1.:金属硫化物形成的共熔体。例:Cu2S—FeS,铜锍;PbS—FeS,铅锍;Ni3S2—FeS,镍锍等。在火法炼铜中,锍、铜锍、冰铜均指Cu2S—FeS共熔体。
2.;用富氧空气或热风,将干精矿喷入闪速炉的反应塔空间,使精矿离子悬浮在高温氧化性氧流中进行氧化反应。
3.;将被炉料直接加入鼓风翻腾的熔池中,以液相为连续相,气液固三相接触良好,迅速完成熔炼过程。
4.;以火法炼铜为阳极,以纯铜片或钛板或不锈钢板作阴极,置于盛有含H2SO4的硫酸铜电解液中,通直流电,阳极粗铜溶解,阴极洗出金属铜,制备纯铜的工艺。
5.;以铅银合金板作阳极,压延铝板作阴极,电解硫酸锌溶液,铝板析出金属锌,阳极上放出氧气的过程。
6.;流态化焙烧,将流速增至超过临界值,一部分气体会形成气泡,使整个料层具有沸腾着的液体的状态,这种气—固接触的焙烧方法叫做流态化焙烧。
7.;加锌粉置换cu,cd在锑粉或其他含锑物料作为锑活化剂存在时,加锌粉置换除钴(机理:溶液中共存的杂志在锌粉表面上析出后或锌粉中含有的其他金属作为阴极,锌粉作为阳极,形成微电池,通过电化学作用,促使二价钴离子还原析出)
8.;pb被气流中的氧气或者是呈气泡状态高度分散于熔池中的氧气氧化产生金属铅与pbo,后者又被氧化为feo以及其他造渣组分造渣熔化,最终产出粗铅、含pbo高的炉渣以及含so2的咽气。
9.;在适宜的气氛中,将矿石或精矿加热到一定的温度,使其中的矿物组成发生物理化学变化,以符合下一冶金处理的工艺要求。(凝结成烧块)
10.;将处理好的矿石,精矿或其他原料,在高温下通过氧化还原反应,使矿物原料中金属组分与脉石和杂质分离为两个液相层即金属液和熔渣的过程。
11.黄渣:处理高砷锑炉料时,砷锑被还原为金属形态,与铜、铁等形成砷化物、锑化物,它们相互熔融,即为黄渣。
12.:Cu, Pb, Zn, Ni, Co, Sb, Bi,Cd, Hg, Sn,共十种。(比重较大的贱金属,密度都在6.0 g/cm3以上)
13.:为PbS、Cu2S、FeS、ZnS等硫化物的共熔体。当精矿铜含量较高,要求烧结块中适当提高残硫量,造锍使铜富集在铅锍中。锍是贵金属良好的捕集剂,铅锍的生成会导致进入粗铅的金银量降低。
14.电解精炼—阳极为粗金属,可溶性阳极;电沉积—不溶性阳极(如Pb-Ag合金);
一、炼铜:锍的吹炼吹炼的目的:除去冰铜中的Fe, S及部分其他杂质,得含铜约98%的粗铜.周期性作业:冰铜—造渣期—造铜期—粗铜。吹炼反应 造渣期:FeS + 3/2 O2 === FeO + SO2;FeO + 1/2 O2 === Fe3O4;2FeO + SiO2=== 2FeO.SiO2
吹炼渣:FeO—Fe3O4---SiO2, 造渣期结束后倒出。
造铜期:Cu2S + 1.5 O2 === Cu2O + SO2;Cu2S + 2 Cu2O === 6Cu + SO2 火法炼铜分造锍熔炼和吹炼两步工序进行的原因:1)铜在渣中的损失。2)高熔点物质四氧化三铁的形成
锍吹炼分段操作原因:当铁氧化完以后,可以进一步提高炉内的氧势,使
Ni3S2和Cu2S进一步氧化得到NiO和Cu2O,所以在铁接近快氧化完以后,应将形成的转炉渣从炉内倒出,以免大量的Cu2O与NiO进入渣中。
一般造锍熔炼的铜锍品味在0~70%范围内,在1250摄氏度下平衡Po2约为-3.5Pa。在这种熔炼条件下相应的四氧化三铁和氧化亚铜活度及哦啊西欧啊,不会产生析出的固体磁铁的麻烦问题。氧化亚铁活度取决于加入的二氧化硅的数量。因此可以多加些sio2。
E
生成:造锍熔炼过程中产生的部分FeO进一步氧化成四氧化三铁
危害:四氧化三铁是稳定的化合物,熔点高,密度大,它会增加炉渣的粘度和密度,使冰铜与炉渣不易澄清分离,增加铜在渣中的损失,又因冰铜和炉渣的密度小,固体磁性氧化铁易于沉降和堆积在炉床上,使熔炉的工作容积减小,生产能力下降
