摘
要
设计介绍了一套规模为900t/d浮法玻璃生产线的工艺流程,在设计过程中,原料方面,对工艺流程中的配料进行了计算;熔化工段方面,参照国内外的资料和经验,对窑的各部位的尺寸、热量平衡和设备选型进行了计算;分析了环境保护重要性及环保措施参考实习工厂资料,在运用相关工艺布局的基础下,绘制了料仓、熔窑、锡槽、成品库为主的厂区平面图,具体对熔窑的结构进行了全面的了解,绘制了熔窑的平面图和剖面图,还有卡脖结构图,整个设计参照目前浮法玻璃生产的主要设计思路,采用国内外先进技术,进行全自动化生产,反映了目前浮法生的较高水平。
关键词:浮法玻璃、熔窑工段、设备选型、工艺计算。
Abstract The design introduced the technical proce of 900t/d float gla production line.During the planning, for the raw material, the computation of material has been made; and for the melt section, the melting kiln various spots size, The heat balance and the choose of the equipment have been calculated with reference to the domestic and foreign materials and the experience, the environmental protection importance and environmental protection measure have been analyzed.With reference to factory date, under the technology arrangement correlation knowledge foundation, the factory horizontal plan about the storage, the melting kiln, the tin trough and product storage has been finished.The melting kiln structure has been concretely introduced, the horizontal plan and the sectional drawing of the melting kiln, small mouth composition and card neck structure drawing have been draw up.The entire design consulted the main design mentality of present float gla production; took the domestic and foreign advanced technologies; carried on the entire automated production; reflected at present floats production to compare the high level.
keywords: float gla; melting section; choose of the equipment; proce calculation.
目录
前言 ...............................................................................................................................1 第一章 浮法玻璃工艺方案的选择与论证 .................................................................3 1.1平板玻璃工艺方案 ..............................................................................................3 1.1.1有曹垂直引上法............................................................................................3 1.1.2垂直引上法....................................................................................................3 1.1.3压延玻璃........................................................................................................3 1.1.4 水平拉制法...................................................................................................3 1.2 浮法玻璃工艺及其产品的优点 .........................................................................4 1.3 浮法玻璃生产工艺流成图见图1.1 ...................................................................5 图1.1 .............................................................................................................................5 第二章 设计说明 .........................................................................................................6 2.1设计依据 ..............................................................................................................6 2.2工厂设计原则 ......................................................................................................7 第三章 玻璃的化学成分及原料 .................................................................................8 3.1 浮法玻璃化学成分设计的一般原则 .................................................................8 3.2 配料流程 .............................................................................................................9 3.3 其它辅助原料 ...................................................................................................10 第四章 配料计算 .......................................................................................................12 4.1 于配料计算相关的参数 ...................................................................................12 4.2浮法平板玻璃配料计算 ....................................................................................12 4.2.1设计依据......................................................................................................12 4.2.2配料的工艺参数;......................................................................................13 4.2.3计算步骤;..................................................................................................13 4.3平板玻璃形成过程的耗热量的计算 ................................................................15 第五章 熔窑工段主要设备 .......................................................................................20 5.1 浮法玻璃熔窑各部 ...........................................................................................20 5.2熔窑主要结构见表5.1 ......................................................................................21 5.3熔窑主要尺寸 ....................................................................................................21 5.4熔窑部位的耐火材料的选择 ............................................................................24 5.4.1熔化部材料的选择见表5.3........................................................................24 5.4.2卡脖见表5.4................................................................................................25 5.4.3冷却部表5.5................................................................................................25 5.4.4蓄热室见表5.6............................................................................................25 5.4.5小炉见表5.7................................................................................................26 5.5玻璃熔窑用隔热材料及其效果见表5.8 ..........................................................26 第六章 熔窑的设备选型 ...........................................................................................28 6.1倾斜式皮带输送机 ............................................................................................28 6.2毯式投料机 ........................................................................................................28 6.3熔窑助燃风机 ....................................................................................................28 6.4池壁用冷却风机 ................................................................................................29 6.5碹碴离心风机4-72NO.16C ..............................................................................29 6.6 L吊墙离心风机9-26NO11.2D .........................................................................29 6.7搅拌机 ................................................................................................................29 6.8燃油喷枪 ............................................................................................................29 6.9压缩空气罐C-3型 ............................................................................................29 第七章 玻璃的形成及锡槽 .......................................................................................30 第八章 玻璃的退火及成品的装箱 ...........................................................................32 第九章 除尘脱硫工艺 ...............................................................................................33 9.1 除尘工艺 ...........................................................................................................33 9.2 烟气脱硫除尘 ...................................................................................................33 第十章 技术经济评价 ...............................................................................................34 10.1 厂区劳动定员见表10.1 .................................................................................34 10.2 产品设计成本编制 .........................................................................................35 参考文献 .....................................................................................................................38 致
谢 .......................................................................................................................39
前言
英国Pilkington兄弟在20世纪50年代浮法玻璃生产技术的发明付出了坚持不懈的努力,自1953年开始到1959年取得了成功耗时7年,投入了400万英镑。同时美国的Ford公司也为浮法玻璃的成功做出了很多贡献,但是Ford公司递交专利申请书时比Pilkington兄弟晚了几个月,而让Pilkington兄弟独享了此项殊荣。
浮法玻璃因熔融玻璃液漂浮在熔融锡表面成型为平板玻璃而得名。这种生产方法于无需克服玻璃本身重力,可使玻璃原板板面宽度加大,拉引速度大大提高,产量和生产规模增大:由于成型是在熔融金属表面进行,因此可以获得双面火抛光的优质镜面,其表面平整度、平行度可以与机械磨光玻璃相媲美,而机械性能和化学稳定性又优于机械磨光玻璃;同时,采取该讲法可以生产出厚度在0.5~25mm之间的多种品种、规格的玻璃,以满足不同用途的需要;另外浮法工艺还可以在线生产各种本体着色玻璃和镀膜玻璃,大大丰富平板玻璃的范畴,扩大了玻璃在各个领域的应用。因此,随着浮法玻璃生产工艺的出现和不断发展。使得其它的生产工艺逐渐被淘汰,只有Colburgh法与之并存[1]。
除了英国Pilkington公司的浮法技术之外,还有美国Pittsburgh技术比较有名。1975年,美国Pittsburgh平板玻璃公司宣布,他们在Pilkington的工艺基础上采用把玻璃液流道和流槽相结合的宽玻璃液输送系统,使流入锡槽的玻璃液带宽度与成品玻璃的宽度相近,这样可以缩短玻璃液在锡液面上的横向摊平和展薄时间,使玻璃具有更好的内在质量和横向平直性。
