前 言
毕业设计是学生在学校完成了大学四年的全部课程,并在进行了生产实习的基础上进行的一个教学环节,也是学生在校学习阶段的最后一个重要的教学环节,是完成工程师基本训练的一个必不可少的过程。通过毕业设计培养学生综合运用所学知识独立解决本专业一般工程技术问题的能力,树立正确的设计思想和工作作风。
毕业设计是在毕业实习的基础上进行的,根据自己的设计课题,在毕业实习期间认真调查研究、搜索资料。
本次设计是提高CA6140车床上拨叉的加工效率,设计正确的加工工艺路线,以及某道工序的夹具。这次设计涉及到机床,机械加工工艺,工装夹具等机制专业的几乎所有的专业基础知识。是一次全面地,系统地检查自己在大学期间对专业知识学习的情况,在整个设计过程中做到严谨认真,一丝不苟的精神,尽量使自己的设计达到理想的水平,通过独立的查找资料,分析,计算完成方案设计,图纸设计和编写技术文件等,设计了这套比较完整的加工工艺路线,使自己对机制专业有了更深刻的认识。
由于时间短促,经验不足以及水平有限,本次设计难免许多不妥和错误之处,敬请批评指正,以便及时改正。
1.零件分析
1.1 零件的作用
题所给的是CA6140车床上的拨叉,它位于车床变速机构中,主要起换挡作用,使主轴回转运动按照工作者的要求工作,获得所需的速度和扭矩。零件上方的Φ20mm的孔与操作机构相连,下方的Ф50mm的半孔则是用于与所控制齿轮所在的轴接触,通过上方的力拨动下方的齿轮变速,两零件铸造为一体,加工时分开。
1.2 零件的工艺分析
CA6140车床上的拨叉共有两处加工表面。其间有一定的位置要求,分述如下: 1.2.1 以Ф20mm为中心的加工表面
这一组加工表面包括:Ф20mm的孔,以及其上下表面,孔壁上有一个装配时要钻铰的Ф8mm的锥孔,一个M6的螺纹孔,和一个缺口。 1.2.2 以Ф50mm为中心的加工表面
这一组加工表面包括:Ф50mm的孔,以及其上、下端面; 这两组表面有一定的位置要求;
(1) Ф50mm的孔的上、下表面与Ф20的孔的垂直度误差为0.07mm。 (2) Ф20mm的孔的上、下表面与Ф20的孔的垂直度误差为0.05mm。
(3) Ф50mm、Ф20mm的孔的上、下表面以及Ф50mm的孔的内表面的粗糙度误差为3.2um。
(4) Ф20mm的孔的内表面的粗糙度误差为1.6um,精度为IT7。
2.工艺规程设计
2.1 毛坯的制造形式
零件材料为HT200,考虑零件在机床运行过程中所受冲击不大,零件结构又比较简单,故
选
择
铸
件
毛
坯
。
图一 毛坯图
2.2 基准面的选择
2.2.1 粗基准的选择 对零件而言,尽可能选择不加工表面为粗基准,而对若干个不加工表面的工件,则应以与加工表面要求相对位置精度较高的不加工表面作粗基准,根据这个基准原则,现取Ф20mm的孔的不加工外轮廓表面作为粗基准,利用一组共两个短V形块支承两个Ф20mm孔的外轮廓作主要定位面,以消除3个自由度,再用一个支承板支撑在Ф72mm的上表面,以消除3个自由度。
2.2.2 精基准的选择 主要应考虑基准重合问题。当设计基准不重合时,应该进行尺寸换算,这在以后还要专门计算,此处不再重复。
2.3 制定工艺路线
制定工艺路线的出发点,应当是使零件的几何形状、尺寸精度及位置精度等技术要求能得到合理的保证。在生产纲领已确定为中批生产的条件下,可以考虑采用万能性机床配以专用夹具,并尽量使工序集中来提高生产率。除此以外,还应当考虑经济效果,以便使生产成本尽量下降。
1、工艺路线方案一:
工序一:退火
工序二:粗、精铣Ф20 mm、Ф50 mm的下表面,保证其粗糙度为3.2 um 工序三:以Ф20 mm的下表面为精基准,粗、精铣Ф20 mm的孔的上表面,保证其粗糙度为3.2 um,其上、下表面尺寸为30mm,
工序四:以Ф20 mm 的下表面为精基准,钻、扩、铰、精铰Ф20 mm的孔,保证其内表面粗糙度为1.6 um,垂直度误差不超过0.05mm 工序五:以Ф20 mm的下表面为精基准,粗、半精镗Ф50 mm的孔,保证其内表面粗糙度为3.2 um 工序六;以Ф20 mm的下表面为精基准,粗、精铣Ф50 mm的上表面,保证其与孔的垂直度误差不超过0.07mm,其上、下表面尺寸为12mm 工序七:铣断
工序八:以Ф20 mm的孔为精基准,钻Ф8 mm的锥孔的一半Ф4 mm,装配时钻铰
工序九:以Ф20mm的孔为精基准,钻Ф5mm的孔,攻M6的螺纹
工序十:以Ф20 mm的孔为精基准,铣缺口,保证其粗糙度为12.5um 工序十一:检查
上面的工序可以是中批生产,但是其效率不高,并且工序四中的钻孔方法在钻孔是可能会偏离中心。经综合考虑,采用下面的方案二。
工艺路线方案二:
工序一;退火
工序二:粗、精铣Ф20 mm、Ф50 mm的下表面,保证其粗糙度为3.2 um 工序三:以Ф20 mm的下表面为精基准,粗、精铣Ф20 mm、Ф50 mm的孔的上表面,保证其粗糙度为3.2 um,Ф20 mm的上、下表面尺寸为30mm,Ф50 mm的上、下表面尺寸为12mm 工序四:以Ф20 mm 的下表面为精基准,钻、扩、铰、精铰Ф2 0 mm的孔,保证其内表面粗糙度为1.6 um,垂直度误差不超过0.05 mm 工序五:以Ф20 mm 的下表面为精基准,粗、半精镗Ф50 mm的孔,保证其
内表面粗糙度为3.2 um 工序六:铣断
工序七:以Ф20 mm的孔为精基准,钻Ф8 mm的锥孔的一半Ф4 mm,装配时钻铰
工序八:以Ф20 mm的孔为精基准,钻Ф5 mm的孔,攻M6的螺纹
工序九:以Ф20 mm的孔为精基准,铣缺口,保证其粗糙度为12.5 um 工序十:检查
2.4 机械加工余量、工序尺寸及毛坯尺寸的确定
