毕
系 别:班 级:学生姓名:学 号:指导老师:业 实习报 告
机械与动力工程系 机制09级2班 胡楠 0828070158
目录
一、冲压的意义特点及其材料„„„„„„„„„„„„„„„„1
(一)冲压
(二)加工特点
(三)冲压材料
(四)冲压模具
二、热成形极限实验模具的设计„„„„„„„„„„„„„„„6
(一)模具结构
(二)22MnB5钢板的热成形极限试验
三、高强度钢板应用及其成形问题„„„„„„„„„„„„„„9
(一)高强度钢板的应用
(二)高强度钢板成形存在的主要问题
(三)高强度钢板的性能及成形特点
(四)高强度钢板力学性能
(五)高强度钢板的成形特点
四、汽车用高强度钢热成型技术„„„„„„„„„„„„„„„11
(一)汽车用热成形高强度钢
(二)高强度钢板热成形加工工艺
(三)国内外研究现状
(四)热成形技术的应用发展
五、结束语„„„„„„„„„„„„„„„„„„„„„„„„17
六、参考文献 „„„„„„„„„„„„„„„„„„„„„„18
高强钢板热成形极限胀形实验模具设计及工艺分析
一、冲压的意义特点及其材料
(一)冲压
冲压靠压力机和模具对板材、带材、管材和型材等施加外力,使之产生塑性变形或分离,从而获得所需形状和尺寸的工件(冲压件)的成形加工方法。冲压和锻造同属塑性加工(或称压力加工),合称锻压。冲压的坯料主要是热轧和冷轧的钢板和钢带。全世界的钢材中,有60~70%是板材,其中大部分经过冲压制成成品。汽车的车身、底盘、油箱、散热器片,锅炉的汽包,容器的壳体,电机、电器的铁芯硅钢片等都是冲压加工的。仪器仪表、家用电器、自行车、办公机械、生活器皿等产品中,也有大量冲压件。浅谈高强度钢板的冲压应用
介绍了高强度钢板在汽车白车身结构上的应用及其在冲压成型过程中容易产生的质量缺陷。根据高强度钢板的力学性能及及其成型特点,冲压工艺设计及其模具结构设计上提出解决高强度钢板难成型的措施。
冲压加工是借助于常规或专用冲压设备的动力,使板料在模具里直接受到变形力并进行变形,从而获得一定形状,尺寸和性能的产品零件的生产技术。板料,模具和设备是冲压加工的三要素。按冲压加工温度分为热冲压和冷冲压。前者适合变形抗力高,塑性较差的板料加工;后者则在室温下进行,是薄板常用的冲压方法。它是金属塑性加工(或压力加工)的主要方法之一,也隶属于材料成型工程技术。
冲压所使用的模具称为冲压模具,简称冲模。冲模是将材料(金属或非金属)批量加工成所需冲件的专用工具。冲模在冲压中至关重要,没有符合要求的冲模,批量冲压生产就难以进行;没有先进的冲模,先进的冲压工艺就无法实现。冲压工艺与模具、冲压设备和冲压材料构成冲压加工的三要素,只有它们相互结合才能得出冲压件。
(二)加工特点
冲压件(图1)与铸件、锻件相比,具有薄、匀、轻、强的特点。冲压可制出其他方法难于制造的带有加强筋、肋、起伏或翻边的工件,以提高其刚性。
1
图1 冲压件
由于采用精密模具,工件精度可达微米级,且重复精度高、规格一致,可以冲压出孔窝、凸台等。冷冲压件一般不再经切削加工,或仅需要少量的切削加工。热冲压件精度和表面状态低于冷冲压件,但仍优于铸件、锻件,切削加工量少。
冲压是高效的生产方法,采用复合模,尤其是多工位级进模,可在一台压力机(单工位或多工位的)上完成多道冲压工序,实现由带料开卷、矫平、冲裁到成形、精整的全自动生产。生产效率高,劳动条件好,生产成本低,一般每分钟可生产数百件。如冲压三通(图2)与机械加工及塑性加工的其它方法相比,冲压加工无论在技术方面还是经济方面都具有许多独特的优点主要表现如下。
冲压加工的生产效率高,且操作方便,易于实现机械化与自动化。这是因为冲压是依靠冲模和冲压设备来完成加工,普通压力机的行程次数为每分钟可达几十次,高速压力要每分钟可达数百次甚至千次以上,而且每次冲压行程就可能得到一个冲件。
图2 冲压三通
2
