1我国新型干法水泥生产技术的现状及发展新型干法水泥生产技术的问世与发展,为水泥生产线大幅度提高产量和降低能耗提供了技术保障。1970年,我国就开始了对新型干法水泥生产技术的研究,几乎与德国和日本在同一个时期起步。在研究、引进、消化国外先进技术的基础上,我国先后建成了一批700~4000ffd不同规模的现代化水泥生产线,为新型干法水泥工艺技术和装备的国产化奠定了坚实的物质基础。20世纪年代中期,我国天津、南京、成都、合肥四大水泥工业设计院对新型干法水泥生产技术展开了“优化设计、低投资、国产化”工作。1993年,吉林双阳水泥厂2000ffd水泥熟料生产线建成投产,投产后很快实现达标达产,标志着我国自主开发的预分解窑技术已经成熟。20世纪初,技术水平更高的5000ffd熟料生产线又开发成功,掀起了我国新型干法水泥生产线的建设新高潮,新建生产线一般都能在很短的调试期后达标、达产。到目前为止,我国已实现了4000~6000t/d熟料新型干法水泥生产线成套装备基本自给,规模生产线的装备国产化率达到90%,装备的性能也达到了国际先进水平。其中海螺建成的4条日产万吨生产线已经成功投产运行多年。2008年末,我国已经建成投产的新型干法窑934条,熟料产能达7.8亿吨,新型干法水泥占到了总产量的62%。2008年已经开工建设但尚未投产的还有近100条生产线,到2009年末预计新型干法窑的熟料产能接近9亿吨。2000~2500L/d和4000~5000t/\'d预分解窑目前是我国新型干法水泥生产线的主流窑型。2008年我国2000~2500∥d生产线323条,生产能力占总产能的31.61%;4000~5000L/d生产线221条,生产能力占总产能的43.5%;6000~6500ffd生产线14条,生产能力占总产能的3.49%;7200L/d以上生产线6条,生产能力占总产能的2.26%;·1·
Null 700~1800t/d的小型新型干法生产线345条,生产能力占总产能的近16%。1.1新型干法水泥生产技术的现状新型干法水泥生产技术代表着当今世界水泥生产的潮流,其生产能力已达到世界水泥生产能力的60%以上。20世纪80~90年代中期,我国引进一批3000t/d、4000t/d生产线,与此同时,进行国产化4000t/d生产线装备的开发。冀东二线国产化4000t/d生产线的成功运用,不但降低了工程投资,而且为更大规模的国产大型化装备的开发积累了经验。20世纪90年代以来,一些大型化生产线相继在国内建成投产。如山东大宇7200t/d熟料生产线及华新5000t/d、京阳5500t/d生产线。这些生产线以其生产稳定、产品质量好、运行成本低,在国际、国内的产品市场占有了一定的份额,并显示出强劲的市场竞争力。这些生产线的投产和稳定运行,标志着我国水泥装备现代化、大型化技术已成熟。1.1.1原料均化技术新型干法水泥生产产品质量得以保证的关键是原料均?1.1.1原料均化技术新型干法水泥生产产品质量得以保证的关键是原料均化技术的应用。已投入应用的技术装备如下:(1)矿山设计采用矿化模型系统(CQMS)。以此制定的搭配开采方案保证了所开采的矿石中的主要成分的稳定性,同时也为低品位矿石的有效利用创造了条件。(2)原料预均化技术已在我国得到广泛应用,其工艺与设备13益发展和完善;预均化效果不断提高;堆、取料各个环节实现了自动控制;减小了原料的短期和长期波动;堆场占地面积逐渐减小;节约了大量天然资源和能源等。开发出的圆形、长形原料预均化堆场,可根据建设条件灵活运用,设置具有良好均化效果的原燃料预均化堆场。国内已具备提供满足不同生产规模的预均化堆场技术装备的条件(圆形堆场直径可达1lOm;矩形堆场跨度.2.
Null 达50m,可满足2000~10000t/d级规模生产线的需要)。(3)配置计量精确的块状和粉状物料计量装置,并通过质量控制系统及时调整各种原料的喂料比例,确保出磨生料和水泥的合格率。(4)生料均化技术由间歇式空气搅拌库逐步发展到投资省、操作简单、电耗低的连续式均化库。采用高均化效果、低耗电和高卸空率的生料均化库(H值达8以上,电耗约0.25kW-h/t,卸空率大于98%),确保人窑生料的合格率。1.1.2预分解窑节能煅烧工艺和技术装备(1)成功研发出具有自主知识产权的新型高效、低阻、低NO。的预分解系统,主要技术指标达到国际先进水平,全面提升了中国新型干法水泥熟料烧成系统的国产化、大型化技术水平。通过系统实验研究,开发了系统压损在4000~4800Pa的高效、低压损的五级旋风预热器系统。目前已投人生产运行的有2000t/d、2500t/d的单系列和2500t/d、3200t/d、5000t/d的双系列。同时,预热器内筒、锁风阀、耐火衬料等的改进确保了熟料煅烧系统的可靠性和热耗的降低。(2)通过对各种燃煤(包括无烟煤、低热值煤和含高硫煤等)的燃烧特性及在窑炉工况条件下的燃烧机理研究和工业实验,开发出实用可靠的适合于燃料特性的煅烧技术和装备,为资源的综合利用和降低运行成本创造了条件。该项技术目前已得到推广。(3)为满足不同规模生产线建设的需要,开发设计了回转窑系列产品,包括二支承和三支承的回转窑,其中三支承窑的最大规格为4,5.0mX74m,可满足5000~6000t/d规模生产线的需要。(4)在吸收国外先进技术的基础上,中国已自行开发出了第三代控制流篦式冷却机。采用空气梁供风、高阻力篦床、入料均匀分配、厚料层、脉冲分风及合理的配风等新技术,已广泛地用在13产700~5000t/d熟料生产线上。解决了厚层篦式冷却机冷风不易均匀透过料层的技术难点,冷风和高温熟料进行激烈的换·2·
Null 热:一方面有利于熟料快速冷却;另一方面提高了二次、三次风温度,篦式冷却机的热效率已提高至74%以上,且运转率大幅度提高。开发并推广了第三代TC系列空气梁熟料篦式冷却机。该技术使熟料冷却风量下降至1.6~1.8m3/kg熟料,热回收效率提高到74%以上,设备可靠性确保了烧成系统的运转率在90%以上。(5)开发了可适应不同性能材料(包括无烟煤)燃烧的燃烧器系列,一次风量降至10%以下,具有对燃料适应能力强、调节灵活、有利于保护窑皮及延长衬料使用周期等显著优点。燃烧器的发展趋势是紧跟当今世界工业发展的两大主题——节能和环保,主要体现在:一次风量小,可烧劣质燃料,耐磨损、耐变形,低NO。排放。国内已开发应用了三风道、四风道的多通道煤粉燃烧器,以及燃烧两种以上燃料的五风道的多通道燃烧器。(6)不带补燃炉的纯低温余热发电技术已取得突破,并已在多家水泥厂应用。水泥窑纯低温余热发电,完全利用水泥熟料生产过程中产生的废气余热作为热源,整个热力系统不燃烧任何一次能源,可有效地减少水泥生产过程中的能源消耗,具有显著的节能效果。同时,废气通过余热锅炉降低了排放的温度,还可有效地减轻水泥生产对环境的热污染,具有显著的环保效果。1.1.3节能粉碎粉磨技术与装备(1)粉碎技术与装备。原料的单段破碎工艺具有破碎比大、物料不易堵塞、维修方便、电耗低、工艺流程简单等优点。经过多年的努力,目前已开发出台时产量从80~1800t/d的不同形式的石灰石单段破碎机,并已投入运行。适合于黏性物料破碎的齿辊式破碎机的最大产量已达350~400t/d;破碎高磨蚀性和难破碎性物料的破碎工艺和技术装备也已成熟,可满足工程建设需要。(2)原料烘干粉磨系统。根据原料的易磨性、磨蚀性和烘干的不同要求,分别开发了管磨、辊磨系统。1)带组合式高效选粉机的钢球墨系统(管磨系统)对原料的易磨性和磨蚀性的适应性较广,运行可靠。新近开发的TLS型组·d.
Null 合式高效选粉机因其分离效率高、产品细度调节灵活、结构紧凑等优势,使系统产量提高,电耗降低,同时简化了流程,降低了基建投资。新近开发的管磨机采用了双滑履支撑,配用了先进的边缘滑动装置。其规格已能满足3000t/d和5000t/d级生产线的要求。2)辊式磨系统。在原料适合的前提下,与管磨机相比,辊式磨具有流程简单、节电和烘干能力强等优点。近年来,随着材料工业和机械加工工业的发展,科研设计和装备制造单位在消化吸收国际先进技术的基础上开发出国产化的新一代辊式磨(改善磨辊结构,加快磨盘转速,采用先进可靠的液压装置,提高磨辊压力,配置高效选粉机,采用外循环设计),使磨机的可靠性和易损件使用寿命得以保证(在正常原料条件下辊套和衬板的寿命可达一年半以上),节电效果进一步提高。生料制备已由过去球磨机为主逐步发展为高效率的立式磨为主,生料制备电耗明显降低。目前,国内已具备提供满足5000t/d级以下规模水泥生产线的生料和煤粉制备用的辊式磨系列产品的条件(对于5000t/d级的原料磨需引进部分关键部件)。(3)水泥粉磨系统:1)管磨闭路系统。由高效笼型选粉机、高效布袋收尘器和管磨机组成的水泥粉磨系统,被认为是高新技术对传统流程进行改造的最好实例之一。系统按生产ISO标准水泥产品的要求进行配置,管磨机采用了双滑履支撑,并配用了先进的边缘转动装置;第三代笼型高效选粉机的选粉效率在80%以上;高效布袋收尘器确保在进口含尘达8009/m3的条件下净化气体含尘小于50mg/m3。系统在运转可靠的前提下,实现了高产低耗。目前已投入运行的系统能力为40~lOOt/h(以P042.5计)。2)辊压机系统。辊压机作为预粉磨或半终粉磨过程的主机装备,其技术可靠性和节电优势已为广大用户所认知和接受。与管磨系统相比其粉磨电耗可降低25%。近年来,国产辊压机解决了机体振动、辊磨面损大、寿命.5·
Null 短、自控不协调、液压系统调节不灵活等技术问题,并已形成系列,最大规模能满足半终粉磨系统160t/h产量的配套要求。随着挤压粉磨系统工艺与设备的不断完善、不断大型化,已经形成以辊压机为中心、各种新型设备组合成为优势互补的多种粉磨新工艺,如预粉磨系统、混合粉磨系统、联合粉磨系统、半终粉磨系统等。其技术水平达到了20世纪90年代末期的国际先进水平。挤压粉磨系统已成为水泥粉磨的首选方案,在全国普遍推广应用,最大规格已能满足与5000t/d熟料新型干法水泥生产线配套。3)钢球磨机大型化及其匹配设备的优化改进和提高,不仅提高了单机生产能力,满足了水泥生产线单线规模不断扩大的需求,而且有效提高了粉磨效率。4)在球磨机开流粉磨水泥的系统中,采用微型研磨体的高细高产磨得到广泛推广。高细高产磨技术在磨机仓位设计、磨内筛分、研磨体配比等方面已形成了自己的特色,开辟了广泛的应用市场。在水泥、超细矿渣、超细粉煤灰等生产中,这种开流粉磨系统已经可以达到或接近闭路系统的效果,而投资和运行成本则可以大幅度降低。5)采用新型耐磨材料,改善磨机部件材质,不断提高磨机综合效率和使用寿命。1.1.4自动控制技术新型干法水泥生产工艺线整个流程有近1000台电动机和阀门,数百台机械设备以及上千个开关量,数百个模拟量测点和数十个调节回路。为保证稳定运行和优良的产品质量,需要通过自动控制来完成。近年来,我国广泛采用国际上先进的计算机控制技术、通信技术和图形显示技术,采用分散控制、集中管理的集散型控制系统(DOS),并开发运用了工厂生产管理信息系统(PMIS),实现了系统的可靠、安全和实用的目标。·6- Null 1.1.5环境保护新型干法水泥生产过程作为几乎无污染和生态友好的实践,近年来受到了社会的普遍关注。作为传统水泥生产的主要污染源(粉尘、废水和废气)已得到系统的治理:粉尘排放远低于国家标准允许的排放限度;废水实现了零排放;有害气体(NO;)的排放也得到了有效的控制。水泥工作者们经过长期不懈努力,研制出的环境保护工艺与设备已完全能够满足粉尘以及SO:、NO。达标排放。如:北京水泥厂的2000t,/d熟料新型干法水泥生产线,被国家环保总局确定为“环保教育基地”,国外一家杂志社载文称之为“生态友好型水泥厂”。都江堰拉法基水泥厂的4000t/d熟料新型干法水泥生产线,全厂85个粉尘排放点粉尘排放浓度全部低于20mg/m3,达到了欧洲标准。新型干法水泥生产在最大限度利用工业废渣作为原燃料的同时,在利用工业和生活垃圾等方面具有极大的发展前景。回转窑焚烧可燃废弃物和有毒有害物、工业及生活污泥的研究已取得很大进展,其技术已在几家水泥厂应用,北京水泥厂的焚烧有毒有害废弃物示范工程已经完成。1.1.62500t/d和5000t/d级生产线2500t/d和5000t/d级生产线技术装备基本配置见表1—1。表1-12500t/d和5000t/d级生产线技术装备基本配置┏━━┳━━━┳━━━━┳━━━━━━━━━━━━━━━━━┳━━━━━━━━━━━━━━━━━┓┃┃┃┃2500t/d生产线┃5000t/\'d生产线┃┃序┃车间┃主机┃┃┃┃┃┃┣━━━━━━━━┳━━━━━┳━━╋━━━━━━━━┳━━━━━┳━━┫┃┃┃┃┃能力┃数┃┃能力┃数┃┃号┃名称┃名称┃性能指标┃┃┃性能指标┃┃┃┃┃┃┃┃/t.h一1┃量┃┃/t-h一1┃量┃┣━━╋━━━╋━━━━╋━━━━━━━━╋━━━━━╋━━╋━━━━━━━━╋━━━━━╋━━┫┃┃石灰┃┃进料量:
Null 续表1—1┏━━┳━━━┳━━━━━┳━━━━━━━━━━━━━━━━━━━━┳━━━━━━━━━━━━━━━━━━━━┓┃┃┃┃2500t/d生产线┃5000t/d生产线┃┃┃┃┣━━━━━━━━━━━┳━━━━━┳━━╋━━━━━━━━━━━┳━━━━━┳━━┫┃序┃车间┃主机┃┃能力┃数┃┃能力┃数┃┃号┃名称┃名称┃性能指标┃┃┃性能指标┃┃┃┃┃┃┃┃/t·h一1┃量┃┃/t.h一1┃量┃┣━━╋━━━╋━━━━━╋━━━━━━━━━━━╋━━━━━╋━━╋━━━━━━━━━━━╋━━━━━╋━━┫┃┃窑尾┃┃┃┃┃┃┃┃┃9┃废气┃电收尘┃380000m3/h┃┃1┃620000m3/h┃┃1┃┃┃处理┃┃┃┃┃┃┃┃┣━━╋━━━╋━━━━━╋━━━━━━━━━━━╋━━━━━╋━━╋━━━━━━━━━━━╋━━━━━╋━━┫┃┃┃辊压机┃辊压机TRPl40/100┃┃1┃辊压机TRPl40/100┃┃2┃┃┃水泥┃┃┃┃┃┃┃┃┃┃┣━━━━━╋━━━━━━━━━━━╋━━━━━╋━━╋━━━━━━━━━━━╋━━━━━╋━━┫┃10┃┃┃管磨:钟.2m×lOm┃┃┃管磨:4,4.2m×lOm┃┃┃┃┃粉磨┃水泥磨┃┃120┃1┃┃120┃2┃┃┃┃┃比表面积:340m2/kg┃┃┃比表面积:340m2/kg┃┃┃┗━━┻━━━┻━━━━━┻━━━━━━━━━━━┻━━━━━┻━━┻━━━━━━━━━━━┻━━━━━┻━━┛1.2新型干法水泥生产技术的发展方向“十一五”规划明确提出:全面落实科学发展观,建设资源节约型、环境友好型社会;大力发展循环经济,加强资源综合利用,全面推行清洁生产,形成低投入、低消耗、低排放和高效率的节约型增长方式;加大环境保护力度,降低污染物排放,切实保护好自然生态。为此,中央提出了“十一五”期间国内生产总值单位能耗降低20%左右,主要污染物排放总量减少10%的约束性指标。因此,认真贯彻落实科学发展观,充分合理利用资源,最大限度地降低资源能源消耗,减少污染物排放,满足与社会协调发展的生态要求,尽快实现走新型工业化的目标,推动水泥行业实现可持续发展是摆在水泥从业者面前的重要课题和历史任务。水泥工业是产量大、能耗高的工业。2006年中国水泥产量为12.4亿t,约消耗能源1.5亿t(标煤),占全国能源消费总量的7%左右。当然能耗高的原因,大量落后生产工艺的存在是关键。中国目前还有一半左右的水泥是由国际上业已淘汰的立窑等生产的,其单位能耗比新型干法每吨水泥要高约30。35kg(标煤)。历史造成的结构矛盾,需要加快调整步伐。就新型干法本身来说,我们和世界先进水平相比,单位熟料热耗高250.8kJ/kg(60kcal/kg)左右,单位水泥电耗高lOkW·h/t左右,相当于全年·0.
Null 多消耗420万吨标煤和62亿度电。这一数字也相当可观。就技术装备的差距来说,主要体现在粉磨和烧成两大领域。粉磨领域发展的现状和趋向是料床终粉磨代替了传统的球磨,其代表是立式辊磨,从而大幅度的节电。目前世界上出现了不少无球磨的水泥工厂。烧成领域发展的现状和趋向是:以无漏料新型篦式冷却机、二档短窑、低NO。型分解炉和6级高效预热器系统的新技术代替了原有的系统,达到了进一步大幅度节能、生产稳定可靠、提高对原燃料适应性的效果。为此,必须加强工程技术的研究,加强工艺技术、信息化建设和重大装备的开发和创新,加速水泥生产生态化装备技术的开发,加强企业管理和人才培养,不断推行优化设计。今后的主要研究课题如下:(1)运用CFD高新技术(即计算流体动力学)于新型干法水泥技术研究领域中,如燃烧、分解、预热、烘干、煅烧、冷却、两相流输送、分离、分级、破碎、粉磨、选粉等。并借此技术对新型干法水泥生产技术进行优化、创新开发以及综合性能评估、问题诊断等。(2)加强原料均化技术的研究,进一步扩大低品位原料和工业废渣的应用。进一步强化从原料矿山开采到原料粉磨前均化的措施和手段,减少磨后生料的均化和储存的投资。(3)进一步提高预热预分解系统的技术性能,对于5000t/d及以上规模的烧成系统,使熟料热耗降至2926kJ/kg(700kcal/kg),并进一步降低电耗,开发高性能回转窑和新一代熟料冷却机等关键设备。(4)加快利用新型干法窑处置城市混合型废弃物技术及装备的研究和开发。充分发挥和扩展水泥工业对其他工业产生的废渣、废料、有毒有害废弃物以及城市生活垃圾等利用降解的环保功能,发展循环经济。由于现代水泥工业具有独特的利废功能,可以协助全社会利用和消纳各种废料、废渣和城市生活垃圾等,促进循环经济。1)水泥工业可以消纳的废弃物种类很多,适应范围广:固体、液体或膏体的;块状的或散状的,一般的、危险性的或·】0·
Null 有毒的废弃物等,各种废弃物都可以在水泥窑或预分解炉内燃烧殆尽;2)按照各种废弃物的性能特点,可以分别用作水泥工业的混合材,替代原料或替代燃料,使之物尽其用;3)水泥工业对废料的消纳量很大,因为水泥窑本身的生产量就很高;4)在消纳回收利用废弃物的同时不会影响到水泥和混凝土的正常性能与质量,不会影响水泥生产操作的正常运行,水泥窑对各种废物有很强的适应能力;5)因为水泥窑内温度高(1600\':C),热容量大,热惯性稳固持久,各种有害物质在高温区内的停留时间长(5~15s),所以均能被彻底分解烧尽,窑尾废气中不含二n恶英等,确保环境安全;6)废料燃烧后的残渣,如果其中含有某些重金属等有害物质,这些残渣也都全部固熔在水泥熟料矿物的晶格之中,在水泥混凝土中不能再逸出或析出,不会造成二次污染,没有隐患,环保安全;7)可以利用全国已有的600多台2000t/d以上的新型干法水泥窑,添置少量的废物预处理设施,即发挥其既生产水泥又妥善利用和消纳废物的双重功能,远比新建废物填埋场或焚烧厂更经济更安全。发达国家利用废弃物生产生态水泥已有成熟的经验。在日本40多家水泥企业中,50%以上处理各种废弃物。在欧洲水泥生产者联合会所属的水泥厂中,每年焚烧100万吨有害废物。美国的大部分水泥厂都利用废料煅烧水泥,技术成熟,应用普遍。人们已经认识到,水泥回转窑在处理有毒危险废弃物方面比焚烧炉更有优越性,主要是利用可燃性废弃物(包括固态、液态、气态)代替部分或大部分燃煤和燃油煅烧水泥,既处理了废料,又节约了能源。所以充分发掘和扩展水泥工业其特有的环境保护功能,真正把水泥工业建设成绿色环境保护、可持续发展的产业,发展循环经济是我国水泥工业的发展方向。(5)加大力度进行生料辊式磨系统以及用于水泥预粉磨、终粉磨的辊压机和辊式磨系统的开发和推广应用,使水泥综合电耗降至90kW·h/t以下(以P042.5计)。加速超细粉磨装备技术的开发,最大限度地利用高炉炉渣、粉煤灰等工业废渣用作水泥混合材。-1】- Null (6)加强对工艺装备过程控制智能化及优化控制软件的研究开发,最大限度地提高生产线的质量和产量,降低能耗,提高设备运转率。进一步提高网络技术在生产系统自动化的应用及优化工艺过程企业管理中的应用。(7)研究开发效率更高的除尘装备和降低NO。、SO:、CO:等有害气体的工艺措施和技术装备。(8)加大对预热器、篦式冷却机废气余热发电技术的开发,使废热回收发电量达到35kW·h/t熟料以上,减少CO:排放,发展循环经济,在节能减排上做出应有的贡献。(9)进一步做好个性化设计,力求以最低的投资、最小的资源消耗和最低的生产成本,最大限度地满足市场的需求。(10)随着一批大型新型干法水泥生产线的建设,我们需要花大力气研究开发设备的材料和制造加工问题。现实告诉我们,大型生产线国产化的难点还在于一些大型机械设备的制造加工和材料加工上,这是一个瓶颈,不容忽视。开展装备专用材料的应用研究,以提高装备的性能,如高性能的耐磨金属材料、金属陶瓷材料、耐火材料和隔热材料等。(11)针对劳动生产率不高的现状,要加大技术装备的开发和应用,如物料储存输送、水泥成品包装、袋装及散装发运等。世界水泥技术的发展趋势是以节省资源、节约能源和环境保护为中心,进行清洁生产和高效集约化生产,加强水泥生态化技术和设备的研究、开发,逐步减少天然资源和天然能源的消耗,最大限度地减少环境污染,最大限度地接收、消纳工业废弃物和城市生活垃圾等,使水泥工业达到与环境友好、和谐、共存。新型干法水泥生产技术代表着当今世界水泥生产的潮流,发展新型干法水泥是实现中国水泥工业现代化的必由之路。虽然中国先进的新型干法水泥生产线与国际先进水平已经相当接近,但从整体来看,还存在较大差距。为了使中国新型干法水泥生产工艺与设备的主要技术经济指标逐步赶上甚至超过国际先进水平,同时在环境保护和生态建设方面逐步达到国际先进水平,我们还需要不懈努力。.12·
Null 1.3新型干法水泥生产线工艺流程新型干法水泥生产线工艺过程与其他生产方法相比基本上是相同的。它包括原燃料进厂、原燃料破粉碎、生料制备、熟料煅烧、水泥制成及发运等。典型的新型干法水泥生产线工艺流程如图1-1所示。图1-1典型的新型干法水泥生产线工艺流程·13·
Null 2新型干法水泥生产线的窑炉系统新型干法水泥生产技术是20世纪50年代发展起来的新技术。日本、德国等发达国家以悬浮预热和预分解为核心的新型干法水泥熟料生产装备已达95%以上。我国于1976年投产第一台悬浮预热器及预分解窑,发展至今已经形成了设计、制造、配套、施工的完整装备体系,基本实现了设备国产化。2008年中国水泥产量为13.9亿吨,其中新型干法水泥约8.6亿吨,水泥综合能耗为138kg(标煤),年消耗能源1.88亿吨(标煤)。新型干法水泥生产是公认的低能耗生产技术,比传统回转窑和立窑每吨水泥平均低约30~35kg(标煤)。但在我国,目前国际上普遍采用的新型干法生产工艺的产量仅占62%,节能的任务繁重。而就新干法技术装备本身来说,我国与国际最先进水平还有一定差距。水泥熟料烧成系统是水泥生产过程的中心环节,也是大量消耗燃料的工序。一方面,因为硅酸盐水泥主要由熟料所组成,熟料的煅烧过程直接决定水泥的产量和质量、燃料与衬料的消耗以及窑的安全运转。另一方面,水泥工业是消耗能源较多的产业,而在水泥生产中,熟料煅烧要占全部能耗的80%左右,因此了解并研究熟料的煅烧过程是非常必要的。新型干法水泥生产线的窑炉系统,是熟料燃烧过程发生的主要场所,研究它们的结构特点对降低能耗、提高生产效率和产品质量都有很大的意义。图2.1为五级预热窑外分解窑窑炉系统工艺流程与技术参数示意图。新型干法水泥生产线的窑炉系统,主要由预热和预分解、回转窑煅烧以及水泥熟料冷却三大系统构成。预热预分解系统主要完成水泥生料的预热和石灰质原料的预分解过程,水泥熟料的烧成及其冷却过程分别发生在回转窑煅烧和水泥熟料冷却系统·14·
Null 分解率图2-1窑外分解窑(五级预热器)工艺流程与技术参数(日产3300t/d熟料,耗热3000kJ/kg熟料)1一分解炉(燃料60%);2~回转窑(燃料40%);3一冷却机;4一冷却机三次风人分解炉;5一风机;6一各级旋风预热器G一气体量,m2/kg熟料;气一气体温度,℃;■一物料温度,℃;p一负压,mmH20中。窑炉系统中主要发生着燃料的燃烧,物料与空气之间的剧烈的热交换,甚至某些有害元素的挥发和冷凝等过程。针对不同使用条件下的部件,在耐火材料的配置上也存在着显著的差异,要想准确地确定耐火材料的合理配备方案,有必要系统地了解新型干法水泥生产线窑炉系统的构成及各主要部件的热工特点、工作原理及使用条件,为经济有效地完成耐火材料的配置提供支持。2.1悬浮预热器和预分解窑炉窑尾预热器及预分解炉是在传统的回转窑之前增加一个燃烧及热交换环节,一方面对生料进行预热;另一方面可以使其中·15·
