推荐第1篇:SQE、供应商质量工程师岗位职责
1.负责项目的前后期供应商质量评估与管理工作。2.负责对IQC以及相关人员的培训。3.负责对供应商的资质进行全面的审核。4.负责与供应商就质量方面问题进行沟通。5.负责对供应商方面的不良品进行分析和处理。6.负责制定出具一定的质量标准作为来料检验员的检验标准。7.定期对公司来料供应商进行审核、评估和技术上的帮助。8.负责供应商纠正和预防措施的追踪,避免问题的重复发生。9.不断改进和提高来料检验的程序和体系以及检验员的检验质量。
推荐第2篇:SQE年度计划
某电源公司质量部2008年度SQE工作总结目录:
一、关键指标完成情况
二、2008年工作中的三个亮点
三、与供应商签订质量保证协议
四、跟进产品部发行无物料规格书的材料
五、协助供应商分析材料不良并进行改善
六、2008年工作中的三个重点
七、供应商品质状态
八、供应商导入及辅导
九、原材料在线异常处理
十、2008年本小组工作的总体评价和反思 十
一、2009年工作思路和方向
十二、2009年需要其它部门提供的资源和支持
某电源公司质量部2008年度SQE工作总结内容摘要: 工作思路和方向: 人员检验能力:
提升检验人员问题检验的能力和方法(主要注重之前发生异常及新材料的检验)之材料的检验,包含抽样的方式 检验方法:
对于异常经常发生之供应商重点检查
对于品质一直很稳定之供应商,可以采取减量之检验(重点材料除外) 供应商问题解决追溯方法:
对于品质一直波动之供应商经常到供应商处进行确认,对于发现的问题及时要求其改正;
对于品质多次改善无效之供应商坚决要取消其供应商资格,开发品质优良之进行替代;
对于异常造成损失的,依照质量协议进行处理,以经济手段提升其质量意识。
推荐第3篇:SQE个人简历
个 人 简 历
姓名:** 性别: 出生年月: 身高: 民族: 学历: 大专
专业 :企业管理 血型: 联系方式:
户口所在地:**** 现居住地:
教育背景:
1999.9-2002.7 江苏、盐城、广播电视中等专业学院 2006.4-2009.12 江苏南京农业大学
工作经历:
2003.3-2006.4 在**公司担任qe主要负责廠內外品質異常處理工作和體系工作. 2006.5-2007.11 在**公司担任iso体系工程师负责推行ts16949/iso14001工作和体系维护工作。负责公司内部审核、年审、客户稽核。 2008.1-至今 在**公司担任sqe&iso專員工作
主要负责:1.冲压件风扇电子件,包材类,供货商来料异常处理,制程材料异常处理和判定,iue的改善确认,制定进料检验标准书和新产品变更文件修改. 2.推动供货商内部质量改善,导入常用质量工具. 3.新厂商稽核(采购/rd/品保)择优选择厂商,合格厂商年度qsa/qpa/hsf稽核及辅导, 供应商的异常不定期稽核及辅导,追踪厂商改善效果确认. 4.执行供应商的奖罚措施. 5.材料质量目标达成状况的改善及检讨. 6.供应商质量月报,fai 报表,信赖性报表的跟催及确认,hsf产品及制程管制等.技能 7.qc080000/iso9001:2008/iso14001/ohsas18000的体系推行和文件的编制维护,主导客户稽核、内部稽核、管理评审、年度监审等工作內容. 特长: 1.熟练应用office、sap系统、photoshp、photoshpcs、3d max、auto cad 2.熟练qc七大手法、iso八大原则、ts16949五大工具 3.熟悉iso流程对iso文件编写有一定的能力在公司主要负责iso审备、客户端稽核、供应商稽核、年审、组织公司内部稽核对品质体系执行情况之定期与不定期稽查对品质体系之不适用之处进行评审与提供改善方案. 教育及培训: 2005年-2013年获得iso9001,iso14001,ohsas18001,qc080000,is16949,eicc内审员证书及内部仪器校验证书。
2013.4 公司总部请外训培训6 sigma绿带并完成结业 2013.12 培训iso9001国家注册外审核员。
自我评价:
本人为人正直,好强,能吃苦耐劳,有上进心、责任心、自信心、工作积极,具有团队合作精神,具有一定的组织能力,能互相协调,语言沟通力强,有较强的逻辑思维能力和接受能力。篇2:sqe主管的个人简历模板 sqe主管的个人简历模板
姓 名: 徐先生 性 别: 男
婚姻状况: 未婚 民 族: 汉族
户 籍: 广东 年 龄: 32 现所在地: 广东-东莞 身 高: 167cm 希望地区: 广东
希望岗位: 质量/安全管理类-质量管理/测试经理/主管(qa/qc经理) 质量/安全管理类-供应商管理
质量/安全管理类-sqe/供应商质量工程师
教育经历 2002-09 ~ 2005-07 广东交通职业技术学院 机械电子工程/机电一体化 大专 培训经历
2009-02 ~ 2009-02 sony iso spc 以及品质相关 2008-04 ~ 2008-04 sony gp培训 2003-03 ~ 2003-06 广东交通职业技术学院 cad 中级证书 **公司 (2009-10 ~ 至今)
公司性质: 外资企业 行业类别: 电子、微电子技术、集成电路
担任职位: sqe主管 岗位类别: 质量管理/测试经理/主管(qa/qc经理) 工作描述: 1.配合采购开发新供应商,并对新厂商进行品质系统调查,评估. 2.对合格供应商进行稽核与辅导计划,并实施,跟进完成改善. 3.进料品质管理,厂商重大品质异常改善对策的检讨及跟进. 4.跟进处理因原材料引起客诉和产线投诉. 5.对检查员作出培训提高其检查技巧. 6.品质月报周报的作成. 7.对检查员的日常工作作出管理,确保检查工作能准时完成,确保所有的来料品质得到控制. 8.上司交代的临时任务. **公司 (2007-05 ~ 2009-09)
公司性质: 外资企业 行业类别: 电子、微电子技术、集成电路
担任职位: iqc工程师 岗位类别: 供应商管理
工作描述: a:持续跟进供应商的纠正措施并确认其效果. b:新供应商稽核和评估. c:帮助供应商提高其制程及质量体系能力. d:工程变更确认(工厂,原材料,生产工具和制程) e:给予生产工厂支持以防止来料不良. f:通过相应的行动去提高供应商的能力. g:新机种的导入,有关来料不良解析. h:特采处理.简历
i:sip等品质文书的作成. j:相关品质会议的召开. **公司 (2004-12 ~ 2007-04)
公司性质: 外资企业 行业类别: 家具、家电、工艺品、玩具
担任职位: sqe工程师 岗位类别: sqe/供应商质量工程师
工作描述: a:持续跟进供应商的纠正措施并确认其效果. b:新供应商稽核和评估. c:帮助供应商提高其制程及质量体系能力. d:sip作成. e:给予生产工厂支持以防止来料不良. f:通过相应的行动去提高供应商的能力. 技能专长
专业职称:
计算机水平: 初级
计算机详细技能: 熟练操作cad, pro-2001以及办公室软件. 技能专长: 1.熟悉iqc以及供应商管理. 2.能熟练运用相关的品质工具(spc, pdca, 8d等) 3.品质不良分析. 4.熟悉塑胶,pcb, 五金,包材等物料. 5.熟悉iso9000体系以及sony gp体系. 6.制作sip. 7.供应商审查. 8.新供应商审查. 9.4m变更及特采处理. 语言能力
普通话: 粤语:
英语水平:
英语: 良好
求职意向
发展方向: 希望凭借我多年在iqc和供应链的工作经验以及对品质体系的熟悉能给贵司的发展贡献我的力量,在帮贵司发展的同时我自己也在工作中有进一步的突破与发展。 其他要求:
自身情况
自我评价: 1.良好的英语能力. 2.熟悉不同的生产制程. 3.熟悉质量工具和质量体系(spc,8d,fmea,iso9000& sony-gp) 4.基本了解不同的生产工艺(塑料,五金,pcb以及光学材料) 5.良好的沟通能力和技巧.篇3:sqe个人简历模板 sqe个人简历模板
[日期:2011-04-22] 来源: 作者: [字体:大 中 小] 姓名:个人简历网
目前所在: 天河区
户口所在: 海南
婚姻状况: 未婚
培训认证: 未参加
诚信徽章: 未申请
人才测评: 未测评
我的特长:
求职意向
人才类型: 普通求职
质量检验员/测试员:检验员,技工:售后服务,金属制应聘职位: 品:质量管理
工作年限:3 职 称: 无职称
求职类型: 全职 可到职日期: 随时
月薪要求: 面议 希望工作地区:广 州,深圳, 工作经历
洛阳中信重型机械 起止年月:2010-08 ~ 2009-07 公司性质: 国有企业 所属行业:机械/机电/设备/重工
担任职位: sqe 工作描述: 主要工作内容:
负责供应商的品质管理,出现的质量问题进行分析,找原因,要求供应商改善,并确认改善对策实施的有效性,对供应商的年度审核以及对供应商的辅导及品质改善提升,在公司内部主要起到质检员的作用检验相关产品质量参数,熟练使用相关检验工具。
工作成果:
在sqe岗位上的不断学习进一步提升了自身的沟通能力与检验水平,不管面对客户还是公司内部都有良好的沟通技巧,能独立完成项目的要求跟追踪,形成了对里(质量控制)对外(客户服务)的一体化窗口
离职原因: 家事
深圳瑞泓金属表面处理厂 起止年月:2009-08 ~ 2010-06 公司性质: 民营企业 所属行业:石油/化工/矿产/地质
担任职位: 品质部主管
工作描述: 主要工作内容:
确认及更改公司之品质体系有效文件,维护公司品质体系有效运行,定期制定内部评审及管理审查计划,协调及督导各部门对品质体系中出现不符合项目的改善和追踪是否有效,并记录存档,,督导内部文件之文件分发、回收、保存、更改作年 国 民 身 体 龄:2 4 籍:中 国 族:汉 族 高:1 75 cm 重:6 5 kg 业,协助品质经理相关的品质管理工作,着重负责来料跟成品检验以及监督协助qc,qa的工作,熟练使用常用检验工具如:游标卡尺、角度尺、千分尺、百分表、高度尺,色差仪,膜厚仪等检验仪器
工作成果:
经过一年的品质实线工作以及团队合作结果,使公司成为深圳迈瑞公司的优秀供应商,懂得检验工作的基本流程跟管理
离职原因: 期待更高的挑战
志愿者经历
教育背景
毕业院校: 洛阳理工学院
最高学历: 大专 获得学位: 专 业 一: 机械设计制造及自动化
起始年月 2010-03 语言能力
外语: 英语 良好 其它外语能力:
国语水平: 精通
工作能力及其他专长
善于组织管理,调解员工的工作效率,有良好的沟通能力,熟练运用检验工具,熟悉相关检验流程工作,看懂机械,工程等相关图纸,熟练办公软件office word excel等 自我评价 粤语水平: 一般 终止年月 2010-04 毕业日期: 2008-07 专 业 二: 金属制品表面处理工艺 证书编学校(机构) 所学专业 获得证书 号 深圳迈瑞公司机加中qc七大手法 质量检验合格品管- 心 规 员
作为一个年经人我跟别人一样永不止步的追求,有着吃苦耐劳的精神,社会在进步,科技在攀升,人类的竞争也在日渐激烈,只有脚踏实地,充分发挥自己的才能,赢得认可!篇4:sqe的个人简历模板 sqe的个人简历模板
姓 名: 莫先生 性 别: 男
婚姻状况: 已婚 民 族: 汉族
户 籍: 广东-深圳 年 龄: 32 现所在地: 广东-深圳 身 高: 170cm 希望地区: 广东-中山
希望岗位: 质量/安全管理类-质量管理/测试经理/主管(qa/qc经理) 质量/安全管理类-质量管理/测试工程师(qa/qc工程师) 质量/安全管理类-sqe/供应商质量工程师
寻求职位:
待遇要求: 15000元/月 可面议
最快到岗: 01个月之内
教育经历
1998-08 ~ 2002-07 西安电子科技大学 微电子技术 本科 1995-09 ~ 1998-07 广东省英德市英德中学 理科 高中
培训经历
2009-12 ~ 2009-12 誉杰咨询 iso9001 内审员 iso9001 内审员 2008-02 ~ 2008-07 扬智嘉信咨询 6-sigma 黑带 6-sigma 黑带
工作经验至今10年2月工作经验,曾在4家公司工作 **公司 (2011-01 ~ 至今)
公司性质: 跨国公司(集团) 行业类别: 通讯、电信、网络设备
担任职位: sqe 岗位类别: sqe/供应商质量工程师
工作描述: 负责供应商审核/管理及跟进新产品开发。 1.负责对高端激光黑白打印机的新产品开发及量产跟进。 2.制定并维护工厂验货流程及检验方式。 3.对组装厂进行定期的审查以确保工厂的运行能满足利盟的要求。 4.跟进并协调主要的零部件供应商解决日常出现的主要品质问题以保证生产和出货顺畅。 2011-01~2012-08 跟进单/多功能激光黑白打印机的新产品开发及量产,项目分别在2012年6月及8月进入量产。 个人简历表格下载 2011-12~至今 跟进特种单功能激光黑白打印机的新产品开发。
在每一个新产品的开发阶段,负责制定品质计划及测试计划,并跟进试产中发现的问题点,推动本公司开发部解决设计问题,提出组装方面的改善建议。制定了代工厂的验货流程及检验方式,协调工厂制定内部的抽样流程。
离职原因: 公司经济不景气 **公司 (2009-07 ~ 2010-12)
公司性质: 跨国公司(集团) 行业类别: 其他
担任职位: 高级质量工程师 岗位类别: sqe/供应商质量工程师
工作描述: 负责供应商的质量管理和新产品的日常质量管理。 1.组织新供应商审核工作,与相关人员共同选择、评估新供应商。 2.分析供应商不合格品产生的原因,跟踪验证供应商整改行动。 3.统计&监控供应商的质量绩效,推动供应商持续改善。 4.组织供应商的年度审核工作,跟踪、验证供应商的整改行动。 5.管理dtp实验室(原材料检验及贴合产品测试) 6.负责dtp新产品跟进及日常的质量工作。
主要工作成绩: 1.成功辅导本地供应商达到总部的技术要求并通过宝洁qake审查,完成原材料的本地化。 2.成功把qc的工作重点从成品测试转到制程监控。 3.成功把墨西哥进口cpp薄膜的合格率从原有的70%提高到90%。
离职原因: 个人发展及家庭原因 **公司 (2004-10 ~ 2009-04)
公司性质: 股份制企业 行业类别: 电子、微电子技术、集成电路
担任职位: 岗位类别: 质量管理/测试经理/主管(qa/qc经理) 工作描述:
一、2007-06~2009-04 作为qc部主管工程师(兼esd管理)。 负责smt、cob、focus及成品组装车间的ipqc/oqc管理: 1.制定ipqc oqc kpi和年度预算并每月回顾对应的情况及进行相应的改善。 2.总结每月的品质状况及kpi的差距,召开品质月会,推动生产、工程进行相应的改善。 3.招聘检验人员、工程师等相关人员并指导其进行检验和品质跟进,工作绩效监督及考核。
4.制定或者修订相应的流程文件,规范相关的生产、品质工作。 5.制定并推行qc内部的培训考核及内审机制,提高效率及避免漏失。 6.组织内部的持续品质改善活动 7.跟进新产品的试产和量产全过程的品质活动,跟进重大、重要产品的突发品质事件。 8.处理客户投诉及回复相应的8d改善对策。 9.应对客户的pvi/oba/fai检验和相关的审核。 10.协调出货检验出现的问题,灵活处理保证出货的品质和顺畅。
作为qc部主管工程师,管理一个93人的ipqc/oqc团队,包含9名工程师。 1.在2008年降低smt不良率,从原有的~4000ppm降低到目前低于2500ppm的水平。 2.飞赴北京索尼爱立信,与客户进行了良好的沟通,确保出货的顺畅。 3.改善了ti的品质,从2005年开始保持出货品质dppm最低(ti反馈的数据,与另两家供应商相比),并最终在2008年拿回失去十年之久的“ti优秀供应商”称号。
二、2005-03~2007-06 作为qc部工程师(兼esd工程师)。
负责成品组装车间的ipqc、oqc项目的跟进和管理: 1.跟进新产品试产和量产,提供新产品试产报告,反馈并敦促rnd进行改善。
期间成功跟进gnn / 森海塞尔 (蓝牙耳机)和leapfrog(电机玩具)新客户的新产品试产到量产的导入,同期也成功跟进sony (ps2/ps3游戏机配件)和索尼爱立信(手机配件和蓝牙耳机)新产品试产到量产的导入。 2.编制oqc检验指导书,与pe/qa进行fmea及pmp(qc plan)的制作和审核。 3.编定ipqc重点稽核事项
4.培训及考核检验员和生产部外观检查员,制作gr&r。 5.检验设备的gr&r和cpk计算。 6.制程稽核
7.4m变更跟进及产线品质异常的跟进处理 8.oqc不良品/客退品的分析处理及相关客户投诉的对策回复(8d)
三、2004-10~2005-03 作为ie部esd工程师
导入esd管理系统,及新生产大楼的esd规划与防护。 1.组织相关部门,成立esd小组推动esd工作。 2.建立esd管理系统和制定相关的控制文件 3.培训esd知识 4.评估及购买相关的esd测试设备,防护用具,辅材等等 5.解决生产线的esd问题。期间解决了摩托罗拉客户的摄像头模块在测试区域esd损伤问题。
6.解答客户审核中提到的esd相关问题。
离职原因: 经济危机
**公司 (2002-07 ~ 2004-10)
公司性质: 外资企业 行业类别: 计算机硬件
担任职位: esd 岗位类别:
工作描述: 负责esd研究、esd材料仪器的评估与新产品试产线的esd控制。 1.在实验室研究新一代tmr磁头的esd机理,提出管控办法。 2.评估esd防护材料和相关的仪器 3.解决试产线新产品的esd问题 4.培训助理工程师
5.esd标准和文件的制定
在美国esd协会发表论文“breakdown behavior of tmr head in esd transients”--2004 symposium program seion 5b 在日本rcj协会发表论文“effect of gmr undercoat thickne on dielectric breakdown voltage”
离职原因: 个人发展
技能专长
专业职称:
计算机水平: 中级
计算机详细技能: 熟练使用办公软件及minitab 技能专长: 1.熟悉相关标准(iso***ts16949/icti等)。 2.熟悉电子行业的注塑/smt/cob/成品组装工艺(如蓝牙耳机,摄像头,手机配件等)熟悉相关的产品(成品及pcba)检验标准、抽样技巧如(ansi/asq z1.4、gb2828) 3.6-sigma 黑带,熟悉各项品质工具的使用如fmea,qc7大手法、hoq/msa等等 4.积极主动,较强的领导力及团队建设能力,能够管理将近百人的团队 5.较强的品质意识,良好的数据及逻辑推理能力和解决问题的能力 6.良好的英语、粤语和普通话
语言能力
普通话: 流利 粤语: 流利
英语水平: cet-4 英语: 熟练
求职意向
发展方向: 意向1:发展来料检验及供应商管理方面的能力,完善品质管理技能,为进一步提升自我打好基础。
意向2:提高客户服务及出货管理方面的技能,完善品质管理技能,为进一步提升自我打好基础。
自身情况
自我评价: 1.熟悉相关标准(iso***ts16949/icti等)。 2.熟悉电子行业的注塑/smt/cob/成品组装工艺(如蓝牙耳机,摄像头,手机配件等)熟悉相关的产品(成品及pcba)检验标准、抽样技巧如(ansi/asq z1.4、gb2828) 3.6-sigma 黑带,熟悉各项品质工具的使用如fmea,qc7大手法、hoq/msa等等 4.积极主动,较强的领导力及团队建设能力,能够管理将近百人的团队 5.较强的品质意识,良好的数据及逻辑推理能力和解决问题的能力 6.良好的英语、粤语和普通话篇5:sqe工程师的个人简历模板 sqe工程师的个人简历模板
姓 名: 黄先生 性 别: 男
婚姻状况: 未婚 民 族: 汉族
户 籍: 广西-玉林 年 龄: 29 现所在地: 广东-深圳 身 高: 177cm 希望地区: 广东-深圳、广东-东莞、广东
希望岗位: 经营/管理类-部门主管
质量/安全管理类-sqe/供应商质量工程师
质量/安全管理类-供应商管理
质量/安全管理类-质量管理/验货员(qa/qc) 寻求职位: sqe工程师、品质主管
待遇要求: 6500元/月 可面议
最快到岗: 半个月之内
教育经历
2002-09 ~ 2006-07 广西玉林师范学院 电子信息科学与技术 本科
培训经历 2007-06 ~ 2007-08 东莞乐诗电子塑胶有限公司 iso系列/tqm/qc七大手法
工作经验至今6年9月工作经验,曾在3家公司工作 **公司 (2009-01 ~ 至今)
公司性质: 外资企业 行业类别: 电子、微电子技术、集成电路 担任职位: sqe工程师 岗位类别: sqe/供应商质量工程师
工作描述: 负责对供应商的评审管理(选定,审核,绩效管理);跟进处理来料质量问题,分析处理产线来料异常,辅助供应商进行问题改善。
负责产线剩料的确认和控制。
负责编写检查指示,制作相关测试架。给予iqc检验员提供相关的技术指导和培训。 离职原因: 寻求更好的发展
**公司 (2007-10 ~ 2008-12)
公司性质: 外资企业 行业类别: 家具、家电、工艺品、玩具
担任职位: 品质工程师/采购跟单 岗位类别: qa/品质工程师
工作描述: 1.负责跟进产品的品质,处理产线异常,客诉和供应商的品质问题,陪同客人(如美泰,沃尔玛,intermatic,game,善龙等)验货以及对工厂的稽核.同时主导开展产品过程审核以及产品审核。另外编写产品检验规格,品质计划,不合格品处理办法,协助编写dfame/pfame同时给iqc,ipqc,oqc,lqc提供相关技术指导和培训。 2.转入采购部后,负责供应商的选定,评审,下单,协助iqc处理来料品质问题,协调跟进公司生产与物料交期。
离职原因: 公司倒闭
**公司 (2005-12 ~ 2007-10)
公司性质: 外资企业 行业类别: 电子、微电子技术、集成电路
担任职位: qe工程师 岗位类别: 电子工程师/技术员
工作描述: 负责qa,qc(包括iqc)的技术指导,培训。分析处理来料,生产过程中以及出货验货中出现的异常情况,客户投诉,编写品质计划,质量标准和作业指导。另外负责实验室对产品的可靠性等的相关测试,参与公司iso内审以及陪同客人对公司进行检验,审核。
离职原因: 拖欠工资
技能专长
专业职称:
计算机水平: 全国计算机等级考试二级
计算机详细技能: 熟练使用excel,word等办公软件以及erp/mrp系统。
技能专长: 1.熟悉电子物料的采购流程,有较好的成本控制意识。能够对供应商进行有效管理。
2.熟悉各种电子原件,塑胶五金件,特别是连接器以及电声产品;能熟练操作各种测量工具。
3.熟悉产品的检验和品质控制流程,fmea,cp,qc作业指导书的的编写;能独立处理日常品质问题/客诉;能组织、带领iqc/lqc/ipqc/oqc对产品质量的有效控制;熟悉iso系列,ts16949,en71,astm-f963,rohs,ul,熟练使用新/旧qc七大手法,spc,了解nf,fcc,ce,weee;个人简历模板 4.喜欢篮球和书法,在学校一直担任学生会主席,能组织和参与各活动,工作后经常协助人事部组织公司的各种文艺活动!
语言能力
普通话: 流利 粤语: 流利
英语水平: 口语一般
英语: 良好
求职意向
发展方向: 希望能得到一个更好的发展,学习的空间。更好的为公司发展,做出本人应有的贡献。
其他要求:
自身情况
自我评价: 为人诚恳,活泼开朗,有较强的适应能力,沟通能力,事情处理能力和领导能力,能在压力下工作。
推荐第4篇:SQE个人简历
个 人 简 历
姓名:**
性别:
出生年月: 身高:
民族:
学历: 大专 专业 :企业管理
血型:
联系方式:
户口所在地:**** 现居住地:
教育背景:
1999.9-2002.7
江苏、盐城、广播电视中等专业学院 2006.4-2009.12 江苏南京农业大学
工作经历:
2003.3-2006.4 在**公司担任QE主要负责廠內外品質異常處理工作和體系工作.2006.5-2007.11 在**公司担任ISO体系工程师负责推行TS16949/ISO14001工作和体系维护工作。负责公司内部审核、年审、客户稽核。 2008.1-至今 在**公司担任SQE&ISO專員工作
主要负责:1.冲压件风扇电子件,包材类,供货商来料异常处理,制程材料异常处理和判定,iue的改善确认,制定进料检验标准书和新产品变更文件修改.
2.推动供货商内部质量改善,导入常用质量工具.
3.新厂商稽核(采购/RD/品保)择优选择厂商,合格厂商年度QSA/QPA/HSF稽核及辅导, 供应商的异常不定期稽核及辅导,追踪厂商改善效果确认.
4.执行供应商的奖罚措施.
5.材料质量目标达成状况的改善及检讨.
6.供应商质量月报,FAI 报表,信赖性报表的跟催及确认,HSF产品及制程管制等.技能
7.QC080000/ISO9001:2008/ISO14001/OHSAS18000的体系推行和文件的编制维护,主导客户稽核、内部稽核、管理评审、年度监审等工作內容.特长: 1.熟练应用OFFICE、SAP系统、PHOTOSHP、PHOTOSHPCS、3D MAX、AUTO CAD 2.熟练QC七大手法、ISO八大原则、TS16949五大工具
3.熟悉ISO流程对ISO文件编写有一定的能力在公司主要负责ISO审备、客户端稽核、供应商稽核、年审、组织公司内部稽核对品质体系执行情况之定期与不定期稽查对品质体系之不适用之处进行评审与提供改善方案.教育及培训:
2005年-2013年获得ISO9001,ISO14001,OHSAS18001,QC080000,IS16949,EICC内审员证书及内部仪器校验证书。
2013.4 公司总部请外训培训6 Sigma绿带并完成结业 2013.12 培训ISO9001国家注册外审核员。
自我评价:
本人为人正直,好强,能吃苦耐劳,有上进心、责任心、自信心、工作积极,具有团队合作精神,具有一定的组织能力,能互相协调,语言沟通力强,有较强的逻辑思维能力和接受能力。
推荐第5篇:SQE规范
SQE规范2013
一、零部件新品开发
1.1组织与策划阶段:
1.1.1参与零部件设计数模评审
由项目部组织公司内部相关部门对设计数模进行评审,确认零部件的质量特性,特殊特性。SQE参与设计评审。
备注:项目部组织评审→SQE参与→研发部输出评审数模
1.1.2参与项目启动会议
供应商选定,且数模已发给供应商后,采购部组织供应商及新通达相关部门召开项目启动会,进行技术交流:
(1)向供应商明确项目大概时间,零部件质量目标和要求;
(2)双方明确项目相关责任人及联系方式;
(3)双方明确工装模检具要求(现场工艺人员确认是否需对方案进行认可),对于暂未要求检具的,后续技术质量部可根据质量控制需要提出;
(4)新通达向供应商提出零件所要求的验证、确认、监视、测量、检验和试验活动,以及零部件开发各阶段的接受准则,明确零部件开发各阶段活动所需提供的记录格式及内容(特别是出货检验报告形式:检查报告/检测工艺卡/三坐标);
(5)技术质量部明确零部件PPAP要求(提交等级,各阶段提交内容);
(6)对于未召开项目启动会的零部件,研发部需另行发布需重点监控零部件清单以及具体的特别活动要求;
(7)供应商对上述新通达要求回复活动计划,风险程度,对新通达的工作要求。 备注:采购部发布会议通知→SQE参与→会议纪要
1.1.3收集开发阶段PPAP资料
零部件清单发布且供应商确定后,SQE确定供应商生产件批准材料清单、级别(或根据供应商质量保证能力调整提交级别)。
向供应商收集《供应商开发计划》并通报相关部门,有异议的由技术质量部转给供应商。 对于3级审批零件还需向供应商收集《产品/过程设想提案》、《产品品质和可靠性目标研究结果/计划》资料,并转技术中心审核,跟踪审核意见,将审核结果反馈供应商。
备注:SQE组织确定供应商生产件批准材料清单、级别→供应商提交《供应商开发计划》/《产品/过程设想提案》、《产品品质和可靠性目标研究结果/计划》→SQE→采购部/研发工程师→审核意见→SQE→供应商
1.2工装正规化(ET):
1.2.1收集ET阶段PPAP资料
按开发主计划进度,收集PPAP部分电子版资料,并转发相关部门审核;对于新通达设计开发或由供应商同步开发的,向供应商收集《产品图纸及工程规范》;对于PPAP三级提交的零件,向供应商收集《设计失效模式及后果分析》;在项目启动会确认的出货检测项,供应商整理后,向供应商收集《检查报告》表格及项目启动会中,明确需提交的其他相关报告表格(如检测工艺卡)。
备注:SQE向供应商收集《产品图纸及工程规范》、《设计失效模式及后果分析》→研发工程师审核并提出审核意见→SQE将审核意见转供应商
SQE向供应商收集《检查报告》/其他相关检测表格→研发工程师、现场工艺人员审核并提出意见→SQE将审核意见转供应商
1.2.2负责零部件验证试验的跟踪、判定
研发部发布专用件设计验证性能试验清单,SQE转发供应商,并要求供应商在性能试验清单发布后7个工作日内发布试验详细进度计划,SQE根据进度计划监控试验实施进度,并每周进行一次进度汇报。SQE仅对试验进度负责,对试验结果不合格的零件由研发部负责整改。 备注:研发部发布专用件设计验证性能试验清单→SQE→供应商→实施计划→进度跟踪→试验报告→研发部
1.2.3负责试制样件确认
对所有试制样件的检验,要求技术质量部SQE参与。对所有试制样件的生产,原则上要求技术质量部SQE(必要时组织现场工艺员、研发部等部门)到供应商现场对试制样件制造工艺、原材料型号、出货检验方式进行确认,并对检验结果进行签字认可,技术质量部检验员进货检验时只检验外观。对于不能前往供应商现场进行试制样件检验方式确认的,要求技术质量部SQE参与进货检验,并对检验结果进行确认。对于无法判定结论的样件,应该由SQE组织研发部设计人员共同确认是否可用。
对于送检不合格零件,SQE需在一个工作日内反馈供应商,供应商需在两个工作日内回复原因、整改措施及可提供整改件的时间节点。不合格样件原则上都应做退货处理,如还需装表使用,必须经由项目部、研发部、技术质量部共同评审同意,否则对使用部门擅自使用旧批次不合格样件提出考核。SQE监控样件的整改进度,并在样件整改完成后,及时要求供应商重新送样验证,直到样件合格。必要时,SQE需到供应商现场进行送检不合格问题整改确认。 供应商出货检验报告中的三座标检测数据转研发部,研发部审核意见反馈技术质量部,由技术质量部将确认结果反馈供应商。
检验时,发现重发问题、未经同意将旧批次不合格品发至新通达现象,将对供应商提出质量考核。
备注:样件送检→SQE、检验员检验并记录检验结果→SQE判定送检结论/无法判定结论的由SQE组织研发部评审→送检结论反馈供应商
1.2.4负责确认样件装表状态
ET样表试装时,SQE应结合过往不良数据对装表过程进行跟踪,关注外购零部件的关键尺寸、轮廓尺寸、面差、间隙、配合松紧度等情况。识别零件装车后状态,审核确认检具方案时零件状态与实际装表尽可能一致。识别外观件A、B级面,后续模具方案、外观检查时重点关注。
1.2.5装表问题、整表评审问题整改跟踪
对于不合格项,与相关部门/供应商确认整改对策。
因零件尺寸不良导致的质量问题,要求供应商派技术人员到新通达进行每轮装表跟踪,直至问题的关闭。因零件外形尺寸、功能等不良导致的质量问题,要求各分管SQE确认现表问题,并在两个工作日内反馈供应商,如供应商不能及时回复不良原因及整改对策,要求供应商派技术人员到新通达进行实表问题确认。如供应商整改不及时或配合不积极,可提出相应考核。必要时,SQE需到供应商现场进行质量问题整改确认。
样件验收依据及所有疑难问题点必须与研发设计工程师共同确认。
备注:样件试装通知→SQE跟踪装表过程→质量问题→对策回复→跟踪整改→整改验证
1.2.6负责OTS封样工作
对于需要封样的零件,SQE组织各相关部门及供应商进行封样工作。
1.2.7收集ET阶段PPAP资料
供应商工装模具、检具完成后,向供应商收集《过程流程图》、《过程失效模式及后果分析》、《量、检具承认申请书》、《供应商试验报告(设计验证)》,并转发负责审核部门,跟踪审核进度,将审核意见反馈供应商,并督促供应商整改。
备注:供应商提交《过程流程图》、《过程失效模式及后果分析》、《量、检具承认申请书》、
《供应商试验报告(设计验证)》→SQE→研发设计工程师→审核意见→SQE→供应商
1.3工程正规化(PT)
1.3.1收集PPAP资料
按开发主计划进度,向供应商收集《供应商控制计划》、《零部件供应链图》、《过程失效模式及后果分析》、《过程能力研究结果》、《供应商试验报告(产品验证)》、《常见故障模式及分析处理办法》、《包装规范及外观批准申请书》,并转相关部门审核,跟踪审核进度,将审核意见反馈供应商,并督促供应商整改。
备注:供应商提交《供应商控制计划》、《零部件供应链图》、《过程失效模式及后果分析》、《过程能力研究结果》、《供应商试验报告(产品验证)》、《常见故障模式及分析处理办法》、《包装规范及外观批准申请书》→SQE→采购部、项目部→审核意见→SQE→供应商
1.3.2负责组织PPAP的批准
SQE收集全套整改完成的PPAP文件发放给相关部门按文件判定基准审核。所有PPAP电子版文件审核完成后返回技术质量部,由技术质量部发供应商修订后打印。供应商需在PT转SOP前将纸质文件返回新通达技术质量部,转相关部门书面批准。技术质量部根据各部门签署情况,在生产件批准申请书上签署最终结论意见。
备注:供应商提交全套整改完成的PPAP文件→SQE→研发部、项目部、采购部→签署意见→SQE→批准
1.4试生产阶段(SOP)
1.4.1负责初期流动活动期间供应商品质问题的监控
根据初期流动管理规定,发布初期流动管理清单以及通知书,并跟踪初期流动管理阶段外购零部件的质量状况。
1.4.2负责供应商初期流动活动退出申请的审批
根据初期流动管理办法,对满足退出初期流动管理的零件,同意退出初期流动审批。
1.4.3负责量产后外协件质量问题的整改及监控
正式量产后,监控零部件的质量表现,对于质量问题督促供应商进行整改。
二、生产过程零部件质量管理
2.1生产现场突发质量问题的零部件SQE需进行及时处理;在保证生产不停线的情况下,与供应商质量部沟通,采取临时措施并要求供应商质量部在接到通知后7个工作日之内提交问题整改分析报告,SQE负责整改后的零部件效果验证跟踪。
2.2每月SQE对各自负责的零部件生产过程质量进行排名,排名最后三名的供应商,将对此开展质量专项整改活动,此项活动可调动技术质量部所有人员参与,问题整改验证跟踪由该零部件SQE负责。同时将此项活动作为月度零缺陷工程会议的一部分。
三、市场售后零部件
3.1 对客户现场投诉产品上的零部件问题,SQE配合生产现场质量工程师一同处理,现场质量工程师负责与客户直接对接,并按客户要求提交的时间结点编写整改分析报告;
3.2 SQE负责售后零部件问题的处理工作,对供应商进行反索赔或专项整改。反索赔按照与供应商签订的质量保证协议进行处理;对需专项整改的问题成立售后质量问题整改小组,SQE调动售后人员完成整改与验证跟踪工作。
四、供应商体系管理
4.1供应商体系证书管理,每年排查一次供应商体系证书数量,每月监察供应商体系证书运行有效性,并建立供应商体系证书一览表。
4.2新进供应商的体系审核,SQE配合采购部参与新供应商的评审工作,根据不同的供应商等级开展,按照评审表得出综合结果,对不满足体系审核要求的供应商,要求限期整改,整改合格后方可纳入新通达供应商管理体系,整改不合格取消纳入资格。
五、供应商数据考核
5.1 SQE每月统计生产现场处理问题跟踪记录表,对生产线发生的零部件质量问题进行处理、统计、跟踪,做到每一个问题都有追溯性。并且将此统计数据纳入供应商考核。
推荐第6篇:SQE管理员
SQE-Supplier Quality Engineer 供应商品质(管理)工程师
新产品开发初期,SQE主要负责来料品质的控制和跟进,跟进所属供应商的来料品质状况,便于后期量产时进行关键性的评比和审核,接受或不接受此供应商。
具体事项:1)收集供应商资料;2)同所属供应商共同改善来料品质;3)跟进来料及所属供应商所做的改善措施及结果如何;4)量产前根据之前所收集资料评估供应商PASS或REJECT
附SQE主要工作职责(因现代化工厂的告诉发展,传统的SQE不能覆盖所有公司对职位的定义):
1.推动供应商内部质量改善
1.1 推动供应商成立完善的质量保证小组.