冲压时由于模具保证了冲压件的尺寸与形状精度,且一般不破坏冲压件的表面质量,而模具的寿命一般较长,所以冲压的质量稳定,互换性好,具有“一模一样”的特征。
冲压可加工出尺寸范围较大、形状较复杂的零件,如小到钟表的秒表,大到汽车纵梁、覆盖件等,加上冲压时材料的冷变形硬化效应,冲压的强度和刚度均较高。
冲压一般没有切屑碎料生成,材料的消耗较少,且不需其它加热设备,因而是一种省料,节能的加工方法,冲压件的成本较低。由于冲压具有如此优越性,冲压加工在国民经济各个领域应用范围相当广泛。例如,在宇航,航空,军工,机械,农机,电子,信息,铁道,邮电,交通,化工,医疗器具,日用电器及轻工等部门里都有冲压加工。不但整个产业界都用到它,而且每个人都直接与冲压产品发生联系。像飞机,火车,汽车,拖拉机上就有许多大,中,小型冲压件。小轿车的车身,车架及车圈等零部件都是冲压加工出来的。据有关调查统计,自行车,缝纫机,手表里有80%是冲压件;电视机,收录机,摄像机里有90%是冲压件;还有食品金属罐壳,钢精锅炉,搪瓷盆碗及不锈钢餐具,全都是使用模具的冲压加工产品;就连电脑的硬件中也缺少不了冲压件。
弯曲:将金属板材、管件和型材弯成一定角度、曲率和形状的塑性成型方法。弯曲是冲压件生产中广泛采用的主要工序之一。金属材料的弯曲实质上是一个弹塑性变形过程,在卸载后,工件会产生方向的弹性恢复变形,称回弹。回弹影响工件的精度,是弯曲工艺必须考虑的技术管件。
拉深:拉深也称拉延或压延,是利用模具使冲裁后得到的平板坯料变成开口的空心零件的冲压加工方法。 用拉深工艺可以制成筒形、阶梯形、锥形、球形、盒形和其他不规则形状的薄壁零件。如果与其他冲压成形工艺配合,还可制造形状极为复杂的零件。在冲压生产中,拉深件的种类很多。由于其几何形状特点不同,变形区的位置、变形的性质、变形的分布以及坯料各部位的应力状态和分布规律有着相当大的、甚至是本质的差别。所以工艺参数、工序数目与顺序的确定方法及模具设计原则与方法都不一样。各种拉深件按变形力学的特点可分为直壁回转体(圆筒形件)、直壁非回转体(盒形体)、曲面回转体(曲面形状零件)和曲面非回转体等四种类型。
3
拉形:是通过拉形模对板料施加拉力,使板料产生不均匀拉应力和拉伸应变,随之板料与拉形模贴合面逐渐扩展,直至与拉形模型面完全贴合。拉形的适用对象主要是制造材料具有一定塑性,表面积大,曲度变化缓和而光滑,质量要求高(外形准确、光滑流线、质量稳定)的双曲度蒙皮。拉形由于所用工艺装备和设备比较简单,故成本较低,灵活性大;但材料利用率和生产率较低。
旋压是一种金属回转加工工艺。在加工过程中,坯料随旋压模主动旋转或旋压头绕坯料与旋压模主动旋转,旋压头相对芯模和坯料作进给运动,使坯料产生连续局部变形而获得所需空心回转体零件[2]。
(三)冲压材料
冲压用板料的表面和内在性能对冲压成品的质量影响很大。对于冲压材料的要求是:
厚度精确、均匀。冲压用模具精密、间隙小,板料厚度过大会增加变形力,并造成卡料,甚至将凹模胀裂;板料过薄会影响成品质量,在拉深时甚至出现拉裂。
表面光洁,无斑、无疤、无擦伤、无表面裂纹等。一切表面缺陷都将存留在成品工件表面,裂纹性缺陷在弯曲、拉深、成形等过程可能向深广扩展,造成废品。
屈服强度均匀,无明显方向性。各向异性(见塑性变形的板料在拉深、翻边、胀形等冲压过程中,因各向屈服的出现有先后,塑性变形量不一致,会引起不均匀变形,使成形不准确而造成次品或废品。
均匀延伸率高。抗拉试验中,试样开始出现细颈现象前的延伸率称为均匀延伸率。在拉深时,板料的任何区域的变形不能超过材料的均匀延伸范围,否则会出现不均匀变形。
屈强比低。材料的屈服极限与强度极限之比称为屈强比。低的屈强比不仅能降低变形抗力,还能减小拉深时起皱的倾向,减小弯曲后的回弹量,提高弯曲件精度。
