超声波探伤工艺规程
1 适用范围
1.1 本规程适用于造船、修船、海洋工程及军工产品的船舶焊接焊缝的超声波探伤
1.2 本规程适用于材料厚度不小于6mm的铁素体钢全焊透熔化焊对接焊缝脉冲反射法手工超声波检验.
1.3 本规程不适用于铸钢及奥氏体不锈钢焊缝;外径小于159mm的钢管对接焊缝;内径小于200mm的管座角焊缝及外径小于250mm和内外径之比小于80%的纵向焊缝. 2 引用标准
ZBY344-85 超声波探伤用探头型号命名方法
ZBY231-84 超声波探伤用探头性能测试方法
ZBY232-84 超声波探伤用1号标准球块技术条件
CB/T3559-93 船舶钢焊缝手工超声波探伤工艺和质量分级
CB/T11345-89 钢焊缝手工超声波探伤方法和探伤结果的分级
JISZ3060-85 钢焊部的超声波探伤试验方法及试验结果的等级分类方法
GJB64.1-97 舰船船体规范(水面舰艇) AWS D1.1-2001美国焊接协会无损检验标准
3 探伤人员
3.1 从事焊缝探伤的检验者,应具有焊缝超声波探伤实践经验,并掌握一定的材料、焊接基础知识.
3.2 超声波探伤人员,应具有国内外各船级社相互认可的Ⅱ级以上资格证书.
3.3 持有Ⅱ级以上超声波探伤者,才能进行实际探伤并签发探伤报告。其资格证书必须在有效期内。
4 探伤仪、探头和系统性能
4.1 探伤仪
使用A型显示脉冲反射式探伤仪,工作频率范围为1-5MHz,仪器配备衰减器或增益控制器,其精度为任意相邻12dB误差在±ldB,步进级每档不大于2dB,总调节量应大于60dB.水平线性误差不大于1.0%,垂直线性误差不大于5.0%.
4.2 探头
4.2.1 探头规格型号应按ZBY344-85标准的规定作出标志.
4.2.2 斜探头的公称折射角ß为45º;60º;70º或K值为1.0;1.5;2.0;2.5. 4.2.3 折射角的实测值与公称值的偏差不大于2º. 4,2.4 探头频率通常使用2.5MHz或5MHz.
4.3 系统性能
4.3.1 系统有效灵敏度必须大于评定灵敏度10dB以上.
4.3.2 斜探头远场分辨力Z≥6dB.
4.3.3 探伤仪、探头、系统性能、除灵敏度余量外,均按ZBJ04001的规定方法进行试.
4.3.4 超声波探伤仪器按标准规定,每三个月至六个月进行周期技术鉴定一次.
5探伤用试块
5.1 对比试块应采用与被检工件相同或声学性能相近的材料制成.该材料用直探头检,不得有大于至Ф2.0平底孔当量直径的缺陷.
5.2 试块的制做应符合ZBY232和JB4126的规定.
5.3 试块一般采用V
1、V
2、CSK-1A以及与标准规定相对应的对比试块. 5.4 现场检测时,也可以采用其它形式的等效试块.
5.5 超声波探伤用标准试块应送计量部门每年进行一次检定
6耦合剂及补偿
6.1 通常采用机油,浆糊,甘油和水等透声性好,且不损伤检测工件表面的耦合剂. 6.2 在现场检测和缺陷定量时,应对工件表面粗糙度引起的能量损耗进行补偿.(一般为4—6d
.
6.3 在现场检测和缺陷定量时,应对材料衰减引起的检测灵敏度降低和缺陷定量误差进行实测补偿.
7探伤前的准备
7.1 检测面
7.1.1 探头扫查的区域范围内应无焊接飞溅物、氧化皮、油垢及其它杂质。被检测表面应平整光滑,便于探头移动扫查,表面粗糙度Ra应达到6.3um.探头移动区域应不小于1.25P;P=2TK或P=2Ttg ß式中P一跨距mm,T一母材厚度mm,K一探头K值,ß一探头折射角.
7.1.2 探测区域的宽度应为焊缝本身宽度,再加上焊缝两侧各10mm—20mm的热影响区.
7.1.3 斜探头探伤,通常使用一次反射法的半波程和全波程在焊缝的单面双侧进行探侧.当材料厚度大于50 mm,可采用双面双侧进行.
