板坯连铸机的现代化高效性技术改造
招聘(广告)
市场竞争是无情的,只有提高产品质量,降低生产成本,才能在市场上立于不败之地。现代化技术改造主要是要提高生产率,降低生产成本,提高操作灵活性,降低工人劳动强度,尤其重要的就是要提高产品质量。连铸高效化已经成为推动我国钢铁工业结构优化的重大技术,越来越多的企业正在进行高效连铸的技改工作。
连铸机的组成
连铸机是一种高质、高效、低耗的铸锭设备。在国内外,冶金企业中发展和应用较快较广。连铸机的重要组成如图1所示。
板坯连铸机技术改造
连铸机的改造主要是通过一些新的技术来对铸机进行改造以此来达到连铸的现代化高效性和提高产品质量目的。
1 板坯连铸机滑动水口液压传动系统
(1)滑动水口概述
板坯连铸机中的中间包是连铸生产线上的重要设备。滑动水口是安装在中间包底部用来控制钢液从中间包流到结晶器的流量。液压滑动水口克服了塞棒工作时出现的断裂、熔融、变形、钢流关不住等故障。
(2)滑动水口液压传动系统工作原理
滑动水口液压传动系统最终可以实现自动的现代化控制,只有高自动化水平的工厂才能以低成本来实现高质量产品的生产。同时达到生产的高效性和降低工人劳动强度的目的。滑动水口液压传动系统的自动控制是利用液位检测信号和水口实际位置的位置检测信号与设定值相比较所产生的误差来控制滑动水口驱动液压缸动作,自动调节滑动水口开度的大小以调节钢液流量,实现随动控制。其工作流程如图2。
根据滑动水口液压传动系统其工作流程图可以设计出滑动水口液压系统如图3。
如当DT2通电。滑动水口开启时的主油路如下:
进油路压力源P→换向阀右位(液控单向阀
2、3K口)→伺服阀右位→液控单向阀2→节流阀5→单向阀8→液压缸右腔,活塞左移,滑动水口开启;回油路液压缸左腔→滤油器13→单向阀10→单向阀7→液控单向阀3→伺服阀右位→油箱。
滑动水口关闭时的主油路是:
压力源P→换向阀右位(液控单向阀
2、3K口)→伺服阀左位→液控单向阀3→节流阀6→单向阀11→液压缸左腔,活塞右移,滑动水口关闭;回油路液压缸右腔→滤油器12→单向阀9→单向阀4→液控单向阀2→伺服阀左位→油箱。
在油路中,还应装有液压检测器与位置检测器,液压检测器用来传递结晶器中钢水的实际位置再与初始液位设定进行比较放大后输入液位调节器中。位置检测器则用来传递液压缸实际位置再与滑动水口开度设定比较放大后输入到开口调节器,最终向伺服阀输入信号。这样来实现自动调节滑动水口开度的大小。
2 板坯连铸机液压振动
液压振动技术是近些年来开发的新技术,它具有机械振动所没有的优越性,目前已在现代化高效的大型板坯连铸机振动装置上得到了普遍的采用。
(1)连铸机结晶器振动概述 在连铸技术的发展过程中,只有采用了结晶器振动装置后,连铸才能成功。结晶器振动的目的是防止拉坯时坯壳与结晶器粘结,同时获得良好的铸坯表面,即结晶器向上运动时,会减少新生的坯壳与铜壁产生粘着,以此防止坯壳受到较大的应力,使铸坯表面出现裂纹;而当结晶器向下运动时,借助摩擦,在坯壳上施加一定的压力,愈合结晶器上升时拉出的裂痕,这就要求向下运动的速度大于拉坯速度,形成负滑脱。机械式的振动装置由直流电动机驱动,通过万向联轴器,分两端传动两个蜗轮减速机,其中一端装有可调节轴套,蜗轮减速机后面再通过万向联轴器,连接两个滚动轴承支持的偏心轴,在每个偏心轮处装有带滚动轴承的曲柄,并通过带橡胶轴承的振动连杆支撑振动台,产生振动。机械振动一般采用正弦曲线振动,振动波形、振幅固定不变。液压振动技术采用液压系统作为振动源,具有控制精度高、调整灵活、在线设备体积小、重量轻、维护简单等特点,它不仅能满足高频振动的要求,消除电机,减速器传动中由于冲击负载所造成的电机烧损和减速器损坏等问题,更主要的是它可以根据工艺条件的要求任意改变振动波形,控制负滑动速度与负滑动时间,改善结晶器与铸坯之间的润滑和脱模,减少粘结性漏钢事故;同时可降低高拉速条件下的振动频率,减少机构磨损。
