实验一 材料力学万能试验机的认识
一、液压式材料万能试验机
图1为油压式万能试验机,利用油压加力,可作拉伸、压缩、剪切、弯曲等实验。 1.构造原理:图1为万能试验机的构造原理图,分为加力、测力、自动绘图三个部分。 (1) 加载系统:加载系统由油箱、油缸、工作台、机座等组成。机座
14、光滑立柱7及上横梁6固定不动,开动马达后,油泵将油经过送油阀17和油管③送至工作油缸内,推动活塞5带动工作台11上升。若试件放在工作台11上,则受压缩。试件受力的大小与油压的大小成正比关系。
(2) 测力系统:测力为重摆平衡式。试件受力后,油缸内油压逐渐增加,高压油经油管④⑤进入到测力油缸(28)内,使测力活塞(27)向下移动,通过连杆(26),使摆锤摆起,推动齿杆(21)带动齿轮(15),即可使指针转动,从而由示力盘上得到相应的载荷。更换摆锤重量,即可得到不同的测力范围。 (3)绘图系统:记录仪。
图1 万能试验机结构原理图
1.马达 2.上支架 3.螺杆 4.工作油缸 5.活塞 6.上横梁 7.光滑立柱 8.压板 9.支座 10.夹头 11.工作台 12.夹头 1 3 .手柄 1 4 .机座 1 5 .齿轮 1 6 .指针 1 7 .送油阀 1 8 .油泵 1 9 .马达 2 0 .度盘 2 1 .齿杆 22.推杆 23.回油阀 24.摆杆 25.平衡锤 26.连杆 27.测力活塞 28.测力油缸 29.油箱 30.摆锤
2. 操作方法: ① 选择力盘。根据试件尺寸和实验要求,选择合适的测力范围,加上相应的摆锤。 ② 选择合适的夹具及其附件。
③ 调整零点:开启马达,将油打入工作油缸,使工作台稍微升起,以平衡掉工作台自重,然后旋转齿杆21,使示力盘指针指零。
④ 安装试件。作压缩实验,试件放在工作台的中心;如果作拉伸实验,则将试件夹入上、下夹头
12、10中。
⑤ 调整好自动绘图装置。
⑥ 加载实验。加载前检查各油阀是否关闭,然后开动马达,微开送油阀,缓慢加载。 ⑦ 卸载。实验完毕后,打开回油阀退油,关闭电门。 3. 注意事项
① 开马达前,应将送油阀,回油阀都关闭。
② 为保证均匀缓慢加载,特别是试件将要受力时,送油阀不应开得过大,以防过载。 ③ 试件受力后及加载,卸载过程中,不准开动上支架马达,以免损坏机器。 ④ 送油阀不要关得过紧,以免损坏阀针。
二、电子万能材料试验机
微机控制电子式万能试验机是配备全数字化测量控制系统的新型试验机,它主要用于橡胶、塑料、纸张、皮革、金属丝、金属箔、织物、线绳、胶带、粘结剂等材料拉伸、剥离等力学性能试验。适用于工矿企业的质量检测、大专院校的教学,科研单位的材料研究。 特点:
1、它具有准确的加载速度和测力范围,能实现恒荷载、恒应变和恒位移自动控制,也有低周循环荷载、循环变形和循环位移的功能;
2、试验机配有计算机测控系统,可通过键盘设置试验条件并进行操作;实验后可直接由计算机显示和打印试验曲线和试验结果
3、试验机一般为门式框架结构,紧凑,体积小,重量轻。
三、材料力学实验开放式教学平台
YDD-1型多功能材料力学试验机是针对《材料力学》实验教学开发的新型试验设备,能够完成《材料力学》教学大纲规定的基本试验。包括典型材料的拉压试验、测定材料弹性模量和泊松比的试验、扭转试验、剪切实验、梁弯曲正应力电测试验、弯扭组合正应力电测实验、等强度梁实验及压杆稳定实验等。
可完成的试验
在YDD-1型多功能材料力学试验机上可进行如下的实验
1、金属材料拉伸、压缩试验
2、金属材料压缩试验
3、金属材料正、反向反复扭转试验
4、拉、压交变加载弹性模量E及泊松比μ电测试验
5、正、反向扭转测G试验
6、不同支座形式的梁交变弯曲电测试验
7、交变加载带内压弯扭管弯扭组合电测试验
8、带侧向干扰压杆稳定电测试验
9、交变加载等强度梁电测试验
10、压力容器电测试验
11、偏心拉伸、偏心压缩电测试验
与传统试验机与组合实验台相比主要有以下特点:
1、最为基本的拉压、扭转、弯扭试验组合在同一设备上完成;
2、国标试件最小夹头设计,有利于试件的快速装夹。
3、加载采用单实验空间的拉、压反复加载方式,方便实现拉压交变加载;
4、可进行油缸类压力容器应力状态电测实验,可演示不同方向应力变化对应变的影响综合性、设计性实验等。