“CA6140车床拨叉”零件的材料为HT200硬度为190~210HB,毛坯重量为2.2Kg,生产类型为中批量,铸件毛坯。又由>(以下称〈〈工艺手册〉〉表1.3-1查得毛坯的制造方法采用壳模铸造级,表2.2-4查得加工余量等级为G级,选取尺寸公差等级为CT10。
根据以上资料及路线,分别确定各加工表面的机械加工余量、工序尺寸及毛坯如下:
1、延轴线方向长度方向的加工余量及公差(Ф20mm、Ф50mm端面) 查《工艺手册》表2.2~4取Ф20mm、Ф50mm端面长度余量为2.5mm(均为双边加工)。 铣削加工余量为:a)粗铣:1.5mm b)精铣:1mm 毛坯尺寸及公差为:(35土0.3)mm ( 17土0.25)mm
2、内孔(Ф50mm已铸成孔)查《工艺手册》表2.2~2.5,取Ф50mm已铸成长度余量为3mm,即已铸成孔Ф44mm。
镗削加工余量为:a)粗镗:2mm b)半精镗:1mm
0.50毛坯尺寸及公差为:(48土0.3)mm (500.25)mm
3、其他尺寸直接铸造得到。
2.5 确定切削用量及基本工时
2.5.1 工序二:粗、精铣孔Ф20mm、Ф50mm的下表面
(1) 加工条件
工件材料:HT200。бb=0.16GPa HBS=190~210,铸件 机床:XA5032立式铣床
刀具;W18Cr4V硬质合金端铣刀
W18Cr4V硬质合金端铣刀,牌号为YG6,由《切削用量简明手册》〉后称《切削手册》表3.1查得铣削宽度ae
o手册》表3.2选择刀具的前角ro=+5o;后角ao=8o;副后角a’o=8,刀齿斜角λs=-10,主刃Kr=60o,过渡刃Krε=30o,副刃Kr’=5o,过渡刃宽bε=1mm
(2) 切削用量
1)粗铣Ф20mm的下表面
a)切削深度 因切削用量较小,故可以选择ap=1.5mm,一次走刀即可完成所需尺寸。 b)每齿进给量:由《切削手册》表3.30可知机床的功为7.5KW,查《切削手册》表3.5可得f=0.14~0.24mm/z,由于是对称铣,选较小量f=0.14mm/z c)查后刀面最大磨损及寿命
查《切削手册》表3.7,后刀面最大磨损为(1.0~1.5)mm 查《切削手册》表3.8, 寿命T=180min d)计算切削速度 按《切削手册》表3.27中的公式:
vccvdoqvkmprv
Tapxvfzyvuvaez也可以由表3.16查得vc=98mm/s n=439r/min vf =490mm/s 又根据XA5032铣床参数,选 n=475r/min vf =600mm/s,则实际的切削速度为:
doncvc
1000
即vc=3.1480475=119.3m/min,实际进给量为:
1000fzv即fzv=
vfcncz
600=0.13mm/z 47510e)校验机床功率 查《切削手册》表3.24,Pcc=1.1KW,而机床所提供的功率Pcm为1.7KW,所以Pcm> Pcc,故校验合格。
最终确定ap=1.5mm nc=475r/min vfc=600mm/min vc=119.3m/min fz=0.13mm/z f)计算基本工时
tmL Vf公式中: L=l+y+Δ;根据《切削手册》表3.26,可得 l+Δ=12mm,所以L=l+y+Δ=32+12=44mm 故 tm=44/600=0.073min 2)粗铣Ф50mm的下表面
a)铣削Ф50mm的下表面与铣削Ф20mm的下表面的相关参数及其用量等都相同。即
ap=1.5mm nc=475r/min vfc=600mm/s vc=119.3m/min fz=0.13mm/z b)计算基本工时
tmL Vf公式中: L=l+y+Δ;根据《切削手册》表3.26,可得 l+Δ=0所以L=l+y+Δ=72mm 故 tm=72/600=0.12min 3)精铣孔Ф20mm的下表面
a) 切削深度 因切削用量较小,故可以选择ap=1.0mm, 一次走刀即可完成所需尺寸 b)每齿进给量:由《切削手册》表3.30可知机床的功为7.5KW,查《切削手册》表3.5可得f=0.5~0.7mm/r,由于是对称铣,选较小量f=0.7mm/r c)查后刀面最大磨损及寿命
查《切削手册》表3.7,后刀面最大磨损为(1.0~1.5)mm 查《切削手册》表3.8, 寿命T=180min d)计算切削速度 按《切削手册》表3.27中的公式:
cvdoqvvcmkprv
Tapxvfzyvuvaez也可以由表3.16查得vc=124mm/s vf =395mm/min n=494r/min,根据XA5032铣床参数,选 n=475r/min vf =375mm/min , 则实际的切削速度为
doncvc
10003.1480475所以vc==119.3m/min,实际进给量
1000fzv所以fzv= 375=0.08mm/z 47510vfcncz
e)校验机床功率 查《切削手册》表3.24,Pcc=1.1KW,而机床所提供的功率Pcm为1.7KW,所以Pcm> Pcc,故校验合格。
最终确定ap=1.0mm nc=475r/min vfc=375mm/min vc=119.3mm/min f)计算基本工时
tmL Vf6
公式中: L=l+y+Δ;根据《切削手册》表3.26,可得 l+Δ=80mm, 所以L=l+y+Δ=32+80=112mm 故 tm=112/375=0.3min 2)精铣Ф50mm的下表面
a)铣削Ф50mm的下表面与铣削Ф20mm的下表面的相关参数及其用量等都相同。即 ap=1.0mm nc=475r/min vfc=375mm/min vc=119.3mm/m b)计算基本工时
tmL Vf公式中: L=l+y+Δ;根据〈〈切削手册〉〉表3.26,可得 l+Δ=80mm所以L=l+y+Δ=72+80=152mm 故 tmL=152/375=0.405min Vf2.5.2 工序三:粗、精铣孔Ф20mm、Ф50mm的上表面