1.2 供应商过程变更及材质变更的确认管控动作.
1.3 新材料及变更材料的管控.
1.4 推动厂商导入常用的质量工具,SPC, 6Sigma 等品管手法。
1.5 材料质量目标达成状况的改善及检讨。
1.6 不合格项目的改善确认动作。
1.7 材料异常的处理及成效的确认。
1.8 往来供应商的品质管控。
1.9 供应商风险评估。(资深SQE)特别声明:供应商质量管理不是SQE一个群体就能够做好
的事情
2.推行执行SQM的系统程序文件.
2.1 供应商的评监,择优选择厂商。(不一定所有的SQE都能够)
2.2 供应商的定期及特殊审核的执行。
2.3 供应商的辅导,提升质量。
2.4 执行供应商的奖罚措施。(不一定所有的SQE都能够)
2.5 建立完善规范的材料进料检验程序及QIP。
2.6 外协厂商SOP(作业指导书)、QC工程图的制订。
推荐第7篇:SQE工作总结
个人工作总结-2013年度
时光荏苒,公司又走过了一个辉煌年。回首2013年,我在公司及部门领导的指导带领下,在各位同事的协同下,基本完成了各项任务。主要工作有: 1.通过反复的调试比对超声波和热熔机,完成了b客户表贴式和嵌入式按钮线路板熔接保持力的问题,使量产产品的线路板保持力符合要求,解决了客户飞检投诉的问题。 2.优化并发布了供应商索赔制度,同时完成了供应商的索赔工作,全年索赔共计约合人民币21万多元。
3.参与新开发的北美项目的第一阶段任务,一周内指导供应商完成ppap资料31份。 4.从6月份起,给三家零库存供应商制定了改善辅导方案和计划,定期辅导,并定期监督检查完成状况。通过此次辅导,各家供应商在管理流程上有了初步改善,都已经建立了专职检验员制度。其中甲供应商连续三个月的fpy和otd都已达标。 5.与技术工程师和采购同仁一起,对乙供应商(pcb板供应商)进行多次审核,帮助其查找问题,验证其纠正预防措施的有效性,减少生产对原材料的投诉,保证公司产品按时保质出货。
6.与质量工程师一起,通过对供应商的多次审核辅导,帮助他完成按钮组装的可量产化工作,完成了公司产品外包的工作。
此外,我还能积极参与公司组织的各项理论和专业知识培训,为后续工作能更好的开展打下铺垫。 过去的一年里虽然取得一些成绩,但也有需要提升的空间: 1.需要强化项目管理的知识,参与项目的过程中,要能更加积极主动。 2.对供应商管理方面,要想办法培养供应商解决问题的主动性和能动性,而不是我们催就动,我们不催就没有动静。 3.平时工作中,与供应商沟通时,要能控制自己的情绪,要通过交流让对方接受自己的观点,明白自己的要求。 2014年公司即将开发更多优秀的客户,展现在自己面前的将是一片任自己驰骋的沃土,但同时也感受到了沉甸甸的责任,在今后的工作和生活中我将继续努力学习,深入实践,不断提升自我。 xxx 2014-1-3篇2:2011sqe年度个人总结
年度工作总结
时间流逝,岁月如梭,2011年已悄然走过。在这一年中,本人在公司和部门领导的指导下、在各位同事的协助下,基本完成了年初计划中所定的各项工作。回想这一年来,本人服从领导,努力工作,严格要求自己,不断提高,自我加压,保证工作质量,严把质量关。保质保量地完成了领导交办的各项任务,主要做了以下一些工作:
一、新品开发
1、完成##2011款项目开发,共涉及12个零件的开发,均满足开发节点及质量要求。
2、完成##一阶段性能提升项目开发工作,共涉及5个零件的开发,均满足开发节点及质量要求,
3、新##项目开发任务,包括多媒体系统灯具等关键项目目前正在进行中,在tr阶段开始积极参与技术方案的确定并积极参与联合设计方案的确定,如尾灯led布局,车厢阅读灯,多媒体系统人机互动界面等,有效降低投产后发生质量风险与用户抱怨的可能,预计2012年可完成开发任务。
4、完成总装信息联络任务,减少总装抱怨。
5、组织sqe落实top10年度控制任务,实际退出6家, 2家正在办理中,剩余两家。
6、共完成ppap认可70余件
二、现场问题、质量改进、售后等问题处理
1、处理电器现场问题90多起,主要涉及装配干涉、生产缺货、产品质量等诸多问题,均在第一时间解决现场问题,做到了无停线,零抱怨,零遗留。
2、走访售后服务站9次,验证和了解了前期质量问题的改进情况,并找到了数码播放器(死机问题),cd机(改装导致进水)异常索赔等故障发生原因,为后续质量改进提供了有效和及时第一手资料,促进了质量改进项目的完成。
3、共完成8项公司质量改进项目,其中中央控制盒改进,雨刮器改进等诸多项目均得到质量部,售后和客户的共同认可。
三、其他方面
1、积极参加各种群众性质量管理活动(如:合理化建议活动等)。
2、认真学习理论知识,学习各种方法技巧,参加各种专业培训,如:pcpa、apqp、tr、pcpa等,在后续工作中将进一步加强专业性工作的学习
3、对项目管理的认识有了一定的提升,在2012年工作中要加强项目管理的计划性和及时性跟踪,以及相关部门的协调工作。
四、几点感想和体会
在这一年时间里,部门领导和科长对我关怀备至,时常给我鼓励和帮助。使我感到:
1、工作要一丝不苟
工作时一定要一丝不苟,仔细认真。不能出错,平时要经常反思一下自己的工作,以确定自己的工作万无一失。工作之余还要经常总结工作教训,不断提高工作效率。在这一年时间里,同事们严谨、认真的工作作风给我留下了深刻的印象,我也从他们身上学到了很多自己缺少的东西。
2、工作要勤于思考 sqe岗位的日常工作比较繁琐,而且比较枯燥,这就需要我们一定要勤于思考,改进工作方法,提高工作效率,减少工作时间。
3、工作要不断学习
要不断的丰富自己的专业知识和专业技能,这会使我的工作更加得心应手。一个人要在自己的职位上有所作为,就必须要熟知专业知识,并在不断的学习中拓宽自己的知识面。 2011年的结束,2012年的到来,是开端也是结束,展现在自己面前的是一片任自己驰骋的沃土,也感受到了沉甸甸的责任,在今后的工作和生活中我将继续努力学习,刻苦钻研,深入实践,不断提升自我。
吴发强
2011年12月22日篇3:sqe工作怎么做(个人经验总结分享) sqe工作怎么做——个人经验总结分享
两年前进这个公司的时候,我被安排到做sqe的工作,当时的我对“sqe”是什么一点概念都没有,简直是一头雾水,工作内容是什么?怎么开始着手去做?虽然公司设置了一个供应商管理部的空壳子,可是寥寥几个人做的工作也只是催催供应商交货,整改产品质量,要求提交8d报告什么的。在没有经验、没人指导的情况下,我开始了我摸着石头过河的sqe经历。
如今转做其他工作的我想结合以前摸索出来的sqe工作方法总结一下我所认为的sqe工作应该怎么做。
我们公司是一个做汽车电子产品的企业,规模不算很大,但是麻雀虽小五脏俱全,杂七杂八的事情也不少。一开始给我的感觉sqe的工作就是介于采购部和品质部之间的辅助性工作。虽说是供应商质量工程师但是iqc、scm、sqm的工作都会做一些。当然了肯定是没有专门做这些工作的人员做的系统和专业,iqc就不用说了,为了保证来料顺利供应生产,除了控制数量、检查质量和催交货期之外也就是培训人员检测方法、现场验货加上辅助仓库盘点的事情。scm方面的工作主要就是帮助采购人员协助客户提出的设计变更和工程变更va/ve提案要求供应商配合做到cost down。sqm方面我们还是有分工的,供应商管理谈不上,也就只是按照产品的性质划分的,比如负责树脂件、钣金件的大部分时间都在跑现场和供应商,疲于处理各种各样的现场不良,用于供应商管理的时间少之又少;负责电器、总装零件的,现场倒是没有多少事情的,只有售后出现的不良,那样,除了解决市场问题外,重点就需要放在供应商管理上。
刚开始接触的时候,经常跟着别人跑供应商去解决一个又一个问题,通过这些问题的解决我也积累了一些经验,慢慢的从这些问题里就看到了相关供应商存在的弊病在哪里,随着专业知识的增长就开始不满足于解决单个问题了,也想分析出现这些问题的原因,希望把这些问题都控制在供应商内部,甚至更进一步提出自己的看法想帮供应商把问题的隐患消除掉,自然而然的就进入了供应商管理的角色。当然在这个时候就发现这个角色对自己的能力和对各方面的知识经验要求很高,只有多接触,多学习,多和供应商一起解决问题才能得到能力的提升,否则只能是做一些像救火队员一样的事情,哪里发现问题就去哪里解决,整天疲于奔命不说还消耗掉了自己的耐心,变得只为解决问题而解决问题,自己得不到提高更别提做供应商管理了。
至于sqe工作的重点应该放在哪里,这个也是一直困扰我的问题。曾经我有一个同事工作非常努力,整天泡在供应商那里忙着做供应商审查,帮供应商建立品质体系,忙忙碌碌的却在我们公司内看不到什么成果,被老板询问的时候他回答说要帮助供应商和我们公司一起成长。当然,扶持供应商的做法不错,但是他显然是没搞清楚sqe工作的重点。sqe的使命就是通过对供应商的品质进行管理来保证来料品质,其核心是保证来料品质而不是去帮供应商做qe。指望着通过sqe了解的那点三板斧的皮毛功夫就能提高供应商品质,那供应商聘请的专业的qe、me人员岂不是乐得坐享其成你的成果了?
诚然,供应商的品质体系建立是非常有必要的,出了品质问题找供应商要8d报告也是非常有必要的,但这并不能保证能够提升供应商的品质,毕竟品质的提升是一个非常复杂的过程,不是通过解决一两个问题,提交几个8d报告就能显著改善的。 sqe和供应商站的角度不一样,对待质量的看法也就不一样。sqe是站在客户的角度审视产品,不仅局限于产品的生产技术和工艺,反而能从产品的使用机能和产生的效果来分析。也许供应商自己的人员在专业、管理、经验上更丰富,但从他们自己的角度也许未必能够发现问题。所以在内行看来是外行的sqe往往能跳出供应商自己的思维模式,在某些方面提出建设性的意见从而使供应商得到提高也不是不可能的事,所以,sqe也要发现自身的优势,虽然没有供应商对产品研究的专业,但是sqe接触的零件种类比较多,虽然可能能力没有供应商强但是却有很多机会从不同的供应商那里学到工艺、过程控制、管理、检验等有优势的东西,将这些东西自己掌握吸收以后用来指导别的供应商也是能弥补供应商之间的相互劣势,还能使自己的客户身份得到供应商的尊重的方法。 如今,很多企业在开发供应商资源的时候往往都会采用两家供应商供货的方式,这样不仅避免了其中一家出现质量问题造成无法供料影响生产的情况,还能通过两家份额比例的分配制约供应商,使两家同一产品的供应商为了拿到大份额相互竞争,提高品质,降低价格,还能使两家优势互补,相互借鉴,共同提高。这样sqe在对供应商指导的时候就可以做出比较,能用一方的优势作为自己的经验指导给另一方,提高了自己在供应商心中的地位也实现了指导供应商的成绩。当然也有一些sqe懂的不多却经常以客户身份自居,在一些问题上去挑战供应商,但每次讲的道理都不够充分,不能使供应商信服,反而要供应商一定按照自己的要求做,那样做的后果是让供应商觉得受到了强迫,久而久之sqe在供应商心目中的威信扫地,人格魅力荡然无存,导致引起供应商的逆反心理工作上不愿去配合,工作不好推进不说,在供应商眼中这样的sqe除了有个客户的身份,其他的狗屁不是!
有些大的供应商很牛,有的时候都不愿意理小客户的sqe,遇到问题需要他们配合时要么敷衍了事,要么拖拖拉拉拿不出个结果。这样给sqe的工作带来很大的麻烦。所以,sqe不仅需要自己有过硬的专业知识使供应商信服,还要搞好和供应商的关系。很多问题供应商自己看到或者没看到的(有些是不容易改变的)都懒得去整改,都想应付过去就算了,这是人的本性,没办法,这时候sqe就要起一定的作用了,不光要催8d改善报告等,还要跟踪改善落到实处,现场审查甚至驻场跟催就是有必要的,只有保证供应商改善完成了才是问题的解决的根本。搞好和供应商的关系很重要,但是最重要的也是最根本的sqe要树立自己的权威,在关键时刻施加压力,不要手软,实在遇到不配合或者屡教不改的供应商要拿出自己的强势手段对供应商进行处罚。
以上,是我对自己曾接触到的sqe工作的一点看法,虽然在sqe职位工作的时间不长但是学到了很多东西,以后不论自己是否还有机会从事sqe的工作,但姑且先把这些心得写下来以便将来能活用的到。篇4:sqe 工作经验总结
本人2003年毕业后,鬼使神差般地进入了quality这个领域,一直从事sqe工作也有近4年的光景,今天把自己的一些做事方式,态度及sqe的职责show出来,供同行和外行加以褒贬,让自己吸取更多的精华,剔除糟粕. 备注,我所负责的材料主要是ee(pcb/fpc/pcba/fpca,rlc 及connector),所以下面很多的工作经验之谈是站在ee这个面展开的,不过,相信对于负责其他材料的同仁还是有一定的帮助的,毕竟sqe是技术及管理共存的一个职业. 当然,在此show出这么多个人经验之谈,也不乏有推荐自己之意,我相信我绝对是适合的人选。
一,绩效--就是通常说的kpi (key performance indictor) 但事实上,个人觉得真正衡量sqe的ability应该是supplier 8d回复的时效性及有效性,之所以这样说,是因为材料的特殊性,相信sqe同仁有同样的感触. 当然,有些材料本身supplier的sense或者其proce已经达到很高的水准,其品质面本来就很少出状况,来衡量管理这样材料的sqe performance,真的很难定夺,也许就是production的dppm trend chart 及service(training and so on). 二,职责(responsibility) 围绕保证品质来料这目的,sqe应负起如下的责任, 1.对供应商进行例行的绩效评估和audit. 2.品质监督和异常协辅
3.npi(new product 导入)/ecn 变更时,供应尚制程及产品的确认,cip的改善. 4.gp 产品及其管制. 针对以上四点,小弟我浅谈下我的经验,供各大侠指导. 1.对供应商进行例行的绩效评估和audit. 1.1导入新厂商阶段,一般有pur/rd/sqm/esh部门共同参与,sqe此阶段需要做的是让supplier提供供应商调查报告及工厂内部组织架构等等大项,此阶段主导者应该是pur. 1.2对供应商进行qpa(quality proce audit),这需要依据具体的产品来衡量,但不外乎receiving inspection, warehouse, mrb, production line, rework proce, oqc and packing&store, record and so on. 机, 3.machine maintained 4.measurement/tool 精确度
料, 5.区分隔离 6.保存期及保存方式
法, 7.traceability&identification 8.spc, fai checklist 环, 9.esh 10.温湿度 qpa的frequency,目前很多公司已经没有强制的定义,只要公司一出现比较大的case, sqe就驻厂,针对相关站别进行audit.事实上,这样做起来的确很有效果,sqe第一时间内了解到
不良品,然后又第一时间内去supplier端去audit相关proce,相信很大程度上能很快解决问题,使公司顺利生产,让supplier及时改善. 1.3对供应商qsa(quality system audit),通过对supplier系统面的audit,是希望指出supplier在整个面上的不足,一般来说,sqe主要audit的item如下, a.document management b.供应商之supplier的管理. c.product identification & traceability d.proce control e.检查和测试管理. f.calibration g.nonconforming product control. h.handling, package, storage and delivery i.record—这一项适合所有的audit items. 当然事实上,sqe重点放在上面items外,其实还是有些需要audit的项目,比如quality system, contact review, 甚至设计管理. 一般来说,qsa一年一次. 事实上,真正反映supplier performace的是qbr 会议,参与部门有pur, technology and sqm,分数比例一般为pur-- 35%, t-- 30% sqm -- 35%. 主要出发点 pur—delivery/cost/service t—technology share / service sqm—quality iue/ service ps: sales 人员注意,客户的3个主要对外窗口都很注重service. 这样的qbr meeting一般有sqm主导,当然supplier参加的窗口也应该是对应的sales/t/qa(cs) 部门. 个人认为后续product的竞争力应在品质上,所以站在sqe的角度上,我是希望sqm的比重可以适当加重. 1.4gpa(green product audit),目前很大部分公司已将此audit纳入qsa中,在这我就不细谈了.但重要的还是离不开如下6点: a.gpa的文件规范系统. b.proce management system c.training d.supplier’s 外包管理 e.ec管制(后面会细谈) f.检验和分析. 2.品质监督和异常协辅
个人很在乎的是能够很好的push supplier建立fmea部门,这样做的好处如下: 对应supplier a.但有异常发生时,能很快的组织起分析小组,尽快找到问题点,预防问题的进一步扩大, b.很快的处理异常,以达到最低限度的减少损失, c.buglist,作为经验的积累,方便后续品质的追踪. d.能很大程度上消除公司”踢皮球”的坏习惯. 对于公司(customer) a.defect sample分析的时效性得以保证.(8d cycle times) b.sqe可以第一时间内,review8d report,可以很快的找到对应分析窗口. 诚然,fmea小组的建立不能很快的让supplier看到自己利益的增长,但我敢保证fmea团队绝对是supplier和customer 很好的沟通桥梁.由于fmea团队的重要性,一般我都是直接找supplier site manager来谈,因为fmea小组需要很强的技术分析能力,很好的工厂执行力及分析defect的仪器设备, 这些都需要site manager的大力support. 相信优秀的sqe能明白我的想法也希望能给相关同仁一些感触. 对于异常协辅,也许很多行外人觉得sqe的技术能力真的有那么专业吗?能协辅supplier进行改善? 诚然sqe是技术和管理共存的一个特殊的岗位,相信没有一定的技术能力是很难让supplier诚服的,也的确sqe没有supplier的pe在技术上的专长,但一般来讲,公司现在很少找单一source supplier, 所以sqe有更多的机会去借鉴不同的经验,各公司一定都有他的长处,我已经习惯将各厂商长处相联结,同时也习惯让supplier习惯我的管理方式.之所以说sqe能给supplier异常辅导,是因为各岗位人员看待问题不一样,pe可能想到了改善的方向,但出与cost的考虑,还是无法进行有效的动作.甚至一些品质iue的轻微改善,一些自工具的设计有可能,等等类似的问题. 总之,sqe会取长补短,集合自己的经验能有效的给出supplier改善的方向. 3.npi(new product 导入)/ecn 变更时,供应尚制程及产品的确认,cip的改善. 先来谈下npi的管控.相信大部分的sqe有这样的体会,公司出现异常后,在最后root cause出来后才发现,原来这样的问题在试产阶段就已经存在,但种种原因,在没有得到解决前,此model已经进入量产阶段,这样以来,sqe就成为大家指责的重点,事实上,sqe会觉得很冤枉,因为,一般来说,试产阶段的iue都是有technology在负责处理,sqe也可能做部分的support,但量产材料一定是sqe在复杂,所以出现这样的问题,sqe做的事情,说的难听点就是在帮人家擦屁股,处理不好,其他部门就觉得sqe能力不够,处理完美,觉得这是sqe份内之事情. )?(这只是个人感慨,请勿当经验交流
所以,从上面的分析,出于对品质的保证,或者说对自己的保护,sqe介入npi阶段是非常必要的. 哪如何介入及介入后如何处理呢?下面细谈. 驻厂管理是必须的. a.如何介入? 一般来说,sqe会和supplier的qa召开周会或者月会,在该会议上,可以将new product review列为review项目.但,大多数公司,npi主导者一定是technology department,有时候甚至等产品量产后才notice qe department,所以,第一步,一定要让supplier technology 部门只要有新产品导入就一定要知会到qe,但大部分公司的pe没有这样的习惯,因为他们的重点可能在技术的改善及提升.所以看似很简单的要求,但实际操作起来就不会那么顺利,所
以sqe就要主动去找supplier site manager去谈,只有大老板关注到这点,才有可行性.这是sqe需要support supplier qe的,记住,与supplier的关系不是指挥与被指挥的关系,win-win才是sqe的最终目的. b.介入后如何管理呢? 一,part failure history/specific failure data 1.review supplier new model status in quality meeting. 2.review fails record and corrective actions. 3.ec list for new product.(in npi period, according to customer requirement, maybe some have some ec) 4.co-work with supplier’s pe&me, planner, rd&ie departments, define the best parameter and define it into sop. 5.supplier ipqc should know these failures and audit proce according to them.二,transportation readine. 1.co-work with supplier related department or field standard, set up new model yield rate criteria. 2.5m checklist (manpower/machine/material/method/environment) 3.document ready.(qc-flow-chart,sop,sip and so on) 4.spc review (dimension, optical, soldering thickne) 5.golden sample management setup. 这些看起来很简单,但运行起来就是在考量sqe的技术含量和管理能力了. 比如,公司的采购一定需要supplier出新产品,但有些问题又没有解决杂办?? 一般我采取的方式有, 1.告之公司t部门,有些问题还没有解决,你要试用出问题,你去处理.—比较坑人. 2.视异常而言,如一些外观问题没有得到处理,要求supplier加强全检次数,把不良卡在supplier端. 如为function问题没有得到解决,就直接要求停止出货.(当然,这需要sqm的大力support,如自己的老板也同意出货,相信真出问题,老板也不会怪罪到你.) 3.在新产品还没达到量产的水准及iue没有完全得到解决时,如pur一定要使用,那就请pur出特采.(一般来说,特采是pur最不想的状况,因为责任别就在自己身上了). 有时,可能只有1pcs的不良,但此不良为zero defect items(ee material,一般为错件,漏件,极性错误),sqe就一定需要supplier找到问题跟源,在没有得到完全解决前,sqe就要拍板,不许出货. 接着来谈ec的管控. ec有二种,veca&vecn. 区别点在于veca为supplier 提供给公司,vecn为公司发给supplier. 之所以将ec拿出来细谈是因为对于电子产品,cycle time比较短,ec的变更就比较多,而且很大一部分异常就是因为ec没有得到很好的管控. 谈及这方面的管控,首先要和大家有个共识,ec的窗口一定是唯一的,一般来说公司的ec窗口有二个,sqm及t, supplier端为qe及t.但大家也应该清楚sqm与外界的接触更多点,所以,在我以前服务的公司,ec窗口为sqm,对应的supplier窗口为qe,只有在ec窗口确定的情况下,ec才能得到很好的管控,不然,我相信很多公司会为这花费很大的精力去处理ec问题. a.vecn 管控. 发起单位可能为t和sqm,一般来说, t主要复杂normal的变更,比如从下个rev,需要增加个零件,象这样类似的变更.有t部门撰写,有sqe知会supplier. sqe主要针对量产时候出现的一些iue,经过验证等,发现变更一些layer out能解决问题.这样类似的变更就有sqe主导. b.veca管控. 一定是supplier的qe提供给sqe. veca提出的items可能很多, 比如厂商一些重要制程参数的变更,生产地的变更,供应商的变更(second source导入).针对iue, supplier验证一些数据,可能变更某些参数能很好的提升良率. 等等类似的问题,supplier均需要提出veca. ps:veca/vecn items 有些公司会规定的很详细. 谈到这点,接着就是变更的时间点要在document写的很清楚,很大部分iue就是因为ec的时间点不明确导致异常的发生. vecn/veca 时间导入有两种, 1.running change.(常说的限时导入) 2.cut-in change. 这就需要和pur及supplier确认清楚product的数量,不然一定会出现问题. 备注:ec是一定需要用docement管控的,这对于sqm还是supplier都是一种保护. 4.gp 产品及其管制. 这点我就不细谈了,xrf等管理,更多的是iqc在执行, 主要的还是做到如上几点.a.gpa的文件规范系统. b.proce management system c.training d.supplier’s 外包管理 e.ec管制
f.检验和分析
另再在此show下本人sqe职场性格,相信也是优秀sqe必备之能力。 1.良好的沟通技巧,与production及工厂内相关部门建立良好的co-work方式,使事事半功倍。 2.解析问题能一针见血,通过qc 7大说法,spc管控等等分析技巧,review supplier 8d report. 3.处理事情及时,提高工厂甚至我们的客户的满意度。 4.熟悉iso9000/ts16949/iso14000等各要求,熟练使用在audit supplier。 5.本身逻辑思维性很强,能深辟的看待问题。 6.在供应商管理方面,强势的管理方式能很好的领导supplier 品质的提升,当然同时会吸纳supplier的一些宝贵的意见,使工厂和supplier double win,很强的独立处理事情能力。篇5:sqe资料--实际操作的精华总结
对于需要面试sqe和转sqe的朋友,这是经典合集总结 sqe工作范畴
sqe供货商管理工程师——(supplier quality engineer)
1、必须要有供应商跟踪的方式,质量问题独立处理的方法;
2、高级职位必须要有成本控制、质量控制管理的清晰思路与意识、坚持的原则底线;
3、供应商的内部品质管理流程、以及可能出现的问题对应方式。
4、稳定性的保证手段。
补充:
1、sqe负责保障供应商所供原材料的质量,在进料检验、生产过程检验、客户抱怨等,只要是由于供应商供货物料质量缺陷引发的,都要及时反馈供应商要求其改善;
2、sqe负责追踪确认供应商的改善报告(8d)及实施效果,必要时可进行现场审核检查;
3、sqe负责制定进货检验部门(iqc)的检验规范及检验计划,并适时对检验员进行培训指导;
4、sqe可以参与供应商初始样品的评估放行工作;
5、sqe每个月或每个季度,对现有供应商的质量状况进行统计评分,对评分较低的供应商提出限期改善要求;
6、sqe参与新供应商开发与审核,与采购、研发部门一起对新供应商进行考核打分,确定其是否可以成为合格供应商。 sqe供应商质量管理工程师
当前现实中sqe角色: ?消防队员 ?工程人员
?审核员、辅导员 ?协调员 ?检验员 ?项目工程师 ?供应商开发 ?医师
sqe当前在企业中的归属部门
质量部
采购部
供应链管理部
绩效管理部
独立
iqc 跨部门项目组
sqe的视角(关注点) 新产品项目
物料质量
客户
部门
关系
采购
技术/规格
质量体系
环保法令法规 sqe工作职责说明
1.推动供应商内部质量改善 1.1 推动供应商成立完善的质量保证小组. 1.2 供应商过程变更及材质变更的确认管控动作. 1.3 新材料及变更材料的管控. 1.4 推动厂商导入常用的质量工具,spc, 6sigma 等品管手法。 1.5 材料质量目标达成状况的改善及检讨。 1.6 不合格项目的改善确认动作。 1.7 材料异常的处理及成效的确认。 1.8 往来供应商的品质管控。 1.9 供应商风险评估。(资深sqe)
特别声明:供应商质量管理不是sqe一个群体就能够做好的事情 2.推行执行sqm的系统程序文件. 2.1 供应商的评监,择优选择厂商。(不一定所有的sqe都能够) 2.2 供应商的定期及特殊审核的执行。 2.3 供应商的辅导,提升质量。 2.4 执行供应商的奖罚措施。(不一定所有的sqe都能够) 2.5 建立完善规范的材料进料检验程序及qip。 2.6 外协厂商sop(作业指导书)、qc工程图的制订。 3.报表执行
3.1 每月的供应商等级评比。 3.2 每年的供应商等级评比。 3.3 供应商mbr, qbr 会议的召开。 3.4 8d report 的发出及时效管控及改善效果的跟进。 3.5 供应商质量月报,far 报表,信赖性报表的跟催及确认
扩展要求
专职审核员auditor 专职供应商辅导员(品质,交付,技术,运作---sta) jqe—连接供应商、本公司和客户端的所有交付环节
项目sqe—专门负责新产品项目中与供应商的协同开发
供应链协调员
优秀sqe胜任需要掌握的知识结构 4.1 qc七大手法; 4.2 8d report 编写; 4.3 辅导稽核技巧;
4.4 五大工具:msa、apqp、spc、fmea、ppap; msa:量测系统分析
apqp&cp:产品质量先期策划&控制计划 spc:统计制程控制 fmea:潜在失效模式 ppap:生产件批准程序
4.5 各类质量体系,如iso900
1、iso/ts169
49、iso1400
1、iso17025等; 4.6 专业、技术、公正(此点最为重要) 优秀sqe掌握的知识结构
新的环境下供应商管理角色越来越多地由专门化的职能人员来承担,
一个标志性的职能就是供应商质量管理工程师-sqe。sqe的应运而生已经有数年了,
目前企业对这一职位的需求在不断增加。但是对于这一个职位,往往是只有要求,没有规范,
靠sqe的自主经验以及和采购人员、产品品质人员的共同协调,很多sqe的上岗是由以往的工作转行,没有接受过系统培训。 sqe供应商质量管理流程
1、衡量供应商的质量
品质结果的衡量--产品质量的测定
品质过程能力指数ca、cp、cpk、ppk、cmk及其应用
品质测量的方法和程序
抽样计划 测量系统分析(msa)介绍
品质过程的衡量--质量保证体系的评审
基于流程的iso9000质量体系
产品质量先期策划apqp的概念及方法
评审的流程
2、分析供应商的质量
过程能力指数分析
基于供应链的流程分析
运用spc识别质量变异
运用fmea识别质量变异
3、提升供应商的质量
解决质量问题
建立组织架构和机制
质量问题改进小组—团队、任务、计划和授权
因果关系图
差错防止
实验设计法doe 预防质量问题
从营运体系的角度帮助供应商建立:
¨ 供应链上下游的技术和标准的一体化
¨ 共享的信息通道和作业流程
¨ 基于标准化的流程管理
从产品和工艺的角度帮助供应商建立:
¨ 产品的鲁棒设计
¨ 工艺的鲁棒设计
从组织和团队的角度帮助供应商建立:
¨ 以品质为核心的企业文化和激励制度
¨ 完善的绩效管理
¨ 有效的培训和员工发展
我们先来看一下下面的(de)英语格式对话: a:how do you do, penny? well, for this job, we need people to work hard.do you think youre suitable for this kind of job? b:oh, yes, i think so. a:ok.please talk something about yourself or introduce yourself. b:„„ a:早上好。我是lydia shen,这个公司的(de)经理。你叫什么名字。 b:你好,沈小姐。我叫penny。我是来应聘见习推销员的(de)。 a:你好,penny。对于这个工作,我们需要刻苦能干的(de)人,你觉得你能适应这样的(de)工作吗? b:恩,我想我能。 a:好吧。那就说说你的(de)情况吧,或者介绍一下自己。 b:„„
该介绍自己了,那么在面试中怎么做自我介绍呢?先来看一些背景知识: background: 面试时需要做自我介绍,这个时候不要细致地谈自己的(de)生活情况或者工作经验,而是要想方设法地让面试官对你有所了解,告诉他一些事情,这些事情应该使你在招聘过程中具有优势。或许你想选取一些有人情味的(de)故事讲给他听,但这么做,你要有把握与面试官的(de)想法吻合。或者可以概述一下最近你干的(de)工作和你正在申请的(de)工作有什么联系,有怎样的(de)帮助,以及你为什么要到这家公司工作等等。特别值得提的(de)是,要举例子,这样你的(de)回答才更具真实性,更容易被接受,才能给对方留下深刻的(de)印象。 或者当面试经理让你做自我介绍的(de)时候,你可以主动问一下对方想知道自己哪方面的(de)情况,这样也便于你的(de)回答更加有针对性。但是这种做法的(de)前提是你对面前的(de)这个面试官有一定的(de)把握,确信这样追问不会引起对方的(de)反感才行。
推荐第8篇:SQE工作总结
个人工作总结-2013年度
时光荏苒,公司又走过了一个辉煌年。回首2013年,我在公司及部门领导的指导带领下,在各位同事的协同下,基本完成了各项任务。主要工作有:
1.通过反复的调试比对超声波和热熔机,完成了B客户表贴式和嵌入式按钮线路板熔接保持力的问题,使量产产品的线路板保持力符合要求,解决了客户飞检投诉的问题。
2.优化并发布了供应商索赔制度,同时完成了供应商的索赔工作,全年索赔共计约合人民币21万多元。
3.参与新开发的北美项目的第一阶段任务,一周内指导供应商完成PPAP资料31份。4.从6月份起,给三家零库存供应商制定了改善辅导方案和计划,定期辅导,并定期监督检查完成状况。通过此次辅导,各家供应商在管理流程上有了初步改善,都已经建立了专职检验员制度。其中甲供应商连续三个月的FPY和OTD都已达标。
5.与技术工程师和采购同仁一起,对乙供应商(PCB板供应商)进行多次审核,帮助其查找问题,验证其纠正预防措施的有效性,减少生产对原材料的投诉,保证公司产品按时保质出货。
6.与质量工程师一起,通过对供应商的多次审核辅导,帮助他完成按钮组装的可量产化工作,完成了公司产品外包的工作。
此外,我还能积极参与公司组织的各项理论和专业知识培训,为后续工作能更好的开展打下铺垫。 过去的一年里虽然取得一些成绩,但也有需要提升的空间:
1.需要强化项目管理的知识,参与项目的过程中,要能更加积极主动。
2.对供应商管理方面,要想办法培养供应商解决问题的主动性和能动性,而不是我们催就动,我们不催就没有动静。
3.平时工作中,与供应商沟通时,要能控制自己的情绪,要通过交流让对方接受自己的观点,明白自己的要求。
2014年公司即将开发更多优秀的客户,展现在自己面前的将是一片任自己驰骋的沃土,但同时也感受到了沉甸甸的责任,在今后的工作和生活中我将继续努力学习,深入实践,不断提升自我。
XXX 2014-1-3
推荐第9篇:SQE Body of Knowledge
I.Management and Leadership
A.Quality Philosophies and Foundations Explain how modern quality has evolved from quality control through statistical proce control (SPC) to total quality management and
leadership principles (including Deming’s 14 points), and how quality has helped form various continuous improvement tools including lean, six sigma, theory of constraints, etc.(Remember)
B.The Quality Management System (QMS) 1.Strategic planning
Identify and define top management’s responsibility for the QMS, including establishing policies and objectives, setting
organization-wide goals, supporting quality initiatives, etc.(Apply) 2.Deployment techniques
Define, describe, and use various deployment tools in support of the QMS: benchmarking, stakeholder identification and analysis,
performance measurement tools, and project management tools such as PERT charts, Gantt charts, critical path method (CPM), resource allocation, etc.(Apply)
3.Quality information system (QIS)
Identify and define the basic elements of a QIS, including who will contribute data, the kind of data to be managed, who will
have acce to the data, the level of flexibility for future information needs, data analysis, etc.(Remember) C.ASQ Code of Ethics for Profeional Conduct
Determine appropriate behavior in situations requiring ethical decisions.(Evaluate)
D.Leadership Principles and TechniquesDescribe and apply various principles and techniques for developing and organizing teams and leading quality initiatives.(Analyze) E.Facilitation Principles and Techniques
Define and describe the facilitator’s role and responsibilities on a team.Define and apply various tools used with teams, including brainstorming, nominal group technique, conflict resolution, force-field analysis, etc.(Analyze)
F.Communication Skills
Describe and distinguish between various communication methods for delivering information and meages in a variety of situations acro all levels of the organization.(Analyze) G.Customer Relations
Define, apply, and analyze the results of customer relation measures such as quality function deployment (QFD), customer satisfaction surveys, etc.(Analyze) H.Supplier Management
Define, select, and apply various techniques including supplier qualification, certification, evaluation, ratings, performance improvement, etc.(Analyze) I.Barriers to Quality Improvement
Identify barriers to quality improvement, their causes and impact, and describe methods for overcoming them.(Analyze)
II.The Quality System
A.Elements of the Quality SystemDefine, describe, and interpret the basic elements of a quality system, including planning, control, and improvement, from product and
proce design through quality cost systems, audit programs, etc.(Evaluate)
B.Documentation of the Quality SystemIdentify and apply quality system documentation components, including quality policies, procedures to support the system, configuration
management and document control to manage work instructions, quality records, etc.(Apply)
C.Quality Standards and Other Guidelines
Define and distinguish between national and international standards and other requirements and guidelines, including the Malcolm Baldrige National Quality Award (MBNQA), and describe key points of the ISO 9000 series of standards and how they are used.[Note: Industry-specific standards will not be tested.] (Apply)
D.Quality Audits 1.Types of audits
Describe and distinguish between various types of quality audits such as product, proce, management (system), registration
(certification), compliance (regulatory), first, second, and third party, etc.(Apply) 2.Roles and responsibilities in audits
Identify and define roles and responsibilities for audit participants such as audit team (leader and members), client, auditee, etc.