消除:合理控制冰铜品位,熔体中保留适量的FeS,减少Fe3O4的生成;添加SiO2促进Fe3O4还原和造渣;维持较高的熔体温度,加速还原反应进行,增大Fe3O4在液体炉渣和冰铜中的溶解度,从而降低固体Fe3O4的生成量。 阳极杂质在电解中的行为杂质总量约为:0.3--0.8% ,分别为O, S, Au, Ag, Pt, Se, Te, As, Sb, Bi, Ni, Fe, Zn, Pb, Co等,分为四类:第一类:正电性金属或化合物,不溶解,进入阳极泥。如O, S, Au, Ag, Pt, Se, Te。第二类:Pb, Sn:发生电溶解,续之以硫酸盐沉淀。第三类:负电性金属,溶解进入溶液。如Ni, Zn, Fe等。Ni溶解进入溶液的量与阳极含氧有关。第四类:电位与铜相近的元素,As, Sb,Bi。既有可能在阴极析出,又能形成“漂浮阳极泥”,即As, Sb, Bi溶解在电解液中,达到过饱和,以SbAsO4, BiAsO4等沉淀,这类沉淀为絮状物,会粘在阴极,影响其化学成分和外观质量。
二、直接炼铅工艺 QSL
硫化铅精矿直接炼铅:原理,反应:PbS+O2=Pb+SO2;PbS+3/2O2=PbO+SO2;高氧位2PbO+PbS=3Pb+SO2;低氧位;在一座炉内控制不同氧位熔炼区:高氧位,产出低硫粗铅还原区:低氧位,使渣中氧化铅还原,降低渣含铅。 熔炼段维持1373 K以下温度:(1)减少铅的挥发;(2)高PbO炉渣对耐火材料有强烈的腐蚀性。
生产过程:
氧化段:炉料加入后,在炉渣-金属-气体乳状熔体中发生反应,生产Pb和PbO,放出热量,实现自热熔炼,粗铅含S 0.3-0.5%,粗渣含铅30-40%。氧化段温度1150oC.还原段:粗渣从隔墙下流入到还原段。粉煤(或天然气)和氧气喷入产生CO和H2,使高PbO炉渣在1250 oC被还原。与氧化段硫化物氧化速度比较,还原速度较慢,还原段长度约为氧化段的2倍
三、湿法炼锌:湿法:焙烧--浸出--净化--电积;硫化锌精矿直接氧压浸出--净化--电积。
(流态化焙烧ZnS转变为ZnO)——(连续复浸出流程:第一段为中性浸出目的是除了使部分锌溶解外,另一个重要目的是保证锌与其他杂质很好的分离,第二段为酸性或热酸浸出PH5~5.2,目的是尽量保证焙砂中的锌更完全的溶解,同时也要避免大量杂质溶解。终点酸度控制在1~5g/L硫酸){渣含锌很高20%,主要是铁酸锌,渣不能废弃,要活法冶金将锌还原会发出来与其他组分分离,然后将收集到的粗氧化锌粉进一步湿法处理}增加高温、高酸浸出,降低酸浸中尚未溶解的铁酸锌及锌化合物,提高锌浸出率,回收油
价金属——浸出液净化锌粉_锑盐法,锌粉-砷盐法,锌粉-黄药法等——锌电积:铅银合金板作阳极,压延铝板作阴极。直流电,阴极析出金属锌,阳极放氧气。
四、铁酸锌问题
浸出渣的处理:
常规流程:火法还原挥发得粗氧化锌,再单独浸出,浸出液返中浸。流程复杂、能耗高,污染环境、投资大。
热酸(高温高酸)浸出:铁溶解进入溶液,要解决从高铁溶液中分离铁的问题。 铁酸锌的溶解 热力学分析:
(1)温度升高,ZnO.Fe2O3稳定区扩大,表明从热力学上讲,温度升高不利于铁酸锌的分解。
(2)In2O3, Ga2O3比锌更难浸出。提高铟、镓浸出率,要提高酸度。 动力学研究:
(1)反应的活化能:E = 58.576 KJ/mol, 温度升高10K,反应速度约提高2倍。
(2)铁酸锌的溶解符合:化学反应控制的收缩未反应核模型:1 - (1-)1/3 = Kt, K = 4.5710-3
浸出率;K 表观速率常数;t 浸出时间
(3)动力学研究表明,为了使铁酸锌以较快的速度溶解,浸出必须采用高温,热力学研究表明,高温下需要高的酸度。实际高温高酸浸出条件:温度368--373K;残酸浓度:40--60 g/L H2SO4; 时间3--4小时。
高压SO2还原浸出铁酸锌
五、反射炉 优点:对原料适应性强;炉子结构简单,对耐火材料要求不高;对自控水平,操作水平要求较低;渣含铜低,不需处理可直接弃去。 缺点:烟气SO2浓度低;仅0.5-2%难于回收利用,环境污染严重;热效率低,能耗高;冰铜品位低,吹炼负荷大;生产率低。 反射炉的发展趋势: 改良;新技术取代。
• NORANDA法优缺点对原料适应性强,备料过程简单,烟尘率低,可产高品位冰铜;
• 辅助燃料适应性大。富氧熔炼基本为自热过程,一般补充燃料率仅为2-3%。 • 炉子无水冷设施,炉体散热小,但炉子寿命较短,现经改进,修炉一次可连续生产400天以上;
• 炉体可转动,导致炉口与烟罩密封不好,漏风大,烟气量大。
• 直收率低,渣含铜高,要选矿处理以渣精矿返回熔炼。
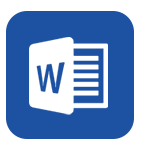