连铸工(高级)实际操作题
一、钢包分级标准?
A级罐:红热周转罐停罐<100分钟的大罐。
B级罐:红热周转罐停罐≥100分钟--<120分钟的大罐。
C级罐:红热周转罐停罐≥120分钟;停产检修、钢包加热≥4小时的大罐;小修罐第一炉。 D级罐:中修罐第一炉、大修罐第一炉。
二、浇钢前结晶器检查哪些内容?
答:1 每浇次浇前浇后必须测量结晶器倒锥度(详细记录在机长交接班本上)。
2将结晶器内弧宽面打开,检查结晶器铜板缝隙是否有残渣异物,否则必须清除干净。 3 将结晶器铜板夹紧,用塞尺插入结晶器铜板角隙,不准≥0.5mm,若超过此尺寸,必须处理或更换新结晶器。 4结晶器在距上口200 mm范围内不允许出现结晶器镀层剥落、龟裂以及深度≥0.5mm的划痕;在200mm 范围以下也不允许出现镀层剥落、龟裂(以露铜为准)以及深度≥1.0mm划痕。结晶器铜板不得有渗水情况。结晶器铜板表面轻微划伤用砂纸打磨 5检查结晶器足辊表面有无冷钢、残渣,是否对弧(新上线时),是否转动、无突出、凹进、明显裂纹及磨损凹坑且不能有大的弯曲变形,若达不到工艺要求必须更换。 6对结晶器各功能进行检查(结晶器调宽、软夹紧压力等),夹紧力必须保证上部1500±100Kg、下部5800±300Kg(若无显示或显示明显过大,通知计控厂进行处理,若未达标,则通知连检进行处理,连铸车间不得调整软夹紧力)。
三、中包小车的检查内容?
答:1中包小车行走轨道上无障碍物,过道上无堆积残钢渣、障碍物。 2中包小车升降同步,无异响及下滑,对中装置正常。 3中包小车行走正常无异样,横移好用无残钢。
4中包滑板机构正常,滑板油缸及接头无漏油,油缸动作无异常,中包滑板操作盒按钮及灯光显示正常,氩气压力、流量计正常。
5 中包小车行走声光报警设施正常,确认行走过程水口不会撞到盖板。
6中包小车上各栏杆完好,上下楼梯牢固、完好;中包小车各护板、挡溅板完好。
四、中包检查的主要内容?
答:1 中包滑板开关正常,中包滑板机械无晃动现象。
2 中包落位平稳,中包与对中装置吻合良好;包盖上无松动的残钢残渣。中包包体无裂纹、变形等异常。
3中包内无杂物,中包水口、滑板氩气畅通,涂料烘烤垮面积<0.5m2,冲击砖外观无异常,否则必须联系处理。
五、简述堵引锭操作
答: 1检查结晶器及引锭头应保持干净、干燥(用风管吹); 2将堵引锭材料准备齐全;
3用钢钎将纸绳依次堵入结晶器和引锭头之间缝隙内(先外弧,后内弧,再两侧),并与引锭头平齐(不得凸出);
4用手将密封胶挤在手指上,依下而上均匀地嵌入结晶器的铜板角缝隙内;
5第一炉钢水精炼结束后,将未受潮、无油污、无夹杂物的铁钉沫铺在引锭头上,并表面铺平,厚度约20~25mm左右;
6将两块小铁片互相垂直地围住燕尾槽拐弯和斜坡处,并在小铁片和斜坡处的纸绳之间放满铁钉沫; 7冷却弹簧的放置:将两根冷却弹簧牢固地竖放斜靠在薄铁片上,在燕尾槽内竖放一排冷却弹簧;在引锭头两边平行宽面铜板放三层冷却弹簧;中包水口下方及周围附近平行宽面靠铜板先放一排一层冷却弹簧(250mm宽度可放两排),再垂直宽面放一排一层冷却弹簧。 8用刷子粘上菜籽油均匀地刷在铜板上。
9收拾所有的工器具,并清扫结晶器盖板,切勿将杂物掉进结晶器内。 10浇铸准备条件具备后将铸机状态转入“浇铸准备”。
六、什么叫连铸坯热装热送? 答:利用连铸坯的热量配合相应得措施与轧制工序紧密衔接就是连铸坯热装热送。与连铸坯冷装相比,连铸坯热送热装的主要优点是:
1、节约能源。铸坯热装入炉温度越高,节能效果越好。
2、提高成材率,节约金属消耗。
3、简化生产工艺流程,降低费用成本。
4、减少工序,提高产品质量。
七、中包在连铸过程中起什么作用?