Null 的碳酸盐矿物产生约85%的分解率,它们的出现是新型干法生产最有意义的发展。预热器的特点在于高度分散的生料在悬浮状态下进行气固热交换,具有传热迅速、热效率高、单位容积大、热耗低等优点,而预分解炉的出现则大大提高了系统的热效率和窑系统的产量,推动水泥生产过程朝着优质、高效、低耗、符合环保要求和大型化、自动化的方向发展。新型干法水泥生产技术的发展就是悬浮预热器及预分解技术的发展,其第一阶段是20世纪50年代初到70年代初,悬浮预热技术诞生和发展的阶段;第二阶段是20世纪70年代初至今,预分解技术诞生和发展的阶段。可以说预热器及分解炉的发展推动着新型干法水泥生产技术的发展,也是新型干法水泥生产技术发展的重要衡量指标。2.1.1悬浮预热器的发展和工作原理2.1.1.1悬浮预热器的分类悬浮预热技术是指低温粉体物料均匀分散在高温气流之中,在悬浮状态下进行热交换,使物料得到迅速加热升温的技术。悬浮预热器的主要作用是对水泥生料的预热。早期悬浮预热器的种类较多,其分类方法主要有以下三种:(1)按制造厂商分类命名:洪堡型、史密斯型、多波尔型、维达格型、盖波尔型等数种。(2)按热交换工作原理分类:同流热交换为主、逆流热交换为主和混流热交换三种。(3)按预热器组成分类:数级旋风筒组合式、以立筒为主的组合式和旋风筒与立筒(或涡室)混合组合式三种。以上三种分类方法,第一种比较直观,第
二、三种虽然着眼角度不同,但密切关联。但是严格地说,各种悬浮预热器都有同流及逆流的热交换效果,都属于混流热交换设备,虽然由数级旋风筒组合的预热器,物料同气流的热交换,主要是在各个旋风筒(包括管道)发生,因此分类中称之为以同流热交换为主的悬浮预热器。以立筒为主组合的预热器,虽然系统中匹配有1~2级旋风·】6·
Null 筒,但旋风筒主要起收尘作用,物料同气流的热交换主要是在立筒内进行,故分类中划为以逆流热交换为主的悬浮预热器。而在旋风筒与立筒(或涡室)混合组成的预热器中,同流及逆流两种热交换方式均起重要作用,故称之为混流热交换型悬浮预热器。2.1.1.2悬浮预热器的发展及典型结构A旋风预热器的发展及主要形式丹麦工程师M.VogelJorgensen于1934年7月25日获得了“用细分散物料喂入回转窑的方法和装置”的专利证书,从此掀开了预热器快速发展的历史。图2-2是四级旋风预热器具有现在最普遍采用的预热器的全部特征。田口图2-2四级旋风预热器示意图20年后,德国Humboldt公司的FMuller在上述专利的基础上改进的第一台洪堡型旋风预热器于1951年投入生产。洪堡型旋风预热器是把生料的预热和部分分解由悬浮预热器来完成,代替了回转窑部分回转筒体的功能,达到了缩短回转窑长度、增大气料接触面积、提高热交换效率和窑系统生产效率的目的。从传统干法窑与一般悬浮预热器窑的比较(图2-3)中可以看出,这样的设计有利于降低熟料的烧成热耗。洪堡型旋风预热器见图2.4,生料由上部I级旋风筒连接风管喂入,喂入量16509/kg熟料。根据对四级旋风预热器的热工研·17·
Null 为15~25m/s。生料在预热器中停留时间大约25s,生料停留时间为它在各级连接风管通过时间及在旋风筒中分离时间之和。在这段时问内,生料粉由50。C预热到800。C,而上升窑废气由1100。C降低到330。C。洪堡型旋风预热器在1951年投入生产后,1952年美国福勒公司第一个购买了洪堡公司的专利,之后日本、法国、印度等国家的制造厂商相继购买了该制造专利。1966年,洪堡公司开发了大产量双系列旋风预热器系统。除了洪堡型旋风预热器之外,还有伯力鸠斯多波尔预热器(图2—5口,该公司习惯从下部开始排列旋风筒级别)、维达格型旋风预热器(图2.56)、米亚格型旋风预热器(图2—5c)、丹麦史密斯公司旋风预热器等形式的旋风预热器。以下几条措施可以有效地保证旋风预热器中下降生料和上升气流热交换的效率:图2.5其他形式旋风预热器。一伯力鸠斯多波尔预热器;6一维达格型旋风预热器;c一米亚格型旋风预热器(1)生料颗粒应尽可能均匀地分散到气流中,使每级连接风管中横断面的热传导状态最好,不希望生料颗粒聚集成股,否则会引起事故。(2)气流在上升连接管道中应产生湍流,才能使气体和生料间产生强烈的混合,这样才能产生理想的热交换状态。·19·
Null (3)尽管在连接风管中气体与生料间热交换时间只要0.1S就足够,但是为了更好地传热给生料,生料在预热器中应有足够的停留时间。(4)各单级旋风筒连续地布置成高效逆流热交换系统,这种情况能产生最好的热交换。(5)在整个预热器系统中,各个进口及出口处要尽量避免积灰,因为积灰会引起内部生料再循环而增加热损,同时积灰会严重降低单级旋风筒的分离效率,增加系统通风阻力。B逆流式立筒悬浮预热器对于旋风预热器的每一级来说,生料和热气流在连接风管及旋风筒中热交换是顺流式,即按分段顺流原理工作,或者有一级是采用逆流的涡流室工作。逆流式立筒悬浮预热器,则几乎各级都是采用逆流热交换的钵,最上一级为从热气流中分离生料采用双旋风筒与连接风管。逆流式立筒悬浮预热器主要有克虏伯一伯力鸠斯公司的克波尔逆流悬浮预热器、原民主德国德骚公司的查波(ZAB)悬浮预热器和捷克的普列洛夫逆流悬浮预热器。C旋风悬浮预热器与逆流式立筒悬浮预热器比较逆流或立筒悬浮预热器由于结构简单,气体通风阻力小,适合含碱、氯、硫高的生料,不容易堵塞,不用设旁路,不存在胀缩连接问题,漏风量小。另外,立筒是自承重结构,因此土建投资费用较小。但是逆流式立筒悬浮预热器具有决定性的热工缺点,生料只能以股状形式由一钵送至另一钵,气料的热交换很差。以致立筒分离生料效率远远低于旋风筒,因此立筒预热器料热交换效率远远低于旋风预热器,在国际市场上,立筒预热器逐渐消失。在吸收国外先进技术及模型试验的基础上,目前,我国悬浮预热器已经走在世界前列。中材国际南京水泥设计研究院开发设计的旋风预热器带分解炉系统具有高效低阻的特点,其操作指标达到国际先进水平。现已开发700~10000t/d等各种规格的预热器系统,并得到广泛使用。近年来,我国天津水泥研究设计院在总结国内外经验的基础·20·
Null 上,研制开发出了六级预热器系统。该系统出预热器废气温度可降低至280。C左右,按五级预热器系统较好的出预热器废气温度310。C考虑,可降低30。C左右,气体量按1.43(标态)In3/(kg·e1)考虑,则降低能耗6410/(kg·e1)。烧成窑尾系统采用六级预热器后,出预热器系统的废气温度已大幅度降低,可以结合采用管道喷水和无增湿塔方案。由于废气温度被降至280。C左右,喷水降温只需100℃左右即可满足废气直接入袋收尘器的要求,大大降低了能耗。天津水泥研究设计院悬浮预热器类型及主要性能指标见表2-1。表2-1天津水泥研究设计院悬浮预热器类型及主要性能指标┏━━━━━━━━━━┳━━━━━┳━━━━━┳━━━━━┳━━━━━┳━━━━━┳━━━━━┳━━━━━┳━━━━━┳━━━━━┓┃┃700t/d┃1000t/d┃b000t/d┃2000t/d┃2500t/d┃2500t/d┃3000t/d┃4000t/d┃5000t/d┃┃规模┃┃┃┃┃┃┃┃┃┃┃┃(单系列)┃(单系列)┃(单系列)┃(双系列)┃(单系列)┃(双系列)┃(双系列)┃(双系列)┃(双系列)┃┣━━━━━━━━━━╋━━━━━╋━━━━━╋━━━━━╋━━━━━╋━━━━━╋━━━━━╋━━━━━╋━━━━━╋━━━━━┫┃生产能力/t·d1┃700┃1000┃2000┃2000┃2500┃2500┃3000┃4000┃5000┃┣━━━━━━━━━━╋━━━━━┻━━━━━┻━━━━━┻━━━━━┻━━━━━┻━━━━━┻━━━━━┻━━━━━╋━━━━━┫┃分辨率/%┃≥90┃≥92┃┣━━━━━━━━━━╋━━━━━┳━━━━━┳━━━━━┳━━━━━┳━━━━━┳━━━━━┳━━━━━┳━━━━━╋━━━━━┫┃一级筒出口温度/℃┃≤340┃≤340┃≤330┃≤330┃≤325┃≤325┃≤325┃≤320┃≤310┃┣━━━━━━━━━━╋━━━━━┻━━━━━┻━━━━━┻━━━━━┻━━━━━┻━━━━━┻━━━━━┻━━━━━┻━━━━━┫┃系统阻力/Pa┃≤4800┃┣━━━━━━━━━━╋━━━━━━━━━━━━━━━━━━━━━━━━━━━━━━━━━━━━━━━━━━━━━━━━━━━━━┫┃锁风阀结构形式┃外支承式滚动轴承┃┣━━━━━━━━━━╋━━━━━━━━━━━━━━━━━━━━━━━━━━━━━━━━━━━━━━━━━━━━━━━━━━━━━┫┃内筒式结构形式┃钢板焊接,挂片轴承┃┣━━━━━━━━━━╋━━━━━┳━━━━━┳━━━━━┳━━━━━┳━━━━━┳━━━━━┳━━━━━┳━━━━━┳━━━━━┫┃分解炉形式┃TC.nA┃TC.DD┃TDF┃1℃_DD┃TDF┃TDF┃TDF┃TC。D.D┃偈D.1DF┃┣━━━━━━━━━━╋━━━━━╋━━━━━╋━━━━━╋━━━━━╋━━━━━╋━━━━━╋━━━━━╋━━━━━╋━━━━━┫┃设备总重/t┃147┃141┃239┃265┃339┃324.5┃355┃468┃650.620┃┗━━━━━━━━━━┻━━━━━┻━━━━━┻━━━━━┻━━━━━┻━━━━━┻━━━━━┻━━━━━┻━━━━━┻━━━━━┛2.1.1.3悬浮预热器的工作原理悬浮预热器是构成预分解系统的主要气固反应单元。悬浮预热器充分利用窑尾排出的高温废气或分解炉底部燃烧产生的高温烟气,然后经最下级旋风筒收集入窑,提高系统的热效率,以降低系统热耗,提高熟料产量,是预热器的主要任务。因此,它必须具备使气固两相能充分分散均匀、迅速换热、高效率分离等三个功能。只有具备这三个功能,并且尽力使之高效化,才能最大限度地提高换热效率,为整个生产线的优质、高效、低耗和稳定生产创造条件。构成各种悬浮预热器的热交换单元设备主要有旋.21·
Null 风筒(包括连接管道)及立筒(涡室)两种,所有的悬浮预热器窑都是由这两种热交换单元设备中的一种单独或者混合组成。前面已经介绍了旋风预热器和立筒预热器的发展和主要形式。目前,立筒预热器已经趋于淘汰,预分解窑主要采用旋风预热器作为预热单元装备。‟由旋风筒及其连接管道组成的热交换单元设备,属于化学工业中流化床的一种,即稀相输送床。在每一级热交换单元中,生料颗粒总是从本级旋风筒及下一级旋风筒之间的连接管道的近下一级旋风筒出口处的上升管道区段中加入,并随即被撒料装置分散,首先被气流携带作加速运动,而后进入等速阶段。在加速段,随着生料粉颗粒被加速,气流与颗粒之间相对速度不断减小,对流换热系数也不断减小;在等速阶段,由于气固相相对速度稳定,对流换热系数也基本保持恒定。但无论在加速或者等速阶段,随着热交换的进行,气流和粉粒之间的温差不断减小。研究表明:在稀相输送加热管道中,由于它在加速段的起始区,由于气固两相具有对流系数大、换热面积大和温差大的特点,故换热效率很高。也就是说,在以旋风筒及其连接管道组成的热交换单元中,生料粉与高温气流的换热,主要发生在连接管道中,而在管道中进行的热交换又主要发生在生料颗粒的加速运动段的起始区。至于旋风筒本身在热交换单元中的作用,许多理论研究及实践证明,它的主要任务在于气固分离。采用多级换热单元的主要目的在于提高预热器的热效率。因为从热力学第一定律出发,即使在良好的换热条件下,气固换热总是有一个极限的,单级换热不利于热气流中热焓的有效利用;从热力学第二定律出发,换热温差越大,固有焓损失越大,焓效率越低,只有在理想状态下等温换热才能没有焓损失。因此,开发一个新工艺、新过程,既要从提高换热率及焓效率出发,力求采用具有更多换热单元的预热器系统,减少各级的换热温差;在实际工作中也必须考虑各种具体情况,确定预热器的级数,综合权衡,才能获得最佳的技术经济效益。.22.
