生产流程企业标准
一、业务部工作流程
⒈工作流程:客户意向或市场需求→产品报价→合同订立→产前确认评审→计划下单→制程跟踪→出货→售后服务 ⒉业务部与客户签订订单后,会同生产、技术、采购等部门进行详细核算与生产技术能力评估(评审)。 ⒊评审完成后由计划跟单下达生产计划(订单)。 ⒋产品制程跟踪、随时掌握产品生产进度。
⒌订单在执行中,如客户对订单有变更或由于公司原因不能按交货期交货,应及时与客户协商,并将协商结果通知相关内部 ⒍根据合同交货期与客户沟通支付余款、安排出货日期,并通知生产部。
⒎交货后,及时了解客户对产品的装配使用情况,并将客户的需要改善的问题反馈给相关部门,完善以后的产品。
二、生产部工作流程
⒈工作流程:接受业务订单→生产负荷分析→生产制造令→备料→物料发放及领用→生产→生产数据分析及计划达成统计→产品入库→出货
⒉生产部接到业务订单后,进行生产负荷分析,依据产能状况及订单数量,决定是否需要加班生产。 ⒊根据业务订单制定《生产制造单》并发各部门、车间 ⒋根据库存材料情况,填写《材料申购单》,交采购部
⒌根据订单交期和设备产能,制定月生产计划及周生产排程。
⒍根据预订损耗备料,原则上,按订单数量多百分之五备料,完成后据实补足余额,以减少库存品。 ⒎物料的发放要做到先到先出,按单发放,不能超额发放。
⒏调查并记录各车间每天完成的数据,以了解生产进步情况并加以控制(每天的生产情况与预计情况进行对照) ⒐找出实际进度与计划进度产生差异的原因,并采取相应措施。
⒑出现人员、设备有工作负荷过多、过少或负荷不均之情形,超负荷时可调其他部门或车间人员或设备支援;负荷不足时,适当增加其工作量,减少浪费。
⒒检查并督促各工序作业人员依据《作业指导书》及《安全操作规程》从事作业。
⒓协助品管部门做好在制品质量检测,对不良产品及时处理,并采取适当措施保证后续在制品质量 ⒔因客户变更订单内容或因生产异常造成生产作业更改,应及时调整生产计划。
⒕依据生产进步及生产日报表掌握每日生产之进步、效益及品质,做好生产数据分析及计划达成率统计。 ⒖所有自产产品,都必须百分百经过品管的检验合格后,方可入库。 ⒗按业务部出货通知按时出货
注:①在生产过程中,如发现各部门未能配合或及时完成相应任务的,可填写部门协助申请单,由计划管理出面协调,或可通知行政部门组织开展临时会议解决。②如生产环节以至影响生产计划未能及时交货的,生产部门负有不可推卸之责任
三、采购部工作流程
⒈工作流程:接收采购申请单→收集信息→询价→比价、议价→采购计划→要样→样品核准→下采或订立合同→协调、沟通→跟催→验收→付款
⒉采购部在接收到相关部门的《材料申购单》后,承办人员应查看库存资料或询问仓库人员,以确认有无库存或库存数量多少。
⒊了解供应商档案资料,了解采购之价格。
⒋研究市场供料状况及管道,通过询价、比价、议价来决定有利价格; ⒌选定供应商后应及时编制《采购计划》并发给相关部门。 ⒍向选定的供应商提供采购物品的具体要求。
⒎收到供应商的样品后,召集相关部门人员对样品进行检测、评审,不合要求时,必须要求其改进,直到样品符合要求。 ⒏供应商改进后仍不到要求时,应更换供应商及修改《采购计划》并通知相关部门。 ⒐样品经检测、评审合格后,下单采购或与供应商签订《采购合同》,其上必须写明:品名、数量、规格、质量要求、单价、金额、交期、包装方式、运输方式、结算方式、违业责任等内容。 ⒑采购确立后,将采购单发相关部门及仓库。