答:中包是放在钢包与结晶器之间的中间容器,是实现多炉连浇所必需的过渡容器。 1.减压:控制钢流,减少钢水静压力。
2.稳流:稳定钢流,减少钢流冲击所引起的飞溅,使液面平稳。 3.除夹杂:钢水在中包内停留时,夹杂物上浮。 4.分流:将钢水分配给各结晶器,起到分流作用。
八、影响结晶器液位控制有哪些因素?
答:1.中间包滑板或浸入式水口吹Ar量太大;
2.为避免水口堵塞的冲棒;
3.拉速变化频繁,造成液面波动大;
4.浸入式水口堵塞造成偏流引起液面波动。 5.自动控制液面检测器发生故障或操作不当; 6.结晶器内钢水偏流; 7.扇形段开口度不良。
九、结晶器锥度为什么要调整?
答:结晶器内热的传递路线是:钢水→坯壳→渣衣→气隙→铜板→冷却水带去热量。其中最大障碍是气隙,所以锥度调整是关键。锥度过小,由于铸坯收缩,气隙过大,在整个结晶器内坯壳得不到很好冷却。相应部位坯壳变薄,出结晶器后,由于钢水静压力产生侧面鼓肚,严重时造成漏钢。这就是裂纹性漏钢。锥度过大,气隙过小,拉坯阻力较大,严重也可能造成漏钢的危险。所以锥度一定要按规定调整。
十、大罐有桶底(冷钢)座开浇第一炉有何不利?
答:有桶底的大罐,用作第一炉开浇,其直接影响开浇成功率。包底冷钢熔化需要吸收大量的热量,使包底附近的钢水形成一个低温区,而这些低温钢水又恰恰是最先进入中间包,很容易在中包内造成低温水口碗处结冷钢,而使开浇失败。 十
一、结晶器内更换保护渣时应注意什么? 答:1.捞渣时不能过深,并且不能刮着坯壳。
2.要边捞渣边添加新保护渣,避免钢水液面暴露与空气接触。 3.适当降低拉速或在拉速较低时进行。 4.换渣时应保持结晶器液面的绝对稳定。 十
二、开浇引锭头漏钢主要原因?
答:1.堵引锭头材料不干燥、不干净,引起“爆炸”使坯壳达不到正常要求强度而漏钢。
2.冷却料摆放不规范,钢水进入结晶器后,结晶器底部冷却不良,形不成坚硬有一定强度底而漏钢。 3.引锭头纸绳未堵好,当拉矫机启动后,钢水从缝隙漏出。
4.开浇出苗过快过大,钢流会将结晶器底部铁钉、方钢冲散移位,无底冷却既易漏钢又不易脱锭;出苗钢流过小会造成先期到钢水不能很快将底部铁钉、方钢粘连,一旦拉矫起步,铁钉松动遇冷却水冲垮冲散,腾空底部会因承受钢水静压力而漏钢。 5.开浇钢流喷溅过大,结晶器角部挂钢后,未能及时停机处理,坯壳阻力增大挂破漏钢。 6.出苗时间短,起步升速快,钢水未形成一定强度坯壳,难以承受钢水静压力,出结晶器后漏钢。
7.引锭头自动下滑导致引锭头纸绳松动,开浇出苗中直接导致钢水从铜板周边漏钢。 8.结晶器铜板接缝超标,造成钢水嵌入接缝中,形成结晶器内挂阻力,坯壳拉裂漏钢。 十
三、造成非计划停浇的主要原因有哪些? 答:1.钢水温度低,造成水口堵;
2.钢水成分出格,避免造成废品; 3.生产节奏滞后,造成钢水未接上;
4.连铸操作工判断失误或操作失误引起的水口堵死和漏钢、溢钢事故; 5.因耐材不稳定造成的事故;
6.大罐系统的事故(包括引流不开);
7.设备发生突然故障或意外情况引起的水、电、气、油中断等致使被迫停浇。 十
四、一块热送坯的标志C6170351030请说明各位位数表示的内容? 答:C——表示三炼钢;
6——表示2006年生产的 ; 1——表示1号炉生产的 ; 7036——表示熔炼号; 1—-表示为1流
03——表示此炉钢的第3块坯; 0——表示分割号。
十五、连铸钢水温度过高有什么危害?
答:1.会使铸坯柱状晶发达,会促进中心偏析,疏松和裂纹等缺陷的发展;
2.加剧钢水自身的二次氧化及对钢包包衬、水口耐火材料的熔损,从而污染钢水; 3.引起水口失控,并使铸坯减薄而产生漏钢事故; 4.低拉速连铸,降低铸机的生产率。
十六、大包引流不开的主要原因有哪些?
