浅谈学习《丰田模式》的几点体会
2015年12月15日,收到公司发放的《丰田模式》一书,出自于内心对丰田汽车质量的高度认同,心中难免有点小激动,也比较认真拜读了一遍。作者杰弗瑞·莱克教授对丰田的研究已逾20载,遍访丰田工厂,才写下了这篇巨作,由于个人的知识面及理解能力十分有限,短时间难以消化,写下支言片语肤浅地谈以下几点体会。
丰田始于1926年丰田佐吉创立的丰田自动织布机厂,经过90年的发展,成为当今世界汽车业的翘楚,缔造了一个令世人称奇的商业神话。而丰田模式是数代丰田人共同谱写并根织于丰田人的基因里。学习丰田模式,必须持续不断“干中学”,非一日之功也。丰田模式成功的基础——思维、理念、流程,视“持续改善”和“尊重员工”为丰田精神的两大支柱,说到底是培养、建立精益的学习型企业的文化。
精益化之路是充满不确定性和挑战的,作业流程的卓越性是战略武器。这也是大多数从事精益转型企业把重心放在“流程”上原因。下面浅析建立连续作业流程的几个要素。
1、生产线的建立
正确的流程始于“单件流”(在此我把作业流狭义为产品流),即理想化的生产线上每个工序上只有一件产品在流动。让生产线的产品能够连续流动而又不产生任何积压。生产线每个关、重岗位设置生产停止按钮及异常警报灯,只要该工序有质量问题按下停止按钮(丰田
取名“安灯系统”),整条生产线即停止,警灯闪烁,可以想像这要求解决问题是多少的急迫,即可以让质量问题无法藏匿而得到迅速解决。这是生产线的建设原则,也是丰田模式的重要原则——建立立即暂停以解决问题、从一开始就重视质量控制的文化。
生产线的内检制,即生产线关、重位置应设计自动检测设备,这是生产线连续流的重要手段,没有节拍一致的自检系统,生产不是成功的。
2、拉动式生产
拉动式生产方式的精髓是我后工序需要前工序产品才能补充,在整个作业来看,客户需求1件,我们就补充1件。而传统的生产方式是推动式生产,通常是工序越靠前,存货积压越多,而且每工序都有大量存货堆积在现场或其它角落(现在我们还有许多自制弹簧未用完,这是多么可怕的事)。试想这种生产方式下,某工序出问题,可能就是批量问题,即使自检发现不是批量问题,报废数量也不是小数,除非每件产品生产出来立即检测(即全检)。再者,出了问题也不可怕,还有大量在制品可用呢,一拖再拖,形成了惰性文化。在丰田模式中根本不讲存货管理,存货在丰田人的眼中就是一种浪费,而拉动生产方式可以有效地降低存货。现在我们正在尝试和力推,阻力不少。
3、职务工作标准化
工作的标准化是持续改善与授权员工的基础。标准化的三要素是节拍时间、顺序步骤、手边存货。制定标准化必须依据这三要素。今井正明在其探讨持续改善的经典著作《改善》中指出,任何流程除非
标准化,否则不可能达到真正的改善;一个流程若乱无章法、经常改变,那么,任何针对此流程的改善只不过是多增加一项变化的种类,偶尔会被使用,但大多数时候被遗忘或忽略在一边。也就是必须先把流程标准化,继而使其稳定,然后才能谈持续改善,标准化工作任重道远。
4、可靠防错技术
人防远不如技防,技术防错永远是质量控制的最可靠手段,防错技术应用在产品开发之初,就该放到重中之重的位置加以实施及应用。
5、快速的设备切换技术
没有快速的设备切换技术,连续作业流可能中断(某个生产设备发生故障,导致整个作业小组停顿;生产设备转换时间超预期,延误整个作业小组而致生产停顿,为创造单件流或连续作业流,必须投资某个流程而导致投资增大),这是创建单件流或连续作业流必须付出的成本与代价,却致许多公司望而却步,不敢贸然化大力气持续改善。
前面是对连续作业流的理解,为什么连续作业流在精益生产或丰田模式中如此重要?因为在制造工厂中,核心的价值流程是指作业现场,而作业现场主要作业流程,所以就不难理解连续作业流程有多么重要,它是精益生产之根本,也可以说没有连续的作业流程,就没有精益的丰田模式。同样在产品研发部门中,核心价值流程就是产品研发流程,现场的连续作业流程的思路同样适用于其它流程(产品开发流程当然也不例外)。那变革我们就从现场作业流开始吧!这是我们改善的基,根据上述原则一条线一条线改善,成效会逐渐显现。
丰田公司有它的独特的发展模式,它是经历一系列领导人完善、修正之后逐渐演进而成,这其中有非常丰富的文化遗风。放眼世界,学习丰田的企业很多,却成不了第二个丰田;当年学邯钢,如今邯钢安在?中国出了一个华为让世界同行胆寒,但又有多少企业学的像华为?我们山青公司有自己发展轨迹,亦有自己独特的企业文化,所以必须要自己的根基上建立自己的发展模式,但丰田模式的精髓14原则个个值得我们去消化吸收并转换成适合我们的事业与环境背景的语言并践行之。
用丰田精益的思维去审视我们的作业流程,本书第90页有句特别震撼人的话“多数作业流程中,有90%的浪费”,生产过剩、在现场等候的时间、不必要的运输、过度处理或不正确处理、存货过剩、不必要的移动搬运、瑕疵、未被使用的员工创造力。而生产过剩是被视为头号浪费。再用这种思维思考我们的生产线、思考我们在制品、思考我们的业务流程等,一下觉得每条都发挥的“很好”,时时时刻刻都在浪费。所以集公司之力,建一条模范线就显得非常必要,彻底改变现推动式生产方式,成为其它生产线或供应商学习改善的榜样。
用丰田处理问题的原则去管好日常事务。丰田模式中有几点特别经典的原则,如制定决策时要稳健,穷尽所有选择,并征得一致意见,实施决策时要迅速;通过可视化管理使问题无所隐藏;亲临现场,彻底了解情况(现地现物)等等,这些是放之四海皆准的真理,却刚好是软肋,是大多数人不容易做到。现在每天化大量时间在开会,在纸上绘“蓝图”,凭想像或推理制定措施,在屏幕上推演解决问题等等。
能在现场一蹲几个小时发现问题并提出改善建议,可不是一朝一夕的事,这是一种能力,一种功夫,需长时间的修炼。现在的与技术员尤其缺乏这种能力。实事已经证明,肯动手的技术人员,设计能力也亦强,不管以哪种方式,都必须鼓励和要求技术员深入到现场去发现问题和改善流程。
用丰田的供应商管理理念去管理供应链。丰田的供应商与丰田公司是伙伴关系,他们有共同的目标并为之而奋斗,激励并助其改善。供应商是企业整个生产作业流程的一部分,供应商的能力及改善程度直接决定企业生产作业流程的顺畅及成本。随着公司准时送货制度的推进,供应商已表现出诸多的不适应,压低存货、减少库容面积、提高周转速度是我们必然选择,接下来,我们与供应商一起“干中学”,举办现场学习班,共同推动条码及时间窗交付,让物质流动起来。
现只通读本书一遍,从字面知晓些皮毛,我会以每天2至3页继续拜读下去,并将领悟到知识用于实践。
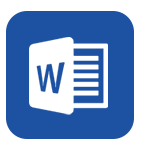