7.2 仪器调整
7.2.1 在CSK-1A或IIW标准试块的R100处,测量探头入射点(探头前沿距离).
探头在R100处前后移动,找出示波屏上最高反射波这一点位置后,固定探头,R100的零点处,即为探头入射点.入射点到探头前沿的距离,即为探头前沿距离.
7.2.2 在CSK-1A或IIW试块上利用Ф50圆弧面和Ф1.5横孔实测探头的折射角.
7.2.3 探头在试块A、B、C三个不同位置上前后移动找出最高反射波后,固定探头测量x
1、x
2、x3距离,利用下面公式,即可计算探头折射角. X1+a-35 A位置时 ß=tg-1------------ 70 X2+a-35
B位置时 ß=tg-1------------ 30 X3-a
C位置时 ß=tg-1------------ 15
注:探头折射角的正切tgß值即为探头K值(水平与深度比值); ß为探头折射角度(实测);
a为探头前沿距离.
7.2.4 探测范围调节
7.2.4.1 最大探测范围应调至萤光屏时基线满刻度的2/3以上.并根据委托通知单的被检材料厚度,选择探头折射角,在CSK-1A,IIw或对比试块上进行时基扫描比例调节(水平、深度、声程).7.2.4.2 用K2探头在CSK-1A试块上以水平1;1或深度1:1调节.
7.2.4.3 探头入射点对准R100、R50圆心,找出产生圆弧面最高反射波(R100或R50).
7.2.4.4 计算圆弧面的水平距离和深度距离
S1=R50×Sin63.4º=44.7mm S1S2代表水平
S2=R100 x Sin63.4º=89.4mm
H1=R50 x Con63.4º=22.35mm H1H2代表深度
H2=R100 x Con63.4º=44.7mm
7,2.4.5 调整水平1:1,表示每格代表水平距离10 mm,则将两圆弧面反射波通过水平微调钮,调节到44.7 mm/10格和89.4 mm/10格,深度与声程调节按此类推.
7.3 绘制距离一波幅曲线
7.3.1 探头入射点、探头折射角、水平或深度、声程按比例调节后,首先选定标准规定的对比试块上扫查相对应的Φ1.2 x 32;Φ2.0 x 60;Φ3.0 x 25;Φ1.0x 6;Φ4 x 4不同试块上的第一点反向反射体(不同孔径、不同深度、不同声程),使之反射波达到
最高,在示波屏上标注第一点,固定探头记下dB值.
7,3.2 根据标准规定相对应的距离一波幅曲线灵敏度,调节衷减器降低dB值,获得第二点,再降低dB值,获得第三点,并用记号笔标注在示波屏上,然后恢复到第一点的dB值。
7.3.3 用探头扫查下一个反射体位置,重复7.3.1和7.3.2的操作步骤,又获得三个点.然后恢复到第一点的dB值.
7.3.4 用探头扫查下一个反射体位置,重复7.3.3的步骤,又获得三个点,然后恢复到第一点的dB值.7.3.5 把上述相对应的点连起来, 即获得三条曲线。(判废线、定量线、测长线).
7.3.6 若需要探测40mm以上不同厚度的反射体,距离一波幅曲线,需将第一点的波高重新选择在80%以上,重复上述步骤即可.
7.3.7 也可利用标准规定的对比试块上不同深度的孔或声程,作出一条基准线.再根据所选用标准规定的距离一波幅曲线的灵敏度的dB差值,记录在示波屏面板上.
7.3.7测长线(评定线)以下一为I区.勿略不计.测长线以上,定量线以下为II区,应记录测长.定量线以上判废线以下为Ⅲ区,应进行定量测长评定.判废线以上为Ⅳ区,为判废区.
7.4 校验
7.4.1 每天探伤工作前,应在对比试块上进行扫描时基线性比例和距离一波幅曲线校验,校验点不少于2点.当发现与原测定曲线有误差时,应重新绘制.
8.0探伤检测要求
8.1 根据驻生产车间检查员提出的超声波探伤申请单,探伤人员应了解被探工件材质、结构,曲率、厚度、焊接方法,坡口形式、焊缝余高及背后衬垫沟槽等情况,做好探伤前技术准备.
8.2 探伤扫查速度不应大于150 mm/s.探头应覆盖整个探伤面并有10%的重叠.