答:1.大包水口不干净、有异物,造成水口堵塞;
2.引流砂颗粒不均匀,使得流动性不好,堵塞水口; 3.引流砂潮湿、结块,烘烤后使引流砂烧结; 4.大包水口内温度太高,使引流砂烧结;
5.钢水积压时间长,底部温度低,水口处结冷钢 十
七、什么叫中心偏析?产生原因及预防措施?
答:中心偏析是指铸坯中化学成分的差异,在铸坯横断面试样上每隔一定距离从表面向中心取样进行化学分析,发现中心的碳、S、P等元素含量明显高于其他部位。
原因:是由于连铸坯的柱状晶过分发展引起的,此外机械原因(如坯壳的鼓肚变形)也会引起铸坯的中心偏析。
措施:
1、低温浇注;
2、低拉速,超声波振动;
3、电磁搅拌等方法;
4、采用轻压下技术;
5、减少钢中P、S;
6、控制好开口度 十
八、二次冷却与铸坯表面质量的关系?
答:1.表面纵裂:主要原因是二次冷却局部过冷产生纵向凹陷而导致纵向裂纹。 2.表面、角部横向裂纹:在二次冷却的水量过大,喷嘴偏斜直射铸坯角部等造成了表面横向裂纹。
3.表面对角线裂纹:一般出现在方坯中,原因是四个面喷水不均匀,喷嘴堵塞等造成。
十九、连铸漏钢的根本原因?主要有哪几种类型?
答:产生漏钢的根本原因是结晶器内坯壳薄且生长不均匀,当铸坯出结晶器下口后,承受不住钢液的静压力以及其它应力的综合作用,坯壳的薄处被撕裂,钢液漏出,造成漏钢。 连铸漏钢类型主要有:粘连漏钢、开浇漏钢、裂纹漏钢、挂钢漏钢、内挂漏钢、封顶漏钢、高温高拉漏钢以及设备原因引起的漏钢。
二
十、你怎样保证取提样合格?
答:1.取样前的准备工作必须到位。
2.取样前钢水表面要平静、取样部位正确。
3.取样时用样模底部将钢渣扒开方可将样模插入钢水中。
4.按规定将样模要插入钢水深度≥300mm,要停留几秒钟,使其钢水能够将样模装满。5.提样时,样模不要倾斜,要平稳。
二十一、在浇铸过程中突然发生角裂应采取什么措施? 答:1.检查或更换结晶器保护渣;
2.拉速是否过高;
3.结晶器水、二冷水是否按工艺标准配给; 4.检查钢水[P]、[S]含量是否正常; 5.水口是否对中,有无破损和穿孔;
6.以上措施仍不能消除,则停浇检查结晶器倒锥度是否正常和漏水。 二十
二、实现热装和直接轧制的技术关键有哪些?
答:为了实施热装和直接轧制,必须解决的关键技术问题有:
1.无缺陷铸坯的生产技术,包括防止铸坯表面缺陷和内部缺陷的一系列措施以及热态下铸坯质量的检测技术;
2.高温铸坯的生产技术,包括铸坯保温,液芯复热、铸坯快速运送和补偿加热等; 3.提高直送率的技术,使各工序协调匹配,稳定均衡,有节奏地连续生产。 二十
三、影响振痕深度的因素有哪些?
答:影响振痕深度的因素有很多,主要有下面几个方面:
1、振动频率和振幅,高频振动下的振痕深度较浅,振幅增加,振痕深度增加。
2、拉速。其他条件不变,拉速增大,振痕变浅。
3、负滑脱量和负滑脱时间。负滑脱时间越长,坯壳凹陷的越深。
4、保护渣性能。黏度越大,振痕越浅。 二十
四、钢水温度不均匀有哪些原因?
答:1.氩后至开浇时间过长,造成温度重新分层;
2.吹氩过程中所加入的调温废钢没有完全熔化和均匀,造成温度分层不均匀; 3.吹氩时间过短或透气效果不好,钢水没有完全均匀,造成温度不均匀; 4.大罐烘烤不良,造成温降大,内外钢水温度不均匀。 二十
五、连铸坯的凝固组织结构是怎样的?
