人字门船闸
1 工艺流程
1.1 人字门制造工艺流程
制造工艺
施工准备→零构件制造→检验→组装→检验→焊接→检验→机加工→预组装→检验→防腐→检验→竣工验收→出厂。 1.2 零构件制造工艺流程
工艺性审查→工艺设计→备料→划线→下料→边缘加工→零件机加工→零件矫正→检验→组装→检验→焊接→检验→校正→防腐→检验→构件验收→构件成品。
2 工艺性审查
2.1 图样审查:审查图样的绘制是否符合国标规定、是否齐全、视图是否表达清楚、尺寸标注是否正确完整清晰合理、技术要求是否合理,合格后交付施工准备和施工使用;
2.2 结构工艺性审查:审查结构是否有利于减少焊接应力与变形、是否有利于减少施工劳动量、是否有利于施工方便和改善施工人员的劳动条件、是否有利于减少应力集中、是否有利于节约材料和合理使用材料,以制定经济、最有效的工艺方法。 3 工艺设计
3.1 按照技术先进、经济合理、技术可行及良好劳动条件等原则,对产品进行工艺分析,编制制造工艺规程,包括工艺过程卡、加工工序卡和加工简图等工艺文件;
3.2 根据施工实际设计和制造施工所需的各种工装,如夹具、卡马、斜楔、专用吊具、拉杆等必须工具。 4 备料 闸门制造所用材料应符合图纸及有关规范规定,并具有出厂合格证,如无出厂合格证、或标号不清、或数据不全、或对数据有疑问者,应重新进行检验、试验,确认合格后才使用。 5 工艺措施 5.1 拼接
闸门构件在划线、下料之前,如果钢板或型钢尺寸不足时,允许拼接。 5.1.1 钢板拼接:拼接缝开“Y”型或双“V”型坡口,坡口的型式和尺寸按GB986/985及设计图纸的规定执行,拼接的钢板最小尺寸大于600mm,接缝局部间隙不大于1mm,钢板平面错位不大于0.5mm,采用埋弧自动焊焊接,焊透,并经无损探伤检查合格,然后磨平焊缝。
5.1.2 型钢拼接:拼接缝开双“V”型坡口,接缝局部间隙不大于1mm,平面错位不大于0.5mm,采用手工焊接,焊透,并经无损探伤检查合格,然后磨平焊缝。 5.1.3 钢板拼接缝不允许出现十字交叉焊缝,主梁腹板的拼接缝应距跨中1米以上,且与其轴线倾斜25°~45°,主梁腹板、边梁腹板的拼接缝与其翼板的拼接缝错开500mm以上。 5.2 划线
5.2.1划线选用的量具要求有较高精度、且具有有效使用期内的计量检定合格证(附修正值);
5.2.2 划线应根据图纸、工序流程卡的要求,在相应材料上进行。
5.2.3 顶梁、底梁、主横梁腹板端头,门轴柱、斜接柱肋板数量较多且形状不规则,应制根据图纸制作样板划线。
5.2.4 划线尺寸按“零件1:1尺寸+割口余量(手工割为2mm,自动割为3mm)+机加工余量+焊接收缩预留量”进行,未裁边钢材加10~15mm裁边量。 5.3 下料
5.3.1 下料前将钢板、型钢矫平、矫直。
5.3.2 规则板件采用半自动切割机,不规则板件采用手工切割,并采用砂轮打磨割口。
5.3.3 小型钢件采用剪切或砂轮切割,大型钢件采用手工切割,并采用砂轮打磨割口。 5.3.4 切割后按规范或设计要求,采用刨边机、刨床或半自动切割机制备焊接坡口,采用半自动切割机制备的坡口应用砂轮机修磨平整。
5.3.5 下料中如发现材料有裂纹、夹层等超标缺陷时,应停止使用,作好记录报告质量管理部门。
5.3.6 下料后视变形情况分别采用机械或火焰等方法进行矫正,采用油漆或样冲对零件进行编号,分类堆放,以备组装。
5.3.7 下料而成的零件其未注公差尺寸的极限偏差应符合DL/T5018表7.1.2规定,其表面形位公差及表面粗糙度应符合DL/T5018款7.1.3、7.1.5规定,矫正后其平面度、直线度、垂直度、扭曲等公差应符合DL/T5018-94表8.1.6规定。 6 门叶构件制造
门叶的构件主要有顶梁、主横梁、底梁、纵梁、门轴柱、斜接柱、面板、次梁、止水座等,其制造工艺措施分述如下。 6.1 门叶的分段