(Understand)
3.Audit planning and implementation Describe and apply the steps of a quality audit, from the audit planning stage through conducting the audit, from the perspective
of an audit team member.(Apply)
4.Audit reporting and follow up Identify, describe, and apply the steps of audit reporting and follow up, including the need to verify corrective action.(Apply)
E.Cost of Quality (COQ)
Identify and apply COQ concepts, including cost categories, data collection methods and claification, and reporting and interpreting results.(Analyze)
F.Quality Training
Identify and define key elements of a training program, including conducting a needs analysis, developing curricula and materials, and determining the program’s effectivene.(Apply)
III.Product and Proce Design
A.Claification of Quality Characteristics
Define, interpret, and claify quality characteristics for new products and procees.[Note: The claification of product defects is covered in IV.B.3.] (Evaluate)
B.Design Inputs and Review
Identify sources of design inputs such as customer needs, regulatory requirements, etc.and how they translate into design concepts such as robust design, QFD, and Design for X (DFX, where X can mean six sigma (DFSS), manufacturability (DFM), cost (DFC), etc.).Identify and apply common elements of the design review proce, including roles and responsibilities of participants.(Analyze)
C.Technical Drawings and Specifications
Interpret technical drawings including characteristics such as views, title blocks, dimensioning, tolerancing, GD&T symbols, etc.Interpret specification requirements in relation to product and proce characteristics.(Evaluate)
D.Design Verification
Identify and apply various evaluations and tests to qualify and validate the design of new products and procees to ensure their fitne for use.(Evaluate)
E.Reliability and Maintainability
1.Predictive and preventive maintenance tools
Describe and apply these tools and techniques to maintain and improve proce and product reliability.(Analyze) 2.Reliability and maintainability indices
Review and analyze indices such as, MTTF, MTBF, MTTR, availability, failure rate, etc.(Analyze)
3.Bathtub curve Identify, define, and distinguish between the basic elements of the bathtub curve.(Analyze)
4.Reliability / Safety / Hazard Aement Tools
Define, construct, and interpret the results of failure mode and effects analysis (FMEA), failure mode, effects, and criticality analysis (FMECA), and fault tree analysis (FTA).(Analyze)
IV.Product and Proce Control
A.Tools
Define, identify, and apply product and proce control methods such as developing control plans, identifying critical control points, developing and validating work instructions, etc.(Analyze)
B.Material Control
1.Material identification, status, and traceability Define and distinguish these concepts, and describe methods for applying them in various situations.[Note: Product recall
procedures will not be tested.] (Analyze)
2.Material segregation Describe material segregation and its importance, and evaluate appropriate methods for applying it in various situations.
(Evaluate)
3.Claification of defects
Define, describe, and claify the seriousne of product and proce defects.(Evaluate)4.Material review board (MRB)
Identify the purpose and function of an MRB, and make appropriate disposition decisions in various situations.(Analyze)
C.Acceptance Sampling1.Sampling concepts
Define, describe, and apply the concepts of producer and consumer risk and related terms, including operating characteristic (OC)
curves, acceptable quality limit (AQL), lot tolerance percent defective (LTPD), average outgoing quality (AOQ), average outgoing quality limit (AOQL), etc.(Analyze)
2.Sampling standards and plans
Interpret and apply ANSI/ASQ Z1.4 and Z1.9 standards for attributes and variables sampling.Identify and distinguish between
single, double, multiple, sequential, and continuous sampling methods.Identify the characteristics of Dodge-Romig sampling tables and when they should be used.(Analyze)
3.Sample integrity
Identify the techniques for establishing and maintaining sample integrity.(Analyze) D.Measurement and Test
1.Measurement tools
Select and describe appropriate uses of inspection tools such as gage blocks, calipers, micrometers, optical comparators, etc.
(Analyze) 2.Destructive and nondestructive tests
Distinguish between destructive and nondestructive measurement test methods and apply them appropriately.(Analyze)
E.Metrology Identify, describe, and apply metrology techniques such as calibration systems, traceability to calibration standards, measurement error and
its sources, and control and maintenance of measurement standards and devices.(Analyze)
F.Measurement System Analysis (MSA) Calculate, analyze, and interpret repeatability and reproducibility (Gage R&R) studies, measurement correlation, capability, bias, linearity, etc.,
including both conventional and control chart methods.(Evaluate)
V.Continuous Improvement
A.Quality Control ToolsSelect, construct, apply, and interpret tools such as 1) flowcharts, 2) Pareto charts, 3) cause and effect diagrams, 4) control charts, 5) check
sheets, 6) scatter diagrams, and 7) histograms.(Analyze)
B.Quality Management and Planning Tools Select, construct, apply, and interpret tools such as 1) affinity diagrams, 2) tree diagrams, 3) proce decision program charts (PDPC), 4)
matrix diagrams, 5) interrelationship digraphs, 6) prioritization matrices, and 7) activity network diagrams.(Analyze)
C.Continuous Improvement Techniques
Define, describe, and distinguish between various continuous improvement models: total quality management (TQM), kaizen, plan-do-check-act (PDCA), six sigma, theory of constraints (TOC), lean, etc.(Analyze)
D.Corrective Action
Identify, describe, and apply elements of the corrective action proce including problem identification, failure analysis, root cause analysis, problem correction, recurrence control, verification of effectivene, etc.(Evaluate)
E.Preventive Action
Identify, describe, and apply various preventive action tools such as error-proofing/poka-yoke, robust design, etc., and analyze their effectivene.(Evaluate)
VI.Quantitative Methods and Tools
A.Collecting and Summarizing Data
1.Types of data Define, claify, and compare discrete (attributes) and continuous (variables) data.(Apply)
2.Measurement scales
Define, describe, and use nominal, ordinal, interval, and ratio scales.(Apply) 3.Data collection methods
Describe various methods for collecting data, including tally or check sheets, data coding, automatic gaging, etc., and identify
their strengths and weaknees.(Apply) 4.Data accuracy
Describe the characteristics or properties of data (e.g., source/resource iues, flexibility, versatility, etc.) and various types of
data errors or poor quality such as low accuracy, inconsistency, interpretation of data values, and redundancy.Identify factors
that can influence data accuracy, and apply techniques for error detection and correction.(Apply)5.Descriptive statistics
Describe, calculate, and interpret measures of central tendency and dispersion (central limit theorem), and construct and
interpret frequency distributions including simple, categorical, grouped, ungrouped, and cumulative.(Evaluate) 6.Graphical methods for depicting relationships
Construct, apply, and interpret diagrams and charts such as stem-and-leaf plots, box-and-whisker plots, etc.[Note: Run charts
and scatter diagrams are covered in V.A.] (Analyze)
7.Graphical methods for depicting distributions Construct, apply, and interpret diagrams such as normal probability plots, Weibull plots, etc.[Note: Histograms are covered in
V.A.] (Analyze)
B.Quantitative Concepts
C.
D.
E.
F.
G.
H.Terminology Define and apply quantitative terms, including population, parameter, sample, statistic, random sampling, expected value, etc.(Analyze) 2.Drawing statistical conclusions Distinguish between numeric and analytical studies.Ae the validity of statistical conclusions by analyzing the aumptions used and the robustne of the technique used.(Evaluate) 3.Probability terms and concepts Describe and apply concepts such as independence, mutually exclusive, multiplication rules, complementary probability, joint occurrence of events, etc.(Apply) Probability Distributions1.Continuous distributions Define and distinguish between these distributions: normal, uniform, bivariate normal, exponential, lognormal, Weibull, chi square, Student’s t, F, etc.(Analyze) 2.Discrete distributions Define and distinguish between these distributions: binomial, Poion, hypergeometric, multinomial, etc.(Analyze) Statistical Decision-Making1.Point estimates and confidence intervalsDefine, describe, and ae the efficiency and bias of estimators.Calculate and interpret standard error, tolerance intervals, and confidence intervals.(Evaluate) 2.Hypothesis testingDefine, interpret, and apply hypothesis tests for means, variances, and proportions.Apply and interpret the concepts of significance level, power, type I and type II errors.Define and distinguish between statistical and practical significance.(Evaluate) 3.Paired-comparison tests Define and use paired-comparison (parametric) hypothesis tests, and interpret the results.(Apply) 4.Goodne-of-fit tests Define and use chi square and other goodne-of-fit tests, and interpret the results.(Apply) 5.Analysis of variance (ANOVA) Define and use ANOVAs and interpret the results.(Analyze) 6.Contingency tables Define, construct, and use contingency tables to evaluate statistical significance.(Analyze) Relationships Between Variables1.Linear regreion Calculate the regreion equation for simple regreions and least squares estimates.Construct and interpret hypothesis tests for regreion statistics.Use regreion models for estimation and prediction, and analyze the uncertainty in the estimate.[Note: Non-linear models and parameters will not be tested.] (Analyze)2.Simple linear correlation Calculate the correlation coefficient and its confidence interval, and construct and interpret a hypothesis test for correlation statistics.[Note: Serial correlation will not be tested.] (Analyze)3.Time-series analysis Define, describe, and use time-series analysis including moving average, and interpret time-series graphs to identify trends and seasonal or cyclical variation.(Analyze)Statistical Proce Control (SPC)1.Objectives and benefits Identify and explain objectives and benefits of SPC such as aeing proce performance.(Understand)2.Common and special causes Describe, identify, and distinguish between these types of causes.(Analyze)3.Selection of variable Identify and select characteristics for monitoring by control chart.(Analyze)4.Rational subgrouping Define and apply the principles of rational subgrouping.(Apply)5.Control charts Identify, select, construct, and use various control charts, including -R, -s, individuals and moving range (ImR or XmR), moving average and moving range (MamR), p, np, c, u, and CUSUM charts.(Analyze)6.Control chart analysis Read and interpret control charts, use rules for determining statistical control.(Evaluate)7.PRE-control charts Define and describe how these charts differ from other control charts and how they should be used.(Apply)8.Short-run SPC Identify, define, and use short-run SPC rules.(Apply)Proce and Performance Capability1.Proce capability studies Define, describe, calculate, and use proce capability studies, including identifying characteristics, specifications, and tolerances, developing sampling plans for such studies, establishing statistical control, etc.(Analyze)2.Proce performance vs.specifications Distinguish between natural proce limits and specification limits, and calculate percent defective.(Analyze)3.Proce capability indices Define, select, and calculate Cp, Cpk, Cpm, and Cr, and evaluate proce capability.(Evaluate)4.Proce performance indices Define, select, and calculate Pp and Ppk and evaluate proce performance.(Evaluate)Design and Analysis of Experiments
1.Terminology
Define terms such as dependent and independent variables, factors, levels, response, treatment, error, and replication.(Understand)2.Planning and organizing experiments
Define, describe, and apply the basic elements of designed experiments, including determining the experiment objective, selecting factors, responses, and measurement methods, choosing the appropriate design, etc.(Analyze)3.Design principles
Define and apply the principles of power and sample size, balance, replication, order, efficiency, randomization, blocking, interaction, and confounding.(Apply)
4.One-factor experiments Construct one-factor experiments such as completely randomized, randomized block, and Latin square designs, and use
computational and graphical methods to analyze the significance of results.(Analyze)
5.Full-factorial experiments Construct full-factorial designs and use computational and graphical methods to analyze the significance of results.(Analyze)
6.Two-level fractional factorial experiments
Construct two-level fractional factorial designs (including Taguchi designs) and apply computational and graphical methods to analyze the significance of results.(Analyze)1.
推荐第10篇:SQE月度工作总结
个人工作总结-2013年度
时光荏苒,公司又走过了一个辉煌年。回首2013年,我在公司及部门领导的指导带领下,在各位同事的协同下,基本完成了各项任务。主要工作有: 1.通过反复的调试比对超声波和热熔机,完成了b客户表贴式和嵌入式按钮线路板熔接保持力的问题,使量产产品的线路板保持力符合要求,解决了客户飞检投诉的问题。 2.优化并发布了供应商索赔制度,同时完成了供应商的索赔工作,全年索赔共计约合人民币21万多元。
3.参与新开发的北美项目的第一阶段任务,一周内指导供应商完成ppap资料31份。 4.从6月份起,给三家零库存供应商制定了改善辅导方案和计划,定期辅导,并定期监督检查完成状况。通过此次辅导,各家供应商在管理流程上有了初步改善,都已经建立了专职检验员制度。其中甲供应商连续三个月的fpy和otd都已达标。 5.与技术工程师和采购同仁一起,对乙供应商(pcb板供应商)进行多次审核,帮助其查找问题,验证其纠正预防措施的有效性,减少生产对原材料的投诉,保证公司产品按时保质出货。
6.与质量工程师一起,通过对供应商的多次审核辅导,帮助他完成按钮组装的可量产化工作,完成了公司产品外包的工作。
此外,我还能积极参与公司组织的各项理论和专业知识培训,为后续工作能更好的开展打下铺垫。 过去的一年里虽然取得一些成绩,但也有需要提升的空间: 1.需要强化项目管理的知识,参与项目的过程中,要能更加积极主动。 2.对供应商管理方面,要想办法培养供应商解决问题的主动性和能动性,而不是我们催就动,我们不催就没有动静。 3.平时工作中,与供应商沟通时,要能控制自己的情绪,要通过交流让对方接受自己的观点,明白自己的要求。 2014年公司即将开发更多优秀的客户,展现在自己面前的将是一片任自己驰骋的沃土,但同时也感受到了沉甸甸的责任,在今后的工作和生活中我将继续努力学习,深入实践,不断提升自我。 xxx 2014-1-3篇二:sqe 工作经验总结
本人2003年毕业后,鬼使神差般地进入了quality这个领域,一直从事sqe工作也有近4年的光景,今天把自己的一些做事方式,态度及sqe的职责show出来,供同行和外行加以褒贬,让自己吸取更多的精华,剔除糟粕. 备注,我所负责的材料主要是ee(pcb/fpc/pcba/fpca,rlc 及connector),所以下面很多的工作经验之谈是站在ee这个面展开的,不过,相信对于负责其他材料的同仁还是有一定的帮助的,毕竟sqe是技术及管理共存的一个职业. 当然,在此show出这么多个人经验之谈,也不乏有推荐自己之意,我相信我绝对是适合的人选。
一,绩效--就是通常说的kpi (key performance indictor) 但事实上,个人觉得真正衡量sqe的ability应该是supplier 8d回复的时效性及有效性,之所以这样说,是因为材料的特殊性,相信sqe同仁有同样的感触. 当然,有些材料本身supplier的sense或者其proce已经达到很高的水准,其品质面本来就很少出状况,来衡量管理这样材料的sqe performance,真的很难定夺,也许就是production的dppm trend chart 及service(training and so on). 二,职责(responsibility) 围绕保证品质来料这目的,sqe应负起如下的责任, 1.对供应商进行例行的绩效评估和audit. 2.品质监督和异常协辅
3.npi(new product 导入)/ecn 变更时,供应尚制程及产品的确认,cip的改善. 4.gp 产品及其管制. 针对以上四点,小弟我浅谈下我的经验,供各大侠指导. 1.对供应商进行例行的绩效评估和audit. 1.1导入新厂商阶段,一般有pur/rd/sqm/esh部门共同参与,sqe此阶段需要做的是让supplier提供供应商调查报告及工厂内部组织架构等等大项,此阶段主导者应该是pur. 1.2对供应商进行qpa(quality proce audit),这需要依据具体的产品来衡量,但不外乎receiving inspection, warehouse, mrb, production line, rework proce, oqc and packing&store, record and so on. 机, 3.machine maintained 4.measurement/tool 精确度
料, 5.区分隔离 6.保存期及保存方式
法, 7.traceability&identification 8.spc, fai checklist 环, 9.esh 10.温湿度 qpa的frequency,目前很多公司已经没有强制的定义,只要公司一出现比较大的case, sqe就驻厂,针对相关站别进行audit.事实上,这样做起来的确很有效果,sqe第一时间内了解到
不良品,然后又第一时间内去supplier端去audit相关proce,相信很大程度上能很快解决问题,使公司顺利生产,让supplier及时改善. 1.3对供应商qsa(quality system audit),通过对supplier系统面的audit,是希望指出supplier在整个面上的不足,一般来说,sqe主要audit的item如下, a.document management b.供应商之supplier的管理. c.product identification & traceability d.proce control e.检查和测试管理. f.calibration g.nonconforming product control. h.handling, package, storage and delivery i.record—这一项适合所有的audit items. 当然事实上,sqe重点放在上面items外,其实还是有些需要audit的项目,比如quality system, contact review, 甚至设计管理. 一般来说,qsa一年一次. 事实上,真正反映supplier performace的是qbr 会议,参与部门有pur, technology and sqm,分数比例一般为pur-- 35%, t-- 30% sqm -- 35%. 主要出发点 pur—delivery/cost/service t—technology share / service sqm—quality iue/ service ps: sales 人员注意,客户的3个主要对外窗口都很注重service. 这样的qbr meeting一般有sqm主导,当然supplier参加的窗口也应该是对应的sales/t/qa(cs) 部门. 个人认为后续product的竞争力应在品质上,所以站在sqe的角度上,我是希望sqm的比重可以适当加重. 1.4gpa(green product audit),目前很大部分公司已将此audit纳入qsa中,在这我就不细谈了.但重要的还是离不开如下6点: a.gpa的文件规范系统. b.proce management system c.training d.supplier’s 外包管理 e.ec管制(后面会细谈) f.检验和分析. 2.品质监督和异常协辅
个人很在乎的是能够很好的push supplier建立fmea部门,这样做的好处如下: 对应supplier a.但有异常发生时,能很快的组织起分析小组,尽快找到问题点,预防问题的进一步扩大, b.很快的处理异常,以达到最低限度的减少损失, c.buglist,作为经验的积累,方便后续品质的追踪. d.能很大程度上消除公司”踢皮球”的坏习惯. 对于公司(customer) a.defect sample分析的时效性得以保证.(8d cycle times) b.sqe可以第一时间内,review8d report,可以很快的找到对应分析窗口. 诚然,fmea小组的建立不能很快的让supplier看到自己利益的增长,但我敢保证fmea团队绝对是supplier和customer 很好的沟通桥梁.由于fmea团队的重要性,一般我都是直接找supplier site manager来谈,因为fmea小组需要很强的技术分析能力,很好的工厂执行力及分析defect的仪器设备, 这些都需要site manager的大力support. 相信优秀的sqe能明白我的想法也希望能给相关同仁一些感触. 对于异常协辅,也许很多行外人觉得sqe的技术能力真的有那么专业吗?能协辅supplier进行改善? 诚然sqe是技术和管理共存的一个特殊的岗位,相信没有一定的技术能力是很难让supplier诚服的,也的确sqe没有supplier的pe在技术上的专长,但一般来讲,公司现在很少找单一source supplier, 所以sqe有更多的机会去借鉴不同的经验,各公司一定都有他的长处,我已经习惯将各厂商长处相联结,同时也习惯让supplier习惯我的管理方式.之所以说sqe能给supplier异常辅导,是因为各岗位人员看待问题不一样,pe可能想到了改善的方向,但出与cost的考虑,还是无法进行有效的动作.甚至一些品质iue的轻微改善,一些自工具的设计有可能,等等类似的问题. 总之,sqe会取长补短,集合自己的经验能有效的给出supplier改善的方向. 3.npi(new product 导入)/ecn 变更时,供应尚制程及产品的确认,cip的改善. 先来谈下npi的管控.相信大部分的sqe有这样的体会,公司出现异常后,在最后root cause出来后才发现,原来这样的问题在试产阶段就已经存在,但种种原因,在没有得到解决前,此model已经进入量产阶段,这样以来,sqe就成为大家指责的重点,事实上,sqe会觉得很冤枉,因为,一般来说,试产阶段的iue都是有technology在负责处理,sqe也可能做部分的support,但量产材料一定是sqe在复杂,所以出现这样的问题,sqe做的事情,说的难听点就是在帮人家擦屁股,处理不好,其他部门就觉得sqe能力不够,处理完美,觉得这是sqe份内之事情. )?(这只是个人感慨,请勿当经验交流
所以,从上面的分析,出于对品质的保证,或者说对自己的保护,sqe介入npi阶段是非常必要的. 哪如何介入及介入后如何处理呢?下面细谈. 驻厂管理是必须的. a.如何介入? 一般来说,sqe会和supplier的qa召开周会或者月会,在该会议上,可以将new product review列为review项目.但,大多数公司,npi主导者一定是technology department,有时候甚至等产品量产后才notice qe department,所以,第一步,一定要让supplier technology 部门只要有新产品导入就一定要知会到qe,但大部分公司的pe没有这样的习惯,因为他们的重点可能在技术的改善及提升.所以看似很简单的要求,但实际操作起来就不会那么顺利,所
以sqe就要主动去找supplier site manager去谈,只有大老板关注到这点,才有可行性.这是sqe需要support supplier qe的,记住,与supplier的关系不是指挥与被指挥的关系,win-win才是sqe的最终目的. b.介入后如何管理呢? 一,part failure history/specific failure data 1.review supplier new model status in quality meeting. 2.review fails record and corrective actions. 3.ec list for new product.(in npi period, according to customer requirement, maybe some have some ec) 4.co-work with supplier’s pe&me, planner, rd&ie departments, define the best parameter and define it into sop. 5.supplier ipqc should know these failures and audit proce according to them.二,transportation readine. 1.co-work with supplier related department or field standard, set up new model yield rate criteria. 2.5m checklist (manpower/machine/material/method/environment) 3.document ready.(qc-flow-chart,sop,sip and so on) 4.spc review (dimension, optical, soldering thickne) 5.golden sample management setup. 这些看起来很简单,但运行起来就是在考量sqe的技术含量和管理能力了. 比如,公司的采购一定需要supplier出新产品,但有些问题又没有解决杂办?? 一般我采取的方式有, 1.告之公司t部门,有些问题还没有解决,你要试用出问题,你去处理.—比较坑人. 2.视异常而言,如一些外观问题没有得到处理,要求supplier加强全检次数,把不良卡在supplier端. 如为function问题没有得到解决,就直接要求停止出货.(当然,这需要sqm的大力support,如自己的老板也同意出货,相信真出问题,老板也不会怪罪到你.) 3.在新产品还没达到量产的水准及iue没有完全得到解决时,如pur一定要使用,那就请pur出特采.(一般来说,特采是pur最不想的状况,因为责任别就在自己身上了). 有时,可能只有1pcs的不良,但此不良为zero defect items(ee material,一般为错件,漏件,极性错误),sqe就一定需要supplier找到问题跟源,在没有得到完全解决前,sqe就要拍板,不许出货. 接着来谈ec的管控. ec有二种,veca&vecn. 区别点在于veca为supplier 提供给公司,vecn为公司发给supplier. 之所以将ec拿出来细谈是因为对于电子产品,cycle time比较短,ec的变更就比较多,而且很大一部分异常就是因为ec没有得到很好的管控. 谈及这方面的管控,首先要和大家有个共识,ec的窗口一定是唯一的,一般来说公司的ec窗口有二个,sqm及t, supplier端为qe及t.但大家也应该清楚sqm与外界的接触更多点,所以,在我以前服务的公司,ec窗口为sqm,对应的supplier窗口为qe,只有在ec窗口确定的情况下,ec才能得到很好的管控,不然,我相信很多公司会为这花费很大的精力去处理ec问题. a.vecn 管控. 发起单位可能为t和sqm,一般来说, t主要复杂normal的变更,比如从下个rev,需要增加个零件,象这样类似的变更.有t部门撰写,有sqe知会supplier. sqe主要针对量产时候出现的一些iue,经过验证等,发现变更一些layer out能解决问题.这样类似的变更就有sqe主导. b.veca管控. 一定是supplier的qe提供给sqe. veca提出的items可能很多, 比如厂商一些重要制程参数的变更,生产地的变更,供应商的变更(second source导入).针对iue, supplier验证一些数据,可能变更某些参数能很好的提升良率. 等等类似的问题,supplier均需要提出veca. ps:veca/vecn items 有些公司会规定的很详细. 谈到这点,接着就是变更的时间点要在document写的很清楚,很大部分iue就是因为ec的时间点不明确导致异常的发生. vecn/veca 时间导入有两种, 1.running change.(常说的限时导入) 2.cut-in change. 这就需要和pur及supplier确认清楚product的数量,不然一定会出现问题. 备注:ec是一定需要用docement管控的,这对于sqm还是supplier都是一种保护. 4.gp 产品及其管制. 这点我就不细谈了,xrf等管理,更多的是iqc在执行, 主要的还是做到如上几点.a.gpa的文件规范系统. b.proce management system c.training d.supplier’s 外包管理 e.ec管制