答:一般情况,铸坯的凝固组织结构从边缘到中心是由细小等轴晶、柱状晶带、中心等轴晶带组成。
1.细小等轴晶带:结晶器内冷却强度很大,钢液和铜壁接触时,冷却速度快,边缘形成等轴晶带。
2.柱状晶带:细小等轴晶带形成过程伴随着收缩,铸坯脱离铜壁形成气隙,降低了传热速度,铸坯形成柱状晶区。
3.中心等轴晶带:随着凝固前沿的推移,温度梯度逐渐减小,当铸坯中部液相温度降至液相线后,心部结晶开始,由于传热受到限制,晶粒较激冷区粗大。 二十
六、什么叫粘连漏钢?发生粘连漏钢的原因有哪些? 答:粘连漏钢是指结晶器弯月面的铸坯凝固壳与结晶器铜板之间无润滑液,使拉坯阻力增大,粘接处被拉断,到达结晶器下口就发生漏钢。
原因是:1)结晶器保护渣性能不良,使熔渣不易流入坯壳与铜板之间形成润滑渣膜。2)异常情况下高拉速。3)结晶器液面波动过大。 二十
七、中包开浇产生冷钢垫棒有哪些原因?
答:1.大包开浇后钢流小或滑板误操作、关闭滑板导致中包液面低。
2.大包钢水平台温低。
3.加废钢过多,吹氩不充分导致温度分层,大包底部温低。 4.中包塞棒烘烤不好。
5.虽然为合格温度钢水,但氩后至开浇时间太长。 6.中包开浇钢流太小,出苗时间长。
二十八、为什么水口容易发生堵塞,怎么解决? 答:水口容易发生堵塞的原因是:
1、钢水温度低、水口未烘烤好,钢水冷凝。这种情况容易发生水口冻死。适当提高钢水温度,加强水口烘烤可以解决。
2、钢中Al2O3含量过高,附着在水口内壁,使水口变窄乃至堵塞,控制钢中的含铝量可以解决。
二十九、铸坯纵裂产生的原因?
答:1.水口与结晶器不对中,使结晶器内钢水偏流;
2.保护渣性能不良; 3.结晶器液面波动; 4.钢水硫磷含量高。
5.浇铸温度及拉速不合理.6.结晶器铜板不光洁或有划痕,造成结晶器内热流密度不均匀。
7.水口的倾角与插入深度不合理,造成注流对坯壳冲刷,影响坯壳均匀生长。 三
十、什么是结晶器非正弦振动,有什么优点?
答:结晶器非正弦振动是结晶器在振动时,其位移量在与正弦振动相同值的前提下,使结晶器上升具有比下降时间更长的振动波形,该波形有利于保护渣的消耗。
结晶器非正弦振动波形使正滑脱时间增长,负滑脱时间减少,减少拉坯阻力,增加保护渣的消耗量,增加铸坯与结晶器的润滑,减少漏钢。
三十
一、当铸中发现铸坯纵裂严重时,应采取哪些措施?
答:1.检查中包水口是否对中,插入深度是否合理,以及水口是否穿孔。
2.保护渣是否化渣良好,若不好及时换渣。 3.检查钢水磷和硫含量是否正常。
4.拉速是否匹配,核对测温值是否准确。 5.结晶器水是否按要求控制 6.〔C〕含量是否在包晶区
7.加稀土位置和速度是否合要求。
8.在采取以上措施仍得不到解决则停机检查设备。 三十
二、影响结晶器液位控制有哪些因素? 答:1.中间包滑板或浸入式水口吹Ar量太大; 2.为避免水口堵塞的冲棒;
3.拉速变化频繁,造成液面波动大;
4.浸入式水口堵塞造成偏流引起液面波动。 5.自动控制液面检测器发生故障或操作不当; 6.结晶器内钢水偏流; 7.扇形段开口度不良。
三十
三、在浇注过程中是如何进行全程保护浇注的?
答:在浇铸过程中采用保护浇铸技术,是改善铸坯质量的重要措施。包括四方面:
1.大包-中包之间有长水口加上Ar封的保护浇注; 2.中包钢液面上有中包保护渣,防止钢水氧化; 3.中包-结晶器之间采用侵入式水口;
4.结晶器钢液面有结晶器保护渣;隔开钢水与空气。 三十
四、如何进行氧管切割点火操作? 答:首先要将氧管头部用可然体预热到一定温度,从而使氧管发生燃烧反应,产生高温熔渣,将氧管熔渣滴流在被切割体表面,使之被加热达到点火温度,一旦被切割体产生氧化反应,便已着火。
三十
五、哪些情况必须进行平台测温? 答:1 无精炼后温度或精炼后温度不合格。
2 精炼结束至大包开浇> 20分钟,平台测温至开浇> 15分钟。 3开浇第一炉和换中包第一炉。
三十
六、连铸为什么要对钢水浇铸温度作严格控制?
