铝的生产流程
1、矿石提取氧化铝工艺
从矿石提取氧化铝有多种方法,例如:拜耳法、碱石灰烧结法、拜耳-烧结联合法等。拜耳法一直是生产氧化铝的主要方法,其产量约占全世界氧化铝总产量的95%左右。70年代以来,对酸法的研究已有较大进展,但尚未在工业上应用。
1.1、拜耳法
系奥地利拜耳(K.J.Bayer)于 1888年发明。其原理是用苛性钠(NaOH)溶液加温溶出铝土矿中的氧化铝,得到铝酸钠溶液。溶液与残渣(赤泥)分离后,降低温度,加入氢氧化铝作晶种,经长时间搅拌,铝酸钠分解析出氢氧化铝,洗净,并在950~1200℃温度下煅烧,便得氧化铝成品。析出氢氧化铝后的溶液称为母液,蒸发浓缩后循环使用。
拜耳法的简要化学反应如下:
由于三水铝石、一水软铝石和一水硬铝石的结晶构造不同,它们在苛性钠溶液中的溶解性能有很大差异,所以要提供不同的溶出条件,主要是不同的溶出温度。三水铝石型铝土矿可在125~140℃下溶出,一水硬铝石型铝土矿则要在240~260℃并添加石灰(3~7%)的条件下溶出。
现代拜耳法的主要进展在于:①设备的大型化和连续操作;②生产过程的自动化;③节省能量,例如高压强化溶出和流态化焙烧;④生产砂状氧化铝以满足铝电解和烟气干式净化的需要。拜耳法的工艺流程见图1。
拜耳法的优点主要是流程简单、投资省和能耗较低,最低者每吨氧化铝的能耗仅3×106千卡左右,碱耗一般为100公斤左右(以Na2CO3计)。
拜耳法生产的经济效果决定于铝土矿的质量,主要是矿石中的SiO2含量,通常以矿石的铝硅比,即矿石中的Al2O3与SiO2含量的重量比来表示。因为在拜耳法的溶出过程中,SiO2转变成方钠石型的水合铝硅酸钠(Na2O·Al2O3·1.7SiO2·nH2O),随同赤泥排出。矿石中每公斤SiO2大约要造成1公斤Al2O3和0.8公斤NaOH的损失。铝土矿的铝硅比越低,拜耳法的经济效果越差。直到70年代后期,拜耳法所处理的铝土矿的铝硅比均大于7~8。由于高品位三水铝石型铝土矿资源逐渐减少,如何利用其他类型的低品位铝矿资源和节能新工艺等问题,已是研究、开发的重要方向。
1.2、碱石灰烧结法
适用于处理高硅的铝土矿,将铝土矿、碳酸钠和石灰按一定比例混合配料,在回转窑内烧结成由铝酸钠(Na2O·Al2O3)、铁酸钠(Na2O·Fe2O
3、原硅酸钙(2CaO·SiO2)和钛酸钠(CaO·TiO2组成的熟料。然后用稀碱溶液溶出熟料中的铝酸钠。此时铁酸钠水解得到的NaOH也进入溶液。如果溶出条件控制适当,原硅酸钙就不会大量地与铝酸钠溶液发生反应,而与钛酸钙、Fe2O3·H2O 等组成赤泥排出。溶出熟料得到的铝酸钠溶液经过专门的脱硅过程,SiO2O形成水合铝硅酸钠(称为钠硅渣)或水化石榴石3CaO·Al2O3·xSiO2·(6-2x)H2O沉淀(其中x≈0.1),而使溶液提纯。把CO2气体通入精制铝酸钠溶液,和加入晶种搅拌,得到氢氧化铝沉淀物和主要成分是碳酸钠的母液。氢氧化铝经煅烧成为氧化铝成品。水化石榴石中的Al2O3可以再用含Na2CO3母液提取回收。
碱石灰烧结法的主要化学反应如下: 烧结:
Al2O3+Na2CO3─→Na2O·Al2O3+CO2 Fe2O3+Na2CO3─→Na2O·Fe2O3+CO2 SiO2+2CaCO3─→2CaO·SiO2+2CO2 TiO2+CaCO3─→CaO·TiO2+CO2 熟料溶出:
Na2O·Al2O3+4H2O─→2NaAl(OH)4(溶解)
Na2O·Fe2O3+2H2O─→Fe2O3·H2O↓+2NaOH(水解) 脱硅:
1.7 Na2SiO3+2NaAl(OH)4─→Na2O·Al2O3·1.7SiO2·nH2O↓+3.4NaOH 3 Ca(OH)2+2NaAl(OH)4+x Na2SiO3─→ 3CaO·Al2O3·x SiO2·(6-2x)H2O↓+2(1+x)NaOH 分解:
