推荐第1篇:夹具设计员岗位职责
1.负责新产品喷漆夹具设计、开发。2.负责量产项目喷漆夹具质量改善与跟踪。3.负责双色喷漆夹_目的前期全程介人。4.负责喷漆夹具使用培训。5.负责喷漆夹具成本控制。
推荐第2篇:CNC编程岗位职责
CNC编程岗位职责
负责整套模具的程序编制、设计出合理的电极并做出标准的EDM图纸,配合各部门做好需要设计变更工作以及跟踪CNC、EDM的现场加工,有些电极需W/C的做出2D图纸协助W/C完成.及时查看刀具的使用以及库存情况,并协助CNC现场加工出符合标准的工件,在不影响质量的情况下编制出高效合格的程序,从而提高加工效率,在工作中要仔细检查,要做好与有关部门的沟通工作来减少不必要的错误,做到防微杜渐。
推荐第3篇:夹具
工装夹具管理流程
1.目的
1.1 有计划地对工装夹具的设计、制造、保管、使用、鉴定及维护进行全过程的控制,确保工装夹具处于良好的使用状态,以保证产品质量,特制定本流程。
2.适用范围
2.1适用于本公司产品开发及正常生产所需的工装夹具。3.职责
3.1 技术项目组:负责工装夹具的设计、组织评审。 3.2生产技术部:是工装夹具的归口单位,负责制造、维修、验收及管理,并建立台账,安全保管。
3.3质量管理部:工装鉴定负责工装夹具的验收及周期鉴定。3.4 生产车间:负责工装夹具的使用、日常维护和临时保管。 3.5 采购部:负责委外工装夹具的采购。 3.6 财务部:负责工装资产的管理、盘点。 4.流程
4.1 工装设计
4.1.1 技术项目组根据新产品开发及生产的需要,提出工艺装备清单和技术要求,组织工艺装备的设计工作。需委外设计加工的工装,技术开发部提供产品接口信息及技术要求。 4.1.2设计人员在规定的时间内完成设计后,组织相关人员对工装可行性进行评审,经工装工程师会签,交总工程师批准。
4.1.3每套工艺装备图纸交技术资料员建立档案,发放、更改、换版、管理具体按照《文件和资料控制程序》相关条款执行。 4.2 制造
4.2.1 自制的工艺装备由工装工程师根据技术图纸、生产制造计划、工装制造周期、安全库存编制工装制造计划。每月5日前下发生产部相关领导。
4.2.2于1个工作日内做好工装下料计划并交采购部分管人员。
4.2.3采购员于3个工作日将所需材料采购回来。(特殊情况因生产急要的需当天采购到位)
4.2.4 工艺装备加工完成后,由制造部门填写“工艺装备检验通知单”, 连同工装一起交工装鉴定站进行验证。 4.3 委外制造
4.3.1对不具备自行设计和制造能力的工艺装备,由技术项目组填写“工艺装备委外设计、制造/修理申请单”,报主管副总经理批准,由采购部选择、确定合适的制造商,项目工程师评审,应充分考虑对方设计和机械加工能力,关键的工艺装备委外加工需同制造商签定《工艺装备验收技术协议》,并跟踪其设计、制造、检测的质量和进度,将跟踪情况记录于“工艺装备协议跟踪记录表”上。
4.3.2工艺装备到厂后,由采购部通知工装工程师进行验收,验收的内容:《工艺装备验收技术协议》上的各项条款得到
满足:
a.包装完好,实物无损伤; b.有产品合格证、检验报告;
c.附件、备品备件、技术资料(包括全套详细设计图 纸)齐全。
4.3.3 验收合格后,工装工程师填写“工艺装备检验通知单”交工装鉴定进行验证,验证按以下形式: a.按工艺装备图样和技术条件自行检验。 b.委托有测量能力的检测单位进行检验。 c.检验该工艺装备生产的工装样品。
4.3.4 验证合格后,工装工程师和工装鉴定员在“工艺装备验证报告”上联合签字,一份交采购员做付款凭证,一份交工装库,做入库凭据,如验证不合格,工装工程师同制造商协调处理,甚至退货。
4.4.鉴定
4.4.1 工装鉴定站无论收到车间返回还是新制工装,于1个工作日完成鉴定,急件工装应当场鉴定完成。验证方式:按工艺装备设计图纸和技术条件进行检验,或检验该工艺装备所生产的样件。
4.4.2 要进行统一编号,编号应反映与产品一致的版次/更改状态,可采用电刻或打钢印。
4.4.3 工装鉴定完毕应出具工装鉴定报告,合格的出具工装合
格证,连同 工装一起交到工装管理员,不合格的连同报告退回工装组返修。
4.5.入库
4.5.1 工装管理员在确认工装夹具合格后,办理入库手续,建立“工艺装备管理台帐”和“工艺装备履历卡”,保存“工艺装备验证报告”、“入库单”等相关质量记录凭证。 4.5.2 所有工装夹具应按规定分类放在专用架子上,并按照有关工装夹具的名称制作标识牌,进行整齐排列,保持工装夹具完整、清洁、帐、卡、物相符,方便取放。 4.6 领用、回收与发放 4.6.1领用
4.6.1.1使用单位需使用工艺装备时,车间员工领用工装需开具领料单,填写车间名称、日期、工装名称、工装编号、数量、领料人,车间班长和工段长签字,连同旧工装一起交回工装库,工装库采用以旧换新模式发放新工装。用完后必须清理干净,及时还库,工艺装备还库时必须附带使用记录。
4.6.1.2 操作工要正确使用,不得野蛮操作,发现异常和损坏立即停止使用,通知工装管理人员进行处理。
4.6.1.3 操作工要做好使用记录,记录内容包括:运行使用时间、加工数、累计加工数。 4.6.2 回收、发放
4.6.2.1工装管理员检查工装的完整性,没有缺件、损坏,工装管理员发放新工装,同时做好新工装登记、旧工装销账、填写工装履历卡,发放人和领料人双方签字确认。4.6.2.2旧工装摆放在待检架上,工装鉴定员与1个工作日完成鉴定,工装鉴定完毕应出具工装鉴定报告,合格的出具工装合格证,连同工装一起交到工装管理员,不合格的连同报告退回工装组返修。
4.6.2.3如车间增加设备或工装丢失等原因无法以旧换新的,由
车间主任在领料单上签字,并说明原因,管理员方可发放。
5.报废
5.1 车间因为使用不当造成工装损坏、丢失,工装管理员负责填写工装报损单,交车间工段长落实责任人,车间工段长2个工作日内落实完成交回工装鉴定员。工装鉴定员每月月底将报损表汇总提交工装工程师。
5.2 工装工程师对报损表的工装损失进行估价,对责任人按估价20%进行处罚,于每月5日前完成上月报损表的评估,报分管技术总监批准后交财务一份,同时各车间发放一份。 5.3 凡属无法修理或修理成本过高的工艺装备可以作报废处理,由工装鉴定员填写“工艺装备报废申请单”交工装工程师审批。
5.4 对关键、重要的工艺装备,项目组组织生产部、质量管理部、使用单位进行鉴定,并出具结论。一般的直接由项目
组出具结论。
5.5工装管理人员负责对报废的工艺装备进行拆卸,将有利用价值的零部件保留登记,无利用价值的作废品处理。 5.6列出报废清单,经技术总监、常务副总核准,报财务部一
份,工装库同时注销台帐。
5.7工装管理员根据工装安全库存进行排查,每周五将低于安全库存的工装用书面形式报工装组负责人,工装组将编入生产计划,安排生产。6.原始凭证及传递路线
6.1 工装组工装生产完上交库房,待鉴定合格后,工装管理员开
具工装进库单,工装生产组交料人签字生效,进库单一式三联,工装组一联、工装管理员一联、财务一联,财务部每周上交一次。工装库、财务部凭票登帐。
6.2 车间凭领料单领取工装,工装管理员凭领料单发料,并做好车间领料台账,当天完成。
6.3 报废工装开具报废清单,连同“工艺装备报废申请单”一起上交财务部销账,同时工装库销账,每月月底上交、销账。
7.搬运与保养
7.1 工装在搬运可用手推车或人工搬运,必须轻拿轻放,严禁堆放,如出现损坏的将按工装损坏5.2项进行报损处理。 7.2 每周对工装进行一次涂油保养,防止生锈。
8.记录与表单
8.1 工艺装备检验通知单 8.2 工艺装备鉴定报告
8.3 工艺装备委外设计、制造/修理申请单 8.4 工艺装备管理台帐 8.5 年度工艺装备周期检定计划 8.6 8.7 8.8
编制: 月工艺装备周期检定实施表 工艺装备报废申请单 工艺装备报损单
审核:
批准:
推荐第4篇:夹具
前言
轴承座的用途
轴承座的作用:轴承座是用来支撑轴承的,固定轴承的外圈,仅仅让内圈转动,外圈保持不动,始终与传动的方向保持一致(比如电机运转方向),并且保持平衡。
因为此零件为大批量生产,为了提高劳动生产率,保证加工质量,降低劳动法强度,需做一种专用夹具,省去加工中繁琐的工序。我们已经学习了机械制造工艺和夹具,对夹具设计有了初步的了解。对于一种批量较大的产品可设计制造一种专业夹具,操作迅速方便,减少了工人的劳动量,可获得较高的加工精度和生产率,对工人的技术水平要求也相对较低。但专用夹具设计制造周期长、夹具制造费用较高。专用夹具的针对性极强、没有通用性,很明显只能适用于产品相对稳定的大批量生产中。
由于所学知识有限,设计能力有限,在设计中难免会有许多错误和不足,恳请老师给予批评指正。
目
录
摘要………………………………………………………………… 1
一、夹具设计任务及要求
1.1 轴承座的重要技术要求……………………………………… 1 1.2 精度及批量分析……………………………………………… 1
二、夹具设计方案的确定………………………………………… 2 2.1 零件工艺分析………………………………………………… 3 2.2 基准面的选择………………………………………………… 3 2.3 定位原理及定位方案的选择及实现………………………… 3 2.4夹紧方式及元器件的选择…………………………………… 4 2.5 夹具总方案…………………………………………………… 6
三、定位误差及夹紧分析与计算………………………………… 7 3.1 影响加工精度的因素………………………………………… 7 3.2 保证加工精度………………………………………………… 8 3.3 夹紧力的数值计算…………………………………………… 8
四、夹具装配图…………………………………………………… 10 感谢………………………………………………………………… 11 参考文献…………………………………………………………… 1
2 摘要
本设计的内容是设计粗铣15 +0.05的平面夹具,零件材料为HT200。选用的铣刀为YG6硬质合金端铣刀。
一、夹具设计任务及要求 1.轴承座上平面的重要技术要求:
15+0.05的上平面与Φ30的孔平行度公差为0.03mm; 15+0.05的上平面与Φ30的孔位置度公差为0.01mm; 15+0.05的上平面平面度公差为0.008mm; 15+0.05的上平面的粗超度为1.6;
1 2.精度及批量分析
(1)本工序有一定位置精度要求,属于批量生产,使用夹具加工是适当的。 (2)考虑到生产批量不是很大,因而夹具结构应尽可能的简单,以减少夹具的制造成本。
二、夹具设计方案的确定 2.1工艺分析
在粗铣铣上底面时,该面相对于底面的尺寸精度和本身表面粗糙度不是很高,由立式铣床直接加工就可以达到要求,其中该面的表面精度由刀具的保证,面的位置精度由设计的夹具来保证。
由于两半平面的平面度要求比较高,公差为0.008,所以为保证这要求,一地面为定位面。而对于15mm的上平面的基准主要是Φ30的孔的中心线,所以也要以其为基准,以消除误差!总体要求如下:
2.2.基准面的选择(夹具体方式的确定)
夹具体是夹具的基本件,它既要把夹具的各种元件、机构、装置连接成一个整体,而且还要考虑工件装卸的方便。因此,夹具体的形状和尺寸主要取决于夹具各组成件的分布位置、工件的外形轮廓尺寸以及加工的条件等。在设计夹具体时应满足以下基本要求。
具有足够的强度和刚度。
2 结构简单、轻便,在保证强度和刚度前提下结构尽可能简单紧凑,体积小、质量轻和便于工件装卸。
安装稳定牢靠。
结构的工艺性好,便于制造、装配和检验 尺寸要稳定且具有一定精度。 清理方便。
达到零件所须的技术要求
故本方案的基准面轴承座底面为基准面。
2.3 定位原理及定位方案的选择及实现
1.工件的定位原理
自由物体在空间直角坐标系中有六个自由度,即沿OX,OY,OZ三个轴向的平动自由度和三个绕轴的转动自由度。要使工件在夹具体中具有准确和确定不变的位置,则必须限制六个自由度。工件的六个自由度均被限制的定位叫做完全定位;工件被限制的自由度少于六个,但仍然能保证加工要求的定位叫不完全定位。 根据零件的技术要求:定位方案确定为两面一孔定位。
2.定位方案的选择及实现
由分析知,零件的定位方案有如下两种:
方案一:采用轴承座底面限制3个自由度,左前端面侧限制两个自由度及Φ30mm孔定位一个自由度;
方案二:采用轴承座底面限制3个自由度,左前端面侧限制两个自由度及左侧面限制一个自由度
比较两种定位方案:方案一的定位中用到设计基准Φ30mm的孔,能减少加工误差,而且夹紧比较方便,可靠。方案二的定位没有用到设计基准Φ30mm的孔,造成基准不重合误差,而且因为切削力主要垂直向下的,所以方案二没有很好的利用左前端面来定位,夹紧。方案二的夹紧需要另外设计,比较浪费材料!所以,选择方案一,比较合理。
具体定位方案如下:
3
3.定位原件的选择
根据定位及夹紧的要求,Φ30mm孔选择菱形销限制1个自由度;下表面选择两个支撑板,限制2个自由度;左端面选择一个支撑钉,联合菱形销限制2个自由度。
2.4.夹紧方式及元器件的选择
1.夹紧机构的三要素是夹紧力方向的确定、夹紧力作用点的确定、夹紧力大笑的确定。
对夹紧机构的基本要求如下:
夹紧作用准确,处于夹紧状态时应能保持自锁,保证夹紧定位的安全可靠。 夹紧动作迅速,操作方便省力,夹紧时不应损害零件表面质量 夹紧件应具备一定的刚性和强度,夹紧作用力应是可调节的。 结构力求简单,便于制造和维修。
2.在本次设计的零件中,考虑到是粗铣,只要是收到向下的切削力,所以当用下平面起支撑和定位作用,所以应该用两个支撑板来定位,支撑!
如下:
4 :
3.由于Φ30mm的孔采用菱形销来定位,限制一个只有度,而切削力的方向主要是向下,所以在Φ30mm孔的位置设计一个圆形压板来起固定和压紧作用,方便,牢固!具体如下:
5 4.左端面限制两个自由度,因为其水平方向的切削力不是很大,所以在左端面设计一定位销,配合Φ30mm的孔的菱形销限制3个自由度。具体如下:
2.5 夹具总体定位及夹紧方案
6
三、定位误差与夹紧分析及计算 3.1影响加工精度的因素
一批工件依次在夹具中进行定位时,由于工序基准的变动对加工表面尺寸所造成的极限值之差称为定位误差。产生定位误差的原因是工序基准与定位基准不相重合或工序基准自身在位置上发生偏移或位移所引起的。
用夹具装夹工件进行机械加工时,其工艺系统中影响工件加工精度的因素很多,与夹具有关的因素有:定位误差ΔP、对刀误差ΔT、夹具在铣床上的安装误差ΔA和夹具误差ΔE,在机械加工工艺系统中,影响加工精度的其它因素综合称为加工方法误差ΔG。上述各项误差均导致刀具相对工件的位置不精确而形成总的加工误差∑Δ。
a.定位误差ΔD ①第一类误差
第一类误差是指工件在夹具上定位时所产生的那部分定位误差。
基准不重合误差是由于定位基准和工序基准不重合而产生的那部分定位误差。在本设计中,由于定位基准和工序基准是重合的,所以基准不重合误差为0。
②第二类误差
第二类误差是定位元件对夹具基准面的尺寸误差及位置度所产生的那一部分定位误差。
零件图规定上面与下底面的距离为15mm.夹具夹紧后,定位误差取决于下底面的制造误差.所以误差为:
Δp=0.02x0.015=0.03 b.夹具在铣床上的安装误差ΔA 因为夹具在铣床上的安装不精确而造成的加工误差,称为夹具的安装误差。 一般取:
Δ Δ水A=0mm =0.2mm 垂Ac.夹具误差ΔE 因夹具上定位元件,对刀或导向元件及安装基面三者之间(包括导向元件与导向元件之间)的位置不精确而造成的加工误差,称为夹具误差,夹具误差大小取决于夹具零件的加工精度的夹具装配时的调整和修配精度。
一般取ΔE=0.02mm d.加工方法误差ΔG
7 因铣床精度,刀具精度,刀具与铣床的位置精度,工艺系统受力变形和受热变形等因素造成的加工误差,统称为加工方法误差,因该项误差影响因素很多,
k1又不便于计算,所以常根据经验为它留出工件公差的3。计算时可设ΔG=3。
k——工件位置公差取0.008 kΔG=310.0080.002mm3
3.2.保证加工精度
工件在夹具中加工时,总加工误差∑Δ为上述各项误差之和。由于上述误差均为独立随机误差,应用概率法加,因此,保证工件加工精度条件是:
p2a2e2g2
0.0320.220.0220.00220.203 即工件总加工误差∑Δ应不大于工件的加工尺寸公差,由以上得知,本夹具完全可以保证加工精度。
为保证夹具有一定的使用寿命,防止夹具因磨损而过早报废,在分析计算工件加工精度时需留出一定精度储备量Jc,因此将上式改为:
≤k-Jc → Jc=k- (3-7)
当Jc≥0时夹具能满足加工要求,根据以上
Jck=-=0.30-0.203=0.097≥0 所以夹具完全可以满足加工要求。
3.4 夹紧力的数值计算
刀具:YG6硬质合金端铣刀,查《切削手册》表3.28可知:
F圆周力:
XFYFuFCFapfzaeZd0qFnWF 其中:
8 CF54.5,ap4.5,XF0.9,fZ0.18,YF0.74,ae28,uF1.0,d0100,qF1.0,n255,WF0,Z10
54.54.50.90.180.74281.010F166.1(N)1.00100255
F1.1F182.7(N) 水平分力:H垂直分力:FV0.3F49.8(N)
KK1K2K3K4 在计算切削力时,必须安全系数考虑在内。 安全系数: 其中:K11.5,K21.1,K31.1,K41.1
FKFH(1.51.11.11.1)182.7364.8(N)
实际需要加紧力为:
KFH364.8Fjia729.6(N)f1f20.5ff(其中1和1为夹具定位面及加紧面上的磨擦系数,
f1f20.25)
由于采用压板夹紧机构,夹紧力一般都比较大,并且切削力方向主要作用在支撑面上,所以该夹紧机构一定可以保证工作。
4 夹具装配图
9
致谢
专用夹具是为零件的某一道工序加工而设计制造的,它广泛用于大量生产中,它不但提高了生产率而且也提高加工精度,改善劳动条件。
通过这次课程设计,我个人对夹具有了更进一步的了解,夹具要保证加工出的产品有较高的精度,就必须要求其自身有较高的精度,定位元件拥有高精度的同时还需要有一定的刚度和强度,以保证在加工过程中自身不会变形和一定的寿命。夹紧机构要求有一定的刚度和强度,以确保在一定的力的作用下夹紧元件不会先于工件发生变形、损坏。夹具体是夹具的主体部分,是与铣床相接的部位、也是支撑夹紧元件、工件的主要部分:要求其有一定的强度和刚度、稳定性,又考虑到经济性一般采用HT200作为夹具体。
而且对夹具的维护保养,及夹具在设计中应该注意的问题有了更进一步的了解,自己的能力在这次课程设计中也得到了提升。在设计的过程中又一次把所学的知识做了一次综合式的复习,为接下来要做的毕业设计做好了很好的准备工作;同时在设计中也发现自己的很多不足之处:缺乏实际的经验,有些实物没有见过很难想像,只能通过找相应的参考资料,然后再通过想象把他们综合到一起,再通过实例对比,进行设计。因此在夹具设计中存在有很多的不足之处,还恳请老师您予以指导和指正。同时,也感谢老师在设计过程中的谆谆教导,使自己及时改正错误方案,收益良多!
11
参考文献
1.《机械制图》第五版,大连理工大学工程画教研室编。2.沈莲主编《机械工程材料》机械工业出版社,北京,2007 3.《机械设计》第八版,西北工业大学机械原理及机械零件教研室编。 4.《机床夹具设计手册》第三版,王光斗,王春福主编。
5.《机械制造工艺设计手册》,哈尔滨工业大学机械知道工艺及自动化教研室王绍俊主编。
6.《简明机床夹具设计手册》,化学工业出版社,吴拓编著。7.王先逵主编《机械制造工艺学》机械工业出版社,北京,2006。
12
推荐第5篇:工装夹具
工装,即工艺装备:指制造过程中所用的各种工具的总称.包括刀具/夹具/模具/量具/检具/辅具/钳工工具/工位器具等.工装为其通用简称.工装分为专用工装/通用工装/标准工装(类似于标准件)
夹具,顾名思义,用以装夹工件(或引导刀具)的装置
模具,用以限定生产对象的形状和尺寸的装置.
刀具,机械制造中使用的刀具基本上都用于切削金属材料,所以“刀具”一词一般就理解为金属切削刀具。
辅具,一般指用以连接刀具和机床的工具.
钳工工具,各种钳工作业所用的工具总称
工位器具,用以在工作地或仓库中存放生产对象或工具的各种装置.检具,生产中检验所用的器具
治具,制造用器具,这个词对应fixture,有时与工装同意,有时也指夹具,一般台资/韩资/日资等电子企业多用该词。
夹具属于工装,工装包含夹具,属于从属关系.
