液压设备维护保养与检查
检查可分类为日常检查,定期检查和综合检查三种,其涵盖事项及时间为:
日常检查
液压泵起动时
运转中或停止时
定期检查
机械设备之检查
回路性能之检查
综合检查
机件及附属机件之分解检查
机件及回路性能之试验
上述三项检查的实施程序和要点分别如下:
(1) 日常检查
A.液压泵起动前後之检查程及要点
起动时之检查顺序如表九,分为液压泵起动前和起动後.
表九 起动检查顺序
a.液压泵起动前之检查
由液面计检查储油箱之油量,经常保持油量维持在储油箱之上限记号处.
以温度计检查储油箱内之油温.当油温至10℃以下时,应小心起动泵浦,起动後,应空转20分钟以上方始承受负荷.油温在0℃以下时,操作运转便具危险.
以温度计检查室温.即使储油箱中之油温较高,但在配管内的液压油,其温度约与室温相近,故在冬天温度在10℃以下时,应小心起动泵浦.
在液压装置没有运转时,压力表的指针应该显示0 kg /c㎡,於起动前应确定之.
制压阀之设定压为0 kg /c㎡时,泵浦之起动负荷很小,若有卸载回路,应以卸载状态开始起动,如此方能避免危险,待得运转正常,方使调至需要之设定压.油压装置,除了应注意低温起动外,仍应注意制压阀之设定状态,小心起动.
b.液压泵起动和起动後之检查
泵浦应以寸动方式起动,即断断续续的开关(on-off),冬季液压油之黏度高时,更应注意制压阀之设定状态慢慢起动,其程序约为下述:
5秒钟ON-OFF(停止)……….3至4次.
连续低压运转(使回路中各部份有个起动预备)10至20分钟.
连续操作.
寸动方法起动液压泵浦後,应确认泵浦吸入,输出,声音的变化和压力表指针的动作(缓缓上升).泵浦起动後超过一分钟仍无输出应即刻停机检查,否则有毁坏之虞.
慎重操作制压阀,使其压力来回上升下降几次,以确认压力变动和动作之关系,然後才设定需要之工作压力.於进行第C项检查时,同时也检查泵浦之噪音.听清楚当压力上升下降时,噪音之变化,有无异常之噪音出现.如有非正常声音连续出现时,要检查在吸入侧配管和泵浦主轴部份有无空气吸入的现象.噪音太大时,尤其在高压运转时,噪音变得很大,此时应检查吸入侧过滤器之阻塞情况.
检查过滤器.从吸入侧过滤器之指示计上可确认滤网阻塞的抵抗状态,此项检查需在泵浦运转之後,马上进行,同时也要核对一下指示计之误差(即起动时和停止时之差).若过滤器装在储油箱内,则要注意泵浦起动时之噪音变化.
检查各处所之配管过滤器阻塞的情形和指示计指出之抵抗状态,这项检查应在泵浦起动之後,液压油通过时马上进行最有效果.
确定制压阀动作正常,试一下卸载回路是否有效压力上升下降几次,以检查各控制阀之应答性和压力表之动
作.检查油压缸或液压马达之动作状态是否如预期,以完成回路之起动预备.
B.液压系统运转中和停止前之检查程序及要点
此项检查是以目视,听觉及触觉为主,主要检查有无因液压泵,液压马达,液压缸或控制阀组等的磨损,而引起外部洩漏,内部洩漏及油温上升等的检查.其检查程序如表十
表十 运转中和停止检查程序
检查要点如下:
以目视方法检查储油箱内液压油气泡,变色(白浊,或变黑)等.若发生有白浊或大量气泡时,应立即调查其原因.以温度计或手摸储油箱侧面,测定油温是否正常,一般应在比室温略高而低於60℃之间.
将压力调至最高,亦即在高压动作时检查压力表指针之振动情况.振幅很大时,或振动缓慢均属不正常.正常之状态应为指针在±3kg /c㎡的范围内振动.
泵浦之噪音以听觉判断.若噪音大且压力表指针振幅很大时,均表示油温过高,此时可能乃因泵浦过份磨损而起.
若有第d项之现象时,可比较泵浦外壳和储油箱内液压油的温度差,若泵浦外壳之温度比储油箱之油温高出5℃以上时,泵浦效率可能是非常低落了.
