效为8.5,白度为71.87),处理效果与汽蒸90min(退浆率为80.42,毛效为8.5,白度为72.04)相比有所提高但提高不多。汽蒸60min、45min时,处理效果不好。所以轧液率为110%时,汽蒸90min适宜。 (2)第二组实验
该组实验处理四个试样,汽蒸时间分别120min、90min、60min和45min。选择轧液率为100%。
表3.52轧液率100%时试剂用量及工艺条件
试样编号 氢氧化钠g
过氧化氢g
氧漂稳定剂g 1 2 3 4 4.8 4.8 4.8 4.8
12.54 12.54 12.54 12.54
1.8 1.8 1.8 1.8
1.6 1.6 1.6 1.6 精练剂g
渗透剂g 汽蒸时间min
0.4 0.4 0.4 0.4
120 90 60 45 ① 退浆率的测定
与3.1.1相同,本次正交实验中用失重法来测定织物退浆率。全退浆工艺同上。
35
青岛大学本科毕业论文(设计)
表3.53轧液率100%时试样退浆率的测定
试样编号 0 1 2 3 4 处理前质量(g) 11.14 11.15 11.20 11.19 11.73
处理后质量(g) 8.68 9.17 9.22 9.34 9.87
质量差(g) 2.46 1.98 1.98 1.85 1.86
退浆率(%)80.27 73.07 72.63 71.31 ②毛效的测定
用毛细效应测试仪测定各个织物的毛效,测定方法同3.1.2所述。
表3.58轧液率80%时试样毛效的测定
试样编号 毛效(cm) 1 4.5
2 2.4
3 2.2
4 2.0
③白度的测定
用SC-80C全自动色差计测量处理后织物白度。测量步骤同3.1.3。
37
青岛大学本科毕业论文(设计)
表3.59轧液率80%时试样白度的测定
试样编号 白度 1 54.82 55.64 54.09平均值 54.85
2 48.54 47.28 45.30 47.04
3 44.05 46.10 44.38 44.84
4 44.58 40.95 43.16 42.90 ④第三组实验结果讨论
由表3.53-3.55得,试样1的退浆率刚刚达标,但是毛效和白度不达标。试样2-4的三种指标都达不到要求。即轧液率为80%时,汽蒸时间长短织物的处理效果均不好。
综合以上3组实验得,轧液率为100%和80%时织物的处理效果不能达到处理要求,所以不选择。轧液率为110%时,汽蒸时间为120min和90min的织物处理效果能达到处理要求,但是两者的处理效果差别不大,所以为了节能选择汽蒸时间90min。 综上,选择轧液率为110%,汽蒸时间为90min。
3.3.3一步法最佳工艺处方及工艺条件的确定
由3.3.1的实验讨论得一步法汽蒸最佳工艺处方为:氢氧化钠24g/L,过氧化氢19g/L,氧漂稳定剂9g/L,精练剂8g/L,渗透剂2g/L。
由3.3.2的实验讨论得一步法汽蒸合理工艺条件为:轧液率110%,汽蒸时间90min。
3.4三步法、两步法和一步法最佳工艺的比较
3.4.1三种方法最佳工艺处理后织物的退浆率、毛效和白度比较
由3.1得三步法最合理工艺为试样1的处方,设为Ⅰ。 由3.2得两步法最合理工艺为试样2的处方,设为Ⅱ。
由3.3得一步法最合理工艺为试样5(一步法第六次实验)的处方,设为Ⅲ。 将三者的处理效果进行比较如下:
38
青岛大学本科毕业论文(设计)
表3.60三种方法的最佳工艺处理效果比较 试样编号 Ⅰ Ⅱ Ⅲ 退浆率% 81.38 94.24 80.91
毛效cm 12.7 8.6 8.2
白度 77.22 76.32 70.72 三步法处理效果较好,特别是在毛效中有明显的优势。两步法处理效果较三步法差一些,虽然其退浆率明显很高,但是其毛效却远远低于三步法。一步法处理效果刚能达标,没有优势。但是三步法做到了省时省物省力,更接近节能环保的要求。
3.4.2三种方法最佳工艺处理后织物强力损失的测量
织物强力测量步骤:
(1)将所要测量织物剪成30cm×5cm的布条,每种布样剪取三个布条。 (2)打开电子织物强力仪的电源。
(3)把剪取的布条固定在电子织物强力仪上使其绷紧。 (4)按下“拉伸”按钮,几秒钟后布条被拉断。
(5)电子织物强力仪与电脑联机,操作完成后,断裂强力等数值会在电脑上有显示。 (6)将所需数据记录下来。每个布样测三次,取其平均值作为织物强力。
表3.61三种方法的最佳工艺处理强力损失比较
试样编号 0(坯布)
Ⅰ 410 445 440 431.7
Ⅱ 500 447 459 468.7
