附件一
英文文献翻译
译文:
1、模具的发展
4、1 模具CAD/CAE/CAM正向集成化、三维化、智能化和网络化方向发展 (1)模具软件功能集成化
模具软件功能的集成化要求软件的功能模块比较齐全,同时各功能模块采用同一数据模型,以实现信息的综合管理与共享,从而支持模具设计、制造、装配、检验、测试及生产管理的全过程,达到实现最佳效益的目的。如英国Delcam公司的系列化软件就包括了曲面/实体几何造型、复杂形体工程制图、工业设计高级渲染、塑料模设计专家系统、复杂形体CAM、艺术造型及雕刻自动编程系统、逆向工程系统及复杂形体在线测量系统等。集成化程度较高的软件还包括:Pro/ENGINEER、UG和CATIA等。国内有上海交通大学金属塑性成型有限元分析系统和冲裁模CAD/CAM系统;北京北航海尔软件有限公司的CAXA系列软件;吉林金网格模具工程研究中心的冲压模CAD/CAE/CAM系统等。
(2)模具设计、分析及制造的三维化
传统的二维模具结构设计已越来越不适应现代化生产和集成化技术要求。模具设计、分析、制造的三维化、无纸化要求新一代模具软件以立体的、直观的感觉来设计模具,所采用的三维数字化模型能方便地用于产品结构的CAE分析、模具可制造性评价和数控加工、成形过程模拟及信息的管理与共享。如Pro/ENGINEER、UG和CATIA等软件具备参数化、基于特征、全相关等特点,从而使模具并行工程成为可能。另外,Cimatran公司的Moldexpert,Delcam公司的Ps-mold及日立造船的Space-E/mold均是3D专业注塑模设计软件,可进行交互式3D型腔、型芯设计、模架配置及典型结构设计。澳大利亚Moldflow公司的三维真实感流动模拟软件MoldflowAdvisers已经受到用户广泛的好评和应用。国内有华中理工大学研制的同类软件HSC3D4.5F及郑州工业大学的Z-mold软件。面向制造、基于知识的智能化功能是衡量模具软件先进性和实用性的重要标志之一。如Cimatron公司的注塑模专家软件能根据脱模方向自动产生分型线和分型面,生成与制品相对应的型芯和型腔,实现模架零件的全相关,自动产生材料明细表和供NC加工的钻孔表格,并能进行智能化加工参数设定、加工结果校验等。
(3)模具软件应用的网络化趋势
随着模具在企业竞争、合作、生产和管理等方面的全球化、国际化,以及计算机软硬件技术的迅速发展,网络使得在模具行业应用虚拟设计、敏捷制造技术既有必要,也有可能。美国在其《21世纪制造企业战略》中指出,到2006年要实现汽车工业敏捷生产/虚拟工程方案,使汽车开发周期从40个月缩短到4个月。
1
原文:J.C.Choi, T.H.Kwon, J.H.Park, J.H.Kim, C.H.Kim,The development of mold 《International Journal of Advanced Manufacturing Technology 》, 2002,p21~28.
译文:
2、热处理下的并行环境
并行模式与串行模式存在根本的不同(见图1)。对于串行模式,设计者大多考虑的是模具的结构与功能,但很难考虑相关的工艺,以致前者的错误很容易蔓延到后面。与此同时,设计本门很少与装配,预算会计和销售部门沟通。这些问题当然会影响模具的开发进度和市场前景。然而在并行模式中,不但以上部门关系联系密切,所有参加模具开发的部门都与买家有密切的交流。这有助于协调各部门消除矛盾,提高工作效率,同时降低成本。
(a)
(b)
2
(a)串行模式
(b)并行模式
图1.基于摸具开发的串行工程与并行工程系统框架示意图
并行环境下的热处理工艺不是在方案和工件确定以后,而是在模具设计的时候制定出来的。这样的话,将有利于优化热处理工艺,充分利用材料。 2.模具热处理CAD/CAE一体化
从图2中可以看出,热处理工艺的设计与模拟是一体化模式的核心。在信息输入产品模块中后,经热处理工艺过程产生的热处理CAD和热处理CAE模块将对于零件图,热处理以后模拟温度场的微观结构分析和可能出现的缺陷(例如过热,烧伤)自动划分网络,如果优化是根据立体视觉技术的结果重新出现,则这项热处理工艺已经被审核。而且工具与夹具的CAD和CAE也集成于这种系统中以并行工程为基础的集成模式可以与其它类似模式共享信息。这样使热处理工艺得到优化,并确保改工艺准确。
3
图2.并行工程热处理CAD/CAE一体化系统框架示意图 2.1采用三维模型和立体视觉技术的热处理
在形成模具的基础上,材料,结构和尺寸的问题能通过热处理三维模型尽快发现出来。在热处理过程中,模具加热条件和相变条件是切合实际的,因为通过计算相变热力、相变动力、相应力、热应力、传热速度、流体动力等已经取得重要突破。例如,能进行局部复杂表面和不对称模具的三维热传导模型计算,和能进行微观结构转变的MARC软件模型。计算机能够在任何时间提交温度,微观结构和应力的信息,并通过连接温度场微观结构领域和力场来显示三维形式的全部改变过程。如果再加上这种特性,则各部分性能都能通过计算机预见。 2.2热处理工艺设计
由于对强度和硬度,表面粗糙度和模具热处理变形的特殊要求,淬火介质的种类、淬火温度、回火温度和时间等参数特性必须经过适当的选择,以及是否使用表面淬火或化学热处理,这种特性必须准确的制定下来。自从计算机技术在最近几十年迅速的发展,难以进行大型计算已经成为过去。通过模拟和仔细考虑热处理特性,热处理后的成本和所须时间,这些都并不难优化热处理工艺。 2.3热处理数据库
热处理数据库在图3中描述。数据库是制定热处理工艺的基础。一般来说,热处理数据库分为材料数据库和工艺数据库。通过材料和工艺来预测特性已成为一种必然的趋势。尽管很难建立一个特性数据库,但通过一系列的测试来建立数据库是必要的。材料数据库包括材料牌号、化学成分、性能和国内外同级别目录表。工艺数据库包括热处理标准、种类、保温时间和冷却温度。基于数据库,热处理工艺可以通过推理规则创造出来
。
图3.热处理数据库 2.4热处理工具和设备
在热处理工艺确定以后,工具及设备CAD/CAE系统传送设计和制造的数值信息来控制装置。通过快速模具成型,可靠的工具和夹具都能被确定。整个程序通过网络传送,不存在任何人为干扰。
4
原文: 2.LI Xiong,ZHANG Hong-bing,RUAN Xue—yu,LUO Zhong—hua,ZHANG Yan., Heat Treatment of Die and Mould Oriented Concurrent Design,《Heat Treatment of Die and Mould Oriented Concurrent Design[J].Journal of Iron and Steel Research》,2006,第13期,P40~43.