以目视法检查储油箱侧面,侧面盖板及油面计处有否漏油.
以目视法检查泵浦主轴处以及各连接部份是否有漏油之现象,於高温高压运转时最易发现.
检查液压缸起动时,停止时之状态以及动作速度.此外,检查於高温高压运转时,在液压缸活塞杆侧油封处有无漏油现象.
确认液压马达之动作,噪音及排量等.
检查电磁阀之线圈磁音和切换时不正常音响.此外以手触摸电磁阀之外壳,检查其温度,一般在高於室温30℃时即属正常.
对照压力表显示之压力,听听是否有制压阀特有的敲叩声并检查其流速音的大小.
以目视法和触摸法检查各配管接头处是否有漏油现象,配管接头下方(如台面,地面)应经常保持乾净,如有液压油外洩之现象时,即可马上发觉.
检查配管,控制阀和液压缸等的振动情形,并检查各固紧螺丝有否松动.在高速或控制阀行切换动作时,最容易发现.
(2) 定期检查
定期检查之目的,为使液压设备经常保持正常状态,确保机械动作可靠性,并及早发现可能的故障点,以增加设备使用寿命.
定期检查与日常检查之不同,在於前者不进行外观检查,检查内涵偏重於预防性,如整体设备容易故障之部份,需要保养的部份及需要检修的地方.可分类为液压元件检查和性能检查两部份,分述如下:
液压元件检查
液压元件检查程序如表十一
表十一 液压元件检查程序
检查实施要点如下:
a.泵浦(Pump)
检查泵浦之按装是否紧固,吸入侧配管有否松动.
检查泵浦和马达之间之连轴器(Coupling)是否有角度偏移,以手转动连轴器检查其旋转之情况及其游隙.有否液压油从主轴侧洩漏(检查有无运转时之漏油痕迹,以确认主轴油封之良否).
检查日常检查时,发现之不正常现象.必要时分解检查之.
b.储油箱(Tank)
从储油箱底部放洩口,以透明容器承接部份液压油,15分钟後检查其沉殿物及水份等.若水份太多时,再从储油箱上部另外取样,沉殿物太多时,应送试验室分析其成份.此外检查过滤器之污染情况,如污染太烈时,更换新油.换油之前应将储油箱内部清洗乾净.
油面计之动作指示是否正常,并与实际之储油箱油量作一比较.
确认油温计动作之精度,必要时以其他的温度计加以核对测试.
另订一温度以核对恒温计之动作精度.
储油箱属气压封入型时,检查有无漏气.可用肥皂水涂抹於封闭缝以判断有无漏气.
储油箱通气口之污染状况,有无变形,阻塞.
其他於日常检查时发现之不正常处.
清洗储油箱上盖及侧板,以利日常检查.
确认储油箱内之油量.油量有显著减少时,可能在储油箱或系统某处有漏油的情形.油量有显著增加时,表示水冷式冷却器有漏水的现象.
c.冷却器(Cooler)
空冷式冷却管检查冷却管表面尘埃和污染油之附著状态,如有显著污染之情况时,或在日常检查时即发现有油温上升,冷却效果低落时,即应分解清洁之.
水冷式冷却管水垢附著於冷却管壁时,会使冷却效果降低,可先检查其管路上的过滤器,再印证日常检查之结果,如确定效率显著降低,应分解清洗.如不须分解时,应检查各迫紧部份及配管接头部份有否漏油的现象.确认电磁阀和恒温计之动作正常.
压力表(preure gauge)
检查接头部份有否漏油现象,表面之玻璃有否破裂.如指示误差和应答性太差时,分解之并检查其喷口(nozzle)部份有无堵塞.
过滤器(filter)
将油箱内吸入口配管上的过滤器拆下,取出滤蕊清洗之.并检查网目有无破损,开口太大的现象.
附外壳之过滤器,应将其外壳拆下倒掉里面的液压油,内部清洗乾净,同时检查有无生銹,破损.
检查旁路阀(By-pa Valve)之动作是否正常.
按装时要注意不可伤及滤蕊之网目,并注意迫紧之按装方式.
管路过虑器(Line filter)
将整个系统之管路过滤器拆下并分解之,检查,清洗.
