序
随着生产现场中的不良品管理水平的逐步提高,以及各部门整合,不良品管理系列规定C版本中的许多内容与实际不符,为使电冰箱生产现场中的不良品管理更上一层楼,产品质量能够满足用户的需求,特对其重新修订,推出不良品管理系列规定D版本。
D版本系列规定主要内容是从生产现场不良品的出现、责任判罚及退废过程中可能发生的一系列问题进行提前预防;同时重新明确各区域的质量管理规定、质量指标等,充分调动人员积极性,对不良吕管理进行全员参与,最大限度的减少不良品的出现。
该系列规定同C版本相比作了较大调整,主要修订了不良品区管理规定、外协件不良品退废程序,同时补充了不良品退废程序,质量事故考核规定,使生产现场不良品管理方面对问题处理作到有据可查,指导现场的生产。
检验处
二零零一年三月二十日
注:该版本的使用解释要归检验处
目录
1、不良品卡使用规定
2、不良品管理条例
3、不良品区管理规定
4、废品退废程序
5、箱门体发泡返修区管理规定
6、总装返修区管理规定
7、喷粉返修管理规定
8、外部责任不良品退废程序
9、回用品管理规定
10、呆滞品管理规定
11、质量事故考核规定
12、新产品不良品管理细则
注:若以前文件与本规定有冲突,按本规定执行。
1、不良品卡使用规定
1. 1生产现场中发现的不良吕,由发现者按一级上溯原则进行责任初判,及时填写不良品卡贴于不良品上,并送入不良品区隔离存放。
1. 2不良品卡的填写必须字迹清晰,名称具体年月日属实,“缺陷”一栏要写清楚缺陷性质,不得漏项(内容齐全,缺陷明确,责任到人),不良品卡必须由责任人签字或同工位或代班班长代签,代签人员必须在24小时内通知责任人。
1. 3进入不良品区的不良品由检验员负责判定状态,即为返修品或为废品,由检验处检验班长负责废品的责任判罚。
1. 4不良品卡要求一卡一物,对大宗原材料(例如:粉末、板料)可以以箱、件为单位填写不良品卡。 1. 5不良品卡一般应贴在不良品缺陷处,若缺陷较为隐蔽,应在缺陷处贴上胶带,将不良品卡贴于明显处,避免不良品卡随机出厂。
1. 6已退废品的不良品卡由财务处退废员汇总后交检验处存档统一管理。
1. 7对已返修合格的返修品的不良品卡由返修人员收卡作为返修工市场链工资的依据。
2. 不良品管理条例
2.1各区域内的不良品必须做到当班日清,特殊情况检验班长同意后可拖延至48小时。
2.2不得出现“三品”混放,即合格品、返修品、废品,必须标识清楚,各自入区,隔离存放。
2.3不得私自销毁、更改或代签不良品卡。 2.4不得私藏不良品或私自处理不良品。
2.5生产中出现的不良品必须随时进行不良品区。 2.6总装线上的不良品未经许可不得随便落地。 2.7不良品判废后回用件必须100%进行优先回用。 兑现方法:
若违反以上条例者,由发现者立即通知检验班长或现场管理员及车间主任或分厂厂长,由检验班长或现场管理员立即填写《质量整改单》明确整改期限,分厂车间主任或厂长必须无条件接受并找出区域责任人,明确整改方案及预防措施。若整改不合格或者24小时未反馈则须重新下发质量整改单,对相关人员加倍兑现。 兑现价值:
直接责任人-30元/次
本班班长-20元/次
车间主任-10元/次
本班检验员-10元/次
分厂厂长-10元/次
对发现者+20元/次
3.不良品区管理规定
3、1不良品区分为返修区与废品区。
3.2操作工在发现不良品后进行初步判断,需返修的填写不良品卡,送到返修区进行返修认为无法返修的,经检验员或检验班长确认送入废品区,并填好《不良品日清控制表》入区一栏。
3.3送入废品区的不良品必须妥善保管,尤其是箱/门体,避免碰伤。检验班长终判后,由退废员收取不良品卡,返修工对已判废件拆废,相关人员于退料单中签字后,出区,同时填写《不良品日清控制表》出区一栏。
3.4返修区域应由专人负责返修当班日清。特殊情况经检验班长同意后可拖延至48小时且两班交接清楚后方可下班。
3.5由各区域责任人负责返修区域的帐、卡、物相符,对无卡入区的不良品有权拒收,并且监督不良品卡的责任者必须是市场链上咬合出的责任人,对不符合者及时反馈质管员或现场检验班长。
