烧结型金刚石砂轮
烧结型金属结合剂砂轮多以青铜等金属作为结合剂,用高温烧结法制造,其结合强度高,成型性好,耐高温,导热性耐磨性好,使用寿命长,可承受较大负荷。因砂轮烧结过程不可避免地存着收缩及变形,所以使用前必须对砂轮进行整形,但砂轮修整比较困难。目前生产常用砂轮对滚整形方法不仅修整时
烧结型金刚石砂轮费时费力,而且修整过程金刚石颗粒脱落较多,修整砂轮本身消耗很大,整形精度较低。
近年来各国学者相继开展了应用特种加工方法修整金属结合剂金刚石砂轮研究工作,主要有电解修整法、电火花修整法复合修整法等。电解修整法速度快,但整形精度不高;电火花修整法整形精度高,既可整形又可修锐,但整形速度较慢;复合修整法有电解电火花复合修整法、机械化学复合修整法等,修整效果较好,但系统较复杂,因此烧结型金刚石砂轮修整问题仍然没有得到很好解决。
此外,由于砂轮制造工艺决定了其表面形貌随机,各磨粒几何形状、分布及切削刃所处高度不一致,因此磨削时只有少数较高切削刃切到工件,限制了磨削质量磨削效率进一步提高。
电镀金刚石砂轮
电镀金刚石砂轮优点:
①电镀工艺简单,投资少,制造方便;
②无需修整,使用方便;
③单层结构决定了它可以达到很高工作速度,目前国外已高达250~300m/s;
④虽然只有单层金刚石,但仍有足够寿命;
⑤对于精度要求较高滚轮砂轮,电镀唯一制造方法。
电镀金刚石砂轮正由于这些优势,电镀砂轮高速、超高速磨削占据着无可争议主导地位。电镀金刚石砂轮存缺陷:镀层金属与基体及磨料结合面上并不存牢固化学冶金结合,磨料实际上只被机械包埋镶嵌镀层金属,因而把持力小,金刚石颗粒负荷较重高效磨削易脱落(或镀层成片剥落)而导致整体失效;为增加把持力就必须增加镀层厚度,其结果磨粒裸露高度容屑空间减小,砂轮容易发生堵塞,散热效果差,工件表面容易发生烧伤。目前国内电镀砂轮制造尚未实现按加工条件要求而优化设计出砂轮最佳地貌,单层电镀金刚石砂轮这些固有弊端必然会大大限制它高效磨削应用。
参考磨商网链接:http://news.momo35.com/ 参考磨商网链接:http://news.momo35.com/
用电化学法制作的金刚石砂轮,包括金刚石修整砂轮,磨削或切削用金刚石砂轮。
已知的砂轮制作过程如下:砂轮工作层含有金刚石磨粒,金刚石磨料被金属结合剂粘结在基体上。首先沉积金属结合剂的厚度为金刚石磨粒高度的20%(上砂),然后继续用金属结合剂把金刚石磨粒粘结(增厚),厚度约为磨粒高度的2/3。这种方法的缺点是磨具工作表面上金刚石浓度太大。
已知的几种调节电镀金刚石砂轮工作表面上金刚石浓度的方法如下:
金刚石磨料预先和填料混合,这些填料可以是盐类、玻璃球或磁铁颗粒。粘结后,20%厚度的填料颗粒被被金属结合剂粘结,这些填料用分别下列方法去除:溶解法、升华法或磁场法。这种方法中填料颗粒尺寸与金刚石磨料颗粒尺寸大致相当,填料用量要能使磨具工作表面上金刚石达到规定的浓度。这几种方法的缺点是填料的去除比较复杂,要求专门的一套方法。
另一种填料的去除比较简单的方法是填料采用球型颗粒,表面光滑,首先沉积金属结合剂的厚度为金刚石磨粒高度的20%(上砂),然后用刷子把填料刷掉,最后继续用金属结合剂沉积至规定厚度。该方法运用了金属结合剂对不同表面粗糙度和形状的颗粒把持能力不同这一效应,其缺点是填料颗粒尺寸与金刚石磨料颗粒尺寸相当,因而粘结后处于同一平面上,用机械法去除填料时,有可能会把部分金刚石磨料一起刷掉,特别是那些形状接近等积状的颗粒、表面光滑的颗粒。
