爆破事故的预防
在煤矿各类事故中,由于爆破引发的直接的或间接事故占煤矿事故的25%左右。爆破事故主要包括早爆、瞎炮、残爆、爆燃等。
一、早爆的预防
在运送爆破材料、制作引药、装药连线过程中发生的意外爆炸事故称为早爆。早爆事故是突然发生的,这时人员未撤离,危害极大。
在爆破施工中,杂散电流、静电感应、雷电、射频电等均可能引起电雷管早爆,在井下危害最大的是杂散电流及静电。
1.杂散电流的防治
杂散电流是指来自爆破电源以外的电流,它可能使电爆网络发生早爆,因此在井下爆破作业中,要经常监测杂散电流,当超过30mA时,必须采取可靠防治措施。
1) 杂散电流的来源
杂散电流主要来源于架线电机车的电气牵引网路漏电、动力或照明交流电路漏电、化学电、大地自然电流及电磁波的感应电流等。
2) 杂散电流的防治
① 加强杂散电流的检测工作,尽量减少杂散电流的来源,特别要注意防止架线电机牵引网路的漏电,可在铁轨接头处焊接铜导线以减少接头电阻;采用绝缘道碴或疏干巷道来增加巷道底板与铁轨之间的电阻等。加强井下机电设备的电缆的维护和检修工作,正确安装和经常检查接地装置。
② 确保电爆网路的质量,爆破导线不得有裸露接头,防止操作导线的绝缘包皮,雷管脚线及放炮母线在接入起爆电源前,均应扭接短路,防止杂散电流流入。 ③ 在爆区采取局部或全部停电的方法可使杂散电流迅速下降,必要时可将爆区一定范围内的铁轨、风水管等金属导体拆除,在装药连线过程中,避免启动和关闭电器。 ④ 及时清除撤落的硝铵炸药和巷道积水,以防止化学电。 ⑤ 尽量采用抗杂散电流电雷管。 2.静电的防治
静电是指绝缘物质上携带的相对静止的电荷,它是由不同的物体接触摩擦时在物质间发生电子转移面形成的带电现象。静电表现为高电压、低电流,静电电位往往高达几千伏特甚至上万伏特。
当高电位的带电体与零电位器或低电位物体接触形成不大的间隙时,就会发生静电放电火花,有可能引起爆区发生早爆事故。如果在瓦斯煤尘爆炸危险地点产生高压放电火花,还可能引起瓦斯煤尘爆炸事故。
预防静电的主要方法是尽量减少静电的产生和将已产生的静电电荷导入大地,以及研制抗静电雷管等。具体如下:
1) 在压气装药系统中采用半导体输药管。半导体输药管在低压时,导电性差,随着电压升高其导出性也相应提高,因而静电不易集聚。 2) 对装药工艺系统采取防静电措施,装药器和输药管都必须接地以防止静电集聚;操作人员应穿半导体胶靴,始终手持装药管,以便随时将身上的电荷导走;深孔装药完毕,再在孔口处装电雷管,以免在意志薄弱过程中引起的电雷管早爆;在意志薄弱期间,雷管的脚线应短路但不接地,以防止杂散电流和静电。 3) 采用抗静电雷管
4) 预防机械产生静电影响,对爆区附近的一切机械运转设备,除要有良好的接地外,雷管和电爆网路要尽量远离,必要时,在连接电爆网路到起爆前,可暂停机械运转。 5) 消除人体静电的产生,在要求高的爆破作业中,作业人员应穿防静电服装和鞋袜。井下工作人员严禁穿化纤衣服。
6) 采用喷雾洒水提高井下空气相对湿度,应采用湿式打眼,严禁干式打眼。 除了以上几种原因引起早爆外,还因注意:
1) 防止机器热能、冲击摩擦、挤压等引起的早爆事故。 2) 严格执行爆破材料的运输、贮存和使用制度。
