3D打印技术以及在快速铸造成形中的应用
字数:2572
来源:环球市场 2017年11期
字体:大 中 小 打印当页正文
摘要:3D打印技术是制造业领域正在迅速发展的一项新技术,其核心思想为增材制造。它以数字模型文件为基础,运用粉末状金属或塑料等可粘合材料,通过逐层打印的方式来构造物体。它无需模具,产生极少的废料,有效缩短了加工周期,在非批量化生产中具有明显的成本和效率优势。3D打印技术在铸造行业中的引入推动了传统铸造成形技术的发展和革新,并迅速改变着铸造行业的面貌。
关键词:3D打印技术;快速铸造成形;应用
1 3D打印技术概述
随着科学与生产技术的不断革新与发展,快速成型技术,尤其是3D打印技术逐渐在制造业中已经占据非常重要的地位,成为不可或缺的一种成形制造方法。在不久的未来,以个性化、数字化、网络化、定制化为突出特点的3D打印制造技术将推动第三次工业革命。
3D打印,又称作增材制造技术,是根据前期设计的CAD三维模型,借助计算机软件控制,在打印设备上逐层增加材料堆积成所需制品造型的一种快速成形制造技术。其运作原理和传统打印机工作原理基本相同。传统打印机是只要轻点电脑屏幕上的“打印”按钮,一份数字文件便被传送到一台喷墨打印机上,它将一层墨水喷到纸的表面以形成一副2D图像。而3D打印机首先将物品转化为一组3D数据,然后打印机开始逐层分切,针对分切的每一层构建,按层次打印。其最大的技术优点是能简化制造程序,缩短产品研制周期,降低开发成本和风险。相比传统的制造工艺,应用3D打印技术节省原材料,用料只有原来的1/3到1/2,制造速度快了3~4倍。
2 3D打印的铸造应用
2.1 3D打印技术在精铸模样制作中的应用
3D打印技术首先被应用于铸造模样的制作,尤其是熔模精铸中的模样制作。SLS、FDM、SLA技术均可用于蜡模的成形,但是由于获得的蜡模强度较低,在后续处理工序中易于破损,并不适合于薄壁件的铸造生产。为解决模样强度不足的问题,人们将成形所用的蜡料替换为其它类型材料,这样制备出的模样可以进行一定程度的加工以改善其表面光洁度,提高铸件的表面质量;但是此后又暴露出了新的问题,如基于非蜡模样制备的型壳容易开裂、脱模后残余灰分高等。
在早期采用3D打印技术获得模样的尝试中,型壳开裂在使用非蜡基模料的情况下非常常见,其原因是在去除模样的过程中,模样因受热膨胀而导致了型壳的开裂。为解决这一问题,3Dsystem公司采用了被称为QuickCast的成形方案,通过在制备模样时采用六角形、四方形或三角形的非实体打印模式,将模样内部材料重量减小95%,形成为内部疏松的树脂模样,这种结构可以在较低的温度下就软化并向模样内部溃缩,避免对型壳造成过大的应力,因而可降低型壳的开裂风险。需要注意的是,由于模样内部结构较为疏松,在涂挂工艺之前有必要在模样表面浸蜡并进行表面修整,以便获得平整的型壳内腔,进而浇注出较高质量的铸件。ZCorp公司则采用一种胶质淀粉原料Zp14进行3D打印,所获得的制件经浸蜡后涂挂耐火材料,以制备型壳并最终浇注零件。
2.2 3D打印技术在精铸蜡模压型制作中的应用
受打印周期的限制,模样的直接3D打印一般适用于单件或数件铸件的铸造生产。为了适应于较大批量的铸件需求,有研究者开始将3D打印技术应用于蜡模压型的制作,而后在通过所制作的压型来批量压制蜡模,以提高铸件的生产效率。
压型的3D打印制备分为直接打印和间接获得两种方式。压型的直接获得意味着通过3D打印直接制备出压型,所制得的压型再用于压制一定批量的蜡模。直接金属激光烧结(DMLS)、激光净形制造(LENS)技术均被成功地应用于压型的3D打印[6,7],以满足快速将中等或较大批量铸件快速推向市场的需求。一些情况下,人们通过3D打印首先获得母模,然后使用母模翻制压型,即间接获得用于压制蜡模的压型。室温固化硅橡胶制模、环氧树脂制模、喷涂金属制模等技术都被成功应用于压型的间接3D打印制造。以采用室温固化硅橡胶制模工艺的精密铸造为例,其工艺实施过程如图5所示,蜡模的制备需要通过如下步骤来完成:(a)建立铸件的CAD模型;(b)采用SLA方法制备光固化模样;(c)翻制RTV硅橡胶压型;(d)压制蜡模。所压制的蜡模经修整、组合后,即可进行涂挂制备型壳,完成后续的精铸流程。工艺适用性评估表明,当铸件需求量在数十个的量级时,这一工艺具有较佳的适用性。
2.3 3D打印技术在铸型制作中的应用
3D打印技术也被应用于陶瓷型壳的直接成形。1993年,位于美国加州的Soligen Technology公司在麻省理工学院发展的3DPAM技术基础上,搭建了直接型壳制作铸造系统(DSPC),直接制备出包含内部芯子的陶瓷型壳,减少了传统熔模精铸中蜡模压制组合、制壳脱蜡等繁琐工序。该DSPC系统通过多个喷头喷射硅溶胶的方式将刚玉粉末粘结起来,未被粘接的刚玉粉被移除,从而获得型壳,所制备的型壳在进行高温焙烧以建立足够的机械强度后,即可进行金属液的浇注。DSPC系统可以用于实现任意形状的零件生产,同时也可适用于包括铜、铝、不锈钢、工具钢、钴铬合金在内的多种不同金属材料的铸件获取,铸件的生产周期可由传统熔模精铸的数周缩减至2-3天,目前这一系统已经被用于制造铸件原型及小批量的全功能铸件生产。
3D打印技术也正在改变砂型铸造工艺流程现状。在传统的砂型铸造生产过程中,需要熟练的技术工人依据图纸或模样来制作砂型,造型、制芯等工序往往耗费大量人力和时间。通过引入3D打印技术,这種局面也正在得到改变———人们已经可以通过3D打印技术快速制备所需的砂型结构,从而缩短造型工艺周期,减少对熟练技术工人的依赖。
3 结语
3D打印技术作为目前一种先进制造技术,近年来已得到快速发展,实际应用领域逐渐增多。但其推广力度还不够大,应该加强教育培训,促进3D打印技术的社会化推广;加大科技扶持力度,提升3D打印技术水平,扩大其在铸造成形领域的技术应用。
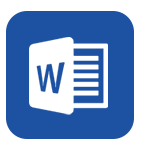