一、工程概况
1.镔鑫特钢1#高炉液压系统共有4个液压系统和一个润滑系统—炉顶润滑系统。1#高炉4个液压系统分别为:1个炉顶液压系统;1个热风炉液压系统和2个炉前液压系统,所有液压、润滑系统中间配管的管道材质均为20#钢的无缝钢管,液压系统施工工序主要包括液压站、系统管路酸洗、配管及油冲洗,液压站设备调试,液压站系统调试及配合液压执行元件试车等。
炉前液压系统主要用来控制左右泥炮、开铁口机的动作,炉前液压系统主要包括液压站、系统管路及泥炮、开铁口机。液压站分别位于出铁场平台上,站内设备由液压泵、油箱和阀台组组成,液压站设备为设备厂家成套提供。站外系统配管为:Φ28*4无缝钢管约400m,Φ34*5无缝钢管约150m。
炉顶液压系统主要用来控制炉顶设备液压缸及炉顶均压阀、放散阀的液压缸的相关动作,炉顶液压系统主要包括液压站、系统管路及液压执行元件。液压站布置在高炉主卷扬机室,站内设备由液压泵、油箱、蓄能器和阀台组组成,液压站设备为设备厂家成套提供。站外系统配管为:Φ22*3无缝钢管约1300m。
炉顶甘油系统主要为上、下密封箱、料闸、气密箱及柱塞阀提供甘油润滑,炉顶甘油系统主要包括甘油站、系统管路及机体配管,甘油站为设备厂家成套提供,设备机体配管为设备厂家出厂前已配完。站外系统配管只需配到设备机体配管的分配器上即可,站外系统配管为:Φ18*3无缝钢管约250m。
热风炉液压系统主要用来控制热风炉区各阀门的动作,热风炉液压系统控制的阀门有:热风阀3台、燃烧阀3台、倒流休风阀1台、混风切断阀1台,煤气切断阀3台、空气切断阀3台、冷风阀3台、烟道阀3台、废气阀3台等,热风炉液压系统主要包括液压站、系统管路及阀门。热风炉液压站设备位于热风炉西侧液压站房内,站内设备由液压泵、油箱、蓄能器和阀台组组成,液压站设备为设备厂家成套提供。站外系统配管为:Φ28*3无缝钢管约7000m。 2.工程特点
(1)施工管道线路长,液压系统数量多,施工工期短。 (2)施工工序复杂,施工质量要求高。
(3)管道大多高空作业,且立体交叉作业,存在较多事故隐患。 (4)液压油属易燃物,液压系统压力高,存在较多安全隐患。
二、施工准备
1.技术准备
(1)认真作好图纸的自审、会审和随机资料学习,发现问题及时与设计部门、设备制造厂家或业主取得联系,做出处理意见。
(2)图纸审核完毕后,编写施工方案及指导施工的技术交底及技改措施。
(3)施工前做好安装的技术交底、安全交底,让施工人员明了设计意图、施工任务及工程特点,掌握好安装的技术要求和施工程序。 2.材料准备及验收
(1)按照设计要求规定的规格、型号、材质向有关部门工程所需的材料计划。
(2)材料到货后,按照有关技术规定进行检查,发现问题即使向有关部门反映,若质量和要求达不到规定要求的应拒绝使用。
(3)施工用型材、板材、管材等材料表面严重锈蚀或缺陷,应及时反映并拒绝使用。 3.设备验收
(1)设备到货后,应进行开箱检查,检查时应有施工单位、制造厂家、业主和监理工程师参加,对发现问题做出详细记录,并及时向有关部门反映。
(2)设备到货后,对所验收的设备及其零件和使用工具应妥善保管,不得使其变形、损坏、锈蚀和丢失。
(3)设备开箱检查,随设备附带的技术资料、图纸、合格证应妥善保管。 (4)设备开箱检查合格后,做好记录,方可办理移交手续。 4.施工验收规范和检验标准
(1)设计图纸中的技术要求和有关技术资料。 (2)设备制造厂家的设备说明书和技术指导书。
(3)《机械设备安装工程施工及验收通用规范》GB50231—98;
(4)《冶金机械设备安装工程施工及验收规范—液压、气动和润滑系统》 YB9246—92;
