I 吉林化工学院本科毕业设计说明书
摘
要
换热器在石油化工行业中有着广泛的应用,本次设计针对水的冷却问题,工艺和操作的要求、经济上的要求、保证安全生产。由所给的设计条件,我们选取了水冷却器,并根据《化工工艺设计手册》、GB150-98和GB151-99等设计标准对冷却器进行了工艺计算和结构设计,进一步确定了冷却器的各种尺寸,并用CAD软件绘制了冷却器的装配图和零件图。
设计出来的流程和设备首先要保证质量,操作稳定,这就必须配置必要的阀门和计量仪表等,并自确定方案时,考虑到各种流体的流量,温度和压强变化使采取什么措施来调节,而在设备发生故障时,加修应方便。在确定某些操作指标和治标和选定设备型式以及仪表配置时,要有经济核算的观点,既满足工艺和操作要求,又使施工简便,材料来源容易,造价低廉。如果有废热可以利用,要尽量节省热能,充分利用,或者采取适当的措施达到降低成本的目的。在工艺流程和操作中若有爆炸、燃烧、中毒、烫伤等危险性,就要考虑必要的安全措施。
关键词:换热器;结构设计;工艺设计;GB150-98;GB151-99
II 吉林化工学院本科毕业设计说明书
Abstract Heat exchangers in the petrochemical industry has a wide range of applications, this design for water cooling, proce and operational requirements, economic requirements, to ensure safe production.Given by the design conditions, we selected water cooler, and under "Chemical Proce Design Manual", GB150-98 and GB151-99 and other design criteria of the cooler to the proce calculation and structural design, further defined the cooler various sizes and uses CAD software to draw the cooler aembly drawings and parts drawing.Procees and equipment designed first to ensure the quality, stable operation, which must configure the neceary valves and measurement instruments and so on, and since established programs, taking into account fluid flow, temperature and preure changes so that the measures taken to regulation, and in equipment failure, plus repair should be easy.In determining the indicators and symptoms of certain operations and the selection of equipment type, and instrument configuration, there must be economic accounting point of view, not only meet the technological and operational requirements, and also allows easy construction, easy sources of material, low cost.If waste heat can be used to try to save energy, make full use of, or take appropriate measures to reduce costs.If in the proce and operators in the explosion, burning, poisoning, burns and other dangers, we must consider the neceary security Key Words:Heat exchangers;Structural Design;Proce Design;GB150-98;GB151-99
II
III 吉林化工学院本科毕业设计说明书
目录
摘
要 ·········································································································································· I Abstract ··································································································· 错误!未定义书签。 第1章
绪论 ······················································································································· I
1.1综述 ··································································································································· I
1.1.1简述 ···························································································································· I 1.1.2固定管板式换热器 ··································································································· I
