车工技能训练教案 实训课题:零件的工艺分析 实习时数:
4课时
实训目标:
掌握车削零件的工艺分析与制定
实训难点: 零件的工艺制定。 实训重点: 零件的工艺分析。 实训方法: 讲授 和 演示及练习
实训准备: 1.机床为普通车床:型号为CD6140A、CDE6140A、CD6136 2.量具:游标卡尺、钢直尺 3.刀具:正偏刀、切刀、
4.材料准备: Ø35㎜×85㎜ 数量: 一件/人
实训内容与步骤:
1、清点学生参加实训的人数。
2、检查学生着装是否达到安全要求。
3、强调操作安全及操作的注意事项。
4、讲解今天的重点零件的工艺分析。
一、相关知识
在实际的零件加工中,特别是高技能考试操作中的车削加工零件中,零件的表面不会是单一的表面组成。往往会由不同形状,不同 尺寸多个表面。在加工零件除了要进行表面车削外,还要进行其他铣、磨、钳及热处理等工种的加工。因此在车削零件前必须对加工零件进行综合的工艺分析,确保加工零件的加工质量。
加工工艺的制定非常重要,普车加工一般不会用手写下来。往往是操作者根据操作的经验,而边操作边制定加工工艺。
1 加工工艺的好坏,直接关系着生产零件的质量的好坏。当会做事的时候,就看谁的加工工艺制定的合理正确。
1、基准的选择
加工基准是保证加工正确的首要条件,也是各加工表面形状等关系的依据,是各表面的加工和测量依据。一般情况下操作者应选择,设计基准与加工基准、安装基准、测量基准相同。这样可以消除加工的积累误差。保证加工质量。 如图:
各表面的设计基准为Ø95h6的两外圆表面所决定的轴线,是各径向尺寸的基准,轴向基准为端面B。
2、工艺基准的选择
在制定工艺加工过程中选择的基准面,称为工艺基准。根据用途不同,工艺基准可分为定位基准、测量基准、和装配基准。 (1) 定位基准
在加工中,用于工件定位的基准称为定位基准。轴类工件
2 的定位基准为两端面的中心孔。根据要求轴类零件的表面要求不高的可以选择一个外表面作为定位基准。但毛坯面只能作为一次装夹的定位。
(2)测量基准 测量时所采用的基准称为测量基准。一般有内孔的工件时,应选择内孔为测量基准。因为内孔的加工比外圆要难,所以要加工好内孔尺寸后,才把外圆尺寸加工好。
(3)装配基准 装配时用来确定零件或部件相对位置所采用的基准称为装配基准。
二、定位基准的选择
零件的加工过程中,合理选择定位基准对保证工件的尺寸精度,尤其是位置精度起着决定性的作用。
1、定位基准分为 粗基准和精基准两种。
用毛坯表面作为定位基准的称为粗基准;用已加工过的表面作为定位基准称为精基准。
2、粗基准的选择时,应着重考虑以下三方面;
(1) 选择不加工表面作为粗基准,这样可以使加工表面与不加工表面之间的位置误差最小。
(2) 在有较多加工表面时,应选择毛坯余量最少的为粗基准。这样容易使工件全部加工起来。
(3) 选择粗基准的表面应尽可能平整,并有足够大的面积,还要除去飞边、毛刺,使之定位准确、夹紧可靠,避免打刀。 (4) 粗基准的表面应避免重复使用。粗基准只允许使用一次,否则
3 将无法保证加工表面间的位置精度。
(5) 粗基准表面一般是夹紧受力的面,它应有足够的刚性,不易变形。
3、精基准的选择
应保证工件的加工精度,同时使工件装夹方便、正确、可靠。(1)一般尽可能的选择设计基准为精基准。 (2) 尽可能使精定位基准与测量基准重合。 (3) 尽可能使装配基准与精基准重合。