3) 由于发爆器使用时间长,按钮或开头的接触片失去弹性,致使按钮虽断开,接触片仍处于接触状态。在发爆器充电过程中就有可能引起早爆事故或因充电电压不足引起拒爆,因此,应经常检查发爆器性能及内部结构,发现问题及时修复。为防止此类早爆引起人员伤亡,要等人员全部撤离危险区后方能开始充电起爆,并加强警戒,严禁先充电 后发警戒信号,式边充电边撤人,严禁用发爆器代替导通表进行电爆网路或电雷管的导通检查。
二、拒爆的预防与处理 通电后,雷管和药卷都不爆炸或雷管炸而药卷不爆炸的炮眼称为拒爆,拒爆不但影响爆破效果,而且给施工带来潜在威胁,处理拒爆不当也会酿成事故。
1.拒爆的原因
根据大量拒爆事故的调查分析,产生拒爆的原因主要有雷管、起爆电源、爆破网路、引药、炸药等几个方面。
2.拒爆的预防措施
1) 禁止使用不合格的爆破器材,不同类型、不同厂家、不同批量的雷管不得混用,爆破材料在使用前,须严格检查其质量和性能。
2) 连线后检查整个线路,查看有无连错或漏连,接头要悬空,并进行爆破网路的计算和起爆前的检测,实测值与计算值之差应小于10% 。
3) 经常检查发爆器和爆破母线,并对发爆器的起爆能力进行验算。
4) 装药前应认真清除孔内的岩(煤)粉,装药时要用炮棍轻推药卷和引药,防止捣实药卷使密度过大或捣坏雷管脚线。
5) 在有水和潮湿炮孔装药时,应采取有效的防水措施或选用抗水炸药。 6) 对硝铵类炸药要采取措施防止间隙效应的发生。 3.拒爆的处理方法
一旦发生拒爆,应立即警戒,并在班组长直接领导下进行处理,并应在当班处理完毕,如当班处理不完,爆破工必须的在现场向下一班交代清楚,并标出记号。处理拒爆时,不允许进行与处理拒爆无关的其他工作。
处理拒爆的方法如下:
1) 因连线不良、错连、漏连造成的拒爆可重新连线爆破,介重新连线爆破前,要检查工作面的顶板、支架和瓦斯情况,确认安全并确保起爆线路完好时,方可重新起爆。 2) 因其它原因造成的拒爆,则应在距至少0.3m处重新打一个和拒爆眼平行的新炮眼,重新装药爆破。重新打眼时,应先弄清楚拒爆眼的角度、深度,切不可距该眼太近,以免发生事故。
3) 处理拒爆时,严禁用镐刨;严禁从拒爆的炮眼中取出引药,或从引药中拉出雷管; 严禁用打眼的方法往外掏或用压风去吹炸药,也不准将炮眼残底(无论有无残药)继续加深,严防发生意外爆炸。 4) 对拒爆的炮眼进行爆破后,应详细检查并收集未爆炸的爆破材料,下班时交回爆破材料库。
三、残爆、爆燃、和缓爆的预防 1.残爆和爆燃
残爆是批炮眼里的炸药引爆后,发爆轰中断而残留一部分不爆药卷的现象。爆燃是炮眼里的药卷未能正常起爆,没有形成爆轰反应不完全,都可能产生灼热的固体颗粒和生成大量有毒气体,存在严重的安全隐患,特别在有瓦斯、煤尘爆炸危险的工作面,须引起充分重视。
造成残爆和爆燃的原因有:
1) 违反规定采用了盖药和垫药的装药结构,由于盖药和垫药牌引药传爆方向的反面,多数不易爆轰,易形成不稳定爆炸而衰减为爆燃或息爆,垫药一般留在眼底,盖药被抛入煤、岩堆中,或在燃烧中散落在煤、岩堆上,有可能引燃瓦斯、煤尘。
2) 装药前炮眼中煤、岩粉未清除干净,在装药过程中药卷间积有煤、岩粉隔层,使药卷不能密接,导致传爆中断或衰减成爆燃。