1.2发展历史 ························································································································ II 1.3换热机组的构造 ········································································································ IV 1.4换热器常见问题及处理 ························································································· IV
第2章
结构设计 ··································································· 错误!未定义书签。
2.1 管箱设计 ···················································································· 错误!未定义书签。
2.1.1 管箱短节 ·············································································· 错误!未定义书签。 2.1.2 分程隔板 ············································································ 错误!未定义书签。 2.1.3 管箱深度 ············································································ 错误!未定义书签。
2.2
封头设计 ··············································································· 错误!未定义书签。
2.2.1 受内压封头计算 ································································ 错误!未定义书签。 2.2.2 受外压封头计算 ································································ 错误!未定义书签。
2.3
圆筒设计 ············································································· 错误!未定义书签。 2.4
管板设计 ··············································································· 错误!未定义书签。
IV 吉林化工学院本科毕业设计说明书
2.5 拉杆和定距管的确定 ························································· 错误!未定义书签。 2.6
折流板设计··········································································· 错误!未定义书签。 2.7 旁路挡板设计 ········································································ 错误!未定义书签。 2.8 容器法兰的设计 ··································································· 错误!未定义书签。 2.9 选取支座 ·················································································· 错误!未定义书签。
第3章
强度校核 ······························································································· V
3.1 前端管箱筒体计算 ································································································ V
3.1.1 计算条件 ·············································································································· V 3.1.2 厚度及重量计算 ···································································································· V 3.1.3 压力实验时应力校核 ··························································································· VI 3.1.4 压力及应力计算 ··································································································· VI
3.2 前端管箱封头计算 ······························································································· VI
3.2.1 计算条件 ············································································································· VI 3.2.2 厚度及重量计算 ································································································ VII 3.2.3 压力计算 ············································································································ VII
3.3
壳程筒体计算 ······································································································ VII
