2014年度下沙质量总结报告
酒庄2014年度下沙工作于11月7日截止,历时20天。据现场监测结果显示,其下沙操作与工艺标准的符合率较高。因此,就整体而言,本年度酒庄下沙工作质量较好。但是,下沙过程中也存在诸多问题。下面,本人将根据现场监测的结果,客观总结数据,深度剖析问题,积极提出相关问题的建议性解决措施,对本年度下沙工作质量情况做一次总结性汇报,以期能在糙沙过程中提高生产质量。其中某些认识不足之处敬请领导审议和指正。
一、下沙问题汇总及分析总结
(一)、现场监测的符合性及问题分析
本年度酒庄下沙无磨粮工艺。故在剖析酱香型白酒生产工艺基础上,对下沙过程中影响酱香白酒发酵的18个工艺关键点做出跟踪监测;对不符合工艺标准的监测项目做出原因分析并提出可行性解决措施;同时,对各班组出现的重点问题做出统计。具体监测项目与标准的符合率如下表1,各班组重点问题统计如下表2:
表1 监测项目与标准的符合率
表2 各班组重点问题汇总
从表
1、2可以得出:
1.润粮水温、润粮堆积温度、上甑操作质量、锅底跑气情况、堆积时间、封窖质量、保窖质量共7项与工艺标准的符合性非常好。
2.蒸粮熟度、伴曲温度、收堆温度共3项与工艺标准的符合性较好,但依然存在蒸粮过熟、温度偏高问题,且在表2中体现出其严重性。
其中,蒸粮熟度与标准的平均符合率为77.3%,其整个下沙过程熟度呈现如下现象:下沙开始前两天蒸粮熟度未达七成,接下来五天左右蒸粮熟度稍过七成熟,余下期间蒸粮熟度均在七成熟左右。
就上述现象原因分析如下:下沙开始前两天蒸粮沿用之前的时间标准(120min),此时的时间标准无法使未磨高粱达到熟度要求;而后,生产部门为达熟度要求,过于延长蒸粮时间,导致蒸粮熟度普遍过七成熟;鉴于蒸粮熟度的不稳定性,通过现场收集数据,从而找到了与熟度标准相适应的蒸粮时间,故下沙后期蒸粮熟度稳定在七成熟左右。
另外,伴曲温度、收堆温度与工艺标准符合性不算太高的原因主要是部分班组摊凉时间较短,熟沙温度未降到适当值时即刻收堆。因此,通过现场监控协调延长摊凉时间后,相关温度得以控制。
3.生沙与母糟拌合均匀程度、上甑时间、上甑气压、蒸粮气压共4项与工艺标准的符合性较低。
生沙与母糟拌合不均匀的原因有:母糟未打散遂拌合、打散后抱斗拌合,经整改后,母糟需打散,工人把打散后的母糟用铁铲平铺于甑前生沙上,从而保证每上一甑生沙均含有一定量细碎母糟。
下沙上甑时间大部分未达标准要求的25—35min,多处在21min左右,因此下沙上甑时间与标准的符合性较差。尽管如此,上甑操作质量却处于较高水平,极少出现未见气上甑的现象。可见酒庄下沙上甑时间与之前标准不太适应,遂上甑时间标准有待修善。
部分酒甑上甑气压、蒸粮气压出现低于标准最低控制线0.15Mpa现象,其符合率偏低的原因与相当部分气压表显示偏低关系密切,为解决气压偏低问题,已与设备部联络更换已鉴定气压表。
4.润粮水量、跑水现象、蒸粮时间、堆积温度共4项与工艺标准严重不符合。因此,其问题也最明显。
本年度酒庄下沙润粮水量严重超过标准28桶,处于33桶左右,同时润粮过程跑水严重。
究其原因分析如下:本年度酒庄下沙无磨粮工艺,高粱吸水较差。因此,为保证高粱尽可能吸收水分,生产部根据实际情况加大了润粮水量,同时也导致润粮过程严重跑水。
本年度下沙蒸粮时间除磨粮实验班五班外,其余班组均超过标准(120min),其平均符合率为6.6%。
究其原因分析如下:普通班组同样受到磨粮工艺影响,之前的蒸粮时间标准已经不能满足熟度要求,为达熟度要求必须延长蒸粮时间,故沿用之前标准的符合率仅为6.6%,当蒸粮时间定为150分钟左右时,其符合率为52%。
酒庄下沙时堆子腰部积温度普遍高于标准最高控制线48℃,其原因分析如下:下沙堆积发酵升温较快,一般丢堆24h后堆子腰部表面往下3—15cm处温度即可达到标准要求的45—48℃,然此时处于本班下班期间,不便下窖,而隔一天后再下窖,必然烧堆,温度达50—60℃,故堆积温度与标准符合率仅为17.6%。
(二)其他相关问题汇总、原因、措施解析 1.前期所有班组润粮用水浑浊。