3) 在较深炮眼中,药卷和眼壁间存在间隙,由于间隙效应造成部分药卷拒爆或爆燃。 4) 装药时药卷被捣实,密度增大、传爆稳定性降低,造成爆燃或拒爆。 5) 炸药质量差,或在潮湿的水炮眼内未采用防水措施或抗水炸药,使炸药起爆敏感度下降; 或者雷管起爆能力不足,使药卷不能达到稳定爆轰,造成熄爆和爆燃。 残爆和爆燃的预防措施:首先应严格检查炸药雷管的质量,不合格的药卷和雷管不能使用,并按规定制作引药,装药前认真清除炮眼中的煤(岩)粉;其次装药时轻送炸药,不要猛力捣实药卷了,严禁采用盖药和垫药,并采取措施防止间隙效应发生。
2.缓爆
在爆破网路通电以后,炮眼内雷管按时爆炸后,炸药未能立即发生爆炸,但引起了炸药的热分解或爆燃,继而转为爆炸;或者雷管起爆量不正常,其传导和点燃时间过长,导致药卷非正常延期爆炸,这种现象称为缓爆。
发生缓爆的原因主要有:
1) 起爆能不足、炸药雷管变质、药卷密度过大或过小,炸药的热分解或爆燃形成的热量和压力在密闭的炮眼内逐渐积聚,使其转化为爆炸。此外,雷管的电引火装置和起爆药的质量不合格,也会引起缓爆。
2) 炮眼内药卷缓爆时间可达几分钟,甚至十几分钟或更长,往往发生在爆破工爆破后返回工作面检查时,因而最容易造成伤亡事故。所以,爆破后,不要过早地进入工作面进行检查和处理。
3) 预防缓爆的主要措施有:选用合格的炸药和雷管,装药密度应处于最佳密度之间,意志薄弱时防止 用力过猛捣实炸药;保证足够的起爆能,使炸药达到稳定爆轰;电雷管使用前严格检查其起爆能力和引火装置,确保电雷管的延期时间准确。
四、放空炮的防治 当炮眼中炸药爆炸后,形成的爆炸作用难以克服岩石的抵抗作用,爆炸气体沿炮眼喷出,只在眼壁和眼口处造成局部破坏,而不能按预期效果破碎岩(煤)体,这种现象称为放空炮。放空炮不公不能破碎岩(煤)体,达不到爆破的目的,而且喷出的高温高压气体的产物还可能引起瓦斯、煤尘爆炸,严重威胁矿井安全,必须引起足够的重视。
产生放空炮的原因主要有:爆破参数设计不合理或未按设计要求施工,造成炮眼密度过大或过小、装药量不足的等;炮眼封泥长度不够或封泥材料和质量不合要求;炸药雷管质量差、起爆能不足、传爆不稳定、爆炸威力小孩 起爆顺序不合理或雷管段别装错,造成后爆眼先爆,抵抗过大现象。
预防空炮的措施主要有:合理确定爆破参数,正确布置炮眼和确定起爆顺序;严格检查炸药雷管质量,不合格吕严禁使用;保证炮眼封泥长度和充填质量;采用合格的炮泥材料;严格按照爆破说明书和规程要求操作。
爆破后发现放空炮炮眼,必须的先检查其深度、角度,并在距其0.3m以上的地方重新打眼装药爆破。在有瓦斯工作面,须将放空炮的炮眼用黄泥封住,心防止炮眼里积存瓦斯,严禁在放空炮的炮眼中再装药爆破,严禁存放空炮的炮眼中重新夺得打眼 。
五、爆破崩倒支架和崩坏输送机的防治 1.爆破崩倒支架
爆破崩倒支架是引起工作面冒顶事故的主要原因之一,不利于顶板管理,而且易崩坏支架、使支架达不到要求的支撑力而失效、增加生产成本、危及工作面生产安全。此类事故虽严重性大的不多,但经常发生、累计起来危害很大,须引起重视。
爆破崩倒支架的原因主要有:支架架设不符合质量、规格要求,支架没打上劲、背得不实、棚顶空等,爆破前未经检查和加固处理;爆破参数选择不当,炮眼浅、装药量大,眼口朝向支架;爆破后有大块崩出,或抛出距离远、抛掷力大;支架紧靠煤壁、放炮前未松帮,炮道宽度不够等。