(4) 尽可能使基准统一,除第一道工序外,其余的尽量采用同一精基准来加工大多数表面。这一原则对于多道工序、多个工种加工的工件或位置精度要求较高的表面尤其重要。它可减少定位误差,提高加工精度,且全球装夹。
三、加工表面的选择
选择零件各表面加工方法,是拟定零件加工工艺路线的主要任务之一。对待零件的各加工表面,有不同的加工方法,而同一表面有几种加工方法,而不同的加工方法,又具有不同的技术经济效果。选择加工方法,一般是根据经验或查表来确定。一般要考虑几个因素:
1、加工经济指数。
2、工件的结构形状和尺寸大小。
3、工件材料性能和热处理的影响。
4、生产效率。
5、现有的生产条件。
6、个人的操作水平。
四、划分加工阶段
1、一般根据工件的结构形状与精度要求,分为粗、精加工。 (1)粗加工阶段 (2)半精加工阶段 (3)精加工阶段
(4)光整加工或超精加工阶段
2、确定加工顺序 (1)工序 (2)安装 (3)工位 (4)工步
实训要求:
1、合理的选择加工基准,注重定位基准的选择。。
2、合理的制定零件的加工工艺路线。
3、充分的利用现有的条件,制定加工工艺。
实训效果:
能合理制定较复杂工件的加工工艺路线。
教学反思:
学生通过训练对加工基准概念初步认识,但在加工过程中,基准的选择应用及基准的过渡,还应加强练习。
5 实训课题:典型轴类工件的工艺分析 实习时数:
4课时
实训目标:
掌握典型轴类零件的工艺分析与制定
实训难点: 典型零件的加工。
实训重点: 零件的工艺分析与工件的尺寸精度。 实训方法: 讲授 和 演示及练习
实训准备: 1.机床为普通车床:型号为CD6140A、CDE6140A、CD6136 2.量具:游标卡尺、钢直尺、千分尺 3.刀具:正偏刀、切刀、
4.材料准备: Ø50㎜×10㎜ 数量: 一件/人
实训内容与步骤:
1、清点学生参加实训的人数。
2、检查学生着装是否达到安全要求。
3、强调操作安全及操作的注意事项。
一、技能训练任务 1.技能训练用图
Tr32×12(P6)30 °1.5±0.01233151038106
6 2.图样工艺分析
(1)工件材料为Ø50×120㎜的45#钢棒料.(2)工件形状为双头的梯形螺纹、带有偏心和圆锥体工件。 (3)工件的外圆精度要求较高,应选择两顶的方法进行精加工。 (4)工件应分为粗、精加工两个阶段进行加工。
(5)螺纹的粗加工,应保留牙顶宽度在2.5~2.6㎜左右。 (6)工件两端面应打A3的中心孔,尽量的保证两中心孔的同轴度。 (7)精车外圆时,应采用试车的方法。保证工件的尺寸精度。 (8)加工完工件尺寸后,应全面检查所有的尺寸,并去毛刺。
实训要求:
1、注重定位基准的选择,两中心孔的加工质量。
2、确保外圆尺寸精度的控制。
3、粗车的留有精车余量,不宜过多。
实训效果:
提高学生的综合加工能力,重点是工件的工艺分析与加工尺寸控制。 教学反思:
通过加工有了,综合加工的基本认识。对综合技能有一定的
的提高。
7 实训课题:零件的尺寸精度与形位精度的控制 实习时数:
4课时
实训目标:
掌握零件的尺寸与形位精度的加工方法
实训难点: 零件的尺寸精度加工。 实训重点: 零件的加工练习。 实训方法: 演示及练习
实训准备: 1.机床为普通车床:型号为CD6140A、CDE6140A、CD6136 2.量具:游标卡尺、钢直尺、千分尺 3.刀具:正偏刀、切刀、