3.6《不良品日清控制表》的填写与管理:
3.6.1表中“昨日结存”“今日入区”“待处理”于任何时候保持动态平衡即“昨日结存数”+“今日入区数”=“今日出区数”+“待处理数”。
3.6.2每一次出区必须在“待处理”栏内进行小结,若结存有余数,则在该栏记数与区域内实物相符。
3.7《月度不良品控制台帐》的填写与管理:
3.7.1分厂当班班长与现场检验员每天必须审核此表,核对并确认填写数据的真实性。
3.7.2该表的使用,规定为8:00-17:00,时间段17:00至次日8:00前的不良品总数,转入次日的“昨日结存”栏内。
3.7.3不良品日清率为当日出区数除以当日入区数。
3.8分厂班长至少每2小时审核一次不良品区,并在《不良品日清控制表》上签字确认,对不符合项按-5元/次考核责任者。检验处现场检验员每2小时复审一次,对不符合项立即纠偏,并对直接责任人及分厂班长按-5元/次进行考核。
3.9《不良品日清控制表》和《月度不良品控制台帐》由检验班长收取存档管理,保存二年后方可销毁。
4、废品处理程序
4、1生产过程中发现的不良吕由发现操作工或检验员填写不良品卡,进行责任初判后(发现者若为操作工,须经检验员确认)送不良品区进行隔离存放,(钣金、喷粉、吸附区域可先入不良品区,后由检验员员确认)现场检验班长对责任人进行终判。
4.2在生产现场中各废品区设置《每日不良品出入区控制台帐》及《不良品日清控制台帐》,每学4小时至少清理一次,若每超声波小时则按-1元/件索赔分厂当班班长及区域责任人(返修工)。 4.3对于同缺陷部件判废权按以下执行:
钣金、喷粉、吸区域:
20件以下由相关区域检验班长退废
20-30件由检验处现场管理员退废
30-60件由检验处延长退废
60件以上由部长退废
箱/门体发泡、总装、检测区域:
5件以下由相关区域检验班长退废
5-10件由检验处现场管理退废
10-15件由检验处处长退废
15件以上由部长退废
4.4对退料单中同缺陷部件废品的退废严格按以上权限签字执行。 4.5对于箱门体发泡、总装、检测区域,连续出现的同缺陷废品5件以上,钣金、喷粉、吸附区域性0件以上,分厂必须按三不庭原则追究管理位责任由质量厂长签字厂内通报后方可退废对于箱门体发泡沫塑料、总装、检测区域,连续出现的同缺陷废品5件以上,钣金、喷粉、吸附区域件以上的处理决定必须有部长的签字,全公司通报后方可予以退废。
4.6对于不同数量的不合格品退废时由退废员负责通知相关人员到废品区判废后方可破坏退废。
4.7相关退废人员无法在退料单中签字,不良品卡上一阶段有检验员判定状态的签字,检验签字及外部缺陷责任人的签字即可。
4.8退料单任何人不得随意涂改,若有改动须重新找相关人员签字确认,否则按-5元/件兑现责任人。
4. 9一经判为废品,由分厂操作工拆除可利用零部件,破坏至无法再利用拆废仅能在分厂废品区域内进行由退废员负责监督拆卸、破坏情况,若发现数量不符或可利用件未拆除 ,必须严格按废品价值10倍兑现分厂责任人。
4.10由废品库退废员对退料单进行闸口,必须要有相应权限的人员签字并且对废品的破坏程度进行审核,若发现有误,必须及时反馈检验处对责任作出考核,但发现不及时,则按-5元/件兑现废品库退废员。
4.11对于退废的外协件不良品,由外协检验员据《质量承诺书》以《处罚通知单》形式通知相关部门,对外协厂进行经济索赔。
4.12废品出厂开具出门证,必须经资材处、分厂会签。废品出厂时,由
经警对照物品检验,若审出不符合项按废品价值兑现配送处退废员责任确认无误后方可允许出厂。 4.13责任判罚程序:
4.13.1对于分厂内部原因千万的废品由发现者或质检员按一级上溯原则进行责任初判,由检验班长进行终判。
4.13.2对于外部原因不良品责任判罚10件以下由检验班长终判,10-20件由检验处现场管理员终判,20-30件由检验处长终判,30件以上由部长终判。
4.13.3相关责任人必须在不良品卡中签字。