作为上述方法的改进,填料尺寸选择为金刚石磨料颗粒尺寸的1.5-5.0倍:在用金属结合剂进行第一次电沉积时,金刚石磨料被约为其高度20%的金属结合剂层所粘结,而填料颗粒则为厚度被约为其高度4-13%的金属结合剂层所粘结,这种厚度的金属结合剂层不能把持住任何形状、任何粗糙度的填料颗粒,因而用刷子、油石、刀具轻轻碰撞就能把填料从砂轮表面除去。
这种工艺既简化电镀金刚石砂轮的制造方法,又能调节砂轮工作表面上金刚石浓度
参考磨商网链接:http://news.momo35.com/
1 磨削技术发展概述
一般来讲,按砂轮线速度Vs的高低将磨削分为普通磨削(Vs
高速高效磨削、超高速磨削在欧洲、美国和日本等一些工业发达国家发展很快,如德国的Aachen大学、Bremm大学、美国的Connecticut大学等,有的在实验室完成了Vs为250m/s、350m/s、400m/s的实验。据报道,德国Aachen大学正在进行目标为500m/s的磨削实验研究。在实用磨削方面,日本已有Vs=200m/s的磨床在工业中应用。
我国对高速磨削及磨具的研究已有多年的历史,如湖南大学在70年代末期便进行了80m/s、120m/s的磨削工艺实验;前几年,某大学也计划开展250m/s的磨削研究(但至今尚未见到这方面的报道),所以说有些高速磨削技术还只是实验而已,尚未走出实验室,技术还远没有成熟,特别是超高速磨削的研究还开展得很少。在实际应用中,砂轮线速度Vs一般还是45~60m/s。
国内外都采用超精密磨削、精密修整、微细磨料磨具进行亚微米级以下切深磨削的研究,以获得亚微米级的尺寸精度。微细磨料磨削,用于超精密镜面磨削的树脂结合剂砂轮的金刚石磨粒平均直径可小至4µm。日本用激光在研磨过的人造单晶金刚石上切出大量等高性一致的微小切刃,对硬脆材料进行精密磨削加工,效果很好。超硬材料微粉砂轮超精密磨削主要用于磨削难加工材料,精度可达0.025µm。日本开发了电解在线修整(ELID)超精密镜面磨削技术,使得用超细微(或超微粉)超硬磨料制造砂轮成为可能,可实现硬脆材料的高精度、高效率的超精密磨削。作平面研磨运动的双端面精密磨削技术,其加工精度、切除率都比研磨高得多,且可获得很高的平面度。电泳磨削技术也是一种新的超精密及纳米磨削技术。
随着磨削技术的发展,磨床在加工机床中也占有相当大的比例。据1997年欧洲机床展览会(EMO)的调查数据表明,25%的企业认为磨削是他们应用的最主要的加工技术,车削只占23%,钻削占22%,其它占8%;而磨床在企业中占机床的比例高达42%,车床占23%,铣床占22%,钻床占14%。我国从1949~1998年,开发生产的通用磨床有1800多种,专用磨床有几百种,磨床的拥有量占金属切削机床总拥有量的13%左右。可见,磨削技术及磨床在机械制造业中占有极其重要的位置。
为什么磨削技术会不断地发展?主要原因如下:
加工精度高 由于磨削具有其它加工方法无法比拟的特点,如砂轮上参与切削的磨粒多,切削刃多且几何形状不同;仅在较小的局部产生加工应力;磨具对断续切削、工件硬度的变化不很敏感;砂轮可实现在线修锐等,因而可使加工件获得很高的加工精度。
加工效率高 如缓进给深磨,一次磨削深度可达到0~25mm,如将砂轮修整成所需形状,一次便可磨出所需的工件形状。而当Vs进一步提高后,其加工效率则更高。