答:1.合适的浇铸温度是顺利连铸的前提。如:浇铸温度过低,将会造成中包水口堵塞,迫使浇铸中断;如果太高,不但容易引起塞棒、水口侵蚀,而且会使坯壳减薄和厚度不均,造成漏钢。
2.合适的浇铸温度又是获得良好铸坯质量的基础。理论和实践都表面,注温偏高,会加剧钢水的二次氧化及钢水对包衬耐火材料的侵蚀,从而是铸坯中非金属夹杂物增多,还会助长鼓肚、内裂、中心疏松和偏析等多种缺陷的产生。而注温偏低,易使结晶器内钢液处形成冷壳,恶化铸坯的表面质量,并且会给钢的纯净度带来不良影响。 三十
七、旋转塔旋转的七个条件是什么?
答:① 变频器接通。 ②齿轮润滑开。 ③抱闸开。
④ 锁紧装置打开。 ⑤小齿轮连接。 ⑥ARM 1&2在顶部位置。 ⑦ 空气压力正常。
三十
八、在连铸生产中,保护渣的主要作用是什么? 答:
1、绝热保温防止散热。
2、隔开空气防止二次氧化,保证钢的质量。
3、吸收钢水中上浮夹杂物。
4、在结晶器壁与凝固壳之间形成一层渣膜,起润滑作用,减少拉坯阻力,防止坯壳与结晶器壁的粘结。
5、充填坯壳与结晶器之间的气隙,改善结晶器传热。 三十
九、拉矫机启动后0~5S时间内自动执行哪些功能?
答:1)浇铸时间开始启动。
2)结晶器水阀锁定于打开位置。
3)结晶器振动启动。
4)烟气风机启动。
5)跟踪系统开始记数。
6)切割Ⅰ、Ⅱ、Ⅲ组辊在2HZ频率速度下工作。
7)0~5S延时后,喷淋水切断1打开。
8)主风机启动。 四
十、“送引锭”状态与“浇铸结束+送引锭”状态要求的条件有何不同?
答:1)浇铸结束+送引锭,不要求扇形段处于原始位置,只要求浇
铸结束后拉坯长度大于16米,而“送引锭”状态要求扇形段处于原始位置。
2)浇铸结束+送引锭,不要求喷淋水全部关闭,只要求弧形段
的水阀关闭,“送引锭”状态要求喷淋水全部关闭。
四十
一、假设:因跟踪系统的记数故障,在“浇铸结束+送引锭”状态下已送完引锭,而铸坯未拉出(显示已拉出),应如何操作?
答:①将状态选为手动,在P400以P2压力压下部分驱动辊。
②调出直流变频器画面,选择EMERGENCY。 ③打开BAR A或BAR B。
④由P400拉出铸坯,抬起驱动辊(直线段)。 ⑤关闭BAR A或BAR B。
⑥将状态选为手动、送引锭准备。 ⑤ 通知电工将状态改为送引锭状态。
四十
二、结晶器锥度为什么要调整?
答:结晶器内热的传递路线是:钢水→坯壳→渣衣→气隙→铜板→冷却水带去热量。其中最大障碍是气隙,所以锥度调整是关键。锥度过小,由于铸坯收缩,气隙过大,在整个结晶器内坯壳得不到很好冷却。相应部位坯壳变薄,出结晶器后,由于钢水静压力产生侧面鼓肚,严重时造成漏钢。这就是裂纹性漏钢。锥度过大,气隙过小,拉坯阻力较大,严重也可能造成漏钢的危险。所以锥度一定要按规定调整。
四十
三、实现热装和直接轧制的技术关键有哪些?
答:为了实施热装和直接轧制,必须解决的关键技术问题有:
1.无缺陷铸坯的生产技术,包括防止铸坯表面缺陷和内部缺陷的一系列措施以及热态下铸坯质量的检测技术;
2.高温铸坯的生产技术,包括铸坯保温,液芯复热、铸坯快速运送和补偿加热等; 3.提高直送率的技术,使各工序协调匹配,稳定均衡,有节奏地连续生产。 四十
四、我厂主要轧后废有哪些?:
答:硅钢厂的结疤、分层、气泡、夹杂。主要为结疤:分析原因主要是铸坯表面“冷痣”、异物压入。
轧板厂的裂纹;边裂,纵裂,分析主要原坯上有裂纹(氧化)原点。
冷轧厂的夹杂,主要集中在IF、WYK、低碳深冲钢;特点主要是线状,不连续夹杂。 四十
五、保护浇铸操作步骤?