自1959年2月浮法玻璃生产成功以来,浮法玻璃得到迅速的推广。截至2003年,全世界已有36个国家和地区建成了140多条浮法玻璃生产线,总量达到3亿吨左右,并占到平板玻璃总量的80%以上,目前国外一些大公司掌握了较为先进的玻璃制造技术,可以生产出0.5~25mm之间各种厚度的浮法玻璃,其玻璃熔窖拉引规模也在150~100t/d之间不等。
当今世界的玻璃市场上,玻璃与玻璃加工业主要由5家玻璃公司所垄断,其总生产能力占全球玻璃生产能力的70%以上,仅日本旭硝子一家公司的市场占有率就达到了21%,英国皮尔金顿公司为12%,美国PPG11%。
我国浮法玻璃生产工艺从1965年开始实验,到1971年生产性试验线建成投产并取得成功,用了近7年的时间。在试验线投产时只能生产6mm厚的玻璃,到1972年,能够比较稳定的生产出4~9mm玻璃,并试拉了3mm玻璃;1978年,对试验线时行了熔窑该烧重油、扩大生产能力的改建;1980年,国内仅有的一条试验线已能的生产出3~10mm厚度的浮法玻璃;1981年4月,试验线采取的生产技术通过国家级技术鉴定,获国家银质发明奖。由于该生产试验线是在原洛阳玻璃厂试验成功的,故命名为中国“洛阳浮法玻璃工艺技术”(简称“洛阳浮法”)。
自“洛阳浮法”诞生以来,我国玻璃工业进入了一个快速发展时期。浮法玻璃技术被迅速推广,一批采用“洛阳浮法”技术的浮法玻璃生产线陆续建成,目前我国已成为世界上生产规模最大的平板玻璃生产国。截至2009年底,我国已建成投产的浮法玻璃生产线有125条,而采用“洛阳浮法”技术的生产线多达八十余条,其日拉引量一般为400~900t,原板厚度1.1~25mm,总生产能力达到3.13亿重箱 /年。目前,我国玻璃工业先后在日熔化量、玻璃技术装备、节能降耗、环境保护、多功能玻璃开发以及超薄、超厚品种形制方面都取得了重大突破,一些先进技术与国外的差距也正逐步缩小,我国浮法工艺技术从20世纪80年代已开始身发展中国家出口。
与发达国家相比,我国玻璃企业规模一般比较小,并且技术水准参差不齐。目前,我国有大大小小的玻璃企业几百家,但普遍存在着规模小、整体水平不高、结构单一的特点,并且地域分布不均衡,经济发达地区数量多、规模大、技术也较为先进,代表着我国浮法技术发展的新水平。目前,国内比较大的几家玻璃企业市场占有率仍然较低,最大的玻璃集团年销售额仅2~3亿美元,与国外大公司相比差距很大。
今后玻璃发展的目标是将常规的和特殊的技术进步结合起来,实现浮法玻璃生产技术、装备的新突破,并在新产品开发、功能化、环保等多方面加大技术研究力度,以促进玻璃工业可持续发展。
第一章 浮法玻璃工艺方案的选择与论证
1.1平板玻璃工艺方案
平板玻璃规模化生产直到18世纪才真正出现。在18世纪生产平板玻璃的方法主要有两种:一是冠形制板法二是圆筒法。后来进一步改进出现了Sieverts法,1903处发明了Lubers法,到20世纪后出现了很多很好的生产平板玻璃的方法。
1.1.1有曹垂直引上法
其形成特点是利用槽子砖成型,由于静压力作用,玻璃液从槽口向上涌出形成板根,板根处玻璃液受引上机石棉辊拉引继续上升,并经受水冷却器急冷,逐渐硬化形成玻璃原板,进入引上机膛退火。原板经切割而成原片。玻璃性质、板根成形、边子成形、原板拉伸力是影响玻璃成形的决定性因素。其缺点是由于使用槽子砖,玻璃板的波筋、线道等缺陷难以根除,光学畸变较重,产量低。
1.1.2垂直引上法
利用引砖成形,玻璃带通过设置在玻璃液面经上的一对水平冷却器冷却后被引上拉引。表层玻璃一方面抵抗重力减少厚度,另一方面被引上进一步冷却到最后固化,过到一定厚度和宽度,继续引上,引砖是无槽垂直引上的重要形成设备,有挡热,分流和稳定板根的作用。形成板根的玻璃液由表面流的玻璃自由汇合被引上进入板根。玻璃液的温度和对流还有引上室的气流波动对原板形成有极大影响。其缺点是生产操作难,玻璃厚度差的大,不易生产小于2mm的薄玻璃。
1.1.3压延玻璃
它是利用水平连续压延法,能大量生产。从玻璃熔窑末端流液口连续地流出玻璃液,通过用水冷却的上下一对辊子之间,没冷却的玻璃液被压延辊压成一定厚度的玻璃板,随两辊回转玻璃板被向前拉引,经输送辊道进入退火窑,冷到室温。其缺点是玻璃的厚度的均匀性不好,不易生产薄玻璃。
1.1.4 水平拉制法
它是在玻璃熔窑末端设置浅引上室,玻璃带在引上室中有表面被拉引,经水冷却辊冷却 ,黏度增加,玻璃被连续拉引成带状玻璃板垂直上升到60cm左右高的位置,在此经加热软化的玻璃板借助转向辊将玻璃弯成不平方向,送进退火窑。这种方法生产的质量好,产量高。其缺点是由于形成室结构复杂,不易控制。 1.2 浮法玻璃工艺及其产品的优点
1.质量好,由于玻璃液是在锡槽中抛光,具有很好的抛光效果,也不会因为机械磨光引起的玻璃缺陷。
2.产量大,浮法玻璃采用全自动,不需要庞大的沙子分级和机械磨光设备,成品率高,且采用自动化,规模扩大。
3.品种多,采取这种方法可以生产出厚度在0.5~25mm之间的多种品种、规格的玻璃,以满足不同用途的要求。另外,浮法工艺 还可以在线生产各种本体着色玻璃和镀膜玻璃,大大丰富了平板玻璃的范畴,扩大了玻璃在各个领域的应用。
综上,浮法生产是目前世界上最先进的生产技术,到2008年,浮法玻璃占玻璃生产行业的76.7%以上,中国建成的洛阳浮法线有146条,其是拉引量在300~700t,原板厚度为1.1~25mm,总生产能力到3.06亿箱/年。
1.3 浮法玻璃生产工艺流程图
图1.1玻璃生产工艺流程图
第二章 设计说明
本设计采用最先进的玻璃生产工艺之浮法玻璃生产技术,积极采用先进的设备和技术,以提高生产质量,提升产量为目标努力使各方面达到世界先进水平。设计中大量收集目前国内外先进技术,对结构进行改善还为将来生产规模的扩大留有余地。在收集大量数据的基础上做出合理、科学、先进的设计。
2.1设计依据
产品方案:
浮法平板玻璃; 生产规模:
日熔化量为900t; 工作制度:
52/5/8; 玻璃厚度:
5mm; 玻璃原板宽度:4000mm; 玻璃净板宽度:3500mm; 总成品率:
80%; 产品品种:
平板玻璃; 冷修周期:
8年; 玻璃的化学成分见表2.1
表2.1 玻璃化学成分表
单位:%(质量分数)
化学成分 含量 SiO2 72.0 Al2O3 1.0
Fe2O3 0.1
CaO 8.5
MgO 4.00
R2O 14.3
SO3 0.1
All 100 所用各原料的化学成分见表2.2
表2.2 各原料的化学成分
单位:%(质量分数)
原料
硅砂 白云石 石灰石 纯碱 芒硝 煤粉 含水率
1.0 0.3 2.0 1.8 4.2 SiO2 98.76 0.69 0.3
Al2O3 0.56 0.15
Fe2O3 0.08 0.13 0.07
CaO 0.14 31.57 55.4
MgO 0.02 20.47 0.2
N2O 0.19
57.94
Na2SO3
C
1.10
0.29
0.05
0.5
0.37
41.47
95.03
84.11
2.2工厂设计原则
采用先进、可靠的技术措施的装备,确保能生产出满足企业要求的平板玻璃。 以满足浮法线高标准产品质量和品种要求为前提,进行设备选型,既要有效控制投资,又必须确保达到使用要求,确保总体目标和实现。环境保护、职业安全卫生、节能、消防等方面均要符合国空的相关标准规范、规定。总体规划的布局合理、道路通畅,方便管理,最大限度利用厂区原有场地和设施。全面解决工厂生产,厂外运输和各种物料储备的关系。应该考虑工厂建成后生产潜力的可能和留有工厂发展的余地。
第三章 玻璃的化学成分及原料
3.1 浮法玻璃化学成分设计的一般原则
玻璃科学为玻璃成分设计提供了重要的理论基础,包括玻璃形成和结构理论,相平衡,成分和性质与结构的关系等方面,但迄今在大部分情况下,理论还只能定性地为玻璃成分设计指出方向,必须反复通过实践调整成分以获得所需性能的玻璃。
一般说来,玻璃成分设计要考虑的主要方面如下。
(1)必须满足使用性质的要求,即依赖于成分和性质与结构的关系。就目前玻璃科学发展水平而言,主要阐述成分和性质之间的关系,成分和结构间的关系还未能精密确定。
(2)所设计的成分必须能够形成玻璃并具有较小的析晶倾向,因而可以借助于玻璃形成区域图和相图来确定。
(3)必须符合熔制、成型等工艺要求。
浮法玻璃化学成分是由普通平板玻璃基础上设计出来的,是由钠钙硅玻璃组成演变而来的。根据Na2O-CaO-SiO2系统相图确定该系统中能够形成玻璃的组成范围为:12%~18% Na2O,6%~16% CaO,68%~82% SiO2,但在实用玻璃组成中该系统的组成范围为:12%~15% Na2O,8%~12% CaO,69%~73% SiO2。在这个三元系统玻璃组成中,容易形成两种析晶组成,失透石(Na2O·CaO·SiO2)和硅灰石(CaO·SiO2),在生产实践中当引入MgO和Al2O3时,不仅玻璃的析晶性能得到改善,而且热稳定性和化学稳定性均得到改善,因而形成了普通平板玻璃化学成分(表3.1)。表中Fe2O3为原料中杂质所致,并非设计数值,而是限制数值;而SO3主要是由澄清剂芒硝引入[3]。
表3.1 普通与浮法玻璃化学成分比较
单位:% 化学成分 普通玻璃 浮法玻璃
SiO2 71~73 71.5~72.5
Al2O3 1.5~2
Fe2O3
CaO 6.0~6.5 8.0~9
MgO 4.5 4.0
R2O 15 14~14.5