本工序的切削用量及基本工时与工序一中的粗、精铣孔Ф20mm、Ф50mm的下表面相同。
2.5.3 工序四:钻、扩、铰、精铰Ф20mm的孔
(一) 钻Ф18mm的孔 (1)加工条件
工艺要求:孔径d=18mm, 孔深l=30mm,通孔 ,用乳化液冷却
机床 :Z535型立式钻床
刀具 :高速钢麻花钻头
选择高速钢麻花钻头,其直径do=18mm,钻头几何形状为:由《切削手册》表2.1及表2.2 选修磨横刃,β=28o αo=10o 2Φ=118o 2Φ1=70o bε=3.5mm b=2mm l=4mm (2) 切削用量 1) 决定进给量f a)、按加工要求决定进给量 根据《切削手册》表2.7,当铸铁的强度 бb
给机构允许的轴向力为11760N(Z535钻床允许的轴向力为15696N(见《工艺设计手册》表4.2-14)时,进给量为1.5mm/r。
从以上三个进给量比较可以看出,受限制的进给量是工艺要求,其值为f=0.70~0.86mm/r,根据Z535钻床说明书,选f=0.80mm/r(见《工艺设计手册》表4.2-16),又由《切削手册》表2.19可以查出钻孔时的轴向力,当f=0.80mm/r do
由《切削手册》表2.12,当do
n1000V do
100014.4=255r/min 3.1418根据Z535钻床说明书,可考虑选择nc=275r/min(见《工艺设计手册》表4.2-15) 所以n=4)检验机床扭转及功率
根据《切削手册》表2.21,当f Mc
又根据《切削手册》表2.23,当бb=(170~213)MPa
do
tmL nf8
L=l+y+Δ 由《切削手册》表2.29查得y+Δ=9mm 309故 tm=0.18min 2750.8
(二) 扩Ф19.8mm的孔 (1)加工条件
工艺要求:孔径d=19.8mm, 孔深l=30mm,通孔 ,用乳化液冷却
机床 :Z535型立式钻床
刀具 :高速钢扩孔钻头
选择高速钢扩孔钻头,其直径do=19.8mm,钻头几何形状为:由《切削手册》表2.5 ro=18o ao=10o kr=60o krε=30o β=15o ba1=1mm (2) 切削用量 1) 决定进给量f a)、按加工要求决定进给量 根据《切削手册》表2.10,当铸铁的强度 бb200HBS
do=19.8mm时,f=(0.9~1.1)mm/r 由于L/d=30/19.8=1.52 因扩孔之后还须铰孔 ,故取修正系数K=0.7 所以 f=(0.9~1.1)x0.7=(0.63~0.77)mm/r b) 按钻头强度决定进给量 根据表2.8,当бb=190MPa,do=19.8mm,钻头强度允许的进给量f=1.75mm/r c)按机床进给机构强度决定进给量 根据表2.9,当бb210MPa,do20.5mm,机床进给机构允许的轴向力为11760N(Z535钻床允许的轴向力为15696N(见《工艺设计手册》表4.2-14)时,进给量为1.5mm/r。
从以上三个进给量比较可以看出,受限制的进给量是工艺要求,其值为f=(0.63~0.77)mm/r,根据Z535钻床说明书,选f=0.64mm/r(见《工艺设计手册》表4.2-16),又由《切削手册》表2.19可以查出钻孔时的轴向力,当f=0.64mm/r do
由《切削手册》表2.12,当do
cvdozvvcmxvTapfyvkv
可知f=0.64mm/r时, do=19.8 mm时,Vt=27m/min 切削速度的修正系数由《切削手册》表2.31可知 Ktv=1.0 Kmv=1.0 KTv=1.0 Klv=0.85 所以 V=VtxKv=27x1.0x1.0x1.0x0.85=23m/min
n1000V don=100023=370r/min 3.1419.8根据Z535钻床说明书,可考虑选择nc=375r/min(见《工艺设计手册》表4.2-15) 4)检验机床扭转及功率
根据《切削手册》表2.21,当f Mc
又根据《切削手册》表2.23,当бb=(170~213)MPa do
tm L=l+y+Δ 由《切削手册》表2.29查得y+Δ=10mm 3010故 tm=0.13min 3750.8(三) 粗铰Ф19.94mm的孔 (1)加工条件
工艺要求:孔径d=19.94mm, 孔深l=30mm,通孔
机床 :Z535型立式钻床
刀具 :高速钢铰刀
L nf 选择高速钢铰刀,其直径do=19.94mm,钻头几何形状为:由《切削手册》表2.6 ro=18o ao=10o kr=60o krε=30o β=15o ba1=1mm (2) 切削用量 1) 决定进给量f 根据《切削手册》表2.11,当铸铁的强度
б
b
170HBS
do=19.94mm时,f=(1.0~2.0)mm/r,又由于粗铰之后还要精铰,所以应该选最大的进给量 即 f=2.0mm/r
2)决定钻头的磨钝标准及寿命
由《切削手册》表2.12,当do
cvdozvvcmxvTapf可知,vc=7.7m/min 切削速度的修正系数由《切削手册》表2.31可知 Ktv=1.0 Kmv=1.0 KTv=1.0 Klv=0.85 所以 V=VtxKv=7.7x1.0x1.0x1.0x0.85=6.55mm/min
nyvkv
1000V do10006.55=105r/min 3.1419.94根据Z535钻床说明书,可考虑选择nc=140r/min(见《工艺设计手册》表4.2-15) 所以n=4)检验机床扭转及功率
根据《切削手册》表2.21,当f Mc
又根据《切削手册》表2.23,当бb=(170~213)MPa
do
tm
L=l+y+Δ 由《切削手册》表2.29查得y+Δ=10mm 3010故 tm=0.14min 1402.0(四) 精铰Ф20mm的孔 (1)加工条件