(5)《现场设备、工业管道焊接工程施工及验收规范》GB50231—98; (6)《压缩机、风机、泵安装工程施工及验收规范》JBJ29—96; (7)《钢结构工程施工及验收规范》GB50235—97; 5.基础验收
(1)设备基础的标高、中心线符合设计要求,并有标记,验收合格,并已办理中间工序交接。
(2)设备基础地脚螺栓符合图纸要求,且混凝土强度应达到设计要求强度。 6.施工条件
(1)基础验收合格且办理完工序中间交接手续。 (2)所安装的设备、材料等已准备到位。
(3)厂房内的天车已经安装完毕,并能满足使用。 (4)施工现场有施工需要的用水、用电,并能充足供应。 (5)施工人员到位,施工机具准备齐全。
三、施工工艺流程及技术要求
1#高炉共有4个液压系统和一个润滑系统—炉顶润滑系统。1#高炉4个液压系统分别为:1个炉顶液压系统;1个热风炉液压系统和2个炉前液压系统,所有液压、润滑系统中间配管的管道材质均为20#钢的无缝钢管,因此,所有液压、润滑系统管道安装前必须进行酸洗工作。结合该工程特点及以往工程经验,该工程所有液压、润滑系统管道采用槽式酸洗法进行酸洗;液压、润滑系统管道焊接采用手工氩弧焊焊接,焊丝采用Φ2.5mm、材质为H08Mn2SiA的焊丝.因此,1#高炉4个液压系统和1个润滑系统施工工艺流程如下:
设备基础验收
阀门、管材管件准备→↓←设备开箱检查
管道酸洗、涂装
↓
液压站设备及执行元件安装
↓
管道支架制作安装
↓
管道切割弯曲加工
↓ 管道焊接 ↓ 管道安装 ↓
中间配管循环油冲洗
↓ 系统压力试验
↓ 调整和试运转
润滑系统管道施工时,在进行管道酸洗,且管道安装完毕后,不对中间配管进行循环油冲洗。只需用压缩空气对管道进行吹扫,并在打甘油时将管道与设备机体配管处分配器入口管道拆开,将管道内的第一管甘油放掉之后再将接口与分配器接口接上。
四、液压润滑系统安装工艺流程及方法
1.液压站设备安装:
液压站设备为成套设备,因此,液压站设备安装时,先安装设备油箱,再根据设备间连接设备管安装液压油泵组、阀台和蓄能器。液压站设备安装应符合以下要求:
成套液压站安装要求
(1)纵横中心线允许差10mm。 (2)标高允许差±10mm。 (3)铅垂度允许5/1000mm。 油箱、蓄能器、阀架安装要求 (1)油箱的水平公差或垂直公差为1.5/1000mm;纵、横中心极限偏差为±10mm;标高极限偏差为±10mm。
(2)阀架的水平度或铅垂度公差为1.5/1000mm。
(3)重力式蓄能器铅垂度公差为0.1/1000mm;非重力式蓄能器铅垂度公差为1/1000mm。
电液伺服阀等高精密阀安装要求
(1)必须在系统油冲洗合格后方可安装。
(2)安装前切勿拆下保护板和力矩马达上盖,更不许拨动调零机构。 (3)安装时安装接合面应认真检查清洗,必须十分洁净。 (4)紧固连接螺栓时,应对称的均匀拧紧,拧紧程度应适当。 (5)严格按图纸上的位置安装伺服阀,以免影响系统的控制精度。 2.管道酸洗
所有液压、润滑系统中间配管的管道材质均为20#钢的无缝钢管,因此,液压、润滑系统管道安装前必须进行酸洗工作。结合该工程特点以及以往的工作经验,该工程所有液压、润滑系统管道采用槽式酸洗法进行酸洗。
(1)槽式酸洗前准备