SO3
0.1%以内,最好在0.08%以下,以使玻璃有良好的透光率,经调整后浮法玻璃化学成分见上表。
用于制备琧配合料的各种物料,统称为玻璃原料。根据它们的用量不同,分为主要原料和辅助原料两类。主要原料指玻璃中引入各种组成氧化物的原料,如石英砂、白云石、尾砂、纯碱和芒硝等。辅助原料是使玻璃获得某些必要的性质和加速熔制过程的原料。它们用量少,但其作用并不是不重要。根据作用不同,分为澄清剂,脱色剂,氧化剂和还原剂等,对原料质量主要有以下要求:原料引入的主要成分含量高,杂质含量低,不得超标;原料组成粒度分布合理,以保证配合料均匀度达最佳状态,玻璃熔制质量好;原料中难溶矿物的含量和粒度符合要求,避免玻璃成品上形成固体夹杂物。
3.2 配料流程
3.2.1 硅砂系统为引入SiO2的原料,SiO2的想对分子质量是60.06,密度是2.4~2.5g·cm-3。SiO2是玻璃形成骨架的主体,以[SiO4]的结构组成不规则连续网络结构。它本身就可以开成玻璃,即石英玻璃,引入二氧化硅的作用,是提高玻璃的熔制温度、黏度、化学稳定性、热稳定性、硬度和机械强度,同时它又能降低玻璃的热膨胀系数和密度。
合格的硅砂由汽车运输进厂,入喂料仓,经电磁振动给料机喂料,斗式提升至均化库料堆上放的带卸料小车的带式输送机上,进行均化堆料作业。
用于配料的硅砂,有门式耙料机均化取料,经带式输送机运至1#式提升机,提升入中间仓,有电磁振动给料机喂入平面摇筛进行保护性筛分,筛下物同2#斗式提升机提升,以带式输送机送入粉库贮存,当门式耙料机发生故障时,同轮式装载机代替,经带式输送机运至1#斗式提升机,提升入 中间仓进行筛分作业。
3.2.2 白云石系统 为引入MgO的原料,MgO的相对分子质量是40.32,它在硅酸盐玻璃中是网络外体氧化物。玻璃中经3.5%以下的MgO代替部分CaO,可使玻璃形成硬化速度变慢,降低玻璃的析晶倾向,提高玻璃的化学稳定性的机械强度。
白云石块料同汽车运输进厂,由抓斗桥式起重机运至喂料仓,通过电磁振动给料机喂入鄂式破碎机进行破碎。破碎后的物料经斗式提升到中间仓,再由电磁振动给料机喂入锤式破碎机进行细碎,细碎后的物料经斗式提升机升入两台六角筛进行筛分,筛上物返至锤式破碎机细碎,再提升、筛分,筛下的合格物料由斗式提升机升入库顶带式输送机,送入粉库贮存。
3.2.3 尾砂系统为引入Al2O3的原料,Al2O3的相对分子量为101.94,密度为3.84g·cm-3。它属于玻璃的中间体氧化物,能降低玻璃的结晶倾向,提高玻璃的化学稳定性、化学稳定性、热稳定性、硬度、机械强度和折射率,减轻玻璃对耐火材料的侵蚀,并有助于氟化物的乳浊。
利用原有加工系统,合格粉料由斗式提升机提升,然后经过双向闸门和带式输送机送投影仪粉库贮存。
3.2.4 石灰石系统为引入CaO的原料,CaO的相对分子量为56.08,密度为2.6~2.8 g·cm-3,是玻璃结构网络外氧化物,其主要作用是稳定剂,即增加玻璃的化学稳定性和机械强度。主要矿物是方解石,是一种微晶或潜晶结构的化学与生物化学沉积岩。
利用原有加工系统,合格粉料由斗式提升机提升,然后经过双向闸门和带式输送机送投影仪粉库贮存。
3.2.5 纯碱、芒硝系统为引入R2O的原料,Na2O的相对分子量是62,密度2.27 g·cm-3,是玻璃网络外氧化物,可降低玻璃的黏度,使玻璃易于熔融,是玻璃的良好溶剂。可增加玻璃的热膨胀系数,降低玻璃的热稳定性,化学稳定性和机械强度。
纯碱、芒硝由火车运输进厂,由手推车从袋装原料库运至原料车间倒料处,人工拆袋倒料经斗式提升机提升入立角筛进行筛分,筛上物经笼型碾粉机粉碎再提升、筛分,筛下的合格料由斗式提升机提升入粉库贮存。
3.2.6 煤分系统它引入的主要成分是还原C,因为芒硝是主要澄清剂,它在熔窑内高温分解产生O2和SO2,所以使用芒硝里还要使用澄清剂,而煤分就是一个很好的选择。
袋装的煤粉由汽车运输进厂,由手推车从库房运至粉库吊运孔处,经电动葫芦提升至粉库顶,人工拆袋倒料送入粉库贮存。
3.2.7 称量混合系统,各种粉料按配比分别采用“减量法”的“增量法”电子秤进行准确称量,通过称量带式输送机运至预定的混合机混合,混合时加适量水蒸汽,以前常加水混合,但加水蒸汽有更多好处,比如混合料不易结团,混合料更为均匀,粒度相差不太大,混合均匀的配合料卸入中间仓,再由配合料带式输送机运至浮法联合车间窑头料仓,之后便进行熔窑的熔化、锡槽的成型、退火窑退炎,经过切裁得到相应规格的成品。
原料工艺有三个关键部位:原料成分、原料的颗粒大小和原料混合的均匀度,实际生产中各种原料的控制粒度范围见表3.2。 3.3 其它辅助原料
1)澄清剂 往玻璃配合料或玻璃液中加入一种高温时本身能气化或分解放出气体,以促进排除玻璃液中气泡的物质,称为澄清剂。浮法玻璃常用的澄清剂有三氧化二锑、硝酸盐、硫酸盐、氟化物、二氧化铈。
表3.2 实际生产中各种原料的控制粒度范围
原料
硅砂
粒度范围 ≥0.71 0.71~0.50 0.50~0.106
品质百分比%
0 ≤5.0 ≥91.0 ≤4 0 ≥92.0 ≤8.0 0 ≥92.0 ≤8.0 0 ≤4.0 ≥78.0 ≤18.0 ≤2 ≤75
含水率%
到收贷时硅砂水分
≤5
粉料含水率≤0.5
粉料含水率≤0.5
粉料含水率≤0.5 白云石
石和石
长石 纯碱
含水率≤0.7
2着色剂 使玻璃着色的物质,称为着色剂。其作用是使玻璃对光线产生选择性的吸收,呈现一定的颜色。根据着色剂在玻璃中呈现形态不同,分为离子着色剂、胶态着色剂和硫硒化物着色剂三类。浮法玻璃常用离子着色剂即过渡金属元素和稀土元素的化合物。
3)脱色剂 对浮法玻璃透明度危害最大的是微量的铁,其次是铬、钒、钛。脱色主要是如何减弱和中和铁的着色作用的问题。方法主要有物理脱色和化学脱色。常用的物理脱色剂有二氧化锰、氧化钴、氧化镍、氧化钕。常用的化学脱色剂有硝酸钠、硝酸钾、三氧化二锑、氧化铈、氧化锰。
4)碎玻璃 在玻璃生产和加工和各个环节,总会产生一定量的碎玻璃,如生产中的不合格产品及切裁下来的边子等。从工艺上看,有利于配合料的熔化,澄清,节能,提高产量,降低成本等。使用碎玻璃的过程中必须注意几个问题:二次挥发;二次积累;对某些化学稳定性差的玻璃,由于表面水解造成表面层与内层成分之间的差别,若熔制温度较低或玻璃的对流不大时,在熔制后的玻璃液内部往往留下明显的差别;当玻璃重熔时,热分解会使氧化铁转变为氧化亚铁,同时也影响硒的脱色作用,使玻璃的颜色变坏。热分解出来的氧,容易扩散到周围的气泡中去,与之一起益处玻璃液外,导致玻璃缺氧,呈还原性制。对变价元素为基础的颜色玻璃会引起色泽上的变化;在碎玻璃中含有少量的化学结合气体,在重熔时产生相当于二次气泡那样的微小气泡,因此,加入碎玻璃多时就难于澄清;使用外购玻璃时,除要进行清洗、选别、除杂和磁选除铁外,还必须经常取样,进行化学分析,对配合料配方进行调整。
第四章 配料计算
4.1 于配料计算相关的参数
飞散量1)纯碱飞散率=×100%
纯碱总用量芒硝中的Na2O×100% 2)芒硝含率=纯碱引入的Na2O+芒硝引入的Na2O3)配合料SO3含量=芒硝加入量(kg)×80×芒硝含量%
142×配合料(t)×玻璃获得率%4)炭粉含量=炭粉用量×炭含量%×100%
芒硝用量×芒硝含量%炭粉加入量×炭含量%5)想配合料炭含量=
配合料量×玻璃获得率%100kg玻璃液×100% 6)玻璃获得率=制100kg玻璃液用的原料的量4.2浮法平板玻璃配料计算
4.2.1设计依据
产品方案:
浮法平板玻璃; 生产规模:
日熔化量为900t; 工作制度:
52/5/8; 玻璃厚度:
5mm; 玻璃原板宽度:4000mm; 玻璃净板宽度:3500mm; 总成品率:
80%; 产品品种:
平板玻璃; 冷修周期:
8年; 玻璃化学成分见表4.1
表4.1 玻璃化学成分表
单位:%(质量分数)
化学成分 含量 SiO2 72.0 Al2O3 1.0
Fe2O3 0.1
CaO 8.5
MgO 4.00
R2O 14.3
SO3 0.1
All 100 各原料的化学成分见表4.2
表4.2 各原料的化学成分
单位:%(质量分数)
原料
硅砂 白云石 石灰石 纯碱 芒硝 煤粉 含水率
1.0 0.3 2.0 1.8 4.2 SiO2 98.76 0.69 0.3 1.10
Al2O3 0.56 0.15
0.29
Fe2O3 0.08 0.13 0.07 0.05
CaO 0.14 31.57 55.4 0.5
MgO 0.02 20.47 0.2 0.37
N2O 0.19
57.94 41.47
Na2SO3
95.03
C
84.11 4.2.2配料的工艺参数; 计算基础:100kg玻璃液; 计算精度:0.001 纯碱灰散率:1.5%; 玻璃获得率:80%; 碎玻璃掺入率:20%; 芒硝含量:3%; 碳粉含率:4%; 4.2.3计算步骤;
1、芒硝用量的计算,设生产100KG玻璃液用xkg芒硝。
x×0.4147=3%
14.3x=1.034(kg) 芒硝引入和各物质的量如下;
SiO2=0.0103(kg)
Al2O3=0.003(kg) Fe2O3=0.001(kg)
CaO=0.005(kg) MgO=0.004(kg)
N2O=0.429(kg)
2、纯碱用量的计算。
14.30.429纯碱用量==23.940(kg)
0.579
43、煤粉的用量,设用量为x kg.x×0.8411=4.7%
1.034×0.9503x=0.055(kg)
4、硅砂用量计算,设用量为x.0.9876x=72.0-0.010