将检查重点放在尘埃的附著量,变色(细微之尘埃附著)以及附著物之大小和性质.检查其性质可推定污染物之发生源.
以乾净之煤油,汽油等溶解性液体清洗.
以质地较好的尼龙(nylon)布擦拭表面.
再以洗涤液彻底清洗乾净.
其他检查项目及注意事项如同第(e)项.
g.压力控制阀(Preure control valve)
制压阀,减压阀,顺序阀,抗衡阀等之检查程序如下述:
分解检查先导形控制阀之先导阀门(pilot poppet)及其阀座上之接触面,若有磨损,痕迹过甚者,应及早更换(阀门部份可视为消耗品).此外要检查弹簧有否变形,破损,O形油环是否松弛和变形等.
以手动方式确定主圆轴(main spool)之滑动平滑无阻.
於日常检查时发现有压力表指针振动,动作缓慢及不安定现象等情形时,应藉此机会小心检视内部机件之动作状态.减压阀,安全阀,顺序阀等由於动作较不频繁,故3个月检查一次足矣,直接动作型之压力控制阀亦如是.但主要仍需视实际情况而定,并非绝对如此.
h.电磁阀(Solenoid Valve)
对於用为安全装置之电磁阀,如使用於卸载回路者,应妥为检查,先以手动操作方式确定所有之动作正确无误.通电後检查切换时之振动和声音,固定螺丝之松动和电磁阀内可动部份之磨损,手之触觉(对振动)和人耳的听觉(对声音)来加以判断,如有不正常时应分解作详细之检查.此外若闻有臭味时,可能是线圈之绝缘材料不良,要注意检查以防线圈烧毁.
於日常检查时发现有通电後之磁音和温度上升之现象,应藉此机会分解检查.
i.方向控制阀(Directional control valve)
检查按装部位之螺栓,配管部份,放洩配管和先导配管部份之振动和有无松动,漏油之现象.
对日常检查发现时之异常现象,做详尽之分解检查.
j.流量控制阀(Flow control valve)
检查按装部位之螺栓和配管部份之振动和有无松动,漏油之现象.
对日常检查发现之异常现象,作详尽之分解检查.
k.蓄压器(Accumulator)
检查气体之封入压力.以压力表测定当油压力为0时,回路之最低工作压力应保持在原来之60%至70%之间,且不得低於制压阀设定压力之20%至25%.
以肥皂水涂抹蓄压器之外缘,检查有无漏气的现象.对於气囊式和活塞式之封入部份以及填料部份应详加检查.
对於重锤式之蓄压器则应检查其柱塞和外部是否有漏油之现象.
日常检查之追踪处理.
l.配管(piping)
以手触摸各接头,法兰(Flange)之下部,检查有无漏油现象.
检查先导配管,放洩配管支撑部之振动,并看有无漏油.
检查整个系统配管的支撑部有无松动,及其振动之情况.
分解各配管接头部份,检查其内部之生銹情形,并更换油封带( Seal tape)
m.其他
检查液压缸,液压马达之固定螺丝有无松动及漏油情形,尤其对於较为复杂,於日常检查时无法确认之问题,应仔细检查.
高压油管之松动,变质,伤痕等,都应列为定期检查之重点,如发现有不良情形即刻换新(高压油管视为正常消耗品).
检查压力开关,继电器和极限开关等电气系统的零件,动作是否正常.
液压系统性能检查
储油箱内之油温维持50℃至60℃,并保持整个系统之压力为最高之工作压力,以检查油压装置全体之运转上和操作上之性能.此时宜参使用说明书上所示之性能资料,以检验设备之性能是否衰减,其检查流程如表十二.表十二 性能检查流程
其检查重点如下:
来回几次卸载,负载之操作,以检查泵浦之噪音及振动.
检查压力表指针之振动.此外也要检查制压阀之振动声音.制压阀之性能正常时,压力表指针之振幅,应在最高压力之±3%以内.
使用最高之工作压力,操作方向控制阀以检查切换时之振动与陡震.并检查止回阀有无震颤(chattering)现象吊起之噪音.
检查油压缸及液压马达之动作状态.
动作中之速度.
起动,停止时之状态(变速动作,陡震).
停止状态时有否自然下降或前进之异常现象.
应答性(电源接上後至油压缸和油压马达动作之时间).