5、扭转加载采用双向扭转方式,可进行反复双向扭转的综合性实验。
6、带侧向干扰的压杆稳定实验装置可准确按压杆失稳定义演示压杆失稳现象。
7、所有被测参量均采用电测的方式,数据采集系统采样通道多、采样频率高、采样种类多。设置8个并行通道(可扩展至128通道),可进行应变、电压、脉冲计数等测量,采样频率可达200Hz。
8、在测试过程中以窗口的形式显示各种测试数据的实时曲线、X-Y曲线、棒图等,每个窗口4条曲线,最多可开设16个窗口。在实验过程中可随时增加、减少观测窗口的数量及排列方式,随意调整窗口的测量通道及坐标、曲线颜色等窗口参数。
9、实验过程可通过设置报警参数达到自动控制反向加载的功能,且可在实验过程中不停止数据采集的情况下修改报警参数,有利于实验的循序渐进确保证试件的安全。
10、配备摄像头、屏幕实时拷贝软件等可将试验操作过程、实验现象、实验数据同步保存。同时非常方便教师制作实验教学多媒体课件。
11、加载方式可连续加载也可分级加载,实验过程中不需记录数据,实验完成后可对实验数据进行二次非线性修正分析,进行不同通道数据的四则运算,并可将数据转化为Excell、Matlab、位图文件等数据格式,方便数据的调用与二次分析。
12、配有双主机的同步网络教学系统,教师讲解时可将带有试验机的1号教师机上的内容同步地传输到每一台学生机上。
13、开发了“《材料力学》实验开放式实验教学平台”,该平台将实验指导书、实验预习报告、实验报告、实验数据库、实验过程视频讲解、实验过程动画演示、数据采集分析环境、相关文献等与实验教学有关的内容以网站的形式链接在一起,学生在实验前可分析以往的实验数据,实验过程中根据自身的情况观看不同的教学课件,自行掌握实验进度,学生可在无教师讲解的情况下独立完成实验设备操作,达到开放式实验教学的目的。
14、在教师机的桌面上设有学生机主机电源控制按钮,实验前教师根据学生对实验的了解程度决定是否可以开机实验,实验过程中教师如发现学生有安全隐患可直接关闭任意一台学生机的主机,以确保实验安全。
实验二 拉 伸 实 验
1、概述
常温、静载作用下(应变速率≤10-1)的轴向拉伸实验是测量材料力学性能中最基本、应用最广泛的实验。通过拉伸实验,可以全面地测定材料的力学性能,如弹性、塑性、强度、断裂等力学性能指标。这些性能指标对材料力学的分析计算、工程设计、选择材料和新材料开发都有极其重要的作用。
2、实验目的
2.1 测定低碳钢的下列性能指标:两个强度指标流动极限s、强度极限b,两个塑性指标断后伸长率、断面收缩率;测定铸铁的强度极限b。
2.2观察上述两种材料在拉伸过程的各种实验现象,并绘制拉伸实验的F-l曲线。
2.3分析比较低碳钢(典型塑性材料)和铸铁(典型脆性材料)的力学性能特点与试样破坏特征。
2.4了解实验设备的构造和工作原理,掌握其使用方法。
3、实验原理
对一确定形状试件两端施加轴向拉力,使有效部分为单轴拉伸状态,直至试件拉断,在实验过程中通过测量试件所受荷载及变形的关系曲线并观察试件的破坏特征,依据一定的计算及判定准则,可以得到反映材料拉伸试验的力学指标,并以此指标来判定材料的性质。为便于比较,选用直径为10mm的典型的塑性材料低碳钢Q235及典型的脆性材料灰铸铁HT200标准试件进行对比实验。常用的试件形状如图1.1所示,实验前在试件标距范围内有均匀的十等分线。典型的低碳钢(Q235)的FL曲线和灰口铸铁(HT200)的FL曲线
图1.1常用拉伸试件形状
如图1.2、图1.3所示。
图1.2
低碳钢拉伸FL曲线 图1.3 铸铁拉伸FL曲线
Fp-比例伸长荷载;Fe-弹性伸长荷载;Fsu-上屈服荷载; Fb-极限荷载 Fsl-下屈服荷载;Fb-极限荷载;Fk-断裂荷载 低碳钢Q235试件的断口形状如图1.4所示, 铸铁HT200试件的断口形状如图1.5所示,
图1.4 低碳钢Q235试件拉伸实验断口形式
观察低碳钢的FL曲线,并结合受力过程中试件的变形,可明显地将其分为四个阶段:弹性阶段、屈服阶段、强化阶段、局部变形阶段。
图1.5 铸铁HT200试件拉伸实验断口形式
这样通过对低碳钢拉伸实验过程中FL曲线的分析就可以得到反映低碳钢抵抗拉伸荷载的力学性能指标:屈服强度:s,抗拉强度:b,延伸率:5/10,断面收缩率:,断裂应力:k。