f.检验和分析
另再在此show下本人sqe职场性格,相信也是优秀sqe必备之能力。 1.良好的沟通技巧,与production及工厂内相关部门建立良好的co-work方式,使事事半功倍。 2.解析问题能一针见血,通过qc 7大说法,spc管控等等分析技巧,review supplier 8d report. 3.处理事情及时,提高工厂甚至我们的客户的满意度。 4.熟悉iso9000/ts16949/iso14000等各要求,熟练使用在audit supplier。 5.本身逻辑思维性很强,能深辟的看待问题。 6.在供应商管理方面,强势的管理方式能很好的领导supplier 品质的提升,当然同时会吸纳supplier的一些宝贵的意见,使工厂和supplier double win,很强的独立处理事情能力。篇三:三年质量工程师工作总结2012年4月22日0243 工作总结
尊敬南方天合底盘系统有限公司的领导:
您好!非常感谢公司领导能给派遣自己到南京分公司宝学习和实践的机会,时间总是不等你,一年的委派期马上就要结束了(2011年5月10日——2012年5月10 日)。 本人大学毕业工作快三年了(2009年6月-2012年6月) 2009年6月22日—2009年7月22日质量部实习; 2009年7月22日-2011年5月11日制动盘业务单元的qe工作; 2011年5月10日-2012年5月10日派遣南京分公司管理质量 三年的工作实践中学习经历概述,主要包含五个方面:1,离开学校,坚持质量信仰;2,公司面试实习,理想和信仰让自己充满激情,脚踏实地的学习;3制动盘qe工作2年,打下坚实的质量管理工具使用基础;4南京1年,再接再厉,全面了解trw工厂质量管理活动规律(cmpa,pma).5制定自己未来三年计划。
第一,离开学校,坚持质量信仰;
毕业于重庆理工大学汽车学院工业工程专业,专业下设《质量管理与产品可靠性》课程,第一次接触并了解质量管理发展历史和一些理论,如,抽样样本量,小概率事件,标准差,质量环,控制图,6sigma等等专业名称,所有的理论都让自己好奇,产生兴趣去学习和研究质量管理工作在企业的运行规律,为了了解质量活动的运行规律,到民营企业去实习,实习期间了解到企业的质量管理活动,以及汽车行业强制执行国际质量活动标准ts16949,在校论文答辩期间,大量的翻
阅质量管理的文献和论文,并完成自己的毕业论文《如何在民营企业中有效的推行ts16949_以惠正机械有限公司为例》,对质量的浓厚兴趣和热爱让我渴望更加深刻的学习他,研究其运行规律,但是只是从理论上了解是远远不够的。在马克思理论中明确;“实践是检验真理的最好方法”;在古语中有:“天行健,君子以自强不息,地势坤,君子以厚德载物”就是一个道理,任何事物都有其本身运行的规律,人只有不断努力学习,实践才能了解和掌握其客观规律,总结理论为人们所用。自己本来是农村出来的小孩,比别人差了几代人,别人在走的时候,自己就得快跑,慢慢的自己喜欢奔跑的感觉,学习和努力让感觉自己时刻都在奔跑的感觉,所以喜欢质量,了解质量,研究质量,努力去实践质量管理活动,现在物欲横流的社会,诱惑和利益很多,选择一种信仰,并坚持这份信仰,那么就会一直在奔跑。希望通过自己努力学习和研究质量管理活动运行规律,让其为我所用,为重庆民营企业的发展献一份力,让重庆的摩托城变成想美国底特律一样的汽车城。怀揣空空的理想是不行的,任何理论都必须要实践来检验,实践是真理最好的检验。怀着对质量的热爱,和夸张的理想,自己做出了人生的第一个选择,一,选择从事质量管理工作;二,选择努力进入南方天合底盘系统有限公司,一个双500强的企业,其中外方为美资公司trw ,100年一直是给福特配套,而福特,通用质量管理活动规律的归纳就是现在汽车行业强制推行的ts16949,能够进入这样的企业,就可以了解和学习实践100多年总结下来的质量管理活动的规律是自己的荣幸。
第二,司面试实习,理想和信仰让自己充满激情,脚踏实地的学习; 首先,公司面试,理想和信仰让自己充满激情;
面试两个问题:1“为什么一个干了十年铸造的老工程师我没有要,而选择一个刚刚毕业的大学生”;2“为什么这么多大学生中我要选择你这个呢”两个问题回答:“一个老工程师是不是您需要的,您一眼都能够看出来,而刚刚毕业的大学生就想毛坯一样,能否被加工成合格品,就要看他自己努力和学习。 “很多的大学生毕业就等于失业,而我不是,我知道自己喜欢什么,要得到什么”就这样我获得了一个月实习的机会,当时心喜若狂。
其次,公司实习,让自己脚踏实地学习;
实习一个月期间 秉着 “天将降大任于世人也,必先苦其心志,牢其胫骨,饿其体肤”!不怕苦不累的精神,自己需要投入120%热情和精力来学习,例如首对公司主要运用产品和生产线进行了解,识别,记录;对cd345钳装配线现场的s.o.s与控制计划相比对;跟着李川老师学习,机加质量问题处理,控制图对过程能力识别;跟彭渝老师学习,了解总泵机加和装配,c307制动盘机加线。跟周兴伟老师学习,了解公司的基本运营,质量手册和各个过程的作业指导书;对现场11系统进行初步的学习,并发现质量控制的体系;跟卿明老师学习,学习6-sigma,及其了解他在实际应用的作用; 利用晚上的时间学习质量五大工具,11系统,sps精益生产手册。
一个月结束了:一份耕耘,一份收获。在收获知识的同时,也收获自己人生发展路上最好的老师,细心讲解工艺的老师傅;和耐心指
导传授知识的同事;更理解质量管理活动的重要意义,长期不断发展,新理论不断更新。(解决问题的成本远远的大于问题预防的成本;任何忽略作业指导书上要求的做法,都有可能给公司带来巨大的损失)从而让自己更加坚定自己的信仰是正确的。
第三,制动盘qe工作2年,打下坚实的质量管理工具使用基础; 这两年整个公司质量管理活动正处在高潮的阶段,为获得福特的q1而努力,制动盘业务单元是当时一个重点,制定现场质量管理活动提升计划,过程能力提升计划,整个项目历时一年之久,大大小小事情做了很多,主要有以下四个方面;1,改善制动盘计数型不良品隔离箱,对不良品进行编号,实物和不良品审理单一一对应,严格控制不良品的转移活动。2,引进马波斯先制动盘测量系统,缩小测量变差,提高sc项目cpk过程能力,并定期完成msa,形成趋势图,向客户展示质量管理活动的表现状态。3,执行k表cpk监控系统,形成趋势图,定期向客户展示其过程能力。4,引进spc监控系统,及时识别过程变差原因,进行有效预防的管理活动,并有效进行刀具管理。为获得q1的质量管理活动经历一年之久,争强客户的信任度,并获的福特马自达j68,j53等一系列的新项目。这个也有整个制动盘团队共同努力一份辛苦。质量的五大工具,新/旧七大质量工具,质量活动pdca管理规律,问题管理程序,机加检查技术,3l5w,8d等等质量工具反复实践,并使用质量工具在与团队成员和客户进行有效沟通,为自己打下坚实质量工具使坚实的基础。
第四,南京1年,再接再厉,全面了解trw工厂质量管理活动规律(cmpa,pma)
南京工厂质量管理活动也不在仅仅是一个业务单元那么单一,而是相当于一个公司的质量管理活动的管理范畴,更有机会接触到trw对一个分公司经营运行,质量管理活动标准要求。对自己来说是一个难得的学习和实践的质量管理活动规律的机会。怀揣着自己的信仰,来到人生底不熟的南京,远离家乡,奉献青春,无怨无悔!!2011年5月10日达到南京到2012年5月10 日,整整一年的时间,过完春,夏,秋,冬四季;这一年,大大小小事还是做了不少,主要有以下4个方面:1.客户交流,完成转产的工程变更;2,质量检测量具,检测设备,检测技术全面学习和转移;3,了解sqe,cqe,qe工作,构建质量管理框架;4,了解审核。 首先:客户交流,质量体系建设与审核。
南京工厂建立,是公司三年来同时发生工程变更产品最多,任务量最多的一次质量管理活动,包括长安项目10项,马自达项目8项。而有计划的与客户沟通,完成整个变更管理活动,获得客户批准psw成为南京团队的首要任务。通过努力与公司各个部门有效沟通,制定有效的客户交流计划,最终通过团队努力,按照trw变更管理活动要求,完成长安全部项目,马自达7项产品场地变更工程变更活动,并获得客户批准。
其次:质量检测量具,检测设备,检测技术全面学习和转移。 南京团队成立只有12人,分管不同领域,而检测量具,检测篇四:2011sqe年度个人总结
年度工作总结
时间流逝,岁月如梭,2011年已悄然走过。在这一年中,本人在公司和部门领导的指导下、在各位同事的协助下,基本完成了年初计划中所定的各项工作。回想这一年来,本人服从领导,努力工作,严格要求自己,不断提高,自我加压,保证工作质量,严把质量关。保质保量地完成了领导交办的各项任务,主要做了以下一些工作:
一、新品开发
1、完成##2011款项目开发,共涉及12个零件的开发,均满足开发节点及质量要求。
2、完成##一阶段性能提升项目开发工作,共涉及5个零件的开发,均满足开发节点及质量要求,
3、新##项目开发任务,包括多媒体系统灯具等关键项目目前正在进行中,在tr阶段开始积极参与技术方案的确定并积极参与联合设计方案的确定,如尾灯led布局,车厢阅读灯,多媒体系统人机互动界面等,有效降低投产后发生质量风险与用户抱怨的可能,预计2012年可完成开发任务。
4、完成总装信息联络任务,减少总装抱怨。
5、组织sqe落实top10年度控制任务,实际退出6家, 2家正在办理中,剩余两家。
6、共完成ppap认可70余件
二、现场问题、质量改进、售后等问题处理
1、处理电器现场问题90多起,主要涉及装配干涉、生产缺货、产品质量等诸多问题,均在第一时间解决现场问题,做到了无停线,零抱怨,零遗留。
2、走访售后服务站9次,验证和了解了前期质量问题的改进情况,并找到了数码播放器(死机问题),cd机(改装导致进水)异常索赔等故障发生原因,为后续质量改进提供了有效和及时第一手资料,促进了质量改进项目的完成。
3、共完成8项公司质量改进项目,其中中央控制盒改进,雨刮器改进等诸多项目均得到质量部,售后和客户的共同认可。
三、其他方面
1、积极参加各种群众性质量管理活动(如:合理化建议活动等)。
2、认真学习理论知识,学习各种方法技巧,参加各种专业培训,如:pcpa、apqp、tr、pcpa等,在后续工作中将进一步加强专业性工作的学习
3、对项目管理的认识有了一定的提升,在2012年工作中要加强项目管理的计划性和及时性跟踪,以及相关部门的协调工作。
四、几点感想和体会
在这一年时间里,部门领导和科长对我关怀备至,时常给我鼓励和帮助。使我感到:
1、工作要一丝不苟
工作时一定要一丝不苟,仔细认真。不能出错,平时要经常反思一下自己的工作,以确定自己的工作万无一失。工作之余还要经常总结工作教训,不断提高工作效率。在这一年时间里,同事们严谨、认真的工作作风给我留下了深刻的印象,我也从他们身上学到了很多自己缺少的东西。
2、工作要勤于思考 sqe岗位的日常工作比较繁琐,而且比较枯燥,这就需要我们一定要勤于思考,改进工作方法,提高工作效率,减少工作时间。
3、工作要不断学习
要不断的丰富自己的专业知识和专业技能,这会使我的工作更加得心应手。一个人要在自己的职位上有所作为,就必须要熟知专业知识,并在不断的学习中拓宽自己的知识面。 2011年的结束,2012年的到来,是开端也是结束,展现在自己面前的是一片任自己驰骋的沃土,也感受到了沉甸甸的责任,在今后的工作和生活中我将继续努力学习,刻苦钻研,深入实践,不断提升自我。
吴发强 2011年12月22日篇五:sqe工作经验心得大集合 sqe工作经验谈
一个sqe前辈的经验之谈!(转发) kobe_zou 发表于: 2009-5-25 17:53 来源: 半导体技术天地
以下是一个sqe前辈的经验之谈,希望对大家有所帮助!!! sqe 工作经验浅谈!转发
作者:jevonsge
----------------- 本人2003年毕业后,鬼使神差般地进入了quality这个领域,一直从事sqe工作也有近4年的光景,今天把自己的一些做事方式,态度及sqe的职责show出来,供同行和外行加以褒贬,让自己吸取更多的精华,剔除糟粕. 备注,我所负责的材料主要是ee(pcb/fpc/pcba/fpca,rlc 及connector),所以下面很多的工作经验之谈是站在ee这个面展开的,不过,相信对于负责其他材料的同仁还是有一定的帮助的,毕竟sqe是技术及管理共存的一个职业. 当然,在此show出这么多个人经验之谈,也不乏有推荐自己之意,我相信我绝对是适合的人选。
一,绩效--就是通常说的kpi (key performance indictor) 当然,有些材料本身supplier的sense或者其proce已经达到很高的水准,其品质面本来就很少出状况,来衡量管理这样材料的sqe performance,真的很难定夺,也许就是production的dppm trend chart 及service(training and so on). 二,职责(responsibility) 围绕保证品质来料这目的,sqe应负起如下的责任, 1.对供应商进行例行的绩效评估和audit. 2.品质监督和异常协辅
3.npi(new product 导入)/ecn 变更时,供应尚制程及产品的确认,cip的改善. 4.gp 产品及其管制. 针对以上四点,小弟我浅谈下我的经验,供各大侠指导. 1.对供应商进行例行的绩效评估和audit. 1.1导入新厂商阶段,一般有pur/rd/sqm/esh部门共同参与,sqe此阶段需要做的是让supplier提供供应商调查报告及工厂内部组织架构等等大项,此阶段主导者应该是pur. 1.2对供应商进行qpa(quality proce audit),这需要依据具体的产品来衡量,但不外乎receiving inspection, warehouse, mrb, production line, rework proce, oqc and packing&store, record and so on. 针对这些站别,总结起来,按照人,机,料,法,环五项,集合公司的qpa checklist进行audit. 机, 3.machine maintained 4.measurement/tool 精确度
料, 5.区分隔离 6.保存期及保存方式
法, 7.traceability&identification 8.spc, fai checklist 环, 9.esh 10.温湿度 qpa的frequency,目前很多公司已经没有强制的定义,只要公司一出现比较大的case, sqe就驻厂,针对相关站别进行audit.事实上,这样做起来的确很有效果,sqe第一时间内了解到不良品,然后又第一时间内去supplier端去audit相关proce,相信很大程度上能很快解决问题,使公司顺利生产,让supplier及时改善. 1.3对供应商qsa(quality system audit),通过对supplier系统面的audit,是希望指出supplier在整个面上的不足,一般来说,sqe主要audit的item如下, a.document management b.供应商之supplier的管理. c.product identification & traceability d.proce control e.检查和测试管理. f.calibration g.nonconforming product control. h.handling, package, storage and delivery i.record—这一项适合所有的audit items. 当然事实上,sqe重点放在上面items外,其实还是有些需要audit的项目,比如quality system, contact review, 甚至设计管理. 一般来说,qsa一年一次. 事实上,真正反映supplier performace的是qbr 会议,参与部门有pur, technology and sqm,分数比例一般为pur-- 35%, t-- 30% sqm -- 35%. 主要出发点 pur—delivery/cost/service t—technology share / service sqm—quality iue/ service ps: sales 人员注意,客户的3个主要对外窗口都很注重service. 这样的qbr meeting一般有sqm主导,当然supplier参加的窗口也应该是对应的sales/t/qa(cs) 部门. 个人认为后续product的竞争力应在品质上,所以站在sqe的角度上,我是希望sqm的比重可以适当加重. 1.4gpa(green product audit),目前很大部分公司已将此audit纳入qsa中,在这我就不细谈了.但重要的还是离不开如下6点: a.gpa的文件规范系统. b.proce management system c.training d.supplier’s 外包管理 e.ec管制(后面会细谈) f.检验和分析. 2.品质监督和异常协辅
对于品质监督,我很是赞同baseline management,通过驻厂的方式,及时有效的audit厂商各站别的问题,同时给予厂商qa部门的大力support,提升其执行力. 个人很在乎的是能够很好的push supplier建立fmea部门,这样做的好处如下: 对应supplier a.但有异常发生时,能很快的组织起分析小组,尽快找到问题点,预防问题的进一步扩大, b.很快的处理异常,以达到最低限度的减少损失, c.buglist,作为经验的积累,方便后续品质的追踪. d.能很大程度上消除公司”踢皮球”的坏习惯. 对于公司(customer) a.defect sample分析的时效性得以保证.(8d cycle times) b.sqe可以第一时间内,review8d report,可以很快的找到对应分析窗口. 诚然,fmea小组的建立不能很快的让supplier看到自己利益的增长,但我敢保证fmea团队绝对是supplier和customer 很好的沟通桥梁.由于fmea团队的重要性,一般我都是直接找supplier site manager来谈,因为fmea小组需要很强的技术分析能力,很好的工厂执行力及分析defect的仪器设备, 这些都需要site manager的大力support. 相信优秀的sqe能明白我的想法也希望能给相关同仁一些感触. 对于异常协辅,也许很多行外人觉得sqe的技术能力真的有那么专业吗?能协辅supplier进行改善? 诚然sqe是技术和管理共存的一个特殊的岗位,相信没有一定的技术能力是很难让supplier诚服的,也的确sqe没有supplier的pe在技术上的专长,但一般来讲,公司现在很少找单一source supplier, 所以sqe有更多的机会去借鉴不同的经验,各公司一定都有他的长处,我已经习惯将各厂商长处相联结,同时也习惯让supplier习惯我的管理方式.之所以说sqe能给supplier异常辅导,是因为各岗位人员看待问题不一样,pe可能想到了改善的方向,但出与cost的考虑,还是无法进行有效的动作.甚至一些品质iue的轻微改善,一些自工具的设计有可能,等等类似的问题. 总之,sqe会取长补短,集合自己的经验能有效的给出supplier改善的方向. 3.npi(new product 导入)/ecn 变更时,供应尚制程及产品的确认,cip的改善. 先来谈下npi的管控.相信大部分的sqe有这样的体会,公司出现异常后,在最后root cause出来后才发现,原来这样的问题在试产阶段就已经存在,但种种原因,在没有得到解决前,此model已经进入量产阶段,这样以来,sqe就成为大家指责的重点,事实上,sqe会觉得很冤枉,因为,一般来说,试产阶段的iue都是有technology在负责处理,sqe也可能做部分的support,但量产材料一定是sqe在复杂,所以出现这样的问题,sqe做的事情,说的难听点就是在帮人家擦屁股,处理不好,其他部门就觉得sqe能力不够,处理完美,觉得这是sqe份内之事情. (这只是个人感慨,请勿当经验交流?) 所以,从上面的分析,出于对品质的保证,或者说对自己的保护,sqe介入npi阶段是非常必要的. 哪如何介入及介入后如何处理呢?下面细谈. 驻厂管理是必须的. a.如何介入? 一般来说,sqe会和supplier的qa召开周会或者月会,在该会议上,可以将new product review列为review项目.但,大多数公司,npi主导者一定是technology department,有时候甚至等产品量产后才notice qe department,所以,第一步,一定要让supplier technology 部门只要有新产品导入就一定要知会到qe,但大部分公司的pe没有这样的习惯,因为他们的重点可能在技术的改善及提升.所以看似很简单的要求,但实际操作起来就不会那么顺利,所以sqe就要主动去找supplier site manager去谈,只有大老板关注到这点,才有可行性. 这是sqe需要support supplier qe的,记住,与supplier的关系不是指挥与被指挥的关系,win-win才是sqe的最终目的.b.介入后如何管理呢? 一,part failure history/specific failure data 1.review supplier new model status in quality meeting. 2.review fails record and corrective actions. 3.ec list for new product.(in npi period, according to customer requirement, maybe some have some ec) 4.co-work with supplier’s pe&me, planner, rd&ie departments, define the best parameter and define it into sop. 5.supplier ipqc should know these failures and audit proce according to them. 二,transportation readine. 1.co-work with supplier related department or field standard, set up new model yield rate criteria. 2.5m checklist (manpower/machine/material/method/environment) 3.document ready.(qc-flow-chart,sop,sip and so on) 4.spc review (dimension, optical, soldering thickne) 5.golden sample management setup. 这些看起来很简单,但运行起来就是在考量sqe的技术含量和管理能力了. 比如,公司的采购一定需要supplier出新产品,但有些问题又没有解决杂办?? 一般我采取的方式有, 1.告之公司t部门,有些问题还没有解决,你要试用出问题,你去处理.—比较坑人. 2.视异常而言,如一些外观问题没有得到处理,要求supplier加强全检次数,把不良卡在supplier端. 如为function问题没有得到解决,就直接要求停止出货.(当然,这需要sqm的大力support,如自己的老板也同意出货,相信真出问题,老板也不会怪罪到你.) 3.在新产品还没达到量产的水准及iue没有完全得到解决时,如pur一定要使用,那就请pur出特采.(一般来说,特采是pur最不想的状况,因为责任别就在自己身上了). 有时,可能只有1pcs的不良,但此不良为zero defect items(ee material,一般为错件,漏件,极性错误),sqe就一定需要supplier找到问题跟源,在没有得到完全解决前,sqe就要拍板,不许出货. 接着来谈ec的管控. ec有二种,veca&vecn. 区别点在于veca为supplier 提供给公司,vecn为公司发给supplier. 之所以将ec拿出来细谈是因为对于电子产品,cycle time比较短,ec的变更就比较多,而且很大一部分异常就是因为ec没有得到很好的管控. 谈及这方面的管控,首先要和大家有个共识,ec的窗口一定是唯一的,一般来说公司的ec窗口有二个,sqm及t, supplier端为qe及t.但大家也应该清楚sqm与外界的接触更多点,所以,在我以前服务的公司,ec窗口为sqm,对应的supplier窗口为qe,只有在ec窗口确定的情况下,ec才能得到很好的管控,不然,我相信很多公司会为这花费很大的精力去处理ec问题. a.vecn 管控. 发起单位可能为t和sqm,一般来说, t主要复杂normal的变更,比如从下个rev,需要增加个零件,象这样类似的变更.有t部门撰写,有sqe知会supplier. sqe主要针对量产时候出现的一些iue,经过验证等,发现变更一些layer out能解决问题.这样类似的变更就有sqe主导.b.veca管控. 一定是supplier的qe提供给sqe. veca提出的items可能很多, 比如厂商一些重要制程参数的变更,生产地的变更,供应商的变更(second source导入). 针对iue, supplier验证一些数据,可能变更某些参数能很好的提升良率. 等等类似的问题,supplier均需要提出veca. ps:veca/vecn items 有些公司会规定的很详细. 谈到这点,接着就是变更的时间点要在document写的很清楚,很大部分iue就是因为ec的时间点不明确导致异常的发生. vecn/veca 时间导入有两种, 1.running change.(常说的限时导入) 2.cut-in change. 这就需要和pur及supplier确认清楚product的数量,不然一定会出现问题. 备注:ec是一定需要用docement管控的,这对于sqm还是supplier都是一种保护. 4.gp 产品及其管制. 这点我就不细谈了,xrf等管理,更多的是iqc在执行, 主要的还是做到如上几点. a.gpa的文件规范系统. b.proce management system c.training d.supplier’s 外包管理 e.ec管制
f.检验和分析
另再在此show下本人sqe职场性格,相信也是优秀sqe必备之能力。 1.良好的沟通技巧,与production及工厂内相关部门建立良好的co-work方式,使事事半功倍。 2.解析问题能一针见血,通过qc 7大说法,spc管控等等分析技巧,review supplier 8d report. 3.处理事情及时,提高工厂甚至我们的客户的满意度。 4.熟悉iso9000/ts16949/iso14000等各要求,熟练使用在audit supplier。 5.本身逻辑思维性很强,能深辟的看待问题。 6.在供应商管理方面,强势的管理方式能很好的领导supplier 品质的提升,当然同时会吸纳supplier的一些宝贵的意见,使工厂和supplier doube win,很强的独立处理事情能力。
发布: 2008-1-26 16:40 | 作者: weifenglin | 来源: 6sq.net | 查看: 783次
从事sqe工作已有两年,一套工作经验渐渐成形.在此拙作出来,以让sqe新人参考,让行内高手指教. 一.绩效﹕ sqe 的使命﹐是通过对供货商的品质管理﹐以保证来料的品质。因此﹐vlrr是sqe 绩效的主要反映。
二.职责﹕
围绕保证来料品质这目的﹐sqe 应负起以下四点职责﹔ 1.对供应商例行品质绩效评估与稽核; 2.品质监督与异常辅导; 3 .new/ec产品导入时的供货商制程与产品确认和持续改善(cip); 4.gp产品及其制程管制等; 针对此四点职责﹐以下是我的一点经验﹕ 1.对供应商例行品质绩效评估与稽核; 1.1导入新厂商: 一般内容有:对新供货商作总况调查﹑qsa(qaulity system audit), qpa(quality proce audit)﹑签定品质合约; 1.2供应商例行品质绩效评, 每月评分与制程稽核qpa; 每月评分三要素tqr: technology.quality.response; 每月一评﹐评分结果分a/b/c/d等级。 1.3 制程稽核(qpa)每季度末由sqe制定下季度的稽核计划. 制程稽核方式﹕针对不同的站别, including receiving inspection﹑warehouse﹑mrb﹑p/l﹑secondary operations﹑oqc﹑packing and stock and so on. 总结起来﹐重点项目由 人﹑机﹑料﹑法﹑环五项构成﹐具体事项按公司qpa list点检。
机﹕3 设备/校验。4 治具/测量; 料﹕5.物料分区.6 保存期/保存方式; 法﹕7 可追溯性; 8.spc, 自检, clca检讨; 环﹕9 安全防护.10 湿/温度; qsa 通常每年一评。
第11篇:SQE英文求职信
sqe的个人简历模板
姓 名: 莫先生 性 别: 男
婚姻状况: 已婚 民 族: 汉族
户 籍: 广东-深圳 年 龄: 32 现所在地: 广东-深圳 身 高: 170cm 希望地区: 广东-中山
希望岗位: 质量/安全管理类-质量管理/测试经理/主管(qa/qc经理) 质量/安全管理类-质量管理/测试工程师(qa/qc工程师) 质量/安全管理类-sqe/供应商质量工程师
寻求职位:
待遇要求: 15000元/月 可面议
最快到岗: 01个月之内
教育经历
1998-08 ~ 2002-07 西安电子科技大学 微电子技术 本科 1995-09 ~ 1998-07 广东省英德市英德中学 理科 高中
培训经历
2009-12 ~ 2009-12 誉杰咨询 iso9001 内审员 iso9001 内审员 2008-02 ~ 2008-07 扬智嘉信咨询 6-sigma 黑带 6-sigma 黑带
工作经验至今10年2月工作经验,曾在4家公司工作 **公司 (2011-01 ~ 至今)
公司性质: 跨国公司(集团) 行业类别: 通讯、电信、网络设备
担任职位: sqe 岗位类别: sqe/供应商质量工程师
工作描述: 负责供应商审核/管理及跟进新产品开发。 1.负责对高端激光黑白打印机的新产品开发及量产跟进。 2.制定并维护工厂验货流程及检验方式。 3.对组装厂进行定期的审查以确保工厂的运行能满足利盟的要求。 4.跟进并协调主要的零部件供应商解决日常出现的主要品质问题以保证生产和出货顺畅。 2011-01~2012-08 跟进单/多功能激光黑白打印机的新产品开发及量产,项目分别在2012年6月及8月进入量产。 个人简历表格下载 2011-12~至今 跟进特种单功能激光黑白打印机的新产品开发。
在每一个新产品的开发阶段,负责制定品质计划及测试计划,并跟进试产中发现的问题点,推动本公司开发部解决设计问题,提出组装方面的改善建议。制定了代工厂的验货流程及检验方式,协调工厂制定内部的抽样流程。
离职原因: 公司经济不景气 **公司 (2009-07 ~ 2010-12)
公司性质: 跨国公司(集团) 行业类别: 其他
担任职位: 高级质量工程师 岗位类别: sqe/供应商质量工程师
工作描述: 负责供应商的质量管理和新产品的日常质量管理。 1.组织新供应商审核工作,与相关人员共同选择、评估新供应商。 2.分析供应商不合格品产生的原因,跟踪验证供应商整改行动。 3.统计&监控供应商的质量绩效,推动供应商持续改善。 4.组织供应商的年度审核工作,跟踪、验证供应商的整改行动。 5.管理dtp实验室(原材料检验及贴合产品测试) 6.负责dtp新产品跟进及日常的质量工作。 主要工作成绩: 1.成功辅导本地供应商达到总部的技术要求并通过宝洁qake审查,完成原材料的本地化。 2.成功把qc的工作重点从成品测试转到制程监控。 3.成功把墨西哥进口cpp薄膜的合格率从原有的70%提高到90%。
离职原因: 个人发展及家庭原因 **公司 (2004-10 ~ 2009-04)
公司性质: 股份制企业 行业类别: 电子、微电子技术、集成电路
担任职位: 岗位类别: 质量管理/测试经理/主管(qa/qc经理) 工作描述:
一、2007-06~2009-04 作为qc部主管工程师(兼esd管理)。 负责smt、cob、focus及成品组装车间的ipqc/oqc管理: 1.制定ipqc oqc kpi和年度预算并每月回顾对应的情况及进行相应的改善。 2.总结每月的品质状况及kpi的差距,召开品质月会,推动生产、工程进行相应的改善。 3.招聘检验人员、工程师等相关人员并指导其进行检验和品质跟进,工作绩效监督及考核。
4.制定或者修订相应的流程文件,规范相关的生产、品质工作。 5.制定并推行qc内部的培训考核及内审机制,提高效率及避免漏失。 6.组织内部的持续品质改善活动 7.跟进新产品的试产和量产全过程的品质活动,跟进重大、重要产品的突发品质事件。 8.处理客户投诉及回复相应的8d改善对策。 9.应对客户的pvi/oba/fai检验和相关的审核。 10.协调出货检验出现的问题,灵活处理保证出货的品质和顺畅。
作为qc部主管工程师,管理一个93人的ipqc/oqc团队,包含9名工程师。 1.在2008年降低smt不良率,从原有的~4000ppm降低到目前低于2500ppm的水平。 2.飞赴北京索尼爱立信,与客户进行了良好的沟通,确保出货的顺畅。 3.改善了ti的品质,从2005年开始保持出货品质dppm最低(ti反馈的数据,与另两家供应商相比),并最终在2008年拿回失去十年之久的“ti优秀供应商”称号。
二、2005-03~2007-06 作为qc部工程师(兼esd工程师)。
负责成品组装车间的ipqc、oqc项目的跟进和管理: 1.跟进新产品试产和量产,提供新产品试产报告,反馈并敦促rnd进行改善。
期间成功跟进gnn / 森海塞尔 (蓝牙耳机)和leapfrog(电机玩具)新客户的新产品试产到量产的导入,同期也成功跟进sony (ps2/ps3游戏机配件)和索尼爱立信(手机配件和蓝牙耳机)新产品试产到量产的导入。 2.编制oqc检验指导书,与pe/qa进行fmea及pmp(qc plan)的制作和审核。 3.编定ipqc重点稽核事项
4.培训及考核检验员和生产部外观检查员,制作gr&r。 5.检验设备的gr&r和cpk计算。 6.制程稽核
7.4m变更跟进及产线品质异常的跟进处理 8.oqc不良品/客退品的分析处理及相关客户投诉的对策回复(8d)
三、2004-10~2005-03 作为ie部esd工程师
导入esd管理系统,及新生产大楼的esd规划与防护。 1.组织相关部门,成立esd小组推动esd工作。 2.建立esd管理系统和制定相关的控制文件 3.培训esd知识 4.评估及购买相关的esd测试设备,防护用具,辅材等等 5.解决生产线的esd问题。期间解决了摩托罗拉客户的摄像头模块在测试区域esd损伤问题。
6.解答客户审核中提到的esd相关问题。
离职原因: 经济危机
**公司 (2002-07 ~ 2004-10)
公司性质: 外资企业 行业类别: 计算机硬件
担任职位: esd 岗位类别:
工作描述: 负责esd研究、esd材料仪器的评估与新产品试产线的esd控制。 1.在实验室研究新一代tmr磁头的esd机理,提出管控办法。 2.评估esd防护材料和相关的仪器 3.解决试产线新产品的esd问题 4.培训助理工程师
5.esd标准和文件的制定
在美国esd协会发表论文“breakdown behavior of tmr head in esd transients”--2004 symposium program seion 5b 在日本rcj协会发表论文“effect of gmr undercoat thickne on dielectric breakdown voltage”
离职原因: 个人发展
技能专长
专业职称:
计算机水平: 中级
计算机详细技能: 熟练使用办公软件及minitab 技能专长: 1.熟悉相关标准(iso***ts16949/icti等)。 2.熟悉电子行业的注塑/smt/cob/成品组装工艺(如蓝牙耳机,摄像头,手机配件等)熟悉相关的产品(成品及pcba)检验标准、抽样技巧如(ansi/asq z1.4、gb2828) 3.6-sigma 黑带,熟悉各项品质工具的使用如fmea,qc7大手法、hoq/msa等等 4.积极主动,较强的领导力及团队建设能力,能够管理将近百人的团队 5.较强的品质意识,良好的数据及逻辑推理能力和解决问题的能力 6.良好的英语、粤语和普通话
语言能力
普通话: 流利 粤语: 流利
英语水平: cet-4 英语: 熟练
求职意向
发展方向: 意向1:发展来料检验及供应商管理方面的能力,完善品质管理技能,为进一步提升自我打好基础。
意向2:提高客户服务及出货管理方面的技能,完善品质管理技能,为进一步提升自我打好基础。
自身情况
自我评价: 1.熟悉相关标准(iso***ts16949/icti等)。 2.熟悉电子行业的注塑/smt/cob/成品组装工艺(如蓝牙耳机,摄像头,手机配件等)熟悉相关的产品(成品及pcba)检验标准、抽样技巧如(ansi/asq z1.4、gb2828) 3.6-sigma 黑带,熟悉各项品质工具的使用如fmea,qc7大手法、hoq/msa等等 4.积极主动,较强的领导力及团队建设能力,能够管理将近百人的团队 5.较强的品质意识,良好的数据及逻辑推理能力和解决问题的能力 6.良好的英语、粤语和普通话篇2:sqe主管的个人简历模板 sqe主管的个人简历模板
姓 名: 徐先生 性 别: 男
婚姻状况: 未婚 民 族: 汉族
户 籍: 广东 年 龄: 32 现所在地: 广东-东莞 身 高: 167cm 希望地区: 广东
希望岗位: 质量/安全管理类-质量管理/测试经理/主管(qa/qc经理) 质量/安全管理类-供应商管理
质量/安全管理类-sqe/供应商质量工程师
教育经历 2002-09 ~ 2005-07 广东交通职业技术学院 机械电子工程/机电一体化 大专 培训经历
2009-02 ~ 2009-02 sony iso spc 以及品质相关 2008-04 ~ 2008-04 sony gp培训 2003-03 ~ 2003-06 广东交通职业技术学院 cad 中级证书 **公司 (2009-10 ~ 至今)
公司性质: 外资企业 行业类别: 电子、微电子技术、集成电路
担任职位: sqe主管 岗位类别: 质量管理/测试经理/主管(qa/qc经理) 工作描述: 1.配合采购开发新供应商,并对新厂商进行品质系统调查,评估. 2.对合格供应商进行稽核与辅导计划,并实施,跟进完成改善. 3.进料品质管理,厂商重大品质异常改善对策的检讨及跟进. 4.跟进处理因原材料引起客诉和产线投诉. 5.对检查员作出培训提高其检查技巧. 6.品质月报周报的作成. 7.对检查员的日常工作作出管理,确保检查工作能准时完成,确保所有的来料品质得到控制. 8.上司交代的临时任务. **公司 (2007-05 ~ 2009-09)
公司性质: 外资企业 行业类别: 电子、微电子技术、集成电路
担任职位: iqc工程师 岗位类别: 供应商管理
工作描述: a:持续跟进供应商的纠正措施并确认其效果. b:新供应商稽核和评估. c:帮助供应商提高其制程及质量体系能力. d:工程变更确认(工厂,原材料,生产工具和制程) e:给予生产工厂支持以防止来料不良. f:通过相应的行动去提高供应商的能力. g:新机种的导入,有关来料不良解析. h:特采处理.简历
i:sip等品质文书的作成. j:相关品质会议的召开. **公司 (2004-12 ~ 2007-04) 公司性质: 外资企业 行业类别: 家具、家电、工艺品、玩具
担任职位: sqe工程师 岗位类别: sqe/供应商质量工程师
工作描述: a:持续跟进供应商的纠正措施并确认其效果. b:新供应商稽核和评估. c:帮助供应商提高其制程及质量体系能力. d:sip作成. e:给予生产工厂支持以防止来料不良. f:通过相应的行动去提高供应商的能力. 技能专长
专业职称:
计算机水平: 初级
计算机详细技能: 熟练操作cad, pro-2001以及办公室软件. 技能专长: 1.熟悉iqc以及供应商管理. 2.能熟练运用相关的品质工具(spc, pdca, 8d等) 3.品质不良分析. 4.熟悉塑胶,pcb, 五金,包材等物料. 5.熟悉iso9000体系以及sony gp体系. 6.制作sip. 7.供应商审查. 8.新供应商审查. 9.4m变更及特采处理. 语言能力
普通话: 粤语: 英语水平:
英语: 良好
求职意向
发展方向: 希望凭借我多年在iqc和供应链的工作经验以及对品质体系的熟悉能给贵司的发展贡献我的力量,在帮贵司发展的同时我自己也在工作中有进一步的突破与发展。 其他要求:
自身情况
自我评价: 1.良好的英语能力. 2.熟悉不同的生产制程. 3.熟悉质量工具和质量体系(spc,8d,fmea,iso9000& sony-gp) 4.基本了解不同的生产工艺(塑料,五金,pcb以及光学材料) 5.良好的沟通能力和技巧.篇3:sqe工程师的个人简历模板 sqe工程师的个人简历模板
姓 名: 黄先生 性 别: 男
婚姻状况: 未婚 民 族: 汉族
户 籍: 广西-玉林 年 龄: 29 现所在地: 广东-深圳 身 高: 177cm 希望地区: 广东-深圳、广东-东莞、广东 希望岗位: 经营/管理类-部门主管
质量/安全管理类-sqe/供应商质量工程师
质量/安全管理类-供应商管理 质量/安全管理类-质量管理/验货员(qa/qc) 寻求职位: sqe工程师、品质主管
待遇要求: 6500元/月 可面议
最快到岗: 半个月之内
教育经历
2002-09 ~ 2006-07 广西玉林师范学院 电子信息科学与技术 本科
培训经历 2007-06 ~ 2007-08 东莞乐诗电子塑胶有限公司 iso系列/tqm/qc七大手法
工作经验至今6年9月工作经验,曾在3家公司工作 **公司 (2009-01 ~ 至今)
公司性质: 外资企业 行业类别: 电子、微电子技术、集成电路
担任职位: sqe工程师 岗位类别: sqe/供应商质量工程师
工作描述: 负责对供应商的评审管理(选定,审核,绩效管理);跟进处理来料质量问题,分析处理产线来料异常,辅助供应商进行问题改善。
负责产线剩料的确认和控制。
负责编写检查指示,制作相关测试架。给予iqc检验员提供相关的技术指导和培训。 离职原因: 寻求更好的发展
**公司 (2007-10 ~ 2008-12)
公司性质: 外资企业 行业类别: 家具、家电、工艺品、玩具
担任职位: 品质工程师/采购跟单 岗位类别: qa/品质工程师
工作描述: 1.负责跟进产品的品质,处理产线异常,客诉和供应商的品质问题,陪同客人(如美泰,沃尔玛,intermatic,game,善龙等)验货以及对工厂的稽核.同时主导开展产品过程审核以及产品审核。另外编写产品检验规格,品质计划,不合格品处理办法,协助编写dfame/pfame同时给iqc,ipqc,oqc,lqc提供相关技术指导和培训。 2.转入采购部后,负责供应商的选定,评审,下单,协助iqc处理来料品质问题,协调跟进公司生产与物料交期。
离职原因: 公司倒闭
**公司 (2005-12 ~ 2007-10)
公司性质: 外资企业 行业类别: 电子、微电子技术、集成电路
担任职位: qe工程师 岗位类别: 电子工程师/技术员
工作描述: 负责qa,qc(包括iqc)的技术指导,培训。分析处理来料,生产过程中以及出货验货中出现的异常情况,客户投诉,编写品质计划,质量标准和作业指导。另外负责实验室对产品的可靠性等的相关测试,参与公司iso内审以及陪同客人对公司进行检验,审核。
离职原因: 拖欠工资
技能专长
专业职称:
计算机水平: 全国计算机等级考试二级
计算机详细技能: 熟练使用excel,word等办公软件以及erp/mrp系统。
技能专长: 1.熟悉电子物料的采购流程,有较好的成本控制意识。能够对供应商进行有效管理。
2.熟悉各种电子原件,塑胶五金件,特别是连接器以及电声产品;能熟练操作各种测量工具。
3.熟悉产品的检验和品质控制流程,fmea,cp,qc作业指导书的的编写;能独立处理日常品质问题/客诉;能组织、带领iqc/lqc/ipqc/oqc对产品质量的有效控制;熟悉iso系列,ts16949,en71,astm-f963,rohs,ul,熟练使用新/旧qc七大手法,spc,了解nf,fcc,ce,weee;个人简历模板 4.喜欢篮球和书法,在学校一直担任学生会主席,能组织和参与各活动,工作后经常协助人事部组织公司的各种文艺活动!
