第一章 绪论
1.1 目的及意义
随着工业自动化水平的不断提高,大型火电厂发电机组主机设备均被配备了先进可靠、协调统
一、高度自动化的极其完善的控制系统。其良好的人机界面,优越的控制性能,准确的故障诊断与显示,大大提高了机组的运行效率,降低了劳动强度,简化了操作,也提高了故障处理速度。与先进的主机控制系统相比,输煤控制系统则显得较为落后,其自动化水平和工作效率与经济发展的要求不相适应。特别是上个世纪年代及其以前建设的火力发电厂,其输煤控制系统多为强电集中就地控制方式,采用继电器和按钮组成逻辑电路。这种控制方式与程控系统相比:功能差、系统可靠性差,自动化程度低,需要运行人员数量多且劳动强度大。
随着电力体制改革的不断深化,发电市场的竞争将日趋激烈,提高管理水平和工作效率,特别是提高设备的管理水平,提高设备的自动化程度及可靠性程度,从而达到减员增效的目的。火电厂的输煤系统是火电厂的一个重要组成单元,特点是运行情况恶劣,条件复杂,转动机械多,作业线长,设备分散,尤其对运行人员来讲,现场冗员过多且工作强度大,并且粉尘,噪音等影响运行人眼的身心健康。因此,火电厂输煤程控技术是提高输煤系统自动化程度及可靠性程度的必然选择,也是火电厂提高市场竞争能力的必然要求。
1.2 国内外研究现状
1.2.1 PLC在输煤系统中的应用简介
可编程控制器(Programmable Logic Controller简称PLC)是80年代发展起来的新一代控制装置,是自动控制、计算机和通信技术相结合的产物,是一种专门用于工业生产过程控制的现场设备,由于控制对象的复杂性,使用环境的特殊性和运行长期连续性,使PLC在设计上有自己的明显特点:可靠性高,适应性广,具有通信功能,变成方便,结构模块化。在现代集散控制系统中,PLC已经成为一种基本控制单元,在工业控制领域中应用前景极其广泛。
随着电力工业的迅速发展,火力发电厂单机容量和装机容量日益增大,输煤系统的规模也愈来愈大,传统的强电集中控制手段已经很难适应。从八十年代引进工程开始,输煤系统逐步采用以PLC为主机的程控技术,实现子自动化控制。PLC在技术上不仅具有控制功能强、能够适应恶劣的工作环境、维护方便、可在线修改等特点。不但能完成复杂的继电器逻辑控制,而且能完成模拟量控制及智能控制,并能实现远程通讯、联网、上位机监控等功能,完全可以适应输煤系统多种功能控制的要求,并为全厂实现计算机控制创造了条件。
1.2.2 与本课题相关的国内外研究情况
随着可编程控制器应用范围的不断扩大,从20世纪80年代开始,国内火力发电厂开始使用可编程控制器对其输煤系统进行自动控制。当时,多数电厂使用检测元件、执行器和电动机作为第一级,可编程控制器作为控制装置组成二级控制系统对输煤系统进行控制。该系统在功能上主要以处理开关量为主。80年代后期,许多大型火力发电厂对输煤控制系统进行了技术改造,使用了高性能可编程控制器、高速数据通信网络和过程控制计算机,组成三级分布式控制系统完成输煤系统的控制。控制系统在功能上增加了对模拟量的处理,规模上从整体式发展到模块式,且形成了网络。90年代,输煤控制系统除了采用性能高、网络功能强的可编程控制器外,还采用了速度更快、容量更大的计算机,在过程控制计算机上面使用生产控制计算机,组成了司机控制系统。生产控制计算机主要承担生产管理功能和适应优化数模的功能。进入21世纪,输煤程控系统多采用PLC集散控制方式,所有操作均在上位机上进行,可实现按流程的连锁起停,也可实现解除连锁的手动控制。
近年来,随着可编程控制器及及其网络的迅猛发展,PLC不但在现场控制及使用,而且深入到生产监控级及生产管理级中,操作站或终端设备中配置Factory Link-ⅳ,Control View等高级组态工具软件,可以提供多种功能及各式各样生动的画面。伴随着这种发展,输煤程控技术也将朝着管理一体化及高度自动化,高度智能化,信息化发展。输煤程控不再仅仅是控制输煤系统的生产运行,而将更多的开发出设备故障检测及诊断功能,更多的设备信息管理功能等,并将与厂级MIS系统联网,实现更加远程的监控管理。
与国内输煤控制系统相比,国外在散料输送自动化方面应用了许多新技术。在系统结构方面,除应用四级计算机控制系统外,还应用泄漏电缆(一种类似于同轴电缆,但屏蔽层开孔作为发射和接收天线)代替普通无线控制,从而获得抗干扰强、信号稳定的无线控制信号,对大型移动机械进行控制。在单元控制方面,主要采用节能控制技术。在人工智能的应用方面,一是对原料堆积和混料进行智能控制,另一方面对运输机械进行智能控制。皮带运输机动作顺序是根据机械装置和作业条件、皮带运输机相互关系、输送量等因素,并有一定的规则来支配的。新的系统把这些因素和规则形成规则库,运用智能控制使系统更有柔性。
1.3主要研究内容
本课题主要研究的内容有:
1.研究分析输煤程控系统的关键设备之一——可编程控制器的结构、特点、技术性能指标及其联网与通信技术。
2.以某火力发电厂为例,详细介绍输煤程控系统的组成及设备情况,分析输煤程控系统的监控方式及特点,系统应达到的控制要求,并简单介绍一下工业电视监控系统的组成及功能。
3.
