摘要:本文对具有AS脱硫煤气净化装置的焦化企业的操作经验进行了全面总结,提出了各个工序生产环节的操作要领,值得采用AS脱硫煤气净化工艺的生产厂借鉴。
采用AS脱硫煤气净化的工艺流程见图1 。
图1
AS法焦炉煤气脱硫净化的工艺流程
从图1可看出, 该工艺技术的核心是氨硫洗涤装置和脱酸蒸氨装置,无论其氨和硫的最终产品是那一种,其核心部分的操作是非常重要的。 1 氨硫循环洗涤系统
众所周知,煤气中有CO2存在的条件下,以氨吸收煤气中的硫化氢是选择性吸收过程,因此在设计脱硫塔时,必须按选择性吸收的条件确定煤气在脱硫塔的停留时间。在此条件下,煤气脱硫的效率是否能达到预定的指标,吸收操作温度和氨硫比是至关重要的;而洗涤系统能否顺利运行,消除带到系统内的焦油等污染物的程度则是关键环节。 1.1 吸收操作温度和氨硫比
(1)吸收操作温度对脱硫效率的影响。 石家庄焦化厂的经验,洗涤操作温度每升高2~3℃,脱硫效率约下降4%~5%;宣钢焦化厂的实践表明,在煤气20~40℃范围内每增加1℃对塔后煤气中的H2S含量影响也很大。可见温度对脱硫操作十分敏感,控制在22±1℃最为理想。根据各厂的操作经验,为了保证理想的脱硫操作温度必须做到以下几点。 ① 重视煤气初冷器的操作。目前焦化厂一般采用带断塔板的高效横管式煤气初冷器,把煤气温度降至≤22℃。其主导思想是在冷却煤气的同时,将煤气中的萘含量降低到0.4g/m3以下,使荒煤气中的杂质尽可能在前工序冷凝下来,使堵塞、腐蚀问题不再向后续工序蔓延。为了实现初冷器的上述作用,首先必须保证提供低于18℃的低温水;操作中严格控制初冷器喷洒冷凝液量和冷凝液中焦油含量。石家庄焦化厂和宣钢焦化厂的生产实践表明,只要保证冷凝液喷淋密度>2m3/(m2·h),(其中下段焦油含量40%~50%,中段焦油含量4%~10%)。煤气在初冷器中冷却至22℃以下时,初冷器后煤气含萘量能达到≤0.4g/m3的要求。此外,为了保证初冷器的连续运行,减少初冷器的堵塞,在初冷系统应增加热循环氨水冲洗装置;为了减少煤气雾滴的夹带,可在初冷器后增设机械捕集焦油雾滴的装置。
② 脱硫塔终冷段是控制系统操作温度的重要环节。氨硫循环洗涤在正压操作时,初冷器虽然把煤气温度降至22℃左右,但由于鼓风机的压缩,机后煤气温度上升,露点也有变化。马钢焦化厂和攀钢焦化厂的实际操作表明,脱硫塔终冷段的设计所采用的数据偏紧,能力偏小,不能满足工艺的要求。在今后设计中要对脱硫塔终冷段给予足够的重视,要留有余地,使其能起到保驾的作用。 ③ 脱硫塔必须保持在恒温下操作。氨硫循环洗涤的整个过程均为放热反应,为了获得高的脱硫效率,保持恒温下操作,就必须及时把吸收反应热除掉。从石家庄焦化厂和攀钢焦化厂的实际操作来看,进入脱硫上段的半富氨水未经冷却直接进入脱硫塔上段,而此温度常高达26℃左右,直接影响了吸收效率,石家庄焦化厂增加了冷却器,对脱硫效率起到了保证作用,见图2。此外,石家庄焦化厂还增加了脱硫塔中部液面自动调节,避免由于剩余氨水量的变化,造成中部液位不稳定,部分温度较高的富氨液不经换热而从断塔盘升气孔溢至脱硫段,使洗涤温度升高而影响脱硫效率,这个措施是否可以借鉴,值得大家进一步商榷
图2
石家庄焦化厂改进后的工艺流程
(2)氨硫比对脱硫效率的影响