人字门的制造可根据场地、运输起吊能力进行分段制作,然后运至现场拼装。门叶的分段应遵守以下原则:
6.1.1 面板分段位置应与斜接柱、门轴柱的前封板分段位置相互错开150mm以上。
6.1.2 斜接柱、门轴柱端板分段位置应与相应的前后封板分段位置相互错开150mm以上,并且必须避开中枢的安装位置,里支承肋100mm以上。 6.1.3 分段区格内纵梁、斜接柱、门轴柱的隔板均不应断开。 6.1.4 门叶出厂前必须在平台进行预组装。 6.2 顶梁、主横梁、底梁、纵梁的制作
6.2.1 构件组装前,对腹板、翼板等零件进行复检,确认尺寸无误且矫正平直后,方可进行组装。
6.2.2 组装时,先将翼板置于平台上划出基准线、组装线,对基准线、组装线进行复检合格后,在经过检验合格的点对模上组装点焊。腹板和翼板均有拼接缝时,其拼接缝应错开布置500mm以上。
6.2.3 组装时,应保证腹板与翼板相互垂直,其垂直度误差不得大于1.0mm。 6.2.4 组装点对的定位焊应按DL/T5018-2004款4.3.7规定。 6.2.5 焊接优先采用埋弧自动焊,并采用工装或专用的变位装置,形成船形焊位。 6.2.6 焊接完毕,应将焊渣、飞溅等清理干净,并对焊缝进行检验,合格后,对弯、扭曲变形采用火焰或机械的方法进行矫正,对翼板的角变形采用矫正机进行矫正。
6.2.7 顶梁、主横梁、底梁、纵梁制造的允许偏差应符合DL/T5018-2004表7.6.2规定。
6.3 水平次梁制造
6.3.1 焊接次梁制造措施参照3.4.1执行,其制造的允许偏差应符合DL/T5018表7.1.7规定。
6.3.2 型钢次梁制造的允许偏差应符合DL/T5018-2004表7.1.6规定。 6.4 面板制造
6.4.1 面板对应门叶分节拼接,门轴柱、斜接柱处的面板待门叶整体组焊,翻身后再进行拼接,其宽度与高度方向预留焊接收缩余量及修边量。
6.4.2 面板拼接时应避免出现十字接缝,同时应使面板拼接焊缝与梁构件组装焊缝错开,其错开间距应不小于200mm。
6.4.3 面板的拼接严格按焊接工艺指导书执行。
6.4.4 面板接焊完毕,应对其焊缝进行无损探伤检查,并矫正变形,使其局部平面度,在每米范围内不大于2mm。 6.5 门轴柱、斜接柱制造
门轴柱、斜接柱的制造与门叶整体组装、焊接同步进行。 7 门叶整体组装 7.1划组装线
7.1.1 在平台上将分节制造的面板进行整体组合。
7.1.2 先划门叶纵中心线,底梁腹板中心线作为基准,然后划主横梁、次梁、顶梁组装线,梁间距加0.6~0.8/1000的收缩余量,划纵梁、门轴柱隔板、斜接柱隔板装配线。
7.1.3 检查划线是否正确,要求顶、底主梁与斜接柱、门轴柱端板组成的矩形及门叶外形矩形的对角线相对差≤3mm。 7.2 组装 7.2.1 组装顺序:面板→底梁→主横梁→顶梁→次梁→纵梁→门轴、斜接柱前封板→门轴、斜接柱端板→门轴、斜接柱隔板→门轴、斜接柱加强肋→(焊接)→门轴、斜接柱后封板→(焊接→翻身)→门轴、斜接柱面板→(焊接)→底止水座、中缝止水座→其它所有零、构件组装。
7.2.2 检查各零、构件组装尺寸符合规定后,采用手弧焊进行定位焊。 7.2.3 组装的允许公差和偏差除符合DL/T5018-2004表7.6.1规定外,还需符合下列要求:
1)门叶底梁倾斜度≤2mm; 2)止水座面处不平度≤2mm; 3)纵梁隔板错位≤2mm
4)侧止水螺栓孔中心至门叶中心距±1.5mm
5)门叶宽和高的对应边之差不超过相应尺寸公差的一半 6)中缝止水螺孔中心至中枢支承中心距离±0.5mm。 8 门叶焊接
8.1 焊接前,按DL/T5018-2004款4.1规定进行焊接工艺评定,编制焊接工艺规程。
8.2 按DL/T5018-2004款4.2规定,持有有效合格证的焊工才能参加相应焊接。 8.3 焊缝分类根据DL/T5018-2004款4.3.1进行划分。