同样通过对铸铁试件FL曲线的分析就可以得到反映铸铁抵抗拉伸荷载的相应力学性能指标,对于典型的脆性材料铸铁,观察其FL曲线可发现在整个拉伸过程中变形很小,无明显的弹性阶段、屈服阶段、强化阶段、局部变形阶段,在达到最大拉力时,试样断裂。观察实验现象可发现无屈服、颈缩现象,其断口是平齐粗糙的,属脆性破坏但由于铸铁在拉伸实验过程中没有表现出塑性指标,所以,在拉伸实验过程中我们只能测得其抗拉强度:b。
4、实验方案
4.1实验设备、测量工具及试件
YDD-1型多功能材料力学试验机(图1.8)、150mm游标卡尺、标准低碳钢、铸铁拉伸试件(图
图1.8 YDD-1型多功能材料力学实验机
1.1)。
YDD-1型多功能材料力学试验机由试验机主机部分和数据采集分析两部分组成,主机部分由加载机构及相应的传感器组成,数据采集部分完成数据的采集、分析等。
试件采用标准圆柱体短试件,为方便观测试件的变形及判定延伸率,试验前需用游标卡尺测量出试件的最小直径,并根据试件的最小直径(d0)确定标距的长度(L0,需进行必要的修约),并在标距长度内均匀制作标记,为方便数据处理,通常将标距长度10等份刻痕。 4.2 装夹、加载方案
安装好的试件如图1.9所示。实验时,装有夹头的试件通过夹头与试验机的上、下夹头套相联接,上夹头套通过铰拉杆与试验机的上横梁呈铰接状态,实验时,当油缸下行带动下夹头套向下移动并与夹头相接触时,试件便受到轴向拉力。加载过程中通过控制进油手轮的旋转来控制加载速度。 4.3 数据测试方案
图1.9 拉伸实验试件的装夹
试件所受到的拉力通过安装在油缸底部的拉、压力传感器测量,变形通过安装在油缸活塞杆内的位移传感器测量。 4.4 数据的分析处理
数据采集分析系统,实时记录试件所受的力及变形,并生成力、变形实时曲线及力、变形X-Y曲线,图1.10为实测低碳钢拉伸实验曲线,图1.11为实测铸铁拉伸实验曲线
图1.10 实测低碳钢拉伸实验曲线
在图1.10中左窗口,力、变形实时曲线,上部曲线为试件所受的力,下部曲线为试件
图1.11 实测铸铁拉伸实验曲线
的变形。右窗口,力、变形的X-Y曲线,从力变形的X-Y曲线可以清晰地区分低碳钢拉伸的四个阶段,弹性阶段、屈服阶段、强化阶段和颈缩断裂阶段。在左窗口中,通过移动光标可以方便地读取我们所需要的数据,屈服荷载Fs、极限荷载Fb、断裂荷载Fk。
实验中需要的其它数据,原始标距断裂后的长度LK、断裂处最小截面面积AK,依据实验要求由游标卡尺直接或间接测量。
在图1.11中,透过移动光标可得到铸铁拉伸的极限荷载Fb,通过峰值光标或利用统计功能可方便得到极限荷载。
得到相关数据后,依据实验原理,就可以得到我们所需要的力学指标。
5、完成实验预习报告
在了解实验原理、实验方案及实验设备操作后,就应该完成实验预习报告。实验预习报告包括:明确相关概念、预估试件的最大载荷、明确操作步骤等,在完成预习报告时,有些条件实验指导书已给出(包括后续的试验操作步骤简介)、有些条件为已知条件、有些条件则需要查找相关标准或参考资料。通过预习报告的完成,将有利于正确理解及顺利完成实验。
有条件的同学可以利用多媒体教学课件,分析以往的实验数据、观看实验过程等。
完成实验预习报告,并获得辅导教师的认可,是进行正式实验操作的先决条件。
6、实验操作步骤简介
6.1试件原始参数的测量及标距的确定
实验采用标准短试件,试件形状见图1.6,用游标卡尺在标距长度的中央和两端的截面处,按两个垂直的方向测量直径,取其算术平均值,选用三处截面中最小值进行计算。 6.2装夹试件
6.2.1旋转上夹头套使之与上横梁为铰接状态。
6.2.2用楔形片将试件的两端安装到夹头内,图1.12为试件装夹示意。
图1.12试件装夹示意
6.2.3调整试验机下夹头套的位置,操作步骤:关闭“进油手轮”,打开“调压手轮”,选择“油泵启动”,“油缸上行”,打开“进油手轮”,下夹头套上行,此时严禁将手放在上、下夹头套的任何位置,至合适位置后,关闭“进油手轮”。
6.2.4将带有夹头的试件安装到上下夹头套内。
6.2.5调整下夹头套至拉伸位置。操作步骤:选择“拉伸下行”,打开进油手轮,下夹头套下行,控制下夹头套移动速度,下夹头进入下夹头套,当试件夹头和夹头套的间隙在2-3mm时,关闭“进油手轮”,此时试件可以在夹头套内灵活转动。关闭“调压手轮”,试件装夹完毕。