Ⅲ 516 508 462 495.3 断裂强力测量555 值N 544 495 断裂强力平均531.3 值N 强力损失% —
18.7 11.8 6.8 由表中数据得,三步法处理的织物强力损失最严重,两步法次之,一步法强力损失最小。
39
青岛大学本科毕业论文(设计)
4.结论
4.1三步法最佳工艺
经过正交实验可以确定三步法最佳工艺为:
退浆工艺
氢氧化钠 8g/L 渗透剂JFC 1g/L 轧液体积 200ml 80-85℃轧碱,汽蒸45min 轧液率=110%
煮练工艺
氢氧化钠 40g/L 精练剂 6g/L 轧液体积 200ml 55℃轧煮练液,汽蒸90min 轧液率=110%
氧漂工艺
过氧化氢(100%) 4.5g/L 氧漂稳定剂 2g/L 精练剂 4g/L 氢氧化钠调pH至10.5-11 轧液体积 200ml 常温轧氧漂液,汽蒸45min 轧液率=110% 4.2两步法最佳工艺
经过正交实验可以确定两步法最佳工艺为:
40
青岛大学本科毕业论文(设计)
退煮工艺
氢氧化钠 20g/L 精练剂 6g/L 轧液体积 200ml 55℃轧退煮液,汽蒸90min 轧液率=110% 氧漂工艺
过氧化氢(100%) 5g/L 氧漂稳定剂GEO 2.5g/L 精练剂 4g/L 氢氧化钠调pH至10.5-11 轧液体积 200ml 常温轧氧漂液,汽蒸45min 轧液率=110% 4.3一步法最佳工艺
经过一系列正交实验和单因素实验可以确定一步法最佳工艺为:
氢氧化钠 23g/L 过氧化氢(100%) 19g/L 氧漂稳定剂 9g/L 精练剂 8g/L 渗透剂 2g/L 轧液体积 200ml 常温轧工作液,汽蒸90min 轧液率=110% 4.4节能环保工艺的选择
由4.1-4.3三种工艺处方可明显看出,一步法处理过程最简捷方便。三步法要对织物进行三次汽蒸,汽蒸时间太长,并且碱用量很高,织物强力损失(18.7%)非常严重。两步法虽然缩短了加工时间,但是其汽蒸时间仍然较长使织物强力损失(11.8%)还是很大。
41
青岛大学本科毕业论文(设计)
一步法将加工时间大大缩短使操作方便,降低了碱的用量,织物强力损失(6.8%)明显下降。所以一步法工艺减少了化学品的用量,节省了能源并使污水处理负担减轻,缩短了加工时间节约热能。而且一步法对织物强力损失较轻。所以一步法最佳工艺最接近节能环保要求。
42
青岛大学本科毕业论文(设计)
谢辞
在本论文的写作过程中,赵云国老师倾注了大量的心血,从选题到实验大纲,到一遍又一遍地指出实验方案中的具体问题,严格把关,循循善诱,在此我对赵老师表示衷心感谢。赵老师渊博的专业知识和精益求精的工作作风将是我今后学习工作的榜样。
还要感谢同组的姜娟、李瑞颖和柳进杉同学,在实验过程中她们也提出了许多宝贵意见给我很多启发。对你们的帮助和支持,我在此表示感谢。
再次感谢所有在实验中给与我帮助的老师和同学们!
43
青岛大学本科毕业论文(设计)
参考文献
[1]陈英.染整工艺实验教程 北京:中国纺织出版社,2009.7 [2]冯开隽,薛嘉栋.印染前处理 北京:中国纺织出版社,2006.11:3-15,141-144,198-201 [3]阎克路.染整工艺与原理(上册) 北京:中国纺织出版社,2009.9 [4]〔美〕华伦.S珀金斯著;陈英,王建明,王晓春译.纺织品染整基础 北京:中国纺织出版社,2004.3 [5]徐谷仓.染整织物短流程前处理 北京:中国纺织出版社,1999.9:6-12,31-33,93 [6]王菊生,孙凯.染整工艺原理(第一册) 北京:中国纺织出版社,1982.10:116-122 [7]周宏湘.染整技术350问 北京:中国纺织出版社,1995.12:2-4 [8]魏竹波,康保安.纺织工业清洁技术 北京:化学工业出版社,2003.7:3-6,54-106 [9]吴赞敏.纺织品清洁染整加工 北京:中国纺织出版社,2007.1 [10]曹修平.染整产品质量控制 北京:中国纺织出版社,2002.3:42-44,47-52 [11](比利时)索尔维公司编著;丁晓芬等译.漂白手册 北京:中国纺织出版社,2005.11:14-16 [12]宋慧君.染整概论 上海:东华大学出版社,2009.4:36-54 [13]宋心远,沈煜如.新型染整技术 北京:中国纺织出版社,1999.11:69-122 [14]高淑珍,赵欣.生态染整技术 北京:化学工业出版社,2003.6:202-207 [15]房宽峻.第八届全国染整前处理学术研讨会论文集,2009.
44
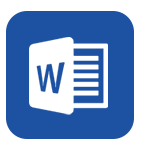