加工硬化性低。冷变形后出现的加工硬化会增加材料的变形抗力,使继续变形困难,故一般采用低硬化指数的板材。但硬化指数高的材料的塑性变形稳定性好(即塑性变形较均匀),不易出现局部性拉裂。
4
在实际生产中,常用与冲压过程近似的工艺性试验,如拉深性能试验、胀形性能试验等检验材料的冲压性能,以保证成品质量和高的合格率。
(四)冲压模具
图3 冲压
模具的精度和结构直接影响冲压件的成形和精度如图3。模具制造成本和寿命则是影响冲压件成本和质量的重要因素。模具设计和制造需要较多的时间,这就延长了新冲压件的生产准备时间。模座、模架、导向件的标准化和发展简易模具(供小批量生产)、复合模、多工位级进模(供大量生产),以及研制快速换模装置,可减少冲压生产准备工作量和缩短准备时间,能使适用于大批量生产的先进冲压技术合理地应用于小批量多品种生产。
二、热成型极限实验模具的设计
(一)模具结构
结合超高强度钢板高温胀形试验要求,参照GB/T15825.8~2008《金属箔板成型性能与试验方法,第八部分:成型机线图(FLD)测定指南》,本课题组自行设计并制造了满足高温胀形实验功能要求的模具如图4所示。
模具的运动过程是:首先利用安装在卸料板上的定位销是毛坯定位,凸模在压力机活塞的作用下想下运动,依靠聚氨酯产生的巨压扁力,通过拉延筋将板料压死,然后凸模对板料胀形。通过一定的试冲,调整限位块控制凸模行程,然后凸模上行。超高强钢板的高温胀型模具,在模具结构和功能要求上与传统的冲压模具有很大的区别:配料定位要求快速准确。由于高温板料在空气中的暴露时间不会过长,否则坯料温度下降过多,因此坯料必须能够在模具中迅速定位。模具材料需有良好的热力学性能。
5
图4 模具结构主视图
高温坯料的热量部分将通过模具散失,势必造成模具温度升高,尤其表面温度上升剧烈。在如此恶略的工作条件下,模具还必须有足够高的硬度能抵御与坯料发生热摩擦。
模具须有一定的隔热能力,减少模具对板料的降温。以实现不同高温断下,进行胀形实验。
(二)22MnB5 钢板的热成形极限试验
采用刚性凸模膨胀试验方法,通过改变式样宽度实现不同的应变路径,采用坐标网格应变分析方法,获得22MnB5钢板高温状态下的和成分表1和成形极限图(FLD)图5。
表1 22MnB5成分化学成分组成(%)
6
图5 成形极限图 1.试件制作
按照GB/T15825.8-2008,试样为矩形,试样长度为180mm,宽度分别取180、160、140、120、100、80、60、40、20mm共9种。随着宽度从180mm减小到20mm,应变状态也实现了从双向拉伸到平面应变再到单向拉伸的转变。采用坐标网格应变分析方法并结合本试验条件的要求,采用光化学蚀刻法印制直径2.5mm的圆网格。光化学蚀刻方法印制在钢板上网格即使经过高温热处理过程,冷却至室温后仍然清晰可见。 2.试验流程
为使试验结果更准确地反应超高强度钢板在热冲压成形过程中的成形性能变化,更科学地指导后续研究,故依照使劲热冲压成形工艺过程来设计本实验。
试验流程:现在电炉里把试件加热到900摄氏度,保温5min已获得均匀的奥氏体组织。快速将时间转移至模具中(大约经过4s),然后以50mm/s进行快速冲压。事先在模具卸料板上铺上厚度为0.8mm的绝热石绵纸以减少时间温度的下降,同时通过红外测温仪检测试验的温度变化。 3.试验结果
尽管有石棉纸起到一定的隔热效果,试件在冲压过程中还是会有降温,试件的初始平均胀形温度为813摄氏度,终了温度为796摄氏度,本文视其在800摄氏度时等温成形。试验得到的最终试件如图6所示:
7
图6 高温胀形试验试件
选择靠近裂纹区或颈缩区的网格点作为临界点,通过应变分析软尺测量该区域网格变形。最终得到22MnB5钢板800摄氏度下的成形极限图,如图5所示。
三、高强度钢板应用及其成型问题
(一)高强度钢板的应用
近年来,高强度钢板已经逐渐成为汽车工业中发展最快的轻质金属材料之一,在汽车上的应用比例不断增加,已经成为颇具竞争力的汽车轻量化材料,具有很大的优势。