Null 2.1.2分解炉的发展和工作原理2.1.2.1分解炉的发展概况预分解(或称窑外分解)技术的特点是在预热器和窑之间增设分解炉,在分解炉中加人占总用量50%~60%的燃料,使燃料燃烧的过程与生料的预热和分解过程,在悬浮状态或沸腾状态下迅速地进行。是指将已经过悬浮预热后的水泥生料,在达到分解温度前,进入到分解炉内与进入炉内的燃料混合,在悬浮状态下迅速吸收燃料燃烧热,进行高速传热过程,使生料中的碳酸钙迅速分解成氧化钙的技术。传统水泥熟料煅烧方法,燃料燃烧及需热量很大的碳酸盐分解过程都是在窑内进行的。预分解技术发明后,熟料煅烧所需的60%左右的燃料转移到分解炉内,并将其燃烧热迅速应用于碳酸盐分解进程,这样不仅减少了窑内燃烧带的热负荷,并且入窑生料的碳酸盐分解率达到95%左右,从而大幅度提高了窑系统的生产效率。20世纪70年代初,日本石川岛重工业公司(Ishikawajima.HarimaHeavyIndustriesCo.Ltd,简称IHI)从水泥熟料煅烧理论出发,认为回转窑烧成带主要靠辐射热进行热交换,其热交换效率比较高,而在温度较低的分解带,使生料悬浮在窑废气中,它们之间热交换更剧烈,热交换效率更高。依据这一理论,1971年日本石川岛公司研制出世界上第一台预分解窑(SF窑),并在日本水泥公司进行预分解技术实验获得成功。虽然这一阶段分解炉的功能及对中、低质燃料的适应性较差,但是预分解窑与其他各种干法窑型相比所展现出的良好性能,深受用户青睐,发展十分迅速。1973年国际爆发石油危机之后,油源短缺,价格上涨,许多预分解窑被迫以煤代油。原来以石油为燃料研制开发的分解炉难以适应,从而通过总结、改进,各种第二代、第三代的改进型分解炉应运而生。例如N—SF炉、CFF炉、高径比(H/D)增大的MFC炉及N—MFC炉等的出现即为典型代表。在此期间,中国许多科研设计单位在吸取国际各种预分解窑设计和生·23- Null 产经验的基础上,研制成功以煤为燃料的各种类型预分解窑,并且加大了它们的生产规模。20世纪80年代以来,随着生产经验的积累和预分解技术的提高,更为重要的是为了降低综合能耗和生产成本,提高各自的竞争能力,并促进预分解窑的技术发展,分解炉由单纯炉型和结构的改进,发展成为对预分解窑全系统的旋风筒一换热管道一分解炉一回转窑一冷却机(简称筒、管、炉、窑、机),以及与之配套的耐火、耐热、隔热、耐磨材料的制造技术、自控技术、环保设施等的整体改进开发阶段。中国预分解窑的研制开发工作也是从20世纪70年代开始的,先是以油为燃料,1976年在四平市石岭水泥厂建成第一台SF窑,随后转入以煤为燃料的各种类型预分解窑的研制、开发和建设,迈出了中国当代水泥工业科技进步的步伐。自70年代末期以来,为了加速科技进步,赶超国际先进水平,中国组织了日产4000t熟料大型预分解窑生产线成套装备的引进工作。80年代初期在装备引进的同时又对日产2000t熟料大型预分解窑生产线成套装备开发进行科技攻关、设计、设备制造和建设,建成江西、鲁南、耀县等厂的预分解窑生产线。到目前为止,各个设计研究单位,已经比较熟练地掌握了悬浮预热和预分解技术,各自研制开发了具有中国特色的预分解窑系统。我国天津院开发完成了高效环保型的1vrF形式的分解炉,该装置具有三喷腾和碰顶效应、TTF炉固气停留时间比大,上下料点合理分料,分解炉中部局部温度可达1300oC,可大幅提高煤粉燃烧效果,高温区间设计1.5s,可保证劣质煤及无烟煤的充分燃烧;二通道对称四点喷入喂煤,优化分解炉温度场;开发了燃料分级、分风分级分解炉组织燃烧技术减低NO;排放,确保系统NO,指标
Null 类;按其作用原理又可以分为悬浮和沸腾两种方式,悬浮式按气流运动不同又有各种方式,见表2-2。下面简单介绍几种典型分解炉结构。表2-2几种典型分解炉的分类┏━━━━┳━━━━━━━━━━┳━━━━━━━┳━━━━━━━━━━━━━━━┓┃分类┃气流主要运动方式┃分解炉名称┃生产企业┃┣━━━━╋━━━━━━━━━━╋━━━━━━━╋━━━━━━━━━━━━━━━┫┃┃旋流式┃SF型┃日本石川岛公司┃┃┃┣━━━━━━━╋━━━━━━━━━━━━━━━┫┃┃(旋风式)┃FCB型┃法国FCB公司┃┃┣━━━━━━━━━━╋━━━━━━━╋━━━━━━━━━━━━━━━┫┃┃喷腾式┃F.LSmitll型┃丹麦史密斯公司┃┃┣━━━━━━━━━━╋━━━━━━━╋━━━━━━━━━━━━━━━┫┃┃┃Prepol型┃原联邦德国伯力鸠斯公司┃┃┃紊流式┃┃┃┃┃┣━━━━━━━╋━━━━━━━━━━━━━━━┫┃┃┃Pyroclon型┃原联邦德国洪堡一维达格公司┃┃┣━━━━━━━━━━╋━━━━━━━╋━━━━━━━━━━━━━━━┫┃┃涡流式┃RSP型┃日本小野田公司┃┃悬浮式┃┃┃┃┃┣━━━━━━━━━━╋━━━━━━━╋━━━━━━━━━━━━━━━┫┃┃┃N—SF型┃日本石川岛公司┃┃┃┣━━━━━━━╋━━━━━━━━━━━━━━━┫┃┃┃C—SF型┃日本石川岛公司┃┃┃┣━━━━━━━╋━━━━━━━━━━━━━━━┫┃┃复合式┃KSV型┃日本川崎公司┃┃┃┣━━━━━━━╋━━━━━━━━━━━━━━━┫┃┃(旋流一喷腾式)┃NKSV型┃日本川崎公司┃┃┃┣━━━━━━━╋━━━━━━━━━━━━━━━┫┃┃┃D.D型┃El本神户制钢公司┃┃┃┣━━━━━━━╋━━━━━━━━━━━━━━━┫┃┃┃UNSP型┃日本宇部公司┃┣━━━━╋━━━━━━━━━━╋━━━━━━━╋━━━━━━━━━━━━━━━┫┃┃┃MFC型┃日本=募公司┃┃沸腾式┃流态化(浓相至稀相)┃┃┃┃┃┣━━━━━━━╋━━━━━━━━━━━━━━━┫┃┃┃NMFC型┃日本三菱公司┃┗━━━━┻━━━━━━━━━━┻━━━━━━━┻━━━━━━━━━━━━━━━┛A旋流式分解炉旋流式分解炉,又称旋风式分解炉,以sF型为代表。现已发展为NSF(NewSuspensionPreheaterFlashCaleiner)型,它的原理已经发展为旋流一喷腾式分解炉类型。sF分解炉是日本石川岛公司在1971年开发的世界上第一台预分解炉。其结构如图2-6所示。SF分解炉上部是圆柱体,下部呈锥形,在最下部是三次风切向吹入,同下部窑尾排出废气混合,以旋流方式进入分解炉内,3个喷油嘴和c3旋风筒卸出生料人炉喂料口都设在分解炉顶部,因此结构简单,经试验发现喷油嘴设置在炉顶燃料燃烧时问太短,改进后将喷油嘴移到锥体下部,生料入口留在顶部。经多次实验、热工及流体动力学测定才使sF分解炉定型,保证了生料与气流的热交换,炉内温度830~910。C之间,有利于生料分解。但是燃料与生料在SF分解炉中的停留时间过短,只有3~4s时间,-25·
Null 不利于燃料充分燃烧和高温气流与生料混合进行换热,因此开发时只能烧油。1号油嘴—一出口—·一人口生料入口┏━━┳━━━━┓┃羰┃蕊┃┣━━╋━━━━┫┃¥┃止┃┃┃r\'-┃┃┣━━━━┫┃┃┃┗━━┻━━━━┛图2-6SF分解炉结构及分解炉内温度分布根据对中国煤燃烧性能的试验结果,以及日本赤穗二厂SF分解炉(图2—6)烧煤粉对生产产生不良结果,公司为冀东水泥厂重新设计了烧煤粉的NSF分解炉(图2.7),与SF相比,首先,将SF分解炉燃料喷嘴由炉顶移到旋流室顶部,以一定角度向下喷吹,使喷出的煤粉直接喷入三次风中。其次,将SF分解炉炉顶喂·26·
Null 料口下移,c3筒卸出生料通过分料阀分成两部分,一部分喂到出窑的上升烟道内,降低窑尾废气温度,减少烟道结皮。另一部分生料喂人NSF分解炉锥体下部,由于生料喂料口下移及NSF分解炉加高延长了生料在炉内停留时间,有利于气料间热交换,使人窑生料分解率提高到90%以上。最后,取消了原来SF分解炉上升烟道中设置平衡窑内和三次风管内压力的缩口,在烟道内加生料可以消耗气流部分动能,适当控制三次风管进分解炉闸门,同样可以取得窑与分解炉之间的压力平衡。NSF分解炉的缺点在于NSF分解炉是侧面出口,且出口高度大,占有分解炉高度三分之一左右,使炉内产生偏流、短路和形成稀薄生料区,影响炉内气料的热交换。图2-7NSF分解炉系统-27·