译文:
3、压铸模具系统的发展
压铸工艺是用于制造精确尺寸,轮廓分明的金属部件的主要选择之一。压铸的模具设计的几个阶段包括,并且需要大量的时间。此外,经常性的修改是必需的,由于在达到一个可接受的初始模具设计的复杂性。因此,模具设计通常非常耗时。如果适当的应用软件开发,集成了不同的模具设计阶段,并允许模具设计编辑压铸行业将大大受益。此外,模具正在越来越多地进行设计,压铸全部或部分与3维计算机辅助设计(CAD ) ,作为3维CAD增强了复杂模具设计的可视化,并帮助用户在设计修改。因此当务之急是要建立一个计算机辅助的模具设计系统,缩短模具设计同时代一直在单独管芯元件的自动化或半自动化设计一些最近的研究,但是在这些方面小发表的作品。大多数已发表的作品集中的模具设计浇注系统上。例如, Wu等人。 [ 1 ]提出了浇注系统的原型设计,使用P -Q技术和基于特征的参数化设计压铸。该系统是建立在商业的Unigraphics CAD系统。还有被称为DiEdiFice商业模具设计中的应用[ 2 ] ,侧重的模具设计浇注系统上。它是一种三维设计应用压力压铸用来设计一个精确和高效的浇口和流道系统。 DiEdiFice不协助建立喷射器,并涵盖腔inserts.With考虑到整个模具设计系统, Choi等人。 [ 3 ]开发了基于AutoCAD平台之上的系统。但是,该系统仅适用于简单的形状,如帽形。此外,该系统只能用于单印象模具和具有无底切的产品。 Zhang等人。 [ 4 ]也做了一个集成的CAD / CAE系统,用于压铸的一项研究。当时的想法是,以确定模具的几何形状和采用CAD工艺参数,然后利用CAE软件包,以优化的基础上,仿真分析流程设计。另一方面,一些专门的软件套件已经被引入半自动化注塑模具的设计。这样的软件包的一个例子是IMOLD (智能模具设计与装配系统) [ 5 ] 。虽然有压铸模具和注塑模具之间有一些相似之处,前者浇注
5
系统的设计更为复杂[ 1 ] 。因此IMOLD和半自动化的注塑模具设计其它相似的专门的软件产品的不适合在本研究进行的模design.The方法包括: (1)基于特征和基于约束的建模, (2)参数化设计和(3)几何形状和边界表示( B- REP)拓扑模型提取技术。基于特征的模型构建的产品的模型上直接的功能的基础。基于特征的模型不仅包含基本的几何和拓扑数据,而且高层次的信息,这使得模具设计人员相对复杂形状添加到他们的设计中。基于约束的建模涉及了用于创建一组可控制的变化如何,可以向组几何元素的规则限制。为代表的3D形状的几何约束可分为以下三种类型:拓扑约束,结构约束和尺寸约束[ 6 ] 。在参数化系统基于约束的建模捕获并依次解决了约束方程。因为它解决不了耦合方程,可预测的模式将导致。基于约束的建模允许CAD系统来捕捉模设计者的意图和关系可以基于此的意图。基于约束的造型也允许更改可以通过模式迅速传播。参数化设计处理可变尺寸为控制参数,它是基于参数创建模型的有效工具。参数设计不仅增加了设计效率,而且也使更新和现有设计的修改更容易和更快,因为这些可以通过改变参数模型的参数来实现[ 7,8 ] 。边界表示法是一种常用的实体建模表示方法。在这个方案中固体的代表在各个曲面,边和顶点的条款。 B-代表模型比构造实体几何( CSG)的一个更为明确的表示,并且可以分为两部分,拓扑结构和几何形状。拓扑记录面,边和顶点通过在数据结构的指针的装置的连接,同时几何定义的确切形状和各边缘的位置,朝向和vertices.The建议压铸设计系统使模具设计人员创建一个压铸模具与产品零件模型开始。模具设计人员可以设计出与模具型腔嵌件,核心幻灯片,模具基地,浇注系统,顶出系统和标准组件。此外,该系统可确保当模具设计者修改模具的设计,这些变化可以容易地进行。该系统使用Visual C + +语言在SolidWorks的2001平台上开发。该模具设计系统的实施是说明与案例研究。工作的详细内容在下面的章节中描述。
原文:Y.K.Woon1 and K.S.Lee1 《Development of a die design system for die casting》,2004,p399~411
6
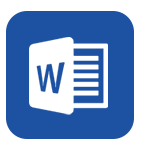