3.3.1 计算条件 ············································································································ VII 3.3.2 厚度及重量计算 ······························································································ VIII 3.3.3 压力试验时应力校核 ······················································································ VIII 3.3.4 压力及应力计算 ································································································· IX
3.4 开孔补强计算 ········································································································· IX
3.4.1 计算条件 ············································································································· IX 3.4.2 开孔补强计算 ······································································································ X 3.4.3设计条件 ················································································································ XI 3.4.4 开孔补强计算 ····································································································· XI 3.4.5
设计条件 ·········································································································· XII
IV
V 吉林化工学院本科毕业设计说明书
3.4.6 开孔补强计算 ·································································································· XIII
3.5 延长部分兼作法兰固定管板式管板 ·························································· XIV
3.5.1 设计计算条件 ·································································································· XIV
3.5.2 仅有壳程压力作用
Ps下的危险组合工况(
Pt0) ··································· XX
PP03.5.3 仅有壳程压力作用t下的危险组合工况(s) ······························· XXVI
第4章
换热器的制造、检验、安装与维修 ·························· XXXII
4.1 换热器的制造、检验与安装 ······································································· XXXII
4.1.1筒体 ·················································································································· XXXII 4.1.2 换热管 ············································································································· XXXII 4.1.3 管板 ················································································································· XXXII 4.1.4折流板、支持板 ··························································································· XXXIII 4.1.5管束的安装 ··································································································· XXXIII 4.1.6换热器的组装 ······························································································· XXXIII 4.1.7压力试验 ······································································································· XXXIII
4.2换热器的安装、试车和维护 ······································································ XXXIII
4.2.1安装 ················································································································ XXXIII 4.2.2试车 ················································································································ XXXIV 4.2.3维护 ················································································································ XXXIV