检查整个系统之配管振动,尤其应注意控制阀切换时放洩配管,先导配管之振动和发热情况.
操作系统之压力控制阀(制压阀,顺序阀,减压阀,抗衡阀,卸载阀,安全阀等),以确认压力之升降是否正常其压力设定是否正确.
操作压力开关以确认其动作和压力设定.
确认恒温计之动作与温度设定.
全系之控制阀於中立位置时,检查流速音及回流侧配管之放洩量.
检查储油箱之压油油量.
以上在性能检查时,若发现有不正常时,应立即究明原因,并排除之.此外应在运转管理记录表上,详细记明检查处所及状态.
(3) 综合检查
A.综合检查之目的在於检查油压设备全体之性能,效率,寿命等,并针对性能低劣和容易故障之处所加以修理.且检讨,判断更换之必要性.
B.与他类检查不同,综合检查不著重於设备动作信赖性的检查,而是诊断其效率之变化和寿命.共就故障加以修理及研判对策.
C.发觉使用上不妥的部份以及寿期将届的机件,并加以改正或更新.
D.详细检讨研判运转管理记录表,将检查重点置於长期使用的机件和故障频繁的部位,并釐订未来一年维护的重点,预测机件更新之时间表.
E.综合检查著重於整个装置主体之分解及性能检查,故应预先吸取相关知识,如详细研读使用说明书和构造图面等.
F.对於新设备或旧设备之诊断,最好能有专门人员指导.
综合检查之程序如表十三.综合检查程序检查要点如下:
泵浦
运转时躁音太大或运转时间超过3,000小时之泵浦,应予分解检查.
分解泵浦并检查内部之滑动部份的磨损情形.泵浦主轴油封的磨耗,主轴的磨损,主轴轴承座,轮叶和凸轮环,转子,齿轮之齿端和侧面,活塞和斜板等滑动部份之磨损,伤痕,都应仔细检查.
铁銹,毛头,磨损,伤痕等的修整,不良部分的更新,都应审慎从事.在重新组立之前,各类机件均要清洗乾净.组立完成後应行性能试验.
试验内容包括压力升降,压力变动,容积效率(测定泵浦之排出量),噪音之测定等,并与初期之性能作比较检讨.仔细测定马达主轴与泵浦主轴之同心度,检查联轴器之按装,配管之连接,固定螺丝之状态等等.
储油箱内部
将全部之液压油放光.经液压油分析的结果颢示仍然正常时,将储油箱上部以下80%的乾净油取出存入油桶内,底部20%受污染的油丢弃.
以轻质油(如煤油)将储油箱内壁仔细冲洗乾净.
检查油箱内之处理(如涂装)状态,若发现有剥离及生銹的情形,应在除却後再加以表面处理.铁銹大部份都发生在储油箱上盖之内面,涂装离则大部份发生在底面,泵浦吸入口附近.
检查储油箱四周之填料,如发现有膨胀太大等不良时,宜即刻更换.
检查压油之过滤(20μ之过滤器足矣),并添加液压油至容许之最高油面为止.
油面计之动作确认
应先将储油箱里的油汲出.
对直接式之油面计,观察指示板之油量升降是否正常.
对隔测式之油面计,以手触摸或手动方式确认其动作正常与否.
恒温计,油温计
储油箱须开放
将棒状温度计之感温部浸至油面以下,量得之温度再与其他之温度计之读数比较,检查使用於该系统内温度计之误差.
检查温度计之感温部在储油箱内底面的位置.感温部不能在储油箱液面下限之上.此外,储油箱内之最低温度在箱底之处,最高温度则在箱预之处,故温度计之感温部宜在油量容许下限和箱底之中间最为适当.空气滤清器
将滤清器之上盖打开,取出过滤蕊子并予更新.
液压油之分析
液压油使用6个月以上时,应进行化学分析以检查其劣化,污染的程度.对於一般之液压装置,除了应用化学分析判断液压油之污染外,也可检查滤清器污染,堵塞的程度(质和量),用以研判液压油劣化的情形.
冷却器
水冷式之冷却器,应将其本体和热交换部份分解,并把水份仔细清除.
检查冷却管之变色,缺口和接绛处有无裂隙.尤其要注意流入口流出口部份,管的表面变化,控制阀底板,端板之配管有无缺口或松动以及冷却管的磨损与腐蚀,这些都是检查的重点.