工程材料不断发展 许多材料(如陶瓷材料、玻璃材料等)在工业中的应用不断扩大,有些材料只能采用磨削加工,需要有新的磨削技术及磨削工艺与之相适应。
新的磨料磨具 如人造金刚石砂轮、CBN砂轮的出现,扩大了磨削加工的应用范围。
相关技术的发展 如砂轮制造技术、控制技术、运动部件的驱动技术、支撑技术等,促进了磨削技术及磨削装备的发展。
总之,磨削技术发展很快,在机械加工中起着非常重要的作用。目前,磨削技术的发展趋势是,发展超硬磨料磨具,研究精密及超精密磨削、高速高效磨削机理并开发其新的磨削工艺技术,研制高精度、高刚性的自动化磨床。
2 磨削的关键技术研究
就磨削而言,特别就高速高效磨削、精密及超精密磨削而言,其涉及的内容广泛,不仅包括磨削本身的技术,也集中了其它相关的技术。关键技术介绍如下:
2.1 磨削机理及磨削工艺的研究
通过对磨削机理和磨削工艺的研究,揭示各种磨削过程、磨削现象的本质,找出其变化规律,例如,磨削力、磨削功率、磨削热及磨削温度的分布、切屑的形成过程、磨削烧伤、磨削表面完整性等的影响因素和条件;不同工件材料(特别是难加工材料和特殊功能材料)和磨削条件的最佳磨削参数;磨具的磨损,新型磨具材料的磨削性能等,只有通过磨削机理和磨削工艺的研究,才能确定最佳的磨削范围,获取最佳的磨削参数。
对普通磨削而言,在磨削机理和磨削工艺方面已开展了广泛而深入的研究。在精密及超精密磨削、高速高效磨削的磨削机理和磨削工艺方面,针对不同的工程材料(如陶瓷和玻璃)国内外开展了一些研究,但还很不全面,尚未形成完整的理论体系,还需进行广泛的研究,找出其内在的规律。可见,需要进一步研究的重点有,①磨削过程、磨削现象(如磨削力、磨削温度、磨削烧伤及裂纹等)的研究;②磨削工艺参数优化的研究;③不同材料(常用材料)的磨削机理的研究;④磨削过程的计算机模拟与仿真的研究。
2.2 高速、高精度主轴单元制造技术
主轴单元包括主轴动力源、主轴、轴承和机架几个部分,它影响着加工系统的精度、稳定性及应用范围,其动力学性能及稳定性对高速高效磨削、精密超精密磨削起着关键的作用。
提高砂轮线速度主要是提高砂轮主轴的转速,特别是在砂轮直径受到限制的场合(如内圆磨削)。因而,适应于高精度、高速及超高速磨床的主轴单元是磨床的关键部件。而对于高速高精度主轴单元系统,应该是刚性好,回转精度高,运转时温升小、稳定性好、可靠,功耗低,寿命长,同时,成本也应适中。要满足这些要求,主轴的制造及动平衡,主轴的支撑(轴承),主轴系统的润滑和冷却,系统的刚性等是很重要的。
国外主轴单元技术的发展很快,有些公司专门提供各种功能的主轴单元部件,这种主轴单元部件可以方便地配置到加工中心、超高速切削机床上。近年来高速和超高速磨床越来越多地用电主轴作为其主轴单元部件,如美国福特公司和英格索尔(Ingersoll)公司推出的加工中心,其主轴单元就是用的电主轴,其功率为65kW,最高转速达15,000r/min,电机的响应时间很短;在EMO\'97上,电主轴是机床制造技术中最热门的功能部件,参展商达36家;美国Landis公司的超高速曲轴、凸轮轴磨床的砂轮主轴,也都用电主轴。
目前,国内主轴单元的速度大约在10,000r/min以下,且其精度、刚性及稳定性有待于考验和提高。同时,缺乏高速、高精度、大功率的主轴单元(电主轴)。需要进一步研究的重点如下:①大功率、高转速和高精度的驱动系统的研究与开发;②高刚性、高精度、高转速重负荷的轴承或支承件的研究与开发;③高速、高刚性、高精度的砂轮主轴和工件头架主轴的制造技术。