完成设计输煤程控系统的关键部分:输煤、配煤的功能设计,实现输煤程控系统的控制功能要求,给出几个典型的输煤控制逻辑图。
第二章 MONDICON可编程控制器
2.1 概述
工业生产的各个领域都包含着大量的开关量(又称数字量)和模拟量。在可编程控制器问世以前,数字量和模拟量的控制主要用继电器、接触器或分立元件的电子线路来实现,它取代了原来的手动控制方式,并迅速成为工业控制的主流。这是自动控制的开始,也是以后诸多形式控制设备的基础。
随着生产力的发展和科学技术的进步,工业生产领域对控制系统提出了更高的要求,可编程控制器正是顺应这一要求出现的,它是以微处理器为基础的新兴工业控制装置。可编程控制器技术与CAD/CAM技术、工业机器人技术共同构成了现代工业自动化的三大支柱产业。
在自动控制领域中,目前国内外有许多生产PLC的厂家,而每个生产厂家都有自己的系列化产品,指令兼容,外设容易扩展;但不同厂家生产的PLC,梯形图、指令及各种配件均有一些差异,不利于PLC的普及。本文将以莫迪康公司的Quantum系列可编程控制器为例介绍有关PLC的一些基本概念。
2.2 Quantum系统硬件模块和编程软件
Quantum可编程控制器是具有数字量处理能力的专用计算机系统,它具有模块化、可扩展的体系结构,可用于工业和制造过程的实时控制,具有可靠性高、安装方便、易于使用和性能价格比高等特点,是MONDICON继984系列之后推出的新型PLC系列产品。系统包括CPU模块、I/O模块、通信模块、智能模块、电源模块和底板。 2.2.1 CPU模块
CPU是一种数字化的电子操作系统,它使用用户保存在PLC中的指令进行操作。这些指令用于实现一些专用功能,诸如逻辑、过程顺序控制、时序、耦合、算术运算等,以通过数字量和模拟量输出对不同类型的设备装置和过程进行控制。Quantum CPU 是位于Quantum本地I/O底板上的一个CPU模板。CPU内含有执行存储器、应用程序存储器、通讯端口状态LED指示灯。LED状态指示灯显示CPU本身及所有通讯端口的工作是否正常,以便及时进行故障检修。
Quantum CPU 使用闪存存储器(Flash Memory)技术,支持控制器的执行存储器和指令集。操作系统的升级可通过Modbus 和Modbus Plus通讯端口直接下装给CPU的闪存存储器,代替、更换EPROM芯片或执行卡执行现场修改。
Quantum CPU 还作为通信总线的主控,控制Quantum系统的本地、远程和分布式I/O。
2.2.2 I/O模块
数字量I/O模块的主要作用是实现PLC与外部设备之间数字信号的连接。它完成电平转换、电气隔离、串/并型数据转换、码字错误检测以及提供具有足够驱动能力的各种数字驱动信号等工作,有时还可提供各种中断和通讯等方面的控制信号。数字量I/O模块通常配置有相应的LED状态显示器,以利于操作人员的监测。
模拟量I/O模块主要实现PLC与外部I/O装置之间模拟信号的连接。其中模拟量输入模块主要完成阻抗匹配、I/V转换、小信号放大、信号滤波以及A/D转换等功能,实现将被控对象送出的模拟量转换成PLC易于处理的数字量的作用。模拟量输出模块主要完成阻抗匹配、功率放大和波形校正等功能,以便向被控对象提供正常工作所需要的模拟控制(驱动)信号。
在一些高精度和抗干扰的PLC系统中,模拟量I/O也需要由光电隔离措施。由于模拟信号的隔离问题远比数字信号隔离困难,因此常在模拟量I/O模块上肢配置若干具有隔离措施的端口,以降低系统的复杂度和成本。需要指出的是:在模拟量I/O模块中,模拟信号一般不能用光电耦合器作隔离,因为他不能保证良好的线性度,因此往往采用成本较高的隔离放大器来实现隔离作用。模拟量I/O模块中的数字逻辑部分可以采用光电隔离器来隔离。
Quantum系列PLC使用全范围、高性能的I/O模块,符合国际上认可的IEC电气标准,确保恶劣工作环境下的可靠性。Quantum的I/O模块允许带电插拔,这种特性为现场运行维护带来了许多方便。
所有的Quantum PLC I/O模块均可使用编程软件实现软件配置。I/O的软件配置允许用户为每个模块配置I/O地址。软件寻址使现有系统在加入模块或改变I/O配置时,无需从物理上改变应用程序。软件配置的另一个优点是删除空槽,这是由物理地址系统来建立地址映像的限制而造成的。I/O Map 的概念是基于智能模块的扩充,该智能模块需要地址范围以外的额外信息。
2.2.3 电源模块
PLC中的电源系统一般由三类:第一类是供PLC中TTL芯片和集成运放使用的基本电源(+5V和+15V直流电源);第二类是供输出接口使用的高压大电流的功率电源;第三类是锂电池及其充电电源。考虑到系统的可靠性和光电隔离器的使用,不同种类电源具有不同的接线。
Quantum电源模块为Quantum底板提供标准电压和保护系统免受噪声和电源波动的干扰,从而保证系统工作于典型的工厂电气环境。一旦发生意外的电器问题时,它保证系统有足够的时间完成安全、有序的停机。电源模块有24VDC、48/60VDCh和115/230VAC三种,以满足不同的电压需要。电源与使用地点无关,本地与远程等系统结构可使用同一电源。Quantum系列PLC中,有三种类型的电源可供选用:低功率独立型、大功率可累加型和高功率冗余型。