Null 日本秩父水泥厂为了克服NSF分解炉的缺点,研制出秩父式SF(C.SF),其系统示意图见图2-8。为克服NSF侧面出口产生的缺点,c—sF改为顶部涡室出口。为使气料产生喷腾效果,在涡室下面设置缩口,克服了气流偏流和短路现象,各区气流到达C。筒入口路程基本相同,并且通过增设连接管,使生料在分解炉中停留时间增加到15s以上,有利于燃料完全燃烧和加强气流与生料间的热交换,使入窑生料分解率达到90%以上。图2—8C—SF分解炉系统不意图口一原理图;6一系统图我国成都建筑材料工业设计研究院对SF、NSF和、C—SF分解炉炉型进行了分析、反求、试验后,开发了适合于烧劣质煤的CDC分解炉(见图2-9)。CDC分解炉在炉体的圆柱段设置有缩口,通过此缩口来改变料气运行轨迹,加强喷腾效应;同时,将c.sF分解炉出口涡室加高,采用了类似DD分解炉出口的径向出口方法,使得路子顶部出El风上方留有气流迂回空间,增强物料在气流内的返混,达到延长料气停留时间,改善炉内浓度场及温度场分布均匀性,提高熔炉利用率的目的。B涡流燃烧式分解炉涡流燃烧式分解炉是在RSP分解炉中加流化床,可以强化物料的分散,延长物料滞留时间及粗颗粒煤粉的燃烧时间,达到提·28·
Null 的停留时间,一方面可以防止物料沉降,延长物料在流化床上的滞留时间;另一方面可以使未燃尽的大颗粒煤粉进一步燃烧。RSP/F分解炉的分散功能将有利于提高物料的悬浮分散性,提高生料分解率。改造后的RSP/F分解炉还可以有效地缓解C,、c,预热器塌料带来的严重后果。可见,RSP/F分解炉不仅可以使煤粉充分燃烧,改善物料的分散程度,提高分解效率,还具有缓解塌料、预防生产事故的作用。C沸腾式分解炉日本三菱重工、三菱矿业和水泥公司开发MFC(MtsulishiFludizedCalciner)分解炉,它们将化学工业硫化床用于煅烧水泥,于1963年开始试验并于1968年获得MFC设计专利。MFC分解炉结构如图2—10所示。它由一个钢板卷成圆筒体,为了保护简体和减少散热损失,在筒体内镶有隔热砖和耐火砖。在简体下部装有流化床,流化床下部有一个空气室,设有进风口,流态化风机鼓入高压风,通过喷嘴吹向流化层。原始型MFC分解炉(图2-11口)经使用后发现炉底流化床面积很大,通过流化床的最低风速应控制在0.8m/s以上才能使生料形成流化层,造成流化空气和三次空气比高于0.3:0.7。因此,一方面,造成三次空气回收热量减少,造成整个分解窑系统热耗增高;另一方面,由于流化床面积大,很难保持适当和稳定均匀的流化速度,使炉内煅烧条件恶化。改进型MFC分解炉(图2-11b)把流化床面积缩小,采用流化一悬浮叠加原理,延长了物料在炉内滞留时间。生料在炉内分解率达50%~60%后,通过斜烟道进入窑尾上升烟道底部,再利用窑气中过剩氧使燃料继续燃烧,同时使生料分解率提高到90%以上。这就是两步到位的模式。N.MFC型分解炉(图2-11c)是三菱重工在20世纪80年代中期开发的,它进一步增大了分解炉的高径比,将流化床面积减至尽可能小,使流化空气量降至最小。同时,将全部生料喂入炉内,形成稳定流化层。MFC分解炉具有热交换效率高,燃烧稳定,物料停留时间长,·30·
Null ┏━━━━━┳━━━━┓┃雨0X3300┃/炉1┃┃≮一┃/利┃┃04600┃三次┃┃下酬I┃蟊┃┃溜刊┃┃┃裂┃┃┣━━━━━┻━━━━┫┃}Ⅱ砦-4岔l上、啼┃┗━━━━━━━━━━┛流化床空气人口图2-11MFC分解炉结构图n一原始型;b--改进型;c—N-MFC型可燃烧劣质煤、粗粒煤的突出优点。另外,由于炉内为还原气氛,可以减少NO。的排放量,出炉料流稳定性高,出炉生料分解率及料温稳定。但是,由于需要设置流态化高压鼓风机,使流程复杂化,增加了系统电耗,而且结构和操作复杂。D烟道式分解炉1964年,原联邦德国用油页岩作为水泥原料在悬浮预热器中煅烧,开始了窑外分解技术的应用,但是真正烧油及煤的分解炉的研究,是日本1974年开始的,特别是洪堡和伯力鸠斯两大水泥设备制造商,它们将窑尾与最低一级旋风筒之间连接烟道增高并弯曲向下,用延长烟道的方法开发出各自分解炉专利。a洪堡公司Pyroclon分解炉洪堡公司分解炉系列如图2—12所示。Pyroclon—S分解炉的特点是上升烟道分解炉用的燃烧空气从回转窑内通过,它适合于对带多筒冷却机的SP窑进行改造。Py—roclon—R分解炉基本和Pyroclon—S相同,主要差别是,R型使用单独三次风管供应三次风,和窑尾废气一起作为分解炉燃料燃烧用风。这样可以降低分解炉内二氧化碳的分压,提高分解温度。Py一-31- Null 解炉下行烟道进入最下一级旋风筒。洪堡公司各种分解炉适用于各种燃料,可以控制分解炉内各区温度,使料气能很好混合,降低废气中NO。和CO的含量,使整个分解窑系统压强降低。除此之外,设备相对简单,生料分离效率高,并且适合于燃烧劣质燃料。b伯力鸠斯公司Prop01分解炉德国伯力鸠斯公司分解炉,同洪堡公司Pyroclon分解J炉一样将窑尾烟道延长变成分解炉,不同之处是在伯力鸠斯多波尔悬浮预热器基础上设置了一条整体烟道。伯力鸠斯分解炉系列如图2—13所示。图2—13伯力鸠斯公司Pmp01分解炉系列8一AT;6一AS;c—AS-CC;d—AS—MSCPropol—AT型分解炉所用的燃烧空气全部由窑内通过,适合于改造带多筒冷却机的sP窑。Prop01.AS型分解炉所用的燃料空气一部分来自三次风管,另一部分由窑内通过。PropolAS—CC型分解炉是在As分解炉基础上改进而成的,主要适合于烧劣质煤,特别是易烧性差的燃料,如无烟煤、石油焦等。PropolAS—MSC型分解炉是在AS基础上为降低窑系统NO。排放量而研究出来的。它主要采用了多级燃烧的设计已达到降低NO。排放的目的。伯力鸠斯Propol系列分解炉的适用范围见表2-3。·33- Null 表2-3各种Prop01分解炉适用范围┏━━━━━━━━━━┳━━━━━━┳━━━━━━┳━━━━━━┳━━━━━━┓┃分解炉型┃AT┃AS┃AS.CC┃AS.MSC┃┣━━━━━━━━━━╋━━━━━━╋━━━━━━╋━━━━━━╋━━━━━━┫┃高碱原料旁路放风:┃┃┃┃┃┣━━━━━━━━━━╋━━━━━━╋━━━━━━╋━━━━━━╋━━━━━━┫┃预防生成结皮┃▲▲┃▲▲▲┃▲▲▲┃▲▲▲┃┣━━━━━━━━━━╋━━━━━━╋━━━━━━╋━━━━━━╋━━━━━━┫┃生料低碱水泥┃▲┃▲▲▲┃▲▲▲┃▲▲▲┃┣━━━━━━━━━━╋━━━━━━╋━━━━━━╋━━━━━━╋━━━━━━┫┃燃料特性:┃┃┃┃┃┣━━━━━━━━━━╋━━━━━━╋━━━━━━╋━━━━━━╋━━━━━━┫┃团块状┃▲▲▲┃▲▲┃▲▲┃▲▲┃┣━━━━━━━━━━╋━━━━━━╋━━━━━━╋━━━━━━╋━━━━━━┫┃高灰分┃▲▲▲┃▲▲▲┃▲▲▲┃▲▲▲┃┣━━━━━━━━━━╋━━━━━━╋━━━━━━╋━━━━━━╋━━━━━━┫┃低品位┃▲┃▲▲┃▲▲▲┃▲▲┃┣━━━━━━━━━━╋━━━━━━╋━━━━━━╋━━━━━━╋━━━━━━┫┃适应各种燃料┃▲┃▲▲┃▲▲▲┃▲▲┃┣━━━━━━━━━━╋━━━━━━╋━━━━━━╋━━━━━━╋━━━━━━┫┃环境保护要求:┃┃┃┃┃┣━━━━━━━━━━╋━━━━━━╋━━━━━━╋━━━━━━╋━━━━━━┫┃低NO,排放量┃▲▲┃▲▲┃▲▲┃▲▲▲┃┣━━━━━━━━━━╋━━━━━━╋━━━━━━╋━━━━━━╋━━━━━━┫┃配套设备范围:┃┃┃┃┃┣━━━━━━━━━━╋━━━━━━╋━━━━━━╋━━━━━━╋━━━━━━┫┃小于2000t/d┃▲▲┃▲▲┃▲▲┃▲▲┃┣━━━━━━━━━━╋━━━━━━╋━━━━━━╋━━━━━━╋━━━━━━┫┃2000~3000t/d┃▲▲▲┃▲▲┃▲▲┃▲▲┃┣━━━━━━━━━━╋━━━━━━╋━━━━━━╋━━━━━━╋━━━━━━┫┃大于3000t/d┃▲┃▲▲▲┃▲▲▲┃▲▲▲┃┣━━━━━━━━━━╋━━━━━━╋━━━━━━╋━━━━━━╋━━━━━━┫┃LowNO。燃烧器┃┃▲▲▲┃▲▲▲┃▲▲▲┃┣━━━━━━━━━━╋━━━━━━╋━━━━━━╋━━━━━━╋━━━━━━┫┃多级燃烧┃┃▲┃▲┃▲▲▲┃┗━━━━━━━━━━┻━━━━━━┻━━━━━━┻━━━━━━┻━━━━━━┛注:▲▲▲很适合;▲▲适合;▲尚司;一不适合。2.1.2.3新型分解一预烧系统预分解系统是新型干法水泥中的核心组成部件,不同类型的预分解系统可适应不同的应用环境且实现不同的效果。有人研究了高产、高稳定性预分解系统,劣质及无烟煤分解炉烧成装置和高原型煤种普适性水泥熟料循环煅烧系统等多种关键技术与装备、生产线并成功应用于三条水泥熟料工业化中。A高产、高稳定性预分解系统为了提高分解炉内无聊的分解率,该研究通过引人带旋流的三次风增加物料的横向运动,从而提高物料的分解。在此基础上,采用CFD技术对该类型预分解系统的运行和结构参数进行优化设计,分析发现增大分解炉的容积可以增加煤粉和物料在分解炉内停留时间,从而为进一步增产降耗奠定理论基础。高产、高·34.