4.13.4对于超过24小时存放于现场未找相关人员进行责任判罚该部分不良品责任价值由分厂承担,分厂负责人负责分解。
4. 14本规定的执行由检验处、配送处、劳人保处及审核队相关管理人员审核,对于违反以上规定者,按程序规定进行责任价值兑现。
5.箱门体发泡返修区管理规定
5. 1箱体发泡返修区内的不良品正常情况下保持在通常情况下台以内。若超过节台,返修人员应及时通知发泡班长停车组织返修返修止≤4台时可恢复生产,否则兑现返修人员及发泡班长各-50元/次。发泡区不得积压不良品,特殊情况如出现缺料、分层、模具等问题引起的批量不良品,必须在质量部门明确方案后在规定的时间内积极组织返修。
5. 2为及时发现产品缺陷,对发泡后至清修上线的在产数量明确规定,否则按不良品超标兑现发泡班长责任价值。 A.对145L以下在产箱体可存为50台。
B、145L以上在产箱体可存为40台。
5.3门体发泡不良品随出随清,发现废门体立即填写不良品卡,检验员确认后直接入废品区。对于可返修的门体发现后立即进行清理返修若返修门体积压超过10件,必须停车组织返修清理至≤5件,返方可继续生产,当班出现的不良品当班必须清理完毕,班后不得留存,否则按每次-50元/次兑现责任班长。
5.4箱体发泡返修人员对不良品必须认真返修并如实填写《返修记录》,对该缺陷的责任价值2小时内必须兑现到位。
5.5返修区域内的不良品必须做到当班日清,若两班交接时数量超过3台,所超出的不良品由上班返修人员承担责任价值-5元/台,上班发泡检验员-2元/台。
5.6发泡检验员至少每隔2小时对返修记录审核一次对填写不及时、不属实者作出考核。同时对返修人签发的价值券进行抽检,班后对返修工的返修记录进行确认对于在规定时间内未找责任人签字、记录填写混乱、态度恶劣者,报检验班长否决其当日工资。
5.7由发泡工艺员据检验员确认的返修记录表,填写返修人员的“三E”卡,月底计算出返修人员的工资,经检验处现场检验班长审核后报劳工处兑现。
6.总装返修区管理规定
6. 1检验员检出缺陷后在跟单上标记,转返修线进行返修对于检修人员不能清理的缺陷,必须填写不良品卡,责任人签字确认后贴于冰箱上,转返修线进行返修。
6.2返修人员对缺陷产品进行认真返修,并如实填写《返修记录》,对返修缺陷的责任价值2小时内必须兑现责任到位。
6.3返修线的不良品必须当班日清,若两班交接时数量超过3台,所超出的不良品由前检漏检验员兑现上班返修人员责任价值-5元/台。
6.4前排、前检漏检验员及检验班长随时巡检对查出的不符合项按-10元/项兑现责任人,相关工艺员-5元/项,对查出的严重不符合项或多次整改不到位或态度恶劣者否决当日维修所的。班后由1名前排检验员负责确认返修记录中的缺陷及数量。
6.5月底由总装工艺员对确认的返修记录计算出返修人员的工资,经检验处现场检验班长审核后报劳工处兑现。
7. 喷粉返修管理规定
7.1喷粉工序的返修区正常情况下,保持在40台以内,返工修区超过40台;返修人员应及时通知喷粉班长停产组织返修否则兑现喷粉班长-50元/次。
7.2二次喷粉后的不良品,不允许再次打磨,若三次喷粉则按A级质量事故处理,并按-100元/件激励责任人。
7.3喷粉区域于返修人员的工资所得必须为返修工件所得,返修工必须按一级上溯市场链进行责任总现。班后将所得工资记入“三E”卡,工艺员
对其确认检验班长进行巡检,若发现严重不符项且态度恶劣者,予以否决当日返修所得工资。月底由质管处技术科汇总,检验处现场检验班长审核后劳人保处兑现。
7.4正常生产过程中因设备原因千万的指标内废粉,至少5天清理一次,对超出指标的废粉兑现责任到位。 8. 外部责任不良品退废程序
8.1外协件部分:
为提高外协件质量水平,减少外协件不合格品的出现数量并及时日清,做到对外协厂的公开、公平、公正原则,针对现场外协件不良品数量的日趋增多,针对外协不良品退废程序规定如下:
8.1.1现场外协件不良品指现场操作工挑选出的不合格品或隐性缺陷不合格品(即成型后表现出缺陷的不合格品),现场操作工必须每日清理并由检验员确认不良品缺陷性质及数量,填写退料单和不良品卡。 8.1.2退料单与不良品卡时间必须一致,且为当日退废时间,相关权限人员(同缺陷部件10件以下由检验班长,10件以上进心0件以下由现场管理员,20件以上30件以下由检验处长,30件以上由部长)确认,手续齐全的情况下,由外检人员确认后退库,由外协厂家及时处理。 8.1.3存放于现场的外协件不良品若需8小时内未办理退料手续,则不良品价值由分厂承担。
8.1.4外协件不良品的责任判罚由检验处进行终判,若终判后,有异议,则由质管处仲裁。
8.1.5外协件不良品严重缺陷或责任模糊时,外协检验员须现场同现场检验人员共同确认。
8.1.6对于外观缺陷批量外协件,及时在工位或材料库进行开箱检查,严格按一级上溯原则进行责任判罚。
8.1.7钣金、喷粉、吸附、发泡、板材等技术性较强工序出现的外协件不良品10件以上,须由质管处相关工艺员确认写明意见方可退废。 8.1.8外协检验员每天对自己所管外协件不良品进行清理,对于严重缺陷必须对外协厂下《质量整改通知单》,对于连续两次出现严重缺陷的外协厂家停止供货,对积压外协件不良品过多不及时退料的工位兑现责任人-50元,车间负责人-30元。
8.1.9外协检验员参照退料单对外协厂家进行经济索赔,(公式为单台价格×台数×倍数),索赔根据《质量承诺书》,以《处罚通知单》的形式通知相关部门,一式四联,一联配套处,一联财务处,一联外协厂家,一联由外协统计存档。外协检验员对外协厂家索赔应作到公平、公正、公开原则,不能多罚,不能少罚,对于弄私舞弊者,视情节给予严重处理。 8.2工艺原因
8.2.1正常生产中,由于设备过滤出的粉末在指标范围内的均免于考核,但分厂必须提供出从上次退粉到这次退粉的用粉数量,以书面形式上交检验处,配套保管员签字确认检验处现场检验班长负责审核,建帐存档,凡超出指标的粉末其废品价值由分厂承担。
8.2.2对于钣金原材料每件上下2张顶底料均不作考核。退料程序同粉末的退料程序。
8.2.3对于质管处工艺、技术通知错误导致的不良品由质管处相关人员承担责任价值。
8.2.4对于工艺验证的不良品由质管处相关工艺员确认。每次不良品不
得大于3件。
8.2.5对于工艺解剖千万的不良品由工艺员确认即可,每周最多2台。
9. 回用品管理规定
9.1生产过程中出现的缺陷受各种因素限制,不能立即解决或避免更大的损失,在不引起最终性能降低,不会引起用户投诉的情况下,根据缺陷等级由责任分厂提出申请回用,并注明责任人。
9.2由分厂管理人员填写《回用品通知单》提出申请,表格一式三联由质管处会签使用意见。
9.3检验处最终裁定缺陷产品是否可以使用,判定回用品的可追溯办法,以《检验处信息传递单》形式宣贯到下工序检验员,车间方可使用。 9.4回用品可追溯性办法采用在一体式跟单中做出跟踪标记的办法实话可追溯性。
9.5办理回用品的权限如下: A级缺陷
不允许带缺陷运转
B级缺陷
由质管处长与检验处长联合批准 C级缺陷
检验延长或指定人员
D级缺陷
检验处现场管理员或检验班长
9.6缺陷产品若可回用,由检验处同时给责任分厂下发《质量整改通知单》,及时进行整改。并且按其废品价值的5%考核责任分犬 ,考核数额在回用品通知单中体现,月底由检验处汇总交劳工处兑现相关责任部门。 9.7合同产品不得使用不合格产品。
1.下发一张质量整改单对责任部门负责人落实价值-10元,对部门主管人员落实价值-20元,若整改部门为分厂,则对分厂厂长落实落实责任价
值-10元,对相应车间主任各落实价值-20元。
2.对下发质量整改单前出现的不良品和造成的损失,由检验处根据有关规定进行责任价值兑现,由责任部门落实到责任人。
3.对于问题的整改必须要有原因分析,必要时提供有关的见证性资料。 4.对于已出现的有处理意见,对处理意见有责任部门公布,由检验处报劳人保处兑现。
5.有解决和预防措施,并有见证性资料,缺少任何一项视为不可接受。 6.若对《质量整改单》不可接受,部门负责人承担责任价值20元,车间主任各承担责任价值50元。