2.2.4 ASCⅡ模块 Quantum的140ESI06210 ASCⅡ模块是一种通用的ASCⅡ接口,提供与第三方设备通信和交换数据的能力。这些设备是典型的基于工业应用的设备,它们不提供标准通信。该模块多数应用在与打印机、条形码阅读器和扫描仪通信。同样,也有一些设备如称重设备、仪表和其他测量设备使用这种通信方法为简单的点对点ASCⅡ通信方式。该ASCⅡ信息包含在ESI模块中,由Quantum控制器逻辑程序触发。信息离线开发并下装到ESI模块中,利用这些信息,该模块可自主地和ASCⅡ兼容装置进行通信。
ESI模块的开发环境包括一台连接到Quantum PLC模块上的计算机,该计算机运行Modsoft或Concept软件,带可选的ESI可装载功能块。
2.2.5 底板
Quantum系列PLC使用公用底板,底板上有
2、
3、
4、
6、10和16槽位六种型号可供选择。16槽底板的型号为140XBP01600模块插在底板上,每一个槽位上插一个模块。底板提供控制信号及模块的电源。这个来自系统供电的电源仅仅为模块供电,而不能用于现场供电。底板中每一个槽位的电气特性都是一样的,即任何模块可插入任意一个槽位中,不存在对槽位的依赖关系,也不存在某些模块必须安装在某一特定底板的问题。对底板的限制仅是模块电源容量及寻址空间。所有寻址全通过软件进行,无需经DIP开关来进行模块配置。此外,底板可用于本地I/O、远程I/O和分布式三种系统结构,无须为某种结构选择专门的底板。底板只要选择包含有足够可用的槽位,能安装下需要的模块并留有将来扩展余地即可。
2.2.6 Concept编程软件
Concept是用于Modicon TSX Quantum 可编程控制器的编程组态工具,适用于Windows操作系统。它包括IEC编程语言功能块图(FBD)、梯形图(LD)、顺序功能流程图(SFC)、指令表(IL)和结构化文本(ST),以及面向Modsoft的梯形图(LL984)。
Concept的控制程序按区段设计,在每一个区段中,只能使用FBD、LD、SFC、IL、ST和LL984中的一种。将所有的区段联合成一个整体就组成了Concept的控制程序。在程序内,IEC区段(FBD、LD、SFC、IL、ST)可以任意次序安排,而LL984区段总是在IEC前编辑为一个段。
Concept具有离线编程和在线编程两种方式,此外,还提供一个模拟其用于模拟可编程控制器的功能。该功能可以在没有硬件的情况下,”联机”调试、验证用户程序。
在处理各种不同的编程语言时,可使用Concept提供的FBD、LD、SFC、IL、ST和LL984编辑器。除上述于编程语言有关的编辑器外,还有数据类型编辑器、变量编辑器和参考数据编辑器宫编辑时使用。
采用Concept进行可编程控制器编程是以项目(project)、可编程控制器配置(configuration)、程序(program)和区段(segment)分级来完成的。
Concept的设计项目包括下面的主要步骤。 1.启动Concept。
2.
使用配置器配置硬件。 3.
编程。
4.
项目的保存、下载和测试。 5.
优化和断开。
6.生成一套完整的Concept文件。
2.3 Quantum PLC系统结构
Quantum 系列PLC提供了一个高度灵活的系统结构,从中央集中控制系统到高级分布系统及联网的分布控制系统,灵活组合的系统结构可使控制系统达到很高的性能价格比,最大程度的满足控制要求。
2.3.1 本地I/O Quantum系列支持本地I/O结构。在这种系统结构中,本地I/O模块能够与CPU模块与电源模块安装在一个底板上,最少有1个(3槽位底板,含1块CPU模块和1块电源模块),最多有14个(16槽位底板,含CPU模块。电源模块),本地站最多可提供488个I/O点。
2.3.2 分布式I/O
Quantum PLC提供分布式I/O结构。这种I/O结构基于Modbus Plus网络技术,适用于I/O信号分布在较大的区域的应用场合。分布式I/O结构是用于本地I/O一样的I/O模块,使用双绞线连接不同的分站。分布式结构对一台CPU支持三个网络,每个网络距离为2000m,对系统结构提供可选的网络策略。如果要求更远的距离,可使用光纤中继器。
2.3.3 远程I/O
当系统需要大量的I/O分站,且需要具有极高的I/O性能,或需要与现在的Modicon远程I/O分站连接时,可使用Quantum PLC的远程I/O结构。Quantum的RIO网络为高速(1.544Mbit)局域网(LAN),它采用同轴电缆和CATV介质技术。RIO网络中,大部分数据在RIO处理器和RIO适配器之间进行传送,对I/O的一个分站小于1ms.Quantum的RIO网络采用S908的远程I/O通信协议,因此,Quantum系列PLC可通过远程I/O处理器,把Modicon984系列原有的800、200系列I/O作为自己的一个远程站处理。
远程I/O使用同轴电缆,网络距离可达4500m,最多可达31个远程I/O站,每个分站支持128个I/O字(64字输入/64字输出)。远程I/O电缆拓扑结构包括一条线性主干线、主干线分支器、接至远程I/O接口的分站电缆。
2.3.4 Modbus和Modbus Plus网络
Quantum系列的控制器与控制器、控制器与人机接口产品、控制器与计算机之间的通讯,延续了Modicon 传统的 Modbus(MB)和Modbus Plus(MB+)的两种网络方式。
Modbus是一种工业标准主/从协议,使用RS-232通信口。Modbus可用在只有装置的点对点控制方式,或只用在具有247台从设备的网络结构中。