液压管道槽式酸洗前应先制作三个酸洗用槽子,分别作酸洗槽、中和槽和钝化槽,槽子制作主要用δ=8mm钢板和[10#槽钢,槽子规格为1m(宽)*1m(高)*12m(长),槽子制作时钢板必须双面焊接,防止腐蚀、渗漏,并在三个槽子的底部各安装一个DN50的闸阀作排污阀。槽子制作完毕后,在槽子内部0.85m高的洁净水,对槽子进行渗漏试验,有漏水现象必须进行放水返修,返修后再装入0.85m高的洁净水,对槽子进行渗漏检查,经检查不渗漏后方可投入使用。并还需制作一个管子存放架,以便于管子风干,管子存放架主要用[10#槽钢进行制作,存放架一端高另一端低,高差大约为0.4m,以便管子内部钝化液排出,以加快管子的风干速度。
(2)酸洗用化学溶液配制 1.酸洗槽溶液的配制
酸洗液的作用主要是利用稀释的弱酸将管子内外壁的锈腐蚀干净。在酸洗槽内加入0.5m高的洁净水,再向其加入浓度为30%的盐酸约2.5t,之后,再在其加入约0.3t乌洛托品,并将乌洛托品、盐酸和水的混合物用铁棒搅匀,用PH试纸检查溶液的酸性,PH值达到2~1即可。
2.中和槽溶液的配制
中和液的作用主要是利用稀释的弱碱将管子酸洗时管子内外壁上余酸中和干净。在中和槽中加入0.55m高的洁净水,再向其加入浓度为25%的氨水1.5t,之后,将氨水和水的混合物用铁棒搅匀,用PH试纸检查溶液的碱性,PH值达到10~11,碱性达不到要求可继续加入氨水,及至PH值达到10~11即可。
3.钝化槽溶液的配制
钝化液的作用主要是利用化学反应在管子内外壁形成一层不易腐蚀的钝化膜。在钝化槽内加入0.65m高的洁净水,再向其加入浓度为25%的氨水1.5t,之后,再在其加入0.7吨亚硝酸钠,并将亚硝酸钠、氨水和水的混合物用铁棒搅匀, 用PH试纸检查溶液的碱性,PH值达到8~10,碱性达不到要求可继续加入氨水,及至PH值达到8~10即可。
(3)管道酸洗
管材验收合格,酸洗化学溶液配制完毕后,即可进行管道酸洗。先将管道包装捆打开,使管子成松散状态,再将管子放入专用酸洗筐内用16t汽车吊吊入酸洗槽内进行酸洗,放入酸洗槽内的管子不宜过多,将管子吊入酸洗槽时,管子必须倾斜放置,并将管子来回拨动,使管道内空气全部跑出,使管子内部充满酸洗液。管子酸洗时间大约3~4小时,酸洗时间以放入酸洗槽内的管子内外壁都呈现出金属光泽为合格。待酸洗合格后,捞出用清水冲洗掉浮酸后将管道立即吊放入中和槽内进行中和处理,中和处理的时间大约3~5分钟,中和后将管道立即吊放入钝化槽内进行钝化处理。钝化处理的时间大约为1~2小时
钝化完毕后,将管子从钝化槽中捞出,放置在事先准备好的存放架上进行风干。待管道风干后在管道端口用塑料胶布将管道两端管口封好以免灰尘、杂物进入管道。之后,再在管子外壁涂刷上防锈漆,待防锈漆干后,再涂上面漆。涂装时,必须在距离管子两端管口大约50mm~100mm不能进行涂装,以便管子进行焊接。管子酸洗过程中,要不定期地对酸洗槽、中和槽和钝化槽内溶液的PH值进行检查,PH值达不到要求时,及时补充相应的酸和碱。 (4)管道加工 管道安装焊接前,必须对管道进行加工,管道加工主要指管子煨弯、管子切割、管道坡口加工等。 1.管子煨弯
液压、润滑系统管道煨弯采用冷弯法煨制,本工程中液压、润滑系统管道的管径小(最大管径为Φ34),弯管煨制采用弯管器或液压弯管机进行煨弯。弯管必须符合以下要求:
a.弯管的最小弯曲半径不得小于管外径的3倍,管子工作压力越高,管子弯曲半径越大。
b.管子弯曲后的椭圆率应不超过8%,弯曲角度偏差应不超过±1.5mm/m。 2.管子切割
碳素钢管宜采用机械切割,如用管刀切割时其管口内被挤起的部分应除去。
切口端面应平整,其倾斜偏差不应大于管子外径的1%,且不得超过3mm。多根管道同排布置时,应将相邻管道的法兰、活接头等错开,距离为100—200mm。
与软管总成连接的管段,在其确定长度时应加4%的余量。
3.管道坡口加工