答:1.钢包和中包车到浇注位后,手动调节使长水口对准大包下水口。
2.把手动液压阀打到升位,机械手上升,长水口与大包下水口压紧调正后,锁紧机械手。 3.浇完一炉后,升起回转臂的同时,把手动液压阀打到下降位,机械手下降,长水口与大包下水口脱开,把手动液压阀打到中间停止位,机械手停止下降。 4.用氧气清理干净里面的残钢后放入石棉垫圈。
5.下一炉开浇,观察钢水从长水口流出后,将浇注位回转臂降至低位。 四十
六、旋转塔传动、升降系统的检查内容?
答:1检查旋转塔旋转(正、反转)、升降是否平稳有无异响,速度正常,在浇注位停止是否在范围内。
2检查大包操作台按钮及指示灯是否正常,紧急停止按钮是否处于释放状态 3铸机检修后应检查事故紧急旋转是否正常和事故位是否在事故大罐上方。 4 检查大包加盖机构的回转、升降是否正常;检查大包盖耐火材料状况,大包盖的位置是否合适。 四十
七、大包不能自开的情况下,应如何操作?
答:1 当已安装好保护管的大包不能自开时,需对大包滑动水口进行引流。 2 提升大包将保护管取下并把大包保护管移到大包浇铸孔侧面位置。 3 把大包滑板完全打开,用氧管对大包进行引流,小氧掏砂,边往里伸边抖动,使结块的引流砂下来后,再开大氧烧冷钢。引流时一人烧氧,一人开关阀门,两人要配合好,防止氧气回火伤人。引流时不要烧坏滑动水口机构。
4在引流过程中,应适当降低浇注速度(在规定范围内),以防止中包下渣。 5 引开钢流后,应及时关闭钢包滑板,并将保护管旋转到浇注位,安装上保护管,重新打开滑板进行正常浇注。
四十
八、如何安装浸入式快换水口?
答:1 检查液压缸及其部件是否漏油,转动是否灵活,活塞杆无裂纹、无变形,
2检查滑动水口机构安装情况,重点检查下滑板表面是否平整,表面不能粘有异物,否则应清除;
3检查浸入式水口滑道内有无异常;
4检查导向板、盲板无粘钢、破损、变形,表面平整,尺寸符合要求。
5将滑板液压油缸安装固定好,进行中包滑板试滑,能全程灵活控制,无卡阻现象。
6试滑滑板正常后,准备好浸入式水口(应检查水口上表面,如发现有裂纹或不平整,不能安装使用)、导向板、石棉保温筒。
7 把中包升到合适高度,安装快换油缸,注意固定销要固定到位。 8 先安装导向板,然后安装中包浸入式水口,安装浸入式水口要轻拿轻放,防止水口受损伤。安装时不得使用盲板导向。水口到位后,安装盲板。安装的每一步必须确保快换油缸接手挂紧到位,防止未挂紧造成油缸连杆顶弯。 9 水口安装完毕后,套上水口石棉保温筒,石棉保温筒破损不得使用。然后落中包至最低位,进行水口对中。
四十
九、添加保护渣注意的事项?
答:1.添加保护渣要勤加、少加、均匀加,渣厚度控制在30-50mm左右,液渣厚度8—15mm;2.当浇铸过程中,保护渣变粘、结团或烧氧后,应降低铸机拉速后再换渣(降两档左右);3.换新渣时用新渣扒沿熔渣面走,不要粘钢,一边捞渣,一边马上推入新渣,换渣完毕待渣熔化正常后调至正常拉速;
4.换渣尽可能选择在每炉钢浇铸中期的高温区进行,调拉速要求缓慢均匀。 5.浇铸过程中不应用渣钩在结晶器内大面积搅动,要检查渣的状况,可采用渣钩“点动”进行,检查熔渣粘度及化渣情况,发现大的渣条、圈,应随时挑出; 6.当保护渣结块、结团、明显受潮时,不得用于结晶器。 五
十、结晶器无振动的处理措施?