(2)液压振动原理
液压振动工作流程如图4所示。
液压振动的动力装置为液压油源,它作为动力源向振动液压缸提供稳定压力和流量的油液。液压振动的核心控制装置为振动伺服阀。振动伺服阀灵敏度极高,油源提供动力如有波动,伺服阀的动作就会失真,造成振动时运动不平稳和振动波形失真。为此,要在系统中设置蓄能器以吸收各类波动和冲击,保证整个系统的压力稳定。正弦和非正弦曲线振动靠振动伺服阀控制,而振动伺服阀的控制信号来自曲线生成器,主控室的计算机通过PLC控制曲线生成器设定振动曲线(同时也设定振幅和频率)。曲线生成器通过液压缸传来的位置反馈信号来修正振幅和频率。经过修正的振动曲线信号转换成电信号来控制伺服阀。只要改变曲线生成器即可改变振动波形、振幅和频率。曲线生成器输入信号的波形、振幅和频率可在线任意设定,设定好的振动曲线信号传给伺服阀,伺服阀即可控制振动液压缸按设定参数振动。在软件编程中,同时还可以设置多种报警和保护措施以避免重大事故的发生。这种在线任意调整振动波形、振幅和频率是机械振动所实现不了的。
根据液压振动系统其工作流程图可以设计出液压伺服控制系统如图5。
在图5所示的系统中,伺服阀是系统的核心所在,用于控制液压缸运动的方向与速度。伺服阀的进、出油口回路上接有4个截止阀通过手动关闭,用于在维修时将伺服阀与油路隔离。进回油路上有2个小型蓄能器,用于进一步吸收流量脉动,同时可以提高伺服液压缸开始动作时的响应速度。图中的两个溢流阀是作为安全阀来用的。在回路中,还应装有位置传感器与压力传感器,用于实现反馈控制。过滤器精度达3μm,保证了伺服阀对油源清洁度的要求。并应设置了多个测压接头,便于故障的查找。
振动台液压缸是一种特殊的液压缸,内部应装有位置传感器。由于振动缸处在高温、多尘、潮湿恶劣的环境中,所以缸内还应设计压缩空气通道,进行液压缸的冷却和吹扫。振动伺服液压缸结构上应是典型的双杆双作用对称缸,因为双杆双作用缸具有动态控制性能好,缸工作容腔小、刚度高、伺服控制阀块可直接安装在振动液压缸缸体上等特点,也因为这样有利于提高液压系统的动态响应性。此外,双杆双作用缸还具有短行程、导向密封面长的特点。最后,由于要求伺服液压缸在起动过程中反应灵敏,因此应选用摩擦阻力小,密封效果好的密封件,保证伺服液压缸工作平稳。
与机械振动相比,板坯连铸机的液压振动装置具有一系列优点:①振动力由两点传入结晶器,传力均匀;②在高频振动时运动平稳,高频和低频振动时不失真,振动导向准确度高;③结构紧凑简单,传递环节少,与结晶器对中调整方便,维护也方便;④采用高可靠性和高抗干扰能力的PLC控制,可长期保证稳定的振动波形;⑤可改变振动曲线,并可在线设定振动波形等,增加了连铸机可浇铸的钢种;⑥改善铸坯表面与结晶器铜壁的接触状态,提高铸坯表面质量并减少粘结漏钢。在快速浇铸中要求提高结晶器振动装置的频率,同时,为提高产品质量,要求采用各种不同的振动波形。而液压伺服振动装置的主要优点正是能够精确连续地改变振动波形、振幅和振动频率。所以,液压伺服振动技术将是板坯连铸振动技术的一个发展趋势。
3 高效连铸的核心技术——结晶器技术
众所周知,结晶器是连铸机的“心脏”,国内外各种高速连铸技术的开发均以结晶器为中心来展开,高效连铸的结晶器技术,同常规连铸相比,高速连铸结晶器主要在以下三个方面进行突破。
(1)增加铜管长度
高拉速条件下,为加速结晶器内钢水的凝固,延长一冷段是直接有效的措施。如奥地利VAI公司的普通结晶器的800mm增加到1000mm,卢森堡PaulWurth公司的高速结晶器长度由700mm延长至1000mm,连铸技术国家工程研究中心(以下简称连铸中心)研制的连续锥度结晶器长度由700mm增至1000mm,冶金设备研究院开发的GS—型曲面结晶器长度由700mm加至1000mm等。