冷却水管道内水垢很多时就应检查水质.若在冷却水配管的途中设有过滤器时,也应拆下检查.
检查填料并加更新.
对於空冷式冷却器之检查,应著重於缺口,松动等的缺点.
压力控制阀
分解检查所有压力控制阀的内部机件.
取出阀门,弹簧,活塞,并依下述重点检查之.
生銹(特别是在滑动部位).
缺口,磨损,偏心(单边磨损),毛头.
尘垢之附著(特别是在细孔部).
弹簧之变形,破损.
本体滑动面,阀座部以及铸造部份.
以手动方式检查圆轴管和本体之间隙,此外以自由落体之方式检查圆轴管之动作.
长期使用後应检查其内部洩漏量和放洩量.尤其对於前者,若发现有异常时应作内部洩漏试验,并判断更换之必要性.
电磁阀
各自选择使用最为频繁,最不频繁和故障次数最多之电磁阀,加以分解检查.
检查电气系统之端子板,配线,电阻及电压等.
圆轴阀
选择使用最为频繁,最不频繁和故障次数最多者,加以分解检查.
依下述重点检查
全体之污染物附著状态与生銹之情形.
滑动面之缺口,腐蚀,磨损,毛头等.
本体内之滑动面和铸造部份.
弹簧之尺寸,变形和破损.
附有孔道者,检查有无阻塞,缺口和腐蚀等.
检查内部洩漏量,先各别检查有无异常,再检查所有之控制阀的总和洩漏量.
流量控制阀
将使用最为频繁之控制阀分解检查.
主要检查下列各处.
孔口部份之缺口和磨损等.
压力补偿机构之轴和弹簧之状态.
限流状况和刻度之关系.
其他之控制阀
卸载回路和安全回路中所使用的机件,使用较为频繁的直角止逆阀,先导操作止逆阀产生高背压之各种阀件,若使用频繁,且使用条件较为苛酷者,均应详细分解检查,尤其动作信赖性要求较高者应注意.
伺服阀和用在伺服回路的精密控制阀,较难调整应请专家或制造商的专人指导.
检查配管内部污染物的附著状态和生銹的情形,污染物附著的情形很严重时,整个液压系统应加冲洗.机能诊断
在油温为50℃至60℃,压力为最高压力的条件下,进行下列之机能试验.
检查泵浦之输出量,噪音和振动等.
所有之压力控制阀均应经确认其动作并设定在适当之值.
调整流量控制阀之设定值.并检查液压缸及液压马达之动作.
检查方向控制阀之动作,并调整其切换时的冲击和速度.此外要检查在回流侧之内部洩漏量,以期早日发现大量洩漏的不良,若有洩漏增大的现象时,应检讨回路此时之必要油量和泵浦现时的输出量是否能够配合,泵浦效率如己降低,无法提供充足之油量时,应考虑更换洩漏量太大的控制阀.
确认电磁阀之动作.以手触摸和听觉判断噪音,电磁音和动作不良.
检查油压缸之性能
检查活塞迫紧和活塞杆迫紧是否良好.此外应检查活塞杆有无伤痕和磨损之情形.内外之洩漏量太大时,应分解检查之.
检查固定螺丝有无松动.
检查液压马达之放洩量和噪音,如果认为有异常时应分解检查.
确认液压装置之所有机能如速度控制,振动,蓄压器之动作,应答性等.
检查配管,配管接头,配管支撑等,确认有无松动和振动.尤其对於高压橡皮管更应仔细检查,看有无伤口,变质等并判断其堪用时限.
再检讨运转管理记录,以发现问题点设法改良.例如过滤器容易不足,冷却器容易不足,泵浦之馀裕率不足,蓄压器容量不足等.
将液压装置整个系统清洗乾净,早期发现液压油洩漏,使操作顺利,此外外观之涂装,危险标示,操作上注意标示等,应重新妥为整备.
检查安全控制装置和指示装置之机能.
检查整个系统有关电气控制之机件.
注:此文中所述器件,非我厂每一台设备均相同配置,请按照实际情况逐项检查之.
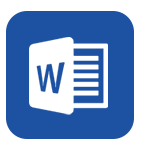