6.3连接测试线路
按要求联接测试线路,一般第一通道选择测力,第三通道选择测位移。联线时应注意不同类型传感器的测量方式及接线方式。联线方式应与传感器的工作方式相对应。 6.4设置数据采集环境 6.5 加载测试
在试件装夹完毕,并确定数据采集系统能正常工作后,就可以进行加载测试了。具体操作步骤如下:
首先需要确定试验机的状态,“进油手轮 ”关闭,“调压手轮 ”关闭。 然后选择“油泵启动”,“拉伸下行” ,完成后,开始数据采集,选择“控制”--“平衡”--“清除零点”,“启动采样”。左窗口,采集到的零点数据,打开“进油手轮”进行加载测试,控制加载速度,注意观察各阶段实验现象,起始阶段应缓慢加载。试件受力后,首先是弹性阶段试件所受的荷载与试件的变形呈线性关系。接着进入屈服阶段此时试件所受的力在一定范围内浮动震荡而位移不断地向前增加,这就是低碳钢的屈服现象。离开了屈服阶段后,进入了强化阶段。此时应旋转“进油手轮”加快加载速度,可以看到试件的变形明显加快。注意捕捉颈缩点,颈缩后,为观察颈缩现象,应放慢加载速度,注意捕捉颈缩点,及观看颈缩现象。当出现颈缩后,放慢加载速度,至试件断裂后,关闭“进油手轮”,“停止采样”,“油泵停止”,“拉压停止”。
这样就完成了实验的加载测试过程。
7、分析数据完成实验报告
7.1 验证数据
设置双窗口显示数据,左窗口实时曲线、右窗口力-位移X-Y曲线。单击左窗口,横向压缩数据,显示全数据;单击右窗口,X-Y增加数据,显示力-位移X-Y曲线。从低碳钢拉伸实验曲线中应清晰区分低碳钢拉伸的四个阶段,铸铁则无屈服阶段。 7.2读取数据
7.2.1荷载数据的读取
图1.10中,采用双光标可以方便地得到低碳钢拉伸的屈服荷载和极限荷载。选择并移动单光标,结合试件的变形,读出试件的断裂荷载。
铸铁无屈服荷载,极限荷载的读取同低碳钢。 7.2.2试件变形指标的读取
首先,将断裂后的试件从上下夹头套中取出,观察断口形式。然后将断裂后的试件对接,用游标卡尺测量断口直径,垂直方向测量两次,然后测量断裂后试件的标距。为了方便测量,我们也可以把试件先取出,然后再测量,采用专门的取出垫块,将带有夹头的试件断口向上放在垫块上,用试件断口保护套套住试件,用锤子敲击试件保护套,便可将断裂后的试件取出,当然,试件的取出工作需要在地面上进行。
需要注意的是:当断口距标距端点的距离小于或等于L0/3时,则需要用“移位法”来计算LK。 7.3 分析数据
通过实验前的测量及实验后的数据读取就得到了我们所需要的数据,代入相应的公式或计算表格即可得到拉伸的各项力学指标。 7.4完成实验报告
通过观察试验现象、分析试验数据就可以进行试验报告的填写了,完成实验报告的各项内容。并总结试验过程中遇到的问题及解决方法。
实验三 压 缩 实 验
1、概述
实验表明,工程中常用的金属塑性材料,其受拉与受压是所表现出来的强度、刚度和塑性等力学性能是大致相同的。但广泛使用的脆性材料如铸铁、砖、石等,其抗拉强度很低,但抗压强度却很高。为便于合理选用工程材料,以及满足金属成型工艺的要求,测定材料受压时的力学性能是十分重要的。因此,压缩实验和拉伸实验一样,也是测定材料在常温、静载、单向受力状态下力学性能的最常用最基本的实验之一。
2、实验目的
2.1测定低碳钢压缩实验的屈服极限s; 2.1测定铸铁压缩实验的抗压强度b;
2.3观察并比较低碳钢(塑性材料的代表)和铸铁(脆性材料的代表)在压缩时的变形和破坏现象。
3、实验原理
对一确定形状试件(详见试件的制作)两端施加轴向压力,使试件实验段处于单轴压缩状态,试件产生变形,在不断压缩过程中不同材料的试件会有不同的实验现象, 在实验过程中通过测量试件所受荷载及变形的关系曲线并观察试件的破坏特征,依据一定的计算及判定准则,可以得到反映材料压缩试验的力学指标,并以此指标来判定材料的性质。为便于比较,选用如图2.1所示直径相同的典型塑性材料低碳钢Q235及典型的脆性材料灰铸铁HT200标准试件进行对比实验。
图2.1压缩试件
图2.2低碳钢压缩FL曲线 图2.3铸铁压缩FL曲线 典型的低碳钢(Q235)的FL曲线和灰口铸铁(HT200)的FL曲线如图2.2、图2.3所示。
