间歇釜式反应器和平推流反应器中,返混为零;全混流反应器中,返混 极大 ;多釜串联反应器,釜数越多,返混程度越小。实际反应器中,一般都有一定程度的返混。基本反应器:间歇釜式反应器、连续釜式反应器、连续管式反应器和多釜串联反应器 对整个反应器进行物料衡算:
流入量 = 流出量 + 反应量 + 累积量
某组分流入量=某组分流出量+某组分反应消耗量+某组分累积量
1.间歇釜式反应器
特点:1)一般为液相反应,密度变化不大,可视为等容过程;2)物料混合完全;3)间歇操作反应期间无进料和出料
装料系数,一般在0.4~0.85之间,不起泡不沸腾的物料可取0.7~0.85,易起泡或沸腾的物料可取0.4~0.6V1=V2/n
0.连续操作管式反应器
优点:具有容积小、比表面大、返混少、反应参数连续变化、易于控制的优点,
缺点:对于慢速反应,则有需要管子长,压降大的不足。
适用:液相反应和气相反应。由于PFR能承受较高的压力,用于加压反应尤为合适。
1.间歇反应器与平推流反应器需要的容积相同。
但因为间歇反应器中存在辅助时间与装料系数。所以它需要的总容积较平推流反应器较大。 对于反应时间很短,辅助时间相对较长的反应来说,选用管式反应器较为合适。
2.对简单反应,选择反应器型式有如下几条原则可供参考。
对零级反应,选用单个连续釜和管式反应器需要的容积相同,而间歇釜因有辅助时间和装料系数,需要的容积较大。
反应级数越高,转化率越高,单个连续釜需要的容积越大,可采用管式反应器。如反应热效应很大,为了控制温度方便,可采用间歇釜或多釜串联反应器。
液相反应,反应慢,要求转化率高时,采用间歇反应釜。
气相或液相反应,反应快,采用管式反应器。
液相反应,反应级数低,要求转化率不高;或自催化反应,可采用单个连续操作的搅拌釜。
3.反应器型式选择
设置较高的CA:采用管式反应器。因管式反应器内反应物的浓度较连续釜式反应器为高,其次则采用间歇釜式反应器或多釜串联反应器。
设置较低的CA:采用连续釜式反应器。但在完成相同生产任务时,所需釜式反应器体积较大。故需全面分析,再作选择。
与浓度无关:选用管式反应器,因同样选择性下其生产能力较大。
4.管式反应器特点:
(1)反应物浓度和化学反应速度随管长变化。
(2)管式反应器具有容积小、比表面大、单位容积的传热面积大,特别适用于热效应较大的反应。
(3)由于反应物在管式反应器中反应速度快、流速快,所以它的生产能力高。
(4)管式反应器适用于大型化和连续化的化工生产。
(5)和釜式反应器相比较,其返混较小,在流速较低的情况下,其管内流体流型接近与理想流体。
(6)管式反应器既适用于液相反应,又适用于气相反应。用于加压反应尤为合适。此外,管式反应器可实现分段温度控制。
缺点:反应速率很低时所需管道过长,工业上不易实现
分类:(1)水平管式反应器 (2)立管式反应器(3)盘管式反应器(4)U形管式反应器
换热方式:(1)套管或夹套传热 (2)套筒传热 (3)电流加热 (4)烟道气加热
双膜理论模型
(1)基本假定
气液两相沿接触界面均存在一个滞留膜,气相组分A传递阻力完全集中在气膜内,相界面本身无传递阻力;组分A由界面传递到液相主体的阻力完全位于液膜内,液膜以外的湍动足以消除浓度梯度。
(2)实质:定态理论
(3)缺点:双膜存在是理论先决条件,与事实不符。但包含两个基本特征-溶解和扩散
1.固定床反应器的特点
结构简单很少催化剂损耗很小气固返混较长的扩散时间及距离高床层压降 床内取热供热困难催化剂取出更新困难催化剂颗粒大,效率低
压力降产生原因
(1)摩擦阻力:由于流体与颗粒表面之间的摩擦产生。
(2)局部阻力:流体在孔道内的收缩、扩大及再分布所引起的。
低流速时,摩擦阻力为主;
高流速及薄床层中流动时,以局部阻力为主。
(1)属于流体的:气流速度、流体的粘度、密度等物理性质