语言能力
普通话: 流利 粤语: 流利
英语水平: 口语一般
英语: 良好
求职意向
发展方向: 希望能得到一个更好的发展,学习的空间。更好的为公司发展,做出本人应有的贡献。
其他要求:
自身情况
自我评价: 为人诚恳,活泼开朗,有较强的适应能力,沟通能力,事情处理能力和领导能力,能在压力下工作。篇4:英文个人简历及英文求职信模板 april 13, 2000 p.o.box 36 tsinghua university beijing, china 100084 dear sir/madam: your advertisement for a network maintenance engineer in the april 10 student daily interested me because the position that you described sounds exactly like the kind of job i am seeking. with many thanks, wang lin april 13, 2000 room 212 building 343 tsinghua university, beijing 100084 ms.yang: i will be in the shanghai area the week of april 16.please call me at 136001216901 to arrange a convenient time when we may meet to further discu my background in relation to your needs.i look forward to meeting you then. sincerely, cheng dan april 13, 2000 p.o.box 36 biit university beijing, china 100000 dear sir/madam: 昁now new technologies that show instant profit, such as cad/cam. this is but a brief summary of my abilities.and there is much, much more to share.i feel i have strong marketable skills in which you would be interested.please contact me if you would like to hear and see more. with many thanks, huang yan april 13, 2000 p.o.box 36 biit university beijing, china 100000 dear sir/madam: please consider me for your sales management program.my background is one of selling ideas, concepts and programs, and of motivating myself and others to realize our potential. attitudes predict behavior - or so goes the saying in sales.if this holds true, i am sure to be as succeful in sales management as i am in my college endeavors.my unceasing optimism, self-determination and ability to set goals have allowed me to achieve academic and personal objectives. because of my can do attitude, sales will provide the challenge and opportunity to continue my succeful history of setting and achieving goals.please allow me the opportunity to elaborate on how my background predicts sales succe.i guarantee youll be providing your corporation with an outstanding sales management.thank you for your attention. sincerely, deng yun april 13, 2000 p.o.box 36 biit university beijing, china 100000 dear sir/madam: 旸eveloped a tool to track and forecast price,quantity,and revenue, which enables client to monitor busine performance 旾mplemented a customized end-to-end testing proce and sql database sincerely, gu bin篇5:sqe个人简历模板 sqe个人简历模板
[日期:2011-04-22] 来源: 作者: [字体:大 中 小] 姓名:个人简历网
目前所在: 天河区
户口所在: 海南
婚姻状况: 未婚
培训认证: 未参加
诚信徽章: 未申请
人才测评: 未测评
我的特长:
求职意向
人才类型: 普通求职
质量检验员/测试员:检验员,技工:售后服务,金属制应聘职位: 品:质量管理
工作年限:3 职 称: 无职称
求职类型: 全职 可到职日期: 随时
月薪要求: 面议 希望工作地区:广 州,深圳, 工作经历
洛阳中信重型机械 起止年月:2010-08 ~ 2009-07 公司性质: 国有企业 所属行业:机械/机电/设备/重工
担任职位: sqe 工作描述: 主要工作内容: 负责供应商的品质管理,出现的质量问题进行分析,找原因,要求供应商改善,并确认改善对策实施的有效性,对供应商的年度审核以及对供应商的辅导及品质改善提升,在公司内部主要起到质检员的作用检验相关产品质量参数,熟练使用相关检验工具。
第12篇:SQE经典案例
先介绍一下我写这个mail的背景。我所负责的大部分供应商都是多品种,小批量的性质,民营企业很多。现在供应商本身迫于成本压力,利润降低,会拼命接很多订单(不同客户的),所以他们内部也是超负荷的运行。这一点从和我们对应窗口的人员负责的工作之多就可以看出几分。对应人员经常离职,人员频繁流动也是一个很大的问题。对于对应人员压力大,我曾写过一封mail,当时引起了供应商和我们高层经理的轰动。后来我们总经理把厂商的总经理叫过来,针对于我mail提到的相关问题,做了一个Action Plan,最重要的是把我们对应QE原来负责18个客户,变成了负责3个客户,其中主要负责我们,呵呵,算是解决了困扰我的一个很大问题
这里和大家分享一下,当然也非常欢迎各位拍砖,或给出自己的建议,谢谢。
Subject: 问题背后的问题 A经理,
今日到贵司拜访,和B工交流了不少,当时还想再找你再沟通一下,不巧你在开会。推动贵司品质工作已经持续了将近一年,个人感觉作为一个SQE,如果不致力于挖掘问题背后的问题,我想以贵司目前的状态,我个人感觉要明显提高我司来料质量水平,可能至少还需要三年。长久以来,其实一直也想把自己的一些想法总结成文字,于是干脆就在mail里汇总一下我个人的一些浅见,希望贵司能有所借鉴:
如下按重要程度依次排序 1)贵司品质部门的人力资源问题。
目前B工给我的感觉就是有心无力。总体来说,贵司目前能够维持的水准就是还算及时的处理我司发现的不良品,比如一些返工和挑选等。基本上对于我反馈的不良信息,还是可以反馈到内部提醒相关人员注意。其他更深一步改善和预防动作,除了我司客户投诉的严重问题,其他问题基本上是很难得到及时,彻底的执行了。 目前B工的说法是他需应对18个客户,但是自己仍然可以把60~70%的时间放在我们公司身上。(我对此还是有点怀疑),我个人的建议是尽量能为我司设置一个专职的QE,我司产品现在又有80多种转到贵司(其他供应商转过来的),再加上55个新品,后续将逐渐扩大的国外直供零件项目(贵司目前做了一些了吧)。我司多品种小批量高质量要求这个特点,我司希望贵司报价时能够把这个QE的质量成本算进去,一个工程师的工资一个月没有多少,但是他能够带给贵司和我司的品质成本的降低将是非常巨大的,望考量。
无论怎么说,作为贵司的品质经理,如果无法合理的分配管理品质部门的人力资源问题,整个部门就会陷入两个恶性循环的怪圈。不仅整个公司品质水平会恶性循环,人员离职率也会恶性循环。贵司整体品质水平的基础相对来说是比较差的,之前贵司企业规模不大的时候并没有打好基础,现在工厂发展过快,规模过大导致管理无法跟上,在目前比较差的水平上想要做绝地反击,在人力资源跟不上的情况下几乎是不可能的。按照一般的通用的说法,制造行业来讲,一个公司品质人员的配比应该是6~12%的话,那么500人的工厂应该最多有30~60人是做品质相关的工作的,在贵司目前这个基础薄弱阶段,个人建议只有在人员过饱和的状况下才能有可能打一个胜仗,否则因为资源太少,即便假设贵司目前的QE都是精英,可以很敬业,每天加班加点地奋斗,希望扭转品质局面,这种敬业精神顶多维持半年,在QE工资满意,感觉自己学习很多收益匪浅,得到及时奖励(涨工资和年终奖,还有口头表扬),这三者跟得上的情况下也最多维持一年。一年以后一旦品质局面仍然没有明显改变,精英们必将疲累,黯然离去,剩下的精英因为新进人员总是跟不上离职人员的数量,将一直承担几倍的工作量,一般也只有两个选择,要么混日子,要么也是黯然离去,肯定不会选择的是累死。建议贵司先以人海战术,60人搞品质,质量水平搞上去了,这些品质人员肯定也会自然流失,最后只需30人维持就够了。
贵司地理位置偏僻,人员肯定不好招,如全都找有经验的人,因为正处于快速发展阶段,这些人很容易流失,建议,60~80%招一些刚毕业的没有工作经验的但是性格比较优秀具有快速学习能力的人,这些人因为重视经验累积,所以会呆的时间长一点,另外自身尤同一张白纸,会比较容易接受经理的意见和想法,做事也会更积极一些。以上是一些台资企业普遍的做法,但是要有个基础就是有愿意分享的老人带新人,并要让新人学习的过程中随时把学到的经验整理成公司的流程,文件,操作指导,ppt,教材,以便加速缩短后面再来新人的学习过程。基本上在有完善操作指导,ppt,教材和一个有经验的老人带领的前提下,入手的时间可以从3个月缩短到1个月。
人力资源紧缺带来的问题就是表面上在老总的眼里事情都完成了,实际上背后严重的是PDCA的Plan, Check, Action全部被省略掉了,每天只有Do do do, 如果只有Do do do,没有Plan,没有Check,没有Action,这也就没有了持续改进,这样一个企业很难向前发展。解决资源问题不敢说解决80%问题,但至少50%的问题是可以解决的。解决了资源问题,也能让敬业负责的老员工能喘口气不会被累的要离职了,大家也能每天有时间思考思考如何把工作做得更好,生产部的也能有时间培训培训,质量部的也能多做点预防,维修部的也能多做点维护和保养,只有停下脚步,才能走的更快更远。 2)终检检验指导书的制定
解决掉第1个人力资源问题以后,剩下的工作才真正有可能展开。也就是第二重要的,保证每种产品都有终检检验指导书,这个必须要人花大量的精力去制作的,如果贵司连产品的终检检验指导书都没有,如何让检验员知道客户关注的重点是什么?目前我知道B工很努力,完成了不少重要料件的终检检验指导书,但是对于新品,基本上是有心无力,对于我们公司尚且如此,对待其余17个客户,他们外一要是有新品过来,如何完的成终检检验指导书?
3)首检和制程检验指导书的制定
解决掉第2个问题之后,贵司的终检检验员终于能够抓住客户关注的重点了,剩下就是如何让贵司的制程检验员(听说目前还没有这个职位?)去监督生产部的操作员如何能够抓住品质要点,所以每个工序必须要靠首检和制程检验来解决。没有首检流程,首件不确定的话,贵司必将经常面临批量性报废的问题。 4)在线检验指导书SIP的制定
解决掉第3个问题之后,贵司的制程检验员可以避免掉在线的一些批量性报废的问题了,下一步真正要让操作员从源头上不生产不良品,必须依靠给操作员自己看的检验指导书才能解决。但是目前贵司操作员用于指导自己操作的操作指导书都没有,或者都没看过,更不要提检验指导书了。这个问题可以靠先让班组长看操作指导和检验指导书来解决,至少要保证在线的班组长能够领会客户的质量需求。 5)单个零件不良历史的制定
解决掉第4个问题以后,可以让生产部的人慢慢能够领会客户的质量需求了,把大家的质量意识从质量是检验出来的到质量是制造出来的开始逐渐的转变,下一步就是让在线的操作员真正地了解我这一道工序有哪些可能的不良会产生,这个才是最重要的。这个不良历史我会做一个范本给你们看看。知道如何操作,知道如何自检,知道不良历史,只有这样才真是从源头解决了问题,才能最大限度地避免掉后期大量的人力和物力的浪费。 6)贵司品质部门的人员分配问题。
2,3,4,5的就是做文件,需要耗费大量的时间,这不得不引申出贵司目前内部QE分工的另一个问题。贵司目前明显的一个薄弱环节就是QE前期介入不够,让技术部制作出来的工艺并没有得到品质人员的校验(举个简单例子来说,假设客户变更图纸,加了一个孔,于是技术部就会做了相应的工艺更改,加了一个钻的工艺,孔就完成了。客户真的只是要一个孔么?实际上这个孔是和另一个孔相交的,两孔相交,必然会出毛刺,总有一个孔就无法正常的通过通规了,这个隐含的品质要求就是不能有毛刺,实际上很可能没有QE的介入,去毛刺的工艺就会可能因为技术部人员品质意识的缺乏导致漏制定,从而造成了后期一系列的品质问题。当然以上只是一个假设,很多时候技术部还是有很多品质经验的,这种问题一般也都会做去毛刺工艺)
贵司客户众多,随之而来的新品,设计变更肯定更是多多多,目前客户的要求也越来越多,首件样品的品质报告更是种类繁多,材质证明(可能以前大部分客户只要这一个),尺寸报告,甚至Cpk报告,控制计划,甚至FMEA,包装方式,贵司目前技术部只能承担包装方式的制定,其他呢?全部落到了身兼数职的QE身上,QE不仅每天要去客户那边返工,给客户写8D对策,又要内部推动质量改进,良率提升,报废率减少,追查不良根本原因,很多时候前期的东西会强烈的和后期的工作冲突。 贵司可以根据自身的实际情况,找一些文员给客户制定前期新品的文书工作,准备这些文件,最后给QE审阅就行,这样可以大大减少QE的工作,提高他们的效率。QE实际上还可以继续细分,新品QE,处理客户投诉的CQE,推进内部改进的PQE,像我们管厂商的这种SQE是比较容易分开的就不说了,贵司如果继续停留在我们只是小公司的阶段,让QE身兼数职,反而会导致部门整体效率低下,客户新品的品质也没做好,已经量产的投诉也没人有时间处理,内部的质量成本也没有人花时间去降低。。。。。。将来的分工和细化是一个必然经历的阶段
如果新品做不好,前期不做防火动作,后期必然无法有稳定的质量,一定会形成四处着火,四处救火的恶性循环。
在不同的公司,QE在项目开发中的作用是不一样的,有的公司产品开发以QE为主角展开,有的以项目工程师为主角展开。不管是以项目为主角还是以QE为主角,但大家真正做的事情都差不多,只不过是在权限和职责上有所不同。以汽车行业产品开发为例在整个产品开发过程中,新品QE也是项目小组成员之一,他有以下工作必须完成:
1、主导产品检验规范的设计。内容包括检验工具策划、检验方法策划、检验频次策划等。
2、各类作业指导书编制。比如进料、过程、出货等指导书、各种检验记录表格的编制。
3、过程能力统计。有需要的生产工序的过程能力的统计。
4、收集产品开发的出现的质量问题,并主导进行持续改进。(这个工作在产品开发的过程中占得比重较大)。
7)抓住重点,优先选择项目进行推进
以上说了这么多,我想贵司肯定自己早就意识到了,并且应该也是一直想做,但是也是处于有心无力的状态。我后续将把我司找3个最重点的料件的相关文件制定工作逐渐推行,准备着手和B工一起先共同做一些范本,只有让贵司各部门体会到好处,才能有继续推行的可能。
以上只是个人一些想法和建议,结合贵司实际状况,仅供参考,希望能有所借鉴。另外希望两点贵司必须坚持住:一是希望贵司继续坚持推进MRB有效深入执行,深入向生产部贯彻质量是制造出来的,向技术部贯彻质量是设计出来的,共创全面质量管理的观念,才能有希望不再让品质部一个部门唱独角戏徒做无用功的局面出现。二是狠抓数据收集,用数据挣得老板支持。老板只对数字敏感,永远记住这点。 如下图这八个字是我最想送给贵司的。这是苏州的一家企业,具体经营状况如何我不太了解,我只是路过偶拍,我想能够打出这样条幅的,这家企业的老总一定厉害的不得了,将来企业的发展一定大有作为。大部分私营企业在快速发展过程中,一定会面临资源和管理跟不上发展速度的问题,中高层管理者如何在成日应付订单交货处理客户投诉的忙碌中摆正态度,打好管理和品质的基础,做好PDCA,秉持住先做强再做大的理念,才能在价格战争中打造自己的核心竞争力以便发展的更大更强。
第13篇:SQE任职资格
岗位职责:
· Make root cause analyse of none conform parts; 针对不一致的产品分析根本原因
· Communication and improvement supplier quality problem (8D report);、沟通和改善供应商质量问题(8D报告)
· React and improve the quality control plan for better efficiency; 反应和改进质量控制计划以得到更好的效率
· Audit supplier and help them to establish a proce control of quality; 供应商审核和帮助他们建立过程质量控制方法 · Manage none conform parts with ERP system; 在ERP系统中管理不一致的产品 · Arrange IQC work.安排IQC的工作
任职资格的具体描述:
· Bachelor degree or above in electrical, mechanical engineering or automation; 电气科学、机械工程或自动化学士学位或者以上 · Experience in machine tool or related industries; 机床或相关行业经验
· Proficient in English (oral/written) (CET-6 and above); 精通英语(口语和协作)(六级或更高) · Using WINDOWS office software skilfully; 熟练地使用办公软件
· 5 years quality experience ERP system experience; 5年质量经验和ERP系统使用经验
· Manage employees experience will be an aet; 管理员工的经验将是一笔财富
岗位职责:
1、Improvement of quality system, procedures planning and preparation 改进质量体系和程序计划准备
2、Implementation of central quality standards in quality area 在质量领域实现质量标准化
3、Organization of external, internal audit, customer audit 组织外部和内部审核、顾客审核
4、Organization and planning of product audit 组织和计划产品审核
5、Quality documents 质量文件
任职资格的具体描述:
1, Master majored in mechanics or metal material science(preferable Germany returnee) 主修金属或材料科学(最好是德国海龟) 2, 2-4 years working in auto industry 2-4年汽车行业工作经验
3, Knowledge on TS16949 and lean production 熟悉TS16949和精益生产
4, General leadership requirement of CNTP 一般领导的CNTP要求
职位名称:供应商质量工程师 发布日期: 2014-08-11
工作地点:
北京 工作年限: 5-7年
学
历:
本科
Key Accountabilities:
· Identify quality plan for resourcing components and aistant to internal/external quality team; 确定关于资源组件和协助内外部质量团队的质量计划。 · Aistant to supplier PPAP audit; 协助进行供应商PPAP审核
· Supplier quality system or on site audit; 供应商质量体系或现场审核
· Supplier management, problem solving; 供应商管理、质量问题解决
· Aistant to Purchasing Engineer to select new suppliers 协助采购工程师选择新供应商
· Support to incoming inspection, testing or validation 支持来料检查、试验、确认
Qualifications & Requirements:资格和要求
· Bachelor’s degree or above in mechanical engineering, at least 3 years experience in quality side; 机械工程学士学位或以上,质量方向至少三年工作经验
· Familiar with drawings, specifications, materials analysis or inspection proce; 熟悉机械制图、规格、材料分析或检查过程 · Familiar with TS16949 system; 熟悉TS16949体系
· Advanced PC and English language skills.高级的电脑和英语语言能力 Key Competencies:关键能力 · Priority Setting 优先级顺序 · Informing 通知
· Proce Management 过程管理
· Problem Solving 问题解决
· Drive for Results 推动结果
· Functional / Technical Skills 功能/技术能力 · Customers Focus 顾客焦点 · Decision Quality 质量决定
· Timely Decision Making 及时对策
· Interpersonal Savvy 人际理解能力/沟通
岗位职责:
Prepare neceary documentation and contribute to continuous improvement proce (CIP).Provide concepts, methods to optimize proce and product performance.Supplier evaluation and standard proce audit.Develop and define the measures together with supplier, with considering the project timing and risk claification.Supplier development/ Tier-n management.Evaluate and develop suppliers, using preventive methods for early identification and minimization, which are high risk and take on projects that are difficult due to part complexity, safety parts, short timing, etc.Work with suppliers, and if neceary with Tier-n suppliers;
support problem resolution activity at the supplier when quality iues arise, if required by setting up an interdisciplinary team.Preventive supplier and maturity management/ FMEAs.Ensure that maturity levels are efficiently maintained with suppliers, focusing on components with an enhanced maturity level risk.Plan, organize and conduct “Round Tables” with cro functional team for early identification of maturity level problems through mandatory and active involvement of suppliers.Aement of quality-related parameters along the product creation proce and result communication.Control implementation of defined corrective measures and monitor their effectivene together with suppliers.Production proce and product audit.Planning, co-ordination and execution of audits as a responsible lead auditor.Iuance of the audit report.Based on audit findings, controlling of neceary improvement measures and appropriate implementation, as well as the effectivene measuring of corrective actions.If neceary, re-auditing of supplier’s procees.Set up sampling schedule and get supplier’s commitment for defined milestones.Define sampling features.Monitor first out of series tooling produced parts where neceary. Perform or coordinate external sampling for dimensions and material properties.Coordinate with Engineering functional and performance tests and compile all relevant documents.Hand Shake/ Recovery Serve as contact partner, resource of knowledge and experience for QM-Plant throughout the whole project for designated parts.Coordinate and oversee hand over meeting to the quality engineer of the plant with explanation, if neceary, of defined measures for part, proce or supplier.Support recovery proce with technical expertise for joint-venture.任职资格的具体描述:
Bachelor degree in engineering is required.Master degree is preferred.Minimum of 3 years automotive industry (or comparable) experience, quality and manufacturing experience preferred.Highly trained in more than 1 commodity area – expert in engineering /manufacturing proce’s for either power train/chais, exterior/interior, Body-In-White or electrical.Significant experience in PPAP requirements (i.e.Control Plan, PFMEA, Flow chart, etc.).Interpersonal and problem solving skills, team orientation is neceary along with computer competency, e.g.MS Office.Familiar with ISO/TS16949, VDA 6.3.Excellent written and spoken Command of English or German.岗位职责: Key Objectives:
The Aistant Manager Parts Quality & Supplier Quality is responsible to aure product and proce quality of supplied parts and support BMW AG Purchasing & SQA Departments on all Global Sourcing Activities in China related to parts quality and supplier quality management iues.
Major Responsibilities:
Quality evaluation within the Supplier Selection Proce.
Supplier visits for Supplier Pre-Selection, Supplier Project Aements and Supplier Evaluations.
Supplier Development.
Steering & monitoring of Global Project according to BMW Quality Procees (eg.RMT). Preparation and support for Proce Series and ISIR-Procedure (PPAP). Product and Proce Audits at suppliers, Supplier Requalification. Follow-up of measurements and actions defined out of Proce Series and Supplier Audits. Analyze parts quality problems and coordinate the problem solving proce.
Compilation and translation (Chinese to English/German) of relevant quality documents. Decision on the suitability of potential suppliers for Global Sourcing in terms of QMT. QMT-Contribution to the supplier pre-selection and supplier selection. Evaluation of risks and supplier qualification costs.
Decision on required supplier measurements and actions to aure and improve parts and proce quality 任职资格的具体描述: Education / Degree: 教育/学历
University degree in electrical / mechanical / automotive engineering. 电器/机械/汽车工程大学学位 Knowledge / Skills / Competences: 知识/技能/能力
Experience in proce and product quality and related manufacturing procees
(e.g.machining, stamping, injection molding, die casting, aluminum casting, manufacturing proce of electrical & electronic components, tooling). Basic economics knowledge.
Good Knowledge of Quality Methods and Quality Tools (e.g.Poka-Yoke, FMEA, 8D-Report „).
Familiar with Statistical Proce Control and statistics calculation methods. Good understanding of technical drawings and quality specifications. Experience in Product and Proce Audits.
Ability to work in a team, good communication skills, ability to aert oneself, keen perception.Strong Quality Awarene and Target Orientation.
Chinese and English fluent; good knowledge of German language is an advantage Intensive knowledge about local mentality, culture and conventions.
Good knowledge of Windows and MS-Office (Word, Excel, PowerPoint, Outlook „).职位描述:
1.Responsible for tracing and managing the milestones of the car project with supplier; 1.负责跟踪并管理供应商汽车项目的时间表;
2.Improving supplier quality standard for meeting the quality requirement of the OEM; 2.提高供应商的质量标准使其达到原始设备制造商的质量要求; 3.Regular supplier on-site audit; 3.定期地进行供应商现场审核;
4.Follow-up all the proce development until 3 months after SOP by using project management knowledge and quality knowledge and tools; 4.运用项目管理知识和质量管理知识和工具,对进入SOP工艺开发之后的3个月进行后续跟踪;
5.Documentation of project status; 5.提交项目状态的文件; 6.Initial samples’ acceptance; 6.初始样品的验收;
7.Performs other related duties as aigned.7.执行其他指派的相关任务。
1.Bachelor Degree or above in automotive engineering, engineering or other related field; 1.汽车工程、工程类及其他相关专业本科以上学历;
2.Experience of quality management, ideal experience at OEM; 2.有质量管理经验,有OEM工作经验者优先; 3.Technical competences (ie: mechanical, electronic„) 3.具备技术能力(例如机械、电子等);
4.Knowledge of proce development and quality tools (ie: capability studies); 4.熟悉工艺开发和质量工具(例如性能研究); 5.ISO TS knowledge is a plus; 5.有ISO TS相关知识者优先;
6.Experience of project management; 6.有项目管理经验;
7.Strong communication skills and high motivation dealing with people; 7.较强的沟通交流能力,善于人际交往;
8.Fluent in both spoken and written English, German or French is a plus; 8.流利的英语听说读写能力,懂德语或法语者优先; 9.Flexibility on travelling; 9.能够适应出差;
岗位职责:
1、负责保障供应商所供原材料的质量,由于供应商供货物料质量缺陷引发的问题要及时反馈供应商要求其改善;
2、负责追踪确认供应商的改善报告及实施效果,必要时可进行现场审核检查;
3、负责制定进货检验部门的检验规范及检验计划,并适时对检验员进行培训指导;
4、可以参与供应商初始样品的评估放行工作;
5、每月或每季度,对现有供应商的质量状况进行统计评分,对评分较低的供应商提出限期改善要求;
6、参与新供应商开发与审核,与采购、研发部门一起对新供应商进行考核打分。任职资格的具体描述:
1、负责保障供应商所供原材料的质量,由于供应商供货物料质量缺陷引发的问题要及时反馈供应商要求其改善;
2、负责追踪确认供应商的改善报告及实施效果,必要时可进行现场审核检查;
3、负责制定进货检验部门的检验规范及检验计划,并适时对检验员进行培训指导;
4、可以参与供应商初始样品的评估放行工作;
5、每月或每季度,对现有供应商的质量状况进行统计评分,对评分较低的供应商提出限期改善要求;
6、参与新供应商开发与审核,与采购、研发部门一起对新供应商进行考核打分。
岗位职责:
1.Full quality control of the project products and compile quality documentation, guarantee the qualified products shipped to the customers.1.针对项目产品的完整质量控制,编译质量文件,保证运送至客户处的产品质量。 2.Audit the outsourcing supplier quality control and related documentation.审核外包供应商质量控制和相关资料
3.Supervise and track the supplier’s manufacturing proce and periodically form minutes and tracking reports, monitor Supplier quality improvement and supplier quality performance report and analysis.监督和跟踪供应商制造的过程和定期的记录和跟踪报告,监控供应商质量改进和供应商质量绩效报告并分析。
4.Responsible for the outsourcing inspector’s management and training.负责外包产品检查员的管理和培训
5.Responsible for the reception of project products auditing from outside.负责接受外部项目产品审核
6.Organize NCR and POR investigation and other quality improvement activity.组织NCR(不符合报告)和POR调查和其他质量改进行动 7.Compile project plan and yearly report.编制项目计划和年度报告
任职资格的具体描述:
1.Bachelor’ degree or above in mechanical engineering.1.机械工程学士学位或以上
2.8+ years’ work experience, including + 5 years’ work experience in supplier quality. 2.八年以上工作经验,包括5年质量管理工作经验。 3.Project management background is preferred.3.项目管理背景优先。
4.Familiar with APQP,PPAP and TS16949.4.熟悉APQP 5.With team work spirit, be good at communication and conflict management..5.有团队工作精神,在交流和冲突管理方面有优势
6.Auto industry work experience and team management experience is a plus.6.汽车行业工作经验和团队管理经验 7.Proficiency in English.7.熟练地英语水平
岗位职责:
1.负责新项目供应商 APQP 过程的管理和执行 1) 负责配合采购部参与新供应商的潜在供应商评审 2) 负责参与项目启动会,在项目启动会上团队确认关键技术问题和项目时间节点,确认 ESI 和供应商产能调查表的输入情况,完成项目启动会议纪要 3) 负责根据特定零件类别的设计评审表,协调供应商参与零件设计评审,自己参与零件设计评审,给出设计的可制造性,零件 检具可制造性和特殊特性传递等方面的评审意见 4) 负责监控供应商零件 APQP 状态,对于供应商 APQP 活动未能按时准确输出的负责牵头建立反应计划并推动反应计划闭环运行,对于高风险问题能予以识别和通报(一些关键的 APQP 输出应包括图纸,零件流程图,零件检具策划,零件 FMEA, 零件特殊特性清单,零件 OTS ,零件 PPAP ,零件交样质量及改进等) 5) 负责审核零部件 PPAP 文件,按照 PPAP 手册要求,按照公司体系要求的 PPAP 文件清单, PPAP 检查清单进行逐项确认和检查供应商 PPAP 文件质量,推动 PPAP 进度 6) 负责对供应商进行过程 PSO ( 过程签发 ) 审核,节拍审核。按照公司 PSO 检查清单逐项确认供应商过程情况,特别关注特殊特性过程的策划和实施,供应商 GP12 过程实施,过程能力等的表现 7) 负责审核供应商启动遏制计划及监督其执行。检查供应商启动遏制检查内容是否覆盖所有特殊特性和客户关注点,检验方法的策划是否满足供货节拍,遏制区域是否独立且设立了缺陷和趋势统计方法,遏制检查员工是否训练有素 8) 负责审核供应商的启动准备 9) 负责 YFK 新项目进料检验的策划和及及时实施,应包括进料检验控制计划的编制,新量检具的策划,检验员的培训等,并负责制定零件类进料检验方法的持续改进 10) 负责审核供应商年度型式试验计划,完成质量协议等文件化工作 2.负责供应商产品和零件的测量,分析和改进 1) 负责针对项目开发过程中以及启动初期供应商质量问题,对供应商发出问题整改需求,落实现场短期措施,审核供应商 PRR ,确认供应商原因分析正确短期和长期措施有效,对供应商进行绩效考评,跟踪供应商绩效趋势,采取供应商提高措施,监控供应商 PPM 及供应商材料退货还有索赔 2) 支持投产项目供应商质量问题的处理 3) 负责一级受控供应商质量问题的处理和过程改进直至退出一级受控 3.3.负责供应商制造过程的测量,分析和改进 1) 负责通过审核供应商 PFMEA 以及现场 PSO 的结果,对供应商过程能力提出持续改进指导 2) 负责对供应商实施过程审核,安全性审核,产品审核,技术审计等对供应商过程能力进行评价和改进指导 4.4.负责在 TS16949 的框架下对部门及公司质量体系持续改进 1) 提出供应商能力提升计划 , 对供应商进行审核或飞行审核,制订供应商访问计划,并负责输出访问会议纪要及产品和过程审核报告 2) 负责持续的对供应商零件产品和过程知识进行知识积累和经验教训总结,形成内部分享和对设计评审表, PSO 审核表等体系文件的持续改进 5.质量部长安排的其他工作任务和职责
任职资格的具体描述:
1.机械或工科,本科以上 2.2 年以上相关汽车行业质量工作经验 3.掌握质量体系知识 4.掌握产品测量技术 5.掌握 8D 工具和思维 6.掌握 PFMEA 的应用和思维 7.掌握质量审核能力 8.良好的英文能力,逻辑思维能力,团队组织能力,协调安排和时间管理能力 9.产品知识和产品经验
岗位职责:
Responsible for developing, applying, revising, and maintaining quality standards for proceing materials, solving complex quality engineering problems in creative and effective ways.
l Provides technical direction and guidance to supplier.l Has a strong working knowledge of quality and reliability concepts, supplier management, with respect to quality and reliability, and general manufacturing operations busine management relative to all functional groups.Capable of managing any commodity.l Interfaces with other Apple functional groups as resources to optimize suppliers quality programs.l Participates in the development and implementation of Product Quality Plan (PQP) for specific commodities with SQE’s at other sites. l Aees supplier’s production and quality programs.
l Evaluates the supplier procees and proce controls to ensure product quality and reliability is built in.Develops supplier capability (including neceary training),establishes proper reporting of in-proce and final inspection and test results to Apple.
l Responsible for FAI proce and monitors performances of PVT, identifying and auring neceary corrective actions are taken.Authorizes and monitors the startup of production at the supplier site.
l Establishes discovery audit procedures and ensures performance to standards by Apple test personnel.Responsible for Cpk proce.
l Monitors each supplier’s performances through measurements of production line statistics, company inspections management so that effective corrective action plans can be sett in place if neceary.
l Supports Supplier Quality Engineering in improving and reporting vendor procees. l Works as a part of a New Products introduction team draw up and/or coordinate and implement the PQP for the site.In conjunction with the design engineers and the site engineers, determine the proce goals for products. l Participates in yield improvement efforts.
l Responsible for specific tasks as park of a team involved in the introduction of new products or procees.
l Provides full support to an aigned area of production/service.
l May direct the activities of other engineers and technicians on specific tasks.
l Acts as a project leader on design of experiments and the analysis of test date to determine outcome.任职资格的具体描述: Key Responsibilities: Responsible for developing, applying, revising, and maintaining quality standards for proceing materials, solving complex quality engineering problems in creative and effective ways.
l Provides technical direction and guidance to supplier.l Has a strong working knowledge of quality and reliability concepts, supplier management, with respect to quality and reliability, and general manufacturing operations busine management relative to all functional groups.Capable of managing any commodity.l Interfaces with other Apple functional groups as resources to optimize suppliers quality programs.l Participates in the development and implementation of Product Quality Plan (PQP) for specific commodities with SQE’s at other sites. l Aees supplier’s production and quality programs.
l Evaluates the supplier procees and proce controls to ensure product quality and reliability is built in.Develops supplier capability (including neceary training),establishes proper reporting of in-proce and final inspection and test results to Apple.
l Responsible for FAI proce and monitors performances of PVT, identifying and auring neceary corrective actions are taken.Authorizes and monitors the startup of production at the supplier site.
l Establishes discovery audit procedures and ensures performance to standards by Apple test personnel.Responsible for Cpk proce.
l Monitors each supplier’s performances through measurements of production line statistics, company inspections management so that effective corrective action plans can be sett in place if neceary.
l Supports Supplier Quality Engineering in improving and reporting vendor procees. l Works as a part of a New Products introduction team draw up and/or coordinate and implement the PQP for the site.In conjunction with the design engineers and the site engineers, determine the proce goals for products. l Participates in yield improvement efforts.
l Responsible for specific tasks as park of a team involved in the introduction of new products or procees.
l Provides full support to an aigned area of production/service.
l May direct the activities of other engineers and technicians on specific tasks.
l Acts as a project leader on design of experiments and the analysis of test date to determine outcome.岗位职责:
1.贯彻工厂的质量方针和目标,执行质量控制标准,确保产品的质量得到有效控制。2.监督指导质量检验程序、方法及文件的有效执行,确保产品(包括主要原辅材料、零配件、外协件等)符合质量标准要求。
3.制定部门的业务指标及衡量部门的工作业绩。
4.负责组织协调相关部门对过程中存在的产品质量缺陷和顾客报怨问题进行原因分析,并制定纠正措施和实施跟踪反馈,达到减少浪费和持续改进的目的。5.协助体系工程师做好公司的质量体系有效运行及维护工作 6.做好公司管理层与下属员工之间的信息桥梁。
7.指导质量工程师做到及时有效地分析生产过程中存在的质量问题。
8.负责监督生产产品所设计的计量器具和试验设备得到及时校验,保证测量结果的有效性。9.负责督导在新产品工艺开发过程中产品质量满足顾客要求,确保产品在投产后的质量状况得到有效控制。
10.负责指导分供方的质量改进及分供方的批准。11.理解顾客的相关标准和要求,与顾客进行有效地沟通。 12.充分利用部门的资源,合理分派部门的工作。
13.负责培训和管理下属人员,不断提高下属人员素质水平。14.就部门的相关事宜与其他部门进行沟通协调。
体描述:
-工科大学学历,5年以上质量管理经验。 1.具有质量管理体系内审员资格。
2.熟悉工厂产品工艺、质量标准要求、计量和检测管理的基本知识。
3.熟练应用FMEA/SPC/QFD/DOE/8D5WHY/AQP/PPAP/MSA/防错Benchmarking/排列图/因果图等质量管理工具。
4.充分理解TS16949质量体系的基本知识。5.掌握有效的沟通技巧。
第14篇:SQE面试技巧
工作职责:
1.作为一个sqe,你能简单介绍一下你的工作职责吗? 2.针对供应商质量问题,在实际工作中你是如何解决的,举1,2个例子说明? 3.如何综合全面的管理和评估供应商的质量,你有社么方式和方法? 4.如何持续的改善供应商的质量,你运用社么样的方法来实现? 5.针对新的供应商,你是如何导入的?
简单的质量知识: 1.你了解fmea吗,说明o,s,d, rpn是何解释,举例说明fmea? 2.spc, 有那些控制工具,各使用在何场合,cp,cpk;cpk, ppk的区别? 3.简单说明iso9000/ts16949的八大原则? 4.举一个例子说明如何完成gr&r? 5.你对6sigma有多少了解,概述一下6sigma,举例说明假设检验和doe. 呵呵,以上都是小弟在interivew过程中经历过的问题。
当然还有一些专业性的问题,基本都是关于产品的问题点,root cause, 如何改善,比如说注塑成形会产生社么问题,原因是设么,如何改善等等。
另外,如果你是去欧美企业,上面的问题可能都会是英文提问,然后英文回答, 呵呵。
答1.1.作为一个sqe,你能简单介绍一下你的工作职责吗? 简单点,就是要公司花钱买到好的产品和服务,以保证本公司的产品质量.sqe就是要监督和辅导供应商达到公司产品质量要求甚至超越公司要求. 2.针对供应商质量问题,在实际工作中你是如何解决的,举1,2个例子说明? 若公司出现质量问题,是供应商来料问题,首先要看是新供应商还是一直配合的供应商,新供应商就要有针对性了,第一要告诉他们我们公司要求,及测试要求等,还要去现场进行辅导和培训.旧的供应商要写改善报告,在去现场验证.不是很严重可以根据下批来料进行验证.举例就不说了. 3.如何综合全面的管理和评估供应商的质量,你有社么方式和方法?
首先要看是什么产品,针对产品(电子产品)进行分类是五金产品\包材\pcb还是其它,举例:五金产品从新供应商导入到正式订单,iqc对来料进行评估(包括产品质量\交期等),以数据进行分析. 4.如何持续的改善供应商的质量,你运用社么样的方法来实现?