1开浇或铸中结晶器无振动或振动停止,关闭中包滑板,迅速将拉速降为0.25m/min。 2通知中控与电气室联系,通知结晶器无振动,并进行处理。同时通知P30控制中包钢水量。中控、P300此时注意检查振动信号及参数是否正常。
3停振时间超过3min,停止浇铸进行封顶;若正常,确认铸坯交接部位通过结晶器下口后,再开始升速,按开浇要求进行控制。
4中控操作工在停振后进行漏钢预报曲线监控。 论述题:
一、简述水口快换操作步骤? 答:1确认用于快换的水口烘烤正常。 2准备好快换水口气动夹,并通气试用;准备好快换水口小车、上下盲板专用工具、捞渣扒等。
3打开快换机械接手,取下盲板,同时降低拉速至0.6m/min,同时调整氩气流量。并把烘烤好的水口推至结晶器盖板旁边。
4把水口轻放在快换水口小车上,适当抬高中包小车,调整好角度,把水口插入滑道,确认到位后,挂上快换机械接手,确认接手挂好后,按下操作面板 “FIRE” 开关进行快换(此时绿灯长亮),换完后,把夹子夹在旧水口上将旧水口取出结晶器。注意过程动作要轻,不要损坏水口和接触结晶器铜板。
5降下中间包至标准位。水口换完后,待液面平稳后清理结晶器内的渣条并进行换渣操作,换完渣后,打开机械接手,上好盲板,然后比照开浇升速缓慢升速、调节氩气流量。
二、简述3#结晶器在线调宽的操作? 答:1如需进行结晶器在线调宽,按中控通知选择调宽方式:选择二级机方式调宽时,由二级机完成调宽,选择一级机方式调宽时,由中控一级机完成调宽。
2开始调宽时将拉速降至1m/min。调宽前4米,在结晶器调节操作箱LC221上将显示调宽相关信息,结晶器调节操作箱LC221上Adj.Start〔K9〕灯闪烁。调宽过程中,结晶器调节操作箱LC221上Adj.Start〔K9〕灯和结晶器打开〔K12〕灯常亮。 3在结晶器调宽结束后,结晶器调节操作箱LC221上Adj.Start〔K9〕和结晶器打开〔K12〕灯熄灭,结晶器夹紧〔K11〕灯亮,结晶器调节操作箱LC221上调宽相关信息自动清除。接到中控调宽完毕信息后,将结晶器调宽操作模式设定为“远程自动”(AUTO OPERATOR)模式。
4调宽操作结束(即拉速为1m/min)时,不要立即升拉速,应对结晶器液面及渣况等进行确认,发现渣况不良如结团等异常情况时,进行换渣操作。
三、简述3#开浇升速过程?并画出开浇升速曲线?
答:启动拉矫机自动升速到0.4m/min,稳30秒;再按0.2m/min2的加速度升速到0.8m/min,稳90秒;再按0.2 m/min2的加速度升速至典型拉速。
开浇升速曲线1.201.000.800.600.400.200.00020406080100120140160180200220240260280300
四、如何预防粘连漏钢?
答:⑴严格按技术要求使用结晶器保护渣,禁止随意代用;
⑵监护保护渣的使用状况,确保保护渣性能良好,无结团现象,无大的渣条出现,熔化速度正常,液渣层厚度保持在8——12mm,渣层总厚度控制在30mm左右, ⑶挑渣条时,一是注意不要破坏初生的坯壳;二是要降速0.1—0.2m/min。 ⑷若遇渣条不断的出现时,则可能是保护渣成份性能有异常而造成的,应马上更换新渣。 ⑸换渣应注意以下几点原则:一是尽量在高温阶段换渣;二是拉速降低0.1—0.2m/min;三是两人配合捞旧渣,边换新渣,等水口一侧换完之后再换另一侧;四是换渣动作要轻缓,换渣注意只捞粗渣,不宜过度,此外,换完旧渣后,应先将拉速稳定2min后才缓慢升速。
⑹浇喂稀土钢喂丝时导管必须在水口两侧交替进行,一炉一换,喂丝位置为距水口100-150mm处,稀土丝质量不佳时必须立即更换; ⑺确保合适的拉速,拉速变化幅度要小。
五、我厂质量异议主要有哪两类?特征及产生的原因? 答:1.分层:
特征:钢板内部或断面上出现分离层,有时在分层的缝隙中有肉眼可见的夹杂物。分层在边缘时,一张钢板明显成二层板,在中部时,会出现小波纹或小鼓包,钢板冲压时分离层分开。
原因:
1、轧制头、尾未切尽(此情况异议量较小)。
2、内裂轧制未焊合,中心偏析严重。
3、非金属夹杂、气体集中分布。 2.表面夹杂: 特征::在钢板表面呈现点状、块状或条状的非金属夹杂物(耐火材料、保护渣、AL2O3),沿轧制方向间断或连续分布。 原因:
1、钢中非金属夹杂物。
2、注中保护渣带入。
3、耐材带入等。
六、中间包水口插入深度控制原则?
