第一章
1.冲压概念
利用安装在压力机上的冲模对材料施加压力,使其产生分离或塑性变形,从而获得所需零件的一种压力加工方法。冲压加工通常是在室温下进行,故称冷冲压(cold preing )。 2.冲压成形特点
优点: ①制件复杂废料少;②精细光滑互换好;③刚度较高节省料;④易于控制效率高;⑤大批生产成本低。
缺点:单件小批量生产、精度高、技术要求高,技术密集,要求板材有良好的冲压成形性能,制造成本高。生产中有噪声。所以,冲压成形适宜批量生产。 3冲压工序的分类.分离工序:即冲裁工序是指使板料按一定的轮廓线断裂分离而获得一定形状、尺寸的冲压件的工序。分离工序主要有冲孔、落料、切断、切舌、切边、剖切、整修及精冲等。
成形工序:冲压成形时,变形材料内部的等效应力超过屈服极限,但未达到强度极限,使材 料产生塑性变形,从而成形零件。成形工序主要有弯曲、拉深、成形、冷挤压等。
第二章
1.金属塑性变形的基本概念
在外力的作用下,金属产生的形状和尺寸变化称为变形,变形分为弹性变形与塑性变形.弹性:卸载后变形可以恢复特性,可逆性
塑性:物体产生永久变形的能力,不可逆性
2.塑性:指金属在外力的作用下,能稳定的发挥塑性变形而不破坏其完整性的能力。 3.变形抗力:金属产生塑性变形的力为变形力,金属抵抗变形的力称为变形抗力。 4.加工硬化:材料的强度指标随变形程度的增加而增加,塑性随之降低。
5.硬化指数:是表明材料冷变形硬化性能的重要参数,对板料的冲压性能以及冲压件的质量都有较大的影响。
6.成形极限:指材料在冲压成形过程中能达到的最大变形程度。
成形质量:是指材料经冲压成形以后所得到的冲压件能够达到的质量指标,包括尺寸精度、厚度变化、表面质量及物理力学性能等。
第三章
1.冲裁变形过程:间隙正常、刃口锋利情况下,冲裁变形过程可分为三个阶段: 1)弹性变形阶段 :变形区内部材料应力小于屈服应力 。
2)塑性变形阶段 : 变形区内部材料应力大于屈服应力。凸、凹模间隙存在,变形复杂,并非纯塑性剪切变形,还伴随有弯曲、拉伸,凸、凹模有压缩等变形。
3)断裂分离阶段
:变形区内部材料应力大于强度极限。裂纹首先产生在凹模刃口附近的侧面→凸模刃口附近的侧面→上、下裂纹扩展相遇→材料分离。 2.冲裁间隙对断面质量影响因素
(1)材料性能的影响 (2)模具间隙的影响
间隙小,出现二次剪裂,产生第二光亮带;间隙大,出现二次拉裂,产生二个斜度
(3)模具刃口状态的影响 当凸模刃口磨钝时,则会在落料件上端产生毛刺;当凹模刃口磨钝时,则会在冲孔件的孔口下端产生毛刺;当凸、凹模刃口同时磨钝时,则冲裁件上、下端都会产生毛刺。 3.冲裁间隙尺寸精度及其影响因素
冲裁件的尺寸精度:指冲裁件的实际尺寸与图纸上(或公差)基本尺寸之差。
该差值包括两方面的偏差: 一是冲裁件相对于凸模或凹模尺寸的偏差;二是模具本身的制造偏差。
影响因素:(1)冲模的制造精度(零件加工和装配)(2)材料的性质(3)冲裁间隙
4.冲压力:
是指冲压加工过程中,压力机滑块所必须同时担负的各种压力的总和。冲裁时可能产生的压力包括冲裁力、卸料力、推件力及顶件力。模具结构不同,冲压力所包括的上述压力也有所不同。
1)冲裁力的计算
冲裁力:冲裁过程中凸模对板料施加的压力。
用普通平刃口模具冲裁时,冲裁力F一般按下式计算:
FKLtb注:
F——冲裁力; L——冲裁周边长度;t——材料厚度;平刃口模具冲裁,估算冲裁力F=Ltσb σb ——材料的抗拉强度
卸料力、推件力及顶件力的计算:
KF卸料力
F X
T
nK
T F
顶件力
FDKDFX
推件力
F采用弹性卸料装置和下出料方式的冲裁模时: FZFFXFT采用弹性卸料装置和上出料方式的冲裁模时: FZFFXFD采用刚性卸料装置和下出料方式的冲裁模时: FZFFT例题:如图,冲裁件材料为10钢,板厚2mm 的支架连接板,年产量20万件,试计算冲压 力,并选择冲压设备。(抗剪强度τ=350MPa) 解(1)落料力:
F落=1.3Ltτ=1.3×150×2×350=136.5KN
(2)冲孔力
F冲=2×1.3Ltτ=2×1.3πdt τ
=2×1.3×3.14×8.5×2×350=48.58KN
(3)卸料力
F卸=K卸F落=0.05×136.5=6.83KN
(4)推件力
F推=nK推F冲=4×0.055×48.58=10.69KN
该落料冲孔复合模采用倒装结构及弹压卸料和下料(冲孔废料)方式,则总冲压力为:
F总=F落+F冲+F卸+F推
=(136.5+48.58++6.83+10.69)=202.6KN 5.压力中心的确定
冲压力合力的作用点。模具的压力中心应该通过模柄的中心线(压力机滑块的中心线),否则冲压时滑块就会承受偏心载荷,导致滑块导轨和模具导向部分不正常的磨损,还会使合理的间隙得不到保证,从而影响冲件的质量和降低模具寿命甚至损坏模具。 压力中心确定方法 :解析法、作图法、悬挂法 6.冲裁件的工艺性
是指冲裁件对冲压工艺的适应性,即冲裁件的结构、形状、尺寸及公差等技术要求是否符合冲裁加工的工艺要求。
冲裁工艺性好是指能用普通冲裁方法,在模具寿命和生产率较高、成本较低的条件下得到质量合格的冲裁件。
(1).冲裁件的结构工艺性
1)冲裁件的形状应力求简单、对称,有利于材料的合理利用。
2)冲裁件内外形的转角处要尽量避免尖角,应以圆弧过渡,以便于模具制造,减少热处理开裂,减少冲裁时尖角处的崩刃和过快磨损。
3)尽量避免冲裁件上过长的凸出悬臂和凹槽,悬臂和凹槽也不宜过小。 4)冲裁件的最小孔边距,为避免工件变形,孔边距不能过小。
5)在弯曲件或拉深件上冲孔时,孔边与直壁之间应保持一定距离,以免冲孔时凸模受水平推力而折断。
6)冲孔时因受凸模强度的限制,孔的尺寸不应太小,否则凸模易折断或压弯。 (2)冲裁件的尺寸精度和表面粗糙度
冲裁件的精度一般可分为精密级与经济级两类。
1) 冲裁件的经济公差等级不高于IT11级,一般要求落料件公差等级最好低于IT10级,冲孔件最好低于IT9级。如果工件要求的公差等级较高时,冲裁后采用整修或采用精密冲裁。 2) 冲裁件的断面粗糙度与材料塑性、材料厚度、冲裁模间隙、刃口锐钝以及冲模结构等有关。当冲裁厚度为2mm以下的金属板料时,其断面粗糙度Ra一般可达12.5~3.2μm。 (3)冲裁件尺寸标注
冲裁件尺寸的基准应尽可能与其冲压时定位基准重合,并选择在冲裁过程中基本上下不变动的面或线上。
(4)冲裁加工的经济性分析
1)冲裁件的制造成本
冲裁件的制造成本包括:C C材2)降低冲压件成本的途径
C工C模
⑴降低小批量生产中的冲压件成本; ⑵使工艺合理化; ⑶多件同时冲压;⑷冲压过程的高速自动化; ⑸提高材料的利用率; ⑹节约模具费用。 7.精密冲裁特点
(1)变形区处于三向压应力状态
使材料以纯剪切的形式实现分离。通过①小间隙
②齿压边圈+顶件块压紧材料来实现 。
(2)小间隙
约为普通冲裁的10%
(3)凹模带有小圆角
R=0.1t,避免刃口处应力集中
以上三点使材料冲裁时不出现开裂和撕裂,获得平滑塑性剪切断面。
(4)更大的冲裁力
F=(2.3~2.5)F普通
第四章
1.弯曲变形区的应力、应变分析
板料在塑性弯曲时,变形区内的应力应变状态取决于弯曲毛坯的相对宽度 b/t 以及弯曲变形程度。
2.应力中性层:板料截面上的应力由外层的拉应力过渡到内层的压应力,其间金属的切向应力为零的金属层。
变形程度较小时,应力中性层和应变中性层相重合,均位于板料截面中心的轨迹上。
变形程度比较大时,由于径向压应力的作用,应力中性层和应变中性层都从板厚的中央向内侧移动,应力中性层的位移量大于应变中性层的位移量。
应变中型层:是指在变形前后金属纤维的长度没有发生改变的那一层金属纤维。 3.偏移:
在弯曲过程中,坯料沿凹模边缘滑动时要受到摩擦阻力的作用,当坯料各边所受到的摩擦力不等时,坯料会沿其长度方向产生滑移,从而使弯曲后的零件两直边长度不符合图样要求,这种现象称为偏移。