x=72.8(kg) 由硅砂引入各氧化物的量见表4.3
表4.3硅砂引入各氧化物的量
单位:kg
原料 硅砂 SiO2 73.8
Al2O3 0.408
Fe2O3 0.1
CaO 0.058
MgO 0.014
R2O 0.138
5、白云石和石灰石用量计算,设白云石为x,石灰石为y 0.3157x+0.554y=8.5-(0.058+0.005)=8.437 0.2047x+0.002y=4.0-(0.014+0.004)=3.982 x=19.403(kg)
y=4.172 (kg) 由白云石和石灰石引入各氧化物的量见表4.4 表4.4白云石和石灰石引入各氧化物的量
单位:kg
原料 白云石 石和石
SiO2 0.134 0.012
Al2O3 0.029
Fe2O3 0.025 0.002
CaO 6.126 2.311
MgO 3.972 0.008
6、校正纯碱用量和挥散率,设用量为X,挥散为Y x×0.5794=14.3(0.429+0.138)
x=23.702(kg) y=0.01
523.702+yy=0.361(kg)
7、校正硅砂用量设用量为x 0.9876x=72.0-0.0103-0.134-0.012=71.844 x=72.746(kg)
8、玻璃获得率
玻璃获得率=100/121.112=82.5%
9、换料单位计算
碎玻璃掺入率:20%,配合料的含水为4%,混合机容量为1000KG。 以硅砂为例 干基=[1000湿基=(1000×20%)]×60.065%=480.52kg
465.52=485.37kg
11.0%由于水分含量为4% 800/96%=833.33kg 833.33-799.61=33.72kg 所以还有加水33.7kg.
900×33.7=30.33t 对于日产900 t,所以每天加水量=
10、汇总成原料用量见表4.5
表4.5各原料年用量表
原料 日用量(干基)t/d 硅砂 白云石 石灰石 纯碱 芒硝 煤粉 合计 碎玻璃 总计 654.7 174.6 37.54 213.3 9.306 0.495 1090 180 1207
含水率 (%) 1.0 0.3 2.0 1.8 4.2 2.1
损失率 (%) 1.0 0.5 0.5 0.5 0.5 0.5
湿基 (t/d) 661.3 175.1 38.3 217.2 9.71 0.506 1102.2 180 1282
日进厂量 (t/d) 668 176 38.5 218.3 9.7 0.509 1111 180 1291
年进厂量(t/a) 243823 64249 14056 79687 3564 185 405563 65700 471263 4.3平板玻璃形成过程的耗热量的计算
各原料在湿基中的百分比见表4.6
表4.6 原料 100k g湿基中的含量
硅砂 白云石 石灰石 纯碱 芒硝 煤粉 合计 59.99 15.89 3.476 19.70 0.881 0.046 100
98.76 0.69 0.3 1.10
0.56 0.15
0.29
0.08 0.13 0.07 0.05
0.14 31.57 55.4 0.5
0.02 20.47 0.2 0.37
0.19
57.94 41.47
84.11
SiO2
Al2O3
Fe2O3
CaO
MgO
N2O
C (1)原始资料 ① 料方及原料组成;
② 碎玻璃用量占全部的20%; ③ 配合料水分4%;
(2)100kg湿粉料中形成氧化物的量见表4.7、4.8 表4.7100kg湿粉料中形成氧化物的量
氧化物数量
原料 形成玻璃液的氧化物的计算
SiO2
Al2O3 Fe2O
30.323
0.046
CaO
0.081
MgO
0.012
N2O
0.109
0.022
0.019
4.816
总量
57.42
59.998×0.96×0.987=56.849 56.849 59.998×0.96×0.0056=0.323
硅砂 59.998×0.96×0.0008=0.046 59.998×0.96×0.0014=0.081 59.998×0.96×0.0002=0.012 59.998×0.96×0.0019=0.109 15.891×0.96×0.0069=0.105 0.105 白云石 15.891×0.96×0.0015=0.022 15.891×0.96×0.0013=0.019 15.891×0.96×0.3157=4.816
15.891×0.96×0.2074=3.164
表4.8100kg湿粉料中形成氧化物的量
氧化物数量
原料 形成玻璃液的氧化物的计算
SiO2
Al2O3
Fe2O3
CaO
3.164 8.126
MgO
0.007
N2O
总量
1.948 3.476×0.96×0.003=0.010
石灰石
0.010 3.476×0.96×0.0007=0.002 3.476×0.96×0..554=1.849 3.476×0.96×0.002=0.007
0.002
1.849 纯碱 19.708×0.96×0.5794=10.96
20.009
0.002
0.004
0.004
0.003
10.962 10.962
0.351
0.3649 0.881×0.96×0.011=0.009 0.881×0.96×0.0029=0.0024
芒硝 0.881×0.96×0.0005=0.0004 0.881×0.96×0.005=0.004 0.881×0.96×0.0037=0.003 0.881×0.96×0.4147=0.351
合计 玻璃成分%
56.973
0.347
0.071
6.75
3.186 11.442 78.769
72.329 0.4405 (3)生成硅酸盐耗热 以1kg湿粉料计,单位是kj/kg。 由CaCO3生成CaSiO3时反应耗热量q1 q1=1536.6GCaO=1536.6×(0.01849+0.00004)=28.47
由MgCO3生成MgSiO3时反应耗热量q2 q2=3466.7GMgO=3466.7×(0.00012+0.00007+0.00003)=1.144
由CaMg(CO3)2生成CaMg(SiO3)2时反应耗热量q3 q3=2757.4GCaMgO2=2757.4×(0.04816+0.03164)=220.04
由NaCO3生成NaSiO3时反应耗热量q4 q4=957.7GNaO2=957.7×0.10962=104.9
由Na2SO3生成Na2SiO3时反应耗热量q5 q5=3476.1GNa2O=3476.1×0.00351=12.2 1kg湿粉料生成硅酸盐耗热
qi=q1+q2+q3+q4+q5 =28.4731+1.14401+220.0405+104.983+12.2 =366.8 (4) 配合料用量计算
在粉料中挥发分占22%,在1kg粉料中加上玻璃0.2kg,得到
10.22+0.2=0.98(kg玻璃液)
因此,熔成1kg玻璃液的粉料量为
1=1.0204 0.98所用碎玻璃量
0.2G碎==0.2040
0.98熔成1kg玻璃液所要的配合料的量 G粉=G配=G粉+G碎=1.0204+0.2040=1.224
(5) 玻璃形成过程的热量平衡 以1kg玻璃液计,单位kJ/kg从0℃算起
①支出热量
a、生成硅酸盐耗热Q1 Q1=qi•G粉=366.842×1.0204=374.3
b、形成玻璃热耗
Q2=374G粉(1-0.01G气)=374×1.0204(1-0.01×22)=297.6
c、加热玻璃液到1400℃耗热Q3 c玻=0.672×4.6×104t=0.672×4.6×104×1400=1.316
Q3=c玻×t玻=1.3168×1400=1844
d、加热逸出气体到1400℃耗热Q4,1400℃时逸出气体平均比热
c气=0.01[cco2•(CO2%+SO2%)+cH2O•H2O%
=0.01(2.325×57.10+1.824×42.90)
=2.110kJ/(m3•°C)
Q4=0.01v气G粉c气t熔=0.01×14.504×1.0204×2.110×1400=437.1
e、蒸发水分耗热Q5
Q5=2491G粉•G水=2491×1.0204×0.05=127 f、原料带入热量Q6,设配合料入窑时为20℃
c玻20°104×20=0.756 C=0.7511+2.65×Q6=G粉c粉t粉+G碎c碎t碎=1.0204×0.963×20+0.2040×0.756×20=16.56
所以1kg玻璃液的形成耗热Q Q=Q1+ Q2+ Q3+ Q4+ Q5- Q6
=374.325+297.671+1844+437.189+127.0908-16.68=3063 1t 玻璃液的形成耗热=3.06×106kJ 每天耗热=3063595.8×900=2.8×109 kJ 第五章 熔窑工段主要设备
浮法玻璃熔窑属于横火焰蓄热式池窑,如图5.1。浮法玻璃熔窑根据各部功能其构造分为玻璃熔制、热源供给、余热回收、排烟供气四大部分。
图5.1熔窑结构图
5.1 浮法玻璃熔窑各部