原因:加热沸腾后灌内水垢脱落致润粮水浑浊 处理措施:先清除水垢再加热润粮用水。
2.十七班班十八班润粮时所用水桶与其他班组不一致,使加水量不同。 原因:标准不锈钢水桶丢失一只。 处理措施:糙沙时从新补充一只标准水桶。
3.部分班组润粮前,高粱分配不均匀,导致各堆高粱总量不一,最终影响润粮效果。
原因:物流部所送高粱连续堆放,未按相应袋数分开堆放。 处理措施:糙沙送粮按每堆所需袋数分开堆放。 4.所有班组润粮翻拌操作质量较差即未铲通。 原因:翻拌节奏欠协调,力度不够。
处理措施:协调翻拌节奏,尽可能由男工完成。
5.若润后高粱第二天不及时蒸粮,再堆一天后易发霉生牙,降低高粱利用率。 原因:充分吸水的高粱在中温、高湿、长时间堆积环境下易发芽生霉。 处理措施:可在堆积期间用行车翻拌一次并适当浇灌少许热水。 6.多数班组上甑过程中,甑内粮食未呈锅底状即边高中低。 原因:上甑工对上甑标准认识不足或操作技能欠佳。 处理措施:以班为单位,各班长现场培训指导。 7.大部分班组甑盖跑气。
原因:生产部实验高压蒸粮,排气阀门调至半开状态致甑内压力大于甑盖压力。 处理措施:以与设备部沟通,进行了甑盖加压处理。 8.少部分班组下甑后往甑内注水。 原因:班组擅自增加补水工艺。 处理措施:取消补水操作。
9.部分班组上堆不均匀,导致堆积发酵升温不一致。 原因:上堆时行车工未将斗内糟醅均匀铺在堆子表面。 处理措施:以班为单位加强行车工上堆理论及实践培训。
10.部分中班下班后晾堂窗户未关,导致堆子迎风面与背风面升温不一致。 原因:班组质量意识淡薄。
处理措施:班组应加强监督管理,中班下班后应检查晾堂窗户关闭情况。 11.前期实验班5班磨粮粉碎度偏低。 原因:磨粮机调节欠佳。
处理措施:进行多次调节试验,确保磨粮粉碎度达标。 12.下沙所用尾酒酒精度未达标准8—15%(v/v)。
原因:全封闭连续式的尾酒流酒及储存系统难以有效监控其酒精度。 处理措施:糙沙过程中尾酒随接随用,接酒工适时监测尾酒酒精度保证其符合标准。
13.前三个窖未使用新老窖泥混合封窖。 原因:老泥保管较差,已发臭,不宜利用。
14.六车间甑区同一甑子电子气压表与普通气压表显示不一致。 原因:两种气压表均未校准。
处理措施:设备部应及时拆卸校准后启用或使用更换校准后的新表。 15.六车间润粮区域无排水沟,润粮后积水难排。 原因:润粮跑水严重,无排水沟排水。 处理措施:使用人工清扫排水。
二、下沙各部分粮醅理化检验结果总结
为探究无磨粮工艺的下沙糟醅水分变化情况,质检部分别对上甑前高粱、下甑熟沙、丢堆糟醅、下窖糟醅进行了水分检测,其最终检测结果分析总结如下:
沙上甑前高粱水分平均值35.2%。下甑水分平均值为35.7%。丢堆水分平均值为37.21%。。下窖水分平均值为37.27%即总体在标准(36—40%)范围内,下沙下窖糟醅的水分合格率为70.63%,其中水分偏低率20.63%,一号窖水分偏低的班组较多,水分偏高率8.73%。
从上述结果可得出如下两个结论:
其一,当上甑前高粱水分含量在35%左右时,下窖水分含量基本能保证在标准范围内。
其二,丢堆糟醅与下窖糟醅水分含量差别不大,为保证糟醅水分检验报告指导下窖可提前一天取样。
三、糙沙现场监测工作安排
首先,就糙沙现场检测项目而言,由于下沙与糙沙工艺相近,故监测项目与下沙不变,但在糙沙监测中当对下沙过程中出现问题频率较高及对生产质量影响较大的项目做出重点监控。通过对下沙生产质量的分析,不难得出下沙生产过程中出现频率较高且对生产质量影响大项目有:润粮操作质量及跑水情况、伴曲温度、收堆温度、上甑气压、蒸粮气压、甑底是否添加谷壳、下窖堆积温度等。
其次,就现场违反工艺操作或不满足标准要求所呈现的问题将全面汇总呈报,其中能在现在处理的当现场处理,而需开出纠正预防单或工作联络单整改的当与相关部门沟通解决,继而不断跟踪验证,确保整改效果。
综上所述是我对2014年度酒庄下沙工作质量的分析和总结,如有分析不到或者不正确的地方,敬请领导指正。
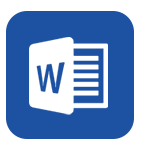