(2)属于床层的:床层的高度、床层空隙率和颗粒特性如形状、粒度等
压力降过大对反应的影响: 影响生产能力;影响床层中的浓度和温度分布;增加动力消耗。 降低压降的方法:降低流速、增大空隙率、减小床层高度、增加催化剂颗粒直径等。
1单段绝热式
特点:结构简单,反应器生产能力大,但反应过程中温度变化较大。
适用:1.反应热效应不大,反应过程允许温度有较宽变动范围的反应过程;2.热效应较大的反应只要对反应温度不很敏感或是反应速率非常快的过程,有时也使用这种类型的反应器。 2多段绝热式
特点及适用:多段绝热式弥补了单段绝热式的不足;
冷激式反应器结构简单,便于装卸催化剂,内无冷管,避免由于少数冷管损坏而影响操作,特别适用于大型催化反应器。
1对外换热式
特点:小管径,传热面积大,有利于强放热反应;热效果好,易控制床层温度;管径较细,故反应速率快,选择性高;结构较复杂,设备费用高。
适用 : 原料成本高,副产物价值低以及分离不是十分容易的情况。
2自热式
特点:把原料的预热和产物的冷却过程融为一体,大大提高了能量利用水平。
应用:只适用于热效应不大的高压放热反应过程。如中小型合成氨厂的氨合成和甲醇的合成。
2.流化床反应器
优点:温度分布均匀;提高了催化剂的内表面利用率;能够实现反应过程和再生过程的连续化;所需的传热面积大为减小;设备生产强度大,适用于大规模生产。
缺点: 1)气体返混严重,转化率降低2)增加了催化剂的损耗和设备及管道等的磨损。 流化床适用于: A、热效应很大的放热或吸热反应; B、要求有均一的反应温度和需要精
确控制温度的反应; C、催化剂寿命较短,操作较短时间就需要更换(或活化)的反应。一般不适用于:A、要求高转化率的反应;B、要求催化剂床层有温度分布的反应。
流化床层中流体的流动
固定床阶段:u0≤umf时,固体粒子不动,床层压降随u0增大而增大;
流化床阶段:umf≤u0≤ut时,固体粒子悬浮湍动,床层分为浓相段和稀相段,u0增大而床层压降不变;
输送床阶段:u0>ut时,粒子被气流带走,床层上界面消失,u0增大而床层压降有所下降。
1.实际流化床与理想流化床差异的原因:固定床阶段,颗粒之间由于相互接触,部分颗粒可能有架桥、嵌接等情况,造成开始流化时需要大于理论值的推动力才能使床层松动,即形成较大的压力降。
(1)沟流消除:物料预先干燥;加大气速;合理设计分布板
(2)大气泡 消除:在床层内加设内部构件可以避免产生大气泡,促使平稳流化
(3)腾涌 消除:在床层过高时,可以增设挡板以破坏气泡的长大,避免腾涌发生
对萃取剂的基本要求:(1)选择性强(2)溶解度大(3)挥发性小(4)经济、安全要求 共沸精馏的概念:
第三组分(恒沸剂或挟带剂)与原溶液中一或两个组分形成恒沸物,使原有组分间的相对挥发度 增大,再用一般精馏方法分离。
最低恒沸物的体系:恒沸物为塔顶产品,塔底得纯组分;
最高恒沸物的体系:恒沸物为塔底产品,塔顶得纯组分。
恒沸精馏流程取决于共沸剂与原组分形成的恒沸液的性质。
1.形成共沸物的条件和特性:(1)在恒温下,两液相共存区的溶液蒸汽压大于纯组分的蒸汽压,但蒸汽组成介于两液相之间,这种系统就形成非均相共沸物。(2)在恒温下,两液相共存区的溶液蒸汽压大于纯组分的蒸汽压,但蒸汽组成并不介于两液相组成之间,这种系统不形成非均相共沸物而形成均相共沸物(3)在恒温下,两液相共存区的溶液蒸汽压介于纯组分的蒸汽压之间,而蒸汽组成并不介于两液相组成之间,这种系统不形成共沸物。
1.共沸剂的选择原则:1)共沸剂至少应与原溶液的组分之一形成共沸物且该共沸物的Tb与原溶液组分的Tb或原溶液共沸物的 Tb相差越大越好。一般希望>10K。2)新共沸物所含共沸剂的量要小,以减少共沸剂用量、节省能耗和降低设备投资。3)新共沸物最好为非均相共沸物,便于用分层方法分离,使共沸剂易于回收。4)有较好的物理、化学性能。 溶剂选择 (萃取)范围较广一定要形成共沸,选择余地小(共沸)