结 论 ························································································································· XXXV 参考文献 ······················································································································· XXXVI 致谢 ··································································································································· XXXVII
- V
II 吉林化工学院本科毕业设计说明书
一次称为一个壳程。为提高管内流体的速度,可在两端封头内设置适当隔板,将全部管子平均分隔成若干组。这样,流体可每次只通过部分管子而往返管束多次,称为多管程。同样,为提高管外流速,可在壳体内安装纵向档板使流体多次通过壳体空间,称多壳程。在管壳式换热器内,由于管内外流体温度不同,壳体和管束的温度也不同。如两者温差很大, 换热器内部将出现很大的热应力,可能使管子弯曲,断裂或从管板上松脱。因此,当管束和壳体温度差超过50℃时,应采取适当的温差补偿措施,消除或减小热应力。
1.2发展历史
二十世纪20年代出现板式换热器,并应用于食品工业。以板代管制成的换热器,结构紧凑,传热效果好,因此陆续发展为多种形式。30年代初,瑞典首次制成螺旋板换热器。接着英国用钎焊法制造出一种由铜及其合金材料制成的
III 吉林化工学院本科毕业设计说明书
在完成同样传热量的条件下,采用逆流可使平均温差增大,换热器的传热面积减小;若传热面积不变,采用逆流时可使加热或冷却流体的消耗量降低。前者可节省设备费,后者可节省操作费,故在设计或生产使用中应尽量采用逆流换热。
当冷、热流体两者或其中一种有物相变化(沸腾或冷凝)时,由于相变时只放出或吸收汽化潜热,流体本身的温度并无变化,因此流体的进出口温度相等,这时两流体的温差就与流体的流向选择无关了。除顺流和逆流这两种流向外,还有错流和折流等流向。
在传热过程中,降低间壁式换热器中的热阻,以提高传热系数是一个重要的问题。热阻主要来源于间壁两侧粘滞于传热面上的流体薄层(称为边界层),和换热器使用中在壁两侧形成的污垢层,金属壁的热阻相对较小。
增加流体的流速和扰动性,可减薄边界层,降低热阻提高给热系数。但增加流体流速会使能量消耗增加,故设计时应在减小热阻和降低能耗之间作合理的协调。为了降低污垢的热阻,可设法延缓污垢的形成,并定期清洗传热面。
一般换热器都用金属材料制成,其中碳素钢和低合金钢大多用于制造中、低压换热器;不锈钢除主要用于不同的耐腐蚀条件外,奥氏体不锈钢还可作为耐高、低温的材料;铜、铝及其合金多用于制造低温换热器;镍合金则用于高温条件下;非金属材料除制作垫片零件外,有些已开始用于制作非金属材料的耐蚀换热器,如石墨换热器、氟塑料换热器和玻璃换热器等。
III
- 4
VI 吉林化工学院本科毕业设计说明书
有效厚度:enC1C212210mm
2.1.3 压力实验时应力校核 压力试验类型:液压试验 试验压力值:PT1.25p[]1701.250.50.625MPa []t170压力试验允许通过的应力水平[]T:[]T0.90S0.900.85275244.80MPa 试验压力下圆筒的应力:TPT(Die)0.625(80010)25.31MPa
2e210应为T[]T所以校核结果合格 2.1.4 压力及应力计算
2e[]t2101470.853.42MPa 最大允许工作压力:[PW](Die)(80010)t设计温度下 计算应力:Pc(Die)0.5(80010)20.25MPa
2e210[]t1470.85138.55MPa
应为[]tt 结论:筒体名义厚度大于或等于GB151中规定的最小厚度12.00mm,合格
2.2 前端管箱封头计算
2.2.1 计算条件
计算压力:Pc0.50MPa
VII 吉林化工学院本科毕业设计说明书
设计温度:t=110.00C 内径:Di800.00mm 曲面高度:hi200.00mm 材料:Q345R板材
实验温度许用应力[]=170.00MPa 设计温度许用应力[]=170.00MPa 钢板负偏差C1=0.30mm 腐蚀余量C22.00mm 焊接接头系数:0.85 2.2.2 厚度及重量计算
t1Di形状系数:k262hi计算厚度:21800221.0000
62400kP10.5800cDi1.25mm t2[]0.5Pc21890.850.50.512.00mm 名义厚度:nC1C23.55圆整后为4,可取名义厚度为有效厚度:enC1C2120.329.70mm 结论:此厚度满足最小厚度要求 2.2.3 压力计算
2[]te21890.859.7]3.87229MPa 最大允许工作压力:[PWkDi0.5e18000.59.7结论:合格
2.3 壳程筒体计算
2.3.1 计算条件 计算压力:Pc0.4MPa
VII
- 4
X 吉林化工学院本科毕业设计说明书
接管腐蚀裕量:1mm 接管厚度负偏差:Clt0.875mm 接管材料许用应力:[]=140.0MPa
t2.4.2 开孔补强计算 壳体计算厚度:PcDi0.48001.35mm
2[]tPc21400.850.4PcDi0.4180.308mm t2[]Pc214010.4接管计算厚度:t[]t1401 接管材料强度消弱系数:frr[]140开孔直径:ddi2C182324mm
d=123
Ad2et(1fr)241.35032.4mm2
壳体多余金属面积:
A1(Bd)(e)2et(e)(1fr)
(5524)(8.51.35)0221.65mm2
接管多余金属面积:
XI 吉林化工学院本科毕业设计说明书
A22h1(ett)fr2h2(etC2)fr
29.17(0.50.026)108.69mm2 补强区焊缝面积(焊脚取8.0mm)
1A327749mm2
2由于A1+A2+A3=279.34mm2>A=32.4mm2 所以不需要另加补强。 接管:B 454 2.4.3设计条件
接管实际外伸长度:156mm 接管实际内伸度:0mm 接管焊接接头系数:1 接管厚度负偏差:Clt1mm 接管材料许用应力:[]=130.0MPa
t2.4.4 开孔补强计算 壳体计算厚度:PcDi0.48001.35mm t2[]Pc21400.850.4PcDi0.4370.331mm