Null 稳定性预分解系统如图2—14所示。┏━━━━━━━━━━━━┳━━━━━━━━┓┃┃出口┃┃4300┃疋.┃┃l·┃,一l┃┃l}┃、┃┣━━━┳━━━┳━━━━╋━━┳━━━━━┫┃┃┃5j┃700┃┃┃┃┣━━━━╋━━┫┃┃o┃┃一┃┃┃┃o┃┃┃┃┃┃呈┃┃┃┃┃┃n┃┃┃┃┃┃┃生料┃┃┃┃┃┃入口┃┃┃┃┃┃┃┃┃——┃┃┃。∑┃电┃I┃二┃┃1┃r三}┃┃┃?,┃┃o┃奴诫┃┃戮1?┃┃┣━━━┻━━━━╋━━┻━━━━━┫┃寸,┃┃┃┣━━━┻━━━━━━━━╋━━━━━━━━┫┃次风入口/M┃弋2650┃┗━━━━━━━━━━━━┻━━━━━━━━┛生料。昌寸二次风入口风入口I『/姆入口煤露C…口图2—14高产、高稳定性预分解系统n一喷旋分解炉正视图;6一下部放大图;c一俯视图B劣质及无烟煤分解炉烧成装置针对劣质及无烟煤的特点,参照现有预热器、分解炉结构的特点,借鉴国内相似工况条件的技术特征,计算调整预热器结构参数,开发设计劣质及无烟煤分解炉烧成装置。劣质及无烟煤分解炉烧成装置如图2—15所示。与劣质及无烟煤分解炉烧成装置配套的是高效窑外分解窑。该窑设计主要基于高容积产量,其途径通过调整烧成带、过渡带长度和耐火材料的材质以适应窑高速运行状况下对新型燃烧器、高产量等的适应性。C高原型煤种普适性水泥熟料循环煅烧系统(简称:循环预烧系统)高原型煤种普适性水泥熟料循环煅烧系统主要由两部分构成,一是具有常规功能的分解炉,二是具有进一步提高物料分解率和温度的预烧炉。该系统基本工艺流程如图2—16所示。·35.? Null 2.2回转窑2.2.1回转窑的功能和发展回转窑诞生于1885年,经过120多年的发展和完善,经历了多次重大的技术革新。自第一代回转窑投入生产以来,其简体形式已经变革、发展,但主要是直筒型和各种局部扩大型两种。实践经验和理论研究表明,直筒型是现时最有效的窑体结构,现代预热器窑和窑外分解窑的筒体一般都是直筒型。表2_4为中材国际南京水泥设计研究院设计生产的回转窑主要性能参数,均为直筒型。表2_4南京水泥设计研究院回转窑主要性能参数┏━━━━━━━┳━━━━━━━━━┳━━━━━━━━┳━━━━━━┳━━━━━┓┃规格/m┃参考产量/t·d1┃转速/r-min-1┃斜度/%┃支承数量┃┣━━━━━━━╋━━━━━━━━━╋━━━━━━━━╋━━━━━━╋━━━━━┫┃4,3.2X50┃1000┃O.36~3.5┃4┃3┃┃∞.5X54┃1500┃O.35~3.5┃4┃3┃┃64×56┃2000┃O.6~3.6┃4┃3┃┃64×60┃2500┃O.4~4┃4┃3┃┃64.3×60┃3000┃0.4~4┃4┃3┃┃64.6X70┃4000┃O.36~4┃4┃3┃┃64.8×74┃5000┃O.35~4┃4┃3┃┃4,5×74┃6000┃O.35~4┃4┃3┃┃65.6X84┃7500┃O.36~4┃4┃3┃┃踊.2x92┃10000┃0.4—3.9┃4┃3┃┃4,5.2X61┃5500┃O.38~3.8┃3.5┃2┃┗━━━━━━━┻━━━━━━━━━┻━━━━━━━━┻━━━━━━┻━━━━━┛作为水泥熟料矿物最终形成的煅烧技术装备,它主要在以下五方面发挥作用。(1)燃料燃烧装置。作为燃料燃烧装置,它具有广阔的燃烧空间和热力场,可以供应足够的空气,装备优良的燃烧装置,可以保证燃料充分燃烧,为熟料烧成提供必备的热量。·37·
Null (2)热交换作用。作为热交换装置,它具有均匀的温度场,可以满足水泥熟料形成过程中各个阶段的换热要求。(3)化学反应功能。作为化学反应器,随着水泥熟料矿物形成不同阶段的不同需要,它既可以分阶段满足不同矿物形成对热量、温度的要求,又可以满足它们对时间的要求,是目前用于水泥熟料矿物最终形成的最佳设备。(4)输送物料功能。作为输送设备,由于物料在回转窑内的填充率、转速和窑斜度都很低,因此具有更大的利用潜力。(5)降解利用废弃物。20世纪末以来,随着环境保护意识的加强,回转窑表现出优越的环保功能。它具有高温、稳定热力场的突出优点,已经成为降解利用各种有毒、有害、危险废弃物的最好装置之一。回转窑具有多种功能和优良品质,近半个世纪中它在一直独立承担着水泥生产过程中的熟料煅烧任务。但是,它也存在着许多的缺点和不足。首先,作为热交换装置,窑内主要表现为“堆积态”换热,换热效率有限,影响生产效率的提高和能耗的降低。其次,熟料煅烧过程大量生成NO。等有害成分,造成严重的大气污染。最后,回转窑产出的高温熟料热量很难回收,如果没有效率很高的冷却机配合,将造成热量的巨大浪费,而缓慢冷却是影响熟料质量的。回转窑的主要发展方向都是围绕着它的缺点而展开的。一方面,是对回转窑本身的改进,例如对窑直径的部分扩大、窑长度的变化等,以达到改进换热条件,改变气流速度或延长滞留时间的目的;另一方面,则是将某些熟料形成的化学反应移到窑外进行,以改善换热和化学反应条件。从1928年立波尔窑的诞生,1932年旋风预热器专利的获取,1950年旋风预热窑的出现,1971年预分解窑的诞生,以及20世纪80年代长径比为10的两支点短回转窑用于生产等,这些对回转窑功能削弱的技术革新过程至今仍在进行。这样,就使凡是能采用比回转窑更加优越的设备进行的水泥熟料煅烧过程,都转移到窑外进行,以尽量克服其固有的·38- Null 缺点和不足。但是,到目前为止,熟料煅烧的最后烧结过程,仍采用回转窑来完成,还没有研制开发出可用于现代化大型生产的更好装备。特别是回转窑所具有的降解利用各种废弃物的优良环保功能被挖掘利用后,更赋予其新的发展活力。随着窑的产量提高,窑的容积产量从3.ot/(d·m3)逐步上升至6.or/(d·m3)。回转窑筒体散热损失从三档窑的大于35keal/kg下降至二档窑的26~30keal/kg。窑速从3r/rain提高至4r/rain以上,物料在窑内停留时间从40rain逐步下降至30min以下。二档窑和三档窑相比,设备重量降低约10%左右,此外还具有运行平稳、安装简单、维护方便等优点。20世纪80年代初,第一台L/D
Null 图2—17回转窑简体变形情况有增加筒体刚性的作用。轮带是由铸钢或锻钢制成,锻造轮带其截面为实心结构,质量好使用年限长,但是散热差,刚性差,制造工艺复杂。截面尺寸较大的轮带,一般采用铸造,其截面有实心矩形和空心箱形两种。轮带的安装方法主要有两种,一种是固定式,将轮带通过垫板直接铆在筒体上。这种安装方式限制了筒体的自由膨胀,轮带与筒体之间的热应力较大,目前很少使用。另一种是活套在筒体上,如图2—18所示,在筒体上铆接或焊有垫板,轮带与垫板之间留有适当的空隙,一般3~6mm,它既可以控制热应力又可以充分利用轮带的刚性,使之对简体起到加固作用,因此是目前应用较多的安装方法。2.2.2.3托轮托轮设置在每道轮带的下方两侧,支撑窑的部分重力。它是一个坚固的钢质鼓轮,通过轴承支撑在窑的基础上,为了节省材料和减轻质量,轮带中设有带孔的辐板,托轮的中心贯穿一轴,两轴颈安装于两轴承之中(见图2.19)。托轮的直径一般为轮带直径的四分之一,其宽度比轮带宽50~lOOmm。图2—20为托轮的轴承结构。2.2.2.4挡轮组回转窑筒体与水平呈一定斜度安装,长期运转后,由于筒体弯曲和轮带与托轮的不均匀磨损,特别是由于轮带与托轮接触面之间摩擦因数的变化,经常引起筒体的上下窜动。这个窜动必须.40.
Null 好坏,对窑系统的运转和生产指标具有重要意义。窑的密封主要有非接触式和接触式两大类。前者包括迷宫式与气封式两种,后者则有端面摩擦和径向摩擦两种。2.2.3回转窑的工作原理回转窑的工作原理主要集中了物料在回转窑内的运动、回转窑内气体的流动、燃料的燃烧等主要过程和基本规律。2.2.3.1窑内物料的运动新型干法水泥生产所采用的窑外预热预分解将预热和分解分别移到预热器和分解炉中进行,窑内只有小部分的分解反应。一般认为从窑尾起至物料温度1300℃为过渡带,主要任务是物料升温及部分碳酸盐分解和固相反应;物料温度1300~1450~1300。C区问为烧成带,主要完成水泥熟料主要成分的最终烧成。窑内物料的运动可以用图2-22来说明。物料进入回转窑后,由于筒体以一定速度转动并且与水平面有一定的倾斜度,物料逐渐由窑尾向窑头运动。┏━━━━┳━━━┓┃纩┃]以┃┃f┃┃┣━━━━╋━━━┫┃屹┃猫占┃┃┣━━━┫┃爿┃爿7┃┗━━━━┻━━━┛图2-22回转窑内物料运动示意图由图2-22看出:△S=htana式中^——物料平面弦长;(2-1)·43·
Null a——回转窑筒体的斜度。很容易得出h=2Rsin要(2—2)式中尺——筒体半径;„D——物料平面与简体中心形成的圆心角。那么AS=Disin.--翌g-tand(2-3)二式中Di——回转窑筒体有效内径。物料前进AS距离后,又被埋在物料中,重复以上的运动过程,在不断的反复过程中前进,每翻滚一次就前进一个2xS。2.2.3.2窑内气体的流动气体在回转窑内流动时,伴随有燃料的燃烧、物料的煅烧,气体的温度、组成随时都在变化。因此,气体的流动是相当复杂的,特别是燃烧带内的气体流动更为复杂。回转窑燃烧带内的气体流动,可以近似为射流流动。根据流体力学得知,该射流是指流体由喷煤嘴喷射到较大空问并带动周围介质(二次风)流动形成流股(火焰)的流动,流体喷入到有限空间(燃烧带空间),显然回转窑内火焰的射流应属于限制射流。绝大多数的射流都属紊流流动,在射流内气体质点有不规则的脉动,气体由喷嘴喷出后,由于紊流质点的脉动扩散和分子的黏性扩散作用,使得喷出的一次空气质点和周围的二次空气质点发生碰撞,进行动量交换,把自己的一部分动量传递给相邻的气体,并带其他质点向前流动。又由于回转窑是一个直径有限的圆筒,当前面的气体被推向前进时,后面的气体变得稀薄而压力下降,即在喷煤嘴处造成一定的负压(抽力),使二次空气连续不断吸收进流股内,与一次空气混合,并逐渐向中心扩撒,射流断面逐渐扩大,气体量逐渐增多。燃烧带火焰长度,主要决定燃烧带气体流速,为了保持适当.44·
Null 的火焰长度,燃烧带气体流速可按下式进行计算:既2丽10306A00m币qi„2-4)式中%——燃烧带气体流速,m3/(Ill2·s);A——1kg燃料燃烧生成的气体量,ITl3/kg;m——回转窑的小时产量,t/h;g——熟料的单位热耗,kg/kg-ck;D。——燃烧带内径,m;Q。。。。——燃料的应用基低位热值,kJ/kgo除燃烧带以外气体在窑内的流动,近似于气体在管道内的流动,一般流动状态属于湍流范围。沿窑截面气流速度分布比较均匀,但在窑头及窑尾处,气流速度分布受窑头、窑尾及烟室形状和密闭情况的影响。这些地方往往由于通风截面的变化和方向的改变而形成涡流,导致流体局部阻力增大。如果结构形式不当,则会影响窑内通风,使高温火焰不顺畅,影响窑的正常操作及热工性能。气体在窑内流动,流速是一个十分重要的参数。它一方面影响对流换热系数的大小;另一方面影响着高温气体与物料接触时间。如果气体流速增大,传热系数增大,但气体与物料接触时间缩短,总的传热量反而减少,使废气温度升高,熟料热耗增加,窑内扬尘增大。窑内气体流动与窑内径的关系为陬兰。ciD3oc丁DD(2_5)1Tn2。£4五∥式中肛一回转窑内气体流速;Q——回转窑的发热能力。由此可以看出,窑内需要的气体流速与窑的直径成正比,即随窑径的增加,窑内风速也要求增加。2.2.3.3窑内燃料的燃烧回转窑内煤粉燃烧所形成的火焰属于湍流扩散火焰,燃烧过·45· Null 程可分为四个阶段:燃料与空气混合;释放挥发分;挥发分燃烧;固定碳燃烧。碳粒的燃烧过程可用以下化学反应式表示:C+02_C02C+0:叫CO一级反应2C+02卅C02CO:+C卅C0二级反应·CxOy+02刊colmco,+nCOCxO,.J。式中,m、n决定于燃烧过程和条件即碳氧结合比卢2罴。碳粒的燃烧过程也是燃烧物的消耗过程,可以利用单位时间内氧的消耗量或碳的消耗量来表示。2.3熟料冷却机2.3.1熟料冷却机的发展世界上第一台熟料冷却机是1980年出现的单筒冷却机,多筒冷却机是1923年由丹麦史密斯公司设计出现,在1965年后又改进成新型多筒冷却机。在这一时期也是SP窑最为流行时期,新型多筒冷却机多配置在新建的sP窑上。但是自从1973年开发出分解炉NSP窑新技术后,由于多筒冷却机不能提供三次风供分解炉燃烧用,转而采用篦式冷却机的较多?2.3.1熟料冷却机的发展世界上第一台熟料冷却机是1980年出现的单筒冷却机,多筒冷却机是1923年由丹麦史密斯公司设计出现,在1965年后又改进成新型多筒冷却机。在这一时期也是SP窑最为流行时期,新型多筒冷却机多配置在新建的sP窑上。但是自从1973年开发出分解炉NSP窑新技术后,由于多筒冷却机不能提供三次风供分解炉燃烧用,转而采用篦式冷却机的较多。与之相适应,篦式冷却机由第一代发展为第二代。1984年IKN公司提出“阻力篦板”概念产生了第三代篦式冷却机。篦式冷却机在1940年才用于水泥工业中,它分为往复式、移动式和振动式。往复式篦式冷却机是用许多排篦板向前和后退运动来送熟料,而移动式篦式冷却机是用环形连续篦式床来输送熟料、振动式篦式冷却机是把篦床作为振动输送槽来输送熟料,后两者由于结构存在一些缺陷而被淘汰。篦式冷却机因单位篦床产量反复提高,不断提高热回收效率和不断降低磨损及维护费-46.