2.3 精密、高速进给单元制造技术
进给单元包括伺服驱动部件、滚动单元、位置监测单元等。进给单元是使砂轮保持正常工作的必要条件,也是评价高速、高效及超高速磨床性能的重要指标之一,因此,要求进给单元运转灵活,分辨率高,定位精度高,没有爬行,有较大的移动范围(既要适合空行程时的快进给,又要适应加工时的小进给或者微进给),既要有较大的加速度,又要有足够大的推力,刚性高,动态响应快,定位精度好。
数控机床普遍采用旋转电机(交直流伺服电机)与滚动丝杠组合的轴向进给方案。但随着高速高精度加工的发展,国内外都普遍采用了直线伺服电机直接驱动技术,高动态性能的直线电机结合数字控制技术,可达到较高的调整质量,也可满足上述要求,如德国西门子公司就在CIMT\'97作了直线电机120m/min高速进给的表演,而该公司的直线电机最大进给速度可达200m/min,其最大推力可达6600N,最大位移距离为504mm。又如日本三井精机公司生产的高速工具磨床,主轴上下移动(行程25mm)采用直线电机后,可达400次/min,是原来的2倍,加工效率提高3~4倍。我国国产数控进给系统(特别是高速、高精度进给系统)与国外相比还有很大的差距,其快速进给的速度一般为24m/min。可见,为了适应精密、高速及超高速磨床的发展,在以下几个方面应重点研究:①高速精密交流伺服系统及电机的研究;②直线伺服电机的设计与应用的研究;③高速精密滚珠丝杠副及大导程滚珠丝杠副的研究;④高精度导轨、新型导轨摩擦副的研究;⑤能适应超精密磨削的高灵敏度、超微进给机构和超低摩擦系数的导轨副的研究。
2.4 砂轮制造及其新技术
随着工程材料的发展及其应用,CBN砂轮和人造金刚石砂轮的应用越来越广泛,而砂轮的许用线速度也要求较高,一般在80m/s以上。单层电镀CBN砂轮的线速度可达250m/s,发展超高速磨削也需要150m/s以上的砂轮,但国内80~120m/s的CBN砂轮仍在研制之中。
此外,砂轮的设计,其截面形状的优化、粘结剂的结合强度及其适用性、砂轮基体的材料、砂轮的制造技术(特别是对微细磨料磨具的制造技术)等都是非常重要的,仍需对一些关键技术进行攻关:①砂轮基体材料及制造技术的开发、设计及其优化;②砂轮新型粘结剂(特别是适用于制造微细磨料磨具的粘结剂)的研究;③新型磨料的制备工艺,如可使磨料容易产生新的切削刃;④新型砂轮的制造工艺,既要使砂轮具有足够的容屑空间,也要有更好的凸出性;⑤适合于超精密磨削的超微粉砂轮的制备技术。
2.5 机床支承技术及辅助单元技术
机床支承技术主要是指机床的支承构件的设计及制造技术。辅助单元技术包括快速工件装夹技术,高效冷却润滑液过滤系统、机床安全装置、切屑处理及工件清洁技术、主轴及砂轮的动平衡技术等。
磨床支承构件是砂轮架、头架、尾架、工作台等部件的支撑基础件。要求它有良好的静刚度、动刚度及热刚度。对于一些精密、超高速磨床,国内外都有采用聚合物混凝土(人造花岗岩)来制造床身和立柱的,也有的将立柱和底座采用铸铁整体铸造而成,还有采用钢板焊接件,并将阻尼材料填充其内腔以提高其抗震性,这些都收到了很好的效果。
应在以下几个方面(特别是下一代磨床的设计)加强研究:①新型材料及结构的支承构件的优化设计及制造技术的研究;②砂轮动平衡技术的研究;③磨削液过滤系统的研究;④安全防护装置的设计制造技术的研究;⑤精密自动跟刀架及支承件的研究。