2[]tPc214010.4接管计算厚度:t[]t1401 接管材料强度消弱系数:fr[]r140开孔直径:ddi2C37643mm 补强区有效宽度:B=2d=243=86mm 接管有效外伸长度:h1dnt43413.11mm 接管有效内伸长度:h20mm 开孔消弱所需的补强面积:
XI
- 4
XIV 吉林化工学院本科毕业设计说明书
所以不需要另加补强。
2.5 延长部分兼作法兰固定管板式管板
2.5.1 设计计算条件 1.壳程圆筒:
设计压力:PS0.4MPa 设计温度:TS1500C平均金属温度:ts150oC 装配温度:t015OC 材料名称:Q345R 设计温度下许用应力:[]=140MPa
t平均金属温度下弹性模量:ES2.06105MPa平均金属温度下热膨胀系数:s1.18105MPa 壳程圆筒内直径:Di800mm 壳程圆筒名义厚度:s12mm 壳程圆筒有效厚度:se8.5mm
壳体法兰设计温度下弹性模量:E'f1.992105MPa
壳程圆筒内直径横截积:A0.25Di20.253.14800250.24104mm2 壳程圆筒金属横截面积:
ASS(Dis)3.1412(80012)0.30596105mm2
2.管箱圆筒:
XV 吉林化工学院本科毕业设计说明书
设计压力:Pt0.5MPa 设计温度:TS110OC 材料名称:16Mn 设计温度下弹性模量:En1.992105MPa 壳程圆筒名义厚度:h12mm 壳程圆筒有效厚度:he10mm
管箱法兰设计温度下弹性模量:E'"f1.992105MPa 3.换热管:
材料名称:20(GBT8163) 管子平均温度:tt110OC
设计温度下管子材料许用应力:[]tt=132MPa 设计温度下管子材料屈服应力:st245MPa 设计温度下管子材料弹性模量:n1.884105MPa平均金属温度下管子材料弹性模量:Et1.903105MPa
平均金属温度下管子材料热膨胀系数:t1.166105mm/mm0C 管子外径:d=25 mm 管子壁厚:t2.5mm 管子根数:n=453 换热管中心距:S=32mm 一根管子金属横截面积:at(dt)3.142.5(252.5)176.625mm2 换热管长度:L=3000mm 管子有效长度:L=3000mm 管束模数:Ke7680MPa
管子回转半径:i0.25d2(d2t)20.25252(2522.5)28.004mm
XV
- 4
XVIII 吉林化工学院本科毕业设计说明书
"12Efbf"kf12Dibf2"fDi3"Eh3122.061053221452.09100.0005254 12800328007MPa6.壳体法兰: 材料名称:20II 管箱法兰厚度:'f20mm 法兰外径:Df240mm
法兰宽度:bf(DfDi)/2(24020)/2110mm 比值:s/Di5/8000.006 比值:'f/Di20/8000.025
系数C':按s/Di,'f/Di,查GB151-1999图25得C"=0.00 系数":按s/Di,'f/Di,查GB151-1999图26得"=0.0003108 旋转刚度:
2E"b1ffk"f12Dibf2"fDi3"Eh3122.0610511022052.09100.0003108 128001108006MPa
XIX 吉林化工学院本科毕业设计说明书
7.系数计算:
法兰外径与内径之比:KDfDi'240/1351.78
壳体法兰应力系数Y:按k查GB150-1998表9-5得k=20.81
~kf3.1460.0006133 选择刚度无量纲参数:kf4kt47680~管板第一弯矩系数:按k, kf查GB151-1999图27得m10.01
m0.019.16 系数:~1kkf1.780.0006133按kt,kf查GB151-1998图29得G25.0141 换热管束与不带膨胀节壳刚度之比:
Etna2.06105453176.625Q6.35
ESAS2.061051.26104管板第二弯矩系数:按K,Q查GB151-1999图28(a)得m24 系数:M1m10.010.000247
2k(QG2)21.78(6.355.0141)系数:按K,Q查图30得G30.002206 法兰力矩折减系数:~kf0.00061330.2175 ~(kfG3)0.00061330.0022062.8652.865~~法兰力矩变化系数:MfMkf/k"f0.7963
10~M其中111.223 '6k"f0.217510kf8.管板系数:
管板开孔后面积:A1A0.25nd2
= 5.0241050.254533.142522.802105mm2 管板布管区面积:Atns2Ad4533227.3251052.871105mm2
XIX
- 4
XXII 吉林化工学院本科毕业设计说明书
1(1V)G11(11.0233)0.9~0.04006 不计温差应力时:r4(QG2)46.355.0141~1(1V)G11(10.2683)2.90.04668 计温差应力时 :r4(QG2)46.355.014111.管板布管区周边处径向应力系数:
~'不计温差应力时:r3(1V)m3(11.0233)0.207250.0055
4(QG2)k4(6.355.0141)5.07~'3(1V)m3(10.2683)1.45310.01384 计温差应力时 :r4(QG2)k4(6.355.0141)5.0712.管板布管区处剪切应力系数:
~不计温差应力时:p1(1V)111.02330.0445
4(QG2)46.355.0141~1(1V)110.26830.0161 计温差应力时 :p4(QG2)46.355.014113.壳体法兰力矩系数:
不计温差应力时: ~~MwsMmMfM10.21750.10990.79630.0002470.023707 计温差应力时: ~~MwsMmMfM10.2175(0.0311)0.79630.0002470.006961 14.管板径向应力: 不计温差应力时:
Di0.5715800~P计算值:r0.040063.246851.62MPa ra0.448许用值:1.5[]tr1.5189283.5MPa
22XXIII 吉林化工学院本科毕业设计说明书
计温差应力时:
Di0.5715800~Pr0.04668(11.479)212.7MPa ra0.448许用值:3[]tr3189567MPa 15.管板布管区周边径向应力: 不计温差应力时: 计算值:
Pa'Dikk2'rr1(2m)m2m3.24680.57158000.00550.4483.64MPa22225.075.07210.2072520.2072520.20725
许用值:1.5[]tr1.5189283.5MPa 计温差应力时: 计算值:
PDr'ar'i2kk21(2m)m2m2(11.479)0.5715800(0.01384)0.4480.1628MPa5.075.07211.453121.453121.4531