从节能方面考虑,减小汽车净重量,可以减低油耗。研究表明汽车重量减小1%,可节省燃料消耗0.6%~ 1%。各车型轿车设计空车净重量一般为汽车总重量的60%~80%,如采用轻量化材料,将对轿车性能节能具有重要的意义。
高强度钢板在成本与强度方面,具有很强的优势,其采用成为汽车轻量化最具竞争力的有效应用。
(二)高强度钢板成型存在的主要问题
高强度钢板虽然在汽车上应用的比例增加,但是钢板高强度化容易引起塑性下降,成形性变差,而屈服强度的提高,则引起畸变和回弹效应,增加形状不稳定性,因而高强度钢板是一种难成行的材料。典型的成型却鲜有拉毛、形状不合、尺寸精度不良和卡模具等。
零件拉毛。拉毛是在两个相对滑移的固体之间产生的一种肉眼可见的表面损伤。零件拉毛是高强度钢板冲压成型的过程中常见的缺陷之一。对于汽车覆盖件而言,零件的拉毛直接影响着覆盖件的表面品质,微笑的拉毛可能会在零件涂漆后引起管线漫反射而影响汽车外覆盖件的光泽,颜色等。较大的拉毛缺陷,可能会导致尤其无法覆盖而造成零件报废。此外,由于其需要大的成型力,连续加工
8
时,若磨具温度升高,则零件与模具摩擦阻力加大进而发生粘着,造成零件严重拉毛,使得模具表面损伤,造成修模次数增加。
形状不合。高强度钢板相对于普通钢板屈服强度较高,所需要的成型力也很高,导致模具拉严禁不能有效控制配料的流动,使得零件易发生起皱现象。起皱不仅会造成零件卡模和裂纹,也难以在成型后期消除,其结果往往导致形状不合。由于不能在成型后起消除起皱,冲压件不能再下死点成型;而且成型后的弹性后附引起的形状不良以及起皱引起的面应变也是很大的问题。
尺寸精度不良。高强度钢板强度升高时,残余应力增大,成型后的卸载过程中内弹性应变能的释放,应力得到重新分布后,零件形状也发生改变。当回弹量超过容差后,就成为成型缺陷,影响零件的尺寸精度,导致零件最重的形状不合格。这是高强度钢板成形中最为严重的问题,回弹引起以冲压件角度不合和面翘曲;随着材料强度的提高,角度不合格和面翘曲变得严重。
模具损伤。高强度钢板成型力,一时坯料与模具的接触压力增大。这样,易发生零件与模具黏着现象,导致模具表面损伤严重,影响模具寿命。若这一现象更为严重,则需要修正模具,这不但需要有更为合适的材质对模具进行表面处理和淬火处理,还增加模具成本及维修费用。
(三)高强度钢板的性能及成型特点
如上所述,高强度钢板在冲也成型时易产生拉毛、起皱、回弹等形状、尺寸精度不良等缺陷,为了有效解决高强度钢板成型特点入手研究,采用合适的冲压工艺及其模具设计方法。
(四)高强度钢板力学性能
抗拉强度高,成型力随着拉伸深度的增加而急剧增加,回弹量也随之相应增加;含碳量和合金元素的增加降低了材料的成型性能;深拉伸时,搞得成型力和变形量将增加起皱的趋势;材料剪切强度高,剪切力增加。
(五)高强度钢板的成型特点
高强度钢板的成型方法不同于普通钢板,DC0
1、DC0
4、DC06及B340等普通钢板的成型方法,属于基础常规的方法,但440、590、780等高强度钢板的成 型方法,侧有明显的不用。
9
四、汽车用高强度钢热成型技术
(一)汽车用热成型高强度钢
长期以来,钢铁一直是汽车工业的基础,虽然汽车制造中铝合金、镁合金、塑料及复合材料的用量不断增加,但高强度钢以其具有的高减重潜力、高碰撞吸收能、高疲劳强度、高成型性及低平面各向异性等优势[1,2],已经成为汽车工业轻量化的主要材料。21世纪的汽车行业以降低燃料消耗、减少CO2和废气排放成为社会的主要需求,为适应这种发展趋势,钢铁业已开发出许多种类的高强度钢板来帮助减轻汽车质量,同时提高汽车的安全性。为兼顾轻量化与碰撞安全性及高度下冲压件回弹与模具磨损等问题, 热成型高强度钢及其成型工艺和应用技术应运而生。目前凡是达到U-NCAP碰撞4 星或5 星级水平的乘用车型, 其安全件(A/B/C 柱、保险杠、防撞梁等)多数采用了抗拉强度为1 500 MPa、屈服强度为1 200 MPa 的热成型高强度钢。同时, 为解决高强度钢冷成型中的裂纹和形状冻结性不良等问题,出现了热冲压成型材料,已用其进行了强度高达1 470 MPa 级汽车部件的制造。本文首先介绍高强度钢热成型加工工艺及其关键技术然后分析了国内外热成型研究成果与现状,最后对热成型技术的应用发展进行了展望。