7.对于质量整改拖期的,每拖期一天部门负责人承担责任价值5元,主管人员承担责任价值10元,若整改部门为分厂,每拖期一天分厂厂长承担责任价值5元,车间主任各承担责任价值10元,拖期5天视为不可接受。
8.对不可接受的重新下发《质量整改通知单》
9.对整改完成效果良好的,视情况予以奖励有关人员10-100元的奖励。
10. 呆滞品管理规定
10.1生产现场中所有半成品件的存放时间不得48小时,其中门封条的存放时间不得24得小时,若有超出则严格按废品对待,计算出成本价,由区域责任人承担,即时兑现。
10.2检验处检验人员巡检出的超时半成品以质量整改单形式通知由车间主任及质量厂长及所承担的废品价值。
10.3由于保龄球划处安排转产或质管处工艺更改导致的呆滞品,处理期限为三天,并报消化计划,否则皆按废品价值兑现相关责任部门。
10.4呆滞品的退废程序同现场生产中出现的不良品退废程序,若呆滞品价值达到一定限度,均按质量事故对管理位责任人处理。 10.5呆滞品判废后必须由责任人签字确认。
十一.质量事故考核规定 11. 1以下情况之一为重大质量事故 A. 造成直接经济损失4000元以上。
B.连续生产废吕后令其查找原因致使停产4小时以上。 C.连续出现A级缺陷10台以上。 11.2以下情况之一般质量事故
A造成直接经济损失4000元以下,500元以上。
B连续出现A级缺陷10台以下,3台以上,B级缺陷10台以上。 11.3凡发生重大质量事故,必须立即由发生部门填写《质量事故报告单》于24小时内报质管处,由质管处根据情节分别给予行政处分和按价值的10-20%落实责任价值,并将处理意见报部长室批准后执行。
11.4凡发生一般质量事故,必须立即由发生部门填写《质量事故报告单》于24小时内报检验处,并根据情节和返修品损失价值的5-10%,予以落实责任价值。
A. 重大事故:承担责任价值300元以上,退劳务市场。 B.一般事故:承担责任价值200元,工种下转。
11.6因责任心差未按要求进自互检或分析、预防审核而造成的: A. 重大事故:承担责任价值200元,工种下转。 B.一般事故:承担责任价值100元。
11.7每发生一次重大质量事故,对分厂质量厂长兑现责任价值-50元, 发生一次一般质量事故,分厂质量厂长兑现责任价值-30元,其余管理人员均按5.4规定兑现责任价值。
11.8如延误不报或弄虚作假,则加倍兑现分厂厂长及相关管理人员。如延误不报或弄虚作假,则对分厂厂长从严处理。
11.9各部门建立《质量事故登记台帐》,质管处负责建立《重大事故登记台帐》,检验处负责建立一般事故登记台帐。
11.10根据质量事故发生情况,月终由质管处对重大事故,检验处对一般质量事故分别总结报质管处,由质管处进行综合总结。
十二.新产品不良品管理细则
1.在新产品试制过程中对生产厂箱门体发泡区域均有一定不良品免于考核,在100台小批量试制阶段2%免于考核,在1000台批量试制阶段0.5%免于考核,其它皆考核生产分厂。
2.新产品试制期间由于设计失误导致的不良品责任由科研所承担,1000台以后阶段,技术资料移交质管处后,则由质管处承担。
3.新产品对于钣金、吸附新模具调模废品15件以内免于考核,对于箱门体发泡新模具废品3台以内免于考核。
4.老产品新发泡模具的调模废品数3台,吸附模具调模废品为模8模,钣金模具调模废品为5模。
5.平时正常调模废品2模免于考核,月底据企划处确认的换模单统一减免。
6.由于特殊原因所千万的废品数量100台以上,可由责任分厂提出申请进行减免,由质管处、检验处会签,部长批准后生效。
7.对于模具交接前因调试导致的不良品数超出指标的不良品数由设备处向外协单位进行索赔,对于交接后该部分不良品由责任分厂或设备处承担。
8.由设备处牵头新模具调试并确认指标内的不良品。
9.对于同总厂转产产品的模具调试按老产品新模具调试,并由设备处模具管理员确认指标内的不良品。
10. 对于海外事业部
一、二分厂转产模具高度均按正常换模调试。指标执行。
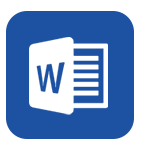