2NaOH+CO2─→Na2CO3+H2O NaAl(OH)4─→Al(OH)3↓+NaOH 中国碱石灰烧结法生产氧化铝的主要技术成就是:在熟料烧成中采用低碱比配方,在熟料溶出工艺中采用二段磨料和低分子比溶液,以抑制溶出时的副反应损失,使熟料中Na2O和Al2O3的溶出率分别达到94~96%和92~94%。Al2O3的总回收率约90%,每吨氧化铝的Na2CO3的消耗量约95公斤。碱石灰烧结法可以处理拜耳法不能经济地利用的低品位矿石,其铝硅比可低至3.5,且原料的综合利用较好,有其特色。
碱石灰烧结法的常用流程见图2
1.3、拜耳-烧结联合法
可充分发挥两法优点,取长补短,利用铝硅比较低的铝土矿,求得更好的经济效果。联合法有多种形式,均以拜耳法为主,而辅以烧结法。按联合法的目的和流程连接方式不同,又可分为串联法、并联法和混联法三种工艺流程。
① 串联法是用烧结法回收拜耳法赤泥中的Na2O和Al2O3,用于处理拜耳法不能经济利用的三水铝石型铝土矿。扩大了原料资源,减少碱耗,用较廉价的纯碱代替烧碱,而且Al2O3的回收率也较高。
② 并联法是拜耳法与烧结法平行作业,分别处理铝土矿,但烧结法只占总生产能力的10~15%,用烧结法流程转化产生的NaOH补充拜耳法流程中NaOH的消耗。
③ 混联法是前两种联合法的综合。此法中的烧结法除了处理拜耳法赤泥外,还处理一部分低品位矿石。
中国根据本国的铝矿资源特点,发展出多种氧化铝生产方法。50年代初就已用碱石灰烧结法处理铝硅比只有3.5的纯一水硬铝石型铝土矿,开创了具有特色的氧化铝生产体系。用中国的烧结法,可使Al2O3的总回收率达到90%;每吨氧化铝的碱耗(Na2CO3)约 90公斤;氧化铝的SiO2含量下降到0.02~0.04%;而且在50年代已经从流程中综合回收金属镓和利用赤泥生产水泥。60年代初建成了拜耳烧结混联法氧化铝厂,使Al2O3总回收率达到91%,每吨氧化铝的碱耗下降到60公斤,为高效率地处理较高品位的一水硬铝石型铝土矿开创了一条新路。中国在用单纯拜耳法处理高品位一水硬铝石型铝土矿方面也积累了不少经验。
根据物理特性的不同,电解用氧化铝可分为三类:砂状、粉状和中间状(表3)。
目前铝工业正研制和采用砂状氧化铝,因为这种氧化铝具有较高的活性,容易在冰晶石溶液中溶解,并且能够较好地吸收电解槽烟气中的氟化氢,有利于烟气净化。
炼铝用氧化铝的化学组成一般如下: Al2O3 SiO2 ZnO Na2O P2O5 灼减 >98.35%
Fe2O3 TiO2 CaO
0.01~0.04% <0.005% 0.007~0.07% <0.003% <0.002% 0.01~0.04% 0.003~0.02% 0.3~0.65%
<0.003% 0.2~1.5%
V2O5 Cr2O3 1.4、赤泥
赤泥是制铝工业提取氧化铝时排出的污染性废渣,一般平均每生产1吨氧化铝,附带产生 1.0~2.0吨赤泥。中国作为世界第4大氧化铝生产国,每年排放的赤泥高达数百万吨。
赤泥矿物成分复杂,采用多种方法对其进行分析,主要有以下几种方法:偏光显微镜、扫描显微镜、差热分析仪、X衍射、化学全分析、红外吸收光谱和穆斯堡尔谱法等七种方法进行测定,其结果是赤泥的主要矿物为文石和方解石,含量为60%~65%,其次是蛋白石、三水铝石、针铁矿,含量最少的是钛矿石、菱铁矿、天然碱、水玻璃、铝酸钠和火碱。其矿物成分复杂,且不符合天然土的矿物组合。在这些矿石中,文石、方解石和菱铁矿,既是骨架,又有一定的胶结作用;而针铁矿、三水铝石、蛋白石、水玻璃起胶结作用和填充作用。
