汽车设计是考虑人机工程、交通工程、制造工程、运营工程、管理工程的系统工程,需要了解车身结构、制造工艺要求、空气动力学、
人机工程学、工程材料学、机械制图学、声学、光学、绘画、雕塑和色彩等基本知识。 汽车开发的前期工作,是分析各方面的影响因素,明确汽车开发的目的和工作方向。
1、汽车开发规划:
1)、确定具体的车型;
2)、进行可行性分析(用户需求、市场情况、技术条件、工艺分析、成本核算); 3)、拟定汽车的初步方案(绘制方案图、性能计算、选定汽车技术规格和性能参数); 4)、制定出设计任务书(对汽车的形式、各个主要尺寸、主要质量指标、主要性能指标以及各个点成的形式和性能等具体要求)。
2、谈谈概念设计:概念设计,是对下一代车型或未来汽车的总概念进行概括描述,确定汽车的基本参数、基本结构和基本性能的设计,
概念设计同样需要研究产品的开发目的、技术水平、企业条件、目标成本、竞争能力等。
3、前期造型设计规划:
1)、从脑到手:草图
拿支铅笔把脑子里的想法表现出来,没必要画得很精致。
2)、初步定稿:草图+说明
思路明确,主体线条和大方向上的细节设计应有所表现,适当的地方加上简单说明。 3)、理念表达:效果图
把思路和理念用更细腻的手法表现,加入细节描绘和色彩,通过精致的绘图表达这款车的直观感受和立体效果,效果图和最后的整车的细节 未必完全相同,但表现出来的气质却是一脉相承的。 4)、内部设计:内饰效果图
详细描绘车内的各种细节和布局,加上必要说明。 5)、观感评估:1:5油泥模型 6)、改进阶段:1:1油泥模型 7)、测量阶段:三维坐标测量
8)、最后阶段:电脑设计 9)、完成
附:汽车是有生命的:眼睛—前照灯,嘴—进风口,肺—空气滤清器,血管—油路,神经—电路,心脏—发动机,胃—油箱,脚—轮胎, 肌肉—机械部分。
汽车内外饰工程设计要点
1、整车四大工艺:冲压、焊接、涂装、总装。
2、汽车动力性指标通常的评价参数:最高车速、加速时间、最大爬坡度。
3、典型的汽车总体结构包括:车身、发动机、底盘、内外饰、电器。
4、国际中规定汽车正面碰撞最低车速为:48km/h。
5、CNCAP(中国新车安全评定)中最高为5+。
6、驾驶舱布置需要与总布置(主要部门)协调。
7、汽车漏水的主要原因:车门变形不符合设计要求、密封条设计不合理、装配误差。
8、立柱类的小件装配到车身上时不需要设计专门的定位导向柱。
9、遮阳板的主要功能是遮挡强光影响,防止驾驶员眩晕。
10、与NVH性能关系密切的内饰件有:顶盖内衬、地毯、发动机仓隔热垫。
11、MOLDFLOW软件可以分析注塑件:变形情况、在模具中的流动情况、材料充模情况。
12、设计顺序:效果图、CAS面、油泥模型、A级面、工程化。
13、效果图分析内容:产品成型工艺性、安装可行性、成本可行性。
14、在车辆开发CAS面和模型阶段,仪表板设计人员需要配合其他部门对仪表板进行可行性分析:组合仪表视野分析、内部凸出物法规校核、前除霜风口、侧除霜风口位置可行性分析。
15、设计塑料件时某些地方可以不放拔模斜度,拔模斜度要考虑产品是否有皮纹。
16、2D图的功能包括:指导模具制作、指导零部件入厂验收、指导生产。
17、快速样件的作用:验证外观效果、验证设计结构、验证装配可行性。
18、运用START MODEL格式进行设计的好处:便于修改、提高设计效率、规范数据设计过程。