在大于15m的长距离应用中,使用调制解调器,通过RS-48
5、电话线、红外线、光纤、微波等多种介质可实现Modbus连接。通过调制解调器将网络连接到公共载波线上,可使MB网络拓扑到4500m的距离。
Modbus Plus 网络是一种高速对等的局域网,这一局域网络允许主计算机、控制器和其他数据源,通过低价的双绞线(最远通讯距离可达500m)或光缆,在整个工厂进行对等通信。Modbus Plus作为一个确定性的令牌传递网络以1M波特率通信,快速访问过程数据。典型应用包括:控制联网与互锁、数据采集、程序上装与下装、远程在线编程等。
所有的Quantum CPU 上均有Modbus和Modbus Plus通信口,因此,在Quantum CPU和140NOM21x00 Modbus Plus网络模块上,可自动实现Modbus和Modbus Plus的桥梁。此桥接方式把Modbus的信息直接送到Modbus Plus网络,以便于实现Modbus 和Modbus Plus设备的连接。
7网桥可以使单个的Modbus Plus网络来连接在一起,从而使总的可寻节点数量超过1.6×10个。双绞线中继器可以使通信距离长达2000m,而光纤模块(140NOM25200)和中继器的使用可使两节点间的通信距离达到3000m,总长达到12km.对于不允许停机的应用,双缆Modbus Plus能够在各种网络元件及其选件上采用。双缆允许Modbus Plus通过两条独立电缆进行通信。 2.3.5 Ethernet以太网
Ethernet网络标准是目前世界上使用最为普遍的网络。Ethernet网络属于“基频”(Baseband),即在一条传输线路上、一个时间内只能传送一个数据,其媒介取得方法为CSMA/CD。
Quantum PLC的Ethernet网络模块有两种型号:140NOE21100和140NOE25000,前者为10BaseT双绞线带RJ45连接器,后者为10BaseFL光纤带ST连接器。这些模块预装有TCP/IP堆栈和Modbus协议,并通过闪速存储器支持用户升级。NOE模块只用于本地CPU地板,186控制器支持两个NOE模块,486控制器支持6个NOE模块。由于NOE模块有自己的处理器,所以对控制器扫描的影响很小。NOE和CPU之间的数据交换在控制器扫描结束时进行。
NOE模块由Concept 2.0和Modsoft 2.4 软件支持,这两个软件允许用户通过TCP/IP Ethernet为Quantum控制器进行程序编制和归档。
NOE模块支持EthernetⅡ和IEEE802.3格式,其IP地址从模块MAC地址中自动生成或者由TCP/IP网络管理人员指定。
使用双绞线或光缆,NOE模块可以和集线器(HUB)连接。集线器可以独立使用或通过10Base
2、10Base5或10BaseT网络竹竿来实现相互之间的连接。网络可以使用中及其延伸其距离,也可使用网桥将不同网络连接起来延伸其距离。使用路由器可以将Quatum PLC连接至广域网中。
使用Quantum PLC的Ethernet在几个控制器之间或在主机之间进行对等信息传递时,可以使用MSTR通信指令。编程一个MSTR梯形逻辑指令,可以读出和写入控制器的信息。控制器每次扫描时,有4个MSTR指令服务于每个NOE模块。
2.3.6 热备系统
当应用系统对安全性有较高要求时,可选择Quantum PLC的热备系统结构。热备系统的核心是备用控制器,在主控制器发生故障时,保证现有状态的自动化切换。这样可以使要求严格的过程不受控制硬件故障的影响,其结果是系统安全性的提高和停机时间的减少。
在热备系统中,每个主控制器开始扫描时,当前寄存器和I/O和状态表通过高速、安全的光纤通信链路传送至备用系统。当主控制器发生故障时,热备处理器能在48m内能代替主控制器,对具有最新I/O和寄存器状态信息的系统进行控制,使没有波动、进行控制的传送具有最小的过程影响。快速、平稳的切换可以使要求严格的过程不受任何控制的影响。
为了增加系统可靠性,热备系统与双电缆Quantum 远程I/O系统兼容。双电缆远程I/O布线在一个I/O链路受到损坏和断裂时,其他的链路仍能继续工作并控制过程,以保证较高的系统完整性。
第三章
输煤程控系统及控制要求
3.1 输煤程控系统概述
3.1.1 输煤控制系统内容
火电厂输煤系统是完成煤炭接收、运输、存储任务的设备和设施的组合,它包括从运煤车辆或船舶进厂卸煤起,把煤运入锅炉房原煤仓的整个工艺过程。煤炭运至发电厂后的计量、卸载、储存、输送、筛分、破碎等厂内处理过程都是在这一系统中完成的。 1.卸煤控制。完成来煤的地卸载任务。主要机械是翻车机。
2.输煤控制。主要解决皮带机启、停及保护连锁,出力指示,紧急跳闸等。 3.斗轮堆取料机控制。用于堆煤和取煤。
4.配煤控制。有重量传感器、超声波料位仪或其他物位探测装置测定主厂房原煤仓的煤位,从而决定各煤仓的煤量分配。常用的配煤设备有犁式卸煤器、卸煤车等。 5.转运站控制。用于运行方式及路径的切换,主要控制分流设备如挡板、分煤门、闸板门等,也包括辅助设备如磁铁分离器、金属探测器、木块分离器及给煤机等控制。
6.碎煤机控制。用于碎煤机起、停控制及过负荷保护、振动、超温保护联锁。
7.计量设备。带有瞬时值、累积值指示、打印、记录的电子皮带秤,可显示并记录进煤量、耗煤量等。