Null 用,以及降低单位冷却空气而降低收尘空气量,而得到大家竞相采用。熟料冷却机有近十种形式,但现代新型干法烧成系统多用单筒、多筒和篦式冷却机。这些冷却机要完成以下任务。(1)尽可能多地把熟料中显热(1200~1500kJ/蚝熟料)回收进烧成系统,加热二次空气和三次空气,尽可能提高
二、三次空气温度,把烧成系统燃料消耗降至最低。(2)尽量提高熟料冷却速度,以提高水泥质量和提高熟料的易磨性。(3)要把熟料冷却到尽可能低的温度,以满足熟料输送、贮存和水泥粉碎的要求。水泥工业的回转窑诞生之初,并没有任何熟料冷却设备,热的熟料倾卸于露天堆场自然冷却。19世纪末期出现了单筒冷却机。1910年德国克虏伯·格罗生(KruppGrason)公司把多筒冷却机引用到水泥工业,称为康森特拉(Concentra)冷却机,1922年丹麦史密斯公司开始制造这种冷却机,并命名为尤纳克斯(Unax)冷却机。1930年德国伯力休斯公司在发明了立波尔窑的基础上研制成功回转篦式冷却机,称为Recupol。随后不久,英国阿利斯.查默尔(Allis—Chalmers)公司又开发出震动式篦式冷却机。1937年美国富勒(Fuller)公司开始生产第一台推动篦式冷却机。100多年来,在国际水泥工业科技进步的大潮中,有的不断改进,更新换代,长足发展;有的已经被淘汰。20世纪80年代末出现的第三代可控气流篦式冷却机,其性能虽较第二代厚层篦式冷却机优良,但仍然存在结构复杂,篦下需设置拉链机,机身占用高度高,冷却风量较大且篦板篦缝喷出风速过高等问题。进一步改善通风效率、提高热回收率、简化装备结构、提高运转率、降低装备高度、减少基建投资已成为冷却机发展的方向。90年代中期,国外出现了无漏料冷却机,工艺性能优良,装备简化,此类冷却装备中,近年来投人生产的步进式无漏料高效冷却机性能尤为优良,该机由若干条纵向熟料冷却输送通·47·
Null 道组成,运行速度随料层冷却情况自动调节,通道单独通风,热交换时间可以控制,确保不同粒径熟料得以冷却,冷却风量(标态)约1.6m3/kg熟料,热回收率超过74%~76%,篦床有效面积负荷>45t/(ITl3·d)。同时,该篦式冷却机具有结构紧凑,机内无输送部件,篦板不与热熟料直接接触,磨蚀量少,熟料输送无阻碍,输送效率稳定,模块化设计,安装维护方便,篦下无漏料,无须设置拉链机,整机高度低等一系列优点。目前,熟料冷却机在水泥工业生产过程中,已不再是当初仅仅为了冷却熟料的设备,而在当代预分解窑系统中与旋风筒、换热管道、分解炉、回转窑等密切结合,组成了一个完整的新型水泥熟料煅烧装置体系,成为一个不可缺少的具有多重功能的重要装备。熟料冷却机的功能及其在预分解窑系统中的作用如下:(1)作为一个工艺装备,它承担着对高温熟料的骤冷任务。骤冷可阻止熟料矿物晶体长大,特别是阻止硅酸三钙晶体长大,有利于熟料强度及易磨性能的改善;同时,骤冷可使液相凝固成玻璃体,使氧化镁及铝酸三钙大部分固定在玻璃体内,有利于熟料的安定性的改善及抗化学侵蚀性能。(2)作为热工装备,在对熟料骤冷的同时,承担着对人窑二次风及入炉三次风的加热升温任务。在预分解窑系统中,尽可能地使
二、三次风加热到较高温度,不仅可有效地回收熟料中的热量,并且对燃料(特别是中低质燃料)起着预热、提高燃料燃尽率和保持全窑系统有一个优化的热力分布都有着重要作用。(3)作为热回收装备,它承担着对出窑熟料携出的大量热焓的回收任务。一般来说,其回收的热量随
二、三次风进入窑、炉之内,有利于降低系统煅烧热耗,以低温热形式回收亦有利于余热发电。否则,这些热量回收率差,必然增大系统燃料用量,同时亦增大系统气流通过量,对于设备优化选型、生产效率和节能降耗都是不利的。(4)作为熟料输送装备,它承担着对高温熟料的输送任务。.48.
Null 对高温熟料进行冷却有利于熟料输送和贮存。2.3.2熟料冷却机的结构与工作原理2.3.2.1单筒冷却机结构及工作原理单筒冷却机结构上类似于回转窑,其工作原理是通过逆流传热,以及通过内部装置使熟料布满整个筒体横截面对流换热的终和换热方式。现代新型单筒冷却机如图2-23所示。在通体前一段最前面25m,没有任何内部扬料装置。在开始最热的1区可装有三排破碎齿;接着2区和3区装有半扬料斗板。在此后面40m全长区段,衬有铁板,在4区和5区装有闭式扬料勺,出口(6区)装有开式弧形扬料板。6哆黛3m/\、~弋r尸幽2-23新型单筒冷却机2.3.2.2多筒冷却机结构及工作原理新型多筒冷却机一般有9~10个冷却筒配置在窑筒体周围,每个冷却筒通过弯管同窑筒体卸料1:3相连接,故窑卸出熟料通过弯管进入冷却筒。冷却筒是通过两个支架支承在窑筒体延长段上,延长窑筒体末端装有一个附加轮带托轮支承装置来承受冷却筒附加重量。·49.
Null 多筒冷却机的每个冷却筒,通过两个支架固定在窑筒体延长段上。多筒冷却机工作原理及工艺过程同单筒冷却机基本相同,故其内部装置也基本相同。如图2—24所示,高温熟料通过进口弯道进入冷却筒后,首先进入最前端,接着进入三排破碎齿区,随后是扬料板区,紧接着是装有扬料勺和撒播扬料装置区。图2-24多筒冷却机的冷却筒内部装置冷却筒出口端包在卸料壳罩中,在那里熟料通过冷却筒末端格筛筛分,留在格筛上的大块熟料喂入熟料破碎机中。窑的末端设计呈锥形缩口,一方面可以降低窑门的密封面积,形成一圈很高挡坝,使高温的熟料堆积在出口,延长熟料在窑内停留时间,降低熟料进入冷却筒时的温度。另外在冷却筒进口套管处装有破碎棒,可以防止大块熟料进人冷却筒,特别是可防止垮落窑皮堵塞进口弯管和损坏冷却筒中扬料装置。2.3.2.3篦式冷却机结构与工作原理到目前为止,篦式冷却机经过了四代的发展,各带篦式冷却机的主要性能特点见表2-5。·50·
Null 表2-5各代篦式冷却机主要性能特点┏━━━━━━━━━━━━━┳━━━━━━━━━━┳━━━━━━━━━━┳━━━━┓┃┃单位篦床面积产量┃单位冷却风量(标态)┃热效率┃┃代别┃┃┃┃┃┃/t·(m2·d)一‟┃/m3·kg一1┃/%┃┣━━━━━━━━━━━━━╋━━━━━━━━━━╋━━━━━━━━━━╋━━━━┫┃第一代富勒型篦式冷却机┃25~27┃3.5~4.0┃
Null 装有气动双翻板阀的下料管落到漏到拉链机内,由拉链机输送到熟料输送机。冷却空气和高温熟料进行热交换后,一部分作为二次空气入窑;另一部分被利用给分解炉供风,剩余部分经热交换器、袋式收尘器后排空。经过热交换器及收尘器收集下来的灰尘通过回灰螺旋输送机送到熟料输送机上。冷却后的熟料及回灰通过熟料输送机输送到熟料库内。富勒型水平推动篦式冷却机每段篦床的第一排篦板是活动的,利用物料推进,可以减少“堆雪人”现象。篦板排列床用“单宽”、“双宽”交错排列,使篦缝不在同一直线上,减少篦板磨损。按不同地方结构,采取良好的密封装置,保证冷风利用率,提高了冷却机的冷却效率。其主要性能特点有:(1)富勒型篦式冷却机具有较高的热传递效率,入窑和入炉的风量和风温易于控制,便于自动化程度的新型干法窑操作。(2)经过冷却后的熟料温度较低。由于运用了“淬冷”技术,改善了熟料的易磨性。(3)应用了“厚料层”冷却理论(料层在500~600mm),篦床单位面积产量高达43t/(m2·d)。(4)系统配置了三元控制及安全监测装置,保证冷却机高效、稳定操作。B第二代篦式冷却机(ClaudiusPeters冷却机)德国ClaudiusPeters公司20世纪70年代开发和应用的水平液压推动篦式冷却机(CP冷却机,图2—26)利用液压传动代替了传统的机械传动,使冷却机的运行变得更加稳定、安全、可靠。第二代篦式冷却机采用液压传动,在冷却机每一篦床的两侧装配有液压油缸推动架,同步驱动篦床。篦床由固定篦板和活动篦板相间排列组成,活动篦板由液压系统推动,最大冲程125mm,冲程数在4~22L4:/min范围内变动。出窑熟料落在篦床上,受到活动篦床的推挤向出口方向运动,冷空气从冷却机底部鼓入风室,并垂直穿过高温熟料层,进行热交换。高温气体分别作为二·52·
Null 拉链机图2-26ClaudiusPetersHE5—850型冷却机构造次风(1100~1300℃)、三次风(700~8000C)进入窑内和通过三次风管进入分解炉。一部分低温气流(300。C)作为干燥介质进入风扫式煤磨,剩余废气有排气口通过电收尘器后排人大气。细小的熟料颗粒穿过冷却机篦孔落人9个集灰斗,由气动闸阀和电动瓣阀定期排人拉链机;大块熟料从篦板床冷端卸到倾斜的篦栅上,经锤式破碎机破碎后,卸入熟料输送机。首先,CP冷却机采用了槽型阻力篦板(Mulden篦板),与传统的篦板相比,Mulden篦板具有明显的优势。一是采用1适应热应力需要的新设计,可消除篦板弯曲;二是篦板漏料可减少30%以上,并可长时间保持篦板间较小的问隙,避免受热熟料冲击区域的冲蚀;三是篦板寿命可较传统篦板延长近2倍。篦板间搭接方式独特,于两个篦板之间搭接部分的横向间隙。采用了抗漏料侧部篦板,减小了侧向间隙以减小漏料及磨损。其次,为保证篦床均匀供风,CP冷却机除在篦板结构上采取上述措施外,在供风系统中则采用了空气梁充气技术。同时,增设了喷水装置。最后,CP冷却机广泛使用了液压技术和自动控制技术。比如,在冷却机的传动和辊式破碎机的传动均采用了液压系统,从而既可降低系统能耗,又能增加系统生产能力和系统运行的稳定性。.53·
Null c第三代篦式冷却机(IKN悬摆式冷却机)冯-韦特在1983年开始研究改善冷却操作稳定性、冷却机热回收性能课题,提出控制气流的“高阻力”篦板概念,形成“阻力”篦板,而创造出第三代篦式冷却机。主要具有如下特点:(1)采用水平式喷流的COANDA喷流篦板:熟料层内的气流分布是有效冷却的关键,具体地说,固体和气体的流动速度在每一体积单元内必须一致,气体流动是在熟料层内的空隙中进行的水平喷流贴近篦板表面,等效于篦板张开无数喷口,同时由于篦板对气流阻力很大,故使得气流在熟料层内所有空隙中的垂直上升速度几乎处处相等。因此熟料层内可获得一条光滑的温度分布曲线,接近冷风的是冷熟料,而热熟料则靠热风端,如果在熟料分布不均匀气流便可能穿透某些阻力较小的部位,导致气流和熟料分布紊乱,降低它们之间的热交换。在传统篦式冷却机中,垂直喷流引起反向空气流动,于是卷起一些流态化细粉,以热喷砂形式喷向篦板表面,造成篦板的损坏,这种篦板磨损可使篦缝面积每年增加4%。通常用缩小篦缝的办法来增加篦板对气流的阻力,然而窄缝会产生更加强烈的空气喷流并在熟料层内引起湍流,导致更强的喷砂效应,使磨损加剧。IKN将具有COANDA效应的水平喷流引入到熟料冷却中,从而找到了彻底解决这一问题的办法:用向篦板表面切向倾斜的弯曲气缝送气的方式来取代传统的垂直喷流COANDA喷流篦板的设计,保证熟料不能通过通气缝,喷出的强劲气流贴近篦板表面,同时其具有的高阻力使得该气流场均匀向上分布,于是料层空隙中的细粒被扫清,空隙成为良好顺畅的气流通道,这些通道均分布于整个料床内,使向上气流阻力很小且处处均匀。(2)运用空气梁技术的熟料人口分配系统(KIDS)传统篦式冷却机在熟料入口处都有下述问题:由于热交换差及冷却速度低而导致熟料矿物活性低且易磨性差;由于热回收率低而热耗大;由于篦板阻力小而导致熟料层经常被冷却气流穿透,从而破坏熟料和气流之间的热交换,并使一些篦板直接经受高温熟料,导致·54.