(1)熔化部 熔化部是进行配合料熔化的玻璃液澄清、均化的部分,由于采用火焰表面加热的深化方式,熔化部分为上下两部分,上部是火焰空间,下部是窑池。火焰空间是由胸墙、大旋、前端墙和后山土墙组成的空间体系。火焰空间内充有来自热源供给部分的炽热气体,在此,火焰气体将自身热量用于熔化配合料,也传给玻璃液、窑墙和窑顶(大旋)。火焰空间应能满足燃料完全燃烧,保证供给玻璃熔化和澄清所需的热量,并尽量减少散热。窑池是配合料熔化成玻璃液并进行澄清、均化的地方,它应能供给足量的熔化完全的透明玻璃液。窑池由池壁和池底构成。池壁和池底均由大砖砌筑,为方便大砖的制造,减少材料的加式量的方便施工,窑池都是呈长方形或正方形。为使窑池达到一定的使用期限,池壁厚度为250~300mm,池底厚度根据其保温情况而定,不采用保温的池底厚度为300mm。
(2)加料口 浮法玻璃采用正面投料,加料口设地在熔窑纵轴的前端,由投料池上部挡墙组成。投料池是突出于窑池外面和池窑相通的矩形小池。传统的投料池宽是熔化池宽的85%左右,投料池的料壁上平面与池窑的上平面相齐,投料池池壁使用的耐材料与熔化部材料相同。在实际生产中,投料池侵蚀严重,尤其在投料池的拐角处,两面受热,散热面积小,冷却条件差,是池窑中最容易损毁的部位。现代浮法熔窑很多采用与熔化部等宽的加料池,使得料层更薄,并能防止偏料,更避免了因拐用砖损毁带来的热修麻烦。
(3)冷却部 是熔化好的玻璃液进一步均化和冷却的部位,也是将玻璃分配给各成型设备的部位。冷却部应提供纯净、透明、均匀且温度稳定的玻璃液。与熔化部相同冷却部也为矩形窑池,也分为上下层,结构与熔化部大致相同。
(4)分隔装置 分隔装置有气体分装置和玻璃液分隔装置。气体空间分隔装置主要有矮旋、吊矮旋、吊旋等;玻璃液分隔装置有卡脖、冷却水管、窑坎等。
5.2熔窑主要结构见表5.1
表5.1熔窑主要结构
项目 熔化能力 窑龄 燃料种类 热值 油耗 熔化率 小炉对数
一侧小炉总宽占熔化带长 每天每吨玻璃占冷却部面积
数值 900 8 重油 9600 123 2.45 8 52.77 0.212
单位 t/d 年
Kcal/kg(1 Kcal = 4.1868 KJ)
t/d t/(m2d) 对 % m2/(t·d) 5.2.1熔化部窑池面积Fm=Q/K 其中Fm为熔化面积单位m2,Q熔窑规模单位t/d,K为熔化率单位t/(m2d)。
Fm=Q/K=900/2.45=367.347(m2) 澄清带长取15.2m 5.2.2冷却部面积 采用熔化部面积和冷却部面积的比例来确定,比例系数为0.29(经验参数),已知熔化部面积为568.5 m2
F熔/F冷=1/0.29
F冷=164.865 m2例 冷却部宽和长满足X/Y=0.59
X=9.86
Y=16.71 5.3熔窑主要尺寸
(1)窑池设计 熔化部窑池面积如上计算。浮法玻璃熔窑熔化部的长度关系到玻璃液在熔窑内和停留时间,应满足熔化澄清的要求,一般由三部分成:前脸墙与1#小炉中心线的距离一般为3.5~4.0m,主要考虑到熔化作业对前脸墙和1#小炉蓄热室的侵蚀情况以及配合料的熔化难易;小炉间距之和在3.5m左右,主要考虑到火焰的覆盖面积;末对小炉中心到分隔装置的距离主要考虑到澄清均化的需要,还要考虑安设检测孔、大砖门、耳池等需要,一般在15m左右。
(2)火焰空间设计 火焰空间与窑池等长,比窑池宽300~500mm,这是为了能够牢固的托住胸墙,防止池壁侵蚀后胸墙下倾和避免火焰过长时胸墙烧蚀。火焰空间的高度主要由胸墙高度和大旋旋股合成。胸墙的高度在1500~2000mm左右。大旋空间的高的确定要考虑大旋的结构强度,设计时为了方便,常采用股跨比或旋高的比值来表示,燃油熔窑的旋高一般为1/9~1/7。
(3)投料池设计
投料池的长度需考虑投料机的推料行程,还要求前脸墙不受投料机推力的影响。当选用斜毯式投料机时投料口长度在2.3m左右。投料池宽度取决于投料机的宽度和所用投料机的台数,希望投料池宽度被投料机占满,两侧不要留得过空,以防玻璃液溢出或散热增多。计算式为B=nB+200(mm)。
(4)分隔装置
浮法玻璃熔窑的卡脖宽度小到熔化池宽度的40%~50%,采用搅拌器,再在卡脖处穿大水管,则其长度为4.8~5.5m。
(5)小炉结构设计
浮法玻璃熔窑的小炉、蓄热室设置在池窑的两侧,对称布置,本设计采用8对。小炉底下的操作空间尺寸,即熔窑池壁外侧到蓄热室内侧墙处的距离,一般此距离取2.7~3.2m,脖底到操作平台的高度一般取1.8m左右。
小炉喷出口结构尺寸 宽度一般不小于1.4m,可以用一侧小炉喷出口宽度之和占熔化带长的百分数计算,一般在45%~55%。则 nB/[d1+(n-1)d2+1]=45%,式中n为小炉对数;B为小炉口宽度,d1为前脸到1#小炉中心线的距离,d2为小炉中心线的距离,喷出口宽度与高度的比值在2.3~2.5左右,喷出口的旋升高一般取1/10~1/8。
(6)蓄热室结构设计
蓄热室长度决定与小炉的对数和间距,用L=d1+(n-1)d2+d3计算,式中d1为1#小炉中心线到蓄热室前端墙内侧的距离,一般取1.2~1.6或d1=d2/2;n小炉对数;d2小炉中心线距离,d3末对小炉中心线到蓄热室后端墙内侧的距离,一般取d3=d1。设计蓄热室尺寸就是设计蓄热室格子尺寸,高度和宽度的适宜比值为2.0~2.3。
(7)火焰空间计算
火焰空间是由胸墙、大碹。前脸墙和后山墙组成的空间体系。其长度与窑池相等,其宽度比窑池宽200~300mm。火焰空间高度由胸墙高度和窑碹碹股高度合成。
各部位主要结构尺寸见表5.2
表5.2熔窑的主要结构尺寸
单位(m/m2)
宽度
投料口
长度 玻璃液深度
宽度 长度
熔化带
玻璃液深度 熔化面积 宽度 长度
澄清带
玻璃液深度 澄清面积 宽度 长度
卡脖
玻璃液深度 卡脖面积 宽度
冷却部 冷却部
长度 玻璃液深度 冷却部面积 小炉对
小炉
1#~7#小炉口内宽 8#小炉口内宽
内宽
蓄热室
总长度 格子体体积
1.10 28.62 9.86 16.71 1.30 164.76 8 1.96 1.60 4.71 23.73 1158.14 1.30 214.776 5.3 5.4 1.30 367.347 14.13 15.2 13.4 2.4 1.30 14.13 26.0 窑体总长度 长度 70.72 胸墙高度的计算,必须满足火焰空间使燃料完全燃烧。如容积太小火焰不能充分伸展,造成燃料不能完全燃烧,达不到所要求的温度,即浪费了燃料,提高了成本,。胸墙太高则散热量大也不利于生产。浮法窑烧重油其胸墙高度在1500~2000mm。根据各方面情况,取1800mm。
窑碹碹股高度计算,根据熔窑的结构,在保证大碹足够强度的情况下,大碹应尽量低,因为股跨越大,熔窑散热量也就越大,经计算,本设计煌碹升高取113/1000。
火焰空间设计合理与否常采用热负荷的指标来核定其容积。火焰空间的热负荷值是指单位空间容积每小时燃料燃烧所发出的热量,也称为火焰空间容积热强度,单位为W/m3。火焰空间的热负荷一般在100000 W/m3左右。
窑碹碹股面积=[(50.98/360)×3.14×(5.661/0.43)2]-[(5.661/0.43)×0.9026×11.362×0.5]=9.562 m3为
火焰空间容积=(9.562+11.362×1.800)×70.72=2129.404 每小时燃油发出的热=(9600×1000×4.18×123)/24=205656000 火焰空间热=205656000/2129.404=96579.137(W/m3) 由此可以推断火焰空间设计合理,且可以使熔窑熔化充分。
5.4熔窑部位的耐火材料的选择
5.4.1熔化部材料的选择
表5.3熔化部材料的选择
胸墙
熔化带 澄清带
大碹 前脸翼墙
33#电熔AZS(氧化法普浇)
优质硅砖
优质硅砖
33#电熔AZS(氧化法普浇)
优质硅砖
前脸翼墙
33#电熔AZS(氧化法普浇)
优质硅砖
L型吊墙
复合结构
5.4.2卡脖
表5.4卡脖材料的选择
铺面砖
池底
密封料 池底砖
池壁 胸墙 顶碹 卡脖小吊墙
电熔α-β砖(氧化法无缩孔)
刚玉质密封料 粘土大砖(BN-4a) 电熔α-β砖(氧化法普浇)
优质硅砖 优质硅砖 烧结莫来石砖
5.4.3冷却部
表5.5冷却部材料的选择
铺面砖
池底
密封料 池底砖
池壁 胸墙 大碹 前山墙 后山墙
流道出口碹
Jargal H RN
电熔α-β砖(氧化法无缩孔)
刚玉质密封料 粘土大砖(BN-4a)
电熔α-β砖(氧化法普浇)
优质硅砖 优质硅砖 优质硅砖 优质硅砖
5.4.4蓄热室
表5.6蓄热室材料的选择
上段
墙体
中段 下段
高纯镁砖(DM-98) 直接结合镁铬砖(DMC-12)
粘土砖 炉条碹 顶碹
顶层 上段
低气孔粘土砖 优质硅砖
RADEX VZ-CN(三层) 高纯镁砖(DM-98) 高纯镁砖(DM-98) 直接结合镁铬砖(DMC-12) 低气孔粘土砖(ZGN-42) 高纯镁砖(DM-98) 高纯镁砖(DM-98) 高纯镁砖(DM-96) 直接结合镁铬砖(DMC-12) 低气孔粘土砖(ZGN-42) 格子砖1#~7# 中段 下段 底层 顶层 上段
格子砖8# 中段 下段 底层
5.4.5小炉
表5.7小炉材料的选择
小炉底 小炉侧墙 小炉顶墙 喷嘴砖及间隙砖
33#电熔AZS砖(氧化法无缩孔) 33#电熔AZS砖(氧化法普浇) 33#电熔AZS砖(氧化法普浇) 33#电熔AZS砖(氧化法无缩孔)
5.5玻璃熔窑用隔热材料及其效果
表5.8玻璃熔窑用隔热材料
工作衬
部位
材质 硅砖 硅砖
窑顶 硅砖 硅砖 厚度 350 350 350 350
隔热材料品种
无 轻质硅砖 轻质硅砖 轻质硅砖 隔热砖
厚度
65 114 114 65
度/℃ 1600 1600 1600 1600
温度/℃ 285 219 191 142
非工作衬
窑衬工作面温
窑处工作面