低碳钢Q235试件的压缩变形过程如图2.4所示,铸铁HT200试件的压缩破坏形状如图2.5所示。
图2.4 低碳钢Q235试件压缩实验变形过程
图2.5 铸铁HT200试件压缩实验破坏现象
观察F-l曲线,及试件的变形可发现,低碳钢F-l曲线有明显的拐点,称之为屈服点,以此点计算的屈服强度sFs/S0,其值与拉伸时屈服强度接近,继续加载,试件持续变形,由中间稍粗的鼓形变成圆饼形,但并不发生断裂破坏。铸铁的F-l曲线无明显拐点,当压力增大时,试件表面出现交错的剪切滑移线,试件中间略微变粗,持续加压剪切滑移线明显增多、增宽,最终试样在与轴线大约成45~55的方向上发生断裂破坏,此时施加的压力达到最大值,并以此值定义铸铁的抗压强度bFb/S0。
实验表明材料受轴向力产生压缩变形时,在径向上会产生一定的横向延伸,尤其是到屈服点以后这种变形更为明显,但由于试件两端面与试验机垫板间存在摩擦力,约束了这种横向变形,故压缩试样在变形时会出现中间鼓胀现象,塑性材料试件尤其明显。为了减少鼓胀效应的影响,通常的做法是除了将试样端面制作得光滑外,还在端面上面涂上润滑油以进一步减小摩擦力,但这并不能完全消除此现象。
4、实验方案
4.1实验设备、测量工具及试件
YDD-1型多功能材料力学试验机(图1.8)、150mm游标卡尺、标准低碳钢、铸铁压缩试件(图2.1)。
YDD-1型多功能材料力学试验机由试验机主机部分和数据采集分析两部分组成,主机部分由加载机构及相应的传感器组成,数据采集部分完成数据的采集、分析等。
试件采用标准圆柱体短试件,为方便观测试件的变形及测量低碳钢试件的真实应力,试验前需用游标卡尺测量出试件的最小直径(d0)及高度(H0)。 4.2 装夹、加载方案
安装好的试件如图2.6所示。压缩试验时,试件放在下承压板的中央,当控制下承压板上行,试件和
1 2 3 4 5 6
图2.6 压缩实验试件的装夹 上部承压板接触时就会对试件施加一轴向压力。压缩试验时,上承压板为一固定承压板,下承压板为一活动铰承压板,在加载过程中起到自动找正的作用,从而保证试件处于单轴受压状态。加载时通过控制进油手轮的旋转来控制加载速度。 4.3 数据测试方案
同拉伸实验一样,试件所受到的压力通过安装在油缸底部的拉、压力传感器测量,变形通过安装在油缸活塞杆内的位移传感器测量。与拉伸试验所不同的是,在压缩实验中我们所测得的力及位移均为负值。 4.4 数据的分析处理
数据采集分析系统,实时记录试件所受的力及变形,并生成力、变形实时曲线及力、变形X-Y曲线,图2.7为实测低碳钢压缩实验曲线,图2.8为实测铸铁压缩实验曲线。
图2.7 实测低碳钢压缩实验曲线
图2.8 实测铸铁压缩实验曲线 左窗口为力和变形的实时曲线窗口,右窗口为力和变形的X-Y曲线窗口。通过移动光标可以方便地读取我们所需要的数据。
得到相关数据后,依据实验原理,就可以得到我们所需要的力学指标。
5、完成实验预习报告
在了解实验原理、实验方案及实验设备操作后,就应该完成实验预习报告。实验预习报告包括:明确相关概念、预估试件的最大载荷、明确操作步骤等,在完成预习报告时,有些条件实验指导书已给出(包括后续的试验操作步骤简介)、有些条件为已知条件、有些条件则需要查找相关标准或参考资料。通过预习报告的完成,将有利于正确理解及顺利完成实验。
有条件的同学可以利用多媒体教学课件,分析以往的实验数据、观看实验过程等。
完成实验预习报告,并获得辅导教师的认可,是进行正式实验操作的先决条件。
6、实验操作步骤简介
6.1试件原始参数的测量
用游标卡尺在试件的中央按两个垂直方向多次测量试件的直径以及试件的原始高度,并将实验数据填入实验表格。 6.2装夹试件
6.2.1实验预压
操作步骤:打开“压力控制手轮”,选择“启动油泵”、“压缩上行”,打开“进油手轮”,油缸活塞杆上行,上、下承压板接触,压力表显示当前力值,旋转“调压手轮”,荷载变化,证明加载设备正常工作。
6.2.2试件安装
打开“压力控制手轮”、选择“拉伸下行”,至下夹头运行至试件安装位置,关闭“进油手轮”、将试件放在下部承压板的中央、选择“压缩上行”、打开“进油手轮”,油缸活塞杆上行至试件上部距离上部承压板1-2mm时关闭“进油手轮”,关闭“调压手轮”。这样就完成了试件的装夹。 6.3连接测试线路