1)产生偏移的原因
(1)弯曲件坯料形状不对称
(2)弯曲件两边折弯的个数不相等
(3)弯曲凸、凹模结构不对称 。 此外,坯料定位不稳定、压料不牢、凸模与凹模的圆角不对称、间隙不对称和润滑情况不一致时,也会导致弯曲时产生偏移现象。 2)控制偏移的措施
(1)采用压料装置,使坯料在压紧状态下逐渐弯曲成形,从而防止坯料的滑动,而且还可得到平整的弯曲件。
(2)利用毛坯上的孔或弯曲前冲出工艺孔,用定位销插人孔中定位,使坯料无法移动。 (3)根据偏移量大小,调节定位元件的位置来补偿偏移 。
(4)对于不对称的零件,先成对地弯曲,弯曲后再切断。
(5)尽量采用对称的凸、凹结构,使凹模两边的圆角半径相等,凸、凹模间隙调整对称。 4.最小弯曲半径rmin:
在板料不发生破坏的条件下,所能弯成零件内表面的最小圆角半径。
常用最小相对弯曲半径rmin/t表示弯曲时的成形极限。其值越小越有利于弯曲成形。
影响最小弯曲半径的因素: 1)材料的力学性能:材料塑性好,允许变形量大,rmin越小. 2)弯曲中心角 弯曲时,直边部分纤维将牵制弯曲区受拉状态。
当弯曲中心角>90°时:对减小rmin作用不大。 3)材料的纤维方向(弯曲方向)
当弯曲中心角<90°时:弯曲角愈小,对减小rmin愈有利;
板料经轧制以后产生纤维组织,使板料性能呈现明显的方向性。一般顺着纤维方向的力学性能较好,不易拉裂。
4)板料的表面质量与剪切断面质量
质量越好, rmin越小。 5)板料的相对宽度 6)板料的厚度 5.弯裂
弯曲时板料的外侧受拉伸,当外侧的拉伸应力超过材料的抗拉强度以后,在板料的外侧将产生裂纹,此种现象称为弯裂。
实践证明,板料是否会产生弯裂,在材料性质一定的情况下,主要与弯曲半径r与板料厚度t的比值r/t(称为相对弯曲半径)有关,r/t越小,其变形程度就越大,越容易产生裂纹。
6.回弹
塑性弯曲时伴随有弹性变形,当外载荷去除后,塑性变形保留下来,而弹性变形会完全消失,使弯曲件的形状和尺寸发生变化而与模具尺寸不一致,这种现象叫回弹。
7.影响回弹的因素
1).材料的力学性能
屈模比σs/E越大,回弹越大。即:σs越高,弹性模量E越小,回弹量越大。(塑性变形前的弹性变形量大)
2).相对弯曲半径r/t
相对弯曲半径r/t越小,变形量越大,弹性变形量所占比例越小,回弹越小。
3).弯曲中心角α
弯曲中心角α越大,表明变形区的长度越长,故回弹的积累值越大,其回弹角越大。但对弯曲半径的回弹影响不大。
4)弯曲方式及校正力大小
(1)在无底凹模内作自由弯曲时,回弹最大。(2)在有底凹模内作校正弯曲时,回弹较小。校正弯曲圆角部分的回弹比自由弯曲时大为减小。校正弯曲时圆角部分的较小正回弹与直边部分负回弹的抵销 ,回弹可能出现正、零或是负三种情况。(3)在弯曲U形件时,凸、凹模之间的间隙对回弹有较大的影响。间隙越大,回弹角也就越大。
5)工件的形状
工件的形状越复杂,一次弯曲所成形的角度数量越多,使回弹困难,因而回弹角减小。
6)模具间隙
在压弯U形件时,间隙大,材料处于松动状态,回弹就大;间隙小,材料被挤压,回弹就小。
8.弯曲件坯料尺寸的计算
1)圆角半径r>0.5t的弯曲件
按中性层展开的原理,坯料总长度应等于弯曲件直线部分和圆弧部分长度之和,即
Lzl1l2180l1l2180(rKt)2)圆角半径r
按变形前后体积不变条件确定坯料长度。通常采用经验公式计算
Ll1l2(0.4~0.6)t8.弯曲件的工序安排原则
1.形状简单的弯曲件:采用一次弯曲成形;形状复杂的弯曲件:采用二次或多次弯曲成形。 2.批量大而尺寸较小的弯曲件:尽可能采用级进模或复合模。
3.需多次弯曲时:先弯两端,后弯中间部分,前次弯曲应考虑后次弯曲有可靠的定位,后次弯曲不能影响前次已成形的形状。
4.弯曲件形状不对称时:尽量成对弯曲,然后再剖切(见图)
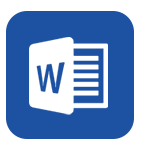