答:中间包水口控制原则:保证结晶器液面无大的翻动或过死、液面无冷钢,结晶器流场环流正常。
1.开浇时中包水口插入深度控制在低位,开浇正常后提升水口至标准范围; 2.正常浇铸过程中,温低时水口插入深度宜浅。
3.浇铸过程中调整水口插入深度时,注意升降幅度不得过大,每次调整幅度不要超过20mm,可分段调整。
七、3#机免烘烤水口使用操作要求?
答:1正常情况下如炉数较多时,需进行水口快换时使用正常水口烘烤后快换。 2异常情况下未准备备用烘烤水口(如水口断、穿、裂、吊底等),可使用免烘烤水口。 3免烘烤水口必须离线烘烤5—10分钟以烘干水分后再进行快换;换操作同正常水口。 4快换完后注意水口周围是否有冷钢存在,并进行处理。
5快换完后立即准备正常水口进行烘烤,烘烤达到要求后再次进行快换。 6免烘烤水口寿命较短,浇铸炉数只有1—2炉,不得长时间浇铸。
八、中包涂抹料的烘烤操作 1中包配上浇钢平台后检查包盖完好、中包内无异物,无垮料等现象。
2中包配上中包车后,无计划不允许烘烤,中包烘烤器严禁有明火,等到厂调下计划时和浸入式水口同步大火烘烤,烘烤时间原则上控制在60—90分钟,不得小于60分钟 3大火火焰:煤气火焰打到包底后反弹至中包高度的一半以上,中包包沿以下,不允许煤气火焰高于中包盖。
4烘烤过程中检查涂料烘烤状况和开浇管状况。
5开浇前检查涂料烘烤状况,若发现涂料烘烤垮,面积≥0.5m,可见永久层时,安排换包。对烘烤中出现裂纹时,可使用;对烘烤中局部鼓胀,涂料上部与永久层分离,可使用;若发现开浇管烘烤破或熔化使水口通道变窄,必须更换中包。
6开浇管涂料中包大火烘烤超过1.5小时仍不能开浇必须改中火烘烤。中火指:加风后,煤气火焰打到包底不反弹,最长烘烤时间(大火烘烤至开浇时间)≤720min,烘烤超时必须更换。
九、
1、2#机浇铸结束操作及注意事项 4.1大包浇完后,浇铸中包剩余钢水。
4.2待中包钢水为20吨左右时,两流拉速降为1m/min 4.3待中包钢水为15吨左右时,两流拉速降为0.8m/min 4.4待中包钢水为10吨左右时,两流拉速降为0.6-0.8m/min 4.5待中包钢水≤8吨后,应将拉速控制在0.6-0.8m/min,进行捞渣操作(尽量少捞渣),关闭中包滑板,按下“浇铸结束”按钮。
4.6用氧管轻轻搅动钢液面,当坯壳露出后即可停止搅动,同时尽量不使钢水暴露。 4.7以0.3m/min2的升速速度平稳地提升铸机拉速,可将拉速升至正常拉速的120-130%。 4.8如尾坯上涨,则将铸机拉速回零,采用辅助手段使之完全凝固后,方可拉坯。 注意事项:
1、尾坯上涨,严禁尾坯出结晶器。
2、封顶后,在保证正常浇铸情况下尽量在最短时间内升速,避免低拉速时间过长。
3、升速、降速过程中应均匀、平稳。
4、封顶时如必须打水,应先停机,直到尾坯内部水被蒸发干后才能在此启动拉矫机;同时打水应打在结晶器铜板上,打水时绝不允许搅动液面,液面晃动或波动时不允许打水。打水时应注意站位,注意安全。
十、大包位置及称重故障的处理方式?
答:1.大包位置及称重信号出现故障,易造成铸机开浇不能投入二级机,或铸中炉次数据不能自动更新采集,应采取人工模拟信号的方式来解决,特别是浇次首炉开浇前。在二级机“浇铸”画面按“视图”→“紧急情况”进入铸机模拟画面;
2.大包到位信号故障,单击“旋转台”→“位置”选项,绿色方块变红,则进入大包位置仿真模拟状态、此时在中间操作区域可根据大包实际位置状况将选定的大包臂人工“旋转”至浇铸位或坐包位;
23.大包称重故障时,哪个臂有问题,点击哪个臂,使变红,钢水坐上旋转塔,点“坐包”,输入重量、皮重,确认炉次、计划、钢种等,转到浇注位后,中包称重如正常,随中包重量的增加,大包可以自动开浇(如不能自动开浇,降低大包钢水重量或按中包称重故障处理)。大包浇完后,转至接收位,点相应臂的“卸载”。
第三炼钢厂:杨新泉 2006年10月26日
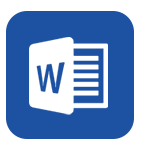