按要求联接测试线路,同拉伸实验,一般第一通道选择测力,第三通道选择测位移。 6.4设置数据采集环境 6.5 加载测试
在试件装夹完毕,并确定数据采集系统能正常工作后,就可以进行加载测试了。具体操作步骤如下:
首先需要确定试验机的状态,“进油手轮 ”关闭,“调压手轮 ”关闭。 然后选择“油泵启动”,“压缩下行” ,完成后,开始数据采集,选择“控制”- “平衡”- “清除零点”,“启动采样”。左窗口,采集到的零点数据,打开“进油手轮”进行加载测试,控制加载速度,注意观察各阶段实验现象,起始阶段应缓慢加载。打开进油手轮进行加载测试,同时注意观察试件屈服、变形等实验现象,开始时应当慢一点。首先是弹性阶段试件所受的荷载与试件的变形呈线性关系,接着便是屈服阶段,试件很快就离开了屈服阶段,控制进油手轮持续加载,这时可以增大进油手轮的开启程度以增大试件所受的荷载。至120KN,关闭“进油手轮”,“停止采样”,“油泵停止”,“拉压停止”。观察试件的变形。打开“调压手轮”,“停止采样”,选择“拉伸下行”油缸活塞杆下行,取出试件。比较试件压缩前后的变化。
7、分析数据完成实验报告
7.1 验证数据
首先双窗口显示全部实验数据,左窗口实时曲线、右窗口力-位移X-Y曲线。从低碳钢压缩实验曲线中应清晰区分低碳钢压缩的屈服点,铸铁则无屈服点。 7.2读取数据
7.2.1荷载数据的读取
低碳钢压缩实验中,选择单光标,选择左右图光标同步,放大左图屈服阶段,读取屈服荷载。当然也可以像拉伸试验一样采取双光标读出屈服荷载。将得到的数据,填入到相应表格。这样就得到了屈服极限σs。
铸铁压缩实验中,无屈服荷载,极限荷载的读取同低碳钢。 7.2.2试件变形指标的读取
用游标卡尺测量压缩后试件的最大直径及高度,填入到相应表格,以得到此次低碳钢压缩实验过程中的最大应力。这样就完成了数据分析的过程。 7.3 分析数据
通过实验前的测量及实验后的数据读取就得到了我们所需要的数据,代入相应的公式或计算表格即可得到压缩的各项力学指标。
低碳钢屈服强度
sFS/S0
铸铁的强度极限
bFb/S0
对于铸铁试件而言,由于其无屈服现象,故其不存在流动极限s。
对于低碳钢试件而言,由于在压缩过程中试件的面积不断增大,承受的荷载持续增加,习惯上认为低碳钢试件无极限承载力,但假如计算时考虑试件面积的变化,会发现达到一定荷载后,压缩过程的应力应变曲线趋于平缓。在实际实验时,可以通过利用在压缩过程中测得的试件高度的变化来求得试件的对应面积,这样就可以得到压缩过程的曲线,实际分析时往往将数据转化为Matlab格式后进行分析处理,另外,在荷载较大时需考虑机架变形引起的测试误差,可通过在不加试件压缩的情况下测得机架变形与荷载的对应关系,在实际分析数据时去掉此系统误差,这样就可以较准确地得到低碳钢压缩时的曲线。实测的低碳钢压缩过程的FL与曲线的比较如图2-9所示。
实际上由于低碳钢试件在压缩过程中变形并不均匀,应力沿试件的高度并非均匀分布。可以用试件压缩过程的最大荷载除以试件压缩过
程的最大面积近似求得压缩过程的最大应力。
图2.9 实测低碳钢压缩实验FL曲线与7.4 完成实验报告 曲线比较
通过观察实验现象、分析实验数据就可以进行实验报告的填写了,完成实验报告的各项内容。并总结实验过程中遇到的问题及解决方法。
实验四 扭 转 试 验
1、概述
工程中有许多承受扭转变形的构件,了解材料在扭转变形时的力学性能,对于构件的合理设计和选材是十分重要的。扭转变形是构件的基本变形之一,因此扭转实验也是材料力学基本实验之一。
2、实验目的
1、测定低碳钢的扭转屈服强度s及抗扭强度b。
2、测定铸铁的抗扭强度b。
3、观察、比较低碳钢和铸铁在扭转时的变形和破坏现象,分析其破坏原因。
3、实验原理
对一确定形状试件两端施加一对大小为Me的外力偶,试件便处于扭转受力状态,此时试件中的单元体处于如图3.1所示的纯剪应力状态。
图3.1纯剪应力状态
对单元体进行平衡分析可知,在与试样轴线成45角的螺旋面上,分别承受主应力
01,3的作用,这样就出现了在同一个试件的不同截面上拉压的情形。这样对于判断材料各极限强度的关系提供了一个很好的条件。
图3.2为低碳钢Q235扭转实验扭矩T和扭转角的关系曲线,图3.3为铸铁HT200
图3.2低碳钢Q235扭转T曲线
