手工放样——应用函数计算器,按照规定的计算方法对铁塔结构尺寸进行计算确定的过程。
计算机放样——应用铁塔放样软件,在计算机上进行铁塔计算放样的过程。
计算放样发展历史
最初的阶段,由于使用的计算工具及相关的理论基础不是很完善,普遍采用放大样的方式,即是在地面上按照1:1的比例进行实样计算和测绘。后来,广泛应用三角函数和立体几何的知识原理,采用函数计算器按照建立的数学模型进行放样工作。随着计算机在各个行业的广泛应用,一些民间人士开始着手开发计算机放样的应用软件,并逐步在全国范围内各厂家进行试用,后来又不断地进行修改和升级。现在的计算机放样软件有二维和三维两种,在全国各个厂家得到了广泛的应用。我公司采用的是李平一先生主持开发的二维计算机铁塔放样软件。
放样的作用
放样是对铁塔设计图纸进行结构尺寸校核和确定后,按照规定的技术术语将每一个部件的尺寸特性在零件图上进行描述,为生产加工提供参照依据。
对角钢部件,是零件图;对钢板件,是零件图和样板。这两种材料,在计算机中还有一套可以经过转换即成为自动生产线能够识别和接收的电子文件。
下料工艺
下料采用机械剪切、锯割或者火焰切割的方式,将原材料加工成规定的尺寸或者形状的工序产品的过程。一般情况下,优先采用机械剪切,其次采用火焰切割。
角钢的下料
角钢的下料方法有压力切断、齿锯切断、气割切断等。分别对应的设备为压力机、锯床、火焰自动/半自动切割机等。
1)厚度≥16mm的使用锯床切断。
2)10mm≤厚度
3)厚度≤8mm一般使用手动线切断。
4)角钢异形件(普通剪切工艺满足不了加工需要的)使用乙炔气割切断。
钢板的下料
钢板的下料方法有压力切断、气割切断等。分别对应的设备为剪板机、火焰自动/半自动切割机等。
1)板厚度≥25mm或异形件的使用乙炔燃切断
2)板厚度
下料的注意事项
合理调整剪切刀口间隙能提高刀口寿命和提高剪切质量,可减少冷拉角和毛刺等缺陷。刀口间隙与被剪切工件的厚度和材质有关。
操作人员必须明确剪床的最大剪切能力,不准超过规定的范围剪切。剪前要检查上下刀口间隙是否合适。间隙与钢板厚度和材质有关,一般为被工件板厚6%~12%。切Q345板要比Q235钢的间隙偏小。
采用火焰切割时要考虑留出割口余量。
钢印标识工艺
钢印标识的目的和意义
对铁塔零部件进行有效识别以便于生产和施工。
钢印标识的组成
塔材部件上的钢印一般由三部分组成:工程代号、塔型代号、部件编号。组间距必须大于一个字的距离。
钢印标识的位置要求
1)四个禁区不得有钢印,一制孔区,二铣刨区,三制弯区,四焊接区,以保护钢印的完整性。
2)钢印的深度:塔材厚度在6mm以下时为0.7~1.0mm,大于6mm时为1.0~1.5mm。
3)钢印不得印在靠近塔材的轧制边和剪切边。
号料工艺
手动冲孔时需对零部件进行号料,号料专用的划针、冲子等工具必须尖锐锋利,靠板垂直无倾斜。
对于长宽与样杆样板略有出入时(在标准范围内),必须在号料时进行调整以保证两端或两边不致超差太大。调整不了的返回上工序处理。
样杆样板上的孔径符号不清不准号料
号料后的孔径符号、心线等必须圈划清楚、正确。
钻孔件先进行勒心(样冲定位)
先制孔角钢件在制弯前号孔要按先制孔的规定,曲点到主要加热面第一个孔距应大于100mm,次要加热面大于30mm。小于以上极限值时,必须预留孔,等制弯后再补钻这些预留孔。
制弯工艺
制弯分为冷弯和热制两种。除弯度较小的角钢及板件可以采用冷曲外,其余的一律进行加热后煨弯制弯。
角钢:曲筋、曲面、开角、合角
钢板:弯曲
钢件加热温度控制在1000~1100℃,工件终温在750~850℃,不得出现过烧。加热温度与炽热颜色关系如下表:
炽热颜色温度(℃)炽热颜色温度(℃)炽热颜色温度(℃)
棕黑色520-580樱红色780-800暗黄色1050-1150
棕红色580-650浅樱红色800-830浅黄色1150-1250
暗红色650-750浅红色830-880白热色1250-1350
暗樱红色750-780红黄色880-1050