赤泥的物理性质:颗粒直径0.088~0.25毫米,比重2.7~2.9,容重0.8~1.0,熔点1200~1250℃。
赤泥的化学性质:赤泥的pH值很高,其中:浸出液的pH值为12.1-13.0,氟化物含量11.5 mg·L-1-26.7 mg·L-1;赤泥的pH值为10.29-11.83,氟化物含量4.89 mg·L-1-8.6 mg·L-1。按GB 5058-85有色金属工业固体废物污染控制标准,因赤泥的pH值小于12.5,氟化物含量小于50 mg·L-1,故赤泥属于一般固体废渣。但赤泥附液pH值大于12.5,氟化物含量小于50 mg·L-1,污水综合排放划分为超标废水,因此,赤泥(含附液)属于有害废渣(强碱性土)。
2、铝电解
铝电解的原理是使直流电通过以氧化铝为原料、冰晶石为溶剂组成的电解质,在950~970℃下使电解质熔液中的氧化铝分解为铝和氧。由于比重的差别在阴极上析出的铝液汇集于电解槽槽底,而在阳极上析出二氧化碳和一氧化碳气体(见熔盐电解)。铝液从电解槽中吸出,经过净化除去氢气、非金属和金属杂质并澄清后,铸成各种铝锭,其流程示意见图3。
2.1、铝电解过程的电化学反应
冰晶石-氧化铝熔液具有离子结构,其中阳离子有Na+和少量Al3+,阴离子有AlF咶、AlF嬄和Al-O-F络合离子以及少量O2-和F-(见熔盐)。在温度1000℃下,钠在析出电位大约比铝负250毫伏。由于阴极上离子的放电不存在很大的过电压,所以阴极反应是:
Al3+(络合的)+3e─→Al 而阳极反应是:
6O2-(络合的)+3C-12e─→3CO2 铝电解过程的总反应式是: 2Al2O3+3C─→4Al+3CO2 由于溶解在电解质熔体中的Al被CO2所氧化,引起电流效率降低,所以铝电解的总反应式实际上应为:
式中N 为阳极气体中的CO2/(CO+CO2)体积百分比。
在冰晶石-氧化铝溶液中,Al2O3的含量一般保持3~5%,为了改善电解质的性质,通常添加铝、镁、钙和锂的氟化物。
2.2、工业铝电解槽的发展
工业铝电解槽大致分为侧插阳极棒自焙槽、上插阳极棒自焙槽和预焙阳极槽三种。预焙阳极电解槽又分边部加料槽和中间加料槽两种。19世纪末开始用小型预焙阳极电解槽生产,电流在8000安以下,直流电耗高达42000千瓦·时/吨。1923年以后,这种槽型为侧插阳极棒自焙槽所代替,到20世纪30年代末,电流强度最高达 25000安,直流电耗为20000~25000千瓦·时/吨。侧插阳极棒电解槽的特点是技术装备简单,投资较小;但缺点是烟气处理比较困难,机械化程度较差,不易大型化等。
为了提高电解槽的机械化操作水平,改进烟气收集和净化的方法,50年代法国开始使用上插阳极棒自焙槽;到60年代直流电耗达 14500千瓦·时/吨左右,并大大提高了劳动生产率。80年代的上插阳极棒自焙槽又得到了改进,吨铝直流电耗降低到13800千瓦·时左右,并由于阳极工艺的改进,采用了“干阳极糊”(用高软化点沥青、低沥青配比的阳极糊)大大减少了沥青烟气的散发,改善了环境保护的条件。上插阳极棒电解槽的优点是:机械化水平较高。缺点是不易大型化,烟气处理也比较困难。
现代化的大型电解铝厂多数采用中间加料大型预焙槽(典型实例见图4),其优点为单槽产能高,打壳加料可以自动化,适于用计算机控制,电解槽密闭程度高,集气效率高(90~95%)。
中国50年代开始建立了铝电解工业,对侧插阳极棒自焙槽的建设和生产积累了丰富的经验,吨铝直流电耗达15000千瓦·时以下,80年代建成的160000安的中间加料大型预焙槽,直流电耗可达13800千瓦·时左右。
2、
3、铝电解废气净化 铝电解槽的阳极气体中含有有害成分,例如氟化氢、冰晶石粉尘等,严重地污染环境,所以阳极气体需要净化。净化方法有湿法和干法两种。