图3.3铸铁HT200扭转T曲线 试件的扭转实验扭矩T和扭转角的关系曲线。图3.4为低碳钢和铸铁扭转破坏断口形式
图3.4低碳钢和铸铁扭转破坏断口形式
由图3.2低碳钢扭转T曲线可以看出,低碳钢Q235的扭转T曲线类似于拉伸的FL曲线,有明显的弹性阶段、流动屈服阶段及强化阶段。在弹性阶段,根据扭矩平衡原理,由剪应力产生的合力矩需与外加扭矩相等,可得剪应力沿半径方向的分布为:
T* IP在弹性阶段剪应力的变化如图3.5所示
图3.5 低碳钢扭转试件弹性阶段应力分布变化
在弹性阶段剪应力沿圆半径方向呈线性分布,据此可得
maxT*rT IPWP当外缘剪应力增加到一定程度后,试件的边缘产生流动现象,试件承受的扭矩瞬间下降,应力重新分布至整个截面上的应力均匀一致,称之为屈服阶段,在屈服阶段剪应力的变化如图3.6所示
称达到均匀一致时的剪应力为剪切屈服强度(s),其对应的扭矩为屈服扭矩,习惯上将屈服段的最低点定义为屈服扭矩,同样根据扭矩平衡原理可得:
s
3Ts*3Ts 4IP4WP
图3.6 低碳钢扭转试件屈服阶段应力分布变化
应力均匀分布后,试件可承受更大的扭矩,试件整个截面上的应力均匀增加,直至试件剪切断裂,如图3.4所示,最大剪应力对应的扭矩为最大扭矩,定义最大剪应力为剪切强度。
b3Tb 4WP通过以上的分析可知:在低碳钢的扭转时,可以得到剪切强度极限,但由于不同材料的破坏形式并不一致,其剪切强度的计算公式并不相同,鉴于此,为方便不同材料力学特性的比较,国标《金属扭转实验方法》(GB/T10128-1988)规定,材料的扭转屈服点和抗扭强度按公式τsTs/WP,τbTb/WP计算。需要注意的是,国标定义的强度为抗扭强度而非剪切强度。
由图3.2铸铁扭转T曲线可以看出,铸铁HT200的扭转T曲线类似于拉伸的FL曲线,没有屈服阶段及强化阶段。从图3.1纯剪应力状态及图3.4铸铁扭转破坏断口形式可以看出,铸铁试件是沿与轴线成45度螺旋面方向被拉伸破坏的,也就是说,在图3.1纯剪应力状态单元体中,拉应力首先达到拉伸强度值。其抗扭强度的计算同低碳钢试件,且此时抗扭强度等于最大扭矩时的最大剪应力(即边缘剪应力)。
由以上分析可知:铸铁的扭转破坏是由于拉应力引起的拉伸破坏,通过扭转实验可间接测得铸铁试件的拉伸强度,但无法得到其剪切强度。
4、实验方案
4.1实验设备、测量工具及试件
YDD-1型多功能材料力学试验机(图1.8)、150mm游标卡尺、标准低碳钢、铸铁扭转试件(图3.7)。
YDD-1型多功能材料力学试验机由试验机主机和数据采集分析系统两部分组成,主机部分由加载机构及相应的传感器组成,数据采集部分完成数据的采集、分析等。 试件采用两端为扁形标准扭转试件,按国标《金属扭转实验方法》(GB/T10128-1988)的规定制作,试件的两端与试验机的上、下扭转夹头相联接。为方便观测试件的变形,试验前需用游标卡尺测量出试件的最小直径(d0)。为方便观测试件的变形、观察实验现象实验前在试件上作一组如图3.7所示的矩形框标记。
图3.7 常用扭转试件
4.2 装夹、加载方案
安装好的试件如图3.8所示。试件两端为扁形,扭转试验时,试件的两端与试验机的上、下扭转夹头相联接,夹头中间有矩形加载槽。上夹头通过花键轴与扭矩传感器联接,花键轴在扭矩传感器中可上下滑动,以适合安装试件。下夹头通过双键与试验机的扭转轴相联接。扭转时,扭矩传感器固定不动,扭转电机带动下夹头转动,试件受到扭转。 4.3 数据测试方案
扭矩通过上夹头-花键轴传至扭矩传感器,试件的转角通过安装在扭转轴上的光电编码器转化为电压方波信号,转轴每转过一个确定的角度,光电编码器就输出一个方波信号,这样,通过记录方波的数量就可以知道试件的转角,扭转时,数据采集系统每检测到一个方波就记录一次数据,并将方波数量代表的转角作为X轴,扭矩作为Y轴显示数据,这样就得到了扭转试验的扭矩-转角曲线。 4.4 数据的分析处理
数据采集分析系统,实时记录试件所受的扭矩及转角,并生成扭矩、转角实时曲线。图3.9为实
1、3-扭转上下夹头, 2-扭转试件 ,
4-左立柱,5-扭矩传感器 图3.8 扭转实验试件的装夹
3.9实测低碳钢扭转Tφ曲线
测低碳钢Q235扭转实测曲线,图3.10为实测铸铁HT200的扭转实测曲线。