8.辅助系统控制。包括取样装置、除尘和集尘装置、暖通空调、冲洗排污、消防火警等装置的控制。
9.信号报警系统。设备和人员的安全保护动作,设备异常,煤仓间煤位高、低、超高、超低、动力电源故障,输煤设备及辅助、火警、除尘、集尘、取样、暖通系统的故障等均有事故报告。 10.控制屏。一个实现上述各控制要求及信号指示的控制屏,屏上有全系统的模拟流程指示。
3.1.2 输煤程控系统要求
1.所有设备可以分自动和手动两种运行方式,系统自动运行时,不影响其它设备手动操作。
2.自动运行分输煤自动和配煤自动。
3.在紧急情况下,可以立即停止各个设备的运行。 4.在自动运行方式下,系统启动过程可以启动。 5.皮带及其他设备必须连锁运行。
6.自动运行时,电动三通自动对准位置,并检查位置是否准确。
7. 系统启动时,必须提前沿线预告,然或按逆流方向逐段延时启动,前一段启动的条件是后一段皮带的合闸反馈信号和速度开关信号。
8. 系统正常停止时,按顺煤流方向逐段延时停止。
9. 皮带的以及跑偏、皮带打滑信号、原煤仓告料位信号、电机过载信号等作为一般报警信号,不应引起系统紧急停止;皮带的二级跑偏、落煤管堵煤信号、皮带撕裂信号应使系统紧急停止。一般报警信号、紧急报警信号和设备连锁都可以由操作人员解除,以便局部故障、检修或试验时系统可继续运行。
10.自动配煤时,需先选择尾仓、优先仓、旁路仓以及自动配煤方式,即顺序配煤和低仓优先配煤。顺序配煤时,按照#1仓、#2仓…..尾仓的顺序加煤,遇到旁路仓时自动跳过。低仓优先配煤时,先给出现低低料位信号的煤藏加煤,然或给出现低料位信号的煤仓加煤,消除低料位信号后,再按#1仓、#2仓…..尾仓的顺序加煤,遇到旁路仓时自动跳过。 11.通过入场煤皮带秤和入炉煤皮带秤提供的信号,累计计算各段时间内的入厂煤量、入炉煤量、入仓煤量。
3.1.3 输煤控制系统的控制方式
输配煤系统的运行一般具有程序自动控制(简称程控)、集中手动控制(简称集控)和就地现场控制三种控制方式。
就地手动控制方式是在运煤机械设备的附近安装控制箱,箱上配有控制方式选择开关和操作按钮,设备的就地操作和停止可通过按钮来实现。这种控制方式常用于设备检修后的调整,设备程序控制启动前的复位,也可用在集中控制、程序自动控制方式发生故障时的备用操作。不便操作的设备和不需要参加程序启动的设备也使用就地手动控制。
集中手动控制是设备的起、停控制集中在一个控制屏上,联锁保护通常由继电器逻辑阵列实现的一种控制方式。控制屏上有设备运行工况的模拟指示、信号报警等,可以实现简单运行控制方式及设备连锁的一般要求。
程序自动控制是将输煤系统有关设备按生产工艺流程的要求,事先编制好各种运行方式的控制程序。操作人员通过计算机键盘或鼠标,选择要执行的运行方式,在CRT显示器的模拟图上,可以显示出所选运行方式中各个设备的状态。如果运行条件具备,操作人与那可以通过计算机键盘或鼠标发出控制指令,设备按程序自动启动、运行和停止,同时将各种信息传送给计算机。程序控制是输煤系统正常运行的主要控制方式。
3.2 输煤系统控制功能
根据生产工艺的要求,输煤程控系统应实现以下控制功能。
1. 启动预报
程序启动前,应根据现场设备的情况和工艺要求,注意选择给煤、输煤、配煤设备和除尘设备,同时选择各交叉点挡板的位置,以确定整个系统的程序运行设备。在某一程序的运行方式被选定后,控制系统的CRT上出现与预选设备闪光信号。运行设备确定无误后,即可进行程序启动预报,所选运行线路的皮带沿线即发出预报警告,时间一般为30秒。 2.
程序启动和停止
启动预报成功后即可进行程序启动,启动方向为逆煤流方向。从最后一条皮带开始,设备延时30秒依次启动。
在运行过程中如出现设备故障,则故障点前级(逆煤流方向)设备停机,故障点后即设备延时停止。当配煤系统给锅炉的最后一个原煤仓配满煤时,煤位检测装置发出高煤位信号,此时程序自动发出停止指令,运行设备经过一定时间的延时后,按顺煤流方向逐个自动地停止设备。 3. 程序自动配煤
配煤控制有顺序配煤和程序配煤两种方式。
顺序配煤是从1号仓开始逐个进行配煤,配到高煤位开始出现后转入下一个仓配煤,程序配煤是根据现场料位计发出的煤位信号自动控制犁煤器抬落进行配煤,即低煤位优先配、顺序高煤位配。在顺序配煤过程中,如果出现低煤位信号,不管原来在哪里配都将立即中止而转入对低煤位信号的仓配煤,即出现低煤位信号的仓要优先配。若是有两个以上的仓同时出现低煤位的信号,则按顺煤流方向依次配煤至低煤位信号消失后延时一段时间。当全部低煤位消失时,各仓的配煤将按顺煤流方向依次进行,当配至仓尾出现高煤位时,系统提示“配煤一周完毕”。对于高煤位已消失的仓,可根据操作人员发出的重配指令,继续循环配煤。如果需要停止配煤,操作人员按下程停按钮,选择相应的配煤流程,系统自动按顺煤流方向延时停止皮带机,皮带上的余煤将平均分配到各仓内。
程配时还可设置检修仓,可使配煤程序跳过检修仓配煤,直至尾仓。还可通过对尾仓或配煤仓的设置,实现对任意一段仓的配煤或对任意某几个仓的配煤。 4.分炉计量功能。
在配煤加仓的过程中,上位机接收来自电子皮带秤的煤重脉冲信号,再结合现场其他设备例如皮带机、犁煤器等的状态信号,应用计算机技术对实际加煤量进行分仓计量,同时将超声波料位计的料位信号转化为煤重数值,对实际燃煤量进行分炉计量,使计算精度达到技术规范要求。 5.故障监测及保护连锁功能