在洗涤吸收过程中,NH3除吸收H2S以外,还与其他酸性组份化合,特别是与CO2及HCN化合。一般煤气中原有的NH3/H2S比大致在0.6~0.9之间,从理论上讲,足以除去煤气中在H2S。实际上焦炉煤气自身的NH3/H2S比远远不能满足脱除H2S的需要。从资料中得知,采用当今常用的钢板网吸收塔,如果煤气最终含H2S要求达到0.5g/m3时,按照典型的氨循环洗涤脱硫工艺,NH3/H2S比必须达到5左右,为了在操作中能够保持所需要的氨硫比,一方面必需加强洗氨操作;另一方面必须使氨循环于吸收过程中,加强脱硫富液的再生,以控制脱酸贫液的组成,使得循环于洗涤系统的脱酸贫液有较大的NH3/H2S比,在满足脱硫塔喷洒密度的前提下,控制氨的循环量。德国的设计资料表明,脱硫富液中的CO2/H2S比为3左右;脱酸贫液H2S含量为2.5g/L左右,其含氨浓度在20 ~25g/L。石家庄焦化厂的操作数据(见表1,表2),完全证实了以上的分析和论断。
表1 石家庄焦化厂的实际操作数据
表2 石家庄焦化厂1998年10月的操作数据
因此,在控制好脱酸贫液组成的前提下,稳定脱酸贫液的循环是保证氨硫比的重要手段。实际操作中往往由于洗涤塔内喷头堵塞造成循环量上不去,喷淋密度得不到保证,完全打乱了洗涤的操作制度,致使脱硫效率急骤下降。从石家庄焦化厂的操作数据(见表3)表明,出当喷头进行清扫后,脱硫效率明显上升。马钢焦化厂通过1998年12月中旬对系统进行清扫和更换洗涤塔喷头后,净化指标达到了NH3≤0.038g/m3,H2S≤0.6g/m3的水平。
表3 石家庄焦化厂清洗脱硫塔前后的操作数据
(3)洗氨塔下段加碱量的控制
控制洗氨塔下段加碱量的目的是保证氨硫循环洗涤系统脱硫效率;同时利用其碱性在固定铵蒸氨塔中分解固定铵盐。因此,碱洗段的操作对煤气净化具有不可忽视的作用。加碱量的多少,取决于固定铵盐的含量,一般将蒸氨废水的pH值控制在9左右。
1.2 电捕焦油器和剩余氨水除油是洗涤系统顺利运行的关键
(1)电捕焦油器。初冷器后的电捕焦油器是保证进入洗涤系统煤气质量及顺利运行的又一关键设备。与我国以往的常规流程不同,采用AS脱硫工艺的煤气净化流程,若没有电捕焦油器的高效除焦油雾,后续工序将产生严重堵塞,肯定是无法顺利生产的。不少厂家在开工初期,由于电捕焦油器的开工率低,捕集效果差,致使整个煤气净化装置的顺行受到威胁,这已经为国内各厂的实际操作所证实。如宣钢焦化厂开工初期的开工率仅为70%~80%,器后含焦油高达500mg/m3;石家庄焦化厂由于含氧分析仪的联锁设定值问题,电捕焦油器断电频繁,开工不正常,严重影响了后续工序的正常生产。
AS脱硫工艺对煤气中焦油雾的允许含量要求是严格的,一般应达到≤20mg/m3的指标。由于目前已投产的各厂对电捕焦油器的操作均较重视,从设备制造、工艺系统、操作管理以及维护检修上采取了不少措施,绝大部分厂家开工率及捕焦油率都能达到指标要求。武钢焦化厂煤气中含焦油量在30mg/m3以下,开工率达100%;石家庄焦化厂器后含焦油保持在13~20mg/m3;宣钢焦化厂在满负荷下操作,即使使用一台电捕焦油器也能将焦油雾降至20mg/m3以下;马钢、包钢、昆钢、本钢焦化厂也都达到了电捕焦油器后煤气中含焦油雾的指标要求。保证电捕器正常操作的关键主要有:
① 严格考核焦炉无烟装煤操作,避免过量空气带入荒煤气而造成煤气中氧含量过高。同时,适当放宽氧含量报警、停机的界限,一般可放宽到2%~4%,以确保电捕焦器的长期连续运行
② 在设备安装时,要将电晕极与沉降管之间的距离偏差严格控制在±2mm之内。
③ 绝缘箱采用氮气保护。
④ 定期用热氨水冲洗和清扫,必要时停机后用人工清扫电晕丝及蜂窝沉降管上的焦油、萘疤等沉集物,使电捕焦油器处于最佳工作状态。