19、增加加强筋或安装点可以有效改善产品强度。 20、顶盖内衬成型方式:热压。
21、处理皮纹亮度高的方式:模具喷沙、产品工艺参数调整。
22、工装样件提供时如检具未验收,可采取全尺寸检测方式确认工装产品与设计数据的符合性。
23、不同材料、皮纹、光泽度的零件选用同种颜色时,应采用特殊产品单独封样方式保证试装成功。
24、能确保内饰板与座椅条纹绒面料(方向不同,色差不同)的一致性是:技术条件明确装配方向、封样。
25、车内噪声的主要处理方法:吸声处理、隔声处理。
26、驾驶员座舱里可见的属于内饰的零件,有:顶棚、地毯、遮阳板、座椅、ABCD立柱、仪表板、搁物板、门内饰板、玻璃。
27、汽车内饰件装配到车身以后的主要问题:不满足功能要求、装配以后容易脱落、内饰件外观不满足要求、各内饰件配合间隙不符合要求。
28、汽车内饰挥发性有机物(VOC)主要来源:仪表板、地毯、顶棚、座椅。
29、内饰零件之间要预留足够的空间给碰撞过程中弹出的气囊,以及用于碰撞过程中变形和吸收能量。 30、汽车内饰塑料采用的比较多的材料有:PP、PVC、ABS、POM、PC、PA
6、PA66等。
31、内饰件通常的色差要求是:△E
32、仪表板总成包括:中控箱、通风除霜管、手套箱总成。
33、注塑汽车仪表板的主要材料:ABS/PC。
34、汽车软质仪表板的主要作用是:改善零件手感和外观。
35、仪表板上手套箱的作用:放置物品、碰撞时提供乘员膝部保护。
36、仪表板出风口对风有2个控制功能。
37、仪表板出风口在使用过程中,出现排风异响的可能原因:出风口安装不可靠,没有紧固在仪表上;出风口的导风页片配合间隙不合理, 抖动;空调风门强度不够或设计不合理导致涡流产生。
38、仪表板上各种面罩与仪表板本体的主要连接方式:塑料卡子或卡扣连接。
39、仪表板的最新工艺:搪塑、真空成型、聚氨酯喷塑。
40、汽车仪表板总成上装配着大量的部件,包括驾驶仪表、控制开关、音响娱乐系统、安全气囊。
41、汽车仪表板上手套箱的功能失效形式:手套箱锁无法开启或关闭、手套箱转轴处断裂、手套箱在行驶过程中异响。
42、仪表板本体与前门饰间隙通常设计值是5~8mm。
43、仪表板本体、组合仪表罩、中央控制面板通常壁厚分别为3mm、2.5mm、2.5mm。
44、手套箱箱体与手套箱面板的常用连接方式:螺钉连接、热板焊接、振动摩擦焊。
45、在仪表板设计中,通常中控面板的位置高于仪表板本体面。
46、仪表板出风口材料常用ABS。
47、小轿车的手刹一般布置在:副仪表板上。
48、用于汽车车门减震垫的橡胶材料最可能的硬度(邵尔A型)是65度。
49、车门总成的零件:玻璃升降器、门锁、铰链。 50、车门密封条的加工工艺:挤出。
51、车门装饰板在行驶过程中发响的主要原因:卡扣选用不合理、卡扣与卡座配合间隙不合理、车门装饰板共震。
52、门内饰件分型面位置是由产品设计人员确定的。
53、门内饰板内开拉手与座椅位置有关。
54、主电动开关一般放于左前门。
55、驾驶员侧座椅安全带常用的形式:三点式。
56、汽车座椅设计的主要内容:满足座椅的机械功能、满足人机工程、满足碰撞时强度的要求。
57、座椅的静态舒适性主要指:座椅舒适性、靠背舒适性、头枕舒适性。
58、汽车座椅的主要作用:为人体提供良好的支撑、为驾驶员提供合适的位置和视野、提供碰撞时的安全保护。