输煤系统的各设备均可实现与时间和条件有关的连锁,令系统在满足生产工艺要求的前提下稳定可靠运行,故障监测程序具有对故障信号自动处理及数字滤波的功能,以消除干扰信号对系统的影响。
系统还可对皮带输送机等大型设备进行过流保护监测,对拉线开关状态、皮带打滑、皮带跑片、皮带撕裂、落煤筒堵塞等故障信号进行监测,并进行停机或切换处理,以保护人身安全及设备免受其害。
开关量信号、模拟量信号及远程通讯端口具有继电器或光电隔离保护装置或措施,以确保信号传输的安全性。
3.3 输煤控制系统硬件配置
3.3.1 概述
火电厂输煤程控系统是对整个输煤系统进行自动控制和管理及各项数据采集的一种自动化装置,用于实现输煤系统设备的程控操作和实时监控。
整个系统的监视对象包括皮带输送机、给煤机、碎煤机、除尘器、犁煤机等,同时其相关的皮带跑偏、打滑、纵向撕裂、堵煤以及煤位、煤流等保护和诸多的检测信号也要求进入系统,从而实现输煤系统的自动控制和监视。
输煤程控系统由上位机监控管理系统、PLC系统及传感器检测保护装置组成。主设备布置在输煤控制室,主要有PLC主机柜、上位机、操作台、电源柜等。该系统由2台工业控制计算机互为热备,可编程控制器的处理器CPU亦为双机热备,通讯为双网冗余,设置多个远程I/O子站,输入/输出采用继电器隔离。皮带运行状态及现场设备通过传感器监测,经可编程控制器及工业控制计算机显示在CRT上,供运行人员监视与操作现场输、配煤设备。工业电视可独立自成系统,也在计算机管理系统控制下工作,并设有电视自动跟踪系统进行报警和故障停车。
下面以某电厂的输煤控制系统为例介绍输煤控制系统的基本组成。 流程图见附录图1。
3.3.2 上位机监控系统
主要由2台上位监控机和打印机等外围设备组成,操作系统选用网络功能强大、可靠性高的Windows系列,监控软件采用GE公司的CIMPLICITY4.01开放式监控软件包,可以实现各状态信息的显示及各设备远程控制、故障报警、报表打印、趋势图显示等功能。
在上位控制方式下设备远程控制又可切换为手动和自动两种方式,在手动方式下,由上位监控站操作人员根据工艺流程顺序从上位机一次启动各设备;自动方式下,根据料位情况,由PLC内部程序实现各设备的自动启停。
3.3.3主机控制系统
本地站设有6槽机架,每个机架的配置如下:
中央机架底板 140XPB00600 控制器 140CPU43412 主机电源模板 140CPS12400 本地分支模板 140CRP93200 热备模板 140CHS21000 3.3.3.1.电源模件140CPS12400
程控系统电源的供电采用双路交流220V输入,双路电源均送入交流切换控制器,平时一路工 作,一路备用,可以通过手动或自动切换。交流电源可根据程控设备分成若干分路,每个分路均有指示灯及自动空气开关保护。配有两台DC24V稳压电源、两台DC110V稳压电源和一台直流24V电源切换控制器及一台直流110V电源切换控制器。平时一套工作,另一套作为备用,可手动或自动切换。直流24V电源主要供PLC模块的输入输出继电器使用,直流110V电源主要供现场信号输入使用,以提高抗交流干扰性。每个分路均有指示灯,并配有熔断器保护,另外还具有过载、过压保护。相关的电源短路和接地信号可接入PLC,用于程控系统对电源进行监视和故障报警。上位机还配有不间断电源(UPS),断电时确保上位机能继续工作一定时间作应急处理。 3.3.3.2 PLC140CPU43412 该控制系统采用美国Mondicon的Quantum系列作为主机,构成输煤系统的PLC控制系统。该产品的CPU采用Intel处理器,具有更快的处理速度和更大的内存空间,模块可带电插拔,从而可简化维护,增加系统的可靠性,而且,其坚固的结构,保证即使在最恶劣的现场环境下也能可靠的工作。控制主机控制输煤系统的设备起停及现场信息采集与处理,并通过100M EtherNet网同服务器、上位监控系统相连,进行数据交换。PLC的CPU与I/O模件之间采用远程I/O通讯方式,通讯介质为同轴电缆,具有很强的抗强电磁干扰能力,通讯速率可达1.544M波特率,不加中继器的最远传输距离为15000ft(4573m).此外,为提高程控系统的可靠性,PLC系统采用双机热备设置。在两个完全相同的主机架上各插有一块热备通讯模块,两块热备模块通过两芯光缆彼此相连,每个扫描周期,主CPU都要根据自身的I/O状态表,是备用CPU始终与主CPU保持同步,从而当主CPU模块或系统发生故障时,通过热备通讯模块及热备通讯组件,可以完全同步的、无扰动的进行CPU模块的切换,此时辅助(热备)CPU模块不间断地继续工作。
现场的运行方式、启动顺序、应答信号和故障信息等应用软件放在PLC中。它具有编程简单灵活、面向现场的特点,当现场设备增加或减少时,通过PLC可以非常方便的修改系统的工作方式,并可以随时调出系统的应用程序进行编写与修改。PLC设置一个本地I/O站(双机热备)与若干个远程I/O子站,本地I/O站主要管理控制室附近皮带及附属设备和传感器,远程I/O子站主要控制远方的输煤设备、犁煤器、原煤仓、给煤机及附属设备和传感器等。远程I/O分站与本地I/OPLC主机之间采用双缆通讯网络结构。 3.3.3.3 远程通讯处理器140CRP93200