在图3.9低碳钢Q235扭转实验曲线中,横坐标-试件的转角,纵坐标-试件所受的扭矩,从扭矩-转角曲线可以清晰地区别低碳钢扭转实验的弹性阶段、屈服阶段,并可方便地读取屈服扭矩、极限扭矩。
图3.10实测铸铁扭转Tφ曲线
得到相关数据后,依据实验原理,就可以得到我们所需要的力学指标。
5、完成实验预习报告
在了解实验原理、实验方案及实验设备操作后,就应该完成实验预习报告。实验预习报告包括:明确相关概念、预估试件的最大载荷、明确操作步骤等,在完成预习报告时,有些条件实验指导书已给出(包括后续的实验操作步骤简介)、有些条件为已知条件、有些条件则需要查找相关标准或参考资料。通过预习报告的完成,将有利于正确理解及顺利完成实验。
有条件的同学可以利用多媒体教学课件,分析以往的实验数据、观看实验过程等。
完成实验预习报告,并获得辅导教师的认可,是进行正式实验操作的先决条件。
6、实验操作步骤简介
6.1试件原始参数的测量及标距的确定
实验采用标准短试件,试件形状见图3.7,用游标卡尺在标距长度的中央和两端的截面处,按两个垂直的方向测量试件的直径,填入实验表格取三组数据平均值的最小值进行计算。计算出扭转试件的抗扭截面系数Wp。
为了更好的观察实验现象,实验前,在扭转试件表面制作一组矩形框标记,实验中应注意观察矩形框的变化。 6.2连接测试线路
按要求联接测试线路,一般第3通道选择测扭矩,第八通道选择测转角,第七通道进行扭转方向判断。连接试验机上的转角传感和扭转传感接口。联线时应注意不同类型传感器的测量方式及接线方式。联线方式应与传感器的工作方式相对应。 6.3设置数据采集环境 6.4装夹试件
在确信设备和采集环境运行良好后,便可以进行试件的装夹,安装时,将试件的一端安装在上夹头内,下拉上夹头,使试件的另一端接近下夹头,通过控制电机正反向转动,调整下夹头位置,使试件可以方便的进入下夹头,向下轻推上夹头,松手后,依靠摩擦力保证上夹头不被拉回。反复扭转时,需使用夹头紧定螺钉。
这样便完成了试件的装夹。 6.5 加载测试
在试件装夹完毕,并确定数据采集系统能正常工作后,就可以进行加载测试了。具体操作步骤如下:
选择“控制”- “平衡”- “清除零点”- “启动采样”,选择好存储目录后便开始采集数据。实验时可以通过显示实时数据全貌窗口来观测试件扭转全过程,单击“显示数据全貌”图标,调入显示数据全貌窗口,重排显示窗口,选择被测通道,调整窗口坐标。然后选择“正向扭转”,开始数据采集,试件很快进入屈服阶段,并很快进入强化阶段。注意观察标距线的变化,横向标距线的距离不变,竖向标距线变成螺旋线而且间距变短。由于标距线的距离不断伸长,原来清晰的标距线变得不太清晰。持续扭转,试件断裂后,将上夹头拉起,停止采集数据,停止扭转。取出断裂试件,观察端口形式及标距线的变化。注意观察实验各阶段现象及标记线的变化。
反复扭转时,需启动扭转自动控制功能,并根据需要在测试过程中调整报警参数。
7、分析数据完成实验报告
7.1 验证数据
首先关闭 “显示数据全貌”窗口,在扭矩-转角窗口显示全部实验数据,并验证数据的正确性。从低碳钢扭转实验曲线中应能清晰地看到低碳钢扭转时的屈服及强化阶段,铸铁则无屈服阶段。 7.2读取数据
选择双光标,放大左图屈服阶段,读取屈服扭矩Ts,极限扭矩Tb及转角φ。
7.3 分析数据
将得到的实验数据填入到相应表格,屈服扭矩,极限扭矩,这样就得到了抗扭屈服强度,抗扭强度,剪切屈服强度以及剪切强度。
需要注意的是:
在分析数据时需特别注意区别抗扭强度与剪切将度的区别,抗扭强度的定义是针对荷载类型定义的,有利于不同材料间的相互比较,但无法反映性材料真实的应力状态。剪切强度是按材料破坏时的应力状态定义的,能够反映材料破坏时的真实应力状态,但不同材料破坏时的应力状态并不相同,计算时不同材料需根据材料的破坏特征确定计算公式。 7.4 完成实验报告
通过观察试验现象、分析试验数据就可以进行试验报告的填写了,依据实验原理,将所测得各参数带入相应的计算公式即可得到相应的力学指标。但在各参数的测量过程中,应明确各参数的准确定义,并尽可能减小测量误差。完成实验报告的各项内容。并总结试验过程中遇到的问题及解决方法。
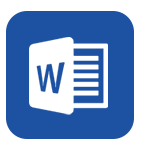