(2)剩余氨水除油。为减少带入系统内焦油等杂质,剩余氨水除油效果的好坏成了能否保证煤气洗涤系统顺利运行的主要予盾。原设计从焦油氨水分离装置送来的剩余氨水是采用砂石过滤装置除油,德国原设计的指标要求过滤后的剩余氨水含油为20mg/L。各厂投产以来均反映砂石过滤效率太低,一般只能达到20%~30%,将大量的焦油带到系统中,造成洗涤塔的喷头和填料、脱酸塔填料和换热设备的严重堵塞,甚至会带入蒸氨塔。致使频繁拆洗换热器和清扫设备,使整个系统时开时停,打乱了正常的生产操作制度,其后果十分严重。为了解决这个难题,各厂均花费了不少脑筋,采取了不少措施,进行了技术设备攻关。如:增加剩余氨水贮槽的容积,延长沉降时间、改变砂石过滤器的工艺操作、将石英砂改为瓷砂、在系统内各设备增设排油口、制定定期排油制度等等,这些措施实施后,虽然使堵塞现象有所缓解,但带油问题并没有得到彻底的解决。武钢焦化厂在设计审查期间,吸取了宝钢溶剂萃取脱酚装置设置苯萃取剩余氨水中焦油的经验,建设了一套剩余氨水焦油萃取脱酚装置,投产后运行正常,操作稳定,萃取后的剩余氨水焦油含量可达50mg/L(最高100mg/L),除油率达到88.2%,这个经验从经济角度综合考虑,是否值得我们借鉴可以进一步商榷。此外,北京焦化厂对剩余氨水除油采用加絮凝剂的办法,不知效果如何。总之,剩余氨水除油问题至今仍是摆在我们面前的一个课题,需要我们去加以解决。在没有得到统一的、较满意的解决办法之前,应该采取综合治理的办法使矛盾尽量缓解。其主要方法有如下几点: ① 加强鼓冷工段焦油氨水分离装置的操作,从源头上加以控制。从目前各厂反映的情况看,采用沉降除渣、静置分离工艺的厂家(如:宣钢焦化厂、武钢焦化厂)分离效果较好,剩余氨水带油较少,矛盾不太突出。
② 加大剩余氨水贮槽和脱硫富液槽的容积,以增加沉降分离的时间,提高分离效果。
③ 系统中的各设备增加排油措施,制定定期排油制度及清扫制度,加强管理。
④ 研究和改进砂石过滤装置的操作,尽量提高其除油效率。 2 脱酸蒸氨装置
与其他吸收过程一样,必须把吸收液的吸收和再生看成一个整体。煤气脱硫富液的再生是在脱酸蒸氨工序完成的。其工艺流程如图3所示。
图3 脱酸蒸氨装置工艺流程
脱酸蒸氨操作的好坏直接关系到脱酸塔的脱酸效率、贫液组成的稳定和排出蒸氨废水的指标。因此该工序处于氨循环洗涤脱硫工艺的重要地位。根据石家庄焦化厂等单位的生产操作实践,控制的关键是保证脱酸贫液的组成。如前所述,如不能控制好脱酸贫液中氨与硫化氢的比和氨与二氧化碳的比,贫液的有效氨浓度就得不到保证,就会大大影响对煤气中硫化氢吸收的效率。脱酸蒸氨工序的技术要点主要有以下几点。
(1)严格控制进入脱酸塔的富液温度。控制进脱酸塔的富液温度是脱酸塔正常操作的关键。其温度应在80~88℃,不得低于75℃。富液温度过低,使脱酸塔部分传质表面变成了传热表面,降低了塔板效率,使脱硫除率大大降低,见表4。
表4 脱酸塔的操作数据
如果维持解析操作,必然要增加进入脱酸塔的蒸汽量以提供热能,这样不但增加了蒸汽耗量,而且大部分蒸汽会冷凝而稀释了贫液,增加了贫液量,影响了贫液组成。为了维持贫液中的氨含量,又不得不从固定铵塔增加氨的补给量,加大了氨在系统中的循环,使能耗增加。保持进料温度的主要措施如下。在设计上,贫富液板式换热器的面积必须考虑一定的富余度,以满足工艺要求;在生产过程中,必须保持板式换热器时刻处于良好的操作状态,发现堵塞后要及时清扫,严格管理制度。
(2)控制进入脱酸塔顶的冷料量。实际操作经验表明,进入脱酸塔顶的冷料量一般控制在富液量的30%左右。其作用是控制酸气浓度和减少氨的损失。当进入脱酸塔的富液温度低时,适当减少冷料量,否则脱酸贫液含H2S将会增高。
(3)保证脱酸贫液的组成,使其含H2S浓度在2.5g/L左右,含氨在20 ~25g/L,其手段之一是调整脱硫塔顶至硫回收装置的酸气量,当贫液含H2S浓度偏高时,增加至硫回收装置的酸气量,反之则减少;其二是调整固定铵塔侧线氨汽补给量,以保证贫液中NH3的浓度达到规定值。 3
氨分解及硫回收装置
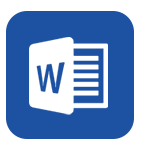