编辑本段应用
夹具是加工时用来迅速紧固工件,使机床、刀具、工件保持正确相对位置的工艺装置。也就是说Workholding工装夹具是机械加工不可缺少的部件,在机床技术向高速、高效、精密、复合、智能、环保方向发展的带动下,夹具技术正朝着高精、高效、模块、组合、通用、经济方向发展。
夹具又称卡具。从广义上说,在工艺过程中的任何工序,用来迅速、方便、安全地安装工件的装置,都可称为夹具。例如焊接夹具、检验夹具、装配夹具、机床夹具等。其中机床夹具最为常见,常简称为夹具。
在机床上加工工件时,为使工件的表面能达到图纸规定的尺寸、几何形状以及与其他表面的相互位置精度等技术要求,加工前必须将工件装好(定位)、夹牢(夹紧)。
应用机床夹具,有利于保证工件的加工精度、稳定产品质量;有利于提高劳动生产率和降低成本;有利于改善工人劳动条件,保证安全生产;有利于扩大机床工艺范围,实现“一机多用”。
夹具通常由定位元件(确定工件在夹具中的正确位置)、夹紧装置、对
刀引导元件(确定刀具与工件的相对位置或导引刀具方向)、分度装置(使工件在一次安装中能完成数个工位的加工,有回转分度装置和直线移动分度装置两类)、连接元件以及夹具体(夹具底座)等组成。
推荐第6篇:夹具说明书
沈阳理工大学应用技术学院机械制造装备课程设计说明书
前言
机械制造技术基础是机械设计制造及其自动化(或机械工程及自动化)专业的一门重要的专业基础课。
机械设计是机械工程的重要组成部分,是决定机械性能的最主要因素。由于各产业对机械的性能要求不同而有许多专业性的机械设计。
在机械制造厂的生产过程中,用来安装工件使之固定在正确位置上,完成其切削加工、检验、装配、焊接等工作,所使用的工艺装备统称为夹具。如机床夹具、检验夹具、焊接夹具、装配夹具等。
机床夹具的作用可归纳为以下四个方面:
1.保证加工精度
机床夹具可准确确定工件、刀具和机床之间的相对位置,可以保证加工精度。
2.提高生产效率
机床夹具可快速地将工件定位和夹紧,减少辅助时间。 3.减少劳动强度
采用机械、气动、液动等夹紧机构,可以减轻工人的劳动强度。
4.扩大机床的工艺范围
利用机床夹具,可使机床的加工范围扩大,例如在卧式车床刀架处安装镗孔夹具,可对箱体孔进行镗孔加工。
机械制造装备设计课程设计是机械设计中的一个重要的实践性教学环节,也是机械类专业学生较为全面的机械设计训练。其目的在于:
1.培养学生综合运用机械设计基础以及其他先修课程的理论知识和生产实际知识去分析和解决工程实际问题的能力,通过课设训练可以巩固、加深有关机械课设方面的理论知识。
2.学习和掌握一般机械设计的基本方法和步骤。培养独立设计能力,为以后的专业课程及毕业设计打好基础,做好准备。
3.使学生具有运用标准、规范手册、图册和查询有关设计资料的能力。
我国的装备制造业尽管已有一定的基础,规模也不小,实力较其它发展中国家雄厚。但毕竟技术基础薄弱,滞后于制造业发展的需要。我们要以高度的使命感和责任感,采取更加有效的措施,克服发展中存在的问题,把我国从一个制造业大国建设成为一个制造强国,成为世界级制造业基础地之一。
1 沈阳理工大学应用技术学院机械制造装备课程设计说明书
1.产前准备
1.1年生产纲领
工件的年生产量是确定机床夹具总体方案的重要依据之一。如工件的年生产量很大,可采用多工件加工、机动夹紧或自动化程度较高的设计方案,采用此方案时,机床夹具的结构较复杂,制造成本较高;如工件的年生产量不大,可采用单件加工,手动夹紧的设计方案,以减小机床夹具的结构复杂程度及夹具的制作成本。如5万件以上夹具复杂用全自动化的设备,5000件小批量生产用手动设备。
1.2生产条件
直径从1毫米以下至120毫米的所有规格钻头都可以使用钻床加工。
台式钻床的加工范围通常在15毫米以下。立式钻床的最大加工范围通常在15~75毫米之间。摇臂钻的最大加工范围在25~120毫米之间。各种钻床主轴的锥孔型号和功率不同。最小的高速台钻的功率只有200W,最大的摇臂钻的功率可以达到25KW。
台钳常用在立式钻床和台式钻床上,只能夹持小型零件,大中型零件通常在摇臂钻上加工,直接夹紧在工作台上。 Z5025型号立式钻床,最大钻孔直径25mm,主轴端至底面距离1000mm,主轴级数9级,主轴转速范围500-2000转每分钟,主轴行程200mm,外形尺寸1050×687×1980。
1.3零件工艺分析
本次课设是要为此图1-3-1中的后托架设计一个钻ǿ6和M6孔的夹具,最终实现将工件定位,更加精确和方便的完成钻孔工作,并保证能夹紧工件,夹紧力要适中,不要使工件变形,又能保证工件所要求的加工精度。
2 沈阳理工大学应用技术学院机械制造装备课程设计说明书
3783±0.0563±0.050.08B0.07A1.60.07A25607φ42217R86+00.025R25671.635±0.07312B1.6501205R7A0.0325φ30.20+0.2φ8φ25.5+0.308121610C-CRz50M6CRz50126.36.32-φ132-φ204628301560156215锪平156072-φ13R120Rz5026.31.620C2-φ10锥孔装配铰孔92未注明圆角半径为R3—5.
图1-3-1
零件图标出了工件的尺寸、形状和位置、表面粗糙度等总体要求,它决定了工件在机床夹具中的放置方法,是设计机床夹具总体结构的依据,本工件放置方法应如图1-3-1所示。工序图给出了零件本工序的工序基准、已加工表面、待加工表面,以及本工序的定位、夹紧原理方案。工件的工序基准、已加工表面决定了机床夹具的方位方案,如选用平面定位、孔定位以及外圆面定位等;定位方案的选择依据六点定位原理和采用的机床加工方法,定位方案不一定要定六个自由度,但要完全定位。工件的待加工表面是选择机床、刀具的依据。确定夹紧机构要依据零件的外型尺寸,选择合适的定位点,确保夹紧力安全、可靠同时夹紧机构不能与刀具的运动轨迹相冲突。
431.φ4606R8φ6Rz50沈阳理工大学应用技术学院机械制造装备课程设计说明书
2.夹具结构设计
2.1定位机构
φ10R854-φ363242.545°4220216φ1016539425931170702109125240804230φ4.5技术要求1.外轮廓倒角为R10。2.突台倒角为R2。1434φ22φ16φ12
图2-1-1定位平面
在夹具设计中,定位方案不合理,工件的加工精度就无法保证。工作定位方案的确定是夹具设计中首先要解决的问题。
根据工序图给出的定位元件方案,按有关标准正确选择定位元件或定位的组合。在机床夹具的使用过程中,工件的批量越大,定位元件的磨损越快,选用标准定位元件增加了夹具零件的互换性,方便机床夹具的维修和维护。
2451044 沈阳理工大学应用技术学院机械制造装备课程设计说明书
设计夹具是原则上应选该工艺基准为定位基准。无论是工艺基准还是定为基准,均应符合六点定位原理。
由于该零件的加工是钻φ6孔并以外表面作为定位面,属面定位类型,因此本次设计采用的定位机构为圆柱销与大平面相结合。圆柱销定位的形式很多,短圆柱销定位限制Y,Z方向的移动,限制两个自由度;长圆柱销定位限制工件的Y,Z方向的转动和移动,限制四个自由度;两个短圆柱销与长圆柱销相同。大平面限制X,Y方向的转动及Z方向的移动。装夹工件时,通过工件孔和心轴接触表面的弹性变形夹紧工件。本次设计的定位选用的是短销与平面相结合,分别限制工件的X、Y方向的移动及转动自由度以及Z方向的旋转自由度。心轴定位的特点为结构简单、制造容易、夹紧可靠,自锁性好,夹紧动作慢、效率低。
2.2夹紧机构
图2-2-1工件放置方式
1.夹紧的目的:使工件在加工过程中保持已获得的定位不被破坏,同时保证加工精度。
2 .夹紧力的方向的确定:
1)夹紧力的方向应有利于工件的准确定位,而不能破坏定位,一般要求主夹紧力应垂直于第一定位基准面。
5 沈阳理工大学应用技术学院机械制造装备课程设计说明书
2)夹紧力的方向应与工件刚度高的方向一致,以利于减少工件的变形。
3)夹紧力的方向尽可能与切削力、重力方向一致,有利于减小夹紧力。
3 .夹紧力的作用点的选择:
1)夹紧力的作用点应与支承点“点对点”对应,或在支承点确定的区域内,以避免破坏定位或造成较大的夹紧变形。
2)夹紧力的作用点应选择在工件刚度高的部位。
3)夹紧力的作用点和支承点尽可能靠近切削部位,以提高工件切削部位的刚度和抗振性。
4)夹紧力的反作用力不应使夹具产生影响加工精度的变形。
4.选择夹紧机构:
设计夹紧机构一般应遵循以下主要原则: 1)夹紧必须保证定位准确可靠,而不能破坏定位。 2)工件和夹具的变形必须在允许的范围内。
3)夹紧机构必须可靠。夹紧机构各元件要有足够的强度和刚度,手动夹紧机构 4)必须保证自锁,机动夹紧应有联锁保护装置,夹紧行程必须足够。 5)夹紧机构操作必须安全、省力、方便、迅速、符合工人操作习惯。 6)夹紧机构的复杂程度、自动化程度必须与生产纲领和工厂的条件相适应。
图2-2-2夹紧机构
6 沈阳理工大学应用技术学院机械制造装备课程设计说明书
选用螺栓螺母夹紧机构来对被加工工件进行夹紧。
螺栓螺母夹紧机构的特点:①结构简单,制造方便加紧可靠施力范围大;②自锁
性能好操;③扩力比80以上,行程S不受限制;④加紧工作慢,效力低。
2.3夹具体的总体设计图:
2.4绘制夹具装配图
图2-3-1总体图
7 沈阳理工大学应用技术学院机械制造装备课程设计说明书
1.装配图按1:1的比例绘制,用局部剖视图完整清楚地表示出夹具的主要结构及夹具的工作原理。
2.视工件为透明体,用双点划线画出主要部分(如轮廓、定位面、夹紧面和加工表面)。画出定位元件、夹紧机构、导向装置的位置。 3.按夹紧状态画出夹紧元件和夹紧机构。
4.画出夹具体及其它联接用的元件(联接体、螺钉等),将夹具各组成元件联成一体。
此机床夹具要用到的零件如下: (1) 工件
(2) 活动垫片 (3) 内六角螺栓 (4) 削边销
(5) 夹具体
(6) 六角螺母
(7)平垫圈
(8) 圆锥销 (9) 圆锥销
8 沈阳理工大学应用技术学院机械制造装备课程设计说明书
(10)圆柱螺旋压缩弹簧 (11)台肩销
(12)调整螺栓
(13)内六角圆柱头螺钉 (14)压板
(15)垫片
(16)螺栓
(17)内六角圆柱头螺钉 (18)定位块
5.标注必要的尺寸、配合、公差等
(1)夹具的外形轮廓尺寸,所设计夹具的最大长、宽、高尺寸。
(2)夹具与机床的联系尺寸,即夹具在机床上的定位尺寸。如车床夹具的莫氏硬度、铣床夹具的对定装置等。
(3)夹具与刀具的联系尺寸,如用对刀块塞尺的尺寸、对刀块表面到定位表面的尺寸及公差。
(4)夹具中所有有配合关系的元件间应标注尺寸和配合种类。
(5)各定位元件之间,定位元件与导向元件之间,各导向元件之间应标注装配后的位置尺寸和形位公差。
6.夹具装备图上应标注的技术要求 (1)定位元件的定位面间相互位置精度。
(2)定位元件的定位表面与夹具安装基面、定向基面间的相互位置精度。
(3)定位表面与导向元件工作面间的相互位置精度。
(4)各导向元件的工作面间的相互位置精度。
(5)夹具上有检测基准面的话,还应标注定位表面,导向工作面与该基准面间的位置精度。
对于不同的机床夹具,对于夹具的具体结构和使用要求,应进行具体分析,订出具体的技术要求。设计中可以参考机床夹具设计手册以及同类的夹具图样资料。 7.对零件编号,填写标题栏和零件明细表:
每一个零件都必须有自己的编号,此编号是唯一的。在工厂的生产活动中,生产
9 沈阳理工大学应用技术学院机械制造装备课程设计说明书
部件按零件编号生产、查找工作。
完整填写标题栏,如装配图号、名称、单位、设计者、比例等。
完整填写明细表,一般来说,加工工件填写在明细表的下方,标准件、装配件填写在明细表的上方。注意,不能遗漏加工工件和标准件、配套件。 8.机床夹具应满足的基本要求包括下面几方面:
1)保证加工精度 这是必须做到的最基本要求。其关键是正确的定位、夹紧和导向方案,夹具制造的技术要求,定位误差的分析和验算。
2)夹具的总体方案应与年生产纲领相适应 在大批量生产时,尽量采用快速、高效的定位、夹紧机构和动力装置,提高自动化程度,符合生产节拍要求。在中、小批量生产时,夹具应有一定的可调性,以适应多品种工件的加工。
3)安全、方便、减轻劳动强度 机床夹具要有工作安全性考虑,必要时加保护装置。要符合工人的操作位置和习惯,要有合适的工件装卸位置和空间,使工人操作方便。大批量生产和工件笨重时,更需要减轻工人劳动强度。
4)排屑顺畅 机床夹具中积集切屑会影响到工件的定位精度,切屑的热量使工件和夹具产生热变形,影响加工精度。清理切屑将增加辅助时间,降低生产率。因此夹具设计中要给予排屑问题充分的重视。
5)机床夹具应有良好的强度、刚度和结构工艺性 机床夹具设计时,要方便制造、检测、调整和装配,有利于提高夹具的制造精度。
10 沈阳理工大学应用技术学院机械制造装备课程设计说明书
结论
在这次历时两个礼拜的课程设计中,发现自己在理论与实践中有很多的不足,自己知识中存在着很多漏洞,看到了自己的实践经验还是比较缺乏,理论到实践的能力还急需提高。让我认识到了仔细认真的重要性。
这次课程设计让我们更能注意到细枝末节。这次课设使我对机床夹具设计有了更深刻的理解,特别使其中的技术要求。同时感觉到了细节的重要性。有时候我们我们错的并不是理论,而是我们很容易忽略的线型和该删掉的线我们没有删掉。作为一个设计者不仅应掌握良好的专业知识,有一个认真仔细的心态,还有有一个冷静的心态,遇到问题不能慌乱,不知所措
首先根据工件的加工要求,我选择了钻床,因此加工方向式垂直与水平面的。然后工件主要定位部分为直径为φ30mm的中心孔和一侧端面,用长销小平面定五个自由度。虽然没有满足六个自由度的要求,但是不影响机床夹具的工作。因为被加工件需要钻2个孔不限制Z向的旋转会增进效率。最后是将定位销和支承板固定在夹具体上,利用销定位、螺柱、螺母和内六角螺钉进行定位、夹紧。这样将工件稳固的夹紧在机床上,能更方便,准确的进行钻孔加工。通过以上这些步骤,此机床夹具可以正常工作,此项设计方案可实施。通过精度验算可知,此项机床夹具可施行。工件的定位、夹紧符合要求。
在设计的过程中,虽然感觉到了我的不足之处,但是我也学到了不少东西。在一定程度上,使我对以前学习过的东西有了加深理解和熟练操作。课程设计是机械专业学习的一个重要的、总结性的理论和实践相结合的教学环节,是综合运用所学知识和技能的具体实践过程。通过本次夹具设计,我对所学的专业知识有了更深刻的理解和认识。课程设计内容源于生产实践,使得课程设计和实践得到了充分的结合,有利于培养解决工程实际问题的能力。上学期在沈飞进工厂实习或参观的时候对夹具也有所了解,而这次课程设计的经历,使我对夹具有了更深刻的认识
我们在这次的学习实践中看到了自己的不足,同时发现到自己的一个不足,意味着我们成长了一点,如果我们每天成长一点点,那么我们会稳扎稳打的走向成功。
11 沈阳理工大学应用技术学院机械制造装备课程设计说明书
致谢
为期两周的课程设计转眼就过去了。通过这两个星期的课程设计,使我综合的运用了几年所学的专业知识。在课程设计中,发现自己在理论与实践中有很多的不足,自己知识中存在着很多漏洞,看到了自己的实践经验还是比较缺乏,理论到实践的能力还急需提高。
首先,感谢学校给我们提供这次难得的实习机会,这让我真切的体会到理论与实际相结合的意义,为我今后的机械制造技术设计思路奠定了基础。从次课程设计中能让我们学习到一些课本中不能引起我们注意的细节东西,感谢学校为我们提供的宝贵学习机会!
我非常感谢我的指导教师张福老师。两周来,我时刻体会着老师严肃的科学态度,严谨的治学精神,精益求精的工作作风,不论天气有多么的炎热,都会在我们身边细心指导。在课外时间,我们不明白一些设计的问题和有关画图方面的问题时,每次去老师那里,老师都会在百忙之中给我们足够的时间去问问题,有时还会和我坐下来一起讨论设计的方案。当我的提出的方案不是经济实用的时候老师会细心讲解给予更好的意见。整个过程,老师都倾注了大量的心血。正是在老师科学、严谨的指导下,我的课程设计才能顺利进行,这篇论文也才得以顺利完成。老师不仅在学习上对我严格要求,在我们的思想行为上都给予了教育与指导。
这次课程设计虽然我完成的不是很成熟,但是通过老师的帮助和自己的努力完成课程设计还是让我有一种自豪感,这是我自己真的去思考,设计,查询资料得来的成果。在这次课程设计结束的时候,我感到有一种轻松感,不是因为课程设计不用再做了,而是因为我从这次课程设计中获得了知识,有所学、有所用。更加知道我们将来能做什么,会做什么,该做什么。让我们对行业有了了解,让我们对自己的未来有了规划。
感谢老师的细心指导!
12 沈阳理工大学应用技术学院机械制造装备课程设计说明书
参考文献
[1] 作者:吴宗泽,罗圣国,书名《机械设计课程设计手册》,出版者:高等教育出版社,出版年:1999,引用部分起止页:37~46。
[2] 作者:李庆余,书名《机械制造装备设计》,出版者:机械工业出版社,出版年:2008年,版次:2版
[3] 作者:张海华,书名《机械制造装备设计指导书》 ,出版者:机械工程系,引用部分起止页:44~46页。
[4] 作者:薛源顺,书名《机床夹具图册》 ,出版者:机械工业出版社, 出版年2003年,版次:1版
推荐第7篇:毕业设计夹具
安徽机电职业技术学院
毕 业 设 计
课题: 偏心轴承夹具设计
系 (部):
机 械 工 程 系
专 业: 机械制造与自动化 班 级: 机自3082 姓 名: 周 润 之
学 号: 1204083095 指导教师: 王 甫
2011 ~ 2012 学年第 一 学期 毕 业 设 计 任 务 书
专业:机械制造与自动化 班级:机自3092 学生:葛日龙 一:设计题目:
螺纹球形轴工艺设计 二:设计内容:
设计螺纹球形轴加工工艺,用数控车床加工;
根据要求,选择机床、刀具、夹具、毛胚,编写加工程序。加工零件。
绘制加工工艺图 制作加工工艺卡片 三 原始文件
规定设计要求的图纸一张
四:完成日期:2012 年 2 月 28 日
指导教师:
年 月 日签发
目 录
前言…………………………………………………………………………………1 摘要(包括关键词)………………………………………………………………1 第1章 概述………………………………………………………………………1 1.1零件图的分析……………………………………………………………11 1.2 机床选择分析……………………………………………………………1 1.3夹具选择分析……………………………………………………………3 第2章 选择工艺方案....................................................6 2.1 分析加工对象 ……………………………………………………………… 4 2.2零件工艺性分析…………………………………………………………6 2.3制订夹具设计方案…………………………………………………………6 第3章 定位误差确定……………………………………………………………14 3.1 定位误差分析和确定………………………………………………………14 3.2 定位元件设计………………………………………………………………1 3.3 定位误差分析与计算…………………………………………………………14 3.4 定位误差的校核……………………………………………………………1 第4章 夹紧力确定…………………………………………………………………1
4.1 工件夹紧力的分析…………………………………………………………1 4.2 夹紧装置的设计……………………………………………………………1 4.3 夹紧力的计算………………………………………………………………1 4.4 夹紧力的校核………………………………………………………………1 第5章 定位元件的设计……………………………………………………………
1(这些由学生自己设计而定,有的可以有,有的可以没有) 5.1 机架设计……………………………………………………………………1 5.2 钻模板设计…………………………………………………………………1 5.3 定位盘设计…………………………………………………………………1 5.4 可换钻套设计………………………………………………………………1 5.5 定位销、开口垫片及垫片设计……………………………………………1 毕业总结…………………………………………………………………………… ……18 致谢……………………………………………………………………………………19 参考文献…………………………………………………………………………………20 附录一(夹具零件图纸)………………………………………………………………21 附录一(夹具零件的加工工艺卡)……………………………………………………21
叫学生按照这个目录搞,内容可以自行加减,大约30页左右纸即可。 图纸要拼起来要有一张A0图纸大即可。
这里的内容有很多不合适的地方,请自行根据情况更改,目录大致按照这个,自行调整。
按照这个目录来,内容是拼凑的,参考一下。
前 言
毕业设计是我院大学的全部基础课、技术基础课之后进行的,这是我们在对所学课程的深入综合性的总复习,也是一次理论联系实际的训练,突出综合素质的培养,并注意加强专业知识的广度,积极吸纳新技术,体现了应用性、实用性、综合性和先进性。因此,它在我们的大学生活中占有重要的地位。在这次毕业设计之我通过在毕业工作前的这次综合性训练,使我在下面几方面中得到了很好的锻炼:
(1)通过本次设计课程的学习,我掌握了冲压弯曲工艺过程设计及模具设计过程的基本方法,合理选择、使用和维护冲压设备,具有设计中等复杂程度冲压见的冲压工艺及模具的能力。
(2)分析零件工艺了解并运用冷冲模课程中的基本理论知识以及在冷冲压生产实习中学到的实践知识,正确地解决一个零件在加工中的工艺尺寸确定等问题。
(3)提高了结构设计能力。通过设计冷冲模的训练,根据被加工零件的加工要求,能设计出高效,经济合理且能保证加工质量的模具的能力。
(4)掌握基本技能训练得到提高,如分析计算,绘图以及合理的选择符合零件加工要求好的方法。
(5)提高了我在模具设计中如何解决问题、如何分析问题的能力。 对我个人而言,我希望通过学校这次毕业设计对我三年来所学是专业课程进行一次适应性训练,从中锻炼自己发现问题、分析问题和解决问题的能力,为今后参加祖国的建设打一个良好的基础。
由于个人能力有限,设计尚有许多不足之处,恳请各位老师给予指教,本人将表示真诚的感谢!
摘要
本设计说明书是围绕着该零件所设计的偏心轴承夹具,是钻床专用夹具。 夹具的材料为Q235,精度等级为自由公差,即IT14级。可换钻套的材料为45钢,表面渗碳。本设计说明书是以正确的参数、表格和插图对夹具进行解析和参照,是一本图文并茂的设计说明书。 本偏心轴承夹具的设计是先对其进行工艺分析、计算,然后再以计算的数据及参考夹具国家标准画出装配草图、零件图等等。由于该零件的外形结构可视为圆形,钻模的构造应该选用带分度装置的回转式钻模; 该夹具具有一定的通用性,生产效率高,精度一般,操作方便及易安装和维修,可以更换钻套、钻模板、定位盘、开口垫片和定位销。制造简单、成本低,安装简单,使用时工件与定位盘的配合精度要求较高,且要保证机架与定位盘的润滑度,夹具寿命较低。
关键词:
通用性、经济性、可行性。 1.