⒒当生产出现异常如客户要提前或延后出货、产品更改等情况,涉及到采购材料的交期变更或材料规格尺寸的变更时,应及
时与供应商协调、沟通。
⒒根据生产部提供的生产进步及采购单交期,提前跟催供应商按时按数交货。
⒓供应商交货前,承办人员应提供供应商携带送货单、订购单等票证,否则仓库将拒收。 ⒔供应商交货时,承办人员应与质检员、仓库管理员共同进行验收、交料、结算和储存工作。
⒕当收到检验员检验来料不合格报告时,承办人员应及时与供应商联系,协商对不良品的解决方案;能自行处理的,应由供应商支付返工费用;不能自行处理的,应要求供应商在可接受范围内处理完毕。
⒖经检验员为不合格的来料及承办人员通知供应商处理不良来料,供应商按时处理的,则应办理退货。 ⒗对供应商延期交货或所送材料不良及退货等情形,按《采购单》或《采购合同》之相关违约条款处理。
⒘判定不合格之材料如属紧急用料,由相关部门决定使用办法,则改判合格直接入库使用,但必须报公司领导批准。
注:采购的各项物品必须在规定时间内到位,否则采购部门违有不可推卸责任,如有无法解决问题需要各部门配合可通知行政部门开展临时会议或填写部门协助单由计划管理员出门协商解决。
四、技术部工作流程
⒈常规产品工作流程:接受生产计划单→编制材料清单→编制工艺单(图纸绘制等工作)→工装夹具的改进→制程异常处理 ①技术部接收到《生产计划订单》后,在明确规定时间期限内编制完成《材料清单》及《工艺单》,并发相关部门。 ②在现有设备、人员基础上寻求生产技术或工艺的改进,以节约材料或提高产品品质。 ③在先有设备上寻求工装夹具的改进,以提高生产效益。
④在生产中出现品质异常时,协同生产部、品质部分析异常原因采取正确措施, ⑤生产中设备出现异常时,及时排除故障。
⑥对委外加工的产品的厂商提供必要的技术支持,以保证产品质量符合要求。
⒉客户特定非标类产品工作流程:接收客户相关技术参数→分析→报价→接受生产计划单→编制材料单、工艺单→工装夹具设计与制作备→技术资料→技术培训→制程异常处理→设备异常处理
①接受到客户特殊要求后召集相关人员分析结构、材料、制造工艺及需要使用的设备、工装夹具等情况。 ②接收到《生产计划订单》后,在规定期限内编制完成《材料清单》及《工艺单》,并发相关部门。 ③根据产品加工需要设计或制备工装夹具。
④生产中出现的品质异常时,协同生产部门、品质部分析异常原因并采取正确措施 ⑤生产中设备出现的异常技,及时排除故障。
注:如因技术部延期交付相关清单与工艺图纸影响耽误生产的,技术部负有不可推卸责任。如在工作过程中需要各部门配合协调的可填写部门协助单有计划管理员跟进协商解决,或通知行政部门开临时会议。
五、品质部工作流程
⒈工作流程:接受生产计划订单→制定品质标准→制定检验规范→进料检验→制程检验→成品检验→出货检验→分析总结 ⒉接收生产制造令后,根据客户要求或行也标准指定《产品品质标准》 ⒊依据品质标准制定《检验规范》。
⒋进料检验:接收仓库通知→相关资料准备→判定→检验方式→标识→检验记录、报告
①检验员接收到仓库员的物料入库通知后,准备与物料相关的品质标准要求、检验方法等及时到库检验。 ②依《检验规范》确定对该物料采用抽检还是全检。
③对检验物料进行分类,合格品、不良品、废品等分开放置并悬挂或贴上检验标示牌(卡)。 ④检验员检验每批次物料后,都必须做好检验记录,填写《检验报告》发相关部门。 ⑤对检验出不符合要求的物料,应查找原因,提出处理措施。