溶剂用量 (萃取)用量波动范围大,用量一般较大用量不易波动(共沸)
能量消耗 (萃取)以消耗显热为主,能耗小以消耗蒸发潜热为主,能耗大(共沸) 溶剂加入方式(萃取)在靠塔顶部加入加入方式灵活,视溶剂性质而定(共沸) 适用范围(萃取)规模大的连续生产连续或间歇操作(共沸)
精密精馏1.不稳态操作时间的增加因素:塔身和产品罐存料大;原料浓度低而产品浓度又要求高;相对挥发度小,理论板数多;塔内汽液流速低,等等;此外还与操作方式有关盐溶精馏-选择一种盐溶液作为添加剂,来达到改变本分离组分之间的相对挥发度,从而达到分离目的。
优点:(1)可以节省能耗;(2)盐一般为不挥发组分,故仅仅在塔釜中出现,可以使产品的纯度提高;(3)盐的分离也较容易。盐可以循环使用。
缺点:盐的溶解回收,固体物料的输送,加料,以及盐结晶引起堵塞、腐蚀等问题,限制了它在工业上的应用。
用途:a)制造无水酒精。b)稀硝酸用硝酸镁脱水制造浓度99.5%的浓硝酸
方法:1)将固体盐加入到回流液中,溶解后由塔顶加入,在塔顶可以得到纯的产品,塔底得盐的溶液,其中的盐回收再用。该法的缺点是回收盐十分困难,要消耗大量热能。2)将盐溶液和回流液混合,此方法应用方便,但盐溶液中含有塔底组分,使塔顶得不到高纯产品。
3)把盐加到再沸器中,盐仅起破坏共沸液的作用,然后再用普通蒸馏进行分离。这种方法只适合用于盐效应很大,或纯度要求不高的情况。
1.加盐为什么会改变α?
宏观 :盐在水中的溶解度较大,使溶液的蒸汽压严重下降,进而导致沸点升高;而盐在醇中的溶解度较小,导致醇溶液的蒸气压下降较小,从而导致相对挥发度增加。
微观 :盐是强电解质,水中会解离为离子,产生电场,水分子极性和介电常数大,易聚集在离子周围使水的活度系数下降,从而使相对挥发度增加。
2.反应精馏优点:1)可以增加反应的转化率及选择性。 2)增加了反应速度,提高了生产能力。
3)由于利用了反应热,节省能量。4)由于将反应器和精馏塔合成一个设备,节省设备投资。
5)对于某些难分离的物系,可以利用反应精馏来获得较纯的产品。例如用丁苯或叔丁苯的转移烷基化来分离间二甲苯对二甲苯的混合物
分子蒸馏过程(四步曲)
(1)物料分子从液相主体向蒸发表面扩散(注意:液相中的扩散速度是控制分子蒸馏速度的主要因素);
(2)物料分子在液层上自由蒸发速度随温度升高而增大,但是,分离因素却随温度升高而降低;
(3)分子从蒸发面向冷凝面飞射。在飞射过程中可能与残存的空气分子碰撞,也可能相互碰撞,但只要真空度合适,使蒸发分子的平均自由程大于或等于蒸发面与冷凝面之间的距离即可。
(4)轻分子在冷凝面上冷凝。如果冷凝面的形状合理且光滑并迅速转移,则可以认为冷凝是瞬间完成的
分子蒸馏技术的特点:操作温度低;蒸气压强低;受热时间短;不可逆性;没有沸腾鼓泡现象;分离程度及产品收率高;无毒、无害、无污染、无残留
分子蒸馏器的模式
(1)降膜式—结构简单。液膜靠重力自然分布下降,较厚,效率低,目前已很少使用;
(2)刮膜式—依靠刮板成膜,较薄,分离效率高,但结构较降膜式复杂。现在国内、外的工业化装置以转子刮膜式为主。
(3)离心式—依靠离心力成膜,很薄,蒸发效率最高,但结构也最复杂,造价高 分子蒸馏设备设计原则
1)正确的选择真空泵组、管道尺寸及密封结构,以保证足够快地达到所需之工作真空度。
2)正确选择蒸发面与冷凝面的形状、距离及相对位置
3)分子蒸馏多用于分离热敏性物质,故要求被加工物料在蒸馏温度下停留较短的时间。
4)力求减少液层厚度及强化液层的流动
5)被蒸馏液体必须预先除气。
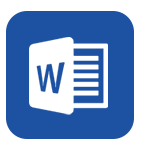