推荐第8篇:夹具课程设计
课程设计说明书
课 程 名 称 机械制造装配设计
设 计 课 程 钻模夹具设计 专 业 机械设计制造及其自动化 姓 名
年 月 日
课 程 设 计 任 务 书
机械械工程 系 机械设计制造及其自动化 专业 学生姓名 班级 学号
课程名称: 机械制造装备设计 设计题目: 钻模夹具设计
课程设计内容与要求:
设计内容:钻削夹具装配图一张,零件图一张。 要求:
1、设计(装配图按夹具要求设计,相关的配合尺寸要标明,在说明书中要有夹具定位计算,夹紧等方案的选择)。
2、零件图要符合工程图的根据要求,图纸的标题要有材料。
设计(论文)开始日期 年 月 日 指导老师
设计(论文)完成日期 年 月 日
年 月 日
1
课 程 设 计 评 语 第 页
机械械工程 系 机械设计制造及其自动化 专业 学生姓名 班级 学号
课程名称: 机械制造装备设计 设计题目: 钻模夹具设计
课程设计片篇幅:
图 纸 共 2 张
说明书 共 16 页
指导老师评语:
年 月 日 指导老师
2
目 录
序言................................................................................................................................1 第一章 设计准备工作..................................................................................................2
1.1 设计前的准备工作 .........................................................................................................2
1.1.1明确工件的年生产纲领 ....................................................................................2 1.1.2 机床的选择 .......................................................................................................2 1.2 熟悉工件图 .....................................................................................................................2
第二章 夹具设计..........................................................................................................4
2.1 定位方案 ...........................................................................................................................4
2.1.1 定位基准的选择 ...............................................................................................4 2.1.2 定位元件的布置 ...............................................................................................5 2.2 结构方案 .........................................................................................................................5
2.2.1 夹具体设计 .......................................................................................................5 2.2.2 分度装置设计 ...................................................................................................7 2.2.3 对刀—导向装置设计 .......................................................................................8 2.2.4 加紧装置设计 ...................................................................................................9 2.3 夹具装配图的绘制 .......................................................................................................10 2.3.1 夹具装配图上尺寸、公差的标准 .................................................................10 2.3.2 夹具公差与配合的选择 .................................................................................11 2.3.3 夹具装配图上形位公差的标准 .....................................................................11 第三章 方案设计论证................................................................................................14
3.1 设计思路 .......................................................................................................................14 3.2 设计方法与结果 ...........................................................................................................14 致谢..............................................................................................................................15 参考文献......................................................................................................................16
1
序言
本课程设计的目的:
1、运用已学过的机床夹具设计及有关课程的理论知识以及生产实习中所获得的实际知识,根据被加工零件的要求,设计既经济合理又能保证加工质量的夹具。
2、培养结构设计能力,掌握结构设计的方法和步骤。
3、学会使用各种手册、图册、设计表格,规范等各种标准技术资料,能够做到熟练运用机械制造技术课程中的基本理论,正确的解决一个零件在加工中的加工基准的选择、定位、夹紧等。
4、进一步培养机械制图、结构设计、等基本技能。专用夹具设计的基本要求 :
1、夹具设计应满足零件加工工序的精度要求。
2、应能提高加工生产率。
3、操作方便、省力、安全。
4、具有一定使用寿命和较低的夹具制造成本。
5、具有良好的结构工艺性:便于制造、检验、装配、调整、维修。机床夹具在机械加工中起着十分重要的作用,归纳起来,主要表现在以下几个方面。
1、缩短辅助时间,提供劳动生产率,降低加工成本。
2、保证加工精度,稳定加工质量。
3、降低对工人的技术要求,减轻工人的劳动强度,保证安全生产。
4、扩大机床的工艺范围,实现“一机多能”。
5、在自动化生产和流水线生产中,便于平衡生产节拍。
1
第一章 设计准备工作
1.1 设计前的准备工作
1.1.1明确工件的年生产纲领
企业在计划期内应当生产的产品产量和进度计划称为生产纲领。企业根据市场需求和自身的生产能力决定生产计划。
该产品年产量为1000件,其设备品率为2%,机械加工的废品率为3%。
N=Qn(1+α%)(1+β%)=1000*1*(1+2%)(1+3%)=1051
该工件的年产量为1051件,其属于轻型零件。故生产类型属于中批生产。
1.1.2 机床的选择
夹具与机床的连接方式,主要可以分为以下两大类:第一类属于夹具安装在机床的回转主轴上。第二类属于夹具安装在机床的工作台上。
根据工件设计要求,此工件要求加工3-Φ16H7的孔。因此该夹具设计应选用第二类连接方式。查《机床夹具设计手册》,选用Z525-1立式钻床。
1.2 熟悉工件图
工件图应该无遗漏地给出制造零件所需的全部信息,包括几何形状、全部尺寸、加工面的尺寸公差、形状公差和表面粗糙度要求、材料和热处理要求、其他特殊技术要求等。
该工件的工件图如下:
2
已知该工件的材料为HT200,加工3–Φ16H7(其它工序已经加工完成)。
3
第二章 夹具设计
2.1 定位方案
2.1.1 定位基准的选择
加工时,使工件在机床上或夹具上占据一正确位置所依据的基准称为定位基准。分析该工件所要加工的孔,该孔与Φ32H7孔之间的距离为60±0.2mm,又是工件的测量基准,这样设计基准与工序基准重合。因此确定该孔的中心线为定位基准。
4
2.1.2 定位元件的布置
为了限制其自由度,定位元件的布置有一下三种方案: 1)、方案一:用一个圆柱销伸入Φ32H7mm孔中限制了两个自由度,用一个支承板支承A面这样限制了三个自由度,用一个浮动圆柱销伸入Φ16H7mm的孔中限制了两个自由度。显然此方案不能满足“六点定位”原理,出现了过定位,并且加工时比较费时需不断移动工作台。
2)、方案二:用一个圆柱销伸入Φ32H7mm孔中限制了两个自由度,用一个支承板支承A面这样限制了三个自由度,用一个浮动V形块限制Φ40的外圆表面。虽然V形块有对中作用,但是其外圆表面没有进行任何加工,其不能保证加工精度的要求。
3)、方案三:用一个圆柱销伸入Φ32H7mm孔中限制了两个自由度,用一个支承板支承A面限制了三个自由度,用一个浮动菱形销伸入Φ16H7mm孔中限制一个自由度。很明显此时满足了“六点定位”原理,在加工完一个孔后,旋转工件90度,在其位置安装一个菱形销用其定位,之后加工第二个孔,以此类推加工第三个。此方案不仅能满足“六点定位”原理,还缩短了加工时间。
在以上三个方案中,第
一、二种方案不能采用;第三种方案使定位误差等于零,其结构比前两种方案复杂,但中批量生产的条件下来看,第三种方案较合适。
2.2 结构方案
2.2.1 夹具体设计
夹具体是夹具的基础体,它将夹具上的各种装置和元件连接成一个整体,并通过它将夹具安装到机床上。它的结构形状及尺寸大小,取决于加工工件的特点、尺寸大小,各种元件的结构和布局,夹具于机床的连接方式,切削力、重力等大小的影响。
夹具体应满足以下几点计算要求:
1、应有足够的强度和刚度。
2、力求结构简单及装卸工件方便 。
3、结构工艺形好。
4、排屑切屑要方便。
5、在机床上安装稳定可靠。
6、具有适当的精度和尺寸稳定性。
夹具体毛坯可以分为四类:
1、铸造夹具体。铸造夹具体如图2-1(a)所示。
2、焊接夹具体。焊接夹具体如图2-1(b)所示。
3、锻造夹具体。锻造夹具体如图2-1(c)所示。
4、装配夹具体。装配夹具体如图2-1(d)所示。
5
(a)
(b)
(c)
(d)
图2-1 夹具体毛坯的类型
6
分析工件本次夹具体的设计采用装配式夹具体,这样可以降低生产成本,减少生产周期,并且精度稳定。
2.2.2 分度装置设计
为了易于保证加工表面间的位置精度,或减少装夹次数,提高生产率,通常多采用分度加工的方法。即在完成一个表面加工以后,依次使工件随同夹具的可动部分转过一定角度或一定距离,对下一个表面进行加工,直至完成全部加工内容,具有这种功能的装置称为分度装置。
按分度的运动形式可以分为回转式和直线移动式两类:
1、回转分度装置。
2、直线分度装置。
对于本工件来说,该工件体积较小,质量较轻,易于手动操作。在夹具设计中,该夹具为单件加工。这样可以提供以下几个方案。
1)、方案一:利用伸入Φ32的圆柱销当做旋转装置,进行手动旋转。分别用浮动菱形销和夹具体底座上的菱形销当做定位装置。
2)、方案二:用浮动菱形销定位Φ16H7的孔,在A面上安装一个旋转装置,使之与Φ16H7的一起旋转。在旋转装置上进行定位。
3)、方案三:在夹具体底座上安装三个浮动菱形销,手动旋转工件,依次对Φ16H7的孔进行定位。
由于加工的工件体积较小质量较轻且夹具为单件生产,不宜采用较复杂的夹具。在上述三个方案中属方案一比较简单,因此采用方案一的方案。
7
2.2.3 对刀—导向装置设计
对刀装置由对刀块和塞尺组成。借助对刀装置可以迅速而准确地确定夹具与刀具的相对位置。
导向装置用于在钻、镗类机床上加工孔和孔系时对刀具进行导向,引导元件主要有钻模和镗模。借助于引导元件可提高被加工孔的几何精度、尺寸精度以及孔系的位置精度。
这次加工是对孔系的加工,因此选取导向装置。 钻套按其结构和使用特点可以分为以下几种类型。 1)、固定钻套。如图2-2(a)和图2-2(b)所示,固定钻套分为A型和B型两种。钻套安装在钻模板或夹具体中,其配合为H7/n6或H7/r6.固定钻套的结构简单,钻孔精度高,适用于单一钻孔工序和小批生产。
2)、可换钻套。如图2-2(c)所示,当工件为单一钻孔工序的大批量生产时,为便于更换磨损的钻套,选用可换钻套。钻套于衬套之间采用F7/m6或H7/m6配合,衬套与钻模板之间采用H7/n6配合。当钻套磨损后,可卸下螺钉,更换新的钻套。螺钉能防止加工时钻套的转动,或退刀时随刀具自行拔出。
3)、快换钻套。如图2-2(d)所示,当工件需钻、扩、铰多工序加工时,为能快速更换不同孔径的钻套,应选用快换钻套。快换钻套的有关配合同可换钻套。更换钻套时,将钻套削边转至螺钉处,即可去钻套。削边的方向应考虑刀具的旋向,以免钻套随刀具自行拔出。
(a) 固定钻套
8
(c) 可换钻套
(d) 快换钻套
图2-2 标准钻套
由于钻孔只能到达IT10~IT13精度,不能达零件所要求的IT7精度,零件所钻孔径为Φ16mm,钻、扩两次便能达到所要求精度,因此需要快换钻套。
2.2.4 加紧装置设计
工件定位后将其位置固定下来,称为夹紧。设计夹紧装置应遵循以下原则:
1、工件不移动原则;
2、工件不变形原则;
3、工件不振动原则;
4、安全可靠原则;
5、经济实用原则。
设计夹紧装置时,夹紧力的确定包括夹紧力的方向、作用点和大小三个要素。 1)、夹紧力的方向
9
夹紧力的方向要有利于工件的定位,并注意工件的刚性方向,不能使工件有脱离定位表面的趋势,防止工件在夹紧力的作用下产生变形。
2)、夹紧力的作用点
夹紧力的作用点应选择在定位元件支承点的作用范围内,以及工作刚度高的位置。确保工件定位准确、不变形。
3)、夹紧力的大小
夹紧力的大小,对于保证定位稳定、夹紧可靠,确定夹紧装置的结构尺寸,都有着密切的关系。夹紧力的大小要适当。
在实际设计中,常采用估算法、类比法和试验法确定所需的夹紧力。当采用估算法确定夹紧力时,其公式为
FwkKFw
式中
Fwk——实际所需夹紧力,N;
Fw——在一定条件下,由静力平衡算出的理论夹紧力,N;
K——安全系数,粗略计算时,粗加工取K=2.5~3,精加工取K=1.5~2。
夹紧机构的旋转 1)、方案一:在Φ50mm圆柱上表面采用开口垫圈的螺旋夹紧机构。 2)、方案二:在Φ50mm圆柱外圆表面利用夹紧机构夹紧外圆。
由于本工件体积较小质量较轻,在加工工件时为单件生产,劳动强度不大。为了是夹紧力的方向与切削力、重力同向,则夹紧力在Φ50mm的轴心上,因此可以选用螺母夹紧。
2.3 夹具装配图的绘制
夹具装配图的绘制,是在夹具结构方案草图经过老师审定之后进行的。 夹具的总装配图应按国家制图标准绘制,绘制比例尽量采用1:1。主视图应按操作者的视线方向绘制。总装配图应将夹具的工作原理、各种装置的结构及其互相关心表达清楚。在完整地表达出夹具工作原理和构造的基础上,视图的数量尽可能少。
2.3.1 夹具装配图上尺寸、公差的标准
一般说来,在夹具总装配图上应标注的基本尺寸和公差有以下几种: 1)、夹具的轮廓尺寸
指夹具的最大轮廓尺寸。当夹具结构中有可动部分时,应包括可动部分处于极限位置时,在空间所占的尺寸。
2)、影响定位精度的尺寸和公差
主要指工件与定位元件及定位元件之间的尺寸、公差。
3)、影响对刀精度的尺寸和公差
主要指刀具与对刀或导向元件之间的尺寸、公差。
4)、影响夹具在机床上的安装精度的尺寸和公差
主要指夹具安装基面与机床相应配合表面之间的尺寸、公差。
10
5)、影响夹具精度的尺寸和公差
主要指定位元件、对刀元件、安装基面三者之间的位置尺寸和公差。
6)、其他重要尺寸和公差
主要指定位元件、对刀元件、安装基面三者之间的位置尺寸和公差。
2.3.2 夹具公差与配合的选择
夹具尺寸会直接影响工件加工精度,取其公差为
j~k
35式中
j——夹具装配图上的尺寸公差或位置公差;
11k——与j相应的工件尺寸公差。
2.3.3 夹具装配图上形位公差的标准
1)、钻套轴线相对于定位表面(或轴线)的平行度、垂直度、对称度。 2)、钻套轴线相对于底座底平面的垂直度。 3)、处于同一圆周位置上的钻套所在圆的圆心相对定位元件的轴心的同轴度。
4)、活动定位件的对称中心线相对定位元件、钻套轴心线的位置度。
11
12
13
第三章 方案设计论证
3.1 设计思路
1)、首先根据已知工件的需要,选择加工机床,应选用立式钻床加工比较合理。
2)、工件主要定位部分为Φ32mmH7的圆孔轴心以及Φ16H7的圆孔,我设想用长销小平面组合与菱形销定位,这样虽限制了五个自由度,但可以满足定位要求。
3)、最后将长销小平面组合固定在一块底板上,长销小平面组合与菱形销定位后,利用内六角螺钉和定位销定位进行夹紧,工件的夹紧力的方向垂直与工件的轴线方向,作用点为轴线上。
3.2 设计方法与结果
1)、首先对工件的加工要进行分析,已知工件上钻3-Φ16H7的孔,根据工件的形状和加工要求,采用钻床比较合理。
2)、在定位方面,采用了长销小平面组合与菱形销定位方式,仅限制了五个自由度,但满足了定位要求。所以只需要将工件夹紧就可以进行加工了,在垂直方向上进行夹紧。利用六角螺母拧紧的方式进行夹紧,由于工件是中批量生产,并且此方式简单使用,而且不影响加工过程,所以最总选择此方案进行夹紧。
3)、最后,对整个夹紧方案分析得出,定位可靠,夹紧工件稳定,所以此夹具设计可行。
14
致谢
本次课程设计是在指导老师的关怀和悉心的指导下完成的。他严谨的治学精神,严肃的科学态度,精益求精的工作作风,深深的感染了我。在指导老师的指导和关心下,我才有信心更好的完成此次课程设计。
机械制造装备课程设计是学完了机械制造装备设计和大部分专业课,并进行了生产实习的基础上进行的又一个实践性教学环节。这次课程设计过程中我遇到了不少的困难,在老师的帮助和在图书馆查阅资料下,最终解决了困难。
这次课程设计使我们能综合运用机械制造技术基础中的基本理论,并结合生产实习中学到的实践知识,独立地分析和解决了零件机械制造问题,设计了机床专用夹具这一典型的工艺装备,提高了结构设计能力和独立解决问题的能力,为今后的毕业设计及未来从事的工作打下了良好的基础。
15
参考文献
1.赵雪松 《机械制造装备设计》 武汉:华中科技大学出版社,2011.1 2.王先逵 《机械制造工艺学》 北京:机械工业出版社,2011.6 3.吴拓 《简明机床夹具设计手册》 北京:化学工业出版社,2010.4 4.李名望 《机床夹具设计实例教程》 北京:化学工业出版社,2009.9 5.陈立德 《机械制造装备设计课程设计》 北京:高等教育出版社,2010.8 6.孙恒 《机械原理》 北京:高等教育出版社,2000.8 7.喻子建 8.张玉 9.成大先 10.高小康
《机械设计习题与解析分析》 沈阳:东北大学出版社,2000.6 《几何量公差与测量技术》 沈阳:东北大学出版社,1999.7 《机械设计手册》 北京:化学工业出版社,1999.8 《互换性与测量技术》 北京:高等教育出版社,2002.3
推荐第9篇:夹具毕业论文
目 录
第一章夹具的简单介绍………………………………………….3
1.1夹具的分类„„„„„„„„„„„„„„„„„„„„„„
31.2夹具设计的基本要求„„„„„„„„„„„„„„„„„„3 第二章 汽车前拖钻孔夹具的作用及分析„„„„„„„„„„3
2.1汽车前拖勾钻孔夹具的作用……………………………………….3 2.2汽车前拖钩零件的分析…………………………………………….4 2.3夹具的分析及定案„„„„„„„„„„„„„„„„„„..4 第三章夹具的设计„„„„„„„„„„„„„„„„„„„4
3.1 导向装置设计„„„„„„„„„„„„„„„„„„„„4 3.2钻套类型的选择与设计„„„„„„„„„„„„„„„„„4 3 .3定位元件的确定„„„„„„„„„„„„„„„„„„„„5 3.4加紧装置„„„„„„„„„„„„„„„„„„„„„„„6 3.5 夹具体的结构设计„„„„„„„„„„„„„„„„„„„7 3.6夹具的安装„„„„„„„„„„„„„„„„„„„„„„8 3.7误差分析„„„„„„„„„„„„„„„„„„„„„„„8 第四章 夹具使用注意事项、保养及维护„„„„„„„„„„9 结束语„„„„„„„„„„„„„„„„„„„„„„„„„10
湖南科技工业职业技术学院
【前言】:
1 选题背景
随着生活水平的提高,人们喜欢上了自己开车野外旅行,但这也是用到拖钩机率最大的时候,根据这一状况选择了汽车前拖钩钻孔夹具设计。同时我们也对夹具有一定的了解。
2设计目的
通过对汽车前拖钩钻孔夹具设计,再通过在设计中在的一些规律进行探讨后,提出了在前拖钩钻孔夹具设计中所应该遵循的原则和基本条件。因为在现阶段的生产中,前拖钻孔夹具的设计充满了丰富的特殊性。不管在生产上的还是在使用方面要做到100%的满意是不可能的,所以在设计方面只可能尽量的使在生产或是在使用方来说,做到便捷化、简约化、消耗功率最小化。从而达到生产率的提高,给公司或企业带来更多利润。
2技能成就未来
湖南科技工业职业技术学院
第一章夹具的简单介绍
1.1夹具的分类
夹具的分类我们就以机床夹具为例,机床夹具的种类很多。
1)按使用机床类型分类,可分为车床夹具、铣床夹具、钻床夹具、镗床夹具、加工中心夹具和其他机床夹具等。
2)按驱动夹具工作的动力源分类,可分为手动夹具、气动夹具、液压夹具、电动夹具、磁力夹具、真空夹具和自夹紧夹具等。
3)按专门化程度可分为以下几种类型的夹具:
a通用夹具 通用夹具是指已经标准化、无需调整或稍加调整就可以用来装夹不同工件的夹具。如三爪卡盘、四爪卡盘、平口虎钳和万能分度头等。这类夹具主要用于单件小批生产。
b 专用夹具 专用夹具指专为某一工件的某一加工工序而设计制造的夹具。结构紧凑,操作方便,主要用于固定产品的大批大量生产。
c 组合夹具 组合夹具是指按一定的工艺要求,由一套预先制造好的通用标准元件和部件组装而成的夹具。使用完毕后,可方便地拆散成元件或部件,待需要时重新组合成其他加工过程的夹具。适用于数控加工、新产品的试制和中、小批量的生产。
d可调夹具 可调夹具包括通用可调夹具和成组夹具,它们都是通过调整或更换少量元件就能加工一定范围内的工件,兼有通用夹具和专用夹具的优点。
1.2夹具设计的基本要求
1) 工装夹具应具备足够的强度和刚度 夹具在生产中投入使用时要承受多种力度的作用,所以工装夹具应具备足够的强度和刚度。
2) 夹具应满足零件加工工序的精度 特别对有多次加工工序的工件,提高夹具的精度,以保证工件的尺寸公差和形状位置公差等。
3) 夹具应达到加工生产率的要求 特别对于大批量生产中使用的夹具,应设法缩短加工的基本时间和辅助时间。
3、夹具的操作要方便、安全 按不同的加工方法,可设置必要的防护装置、挡屑板以及各种安全器具。
5、能保证夹具一定的使用寿命和较低的夹具制造成本 夹具元件的材料选择将直接影响夹具的使用寿命。因此,定位元件以及主要元件宜采用力学性能较好的材料。夹具的低成本设计,目前在世界各国都已相当重视。为此,夹具的复杂程度应与工件的生产批量相适应。在大批量生产中,宜采用如气压、液压等高效夹紧装置;而小批量生产中,则宜采用较简单的夹具结构。
第二章 汽车前拖钻孔夹具的作用及分析
2.1汽车前拖勾钻孔夹具的作用
3技能成就未来
湖南科技工业职业技术学院
由于生产的需要,为了提高生产或运输的效率。在必要的情况下汽车的前拖勾钻孔夹具应运而生 ,其主要作用表现在以下几个方面: 1)缩短辅助时间,提高劳动生产率
准确、可靠的定位和夹紧,可以减轻甚至取消下料和划线工作。减小制品的尺寸偏差,提高了零件的精度和可换性。
2)降低对操作工人的技术要求和工人的劳动强度
由于多数专用夹具的夹紧装置只需工人操纵扳手、手柄即可实现对工件的夹紧,这在很大程度上减少了工人找正和调整工件的时间与难度,或者根本不需要找正和调整,所以,这些专用夹具的使用降低了对工人的技术要求并减轻了工人的劳动强度。
2.2汽车前拖钩零件的分析
根据图1可得基准面为上面的两台阶面所在的平面。我们的目的是要钻削φ17mm、φ13mm、Ra3.2粗糙度的两孔,工件材料45#钢,数量为为中批量。两孔的中心距为74mm 。拖钩两台阶边距长为103.5mm。两圆面为φ34mm和φ25mm。
2.3夹具的分析及定案
钻削两孔,主要是考虑的两中心孔距的确定,加紧装置,定位基准。根据零件图1的分析基准面必须为上面的两台阶面所在的平面,这样才能做到零件能够与车子很好的装配。这样我们推出上下加紧装置上面为固定的,下面为活动的螺钉锁紧装置。两中心孔距的确定需设计两钻套定位,其中心距刚好要与需要加工零件的两中心孔距一致。以圆弧面的两最大端和最左端确定纵向和横向定位。纵向的夹击用螺钉锁紧。如此六个自由度我们控制了五个,可以完全满足加工要求。
第三章夹具的设计
3.1 导向装置设计
根据产品加工图纸和产品技术要求,知此套夹具需要在上定位板1上钻两个φ17mm、φ13mm的钻套,其简图如图2所示:
3.2钻套类型的选择与设计
钻套是钻模上的特有元件,用来引导刀具以保证被加工孔的位置精度和提高工艺系统的刚度。
1.钻套类型。钻套可分为标准钻套和特殊钻套两大类。根据需要选用了标准钻套,其中标准钻套分为固定钻套、可换钻套和快换钻套三种。标准钻套其结构参数、材料、热处理等可查“夹具标准”、或“夹具手册”
4技能成就未来
湖南科技工业职业技术学院
图1
图2
根据汽车钱拖钩钻孔加工的需要选用了快换钻套,根据本工件需要及加工效率尺度精度的要求。钻套与钻模之间采用F7/M6或F7/K6配合,当钻完孔后,可换下螺钉,更换新的铰孔钻套,螺钉能防止加工时钻套能动或退钻头时随钻头拔出。
2钻套的导向长度钻套的高度H增大时,则导向性能好,刀具刚度提高,加工精度高,但钻套与刀具的磨损加剧。一般选取H=1-2.5d。(其中d为所加工钻套的孔径)。
3.钻套的尺寸选择:一般钻套导向孔的基本尺寸取刀具的最大极限尺寸,采用基轴制间隙配合,钻孔时取其公差F7或F8,粗铰孔时公差取G7,精铰孔时公差取G6。