L nf 工艺要求:孔径d=19.94mm, 孔深l=30mm,通孔,精度等级为IT7 机床 :Z535型立式钻床
刀具 :高速钢铰刀
选择高速钢铰刀,其直径do=20mm:钻头几何形状为:由《切削手册》表2.6 ro=0 ao=7o a1=18o (2)切削用量 1) 决定进给量f 根据《切削手册》表2.11,当铸铁的强度 бb170HBS do=20mm,加工精度要求为H7精度时,f=(1.0~2.0)mm/r,由于这是粗铰之后的精铰,所以应该选中等的进给量 即 f=1.5mm/r 2)决定钻头的磨钝标准及寿命
由《切削手册》表2.12,当do
cvdozvvcmxvTapf可知,vc=9.64m/min 切削速度的修正系数由《切削手册》表2.31可知 Ktv=1.0 Kmv=1.0 KTv=1.0 Klv=0.85 所以 V=VtxKv=9.64x1.0x1.0x0.85 x1.0=8.2m/min
nyvkv
1000V do10008.2=131r/min 3.1420根据Z535钻床说明书,可考虑选择nc=140r/min(见《工艺设计手册》表4.2-15) 所以n=4)检验机床扭转及功率
根据《切削手册》表2.21,当f
do
tm L=l+y+Δ 由《切削手册》表2.29查得y+Δ=10mm 3010故 tm=0.19min 1401.52.5.4 工序五:粗、精镗Ф50 mm的孔 (1) 粗镗Ф48mm孔 1)加工条件
工艺要求:孔径d=44mm的孔加工成d=48mm,通孔
机床 :T616镗床
刀具:YG6的硬质合金刀
L nf 刀具为YG6的硬质合金刀,且直径为20mm的圆形镗刀 (2)切削用量 a) 确定切削深度ap 4844 ap==2mm 2b) 确定进给量f 根据《切削手册》表1.5 当粗镗铸铁,镗刀直径为20mm, ap
vcvTmapxvfyvkv
其中:cv=158 xv=0.15 yv=0.40 m=0.20 T=60min KTv=1.0 Kmv=1.0 Ksv=0.8 Ktv=1.0 K= KTvx Kmvx Ksvx Ktv=1.0x1.0x0.8x1.0=0.8 1580.8=62.4m/min 所以 v0.20.156020.580.40100062.4 n=414r/min 3.1448又按T616机床上的转速 选n=370r/min d) 确定粗镗Ф48mm孔的基本时间
选镗刀的主偏角xr=45o 则 l1=3.5mm l2=4mm l=12mm l3=0 又f=0.58mm/r
n=370r/min i=1
tm3.51241=0.09min 0.58370(2)半精镗Ф50mm的孔
ll1l2l3i
nf所以tm1)加工条件
工艺要求:孔径d=48mm的孔加工成d=50mm,通孔
机床 :T616镗床
刀具:YG6的硬质合金刀
刀具为YG6的硬质合金刀,且直径为20mm的圆形镗刀 2)切削用量 e) 确定切削深度ap 5048 ap==1mm 2f) 确定进给量f 根据《切削手册》表1.5 当粗镗铸铁,镗刀直径为20mm, ap
vcvTmapxvfyvkv
其中:cv=158 xv=0.15 yv=0.40 m=0.20 T=60min KTv=1.0 Kmv=1.0 Ksv=0.8 Ktv=1.0 K= KTvx Kmvx Ksvx Ktv=1.0x1.0x0.8x1.0=0.8 1580.8=78.9m/min 所以 v0.20.150.406010.41100078.9 n=503r/min 3.1450又按T616机床上的转速 选n=370r/min h) 确定半精镗Ф50mm孔的基本时间
选镗刀的主偏角xr=45o 则 l1=3.5mm l2=4mm l=12mm l3=0 又f=0.58mm/r n=370r/min i=1
tm3.51241=0.13min 0.41370 2.5.5 工序六:铣断 tmll1l2l3i
nf1) 加工条件
工件尺寸:长72mm 深12mm 加工要求:将双体铣开
刀具: 选高速钢细齿圆锯片刀 由《工艺设计手册》表3.1-27可得,又由(《金属切削手册》第三版)表6-7 B=4mm do=160mm Z=50 d=32mm ro=10o ao=16o 2) 切削用量
a) 决定每齿进给量fz 查《切削手册》表3.4可得 fz=(0.03~0.02)x(1+40%)=(0.042~0.028)mm/z 由于是对称铣 取f=0.028mm/z b) 后刀面最大磨损及寿命
查《切削手册》表3.7后刀面最大磨损为:(0.15~0.20)mm 查《切削手册》表3.8 寿命T=150min c) 计算切削速度
按《切削手册》表3.27中的公式
vc可得vc=76.7m/min 100076.7n=153r/min 160根据XA6132铣床 选主轴转速为 n=150r/min
cvdoqvKv mpvTapxvfzyvuvaeZ所以实际的切削速度为 v=75.36 m/min 工作台每分钟进给量为: fmz=0.026x50x150=195mm/min 又根据XA6132铣床的参数,取工作台进给量为190mm/z
190则:实际的进给量为fz==0.025mm/z
50150d) 校验机床功率
由《切削手册》表3.28中的计算公式可知:
pc=Fc=
Fcv 1000yCFapxFfzFaeuFZdoqFnwFkFc
式中 CF=30 xF=1.0 yF=0.65 uF=0.83 wF=0 qF=0.83 所以计算得
FvFc=163.5N Pc=c=4.8kw
1000XA6132铣床主动电机的功率为7.5KW,故所选的切削用量可以采用 最终确定 vf=190mm/min n=150r/min v=75.36m/min e) 计算基本工时