(二)高强度钢热成型加工工艺 1.热成型加工工艺 (1)理论基础
与传统的冷成型工艺相比, 热成型工艺的特点是在板料上存在一个不断变化的温度场。在温度场的影响下,板料的基体组织和力学性能发生变化,导致板料的应力场也发生变化, 同时板料的应力场变化又反作用于温度场, 所以热成型工艺就是板料内部温度场与应力场共存且相互耦合的变化过程。这就要求热成型用钢板的成分要适应热成型过程中的热循环。 (2)加工工艺
热成型工艺过程为:首先将常温下强度为500~600 MPa 的硼合金钢板加热到880~950 ℃,使之均匀奥氏体化,然后送入内部带有冷却系统的模具内冲压成型,最后快速冷却,将奥氏体转变为马氏体,使冲压件得到硬化,大幅度提高强度。这个过程被称为“冲压硬化”技术[3]。实际生产中,热冲压工艺又分为直
10
接工艺和间接工艺。直接工艺即下料后直接将钢板加热然后冲压成型,主要用于形状简单且变形程度较小的工件;对于形状复杂或拉深深度较大的工件则需要采用间接工艺,即先将下好料的钢板进行预成型,然后再加热实施热冲压。 2.热成型加工关键技术
高强度钢板的热成型技术的关键是用钢选择、钢的表面镀层、模具设计及热成型零件的检测。 (1)热成型用钢选择
目前,热成型用钢均选用硼钢,因微量的硼可有效提高钢的淬透性,使零件在模具中以适当的冷却速度获得所需的马氏体组织,从而保证零件的高强度水平[4,5]。而且硼合金钢板的强度可达到1500MPa,是普通钢板强度的3~4 倍,将其应用于汽车车身上不仅可直接减少料厚,减轻车身质量,还可提高车身的被动安全性。钢板的热成型性主要包括深冲成型性、胀形成型性、延伸凸缘成型性及弯曲成型性等。通常深冲成型性取决于钢板的r值;胀形成型性取决于钢板的延性(均匀延伸性或加工硬化指数);延伸凸缘成型性及弯曲成型性则取决于钢板的局部变形能和显微组织均匀性。硼在延伸凸缘成型性和弯曲成型性的显微组织均匀化方面起到了重要作用,其中22MnB5钢的成型原理与此相符,是典型的热冲压高强度钢,它利用微量的硼元素,通过热成型后快速冷却的方法获得高的成型性和极高的强度。目前,热成型MnB钢板在欧美和日本等主要汽车制造企业已经开始使用。
(2)热成型用钢的表面镀层
在热成型过程中如图7,钢板在高温下暴露于空气中会引起表面氧化而形成氧化铁皮,为不影响涂装工序,热成型后的面的氧化铁皮,这无形中增加了生产成本。而且钢板在氧化的同时也会引起钢板表面的脱碳,进而影响钢板的强度。此外,随着汽车零件耐腐蚀性能要求越来越高,表面进行镀层处理的钢板越来越受到人们的重视,一系列热成型用镀层钢板被相继开发出来。同常规的冷成型用镀层钢板不同,热冲压用钢板的镀层需要具备抗高温和耐腐蚀的特点。目前开发的用于热成型的镀层板包括镀Al板、镀零件需要经过喷丸或酸洗去掉钢板表Al-Si合金板和镀Zn板等。韩国POSCO钢铁公司正在开发纳米镀层板,以提高镀层的结合力,防止镀层在加热和成型淬火过程中剥落。
11
图7 热成型过程中22MnB5 钢的性能变化示意图
(3)热成型模具设计
在热成型过程中,钢板及模具都要经过从室温到900 ℃以上的温度变化, 并且模具集板料成型与冷却淬火过程于一身,所以模具设计是热成型技术的另一个难点[6,7]。其主要技术包括模具表面设计、模具冷却系统设计和模具结构设计等,可利用ABAQUS、LS-DYNA 等软件进行成型模拟和冷却过程模拟。利用材料的高温性能,如流变曲线、摩擦因数、FLD 等参量进行成型模拟,同时进行热传递模拟,这一过程实际是热力学、机械学耦合模拟过程。模拟结果将作为模具设计的重要依据,并据此进行试生产或批量生产。 ①模具材料的选择