4排屑空间h是指钻套底部与工件表面之间的空间。增大h值,排屑方便,但刀具的刚度和孔的加工精度都会降低。由于设计的夹具钻对HT200材料所设计。所以选用h=(0.7-1.5)d。
5钻套的材料选择
由于钻套孔径d≤26mm所以选用45号刚制造,热处理硬度为58-64HRC。生产技术要求为:1.d对D的径向跳动不大于0.01毫米;2.d公称尺寸系刀具的最大尺寸,其允许差为+0.003~+0.013;3.热处理:T10A,淬火HRC60~64;渗碳深度0.8~1.2mm。4.表面发蓝或其它的防锈处理,锐边无毛刺。
3.3定位元件的确定
在选择定位方案时,由于定位方式多种多样,对定位基准、限位基准的确定也有几种不同方
5技能成就未来
湖南科技工业职业技术学院
法,此处采用以下观点: 工件以台阶面上面平面、侧面和圆弧面为定位基准,工件以平面与定位元件接触,此平面就是定位基面,它的理想状态(平面度误差为零)是定位基准。但对于已经加工过的平面,通常忽略其平面度误差,所以认为,定位基面就是定位基准,二者重合;侧面和圆弧面以两v型槽来确定滴定位。即加紧装置为定位三面,夹紧两面,有一面未限定的正好与加工的方向反向。可以不作要求,在夹紧的时候,留有稍微大点的余量即可。其夹紧方式从总装图上可以清晰地看出,在此不在作过多的叙述。
工件的定位误差分析,是设计的重点和难点之一。基准位移误差如:基准不重合误差,构成了定位误差,这些基本概念定义准确严密,在实际的设计过程中需要费一定的时间,用实际例子来说明基准位移和基准不重合这两项误差产生的原因及对加工尺寸的影响,但一涉及到两项误差的合成问题,即定位误差对工序要求的影响,常常容易混淆。与其他定位误差相比较,此夹具取用最基本的定位方式。
定位v型槽加工要求:1.表面发蓝或其它的防锈处理;2.热处理:T10A,淬火HRC60~64;渗碳深度0.8~1.2mm;3.锐边无毛刺。
3.4加紧装置
3.4.1 夹紧基本原理理论
夹紧的目的是保证工件在夹具中的定位,不致因工时受切削力,重力或伴生离心力,惯性力,热应力等的作用产生移动或振动。夹紧装置是夹具完成夹紧作用的一个重要的而不可以缺少的组成部分,除非工件在加工过程中所受到的各种力不会使它离开定位时所需确定的位置,才可以没有夹紧装置。夹紧装置设计的优劣,对于提高夹紧的精度和加工作效率,减轻劳动强度都有很大的影响。
分析各类夹具的基本功能要求可以将夹紧装置概括为两类:第一类是性能要求,主要指定位唯一性、定位稳定性,夹紧稳定性及总体约束;第二类要求是夹具的结构刚性、成本及易操作性、易于维修等要求。本设计目录中功能项包括夹紧对象特征项、加工信息特征及夹紧要求特征。
夹紧对象特征项目:包括夹紧对象类型、材料、形状、体积、数量、物理特性、磁性、导电性、刚性等信息。
加工信息特征项:加工类型、机加工、装配、检测、焊接等、加工参数、切削参数、运动参数、几何参数等。
夹紧要求特征项:主要指性能要求,包括定位要求、定位基准选择,如特征点、特征面。夹
6
技能成就未来
湖南科技工业职业技术学院
紧力大小、夹紧方向、夹紧行程、夹紧松开速率,自锁性等。
元件功能分析:夹紧功能主要包括四种元功能:定位功能、传动功能、执行功能和分度功能等辅助功能。定位功能由定位元件完成,定位元件按定位面特征分为平面定位元件、圆孔定位元件、外圆定位元件。传动功能由中间递力机构完成,该机构一般有三个作用;改变作用力的力一向、大小和自锁作用。目前常用的有以下机构:斜楔机构、螺旋机构、圆偏心机构、杠杆铰链机构、连杆机构、联动机构、对中机构、定心机构等。设计夹紧装置时,应满足下述主要要求:
1)夹紧装置在对工件夹紧时,不应破坏工件的定位,为此,必须正确选择夹紧力的方向及着力点。
2)夹紧力的大小应该可靠,适当,要保证工件在夹紧后的变形和受压表面的损伤不致超出允许的范围。
3)夹紧装置结构简单合理,夹紧动作要迅速,操作方便省力,安全。 4)夹紧力或夹紧行程在一定范围内可进行调整和补偿。
3.4.2加紧装置的设定
使用螺钉加紧,既简化夹具的成本又适应实际生产情况。计算螺钉的夹紧力:W=2QL/ D中/tg(α+φ1)。此公式采用中的数据以M16标准螺纹计算。
α为螺纹升角;tgα=S/лD中; φ1螺纹摩擦角;D中螺纹中径;Q人工作用力;其中有f=0.1(螺母端面与工件间的摩擦系数),φ1=6°34\';计算W=836.8公斤力。很明显这个力足以使零件加紧。
这里的加紧螺钉,根据公司的实际情况选用夹紧螺钉,在其上面做微小改变即可。如在横向加紧中需在螺钉上面焊接一个v形槽来定位加紧圆弧面;在上下加紧中可以直接旋紧使之加紧并起到承受主要压力的作用。这样可以节省成本,制造夹具的时间缩短并以国家标准的规格生产。
夹紧功能的原理方案设计目录是设计目录应用的具体体现,由于夹具种类繁多,如何对其进行抽象化整理,以利于运用设计目录的结构形式,还需要更深入的研究。建立原理方案设计目录涉及的知识面较广,难度较大,目录本身的构造规律也很复杂。这里仅作最基本的原理方案设计研究。
3.5 夹具体的结构设计
夹具体整体轮廓尺寸如下:底座尺寸即板1等于160x110x10毫米,上有4个螺钉孔,上螺
7
技能成就未来
湖南科技工业职业技术学院
钉柱之用,;上贴板尺寸160x110x10毫米, 两个分别为直径为19mm和直径23mm的钻套空孔;中间板2为160x110x10mm,上装有上下的紧固螺钉,m16的;各螺钉柱为m16,肩宽为10mm主要使三板牢固连接,并起到三块板的定位作用;V型槽尺寸为60x50x28mm,其用m10的螺钉固定与板2左端上用来定位零件的左端面;挡板40x40x28毫米也用m10螺钉固定于板2上,主要起到横向定位;此模型是取用最基本的,最简单的大众化模型。夹紧拟取方案:吃零件为钻床加工,所以其夹具所受到力不是很大,所以可以用螺钉加紧和支撑,此设计的好处是装夹工件方便。上贴板上还需焊接一个为m10的紧固螺钉。具体如后面图所示。
3.6夹具的安装
当夹具的各个零件生产出来后,就要对它进行安装。安装夹具看起来是非常简单的事情,但是不同的人安装同样的夹具,其安装的夹具误差都不一样。(从瑞士手表的安装准确度,其秒针走时误差一年相隔一秒与一星期相隔一秒的例子得启示)公司有专人安装夹具的队伍,在某些程度上提高了安装精度。在安装夹具的过程中要注意一些事项:
1)先把各个面上的零件根据制作标准装上去。
2)再一次连接好三块面,必须板与板之间要平行,跟据要使之达到设计要求。
3)垫铁留有余量,在安装上去后,等检验精度的时候再磨削部分余量至达到要求。按照磨损规则是尽量的初次磨削最少的余量,可以使使用时间加长,减少成本。
4)衬套用专用的夹钳装入,实际装入时应有一定的阻力,最佳效果是一次性装入。钻套以旋转的方式逐渐装入,当装入大约2/3时候旋出,再完全装入。
5)定位柱套入后即旋紧螺母,当需要调整精度时再作更换,一般情况是不需要调整和更换的。
3.7误差分析
3.7.1定位误差分析
工件的定位就是使同一工序中的所有工件逐次放置到夹具中,使之占有正确的位置的工艺过程。一批工件逐个在夹具中定位时,由于定位基准与工序基准不重合、定位副制造不准确等原因,使得各个工件在夹具中占据的位置不可能完全一致,势必产生定位误差,即工件在夹具中因定位不准确而产生的工件加工误差。
定位误差实际上是一批工件采用调整法加工时,由于定位所造成的工件加工面相对于工序基准的位置误差。假定在加工时,夹具相对于刀具及切削成形运动的位置经调整后不再变动,那么
8
技能成就未来
湖南科技工业职业技术学院
可以认为加工面的位置是固定的,这样工件加工面相对于其工序基准的位置误差就是由于工序基准的位置变动所引起的。所以,定位误差也就是工件定位时工序基准在工序加工要求(位置尺寸或位置精度)方向上的位置变动量。
应用夹具CAD系统设计夹具时,在未选定夹具定位方案的具体结构之前,尚不能建立定位尺寸链。在系统确定了夹具定位结构之后,就可以根据具体结构建立定位尺寸链进行正计算或反计算。a)正计算就是当已知定位结构中有关定位元件尺寸的公差时,用定位尺寸链求解封闭环公差(即定位误差)。如果所求的定位误差值在允许的公差范围之内,则表明所确定的定位元件的尺寸公差能满足精度要求。否则不能保证精度,就需调整定位结构中定位元件的尺寸公差。如果这些公差无调整的余地则需考虑重新确定定位结构。b)反计算就是已知封闭环的尺寸及公差,确定各组成环的公差,即将允许的定位误差合理地分配到各组成环中去。
3.7.2装备误差分析
“机床夹具装配调整及夹具精度检验”实验,认识到夹具制造工艺特点和工件加工精度的保证方法,认识到夹具总装图公差配合与技术要求的实际意义。从而使我在进行夹具设计时明白到底应标注哪些技术要求有其意义。
安装误差与定位误差:在应用夹具安装工件时,往往由于下列几种因数引起工件的安装误差: 1.夹具本身的误差; 2.夹具在机床上的安装,调整误差; 3.夹紧时,整个夹具或其它元件受力后产生弹性变形; 4.工件的定位基准与定位元件接触后的变形; 5.由于工件的定位基准与设计基准不重合而引起的误差; 6.由于工件的定位基准面与定位元件之间的间隙引起的工件可能的最大的位移。
小结:在实际工作中,应多读些典型机床夹具总图,多调试一些夹具,多了解一些夹具结构方案,从中多学习一些结构工艺性方面的知识,使设计能力有所提高。
第四章 夹具使用注意事项、保养及维护
1)使用前对限位尺寸检查是否还保持正确位置;
2)如果挡销磨损超差,可以进行打磨修复;如果挡板、插销、定位锥头销磨损超差,可以
9技能成就未来
湖南科技工业职业技术学院
重新组装,错开磨损部位后继续使用。
3)使用后需要涂防锈油。
4)在操作中不得用锤子、扁錾或其它物品启动按钮和敲击夹具任何部位(夹具有塑料垫片的,工具可放在基准面上,但要轻拿轻放)。
5)严禁在夹具上堆积过多板件,破坏夹具或其它元件。
工装设计的质量,对生产效率、加工成本、产品质量以及生产安全等有直接的影响,为此,设计焊接工装时必须考虑实用性、经济性、可靠性、艺术性等。
在机械设计和制造过程中,普遍存在尺寸链问题。在把零件组装成机器的过程中,也就是将零件上有关的尺寸进行组合和积累。由于零件尺寸存在制造误差,因此装配时也就会有误差的综合和积累。累积后形成的总误差将会影响机器的工作性能和质量。这就形成了零件的尺寸误差和综合误差之间的相互影响关系。设计工装夹具也不例外。合理地确定零件的尺寸公差和形位公差显得很重要。
结束语:通过这一阶段的毕业设计,我受益匪浅,不仅锻炼了良好的逻辑思维能力,而且培养了弃而不舍的求学精神和严谨作风。回顾此次毕业设计,是大学三年所学知识很好的总结。 此次的设计不仅重温了过去所学知识,而且学到了很多新的内容。相信这次毕业设计对我今后的工作会有一定的帮助。所以,我很用心的把它完成。在设计中体味艰辛,在艰辛中体味快乐。 最后,我要衷心的感谢教育过和指导过我的各位老师,感谢给予我帮助的朋友们,谨献上我最真挚的祝福。
【参考资料】
1、《机床夹具设计》肖继德,陈宁平:北京机械工业出版社,2000年
2、《简明机械零件设计使用手册》胡佳秀,北京机械工业出版社,1999年
3、《机械设计基础》孙宝钧,北京机械工业出版社,1995年
4、《机械制图》周鹏翔,北京高等教育出版社,1993年
10
技能成就未来
湖南科技工业职业技术学院
夹紧螺钉
11技能成就未来
湖南科技工业职业技术学院
钻套
12技能成就未来
湖南科技工业职业技术学院
13技能成就未来
推荐第10篇:组合夹具.
国家职业教育机械制造技术专业教学资源库
组合夹具
一、组合夹具的概念:
组合夹具由一套预先制造好的不同形状、不同规格、不同尺寸的标准元件及部件组装而成。
二、分类:
组合夹具分为槽系和孔系两大类
三、组合夹具的元件
①基础件②支承件③定位件 ④导向件⑤夹紧件⑥紧固件 ⑦夹紧件 ⑧合件 ⑨其他新元件和合件
图1 基础件:1-长方形基础件;支承件:2-长方形垫板,3-长方形支承座,4-方形支承座;定位件:6-圆形定位销,7-圆形定位盘,8-菱形定位销;导向件:5-钻模板,9-快换钻套;紧固件:10-钻套螺钉,11-圆螺母,12-槽用螺栓,13-厚螺母,14-特殊螺母,16-埋头螺钉,17-定位螺钉,18-U形垫圈;连接元件:15-定位键。
1
国家职业教育机械制造技术专业教学资源库
图2 组合夹具组装示意图
图2是一个钻转向臂侧孔的组合夹具,工件以孔及端面在圆形定位销
6、圆形定位盘7上定位共限制五个自由度,另一个自由度由菱形定位销8限制;工件用螺旋夹紧机构夹紧,夹紧机构由U形垫圈
18、槽用螺栓12和厚螺母13组成。快换钻套9用钻套螺钉10紧固在钻模板5上,钻模板用螺帽
14、槽用螺栓12紧固在长方形支承座3上。支承座3用槽用螺栓12和螺帽14紧固在长方形垫板2和长方形基础板1上。图2中未标全的件号参见图1。
组合夹具是机床夹具中标准化、系列化、通用化程度最高的一种夹具,其基本特点是:结构灵活多变,元件能长期重复使用,设计和组装周期短。组合夹具的缺点是:体积较大,刚性较差,购置元件和合件一次性投资大。组合夹具适于在单件小批生产中加工那些位置精度要求较高的工件,常在新产品试制和完成临时突击任务中使用。
2
第11篇:夹具验收报告
焊接夹具验收技术要求
一、焊接夹具制造完成后,由乙方提出申请,甲方派出技术人员到乙方的现场进行焊接夹具预
验收。
二、乙方必须提供以下记录,甲方才能进行预验收工作
1、焊接夹具零部件质量检验记录: 1)焊接工装外观质量检验。 1) 尺寸精度检验。 2) 焊接夹具材料及热处理检验。 3) 表面粗糙度检验。
2、焊接夹具装配检验记录。
3、焊接夹具动态检验记录。
4、经过清点的焊接夹具清单。
5、焊接夹具与其对应的夹具仕样书的吻合情况自检清单。乙方根据上述记录整理成焊接夹具自检报告提供给甲方。
三、焊接夹具的预验收
1、预验收依据: 1) 乙方提供并由甲方确认的验收标准。 2) 产品数模。 3) 焊接夹具技术要求。 4) 焊接夹具验收技术要求。
2、预验收程序: 1) 焊接夹具动、静检验见后附表。 2) 焊接夹具动、静检验合格后,在乙方场地进行试焊接,利用合格的冲压件,焊接成一台总
成,如符检验精度标准,则视为焊接夹具预验收合格。
四、对焊接夹具预验收过程中存在的问题及应采取的措施,乙方必须记录并形成文件,且经双方签字确认。若没有形成文件,甲方视为夹具没有经过本次的预验收。
五、包装运输
1、焊接夹具在乙方工厂预验收合格后包装发运,包装箱内附包装清单一份。同时发运焊接夹具设计图纸资料。
2、焊接夹具应进行防水、防锈处理,焊接夹具应装箱,以防止在运输过程中磕碰。
六:焊接夹具在甲方验收时,乙方必须派出技术人员和调整工人到甲方现场进行调试,甲方技术人员配合,在甲方的验收为焊接夹具的最终验收。
七:乙方调试焊接夹具的时间不能影响合同总体进度。
八、焊接夹具的终验收
1、终验收的前提是焊接夹具符合《xxx技术要求》。
2、乙方在甲方场地进行焊接夹具的安装、调试并进行焊接。
3、乙方提供了完整的、符合要求的焊接夹具技术资料。
4、能连续稳定地生产出20台合格的总成,则焊接夹具终验收合格。
九、本附件与合同具有同等法律效力。
十、本附件未尽事宜,双方通过协商解决。
甲方代表签字: 乙方代表签字:
年 月 日 年 月 日
附表:
焊接夹具动、静态检查表
附件九
xxx设计图纸会签确认书
no:01 注:图纸确认依据焊接生产线技术要求及验收技术要求
焊接夹具及检具自检报告
no:02
2、此项目报告由乙方在预验收前全部提供。 xxx预验收确认书 no:04 篇2:夹具验收标准
一、凌云公司长春分分司新产品焊接夹具验收流程
二、焊接夹具制造完成后,由乙方提出申请,甲方派出技术人员到乙方的现场进行焊接夹具预
验收。
二、乙方必须提供以下记录,甲方才能进行预验收工作
1、焊接夹具零部件质量检验记录: 1)焊接工装外观质量检验。 1) 尺寸精度检验。 2) 焊接夹具材料及热处理检验。 3) 表面粗糙度检验。
2、焊接夹具装配检验记录。
3、焊接夹具动态检验记录。
4、经过清点的焊接夹具清单。
5、焊接夹具与其对应的夹具仕样书的吻合情况自检清单。乙方根据上述记录整理成焊接夹具自检报告提供给甲方。
三、焊接夹具的预验收
1、预验收依据: 1) 乙方提供并由甲方确认的验收标准。 2) 产品数模。 3) 焊接夹具技术要求。 4) 焊接夹具验收技术要求。
2、预验收程序: 1) 焊接夹具动、静检验见后附表。 2) 焊接夹具动、静检验合格后,在乙方场地进行试焊接,利用合格的冲压件,焊接成一台总
成,如符检验精度标准,则视为焊接夹具预验收合格。
四、对焊接夹具预验收过程中存在的问题及应采取的措施,乙方必须记录并形成文件,且经双方签字确认。若没有形成文件,甲方视为夹具没有经过本次的预验收。
五、包装运输
1、焊接夹具在乙方工厂预验收合格后包装发运,包装箱内附包装清单一份。同时发运焊接夹具设计图纸资料。
2、焊接夹具应进行防水、防锈处理,焊接夹具应装箱,以防止在运输过程中磕碰。
六:焊接夹具在甲方验收时,乙方必须派出技术人员和调整工人到甲方现场进行调试,甲方技术人员配合,在甲方的验收为焊接夹具的最终验收。
七:乙方调试焊接夹具的时间不能影响合同总体进度。
八、焊接夹具的终验收
1、终验收的前提是焊接夹具符合《xxx技术要求》。
2、乙方在甲方场地进行焊接夹具的安装、调试并进行焊接。
3、乙方提供了完整的、符合要求的焊接夹具技术资料。
4、能连续稳定地生产出20台合格的总成,则焊接夹具终验收合格。
九、本附件与合同具有同等法律效力。
十、本附件未尽事宜,双方通过协商解决。
甲方代表签字: 乙方代表签字:
年 月 日 年 月 日
附表:
焊接夹具静态检查表
焊接夹具动态检查表
附件九
xxx设计图纸会签确认书
no:01 焊接夹具及检具自检报告 no:02 篇3:焊接夹具验收规范(含表格) 焊接夹具验收规范
(iso9001:2015)
一、产品焊接夹具验收流程
二、焊接夹具制造完成后,由乙方提出申请,甲方派出技术人员到乙方的现场进行焊接夹具预验收。
二、乙方必须提供以下记录,甲方才能进行预验收工作
1、焊接夹具零部件质量检验记录: 1)焊接工装外观质量检验。 1) 尺寸精度检验。 2) 焊接夹具材料及热处理检验。 3) 表面粗糙度检验。
2、焊接夹具装配检验记录。
3、焊接夹具动态检验记录。
4、经过清点的焊接夹具清单。
5、焊接夹具与其对应的夹具仕样书的吻合情况自检清单。乙方根据上述记录整理成焊接夹具自检报告提供给甲方。
三、焊接夹具的预验收
1、预验收依据: 1)乙方提供并由甲方确认的验收标准。 2)产品数模。 3)焊接夹具技术要求。 4)焊接夹具验收技术要求。
2、预验收程序: 1)焊接夹具动、静检验见后附表。 2)焊接夹具动、静检验合格后,在乙方场地进行试焊接,利用合格的冲压件,焊接成一台总成,如符检验精度标准,则视为焊接夹具预验收合格。
四、对焊接夹具预验收过程中存在的问题及应采取的措施,乙方必须记录并形成文件,且经双方签字确认。若没有形成文件,甲方视为夹具没有经过本次的预验收。
五、包装运输
1、焊接夹具在乙方工厂预验收合格后包装发运,包装箱内附包装清单一份。同时发运焊接夹具设计图纸资料。 (转载于:夹具验收报告)
2、焊接夹具应进行防水、防锈处理,焊接夹具应装箱,以防止在运输过程中磕碰。
六:焊接夹具在甲方验收时,乙方必须派出技术人员和调整工人到甲方现场进行调试,甲方技术人员配合,在甲方的验收为焊接夹具的最终验收。 七:乙方调试焊接夹具的时间不能影响合同总体进度。
八、焊接夹具的终验收
1、终验收的前提是焊接夹具符合《xxx技术要求》。
2、乙方在甲方场地进行焊接夹具的安装、调试并进行焊接。
3、乙方提供了完整的、符合要求的焊接夹具技术资料。
4、能连续稳定地生产出20台合格的总成,则焊接夹具终验收合格。
九、本附件与合同具有同等法律效力。
十、本附件未尽事宜,双方通过协商解决。
甲方代表签字: 乙方代表签字: 年 月 日 年 月 日
附表:
焊接夹具静态检查表 篇4:夹具预验收标准
试制车间焊装夹具预验收标准 1.共性问题验收 1.1工艺文件验收
1.1.1工艺装备设计图纸 1.1.2所有工位工程图 1.1.3焊装作业指导书 1.1.4工艺装备清单
1.1.5工艺装备自检报告
1.1.6桁架系统的3d数据及图纸 1.1.7吊具与工位器具3d数据集图纸
以上内容在验收前需检查落实 1.2夹具外观标准 1.2.1外观质量
1.2.1.1夹具外观颜色与要求一致,定位块、夹紧块需发黑处理 1.2.1.2夹具油漆喷涂均匀、美观、无锈蚀或油漆脱落 1.2.2夹具铭牌 1.2.2.1夹具铭牌为铜质板材,铆接固定方式,固定牢靠 1.2.2.2铭牌编号清晰,铭牌号与夹具名称一致 1.2.3气动管路
1.2.3.1进气管颜色为蓝色,出气管颜色为黑色,控制为红色,并采用双层阻燃气管 1.2.3.2管路布置要美观有序,且布置在base板的槽钢内 1.2.4叉车标识线
1.2.4.1较大夹具应有叉车标识线,标识线颜色合适 1.2.5推手和脚轮
1.2.5.1推手高度在800—900mm左右,符合人机工程学,管径合适,质量牢靠 1.2.5.2推手可折叠,不影响焊接工作 1.2.5.3脚轮要运动灵活,一端定向,一端万向,万向轮与推手在同侧,脚轮有自锁装置
1.2.6夹具焊缝质量
1.2.6.1夹具与工位器具焊脚高度在3~5mm 1.2.6.2所有焊缝不允许出现虚焊、脱焊,重要部位须采用连续焊缝 1.2.6.3焊后清理焊渣,焊缝打磨平滑 1.3夹具精度 1.3.1三坐标检验
1.3.1.1对部分夹具进行三坐标抽检 1.3.2base板
1.3.2.1 base及连接板等结构件要求采用q235-a板材和型材焊接而成。 1.3.2.2 base板面长度在1m以下时,板面厚度不低于20mm,型材采用14号槽钢;长度在1m~1.5m 时要求面板厚度在25 mm以上,型材采用14号槽钢;base板面长度超过1.5m时,要求面板厚度在30mm以上,型材采用20号以上槽钢 1.3.2.3base应为一整体,其上平面为安装基准面,安装基准面上还应刻坐标网格线;坐标网格
线的深度 0.3~0.4 mm,线距为100~200mm,坐标网格线的平行度误差:相邻单一间隔距0.10/100mm;累积间隔距0.30/全长。 1.3.2.4刻线的两端刻上坐标号,坐标号应与汽车产品图上的坐标号相一致,要求牢固,光滑平
整,无缺陷。base板最大平面度误差要求0.2mm以内。所有安装销孔与加工基准面之间的公差为±0.05mm,销孔内壁粗糙度为ra1.6 1.3.3 定位销、块,夹紧块 1.3.3.1定位面的位置精度控制在±0.2mm以内。 1.3.3.2定位销的位置精度控制在±0.1 mm以内,且同一件上的定位销相对位置公差为±0.2 mm。
1.3.3.3定位块、定位销至少两维可调,调整量为3mm,垫片为0.5mm+0.5mm+1mm+1mm。 1.3.3.4定位销直径的加工精度:直径-0.10 mm,公差为(0.00~-0.05)。 1.3.4调整垫片
1.3.4.1 1+1+0.5+0.3+0.2 1.3.5手持夹具
1.3.5.1手持夹具应易于操作,质量≤2.5kg 1.3.6夹具的作业高度 1.3.6.1夹具的作业高度应在850---900mm,操作时不弯腰或垫脚等 1.4 装配性 1.4.1操作手柄 1.4.1.1所有手动机构操作手柄均有防滑易握装置(防滑套/球);操作手柄与夹具连接牢靠,方
便、省力操作。 1.4.2定位块
1.4.2.1上下定位块与钣金件要完全贴合,定位松紧度配合良好 1.4.3安装螺栓
1.4.3.1安装螺栓采用强度为8.8级 1.4.4安全防护
1.4.4.1 base板,基座等均无锋利锐角 1.4.5运动单元
1.4.5.1所有运动单元运动灵活且不来回晃动 2.功能性问题检查 2.1上件作业性
2.1.1压头打开高度要便于钣金件放入夹具 2.1.2 夹具的结构、动作应便于板件的定位、加紧 2.1.3 对于特殊的钣金件应有导向装置 2.2定位稳定性
2.2.1 定位销定位部分应高出钣金件3—5mm 2.2.2 所有零件都要稳定定位,特别是小零件要完全精确定位、必要时可以过定位 2.2.3 前后工序的定位基准一致 2.3压块稳定性
2.3.1 启动压头运行动作要缓和,代开角度不可超过120°,以免伤人 2.3.2 手动压头压紧时需有死点,打开角度不可超过120°,以免伤人 2.3.3 气缸压紧力要足够,能满足压紧要求,一般不小于30kg力 2.4 定位销
2.4.1 定位销数量与图纸中数量、直径要一致 2.4.2 定位销应双向可调 2.4.3左右对称夹具无反装 2.5定位块
2.5.1 定位块不得有手磨现象 2.5.2 定位块单独可调
2.5.3 左右对称夹具无装反现象 2.6 焊接作业性
2.6.1 焊接作业性要好,对于不可视焊点应有导向装置,材质为尼龙板。 2.7机构干涉
2.7.1 所有机构间不得有干涉现象,安全间隙不得小于5mm(重点检查动态时的干涉) 2.7.2 所有气管,管接头在静态、动态都不得与夹具机构有干涉 2.8防护
2.8.1 外观焊点应有浮动机构的铜板防护,材料为铬锆铜,厚度为10---12mm 2.8.2 外管件的定位,压紧块为尼龙材料 2.8.3 气缸气动元件要有相应的防护,防止焊钳碰撞损坏 2.9下件作业性
2.9.1 零部件从取出时应较容易且不变形 2.9.2 所有压头打开角度能使零部件方便从夹具中取出 2.10 操作台
2.10.1作业高度为600—800mm,符合人机工程学 2.10.2位置应不影响焊接作业性,且易于人员操作 2.11夹具的气路
2.11.1动作顺序满足夹具操作要求 2.11.2每步动作的先后顺序都有逻辑互锁,防止误动作 2.11.3一个控制阀带气缸总数不大于8个 3.外构件 3.1所有两/三联件进气口处需安装截止阀及快换接头,且所选两/三联件必须携带残压释放三通
阀。
3.2气动元件均为smc产品篇5:设备终验收报告
国产卧加终验收报告
qgt/q2753-r01(01) no: 时间:2013年11月12日 验收地点: 甲方: 乙方: 参加人员 甲方: 乙方: 甲方购买乙方代理的 (合同编号: ),出厂编号为,经甲、乙双方的共同努力下,于2013年7月至10月完成了安装、调试和试生产,项目具备终验收条件,特将终验收工作内容达成如下验收报告: 1.甲方现场工作概述:
在甲、乙双方的积极配合下,x月上旬开始进行x台国产卧加的安装和调试工作: 1)进行设备就位和静态精度检查工作; 2)按技术协议对机床进行空载运行; 3)刀具、夹具、机床附件、备件、工具、技术资料等进行清点和交接; 4)对刀仪安装、调试、培训并投入使用;
5)根据技术协议对机床的配置及各系统进行确认; 6)进行了第一道工序加工程序编制、工艺调试、产品试切加工,平衡节拍,产品全尺寸检查、cmk值测定; 7)进行了第二道工序加工程序编制、工艺调试、产品试切加工; 8)对甲方相关人员进行编程、设备操作、维修及保养培训; 9)x月中旬,甲方将x台国产卧加投入试生产; 10)对试生产过程中发现的问题及时进行整改,达到甲方要求。 2.问题整改及结果: 3.项目验收记录表
验收工作项目和记录见下表: 4.遗留问题
以下遗留问题,是在国产卧加上进行第二序加工内容时发现的问题和处置方法: 5.遗留问题处置要求
遗留问题处置要求见上表,待甲方进口卧加补充到位后,乙方负责第二序加工内容的工艺调试,保证刀具、夹具和工艺达到甲方要求。 6.结论
国产卧加(合同编号: )通过终验收。 7.本报告末尽事宜,按技术协议和商务合同执行。 8.本报告一式肆份,甲乙双方签章(字)生效,各执两份,并与合同书具有同等法律效力。
第12篇:CNC员工编程学徒岗位职责(整理)
编程工作职责
1.负责整个CNC制造过程中加工质量、加工效率、成本控制、出错控制负全部责任。2.CNC车间培养操作员各项操作技能,减少不必要的错误,不断提高其做事积极性,树立起工厂是我家的理念。
3.安排CNC各项工作流程,保证机床更高效率运作,积极配合各个部门各项工作。4.负责EDM外加工的报价及跟进。
5.对批量生产产品整批量报废负连带责任(成本10%)。6.精益求精,用心做最好!