许用值:3[]tr3189567MPa 16.管板布管区周边剪切应力系数: 计算值:pPa~Dt3.24680.5715715.36p0.04453.08MPa 0.448许用值:0.5[]tr0.518994.5MPa 计算值:pXXIII Pa~Dt11.4790.5715715.36p0.01613.56MPa 0.448- 4
XXVI 吉林化工学院本科毕业设计说明书
许用值:3[q]364.3192.9MPa(焊接)
2.5.3 仅有壳程压力作用Pt下的危险组合工况(Ps0) 1.换热管与壳程圆筒热膨胀变形差: 不计温差应力时:0.0 计温差应力时:rt(ttt0)s(tst0) 1.166105(11815)1.18105(13815)0.0002503
2.当量压力组合:
不计温差应力时:PcPt(1)0.4(10.2856)0.51424MPa 计温差应力时:PcPt(1)0.4(10.2856)0.51424MPa 3.有效压力组合: 不计温差应力时:
PatptEt12.6750.40.285602.061055.070096
计温差应力时 :
PatptEt12.6750.40.2856(0.0002503)2.061055.0699
4.基本法兰力矩系数:
4Mm47.421070.0637 不计温差应力时:Mp33Dipa0.57153.148005.0700964Mm47.421070.0637 计温差应力时 :MpDi3pa0.57153.1480035.06995.管板边缘力矩系数:
~~不计温差应力时:MMp0.0637
XXVII 吉林化工学院本科毕业设计说明书
~~计温差应力时 :MMp0.0637
6.管板边缘剪力系数:
~不计温差应力时:VM9.160.06370.583492 ~计温差应力时 :VM9.160.06370.583492
7.管板总弯矩系数: 不计温差应力时:mm1m2V0.0140.5834921.4803
1V10.583492计温差应力时 :mm1m2V0.0140.5834921.4803
1V10.5834928.系数G1e仅用于m>0时G1e3m/k:
不计温差应力时:G1e3m/k31.48030.4/5.070.3504 计温差应力时 :G1e3m/k31.48030.4/5.070.3504 9.当m>0时,由GB151-1999.按k和m查图31(b)得: 不计温差应力时:m>0时,G10.3504 计温差应力时 :m>0时, G10.3504 10.管板径向应力系数:
1(1V)G11(10.583492)0.3504~0.012206 不计温差应力时:r4(QG2)46.355.0141~1(1V)G11(10.583492)0.35040.012206 计温差应力时 :r4(QG2)46.355.014111.管板布管区周边处径向应力系数:
~'不计温差应力时:r3(1V)m3(10.583492)1.48030.0305
4(QG2)k4(6.355.0141)5.07~'3(1V)m3(10.583492)1.48030.0305 计温差应力时 :r4(QG2)k4(6.355.0141)5.0712.管板布管区处剪切应力系数:
XXVII
- 4
XXX 吉林化工学院本科毕业设计说明书
Di~'fMwsPa'4f23.1480016.740.0237075.0700960.5715 42014.44MPa2许用值:1.5[]tr1.5132198MPa 计温差应力时: 计算值:
Di~'fMwsPa'4f23.1480016.74(0.0069)5.06990.5715 420116MPa2许用值:3[]tr3132396MPa 18.换热管轴向应力: 不计温差应力时: 计算值:rG2QV1PPa cQG215.01416.350.5834920.514245.070096
0.28566.355.01417.828MPa许用值:[]tr132MPa []cr46.91MPa 计温差应力时:
XXXI 吉林化工学院本科毕业设计说明书
G2QV1Pa 计算值:rPcQG215.01416.350.5834920.514245.0699 0.28566.355.014136.02MPa许用值:3[]tr396MPa []cr46.91MPa 19.壳程圆筒轴向应力: 不计温差应力时: 计算值:
AcAs(1V)5.024105PaPt(QG2)1.261040.5715(10.583492)0.55.0700967.332MPa6.355.014许用值:[]tl1132132MPa 计温差应力时: 计算值:
AcAs(1V)5.024105PaPt4(QG)21.26100.5715(10.583492)0.55.069913.18MPa 6.355.0141许用值:3[]tr396MPa 20.换热管与管板连接拉脱应力: 不计温差应力时:
ra5.4766176.71094.809MPa 计算值:qdl2530003.14许用值:[q]64.3MPa
ra6.198176.710922.12MPa 计温差应力时:qdl2530003.14许用值:3[q]364.3192.9MPa(焊接)
XXXI
- 4
XXXIV 吉林化工学院本科毕业设计说明书
地角螺栓两侧均有垫铁,设备招平后,斜垫铁,可与设备支座底板悍牢,但不得与下面的平垫铁或滑板焊死。
垫铁的安装不应妨碍换热器的热膨胀。 3.2.2试车
试车前应查阅图纸有无特殊要求和说明。名牌有无特殊标志。试车前应清洗整个系统,并在入口接管处设置过滤网,系统中如无旁路,试车时应增设临时旁路。 试车开始后,开启放气门,使流体充满设备,此设备的物料为蒸汽,开车前应排空残液,以免形成水击,因为此设备的介质有腐蚀性,停车后应降参与介质排净, 开车和停车过程中,应逐渐升温和降温,以免造成压差过大和热冲击。 3.2.3维护
换热器不得在超过铭牌规定的条件下进行,要经常对管壳程介质的温度和压降进行监督,分析换热器的泄露和结构情况。在压降增大和传热系数降低超过一定数值时,应根据介质和换热器的结构,选择有效地方法进行清洗,应经常监视管束的震动情况。
XXXV 吉林化工学院本科毕业设计说明书
结
论
近年来,随着我国石化、钢铁等行业的快速发展,换热器的需求水平大幅上涨,但国内企业的供给能力有限,导致换热器行业呈现供不应求的市场状态,巨大的供给缺口需要进口来弥补。换热器是一种高效紧凑的换热设备,它的应用几乎涉及到所有的工业领域,而且其类型、结构和使用范围还在不断发展。
再沸器作为换热器的一种,在工业生产中的作用也越来越重要,其发展和改进必定引起工业生产效率的大幅度提高。
XXXV
- 4
XXXVIII 吉林化工学院本科毕业设计说明书
为以后走上工作的岗位奠定良好的基础。
在最后,我要感谢我的指导教师王海波在毕业设计这段时间里,给我的指导和帮助,让我少走了很多弯路,学会了许多知识,掌握了新的技能。
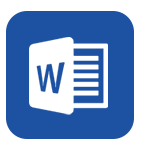