热损失/KJ/(m2h) 25138 15315 11967 7152 硅砖 350 轻质硅砖 隔热砖 隔热砖
114 65 50 214 139 115 115 115
1600 1600 1600 1600 1600 1600 1500 1500 1600
117
319 177 179 440 135 110
5000 28553 9212 9413 57266 8151 5434 硅砖
上部结构锆刚玉砖
(胸墙)
锆刚玉砖 锆刚玉砖 锆刚玉砖
熔化池
锆刚玉砖 350 200
无 三层轻质砖 二层轻质砖
无 轻质高铝砖 轻质粘土砖 轻质粘土砖 再加一层粘土
砖
锆刚玉砖
窑底
粘土砖 锆刚玉砖
窑底
110 300 12
无 锆质捣打料 烧结锆刚玉砖 轻质砖
1300 230 13622
480 1400 171 7988
第六章 熔窑的设备选型
6.1倾斜式皮带输送机
用于将原料车间混合机房混合好的配合料输送到熔化车间窑头料仓,其输送配合料的优点:结构简单、使用时间长、事故少、易于维修、;在其进料口和出料口可采取收尘、密闭和隔断措施;输送平稳,可保证配合料的均匀度,自动化送料,减轻劳动强度,改善工作环境。
主要技术指标:皮带宽度:500(mm)
倾斜角度:15。
6.2毯式投料机
台数:1 主要技术指标:
投料量:300t/d~1100t/d; 料层厚度:100~500 mm; 投料机行程:160~260 mm; 投料机往复次数:15次/分;
附电机:7.5×2KW、重量:30t、电容量:15KW;
6.3熔窑助燃风机
选型:4-68NO.12.5C;
通过计算,熔窑所需助燃空气量为85819m3/h,根据公式;
Q=B1×Q0×760/Pa 式中:Q-风机风量(m3/h);
Q0-熔窑在超符合下需空气量(Nm3/h); B1-储备系数,一般为1.1-1.2; Pa-安装风机当地的大气压(mmHg); Q=1.2×38250×760/760=45900(Nm3/h);
所以,需要助燃风机3台。 风机的全压,按下列公式计算:
P=B2P0按
式中:P-风机风压(MP);
B2-储备系数,一般为1.1-1.2;
P0-熔窑在额定负荷下系统风全压(mmH2O柱); 通过热工计算,该熔窑在负荷下系统的全风压为140 mmH2O柱;
P=1.2×140=168(mmH2O)
Q=85819 m3/h,p=2501Pa,n=1120r/min,左90。 附电机Y280M-4,90KW,带减震支架和减震器
数量:2.6.4池壁用冷却风机
选型:4-72NO.16C Q=121270 m3/h,p=2117 Pa,n=800r/min,左右90。各两台 附电机Y315L-6,110KW,带减震支架和减震器 单重:3.4t、电容量:110KW、数量4台。
6.5碹碴离心风机4-72NO.16C Q=48797m3/h,p=1877 Pa,n=1250r/min,左右90各台
。附电机Y225S-6,30KW,带减震支架和减震器 单重:1.03t、电容量:37KW、数量4台。
6.6L吊墙离心风机9-26NO11.2D Q=19966m3/h,p=3225 Pa,n=960r/min,左90。两 附电机Y225S-6,30KW,带减震支架和减震器 单重:1.45t、电容量:30KW、数量2台。
6.7搅拌机
附电机:2×2.2KW,重量3.9t,电容量:4.4KW。
6.8燃油喷枪
带支架,金属软管,快速接头
燃油喷枪:Ⅰ型枪30套(备6套),Ⅱ型枪10套(备2套)。
6.9压缩空气罐C-3型
V=3 m3,p=0.8 Pa,重量1.06t,数量1个。 第七章 玻璃的形成及锡槽
玻璃液进入锡槽后,在拉边机的作用下拉薄或堆厚。浮法玻璃成型,于其它玻璃成型方法不同,它利用锡液与玻璃液之间性质的差异,由于玻璃液与锡液的互不浸润、密度相差很大及互不反应,使玻璃液浮在锡液的上面,玻璃液在锡液上自然摊开。锡液对玻璃液起到抛光和承托作用。玻璃液自然摊开厚度一般在6~7毫米。
由于锡液容易氧化,锡槽中必须充满还原气体,一般采用氮气和氢气,N2含量约90~97%,由于H2渗透性很强,容易产生气泡,所以H2含量约3~10%,锡槽外部用钢壳密封,气体保持微正压。不同的锡槽气压有所不同。
玻璃液经冷却部流出后,温度在1100℃左右,流经流道,流道有两种:英国皮尔金顿有限公司发明的PB法锡槽和美国匹兹保玻璃公司发明的LB法。PB法是窄道流,玻璃液由唇砖流进锡槽,锡槽进口是喇叭型,LB法则是宽流槽形式,主体结构是直通型。流道还有钢壳、流量闸、安全闸和盖板砖等结构,流量闸控制玻璃液流入锡槽的大小,一个固定产量的生产线其流量一般是固定的,闸板高度不变,它一般是石英砖的,如果闸板出现裂纹,将会影响玻璃的质量,在玻璃上产生气泡。安全闸板由特种钢构成,当锡槽出现大的故障时,可闸死安全闸板进行处理。在锡槽入口出有一对气封箱,通保护气体,防止O2进入锡槽。
玻璃液流入锡槽后,在自身重力和表面张力的作用下,在锡液上摊平,并通过拉边机拉薄或堆厚。拉边机采用全自动悬挂式拉边机。
成型阶段主要分为摊平区、徐冷区、成型区和冷却区。
摊平区
该区温度为1065~996℃,相应的粘度范围为102.7~103.2Pa·S。该区目的是使刚进锡槽的玻璃液能够充分摊平和抛光,达到自然平衡厚度。
徐冷区
该区温度为996~883℃,相应的粘度范围为103.2~104.25Pa·S。在摊平区达到自然厚度的玻璃带因受出口拉辊牵引力的作用,在该区开始纵向伸展。玻璃纵向伸展时将同时减少厚度和宽度,但后者比前者变化显著,因此在该区设置拉边辊,以保持宽度不变,使玻璃带的变化主要是减少厚度。在这一区将使厚度减薄一半,拉边辊的摆角为5°~10°。
成型区 该区温度为883~769℃,相应的粘度范围为104.25~105.75Pa·S。在该区根据生产需要,设置若干对拉边机,给玻璃带以横向和纵向拉力,使玻璃带横向拉薄,在玻璃带增宽的同时减少玻璃带的厚度。
冷却区 该区温度范围为769~600℃,相应的粘度围为105.75~1010范pa·s。玻璃带在该区不再展薄,而是逐步冷却,玻璃带出锡槽的温度为600℃左右。
锡槽中锡液的深度是不一样,而且还设了挡坎,避免锡液回流到880~970℃的高温区,使玻璃板产生波筋。在锡槽出口还经常要清灰,以免粘锡现象的产生。在过渡辊台区,设有SO2的管道,对过渡辊吹扫,二氧化硫对辊子有润滑作用,使玻璃不粘锡。
锡槽的关键部位是流道流槽,有收缩型、直通型、喇叭型三种结构。直通型结构简单,使用于较小规模的生产线;喇叭型结构复杂,玻璃液流通畅,没有死角,使用于生产规模较大的生产线;收缩型由于存在液流死角目前使用较少,这里采用喇叭型结构。流道流槽主要由安全闸板、流量闸板、流槽盖板砖、唇砖和水包组成。
安全闸板由镍铬耐热钢制成,当事故发生时,整体落下起到截流作用。流量闸板通过控制机构调节玻璃液流量,从而控制玻璃带宽度。流量闸板是常用、易损部件,所以选用耐侵蚀、抗热冲击性能好的熔融石英陶瓷。流道、流槽见图7.1。
安全闸板流量闸板流道盖板砖
图7.1 流道流槽结构图
锡槽内采用电加热,一般用硅碳棒或铁铬铝电热丝,保证玻璃液成型时的温度制度。锡槽的附属设备有直线电机、八字砖、挡边轮、冷却器、锡槽玻璃测厚仪和扒渣机。
锡槽主要控制参数:
流道温度:
1110~1115℃
入口温度:
1104℃
保护气体含氧量:
0 ppm
出口温度:
600±5℃
钢板最高温度:
120℃ 第八章 玻璃的退火及成品的装箱
玻璃从锡槽出来后,温度在600℃左右,由过渡辊送入退火窑进行退火。退火包括消除玻璃的暂时应力和永久应力,主要是永久应力。
永久应力是当高温玻璃经退火到室温并达到温度均衡后,玻璃中仍然存在的热应力,也称残余应力。玻璃中残余应力的减少或消除,只有将玻璃重新加热到开始塑性变形时才有可能。玻璃在此塑性变形时的温度范围,称为玻璃的退火温度范围。最高退火温度是指在此温度下保温2min,应力可以消除95%,一般对应于玻璃的转变温度;最低退火温度是指在此温度下保温2min,应力可以消除5%,一般对应于玻璃的应变温度。这两个温度构成了玻璃的退火温度范围[4]。
退火窑壳体采用全钢结构,由若干节组成,根据退火曲线纵向划分为十二个区:A、B
1、B
2、C、D、R
1、R
2、R
3、E、F
1、F
2、F3。
A、B和C区分别为退火窑的退火前区、退火区和退火后区,是退火的关键区,直接影响到玻璃的退火质量。这三区壳体采用隔热保温的形式,在窑内配置合理的加热冷却系统,进行横向分区控制,有效地控制玻璃板的冷却速度和横向温差。由于在这几个区,玻璃温度缓慢下降,所以为了防止玻璃炸裂,一般用辐射冷却即向退火窑通空气管,对窑内进行循环冷却。冷却在A区用顺流方式,在B和C区用逆流方式,这是根据玻璃退火速度决定的。
R区为热区循环直接冷却区,F区则为室风直接强制冷却区,在冷却时,保证玻璃的热应力小于玻璃的最大允许应力。
退火不好一般产生玻璃炸裂,有横炸和纵炸。当玻璃带边部一侧或两侧的压应力值太高时,或玻璃带存在某些弱点时(如结石,夹杂物),会产生横向炸裂。而当玻璃边部张应力值大于玻璃的拉伸强度时,玻璃总是首先在张应力处炸裂。一旦玻璃中存在有薄弱区域,就会产生纵炸。
玻璃从退火窑出来,温度在70℃左右,经全自动在线缺陷检测仪,对产品逐片检测,合格的切割后装箱,不合格的直接报废后进入碎玻璃库。
第九章 除尘脱硫工艺
目前环境保护越来越被大家重视,国家也制定了各项法规严惩。对于工厂每年的环境污染对国家交纳的税,
9.1 除尘工艺