热成型的模具材料不仅要求其具有良好的热强度、热硬度、高的耐磨性和疲劳性能,而且要能保证成型件的尺寸精度[8],同时要能够抵抗高温板料对模具产生的强大热摩擦、脱落的氧化层碎片及颗粒在高温下对模具表面的磨损效应, 并且能够稳定地在剧烈的冷热交替环境下工作。根据模具需要的加热温度,参考热锻用热作模具钢,选用合理的模具材料。如蒂森的热冲压模具就采用了一种具有很高热传导系数的Al2O3/Cu 复合材料。 ②模具凸、凹模设计
由于热胀冷缩的影响,零件最终尺寸与冲压成型时的尺寸存在一定误差,因此为保证零件的尺寸精度,在确定凸、凹模尺寸时必须考虑热胀冷缩效应。
12
③冷却机构的设计
对于热成型零件冷却机构的选择不仅要保证零件的冷却速度足够快, 而且还要避免零件和模具因冷却速度过快而引起的开裂。通常采用在模具内通冷却水的方式对成型后的零件进行冷却。 ④热成型工艺的缺点
零件成型后冷却速度和保压时间较难控制。
热成型件冷却至室温的过程中,不同部位冷却速度不同会导致零件发生严重变形,从而影响成型零件的尺寸精度。
由于热成型零件后续加工难度大,因而只能应用于一道工序即可成型的简单零件(如梁、柱等)。同时,热成型工序并入现有冷成型车间的难度较大。
由于受到模具材料的强度、模具热处理工艺、高应力集中、模具表面温度频繁升高和降低等诸多因素的影响,热成型模具容易失效,导致模具使用寿命降低。这些因素的存在,直接导致了现阶段热成型加工的成本增加、难度增大,使得热成型工艺的应用具有一定的局限性。但是,随着热成型技术的进一步发展,这种局面会进一步改善。 ⑤热成型零件的检测
热成型零件的加工通常需要经过激光切割、冲裁孔、点焊、冷成型、装配及油漆等工序,因此需要对热成型零件进行力学性能检测、形状检测、厚度分布检测等,还要根据不同零件的不同要求,采用不同的方法进行实物性能检测。一个合格的热成型零件应满足高强度、轻量化和安全性的要求,同时还应具备强度与韧性的结合性、尺寸稳定性、可加工性及可焊接性等。
(三)国内外研究现状
国外许多学者对高强度热成型用钢——硼钢做了大量的研究[9,10]。美国的B.Shapiro针对2008年国际板料成型数值模拟会议(NUMSHEET)的Benchmark BM03标准考题,使用LS -DYNA对22MnB5钢进行车身B柱的热成型数值仿真分析,提供了热成型数值仿真中的关键技术参数,包括材料模型的选用、热力机械性能参数、一定应变速率下的应力应变曲线等。并且分别选用MAT-106与MAT-244 材料模型进行研究,最后还提供了详细的仿真过程及计算结果与分析。德国的David Lorenz[12]及瑞典的G.Bergman与M.oldenburg[13]采用LS-DYNA 显式积分计[11] 13
算对高强度钢板进行热冲压成型及淬火冷却仿真分析。提出使用TSHEL(Thermal Shell Element)单元建立有限元模型,通过不同时间步长的热力机械耦合分析实现了单元在平面及厚度方向上的热接触传导,并通过试验验证了TSHELL 单元建模的有效性。瑞典的Paul Akerstrom以试验为基础对硼钢热成型过程的数值模拟方法进行了研究。提出了一种建立高强度钢热成型仿真模型的方法, 准确地预测了板料的变形和力学响应性能。其研究成果表明,准确、可靠的材料模型是提高高强度钢热成型数值模拟精度的关键。
(四)热成型技术的应用发展