管道坡口加工指管子与管子组对焊接前或管子与液压接头体组对焊接前管子的坡口加工,管子坡口加工采用磨光机磨削法进行加工,坡口加工如下图示:
管子加工表面必须平整,不得有裂纹、重皮。管子坡口处的切屑粉末、毛刺、熔渣、氧化皮等必须打磨清理干净。 (5)管道焊接 液压、润滑系统管道焊接指管子加工完毕后,管子与管子组对间的焊接或管子与液压接头体组对间的焊接。液压、润滑系统管道焊接采用手工氩弧焊焊接,焊丝采用Φ2.5、材质为H08Mn2SiA的焊丝。管道焊接必须符合以下要求: a.施焊前应对坡口及附近宽20mm范围内的管壁进行清理,除净其上的油污、漆、锈及毛刺等。
b.管子、管件的对口应做到内壁平齐,内壁错边量应不超过管壁厚度的10%,且不大于1mm。
c.管道点固焊时,点固焊的材料应与正式焊接时的材质一致。点焊固定后应认真检查焊肉,如发现有裂纹等缺陷时,应将焊肉磨开,将点焊固定处打磨平后重焊,点固焊合格后方可进行正式焊接。
d.在焊接全过程中,应防止风、雨、雪的侵袭。
e.焊接完毕后,应将焊缝表面溶渣及其两侧飞溅清理干净。
f.焊接完毕后,应对焊口外观进行检查,焊缝必须圆滑、不得有夹渣、气孔和裂纹等缺陷;焊缝咬边深度不得大于0.5mm、长度不得大于焊缝全长的10%,但不得超过100mm,焊缝余高不得大于3mm。 (6)管道支架安装
管道支架的材料必须符合设计规定要求,支架与其他结构焊接时必须连续满焊,支架中的各焊缝也必须连续满焊,支架焊接也必须符合设计规定要求,设计中无规定时,支架焊接的焊缝焊肉不得小于最薄件的厚度,支架的间距必须符合设计及施工验收规范的要求,管夹与支架焊接时,管夹的底板必须与支架焊接牢固,管夹底板横向两侧都必须有焊点,焊缝焊肉不得小于底板的厚度。同一平面内的管道支架,焊接管夹底板的支架必须在同一平面内,水平度不得大于2/1000;安装门形支、吊架时,支架的垂直度不得大于1/1000。 b.管子不得直接焊接到支架上。
c.管道密封件必须按设计规定的材质和规格使用.d.管道连接时,不得用强力对口\加热管道\加偏心垫等方法来消除接口的空隙\偏差\错口或不同心等缺陷.(7)管道安装
液压管道敷设应按设计图纸和业主的要求进行,具体布置管路时应尽量避免多层相叠布置。管路应不妨碍设备运行,并方便检查。管道敷设时应符合以下要求: a.管道坐标 ±10mm 管道标高 ±10mm 平管水平度 2/1000 主管铅垂度 2/1000 b.管道安装时应尽量避免管道交叉现象,应注意力求排列整齐美观。 c.管道敷设位置应便于装拆、检修,且不得影响生产人员行走,以及电机设备的运转、维护和检修。
d.管子外壁与相邻管道之间边缘的距离应不小于10mm。机体上的管道应尽量贴近机体,但不得妨碍机器动作。
e.管道连接时,不得用强力对口、加热管道、加偏心垫等方法来消除接口的空隙、偏差、错口或不同心等缺陷。 液压、润滑系统中的软管应符合以下要求:
a.软管安装要符合避免急弯,外径大于30mm的软管,其最小弯曲半径不小于管外径的9倍,外径小于及等于30mm的软管,其最小弯曲半径不小于管外径的7倍。软管安装完毕后不得有扭转变形现象。
b.与管接头的连接处应有一段直段过渡部分,其长度应不小于管外径的6倍。 c.在静止及随机移动时,均不得有扭转变形现象;
d.长度除满足弯曲半径和移动行程外,应有4%左右的余量。 e.软管相互间及同他物不得摩擦,离热源近时必须有隔热措施。 (7)管道冲洗
液压配管安装完毕,经检查合格后,即可进行管道油冲洗,管道油冲洗即是将阀台出口处至液压缸处(或液压执行元件处)的现场配管进行油冲洗,将每个液压缸(或液压执行元件)的两根液压管作为一个冲洗支回路,在阀台处制作两根主油管,一根做给油管,另一根做回油管与油冲洗装置连接。将每个液压缸(或液压执行元件)分别与主给油、回油管连接,从而形成一个完整的冲洗回路系统。