I/O站是PLC系统的一部分,它需要一个140CRP93200通讯适配器和主机的远程通讯处理器通讯。本系统采用的远程通讯器是140CRP93200,远程通讯能力由MODBUS ⅱ通讯协议支持,每一个I/O分站和主机的最大通讯距离可达4.57km,通讯速率为1.544M波特。140CRP93200可以支持单根或双根(冗余)通讯电缆.采用冗余电缆可有两根电缆同时传送数据,使用中只采用一根电缆的数据,另一根的数据用作通讯数据的检验,以保证精度。140CRP93200面板上有指示灯,现时各路通讯是否正常。
3.3.3.4 热备组件140CHS21000 热备组件支持CPU及冗余系统,它提供了在系统配置中两个CPU单元之间的通讯,它使主CPU单元和备用CPU单元能完全同步的分享I/O状态。当主CPU发生故障时,通过热备组件,可以完全同步的、无扰地进行CPU模块的切换。
3.3.4 输煤皮带的各种安全保护装置
皮带机的安全保护装置主要有七类:
1.皮带速度信号元件
皮带速度信号元件的主要作用是检测皮带的速度及打滑情况,是反映皮带运行工况的一种主要的信号装置。在输煤系统程序控制中多用速度信号作为主要的联锁条件,用于逆煤流起动皮带、顺煤流停止皮带、发生故障时联跳逆煤流方向的皮带。 2.跑偏开关信号
跑偏开关通过检测皮带的跑偏来实现自动报警和停机。工作时,靠立辊的运动来检测跑偏的程度,可发出二级跑偏(轻跑偏、重跑偏)信号。 3.双向拉绳开关
双向拉绳开关可作为皮带输送机因紧急事故需停机的一种手段。它具有独立性,任意启动一向或双向启动均可发出停机信号,实现对运行人员和设备的保护。 4.堵煤检测装置
该装置用来检测输煤系统中的流槽是否发生堵塞。发生堵塞时,该装置可发出报警信号或停机信号。
5.煤流检测装置
煤流检测装置用来检测皮带机输煤的瞬时状态,可以将其接到控制盘,动态显示输煤系统的工况。
6.皮带过行程(拉长)检测装置
该装置用于检测在长期运行过程中皮带被拉长的情况。装置动作时,可发出报警信号,指示操作员判断运行工况是否正常。 7.纵向撕裂检测器
纵向撕裂保护装置用于检测皮带纵向撕裂,是避免皮带发生损毁事故的重要保护装置。该装置由电控箱和感知器组成。当有大型物料快和其他物品挤压在溜槽出口之间,皮带发生挤伤现象时,A型感知器动作。当皮带被物料穿透时,随皮带运行而挤压B型感知器,通过控制电路发出警告,并自动停机,实现保护作用。
3.3.5 工业电视系统
输煤控制系统配置工业电视作为辅助监视手段,对输煤系统沿线设备进行全面监控。输煤工业电视系统主要由中心设备、前端设备、传输设备、显示器、记录设备、预制电缆等组成。中心设备即主机柜,前端设备包括彩色摄像机、摄像镜头、电动万向云台、防护罩等;传输设备包括中继器、解码器、显示器;记录设备包括监视器、录像机、多媒体操作员站。
该厂工业电视监视系统设置26个监控点,其中6个采用彩色摄像机,另20个监控点采用黑白摄像机;5个监控点带有云台,另21个监控点不带云台;5个监控点采用6倍变焦镜头,1个监控点采用10倍变焦镜头,另20个采用定焦镜头,所有镜头都能自动调光;距离控制室较远6个监控点配有放大器。所有监控点的摄像机和镜头都有防护罩保护,防护等级为IP65。
控制室内布置8台彩色监视器用于显示图像,监视器采用吊装形式。所有操作,包括图像的切换、云台的转动、镜头的变焦等都可在多媒体计算机上完成。
矩阵切换器、控制码分配器和解码器用双绞线串联,共同构成了工业电视监控的控制部分,用于完成云台和镜头的控制。矩阵切换器布置于电视监控柜内,解码器布置在现场摄像机附近。所有摄像机的图像信号都通过各自的视频电缆输入矩阵切换器,矩阵切换器输出8路图像信号,通过视频电缆至监视器。
3.4 软件配置及实现功能
系统控制软件包括可编程控制器(PLC)控制程序编程软件上位机监控软件。可编程控制器PLC编程软件选用于之配套的下位编程软件Concept2.6进行组态和编程,上位监控站的开发软件选用CIMPLICITY高级实时监控软件包。
3.4.1 监视功能
在监控计算机显示器上可以动态实时显示全厂工艺流程,各主要设备的运行状态和过程控制的运行趋势,可以用不同颜色、图形、闪光来反映实时工况,并能实现实时报警、修改及状态显示,按规定时间生成打印各种报表,能在CRT上查询有关数据。
可以显示筒仓前、筒仓后主画面、流程画面即每段皮带机、碎煤机、地下煤仓、配煤犁等都可单独显示;模拟量棒图及数字显示;给煤机给煤量可以在线通过给煤机速度设定窗口调节。
3.4.2 管理功能
系统可实现对所有工艺设备的控制,各控制画面的切换,系统参数的设定,模拟量上、下报警线的设定。
当设备出现故障时,系统会发出语音和声响报警,且在上位监控画面上故障设备急闪烁,操作员可以在检修画面中选择该设备,将其设定为检修状态。此时,在控制画面中,该设备自动挂牌,提示操作员。设备选择时,该设备自动禁选。设备恢复后,在该画面投入该设备即可。系统提供报警记录和操作员的操作记录。
系统能自动生成报警和操作报表以及模拟量数据报表。系统可对运行参数、报警记录、操作记录等数据进行分类、过滤、归档、存储、统计、及事后跳出查看、打印,以模拟图或表格形式统计、打印班、日、周、月的运行操作方式、故障记录、设备使用记录等。
第四章 输煤控制系统功能实现
4.1 皮带机的控制
4.1.1启动允许条件
一 电源正常:
⒈ 电源柜内交流电压为220V; 2.电源柜内直流电压为 24V; 3 .电源保险良好 二 通讯正常
⒈ 主机与PLC 通讯正常 2.PLC与分站通讯正常 3.双机热备正常
三 启流程路径中控制设备均在“程控”位。
1.启动路径中#
1、#
2、#
3、#