8.3 斜探头扫查形式应前后,左右作锯齿形扫查, 同时应做10º—15º的左右转动。
8.4 为准确定位定量缺陷形状,观察缺陷动态波形, 区别缺陷讯号,需采用前后、左右、转角、环绕等四种探头基本扫查方式.
8.5 T型接头的探伤要求
8.5.1 腹板厚度不同时,选用的折射角见下表
8.5.2 采用折射角45º(K1.0)探头在腹板一侧作直射法和一次反射法可探测焊缝及腹板侧热影响区的裂纹.
8.5.3 探测腹板和翼板间末焊透或翼板侧焊缝下层撕裂状缺陷,可采用直探头位置或斜探头在位置(3)翼板外侧探伤. 8.6 角接接头
角接接头探伤面及折射角一般按下图和上表选择探伤位置
8.7 探测缺陷的判定
8.7.1 对所有缺陷反射波幅超过定量线以上的区域和指示长度均要测长和定量定位.
8.7.2 缺陷指示长度的测定。当缺陷反射波幅只有一个高峰点时,可用降低6dB,相对灵敏度测长。判断其是危害性缺陷时,可用找出缺陷最高波幅峰值点后左右移动探头,直至缺陷波消失的绝对灵敏度法测长.当发现缺陷反射波峰值点起伏变化多个峰值点时,应以缺陷两端反射波最高峰值点之间的探头移动长度来确定。也可用绝对灵敏度法测其指示长度.
8.7.3 当判定缺陷反射波可能是危害性缺陷时,用两种探头角度和频率、改变探侧面、结合焊接工艺综合判定.也可辅助用其它探伤检测方法综合判定结果.
8.8 超声波的验收等级, 按各产品船东与验船师认可的探伤位置布置图,提供的探伤标准II级验收.船用管系, 压力容器参照实行.
8.8.1 探伤检测人员判定为危害性缺陷时,无论其缺陷反射波幅高低和尺寸大小,均评为判废等级予以修理. 8.8.2 判定为超标的缺陷、均应返修.修复后区域及热影响区域,必须按原探伤条件进行重复探伤和评级。
8.8.3 在探伤检测过程中,若发现危害性缺陷时,应延长扩大探测扫查范围,直至缺陷波消失为止.
8.8.4 在探测过程中,应做好现场原始记录,必要时需划出草图,并详细标志部位. 8.9 探伤记录和报告
8.9.1 探伤记录应包括,施工单位.工件名称、工件编号焊缝种类、坡口形式、材质、厚度、表面状况、执行规程、验收标
准、仪器型号、频率、角度、耦合剂、对比试块、探伤灵敏度、超标缺陷和评定记录、探伤人员和日期等.
8.9.2 探伤报告内容应包括工件名称、部件名称、工件编号、焊缝编号、探伤方法、坡口形式、探伤部位、探伤仪器、探测灵敏度、探测范围、探伤标准、缺陷状况.探伤结论、探伤人员及审核人员签字.探伤日期及探伤人员资格等. 8.9.3 探伤记录和报告内容应全面明确,字迹清楚、整洁,并应及时发放探伤报告. 8.9.4 探伤报告、原始记录整理后存档.保存期不少于7年.
超 声 波 检 验 工 作 流 程 图
超 声 波 检 测 报 告
ULTRASONIC INSPECTION REPORT 委托单位: 检测日期: 报告编号: Clinet: Date: Report No: 工程名称
Project Name 部件名称
Part Name 焊缝编号
Weld No.材质规格
Material 坡口型式
Groove Type 仪器型号
Instrument 探头型式
Probe Type 试块
Block 耦合剂
Couplant 检测总长
total length 验收标准
Acc.Standard 合格级别
Acc.Grade 构件/检测部位
Examination location 探伤长度
length(mm) 一次返修位置
Location of the first repair 二次返修位置
Location of the second repair 三次返修位置
Location of the third repair 级别 Grade 结果Result 备注
Remarks 合格
Acc.不合格
Unacc.
Inspection Result (Attached Drawing) 检测结果(附图):
检测员: 监督: 审核: Inspector Supervisor Approved (FORM:R1-WP-Q-04, Rev1.0,1/1)
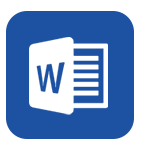