tmL Vf公式中: L=l+y+Δ;根据《切削手册》表3.26,可得 l+Δ=0所以L=l+y+Δ=22mm 故 tmL=22/190=0.12min Vf2.5.6 工序七: 钻锥孔Ф8mm的一半Ф4mm (1)加工条件
工艺要求;孔径do=4mm ,孔深l=32mm, 通孔
机床;Z525立式钻床
刀具: 高速钢麻花钻
选择的高速钢麻花钻的直径为do=4mm 钻头的几何形状为(由《切削手册》表2.7可知
铸铁的强度头几何形状为:由《切削手册》表2.1及表2.2 选β=30o αo=16o 2Φ=118o 2Φ1=70o (2)切削用量 1) 决定进给量f a)、按加工要求决定进给量 根据《切削手册》表2.7,当铸铁的强度 бb200HBS do=4mm时,f=0.18~0.22mm/r 由于L/d=32/4=8>3,故取修正系数K=0.8 所以 f=(0.18~0.22)x0.8=(0.144~0.176) mm/r b) 按钻头强度决定进给量 根据表2.8,当бb=190MPa,do
根据表2.9,当бb210MPa,do10.2mm,机床进给机构允许的轴向力为8330N(Z525钻床允许的轴向力为8830N(见《工艺设计手册》表4.2-14)时,进给量为1.63mm/r。
从以上三个进给量比较可以看出,受限制的进给量是工艺要求,其值为f=(0.144~0.176) mm/r,根据Z525钻床说明书,选f=0.17mm/r(见《工艺设计手册》表4.2-16),又由《切削手册》表2.19可以查出钻孔时的轴向力,当f
由《切削手册》表2.12,当do
n1000V do100017=1354r/min 3.144根据Z525钻床说明书,可考虑选择nc=1360r/min(见《工艺设计手册》表4.2-15) 所以n=4)检验机床扭转及功率
根据《切削手册》表2.21,当f Mc
又根据《切削手册》表2.23,当бb=(170~213)MPa do
tmL nf L=l+y+Δ 由《切削手册》表2.29查得y+Δ=2.5mm 322.5故 tm=0.15min 13600.17
2.5.7 工序八:钻Ф5mm的孔,攻螺纹M6 (1)加工条件
工艺要求;孔径do=5mm ,孔深l=6mm, 通孔
机床;Z525立式钻床
刀具: 高速钢麻花钻
选择的高速钢麻花钻的直径为do=5mm 钻头的几何形状为(由《切削手册》表2.7可知
铸铁的强度头几何形状为:由《切削手册》表2.1及表2.2 选β=30o αo=16o 2Φ=118 2Φ1=70 (2)切削用量 1) 决定进给量f a)、按加工要求决定进给量 根据《切削手册》表2.7,当铸铁的强度 бb200HBS do=5mm时,f=0.27~0.33mm/r 由于L/d=6/5=1.2
根据表2.9,当бbo o210MPa,do10.2mm,机床进给机构允许的轴向力为8330N(Z525钻床允许的轴向力为8830N(见《工艺设计手册》表4.2-14)时,进给量为1.63mm/r。
从以上三个进给量比较可以看出,受限制的进给量是工艺要求,其值为f=(0.27~0.33) mm/r,根据Z525钻床说明书,选f=0.28mm/r(见《工艺设计手册》表4.2-16),又由《切削手册》表2.19可以查出钻孔时的轴向力,当f
由《切削手册》表2.12,当do
n1000V do100013.6=866r/min 3.145根据Z525钻床说明书,可考虑选择nc=960r/min(见《工艺设计手册》表4.2-15) 所以n=4)检验机床扭转及功率
根据《切削手册》表2.21,当f Mc
又根据《切削手册》表2.23,当бb=(170~213)MPa do
tm L=l+y+Δ 由《切削手册》表2.29查得y+Δ=2.5mm 62.5故 tm=0.03min 9600.28(2)攻M6的螺纹
由〈〈工艺设计手册〉〉表6.2-14可知
L nfLl1l2Ll1l2tmi
fnfno 其中:l1=(1~3)p l2=(2~3)p 公式中的no为丝锥或工件回程的每分钟转数(r/min); i为使用丝锥的数量;n 为丝锥或工件每分钟转数(r/min);d为螺纹大径;f为工件每转进给量 等于工件螺纹的螺距p 由上述条件及相关资料有; f=p=1mm/r d=6mm n=680r/min no=680r/min i=1 所以 (1) 切削速度
vdon1000
所以v=3.146680=10.7m/min 1000
(2) 基本工时
622.5622.52tm1=0.03min 68016801 2.5.8 工序九:铣缺口 (1)加工条件
工件尺寸:长为25mm, 宽为10mm 机床:XA5032立式铣床
刀具;W18Cr4V硬质合金端铣刀
W18Cr4V硬质合金端铣刀,牌号为YG6,由《切削用量简明手册》后称《切削手册》表3.1查得铣削宽度ae
a)切削深度 因切削用量较小,故可以选择ap=6mm,一次走刀即可完成所需尺寸。 b)每齿进给量:由《切削手册》表3.30可知机床的功为7.5KW,查《切削手册》表3.5可得f=0.14~0.24mm/z,由于是对称铣,选较小量f=0.14mm/z c)查后刀面最大磨损及寿命
查《切削手册》表3.7,后刀面最大磨损为(1.0~1.5)mm 查《切削手册》表3.8, 寿命T=180min d)计算切削速度 按《切削手册》表3.27中的公式 o
o
o
vccvdoqvkmprv