Null 篦板寿命缩短。在此情形下不可能获得均匀的熟料分布,而易产生“红河”和“雪人”现象。空气梁技术的发明实现了将冷却气流分别送入各排篦板的直接通风。在KIDS中,前6排至9排篦板采用空气梁技术,先将若干COANDA喷流篦板连成为一个整体,再将它们嵌入空气梁并用一些特殊的水平螺栓将其相互固定在一起,以确保它们不发生垂直方向的变形,但允许在受热膨胀或收缩时在水平方向的整体位移,篦式冷却机入口处的空气梁设计为固定式,具有极为可靠的机械性能。(3)采用单缸液压传动的自调准悬摆系统。水泥熟料是一种腐蚀性强的材料,传统篦式冷却机由于“喷砂”效应引起篦板磨损,并且由于活动框架辊轮支撑部件引起机械磨损,故如何降低磨损是所有水泥厂家关心的问题。为了避免这种磨损,研制出IKN悬摆式活动框架(图略)。框架采用了铸件,安装精确。由于活动框架的摆动不再依赖于传统冷却机的辊子运动,而是由弹簧钢板极小的弹性变形来完成,所以这种悬挂系统本身无任何磨损,故无须维护。(4)液压传动的隔热挡板。由于熟料向冷却机内壁尤其是向低温冷端的辐射散热导致熟料层表面被冷却,这就限制了热回收率的进一步提高。针对这一隋况,IKN采取在悬摆冷却机的气体分流交界处悬挂—个气冷的隔热挡板(图略)。它可以用液压方式提起来或放下去。隔热挡板的冷却气体由其底部的COANDA喷嘴喷到熟料层表面,当大块熟料过来时,隔热挡板自动升起让其通过。在粉尘少和冷却机宽的情况下,隔热挡板带来的效益尤为显著。(5)气力自动清除漏料系统。传统冷却机细粒熟料通过篦板漏入仓室,这些漏料用安装在冷却机下方的输送系统输送出去,因此篦板磨损许多活动接口必须密封、润滑和维护。IKN悬摆式冷却机运行时能保持很小的篦板间隙,这些间隙中的熟料被强劲气流喷吹掉,一般情况下没有漏料现象发生,然而当漏料极少时,可能会产生由冷却气体中的水分引起的形成混凝土的问题。为·55·
Null 解决这一问题,IKN开发了气力自动清除漏料系统(PHD),将一钢管伸入盛有细熟料的漏斗集料器中,由冷却风机提供的一般风压在管中产生20~30m/s的风速,它可提起集料器中的细熟料,通过管道送至位于熟料破碎机下面的漏斗之中,直径达20ram的熟料均可被这一系统运走。D第四代篦式冷却机为了使水泥熟料的篦式冷却机能够更好地适应回转窑熟料产量的波动及生产的瞬时变化,以及更好地适应现代化工业生产的需要,史密斯(F.L.Smith)公司和富勒(Fuller)公司开发出了一种全新概念的冷却机新型无漏料冷却机SF(Smith—Fuller)CROSS-BAR冷却机,即第四代推动棒式篦式冷却机。第四代推动棒式篦式冷却机主要由三部分组成:熟料输送、熟料冷却及传动装置。与以往推动篦式冷却机的最大区别是:熟料输送与熟料冷却是两个独立的结构。冷却供风由固定篦床上的篦板提供用以冷却熟料,每块篦板采用机械的空气调节阀,实现冷却空气分布的自动调控,使由于温度变化、料层厚度不均及回转窑出料时产生的粗、细料离析等引起的熟料层阻力差异得以自动均衡,实现最佳的空气分布。篦板是固定的,不输送物料。熟料输送是由在固定篦床上的固定与活动交替排列的横杆作往复运动来输送物料的。运动横杆还起到搅拌、均化熟料作用,使熟料完全暴露在冷空气中,迅速冷却。横杆通过固定夹固定,更换、安装方便。横杆磨损对冷却机的运转及热效率没有影响。该设备结构简单、空气分布更好。其设计优点是:熟料输送机构与熟料冷却机分离,输送、冷却独立完成。篦板是固定的,磨损少,不会发生因篦板间隙加大而降低冷却效果,篦板寿命大大延长,设备故障率低、设备运行可靠;特殊结构篦板可以确保篦下无熟料落人风室,无须设置卸料斗、料封阀和拉链机,结构简单,操作维护方便;设置机械自动空气调节阀;体积、重量小,是第三代控制流篦式冷却机的二分之一到三分之一;模块化设计制造;·56·
Null 附属设备、土建工程、安装工程少;易损件少;液压传动。我国天津水泥设计研究院从丹麦Fons公司引进并联合重新开发、优化设计的第四代行进式稳流篦式冷却机,该冷却机采用标准模块化设计,具有流量自动控制调节功能,水平式篦床无漏料设计,四连杆传动机构-水平推料输送易于维护。2008年天津水泥设计研究院自主研发、设计、制造的TCFC3500型第四代行进式稳流冷却机在江西圣塔投产运行,烧成系统产量3800t/h,工艺性能达到国际先进水平,具有节能、高效的优势。成都建筑材料工业设计研究院自主研发的s型篦式冷却机,具有第四代篦式冷却机的关键技术。通过不同数量的标准模块的组合,可以组合不同规模的篦式冷却机,能覆盖从2500t/d到10000t/d的各种生产规模的生产线,s型篦式冷却机能够降低单位熟料冷却风量,减少单位熟料电耗,节能效果显著。2.4燃料燃烧器水泥熟料的生产过程就是燃料燃烧、气固换热、化学反应、物料输送的过程,在水泥生产过程中,有超过80%的能量是由煤粉的燃烧提供的。燃烧器是燃烧系统的核心部件,燃烧器的主要功能就是将燃料和空气导入炉膛,并加以充分混合使其有利于燃烧。2.4.1燃烧器的发展20世纪70年代以前回转窑用煤粉燃烧器均采用单通道燃烧器,一次风量占燃烧总风量的20%-30%,一次风速40-70m/s,其功能主要在于输送煤粉,对煤、风混合,二次风抽吸作用小,黑火头较长,火焰温度不易提高,不易满足熟料煅烧温度,熟料产量、质量波动较大,且不便调节煤风的混合速率,难于满足生产要求。为了克服传统单通道难以满足生产的特点,国内外相继出现了双通道、三通道和四通道的煤粉燃烧器,甚至烧两种以上燃料的五通道燃烧器,其研制开发的目的在于在一定范围内降低一次风所用比例,从而增加对二次风的利用,提高了燃烧速度,提高系·57.2.4.1燃烧器的发展20世纪70年代以前回转窑用煤粉燃烧器均采用单通道燃烧器,一次风量占燃烧总风量的20%-30%,一次风速40-70m/s,其功能主要在于输送煤粉,对煤、风混合,二次风抽吸作用小,黑火头较长,火焰温度不易提高,不易满足熟料煅烧温度,熟料产量、质量波动较大,且不便调节煤风的混合速率,难于满足生产要求。为了克服传统单通道难以满足生产的特点,国内外相继出现了双通道、三通道和四通道的煤粉燃烧器,甚至烧两种以上燃料的五通道燃烧器,其研制开发的目的在于在一定范围内降低一次风所用比例,从而增加对二次风的利用,提高了燃烧速度,提高系·57.
Null 统热效率。火焰射流中有一定比例的热烟气返混,增加煤粉与燃烧空气的混合,提高燃烧效率,降低燃尽时间。形成稳定而流畅的火焰,保证火焰温度,不会出现回火现象,从而保护窑内材料。丰富的各通道风量、风速调节手段,使火焰形态及温度调整灵活,适宜熟料煅烧。可以适应低品位燃料的燃烧,以加强燃料的综合利用,降低设备价格,减少维护费用及扩大资源的利用。燃烧完全且效率高,能优化窑的操作和稳定窑的运转,为增产降耗提高效益奠定基础。采用分级燃烧技术和煤粉浓缩技术,在燃烧完全的情况下,降低火焰射流中的氧的浓度,有效地降低NO。的排放量,减轻环境污染。2.4.2燃料燃烧器的工作原理由于直流燃烧器的结构相对简单,且适用范围相对较窄,这里主要介绍应用广泛的旋流燃烧器和速差射流燃烧器的工作原理。2.4.2.1旋流燃烧器的旋流理论旋流燃烧器的出口气流是旋转射流,它是通过各种形式的旋流发生器产生的。气流在喷入燃烧室以前,在圆管内做螺旋运动。在气流离开燃烧器时,由于离心力的作用,不仅有轴向速度,还有一个使气流扩散的切向速度。这时,如没有外力的作用,它应当沿着螺旋线的切线方向运动,形成辐射状的环状旋转射流。其主要特点如下:(1)旋转射流的扩散角比较大;(2)气流的旋转效应很快消失;(3)流场中轴向速度的最大值衰减较快;(4)回流区对周围介质的卷吸能力较大。2.4.2.2速差射流煤粉燃烧器原理利用不同速度的同向射流的引射效应,使喷粉管出口处造成负压,从而使高温烟气回流至喷粉口处,并被吸人、混合,使一次风和煤粉提前加热、着火,强化燃烧。图2-27为速差射流煤粉燃·58.
Null 烧器示意图。图2—27速差射流煤粉燃烧器示意图管2.4.3典型燃烧器的结构回转窑煤粉燃烧器由早期的单风道发展到三风道、四风道和烧两种以上燃料的五风道。风道越多性能越好,但是结构也就越复杂,质量越大,造价越高。目前水泥厂多用三通道燃烧器。下面简单介绍几种典型的燃烧器结构。2.4.3.1KHD公司PYRO—Jet燃烧器KHD公司为利用褐煤及石油焦而开发的新型多通道燃烧器,称为PYRO—Jet燃烧器(图2-28)。PYRO—Jet燃烧器是一种多通道结构喷嘴,其中心附加一个或两个气态或液态燃料管子,有时在中央还有一个点火喷嘴。通道结构如下:点火喷嘴;旋流空气通道出口带有螺旋风翅;出口为喷煤口的燃料通道;出口为环形嘴的燃料通道;出口为环形嘴的喷射空气通道。2.4.3.2F.L.Smith公司Duoflex燃烧器丹麦F.L.Smith公司在总结过去采用三通道喷煤管Swirlex型和Centrax型燃烧器经验的基础上,与1996年推出了第三代水泥窑用喷煤管:双调节伸缩式Duoflex燃烧器(图2.29)。其特点·59·
Null 3耐火材料的性能耐火材料是高温工业的重要基础材料,广泛用于冶金、水泥、电力、机械、石油、化工等行业的各种工业窑炉。耐火材料是冶金工业和无机非金属材料工业的“支撑工业”和“先行工业”,耐火材料的品种、质量对高温技术发展起着关键作用。耐火材料的重要性主要体现在:影响炉子生产率(耐火材料如能耐更大的热负荷,炉子生产率可提高12%~20%),影响产品质量(提高耐火材料质量可以显著地减少由于耐火材料被侵蚀而进入产品的夹杂物,从而提高产品质量),影响炉子寿命,以及影响产品成本。研究耐火材料必须了解其性质,性质是评价质量的核心内容和基本依据,而耐火材料的性质又取决于其化学矿物组成和组织结构。在生产中工艺控制与改进的根本目的,就是为了获得具有特定性质的材料。性质是检查生产过程是否稳定的科学依据,也给制订和改进生产工艺提供了线索。性质是合理选用耐火材料的科学依据,了解直接反映实际使用意义的相关性质和间接反映实际使用意义的相关性质,并知晓相关的检验方法和取样要求,从而为我们正确选择耐火材料,合理地完成工业窑炉耐火材料的配置提供科学依据。耐火材料性能包括化学矿物组成、组织结构、热学性质、力学性质和高温使用性质等。3耐火材料的性能耐火材料是高温工业的重要基础材料,广泛用于冶金、水泥、电力、机械、石油、化工等行业的各种工业窑炉。耐火材料是冶金工业和无机非金属材料工业的“支撑工业”和“先行工业”,耐火材料的品种、质量对高温技术发展起着关键作用。耐火材料的重要性主要体现在:影响炉子生产率(耐火材料如能耐更大的热负荷,炉子生产率可提高12%~20%),影响产品质量(提高耐火材料质量可以显著地减少由于耐火材料被侵蚀而进入产品的夹杂物,从而提高产品质量),影响炉子寿命,以及影响产品成本。研究耐火材料必须了解其性质,性质是评价质量的核心内容和基本依据,而耐火材料的性质又取决于其化学矿物组成和组织结构。在生产中工艺控制与改进的根本目的,就是为了获得具有特定性质的材料。性质是检查生产过程是否稳定的科学依据,也给制订和改进生产工艺提供了线索。性质是合理选用耐火材料的科学依据,了解直接反映实际使用意义的相关性质和间接反映实际使用意义的相关性质,并知晓相关的检验方法和取样要求,从而为我们正确选择耐火材料,合理地完成工业窑炉耐火材料的配置提供科学依据。耐火材料性能包括化学矿物组成、组织结构、热学性质、力学性质和高温使用性质等。3.1耐火材料的化学矿物组成3.1.1化学组成化学组成是耐火材料的基本特征,是决定性能优劣的内因条件,是评定原料好坏、组织生产的依据。根据耐火材料中各种化·63·
null
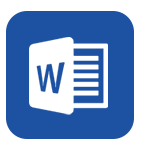