2.6 砂轮在线修整技术
在磨削过程中,砂轮由于磨钝和磨损,需要进行及时修整,特别是对超细磨料砂轮而言,更需频繁修整。普通砂轮修整比较容易;人造金刚石砂轮和CBN砂轮的修整(特别是在线修整)是个难题。
超硬磨料砂轮的修圆及磨料开刃是两个很重要的问题。目前,国内一些学者正在研究激光修整砂轮和电解修整砂轮,以期解决高效实用的修整问题。重要的关键问题有二:①新的、高效实用的砂轮修整技术及其装置;②砂轮在线修整技术。
2.7 环境友好的相关磨削技术
磨削过程中,冷却液的作用主要是冷却和润滑、将磨削热从工件表面带走、冲刷掉磨削时留在工件和砂轮表面上的切屑。但是,鉴于冷却液对环境污染的负面影响,磨削时应尽可能少用冷却液或不用冷却液,因此,应开展对下列关键技术的研究:①对环境不产生污染的冷却剂;②新的冷却方法及冷却装置。
2.8 磨削过程的检测控制技术
磨削过程的检测与控制,主要是通过传感器、分析及信号处理,对磨削过程进行实时监控,例如对砂轮的磨损及破损情况进行监测和控制,对工件的尺寸、形状与位置精度和加工表面质量进行监控。这需要研究新的实用的传感器、检测与监控方法。
有些学者提出,将新型非接触式传感器(声发射传感器)安装在砂轮的基体上,通过信号接收器接收信号并对其进行分析处理,以控制砂轮所受的力,从而监控砂轮的磨损状况。但尚未见到更详细的实验报道。
国内也开发了一些非接触式测量传感器及磨削过程的在线监测、监控技术等,但与国外差距很大。国内应以实用化为目标,进行相关测试技术的研究,研究精度高、可靠性好、实用性强的测试技术与设备。同时,加强对砂轮磨损及破损、砂轮修整状态,工件的加工精度、加工表面质量等在线监控技术进行研究,开展自适应控制及智能控制的研究。
其关键技术有①砂轮的磨损及破损的监控技术;②工件的尺寸精度、形状精度、位置精度和加工表面质量的在线监控技术;③精度高、可靠性好、实用性强的测试技术与仪器。
2.9 磨削过程的仿真与虚拟
随着计算机技术及模拟技术的发展,利用计算机进行磨削基本参数及磨削工艺的仿真是一个重要的研究课题。利用计算机仿真,可以模拟磨削过程,并能分析和预测不同条件下磨削效果和磨床的性能,但仿真必须建立在有充分实验数据的基础之上。目前能使用砂轮地貌模型对砂轮进行仿真,能对磨屑形成过程、能量转换、磨削力变化、磨削区温度、磨削精度和磨削表面质量进行仿真,还开发了分析和仿真磨削过程的软件工具。
虚拟磨床是虚拟制造技术中的一个新的研究领域,可以建立一个逼真的虚拟磨削环境。
总之,我们的研究一方面要跟踪国际科学研究的前沿,更要有创新,要符合自己的国情,所研究的成果要能够应用于生产,以推动我国机械工业的进步。
参考磨商网链接:http://news.momo35.com/
金刚石是目前发现的硬度最高、锋利性较好的磨粒。采用电镀的方法将金刚石磨料\"电镀\"在金属基体上,代替传统的压铸烧结法,不仅投资少、成本低,而且避免了在高温情况下金刚石的氧化,保证了金刚石的硬度和锋利性。
在整个电镀金刚石过程中,90%以上的电镀层结合不良是由于镀前处理不良所致。因此,要提高电镀质量,最主要的是做好镀前处理。
镀前处理的内容大致包括:除油、防锈、浸蚀、酸洗、活化清洗以及加辅助电极和装挂等。
为了提高镀层质量,经过对国内外的电镀行业情况进行分析和比较,结合实际,制定了镀前处理新工艺流程如下:去毛刺清洗涂绝缘胶擦洗化学除油热、冷水冲洗酸洗冷水冲洗电化学除油冲洗阳极处理冲洗入槽。