管道油冲洗前,先对油冲洗用临时管道进行酸洗,临时管道的酸洗质量等同于正式管道酸洗要求,临时管道酸洗合格后,开始制作冲洗回路,冲洗回路的制作等同于正式管道的焊接要求。制作临时管道时,将阀台处球阀配套的接头体焊接到临时管线上;再将液压缸(或液压执行元件)处的两根液压管用液压软管进行短接。检查临时管路及油冲洗装置、油冲洗回路。油冲洗回路不得通过液压站内设备、益流阀、单向阀、液压缸等,甲方指定油冲洗用油牌号。用油量为管道容积与油箱保留油量之和。回油口设置400目滤袋(准备100个),冲洗装置滤芯规格5um(准备96个),滤芯规格3um(准备72个)。冲洗过程中检查滤芯、滤袋及时清洗更换。油冲洗精度达到各系统要求为止。油样化验合格后排除冲洗油,拆除油冲洗装置及油冲洗回路。恢复正式管路。及时向管路内加入正式用油。
干油集中润滑管道在管道酸洗后,现场预制安装。用压缩空气进行吹扫,并在打甘油时将管道与机体配管处分配器入口拆开,将管道内的第一管油放掉,之后再将接口与分配器接口接上。
四、质量保证措施
1工程开工前,向建设单位提交施工方案,对施工方案进行讨论。
2 施工班组认真熟悉施工图纸,技术人员对班组进行详细的技术交底工作。 3 严格按照设计图纸、施工规范、施工方案等有关文件组织施工。 4做好施工自检记录,隐蔽工程检查记录,并办理验收签证手续。 5施工中的计量器具均经计量鉴定部门的检验合格后方可使用。
6对工程事前、事中、事后进行控制,严格执行国家、部标施工验收规范及评定标准。
7落实质量管理责任制,实行奖罚制度。
8管道焊缝射线探伤抽查符合工作压力在6.3Mpa—31.5Mpa的管道抽查15%.
五、安全保证措施
1对参加施工的职工每周进行一次安全教育,提高职工安全意识,坚持安全生产预防为主的方针。
2对施工区域进行定期检查对存在安全隐患的区域要及时整改以达到安全施工的作业环境。
3进入施工现场必须戴好安全帽及劳动保护用品。
4施工用电符合安全技术操作规程的规定,开关箱、电焊机要防潮、防砸、绝缘接地。手持电动工具要配备漏电保护装置。
5氧气、乙炔瓶放置距离不得小于5米,集中存放的要远离火源,顶部要有防砸、防阳光暴晒设施。
6施工现场坑、洞、沟、高空临边要设置临时盖板、护网、栏杆、安全绳等。 7油站要设专人监护,站内设置灭火器材。
8对施工现场主要的施工部位、危险区域、主要通道必须悬挂安全警示牌。 9特殊工种人员必须持证上岗。
六、施工人员、工、机具及材料
1.施工人员
管理人员 6人 电工 2人 铆工 3人 氩弧焊工 5人 电焊工 6人 2.酸洗材料、油冲洗材料
钢板 δ=8mm 126m2 盐酸 30% 2.6t 氨水 28% 1.8t 面粉 100kg 无缝钢管Φ108*4 60m 冲洗滤芯5um 96个 400目滤袋 100个 2.施工机具
电焊机 6台 切割机 Φ500 2台 液压弯管机 3台 25t汽车吊 1台 50t
管工 24人 气焊工 6人 辅助人员 30人 槽钢[10# 50m 乌洛托品 120kg 亚硝酸钠 900kg 耐油橡胶管DN50 100m 无缝钢管Φ76*4 90m 冲洗滤芯3um 72个 氩弧焊机 6台 磨光机 Φ100 6台 油冲洗装置 2台 汽车吊 1台
镔鑫特钢1#高炉工程 液压、润滑系统施工组织设计
审 批: 审 核: 编 制:
2008天津二十冶赣榆项目部 年5月18日
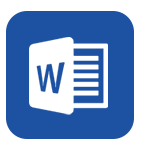