⑥对检验出不符合要求的物料,如属紧急用料,经公司相关领导批准后可按规定实施才采。 ⒌制程检验:首件检验→巡检→判定→标识→检验记录、报告
①生产过程中按《检验规范》的规定对每一道工序在制品实施定时抽检,并做好检验记录。 ②对特殊工序检验,应提高巡检次数和抽检数量。
③对检验完毕的在制品必须分开放置并悬挂或贴上标示(牌)卡。以保证不良品不流入下道工序。
④对生产过程中出现的品质异常,能自行处理的,应及时解决,不能自行处理的应及时报告部门主管和相关负责人
⑤对生产过程中出现的重大品质异常,应及时报告公司领导,对于所有品质异常都必须填写《品质异常报告》发相关部门并存档。
⒍成品检验:全检→判定→标识→检验记录、报告
①按客户或订单要求,按《检验规范》采用正确的检验方法对成品进行百分百全检。
②依据具体的质量标准判定所检产品为不合格时,根据不良情况在检验报告上注明白返工事项。 ③对检验完毕的成品须悬挂或贴上标牌(卡)。 ④所有检验记录、报告都必须发相关部门并存档。
⒎品质部主管定期召集所属人员就进料、制程、成品等检验情况进行统计分析、总结,以不断提高产品质量。并将情况总结报告发至相关部门
六、仓库工作流程
⒈入库工作流程:供应商送货或采购物料回厂→核对采购单→数量验收→品质验收→入库及入帐→表格单据的分发及存档 ①供应商送货到库时,应要求供应商提供送货单、订购单等,仓管员应拒收无票证的物料,特殊情况应要求采购承办人员当面核对物料,无误后方可接收。
②供应商送货或采购员采购物料回厂到库后,应及时通知品管检验人员和采购承办人员。
③核对供应商的送货单的品名、型号、数量等是否与采购单一致,如不一致时应第一时间与采购员进行核对,查明原因并确认后方可收货。
④对于物料数量较大的按大件全点,小件百份十到四十的比列进行数量核查并做好抽查标识;对于较贵重的物料要做到数量全部清点准确;对于小件物料必须用电子称称量重量换算成数量。有异常情况的及时上报并做好记录。
⑤所有物料必须在数量清点完成后,供收双方共同确认情况下签单收货,数量异常签实收数量并要求送货人签名确认方可收货。
⑥仓管员数量验收完成后,协助检验员对物料进行质量验收。
⑦对检验合格的物料要及时按相应位置及物料特性选择合理的摆放方式摆放整齐。 ⑧对检验不合格的物料必须跟进处理结果,对于退货处理的跟进退货时至退回。
⑨做好入仓物标示卡,其上要注明白品名、供应商、入库时间、规格型号、数量等,并将标识卡置于物料正名最容易看到的位置
⑩仓管员依据验收单及时记帐,详细记录物料名称、数量、规格型号、入库时间等,做到帐、货相符合。 并讲入库单据交相关部门并存档。
⒉出库工作流程:用料部门持单领料或采购部退货单→核对单据→发料(记帐)→物料交接→表格单句的分发及存档
①仓管员收到用料部门开具的领料单或采购部门开具的退货单后,应与订单使用材料清单进行核对,如不相符,及时反映给相关人员确认无误后方可发料。
②发料或退货时,仓管员必须和领料部门主管或供应商双方对数量确认无误,共同在领料单或退货单上签字确认。 ③仓管员必须按先进先出的原则发放物料。
④物料出库时,双方应认真清点核对品名、数量、规格等,办清交接手续,若出库后发生货损等情况,责任由承运人承当。 ⑤物料出库后,仓管员应及时根据出库单销帐并清点物料结余余数,做到帐物相符。 ⑥物料发放后及时进行仓库整理。 ⑦将出库单据交相关部门并存档。
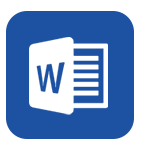