采用软硬兼施的办法,一方面要让供应商感觉和你是很好的朋友,愿意帮助他们,同时要那么去改善产品质量.一方面要对有质量问题的供应商进行惩罚,但是要注意不要过头. 5.针对新的供应商,你是如何导入的? 1.制作审核清单和审核计划.2.查看工程承认样品是否合格.3.通知审核日期.4.现场审核.5.审核结果. 简单的叙述了一下.具体细节要靠自己去领悟. 简单知识就不说了. 答2.本人对sqe的理解为供应商质量管理。来料检验标准的制定,除了质量管理自身的技术,还有供应链管理的知识、项目管理的知识。在质量体系方面,因为要转化为实际的审核过程中,相关职能归属仍在不确定中,主要看每个公司不同分工以及领导人的决策问题等。 但我认为做为sqe来说,必须具有相当深厚的功底,同时,必须要有丰富的过程分析和过程控制经验,快速解决问题的方法和执行力,随着经济的快速发
展,这些是由越来越短的交货周期、来短的产品开发周期来决定。因些sqe对于处理供应商品质问题时,往往其角色是代表公司,处理问题时同时还要兼顾自己公司的产品,供应商的物料以及最终交付给客户的产品,sqe不仅是一个质量工程师的角色,同理担当以及面对公司的复杂状况的一些管理层人员,因此,sqe又必须善于对外对内的沟通,以及利用外资源在处理供应商物料质量问题而进行协调,我想这也是sqe必备的条件之一。也就是所谓的供应商关系管理吧。
我个人认为一个优秀的sqe,能给到公司承上启下的作用,质量与绩效呈水平状态。
答3.哈,lz阅历一定很深厚,interview有6sigma gb的难度了,呵呵. 个人毕业后做sqe也已经三年了,觉得sqe focus还是在厂商质量管理.现在制造业都在cost down,价格偏宜了,但客户要求是越来越高tqrdc.说白了,物廉价价美的产品不存在,老板招你过来就是要解决原材的quality和原材厂商service问题的. 作为衔接厂内与厂商质量的角色,个人的沟通能力尤为重要. 其次是个人掌握的专业知识,包括系统面的,工具,当然还有产品知识和流程,俗话说你有几分功力,厂商就会回你几分功力,所以个人的sense也是很重要地:),在充分运用厂商资源管理好厂商前个人的能力是很重要地. 再次sqe碰到问题一定要有自己的想法,要能坚持自己做事的原则,逻辑一定要清晰。 最后个人觉得管理好厂商真的很困难,范围也很大,怎样管理,个人觉得先设定各项指标kpi,再运用相关quality工具,报表作control,以达到cip的目的 答4.sqe主要是对供应商的提出改进和帮助的。我认为一个好的sqe最主要是把握一个原则就是与供应商互利的双赢。
我记得在做的时候,有一次一个供应商的产品出现了包装上的问题,导致所供的针脚老是歪斜,给我司的上线造成了影响,我马上与他们联系以后,特意却了那个公司进行现场审查。发现包装现场上有堆积现象,针对这一问题在后来的会议
上特别强调了要求他们更改包装的方式,并提出了一些意见,跟踪验证后续产品的该项问题。做到告诉他们如何做,提供更好的服务给我们公司。 综合评价的方式有很多啊,不定期地看厂,做该组供应商的质量反馈,及时与他们联系,然后从态度、工作完成的及时性、反馈问题的验证效果等进行评估。 怎样持续评估的问题,相信这些都有一定的流程的规定的,可以做一个供应商考核体系。
新供应商的导入肯定要按照体系文件的规定了,样品确认、生产实用性、工程、品质、生产共同的介入来引进啊
问题:1.面对供应商8d老是不能及时回复如何处理? 2.面对供应商进料检验老是重复出现同样不良如何处理? 3.面对供应商抱怨退回不良混有制程造成不良如何处理? 4.针对iqc检验员针对同一材料不良判定标准不一致时如何处理?
针对以上问题,各位有何见解?谢谢
答1:老是出现同一不良(主要看看问题出现在那,是否有能了克服,如没有克服能力,看贵司下工序是否影响,没有影响;在看这家供应商与老板的关系,是兄弟企业可以特采吗,如若就按以下处理了!!!
通知采购,工程,撤销其资格。
答2:1.面对供应商8d老是不能及时回复如何处理?
答:追讨8d不是你的目的,主要是了解供应商针对你反馈的8d的内容,内部所做的动作
你可以先要求供应商将内部动作先进行说明,一步一步指导供应商按照8d的格式去作业,
当然有条件可以直接到供应商端开检讨会,确定8d的回答。 2.面对供应商进料检验老是重复出现同样不良如何处理?
答:这个问题我也经常有面对,我一般从2个方面着手,1>先了解供应商此问题产生的原因, 产生此问题的概率,不知道你是何行业,例如塑胶成型过程中,缩水/气纹等问题可能不可避免
必须以检查入手进行及时发现,及时调整机器来控制。2>检查文件的制作上着手,本来qc人员
全部按照sip进行检查,如果sip都有问题,还如何能保证不会产生漏失。 3.面对供应商抱怨退回不良混有制程造成不良如何处理?
答:要求供应商提出抱怨的依据,并和供应商一起开会确定供应商造成不良和你们制程造成的不良如何区分,确认完成后按照供需互利的原则可以要求供应商派出检查人员协同你们的检查人员一起针对退货部分进行确认,可以连续确认几批,确认内部是否存在制程造成之不良品,如果有,内部检讨此部分流出原因,针对内部制程可以请内部品质人员协同检讨改善。
4.针对iqc检验员针对同一材料不良判定标准不一致时如何处理?
答:针对此问题,直接采用实物教育,量化教育的方式,加深iqc检查人员的标准判断准确率,并按照2次/月的比例收集不良/良品,进行检查漏失率的判定,进一步提升iqc检查人员的检标准判断力和检出率! 1.为什么不能及时回复?原因:不重视?能力不足?沟通不畅?...... 2.为什么会有重复不良?原因:制程无法改善?供应商把不良再次塞进来?........................... 多问几个为什么,对症下药是良策.须知你还是只是在面试阶段,如果都像你这样说的,通知采购,撤销资格就好了。。谁都会的事情,还要你来做什么?请你来当老板,通知这个通知那个么?
答3:1.面对供应商8d老是不能及时回复如何处理? ---1)是否跟催,跟催哪个部门哪个人,怎么跟催,跟催是否有效?邮件和传真是不够的,电话要紧; ---2)8d的投诉是否定义清楚,在接收范围内的产品更换投诉,很让供应商接受不了; ---3)我通常喜欢每2h跟催一次,一般在电子邮件的跟催中会注明“几点回复,在线等”之类的词语
作为sqe你要清楚supplier为什么不回报告,是厂商能力不够找不到原因还是别的原因?篇2:sqe面试的问题及应对
工作职责: 1.作为一个sqe,你能简单介绍一下你的工作职责吗? 2.针对供应商质量问题,在实际工作中你是如何解决的,举1,2个例子说明? 3.如何综合全面的管理和评估供应商的质量,你有社么方式和方法? 4.如何持续的改善供应商的质量,你运用社么样的方法来实现? 5.针对新的供应商,你是如何导入的?
简单的质量知识: 1.你了解fmea吗,说明o,s,d, rpn是何解释,举例说明fmea? 2.spc, 有那些控制工具,各使用在何场合,cp,cpk;cpk, ppk的区别? 3.简单说明iso9000/ts16949的八大原则? 4.举一个例子说明如何完成gr&r? 5.你对6sigma有多少了解,概述一下6sigma,举例说明假设检验和doe. 呵呵,以上都是小弟在interivew过程中经历过的问题。
当然还有一些专业性的问题,基本都是关于产品的问题点,root cause, 如何改善,比如说注塑成形会产生社么问题,原因是设么,如何改善等等。 另外,如果你是去欧美企业,上面的问题可能都会是英文提问,然后英文回答, 呵呵。
答1.1.作为一个sqe,你能简单介绍一下你的工作职责吗? 简单点,就是要公司花钱买到好的产品和服务,以保证本公司的产品质量. sqe就是要监督和辅导供应商达到公司产品质量要求甚至超越公司要求. 2.针对供应商质量问题,在实际工作中你是如何解决的,举1,2个例子说明? 若公司出现质量问题,是供应商来料问题,首先要看是新供应商还是一直配合的供应商,新供应商就要有针对性了,第一要告诉他们我们公司要求,及测试要求等,还要去现场进行辅导和培训.旧的供应商要写改善报告,在去现场验证.不是很严重可以根据下批来料进行验证.举例就不说了. 3.如何综合全面的管理和评估供应商的质量,你有什么方式和方法?
首先要看是什么产品,针对产品(电子产品)进行分类是五金产品\包材\pcb还是其它,举例:五金产品从新供应商导入到正式订单,iqc对来料进行评估(包括产品质量\交期等),以数据进行分析. 4.如何持续的改善供应商的质量,你运用社么样的方法来实现?
采用软硬兼施的办法,一方面要让供应商感觉和你是很好的朋友,愿意帮助他们,同时要那么去改善产品质量. 一方面要对有质量问题的供应商进行惩罚,但是要注意不要过头. 5.针对新的供应商,你是如何导入的? 1.制作审核清单和审核计划.2.查看工程承认样品是否合格.3.通知审核日期.4.现场审核.5.审核结果.简单的叙述了一下.具体细节要靠自己去领悟. 简单知识就不说了. 答2.本人对sqe的理解为供应商质量管理。来料检验标准的制定,除了质量管理自身的技术,还有供应链管理的知识、项目管理的知识。在质量体系方面,因为要转化为实际的审核过程中,相关职能归属仍在不确定中,主要看每个公司不同分工以及领导人的决策问题等。 但我认为做为sqe来说,必须具有相当深厚的功底,同时,必须要有丰富的过程分析和过程控制经验,快速解决问题的方法和执行力,随着经济的快速发展,这些是由越来越短的交货周期、来短的产品开发周期来决定。因些sqe对于处理供应商品质问题时,往往其角色是代表公司,处理问题时同时还要兼顾自己公司的产品,供应商的物料以及最终交付给客户的产品,sqe不仅是一个质量工程师的角色,同理担当以及面对公司的复杂状况的一些管理层人员,因此,sqe又必须善于对外对内的沟通,以及利用外资源在处理供应商物料质量问题而进行协调,我想这也是sqe必备的条件之一。也就是所谓的供应商关系管理吧。 我个人认为一个优秀的sqe,能给到公司承上启下的作用,质量与绩效呈水平状态。
答3.哈,lz閱曆一定很深厚,interview有6sigma gb的難度了,呵呵. 個人畢業后做sqe也已經三年了,覺得sqe focus還是在廠商質量管理.現在制造業都在cost down,價格偏宜了,但客戶要求是越來越高tqrdc.說白了,物廉價價美的產品不存在,老板招你過來就是要解決原材的quality和原材廠商service問題的. 作為銜接廠內與廠商質量的角色,個人的溝通能力尤為重要. 其次是個人掌握的專業知識,包括系統面的,工具,當然還有產品知識和流程,俗話說你有几分功力,廠商就會回你幾分功力,所以個人的sense也是很重要地:),在充分運用廠商資源管理好廠商前個人的能力是很重要地. 再次sqe碰到問題一定要有自己的想法,要能堅持自己做事的原則,邏輯一定要清晰。 最后個人覺得管理好廠商真的很困難,范圍也很大,怎樣管理,個人覺得先設定各項指標kpi,再運用相關quality工具,報表作control,以達到cip的目的
答4.sqe主要是对供应商的提出改进和帮助的。我认为一个好的sqe最主要是把握一个原则就是与供应商互利的双赢。
我记得在做的时候,有一次一个供应商的产品出现了包装上的问题,导致所供的针脚老是歪斜,给我司的上线造成了影响,我马上与他们联系以后,特意却了那个公司进行现场审查。发现包装现场上有堆积现象,针对这一问题在后来的会议上特别强调了要求他们更改包装的方式,并提出了一些意见,跟踪验证后续产品的该项问题。做到告诉他们如何做,提供更好的服务给我们公司。
综合评价的方式有很多啊,不定期地看厂,做该组供应商的质量反馈,及时与他们联系,然后从态度、工作完成的及时性、反馈问题的验证效果等进行评估。
怎样持续评估的问题,相信这些都有一定的流程的规定的,可以做一个供应商考核体系。
新供应商的导入肯定要按照体系文件的规定了,样品确认、生产实用性、工程、品质、生产共同的介入来引进啊
问题:1.面对供应商8d老是不能及时回复如何处理? 2.面对供应商进料检验老是重复出现同样不良如何处理? 3.面对供应商抱怨退回不良混有制程造成不良如何处理? 4.针对iqc检验员针对同一材料不良判定标准不一致时如何处理?
针对以上问题,各位有何见解?谢谢
答1:老是出现同一不良(主要看看问题出现在那,是否有能了克服,如没有克服能力,看贵司下工序是否影响,没有影响;在看这家供应商与老板的关系,是兄弟企业可以特采吗,如若就按以下处理了!!!
通知采购,工程,撤销其资格。
答2:1.面对供应商8d老是不能及时回复如何处理?
答:追讨8d不是你的目的,主要是了解供应商针对你反馈的8d的内容,内部所做的动作
你可以先要求供应商将内部动作先进行说明,一步一步指导供应商按照8d的格式去作业,
当然有条件可以直接到供应商端开检讨会,确定8d的回答。 2.面对供应商进料检验老是重复出现同样不良如何处理?
答:这个问题我也经常有面对,我一般从2个方面着手,1>先了解供应商此问题产生的原因,
产生此问题的概率,不知道你是何行业,例如塑胶成型过程中,缩水/气纹等问题可能不可避免
必须以检查入手进行及时发现,及时调整机器来控制。2>检查文件的制作上着手,本来qc人员 全部按照sip进行检查,如果sip都有问题,还如何能保证不会产生漏失。 3.面对供应商抱怨退回不良混有制程造成不良如何处理?
答:要求供应商提出抱怨的依据,并和供应商一起开会确定供应商造成不良和你们制程造成的不良如何区分,确认完成后按照供需互利的原则可以要求供应商派出检查人员协同你们的检查人员一起针对退货部分进行确认,可以连续确认几批,确认内部是否存在制程造成之不良品,如果有,内部检讨此部分流出原因,针对内部制程可以请内部品质人员协同检讨改善。
4.针对iqc检验员针对同一材料不良判定标准不一致时如何处理?
答:针对此问题,直接采用实物教育,量化教育的方式,加深iqc检查人员的标准判断准确率,并按照2次/月的比例收集不良/良品,进行检查漏失率的判定,进一步提升iqc检查人员的检标准判断力和检出率! 1.为什么不能及时回复?原因:不重视?能力不足?沟通不畅?...... 2.为什么会有重复不良?原因:制程无法改善?供应商把不良再次塞进来?..... ...................... 多问几个为什么,对症下药是良策.须知你还是只是在面试阶段,如果都像你这样说的,通知采购,撤销资格就好了。。谁都会的事情,还要你来做什么?请你来当老板,通知这个通知那个么?
答3:1.面对供应商8d老是不能及时回复如何处理? ---1)是否跟催,跟催哪个部门哪个人,怎么跟催,跟催是否有效?邮件和传真是不够的,电话要紧; ---2)8d的投诉是否定义清楚,在接收范围内的产品更换投诉,很让供应商接受不了; ---3)我通常喜欢每2h跟催一次,一般在电子邮件的跟催中会注明“几点回复,在线等”之类的词语
作为sqe你要清楚supplier为什么不回报告,是厂商能力不够找不到原因还是别的原因?
厂商出现同样问题,首先你要知道为什么会出现同样的问题,你如何去辅导厂商改善?如果出现同样的问题就换供应商那么sqe的价值从何体现??? 3.面对供应商抱怨退回不良混有制程造成不良如何处理? 4.针对iqc检验员针对同一材料不良判定标准不一致时如何处理?
这2个问题属于公司管理及检验人员的能力问题。。要想解决这2个问题首先得从公司的流程上着手,为什么生产部会将不良品混入??(管理问题,iqc在确认问题时为什么不能确定是否是制程造成??)
检验员为什么标准不一?(工程师给的标准是否正确??检验员的能力是否达到要求?)
1、2是外部发生问题时的解决方法。
3、4是内部发生问题时的解决方法。
面试官是希望借此了解你的管理思路,以及管理经验。
在这两个方面做回答,就不会太离谱了。 3.面对供应商抱怨退回不良混有制程造成不良如何处理?
退回供应商的产品有制造造成的还好说,最糗的是退给a供应商的产品里面居然有b供应商的产品
1)肯定是要求供应商配合消化的,同时,也要知会采购,由采购施加压力给相关部门来解决;
2)这样的事情发生会降低在供应商心中的地位,如果有流程或足够的人力,退回产品在交给供应商之前,品管需要介入确认; 3)要了解制程是怎样造成的异常,在哪个产品哪个工位,产品的浪费也是时间的浪费,如果制程造成的异常ppm过大,有必要提交给pe,共同对工艺进行提案改善; 4.针对iqc检验员针对同一材料不良判定标准不一致时如何处理 ... 1)如果是尺寸的问题,在相同的仪器上要求共同测量来确认,确认是仪器误差?手法?方法?
2)如果是外观问题,找标准源。没有标准源的,找以往的发生处理史。有标准的,看标准的订定是否通俗易懂便于操作,不方便执行或确认的标准马上修订。 1.面对供应商8d老是不能及时回复如何处理? 2.面对供应商进料检验老是重复出现同样不良如何处理? 3.面对供应商抱怨退回不良混有制程造成不良如何处理? 4.针对iqc检验员针对同一材料不良判定标准不一致时如何处理? 1.若供应商及时采取了改正措施,那么8d报告延期报告可以容忍,若既未采取有效措施,也未回复8d报告,则需你制定督促计划,定期督促,特别是纳期的前1日必须督促。 2.视问题的严重度处理。轻微的不影响技能及关键外观的可以给予特采。否则,保留屡次不良样品,邀请其担当甚至管理者来出差确认,限期改善,如不改善则给予一定惩罚。 3.一般来说,制程中造成的不良,分贵重部品及便宜部品两种。贵重品供应商不会接受不良费用的,要自己消化,因此需要加强制程人员教育,改善制程方法,以减少或避免发生同类问题。便宜部品可以稍微给供应商施加压力,要其接受处理,同时也要邀请制程管理者检讨内部改善措施。 4.此种情况我认为多数属于外观问题。可以制作不良样品展示台,给予检查员进行教育。必要时邀请相关责任部门开会,协商制定限度样本,作为比较检查
作为一个sqe来说,这几个问题肯定经常遇到,个人意见如下:
1、8d不能及时回复,首先需要在开出8d报告的时候了解供应商产生不良的原因可能在哪些方面,需要多少时间作出相应的改善,不能一概而论,在开出8d前与供应商沟通改善需要时间,并在8d上提出要求,形成跟踪表格,及时与供应商沟通完成情况,并在必要时到供应商现场指导。这样8d基本上能按要求回复。
2、老出同样的不良,首先我们需要跟供应商一起分析产生的原因,只有找到了真正的原因,他们的不良品才有可能消除,但如果暂时无法找到原因,可以考虑要求供应商运用检验等方式将不合格品选出。而且相同的不良出现多次,肯定会形成8d报告,要求其做分析,当然要与供应商一起分析,帮助其改进。
3、第三个问题一般情况下可能有些比较难判断,因为有部分物料不良造成的返工替换的物料可能让供应商感觉是制程不良,需要跟供应商解释清楚,同时共同分析产生这种情况的原因。如果是制程人员因素,我们要做内部沟通。与供应商之间的关系是互利共赢的关系,不能因为小的利益影响公司的形象。
4、检验员之间的检验标准有差异,这个大都是检验作业指导书不完善,培训不到位造成,可以考虑修改相
应的作业指导书,图文并茂,加强iqc员工的培训,初期可以考虑发现问题由工程师判定。
1、建立供应商管理动态台帐,记录台帐,进行扣分;
2、加大考核和沟通;
3、加强退回产品件的管理,包括标识,判定等;
4、同意判定标准,要求qc按标准判定。 1.面对供应商8d老是不能及时回复如何处理? 1.确认你所跟踪的人是否对?邮件通知是远远不够的,最重要的是电话。如果多次供应商多次没有反应,可以多次逐级发给供应商的上层领导,给于施加压力。 2.面对供应商进料检验老是重复出现同样不良如何处理?
到供应商处检讨相关问题,对于这种缺陷供应商制造过程的他们是否找到真因(可以采用缺陷再现)?预防措施是什么?纠正措施是什么?两者有了,执行状况如何?(经常性的飞行检查),退一步就是制程产生了,供应商如何保证不良品如何不流到公司?(查阅供应商相关的标准和流程,控制手段)一般重复出现大部原因是系统有问题。 3.面对供应商抱怨退回不良混有制程造成不良如何处理?
确认问题是否属实,制定好本公司不良品的管理文件,也应该给供应商一个合理的解释。不然经常发生此类问题是很下面子的事。 4.针对iqc检验员针对同一材料不良判定标准不一致时如何处理?
尺寸问题很好解决,主要是量具是否有问题?人员的操作手法是否有问题?找到问题后对症下药。
外观问题,标准是否明确?标准是否量化?有没有签定缺陷样品,极限样品?可以作一个外观grr的培训计划。 1.面对供应商8d老是不能及时回复如何处理? 2.面对供应商进料检验老是重复出现同样不良如何处理? -->公司应该有程序明确怎样评估/处理这种质量不能保证的供应商, 不是讲究pdca持续改进嘛,供应商不a的话,只好找新供应商代替它,
如果因某种原因不暂时取代不了,只好反复催促了。
我们的做法是先通过打电话/邮件催促,追不到要求供应商过来面谈,
再不行亲自去供应商那里,双方面对面商讨都是一个很有效的途径。 3.面对供应商抱怨退回不良混有制程造成不良如何处理? ->先与供应商确认这现象,属实的话就好办了,谁出错谁负责。 4.针对iqc检验员针对同一材料不良判定标准不一致时如何处理? ->分两种情况:
a.检验标准订的不合适,修订标准; b.检验员素质/技能问题:培训/教育,再培训/教育......直到他/她胜任或离职。
问:若遇到客户投诉在产线发现你们产品批量不良你是如何处理的? 问:直接打断我~~~~~~~~~我是想问你如果碰到产品在主机厂装配线上发现问题了,同时同批产品已有部分篇3:sqe面试经典问题答案
今天去面试sqe了,共有两个面试官一个是科级(section chief)的、另一个是经理(manager)级别,开始先介绍一下,过去从事的工作及主要内容,谈谈心得体会,接着科长开始发问,下用s表示科长,m表示经理: s:谈谈对sqe主要职能职责的理解。 s:做为sqe你去开发一家供应商,现有两家供应商供你选择,第一家,产品质量符合公司的产品要求,但价格偏高;第二家,产品质量低于公司的产品要求,但价格低可接受。 s:你管理的供应商的产品在生产线上出了质量问题,做为sqe你在如何去处理。 s:案例——本公司有一家供应商是独家供货的,且没有潜在供应商,供y产品,现y产品出现质量问题且会影响产品质量、顾客满意,y产品因工艺缺陷导致的问题,即使是个没有专业知识的普通顾客也能看出问题的存在,且问题不可接受。该家供应商不愿对此问题做出处理,你作为sqe该如何去处理这个问题。 s:现在你已面试成功了,作为一名新手sqe,你又是学质量专业的,从质量专业角度谈谈你该如何去做去展开工作,使自己在这方面做的更出色。
上述为科长的提问,下接经理m的提问: m:本公司现有一产品安装了某公司的t产品,但因t产品的某一质量问题x导致本公司的产品在市场上频繁发生仪表功能失效,顾客抱怨较为强烈,且这一问题困扰公司已十年有余,问题改进了,段时间内消除了,可过不了多久就又会出现,同一问题反复发生,做为sqe你该如何去处理这个问题呢,并杜绝问题的再发生 s:谈谈对sqe主要职能职责的理解。 sqe,顾名思义,主要职能就是管控供应商的来料质量,确保其能符合我们的采购需求,保证我们的生产顺利进行。为了达到这一目标,必须要保证供应商方面生产的稳定,包括良好的质量管控体系,健全的反馈制度和持续改善的能力。至于怎么去保证,就得看sqe,有没能力发现他们的潜在隐患并帮助他们提升改善。 s:做为sqe你去开发一家供应商,现有两家供应商供你选择,第一家,产品质量符合公司的产品要求,但价格偏高;第二家,产品质量低于公司的产品要求,但价格低可接受。 单纯从品质角度,当然是第一家,但往往公司更多考虑成本是否太高。因此,这时最好的办法是两家同时引入,采取二八方法,价格高的给予80%订单(因为另一家的产品质量是不符合产品要求,不可能大量采用他们的),同时以它的质量标准衡量另外一家供应商,督促其进行改善。并许诺改善后会逐步把订单向他们转移。(事实也应该是这样)
然后,就该sqe出场了,可以采用多种方式,包括5why,5w1h等方式,帮助供应商找出质量低的根本原因。搜集统计数据(包括供应商内部出货前、来料后及上线生产时),找出不良的分布及规律,并去供应商现场作针对性验证,从人机物法环分别进行分析,确认是proce问题还是人为问题,proce是硬件问题还是流程设置问题。相信找到解决办法后,供应商会很乐意进行改善。
找出问题并得到解决后,再从根本上着手,帮助其完善质量管理体系,以避免类似问题再次发生。
s:你管理的供应商的产品在生产线上出了质量问题,做为sqe你在如何去处理。
1、马上赶到现场确认产线投诉是否属实,是否可以马上找到临时解决办法以免耽误生产。(一般情况下都有临时对策,只是可能会耽误了产能或提高了成本)
2、如实属且不能立即解决或让步接收,清查库存,换料生产,block住产线退料。召集qa及工程人员,对成品进行分析,是否可以放行。
3、对退料进行分析,初步确认root cause,是产线问题还是来料问题。并统计相关数据,例如来料原始不良率,上线后造成的不良率,及相关风险。保留相关样品。
4、马上通知供应商进行清查内部库存,保证下批来料不会再有类似问题。
5、要求供应商来公司进行确认并检讨,定下解决方案
6、如有必要,亲临供应商内部进行改善监督,密切跟踪随后的几批来料,确认问题得到改善。
7、要求供应商提供正式的8d报告,立档保存,以防再次发生。
8、与供应商谈判,承担相关的赔偿责任。 s:案例——本公司有一家供应商是独家供货的,且没有潜在供应商,供y产品,现y产品出现质量问题且会影响产品质量、顾客满意,y产品因工艺缺陷导致的问题,即使是个没有专业知识的普通顾客也能看出问题的存在,且问题不可接受。该家供应商不愿对此问题做出处理,你作为sqe该如何去处理这个问题。
出现这种情况,如果无法开展第二供应商的开发工作,那么就注定sqe局面很被动,处于弱势方。
1、实地考察,沟通,为什么供应商不愿对此问题作出处理,是成本太高还是技术达不到还是只单纯的怕麻烦?
2、到供应商现场进行验证,看在供应商最大努力程度下,产品质量改善到什么程度。是否可以让步接收。
3、无论结果如何,将此问题highlight给双方高层,并告知前面的结果。因为这已经超出了普通sqe所能决定的范畴。 s:现在你已面试成功了,作为一名新手sqe,你又是学质量专业的,从质量专业角度谈谈你该如何去做去展开工作,使自己在这方面做的更出色。
1、熟悉自己项目的质量要求
2、去产线(包括自己的和供应商的)多看多问多听,熟悉双方的生产状况及质量能力
3、动手统计管辖下供应商的过往来料质量情况,获得第一手资料,了解他们的质量状况。
4、查看管辖下供应商以往的产品质量改善报告,了解该供应商的改善能力
上述为科长的提问,下接经理m的提问: m:本公司现有一产品安装了某公司的t产品,但因t产品的某一质量问题x导致本公司的产品在市场上频繁发生仪表功能失效,顾客抱怨较为强烈,且这一问题困扰公司已十年有余,问题改进了,段时间内消除了,可过不了多久就又会出现,同一问题反复发生,做为sqe你该如何去处理这个问题呢,并杜绝问题的再发生。
首先了解是什么质量问题、严重程度、发生频率、不良比例。
然后搜集样本,取得实物,看是否有明显不良特征,能否通过什么方式进行sorting出来。 通报供应商,要求其技术及品质负责人过来开会,就以上的数据及实物进行分析讨论,初步判定问题是人为造成还是设备或流程问题,并确定改善措施和改善日期,同时对库存品进行sorting。
去供应商现场进行查看,对比改善前后,产品质量是否有明显提升。
要求供应商落实到文件,提供8d报告,并将实际操作规范化。 跟踪一段时间来料品质,时间至少是之前发生频率的两个周期,如果期间无此问题,可以close。如果仍有问题,则重复最后三步工作,直至找出root cause并解决为止。转载请注明出自篇4:sqe面试相关问题
公司最初没有sqe,后来从iqc抽出人来组成sqe,这个部门先后易主于采购,品保,sourcing。虽然sqe基本的东西都知道些,但是面试被问道这个问题,不知如何开口。how do you monitor & control your supplier? 从初选供应商-产品开发审核-进料监控-评级绩效管理-审核??还是举一具体例子来说明?这问题该怎么下手,求助xdjm!!!!!! 我的回答是这样,请各位看下是否enough 如果现在让我管理一家供应商,我首先会了解其现状然后再规划如何管理和monitor
一、了解现状: 1.了解品质状况:从iqc进料lrr 产线vlrr 厂商周/月报 的top3及action close statues 2.了解其组织结构及window 3.了解该供应商产品性能及我司对该材料的使用spec
二、对关键指标lrr vlrr定出target
三、control 及monitor 1.对各指标by week /daily review , review 未达成的原因及open iue追踪 2.audit 1) by case audit :对重大iue必须做对策落实度的audit 并协助厂商寻找真因,必要的时候对厂商人员做品质工具的training 及持续改善的、及品质的重要性等观念的宣导 2)yearly audit:对供应商的品质系统和制程做全方面的稽核,找出问题的隐患,协助提升供应商的品质系统。
四、与供应商做到良好的沟通,让他们认为sqe是帮助他们的,并且有任何事情第一时间
同时sqe也可以这样理解,是链接iqc与供应商之间的一个纽带, iqc同时意味着厂内,其实sqe管理最最根本的就是在厂外也就是供应商处将产生不良或者异常的隐患都解决掉,所以说主要的战场还是在供应商处,要对供应商进行稽核等动作,但是不可能所有的问题都能够做到预防,那么sqe同时也要对iqc的检验的重点进行管理及指导,
也就是说sqe要在供应商处将问题解决,一些解决不掉的或者不能够及时发现的需要iqc进行检验预防,一旦iqc检验出来的问题多了,说明sqe在厂外(供应商处)的管理已经失控了,如果说产线的vlrr超过了标准,那么说明sqe全部的工作失控了!!
同时对于sqe管理来说,标本兼治的方法就是对于供应商进行全面的管控,以求降低来料不良!!
上周去了某外企汽车公司参加了一次面试,apply for sqe,
面试中有两个问题比较tough: 1.你对于ppap的理解是什么? 2.你觉得在项目开发过程中,需要关注供应商哪些方面? 1,ppap,作为一种系统管制计划,其目的就是标准化。在一个新的vendor进来时,我跟你把这样的条条框框都谈好了,以后量产就拿这个去卡。行就pa,不行就reject! 2,无非是价格、品质、交期。但对于我sqe这个职能来说,品质是我最关心的。我会重点考查vendor在材料控制、制程控制、出货控制方面的水平,以及应对突发性批量性异
常的处理能力。
各位好,前几日去一汽车零部件公司面试,当时被问到该公司质量经理这样一个问题。想听听各位的分析和建议。
问:若遇到客户投诉在产线发现你们产品批量不良你是如何处理的? 答:由于小弟所在公司碰到此类情况极少,并且偶然发生的几次都是在客户aql时发现。我就以自己处理的实例回答如下:
紧急措施先立刻给客户换货,并且出具检验证明,保证此批产品无类似问题。接下来我司仓库库存同批号零件数量极少,因此直接报废,请顾客邮寄不良品分析。自查根本原因,过程是否有失控,流程是否变更等,再查供应商原因等等等等。
问:直接打断我~~~~~~~~~我是想问你如果碰到产品在主机厂装配线上发现问题了,同时同批产品已有部分进行了装车销售,并且已有终端客户反馈部分产品出现问题,而且分析是由于已方供应商问题造成,而客户是不可能等你很长时间的,那对于这样的情况你如何处理?已经装配好的产品?销售的产品?未装配的产品?我想听到对于风险评估,质量工具运用,三方沟通协议等等等等方面
当然最后这个问题问好,该质量经理,也稍微为我解了下围,说毕竟不在汽车行业,而且也年轻,多接触就好。
这个问题虽说不了了之,但我始终让我有点郁闷,想请教各位同仁前辈,遇到这类案例,你们一般是如何处理的,尤其是针对主机厂问题的临时措施。
非常感谢
1.先停产。不能停就先停止出货。厂内产品全部pending。 2.评估风险--采购,质量,工程必须参与,甚至还包括你的供应商。必须确认以下的问题:
嫌疑品的范围;问题的严重程度;已出产品客户端的解决方案;已流入终端市场的产品的解决方案。 3.真因分析,改善措施8d。
当产品在客户端,甚至市场上整批出问题的时候,可以想象这是非常严重的状况了。你公司的质量经理应该马上到整车厂去报道,首先想到的是风险评估和应急措施。而且,你的所有措施都必须经过客户的批准。你的任务就是提出客户能接受的解决方案,并且这个方案应该是让你公司的损失降到最低的方案。如果是你供应商的问题,那么你也应该把他拉进来参与整个的过程。所有的人都必须动起来。如果按8d来走的话,相当于把8d拆分成一个个步骤,每个环节都反复研究,修改,得到客户批准。如果按你说的做,那真的是找死的行为,立马会触怒客户。你的什么保证函之类的都是垃圾,还要等客户寄样品更是找死,要马上去客户那里,带着应急方案去,和客户讨论,客户让给什么就给什么,同时厂内,供应商那里立即开始找真因,查产品。看看丰田是怎么死的,就是因为东西在终端市场出了问题,而且造成客户死亡。这种情况下,你看看你的措施,怎么能说服客户?
我觉得提问者想考查处理问题的思路,当有客诉问题时,如何分清先后次序处理,目标应该
是尽可能降低客户及本公司的损失。 建议答案如下:
总方针时可能降低客户及本公司的损失。 1.确认清问题点,及客户方发现的不良率,当前客户方如需确保不停拉,需要多少良品。 2.弄清本公司当前的生产状况,如正在生产当中,通知相关人员此投诉信息,马上对应措施。
3.清查本公司当前良品的库存,是否足够满足客户需求。 4.如转拉生产此款产品,需多久才能交货。 向客户反馈本公司的现状,以达成共识。
对已在客户方装配完成的成品,看客户方想如何解决,一般地要找出根本原因,再分摊成本,或是否之前相互间有此方面的协议。
这是q职业人员必需要考虑的事情;考验你的思维逻辑,以及将你自己定位在哪个层面(公司or客户)个人处理方案如下: 1.临时处理方案: 优先考虑客户端,在允许的情况下不影响客户的生产或者出货;如:小批量的重工(考虑在公司还是在客户端)满足客户需求;其它部分(在途中,在制品,仓存品)需要给客户或者公司取一个最低成本的处理方案,不良品的处理需要公司所有有关部门参与,讨论方案各负其责。
2.长期措施
即回复客户公司是如何改善该不良以及预防类似不良的发生,以及提供改善验证证据或者验证数据说明问题已经解决。
我给你举个例子吧。3年前我在某t1公司做sde的时候,某次我公司一个产品在德国主机厂做可靠度实验时候发现不良,而该不良在正常检验时候不能保证100%检测到。该不良在终端客户使用时可能会造成人身安全问题。客户第一时间停用我公司的该款产品,然后要求分析,同时将样本送第三方分析。我公司技术部门和第三方机构分析结论一致,问题是pcba上某个芯片不良造成的,属于零件质量问题。该产品为我公司美国rd设计,由中国的某家ems厂代工做smt和组装。在此情况下,客户同意改为我公司西班牙分公司做smt组装出货,中国分公司的产品不能出货。然后我就被丢到广东那家ems厂去待了1个月。每天早上和美国总部开会,下午和德国分公司以及客户开会,其他时间就和供应商开会。每天都在供应商的车间里面转来转去,看他们的分析报告,提出问题和意见,follow up所有的open iue,整理报告,doe,第三方检测,金相分析,重工方案的提出,什么都做.还要当心哪些是我能说的,哪些是要让ems厂说的... 在这种时候,你说的每句话都要当心,有些东西只能你知道,有些东西只能你和ems厂知道,有些东西只能你和客户知道,有些东西ems厂知道,他不会说,但是你知道,有些东西ems厂不会说,估计你也不知道.最低层的工兵想的只是发现真因,改善问题。但是从一 开始,从公司层面上,早已成为了政治问题。我们的东西会不会被客户要求全部退货,已经出去的产品会不会被召回,所有的损失能不能charge到我们的供应商身上,这家ems供应商后续还能不能继续供货,这个生意被西班牙分公司接过去了,以后中国公司能不能再接回来。。。等等等等,每天大家都在不停的拨算盘,包括ems供应商,客户,每一方都有自己的算盘。这就是那个质量经理问你的三方协议。
所以不要说sqe就不会面对这些问题,sqe一样的会被丢到前线去打仗,甚至还要面对客户。这种时候往往没有什么流程“程序,只有靠你自己的判断能力,专业技能,沟通技巧去解决,而且你还要在其中保护好自己,努力的不要变成众望所归的炮灰。我想,那个质量经理问楼主的问题,应该就是考察这方面的能力篇5:sqe面试题目 1.作为一个sqe,你能简单介绍一下你的工作职责吗?