玻璃原料的制备过程,有很多的灰尘,对人和机械影响很大,因此在原料车间设置了21套机械除尘系统,设置在原料的输送称量混合等各环节放散粉尘处,在浮法联合车间的熔化工段、切裁工段及碎玻璃系统共设置了12套机械除尘系统,主要设置在窑头投料及碎玻璃系统。除尘系统通过吸风使工艺设备内部形成负压,从而防止了粉尘外逸对人体产生的危害,使得室内操作环境达到国家卫生标准[5]。
除尘原理
含有悬浮尘粒的气体与水相接触,当气体冲击到湿润的器壁时,尘粒被器壁所粘附,或者当气体与喷洒的液滴相遇时,液体在尘粒质点上凝集,增大了质点的重量,而使之降落。
除尘系统选用脉充单机除尘器、脉冲扁布袋除尘器和倒料专用进料式振动清灰布袋除尘器。除尘器净化效率大于99%,具有设备体积小,清灰效率高的特点。
与除尘系统相配,设有压缩空气系统,用于脉冲除尘器的清灰和除尘管道的定期吹扫,保证除尘系统的清洁及管道畅通[6]。
9.2 烟气脱硫除尘
目前国内外的烟气脱硫方法有干法、半干法和湿法三大类。我国一般采用湿法,脱硫的方法有石灰石/石灰法、氨法、钠碱法、海水脱硫、氧化法等方法。
钠碱法脱硫除尘机理:
脱硫原理
湿法烟气脱硫的基本原理是利用SO2溶于水生成H2SO3,然后与碱性物质发生反应,在一定条件下可生成稳定的盐,从而脱去烟气中的SO2。当采用钠碱法时,吸收剂采用纯碱,整个反应过程如下:
Na2CO3+SO3→Na2SO4+CO2↑ Na2SO3+SO2+H2O→2NaHSO3
2NaHSO3+Na2CO3→2Na2SO3+H2O+CO2↑
脱硫除尘工艺流程由洗涤液循环系统、烟气脱硫除尘系统和废液处理系统三部分组成。运行过程如下:配制洗涤液时,人工将纯碱投入洗涤液循环池。洗涤液由洗涤液循环泵泵入脱硫除尘装置,出脱硫装置的洗涤液自流回洗涤液循环池。
第十章 技术经济评价
10.1 厂区劳动定员
表10.1厂区劳动定员
序号 一 (1) 1 2 3 4 5 (2) 1 2 3 4 5 6 (3) 1 2 3 4 二 (1) 1 2 3 4 5 6 7 8 (2) (3) 三 四 五 部门和工种 原料车间 粉碎工段 工长 粉碎工 吊车司机 筛分工 运碱工 混合工段 工长 混合工 皮带工 称量工 碎玻璃工 分析工 维修工段 工长 钳工 焊工 电工 熔制成型车间 熔化工段 工长 熔化工 测温工 投料工 上料工 运碎玻璃工 保窑瓦工 控制室人员 成型工段 退火工段 包装车间 总管理人员 厂非工作人员
一班
1 2 1 2 2 1 2 2 2 1 1 1 2 2 2
1 1 1 1 2 2 2 2 2 1 4
二班
1 2 1 2 2 1 2 2 2 1 1 1 2 2 2
1 1 1 1 2 2 2 2 2 1 4
三班
1 2 1 2 2 1 2 2 2 1 1 1 2 2 2
1 1 1 1 2 2 2 2 2 1 4
轮休
1 2 1 2 2 1 2 2 2 1 1 1 2 2 2 1 1 1 1 2 2 2 2 2 1 4
合计 100 32 4 8 4 8 8 36 4 8 8 8 4 4 28 4 8 8 8 48 4 4 4 4 8 8 8 8 8 4 16 10 10 192
合
计 10.2 产品设计成本编制
玻璃厂的产品成本,是反映工厂设计质量的一个重要指标。它可以反映所设计的工厂,将来在它的生产过程中原材料、燃料、动力的消耗水平,劳动生产率的高低,产品质量的好坏,设备的利用程度,资金运用是否恰当以及企业管理和生产组织的水平。因此,通过编制产品设计成本及对它的分析,可以检测所设计工厂的技术先进性和经济合理性,可以考核它是否符合预计的设计要求。
10.2.1主要设备明细
熔窑
国内先进水平
6365万元
锡槽
国内先进水平
8250万元
退火窑
国内先进水平
7240万元 10.2.2 辅助设施明细
辅助设施
金额(万元) 用途
动力车间
658.56
供应生产车间重油、蒸汽、压缩空气 机械设备
1502.6 汽保车间
683.5 其中:
房屋及建筑物
263.4
供应生产车间保护气体
机械设备
1273
原料车间
1738 其中:
房屋及建筑物
1510
供应生产车间合格的配合料
机械设备
327.6
铁路专用线
1408
运输原料及玻璃产品
合计
9367 900 t/d浮法玻璃建厂总投资:
31222万元 10.2.3 原料费
硅砂:
140元/吨
则一年所用的费用为: 140×243823 = 3413万元 白云石: 89.11元/吨
则一年所用的费用为: 89.11×64249 = 5725万元 石灰石: 60元/吨
则一年所用的费用为: 60×14056 = 84万元 纯碱:
1250元/吨
则一年所用的费用为: 1250×79687 =9960万元 芒硝:
476元/吨
则一年所用的费用为: 476×3564 = 169万元 煤粉:
600元/吨
则一年所用的费用为: 600×185= 11万元
10.2.4 辅助材料费
每年所用的费用为:1.5×5.8×2219112×0.2 = 386万元 10.2.5燃料费:重油3500元/吨,则一年的燃料费为:
123×3500×365 =15713万元 10.2.6 电费
电价每度为0.55元,每天用电为60000度,则每年电费为:
0.55×60000×365 = 1204万元 10.2.7 工资及工资附加费
设直接参见玻璃生产的人数为182人,平均工资为每月1500元,则每年总工资为:
182×1500×12 = 327万元
工资附加费为每人每月400元,则总附加费为:
182×400×12 = 87万元 10.2.8 车间经费
① 车间管理人员工资及工资附加费:车间管理人员约占生产人员的5%,平均每月工资为3000元,则他们每年的总工资为:192×5%×3000×12 = 34万元
② 个人劳动保护费
平均每人每年劳动保护费为2000元,则总保护费为:
192×2000 = 38万元 ③ 固定资产基本折旧费
固定资产价值为24561万元,年折旧率为6%,则基本折旧费为:
245610000×6% =1473万元 ④ 大修理费
全年大修理费=固定资产价值×年大修理率(5%)
245610000×5% = 1228万元 ⑤ 中小修理费
全年中小修理费=固定资产价值×年中小修理费(4%)
245610000×4% = 982万元 ⑥ 消耗材料费
全年消耗材料费=固定资产价值×年消耗材料费率(%)
245610000×6% = 1473万元 10.2.8 企业管理费
① 厂部非生产人员工资及工资附加费
工资平均每人每月1800元,总工资为20×1800×12 = 43万元 工资附加费为20×400×12 = 96000 元 ② 集体劳动保护费
全年集体劳动保护费=全厂职工总数×平均每人每年集体劳动保护费
=192×1000 = 192000 元 ③ 办公费、差旅费、文教费
20×1000 = 20000 元 10.2.9 水费
工人自设水源,因此只需供水系统之电费
1.5×2100×365×0.55 = 57万元 10.2.10运输费
设为工厂服务的汽车台数为20台,每台每年费用为20000 元,则总费用为
20×20000 = 40万元 火车费用:一年总费用815万元 10.2.11 其他费用
以上的费用和为380048006.27+312227500=69227万元 全年玻璃总产量=900×83%×365×40 = 10906200(重箱)
全年总费用之和除全年重量箱产量就得到一重量箱的设计成本,计算如下: 692275506÷10906200= 63.47 元
目前,平板玻璃市场价格为80元每重箱,设一年内价格不变,则
年利润 = (80-63.47)×10906200 = 18027(万元)
参考文献
[1] 林宗寿主编.无机非金属材料学[M] .武汉工业大学出版社,1998,1-6. [2] 张战营主编.浮法玻璃生产技术与设备[M].化学工业出版社,2005,56-58. [3] 樊德琴主编.玻璃工业热工设备及热工测量[M].武汉工业大学出版社,1990,123-125.
[4] 陈国平主编.玻璃的配料与熔制[M].中化学工业出版社,2007,10-15. [5] 陈国平主编.玻璃工业热工设备[M].化学工业出版社,2007,155. [6] 陈正树等编.浮法玻璃[M].武汉工业大学出版社,1997,25-26.
致
谢
大学生活一晃而过,回首走过的岁月,心中倍感充实,当我写完这篇毕业论文的时候,有一种如释重负的感觉,感慨良多。
毕业设计是我在大学里的最后一节课,肖秋国老师是我的最后一位老师,非常感谢肖老师在这期间对我的热心指导。肖老师渊博的专业知识,严谨的治学态度,精益求精的工作作风,诲人不倦的高尚师德,严以律己、宽以待人的崇高风范,朴实无华、平易近人的人格魅力对我影响深远。不仅使我树立了远大的学术目标、掌握了基本的研究方法,还使我明白了许多待人接物与为人处世的道理。本设计从选题到完成,每一步都是在肖老师的指导下完成的,倾注了肖老师大量的心血。在此,谨向肖老师表示崇高的敬意和衷心的感谢!
还要感谢在这大学四年中每一位教过我的老师,都是各科老师对我的精心栽培,使我在专业知识上打下了坚实的基础,所以面对问题时不慌不乱,都可以理性的解决。
最后感谢四年中陪伴在我身边的同学、朋友,感谢他们为我提出的有益的建议和意见,有了他们的支持、鼓励和帮助,我才能充实的度过了四年的学习生活。步入人生的下一个课堂。
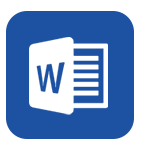