我国首家热冲压零部件有限公司于2005 年在宝钢成立, 用于热冲压成型的高强度钢—— 硼钢由上海宝钢供货。宝钢生产的硼钢牌号分别为BR1500HS (1.85 mm 以上热轧)和B1500HS(1.85mm 以下冷轧),对应于欧洲热冲压高强度钢22MnB5,其屈服强度为1000 Mpa、抗拉强度为1400 Mpa,延伸率为5%。从2005 年开始,试制生产线已完成车身165 个零件的试制,其中12个样件一次试制成功,近年来,热冲压件在车身上的应用越来越广泛。大众公司在最新的第6代PASSAT车型中有9个部件使用MnB 钢板,在新型Golf V6 车型中有5个部件使用MnB 钢板,使用高强度热成型钢板的部件包括A/B/C 柱、加强板、中央通道、保险杠支架等。然而,在车身零部件强度提高的同时,热冲压件的冲击韧性受到越来越多的关注。这是因为其微观组织由非常硬的马氏体构成,所以导致韧性降低。而在车身碰撞试验中,这些零件通常放在承受很高冲击载荷的位置,但是目前还没有可靠的材料可用来进行韧性与脆性之间的转换,所以这是热成型钢在今后发展中亟待解决的问题。国外有关机构已经开始对这一问题进行相关研究,如蒂森最近在对淬火-回火的厚坯的研究中提到,微量铌元素的应用可提高热成型钢的韧性。
五、结束语
本文参照GB/T 15825.8~2008并集合22MnB5钢板的热冲压成形的工艺特征,结合扫了高强度分钢板的热成形极限试验方法。在此基础之上,设计制造了能满足高温胀形要求的热成形极限试验模具,进行了高温下的热成形极限试验。通过坐标网格应变分析方法,以及利用光化学蚀刻方法将网格印制在钢板上,得到了800℃下22MnB5钢板的成形极限图,对研究22MnB5钢板的热成形性能具有重要
14
意义。高强度钢的应用已成为满足汽车减重和增加碰撞性能及安全性能的重要途径,但常规高强度钢在室温下不仅变形能力差,而且塑性变形范围窄,所需冲压力大,容易开裂,同时成型后零件的回弹增加,导致零件尺寸和形状稳定性变差。因此,传统的成型方法难以解决高强度钢板在汽车车身制造中遇到的问题,而热冲压成型技术解决了上述问题。近年来,世界各国汽车业投入大量的精力来开展以硼钢为主的先进高强度钢板开发及热成型技术的研究,并取得了长足的发展。这项技术在我国还属于起步阶段,因此有关高强度硼钢热成型技术的研究对我国汽车工业的发展具有重要意义。
六、参考文献
[1,2]陈和清,彭成宇,魏良庆.高强度钢板及其在汽车制造中的应用[J].模具工程,2007(8):41~46 李小海,模具设计与制造2011,5(3):53~54 [3]郑家贤,冲压零件的工艺性机械工业出版社 1995,第三章8.4:67~73 [4,5]周树银,李琳,曹毅杰主编.冲压模具设计及主要零部件加工,北京理工大学出版社; 第1版
徐政坤,冲压模具设计与制造(5-
4、5-6).化学工业出版社2009-6,2-4:33~35 [6,7]孙彩华.高强度钢板折弯工艺探讨[J].煤矿机械,2002(11) [8]胡琦.超高强钢度硼钢板热冲压的力学性能研究[D].同济大学2008.[9,10]王立影.超高强度钢板热冲压成形技术研究[D].同济大学,2008.[11] Heller T, End B, Ehrhardt B,et al.New High Strength Steels Production, Properties & Applications.40th MWSP Conf Proc, ISS, 1998.25234.[12]Shi M F, Thomas G H, Chen X M.Formability Performance Comparison Between Dual Phase and HSLA Steels.43th MWSP Conf Proc.ISS, 2001, 1652174.[13]谷诤巍,单忠德,徐虹.汽车高强度钢板冲压件热成型技术研究.模具工业,2009,35(4):27~29.
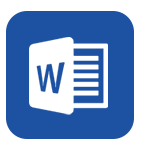