4.材料准备: Ø50㎜×120㎜ 数量: 一件/人
实训内容与步骤:
1、清点学生参加实训的人数。
2、检查学生着装是否达到安全要求。
3、强调操作安全及操作的注意事项。
一、相关知识
影响工件加工质量因素很多,如工件的装夹方法、车刀的几何参数、切削用量的选择、操作者选用的加工工艺、机床的精度等都会对加工精度产生影响。一般加工精度分为尺寸精度与形位精度。尺寸精度要求较高的零件,它的外表面的粗糙度值应要求较小。尺寸精度与形位精度有一定的关系,但不是绝对的。形位精度要求较高的,不一定尺寸精度要求较高。一般只有尺寸精度的要求,还好对应。一但有形位要求时,加工工艺的选择就应采取相应的措施。对于轴类零件来说,主要是采用两顶的方法。
二、尺寸精度的控制方法
8 1.正确的分析零件的加工工艺,选择正确的加工路线。 2.正确的选用加工基准。轴类零件的加工基准为轴心线上。 3.加工零件时,分粗加工与精加工两个阶段,粗车时,留有一定的精车余量。
4.精车时,必须选用试车的方法进行,如:精车余量为0.5㎜时。进刀量,不要一次将余量车去,可第一次车去0.35~0.4㎜,车去一小段后,停下测量再将多余的余量车去。这样能更好的保证尺寸的准确性。
三、形位精度的控制方法 1.加工路线正确的选择。 2.选择正确的装夹方法。
3.精加工与粗加工余量留有适当。不能太少。
4.轴类零件一般选择两顶的方法进行精加工的装夹方法。
一、技能训练任务 1.技能训练用图
Tr32×12(P6)30 °33151.5±0.0121038106
9
实训要求:
1、选用正确的装夹方法。
2、选用合理的加工工艺。
3、将精车与粗车分开,注意加工余量控制。
实训效果:
学会了怎样控制尺寸精度,选用合理的装夹方法。
教学反思:
通过加工练习能正确的掌握精加工与粗加工的方法。基本上能正确的选用合理的装夹方法,确保零件的形位加工精度。
实训课题:典型零件的加工练习实习时数:
4课时
实训目标:
掌握典型零件的车削方法
实训难点: 零件的尺寸精度控制。 实训重点: 零件的加工练习。 实训方法: 演示及练习
10 实训准备: 1.机床为普通车床:型号为CD6140A、CDE6140A、CD6136 2.量具:游标卡尺、钢直尺、千分尺 3.刀具:正偏刀、切刀、
4.材料准备: Ø35㎜×85㎜ 数量: 一件/人
实训内容与步骤:
1、清点学生参加实训的人数。
2、检查学生着装是否达到安全要求。
3、强调操作安全及操作的注意事项。
一、技能训练任务 1.技能训练用图
全部×′
2.工艺分析
(1)备料为Ø30×95㎜
(2)工件为典型的圆锥轴类工件。
(3)外圆尺寸精度的要求较高,形位精度没有要求。 (4)外圆锥角度比较大。
11 (5)加工装夹方法可以选择调头的方式进行加工。
(6)加工时,应先加工工件的右端的台阶各部尺寸精度。然后调头定长,再加工外圆锥左端台阶。
实训要求:
1、保证外圆尺寸精度公差。
2、调头时应先定整长。再加工其他尺寸。
3、加工尺寸控制是整个零件的关键。
实训效果:
掌握了加工方法。尺寸精度的控制,不稳定,时好时坏。
教学反思:
加强练习轴类零件的加工,主要加强外圆尺寸精度的控制。
实训课题:螺纹的加工练习实习时数:
4课时
实训目标:
掌握车削螺纹方法