为防止爆破崩倒支架,应加强支架架设质量,爆破前进行检查,对南通市不合格的支架应进行加固,并松帮,保证支架与煤壁间留有一定宽度和炮道;合理选择爆破参数布置炮眼,严格按照爆破图表要求操作,并根据岩(煤)层条件、顶板情况及时调整炮眼布置和意志薄弱量;采用微差爆破技术,减少抛掷距离、改变抛掷方向,可大大减少爆破崩倒支架事故。
在回采工作面,如发现爆破崩倒支架现象,应先检查顶板,后被补支柱,并划紧背实,否则禁止进行其他工作。在掘进工作面,爆破后应由外向里检查支架与顶板,及时将崩歪和崩倒的支架重新打好,并要求插实背紧,钉好拉条。崩倒支架的地方发生局部冒顶时,应及时采用措施。
2.爆破崩坏输送机
爆破崩坏输送机不仅造成经济损失,而且影响生产。产生此类事故的原因有两方面:一是刮板输送机布置较高,衬垫不平稳,没有支撑和掩盖,溜槽间连接不紧;二是炮眼布置位置低,底眼俯角大,装药量多。
为预爆破崩坏输送机必须交刮板输送机摆平、摆直、摆稳、尽量降低溜槽高度,节与节之间连接要紧,并预先支撑和背实;合理布置炮眼,炮眼位置、角度要适宜,装药量不能过大,并采用合理的起爆顺序,先爆腰、顶眼、后爆底眼,减小向输送机溜槽方向的抛掷边。
六、炮烟熏人的预防
炮烟就是爆破后产生的烟尘,它既包括炸药爆炸后产生的有毒气体,又包含爆炸时产生的煤(岩)粉尘,当炮烟浓度较大或人长时间受到炮烟中的一氧化碳、氧化氮、硫化氢和二氧化硫等有毒气体的毒害时,往往会发生炮烟熏人事故。
1.造成炮烟浓度过大的原因
所用炸药质量低劣,变质严重,炮眼封泥不符合要求,炸药爆炸反应不完全,有毒气体生成量大;一次起爆炸药量过多,超过了工作面通风能力而不能在一定时间内将炮烟排出或者通风管理不善,工作面风量不足,炮烟不能及时排出,而作业人员提前进入工作面;掘进巷道过长,炮烟长时间游浮在巷道中,在局部通风机通风巷道,如因管理不善出现循环覍,或因通风距离长、阻力大、巷道中风流缓慢而不能及时排除炮烟;作业人员在回风道中距爆破地点较近、炮烟浓度大,如未能及时撤离,则易发生炮烟中毒。
2.炮烟熏人的预防措施
炸药爆炸产生的有毒气体,不仅对人体有害,而且还会对瓦斯爆炸起催爆作用。因此必须防止炮烟浓度超限,常用的预防措施有:
1) 选用质量合格的矿井许可炸药,并优先用有毒气体生成量少的的含水炸药;且要保证炮眼封泥长度和质量。
2) 一次爆破的炸药量要与通风能力相适应,每爆炸1kg炸药需要的风量不能小于25m/min。 33) 加强通风管理、减少漏风和通风阻力,局部通风机位置要符合规定、防止形成循环风,采掘工作面应避免串联通风。
4) 爆破前后,在爆破地点20m范围内要充分洒水、以便吸收、溶解部分有毒气体和粉尘,采掘工作面要实施综合防尘。
5) 爆破后要有足够的通风时间,炮烟被新鲜风流冲淡吹散后,作业人员方可进入工作面,在通过炮烟区时,要用湿毛巾堵塞住口鼻、迅速通过。
6) 爆破工作面排烟的回风巷道,应有足够的断面,不应长期堆积坑土、煤、矸等等障碍物,在距爆破地点一定距离的回风巷道中,最好持绳、立牌作为警戒,防止有人进入浓炮烟区。
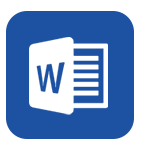