CNC操作员岗位职责
1.每天按时上班,需穿工衣、带厂牌等
2.到指定工作场所认真的做好交接班工作(若有不明白之处应以书面形式交代清楚),白天领班还需把夜班所要做的工件、工具、材料等备好。
服从领班安排,按照领班分配的工作任务,保证按时、按质、按量的完成各项任务。 3.按照在制品制程检验标准,做完的工件需在机上认真、真实的做好自检(包括基准、光洁度、产品外形、尺寸等),检查OK才下机并在程序单上签名。
4.在工作时间或工作区域禁止大声喧哗、嬉笑等,扰乱工作秩序、影响工作或他人的行为(如串岗聊天、吃零食、玩手机、处理私人事务)
5.在操作机床时严禁把安全门打开操作,严格遵守作业指导书及相关安全规定进行作业。
每个加工好的成品必须吹干净残渣、油水等后按照标准摆放整齐,领班检查后送各相关部门。 6.严格的按照8S标准要求,每天将自己负责区域内的8S工作做好,保证工作场所干净整洁、工具摆放整齐。
调机学徒
1.调机学徒负责拆装夹治具,裝刀,对刀等。配合领班或调机师傅及时将工件上机。 2.服从领班安排,按照领班分配的工作任务,保证按时、按质、按量的完成各项任务。
7.3.严格的按照8S标准要求,每天将自己负责区域内的8S工作做好,保证工作场所干净整洁、工具摆放整齐。
第13篇:夹具工装书目
1.超完整夹具零件标准图册-东风汽车公司标准
2、超完整夹具部件标准图册--继夹具零件图册后又一经典
3、《机械制造工艺及专用夹具设计指导》PDG,PDF+书签
4、夹具-非标准夹紧装置PDF(搞工装的朋友不可错过的好资料)
5、《机床夹具设计手册》
6、国外实用机床夹具.pdf,1985年编译的
7、机床夹具结构图册(PDF格式)
8、《焊接工装夹具及变位机械图册》PDF扫描
9、夹具CAD图库(很规范且实用)
10、汽车装焊技术及夹具设计(北京理工大学出版社)
11、《自动化夹具图集》PDF--实用
12、焊接工装设计基础(航空工业出版社)
13、检验夹具设计(机械工业出版社)
14、焊接工装夹具及变位机械的性能·设计·选用(机械工业出版社)
15、重型机械制造、装配、工装设计新技术与技术测量及相关标准手册
16、砂型铸造工艺及工装设计(一本很实用的教科书,对铸造工艺装备设计有参考价值)
17、零件与工装的形位精度理论与应用 (机械工业出版社)
18、机床夹具设计原理(哈尔滨工程大学出版社)PDF清晰
19、金属切削机床夹具设计手册 第2版 浦林祥 20、《实用带压密封夹具图集》胡忆沩 【PDF】机械工业出版社/1998年12月
21、机床夹具设计原理习题集【作者】许新社 栗全庆 PDF (上海科学技术出版社)
第14篇:夹具设计心得体会
心得体会
两周的课程设计结束了,在这次的课程设计中不仅检验了我所学习的知识,也培养了我如何去把握一件事情,如何去做一件事情,又如何完成一件事情。在设计过程中,与同学分工设计,和同学们相互探讨,相互学习,相互监督。学会了合作,学会了宽容,学会了理解。
课程设计是我们专业课程知识综合应用的实践训练,着是我们迈向社会,从事职业工作前一个必不少的过程.”千里之行始于足下”,通过这次课程设计,我深深体会到这句千古名言的真正含义.我今天认真的进行课程设计,学会脚踏实地迈开这一步,就是为明天能稳健地在社会大潮中奔跑打下坚实的基础.
通过这次夹具设计,本人在多方面都有所提高。通过这次夹具设计,综合运用本专业所学课程的理论和生产实际知识进行一次输出轴夹具设计工作的实际训练从而培养和提高学生独立工作能力,巩固与扩充了输出轴夹具设计等课程所学的内容,掌握输出轴夹具设计的方法和步骤,掌握输出轴夹具设计的基本的模具技能懂得了怎样分析零件的工艺性,怎样确定工艺方案,了解了夹具的基本结构,提高了计算能力,绘图能力,熟悉了规范和标准,同时各科相关的课程都有了全面的复习,独立思考的能力也有了提高。
在这次设计过程中,体现出自己单独设计夹具的能力以及综合运用知识的能力,体会了学以致用、突出自己劳动成果的喜悦心情,从中发现自己平时学习的不足和薄弱环节,从而加以弥补。 在此感谢我们的老师.,老师严谨细致、一丝不苟的作风一直是我工作、学习中的榜样.这次模具设计的每个实验细节和每个数据,都离不开老师您的细心指导。
同时感谢对我帮助过的同学们,谢谢你们对我的帮助和支持,让我感受到同学的友谊。
由于本人的设计能力有限,在设计过程中难免出现错误,恳请老师们多多指教,我十分乐意接受你们的批评与指正,本人将万分感谢。
十、设计心得
本次的《机械制造工艺》课程设计让我又重新温习了书本上的内容,我明白了不论什么时候不管干什么事总是离不开书本,不管什么时候从书上我们总可以找得到我们想要的东西。书上的东西永远是基础的,而基础正是向更深的领域迈进,没有这个基础我们永远都不会享受到成功的喜悦。这次的设计我基本上是满意的,因为这是我和本组同学共同完成的这次设计。在此之前我总是莫名其妙感到茫然,不知道从何下手。或者是产生了干脆抄袭别人的想法,但是这一次彭老师制定的这个计划,每个星期都要询问我们的进度,这样子我感觉从一定程度上避免了同学不自己动脑的坏习惯,虽然杜绝不掉,但是我相信经过这次的课程设计后会有更多的同学愿意自主的完成自己的作业和老师分给他们的任务。而不再愿意抄袭别人的,至少我不会了。通过这次的课程设计使我明白了一个良好的设计思路往往可以省掉一大半的时间,所以我感觉今后不论设计什么,一定要在设计思路上下工夫,哪怕前期很慢很慢,但是一旦有了思路那么后期的制作就会势如破竹,会节省很大一部分的时间的。所以我建议同学们以后一定要在这方面下工夫。还有在绘制各种零件图或毛坯图的时候,一定要细心不能马虎一点,因为这些图都比较烦琐,所以必须一步一步来,不可贪图方便。
本次的课程设计,老师要求得很严格,但是老师为了辅导我们不懂的问题不厌其烦的把我们不懂的问题讲了一遍又一遍,真的很感谢老师为我们这么的尽心和尽责。我们一定不会辜负老师的期望,一定会努力的学好每一门知识,不能有骄傲和自满的情绪。更加努力的完善和充实自己,为自己的美好明天努力奋斗。
在最后仍然要再次谢谢老师对我们辛勤的辅导,我们一定不会辜负您的期望,请您放心。
老师您辛苦了!谢谢您!
第15篇:工装夹具管理制度
工装夹具管理制度
1.目的:
为了进一步加强公司内部生产设备和工艺装备的科学化管理,更好地保证产品质量,提高生产效率,降低生产成本,特制订工夹模具管理制度。
2.范围:
本公司所有涉及工夹模具设计、加工制作、使用维护、存放保管、修理、报废处理等工作的所有人员必须认真贯彻学习本制度,并严格遵照执行。 3.操作程序:
3.1工夹模具设计必须符合有关设计标准和设计规范要求。
3.2工夹模具设计必须遵守“保证产品质量,使用操作安全,维护检修方便”基本原则。
3.3工夹模具制造必须按照设计图纸的技术要求,严格选择材料。
3.4图样设计完毕后,应通知有关制造加工、生产使用和维护检修技术人员进行会签研究,以便及时修改。
3.5 加工必须严格按照图纸技术要求和加工工艺要求进行,以确保工夹模具质量。 3.6工夹模具外加工应同供方签订有关加工质量保证书,对加工单位进行必要的合格评定及控制。
3.7工夹模具外加工时,公司负责专项工作的人员应向供方提供详细的技术交底,必要时应派员工进行制作现场监督,以加强同外加工方的工作衔接和协商处理问题。
3.8 所制造的工夹、模具与其配件必须与图纸相符。
3.9 工夹、模具制造完毕后,必须经过试验调整、验证,符合产品技术要求,且质量稳定,使用操作安全,安装检修方便。
4、存放与保管
4.1 工夹、模具制造完毕或外加工回厂后交质检部、生产部进行验证合格后方能入库。
4.2 工夹、模具由使用部门进行存放,并有专职或兼职人员管理。
4.2.1全公司所有工装夹具和模具应按规定分类放在专用架子上,并按照有关工装模具的所编序号进行整齐排列,保持工夹、模具清洁,方便取放。
4.2.2工夹、模具应放在能足够载荷的专用垫板上,并允许适量的多层放置保管。还必须遵从按编号,对号排列整齐,保持良好间距。
4.3本公司所有工夹、模具必须按照各种产品用途,使用设备类别,从入库之日起进行编号。
4.3.1 模具管理员必须建立“模具台帐”和有关标识卡。
4.3.2 所有工夹、模具库存数与使用数,必须做到帐物相符,准确掌握流动情况。 4.4管理员必须将工夹、模具使用维修情况报告生产技术部门。
5、使用与跟踪
5.1车间、班组根据生产使用工夹、模具的情况,填写《模具维修记录》,并经车间负责人签字。
5.2 对不按规定使用工装夹具或造成损坏、丢失者,应视情节进行批评教育或予以罚款。
编制/日期: 审批/日期:
第16篇:夹具设计心得体会
心得体会
两周的课程设计结束了,在这次的课程设计中不仅检验了我所学习的知识,也培养了我如何去把握一件事情,如何去做一件事情,又如何完成一件事情。在设计过程中,与同学分工设计,和同学们相互探讨,相互学习,相互监督。学会了合作,学会了宽容,学会了理解。
课程设计是我们专业课程知识综合应用的实践训练,着是我们迈向社会,从事职业工作前一个必不少的过程.”千里之行始于足下”,通过这次课程设计,我深深体会到这句千古名言的真正含义.我今天认真的进行课程设计,学会脚踏实地迈开这一步,就是为明天能稳健地在社会大潮中奔跑打下坚实的基础.
通过这次夹具设计,本人在多方面都有所提高。通过这次夹具设计,综合运用本专业所学课程的理论和生产实际知识进行一次输出轴夹具设计工作的实际训练从而培养和提高学生独立工作能力,巩固与扩充了输出轴夹具设计等课程所学的内容,掌握输出轴夹具设计的方法和步骤,掌握输出轴夹具设计的基本的模具技能懂得了怎样分析零件的工艺性,怎样确定工艺方案,了解了夹具的基本结构,提高了计算能力,绘图能力,熟悉了规范和标准,同时各科相关的课程都有了全面的复习,独立思考的能力也有了提高。
在这次设计过程中,体现出自己单独设计夹具的能力以及综合运用知识的能力,体会了学以致用、突出自己劳动成果的喜悦心情,从中发现自己平时学习的不足和薄弱环节,从而加以弥补。 在此感谢我们的老师.,老师严谨细致、一丝不苟的作风一直是我工作、学习中的榜样.这次模具设计的每个实验细节和每个数据,都离不开老师您的细心指导。
同时感谢对我帮助过的同学们,谢谢你们对我的帮助和支持,让我感受到同学的友谊。
由于本人的设计能力有限,在设计过程中难免出现错误,恳请老师们多多指教,我十分乐意接受你们的批评与指正,本人将万分感谢。
十、设计心得
本次的《机械制造工艺》课程设计让我又重新温习了书本上的内容,我明白了不论什么时候不管干什么事总是离不开书本,不管什么时候从书上我们总可以找得到我们想要的东西。书上的东西永远是基础的,而基础正是向更深的领域迈进,没有这个基础我们永远都不会享受到成功的喜悦。这次的设计我基本上是满意的,因为这是我和本组同学共同完成的这次设计。在此之前我总是莫名其妙感到茫然,不知道从何下手。或者是产生了干脆抄袭别人的想法,但是这一次彭老师制定的这个计划,每个星期都要询问我们的进度,这样子我感觉从一定程度上避免了同学不自己动脑的坏习惯,虽然杜绝不掉,但是我相信经过这次的课程设计后会有更多的同学愿意自主的完成自己的作业和老师分给他们的任务。而不再愿意抄袭别人的,至少我不会了。通过这次的课程设计使我明白了一个良好的设计思路往往可以省掉一大半的时间,所以我感觉今后不论设计什么,一定要在设计思路上下工夫,哪怕前期很慢很慢,但是一旦有了思路那么后期的制作就会势如破竹,会节省很大一部分的时间的。所以我建议同学们以后一定要在这方面下工夫。还有在绘制各种零件图或毛坯图的时候,一定要细心不能马虎一点,因为这些图都比较烦琐,所以必须一步一步来,不可贪图方便。
本次的课程设计,老师要求得很严格,但是老师为了辅导我们不懂的问题不厌其烦的把我们不懂的问题讲了一遍又一遍,真的很感谢老师为我们这么的尽心和尽责。我们一定不会辜负老师的期望,一定会努力的学好每一门知识,不能有骄傲和自满的情绪。更加努力的完善和充实自己,为自己的美好明天努力奋斗。
在最后仍然要再次谢谢老师对我们辛勤的辅导,我们一定不会辜负您的期望,请您放心。
老师您辛苦了!谢谢您!