实训难点: 螺纹零件的加工。 实训重点: 螺纹车削练习。 实训方法: 讲授 和 演示及练习
12 实训准备: 1.机床为普通车床:型号为CD6140A、CDE6140A、CD6136 2.量具:游标卡尺、钢直尺 3.刀具:正偏刀、切刀、螺纹刀
4.材料准备: Ø30㎜×95㎜ 数量: 一件/人
实训内容与步骤:
1、清点学生参加实训的人数。
2、检查学生着装是否达到安全要求。
3、强调操作安全及操作的注意事项。
一、相关知识
螺纹加工是个。要求有比较熟练操作动作,同时要求掌握螺纹各部尺寸的计算知识。是综合性较强的加工方法。 1.螺纹的车削原理与车削方法
车削原理 车螺纹时,当工件每转一周,车刀纵向位移量必须等于 所车螺纹的一个螺距(或导程)。 2.车削方法
⑴ 直进法 它适用于低速车削螺距小于2㎜及脆性材料的螺纹,也适应于高速车削螺距大于2㎜的螺纹。
⑵ 左右切削法 适用于低速车削螺距大于2㎜的塑性材料的螺纹。 ⑶ 斜进法,适用于低速车削大螺距的螺纹。
二、螺纹车刀
要车好螺纹,必须正确刃磨和安装螺纹车刀。按照工件的性质,螺纹车刀是成形刀具,因此对它有以下几点要求:
1、对螺纹车刀几何形状的要求
① 车刀的刀尖角应该等于牙形角。如车削普通螺纹〔 三角形)时,车刀刀尖角应等于60°,见图2-3-50所示;车英制三角形螺纹时,刀尖角应等于55°,车公制梯形螺纹,刀尖用应等于30°。
13 ②车刀的径向前角γ应该等于零度。
③ 车刀后角因为螺旋升角的影响应该磨得不同。
车削螺纹时,车刀与工件的相对位置因受螺旋运动的影响,使车刀的工作前角和后角发生了变化,这对车削单头三角形螺纹影响不大,但在车削方牙、梯形、多头螺纹时影响就较大,见图23-51别所示。在切削右螺纹时:
α1=(3°~5°)+τ (2-3-11)
α2=(3°~5°)-τ (2-3-12) 式中 α1----车刀左侧的静止后角(刃磨后角)
α2----车刀右侧的静止后角(刃磨后角)
τ― 螺旋升角
(3°~5°)-----工作后角
由于螺旋运动的影响,切削时车刀的前角也发生了变化。见图2-3-52① 所示。如果静止时车刀前角γ=0°,切削右螺纹时,左刀刃上的工作前角为0°+τ;右刀刃上的工作前角为0°-τ。这时右刀刃上的工作前角为负值,切削很不顺利,排屑困难。为了改善切削条件,可将车刀法向(垂直于螺旋线)安装,这时两侧刀刃工作前角都为0°,见图2-3-52 ② 所示;:或在车刀两刀刃磨有较大的前角,见图2-3-52 ③ 所示;或法向装刀并磨有前角,见图2-3-52④所示。 ④除车削滚珠形螺纹外,车刀的左右刀刃必须是直线。
在实际工作中,当用高速钢车刀低速车螺纹时,如果采用径向前角γ等于零度的车刀见图,切屑排出困难,就很难把螺纹车光。这时可采用有5°~15°径向前角的螺纹车刀见图,便可比较顺利地进行切削,并可以减少积屑瘤现象,能车出表面粗糙度较低的螺纹。但是当车刀有了前角以后,牙形角就会产生变化,见图所示。同时刀刃不通过工件轴心线,因此被切削的螺纹牙形(轴向剖面)不是
直线而是曲线。这种误差对一般要求不高螺纹来说,可以忽略不计。但对牙形角的影响不可忽略,特别是具有较大径向前角的螺纹车刀,其刀尖角必须进行修正,或者粗车螺纹时采用有径向前角的车刀,而精车时采用径向前角为零度的车刀。从图中可看出,具有前角γ的车刀,其刀尖角必须小于前角等于零度时的刀尖角ε,才能车出牙形为α的角度。