1、sqe负责保障供应商所供原材料的质量,在进料检验、生产过程检验、客户抱怨等,只要是由于供应商供货物料质量缺陷引发的,都要及时反馈供应商要求其改善;
2、sqe负责追踪确认供应商的改善报告(8d)及实施效果,必要时可进行现场审核检查;
3、sqe负责制定进货检验部门(iqc)的检验规范及检验计划,并适时对检验员进行培训指导;
4、sqe可以参与供应商初始样品的评估放行工作;
5、sqe每个月或每个季度,对现有供应商的质量状况进行统计评分,对评分较低的供应商提出限期改善要求;
6、sqe参与新供应商开发与审核,与采购、研发部门一起对新供应商进行考核打分,确定其是否可以成为合格供应商 2.针对供应商质量问题,在实际工作中你是如何解决的,举1,2个例子说明? 1.新供应商管理: 1.1选择新供应商后先对其进行qsa(品质体系稽核),通过管理职责、资源管理、产品实现、测量分析与改进四个方面确认供应商体系运行状况; 1.2qsa通过后要求供应商送样承认,承认合格后则在供应商进行小批量试产时对进行qpa(过程及产品稽核),过程稽核则通过供应商的控制计划对供应商的生产过程一一确认并找出薄弱部分,要求供应商提出改善计划;产品稽核则按其检验标准对其所生产出的产品进行抽样确认;
2.常交货供应商管理: 2.1来料品质异常处理,向供应商发出scar(供应商改善报告),并进行追踪与确认; 2.2每月对供应商进行考核,考核项目主要是q(品质)、c(价格)、d(交期)、s(服务); 2.3较差供应商现场辅导;
2.4供应商年度评估等。 3.如何综合全面的管理和评估供应商的质量,你有社么方式和方法? 4.如何持续的改善供应商的质量,你运用社么样的方法来实现? 5.针对新的供应商,你是如何导入的?
简单的质量知识: 1.你了解fmea吗,说明o,s,d, rpn是何解释,举例说明fmea? 失效模式及后果分析(failure mode and effects analysis:简称fmea):指一组系统化的活动,其目的在:1)找出、评价产品/过程中潜在的失效及其后果;2)找到能够避免或减少这些潜在失效发生的措施;3)书面总结以上过程,并使其文件化。为确保顾客满意,fmea是对设计过程的完善 fmea主要是将其作为一种控制工具和/或风险分析工具和/或管理工具运用在下列活动中:
1)设计控制;2)生产计划;3)生产控制;4)分承包方的评选和供应商的质量保证;5)冒险分析;6)风险分析;7)召回产品的评估;8)顾客运用;9)说明书和警告标签;10)产品服务和保修;11)工程更改通知;12)制造过程的差异等。 2.spc, 有那些控制工具,各使用在何场合,cp,cpk;cpk, ppk的区别? ①在cp、cpk中,计算的是稳定过程的能力,稳定过程中过程变差仅由普通原因引起,公式中的标准差可以通过控制图中的样本平均极差估计得出。
因此,cp、cpk一般与控制图一起使用,首先利用控制图判断过程是否受控,如果过程不受控,要采取措施改善过程,使过程处于受控状态。确保过程受控后,再计算cp、cpk。 ① 无偏离的cp表示过程加工的均匀性(稳定性),即“质量能力”,cp越大,这质量特性的分布越“苗条”,质量能力越强;而有偏离的cpk表示过程中心μ与公差中心m的偏离情况,cpk越大,二者的偏离越小,也即过程中心对公差中心越“瞄准”。使过程的“质量能力”与“管理能力”二者综合的结果。cp与cpk的着重点不同,需要同时加以考虑 ②由于普通和特殊两种原因所造成的变差,可以用样本标准差s来估计,过程性能指数的计算使用该标准差。
“所谓ppk,是进入大批量生产前,对小批生产的能力评价,一般要求≥1.67;而cpk,是进入大批量生产后,为保证批量生产下的产品的品质状况不至于下降,且为保证与小批生产具有同样的控制能力,所进行的生产能力的评价,一般要求≥1.33;一般来说,cpk需要借助ppk的控制界限来作控制一个将cp和k(表示流程平均值与上下限区间平均值之间的差异)结合起来的流程能力指数,它用来确定流程是否将在容忍度范围内生产产品,cpk通常要么比cp值小,要么与cp值相同。”
在一般的qs9000或ts16949推行过程中,ppk用来表示短期能力指数,cpk用来表示长期能力指数。但是受知识所限,我本人没有看到这方面的权威资料。这位网友的帖子上面也表达了两种不同的观点,而且这两种观点近乎对立。我本人认为,从ppk的计算公式中使用的 分析,ppk表达的应该是一个包含引起变差的普通原因和特殊原因的过程。这样的过程其实就是一个非受控过程,而一个非受控过程在理论上应该是在过程初期和长期过程中都会遇到的 3.简单说明iso9000/ts16949的八大原则? iso9000:
1、以客户为中心
2、领导作用
3、全员参与
4、过程方法
5、管理的系统方法
6、持续改进
7、基于事实的决策方法
8、互利的供方关系 4.举一个例子说明如何完成gr&r? 5.你对6sigma有多少了解,概述一下6sigma,举例说明假设检验和doe. 假设检验:常用的假设检验方法有u—检验法、t—检验法、x2检验法、f—检验法,秩和检验等。
(一)根据所研究问题的要求,提出原假设 和备择假设 。
二)找出检验的统计量及其分布。
三)规定显著性水平,就是选择发生第一类错误的最大允许概率。 doe是试验设计,是指通过优选选择对参品特性影响比较大的各相关参数,确定那些因素重要那些不重要,还有每个因素取什么水平为好;各个因素按什么样的的水平搭配起来是产品 特性指标较好,这就是试验设计。说白了就是考察影响产品特性的各个参数,确定什么样的参数组合些产品特性最好。 design of experiments 我的回答是这样,请各位看下是否enough 如果现在让我管理一家供应商,我首先会了解其现状然后再规划如何管理和monitor
一、了解现状: 1.了解品质状况:从iqc进料lrr 产线vlrr 厂商周/月报 的top3及action close statues 2.了解其组织结构及window 3.了解该供应商产品性能及我司对该材料的使用spec
二、对关键指标lrr vlrr定出target
三、control 及monitor 1.对各指标by week /daily review , review 未达成的原因及open iue追踪 2.audit 1) by case audit :对重大iue必须做对策落实度的audit 并协助厂商寻找真因,必要的时候对厂商人员做品质工具的training 及持续改善的、及品质的重要性等观念的宣导 2)yearly audit:对供应商的品质系统和制程做全方面的稽核,找出问题的隐患,协助提升供应商的品质系统。
四、与供应商做到良好的沟通,让他们认为sqe是帮助他们的,并且有任何事情第一时间通知
做sqe感觉重要是要思路清晰
面试的时候可能他会问你以前是否做过稽核,稽核了哪些项目
你多了解点这家公司的产品, 会涉及到哪些加工技术 ,如smt 他还会问你如果某种情况发生了,你如何处理. 比如:供应商即是你的客户指定的,又是你的竞争对手,你如何处理他造成的质量问题
你去的港企,应该对外语要求多些,多准备点
如果又要懂体系搞审核,又要懂技术确认过程,还要英语,这才是高工资工作。 1.你认为成为优秀sqe的基本条件有哪些? 2.sqe工作的重点是什么? 3.sqe工作的难点是什么? 4.如何面对屡教不改的供应商? 5.如何处理独家供应商? 6.如何现场审核供应商? 7.请制作现场审核时间安排表. 8.sqe应用哪些统计工具? 9.对于供应商不接受的退货如何处理? 提供确凿的证据,争取货源部门的支持,通报后直接扣货款,通知通知高层推动,开发
更多供应商。
10.供应商不同意的现场审核不合格项怎么办? 网友增加的问题: 11.sqe工作职责介绍. 12.sqe如何处理好与供应商、公司采购部、iqc三者之间的关系? 13.你是否对本公司产品所用元器件的生产的流程和产品工艺熟悉? 14.sqe除了良好的基本技术外,还需要哪些技能或素质?(良好的沟通能力 不断的自我提升能力) 15.说说你认为最得意的一件事出来,为什么? 16.你對品質差的供應商是如何進行輔導的,效果如何? 17.你认为稽核供应商哪些方面最重要? 18.对供应商应该采用什么样的方式来管理 19.针对多品种少批量的供应商你如何处理? 20.怎样提升作坊式的供应商能力? 21.你是如何在供应商与公司之间做到公正公平的? 1.你在看供应商的系统会按照checklist一条条看吗? 2.你在看供应商系统时有视觉疲劳吗? 3.你在看供应商系统发现问题时有成就感吗? 4.你看制程会专注于sop吗? 5.你看制程时会注意到参数吗? 6.你会关注制程特性还是产品特性,还是兼顾? 7.第6项的spc你会看到吗? 8.无论什么产品的制程你都可以看吗? 9.是不是看制程只剩下制程的概念,不论电的还是机械的产品? 10.你评价一个供应商需要多长时间? 很好的问题, 不过如果按照checklist 去审核供应商的sqe还不能称之为sqe,只是一个供应商的过程检查员而已,应该在openning meeting之前将自己的审核要求,审核范围,审核时间安排,审核的次序,主要关关注点,希望陪同的人员,文件与记录的提供等等一系列的向供应商的参会人员介绍清楚,最好能够在发出审核要求的同时将上述用邮件方式通知供应商,让供应商充分了解您此行的目的,审核人员,和具体的时间车辆吃饭等的安排一一交代清楚,这样的做法的好处是节约了别人的时间也省了自己的麻烦... 其次,一个成熟的制造企业,必然会有sop也就是所指的标准作业流程,操作,培训,检查,记录等,文件与操作与良录的一致性,只专注于以上任何一项都只能算是走马观花,不能深入的发现问题并寻找解决的方法,当sqe去审核自己的供应商,不只是去找几个问题,再按照checklist 打分再交个差就行了,更主要的是要找供应商不能发现,或已发现但没有动力/意愿去改善的问题,然后与供应商一起寻找改进的方法或紧密的跟进,过程问题少了,质量问题自然也少了,成就感也就自然而然了?? 关于审核供应商的时间长短问题, 之前dell的sqe也问过我, 一般审核一个供应商需要多长时间? 答案当然不是统一的,通过在审核之前了解: 1.该供应商的过往业绩和质量状况, 2.零件的复杂程度 3.零件的可制造性 4.供应商的品牌情况 5.供应商的客户群
6.供应商所取得的认证情况 7.该供应商的行业的地位
8....... 还要看审核的目的: 1.体系审核 2.过程审核 3.突发问题审核 4.iue 审核
6.质量会议跟进的审核
7.还有其它约定的例行审核
要想当好sqe,个人认为一下10 1.、正直,一身正气!
2、良好的沟通技巧(对供应商要换位思考,对公司内部要坚持原则,对客户不卑不亢),良好的英文对话能力
3、熟练掌握审核技巧(iso900
1、ts169
49、rohs、reach)
4、知识面广,熟知生产工艺以及相关工艺参数(冲压、注塑、挤出、机加工、铸造、锻造、组装、pcba制造、焊接、热处理、表面处理,如喷漆、喷粉、电镀、喷丸)
5、熟知生产工艺中的质控点、时时把防呆放在心中!绝不依赖目视全检!
6、良好的时间管理、需要同时、及时处理多件事情!
9、丰富的解决问题的能力,正确的8d思路cad,机械,技术,汽车,catia,pro/e空,镇江- h7 r- [- ?# @0 r3 t4 p
10、lean & 6 sigma 的基本知识
的改善,而sqe主要在供应商端,由qe转为sqe , 必须要做的事情如下: 1.了解供应商管理的流程和kpi.2.供应商的选择和qualify.比如:供应商评比,survey,稽核等。 3.供应商制程和产品的key point,qc flow chart.4.了解供应商一年内的buglist . 5.任何事情必须追到至少5个w.且一直要坚信:没有什么是不可能。 从事sqe工作半年了,一套工作经验渐渐成形。结合网上收集的资料,放在坛子里以让sqe新人参考,让行内高手指教。
一.绩效: sqe的使命就是通过对供货商的质量管理,以保证来料的质量。因此减少客诉和漏失率是sqe绩效的主要反映。
第15篇:SQE工作内容
SQE工作内容
SQE供货商管理工程师(Supplier Quality Engineer)
1、SQE负责保障供应商所供原材料的质量,在进料检验、生产过程检验、客户抱怨等,只要是由于原材料质量缺陷引发的,都要及时反馈供应商要求其改善;
2、SQE负责追踪确认供应商的改善报告(8D)及实施效果,必要时可进行现场审核检查;
3、SQE负责制定进货检验部门(IQC)的检验规范及检验计划,并适时对检验员进行培训指导;
4、SQE可以参与供应商初始样品的评估放行工作;
5、SQE每个月或每个季度,对现有供应商的质量状况进行统计评分,对评分较低的供应商提出限期改善要求;
6、SQE参与新供应商开发与审核,与采购部门一起对新供应商进行考核打分,确定其是否可以成为合格供应商。
SQE工作职责说明
1.推动供应商内部质量改善
1.1 推动供应商成立完善的质量保证小组.
1.2 供应商过程变更及材质变更的确认管控动作.
1.3 新材料及变更材料的管控.
1.4 推动厂商导入常用的质量体系如,SPC, 6Sigma 等品管手法。
1.5 材料质量目标达成状况的改善及检讨。
1.6 不合格项目的改善确认动作。
1.7 材料异常的处理及成效的确认。
1.8 新产品导入阶段的供应商管控
2.推行执行SQM的系统程序文件.
2.1 供应商的评监,择优选择厂商。
2.2 供应商的定期及特殊审核的执行。
2.3 供应商的辅导,提升质量。
2.4 执行供应商的奖罚措施。
2.5 建立完善规范的材料作业指导书
3.1 每月的供应商等级评比。
3.2 每年的供应商等级评比。
3.3 供应商MBR, QBR 会议的召开。
3.4 8D Report 的发出及时效管控及改善效果的跟进。
3.5 供应商质量月报,FAR 报表,信赖性报表的跟催及确认
供应商例行绩效评估和audit.
导入新厂商阶段,一般有PUR/RD/SQM/ESH部门共同参与,SQE此阶段需要做的是让supplier提供供应商调查报告及工厂内部组织架构等等大项,此阶段主导者应该是PUR.
针对这些站别,总结起来,按照人,机,料,法,环五项,集合公司的QPA checklist进行audit.
人, 1.1 training 1.2 comply with WI(work instruction) & SOP
机, 1.3 machine maintained 1.4 measurement/tool 精确度
料, 1.5 区分隔离 1.6 保存期及保存方式
法, 1.7 traceability&Identification 1.8 SPC, FAI checklist
环, 1.9 ESH 1.10 温湿度
2.对供应商QSA(quality system audit),通过对supplier系统面的audit,是希望指出supplier在整个面上的不足,一般来说,SQE主要1.1 document management
1.2 供应商之supplier的管理.
1.3 product identification & traceability
1.4 Proce control
1.5 检查和测试管理.
1.6 Calibration
1.7 Nonconforming product control.
1.8 handling, package, storage and delivery
1.9 Record—这一项适合所有的audit items.
3.GPA(Green product audit),目前很大部分公司已将此audit纳入QSA中,在这我就不细谈了.但重要的还是离不开如下6点:
1.1 GPA的文件规范系统.
1.2 Proce management system
1.3 training
1.4 supplier’s 外包管理
1.5 EC管制
1.6 检验和分析.
第16篇:SQE 工作经验浅谈
SQE 工作经验浅谈!
2007年05月17日 点击
: 17578 编辑
: jevonsge
本人2003年毕业后,鬼使神差般地进入了Quality这个领域,一直从事SQE工作也有近4
年的光景,今天把自己的一些做事方式,态度及SQE的职责show出来,供同行和外行加以褒贬,让自己吸取更多的精华,剔除糟粕.
备注,我所负责的材料主要是EE(PCB/FPC/PCBA/FPCA,RLC 及connector),所以下面很多的工作经验之谈是站在EE这个面展开的,不过,相信对于负责其他材料的同仁还是有一定的帮助的,毕竟SQE是技术及管理共存的一个职业.
当然,在此show出这么多个人经验之谈,也不乏有推荐自己之意,我相信我绝对是适合的人选。
一,绩效--就是通常说的KPI (key performance indictor)
一般来说,衡量一个SQE的指标,主要有abnormal cases, customer complaint, LRR(lots reject rate),SQE的使命是通过对供应商的品质管理,以保证材料在公司的正常生产,所以很多时候,老板总以abnormal case来衡量SQE的performance.
但事实上,个人觉得真正衡量SQE的ability应该是supplier 8D回复的时效性及有效性,之所以这样说,是因为材料的特殊性,相信SQE同仁有同样的感触.
当然,有些材料本身supplier的sense或者其proce已经达到很高的水准,其品质面本来就很少出状况,来衡量管理这样材料的SQE performance,真的很难定夺,也许就是production的dppm trend chart 及service(training and so on).
二,职责(responsibility)
围绕保证品质来料这目的,SQE应负起如下的责任,
1.对供应商进行例行的绩效评估和audit.
2.品质监督和异常协辅
3.NPI(new product 导入)/ECN 变更时,供应尚制程及产品的确认,CIP的改善.
4.GP 产品及其管制.
针对以上四点,小弟我浅谈下我的经验,供各大侠指导.
1.对供应商进行例行的绩效评估和audit.
1.1导入新厂商阶段,一般有PUR/RD/SQM/ESH部门共同参与,SQE此阶段需要做的是让supplier提供供应商调查报告及工厂内部组织架构等等大项,此阶段主导者应该是PUR.
1.2对供应商进行QPA(quality proce audit),这需要依据具体的产品来衡量,但不外乎receiving inspection, warehouse, MRB, production line, rework proce, OQC and packing&store, record and so on.针对这些站别,总结起来,按照人,机,料,法,环五项,集合公司的QPA checklist进行audit.
人, 1.training 2.comply with WI(work instruction) & SOP
机, 3.machine maintained 4.measurement/tool 精确度
料, 5.区分隔离 6.保存期及保存方式
法, 7.traceability&Identification 8.SPC, FAI checklist
环, 9.ESH 10.温湿度
QPA的frequency,目前很多公司已经没有强制的定义,只要公司一出现比较大的case, SQE就驻厂,针对相关站别进行audit.事实上,这样做起来的确很有效果,SQE第一时间内了解到不良品,然后又第一时间内去
supplier端去audit相关proce,相信很大程度上能很快解决问题,使公司顺利生产,让supplier及时改善.
1.3对供应商QSA(quality system audit),通过对supplier系统面的audit,是希望指出supplier在整个面上的不足,一般来说,SQE主要audit的item如下,
a.document management
b.供应商之supplier的管理.
c.product identification & traceability
d.Proce control
e.检查和测试管理.
f.Calibration
g.Nonconforming product control.
h.handling, package, storage and delivery
i.Record—这一项适合所有的audit items.
当然事实上,SQE重点放在上面items外,其实还是有些需要audit的项目,比如quality system, contact review, 甚至设计管理.
一般来说,QSA一年一次.
事实上,真正反映supplier performace的是QBR 会议,参与部门有PUR, Technology and SQM,分数比例一般为PUR-- 35%, T-- 30% SQM -- 35%.
主要出发点 Pur—delivery/cost/service
T—technology share / service
SQM—quality iue/ service
Ps: sales 人员注意,客户的3个主要对外窗口都很注重service.
这样的QBR meeting一般有SQM主导,当然supplier参加的窗口也应该是对应的sales/T/QA(CS) 部门.个人认为后续product的竞争力应在品质上,所以站在SQE的角度上,我是希望SQM的比重可以适当加重.
1.4GPA(Green product audit),目前很大部分公司已将此audit纳入QSA中,在这我就不细谈了.但重要的还是离不开如下6点:
a.GPA的文件规范系统.
b.Proce management system
c.training
d.supplier’s 外包管理
e.EC管制(后面会细谈)
f.检验和分析.
2.品质监督和异常协辅
以abnormal case, customer complaint及LRR数据为基础,对厂商的品质异常,通过review其FMEA/8D report及改善效果的确认,以监督厂商的品质,同时辅导厂商的品质改善与提升.
对于品质监督,我很是赞同Baseline management,通过驻厂的方式,及时有效的audit厂商各站别的问题,同时给予厂商QA部门的大力support,提升其执行力.
个人很在乎的是能够很好的push supplier建立FMEA部门,这样做的好处如下:
对应supplier
a.但有异常发生时,能很快的组织起分析小组,尽快找到问题点,预防问题的进一步扩大,
b.很快的处理异常,以达到最低限度的减少损失,
c.buglist,作为经验的积累,方便后续品质的追踪.
d.能很大程度上消除公司”踢皮球”的坏习惯.
对于公司(customer)
a.defect sample分析的时效性得以保证.(8D cycle times)
b.SQE可以第一时间内,review8D report,可以很快的找到对应分析窗口.
诚然,FMEA小组的建立不能很快的让supplier看到自己利益的增长,但我敢保证FMEA团队绝对是supplier和customer 很好的沟通桥梁.由于FMEA团队的重要性,一般我都是直接找supplier site manager来谈,因为FMEA小组需要很强的技术分析能力,很好的工厂执行力及分析defect的仪器设备, 这些都需要site manager的大力support.
相信优秀的SQE能明白我的想法也希望能给相关同仁一些感触.
对于异常协辅,也许很多行外人觉得SQE的技术能力真的有那么专业吗?能协辅Supplier进行改善?诚然SQE是技术和管理共存的一个特殊的岗位,相信没有一定的技术能力是很难让supplier诚服的,也的确SQE没有supplier的PE在技术上的专长,但一般来讲,公司现在很少找单一source supplier, 所以SQE有更多的机会去借鉴不同的经验,各公司一定都有他的长处,我已经习惯将各厂商长处相联结,同时也习惯让supplier习惯我的管理方式.之所以说SQE能给supplier异常辅导,是因为各岗位人员看待问题不一样,PE可能想到了改善的方向,但出与cost的考虑,还是无法进行有效的动作.甚至一些品质iue的轻微改善,一些自工具的设计有可能,等等类似的问题.
总之,SQE会取长补短,集合自己的经验能有效的给出supplier改善的方向.
3.NPI(new product 导入)/ECN 变更时,供应尚制程及产品的确认,CIP的改善.
先来谈下NPI的管控.相信大部分的SQE有这样的体会,公司出现异常后,在最后root cause出来后才发现,原来这样的问题在试产阶段就已经存在,但种种原因,在没有得到解决前,此model已经进入量产阶段,这样以来,SQE就成为大家指责的重点,事实上,SQE会觉得很冤枉,因为,一般来说,试产阶段的iue都是有technology在负责处理,SQE也可能做部分的support,但量产材料一定是SQE在复杂,所以出现这样的问题,SQE做的事情,说的难听点就是在帮人家擦屁股,处理不好,其他部门就觉得SQE能力不够,处理完美,觉得这是SQE份内之事情.
)(这只是个人感慨,请勿当经验交流
所以,从上面的分析,出于对品质的保证,或者说对自己的保护,SQE介入NPI阶段是非常必要的.哪如何介入及介入后如何处理呢?下面细谈.
驻厂管理是必须的.
a.如何介入?
一般来说,SQE会和Supplier的QA召开周会或者月会,在该会议上,可以将new product review列为review项目.但,大多数公司,NPI主导者一定是Technology department,有时候甚至等产品量产后才notice QE department,所以,第一步,一定要让supplier Technology 部门只要有新产品导入就一定要知会到QE,但大部分公司的PE没有这样的习惯,因为他们的重点可能在技术的改善及提升.所以看似很简单的要求,但实际操作起来就不会那么顺利,所以SQE就要主动去找Supplier site manager去谈,只有大老板关注到这点,才有可行性.
这是SQE需要support Supplier QE的,记住,与supplier的关系不是指挥与被指挥的关系,win-win才是SQE的最终目的.
b.介入后如何管理呢?
一,part failure history/specific failure data
1.Review supplier new model status in quality meeting.
2.Review fails record and corrective actions.
3.EC list for new product.(in NPI period, according to customer requirement, maybe some have some EC)
4.Co-work with supplier’s PE&ME, planner, RD&IE departments, define the best parameter and define it into SOP.
5.Supplier IPQC should know these failures and audit proce according to them.
二,transportation readine.
1.Co-work with supplier related department or field standard, set up new model yield rate criteria.
2.5M checklist (manpower/machine/material/method/environment)
3.Document ready.(QC-FLOW-CHART,SOP,SIP and so on)
4.SPC review (dimension, optical, soldering thickne)
5.Golden sample management setup.
这些看起来很简单,但运行起来就是在考量SQE的技术含量和管理能力了.
比如,公司的采购一定需要supplier出新产品,但有些问题又没有解决杂办??
一般我采取的方式有,
1.告之公司T部门,有些问题还没有解决,你要试用出问题,你去处理.—比较坑人.
2.视异常而言,如一些外观问题没有得到处理,要求supplier加强全检次数,把不良卡在supplier端.
如为function问题没有得到解决,就直接要求停止出货.(当然,这需要SQM的大力support,如自己的老板也同意出货,相信真出问题,老板也不会怪罪到你.)
3.在新产品还没达到量产的水准及iue没有完全得到解决时,如PUR一定要使用,那就请PUR出特采.(一般来说,特采是PUR最不想的状况,因为责任别就在自己身上了).
有时,可能只有1pcs的不良,但此不良为zero defect items(EE material,一般为错件,漏件,极性错误),SQE就一定需要supplier找到问题跟源,在没有得到完全解决前,SQE就要拍板,不许出货.
接着来谈EC的管控.
EC有二种,VECA&VECN.
区别点在于VECA为supplier 提供给公司,VECN为公司发给supplier.
之所以将EC拿出来细谈是因为对于电子产品,cycle time比较短,EC的变更就比较多,而且很大一部分异常就是因为EC没有得到很好的管控.
谈及这方面的管控,首先要和大家有个共识,EC的窗口一定是唯一的,一般来说公司的EC窗口有二个,SQM及T, supplier端为QE及T.但大家也应该清楚SQM与外界的接触更多点,所以,在我以前服务的公司,EC窗口为SQM,对应的supplier窗口为QE,只有在EC窗口确定的情况下,EC才能得到很好的管控,不然,我相信很多公司会为这花费很大的精力去处理EC问题.
a.VECN 管控.
发起单位可能为T和SQM,一般来说,
T主要复杂normal的变更,比如从下个rev,需要增加个零件,象这样类似的变更.有T部门撰写,有SQE知会supplier.
SQE主要针对量产时候出现的一些iue,经过验证等,发现变更一些layer out能解决问题.这样类似的变更就有SQE主导.
b.VECA管控.
一定是supplier的QE提供给SQE.
VECA提出的items可能很多,
比如厂商一些重要制程参数的变更,生产地的变更,供应商的变更(second source导入).
针对iue, supplier验证一些数据,可能变更某些参数能很好的提升良率.
等等类似的问题,Supplier均需要提出VECA.
PS:VECA/VECN items 有些公司会规定的很详细.
谈到这点,接着就是变更的时间点要在document写的很清楚,很大部分iue就是因为EC的时间点不明确导致异常的发生.
VECN/VECA 时间导入有两种,
1.running change.(常说的限时导入)
2.cut-in change.
这就需要和PUR及supplier确认清楚product的数量,不然一定会出现问题.
备注:EC是一定需要用docement管控的,这对于SQM还是supplier都是一种保护.
4.GP 产品及其管制.
这点我就不细谈了,XRF等管理,更多的是IQC在执行, 主要的还是做到如上几点.
a.GPA的文件规范系统.
b.Proce management system
c.training
d.supplier’s 外包管理
e.EC管制
f.检验和分析
另再在此show下本人SQE职场性格,相信也是优秀SQE必备之能力。
1.良好的沟通技巧,与production及工厂内相关部门建立良好的co-work方式,使事事半功倍。
2.解析问题能一针见血,通过QC 7大说法,SPC管控等等分析技巧,review supplier 8D report.
3.处理事情及时,提高工厂甚至我们的客户的满意度。
4.熟悉ISO9000/TS16949/ISO14000等各要求,熟练使用在audit supplier。
5.本身逻辑思维性很强,能深辟的看待问题。
6.在供应商管理方面,强势的管理方式能很好的领导supplier 品质的提升,当然同时会吸纳supplier的一些宝贵的意见,使工厂和supplier doube win,很强的独立处理事情能力。
第17篇:SQE年度工作总结
个人工作总结-2013年度
时光荏苒,公司又走过了一个辉煌年。回首2013年,我在公司及部门领导的指导带领下,在各位同事的协同下,基本完成了各项任务。主要工作有: 1.通过反复的调试比对超声波和热熔机,完成了b客户表贴式和嵌入式按钮线路板熔接保持力的问题,使量产产品的线路板保持力符合要求,解决了客户飞检投诉的问题。 2.优化并发布了供应商索赔制度,同时完成了供应商的索赔工作,全年索赔共计约合人民币21万多元。
3.参与新开发的北美项目的第一阶段任务,一周内指导供应商完成ppap资料31份。 4.从6月份起,给三家零库存供应商制定了改善辅导方案和计划,定期辅导,并定期监督检查完成状况。通过此次辅导,各家供应商在管理流程上有了初步改善,都已经建立了专职检验员制度。其中甲供应商连续三个月的fpy和otd都已达标。 5.与技术工程师和采购同仁一起,对乙供应商(pcb板供应商)进行多次审核,帮助其查找问题,验证其纠正预防措施的有效性,减少生产对原材料的投诉,保证公司产品按时保质出货。
6.与质量工程师一起,通过对供应商的多次审核辅导,帮助他完成按钮组装的可量产化工作,完成了公司产品外包的工作。
此外,我还能积极参与公司组织的各项理论和专业知识培训,为后续工作能更好的开展打下铺垫。 过去的一年里虽然取得一些成绩,但也有需要提升的空间: 1.需要强化项目管理的知识,参与项目的过程中,要能更加积极主动。 2.对供应商管理方面,要想办法培养供应商解决问题的主动性和能动性,而不是我们催就动,我们不催就没有动静。 3.平时工作中,与供应商沟通时,要能控制自己的情绪,要通过交流让对方接受自己的观点,明白自己的要求。 2014年公司即将开发更多优秀的客户,展现在自己面前的将是一片任自己驰骋的沃土,但同时也感受到了沉甸甸的责任,在今后的工作和生活中我将继续努力学习,深入实践,不断提升自我。 xxx 2014-1-3篇2:2011sqe年度个人总结
年度工作总结
时间流逝,岁月如梭,2011年已悄然走过。在这一年中,本人在公司和部门领导的指导下、在各位同事的协助下,基本完成了年初计划中所定的各项工作。回想这一年来,本人服从领导,努力工作,严格要求自己,不断提高,自我加压,保证工作质量,严把质量关。保质保量地完成了领导交办的各项任务,主要做了以下一些工作:
一、新品开发
1、完成##2011款项目开发,共涉及12个零件的开发,均满足开发节点及质量要求。
2、完成##一阶段性能提升项目开发工作,共涉及5个零件的开发,均满足开发节点及质量要求,
3、新##项目开发任务,包括多媒体系统灯具等关键项目目前正在进行中,在tr阶段开始积极参与技术方案的确定并积极参与联合设计方案的确定,如尾灯led布局,车厢阅读灯,多媒体系统人机互动界面等,有效降低投产后发生质量风险与用户抱怨的可能,预计2012年可完成开发任务。
4、完成总装信息联络任务,减少总装抱怨。
5、组织sqe落实top10年度控制任务,实际退出6家, 2家正在办理中,剩余两家。
6、共完成ppap认可70余件
二、现场问题、质量改进、售后等问题处理
1、处理电器现场问题90多起,主要涉及装配干涉、生产缺货、产品质量等诸多问题,均在第一时间解决现场问题,做到了无停线,零抱怨,零遗留。
2、走访售后服务站9次,验证和了解了前期质量问题的改进情况,并找到了数码播放器(死机问题),cd机(改装导致进水)异常索赔等故障发生原因,为后续质量改进提供了有效和及时第一手资料,促进了质量改进项目的完成。
3、共完成8项公司质量改进项目,其中中央控制盒改进,雨刮器改进等诸多项目均得到质量部,售后和客户的共同认可。
三、其他方面
1、积极参加各种群众性质量管理活动(如:合理化建议活动等)。
2、认真学习理论知识,学习各种方法技巧,参加各种专业培训,如:pcpa、apqp、tr、pcpa等,在后续工作中将进一步加强专业性工作的学习
3、对项目管理的认识有了一定的提升,在2012年工作中要加强项目管理的计划性和及时性跟踪,以及相关部门的协调工作。
四、几点感想和体会
在这一年时间里,部门领导和科长对我关怀备至,时常给我鼓励和帮助。使我感到:
1、工作要一丝不苟
工作时一定要一丝不苟,仔细认真。不能出错,平时要经常反思一下自己的工作,以确定自己的工作万无一失。工作之余还要经常总结工作教训,不断提高工作效率。在这一年时间里,同事们严谨、认真的工作作风给我留下了深刻的印象,我也从他们身上学到了很多自己缺少的东西。
2、工作要勤于思考 sqe岗位的日常工作比较繁琐,而且比较枯燥,这就需要我们一定要勤于思考,改进工作方法,提高工作效率,减少工作时间。
3、工作要不断学习
要不断的丰富自己的专业知识和专业技能,这会使我的工作更加得心应手。一个人要在自己的职位上有所作为,就必须要熟知专业知识,并在不断的学习中拓宽自己的知识面。 2011年的结束,2012年的到来,是开端也是结束,展现在自己面前的是一片任自己驰骋的沃土,也感受到了沉甸甸的责任,在今后的工作和生活中我将继续努力学习,刻苦钻研,深入实践,不断提升自我。
吴发强
2011年12月22日篇3:sqe工作怎么做(个人经验总结分享) sqe工作怎么做——个人经验总结分享
两年前进这个公司的时候,我被安排到做sqe的工作,当时的我对“sqe”是什么一点概念都没有,简直是一头雾水,工作内容是什么?怎么开始着手去做?虽然公司设置了一个供应商管理部的空壳子,可是寥寥几个人做的工作也只是催催供应商交货,整改产品质量,要求提交8d报告什么的。在没有经验、没人指导的情况下,我开始了我摸着石头过河的sqe经历。
如今转做其他工作的我想结合以前摸索出来的sqe工作方法总结一下我所认为的sqe工作应该怎么做。
我们公司是一个做汽车电子产品的企业,规模不算很大,但是麻雀虽小五脏俱全,杂七杂八的事情也不少。一开始给我的感觉sqe的工作就是介于采购部和品质部之间的辅助性工作。虽说是供应商质量工程师但是iqc、scm、sqm的工作都会做一些。当然了肯定是没有专门做这些工作的人员做的系统和专业,iqc就不用说了,为了保证来料顺利供应生产,除了控制数量、检查质量和催交货期之外也就是培训人员检测方法、现场验货加上辅助仓库盘点的事情。scm方面的工作主要就是帮助采购人员协助客户提出的设计变更和工程变更va/ve提案要求供应商配合做到cost down。sqm方面我们还是有分工的,供应商管理谈不上,也就只是按照产品的性质划分的,比如负责树脂件、钣金件的大部分时间都在跑现场和供应商,疲于处理各种各样的现场不良,用于供应商管理的时间少之又少;负责电器、总装零件的,现场倒是没有多少事情的,只有售后出现的不良,那样,除了解决市场问题外,重点就需要放在供应商管理上。
刚开始接触的时候,经常跟着别人跑供应商去解决一个又一个问题,通过这些问题的解决我也积累了一些经验,慢慢的从这些问题里就看到了相关供应商存在的弊病在哪里,随着专业知识的增长就开始不满足于解决单个问题了,也想分析出现这些问题的原因,希望把这些问题都控制在供应商内部,甚至更进一步提出自己的看法想帮供应商把问题的隐患消除掉,自然而然的就进入了供应商管理的角色。当然在这个时候就发现这个角色对自己的能力和对各方面的知识经验要求很高,只有多接触,多学习,多和供应商一起解决问题才能得到能力的提升,否则只能是做一些像救火队员一样的事情,哪里发现问题就去哪里解决,整天疲于奔命不说还消耗掉了自己的耐心,变得只为解决问题而解决问题,自己得不到提高更别提做供应商管理了。
至于sqe工作的重点应该放在哪里,这个也是一直困扰我的问题。曾经我有一个同事工作非常努力,整天泡在供应商那里忙着做供应商审查,帮供应商建立品质体系,忙忙碌碌的却在我们公司内看不到什么成果,被老板询问的时候他回答说要帮助供应商和我们公司一起成长。当然,扶持供应商的做法不错,但是他显然是没搞清楚sqe工作的重点。sqe的使命就是通过对供应商的品质进行管理来保证来料品质,其核心是保证来料品质而不是去帮供应商做qe。指望着通过sqe了解的那点三板斧的皮毛功夫就能提高供应商品质,那供应商聘请的专业的qe、me人员岂不是乐得坐享其成你的成果了?
