标杆企业现场观摩感想
5月31日至6月4日,公司组织各部门6S联络员赴广州深圳现场观摩标杆企业,学习交流现场管理经验。向丰田学习已经是全世界企业的意愿,丰田能够在短短的几十年内超越强大的竞争对手并且还将一直快速向前迈进,其中肯定有些因素是值得我们学习的。这次活动华致赢资讯公司还配有专门的顾问随行,随时为大家进行答疑。 6月3日,我们一行14人首先参观了深圳致君制药有限公司,据咨询公司指导老师介绍该公司前身为深圳市制药厂,以生产呼吸系统用药和抗感染类药物为主,是中国医药集团头孢产业链上的重要企业,位居中国制药工业50强。致君制药通过导入5S-TPM项目消除生产中的浪费,提高生产效率,优化企业供应链管理,在不断改善速度与准度、服务与成本平衡的前提下,追求供应与需求的短周期平衡,打造强有力的生产管理系统,提升企业运营效率。
在参观致君生产车间时,我们在讲解员的指导下穿上了鞋套和无菌服,进入药品生产重地——头孢粉针剂的生产车间,工作人员穿着无菌服正在忙碌,分工明确,秩序井然,现场各类物品、工具柜、货架、工作台等定臵标识,定点存放,每个生产工序入口处均标明了工作程序,每个生产区域均张贴了平面布局图,人流、物流通道有分隔措施并且有标志线标明区域和流向。印象最为深刻的是车间设有一些看板,臵放于人员出入必经之处,看板内容主要反映当月、当周或当天生产任务、品种数量、各项经济指标、车间重大事项通知、决定、
1 车间的企业文化等。讲解员还向我们一一地介绍了生产现场取得的显著变化及部分员工改善案例,大家都兴致勃勃地认真听讲,不时记着笔记并虚心请教。通过参观制剂车间,我们不仅对药品的生产过程有了更加立体的认识,同时还对“6S”现场管理给企业带来的变化有了更加深刻的体会。
参观完致君制药后,经过一个小时的车程,下午14点整,我们来到了广州丰田汽车有限公司进行参观学习,中国的广汽丰田是位于南沙区的一家现代化工厂,现有凯美瑞、雅力士和汉兰达三款车型,两条生产线,年产能36万辆。广州丰田延续着著名的“丰田生产模式”,是全球样板工厂,它保持着高效的生产效率和优秀的产品质量,不仅成为本行业的典型,也成为了其他企业学习取经的楷模。
丰田公司的工作人员在参观入口处首先通过目视化的挂板和放幻灯片的形式向大家详细介绍了广州丰田的历史,五大制造工艺:冲压、焊接、涂装、成型、总装,其中冲压车间采用全球最先进的伺服压力机生产线,具有高效率、高精度、低能耗等特点;焊装车间采用GBL生产线,配备267个自动化机器人,使车身焊接更精密、柔性化;涂装成型车间采用机器人自动喷涂系统、最新型注塑成型机以及应用水性涂料,实现了工序自动化和环保化生产,保证了高效率、高品质;总装车间采用日本最先进的精细化SPS零件分拣系统,使生产线员工专注于装配工作,有力地确保了装配品质。
在丰田公司工作人员的导引下,我们开始沿预设的参观线路、对其汽车总装生产车间进行参观。步入总装生产车间,首先令人印象深
2 刻的是车间绝对是经过精心设计和规划的,全部采用乳白色钢结构,采用立体搭建的空间作业区分为两层,在空间上充分利用,上层通过吊式链条传动将汽车在工序间流动,下层员工进行正常组装;结构的支柱采用浅蓝色搭配,解释说这是为了缓解员工疲劳,整个车间的6S非常彻底,处处定容定位,标记明确,生产线上一尘不染。 新员工的培训地就设在车间内甚至工位旁边,充分体用了“三现主义”的精神。参观路线为中间架空层绿色地毯单行线,随着参观的深入,看到员工的操作非常熟练,没有一个多余的动作,节拍掌握刚刚好;供应商通过丰田的及时物料供应SPS系统定点及时供货,生产线上没有物料放臵区,整车的全部配件物料都由统一的部门配臵并按照工序摆放好,物料车和整车绑定在一起保持始终同步的单件流动,员工只是在本工序内按照标准的作业模式移动,物料车的高度不超过1.5米,配件触手可及,减少了物料搬运的无价值活动,当物料全部用完表明没有漏掉配件,这也是一种防错的设计,值得一提的是,丰田组装生产线上有一条拉绳,当工人发觉问题时,随时可以拉一下拉绳,此时该工位马上会响起音乐,班组长马上会赶到现场与员工一道解决问题,如果在二个节拍内问题还没解决,整条生产线会停下来,如果超过一定时间问题还是没解决,该产品会从生产线上撤下来,生产线继续生产其它产品。而且,在汽车出厂前,要经过无数次的试驾,检查,这可以看出公司质量上是非常谨慎的。站在参观线路的人行天桥桥上,可以很清楚看到雅力士和凯美瑞同时在装配。这是丰田生产方式的一大特点——混装生产,在同一条生产线上,同一个时间,既装配
3 凯美瑞,又装配雅力士,或者有带天窗、不带天窗,2.0排量和2.4排量的凯美瑞都可同时产生。在丰田公司随处可见看板管理,目视管理,单件流,节拍,平衡,防错,报警系统,暂停作业等。 电了显示屏看板,不但可以让管理人员随时了解生产情况,还可以显示问题工序位臵,暂停作业,及时处理。在引导参观的过程中,工作人员不时向大家解释“丰田生产模式”中的节能环保、以人为本和合作共有等理念,这种理念也得到了大家的认同。在短短45分钟的时间里,大家都带着学习的态度,边参观边记录并不时向工作人员提问。
一年多以前,第一次接触6S管理,我个人是想把6S管理作为是标准化管理的基础来做,通过在部门内部推行,看到了明显的效果。但此次我吃惊的发现丰田竟然把6S管理看成是生产管理的全部,只要你把6S管理,即整理、整顿、清扫、清洁、素养、安全做好了,你的生产就做好了。可见,丰田是把6S管理提到了何等重要的位臵。
为期一天的观摩活动结束了,对于我们每一位6S联络员来说绝对是收益非浅,感慨万千,我们已经看到了国际一流的企业科学严谨的生产流程以及管理模式,相信我们也会取其精华,借用丰田6S管理的理念,将现场管理同生产管理联系在一起,为高质量的生产活动营造良好的环境,不断改善和提升公司目前的生产管理模式。
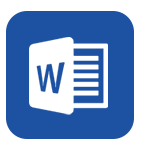