三、技能训练任务
1、技能训练用图
M30×2
实训要求:
1、正确的刃磨普通螺纹车刀,并保证牙形角的正确。
2、按图样要求,正确的调整机床手柄,并检验手柄位置是否正确。
3、合理的选择切削用量。按图样要求加工M30×2的普通螺纹。
4、保证外圆尺寸精度的加工。
实训效果:
能按要求调整机床手柄。基本能刃磨螺纹刀具。大部分学生掌握了普通螺纹的加工方法。 教学反思:
螺纹刀具的刃磨有待加强,螺纹尺寸的控制,应加强练习掌握。
15 实训课题:梯形螺纹的练习实习时数:
4课时
实训目标:
掌握车削梯形螺纹零件的方法。
实训难点: 梯形螺纹刀具的刃磨。 实训重点: 梯形螺纹工件的加工练习。 实训方法: 讲授 和 演示及练习
实训准备: 1.机床为普通车床:型号为CD6140A、CDE6140A、CD6136 2.量具:游标卡尺、钢直尺,千分尺 3.刀具:正偏刀、切刀、梯形螺纹刀
4.材料准备: Ø50㎜×120㎜ 数量: 一件/人
实训内容与步骤:
1、清点学生参加实训的人数。
2、检查学生着装是否达到安全要求。
3、强调操作安全及操作的注意事项。
一、相关知识
在圆柱或圆锥母体表面上制出的螺旋线形的、具有特定截面的连续凸起部分。螺纹按其母体形状分为圆柱螺纹和圆锥螺纹;按其在母体所处位置分为外螺纹、内螺纹,按其截面形状(牙型)分为三角形螺纹、矩形螺纹、梯形螺纹、锯齿形螺纹及其他特殊形状螺纹,三角形螺纹主要用于联接,矩形、梯形和锯齿形螺纹主要用于传动;按螺旋线方向分为左旋螺纹和右旋螺纹,一般用右旋螺纹;按螺旋线的数量分为单线螺纹、双线螺纹及多线螺纹;联接用的多为单线,传动用的采用双线或多线;按牙的大小分为粗牙螺纹和细牙螺纹等,按使用
16 场合和功能不同,可分为紧固螺纹、管螺纹、传动螺纹、专用螺纹等。
车螺纹时,为了保证齿形正确,车刀的安装一定要正确。若装刀有偏差,即使车刀的刀尖角刃磨的十分准确,加工后的螺纹牙形仍全产生误差。对于三角形螺纹、梯形螺纹,它的齿形要求对称和垂直于工作轴线,即两半角相等。装刀时可用样板来对刀,如果把车刀装歪,就会产生齿形歪斜。此外,袋刀时刀尖必须对准工件中心。否则会引起车刀前角的变化。在精车或半精车螺纹时,由于切削力通过车刀作用在拖板上使其配合间隙压缩,另方面由于车刀的反作用力而使工件及主抽位置稍有抬高,遇此情况时,为抵消这种偏差,安装车刀应使刀尖位置比工件中心高出1 / 100 D (D:被加工工件的直径),从而使车削时刀尖的实际位置对准工作中心。
二、车螺纹的调整
为了在车床上车出螺距合乎要求的螺纹,车削时必须保证工件(主轴)转一转,车刀纵向移力的距离等于工件一个螺距值。这就是说,若所车螺纹的螺距和车床丝杠的螺距已经确定,即车床主轴和丝杠必须保证一定的转速比。在现在生产的普通车床中,这个速比关系在设计进给箱和挂轮架时大都考虑进去了,只要查一下标牌就可以知道,按标牌上的要求变换机床手柄位置,并通过试车检查螺纹的刻线是否与要求的相同。
三、技能训练任务
1、技能训练用图
17
×5放大放大
实训要求:
1、按图加工梯形螺纹工件。
2、正确的刃磨和安装梯形螺纹车刀。
3、梯形螺纹部分可分粗车和精车两步进行。
实训效果:
基本能车削梯形螺纹工件。
教学反思:
梯形螺纹的尺寸控制方法,应继续加强练习。
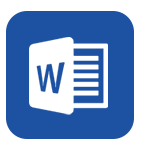