59、地毯的分类:簇绒地毯、针刺地毯、PVC地毯。 60、地毯类零件的成型工艺:热压成型。
61、汽车地毯是重要的NVH(噪声、震动、舒适性)件,对整车的NVH性能有重要影响。 6
2、汽车地毯高度与座椅R点有关。 6
3、地毯增加棉粘的主要作用:消音隔热。
64、汽车乘员约束系统包括:安全带、安全气囊、转向盘。 6
5、PAB:乘员侧安全气囊。
66、汽车安全带的主要作用是在发生事故时,保护驾驶员不因为惯性远离座椅,碰撞仪表板、方向盘等物体。
67、轿车前保险杠与前罩间隙通常为4~5mm。 6
8、前保险杠的作用:装饰车身。 6
9、保险杠常用材料:改性PP。
70、前后保险杠装配以后主要关注保险杠与其他零件的配合处。
71、前保险杠在设计过程中要考虑:接近角、散热器进风面积、车外凸出物要求。 7
2、塑料件的公差等级的影响因素:选用的材料、模具的结构、尺寸大小。 7
3、PVC是难燃烧的材料。
74、高分子材料的三大合成材料为:塑料、橡胶、纤维。 7
5、PE属于热塑性塑料。 7
6、ABS材料的电镀性能较好。
77、PP是目前汽车内饰件用量最大的塑料。 7
8、三元已丙橡胶是目前汽车上最常用的橡胶材料。 7
9、目前顶盖内衬基材的常用材料:PV板。 80、塑料按用途分为:通用塑料、工程塑料、特种塑料。 8
1、评定塑料硬度的有:布氏硬度、洛氏硬度、邵氏硬度。 8
2、尼龙材料具有自润滑性。
83、大型薄壁塑料件的变型是无法避免的,能做的只有减少变形。
84、塑料卡扣在使用一段时间会松动,是由于材料的蠕变和应力松弛引起的。 8
5、POM材料具有自润滑性,是卡扣类零件主要材料。
86、PP材料的加强筋一般为产品厚度的1/3内不容易产生收缩痕。 8
7、吹塑风管常用的材料:PE。
88、两个塑料件装配以后间隙很大,主要的原因是零件变形和卡接设计不合理。 8
9、塑料制品翘曲变形的主要原因:模具温度太高,冷却时间不够;制品厚薄悬殊;模具冷却系统不合理,冷却不均匀。
90、塑料制品有飞边的主要原因:注射压力过大;加料太多;料筒、喷嘴、模具温度太高;模具密封不严。
91、塑料件注射成型的几个阶段:合模、注射、保压、冷却、顶出制品。
92、模具设计顺序:分模面设计、浇注系统设计、排气系统设计、脱模结构设计、冷却系统设计。
93、注塑浇注系统分为:冷流道系统和热流道系统。
94、流道末端必须设计冷料井,防止冷料随着流道系统进入型腔。 9
5、最常见的浇口设计错误就是造成产品出现熔接痕缺陷。
96、模流分析就是利用CAE软件,对塑料件的注塑、保压、冷却、翘曲等工艺工程进行模拟分析。
97、填料的作用:增进塑料的物理性能,如硬度、刚度及冲击刚度。
98、低压反应灌注机(简称低压机),它适用于泡沫熟料的成型,特别适用于软质、半硬质和硬质泡沫塑料,与一般塑料的热塑注射成型
工艺比较,优点在于:它所需压力小、模具承压小、所需锁模力小,特别对形状复杂、薄壁、大型制品其经济优越性十分显著;不用加热,
生产周期短;原料为液体,制品成型是借助于化学反应在模腔内完成。
99、塑料零件成型工艺除了一般的注塑以外,还有其他成型工艺:吸塑、吹塑、PV发泡、热压、搪塑、挤出。
100、微车安全拉手的成型工艺:气辅。 10
1、仪表板产品的模具开发周期最长。 10