湿法净化是用5%的苏打溶液洗涤含氟气体,生成碳酸氢钠和氟化钠:Na2CO3+HF─→NaF+NaHCO3 苏打溶液在洗涤塔内循环使用,直到其中 NaF含量达到25~30克/升为止。然后,把NaF+NaHCO3溶液送至冰晶石合成槽与铝酸钠溶液作用,合成冰晶石:
6NaF+4NaHCO3+NaAlO2─→Na3AlF6+4Na2CO3+2H2O 冰晶石经干燥后,供电解用。
干法净化中用氧化铝作吸附剂。受吸附的HF与Al2O3发生化学反应,生成表面化合物AlF3:
Al2O3+6HF─→2AlF3+3H2O 所用的氧化铝通常是砂状氧化铝。载氟的氧化铝经布袋收尘器回收,再送往电解槽去电解。
2.4、炼铝能耗
炼铝能耗与所用原料和生产方法有关,碱石灰烧结法的能耗较高,拜耳法的能耗较低。从铝土矿开采到铝锭铸造,每吨铝一般消耗总电能约 15600千瓦·时;此外,还消耗热能14.8×106千卡,其分配见表4。可以看出降低能耗是铝工业的一项重要课题。
2.5、铝的精炼 随着铝纯度的提高,它的抗蚀性、可塑性、导电性、反光性等性能愈好。精铝或高纯铝(含Al>99.99%)供许多特殊部门使用。
精铝 以原铝为原料,用三层液电解法制取纯度为99.99%的铝。此法是美国人胡普斯 (W.Hoopes)发明,1922年开始工业化生产。槽内三层液体,各层密度不同:下层是 67%原铝加33%铜的合金(密度为3克/厘米3),用作阳极,其中铜是加重剂;中层是17%NaF、23%AlF
3、60%BaCl2的电解质(密度为 2.7克/厘米3),其中BaCl2是加重剂;上层是电解产物精铝(密度为2.3克/厘米3),用作阴极。电解温度为720~800℃。电解槽槽壁用绝缘材料(镁砖)砌筑。
精炼电解时,铝从阳极合金中转移到阴极上,而原铝中的杂质元素都留在阳极合金中,使铝得到精炼。此法中的阴极电流效率达到97~99%。
高纯铝 以精铝为原料,用区域熔炼法、有机溶液电解法或两法兼用制得;含Al99.999%以上。精铝区域熔炼在卧式管状电炉中进行。铝中杂质硅、铁、铜、镁等的分配系数都小于1,因而富集在液相内,经过12~15次重复熔炼后,可得Al>99.999%的高纯铝。
有机溶液电解法可得到99.9995%的高纯铝。
如以有机溶液电解与区域熔炼串联,可制得超纯度铝(见超纯金属)。预先经过有机溶液电解的铝,再经几次区域熔炼,可在最纯区段得到Al≥99.9995%的产品。
其他炼铝方法的研究 世界各国都在研究新的炼铝方法,主要目标为寻求一个大幅度降低能耗的途径,但大多还处于试验研究阶段。
氯化铝电解法 原理是把工业氧化铝氯化成三氯化铝,然后在多室电解槽内电解,得到纯铝和氯气,氯气返回利用。但三氯化铝制备中的腐蚀和成本较高等问题还未得到解决。
电热法 用低品位铝矿作原料,用焦炭作还原剂,在电弧炉内还原得含Al60%以上的铝硅粗合金,然后降低温度至580℃左右,通过离心分离除去析出的固相,制得含Al达80%左右的中间合金。用此法直接生产硅铝合金,有一定经济意义,但如何获得较好的质量和较好的技术经济指标,则仍然是一个技术课题。
废铝再生 铝及其合金制品的再生日益得到重视。再生铝又称二次铝,现在世界每年从废铝回收的铝量约400万吨,相当于原铝产量的25%左右。由于铝的熔点低,热焓值小,废铝再熔所需的能量仅为从矿石制取原铝的5%左右。此外,原料和投资费也较节省。废铝主要用来生产铝合金。在再熔之前,要先将废铝选拣分类,再加以适当调配和处理,以便达到所需的合金组成。铝的第一次炼制能耗较高,合理回收利用废铝,是节能的一个有力的措施(见再生有色金属)。
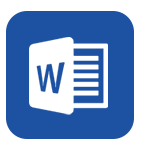