诚然,供应商的品质体系建立是非常有必要的,出了品质问题找供应商要8d报告也是非常有必要的,但这并不能保证能够提升供应商的品质,毕竟品质的提升是一个非常复杂的过程,不是通过解决一两个问题,提交几个8d报告就能显著改善的。 sqe和供应商站的角度不一样,对待质量的看法也就不一样。sqe是站在客户的角度审视产品,不仅局限于产品的生产技术和工艺,反而能从产品的使用机能和产生的效果来分析。也许供应商自己的人员在专业、管理、经验上更丰富,但从他们自己的角度也许未必能够发现问题。所以在内行看来是外行的sqe往往能跳出供应商自己的思维模式,在某些方面提出建设性的意见从而使供应商得到提高也不是不可能的事,所以,sqe也要发现自身的优势,虽然没有供应商对产品研究的专业,但是sqe接触的零件种类比较多,虽然可能能力没有供应商强但是却有很多机会从不同的供应商那里学到工艺、过程控制、管理、检验等有优势的东西,将这些东西自己掌握吸收以后用来指导别的供应商也是能弥补供应商之间的相互劣势,还能使自己的客户身份得到供应商的尊重的方法。 如今,很多企业在开发供应商资源的时候往往都会采用两家供应商供货的方式,这样不仅避免了其中一家出现质量问题造成无法供料影响生产的情况,还能通过两家份额比例的分配制约供应商,使两家同一产品的供应商为了拿到大份额相互竞争,提高品质,降低价格,还能使两家优势互补,相互借鉴,共同提高。这样sqe在对供应商指导的时候就可以做出比较,能用一方的优势作为自己的经验指导给另一方,提高了自己在供应商心中的地位也实现了指导供应商的成绩。当然也有一些sqe懂的不多却经常以客户身份自居,在一些问题上去挑战供应商,但每次讲的道理都不够充分,不能使供应商信服,反而要供应商一定按照自己的要求做,那样做的后果是让供应商觉得受到了强迫,久而久之sqe在供应商心目中的威信扫地,人格魅力荡然无存,导致引起供应商的逆反心理工作上不愿去配合,工作不好推进不说,在供应商眼中这样的sqe除了有个客户的身份,其他的狗屁不是!
有些大的供应商很牛,有的时候都不愿意理小客户的sqe,遇到问题需要他们配合时要么敷衍了事,要么拖拖拉拉拿不出个结果。这样给sqe的工作带来很大的麻烦。所以,sqe不仅需要自己有过硬的专业知识使供应商信服,还要搞好和供应商的关系。很多问题供应商自己看到或者没看到的(有些是不容易改变的)都懒得去整改,都想应付过去就算了,这是人的本性,没办法,这时候sqe就要起一定的作用了,不光要催8d改善报告等,还要跟踪改善落到实处,现场审查甚至驻场跟催就是有必要的,只有保证供应商改善完成了才是问题的解决的根本。搞好和供应商的关系很重要,但是最重要的也是最根本的sqe要树立自己的权威,在关键时刻施加压力,不要手软,实在遇到不配合或者屡教不改的供应商要拿出自己的强势手段对供应商进行处罚。
以上,是我对自己曾接触到的sqe工作的一点看法,虽然在sqe职位工作的时间不长但是学到了很多东西,以后不论自己是否还有机会从事sqe的工作,但姑且先把这些心得写下来以便将来能活用的到。篇4:sqe 工作经验总结
本人2003年毕业后,鬼使神差般地进入了quality这个领域,一直从事sqe工作也有近4年的光景,今天把自己的一些做事方式,态度及sqe的职责show出来,供同行和外行加以褒贬,让自己吸取更多的精华,剔除糟粕. 备注,我所负责的材料主要是ee(pcb/fpc/pcba/fpca,rlc 及connector),所以下面很多的工作经验之谈是站在ee这个面展开的,不过,相信对于负责其他材料的同仁还是有一定的帮助的,毕竟sqe是技术及管理共存的一个职业. 当然,在此show出这么多个人经验之谈,也不乏有推荐自己之意,我相信我绝对是适合的人选。
一,绩效--就是通常说的kpi (key performance indictor) 但事实上,个人觉得真正衡量sqe的ability应该是supplier 8d回复的时效性及有效性,之所以这样说,是因为材料的特殊性,相信sqe同仁有同样的感触. 当然,有些材料本身supplier的sense或者其proce已经达到很高的水准,其品质面本来就很少出状况,来衡量管理这样材料的sqe performance,真的很难定夺,也许就是production的dppm trend chart 及service(training and so on). 二,职责(responsibility) 围绕保证品质来料这目的,sqe应负起如下的责任, 1.对供应商进行例行的绩效评估和audit. 2.品质监督和异常协辅
3.npi(new product 导入)/ecn 变更时,供应尚制程及产品的确认,cip的改善. 4.gp 产品及其管制. 针对以上四点,小弟我浅谈下我的经验,供各大侠指导. 1.对供应商进行例行的绩效评估和audit. 1.1导入新厂商阶段,一般有pur/rd/sqm/esh部门共同参与,sqe此阶段需要做的是让supplier提供供应商调查报告及工厂内部组织架构等等大项,此阶段主导者应该是pur. 1.2对供应商进行qpa(quality proce audit),这需要依据具体的产品来衡量,但不外乎receiving inspection, warehouse, mrb, production line, rework proce, oqc and packing&store, record and so on. 机, 3.machine maintained 4.measurement/tool 精确度
料, 5.区分隔离 6.保存期及保存方式
法, 7.traceability&identification 8.spc, fai checklist 环, 9.esh 10.温湿度 qpa的frequency,目前很多公司已经没有强制的定义,只要公司一出现比较大的case, sqe就驻厂,针对相关站别进行audit.事实上,这样做起来的确很有效果,sqe第一时间内了解到
不良品,然后又第一时间内去supplier端去audit相关proce,相信很大程度上能很快解决问题,使公司顺利生产,让supplier及时改善. 1.3对供应商qsa(quality system audit),通过对supplier系统面的audit,是希望指出supplier在整个面上的不足,一般来说,sqe主要audit的item如下, a.document management b.供应商之supplier的管理. c.product identification & traceability d.proce control e.检查和测试管理. f.calibration g.nonconforming product control. h.handling, package, storage and delivery i.record—这一项适合所有的audit items. 当然事实上,sqe重点放在上面items外,其实还是有些需要audit的项目,比如quality system, contact review, 甚至设计管理. 一般来说,qsa一年一次. 事实上,真正反映supplier performace的是qbr 会议,参与部门有pur, technology and sqm,分数比例一般为pur-- 35%, t-- 30% sqm -- 35%. 主要出发点 pur—delivery/cost/service t—technology share / service sqm—quality iue/ service ps: sales 人员注意,客户的3个主要对外窗口都很注重service. 这样的qbr meeting一般有sqm主导,当然supplier参加的窗口也应该是对应的sales/t/qa(cs) 部门. 个人认为后续product的竞争力应在品质上,所以站在sqe的角度上,我是希望sqm的比重可以适当加重. 1.4gpa(green product audit),目前很大部分公司已将此audit纳入qsa中,在这我就不细谈了.但重要的还是离不开如下6点: a.gpa的文件规范系统. b.proce management system c.training d.supplier’s 外包管理 e.ec管制(后面会细谈) f.检验和分析. 2.品质监督和异常协辅
个人很在乎的是能够很好的push supplier建立fmea部门,这样做的好处如下: 对应supplier a.但有异常发生时,能很快的组织起分析小组,尽快找到问题点,预防问题的进一步扩大, b.很快的处理异常,以达到最低限度的减少损失, c.buglist,作为经验的积累,方便后续品质的追踪. d.能很大程度上消除公司”踢皮球”的坏习惯. 对于公司(customer) a.defect sample分析的时效性得以保证.(8d cycle times) b.sqe可以第一时间内,review8d report,可以很快的找到对应分析窗口. 诚然,fmea小组的建立不能很快的让supplier看到自己利益的增长,但我敢保证fmea团队绝对是supplier和customer 很好的沟通桥梁.由于fmea团队的重要性,一般我都是直接找supplier site manager来谈,因为fmea小组需要很强的技术分析能力,很好的工厂执行力及分析defect的仪器设备, 这些都需要site manager的大力support. 相信优秀的sqe能明白我的想法也希望能给相关同仁一些感触. 对于异常协辅,也许很多行外人觉得sqe的技术能力真的有那么专业吗?能协辅supplier进行改善? 诚然sqe是技术和管理共存的一个特殊的岗位,相信没有一定的技术能力是很难让supplier诚服的,也的确sqe没有supplier的pe在技术上的专长,但一般来讲,公司现在很少找单一source supplier, 所以sqe有更多的机会去借鉴不同的经验,各公司一定都有他的长处,我已经习惯将各厂商长处相联结,同时也习惯让supplier习惯我的管理方式.之所以说sqe能给supplier异常辅导,是因为各岗位人员看待问题不一样,pe可能想到了改善的方向,但出与cost的考虑,还是无法进行有效的动作.甚至一些品质iue的轻微改善,一些自工具的设计有可能,等等类似的问题. 总之,sqe会取长补短,集合自己的经验能有效的给出supplier改善的方向. 3.npi(new product 导入)/ecn 变更时,供应尚制程及产品的确认,cip的改善. 先来谈下npi的管控.相信大部分的sqe有这样的体会,公司出现异常后,在最后root cause出来后才发现,原来这样的问题在试产阶段就已经存在,但种种原因,在没有得到解决前,此model已经进入量产阶段,这样以来,sqe就成为大家指责的重点,事实上,sqe会觉得很冤枉,因为,一般来说,试产阶段的iue都是有technology在负责处理,sqe也可能做部分的support,但量产材料一定是sqe在复杂,所以出现这样的问题,sqe做的事情,说的难听点就是在帮人家擦屁股,处理不好,其他部门就觉得sqe能力不够,处理完美,觉得这是sqe份内之事情. )?(这只是个人感慨,请勿当经验交流
所以,从上面的分析,出于对品质的保证,或者说对自己的保护,sqe介入npi阶段是非常必要的. 哪如何介入及介入后如何处理呢?下面细谈. 驻厂管理是必须的. a.如何介入? 一般来说,sqe会和supplier的qa召开周会或者月会,在该会议上,可以将new product review列为review项目.但,大多数公司,npi主导者一定是technology department,有时候甚至等产品量产后才notice qe department,所以,第一步,一定要让supplier technology 部门只要有新产品导入就一定要知会到qe,但大部分公司的pe没有这样的习惯,因为他们的重点可能在技术的改善及提升.所以看似很简单的要求,但实际操作起来就不会那么顺利,所
以sqe就要主动去找supplier site manager去谈,只有大老板关注到这点,才有可行性.这是sqe需要support supplier qe的,记住,与supplier的关系不是指挥与被指挥的关系,win-win才是sqe的最终目的. b.介入后如何管理呢? 一,part failure history/specific failure data 1.review supplier new model status in quality meeting. 2.review fails record and corrective actions. 3.ec list for new product.(in npi period, according to customer requirement, maybe some have some ec) 4.co-work with supplier’s pe&me, planner, rd&ie departments, define the best parameter and define it into sop. 5.supplier ipqc should know these failures and audit proce according to them.二,transportation readine. 1.co-work with supplier related department or field standard, set up new model yield rate criteria. 2.5m checklist (manpower/machine/material/method/environment) 3.document ready.(qc-flow-chart,sop,sip and so on) 4.spc review (dimension, optical, soldering thickne) 5.golden sample management setup. 这些看起来很简单,但运行起来就是在考量sqe的技术含量和管理能力了. 比如,公司的采购一定需要supplier出新产品,但有些问题又没有解决杂办?? 一般我采取的方式有, 1.告之公司t部门,有些问题还没有解决,你要试用出问题,你去处理.—比较坑人. 2.视异常而言,如一些外观问题没有得到处理,要求supplier加强全检次数,把不良卡在supplier端. 如为function问题没有得到解决,就直接要求停止出货.(当然,这需要sqm的大力support,如自己的老板也同意出货,相信真出问题,老板也不会怪罪到你.) 3.在新产品还没达到量产的水准及iue没有完全得到解决时,如pur一定要使用,那就请pur出特采.(一般来说,特采是pur最不想的状况,因为责任别就在自己身上了). 有时,可能只有1pcs的不良,但此不良为zero defect items(ee material,一般为错件,漏件,极性错误),sqe就一定需要supplier找到问题跟源,在没有得到完全解决前,sqe就要拍板,不许出货. 接着来谈ec的管控. ec有二种,veca&vecn. 区别点在于veca为supplier 提供给公司,vecn为公司发给supplier. 之所以将ec拿出来细谈是因为对于电子产品,cycle time比较短,ec的变更就比较多,而且很大一部分异常就是因为ec没有得到很好的管控. 谈及这方面的管控,首先要和大家有个共识,ec的窗口一定是唯一的,一般来说公司的ec窗口有二个,sqm及t, supplier端为qe及t.但大家也应该清楚sqm与外界的接触更多点,所以,在我以前服务的公司,ec窗口为sqm,对应的supplier窗口为qe,只有在ec窗口确定的情况下,ec才能得到很好的管控,不然,我相信很多公司会为这花费很大的精力去处理ec问题. a.vecn 管控. 发起单位可能为t和sqm,一般来说, t主要复杂normal的变更,比如从下个rev,需要增加个零件,象这样类似的变更.有t部门撰写,有sqe知会supplier. sqe主要针对量产时候出现的一些iue,经过验证等,发现变更一些layer out能解决问题.这样类似的变更就有sqe主导. b.veca管控. 一定是supplier的qe提供给sqe. veca提出的items可能很多, 比如厂商一些重要制程参数的变更,生产地的变更,供应商的变更(second source导入).针对iue, supplier验证一些数据,可能变更某些参数能很好的提升良率. 等等类似的问题,supplier均需要提出veca. ps:veca/vecn items 有些公司会规定的很详细. 谈到这点,接着就是变更的时间点要在document写的很清楚,很大部分iue就是因为ec的时间点不明确导致异常的发生. vecn/veca 时间导入有两种, 1.running change.(常说的限时导入) 2.cut-in change. 这就需要和pur及supplier确认清楚product的数量,不然一定会出现问题. 备注:ec是一定需要用docement管控的,这对于sqm还是supplier都是一种保护. 4.gp 产品及其管制. 这点我就不细谈了,xrf等管理,更多的是iqc在执行, 主要的还是做到如上几点.a.gpa的文件规范系统. b.proce management system c.training d.supplier’s 外包管理 e.ec管制
f.检验和分析
另再在此show下本人sqe职场性格,相信也是优秀sqe必备之能力。 1.良好的沟通技巧,与production及工厂内相关部门建立良好的co-work方式,使事事半功倍。 2.解析问题能一针见血,通过qc 7大说法,spc管控等等分析技巧,review supplier 8d report. 3.处理事情及时,提高工厂甚至我们的客户的满意度。 4.熟悉iso9000/ts16949/iso14000等各要求,熟练使用在audit supplier。 5.本身逻辑思维性很强,能深辟的看待问题。 6.在供应商管理方面,强势的管理方式能很好的领导supplier 品质的提升,当然同时会吸纳supplier的一些宝贵的意见,使工厂和supplier double win,很强的独立处理事情能力。篇5:sqe工作经验心得大集合 sqe工作经验谈
一个sqe前辈的经验之谈!(转发) kobe_zou 发表于: 2009-5-25 17:53 来源: 半导体技术天地
以下是一个sqe前辈的经验之谈,希望对大家有所帮助!!! sqe 工作经验浅谈!转发
作者:jevonsge
----------------- 本人2003年毕业后,鬼使神差般地进入了quality这个领域,一直从事sqe工作也有近4年的光景,今天把自己的一些做事方式,态度及sqe的职责show出来,供同行和外行加以褒贬,让自己吸取更多的精华,剔除糟粕. 备注,我所负责的材料主要是ee(pcb/fpc/pcba/fpca,rlc 及connector),所以下面很多的工作经验之谈是站在ee这个面展开的,不过,相信对于负责其他材料的同仁还是有一定的帮助的,毕竟sqe是技术及管理共存的一个职业. 当然,在此show出这么多个人经验之谈,也不乏有推荐自己之意,我相信我绝对是适合的人选。
一,绩效--就是通常说的kpi (key performance indictor) 当然,有些材料本身supplier的sense或者其proce已经达到很高的水准,其品质面本来就很少出状况,来衡量管理这样材料的sqe performance,真的很难定夺,也许就是production的dppm trend chart 及service(training and so on). 二,职责(responsibility) 围绕保证品质来料这目的,sqe应负起如下的责任, 1.对供应商进行例行的绩效评估和audit. 2.品质监督和异常协辅
3.npi(new product 导入)/ecn 变更时,供应尚制程及产品的确认,cip的改善. 4.gp 产品及其管制. 针对以上四点,小弟我浅谈下我的经验,供各大侠指导. 1.对供应商进行例行的绩效评估和audit. 1.1导入新厂商阶段,一般有pur/rd/sqm/esh部门共同参与,sqe此阶段需要做的是让supplier提供供应商调查报告及工厂内部组织架构等等大项,此阶段主导者应该是pur. 1.2对供应商进行qpa(quality proce audit),这需要依据具体的产品来衡量,但不外乎receiving inspection, warehouse, mrb, production line, rework proce, oqc and packing&store, record and so on. 针对这些站别,总结起来,按照人,机,料,法,环五项,集合公司的qpa checklist进行audit. 机, 3.machine maintained 4.measurement/tool 精确度
料, 5.区分隔离 6.保存期及保存方式
法, 7.traceability&identification 8.spc, fai checklist 环, 9.esh 10.温湿度 qpa的frequency,目前很多公司已经没有强制的定义,只要公司一出现比较大的case, sqe就驻厂,针对相关站别进行audit.事实上,这样做起来的确很有效果,sqe第一时间内了解到不良品,然后又第一时间内去supplier端去audit相关proce,相信很大程度上能很快解决问题,使公司顺利生产,让supplier及时改善. 1.3对供应商qsa(quality system audit),通过对supplier系统面的audit,是希望指出supplier在整个面上的不足,一般来说,sqe主要audit的item如下, a.document management b.供应商之supplier的管理. c.product identification & traceability d.proce control e.检查和测试管理. f.calibration g.nonconforming product control. h.handling, package, storage and delivery i.record—这一项适合所有的audit items. 当然事实上,sqe重点放在上面items外,其实还是有些需要audit的项目,比如quality system, contact review, 甚至设计管理. 一般来说,qsa一年一次. 事实上,真正反映supplier performace的是qbr 会议,参与部门有pur, technology and sqm,分数比例一般为pur-- 35%, t-- 30% sqm -- 35%. 主要出发点 pur—delivery/cost/service t—technology share / service sqm—quality iue/ service ps: sales 人员注意,客户的3个主要对外窗口都很注重service. 这样的qbr meeting一般有sqm主导,当然supplier参加的窗口也应该是对应的sales/t/qa(cs) 部门. 个人认为后续product的竞争力应在品质上,所以站在sqe的角度上,我是希望sqm的比重可以适当加重. 1.4gpa(green product audit),目前很大部分公司已将此audit纳入qsa中,在这我就不细谈了.但重要的还是离不开如下6点: a.gpa的文件规范系统. b.proce management system c.training d.supplier’s 外包管理 e.ec管制(后面会细谈) f.检验和分析. 2.品质监督和异常协辅
对于品质监督,我很是赞同baseline management,通过驻厂的方式,及时有效的audit厂商各站别的问题,同时给予厂商qa部门的大力support,提升其执行力. 个人很在乎的是能够很好的push supplier建立fmea部门,这样做的好处如下: 对应supplier a.但有异常发生时,能很快的组织起分析小组,尽快找到问题点,预防问题的进一步扩大, b.很快的处理异常,以达到最低限度的减少损失, c.buglist,作为经验的积累,方便后续品质的追踪. d.能很大程度上消除公司”踢皮球”的坏习惯. 对于公司(customer) a.defect sample分析的时效性得以保证.(8d cycle times) b.sqe可以第一时间内,review8d report,可以很快的找到对应分析窗口. 诚然,fmea小组的建立不能很快的让supplier看到自己利益的增长,但我敢保证fmea团队绝对是supplier和customer 很好的沟通桥梁.由于fmea团队的重要性,一般我都是直接找supplier site manager来谈,因为fmea小组需要很强的技术分析能力,很好的工厂执行力及分析defect的仪器设备, 这些都需要site manager的大力support. 相信优秀的sqe能明白我的想法也希望能给相关同仁一些感触. 对于异常协辅,也许很多行外人觉得sqe的技术能力真的有那么专业吗?能协辅supplier进行改善? 诚然sqe是技术和管理共存的一个特殊的岗位,相信没有一定的技术能力是很难让supplier诚服的,也的确sqe没有supplier的pe在技术上的专长,但一般来讲,公司现在很少找单一source supplier, 所以sqe有更多的机会去借鉴不同的经验,各公司一定都有他的长处,我已经习惯将各厂商长处相联结,同时也习惯让supplier习惯我的管理方式.之所以说sqe能给supplier异常辅导,是因为各岗位人员看待问题不一样,pe可能想到了改善的方向,但出与cost的考虑,还是无法进行有效的动作.甚至一些品质iue的轻微改善,一些自工具的设计有可能,等等类似的问题. 总之,sqe会取长补短,集合自己的经验能有效的给出supplier改善的方向. 3.npi(new product 导入)/ecn 变更时,供应尚制程及产品的确认,cip的改善. 先来谈下npi的管控.相信大部分的sqe有这样的体会,公司出现异常后,在最后root cause出来后才发现,原来这样的问题在试产阶段就已经存在,但种种原因,在没有得到解决前,此model已经进入量产阶段,这样以来,sqe就成为大家指责的重点,事实上,sqe会觉得很冤枉,因为,一般来说,试产阶段的iue都是有technology在负责处理,sqe也可能做部分的support,但量产材料一定是sqe在复杂,所以出现这样的问题,sqe做的事情,说的难听点就是在帮人家擦屁股,处理不好,其他部门就觉得sqe能力不够,处理完美,觉得这是sqe份内之事情. (这只是个人感慨,请勿当经验交流?) 所以,从上面的分析,出于对品质的保证,或者说对自己的保护,sqe介入npi阶段是非常必要的. 哪如何介入及介入后如何处理呢?下面细谈. 驻厂管理是必须的. a.如何介入? 一般来说,sqe会和supplier的qa召开周会或者月会,在该会议上,可以将new product review列为review项目.但,大多数公司,npi主导者一定是technology department,有时候甚至等产品量产后才notice qe department,所以,第一步,一定要让supplier technology 部门只要有新产品导入就一定要知会到qe,但大部分公司的pe没有这样的习惯,因为他们的重点可能在技术的改善及提升.所以看似很简单的要求,但实际操作起来就不会那么顺利,所以sqe就要主动去找supplier site manager去谈,只有大老板关注到这点,才有可行性. 这是sqe需要support supplier qe的,记住,与supplier的关系不是指挥与被指挥的关系,win-win才是sqe的最终目的.b.介入后如何管理呢? 一,part failure history/specific failure data 1.review supplier new model status in quality meeting. 2.review fails record and corrective actions. 3.ec list for new product.(in npi period, according to customer requirement, maybe some have some ec) 4.co-work with supplier’s pe&me, planner, rd&ie departments, define the best parameter and define it into sop. 5.supplier ipqc should know these failures and audit proce according to them. 二,transportation readine. 1.co-work with supplier related department or field standard, set up new model yield rate criteria. 2.5m checklist (manpower/machine/material/method/environment) 3.document ready.(qc-flow-chart,sop,sip and so on) 4.spc review (dimension, optical, soldering thickne) 5.golden sample management setup. 这些看起来很简单,但运行起来就是在考量sqe的技术含量和管理能力了. 比如,公司的采购一定需要supplier出新产品,但有些问题又没有解决杂办?? 一般我采取的方式有, 1.告之公司t部门,有些问题还没有解决,你要试用出问题,你去处理.—比较坑人. 2.视异常而言,如一些外观问题没有得到处理,要求supplier加强全检次数,把不良卡在supplier端. 如为function问题没有得到解决,就直接要求停止出货.(当然,这需要sqm的大力support,如自己的老板也同意出货,相信真出问题,老板也不会怪罪到你.) 3.在新产品还没达到量产的水准及iue没有完全得到解决时,如pur一定要使用,那就请pur出特采.(一般来说,特采是pur最不想的状况,因为责任别就在自己身上了). 有时,可能只有1pcs的不良,但此不良为zero defect items(ee material,一般为错件,漏件,极性错误),sqe就一定需要supplier找到问题跟源,在没有得到完全解决前,sqe就要拍板,不许出货. 接着来谈ec的管控. ec有二种,veca&vecn. 区别点在于veca为supplier 提供给公司,vecn为公司发给supplier. 之所以将ec拿出来细谈是因为对于电子产品,cycle time比较短,ec的变更就比较多,而且很大一部分异常就是因为ec没有得到很好的管控. 谈及这方面的管控,首先要和大家有个共识,ec的窗口一定是唯一的,一般来说公司的ec窗口有二个,sqm及t, supplier端为qe及t.但大家也应该清楚sqm与外界的接触更多点,所以,在我以前服务的公司,ec窗口为sqm,对应的supplier窗口为qe,只有在ec窗口确定的情况下,ec才能得到很好的管控,不然,我相信很多公司会为这花费很大的精力去处理ec问题. a.vecn 管控. 发起单位可能为t和sqm,一般来说, t主要复杂normal的变更,比如从下个rev,需要增加个零件,象这样类似的变更.有t部门撰写,有sqe知会supplier. sqe主要针对量产时候出现的一些iue,经过验证等,发现变更一些layer out能解决问题.这样类似的变更就有sqe主导.b.veca管控. 一定是supplier的qe提供给sqe. veca提出的items可能很多, 比如厂商一些重要制程参数的变更,生产地的变更,供应商的变更(second source导入). 针对iue, supplier验证一些数据,可能变更某些参数能很好的提升良率. 等等类似的问题,supplier均需要提出veca. ps:veca/vecn items 有些公司会规定的很详细. 谈到这点,接着就是变更的时间点要在document写的很清楚,很大部分iue就是因为ec的时间点不明确导致异常的发生. vecn/veca 时间导入有两种, 1.running change.(常说的限时导入) 2.cut-in change. 这就需要和pur及supplier确认清楚product的数量,不然一定会出现问题. 备注:ec是一定需要用docement管控的,这对于sqm还是supplier都是一种保护. 4.gp 产品及其管制. 这点我就不细谈了,xrf等管理,更多的是iqc在执行, 主要的还是做到如上几点. a.gpa的文件规范系统. b.proce management system c.training d.supplier’s 外包管理 e.ec管制
f.检验和分析
另再在此show下本人sqe职场性格,相信也是优秀sqe必备之能力。 1.良好的沟通技巧,与production及工厂内相关部门建立良好的co-work方式,使事事半功倍。 2.解析问题能一针见血,通过qc 7大说法,spc管控等等分析技巧,review supplier 8d report. 3.处理事情及时,提高工厂甚至我们的客户的满意度。 4.熟悉iso9000/ts16949/iso14000等各要求,熟练使用在audit supplier。 5.本身逻辑思维性很强,能深辟的看待问题。 6.在供应商管理方面,强势的管理方式能很好的领导supplier 品质的提升,当然同时会吸纳supplier的一些宝贵的意见,使工厂和supplier doube win,很强的独立处理事情能力。
发布: 2008-1-26 16:40 | 作者: weifenglin | 来源: 6sq.net | 查看: 783次
从事sqe工作已有两年,一套工作经验渐渐成形.在此拙作出来,以让sqe新人参考,让行内高手指教. 一.绩效﹕ sqe 的使命﹐是通过对供货商的品质管理﹐以保证来料的品质。因此﹐vlrr是sqe 绩效的主要反映。
二.职责﹕
围绕保证来料品质这目的﹐sqe 应负起以下四点职责﹔ 1.对供应商例行品质绩效评估与稽核; 2.品质监督与异常辅导; 3 .new/ec产品导入时的供货商制程与产品确认和持续改善(cip); 4.gp产品及其制程管制等; 针对此四点职责﹐以下是我的一点经验﹕ 1.对供应商例行品质绩效评估与稽核; 1.1导入新厂商: 一般内容有:对新供货商作总况调查﹑qsa(qaulity system audit), qpa(quality proce audit)﹑签定品质合约; 1.2供应商例行品质绩效评, 每月评分与制程稽核qpa; 每月评分三要素tqr: technology.quality.response; 每月一评﹐评分结果分a/b/c/d等级。 1.3 制程稽核(qpa)每季度末由sqe制定下季度的稽核计划. 制程稽核方式﹕针对不同的站别, including receiving inspection﹑warehouse﹑mrb﹑p/l﹑secondary operations﹑oqc﹑packing and stock and so on. 总结起来﹐重点项目由 人﹑机﹑料﹑法﹑环五项构成﹐具体事项按公司qpa list点检。
机﹕3 设备/校验。4 治具/测量; 料﹕5.物料分区.6 保存期/保存方式; 法﹕7 可追溯性; 8.spc, 自检, clca检讨; 环﹕9 安全防护.10 湿/温度; qsa 通常每年一评。
第18篇:SQE工作职责
SQE工作职责
1、负责保障供应商所供原材料的质量,在进料检验、生产过程检验、客户抱怨等,只要是由于原材料质量缺陷引发的,都要及时反馈供应商要求其改善;
2、负责追踪确认供应商的改善报告(8D)及实施效果,必要时可进行现场审核检查;
3、负责参与供应商初始样品的评估放行工作;
4、负责每个月或每个季度,对现有供应商的质量状况进行统计评分,对评分较低的供应商提出限期改善要求;
5、负责参与新供应商开发与审核,与采购部门一起对新供应商进行考核打分,确定其是否可以成为合格供应商。
6、供应商质量目标达成状况的改善及检讨;
7、供应商的定期及异常稽核的执行;
7、供应商的辅导,协助供应商提升产品质量。
8、执行供应商的奖罚措施;
9、供方PPAP资料的初审;
10、供应商审核安排及审核整改资料的收集和验证。
11、上级主管交代的其它事宜。
第19篇:SQE供应商质量管理
SQE供应商质量管理
SQE供应商质量管理
1.按流程进行供应商选择评估规避质量风险
2.建立供应商质量管理体系
3.日常的供应商质量管理
4.APQP、SPC等供应商质量管理工具应用
5.做好内外部协调沟通者
一.对供应商考核评定
按QCD对供应商等级评定
二.供应商质量管理与控制
1.确认供应商质量体系文件建立
2.供应商产品及服务质量的控制
三.供应商产品质量的日常管理
1.供应商检验规范
2.关键零件的追溯
3.生产设备生产能力与保证能力;
4.工艺流程和关键参数;
5.工艺变更确认程序;
6.工艺标准执行情况;
7.质量事故通报告及处理程序。
8.评估供应商质量
9.考核供应商质量
10.对质量问题的分析与处理
11.飞行检查与源头监控
四.供应商关系管理
1.同供应商建立供应链战略伙伴关系
2.库存管理
五.新产品的确认及质量策划
1.产品质量先期策划APQP
2.统计过程控制(SPC)
确定Cpk是否达到要求。
第20篇:浅谈SQE工作
浅谈SQE工作
SQE全称为supply quality engineer故名思议 则主要以供应商质量负责为主。 但是质量管理,千丝万缕,从原先的注重产品检验到注重过程再到设计,甚至整个运营体系。
因此SQE的职责更是相对宽泛。其主要职责为三大块:
1) 项目支持
项目支持这一块主要负责从项目立项开始后的潜在供方评审,供方选择与评价,以及协调供方与开发/采购/物流/质保支持QPN活动的展开,例如:产品数据冻结后的标准确认,材料认可,开模跟踪,模具检具工装的验收,OTS认可,过程确认,FMEA的策划,控制计划的确认,首批首件的认可,2TP的验收等等,要SQE必须要熟悉的前期流程,熟悉APQP策划,具备一定的技术知识,良好的沟通协调能力,清晰的项目管理思路以及良好的抗压能力等。比如上海通用的SQE最主要的工作范畴就是项目管理,要求也相对较高,前期开发阶段SQE被任命为项目经理。
2)采购支持
采购支持这一块主要的工作内容有,供应商开发,立项后的潜在供方评审,供方定点,bom表的下发,与开发/物流/质保对供方进行绩效考核,不断优化整合供应链,另外相应的商务工作例如:报价,核价,质量索赔,退货等,需要有出色的商务谈判能力,审核能力,清晰的供应商管理思路等,这一块主要偏商务。
3)供应商质量管控
供应商质量管控是SQE的核心业务,主要是对量产项目的支持,以及供方审核,体系开发,帮助提升供方质量能力,日常的内部投诉处理,客户抱怨处理,以及QCC改善活动的主导,月度或者年度的供方质量绩效考核等等。这方面的工作量相当大,而且备受争议,往往出力不讨好,也是最辛苦最累的活,不仅仅需要丰富的体系管理知识,质量管控经验,对抗压能力和沟通协调能力的要求相对较高。
总的来说:SQE是一个横向跨部门的管理岗位,工作的重点是如何去管理,通过一种怎样的方式和方法,合理的优化资源配置,利用现有的资源去完成某项任务的管理活动,对资质的要求相对较高,一家公司想要有好的发展必须要有一支优秀的供应链资源的支持,而SQE的天职是配合公司的采购战略如何去优化整合公司的供应链资源,降低风险,提高效益,因而工作相对繁杂,成绩也不容易让人看到,却也是最能锻炼人的一个岗位。
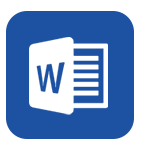