4、#5带式输送机的就地控制箱切到“程控”位。 2.启动路径中的电动三通就地控制箱切到“程控”位。 3.启动路径中的堵煤振打器就地控制箱切到“程控”位。 4.双向给煤机就地控制箱切到“程控”位。
5.启动路径中带式除铁器就地控制箱切到“程控”位。 6.启动路径中盘式除铁器就地控制箱切到“程控”位。 7.启动路径中粗碎机就地控制箱切到“程控”位。 8.启动路径中细碎机6KV开关柜切到“程控”位。 9.启动路径中除大块机就地控制箱切到“程控”位。 10.启动路径中除杂物机就地控制箱切到“程控”位。 11.启动路径中的犁煤器就地控制箱切到“程控”位。 12.启动路径中的除尘器就地控制箱切到“程控”位。 四 启动流程路径中的控制设备均应设置为“联锁”
五 启动流程路径中的控制设备无故障,具备启车条件。 六 启动流程路径中的设备信号及皮带保护装置工作正常 七 超声波煤位计显示煤位正常准确。 八 自动配煤时,煤仓煤位不高。
4.1.2 停流程条件
1.#
1、#
2、#
3、#
4、#5皮带机任一条故障。 2.皮带机打滑; 3.皮带机跑偏; 4.皮带机拉绳;
5.皮带机回路断线及保护动作; 6.双向给煤机故障; 7.三通故障
8.堵煤振打后不通。 9.除大块机故障; 10.粗碎机超温
皮带机的控制逻辑图见附录
4.2 智能化配煤
智能化配煤包括低煤位优先配、顺序配、余煤配三种逻辑,无论哪一种配煤逻辑,它们都归结为如何控制犁煤器的抬起和落下。
控制逻辑图见附录。 结论
电厂输煤程控技术基于PLC及其网络技术,采用PLC集散控制,所有操作均在上位机上进行,整个输煤程控系统由上位机监控管理系统、PLC系统及传感器检测保护装置组成。
本文详细介绍了输煤程控技术的关键设备-可编程控制器及其网络的组成结构、特点以及工作方式,重点研究了Modicon TSX Quantum通信系统,根据某电厂输煤程控系统,具体介绍了输煤程控系统的结构、特点、控制方式以及控制功能,并在此基础上研究了皮带机的控制逻辑和配煤控制逻辑,给出了具体的控制逻辑图,具体分析了系统的功能实现问题。
火电厂尤其是大机组的火电厂,输配煤自动控制系统比较复杂,其所控制的设备很多,分布很广,且所处的环境都很恶劣。只有充分了解各控制设备的作用、功能,作好子系统的规划,充分考虑到环境等因素,才能更好地实现输配煤的自动控制。
参考文献
1.Birk, wolfing.Medvedev, Alexander.Preure and flow control of a pulverized coal injection veel.IEEE
Transaction on Control Systems Technology.2000:919-929 2.黄刚清,张国健,程朝良,入炉煤分炉计量系统的应用探讨,江西电力 2002,(2):33-34 3.T.H.A Gglund.A friction compensator for pneumatic control valves.Journal of proce
Control,2002,:123-126 4.王炜.火电厂输煤系统模糊统计方法的研究.清华大学学报.1998,(2):59-60 5.李锡雄.微型计算机控制技术.科学出版社.1999:4-5 6.吴国伟.300/600MW燃煤电厂输煤控制系统设计及优化。2000,(1):21-24 7.吴华明,刘亚敏,谭建城.2*600MW机组输煤程控系统改造.华东电力.2003,(3):20-21 8.弭洪涛.PLC应用技术 中国电力出版社 2004:6-7 9.商立群.可编程控制器在电厂输煤系统中的应用。煤矿自动化 2000,(3):20-21 10.王华 韩永志.可编程控制器在运煤自动化中的应用.中国电力出版社 北京:2003:10 11.张凯 可编程控制器教程
东南大学出版社 南京:2005 12.云鹏刚 张泽 PLC在电厂输煤自控系统中的应用 微型机与应用 2000.4,19-21 13.陈洪 廖礼初 PLC在皮带机输煤系统中应用 工业自动控制 2000.1 14.刘连凯 骆国强ModiconPLC在热电输煤系统的应用 自动化信息 2005.10 15.刘志远 可编程控制器原理及在电厂中的应用 北京:中国电力出版社,1999 16.白建云 杨晋萍 程序控制系统 北京:中国电力出版社,2005 17.王卫兵 PLC系统通信、扩展与网络互联技术 北京:机械工业出版社,2004.9 18.李季禾 大型火电厂输煤控制PLC网络 湖南电力 2002.5 19.刘卫俊 陈国定 陈惠英 叶康丰 基于PLC和称重控制器的配煤自动控制系统 工矿自动化,2005.12 20.章晓锘 发电厂输煤程控系统设计 华东水电技术,2003.4 21.李文杰 王铁军 刘力源 谢文元 发电厂配煤计算机控制系统 自动化技术及应用,2001.1 22.常瑞杰 PLC在桥式叶轮给煤机控制系统中的应用 山西电力,2001.10 23.姚福强 姚福安 高正中 电厂输煤皮带系统计算机监控方案设计 工业控制计算机,2004.8 24.Concept2.6用户手册 施耐德公司 2005 25.于庆广 闵勇 丁仁杰 信海平孙玉杰 大型火电厂自动配煤系统 电工技术,2001.1 26.中国动力工程学会 火力发电设备技术手册 北京:机械工业出版社,2002.6
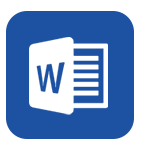