Tapxvfzyvuvaez也可以由表3.16查得vc=77m/min nt=245r/min vft =385m/min 各修正系数为:Kmv=Kmn=Kmvf=1.0 Ksv=Ksn=Ksvf=0.8 故 Vc=VtKv=77x1.0x0.8=61.6m/min n= ntkn=245x1.0x0.8=196r/min vf=vftkvt=385x1.0x0.8=308mm/min 又根据XA5032铣床参数,选 n=235r/min vf =375mm/s,则实际的切削速度为:
vcdonc1000
所以vc=3.14100235=73.8m/min,实际进给量为:
1000fzv所以fzv=
vfcncz
375=0.16mm/z 23510e)校验机床功率 查《切削手册》表3.24, 当бb=(174~207)MPa ae
ap=6mm vf=375mm/min n=235r/min vc=73.8m/min fz=0.14mm/z f)计算基本工时
tmL Vf公式中: L=l+y+Δ;根据《切削手册》表3.26,可得 l+Δ=0mm, 所以L=l+y+Δ=25mm 故 tmL=25/375=0.07min Vf3.绘制零件图和编制工艺文件
3.1 绘制零件图
21
图二:零件图
3.2 编制工艺文件
1 机械加工工艺过程的组成
工艺过程 改变生产对象的形状、尺寸、相对位置和性质等,使其成为成品或半成品的过程。工艺过程又可分为铸造、锻造、冲压、焊接、机械加工、热处理、装配等工艺过程。
机械加工工艺过程 用机械加工方法,改变毛坯的形状、尺寸和表面质量,使其成为零件的过程。
零件的机械加工工艺过程由许多工序组合而成,每个工序又可分为若干个安装、工位、工步和走刀。
工序 一个或一组工人,在一个工作地对同一个或同时对几个工件所连续完成的那一部分工艺过程。
安装 工件经一次装夹(定位和夹紧)后所完成的那一部分工序。
工位 为了完成一定的工序部分,一次装夹工件后,工件与夹具或设备的可动部分一起,相对刀具或设备的固定部分所占据的每一个位置。
工步 当加工表面、加工工具和切削用量中的转速和进给量均保持不变的情况下完成的那一部分工序。
22
2 工序的合理组合
确定加工方法以后,就要按生产类型、零件的结构特点、技术要求和机床设备等具体生产条件确定工艺过程的工序数.确定工序数有两种基本原则可供选择.工序分散原则 工序多,工艺过程长,每个工序所包含的加工内容很少,极端情况下每个工序只有一个工步,所使用的工艺设备与装备比较简单,易于调整和掌握,有利于选用合理的切削用量,减少基本时间,设备数量多,生产面积大.工序集中原则 零件的各个表面的加工集中在少数几个工序内完成,每个工序的内容和工步都较多,有利于采用高效的机床,生产计划和生产组织工作得到简化,生产面积和操作工人数量减少,工件装夹次数减少,辅助时间缩短,加工表面间的位置精度易于保证,设备、工装投资大,调整、维护复杂,生产准备工作量大.批量小时往往采用在通用机床上工序集中的原则,批量大时即可按工序分散原则组织流水线生产,也可利用高生产率的通用设备按工序集中原则组织生产.将工艺规程的内容,填入具有规定的格式的卡片中,使之成为生产准备和施工依据的工艺规程文件。
“机械加工工艺过程卡”和“机械加工工序卡”附后所示
4.夹具设计
为了提高劳动生产率,保证加工质量,降低劳动强度,需要设计专用夹具。 经过与指导老师的协商,决定设计第Ⅵ道工序—铣断双体,本夹具将用于XA6132卧式铣床,刀具为高速钢细齿圆锯片铣刀,对工件进行加工。
4.1问题的提出
本夹具主要用于铣开双体,并且铣开的表面与Φ20mm的孔有一定的公差要求,又在加工本道工序时,Φ20mm的孔已经进行了加工,因此,在本道工序中主要考虑加工面与Φ20mm孔之间的要求,其次是考虑如何提高劳动生产率,保证加工质量,降低劳动强度。
4.2 夹具体设计
4.2.1 定位基准的选择
23
图三定位原理图
由零件图可知:被铣开的那Φ50mm的中心线与Φ20mm孔的中心线之间的公差等级要求较高,且铣开时的设计基准为Φ50mm孔的中心线。为了尽量的减小定位误差,应选Φ20mm孔为主要的定位基准,利用一个圆柱销和一个菱形销定位,消除三个自由度,再在底面用夹具体定位消除三个自由度。以便达到所需要求。
为了提高加工效率,现同时加工四个双体,同时,为了夹具简单,操作方便,利用多点联动夹紧机构夹紧。 4.2.2 切削力及夹紧力的计算
刀具:高速钢细齿圆锯片铣刀 直径do160mm 齿数 Z=50 又由《切削手册》表3.28中的公式:
FCFapxFfzyFaeuFZdoqFnwF
其中: CF30
xF1.0
yF0.65 uF0.83 wF0 qF0.83
do160mm Z=50 ap4mm ae12mm fz0.025mm/z 所以 F=63.5N 水平分力:FH1.1F63.51.169.9N
垂直分力;FV0.3F0.363.519.1N
又在计算切削力时,必须把安全系数考虑在内。安全系数KK1K2K3K4 其中 K1为基本安全系数1.5 K2为加工性质系数1.2
24
K3刀具钝化系数 1.2 K4为切削特点系数(断续切削)1.2 所以 F ′=KFH=69.9x1.5x1.2x1.2x1.2=181.2N 为了克服水平方向的力,实际的夹紧力为 N(f1+f2)= KFH
其中 f1为螺母与螺杆间的摩擦系数
f2为工件与螺杆头(或压板)间的摩擦系数
又查得 f1 和f2为1.6 则
NKFH
f1f2181.2566N
0.160.16又选择的螺旋夹紧机构的基本尺寸如下(根据《机床夹具设计》 第三版表1-2-20、所以 N1-2-
21、1-2-
22、1-2-23查得:
950 r′=0
M12mm
p1mm rz5.675mm a136 30
2tg20.15 L=120mm Q=30N 则 可以提供的夹紧力为:
wQL )rtg1rz(a2 所以w =12030=3140N 5.675tg(136950)又由《机床夹具设计》 第三版表1-2-24查得 当螺纹的公称直径为12mm时 ,螺栓许用的夹紧力为5690N 由以上的数据可知:所选的螺旋机构提供的夹紧力大于所需的,且满足螺栓的许用夹紧力,故本夹具可以安全工作。 4.2.3 定位误差分析
1)定位元件尺寸及公差的确定 本夹具的定位元件为一圆柱销和一菱形销,其参数由(《机床夹具设计手册》图5-3及其表选 两定位销的尺寸及公差为:Φ2000.033mm(定位销的公差取h8)。
2)零件图样规定 Φ20mm的孔的中心线与Φ50mm孔的中心线的长度误差为0.2mm,Φ20mm孔中的定位销与夹具体的垂直度误差为0.05mm,,此项技术要求应由定位销
25
0.021宽配合中的侧向间隙保证。已知Φ20mm的宽为Φ200定位销为Φ200(定mm,0.033mm位销的公差取h8),则 一个定位销与一个孔的定位误差为:
bmax0.021(0.033)/20.027mm
此处引起零件的定位误差为 x0.02720.054mm
(2)计算Φ20mm定位销的中心线与夹具体垂直度误差
定位销的宽度为Φ2000.033mm 夹具体表面的粗糙度Ra1.6um 故 max0.0016(0.033)0.03360.05mm 所以最大垂直度误差能满足零件精度要求 4.2.4 夹具设计及操作的简要说明
如前所述,在设计夹具时,首先要考虑到能保证零件的加工精度,其次是要提高劳动生产率。为此,应先考虑所设计的夹具体与零件在夹具上的定位,在本道工序中,由于零件的底面的定位是用的夹具体,所以其表面粗糙度要求应比较高,视为关键面。又本道工序是铣断,其切削力不大,故在设计夹具时应考虑夹具的简单及利用常用的一些零件。为了提高生产率,可以考虑同时装夹几个零件,并且用了活动杠杆使操作更加节省时间。可以同时装夹四个零件,提高了生产率。
夹具上装有对刀块,可以使夹具在一批零件加工之前很好的对刀;同时,夹具体底面上的一对定位键可使整个夹具在机床工作台上有一正确的安装位置,以利于铣削加工。铣床夹具装配图及夹具体零件图见图示:
26
结
论
毕业设计是学生在校学习阶段的最后一个重要的教学环节,其目的是培养学生综合运用所学的专业和基础理论知识,独立解决专业一般工程技术问题的能力。树立正确的设计思想和工作作风。
经过两个月的毕业设计,获得如下心得:
1.运用机械制造工艺及有关课程的知识,结合生产实习中学到的实践知识。独立地分析和解决工艺问题。初步具有设计一些中等复杂零件的能力。
2.能根据被加工零件的技术要求,运用夹具设计的基本原理和方法。学会拟定夹具设计方案。
3.熟悉并运用有关手册,能快速查表得到所需的数据。 4.有一定的识图制图能力。
通过设计,培养了我综合运用理论知识和专业知识的技能。熟悉一般机械零件的加工工艺过程,设计夹具的能力。
中国加入WTO以后,大量的机械产品技术进入我国市场。中国企业能够与国外产品竞争,拥有自己的国内外市场就必须产品的质量好,技术含量高,价格低廉,这就要求我们扎实学习先进的技术,认真研究。
27
致
谢
本学期是我在学校求学的最后一个学期,也是完成我的毕业设计的时间表,在这最后一个学期里面,我学到了很多知识,其中有很多是很好实用价值的,这在我以后的工作中有大帮助,在此我对我的指导老师杨文生老师的辛勤教诲表示衷心的感谢,感谢他对我们设计的关心和帮助。本次毕业设计是我们大学四年所学知识做的一次总测验,是锻炼也是检验自己四年来所学知识和掌握、运用知识的能力,是我们高等院校学生的最后的学习环节,也是学到最多实际知识的时候。通过这次设计,我学到了许多原来未能学到的东西,对过去没有掌握的知识得到了更进一步巩固。独立思考,综合运用所掌握理论知识的能力得到很大的提高,学会了从生产实际出发,针对实际课题解决实际问题,掌握了综合使用各种设计手册、图册、资料的方法, 也是为我们即将参加工作所做的必要准备,打下基础,更是我们四年机械设计制造及其自动化专业知识的一次综合。
本次设计也暴露了我们不少的缺点和问题:对于所学知识还没有做到仔细、认真消化,许多方面还是只有一个大概的认识,没有深入探讨,对实际事物没有深刻得了解,没有做到理论联系实际,没有达到对所学的知识熟练运用的水平。这也从一个侧面反映出我们设计经验不足,思维不够开拓,不够灵活。从而我得出一个结论:无论是现在还是以后走上工作岗位,还是再深造,都应该虚心向老师和前辈们学习,从而不断完善自我,提高自我水平。
本次毕业设计毕竟是我们做的第一次比较完整,系统的设计,因而难免存在许多缺点和不足之处,还有待于改进。希望各位老师多提宝贵意见。
28
参考文献
[1]、徐嘉元,曾家驹主编《机械制造工艺学》机械工业出版社 97.8 [2]、赵家齐:《机械制造工艺学课程设计指导书》,机械工业出版社 [3]、李益民主编:《机械制造工艺设计简明手册》,机械工业出版社 [4]、艾兴 肖诗纲主编.《切削用量简明手册》.机械工业出版社, 1994 [5]、浦林祥主编.《金属切削机床夹具设计手册》.机械工业出版社, 1984 [6]、王启平主编《机床夹具设计》哈工大出版社 85.12 [7]、东北重型机械学院主编《机床夹具设计手册》上海科学技术出版社 80.1 [8]、徐灏主编《机械设计手册》机械工业出版社 91.9 [9]、《机械制造工艺学》、《机床夹具设计》 (教材)
[10]、孙丽媛主编,《机械制造工艺及专用夹具设计指导》,冶金工业出版社2002 [11]、《机械零件设计手册》 [12]、《机床夹具设计图册》 [13]、《几何量公差与检测》
29
摘 要
拨叉的加工质量将直接影响机器的性能和使用寿命。本次设计旨在提高CA6140车床拨叉的加工效率,由此我们首先对拨叉的结构特征和工艺进行了仔细的分析,然后确定了一套合理的加工方案,加工方案要求简单,操作方便,并能保证零件的加工质量。在制定加工工艺规程的顺序如下: 1分析零件; 2选择毛坯;