8.4焊接采用埋弧焊、气体保护焊或手弧焊,优先采用自动或半自动焊。 8.5 焊接材料严格按图样的规定选用,焊接材料必须具有产品质量合格证,焊条应符合GB51
17、GB51
18、GB984或GB983的有关规定,自动焊用的钢丝符合GB1300和GB8110的有关规定,碳素钢埋弧焊用焊剂符合GB5293的有关规定,焊接材料的贮存与保管严格遵照JB3223的规定执行,焊接材料的烘焙严格按产品使用说明书的规定温度和时间执行。
8.6 在风速大于10m/sb,相对湿度大于90%,温度低于-5℃,雨天、雪天,焊件表面潮湿,焊接接头有缺陷未处理或影响区未彻底清理时,不得施焊。 8.7 焊接严格按DL/T5018-2004款4规定及焊接工艺规程规定的流程、工艺进行,并根据实践对流程、工艺进行修正,焊接过程中随时进行检测,控制焊接变形和焊缝质量,对于焊接变形超差部位和不合格的焊缝,逐项进行处理,直至合格后才进行下一道工序。
8.8 焊接完毕,焊工应把焊渣、飞溅物清除干净,并进行外观自检,而后在焊缝周围显著位置打上焊工代号钢印。
8.9 对所有焊缝进行外观检查,其外观质量按DL/T5018-2004表4.4.1规定执行;对
一、二类焊缝进行超声波探伤,按GB11345评定,一类焊缝BⅠ级合格,二类焊缝BⅡ级合格;需进行射线探伤时,按GB3323评定,一级焊缝ABⅡ级合格,二类焊缝ABⅢ级合格。检查发现有超标缺陷处,找出产生缺陷的原因,由技术部门制定返修工艺进行返修处理,并重新进行检验,同一部位返修次数不能超过两次。 9 门叶矫正
9.1 门叶焊接合格后,对变形超标部位进行局部或整体矫正,使其符合DL/T5018-2004表7.6.1规定。
9.2 矫正后,在面板上划出门叶纵向中心线,同时以纵向中心线为基准划出面板最大轮廓线,采用半自动切割整体修边。 10 门叶机加工
10.1为减少机加工难度,门轴柱、斜接柱端板先整体钻好螺栓孔,再进行组装,孔的定位应考虑预留切割损耗量(2~3mm)和焊接收缩量(分段后,每段门叶长度的0.6~0.8/1000)。
10.2门叶整体拼装合格后,进行整体划线,按图纸及及Q/ZB75-7
3、Q/ZB76-73对侧止水、中缝止水座的连接螺栓孔等进行机加工。
10.3由于底止水座板与门叶焊接,其止水螺孔无法加工,因此要示先加工底止水座板上螺孔,再与门叶组焊。方法是:在平台上放出底止水座板的曲线,按平台上底止水座板的曲线装上底止水座板并加固,再组装上底止水压板,底止水压板与底止水座板根据要求垫上相应厚度钢板块,而后划线钻孔,钻孔时应避开底止水加强板,保证能上止水螺母、螺栓为宜。钻完孔后即可将底止水座板移上门叶与门叶焊接,拆下底止水压板进行扩沉头孔。
10.4 门叶拆开后,在根据设计图纸及规范加工底枢、顶枢、启闭机铰座、导卡座的连接螺栓孔。 11 门叶附件制造
人字门的主要附件有顶枢、底枢、人行桥、枕垫、支垫、启闭铰座、导卡、锁定装置、止水装置等,按图纸及规范Q/ZB75-7
3、Q/ZB76-73制造。 11.1铸钢件的制造
11.1.1铸件尺寸和筋、壁厚的允许偏差及表面质量要求,应符合GB11352《一般工程用铸造碳钢》、GB5680《高锰钢铸件技术条件》机GB6414《铸钢件尺寸公差》中的有关规定。
11.1.2铸件应符合现行《碳素钢铸件分类及技术条件》规定的ZG45铸钢中的II级。
11.1.3铸钢件需经退火或正火处理。
11.1.4人字门铸钢支、枕座不得有裂纹,当有下列缺陷,但经补焊后不影响使用性能者,允许补焊处理:
1)承压加工面上有孔眼等缺陷,其单个面积不超过3cm2,深度不超过该处厚度的1/10,且在同一横向表面上100cm2的面积上不超过一处,总面积不大于所在面积的2%;
2)非承压加工面上有孔眼等缺陷,其单个面积不超过5cm2,深度不超过该处壁厚的1/5,且在每100cm2的面积上不超过一处。