2、仪表板脱模角度一般为WL线的25~27°。 10
3、内饰快速样件通常采用ABS材料制作。 10
4、控制箱杯托设计直径至少为80mm。 10
5、
10
6、刚性指标:弯曲模量。
10
7、座椅静态舒适性主要包括:座椅尺寸参数、座椅表面造型、泡沫特性。 10
8、座椅功能件主要包括:滑轨、调角器、高度调节器、腰托板。
10
9、采用体压分布曲线进行舒适性分析,要求曲线应均匀,不能突大或突小。
110、滑轨按断面结构一般分为C型滑轨和T型滑轨,T型滑轨强度优于C型滑轨。 1
11、微车滑轨行程是由95%美国男子的H点到5%日本女子H点的距离来确定的。 1
12、对R点和H点的区别:R点是总体布置在车身上的基准点,H点是在座椅上的基准点。
1
13、泡沫发泡工艺有:冷、热发泡。 1
14、一般头枕、坐垫泡沫比靠背泡沫稍硬。
1
15、泡沫物理性能指标为:密度、回弹率、拉伸强度、断裂伸长率、25%压缩强度、50%压缩永久变形。
1
16、对2009年2月1日后生产的汽车,座椅应满足国标GB15083-2006。
1
17、在座椅新国标GB15083中更改和新增的要求是:座椅强度、靠背高度、行李箱碰撞。 1
18、座椅CAE分析包括:座椅骨架强度、座椅固定点强度、安全带固定点强度。 1
19、对座椅H点测量的允许误差为:位置为±10mm,躯干角为±2°。 120、座椅安装位置尺寸应符合设计要求,采用专用检具检测。 1
21、
1
22、一般座椅面料为涤纶面料。
1
23、确定组合仪表罩帽沿(仪表板最高点)位置时,要满足低于前方下5°视野线。 1
24、仪表板模块化装配,作门洞通过性检查时,仪表板模块(包括机械手)与门洞法兰边最小应留有50mm间隙。
1
25、作组合仪表布置时,组合仪表中心位置应尽可能使驾驶员的视线处于下视角10~20°范围内。 1
26、作组合仪表布置时,须确定组合仪表中心位置到眼椭圆中心的距离,此距离一般取750±50mm。
1
27、仪表罩的顶点到方向盘轮缘中心的距离一般不小于80mm。
1
28、作CD机布置时,CD机中心位置应尽可能使驾驶员的视线处于下视角15°以下。 1
29、仪表板与转向锁壳最小应留有6mm间隙。
130、仪表板总成是各种仪表、信号、操作开关、空调及娱乐系统的集成,可划分为驾驶侧、副驾驶侧和中控台3大区域。
1
31、仪表板总成3大区域又可分为:A、B、C、D四个控制区。
1
32、仪表板横梁、主仪表板总成、副仪表板总成是仪表板系统中的主要内饰总成,其中,仪表板横梁是主要的传力和受力零件。
1
33、软饰仪表板由表层、缓冲层和骨架三部分使用多种材料构成,常用表皮材料:PVC、ABS/PVC、PP、TPO。
1
34、仪表罩常用材料:ABS、PC/ABS、PP。
1
35、仪表板表皮的典型成型工艺一般为:搪塑、喷塑和吸塑成型工艺。 1
36、仪表板本体的拔模方向与X方向正向一般成25°夹角。
1
37、在仪表板头碰试验中,冲击头的减速度超过80g的持续时间不得超过3ms。 1
38、在仪表板头碰试验中,头碰基准应除去方向盘外缘再加127mm的环带水平向前投影的区域,下边界是与方向盘下缘相切的水平面 (方向盘处于直线行驶位置)。 1
39、POM名称:聚甲醛。
140、与NVH性能关系最为密切的内饰件:前壁板隔音垫。 1