实验步骤
1.去毛刺用砂纸和手锉将工件上的毛刺除去,防止工件表面呈现介电的不良状态。
2.清洗用酒精将工件擦洗一遍,初步清除工件表面的油污。
3.涂绝缘胶将擦洗后的工件,在非镀部位上涂一层快速粘合剂,使非镀部位绝缘。
4.擦洗为了防止需镀部位被涂上绝缘胶,用手锉或砂纸将该部位再打磨一遍,然后冲洗。
5.化学除油除油剂配方。
氢氧化钠具有很强的皂化作用,与动植物油反应,生成可溶性飞皂和甘油。十二烷基硫酸钠是一种表面活呼剂,在其十二烷基疏水基团和硫酸根亲水基团的协同作应下,降低了液体与工作之间的表面张力。它作为一种碱液添加剂,加快了除油速度。碳酸钠和硅酸钠则是两种缓冲剂对处来酸起缓冲作用,使融液的PH值基本上保持不边。将工件置与于上述溶液中,在40℃~60℃的情况下清洗30分钟左右。
6.热、冷水冲洗先用热水冲洗,在用冷书冲洗,避免除油液进入酸溶液中。
7.酸洗酸洗液配方,其目的是去除基体表面的氧化皮。
8.冷水冲洗酸洗后,将工件夹出,用冷水冲洗,然后装挂到电化学除油槽内。
9.电花学除油电化学除油剂配方
把工作装挂在此溶液内,接同点源,先阴级处理1分钟,然后阳极处理3分种。所采用的电流密度为10A/dm2,电极为不锈钢板。电化学除油的反应如下:
阳级除油:4OH--2e=O2+H2O
阴极除油:2H++2e=H2
采用先阴后厌极的联合除油法,具有去油速度快,无氢脆的优点。
10.冲洗将用电化学除油后的工件用书进性行冲细洗,准备竟行阳行处理。
11.阳极处理
阳极处理液配方见表4所示,将基体装挂好,需镀部位插入该液中。负极用铅板,正极用基体。电流密度为25A/dm2,通电时间为3分钟。阳级处理避免了产生氢脆的现象,尤其适合于入槽前的最后一道工序。
12.冲洗入槽将阳极处理完毕的基体快速进行冲洗后,放入电镀槽中,准备电镀。
至此,完成金刚石电镀的整个镀前处理。
实验结果
实验将试件分成五组,在不同的镀前处理工艺流程下进行镀前处理,然后在同一电镀条件下入槽电镀。各组试件具体处理条件。
试样采用15152mm2的铁片。实验时,温度为40℃1℃,电流密度为40MA/dm2,阳极为纯净的2镍板,阴极为试件。
对电镀完的试件进行结合力和脆性两方面的检验。镀层结合力检验是采用定性的实验检测方法即锉刀试验法。所谓锉刀实验法是指用锉刀由基体向镀层方向成45o锉镀层边缘。如镀层不被带起或脱落,则为合格。
当结合力良好时,再进行镀层的脆性检验。脆性检验采用的是弯曲法。弯曲法将试件夹在虎钳上反复弯曲,同时用放大镜观察弯曲部位的变化至出现第一条裂纹为止。
由表5的测量结果可知,采用新工艺,试件表面光洁性好,油污和氧化皮被除净,试件呈现出良好的受镀状态。镀层金属与基体金属间的结合力良好,镀层的均匀性、完整性都较好。
得出来的结论
1.采用机械去毛刺、锉磨需镀部位的方法,防止工件表面呈现介电的不良状态;
2.将十二烷基硫酸钠作为碱添加剂,加强了基体表面的活性,去油速度快、质量好;
3.采用低温去油,使基体不受热应力影响;
4.在化学除油和酸洗后,又采用电化学除油和阳极处理,大大地改变了基体表面的状态,提高了镀液的分散能力和覆盖能力,提高了镀层的均匀性、完整性,增强了镀层的结合力。
参考磨商网链接:http://news.momo35.com/
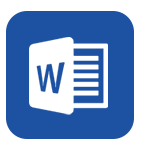