制弯的弯度以卡板为准,其方向曲点位置以样杆或零件图标的图形位置。注意控制不得曲反和曲混件号,特别是先制孔的部件更要注意方向。
清根铲背的火曲件必须在清根铲背后再进行制弯。
制弯时须防止出现局部严重明显突缩。曲件表面不得出现伤痕。
对于弯度较大的角钢件允许采取割口曲后焊接的方法进行。但必须保证焊接质量和强度。
先制孔后制弯的工件需要注意两个问题:一是严防孔形的变化(形变),二是严防孔位的变化(位变)。
防止形变的方法有三种:一是限制主要变形加热面靠近曲点的孔距值>极限值;二是改变和控制加热区尽量远离易变形孔;三是在加热制弯前,在易变形孔内置铁豆(冲孔冲下来和等径铁豆),制弯时带着铁豆用以控制孔形变化,制弯后立即将铁豆取出。有时可以用旧冲头代替铁豆。
冲孔工艺
冲孔是在室温下,利用安装在压力机上的模具对材料施加压力,使其产生分离变形,从而获得所需零件的一种压力加工方法。
冲孔规定
1)厚度<16mm的Q235钢和厚度<14mm的Q345钢件可使用冲床冲孔。厚度≥16mm的Q235钢和厚度≥14mm的Q345钢件制孔需采用钻床钻孔。特殊部件(如挂线角钢和挂线板制孔必须采用钻孔)。
2)冲孔时根据零件的厚度、孔径选取冲模(凹凸模)。凹模内径比凸模外径大0.5mm~2.0mm(视材料厚度而定)。
3)更换冲模时须切断电源,用人力手动盘车方法进行粗调和精调。精调后凹凸模相对同心度在0.05mm以内。
4)滑块调整螺杆在螺母扣内长度L的值不得小于螺杆直径的1.5倍。否则应垫起下模板。
5)选取冲床冲孔能力时,应根据工件厚度、材料材质、冲孔直径来确定冲床的压力功率。
6)同一工件上有几种大小不同直径的孔,在手动冲孔时应先冲小孔后冲大孔。
7)角钢手动冲孔时工件应与冲床工作台平行,与冲头中心线垂直,工件侧面应紧靠心线板,工件上所号孔位中心线就成心线板中心线重合。
钻孔工艺
钻孔效率虽然比冲孔低,但钻孔可解决制弯件的制孔问题,钻孔的孔形比冲孔的孔形符合标准(冲孔存在喇叭口),且钻孔比冲孔的强度要好。铁塔重要构件(如挂线件)按设计要求必须采用钻孔工艺。构件厚度大于16mm(具体见工程技术协议)也必须采用钻孔工艺。
需钻孔的工件必须进行孔位定位。
钻孔前应将所钻孔的工件稳固垫平,且应适当将工件固定。
钻孔应根据工件孔径,选取适当转速、走刀量。钻孔时应有足够的润滑剂,避免钻头切削刃部退火,失去切削能力。
切角、清根、铲背和开坡口工艺
切角:为了提高铁塔节点的刚度,采取紧凑设计的节点。由于构造上的需要,必须将互相碰撞的角钢端部按规定切除某一部分斜角通称为切角。
清根:指将角钢内圆角刨成清根直角。
铲背:指将角钢外直角刨成圆角。
刨边(开坡口):指将板材刨一边或刨一α角便于焊接。
铁塔制造零件焊补孔工艺
1)焊补孔眼时的允许焊补数量:接头处为30%,其它处为50%。超过规定的补孔必须报质量技术部门批准后方可焊补孔眼。
2)焊补孔眼应由合格的焊工担任,不准生产工人自行焊补孔眼。
3)焊补孔眼填充铁豆的厚度不得大于3mm,铁豆应小于堵孔直径4mm。
4)焊补孔眼边缘不得有裂纹、未焊透、夹渣和气孔
5)焊补孔眼处的熔焊金属表面不得高于或低于母材平面0.5mm。
6)焊补孔眼处的飞溅焊渣必须清除。
铁塔试组装工艺
为检验铁塔在设计、加工过程中由于放样、代料、工艺变动、工模具失控、错误操作等工作过失所造成的批量性加工质量问题,须对出厂前的铁塔进行代表性试组装。
1)对新放样的塔型必须进行试组装。
2)试组装可以采取对称结构的半试组装,对于多接腿等多段结构须做到各个试组装。对修改部分要进行必要的局部试组装。
3)试组装时所用的垫木高差应满足塔的坡度要求,不得强行组装。
4)试组装时要按孔径大小使用螺栓,严禁用小直径螺栓穿大孔。
5)螺栓的穿向应是(以塔组立后为准)水平方向由内向外、垂直方向由下向上。
6)重要接点处的螺栓要扭紧,螺杆与构件表面应垂直,外露丝扣数应大于3~6扣。
7)构件与构件、构件与螺栓不得有相互碰撞和空间干涉现象存在。
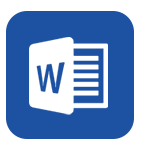