第17篇:夹具设计实例
课程设计的目的 《机床夹具》课程设计是在学完了专业基础课程后进行的一个实践性教学环节。其目的是:
1、培养学生综合应用《机械制造工艺与机床夹具》课程及其它有关先修课程的理论知识,把理论知识和生产实际密切结合,能够根据被加工零件的技术要求,运用夹具设计的基本原理和方法,学会拟订夹具设计方案,完成夹具结构设计,进一步提高结构设计能力。
2、培养学生熟悉并运用有关手册、图表、规范等有关资料文献的能力。
3、进一步培养学生识图、制图、运算和编写技术文件等基本技能。
4、培养学生独立思考和独立工作的能力,为毕业后走向社会从事相关技术工作打下良好的基础。
二、课程设计的要求与内容 本次设计按学号顺序(或者自由组合)分组进行,每人一组,每组一个题目。要求每组根据提供的零件工序图,设计一种专用夹
第18篇:夹具毕业设计说明书
前 言
毕业设计是学生在学校完成了大学四年的全部课程,并在进行了生产实习的基础上进行的一个教学环节,也是学生在校学习阶段的最后一个重要的教学环节,是完成工程师基本训练的一个必不可少的过程。通过毕业设计培养学生综合运用所学知识独立解决本专业一般工程技术问题的能力,树立正确的设计思想和工作作风。
毕业设计是在毕业实习的基础上进行的,根据自己的设计课题,在毕业实习期间认真调查研究、搜索资料。
本次设计是提高CA6140车床上拨叉的加工效率,设计正确的加工工艺路线,以及某道工序的夹具。这次设计涉及到机床,机械加工工艺,工装夹具等机制专业的几乎所有的专业基础知识。是一次全面地,系统地检查自己在大学期间对专业知识学习的情况,在整个设计过程中做到严谨认真,一丝不苟的精神,尽量使自己的设计达到理想的水平,通过独立的查找资料,分析,计算完成方案设计,图纸设计和编写技术文件等,设计了这套比较完整的加工工艺路线,使自己对机制专业有了更深刻的认识。
由于时间短促,经验不足以及水平有限,本次设计难免许多不妥和错误之处,敬请批评指正,以便及时改正。
1.零件分析
1.1 零件的作用
题所给的是CA6140车床上的拨叉,它位于车床变速机构中,主要起换挡作用,使主轴回转运动按照工作者的要求工作,获得所需的速度和扭矩。零件上方的Φ20mm的孔与操作机构相连,下方的Ф50mm的半孔则是用于与所控制齿轮所在的轴接触,通过上方的力拨动下方的齿轮变速,两零件铸造为一体,加工时分开。
1.2 零件的工艺分析
CA6140车床上的拨叉共有两处加工表面。其间有一定的位置要求,分述如下: 1.2.1 以Ф20mm为中心的加工表面
这一组加工表面包括:Ф20mm的孔,以及其上下表面,孔壁上有一个装配时要钻铰的Ф8mm的锥孔,一个M6的螺纹孔,和一个缺口。 1.2.2 以Ф50mm为中心的加工表面
这一组加工表面包括:Ф50mm的孔,以及其上、下端面; 这两组表面有一定的位置要求;
(1) Ф50mm的孔的上、下表面与Ф20的孔的垂直度误差为0.07mm。 (2) Ф20mm的孔的上、下表面与Ф20的孔的垂直度误差为0.05mm。
(3) Ф50mm、Ф20mm的孔的上、下表面以及Ф50mm的孔的内表面的粗糙度误差为3.2um。
(4) Ф20mm的孔的内表面的粗糙度误差为1.6um,精度为IT7。
2.工艺规程设计
2.1 毛坯的制造形式
零件材料为HT200,考虑零件在机床运行过程中所受冲击不大,零件结构又比较简单,故
选
择
铸
件
毛
坯
。
图一 毛坯图
2.2 基准面的选择
2.2.1 粗基准的选择 对零件而言,尽可能选择不加工表面为粗基准,而对若干个不加工表面的工件,则应以与加工表面要求相对位置精度较高的不加工表面作粗基准,根据这个基准原则,现取Ф20mm的孔的不加工外轮廓表面作为粗基准,利用一组共两个短V形块支承两个Ф20mm孔的外轮廓作主要定位面,以消除3个自由度,再用一个支承板支撑在Ф72mm的上表面,以消除3个自由度。
2.2.2 精基准的选择 主要应考虑基准重合问题。当设计基准不重合时,应该进行尺寸换算,这在以后还要专门计算,此处不再重复。
2.3 制定工艺路线
制定工艺路线的出发点,应当是使零件的几何形状、尺寸精度及位置精度等技术要求能得到合理的保证。在生产纲领已确定为中批生产的条件下,可以考虑采用万能性机床配以专用夹具,并尽量使工序集中来提高生产率。除此以外,还应当考虑经济效果,以便使生产成本尽量下降。
1、工艺路线方案一:
工序一:退火
工序二:粗、精铣Ф20 mm、Ф50 mm的下表面,保证其粗糙度为3.2 um 工序三:以Ф20 mm的下表面为精基准,粗、精铣Ф20 mm的孔的上表面,保证其粗糙度为3.2 um,其上、下表面尺寸为30mm,
工序四:以Ф20 mm 的下表面为精基准,钻、扩、铰、精铰Ф20 mm的孔,保证其内表面粗糙度为1.6 um,垂直度误差不超过0.05mm 工序五:以Ф20 mm的下表面为精基准,粗、半精镗Ф50 mm的孔,保证其内表面粗糙度为3.2 um 工序六;以Ф20 mm的下表面为精基准,粗、精铣Ф50 mm的上表面,保证其与孔的垂直度误差不超过0.07mm,其上、下表面尺寸为12mm 工序七:铣断
工序八:以Ф20 mm的孔为精基准,钻Ф8 mm的锥孔的一半Ф4 mm,装配时钻铰
工序九:以Ф20mm的孔为精基准,钻Ф5mm的孔,攻M6的螺纹
工序十:以Ф20 mm的孔为精基准,铣缺口,保证其粗糙度为12.5um 工序十一:检查
上面的工序可以是中批生产,但是其效率不高,并且工序四中的钻孔方法在钻孔是可能会偏离中心。经综合考虑,采用下面的方案二。
工艺路线方案二:
工序一;退火
工序二:粗、精铣Ф20 mm、Ф50 mm的下表面,保证其粗糙度为3.2 um 工序三:以Ф20 mm的下表面为精基准,粗、精铣Ф20 mm、Ф50 mm的孔的上表面,保证其粗糙度为3.2 um,Ф20 mm的上、下表面尺寸为30mm,Ф50 mm的上、下表面尺寸为12mm 工序四:以Ф20 mm 的下表面为精基准,钻、扩、铰、精铰Ф2 0 mm的孔,保证其内表面粗糙度为1.6 um,垂直度误差不超过0.05 mm 工序五:以Ф20 mm 的下表面为精基准,粗、半精镗Ф50 mm的孔,保证其
内表面粗糙度为3.2 um 工序六:铣断
工序七:以Ф20 mm的孔为精基准,钻Ф8 mm的锥孔的一半Ф4 mm,装配时钻铰
工序八:以Ф20 mm的孔为精基准,钻Ф5 mm的孔,攻M6的螺纹
工序九:以Ф20 mm的孔为精基准,铣缺口,保证其粗糙度为12.5 um 工序十:检查
2.4 机械加工余量、工序尺寸及毛坯尺寸的确定
“CA6140车床拨叉”零件的材料为HT200硬度为190~210HB,毛坯重量为2.2Kg,生产类型为中批量,铸件毛坯。又由>(以下称〈〈工艺手册〉〉表1.3-1查得毛坯的制造方法采用壳模铸造级,表2.2-4查得加工余量等级为G级,选取尺寸公差等级为CT10。
根据以上资料及路线,分别确定各加工表面的机械加工余量、工序尺寸及毛坯如下:
1、延轴线方向长度方向的加工余量及公差(Ф20mm、Ф50mm端面) 查《工艺手册》表2.2~4取Ф20mm、Ф50mm端面长度余量为2.5mm(均为双边加工)。 铣削加工余量为:a)粗铣:1.5mm b)精铣:1mm 毛坯尺寸及公差为:(35土0.3)mm ( 17土0.25)mm
2、内孔(Ф50mm已铸成孔)查《工艺手册》表2.2~2.5,取Ф50mm已铸成长度余量为3mm,即已铸成孔Ф44mm。
镗削加工余量为:a)粗镗:2mm b)半精镗:1mm
0.50毛坯尺寸及公差为:(48土0.3)mm (500.25)mm
3、其他尺寸直接铸造得到。
2.5 确定切削用量及基本工时
2.5.1 工序二:粗、精铣孔Ф20mm、Ф50mm的下表面
(1) 加工条件
工件材料:HT200。бb=0.16GPa HBS=190~210,铸件 机床:XA5032立式铣床
刀具;W18Cr4V硬质合金端铣刀
W18Cr4V硬质合金端铣刀,牌号为YG6,由《切削用量简明手册》〉后称《切削手册》表3.1查得铣削宽度ae
o手册》表3.2选择刀具的前角ro=+5o;后角ao=8o;副后角a’o=8,刀齿斜角λs=-10,主刃Kr=60o,过渡刃Krε=30o,副刃Kr’=5o,过渡刃宽bε=1mm
(2) 切削用量
1)粗铣Ф20mm的下表面
a)切削深度 因切削用量较小,故可以选择ap=1.5mm,一次走刀即可完成所需尺寸。 b)每齿进给量:由《切削手册》表3.30可知机床的功为7.5KW,查《切削手册》表3.5可得f=0.14~0.24mm/z,由于是对称铣,选较小量f=0.14mm/z c)查后刀面最大磨损及寿命
查《切削手册》表3.7,后刀面最大磨损为(1.0~1.5)mm 查《切削手册》表3.8, 寿命T=180min d)计算切削速度 按《切削手册》表3.27中的公式:
vccvdoqvkmprv
Tapxvfzyvuvaez也可以由表3.16查得vc=98mm/s n=439r/min vf =490mm/s 又根据XA5032铣床参数,选 n=475r/min vf =600mm/s,则实际的切削速度为:
doncvc
1000
即vc=3.1480475=119.3m/min,实际进给量为:
1000fzv即fzv=
vfcncz
600=0.13mm/z 47510e)校验机床功率 查《切削手册》表3.24,Pcc=1.1KW,而机床所提供的功率Pcm为1.7KW,所以Pcm>Pcc,故校验合格。
最终确定ap=1.5mm nc=475r/min vfc=600mm/min vc=119.3m/min fz=0.13mm/z f)计算基本工时
tmL Vf公式中: L=l+y+Δ;根据《切削手册》表3.26,可得 l+Δ=12mm,所以L=l+y+Δ=32+12=44mm 故 tm=44/600=0.073min 2)粗铣Ф50mm的下表面
a)铣削Ф50mm的下表面与铣削Ф20mm的下表面的相关参数及其用量等都相同。即
ap=1.5mm nc=475r/min vfc=600mm/s vc=119.3m/min fz=0.13mm/z b)计算基本工时
tmL Vf公式中: L=l+y+Δ;根据《切削手册》表3.26,可得 l+Δ=0所以L=l+y+Δ=72mm 故 tm=72/600=0.12min 3)精铣孔Ф20mm的下表面
a) 切削深度 因切削用量较小,故可以选择ap=1.0mm, 一次走刀即可完成所需尺寸 b)每齿进给量:由《切削手册》表3.30可知机床的功为7.5KW,查《切削手册》表3.5可得f=0.5~0.7mm/r,由于是对称铣,选较小量f=0.7mm/r c)查后刀面最大磨损及寿命
查《切削手册》表3.7,后刀面最大磨损为(1.0~1.5)mm 查《切削手册》表3.8, 寿命T=180min d)计算切削速度 按《切削手册》表3.27中的公式:
cvdoqvvcmkprv
Tapxvfzyvuvaez也可以由表3.16查得vc=124mm/s vf =395mm/min n=494r/min,根据XA5032铣床参数,选 n=475r/min vf =375mm/min , 则实际的切削速度为
doncvc
10003.1480475所以vc==119.3m/min,实际进给量
1000fzv所以fzv= 375=0.08mm/z 47510vfcncz
e)校验机床功率 查《切削手册》表3.24,Pcc=1.1KW,而机床所提供的功率Pcm为1.7KW,所以Pcm>Pcc,故校验合格。
最终确定ap=1.0mm nc=475r/min vfc=375mm/min vc=119.3mm/min f)计算基本工时
tmL Vf6
公式中: L=l+y+Δ;根据《切削手册》表3.26,可得 l+Δ=80mm, 所以L=l+y+Δ=32+80=112mm 故 tm=112/375=0.3min 2)精铣Ф50mm的下表面
a)铣削Ф50mm的下表面与铣削Ф20mm的下表面的相关参数及其用量等都相同。即 ap=1.0mm nc=475r/min vfc=375mm/min vc=119.3mm/m b)计算基本工时
tmL Vf公式中: L=l+y+Δ;根据〈〈切削手册〉〉表3.26,可得 l+Δ=80mm所以L=l+y+Δ=72+80=152mm 故 tmL=152/375=0.405min Vf2.5.2 工序三:粗、精铣孔Ф20mm、Ф50mm的上表面
本工序的切削用量及基本工时与工序一中的粗、精铣孔Ф20mm、Ф50mm的下表面相同。
2.5.3 工序四:钻、扩、铰、精铰Ф20mm的孔
(一) 钻Ф18mm的孔 (1)加工条件
工艺要求:孔径d=18mm, 孔深l=30mm,通孔 ,用乳化液冷却
机床 :Z535型立式钻床
刀具 :高速钢麻花钻头
选择高速钢麻花钻头,其直径do=18mm,钻头几何形状为:由《切削手册》表2.1及表2.2 选修磨横刃,β=28o αo=10o 2Φ=118o 2Φ1=70o bε=3.5mm b=2mm l=4mm (2) 切削用量 1) 决定进给量f a)、按加工要求决定进给量 根据《切削手册》表2.7,当铸铁的强度 бb
给机构允许的轴向力为11760N(Z535钻床允许的轴向力为15696N(见《工艺设计手册》表4.2-14)时,进给量为1.5mm/r。
从以上三个进给量比较可以看出,受限制的进给量是工艺要求,其值为f=0.70~0.86mm/r,根据Z535钻床说明书,选f=0.80mm/r(见《工艺设计手册》表4.2-16),又由《切削手册》表2.19可以查出钻孔时的轴向力,当f=0.80mm/r do
由《切削手册》表2.12,当do
n1000V do
100014.4=255r/min 3.1418根据Z535钻床说明书,可考虑选择nc=275r/min(见《工艺设计手册》表4.2-15) 所以n=4)检验机床扭转及功率
根据《切削手册》表2.21,当f Mc
又根据《切削手册》表2.23,当бb=(170~213)MPa
do
tmL nf8
L=l+y+Δ 由《切削手册》表2.29查得y+Δ=9mm 309故 tm=0.18min 2750.8
(二) 扩Ф19.8mm的孔 (1)加工条件
工艺要求:孔径d=19.8mm, 孔深l=30mm,通孔 ,用乳化液冷却
机床 :Z535型立式钻床
刀具 :高速钢扩孔钻头
选择高速钢扩孔钻头,其直径do=19.8mm,钻头几何形状为:由《切削手册》表2.5 ro=18o ao=10o kr=60o krε=30o β=15o ba1=1mm (2) 切削用量 1) 决定进给量f a)、按加工要求决定进给量 根据《切削手册》表2.10,当铸铁的强度 бb200HBS
do=19.8mm时,f=(0.9~1.1)mm/r 由于L/d=30/19.8=1.52 因扩孔之后还须铰孔 ,故取修正系数K=0.7 所以 f=(0.9~1.1)x0.7=(0.63~0.77)mm/r b) 按钻头强度决定进给量 根据表2.8,当бb=190MPa,do=19.8mm,钻头强度允许的进给量f=1.75mm/r c)按机床进给机构强度决定进给量 根据表2.9,当бb210MPa,do20.5mm,机床进给机构允许的轴向力为11760N(Z535钻床允许的轴向力为15696N(见《工艺设计手册》表4.2-14)时,进给量为1.5mm/r。
从以上三个进给量比较可以看出,受限制的进给量是工艺要求,其值为f=(0.63~0.77)mm/r,根据Z535钻床说明书,选f=0.64mm/r(见《工艺设计手册》表4.2-16),又由《切削手册》表2.19可以查出钻孔时的轴向力,当f=0.64mm/r do
由《切削手册》表2.12,当do
cvdozvvcmxvTapfyvkv
可知f=0.64mm/r时, do=19.8 mm时,Vt=27m/min 切削速度的修正系数由《切削手册》表2.31可知 Ktv=1.0 Kmv=1.0 KTv=1.0 Klv=0.85 所以 V=VtxKv=27x1.0x1.0x1.0x0.85=23m/min
n1000V don=100023=370r/min 3.1419.8根据Z535钻床说明书,可考虑选择nc=375r/min(见《工艺设计手册》表4.2-15) 4)检验机床扭转及功率
根据《切削手册》表2.21,当f Mc
又根据《切削手册》表2.23,当бb=(170~213)MPa do
tm L=l+y+Δ 由《切削手册》表2.29查得y+Δ=10mm 3010故 tm=0.13min 3750.8(三) 粗铰Ф19.94mm的孔 (1)加工条件
工艺要求:孔径d=19.94mm, 孔深l=30mm,通孔
机床 :Z535型立式钻床
刀具 :高速钢铰刀
L nf 选择高速钢铰刀,其直径do=19.94mm,钻头几何形状为:由《切削手册》表2.6 ro=18o ao=10o kr=60o krε=30o β=15o ba1=1mm (2) 切削用量 1) 决定进给量f 根据《切削手册》表2.11,当铸铁的强度
б
b
170HBS
do=19.94mm时,f=(1.0~2.0)mm/r,又由于粗铰之后还要精铰,所以应该选最大的进给量 即 f=2.0mm/r
2)决定钻头的磨钝标准及寿命
由《切削手册》表2.12,当do
cvdozvvcmxvTapf可知,vc=7.7m/min 切削速度的修正系数由《切削手册》表2.31可知 Ktv=1.0 Kmv=1.0 KTv=1.0 Klv=0.85 所以 V=VtxKv=7.7x1.0x1.0x1.0x0.85=6.55mm/min
nyvkv
1000V do10006.55=105r/min 3.1419.94根据Z535钻床说明书,可考虑选择nc=140r/min(见《工艺设计手册》表4.2-15) 所以n=4)检验机床扭转及功率
根据《切削手册》表2.21,当f Mc
又根据《切削手册》表2.23,当бb=(170~213)MPa
do
tm
L=l+y+Δ 由《切削手册》表2.29查得y+Δ=10mm 3010故 tm=0.14min 1402.0(四) 精铰Ф20mm的孔 (1)加工条件
L nf 工艺要求:孔径d=19.94mm, 孔深l=30mm,通孔,精度等级为IT7 机床 :Z535型立式钻床
刀具 :高速钢铰刀
选择高速钢铰刀,其直径do=20mm:钻头几何形状为:由《切削手册》表2.6 ro=0 ao=7o a1=18o (2)切削用量 1) 决定进给量f 根据《切削手册》表2.11,当铸铁的强度 бb170HBS do=20mm,加工精度要求为H7精度时,f=(1.0~2.0)mm/r,由于这是粗铰之后的精铰,所以应该选中等的进给量 即 f=1.5mm/r 2)决定钻头的磨钝标准及寿命
由《切削手册》表2.12,当do
cvdozvvcmxvTapf可知,vc=9.64m/min 切削速度的修正系数由《切削手册》表2.31可知 Ktv=1.0 Kmv=1.0 KTv=1.0 Klv=0.85 所以 V=VtxKv=9.64x1.0x1.0x0.85 x1.0=8.2m/min
nyvkv
1000V do10008.2=131r/min 3.1420根据Z535钻床说明书,可考虑选择nc=140r/min(见《工艺设计手册》表4.2-15) 所以n=4)检验机床扭转及功率
根据《切削手册》表2.21,当f
do
tm L=l+y+Δ 由《切削手册》表2.29查得y+Δ=10mm 3010故 tm=0.19min 1401.52.5.4 工序五:粗、精镗Ф50 mm的孔 (1) 粗镗Ф48mm孔 1)加工条件
工艺要求:孔径d=44mm的孔加工成d=48mm,通孔
机床 :T616镗床
刀具:YG6的硬质合金刀
L nf 刀具为YG6的硬质合金刀,且直径为20mm的圆形镗刀 (2)切削用量 a) 确定切削深度ap 4844 ap==2mm 2b) 确定进给量f 根据《切削手册》表1.5 当粗镗铸铁,镗刀直径为20mm, ap
vcvTmapxvfyvkv
其中:cv=158 xv=0.15 yv=0.40 m=0.20 T=60min KTv=1.0 Kmv=1.0 Ksv=0.8 Ktv=1.0 K= KTvx Kmvx Ksvx Ktv=1.0x1.0x0.8x1.0=0.8 1580.8=62.4m/min 所以 v0.20.156020.580.40100062.4 n=414r/min 3.1448又按T616机床上的转速 选n=370r/min d) 确定粗镗Ф48mm孔的基本时间
选镗刀的主偏角xr=45o 则 l1=3.5mm l2=4mm l=12mm l3=0 又f=0.58mm/r
n=370r/min i=1
tm3.51241=0.09min 0.58370(2)半精镗Ф50mm的孔
ll1l2l3i
nf所以tm1)加工条件
工艺要求:孔径d=48mm的孔加工成d=50mm,通孔
机床 :T616镗床
刀具:YG6的硬质合金刀
刀具为YG6的硬质合金刀,且直径为20mm的圆形镗刀 2)切削用量 e) 确定切削深度ap 5048 ap==1mm 2f) 确定进给量f 根据《切削手册》表1.5 当粗镗铸铁,镗刀直径为20mm, ap
vcvTmapxvfyvkv
其中:cv=158 xv=0.15 yv=0.40 m=0.20 T=60min KTv=1.0 Kmv=1.0 Ksv=0.8 Ktv=1.0 K= KTvx Kmvx Ksvx Ktv=1.0x1.0x0.8x1.0=0.8 1580.8=78.9m/min 所以 v0.20.150.406010.41100078.9 n=503r/min 3.1450又按T616机床上的转速 选n=370r/min h) 确定半精镗Ф50mm孔的基本时间
选镗刀的主偏角xr=45o 则 l1=3.5mm l2=4mm l=12mm l3=0 又f=0.58mm/r n=370r/min i=1
tm3.51241=0.13min 0.41370 2.5.5 工序六:铣断 tmll1l2l3i
nf1) 加工条件
工件尺寸:长72mm 深12mm 加工要求:将双体铣开
刀具: 选高速钢细齿圆锯片刀 由《工艺设计手册》表3.1-27可得,又由(《金属切削手册》第三版)表6-7 B=4mm do=160mm Z=50 d=32mm ro=10o ao=16o 2) 切削用量
a) 决定每齿进给量fz 查《切削手册》表3.4可得 fz=(0.03~0.02)x(1+40%)=(0.042~0.028)mm/z 由于是对称铣 取f=0.028mm/z b) 后刀面最大磨损及寿命
查《切削手册》表3.7后刀面最大磨损为:(0.15~0.20)mm 查《切削手册》表3.8 寿命T=150min c) 计算切削速度
按《切削手册》表3.27中的公式
vc可得vc=76.7m/min 100076.7n=153r/min 160根据XA6132铣床 选主轴转速为 n=150r/min
cvdoqvKv mpvTapxvfzyvuvaeZ所以实际的切削速度为 v=75.36 m/min 工作台每分钟进给量为: fmz=0.026x50x150=195mm/min 又根据XA6132铣床的参数,取工作台进给量为190mm/z
190则:实际的进给量为fz==0.025mm/z
50150d) 校验机床功率
由《切削手册》表3.28中的计算公式可知:
pc=Fc=
Fcv 1000yCFapxFfzFaeuFZdoqFnwFkFc
式中 CF=30 xF=1.0 yF=0.65 uF=0.83 wF=0 qF=0.83 所以计算得
FvFc=163.5N Pc=c=4.8kw
1000XA6132铣床主动电机的功率为7.5KW,故所选的切削用量可以采用 最终确定 vf=190mm/min n=150r/min v=75.36m/min e) 计算基本工时
tmL Vf公式中: L=l+y+Δ;根据《切削手册》表3.26,可得 l+Δ=0所以L=l+y+Δ=22mm 故 tmL=22/190=0.12min Vf2.5.6 工序七: 钻锥孔Ф8mm的一半Ф4mm (1)加工条件
工艺要求;孔径do=4mm ,孔深l=32mm, 通孔
机床;Z525立式钻床
刀具: 高速钢麻花钻
选择的高速钢麻花钻的直径为do=4mm 钻头的几何形状为(由《切削手册》表2.7可知
铸铁的强度头几何形状为:由《切削手册》表2.1及表2.2 选β=30o αo=16o 2Φ=118o 2Φ1=70o (2)切削用量 1) 决定进给量f a)、按加工要求决定进给量 根据《切削手册》表2.7,当铸铁的强度 бb200HBS do=4mm时,f=0.18~0.22mm/r 由于L/d=32/4=8>3,故取修正系数K=0.8 所以 f=(0.18~0.22)x0.8=(0.144~0.176) mm/r b) 按钻头强度决定进给量 根据表2.8,当бb=190MPa,do
根据表2.9,当бb210MPa,do10.2mm,机床进给机构允许的轴向力为8330N(Z525钻床允许的轴向力为8830N(见《工艺设计手册》表4.2-14)时,进给量为1.63mm/r。
从以上三个进给量比较可以看出,受限制的进给量是工艺要求,其值为f=(0.144~0.176) mm/r,根据Z525钻床说明书,选f=0.17mm/r(见《工艺设计手册》表4.2-16),又由《切削手册》表2.19可以查出钻孔时的轴向力,当f
由《切削手册》表2.12,当do
n1000V do100017=1354r/min 3.144根据Z525钻床说明书,可考虑选择nc=1360r/min(见《工艺设计手册》表4.2-15) 所以n=4)检验机床扭转及功率
根据《切削手册》表2.21,当f Mc
又根据《切削手册》表2.23,当бb=(170~213)MPa do
tmL nf L=l+y+Δ 由《切削手册》表2.29查得y+Δ=2.5mm 322.5故 tm=0.15min 13600.17
2.5.7 工序八:钻Ф5mm的孔,攻螺纹M6 (1)加工条件
工艺要求;孔径do=5mm ,孔深l=6mm, 通孔
机床;Z525立式钻床
刀具: 高速钢麻花钻
选择的高速钢麻花钻的直径为do=5mm 钻头的几何形状为(由《切削手册》表2.7可知
铸铁的强度头几何形状为:由《切削手册》表2.1及表2.2 选β=30o αo=16o 2Φ=118 2Φ1=70 (2)切削用量 1) 决定进给量f a)、按加工要求决定进给量 根据《切削手册》表2.7,当铸铁的强度 бb200HBS do=5mm时,f=0.27~0.33mm/r 由于L/d=6/5=1.2
根据表2.9,当бbo o210MPa,do10.2mm,机床进给机构允许的轴向力为8330N(Z525钻床允许的轴向力为8830N(见《工艺设计手册》表4.2-14)时,进给量为1.63mm/r。
从以上三个进给量比较可以看出,受限制的进给量是工艺要求,其值为f=(0.27~0.33) mm/r,根据Z525钻床说明书,选f=0.28mm/r(见《工艺设计手册》表4.2-16),又由《切削手册》表2.19可以查出钻孔时的轴向力,当f
由《切削手册》表2.12,当do
n1000V do100013.6=866r/min 3.145根据Z525钻床说明书,可考虑选择nc=960r/min(见《工艺设计手册》表4.2-15) 所以n=4)检验机床扭转及功率
根据《切削手册》表2.21,当f Mc
又根据《切削手册》表2.23,当бb=(170~213)MPa do
tm L=l+y+Δ 由《切削手册》表2.29查得y+Δ=2.5mm 62.5故 tm=0.03min 9600.28(2)攻M6的螺纹
由〈〈工艺设计手册〉〉表6.2-14可知
L nfLl1l2Ll1l2tmi
fnfno 其中:l1=(1~3)p l2=(2~3)p 公式中的no为丝锥或工件回程的每分钟转数(r/min); i为使用丝锥的数量;n 为丝锥或工件每分钟转数(r/min);d为螺纹大径;f为工件每转进给量 等于工件螺纹的螺距p 由上述条件及相关资料有; f=p=1mm/r d=6mm n=680r/min no=680r/min i=1 所以 (1) 切削速度