41、
1
42、内外饰的阻燃性要求的标准中,对燃烧速度要求小于100mm/min。 1
43、定位孔一般要求其中一个是圆孔(hole),另一个是长圆孔。
1
44、关于2D图制作过程:两个呈对称形状的零件或总成,一般绘制左零件;需要编写技术要求且中英文必须对应;车身坐标线间隔是100 或100的整数倍。
1
45、3C认证的零件:地毯、门槛装饰件、安全带。 1
46、汽车密封条通常使用的材料是:EPDM。 1
47、车门内饰板的基本壁厚通常是2.5mm。 1
48、1
49、
150、车身钣金件基准孔的位置公差通常是±0.2mm。 1
51、内外装饰件加强筋的厚度通常是零件基本壁厚的1/3。
1
52、塑料产品的加强筋一般小于为产品厚度的1/3不容易产生缩痕。 1
53、注塑工艺生产过程顺序:合模、注射、保压、冷却、开模、顶出。
1
54、为了提高保险杠与车身钣金搭接的外观质量,避免分型线外露,保险杠模具采用的办法是:内分型设计。 1
55、
1
56、前大灯不属于汽车内饰件。
1
57、汽车底盘系统包括:刹车系统、燃油系统、传动系统。 1
58、与顶衬搭接的零件有:安全拉手、遮阳板、前后框密封条。
1
59、内外饰零件生产中采用的焊接方式有:超声波焊接、摩擦振动焊接、热板焊接。 160、仪表板与前挡风玻璃设计的间隙为5mm。
16
1、注塑成型的主要缺陷:(飞边、流痕、缩痕、银痕)表面凹陷、缩孔、流纹、颜龟不均、烧焦、暗纹、暗斑、银纹、无光泽、泛白、
剥层、白化、浇口裂纹、应力开裂、龟裂、翘曲、扭转、溢边。产生的原因:注射压力、浇口位置、保压时间、模具问题、冷却管路设计不
合理、合模力设计不合理、气孔设计不合理、材料含水率。
16
2、内饰设计与内饰产品质量之间的关系:设计的好坏对最终产品的质量关系重大;不合理的设计会导致塑料件产品缺陷,如外表面缩印、
皮纹效果无法体现等;好的内饰设计需要考虑产品的工艺,不同产品加工工艺对设计影响很大。
16
3、分析设计成凸边支撑和加强肋支撑的作用:容器、罩、壳以及其他带有底部支撑面的塑料件,不宜采用整个底面支撑,而应设计出环形
周边支撑或数点底脚;因为塑料料收缩率大,成型中又易产生较大内应力,很难成型出平直的表面,用整个底面支撑,反而使塑料件放置时 不稳。
16
4、塑料(热塑性)材料常见性能指标有:密度、熔体流动速率、拉伸屈服强度、拉伸断裂伸长率、弯曲强度、弯曲弹性模量、热变形温度、洛氏硬度D、悬臂梁缺口冲击强度。 16
5、塑料模具分型面的选择原则:分型面最好开设在制品截面轮廓最大的部位,以便于使制品顺利脱模;分型面应选择在不影响塑料外观
质量的部位,如四角或边缘,而且由于分型面所产生的飞边,应容易修整清楚;分型面应尽量选在能使制品留在动模一侧的地方,将型芯设在
动模板上,依靠塑料的抱紧力,塑料留在动模一侧,对于无型芯的型腔,就应该将模具型腔设在动模一侧,以便于制品脱模;分型面应尽量
简单,避免采用复杂形状;分型面不应影响塑件的尺寸精度;当分型面作为主要排气面时,应将分型面设计在料流的末端,以利于排气;
一般侧向分型抽芯机构的抽拔距离都较小,选择分型面时应将抽芯或分型距离长的一边放在动定模的开模方向上,短的一边作侧抽芯。
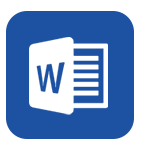