3)非加工面上有孔眼等缺陷,其单个面积不超过8cm2,深度不超过该处壁厚的1/5,总面积不大于所在面积的5%。
11.1.5 铸钢底枢顶盖和底座,顶枢座和锚定座根部转角处及筋板根部,以及承压加工面均不得有裂纹和缩松。当有下列缺陷,经补焊后不影响使用性能者,允许补焊处理:
1)承压加工面上有孔眼等缺陷,其单个面积不超过5cm2,深度不超过该处厚度的1/10,总面积不大于所在面积的3%;
2)轴孔有孔眼等缺陷,其单个面积不超过2cm2,深度不超过该处厚度的1/10,总面积不大于所在面积的2%;
3)非承压加工面上有孔眼等缺陷,其单个面积不超过5cm2,深度不超过该处壁厚的1/5,总面积不大于所在面积的5%; 4)非加工面上有孔眼等缺陷,其单个面积不超过8cm2,深度不超过该处壁厚的1/5,总面积不大于所在面积的5%。
5)其他次要部位出现裂纹,深度不超过壁厚的1/10,长度不超过所在部位长度的1/4,且不超过两条。
11.1.6 当铸件缺陷范围超过上述规定时,应经技术、质量检查等有关部门同意后,方可补焊,并应有补焊措施,补焊后的质量符合设计要求。
11.1.7 铸件缺陷补焊前,应将铸件缺陷处清除干净,呈良好的金属母材,裂纹等缺陷应开坡口及钻止裂纹。补焊应选用接近该铸件性能优质的焊条。 11.1.8 补焊铸件时,应将铸件预热至200°C以上,焊后应进行热处理,以消除内应力。
11.2 附件机加工要求
11.2.1 支、枕垫块应逐对配装研磨,使其接触紧密,局部间隙不大于0.05mm,其累计长度应不超过支、枕垫块长度的10%。
11.2.2 底枢蘑菇头与底枢顶盖轴套进行组装研刮,并满足下列要求: 1)在加工时,定出蘑菇头的中心位置; 2)应转动灵活,无卡阻现象;
3)蘑菇头与轴套接触面集中在中间120°范围内,接触面上的接触点数,在25mm×25mm面积内应有1—2个点。 12 闸门预组装
12.1 将各节门叶面板朝上,按连接顺序以纵向中心为基准顶紧、对齐、找平,进行检查、处理至合格。
12.2 闸门预组装的允许偏差:组合处错位≤2.0mm,偏差除符合DL/T5018-2004表7.6.1规定外,还应符合下列要求:
12.2.1底枢顶盖和门叶底横梁组装后,其中心偏差应不大于2.0mm,倾斜应不大于1/1000。
12.2.2 顶枢、底枢中心的同轴度公差为1.0mm。 13 闸门防腐
13.1 闸门的表面预处理按DL/T5018-2004款6.1规定执行。 13.2 闸门的表面涂装按DL/T5018-2004款6.2~6.3之规定执行。 13.3 闸门的金属喷涂按DL/T5018-2004款6.4~6.5之规定执行。 14 闸门埋件制造
埋件包括底槛、侧轨、顶枢埋件、中枢埋件、底枢埋件等构件,其制造工艺流程为按3.1.2执行,其制造允许偏差及技术要求应符合DL/T5018-2004款7.3规定。 15 竣工验收
15.1 人字门验收,根据需要可分若干阶段进行: 15.1.1 主要材料、铸件和锻件验收。 15.1.2 结构焊接件验收。 15.1.3 制造验收。
15.2 人字门制造质量应符合DL/T5018-2004第10章规定,并满足工程使用要求。 15.3 人字门竣工验收时,应提拱下列验收资料: 15.3.1 主要材料、标准件及外协件的出厂质量证书。 15.3.1 人字门的出厂合格证。 15.3.2 焊缝质量检验报告。 15.3.3 表面防腐蚀质量检验报告。 15.3.4 制造最终检查和试验的测定记录。 15.3.5 重大缺陷处理记录和报告。 15.3.6 设计修改通知单和有关会议纪要。 15.3.7 制造竣工图
15.4 人字门门验收时,应按有关规定办理质量等级评定证书。
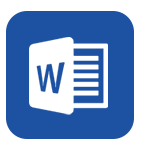