vdon1000
所以v=3.146680=10.7m/min 1000
(2) 基本工时
622.5622.52tm1=0.03min 68016801 2.5.8 工序九:铣缺口 (1)加工条件
工件尺寸:长为25mm, 宽为10mm 机床:XA5032立式铣床
刀具;W18Cr4V硬质合金端铣刀
W18Cr4V硬质合金端铣刀,牌号为YG6,由《切削用量简明手册》后称《切削手册》表3.1查得铣削宽度ae
a)切削深度 因切削用量较小,故可以选择ap=6mm,一次走刀即可完成所需尺寸。 b)每齿进给量:由《切削手册》表3.30可知机床的功为7.5KW,查《切削手册》表3.5可得f=0.14~0.24mm/z,由于是对称铣,选较小量f=0.14mm/z c)查后刀面最大磨损及寿命
查《切削手册》表3.7,后刀面最大磨损为(1.0~1.5)mm 查《切削手册》表3.8, 寿命T=180min d)计算切削速度 按《切削手册》表3.27中的公式 o
o
o
vccvdoqvkmprv
Tapxvfzyvuvaez也可以由表3.16查得vc=77m/min nt=245r/min vft =385m/min 各修正系数为:Kmv=Kmn=Kmvf=1.0 Ksv=Ksn=Ksvf=0.8 故 Vc=VtKv=77x1.0x0.8=61.6m/min n= ntkn=245x1.0x0.8=196r/min vf=vftkvt=385x1.0x0.8=308mm/min 又根据XA5032铣床参数,选 n=235r/min vf =375mm/s,则实际的切削速度为:
vcdonc1000
所以vc=3.14100235=73.8m/min,实际进给量为:
1000fzv所以fzv=
vfcncz
375=0.16mm/z 23510e)校验机床功率 查《切削手册》表3.24, 当бb=(174~207)MPa ae
ap=6mm vf=375mm/min n=235r/min vc=73.8m/min fz=0.14mm/z f)计算基本工时
tmL Vf公式中: L=l+y+Δ;根据《切削手册》表3.26,可得 l+Δ=0mm, 所以L=l+y+Δ=25mm 故 tmL=25/375=0.07min Vf3.绘制零件图和编制工艺文件
3.1 绘制零件图
21
图二:零件图
3.2 编制工艺文件
1 机械加工工艺过程的组成
工艺过程 改变生产对象的形状、尺寸、相对位置和性质等,使其成为成品或半成品的过程。工艺过程又可分为铸造、锻造、冲压、焊接、机械加工、热处理、装配等工艺过程。
机械加工工艺过程 用机械加工方法,改变毛坯的形状、尺寸和表面质量,使其成为零件的过程。
零件的机械加工工艺过程由许多工序组合而成,每个工序又可分为若干个安装、工位、工步和走刀。
工序 一个或一组工人,在一个工作地对同一个或同时对几个工件所连续完成的那一部分工艺过程。
安装 工件经一次装夹(定位和夹紧)后所完成的那一部分工序。
工位 为了完成一定的工序部分,一次装夹工件后,工件与夹具或设备的可动部分一起,相对刀具或设备的固定部分所占据的每一个位置。
工步 当加工表面、加工工具和切削用量中的转速和进给量均保持不变的情况下完成的那一部分工序。
22
2 工序的合理组合
确定加工方法以后,就要按生产类型、零件的结构特点、技术要求和机床设备等具体生产条件确定工艺过程的工序数.确定工序数有两种基本原则可供选择.工序分散原则 工序多,工艺过程长,每个工序所包含的加工内容很少,极端情况下每个工序只有一个工步,所使用的工艺设备与装备比较简单,易于调整和掌握,有利于选用合理的切削用量,减少基本时间,设备数量多,生产面积大.工序集中原则 零件的各个表面的加工集中在少数几个工序内完成,每个工序的内容和工步都较多,有利于采用高效的机床,生产计划和生产组织工作得到简化,生产面积和操作工人数量减少,工件装夹次数减少,辅助时间缩短,加工表面间的位置精度易于保证,设备、工装投资大,调整、维护复杂,生产准备工作量大.批量小时往往采用在通用机床上工序集中的原则,批量大时即可按工序分散原则组织流水线生产,也可利用高生产率的通用设备按工序集中原则组织生产.将工艺规程的内容,填入具有规定的格式的卡片中,使之成为生产准备和施工依据的工艺规程文件。
“机械加工工艺过程卡”和“机械加工工序卡”附后所示
4.夹具设计
为了提高劳动生产率,保证加工质量,降低劳动强度,需要设计专用夹具。 经过与指导老师的协商,决定设计第Ⅵ道工序—铣断双体,本夹具将用于XA6132卧式铣床,刀具为高速钢细齿圆锯片铣刀,对工件进行加工。
4.1问题的提出
本夹具主要用于铣开双体,并且铣开的表面与Φ20mm的孔有一定的公差要求,又在加工本道工序时,Φ20mm的孔已经进行了加工,因此,在本道工序中主要考虑加工面与Φ20mm孔之间的要求,其次是考虑如何提高劳动生产率,保证加工质量,降低劳动强度。
4.2 夹具体设计
4.2.1 定位基准的选择
23
图三定位原理图
由零件图可知:被铣开的那Φ50mm的中心线与Φ20mm孔的中心线之间的公差等级要求较高,且铣开时的设计基准为Φ50mm孔的中心线。为了尽量的减小定位误差,应选Φ20mm孔为主要的定位基准,利用一个圆柱销和一个菱形销定位,消除三个自由度,再在底面用夹具体定位消除三个自由度。以便达到所需要求。
为了提高加工效率,现同时加工四个双体,同时,为了夹具简单,操作方便,利用多点联动夹紧机构夹紧。 4.2.2 切削力及夹紧力的计算
刀具:高速钢细齿圆锯片铣刀 直径do160mm 齿数 Z=50 又由《切削手册》表3.28中的公式:
FCFapxFfzyFaeuFZdoqFnwF
其中: CF30
xF1.0
yF0.65 uF0.83 wF0 qF0.83
do160mm Z=50 ap4mm ae12mm fz0.025mm/z 所以 F=63.5N 水平分力:FH1.1F63.51.169.9N
垂直分力;FV0.3F0.363.519.1N
又在计算切削力时,必须把安全系数考虑在内。安全系数KK1K2K3K4 其中 K1为基本安全系数1.5 K2为加工性质系数1.2
24
K3刀具钝化系数 1.2 K4为切削特点系数(断续切削)1.2 所以 F ′=KFH=69.9x1.5x1.2x1.2x1.2=181.2N 为了克服水平方向的力,实际的夹紧力为 N(f1+f2)= KFH
其中 f1为螺母与螺杆间的摩擦系数
f2为工件与螺杆头(或压板)间的摩擦系数
又查得 f1 和f2为1.6 则
NKFH
f1f2181.2566N
0.160.16又选择的螺旋夹紧机构的基本尺寸如下(根据《机床夹具设计》 第三版表1-2-20、所以 N1-2-
21、1-2-
22、1-2-23查得:
950 r′=0
M12mm
p1mm rz5.675mm a136 30
2tg20.15 L=120mm Q=30N 则 可以提供的夹紧力为:
wQL )rtg1rz(a2 所以w =12030=3140N 5.675tg(136950)又由《机床夹具设计》 第三版表1-2-24查得 当螺纹的公称直径为12mm时 ,螺栓许用的夹紧力为5690N 由以上的数据可知:所选的螺旋机构提供的夹紧力大于所需的,且满足螺栓的许用夹紧力,故本夹具可以安全工作。 4.2.3 定位误差分析
1)定位元件尺寸及公差的确定 本夹具的定位元件为一圆柱销和一菱形销,其参数由(《机床夹具设计手册》图5-3及其表选 两定位销的尺寸及公差为:Φ2000.033mm(定位销的公差取h8)。
2)零件图样规定 Φ20mm的孔的中心线与Φ50mm孔的中心线的长度误差为0.2mm,Φ20mm孔中的定位销与夹具体的垂直度误差为0.05mm,,此项技术要求应由定位销
25
0.021宽配合中的侧向间隙保证。已知Φ20mm的宽为Φ200定位销为Φ200(定mm,0.033mm位销的公差取h8),则 一个定位销与一个孔的定位误差为:
bmax0.021(0.033)/20.027mm
此处引起零件的定位误差为 x0.02720.054mm
(2)计算Φ20mm定位销的中心线与夹具体垂直度误差
定位销的宽度为Φ2000.033mm 夹具体表面的粗糙度Ra1.6um 故 max0.0016(0.033)0.03360.05mm 所以最大垂直度误差能满足零件精度要求 4.2.4 夹具设计及操作的简要说明
如前所述,在设计夹具时,首先要考虑到能保证零件的加工精度,其次是要提高劳动生产率。为此,应先考虑所设计的夹具体与零件在夹具上的定位,在本道工序中,由于零件的底面的定位是用的夹具体,所以其表面粗糙度要求应比较高,视为关键面。又本道工序是铣断,其切削力不大,故在设计夹具时应考虑夹具的简单及利用常用的一些零件。为了提高生产率,可以考虑同时装夹几个零件,并且用了活动杠杆使操作更加节省时间。可以同时装夹四个零件,提高了生产率。
夹具上装有对刀块,可以使夹具在一批零件加工之前很好的对刀;同时,夹具体底面上的一对定位键可使整个夹具在机床工作台上有一正确的安装位置,以利于铣削加工。铣床夹具装配图及夹具体零件图见图示:
26
结
论
毕业设计是学生在校学习阶段的最后一个重要的教学环节,其目的是培养学生综合运用所学的专业和基础理论知识,独立解决专业一般工程技术问题的能力。树立正确的设计思想和工作作风。
经过两个月的毕业设计,获得如下心得:
1.运用机械制造工艺及有关课程的知识,结合生产实习中学到的实践知识。独立地分析和解决工艺问题。初步具有设计一些中等复杂零件的能力。
2.能根据被加工零件的技术要求,运用夹具设计的基本原理和方法。学会拟定夹具设计方案。
3.熟悉并运用有关手册,能快速查表得到所需的数据。4.有一定的识图制图能力。
通过设计,培养了我综合运用理论知识和专业知识的技能。熟悉一般机械零件的加工工艺过程,设计夹具的能力。
中国加入WTO以后,大量的机械产品技术进入我国市场。中国企业能够与国外产品竞争,拥有自己的国内外市场就必须产品的质量好,技术含量高,价格低廉,这就要求我们扎实学习先进的技术,认真研究。
27
致
谢
本学期是我在学校求学的最后一个学期,也是完成我的毕业设计的时间表,在这最后一个学期里面,我学到了很多知识,其中有很多是很好实用价值的,这在我以后的工作中有大帮助,在此我对我的指导老师杨文生老师的辛勤教诲表示衷心的感谢,感谢他对我们设计的关心和帮助。本次毕业设计是我们大学四年所学知识做的一次总测验,是锻炼也是检验自己四年来所学知识和掌握、运用知识的能力,是我们高等院校学生的最后的学习环节,也是学到最多实际知识的时候。通过这次设计,我学到了许多原来未能学到的东西,对过去没有掌握的知识得到了更进一步巩固。独立思考,综合运用所掌握理论知识的能力得到很大的提高,学会了从生产实际出发,针对实际课题解决实际问题,掌握了综合使用各种设计手册、图册、资料的方法, 也是为我们即将参加工作所做的必要准备,打下基础,更是我们四年机械设计制造及其自动化专业知识的一次综合。
本次设计也暴露了我们不少的缺点和问题:对于所学知识还没有做到仔细、认真消化,许多方面还是只有一个大概的认识,没有深入探讨,对实际事物没有深刻得了解,没有做到理论联系实际,没有达到对所学的知识熟练运用的水平。这也从一个侧面反映出我们设计经验不足,思维不够开拓,不够灵活。从而我得出一个结论:无论是现在还是以后走上工作岗位,还是再深造,都应该虚心向老师和前辈们学习,从而不断完善自我,提高自我水平。
本次毕业设计毕竟是我们做的第一次比较完整,系统的设计,因而难免存在许多缺点和不足之处,还有待于改进。希望各位老师多提宝贵意见。
28
参考文献
[1]、徐嘉元,曾家驹主编《机械制造工艺学》机械工业出版社 97.8 [2]、赵家齐:《机械制造工艺学课程设计指导书》,机械工业出版社 [3]、李益民主编:《机械制造工艺设计简明手册》,机械工业出版社 [4]、艾兴 肖诗纲主编.《切削用量简明手册》.机械工业出版社, 1994 [5]、浦林祥主编.《金属切削机床夹具设计手册》.机械工业出版社, 1984 [6]、王启平主编《机床夹具设计》哈工大出版社 85.12 [7]、东北重型机械学院主编《机床夹具设计手册》上海科学技术出版社 80.1 [8]、徐灏主编《机械设计手册》机械工业出版社 91.9 [9]、《机械制造工艺学》、《机床夹具设计》 (教材)
[10]、孙丽媛主编,《机械制造工艺及专用夹具设计指导》,冶金工业出版社2002 [11]、《机械零件设计手册》 [12]、《机床夹具设计图册》 [13]、《几何量公差与检测》
29
摘 要
拨叉的加工质量将直接影响机器的性能和使用寿命。本次设计旨在提高CA6140车床拨叉的加工效率,由此我们首先对拨叉的结构特征和工艺进行了仔细的分析,然后确定了一套合理的加工方案,加工方案要求简单,操作方便,并能保证零件的加工质量。在制定加工工艺规程的顺序如下: 1分析零件; 2选择毛坯;
3设计工艺规程:包括制定工艺路线,选择基准面等;
4工序设计:包括选择机床,确定加工余量,工序尺寸及毛坯尺寸,确定切削用量及计算基本工时等; 5编制工艺文件。
此外,为了提高劳动生产率,降低劳动强度,保证加工质量,需设计专用夹具,本次设计选择了第六道工序铣断双体的专用夹具设计,以满足加工过程的需要。 关键词:拨叉; 工艺规程; 夹具设计
Abstract
Dials the fork proceing quality directly will affect the machine the performance and the service life.This design is for the purpose of enhancing the CA6140 Lathe machine Dials the fork the proceing efficiency, first has carried on the careful analysis from this us to the Dials the fork structure characteristic and the craft, then had determined set of reasonable proceings plans, the proceing plan request are simple, the ease of operation, and can guarantee the components the proceing quality.In formulation proceing technological proce order as follows: 1 analysis the components; 2 choices semifinished materials; 3 designs technological proce: Including division Craft route, preferred orientation datum and so on; 4 working procedures designs: Including chooses the engine bed, the determination proceing remainder, the computation working procedure size and its the Semifinished materials size, the determination cutting specifications and the computation man-hour and so on; 5 establishments technological document.In addition, in order to enhance the labor productivity, reduces the labor intensity, guaranteed the proceing quality, must design the unit clamp, this design chose the six working procedure to The mill breaks Catarmaran Special-purpose jig design, by satisfied the proceing proce the need.Key words: Dials the fork; technological proce; jig desin。
30
目 录
前 言-------------1 1 零件的分析1 1.1 零件的作用-------------------------1 1.2 零件的工艺分析------------------1 2 工艺规程的设计------------------------2 2.1 毛坯的制造形式-----------------2 2.2 基准面的选择---------------------2 2.2.1 粗基准的选择-------------2 2.2.2 精基准的选择-------------2 2.3 制定工艺路线---------------------3 2.4 机械加工余量、工序尺寸及毛坯尺寸的确定-------4 2.5 确定切削用量及基本工时----4 3 绘制零件图和编制工艺卡----------21 3.1 绘制零件图------------------------21 3.2 编制工艺文件---------------------22 4 夹具设计----23 4.1 问题的提出-----------------------23 4.2 夹具体设计-----------------------23 4.2.1 定位基准的选择---------23 4.2.2 切削力及夹紧力的计算------------------------------24 4.2.3 定位误差分析-------------25 4.2.4 夹具设计及操作的简要说明-----------------------26 5 结论-----------276 致谢-----------287 参考文献----29
31
学 号: 200901124193711
河北理工大学成人教育
毕业论文(设计说明书)
论文题目: 学 院: 专 业: 班 级: 姓 名: 指导教师:
拨叉机械加工工艺规程及夹具设计
河北理工大学继续教育学院 机械设计制造及其自动化
09机本培 王 虎 杨文生
2013 年 月 日
第19篇:法兰盘夹具设计.
目录
一、序言 .......................................................................................................................2
二、零件分析 ...............................................................................................................2
1零件的作用 .........................................................................................................2 2零件的工艺分析 .................................................................................................2
三、工艺规程设计 .......................................................................................................3
1确定毛坯的制造形式 .........................................................................................3 2基面的选择 .........................................................................................................3 3制定工艺路线 .....................................................................................................3 4毛坯尺寸的确定与机械加工余量 .....................................................................5 5确定各道工序的切削用量及基本工时 .............................................................5
四、夹具的设计 .........................................................................................................14 1问题的提出 .......................................................................................................14 2夹具设计 ...........................................................................................................14
五、三维建模..............................................................................................................16
五、设计总结 .............................................................................................................21
六、参考文献 .............................................................................................................22
0
一、序言
机械制造装备课程设计是在我们学完了大学的全部基础课、技术基础课、大部分专业课以及参加了生产实习之后进行的。这是我们在进行毕业设计之前对所学各课程的一次深入的综合性的总复习,也是一次理论联系实际的训练,因此,它在我的大学生活中占有重要的地位。
通过本次课程设计,应该得到下述各方面的锻炼:
1、能熟练运用机械制造课程中的基本理论以及在生产实习中学到的实践知识,正确地解决一个零件在加工中的定位、夹紧以及工艺路线安排、工艺尺寸确定等问题,保证零件的加工质量。
2、提高结构设计的能力。通过设计夹具的训练,应当获得根据被加工零件的加工要求,设计出高效、省力、经济合理而且能保证加工质量的夹具的能力。
3、学会使用手册及图表资料。掌握与本设计有关的各种资料的名称、出处、能够做到熟练运用。
此次设计的是CA6140车床法兰盘及夹具设计。首先,对工件进行分析得出工艺路线;再着重进行夹具的设计,其中包括定位的设计、夹紧力的设计,夹紧和定位原件的选择。
由于能力所限,设计尚存在许多不足之处,恳请老师予以指教。
二、零件分析
1、零件的作用
题目所给的零件是法兰盘,为盘类零件,用于卧式车床上。车床的变速箱固定在主轴箱上,靠该法兰盘定心。法兰盘内孔与主轴的中间轴承外圆相配,外圆与变速箱体孔相配,以保证主轴三个轴承孔同心,使齿轮正确啮合。
2、零件的工艺分析
法兰盘零件,要求钻孔Ф6和Ф4,保证尺寸280.3,进行夹具设计,生产批量为中批量生产。以零件心轴和一端面定位,夹紧另外一端面。用快换钻套保证孔Ф6和Ф4的位置,即尺寸280.3。
1
三、工艺规程设计
1、确定毛坯的制造形式
零件材料是HT200。零件年产量是中批量,而且零件加工的轮廓尺寸不大,在考虑提高生产率保证加工精度后可采用铸造成型,采用方法为砂模机器造型。零件形状并不复杂,因此毛坯形状可以与零件的形状尽量接近。
2、基面的选择
基面选择是工艺规程设计中的重要工作之一。基面选择得正确与合理,可以使加工质量得到保证,生产率得以提高。否则,加工工艺过程中会问题百出,更有甚者,还会造成零件的大批报废,使生产无法正常进行。
(1)粗基准的选择
按照有关粗基准的选择原则(如果必须首先保证工件上欲加工表面与不加工表面之间的位置要求,则应以不加工表面为粗基准),现选择Φ45外表面B为粗基准,利用三爪自定心卡盘加持最右端外圆Φ45,并且使卡盘端面紧靠右端面,这样可以消除所有六个自由度,达到完全定位。
(2)精基准的选择。主要应考虑基准重合的问题。当设计基准与工序基准不重合时,应该进行尺寸换算。
3、制定工艺路线
制定工艺路线应该使零件的加工精度(尺寸精度、形状精度、位置精度)和表面质量等技术要求能得到合理的保证。在生产纲领已经确定为中批生量生产的条件下,可以考虑采用通用机床配以志用夹具,并尽量使工序集中来提高生产率。还应当考虑经济效果,以便降低生产成本。
(1) 工艺路线方案一
工序1粗车 Ф100mm柱体左右端面及外圆外圆留有余量。以右端Ф45 mm为粗基准。
工序2钻、扩、粗铰、精铰 20mm孔至图样尺寸并车孔左端的倒角。 工序3粗车Ф45,Ф90的外圆,粗车各端面,粗车Ф90的倒角,粗车3x2的槽,R5的圆角。以Ф20为精基准。
工序4 半精车Ф90外圆及各端面,车槽3×2,R5的圆角。 工序5半精车Φ100左右端面及外圆,精车Ф100的左端面。 工序6粗铣Ф90的左端面;粗铣、精铣 90柱体右侧面。
2 工序7钻 4×Φ9孔。 工序8 钻Φ4孔,铰Φ 6孔。
工序9磨削Φ100的右端面,Φ90外圆及左右端面,Φ45外圆。 工序10 磨削外圆面 Φ100,Φ 90 。
工序11刻字刻线。 工序12镀铬。 工序13 检测入库。
(2 )工艺路线方案二
工序1钻、扩、铰Φ20的孔,以右端Φ45的外圆为粗基准。
工序2粗车Φ100外圆,B面,Φ90外圆及右侧面,3x2槽,Φ45外圆。粗车零件左右端面
工序3粗车零件左右端面,并倒Φ20孔的倒角,以及零件右端45度倒角。 工序4半精车Φ100外圆,Φ90外圆。 工序5半精车零件左端面。
工序6精车Φ100外圆,并倒Φ100,Φ90的倒角。 工序7精车零件右端面。
工序8粗铣Ф90的左端面;粗铣、精铣 90柱体右侧面。 工序9 钻 4×Φ9孔。 工序10钻Φ4孔,铰Φ 6孔。
工序11磨削Φ90外圆及右侧Φ45外圆。 工序12抛光B面。 工序13刻字画线。 工序14镀铬。 工序15检测入库。 (3)工艺方案的比较与分析
上述两种工艺方案的特点在于:方案二考虑以Φ20孔为精加工基准,而方案一则是从右端面开始加工到左端面,然后再钻孔 Φ20mm,这时则很难保证其圆跳动的误差精度等。因此决定选择方案二作为加工工艺路线比较合理。
3
4、毛坯尺寸的确定与机械加工余量
由于本零件材料为灰铸铁,由《工艺手册得》,毛坯为双侧加工,MA为G,加工精度为8到10级,这里选取9级。则,由《机械制造工艺设计简明手册》表2.2-4得:
零件沿轴线方向的加工余量为:2x2.5mm=5mm Ф100径向加工余量为6mm,轴向加工余量为2x2.5mm=5mm Ф90径向加工余量为2x2.5mm=5mm,轴向加工余量为2x2.5mm=5mm Ф45径向加工余量为2x2.5mm=5mm 由《机械零件工艺性手册》表:2-64得:Ф100,Ф90柱体圆角为:R=2mm;右端Ф45的圆角为:R=4mm;