3设计工艺规程:包括制定工艺路线,选择基准面等;
4工序设计:包括选择机床,确定加工余量,工序尺寸及毛坯尺寸,确定切削用量及计算基本工时等; 5编制工艺文件。
此外,为了提高劳动生产率,降低劳动强度,保证加工质量,需设计专用夹具,本次设计选择了第六道工序铣断双体的专用夹具设计,以满足加工过程的需要。 关键词:拨叉; 工艺规程; 夹具设计
Abstract
Dials the fork proceing quality directly will affect the machine the performance and the service life.This design is for the purpose of enhancing the CA6140 Lathe machine Dials the fork the proceing efficiency, first has carried on the careful analysis from this us to the Dials the fork structure characteristic and the craft, then had determined set of reasonable proceings plans, the proceing plan request are simple, the ease of operation, and can guarantee the components the proceing quality.In formulation proceing technological proce order as follows: 1 analysis the components; 2 choices semifinished materials; 3 designs technological proce: Including division Craft route, preferred orientation datum and so on; 4 working procedures designs: Including chooses the engine bed, the determination proceing remainder, the computation working procedure size and its the Semifinished materials size, the determination cutting specifications and the computation man-hour and so on; 5 establishments technological document.In addition, in order to enhance the labor productivity, reduces the labor intensity, guaranteed the proceing quality, must design the unit clamp, this design chose the six working procedure to The mill breaks Catarmaran Special-purpose jig design, by satisfied the proceing proce the need.Key words: Dials the fork; technological proce; jig desin。
30
目 录
前 言-------------1 1 零件的分析1 1.1 零件的作用-------------------------1 1.2 零件的工艺分析------------------1 2 工艺规程的设计------------------------2 2.1 毛坯的制造形式-----------------2 2.2 基准面的选择---------------------2 2.2.1 粗基准的选择-------------2 2.2.2 精基准的选择-------------2 2.3 制定工艺路线---------------------3 2.4 机械加工余量、工序尺寸及毛坯尺寸的确定-------4 2.5 确定切削用量及基本工时----4 3 绘制零件图和编制工艺卡----------21 3.1 绘制零件图------------------------21 3.2 编制工艺文件---------------------22 4 夹具设计----23 4.1 问题的提出-----------------------23 4.2 夹具体设计-----------------------23 4.2.1 定位基准的选择---------23 4.2.2 切削力及夹紧力的计算------------------------------24 4.2.3 定位误差分析-------------25 4.2.4 夹具设计及操作的简要说明-----------------------26 5 结论-----------276 致谢-----------287 参考文献----29
31
学 号: 200901124193711
河北理工大学成人教育
毕业论文(设计说明书)
论文题目: 学 院: 专 业: 班 级: 姓 名: 指导教师:
拨叉机械加工工艺规程及夹具设计
河北理工大学继续教育学院 机械设计制造及其自动化
09机本培 王 虎 杨文生
2013 年 月 日
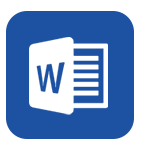