(2)提高冷却强度
为改善结晶器的传热效果,确保结晶器出口具有足够的厚度,一般采用减少铜管与水套的间隙、增加冷却水流速、减薄铜管壁厚、开发结晶器导热性能高的材质等措施来提高一冷强度。如意大利Danieli公司的Danam—1结晶器铜管壁厚为11mm冷却水压12×105Pa、结晶器材质是Cu2Cr2Zr,美国Rokop公司的抛物线结晶器不锈钢水套的间隙是常规的一半等。
(3)采用连续锥度多锥度铜管
拉速提高后,结晶器几何形状需适应铸坯的凝固收缩,从而使铸坯和模壁始终尽可能地接触良好,抑制气隙产生,传热增加且均匀稳定,角部坯壳能和中部坯壳一样均匀地生长,结晶器铜管多采用连续锥度或多锥度来满足这些要求。如瑞典Concast公司的Convex,德国Demag公司的抛物线锥度结晶器,PaulWurth的高速结晶器,连铸中心的连续锥度结晶器,GS—型曲面结晶器等均采用了此技术。以上述技术为核心开发的高速结晶器,可显著地提高拉速,如Convex可提高拉速50%~100%,Danam—1提高54%,Diamold、连续锥度结晶器以及Demag、PaulWurth和Rokop的高速结晶器等均提速50%以上。
4 在线快速调厚调宽的零号扇形段
厚板钢种的铸坯和常规板坯不同点之一就是前者批量小,后者批量大,由于很多厚板钢种都是高级钢种,成分差异大,质量要求高,再加上批量小,则各钢种之间均不能连浇(因为连浇后的交接坯变成废坯,使金属利用率降低,成本提高)。传统板坯连铸机如果浇热轧带钢铸坯,在不改变厚度时,结晶器可以热状态在线调宽,改变厚度时将结晶器和零号扇形段一起吊走更换,才能开始浇注。浇注厚板钢种时,若调整宽度,当板坯厚度较薄时,可停机在线调整结晶器宽度,当板坯厚度较厚,零号段需调宽或者板坯需要调整厚度时均需要将结晶器和零号扇形段一起吊走更换,才能够重新浇铸。在线快速调厚调宽的结晶器用在高速板坯连铸机上,与之相适应地又开发了能够快速调厚、调宽的零号扇形段。这样,浇注不同厚度的板坯时,整个连铸机的辊缝才能够快速得到调节,而不用整体更换任何设备,从而减少了重新对弧的工序,减少了作业时间,提高了板坯连铸机的作业率。
在线快速调厚、调宽的零号扇形段是与在线快速调厚调宽的结晶器相配合的,与传统的零号扇形段相比,结构上有很大变化。其主体结构和二冷区机械夹紧扇形段类似,主要由带辊子的内弧框架,外弧框架,蜗轮蜗杆传动的四个导向柱,夹紧用碟形弹簧组等构成。最大的区别之一在于新的零号扇形段的窄边设有调宽装置及其传动装置,这些结构和结晶器调宽装置类似,不同点在于结晶器窄边是个整体,而零号段窄边为分段式,两者均用电动方式进行调宽,其内腔尺寸是一致的。另一个大的区别在于,这种零号扇形段的调厚传动装置与二冷扇形段差别较大,二冷扇形段的调厚(调整辊子开口度)装置的传动装置与本体设备是脱开的,设置在固定的基础上,由电机驱动,可以整体调整辊子开口度或按铸坯的入口侧或出口侧分别调整。而新的零号扇形段调厚传动装置则与设备本体设计成一体,由两个液压马达进行驱动,只能整体调整辊子开口度。在这种零号扇形段中,液压马达用液压源和主机液压源在一起,当设备安装到位后,用快换接头接通。
结语
以上介绍了板坯连铸机的四项技术,这些技术对板坯连铸机的生产均有着十分重要的意义。连铸高效化是提高铸机的生产率、改善铸坯质量以及降低生产成本而获得较高经济效益的途径,是现代钢铁企业优化结构、技术进步和提高市场竞争力的关键所在。各企业应积极借鉴吸收国内外先进的连铸高效化技术、结合本厂的实际情况、并根据市场的需求状况实施全面系统、分批有序的高效化改造,同时还应联合科研院校积极开发实用的连铸新型技术,推动企业在激烈的市场竞争中不断发展。
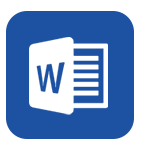