5、确定各道工序的切削用量及基本工时
工序1 :钻,扩,铰Ф20孔 加工条件:
工件材料:HT200 硬度170—241HB,取190HB,机器砂型铸造。 加工要求:钻,扩,铰Ф20孔 机床:Z3040型摇臂钻床 (1)钻 Ф18孔
1)刀具选择:查《机械制造工艺设计简明手册》选用 18高速钢锥柄标准花钻。
2)切削用量选择:查《切削用量手册》得:f=0.70~0.86mm/r,再由《机械制造工艺设计简明手册》C365L 手册》取V =13m/min,vdwnw1000=18m/min。
车床进给量取f =0.76mm/r。查《切削用量简明
1000vnsdw=230r/min,按机床选取n =238r/m,故3)计算基本工时:T=(L+L1+L2)/(f×n)=0.66min。 (2)扩Ф19.8 孔
1)刀具选择:选用 19.8高速钢锥柄扩孔钻。
2)确定切削用量:查《切削用量简明手册》得:f=0.90~1.1mm/r,再由《机械制造工艺设计简明手册》C365L 车床进给量取f =0.92mm/r。扩孔时的切削速度,
4 由《现代机械制造工艺流程设计实训教程》得公式:vc扩=(1/2~1/3)vc钻 查《切削用量简明手册》取VC =0.29m/s=17.4m/min,Vc=(1/2~1/3)VC =5.8~8.7m/min,ns1000vdw=93~140r/min,按机床选取n =136r/m,故vdwnw1000=8.5m/min 。
3)计算基本工时:T=(L+L1+L2)/(f×n)=(91+14+2)/(0.92×136)=0.86min。其中L=91,L1=14,L2=2。
(3)铰Ф20
1)刀具选择:20高速钢锥柄机用铰刀
2)确定切削用量:背吃刀量ap=0.12。由《切削用量简明手册》表2.11 f=1.3~2.5mm/r,取zvf=1.68由《切削用量简明手册》表
w2.30得
yvcdT.axf=7.9m/min,ns1000vd=125.8 r/min按机床选取nw =136 mvvcv0pr/min。所以实际切削速度vdwnw1000=8.54m/min。
3)计算基本工时:T=(L+L1+L2)/(f*n) =0.44min
工序2 :粗车Ф100外圆、车B面,车Ф90外圆及右侧面、3x2槽、Ф45外圆。
加工条件:
机床选择:CA6140车床
刀具1:刀片材料YG6,刀杆尺寸BxH=16x25mm,r010o 060 kr600
s50 kr\'8o \'05o e0.51
刀具2:刀片材料为高速钢,成型车刀,刀杆尺寸30x45 刀具3:刀片才;材料高速钢,切断车刀,刀杆尺寸16x25
(1)粗车Ф100外圆
1)选择刀具:选择刀具1 1)确定背吃刀量a 粗车的余量为1.5mm,一次走刀完成,即a =1.5mm。 2)确定进给量:查《切削用量简明手册》:加工材料HT200、工件直径100mm、切削深度a =1.5mm,则进给量为0.6~0.9 mm/r。再根据CA6140车床说明书,取
5 横向进给量取f =0.86mm/r。选择磨钝标准及耐用度:根据《切削用量简明手册》表1.9,取车刀后面最大磨损量为0.8~1.0。焊接车刀耐用度T=60mm。
3)确定切削速度V :根据《切削用量简明手册》vccvTm.axpfvyv=57.46 m/min,ns1000vdw=172 r/min。按CA6140车床转速(《机械制造工艺设计简明手册》表4.2-8)选择与172r/min相近似的机床转速n =200r/min,则实际切削速度V = 66.6m/min。
4)计算基本工时:按《机械制造工艺设计简明手册》公式计算:T=0.149min。
(2)粗车 Ф90外圆
1)选择刀具:用刀具2 2)确定背吃刀量:粗车外圆ap=1.1mm。
3)确定进给量:由《切削用量简明手册》HT200,刀杆尺寸16 x25,,工件直径为Ф90mm,则f=0.6~0.9 mm/r。再根据CA6140车床说明书,取横向进给量取f =0.86mm/r。由《切削用量简明手册》表1.9查取后刀面磨损最大限度为0.8~1.0,焊接耐用度T=60mm。
4)确定切削速度Vc:根据《切削用量简明手册》表1.27,vccvm/min
Tmv.axpyf=44
vns1000vdw=147.6 r/min,按CA6140车床转速 选择与157.5r/min相近似的机床转速n =160r/min,则实际切削速度V =47.728 m/min。 5)计算基本工时:T=(L+L1+L2+L3)×i/(f×n)=0.153min。
(3)粗车Ф45 外圆 选择刀具1 1)确定切削深度:粗车外圆,一次走刀,则ap=1.1mm。
2)确定进给量:由《切削用量手册》,HT200,刀杆尺寸16x 25,ap=1.1,工件直径为Ф45mm,则f=0.4~0.5mm/r。再由《简明手册》表4.2—3查取f =0.45mm/r。
3)确定切削速度Vc:根据《切削用量手册》表1.27查取:xfvcT.amvyvcvp=62.7 m/min。
ns1000vdw=399 r/min按CA6140车床说明书,选择与399r/min相近似的机床转速n =400r/min,则实际切削速度V = 62.8m/min。
6 4)计算基本工时:T=(L+L1+L2+L3)×i/(f×n) =0.286min。
(4)成型车刀加工B面
1)确定切削深度:一次走刀,则ap=2.5mm。T=120min 2)确定进给量:f=0.035~0.070mm/r。取f =0.050mm/r。
3)确定切削速度Vc:根据《切削用量手册》表1.27查取:vccTvmxvyv=40.602 m/min.apfns1000vdw=121.987 r/min,按CA6140车床说明书,选择与121.987r/min相近似的机床转速n =125r/min,则实际切削速度V =41.605m/min。
4)计算基本工时:T=(L+L1+L2+L3)×i/(f×n) =11.04min。
(5)车Ф90右端面及3x2槽
1)确定切削深度:一次走刀,则ap=2.5mm。
2)确定进给量:由《切削用量手册》表1.4,f=0.6~0.9mm/r。根据CA6140机床说明书(见《工艺手册》表1.31)取f=0.86 mm/r。
3)确定切削速度Vc:根据《切削用量手册》表1.27查取:vccTvmxvyv=13.965 m/min,.apfns1000vd=46.815 r/min。按CA6140车床说
w明书,选择与46.815r/min相近似的机床转速n =50r/min,则实际切削速度。V = 15.072m/min。
4)计算基本工时:T=(L+L1+L2+L3)×i/(f×n) =1.419min。
工序3粗车零件左右端面,并倒Ф20孔的倒角,零件右端45度倒角 加工条件:
机床选择:CA6140车床
刀具1:刀片材料YG6,刀杆尺寸BxH=16x25mm,r010o 060 kr600
s5
0kr\'8o \'05o e0.51
(1)粗车零件左端面,即粗车Ф 100左端面
7 1)确定切削用量ap =1.1mm。
2)确定进给量:查《切削用量简明手册》:取进给量为0.6——0.9 mm/r。再根据CA6140车床说明书(见《机械制造工艺设计简明手册》表1.31查取)进给量取f =0.86mm/r。根据《切削用量简明手册》表1.9,取车刀后面最大磨损量为0.8~1.0。焊接车刀耐用度T=60mm。
3)确定切削速度Vc :根据《切削用量简明手册》表1.27vccvTmv.axpfyv=49.56 m/min
ns1000vdw=149 r/min。按CA6140说明书,选择与149r/min相近似 的机床转速n =160r/min,则实际切削速度V =53m/min。
4)计算基本工时:按《机械制造工艺设计简明手册》公式计算:T= 0.385min。
(2)粗车零件右端面
1)确定切削用量ap =2.5mm。
2)确定进给量:查《切削用量简明手册》:取进给量为0.4~0.5 mm/r。再根据CA6140车床说明书(见《机械制造工艺设计简明手册》表1.31查取)进给量取f =0.45mm/r。根据《切削用量简明手册》,取车刀后面最大磨损量为0.8~1.0。焊接车刀耐用度T=60mm。
3)确定切削速度V :根据《切削用量简明手册》表1.27m/min 1000vvccvTmv.axpfyv=14 nsdw=89r/min按CA6140说明书,选择与89r/min相近似的机床转速n =100r/min,则实际切削速度V =15.7m/min。
4)计算基本工时:按《机械制造工艺设计简明手册》公式计算:T= 0.674min
工序4半精车Ф100外圆、B面,Ф90外圆、Ф45外圆 机床选择:CA6140车床
刀具1:刀片材料YG6,刀杆尺寸BxH=16x25mm,r10 6 kr60
0o000s50 kr8o 5 \'o0e0.51 刀尖圆弧半径0.5mm。
(1)半精车Ф100外圆 用刀具1
8 1)确定背吃刀量:半车的余量为0.9mm,一次走刀完成,即a =0.9mm。 2)确定进给量:查《切削用量简明手册》表1.6:加工材料HT200、工件直径100mm、切削深度a =0.9mm,表面粗糙度为6.3,刀尖圆弧半径0.5mm,则进给量为0.25~0.40 mm/r。再根据CA6140车床说明书,取横向进给量取f =0.30mm/r。车刀耐用度T=60mm。
3)确定切削速度Vc :根据《切削用量简明手册》表1.27vccvTmv.axpfyv=103.071 m/min
ns1000vdw=309.971 r/min。按CA6140车床转速(《机械制造工艺设计简明手册》表4.2-8)选择与309.871r/min相近似 的机床转速n =320r/min,则实际切削速度V = 106.509m/min。
4)计算基本工时:按《机械制造工艺设计简明手册》公式计算:T=0.2.6min
(2)半精车 Ф90外圆 选择刀具:用刀具1。 1)确定背吃刀量: 半精车外圆ap=1.4mm。
2) 确定进给量:由《切削用量简明手册》表1.6,HT200,刀杆尺寸16 x25,表面粗糙度为6.3,刀尖圆弧半径0.5mm,工件直径为Ф90mm,则f=0.25~0.40 mm/r。再根据CA6140车床说明书,取横向进给量取f =0.30mm/r,车刀耐用度T=60mm。
3)确定切削速度Vc:根据《切削用量简明手册》表1.27,yvcT.axf=103.071m/minn1000vd=353.719 r/min。按CA6140车床转速 mvvcvpsw选择与353.719r/min相近似的机床转速n =400r/min,则实际切削速度V =116.557 m/min。
4)计算基本工时:T=(L+L1+L2+L3)×i/(f×n)=0.115min。
(3)半精车Ф45 外圆 选择刀具1 1)确定切削深度:粗车外圆,一次走刀,则ap=1.4mm。
2)确定进给量:由《切削用量手册》,HT200,刀杆尺寸16x 25,ap=1.1,工件直径为Ф45mm,表面粗糙度为6.3,刀尖圆弧半径0.5mm,则f=0.25~0.40mm/r。再由《简明手册》表4.2—3查取f =0.30mm/r。
3)确定切削速度V:根据《切削用量手册》表1.27查取:
9 yvcT.axf=103.071 m/minnmvvcvps1000vdw=686.719r/min按CA6140车床说明书,选择与686.719r/min相近似的机床转速n =710r/min,则实际切削速度V = 107.457m/min。
4)计算基本工时:T=(L+L1+L2+L3)×i/(f×n) =0.246min。
工序5 半精车零件左端面,即Ф100左端面 加工条件:
机床选择:CA6140车床
刀具1:刀片材料YG6,刀杆尺寸BxH=16x25mm,r10 06 kr60
o000s5 0 kr\'8o 5 \'o0e0.51 刀尖圆弧半径0.5mm。
(1) 半精车Ф100左端面
1)确定背吃刀量:半精车的余量为0.9mm,一次走刀完成,即a =0.9mm。 2)确定进给量:查《切削用量简明手册》表1.6:加工材料HT200、工件直径100mm、切削深度a =0.9mm,表面粗糙度为6.3,刀尖圆弧半径0.5mm,则进给量为0.25~0.40 mm/r。再根据CA6140车床说明书,取横向进给量取f =0.30mm/r。车刀耐用度T=60mm。
3)确定切削速度V :根据《切削用量简明手册》表1.27,vccvTmv.axpyf=103.071 m/min。nvs1000vdw=316.235 r/min。按CA6140车床转速(《机械制造工艺设计简明手册》表4.2-8)选择与316.235r/min相近似 的机床转速n =320r/min,则实际切削速度V = 106.509m/min。
4)计算基本工时:按《机械制造工艺设计简明手册》公式计算:T=1.158min。
工序6 精车Ф100外圆,并倒Ф90,Ф100的倒角
1)确定背吃刀量a; 半车的余量为0.5mm,一次走刀完成,即a =0.5mm。 2)确定进给量:查《切削用量简明手册》表1.6:加工材料HT200、工件直径100mm、切削深度a =0.5mm,表面粗糙度为1.6,刀尖圆弧半径0.5mm,则进给量为0.10~0.15 mm/r。再根据CA6140车床说明书,取横向进给量取f
10 =0.12mm/r。车刀耐用度T=60mm。
3)确定切削速度V :根据《切削用量简明手册》表1.27,vccvTmv.axpyf=142.020 m/minnvs1000vdw=452.292 r/min按CA6140车床转速
的(《机械制造工艺设计简明手册》表4.2-8)选择与452.292r/min相近似 机床转速n =450r/min,则实际切削速度V = 141.3m/min。
4)计算基本工时:按《机械制造工艺设计简明手册》公式计算:T=0.315min。
工序7精车零件左端面,即Ф100左端面
1)确定背吃刀量:半车的余量为0.5mm,一次走刀完成,即a =0.5mm。 2)确定进给量:查《切削用量简明手册》表1.6:加工材料HT200、工件直径100mm、切削深度a =0.5mm,表面粗糙度为1.6,刀尖圆弧半径0.5mm,则进给量为0.10~0.15 mm/r。再根据CA6140车床说明书,取横向进给量取f =0.12mm/r。车刀耐用度T=60mm。
3)确定切削速度V: 根据《切削用量简明手册》表1.27,yvcT.axf=142.020 m/min,ns1000vmvvcvpd=452.292 r/min按CA6140车床转速
w(《机械制造工艺设计简明手册》表4.2-8)选择与452.292r/min相近似 机床转速n =450r/min,则实际切削速度V = 141.3m/min。
的4)计算基本工时:按《机械制造工艺设计简明手册》公式计算:T=2.00min。
工序8粗铣Ф90左右侧面,精铣Ф90右侧面 加工条件:
机床的选择:X62W,功率7.5KW,装夹系统刚性好;
刀具的选择:铣刀材料为YG6,由ap=8,ae=11~21mm,根据《工艺手册》表3.1—28,铣刀选择为80~110mm;由《切削手册》表6---7选择刀具如下:粗铣刀为粗齿圆柱形铣刀d1000012,40,L80,d40,r15,
o0oo~45oo,Z=10;精铣刀为细齿圆柱形铣刀d30~35oo1000,L80,d40,r015,012,
o,Z=14,圆柱铣刀寿命为180min。
11 (1)粗铣左侧面,粗铣刀具
1)切削用量:ap=8,ae=11mm ,一次完成
2)确定进给量: 由《切削手册》表3.5当机床X62W功率为5-10KW,采用YG6硬质合金材料加工铸铁取fz=0.14-0.24mm/z,取fz=0.24mm/z。
3)确定切削速度cv0vVc: 由《切削手册》表
sw3,27,yqpvcdtaxfauz=119.619m/minn1000vd=380.952r/min根据X61W机mpvvpzev床说明书(见《切削手册》表4.2-39)取主轴转速n =475r/min.则实际切削速度为Vc =149.15m/min当n =475r/min时,工作台为每分钟进给量是进给速度fm=fz×z×n机=0.24×10×475=1140mm/min.,X62W机床说明书(见《切削手册》表3.23)取fm=950mm/min 4)计算基本工时:T=(L+L1)/fm=(38+5)/950=0.0453 min。
(2) 粗铣右侧面,粗铣刀具
1)切削用量:ap=8,ae=10mm,俩次完成。
2)确定进给量: 由《切削手册》表3.5当机床X62W功率为5-10KW,采用YG6硬质合金材料加工铸铁取3)确定切削速度
fz=0.14-0.24mm/z,取
fz=0.24mm/z。
3,27,
Vc :由《切削手册》表vcdcvqv0ptaxfauzmpvyvpzev=160.952m/min
ns1000vdw=512.586r/min,根据X61W机床说明书(见《切削手册》表4.2-39)取主轴转速n =600r/min.则实际切削速度为Vc =188.4m/min,当n =600r/min时,工作台为每分钟进给量是进给速度fm=fz×z×n机=0.24×10×600=1440mm/min.,X62W机床说明书(见《切削手册》表3.23)取fm=950mm/min。
4)计算基本工时:T=(L+L1)/fm=(48.2+5+38)/950=0.096 min。 (3)精铣右侧面 精铣刀具
1)切削用量: ap=8,ae=1mm ,一次完成
2)确定进给量: 由《切削手册》表3.5当机床X62W功率为5-10KW,采用YG6硬质合金材料加工铸铁取
fz=0.14-0.24mm/z,取
Vc:
fz=0.24mm/z。
3)确定切削速度由《切削手册》表
12 3,27,vccvdq0vptaxfauzmpvyvpzev=404.312m/min,n1000vsdw=1287.618r/min根据X61W机床说明书(见《切削手册》表4.2-39)取主轴转速n =1180r/min.则实际切削速度为Vc 370.52m/min,当n =1180r/min时,工作台为每分钟进给量是进给速度fm=fz×z×n机=0.24×14×1180=2832mm/min.,X62W机床说明书(见《切削手册》表3.23)取fm=1180mm/min。
4)计算基本工时:T=(L+L1)/fm=(48.2+5)/1180=0.0451min。
工序9钻4×Ф9孔
1)刀具选择:选用Ф9高速钢,锥柄标准麻花钻。选用Z525型摇臂钻床。 2)确定切削用量:4个孔共走四次刀。由《切削用量手册》f=0.47—0.57mm/r,由钻床取 f =0.40mm/r.由《切削用量手册》,取V查=0.36m/s=21.6m/min,则n=764.331 r/min由钻床说明书,取n机=850r/min,故 。
3)计算基本工时:其中L1=8,L2=0,L=84,T= 4x0.047min=0.188min。
工序10钻Ф 4mm孔,Ф铰6mm孔 机床选择:选用Z525型摇臂钻床。 (1)钻Ф 4mm孔
1)刀具选择:由《工艺手册》选用 高速钢锥柄标准花钻。
2)确定切削用量:查《切削用量手册》f=0.18~0.22mm/r,由钻床取f=0.22mm/r.由《切削用量手册》取V =0.46m/s=27.6m/min=197r/m,由Z525钻床取n =1700r/min.,故Vc=21m/min。
3)基本工时:L1=10,L2=0,L=12.5,T= 0.07min。 (2)铰 Ф6孔
1)刀具选择:6高速钢锥柄机用铰刀,刀具磨钝标准为0.4—0.6,耐用度T=60min。
2)确定切削用量:加工余量为2mm,故背吃刀量asp=1mm。查《切削用量手册》f=0.27—0.33mm/r,由《工艺手册》f=0.26mm/r。
(3)确定切削速度:计算切削速度vc(cvdTafm0pzvxvyv其中KV=1,)kv ,CV=15.6,ZV=0.2,XV=0.1,YV=0.5,m=0.3,V = 0.21m/s=12.8m/min,n = 679r/min,取
13 n =670,V =8.415 m/min。
3)基本工时:其中L1=10,L2=2,L=7,T= 0.109min。
工序11 磨削Ф90外圆以及零件右端Ф45外圆
1)选择砂轮:WA46KV6P350x40x12。
2)切削用量的选择:砂轮转速n砂=1500 r/min,v砂=27.5m/s。轴向进给量fa=0.5B=20mm,工件速度Vw=10m/min,径向进给量fr=0.015mm/(双行程) 3)切削工时:加工Ф90外圆 圆
t12LbzbK1000vffar=0.819min,加工Ф45外t 12LbzbK1000vffar=1.606min。
工序12抛光B面 工序13刻线、刻字 工序14镀铬 工序15检测入库
四、夹具的设计 1问题的提出
本夹具用来钻Ф4和Ф6的孔,有一定的公差要求,但同时应考虑提高生产率;因此设计时,对本夹具有一定的形位要求,还应装夹方便。本夹具使用在Z525型摇臂钻床上,选用螺旋夹紧。
2、夹具设计
(1)定位和夹紧方案的选择:
由法兰盘零件的特征,采用一销一端面的定位方式,因此用一心轴和一端面的方式定位法兰盘,经过定位后的法兰盘已经限制了五个自由度,在零件的Ф100平面用螺旋夹紧方式夹紧。
(2)切削力及夹紧力计算 1) 切削力的计算:
14 轴向力:其中:
zF.yF.(N)F9.81cFd0fkF。
cF42.7d0
4f0.22
kF0.9
zF1.0
yF0.8 则:F449.3N8 2扭矩:
zM.yM.M9.81cM.d0fkmM,
其中:c0.021
zM2.0
yM0.8kM0.87
则:M0.884N*m 2)夹紧力的计算:
由《机床夹具设计手册》表1-2-20,查得:当D=32,d=8,e=1.7,Ⅲ型,得夹紧力为W0=3680(N)
3)切削力与夹紧力比较
由夹具结构知,轴向力与夹紧力垂直,欲使夹具安全工作,夹紧力产生的摩擦力必须大于轴向力。一般钢铁接触面的摩擦系数为:0.1~0.15。此处取小值0.1。则F总=2f=2×368=736>449.238所以安全。由于钻头直径为Ф4,所以产生的扭矩非常小,夹具可安全工作。
五、三维建模
4.1夹具体三维建
15 模的最后效果
4.2钻模板三维建模的最后效果
16
4.3定位套三维建模的最后效果
4.4加长快换钻套三维建模的最后效果
17
4.5支承钉三维建模的最后效果
4.6六角螺杆三维建模的最后效果
18
4.7夹具总装备三维建模的最后效果
4.8夹具总装备爆炸后三维建模的最后效果
19
20
第20篇:夹具部分习题
第六章思考题与习题
• 什么是机床夹具?它包括哪几部分?各部分起什么作用? • 什么是定位?简述工件定位的基本原理。 • 为什么说夹紧不等于定位?
• 限制工件自由度与加工要求的关系如何?
• 何谓定位误差?定位误差是由哪些因素引起的?定位误差的数值一般应控制在零件公差的什么范围内? • 对夹紧装置的基本要求有哪些?
• 何谓联动夹紧机构?设计联动夹紧机构时应注意哪些问题?试举例说明。
• 试述一面两孔组合时,需要解决的主要问题,定位元件设计及定位误差的计算。
• 根据六点定位原理,分析图 6-52 中所示各定位方案中各定位元件所消除的自由度。
图 6-52 (习题 9 图)
6-52 (习题 9 图)
• 有一批图 6-53 所示零件,圆孔和平面均已加工合格,今在铣床上铣削宽度为 b 的槽子。要求保证槽底到底面的距离为 h
;槽侧面到 A 面的距离为 a+Δa ,且与 A 面平行,图示定位方案是否合理?有无改进之处?试分析之。
图 6-53 (习题 10 图)
• 有一批如图 6-54 所示工件,采用钻模夹具钻削工件上 Φ5mm 和 Φ8mm 两孔,除保证图纸尺寸要求外,还须保证两孔的连心线通过 Φ60 mm 的轴线,其偏移量公差为 0.08mm 。现可采用如图 b、c、d 三种方案,若定位误差大于加工允差的 1/2 ,试问这三种定位方案是否可行( α=90? )?
图 6-54 (习题 11 图)
• 有一批套类零件如图 6-55a 所示,欲在其上铣一键槽,试分析下述定位方案中,尺寸 H1、H2、H3 的定位误差。 • 在可涨心轴上定位(图 b ) ; • 在处于垂直位置的刚性心轴上具有间隙的定位(图 c ) , 定位心轴直径 。
• 夹紧装置如图 6-56 所示,若切削力 F=800N ,液压系统压力 p=2×106Pa (为简化计算,忽略加力杆与孔壁的摩擦,按效 η=0.95 计算),试求液压缸的直径应为多大,才能将工件压紧。夹紧安全系数 K=2 ;夹紧杆与工件间的摩擦系数 μ=0.1 。
• 图 6-57 所示的阶梯形工件, B 面和 C 面已加工合格。今采用图 a 和图 b 两种定位方案加工 A 面,要求 A 面对 B 面的平行度不大于 20? (用角度误差表示)。已知 L=100mm , B 面与 C 面之间的高度
。试分析这两种定位方案的定位误差,并比较它们的优劣。
图 6-55 (习题 12 图)
图 6-56 (习题 13 图)
图 6-57 (习题 14 图)
第 6 章例题
【例题 6.1 】 在套筒零件上铣槽,如图 6 -27a 所示,要求保持尺寸 10 -0.08、8 -0.12 , 其他尺寸已在前工序完成。若采用图 B 的定位方案,孔与销子配合按 H7/g6 ,问能否保持加工精度要求?否则应如何改进? 按 H7/g6 的配合精度,则销子直径应为 为水平放置,故由式( 6.25 )有: ① 对于尺寸 8 -0.12 , △ 基( 8 ) =
,因销子
得 △ 定( 8 ) =0.021+0.03=0.051 在铣床上加工,其平均经济精度为 10 级 , 查表得ω =0.05 ,所以ω + △ 定( 8 ) =0.05+0.051=0.101
② 对于尺寸 10 -0.08 , 又因 △ 基( 10 ) =0 Δ 不( 10 ) =0.15+0.2=0.35 得 △ 定( 10 ) =0.35 所以 ω + △ 定( 10 ) =0.05+0.35 =0.4>δ (10) =0.08 不能满足尺寸 10 -0.08 的要求 .
③ 采用图 c 的改进方案 , 以端面 A 和右端孔为定位基准 , 销子与孔的配合仍然按 H7/g8, 则销子直径为
因 △ 基( 8 ) = △ max =0.5(0.03+0.02)=0.025 △ 不( 8 ) =0.03 得 △ 定( 8 ) =0.025+0.03=0.055 所以 ω + △ 定( 8 ) =0.05+0.055=0.105 [
【例题 6.2 】 如图 6-28 所示零件 , 在铣槽工序中 , 要保证 45 0 50 ,( 其他尺寸已在前工序完成 ).要求设计该工序的定位方案 , 并检查能否满足精度要求 .采用“一面两孔”的定位方案,此方案属于完全定位。φ 30 孔用短圆销、φ 10 孔用短削角销。 销子与孔的配合按 H7/g6, 所以短圆柱销直径为φ 30 圆弧部分直径为φ 10
。
,短削角销削角销宽度 b 及 B 查表 6 — 2 ,得 b=3,B=8 。夹具的制造公差,可取工件相应公差的 1/3 左右,即取两销中心距的制造公差为 δ L d =0.08 ,夹具上 45 0 角的制造公差取△α = 30 \' ( 是定位误差的一部分 ) 。
图 6-28 定位误差
计算实例
在铣床上加工,平均经济精度为 10 级,查表得ω =4 ¢ 。 由式( 6 — 8 )及△α, 45 0 角的定位误差为:
这种定位方案可满足加工精度要求。
若不能满足加工精度要求时,可采用下述方法解决:
• 减小销子与孔的配合间隙,销子直径可选 g5 或 h6 ,同时要适当减小削角销的宽度 b 。
• 采用活动的锥形定位销,使孔与销子无间隙配合,如图 6-29 所示。
图 6-29 活动锥形定位销的应用
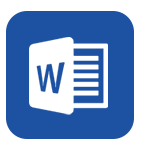